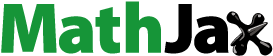
Abstract
Poly (ether-ether-ketone) (PEEK) is one of the most promising engineering plastics in aerospace engineering because of their reliable mechanical properties under various conditions. However, next-generation engineering plastics also call for more comprehensive outputs, such as higher thermal conductivity and antiwear performances. Boron Nitride Nanotubes (BNNT) have been proven to have outstanding physical properties as additives to the resin of the composites. In this article, the influence of BNNT additives on the PEEK resin is studied to provide a more insightful understanding of the development of BNNT-reinforced engineering plastics in the future. It has been found that the interfacial shear strength (IFSS) between BNNT and PEEK is 151% higher than carbon nanotube reinforcements., and amino groups (–NH2) modified BNNT can further improve the IFSS value by 14%. This mechanical improvement is further evaluated, and the molecular mechanisms are explained with an atomistic resolution.
1. Introduction
Thermoplastic components are attracting more and more attention due to their outstanding physical properties and environment-friendly characteristic [Citation1–6]. Poly (ether-ether-ketone) (PEEK) is one of the most popular engineering resins as it can stably work under harsh conditions, such as a temperature up to more than 300 °C [Citation7,Citation8], and chemically corrosive environments [Citation9]. Compared to similar high-temperature thermoplastic resin polyphenylene sulfide, the facture toughness of PEEK is significantly higher [Citation10,Citation11], which broadens the application of PEEK as load-bearing components in mechanical devices. However, the mechanical performances of PEEK resin are still insufficient while facing harsh loading conditions and various additives are considered to improve the mechanical properties of PEEK material, such as fibers (carbon, glass, and Kevlar [Citation5,Citation12–14]) and nano-additives (carbon nanotubes [CNTs] and graphene [Citation15,Citation16]).
Boron Nitride Nanotube (BNNT) has been first synthesized in 1995 [Citation17,Citation18] and after nearly 30 years of development, this advanced functional material has been applied in many fields, such as thermal conductive units [Citation19], biomedical applications [Citation20], electrical and optical devices [Citation21–23], ion separation [Citation24]. For the mechanical performances of BNNT, many works have been conducted on buckling properties [Citation25,Citation26], dynamics properties [Citation27], etc. The mechanical properties of single BNNTs have been investigated utilizing both molecular scale experiments [Citation28] and multiscale modeling, it has high Young’s modulus approximately 1 TPa and a tensile breaking strength around 10–30 GPa [Citation24,Citation29–31]. Despite these mature studies on the performances of single BNNTs, a significant challenge remains in the wide-scale application of these materials. Studies on polyurethane/BNNTs bulk composites have shown that while 0.5 vol% BNNTs enhance the compressive modulus by 38.2%, a concentration of 2% vol% BNNTs increases it by a mere 6.3% due to the clustering effect [Citation32]. Moreover, the mechanical properties of BNNT/polystyrene (PS) composites have been found to improve with the addition of just 1 wt% BNNTs, with a 21% increase in the Young’s modulus [Citation6]. The mechanical and thermal properties of polyvinyl alcohol (PVA) nanocomposites, reinforced by OH-BNNT, found that the tensile fracture strength, Young’s modulus, and elongation at failure of 1.0 wt% OH-BNNT/PVA nanocomposites were increased by 46%, 55%, and 45%, respectively, as compared to pure PVA, which was attributed to the strong interfacial interactions between OH-BNNT and PVA chains [Citation33]. Despite these advances, the underlying reinforcement mechanisms remain largely unknown. Understanding these mechanisms can guide the reliable fabrication of BNNT-reinforced polymers, especially in thermoplastic resins (comparison to thermoset polymers) with low viscosity, poses a significant challenge [Citation34]. Therefore, the BNNT–thermoplastic resins interface bonding and stability, should be carefully addressed [Citation18].
The molecular dynamics (MD) modeling method has been widely adopted to study the mechanisms of how nano-additives interact with polymer matrix and affect the physical properties of composite products [Citation35–38]. The advantage of this method is that the configurational change of these nano-composites can be characterized with a molecular resolution, which reflects how the nano-additives sensitively mediated the physical properties of multi-phase composites at the molecular scale. MD pull-out simulation is currently the novel and widespread technique for investigating the properties of nanomaterial-polymer interfaces [Citation39–41]. For example, Cui et al. investigated the interaction between BNNTs and rubber materials has been studied using the MD pull-out simulation technique and explained the mechanisms of how BNNTs change the overall mechanical performances of BNNT-reinforced rubber material, especially for the property of interface between BNNTs and rubber matrix [Citation42]. Our previous studies on CNT-reinforced PEEK nanocomposites have found that the functionalization strategy of CNTs could significantly improving the interfacial shear strength (IFSS) and Young’s modulus of the CNT/PEEK nanocomposites [Citation15]. Song et al. utilized MD tensile simulations to investigate the load transfer behavior between amine (–NH2)-functionalized CNTs and the epoxy resin matrix. The results indicated an impressive increase of 1195.8% in the maximum interfacial shear stress (ISS) of the functionalized CNT composites compared to the original CNT/epoxy composites [Citation43]. Taghavi et al. studied the interfacial bonding of BNNTs with PS and polythiophen through MD simulations, suggesting that BNNTs might be more effective than CNTs in enhancing applications of nanocomposites [Citation44]. Yang conducted MD simulations on the thermal elastic behavior of BNNTs/polymethyl methacrylate (PMMA) and CNTs/PMMA nanocomposites, the results showed that BNNTs improved the Young’s modulus of the composites more than CNTs, attributed to stronger interfacial bonding between BNNTs and the PMMA matrix [Citation45]. Although a large number of MD simulations have been conducted to study the effects of nanotubes on the interfacial behavior and mechanical properties of polymer composites, similar studies characterizing the interfacial properties between BNNTs and engineering plastics PEEK have not been reported. Therefore, molecular modeling based on MD is required to explore the molecular mechanisms of enhancement and fracture by BNNTs in PPEK nanocomposites.
In this article, the mechanical properties of new system BNNT-reinforced PEEK composites are modeled based on the MD simulation technique. The interfacial bonding property and overall mechanical outputs of BNNT-reinforced PEEK composites are predicted, and compared with those of CNT-reinforced PEEK composites, and the physical mechanisms of the reinforcing effects by BNNTs are explained based on molecular modeling results.
2. Simulation methods and models
The mechanical and interfacial properties of BNNT/PEEK nanocomposites were investigated using MD simulations, as well as CNT/PEEK nanocomposites that are chosen as a control group. The PEEK molecular chains, CNTs, BNNTs were built using the Builder module in Material Studio 8.0 platform (Accelrys, San Diego, CA) by selecting the appropriate monomers and nanostructures, connecting them together, and aligning them as required, as shown in . The visualization was achieved by using the Visual Molecular Dynamics software [Citation46]. Molecular simulations were carried out using the GROMACS 5.1.5 package [Citation47]. The description of atomic interactions in CNT/PEEK and BNNT/PEEK nanocomposites is obtained from GROMOS 54A7 [Citation48] force fields, and the development of force field parameters is conducted on the platform of Automated Topology Builder (ATB) platform [Citation15,Citation49]. The interactions between boron and nitrogen atoms in BNNTs using the parameters proposed in the literature [Citation50], and the parameters of the CNT model are derived from another literature [Citation51].
2.1. Modeling of nanotube/PEEK nanocomposites
To investigate the stochastic reinforcing effect of BNNT and CNT on the mechanical properties of the PEEK matrix, three molecular models were developed, including the PEEK model, BNNT/PEEK nanocomposites model, and CNT/PEEK nanocomposites model. As shown in , in the representative volume element, some 2.8 nm (5,5) CNT molecules or 2.9 nm (5,5) BNNT molecules were randomly distributed, and the matrix contains 10 PEEK chains (60 repeating units of PEEK in each chain), with a size of 7.3 nm × 7.3 nm × 7.3 nm.
To obtain a reasonable initial configuration for the following MD simulations, the initial models were first optimized using the steepest descent algorithm with a tolerance of 10 kJ mol−1 nm−1, NVT ensemble was then performed, using the Nosé–Hoover temperature control method [Citation52] with a controlled temperature of 300 K and incorporating a simulated annealing process with a duration of 2 ns. Finally, a 1 ns NPT ensemble simulation at 300 K [Citation53] using the Parrinello-Rahman pressure control method [Citation54] was conducted to remove internal stresses in the models. The density of the equilibrated PEEK model, CNT/PEEK nanocomposites, and BNNT/PPPEK nanocomposites were 1.20 g cm−3, 1.21 g cm−3, and 1.24 g cm−3, respectively [Citation55]. After the equilibration, a uniaxial tensile simulation was performed for 2 ns with a constant strain rate [Citation35,Citation56]. Periodic boundary conditions (PBCs) were employed during these uniaxial tensile simulations.
2.2. Simulation of nanotube pull-out
Previous studies performed a pull-out simulation of CNT from PEEK matrix and calculated the IFSS [Citation15]. Based on this approach, we incorporated an energy minimization process during the pull-out process to stabilize the system and eliminate potential energy instabilities, and increased the number of data points of energy output for a better comparison of the gap in calculated values (IFSS and interfacial interaction energy). The pull-out simulation of nanotubes was performed in this section using the improved methodology. As illustrated in , a 4.92 nm (5,5) CNT or a 4.98 nm (5,5) BNNT was embedded in the middle of the simulation box. Afterward, six PEEK chains (each chain contains 60 monomers) were loaded into this simulation box. Then, energy minimization and 1 ns NVT and 2 ns NPT relaxation simulations were performed at 300 K in turn, and CNT or BNNT are fixed along their axes during this simulation process.
Modulating the interface through functionalization of nanotubes is a common method to enhance the bonding strength with the matrix. Some studies have investigated the excellent properties of –NH2 as a functional group using experimental and theoretical modeling approaches [Citation57,Citation58]. Therefore, –NH2 functionalization is employed to study the impact of surface modification of BNNTs on the mechanical performance of BNNT-reinforced PEEK materials in this article. Functionalization of nanotubes was conducted using Material Studio 8.0 platform, separately constructing nanotubes and –NH2, the nitrogen atoms in the –NH2 are then linked to the boron atoms in BNNTs and the carbon atoms in CNTs to form covalent bonds, thereby completing the functionalization process. provides the illustration of –NH2 functionalized BNNT and CNT. The amount of –NH2 functionalization is controlled to be the same for BNNTs and CNTs, which are 1 –NH2 per 0.80 nm.
To pull the CNTs and BNNTs from the PEEK matrix, the model in was used as the initial model with the PBC along the nanotube direction. As shown in , the PEEK matrix was fixed during the pull-out process while using non-periodic boundaries for the pull-out direction. CNT and BNNT were pulled in 10 steps at 300 K along the direction of the nanotube axis, each step with a pulling distance of 0.5 nm.
The interaction energy between the PEEK matrix and nanotubes (CNT and BNNT) during the pull-out and uniaxial tension simulations (Coulomb and van der Waals [vdW] interactions) is defined as follows:
(1)
(1)
where,
is the total potential energy of the system,
is the potential energy of BNNTs or CNTs without the PEEK,
is the potential energy of the PEEK without the BNNTs and CNTs.
The IFSS is used to characterize the interfacial properties of nanocomposites and then derive the shear strength of the cut surface according to the following equation. The method can be found in the literature: [Citation15,Citation42,Citation59].
(2)
(2)
(3)
(3)
where,
from Formula (1), is the interaction energy between the PEEK matrix and CNT or BNNT,
and
are the diameter and length of BNNT and CNT, x is the pull-out displacement of CNT and BNNT, and
is the ISS.
3. Results and discussion
In this section, the basic mechanical properties of BNNT-reinforced PEEK composite are modeled by MD methods, including Young’s modulus and ultimate strength. The interfacial bonding properties are specifically investigated as evidence of the mechanical reinforcement by the BNNT nano-additives.
3.1. Modulation of interfacial bonding
In our previous study, it has been validated that the interfacial bonding property between nanotubes and polymer matrix is sensitive to the functional group modification of the nanotubes [Citation15]. provides the molecular configuration during the pull-out process of nanotubes (both CNT and BNNT). No chemical bonding is defined during the modeling process, and the interaction can be mainly attributed to vdW and electrostatic interactions. However, compared to pristine CNT and BNNT, the –NH2 groups enables the formation of hydrogen bonds between the surface-modified nanotubes and ketone groups in PEEK chains. gives the interaction energy between nanotubes and PEEK. The average interaction energy between BNNT and PEEK is significantly higher than that of CNT, which can be further improved by the hydrogen bonds after –NH2 functionalization. It can be found from that, the IFSS values of CNT-reinforced PEEK and –NH2 modification of CNT-reinforced PEEK are 80 MPa and 114 MPa, respectively, which are same as the previous studies [Citation15], verifying the reasonableness and accuracy of the simulation method. The IFSS of BNNT-reinforced PEEK is 151% higher than the CNT-reinforced PEEK. –NH2 modification of BNNT can further improve the IFSS of BNNT by 14%. This group of results indicates that the mechanical reinforcement of PEEK can be significantly improved by BNNTs compared to CNTs modification. However, the shear yield stress of PEEK is around 60–120 MPa [Citation60], whereas the maximum IFSS for BNNT-reinforced PEEK and –NH2 modification of BNNT-reinforced PEEK exceeds that value, thereafter the shear stress starts to be dominated by the matrix.
3.2. Mechanical properties prediction
After the identification of interaction enhancement by BNNT, the tensile behavior of PEEK reinforced by randomly distributed nanotubes is modeled by the MD method. The loading strain rate can affect the mechanical properties of polymer systems, according to our previous research [Citation15], the Young’s modulus of PEEK obtained through tensile simulations increases with the strain rate, when the strain rate is less than 0.1 ns−1, the Young’s modulus stabilizes and becomes closest to the actual value. It has also been validated that, the results of strength and Young’s modulus are slightly higher than the quasi-static experimental results at the macroscale, which is due to the limit of modeling ability by the MD method. Therefore, in this section, a strain rate of 0.1 ns−1 was chosen as the loading condition for MD simulations.
shows the mechanical properties by tensile simulation of PEEK systems with different weight contents of nanotubes, from 1% to 7%. provides the tensile curves of different nanotube-reinforced PEEK systems with the same weight content of 1%. It can be seen that the yielding limit of CNT-reinforced PEEK comes earlier than BNNT-reinforced PEEK, and the ultimate strength of the material is like each other. summarized the variation of Young’s modulus for PEEK reinforced by different nanotubes, also considering the content of nano-addition, where the values of Young’s modulus for CNT-reinforced PEEK nanocomposites are in agreement with previous studies [Citation15], verifying the reasonableness and accuracy of the simulation method. It can be seen that, compared to PEEK polymer, the increase of Young’s modulus by nanotubes ranges from 11% to 20%, depending on the type of nanotubes, when the weight fraction of nanotubes is only 1%. Among these plans, the –NH2 reinforced material shows the most significant improvement (20%) and the pristine CNT gives the lowest improvement result (11%). With the increase of nanotube weight fraction, Young’s modulus increases from 20% (1 wt%) to 30% (7 wt%) for BNNT-NH2 reinforced PEEK. However, different from the nano-composites with low nanotube weight fraction (e.g. 1 wt% and 3 wt%), the improvement by –NH2 functionalization is not obvious when the weight fraction is larger than 5 wt%.
Figure 5. Tensile modeling results of BNNTs reinforced PEEK. (a) provides the tensile curves of PEEK reinforced by different nanotubes; (b) and (c) Young’s modulus and tensile strength of these nanotube-modified PEEK.
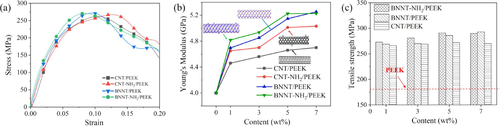
The tensile strength is another important characteristic to evaluate the results of improvement by nano-additives. Herein, we have summarized the reinforcing effects of BNNTs and compared the results with pristine CNTs. The increase of strength by BNNT-NH2 is the largest among all the nanotube reinforcing plans, which is 55%. For pristine BNNT and CNT, the degrees of increase is 53% and 51%, correspondingly. As the nanotube content increases to 7%, the strength increase can be enlarged to 65%. However, considering the high price of BNNT-NH2 addition, the content of 1% is ideal for a general engineering application, which can increase Young’s modulus and strength of the material by 20% and 53%.
To further explain the difference, the interaction energy between nanotubes and the PEEK polymer matrix is summarized in . For all these scenarios, the interaction energy for BNNT-NH2 cases is higher than those pristine BNNT cases, which explains the more outstanding reinforcing effect of the BNNT-NH2. When the deformation strain is smaller than 0.1, for all the nanotube contents (1–7 wt%), the molecular interaction is linearly decreasing. However, when the deformation is larger than 0.1, for the lower content cases (1 and 3 wt%), the interaction energy becomes saturated, which is different from the linear decreasing trend for the higher content cases (5 and 7 wt%). This phenomenon explains the reason why the reinforcing effect is not linearly increasing with the content of BNNTs.
Figure 6. Change of interaction energy during the tensile modeling with respect to the content of BNNTs.
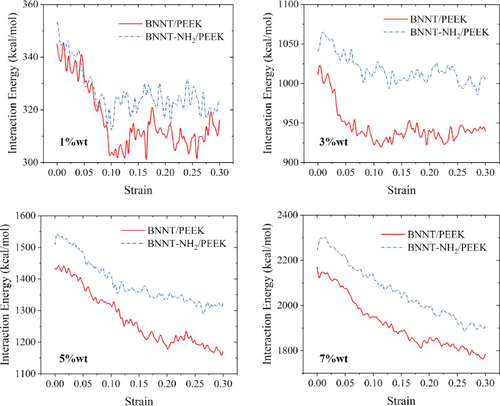
Furthermore, for the BNNT/PEEK nanocomposites (1 wt%), the interfacial interaction energy between BNNTs and PEEK matrix stabilizes at around 300 kcal/mol during the tensile process. In contrast, as depicted in , when a single BNNT is pulled out, the interfacial interaction energy is approximately 700 kcal/mol, significantly surpassing 300 kcal/mol. This indicates that with the increase of tensile strain, once it surpasses the yield stress of the PEEK matrix, the stress starts to be mainly borne by the matrix.
3.3. Molecular mechanisms
The molecular configuration of nanotubes reinforced PEEK is analyzed in this section to further explain the molecular mechanisms of the mechanical enhancement from these nano-additives. provides the interaction configuration of BNNT reinforcement during the tensile simulation. It can be seen that, for pristine BNNT, no polar bond can be formed between the nanotubes and polymer matrix as the BNNT surface does not consist of outstanding positively charged atoms to interact with the ketone group in PEEK molecules. However, with the help of –NH2 modification, the protons in the –NH2 groups perform as the acceptor while the oxygen atom in the ketone group performs as the donor. This coupling interaction forms hydrogen bonds between the nanotubes and PEEK molecules, which explains the further mechanical improvement of BNNT-NH2 reinforced polymers compared to pristine BNNT. The number of hydrogen bonds is summarized during the tensile deformation modeling in , when the nanotube is still embedded in the PEEK matrix, the number of hydrogen bonds has a decrease-to-increase transition because the hydrogen bonds can re-form after the old hydrogen bonds break due to the position change of the nanotubes during tensile deformation. After the nanotubes are pulled out from the matrix, the number of hydrogen bonds can only decrease as no further new hydrogen bonds can be formed.
Figure 7. The molecular mechanism of the nanotube reinforcing effect. (a) the interaction configuration of the BNNT and PEEK interface; (b) the number of hydrogen bonds during the pull-out simulation of BNNT-NH2 from the PEEK matrix; (c) the RDF results for different nanotubes reinforcement plans.
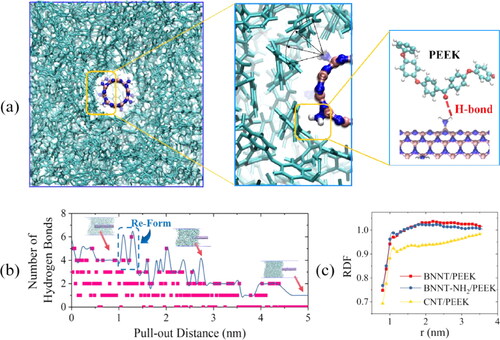
The radical distribution function (RDF) to the position of nanotubes is summarized in . It can be seen that both BNNT and BNNT-NH2 modified PEEKs have a higher RDF value near the surface of the nanotubes, which means a higher density of PEEK molecules can be found near the nanotube surface, which explains the higher interaction energy between BNNT and BNNT-NH2 modified PEEK material in , comparing to the interaction energy in CNT reinforced PEEK materials.
Even though Young’s modulus and strength of the materials are drastically improved by the nanotube additions, the elongation of these materials still significantly decreased compared to pure PEEK materials. This is because the nano-additives introduce nanoscale discontinuity to the polymer matrix. For small deformation cases, these damages will not cause the sudden break of the polymer matrix. However, when the deformation continues, micro-voids started to accumulate from the interface between nanotubes and polymer molecules in the polymer matrix and continued to induce the debonding form the polymer, as illustrated in . This phenomenon indicates that the impact toughness of PEEK material will be decreased by these nano-additives, despite the improvement in stiffness and strength. Further improvement needs to be achieved to increase the impact performance of these functional materials. Such work is being conducted in our lab to achieve this toughness increment by designing the content of fiber reinforcement, including carbon fiber, Kevlar fiber, and long glass fibers.
4. Conclusion
In the present study, the mechanical improvement of PEEK material by BNNTs is investigated by the MD modeling method. The enhancement of interface, Young’s modulus, and strength are studied with an atomistic resolution, as well as the molecular mechanisms. It has been validated that the BNNTs can be ideal nano-additives for the mechanical improvement of PEEK-based materials. The following conclusions can be made from the molding results:
The IFSS between BNNT and BNNT-NH2 nano-additives can be correspondingly increased by 151% and 186% compared to pristine CNT reinforcement.
The Young’s modulus and ultimate strength of the PEEK matrix can be increased by 20% and 53% by only 1 wt% addition of BNNT-NH2 nanomaterials.
The significantly increasing effect of BNNT-NH2 nanomaterial compared to pristine BNNT nanomaterial is due to the hydrogen bonds formed between the –NH2 group and ketones groups in PEEK.
To sum up, MD simulations verified the high-IFSS between BNNTs and PEEK matrix, as well as the addition of BNNTs can significantly improve the Young’s modulus and tensile strength in nanocomposites, to which the addition of –NH2 makes this enhancement more obvious. In comparison with CNT, BNNT can be used as a superior nanofiller, providing more options for further development of high-performance PEEK nanocomposites leading to applications in lightweight structural components.
Authors’ contribution
Zheng Li: Methodology, Validation, Writing—original draft. Tong Li: Conceptualization, Methodology, Funding acquisition, Writing—Review and Editing, Supervision. Zhuoyu Song: Methodology, Writing—Review and Editing. Ke Zhang: Methodology, Writing—Review and Editing. Bo Wang: Methodology, Writing—Review and Editing.
Disclosure statement
The authors declare no conflict of interest.
Data availability statement
Data are available upon reasonable request from the corresponding authors.
Additional information
Funding
Notes on contributors
Zheng Li
Zheng Li, master student in the Department of Engineering Mechanics at Dalian University of Technology. His research area focuses on development of multifunctional nanocomposites.
Tong Li
Tong Li, Associate professor, Department of Engineering Mechanics, Dalian University of Technology. His research interests include the development of multifunctional nanocomposites and multiscale analysis of the mechanical response of composite structures.
Zhuoyu Song
Zhuoyu Song, Ph.D. student in the Department of Engineering Mechanics at Dalian University of Technology. His research area focuses on multiscale analysis of the mechanical response of composite structures.
Ke Zhang
Ke Zhang, member of Sinoma Wind Power Blade Co., Ltd.
Bo Wang
Bo Wang, Director of the Institute of Science and Technology, Dalian University of Technology. His main research interests include structure and multidisciplinary optimisation, advanced materials and structure design for aerospace.
References
- Díez-Pascual AM, Naffakh M, Marco C, et al. High-performance nanocomposites based on polyetherketones. Prog Mater Sci. 2012;57(7):1106–1190. doi: 10.1016/j.pmatsci.2012.03.003.
- Audoit J, Riviere L, Dandurand J, et al. Thermal, mechanical and dielectric behaviour of poly(aryl ether ketone) with low melting temperature. J Therm Anal Calorim. 2019;135(4):2147–2157. doi: 10.1007/s10973-018-7292-x.
- Garcia-Gonzalez D, Rusinek A, Jankowiak T, et al. Mechanical impact behavior of polyether-ether-ketone (PEEK). Compos Struct. 2015;124:88–99. doi: 10.1016/j.compstruct.2014.12.061.
- Zhang Y, Tao W, Zhang Y, et al. Continuous carbon fiber/crosslinkable poly(ether ether ketone) laminated composites with outstanding mechanical properties, robust solvent resistance and excellent thermal stability. Compos Sci Technol. 2018;165:148–153. doi: 10.1016/j.compscitech.2018.06.020.
- Cogswell FN. Components of a thermoplastic structural composite. In: Cogswell FN, editor. Thermoplastic aromatic polymer composites. Oxford (UK): Butterworth-Heinemann; 1992. p. 11–50. doi: 10.1016/B978-0-7506-1086-5.50008-2.
- Zhi C, Bando Y, Tang C, et al. Boron nitride nanotubes/polystyrene composites. J. Mater. Res. 2006;21(11):2794–2800. doi: 10.1557/jmr.2006.0340.
- Attwood TE, Dawson PC, Freeman JL, et al. Synthesis and properties of polyaryletherketones. Polymer. 1981;22(8):1096–1103. doi: 10.1016/0032-3861(81)90299-8.
- Lovinger AJ, Hudson SD, Davis DD. High-temperature crystallization and morphology of poly(aryl ether ether ketone). Macromolecules. 1992;25(6):1752–1758. doi: 10.1021/ma00032a020.
- Yurchenko ME, Huang JJ, Robisson A, et al. Synthesis, mechanical properties and chemical/solvent resistance of crosslinked poly(aryl-ether-ether-ketones) at high temperatures. Polymer. 2010;51(9):1914–1920. doi: 10.1016/j.polymer.2010.01.056.
- Ivanov SG, Beyens D, Gorbatikh L, et al. Damage development in woven carbon fibre thermoplastic laminates with PPS and PEEK matrices: a comparative study. J Compos Mater. 2017;51(5):637–647. doi: 10.1177/0021998316653460.
- Ma C-CM, Lee C-L, Chang M-J, et al. Effect of physical aging on the toughness of carbon fiber-reinforced poly(ether ether ketone) and poly(phenylene sulfide) composites. Polym. Compos. 1992;13(6):441–447. doi: 10.1002/pc.750130607.
- Karsli NG, Demirkol S, Yilmaz T. Thermal aging and reinforcement type effects on the tribological, thermal, thermomechanical, physical and morphological properties of poly(ether ether ketone) composites. Composites Part B. 2016;88:253–263. doi: 10.1016/j.compositesb.2015.11.013.
- Su YN, Zhang SC, Zhang XH, et al. Preparation and properties of graphene/carbon fiber/poly(ether ether ketone) composites. New Carbon Mater. 2017;32(2):152–159. doi: 10.19869/j.ncm.1007-8827.2017.02.005.
- Cao S, Tao Y, Li H, et al. Multiscale hybrid CNT and CF reinforced PEEK composites with enhanced EMI properties. Nanocomposites. 2022;8(1):184–193. doi: 10.1080/20550324.2022.2100683.
- Wang B, Zhang K, Zhou CH, et al. Engineering the mechanical properties of CNT/PEEK nanocomposites. RSC Adv. 2019;9(23):12836–12845. doi: 10.1039/c9ra01212e.
- Arif MF, Alhashmi H, Varadarajan KM, et al. Multifunctional performance of carbon nanotubes and graphene nanoplatelets reinforced PEEK composites enabled via FFF additive manufacturing. Composites Part B. 2020;184:107625. doi: 10.1016/j.compositesb.2019.107625.
- Chopra NG, Luyken RJ, Cherrey K, et al. Boron nitride nanotubes. Science. 1995;269(5226):966–967. doi: 10.1126/science.269.5226.966.
- Golberg D, Bando Y, Tang CC, et al. Boron nitride nanotubes. Adv Mater. 2007;19(18):2413–2432. doi: 10.1002/adma.200700179.
- Chang CW, Fennimore AM, Afanasiev A, et al. Isotope effect on the thermal conductivity of boron nitride nanotubes. Phys Rev Lett. 2006;97(8):085901. doi: 10.1103/PhysRevLett.97.085901.
- Genchi GG, Ciofani G. Bioapplications of boron nitride nanotubes. Nanomedicine. 2015;10(22):3315–3319. doi: 10.2217/nnm.15.148.
- Armaković S, Armaković SJ, Pelemiš SS, et al. Optoelectronic and charge carrier hopping properties of ultra-thin boron nitride nanotubes. Superlattices Microstruct. 2015;79:79–85. doi: 10.1016/j.spmi.2014.12.010.
- Talla JA. Stability and electronic properties of hybrid coaxial carbon nanotubes—boron nitride nanotubes under the influence of electric field. Appl Phys A. 2021;127(8):628. doi: 10.1007/s00339-021-04751-y.
- Jaffrennou P, Barjon J, Lauret JS, et al. Optical properties of multiwall boron nitride nanotubes. Phys Status Solidi B. 2007;244(11):4147–4151. doi: 10.1002/pssb.200776109.
- Azamat J, Sardroodi JJ, Rastkar A. Molecular dynamics simulation of ion separation and water transport through boron nitride nanotubes. Desalin Water Treat. 2015;56(4):1090–1098. doi: 10.1080/19443994.2014.944571.
- Nikkar A, Rouhi S, Ansari R. On the buckling properties of concentric carbon/boron-nitride multi-walled nanotubes: a finite element investigation. Mech Adv Mater Struct. 2019;26(9):816–824. doi: 10.1080/15376494.2018.1430259.
- Guan J, Ashrafi B, Martinez-Rubi Y, et al. Epoxy resin nanocomposites with hydroxyl (OH) and amino (NH2) functionalized boron nitride nanotubes. Nanocomposites. 2018;4(1):10–17. doi: 10.1080/20550324.2018.1457764.
- Yang J-E, Hong YT, Lee J-S. Synthesis and characterization of polystyrene-poly(arylene ether sulfone)-polystyrene triblock copolymer for proton exchange membrane applications. J Nanosci Nanotechnol. 2006;6(11):3594–3598. doi: 10.1166/jnn.2006.17989.
- Ishigami M, Sau JD, Aloni S, et al. Symmetry breaking in boron nitride nanotubes. Phys Rev Lett. 2006;97(17):176804. doi: 10.1103/PhysRevLett.97.176804.
- Song J, Wu J, Huang Y, et al. Continuum modeling of boron nitride nanotubes. Nanotechnology. 2008;19(44):445705. doi: 10.1088/0957-4484/19/44/445705.
- Kang JW, Hwang HJ. Atomistic study of III-nitride nanotubes. Comput Mater Sci. 2004;31(3–4):237–246. doi: 10.1016/j.commatsci.2004.03.004.
- Wei X, Wang M-S, Bando Y, et al. Tensile tests on individual multi-walled boron nitride nanotubes. Adv Mater. 2010;22(43):4895–4899. doi: 10.1002/adma.201001829.
- Li L, Chen Y, Stachurski ZH. Boron nitride nanotube reinforced polyurethane composites. Prog Nat Sci Mater Int. 2013;23(2):170–173. doi: 10.1016/j.pnsc.2013.03.004.
- Lu X, Nautiyal P, Bustillos J, et al. Hydroxylated boron nitride nanotube-reinforced polyvinyl alcohol nanocomposite films with simultaneous improvement of mechanical and thermal properties. Polym Compos. 2020;41(12):5182–5194. doi: 10.1002/pc.25785.
- Goutianos S, Peijs T. On the low reinforcing efficiency of carbon nanotubes in high-performance polymer fibres. Nanocomposites. 2021;7(1):53–69. doi: 10.1080/20550324.2021.1917815.
- Zhang K, Du J, Ren M, et al. Computational design for the damping characteristics of poly(ether ether ketone). J Phys Chem B. 2021;125(33):9588–9600. doi: 10.1021/acs.jpcb.1c03649.
- Wang B, Mao Z, Li D, et al. Multiscale insights into the stretching behavior of kevlar fiber. Comput Mater Sci. 2020;185:109957. doi: 10.1016/j.commatsci.2020.109957.
- Mao Z, Li T, Zhang K, et al. Carbon nanotube reinforced poly-p-phenylene terephthalamide fibers for toughness improvement: a molecular dynamics study. Advcd Theory and Sims. 2020;3(10):2000135. doi: 10.1002/adts.202000135.
- Li Z, Li T, Zhang K, et al. Dynamics responses of graphene nanoplatelets-reinforced polydimethylsiloxane nanocomposites: a molecular dynamics study. Macromol Theory Simul. 2023:2300021. doi: 10.1002/mats.202300021.
- Haghighi S, Ansari R, Ajori S. Interfacial properties of 3D metallic carbon nanostructures (T6 and T14)-reinforced polymer nanocomposites: a molecular dynamics study. J Mol Graph Model. 2019;92:341–356. doi: 10.1016/j.jmgm.2019.08.010.
- Haghighi S, Ansari R, Ajori S. A molecular dynamics study on the interfacial properties of carbene-functionalized graphene/polymer nanocomposites. Int J Mech Mater Des. 2020;16(2):387–400. doi: 10.1007/s10999-019-09472-y.
- Maiti TK, Singh J, Dixit P, et al. Enhancing mechanical and interfacial properties of PEEK/epoxy/SWCNT composites employing aromatic hydroxyl and amine-functionalized SWCNTs. Chem Eng J Adv. 2022;10:100274. doi: 10.1016/j.ceja.2022.100274.
- Cui J, Zeng F, Yuan B. A comparative study on the interfacial characteristics and tensile behaviors of natural rubber composites reinforced by carbon and boron nitride nanotubes. Polym Compos. 2022;43(9):6624–6636. doi: 10.1002/pc.26977.
- Song Z, Li Y, Yang B. The interfacial load-transfer enhancement mechanism of amino-functionalised carbon nanotube reinforced epoxy matrix composites: a molecular dynamics study. Compos Sci Technol. 2021;209:108790. doi: 10.1016/j.compscitech.2021.108790.
- Nasrabadi AT, Foroutan M. Interactions between polymers and single-walled boron nitride nanotubes: a molecular dynamics simulation approach. J Phys Chem B. 2010;114(47):15429–15436. doi: 10.1021/jp106330c.
- Yang S. A thermomechanical comparative study on carbon and boron nitride nanotube-reinforced polymer composites. Mech Adv Mater Struct. 2022;29(24):3556–3569. doi: 10.1080/15376494.2021.1905916.
- Humphrey W, Dalke A, Schulten K. VMD: visual molecular dynamics. J Mol Graph. 1996;14(1):33–38. doi: 10.1016/0263-7855(96)00018-5.
- Hess B, Kutzner C, van der Spoel D, et al. GROMACS 4: algorithms for highly efficient, load-balanced, and scalable molecular simulation. J Chem Theory Comput. 2008;4(3):435–447. doi: 10.1021/ct700301q.
- Schmid N, Eichenberger AP, Choutko A, et al. Definition and testing of the GROMOS force-field versions 54A7 and 54B7. Eur Biophys J. 2011;40(7):843–856. doi: 10.1007/s00249-011-0700-9.
- Koziara KB, Stroet M, Malde AK, et al. Testing and validation of the automated topology builder (ATB) version 2.0: prediction of hydration free enthalpies. J Comput Aided Mol Des. 2014;28(3):221–233. doi: 10.1007/s10822-014-9713-7.
- Bamane SS, Jakubinek MB, Kanhaiya K, et al. Boron nitride nanotubes: force field parameterization, epoxy interactions, and comparison with carbon nanotubes for high-performance composite materials. ACS Appl Nano Mater. 2023;6(5):3513–3524. doi: 10.1021/acsanm.2c05285.
- Li Y, Wang S, Wang Q, et al. A comparison study on mechanical properties of polymer composites reinforced by carbon nanotubes and graphene sheet. Composites Part B. 2018;133:35–41. doi: 10.1016/j.compositesb.2017.09.024.
- Posch HA, Hoover WG, Vesely FJ. Canonical dynamics of the nose oscillator: stability, order, and chaos. Phys Rev A Gen Phys. 1986;33(6):4253–4265. doi: 10.1103/PhysRevA.33.4253.
- Jin K, Feng X, Xu Z. Mechanical properties of chitin–protein interfaces: a molecular dynamics study. BioNanoSci. 2013;3(3):312–320. doi: 10.1007/s12668-013-0097-2.
- Parrinello M, Rahman A. Polymorphic transitions in single crystals: a new molecular dynamics method. J Appl Phys. 1981;52(12):7182–7190. doi: 10.1063/1.328693.
- Zhang K, Yuan X, Li D, et al. Mechanical properties of solution-blended graphene nanoplatelets/polyether-ether-ketone nanocomposites. J Phys Chem B. 2021;125(37):10597–10609. doi: 10.1021/acs.jpcb.1c04609.
- Tang M, Li T, Pickering E, et al. Steered molecular dynamics characterization of the elastic modulus and deformation mechanisms of single natural tropocollagen molecules. J Mech Behav Biomed Mater. 2018;86:359–367. doi: 10.1016/j.jmbbm.2018.07.009.
- Wu X, An W, Zeng XC. Chemical functionalization of boron-nitride nanotubes with NH3 and amino functional groups. J Am Chem Soc. 2006;128(36):12001–12006. doi: 10.1021/ja063653+.
- Zhi CY, Bando Y, Tang CC, et al. Boron nitride nanotubes: functionalization and composites. J. Mater. Chem. 2008;18(33):3900–3908. doi: 10.1039/b804575e.
- Sharma K, Sen Kaushalyayan K, Shukla M. Pull-out simulations of interfacial properties of amine functionalized multi-walled carbon nanotube epoxy composites. Comput Mater Sci. 2015;99:232–241. doi: 10.1016/j.commatsci.2014.12.023.
- Vogler TJ, Kyriakides S. Inelastic behavior of an AS4/PEEK composite under combined transverse compression and shear. Part I: experiments. Int J Plast. 1999;15(8):783–806. doi: 10.1016/S0749-6419(99)00011-X.