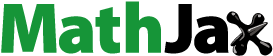
Abstract
Piezoelectricity in ferroelectrics arises from electrostriction biased by their spontaneous polarisation, which can be enhanced through a bias-induced polarisation. Doing so, the piezoelectric response can be tuned and significantly enhanced. In this study, the ferroelectric polymer P(VDF-TrFE) was used to electro-mechanically excite a silicon microcantilever. Using this device, we demonstrate that a bias-induced polarisation improves the piezoelectric response of P(VDF-TrFE). To distinguish between the linear piezoelectric and quadratic electrostrictive effect, lock-in measurements were performed in order to separate the characteristic frequency response of both electro-mechanical phenomena. This work shows the potential for MEMS devices having controllable actuating and sensing properties.
GRAPHICAL ABSTRACT
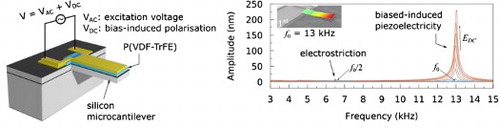
Impact statement
The non-linear nature of the strong electrostrictive effect observed in ferroelectric polymers was used to enhance and control its piezoelectric activity by an electric field. A large and tunable piezoelectric response was verified in polymer-based MEMS resonators, proving the ability to tailor their actuating and sensing properties.
1. Introduction
Besides capacitive and piezoresistive elements for sensing and actuating purposes, piezoelectricity is another well-established transducer mechanism in silicon micro electro-mechanical systems (MEMS), experiencing increasing interest in recent years. In piezoelectric materials, either mechanical strain is induced by an electric field (converse piezoelectric effect) or mechanical stress is converted to electric polarisation (direct piezoelectric effect). In that way, piezoelectric layers integrated in MEMS devices are used as transducers converting mechanical into electrical quantities and vice versa. Due to the reversibility of the piezoelectric effect, a single layer can serve for both actuating and sensing at the same time, enabling self-actuated and self-sensing microsystems. Several applications are reported in literature utilising this unique material property [Citation1–6]. For instance, scanning probes based on the piezoelectric effect are used for excitation and read-out of cantilevers in atomic force microscopy (AFM) [Citation5,Citation6].
Inherent piezoelectricity is only observed in materials having a non-centrosymmetric crystal structure, such as found in the piezoceramic aluminium nitride (AlN) [Citation7,Citation8]. A linear relation between the applied electric field and the resulting mechanical strain is characteristic for this material class. The proportionality constant is the piezoelectric coefficient, e.g. d31 or d33, which in general depends on the direction of the applied electric field and the resulting mechanical strain. It describes quantitively the conversion of the electric field to mechanical strain and vice versa. For instance, the piezoceramic AlN exhibits a d31 of around −2 pm/V, representing only a moderate piezoelectric coefficient [Citation7,Citation8]. In contrast, the ferroelectric lead zirconate titanate PbZr1-xTixO3 (PZT) typically shows more than an order of magnitude larger piezoelectric response with a d31 of around −100 pm/V [Citation9].
Ferroelectrics are a subclass of piezoelectric materials with the additional ability to switch between two polarisation states by applying a sufficient electric field, known as the coercive field. Piezoelectricity is observed in all ferroelectric materials. However, the linear electrostrain characteristic of piezoelectrics is only valid for small electric fields. For higher fields, especially beyond the coercive field, a highly non-linear behaviour of the electrostrain is observed. This non-linear strain-field characteristic is often referred to as the butterfly curve due to its distinctive shape. In the past, it was revealed that the piezoelectric response of ferroelectrics arises from a predominant non-linear electro-mechanical coupling phenomenon, the so-called electrostrictive effect [Citation10,Citation11].
Electrostriction describes the quadratic change of a polarisation-induced mechanical strain () independent of the crystal class and is present even in amorphous dielectric materials [Citation12–15]. In case of a linear relation between the electric field and the electric polarisation (
), it is often referred to as the electric-field-related electrostrictive effect (
). However, many dielectrics, such as ferro-, paraelectrics or relaxors, exhibit highly non-linear dielectric properties and they do not show a quadratic change of an electric-field-induced mechanical strain. For instance, the strain-field characteristic of ferroelectrics, the butterfly curve, is not a quadratic function of the electric field, but the electric polarisation. The electrostrictive strain originates from an electric-field-induced polarisation [Citation12–14]. If dielectrics possess spontaneous polarisation, meaning that a remnant polarisation is present even when no electric field is applied, a linear piezoelectric strain can be observed. Consequently, piezoelectricity observed in ferroelectrics arises from electrostriction biased by spontaneous polarisation [Citation15].
Since electrostriction is present in any dielectrics and due to its non-linear nature, it is possible to generate a piezoelectric response even in non-piezoelectric materials. The inherent spontaneous polarisation of ferroelectrics can be mimicked in any dielectrics via a bias-induced polarisation by applying a DC field. This so-called electric-field-induced piezoelectricity is controlled by the applied DC field, enabling a wide range of adjustable effective piezoelectric coefficients. The latter effect strongly depends on the electrostrictive response of the material. For instance, the piezoelectric AlN shows a strong piezoelectric, but only a poor electrostrictive response, hence, the impact of a bias-induced polarisation on its piezoelectric response is negligible. In relaxor materials, that typically possess a strong electrostrictive response, such as lead magnesium niobite (PMN), a large range of tunable piezoelectric coefficients of at least one order of magnitude was observed [Citation15–18]. As a consequence, a field-induced-bias polarisation offers the potential to significantly enhance or tune the piezoelectric response of ‘normal’ ferroelectric materials, as they typically show a large electrostrictive response, as well. On device level, the ability to tune the piezoelectric response of specific materials is of great interest, thus opening up novel MEMS application scenarios in the field of e.g. AFM.
In the past decades, tremendous effort was put into the development of materials possessing an enhanced intrinsic piezoelectric response, focusing on improved dielectric properties of certain ferroelectrics by studying morphotropic phase boundaries [Citation19] or electron-irradiation methods [Citation20]. Exploiting the non-linear nature of the electrostrictive effect, however, was overlooked, demonstrated by only few studies reported in literature [Citation17,Citation18]. Therefore, we utilise the non-linear electro-mechanical response of a ferroelectric by applying a bias voltage in order to significantly enhance its piezoelectric activity. This approach was verified within a MEMS resonator, showing the ability to tailor its actuating and sensing properties.
In this work, the ferroelectric copolymer of vinylidene fluoride and trifluoroethylene (P(VDF-TrFE)) was integrated on a silicon microcantilever, realising a MEMS resonator driven by the electro-mechanical response of the ferroelectric polymer. In a next step, we analysed the electrostrictive and piezoelectric actuation behaviour of the microcantilever. To distinguish between both effects, lock-in measurements were used in order to separate the characteristic frequency response of the linear piezoelectric from the quadratic electrostrictive effect, respectively. Giving this advanced measurement methodology, it is possible to separate the piezoelectric from the electrostrictive response of P(VDF-TrFE) in unprecedented accuracy. Additionally, a bias-induced polarisation by applying a DC field to the ferroelectric polymer was used to tune the piezoelectric response of the microcantilever by an order of magnitude.
Flexible and soft materials, such as the ferroelectric or piezoelectric copolymer P(VDF-TrFE), have found an increasing number of applications in MEMS devices [Citation21–26]. Due to the low stiffness of polymers compared to inorganic materials, low frequency applications for e.g. energy harvesters are accessible. P(VDF-TrFE) allows the realisation of ferroelectric polymer thin films by spin-on, a well-established, large-scale production technique in MEMS. However, the integration of ferroelectric polymer thin films into a standard silicon MEMS fabrication process is challenging, as typically strong chemicals or etchants are used that may attack this organic material. For this reason, there are only few reports on the fabrication of ferroelectric polymer MEMS devices in literature [Citation21–25]. In this work, we present a fabrication process for ferroelectric polymer microcantilevers by applying standard microfabrication techniques. Using this device, we demonstrate the full potential of P(VDF-TrFE) thin films for MEMS resonators. Besides the linear piezoelectric excitation, the non-linear electrostrictive response of P(VDF-TrFE) is exploited for actuating a ferroelectric polymer microcantilever. Standard piezoelectric materials, such as AlN, do not possess a significant electrostrictive effect. However, ferroelectric materials, such as the ferroelectric polymer P(VDF-TrFE), show a strong electrostrictive response. In that way, the impact of a bias-induced polarisation on the ferroelectric properties of P(VDF-TrFE) including its linear piezoelectric and non-linear electrostrictive characteristics are demonstrated for novel polymer MEMS applications.
2. Materials and methods
The ferroelectric polymer P(VDF-TrFE) is well–known for its piezoelectric properties, having a piezoelectric coefficient d31 of around 10.8 pm/V [Citation27]. It is predestined for soft and flexible MEMS applications due to its low elastic modulus of only 2 GPa at room temperature [Citation28]. The polymer films were fabricated via spin-coating at 2000 rpm for 45 s from polymer solutions under clean room conditions. In this work, a ratio between VDF and TrFE of 70:30 mol% was used. A polymer powder, purchased from Piezotech/Arkema Group, was dissolved at a weight ratio of 4% in the solvent 2-butanone under heating of 50°C. Residual solvent was carefully evaporated at 80°C in air for 10 min, since 80°C is slightly above the evaporation temperature (79.6°C) of 2-butanone. To guarantee satisfying ferroelectric properties, the polymer films were subsequently annealed for 2 h in vacuum at 140°C. Under these conditions, P(VDF-TrFE) preferentially crystallises into the polar β-phase, as it was reported in literature [Citation28,Citation29]. Since it is crucial for this work that the synthesised polymer thin films exhibit ferroelectric properties, the pure polymer thin films were investigated before their integration into a MEMS device. To that end, morphological studies were performed on thin films of P(VDF-TrFE) spin-coated on a silicon substrate. Electrical and electro-mechanical properties were measured by using metal-ferroelectric-metal (MFM) capacitors. The fabrication of these test devices is described elsewhere [Citation28]. In this work, the polymer thin films had a thickness of 500 nm. In general, P(VDF-TrFE) is a semi-crystalline polymer, meaning that it is an intermixture of crystalline and amorphous regions [Citation30]. The morphology of the polymer shows rice-like crystalline domains varying in size depending on the annealing temperature. Figure (a) shows the morphology of P(VDF-TrFE) measured by AFM for a non-annealed and a sample annealed at 140°C. Non-annealed samples, i.e. thin films obtained after the solvent evaporation without any further thermal treatment, contain only very small crystalline domains. However, annealing the polymer at 140°C leads to large crystalline domains with a rice-like microstructure. It should be highlighted that the spin-coated thin films are smooth and homogeneous without any indication for the presence of voids or porous regions. The film roughness of the non-annealed and annealed sample exhibits a root-mean-square roughness of less than 10 nm. For synthesising such smooth polymer thin films by spin-coating, it is crucial to ensure fast evaporation of the solvent 2-butanone. Therefore, the thin films should be immediately placed on a hot-plate for solvent evaporation after the spin-coating process. The implementation of impurities such as particles were avoided by filtering the polymer solution using a filter with a pore size of 0.45 µm. In order to exclude any voids in the film, e.g. caused by the inclusion of air bubbles, the polymer solution was de-gassed in a vacuum desiccator. Following this fabrication process, high-quality thin films of P(VDF-TrFE) are obtained.
Figure 1. Thin film characteristics of P(VDF-TrFE). (a) AFM images showing the height profile of the ferroelectric polymer P(VDF-TrFE) for a non-annealed and annealed sample at 140°C, respectively. (b) Specular XRD measurements of P(VDF-TrFE) confirming the presence of the polar β-phase conformation that renders its ferroelectric properties. The crystallinity raises significantly after the annealing at 140°C. (c) Bistable hysteresis loops of the polarisation as a function of the applied field, revealing the ferroelectric characteristic of the P(VDF-TrFE) thin films synthesised within this work. Additionally, the non-linear longitudinal electrostrain behaviour of the polymer is shown. All measurements have been performed in air at room temperature. The polymer film had a thickness of 500 nm.
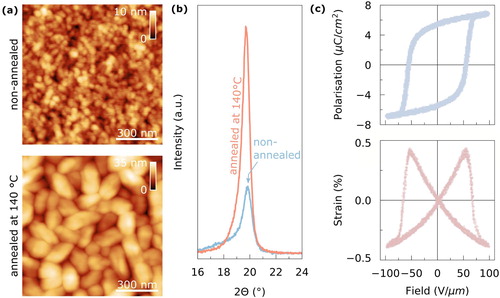
P(VDF-TrFE) may crystallise in different polymorphs [Citation28,Citation29]. Under the fabrication process described above, however, the polar β-phase is the thermodynamically most stable phase of P(VDF-TrFE) at room temperature. Inside of the rice-like crystalline domains, regions are found where the polymer chains arrange into a crystalline structure of the β-phase. The formation of the β-phase was confirmed by specular XRD measurements, as shown in Figure (b), in which the characteristic diffraction peak at a 2θ value of 19.7° is evident for P(VDF-TrFE) [Citation28,Citation29]. Both the annealed and non–annealed sample exhibit β-phase conformation, but the crystallinity of the annealed sample is significantly enhanced. An annealing temperature of 140°C is optimal for a high degree of crystallinity, since annealing at even higher temperatures close to the melting temperature of P(VDF-TrFE) of 158°C results in a collapse of the crystalline domains. However, the formation of β-phase within the polymer thin film is not evident enough to ensure macroscopic ferroelectric activity. The spontaneous polarisation of each rice-like crystalline domain may be randomly distributed and needs to be aligned in the same direction by applying a sufficient DC field of 100 V/µm at room temperature in order to activate ferroelectricity within the P(VDF-TrFE) thin film. The ferroelectric characteristic of P(VDF-TrFE) was proven by measuring the bistable hysteretic response of the polarisation as a function of the applied electric field. For that purpose, a Sawyer-Tower circuit with a reference capacitor of 1 µF was used. Applying a 10 Hz continuous triangular wave signal to the P(VDF-TrFE) thin film results in the typical switching behaviour of the macroscopic polarisation common in ferroelectrics, as shown in Figure (c). The remnant polarisation amounts to 5.6 µC/cm2 and the coercive field to 55 V/µm, which is in good agreement with values reported in literature [Citation28,Citation30]. Figure (c) shows the non-linear electrostrain characteristic, the butterfly curve, of P(VDF-TrFE) obtained by measuring the z-deflection of a polymer MFM capacitor during electrical stimulation in z-direction. Details about the measurement methodology are presented in ref. [Citation28]. It is actually the non-linearity of the electro-mechanical response of P(VDF-TrFE) that is utilised to generate an enhanced effective piezoelectric response by shifting the operating point of the butterfly curve away from the centre by applying a bias voltage, as will be discussed later. Both, the electrical as well as electro-mechanical response of the P(VDF-TrFE) thin films fabricated within this work prove their ferroelectric properties.
To exploit the functional properties, such as piezoelectricity and electrostriction, of P(VDF-TrFE) for MEMS applications, a thin film (∼500 nm) of P(VDF-TrFE) was integrated on a silicon microcantilever. The resulting ferroelectric polymer microcantilever is shown in Figure (a). The microcantilever in this work had a length of 400 µm, a width of 200 µm and a total thickness of 3 µm. In general, the resonance frequency of a cantilever depends on its dimensions. In this work, the dimensions of the microcantilever were chosen such that the resonance frequency of the first flexural mode is found at low frequencies in the range of 10 kHz, allowing the excitation and investigation of even higher flexural modes of the microcantilever. Furthermore, it was intended to realise a micromachined ferroelectric polymer cantilever in order to demonstrate the potential of P(VDF-TrFE) for MEMS resonators given only few studies in literature [Citation21–25]. However, since the integration of a ferroelectric polymer into the batch process of a micromachined silicon cantilever is not straightforward, we present details of the fabrication process in the supplementary material. The main challenge is to carry out a photolithography without the ferroelectric polymer being attacked by solvents contained in standard photoresists. To that end, we used hard masks to pattern the ferroelectric polymer thin films. A 4′′ silicon–on–insulator (SOI) wafer, having a device layer thickness of 2 µm, was used as support for the capacitor-type ferroelectric polymer stack. The multimorph structure of the cantilever is schematically illustrated in Figure (b). A SEM image of the multimorph structure is shown in Figure (c), confirming a film thickness of 500 nm of the P(VDF-TrFE) thin film. It should be noted that the supporting silicon layer ensures a significant distance between the neutral axis of the cantilever and the centre of the ferroelectric polymer, enabling a strong torque for an electro-mechanical actuation of the microcantilever. Electrically stimulated expansion of the functional layer translates into a finite bending moment, which in turn causes deflection of the microcantilever. In general, the deflection of the microcantilever depends linearly on the distance between the centre of the functional layer and the neutral axis of the cantilever [Citation31]. Consequently, if the centre of the ferroelectric polymer layer coincides with the neutral axis of the microcantilever, there would be no bending moment and, thus no deflection. It should be noted that in ref. [Citation21], an asymmetric electrode design was used to shift the neutral axis in order to enhance the deflection of a polymer microcantilever. In contrast, using a SOI wafer ensures a significant shift of the neutral axis through the silicon support layer of predefined thickness. In order to demonstrate that the P(VDF-TrFE) thin film integrated on the silicon microcantilever exhibits ferroelectric properties, the polarisation as a function of the applied field was measured using the Sawyer-Tower circuit, as presented above. As expected for ferroelectrics, a bistable hysteretic response was observed, confirming the ferroelectric state of the P(VDF-TrFE) thin film (see Figure (d)). The hysteresis loops and the remnant polarisation of 5.2 µC/cm2 are in good agreement with the results shown in Figure (c), proving ferroelectricity.
Figure 2. Ferroelectric polymer microcantilever. (a) SEM image showing a ferroelectric polymer microcantilever investigated in this work. (b) Schematic illustration of the multimorph structure of the microcantilever. The cantilever has a length of 400 µm, a width of 200 µm and a total thickness of around 3 µm. Details about the fabrication steps are presented in the supplementary material. (c) SEM image showing the multimorph structure of the microcantilever, proving that the polymer film has a thickness of 500 nm. (d) Bistable polarisation-field hysteresis loops of the P(VDF-TrFE) thin film incorporated on the silicon microcantilever confirming the ferroelectric state of the polymer. (e) Frequency spectrum of the ferroelectric polymer microcantilever when applying an excitation field of 1 V/µm. A large variety of flexural modes is excited in the cantilever as shown in the inset.
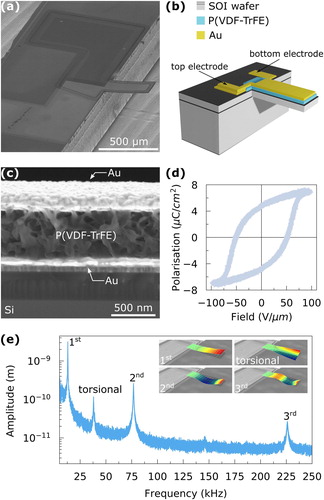
3. Results and discussion
The electro-mechanical response of the microcantilever was measured over a wide range of frequencies up to 250 kHz (see Figure (e)). For that purpose, we used a laser Doppler vibrometer (Micro System Analyser (MSA-500), Polytec). All measurements were performed in air. A small AC field of 1 V/µm was used to excite the cantilever. A variety of flexural modes could be excited, as illustrated in Figure (e). For instance, the first flexural mode of the microcantilever was observed at around 13 kHz (f0 = 13 kHz). The -factor (
= 104) of the first flexural mode of the ferroelectric polymer cantilever measured in air was found to be significant lower compared to standard MEMS cantilevers using stiff piezoceramics like AlN (see Table ) [Citation32–34]. This is attributed to enhanced internal mechanical losses within the soft polymer. In literature, it has been demonstrated that the
-factor decreases with increasing thickness of the polymer film [Citation35]. The thicker the polymer film, the more internal losses cause a decrease of the
-factor. On the other hand, when the polymer film becomes thinner, functional properties, such as the piezoelectric response, will get reduced. In that sense, a polymer thin film with a thickness of 500 nm causes less internal losses, but provides the expected functional properties. The frequency spectrum shown in Figure (e) represents the response of the microcantilever measured at the excitation frequency using a periodic chirp signal.
Table 1. Comparison of key parameters, such as resonance frequency or
-factor, of piezoelectric actuated microcantilevers using P(VDF-TrFE) or AlN. The Q-factors of P(VDF-TrFE) cantilevers are significantly lower compared to AlN cantilevers. The resonance frequency
and
-factor were all measured in air.
With this straightforward approach, however, the electrostrictive response of the ferroelectric polymer cannot be observed, since electrostriction is a quadratic electro-mechanical coupling effect. Exciting the ferroelectric polymer at frequency f generates an electrostrictive response at the doubled frequency 2f [Citation36–38]. In contrast, the linear piezoelectric effect yields a response at the excitation frequency. To measure the response of the electrostrictive effect, we performed lock-in measurements (using the HF2LI Lock-in Amplifier of Zurich Instruments) to get the demodulated signal of the second harmonic (2f) of the swept excitation frequency f. Additionally, we measured the first harmonic (f) in order to get the piezoelectric response. The maximum deflection of the ferroelectric polymer microcantilever was measured at its free end. The electrostrictive and piezoelectric response of the microcantilever as a function of the applied excitation field EAC are shown in Figure .
Figure 3. Electrostrictive and piezoelectric response of the first flexural mode. (a) Amplitude of the first and second harmonic signal as a function of increasing excitation field amplitude EAC measured around the mechanical resonance frequency f0 = 13 kHz and f0/2. (b) Amplitude of the first and second harmonic signal measured over the frequency range from 3 kHz to 15 kHz, which includes f0 and f0/2. The electrostrictive and piezoelectric response are clearly separated. (c), (d) Maximum amplitude of the first and second harmonic resonance peak as a function of the excitation field amplitude EAC. The piezoelectric effect is linear, while the electrostrictive effect shows a quadratic behaviour.
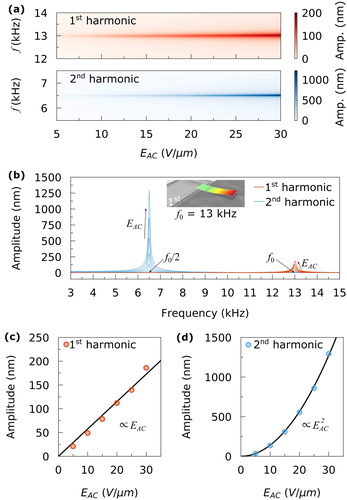
As expected, the piezoelectric response (1st harmonic signal) is measured at the eigenfrequency f0 = 13 kHz of the first flexural mode and the electrostrictive response (2nd harmonic signal) shows a maximum at half the eigenfrequency f0/2 = 6.5 kHz (see Figure (a,b)). Both signals increase with increasing excitation field EAC. The maximum applied excitation field EAC < 30 V/µm was chosen to be significantly below the coercive field (∼55 V/µm) of P(VDF-TrFE) in order to avoid switching within the ferroelectric polymer [Citation30]. At the maximum exciation field of 30 V/µm, the electrostrictive effect causes a deflection of the microcantilever of 1.25 µm. In contrast, the piezoelectric effect yields a deflection of 200 nm, which is six times lower than the electrostrictive excitation. Consequently, the latter approach to drive the microcantilever is much stronger than exploiting the piezoelectric effect.
The maximum amplitude of the microcantilever as a function of the excitation field EAC for the piezoelectric and electrostrictive exciation is shown in Figure (c,d). The maximum amplitude caused by the piezoelectric effect increases linearly with increasing EAC, which is characteristic for piezoelectricity. In contrast, the maximum amplitude of the 2nd harmonic signal shows a quadratic change as a function of EAC, confirming the quadratic nature of the electrostrictive effect. Higher harmonics of the swept excitation frequency were significantly below the first and second harmonic signal level and thus, can be neglected.
The measurements presented in Figure shows the piezoelectric and electrostrictive response of the ferroelectric polymer microcantilever as a function of an applied AC field without applying any additional DC field to the ferroelectric polymer. However, it is known that a bias-induced polarisation by applying an additional DC field can be used to tune the piezoelectric response of the ferroelectric polymer. Analysing the non-linear electro-mechanical response, given by the butterfly curve of P(VDF-TrFE) shown in Figure (c), it is seen that by applying a DC voltage to the polymer the operation point can be shifted to a region where the slope of the butterfly curve is different and, as a consequence, the piezoelectric response. Therefore, we performed similar measurements as presented above, but with an additional DC field. A small AC field of 2.5 V/µm was used to excite the electro-mechanical system. The resulting electrostrictive and piezoelectric response as a function of increasing DC field EDC, but constant AC field EAC = 2.5 V/µm are presented in Figure .
Figure 4. Electrostrictive and piezoelectric response of the first flexural mode as a function of bias field applied to the ferroelectric polymer. An AC field of 2.5 V/µm was used to excite the microcantilever. (a) Amplitude of the first and second harmonic signal as a function of increasing bias field EDC measured around the mechanical resonance frequency f0 = 13 kHz and f0/2. (b) Amplitude of the first and second harmonic signal measured over the frequency range from 3 kHz to 15 kHz, which includes f0 and f0/2, showing the significant contrast between the electrostrictive and piezoelectric response as a function of the applied bias field EDC. (c),(d) Maximum amplitude of the first and second harmonic resonance peak as a function of the bias field EDC. The piezoelectric response increases linearly with increasing EDC. In contrast, an increased EDC shows no impact on the electrostrictive response.

Of course, the ferroelectric polymer microcantilever still shows a piezoelectric response at f0 and an electrostrictive response at f0/2. However, the piezoelectric response increases with increasing DC field EDC, while the electrostrictive response remains constant (see Figure (a)). The impact of a bias-induced polarisation generated by EDC can be clearly seen in Figure (b). For an applied DC field of just 10 V/µm, the piezoelectric response is already five times larger than the electrostrictive response. At the maximum applied DC field of 30 V/µm, the amplitude of the microcantilever caused by the piezoelectric effect is even one order of magnitude higher than the electrostrictive response. In Figure (c), we show the maximum amplitude of the microcantilever generated by the piezoelectric effect as a function of the applied DC field EDC. As expected, a linear relation is found [Citation18]. In contrast, the electrostrictive response remains constant as a function of EDC, since EAC is not changing.
Without any applied DC field, the ferroelectric polymer exhibits a d31 of 10.8 pm/V. From the linear relation in Figure (c), we can calculate the electric-field-induced (effective) piezoelectric coefficient. For the maximum applied DC field of 30 V/µm, an effective d31 of 168.4 pm/V is present, which is more than one order of magnitude larger than the inherent piezoelectric coefficient of P(VDF-TrFE). Given this result, the electric-field-induced piezoelectric response is even stronger than the inherent piezoelectric activity of PZT with a d31 of around −100 pm/V [Citation9].
The results presented in Figure shows that a bias voltage applied to the ferroelectric polymer significantly enhances the piezoelectric response of P(VDF-TrFE), since the amplitude of the microcantilever increases when enhancing the bias voltage, while the excitation signal (AC signal) is kept constant. However, applying a bias voltage generally increases the piezoelectric response of P(VDF-TrFE) but reduces the operation range in which the polymer can be stimulated with an AC voltage, as the operation range of the ferroelectric polymer is limited by the coercive field.
4. Conclusion
We have demonstrated that a bias-induced polarisation can be used to significantly enhance the piezoelectric response of the ferroelectric polymer P(VDF-TrFE). The non-linearity of the electrostrictive effect provides a straightforward approach to generate an improved electric-field-induced piezoelectric activity in ferroelectrics. Micromachined silicon cantilevers with an integrated ferroelectric polymer film for electro-mechanical actuation were realised, allowing to analyse their electrostrictive and piezoelectric response characteristics. Without any bias-induced polarisation, the electrostrictive response is more pronounced compared to the piezoelectric response. The linear/quadratic dependency of the strain as a function of the applied AC field was observed, corroborating the strain-field characteristic of the piezoelectric/electrostrictive effect. We would like to emphasise again that an electrostrictive actuation of a resonant microsystem with a resonance frequency of f0 has to be excited at half the resonance frequency at f0/2, as demonstrated with our ferroelectric polymer microcantilever. All in all, the results gained from the MEMS resonators demonstrate the potential to develop novel MEMS applications requesting controllable actuating and sensing properties. In future works, the converse electrostrictive effect of P(VDF-TrFE) need to be studied in more detail. It could be also interesting to investigate if there is any electro-mechanical coupling between the electrostrictive and piezoelectric effect. Moreover, the electromechanical coupling coefficient of the bias-induced electro-mechanical response of P(VDF-TrFE) requires further investigations.
Supplemental Material
Download PDF (371.3 KB)Acknowledgements
This work has received funding from the European Union`s Horizon 2020 research and Innovation programme under the Marie Skłodowska-Curie grant agreement No. 721874 (SPM2.0).
Disclosure statement
No potential conflict of interest was reported by the author(s).
Additional information
Funding
References
- Muralt P, Polcawich RG, Trolier-McKinstry S. Piezoelectric thin films for sensors, actuators, and energy harvesting. MRS Bull. 2009;34:658–664.
- Gebhardt S, Steffner L, Schlenkrich F, et al. PZT thick films for sensor and actuator applications. J Eur Ceram Soc. 2007;27:4177–4180.
- Khanna PK, Hornbostel B, Grimme R, et al. Miniature pressure sensor and micromachined actuator structure based on low–temperature–cofired ceramics and piezoelectric material. Mater Chem Phys. 2004;87:173–178.
- Kucera M, Wistrela E, Pfusterschmied G, et al. Design–dependent performance of self–actuated and self–sensing piezoelectric–AlN cantilevers in liquid media oscillating in the fundamental in–plane bending mode. Sensor Actuat B-Chem. 2014;200:235–244.
- Lee C, Itoh T, Suga T. Self-excited piezoelectric PZT microcantilevers for dynamic SFM—with inherent sensing and actuating capabilities. Sensor Actuat A-Phys. 1999;72:179–188.
- Giessibl FJ. The qPlus sensor, a powerful core for the atomic force microscope. Rev Sci Instrum. 2019;90:011101.
- Schneider M, Bittner A, Schmid U. Improved piezoelectric constants of sputtered aluminium nitride thin films by pre-conditioning of the silicon surface. J Phys D: Appl Phys. 2015;48:405301.
- Tonisch K, Cimalla V, Foerster C, et al. Piezoelectric properties of polycrystalline AlN thin films for MEMS application. Sensors Actuat A–Phys. 2006;132:658–663.
- Dick AJ. Characterizing effective d31 values for PZT from the nonlinear oscillations of clamped-clamped micro–resonators. Stroj Vestn–J Mech Eng. 2013;59(1):50–55.
- Jona F, Shirane G. Ferroelectric crystals. New York: Dover; 1993.
- Furukawa T, Seo N. Electrostriction as the origin of piezoelectricity in ferroelectric polymers. Jpn J Appl Phys. 1990;29(4):675–680.
- Sundar V, Newnham RE. Electrostriction and polarization. Ferroelectrics. 1992;135:431–446.
- Newnham RE, Sundar V, Yimnirun R, et al. Electrostriction: nonlinear electromechanical coupling in solid dielectrics. J Phys Chem B. 1997;101:10141–10150.
- Newnham RE. Properties of materials: anisotropy, symmetry, structure. Oxford University Press, Oxford; 2005.
- Li F, Jin L, Xu Z, et al. Electrostrictive effect in ferroelectrics: An alternative approach to improve piezoelectricity. Appl Phys Rev. 2014;1:011103.
- Kuwata J, Uchino K, Nomura S. Electrostrictive coefficients of Pb(Mg1/3Nb1/3)O3 ceramics. Jpn J Appl Phys. 1980;19(11):2099–2103.
- Ma W, Cross LE. Tunable electric-field-induced piezoelectricity in high strain relaxor ferroelectric P(VDF-TrFE) copolymer. J Phys: Condens Matter. 2005;17:1011–1018.
- Venet M, Zabotto F, Eiras JA, et al. High and tunable piezoelectric coefficients in 0.675Pb(Mg1/3 Nb1/3)O3-0.325PbTiO3 ceramics. Mater Res Bull 2012;47:2219–2221.
- Liu Y, Aziguli H, Zhang B, et al. Ferroelectric polymers exhibiting behaviour reminiscent of a morphotropic phase boundary. Nature. 2018;562:96–100.
- Zhang QM, Bharti V, Zhao X. Giant electrostriction and relaxor ferroelectric behaviour in electron-irradiated poly(vinylidene fluoride-trifluoroethylene) copolymer. Science. 1998;280:2101–2104.
- Oh SR, Yao K, Zhang l, et al. Asymmetric electrode design for significant performance enhancement of piezoelectric P(VDF-TrFE) polymer microcantilevers. Smart Mater Struct. 2015;25:045035.
- Toprak A, Tigli O. MEMS scale PVDF-TrFE-based piezoelectric energy harvesters. J Microelectromech Syst. 2015;24:1989–1997.
- Ducrot PH, Dufour I, Ayela C. Optimization of PVDF-TrFE processing conditions for the fabrication of organic MEMS resonators. Sci Rep. 2016;6:19426.
- Rashmi KR, Rao AS, Jayarama A, et al. Low frequency piezoelectric P(VDF-TrFE) micro-cantilevers with novel MEMS process for vibration sensor and energy harvester applications. Smart Mater Struct. 2019;28:065022.
- Rashmi KR, Rao AS, Jayarama A, et al. Piezoelectric P(VDF-TrFE) micro cantilevers and beams for low frequency vibrations sensors and energy harvesters. Sens Actuator A. 2019;295:574–585.
- Kim S, Dong Y, Hossain MM, et al. Piezoresistive Graphene/P(VDF-TrFE) heterostructure based highly sensitive and flexible pressure sensor. ACS Appl Mater Interfaces. 2019;11(160006):16017.
- Safari A, Akdogan EK. Piezoelectric and acoustic materials for transducer applications. Springer, New York; 2008.
- Hafner J, Teuschel M, Schneider M, et al. Origin of the strong temperatur effect on the piezoelectric response of the ferroelectric (co-)polymer P(VDF70-TrFE30). Polymer. 2019;170:1–6.
- Tashiro K. Crystal structure and phase transition of PVDF and related copolymers. In: Nalwa HS, editor. Ferroelectric polymers: chemistry, physics, and applications. New York: Marcel Dekker; 1995. p. 63–182. Chapter 2,
- Katsouras I, Asadi K, Li M, et al. The negative piezoelectric effect of the ferroelectric polymer poly(vinylidene fluoride). Nat Mater. 2016;15:78–84.
- Schmid S, Villanueva LG, Roukes ML. Fundamentals of nanomechanical resonators. Springer, New York; 2016.
- Kucera M, Wistrela E, Pfusterschmid G, et al. Characterization of a roof tile-shaped out-of-plane vibrational mode in aluminium-nitride-actuated self-sensing micro-resonators for liquid monitoring purposes. Appl Phys Lett. 2014;104:233501.
- Mayrhofer PM, Wistrela E, Kucera M, et al. Fabrication and characterisation of ScAlN-based piezoelectric MEMS cantilevers. Proceedings of the 18th International Conference on Solid-State Sensors, Actuators and Microsystems (TRANSDUCERS). 2015 June, p. 2144–2147.
- Krupa K, Gorecki C, Jóźwicki R, et al. Interferometric study of reliability of microcantilevers driven by AlN sandwiched between two metal layers. Sensor Actuat A-Phys. 2011;171(2):306–316.
- Dufour I, Lochon F, Heinrich SM, et al. Effect of coating viscoelasticity on quality factor and limit of detection of microcantilever chemical sensors. IEEE Sens. J. 2007;7:230–236.
- Cross LE, Jang SJ, Newnham RE, et al. Large electrostrictive effects in relaxor ferroelectrics. Ferroelectrics. 1980;23(1):187–191.
- Xu T-B, Cheng Z-Y, Zhang QM. High–performance micromachined unimorph actuators based on electrostrictive poly(vinylidene fluoride-trifluoroethylene) copolymer. Appl Phys Lett. 2002;80:1082.
- Khudiyev T, Clayton J, Levy E, et al. Electrostrictive microelectromechanical fibres and textiles. Nat Commun 2017;8:1435.