Abstract
This article overviews several areas of research into architectured materials which, in the opinion of the authors, are most topical and promising. The classes of materials considered are based on meso scale designs inspired by animate and inanimate Nature, but also on those born in the minds of scientists and engineers, without any inspiration from Nature. We present the principles governing the design of the emerging materials architectures, discuss their explored and anticipated properties, and provide an outlook on their future developments and applications.
GRAPHICAL ABSTRACT
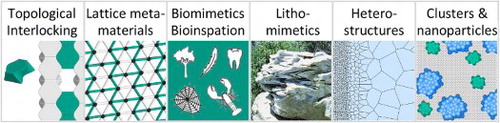
IMPACT STATEMENT
The article addresses several hot topics with a great promise for innovative materials design.
1. Introduction
Development of new materials by designing their inner architecture, rather than manipulating their atomic or phase composition, is an emerging trend in materials engineering [Citation1]. The area of architectured materials is burgeoning, and promising novel approaches have been popping up recently [Citation2]. While it is probably too early for an extensive review of this nascent discipline to be written, we feel that time is ripe for taking a snapshot of the most interesting and promising trends that are shaping up currently. Needless to say, we realize that the choice of what is most trendy and promising is subjective. Still, we believe that one day the directions of research we are focusing on here may become the mainstream ones. What unites the admittedly disparate approaches to materials design presented here is the targeted creation of their structures at a scale intermediate between the micro and macro scales. It is important to stress that we do not connect the taxonomy of the scales with any specific length dimensions. Rather, we understand it in the spirit of synergetics, a structural element of a higher scale being formed through interaction of lower-level objects endowing it with qualitatively new properties [Citation3]. The micro scale elements are the basic components of the material. Depending on the intended outcomes, they may be identified with atoms, molecules, individual phase particles, etc. A structural unit at macro scale is a representative volume element (RVE), which corresponds to a smallest volume of the material that possesses all its properties [Citation4]. An RVE comprises a large number of mesoscopic objects, each of them being formed, in turn, by micro elements that interact with one another [Citation5,Citation6].
The meso scale objects can be created artificially. This is the case, e.g. with topological interlocking materials or man-made elements of the lattice materials, which will be considered below. An alternative approach is by using a naturally emerging meso scale as a result of self-organization of the micro scale elements through their collective interactions [Citation5].
In the philosophy of morphogenesis, the differences between the various forms generated can be both qualitative and quantitative [Citation7]. In the latter case one speaks of a catastrophic, or cataclysmic, transition between the various forms. Since the properties of a material are largely governed by its structure, there are reasons to believe that qualitatively different mesoscopic structures would lead to distinctly different sets of properties. Numerous examples confirming this assertion can be found in Ref. [Citation5] where a bounty of meso structures and the attendant properties of materials are presented. We claim that it is the meso scale in the sense introduced here that offers a fruitful realm for investigation and development of materials with novel properties by way of formation of favorable architectures. This defines an exciting direction in contemporary materials science and engineering—the architectured materials design [Citation1,Citation2].
Structure as a key factor in design of materials is well-known in materials engineering. Here we emphasize its qualitatively different role that becomes the governing one. As distinct from composites, which also entail specially created morphological make-up of a material (such as fibers, layers, inclusions, meshes, etc.), architectured materials are characterized by a greater variety of meso structures. This rich pallet of meso structures offers great opportunities for impacting on a material’s properties in a cardinal way. The elegance and esthetic appeal play a role not to be neglected in materials design, and the connotation with ‘architecture’ in this context is not unintentional.
This article comprises eight sections, each of them being dedicated to a specific class of materials: Topological interlocking materials, Architectured lattice materials, Biomimetic and bioinspired materials, Lithoinspired materials, Heterostructured materials, and Cluster and nanoparticle assembly materials. Sections 2 and 3 deal with material designs born in the minds of materials scientists and engineers without any hints from the structures occurring in Nature or produced by human activity. Sections 4 and 5 deal with materials inspired by the animate or inanimate Nature (biomimetics and lithomimetics, respectively). Sections 6 and 7 discuss materials whose design is suggested by laboratory experiments in which interesting and potentially beneficial structures emerge by self-organization. The heterostructured materials as well as cluster and nanoparticle assembly based materials portrayed there are in that category. In each section, the main ideas and principles of design of the respective material architectures are presented, along with an overview of the key results and an outlook on the future developments. Possible manufacturing technologies for these groups of materials and the areas of their potential applications are also discussed.
2. Topological interlocking materials
Most of engineering materials, including metals, polymers, ceramics, and composites of various kinds, are monolithic ones. For centuries, or even millennia, a traditional approach to improving the properties of such materials has been based on varying their chemical or phase composition and perfecting the manufacturing and processing technologies used to produce them [Citation8,Citation9]. Obviously, there are limits to what can be achieved in this way, and that is where the concept of ‘architectured materials’ [Citation1,Citation2,Citation10,Citation11] comes in. The type of material architecture considered in this section is guided by the general idea that segmenting a material into smaller blocks should improve its fracture resistance, while also offering some further crucial benefits, which will be elucidated below. Indeed, the Weibull statistics tells us that the survival probability of a piece of material depends not only on the magnitude of the applied stress, but also on the volume of that piece, and this dependence is exponential [Citation12]. An attractive possibility of obtaining a segmented material is to use the so-called topological interlocking of the segments—a design principle that was proposed 20 years ago [Citation13,Citation14] but is only now gaining popularity within the materials engineering community. The term topological interlocking (TI) refers to segmented structures comprised by elements whose geometrical shape and mutual arrangement provide constraints on each element, which make removal of the element kinematically impossible. (One has to make a reservation, though, that the elements located at the periphery of the assembly need to be constrained additionally. This can be furnished by an external grillage, tensioning cables passing through the elements, or bars anchoring them) [Citation15].
Initially, two distinctly different families of building block geometries enabling assembly of TI structures were identified. The first one operates with Platonic bodies (tetrahedrons, cubes, octahedrons, dodecahedrons, and icosahedrons) or their truncated variants, as it was proven [Citation16] that all of them permit topological interlocking. A formal procedure of generating such structures mathematically was devised in [Citation17]. The underlying algorithm starts with a tessellation of the middle plane with squares or regular hexagons and transforms them in interlocked 3D elements as the plane moves upwards or downwards. Several assemblies obtained in this way are presented in Figure . This technique of reconstructing polyhedra-based TI structure from middle-plane tessellations was adopted by other researchers, e.g. [Citation18–22], but alternative algorithms were also considered [Citation20]. Interlockable block geometries based on non-planar geometries of the contact surfaces are also possible, cf. Figure . Figure (b) shows an assembly of blocks with topologically interlocked osteomorphic blocks with matching concavo-convex contact surfaces, (a) [Citation14]. Other examples seen in Figure refer to recent work of the research group of Akleman and Krishnamurthy at Texas A&M University who provided elegant techniques of generating interlockable block structures, such as Delaunay lofts, Figure (c), and assemblies inspired by fabric weaves, Figure (d) [Citation23–25].
Figure 1. Monolayers of topologically interlocked Platonic bodies: (a) tetrahedra, (b) cubes, (c) octahedra, (d) dodecahedra, (e) icosahedra (adapted from [Citation15]).
![Figure 1. Monolayers of topologically interlocked Platonic bodies: (a) tetrahedra, (b) cubes, (c) octahedra, (d) dodecahedra, (e) icosahedra (adapted from [Citation15]).](/cms/asset/250ccf94-a7fe-4c8a-ac38-e25dc2e96262/tmrl_a_1961908_f0001_oc.jpg)
Figure 2. Assemblies of interlocked blocks with non-planar contact surfaces: (a) a prototype osteomorphic block generating a topologically interlocked assembly shown in (b); (c) geometrically interlocked space-filling blocks (Delaunay lofts); (d) geometrically interlocked blocks inspired by woven fabric designs.
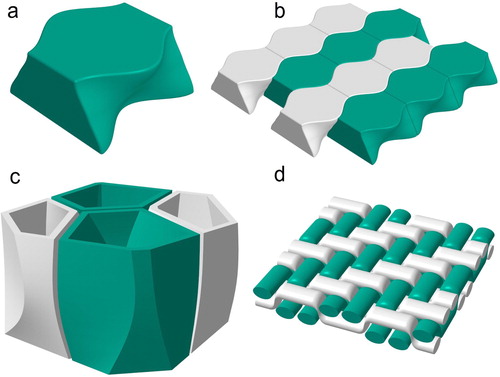
What started off as a nice mathematical exercise, is now becoming a recognized materials design principle. The success of the concept based on topological interlocking is predicated on the remarkable benefits it offers to materials design. Indeed, TI provides facile pathways to assembly (as well as disassembly) of a structure. A further advantage is that any materials, however ‘incompatible’ they may be, can be integrated within an assembly if the blocks made from them have the right shape. This opens a promising avenue for design and manufacturing of hybrid materials, in which a set of desired properties is achieved by combining materials with different functionalities. The mentioned properties also ensure the ease of separation of the constituent materials, which may solve many recycling problems. A defining feature of TI structures is that no adhesives or binders are required to ensure their integrity. Stress concentration-prone connectors, such as LEGO-type pin-and-hole ones, also become obsolete.
There are also significant benefits of structures with TI architecture in terms of their mechanical performance, as illustrated in Figure . Experiments conducted on prototype TI assemblies, commonly under concentrated loading, showed an impressive bendability of otherwise stiff ceramics [Citation26]. The plots in Figure (a) demonstrate clearly how a stiff and brittle material becomes pliable when segmented into interlocked osteomorphic blocks. While a drop of the load-bearing capability of the segmented plate is obvious, the overall area below the curves, which is related to its toughness, is increased significantly. Similarly attractive results were obtained for a range of other TI structures [Citation27–30]. For example, a 50-fold increase in toughness over a monolithic panel was demonstrated for a flat panel comprised by 3D-printed octahedron-shaped blocks [Citation28]. A superior performance of assemblies of tetrahedra-based TI assemblies over their monolithic counterparts under static [Citation27] and dynamic [Citation29] loading was found by the research group of Thomas Siegmund at Purdue University. Through experiments and finite element modeling, the authors demonstrated simultaneous improvement of strength and toughness—commonly the conflicting characteristics—owing to the TI nature of the assemblies tested.
Figure 3. Gainful variation of the mechanical performance of ceramic materials achieved by segmenting them into interlocked osteomorphic blocks: (a) Load vs. deflection diagram for monolithic plates and a TI assembly, after[Citation26]; (b) The effect of TI architecture and porosity (monomodal or bimodal) on the sound absorption coefficient of a ceramic produced by freeze gelation, after [Citation33]; (c) The effect of TI with and without interleaving of the osteomorphic blocks with a soft polymer on the load–displacement response of a flat panel, after [Citation2]. In all cases a concentrated normal load was applied to the middle of the plate.
![Figure 3. Gainful variation of the mechanical performance of ceramic materials achieved by segmenting them into interlocked osteomorphic blocks: (a) Load vs. deflection diagram for monolithic plates and a TI assembly, after[Citation26]; (b) The effect of TI architecture and porosity (monomodal or bimodal) on the sound absorption coefficient of a ceramic produced by freeze gelation, after [Citation33]; (c) The effect of TI with and without interleaving of the osteomorphic blocks with a soft polymer on the load–displacement response of a flat panel, after [Citation2]. In all cases a concentrated normal load was applied to the middle of the plate.](/cms/asset/955ac0ee-df6d-468e-b9fc-7be650526ea2/tmrl_a_1961908_f0003_oc.jpg)
Theoretical predictions showed that TI structures are highly tolerant to local failures. Thus, it was established by percolation analysis [Citation31] that an assembly of osteomorphic blocks can sustain up to nearly 25% of block failures before it would collapse. An acceptable sacrifice of the load-bearing capacity due to segmentation into such a block structure would be by far compensated for by a remarkable gain in fracture resistance [Citation20]. This aspect is especially important for combating brittleness of materials. An increase in the survival probability of an assembly of osteomorphic blocks over that of its monolithic equivalent was quantified in [Citation32] based on the Weibull statistics mentioned above. The gain in the survival probability was shown to increase with a decrease of the Weibull modulus (which is a measure of variability of a material’s fracture toughness). While, in principle, the concept of topological interlocking can be applied across most categories of materials, including the ones discussed in the present article, the greatest benefits would be achieved with most brittle of them. In particular, the use of TI would be a good way to improving the ductility of nanoglasses considered in Section 7 and of most ultrafine-grained materials produced by severe plastic deformation (Sections 5 and 6).
The beneficial features of TI materials are not limited to their mechanical performance. They also exhibit exceptionally good sound absorption properties. Figure (b) displays the frequency dependence of the sound absorption coefficient in the audible frequency range for porous ceramics [Citation33]. The effect of segmentation of a monolithic plate (the lowest curve, in grey) into osteomorphic blocks (black curve), with a peak value of about 0.67, is quite remarkable. Further enhancement of sound absorption by introducing bimodal porosity, in addition to TI, drove the peak even higher, to 0.97, while also broadening the peak.
The materials design paradigm based on topological interlocking can, of course, be combined with other approaches. One particular pathway to that involves the mimesis of nacre structure: by introducing soft layers interleaving the topologically interlocked blocks, additional enhancement of toughness and strength can be achieved [Citation34]. In the context of TI materials, the benefits of this concept were demonstrated for an assembly of osteomorphic ceramic blocks with and without rubber interleaving [Citation2], cf. Figure (c).
The list of attractive features of TI design presented above is not exhaustive. Further examples of potential applications of TI materials and structures, including responsive structures reacting to external stimuli, sandwich structures, protective gear, extra-terrestrial construction, etc., can be found in Chapter 2 of the monograph on architectured materials [Citation2].
It can now be considered as established that topological interlocking is a promising and viable tool for architectured materials with a view to impart on them desired properties. So where are the challenges on the way to their implementation in novel materials and products? These can be identified as follows.
While some of the archetypal families of TI architectures have been identified above, there are an infinite number of possible TI structures. Finding those that best suit a desired property profile of an engineering product is arguably the greatest challenge. For special cases, such as TI structures based on convex polyhedra, some guidance can be obtained by considering a non-dimensional interlocking parameter proposed in [Citation28], but generally, a search in the vast space of potential TI structures would probably not be possible without invoking powerful machine learning techniques.
A second challenge is the difficulty of simulating the mechanical behavior of TI structures by numerical techniques, such as the finite element method. Indeed, a TI structure is not a usual continuum, and the variation of the contact conditions between its elements requires sophisticated and resource-consuming computations.
Structure–property relations for materials architectured by means of TI are not well known yet. This means that extensive experimental work is needed to establish such relations at least for those families of TI structures that have already demonstrated their great potential.
In light of the successful examples of the extraordinary performance of TI structures, we dare to assert that despite these formidable challenges the topological interlocking concept has a promising future as a materials design paradigm.
3. Architectured lattice materials
Lattice materials are composed by a set of interconnected elements (such as rods or plates) which form a periodic structure produced by translation of a characteristic elementary unit cell with a certain symmetry [Citation12,Citation35,Citation36]. This kind of structure is common to many natural and artificial materials. It provides them with a low density and advantageous physical and mechanical properties [Citation37,Citation38]. Usually all constituent elements of a lattice material are identical. They can also be complex, built from elements of a lower length scale [Citation39]. The characteristics of a lattice material are determined by the properties of the constituent elements, the type of their connection at the nodes, and the geometry of the unit cell [Citation12,Citation35]. An interesting analogy with crystal lattices can be drawn by identifying the nodes with atoms and the rods connecting them with the atomic bonds. Then, of course, the symmetry of the crystal structure would suggest the geometry of a rod lattice material. What makes the architectured lattice materials so attractive is the freedom in defining the properties of the bonds (rods) the designer has. This distinguishes them from crystalline materials which must take what they get from the electron structure of the atoms. Using this freedom to vary the properties of the constituent elements of a lattice, a wide spectrum of structural [Citation12,Citation35,Citation39,Citation40] and functional [Citation41,Citation42] characteristics of lattice materials can be obtained. The length scale of the elements of lattice materials can be chosen at will and can reach into the nano range. Some interesting features of downsizing the length of the rods comprising a lattice material have been reviewed in [Citation43].
The crystallographic unit cell may contain atoms of more than one sort, and by analogy, rod lattice materials with more than one kind of rods can be generated. Lattice materials whose elementary unit cell contains different constituent entities offer further great possibilities to extend the material property space [Citation44–51]. Examples of such architectured lattice materials are given in Figure .
Figure 4. Examples of design of elementary unit cells containing elements of different kind: (a) chiral material [Citation44], (b) sponge-inspired material with high buckling resistance [Citation46], (c) hinged lattice with a giant Poisson’s ratio [Citation50], (d) material with a zero Poisson’s ratio [Citation49], (e) programmable metamaterial for energy dissipation with fully reversible deformation [Citation45], (f) damage-tolerant material inspired by crystal microstructure [Citation51], (g) fault-tolerant material [Citation47], (h) three-dimensional auxetic with omnidirectional Poisson's ratio [Citation48]. The white beams are softer than the colored ones; the white and black nods are hinged and rigid, respectively.
![Figure 4. Examples of design of elementary unit cells containing elements of different kind: (a) chiral material [Citation44], (b) sponge-inspired material with high buckling resistance [Citation46], (c) hinged lattice with a giant Poisson’s ratio [Citation50], (d) material with a zero Poisson’s ratio [Citation49], (e) programmable metamaterial for energy dissipation with fully reversible deformation [Citation45], (f) damage-tolerant material inspired by crystal microstructure [Citation51], (g) fault-tolerant material [Citation47], (h) three-dimensional auxetic with omnidirectional Poisson's ratio [Citation48]. The white beams are softer than the colored ones; the white and black nods are hinged and rigid, respectively.](/cms/asset/388aef20-a375-47aa-89fc-6e8bc10489de/tmrl_a_1961908_f0004_oc.jpg)
The design with lattices containing a meso scale structure with elements of different kinds represents a new evolutionary step in the development of this research area [Citation52,Citation53]. A meso structure is a spatial pattern formed by periodic translation of a unit cell built on an original lattice and comprising multiple elementary cells of that lattice (e.g. multiple triangles for a triangular lattice). Inclusion of architecturing at meso scale by allowing variability of the composition of the unit cell increases the number of the degrees of freedom of the system and enables broad variation of the parameters of a regular lattice. This is important for establishing a desired set of properties, which involves multi-criteria optimization. What is even more important is that meso structure imparts to a geometrically regular lattice some cardinally new properties. Thus, the occurrence of forbidden zones in the phonon spectrum [Citation52] or uncharacteristic elastic anisotropy of a triangular rod lattice [Citation53] was achieved in this way. Again, a parallel with the meso scale design for crystal lattices can be drawn. An example of such design embodied in clustered materials is provided in Section 7.
An illustration of the approach proposed in [Citation53] is given in Figure . Figure (a) shows lattice composed of identical elements. Figure (b,c) displays lattices with meso scale unit cells for the case when the rod stiffness coefficient can assume one of two possible values. These unit cells contain 12 or 27 rod elements, respectively. Also shown are the corresponding diagrams for the compliance coefficients in polar coordinates.
Figure 5. Examples of 2D lattices designed to control their anisotropy: (a) lattice with identical elements, and lattices with a meso scale unit cell of 12 rods (b) and 27 rods (c). The white beams are softer than the colored ones; the red dotted line shows the unit cell. The respective diagrams for the compliance coefficients are shown in polar coordinates.
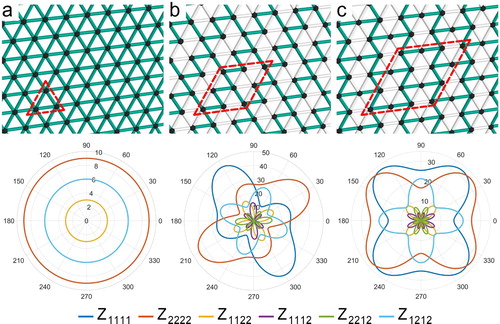
Each rod within a unit cell can in principle be made from any material. Also, the nodes where the rods are joined may be different. The simplest variations amongst the rods can be represented by different stiffnesses assigned to them. This can be furnished either by different elastic moduli of the rods or through differences in their cross-sectional dimensions. The nodes can be chosen to be stiff, hinged, or more intricate, e.g. restricting certain movements of the rods. In addition, the size of the meso scale unit cell may vary from several triangles to the size of the entire structural member of interest.
Thus, the meso structure built on geometrically regular lattices has a great potential in design of architectured materials. However, there is a serious hindrance to realization of this potential. The problem resides in a catastrophically rapid increase of the possible variants of architectured lattice materials with increasing size of the unit cell. To quantify this, we consider a lattice whose elements can be of one of q possible types. Then, for a unit cell containing p elements, the total number of possible variants of the lattice will depend on p exponentially and its order of magnitude will be qp. Problems related to an exponential growth of the volume of data with increasing number of governing parameters are commonly referred to as the ‘curse of dimensionality’—an expression coined by R. Bellman 60 years ago [Citation54]. Efficient methods aimed at overcoming these difficulties have become available owing to recent Machine Learning (ML) studies [Citation55]. Some aspects of the use of ML methods for design of architectured lattice materials were discussed in recent publications [Citation53,Citation56].
Investigations of lattice materials are still in their infancy and that is why it is important to pose the right problems of research in this area now. We see three major directions of research into lattice materials and metamaterials.
(I) Meso scale design. Here two aspects are essential: the structure of the elementary unit cell at meso scale and the characteristics of the constituent elements. The latter can be actuating [Citation57] or responsive, i.e. changing properties in response to external fields or mechanical load. They can also show different responses to tension and compression [Citation58], possess shape memory [Citation59], or have further unusual properties. The meso scale-based design concept is very flexible. Combined with the creativity of the designer, it can lead to a broad range of advanced materials for various applications. Besides, this type of design opens new research directions, such as, for example, analysis of the sensitivity of lattices to production faults—a subject of great significance for manufacturing by 3D printing [Citation60]. Summing up this point, we can say that the potential of meso scale design is huge, as the meso scale unit cells can be chosen freely, which provides a lot of freedom in the bottom-up design of materials with advanced properties.
(II) Application of Machine Learning methods for design of meso scale patterns ensuring desired properties of lattice materials. The authors of [Citation61] proved the validity of the following statement: ‘If in the beginning God gave man just two materials, one sufficiently soft and the other sufficiently rigid (plus some glue and some cutting tools) then man could make everything!’. By ‘everything’ they meant a material that would possess a given elasticity tensor. A numerical realization of a similar idea was reported in [Citation62]. Further development of these concepts becomes possible owing to breakthroughs in deep learning methods, such as GAN and VAE, which allow variation of spatial distributions of pixels/voxels of the base materials within the unit cells [Citation63,Citation64]. The number of parameters that can be varied for 2D and 3D unit cells can be estimated at 104 and 106, respectively. A potential advantage of the meso scale design is the possibility to reduce the number of the variable parameters quite substantially. For instance, a unit cell in 3D consisting of 5 × 5 × 5 octets comprises just 3300 rods. In a way, meso scale design can be seen as a compromise that permits flexible variation of the properties of the material, whilst being very resource effective. In this approach, such ML techniques as Bayesian optimization or genetic algorithms can be used as efficient tools for exploring the structure–property space and for solving the inverse problem [Citation65–67]. A particular problem that can be solved in this way is the determination of the limit values of material characteristics. For isotropic materials, the solution (the so called ‘Hashin-Shtrikman fork’) was provided in a seminal work [Citation68]. It can be claimed that the meso scale approach we promote will enable establishing the limits of the characteristics of a material for the general case of anisotropic materials, be it the 18 invariants of its elasticity tensor or any other characteristics. It is also of great importance that the same strategies allow one to implement the top-down approach to design—starting from the desired material properties and finding a lattice structure that provides them.
(III) Development of new technologies for manufacturing lattice materials with meso structure. Owing to recent advancements of 3D printing and lithography, these technologies found a firm place in the niche area of manufacturing of architectured materials. In our view, fabrication of lattice materials at industry scale by traditional production methods such as casting, metal forming, or joining components by welding or deformation is a formidable challenge. However, some examples demonstrating the feasibility of assembling lattice rod structures have been reported [Citation69,Citation70]. The interlocking technology discussed in Section 2 may be envisioned as a further possible pathway for assembly of lattice materials.
4. Biomimetic and bioinspired materials
Materials are omnipresent in the living world and comprise hard materials, such as bone, seashells, or bird beaks, as well as soft materials, such as cartilage, skin, or silk. These materials are based on few components, mostly proteins and polysaccharides and some minerals, see Figure . These building blocks allow for a great variety of ways in which they can be assembled, leading to diverse properties and multiple functions, from mechanical support to colors and thermal insulation [Citation71].
Figure 6. Biological materials are generally based on few components but acquire a huge diversity of properties and functions due to the multiscale hierarchical structure (adapted from [Citation71]).
![Figure 6. Biological materials are generally based on few components but acquire a huge diversity of properties and functions due to the multiscale hierarchical structure (adapted from [Citation71]).](/cms/asset/0329d83e-e69c-4afd-ae05-1a9ded7e0296/tmrl_a_1961908_f0006_oc.jpg)
In some instances, some of these structures are directly transferred into biomimetic engineering materials. Mostly, however, they inspire the development of engineering structures that use similar structural principles but do not necessarily resemble the biological materials they were inspired from. The reason is that a structural optimization principle will yield results that depend on boundary conditions that are extremely different for a biological system and an engineering one [Citation72].
Over the last 20 years, this field has been developing very rapidly and the publications listed in this area in the Web of Science increase exponentially by roughly doubling every 3 years. There are also several excellent reviews that cover different subfields. For this reason, this section is meant just as a ‘meta-review’ listing and referring to these more detailed surveys. This list follows a classification of the different approaches resulting from the growth of biological materials as compared to the fabrication of engineering materials, published earlier [Citation72], see Figure .
Figure 7. Differences resulting from the growth of biological materials as compared to the fabrication of engineering materials (adapted from [Citation72]).
![Figure 7. Differences resulting from the growth of biological materials as compared to the fabrication of engineering materials (adapted from [Citation72]).](/cms/asset/edd41ce6-7569-4a84-948f-63e7c6bd5a35/tmrl_a_1961908_f0007_oc.jpg)
4.1. Hierarchical structure
A typical result of the natural growth process where building blocks are assembled to larger units, which in turn build up ever larger structures, is the hierarchical nature of biological materials [Citation73]. The advantage is that structures can vary at each of the hierarchical levels and, therefore, adapt to several functions, for instance mechanical, optical or thermal. Protein-based materials, for example, can be soft, hard, elastic, plastic, or sticky, depending on protein-secondary and higher order structures [Citation74].
This led to the development of bioinspired hierarchical materials with advanced properties [Citation75–78]. A material assembled from building blocks has a huge area of internal interfaces between the building blocks that control their properties [Citation79,Citation80]. An extreme case are tessellated materials, where a set of similar two- or three-dimensional tiles are nearly filling a surface or a volume [Citation81]. Progress has been most significant in the development of bioinspired composites and hybrid materials [Citation82–87].
4.2. Structures adapted to enhance specific properties
Structural materials can acquire conflicting properties such as toughness and strength [Citation88], and tough materials can be generated in a bioinspired way based on brittle constituents [Citation89,Citation90]. Plants, for example, also inspire new lightweight constructions [Citation91]. Additive fabrication is an interesting emulation of hierarchical assemblies and bioinspired design approaches are developed for this technique [Citation92].
Surface nano-structuring changes the interaction with fluids, inspired by the well-known self-cleaning capability of lotus leaves. This led to developments of superhydrophobic surfaces [Citation93,Citation94], surfaces with superwettability [Citation95,Citation96], or super lyophilic or -phobic [Citation97]. Moreover, surface structure can make it antiadhesive [Citation98] or ice-repelling [Citation99].
Huge progress has been made in regenerative medicine by the development of bioinspired concepts for tissue engineering [Citation100,Citation101].
Colors can be generated not only by light absorption, but also by diffraction in photonic crystals. Structural colors, antireflective surfaces, and other bioinspired optical materials are being developed [Citation102–105]. Finally, biological systems also inspire flexible electronics [Citation106] as well as neuromorphic electronic materials [Citation107].
4.3. Self-healing and adaptivity
The most interesting properties of bioinspired materials are their various capacities to adapt to environmental stimuli. These properties are also most challenging to transfer into technical adaptation.
Stimulus-responsive shape morphing of materials [Citation108–110] or materials that sense or actuate [Citation111] are becoming exciting avenues in soft robotics [Citation112], biomedical [Citation113] and other types of microrobots [Citation114].
Especially polymeric materials can be processed to be self-healing [Citation115–117] and even to show some adaptivity [Citation118] to the environment.
5. Lithomimetics
We now turn to a very recent new approach to design of architectured materials, referred to as lithomimetics, which was recently proposed in [Citation119]. Although the types of the mesoscale structures it operates with may resemble those also considered in other materials design strategies, there is a defining principle that distinguishes lithomimetics from other approaches. What matters in lithomimetics is not so much the type of a meso structure, but rather the way in which it is generated: through self-organization induced by plastic deformation under pressure. Lithomimetics is chiefly about the processes that emulate those leading to patterns of Earth’s lithosphere, such as beautiful pieces of Nature’s ‘rock art’, e.g. [Citation120]. A few examples of such patterns are shown in Figure [Citation121].
Figure 8. Some spectacular examples of the lithosphere’s patterns (reproduced from [Citation121] with permission from Prof. James Talbot).
![Figure 8. Some spectacular examples of the lithosphere’s patterns (reproduced from [Citation121] with permission from Prof. James Talbot).](/cms/asset/d24acc68-c7d7-4338-8fd0-2ef40b4487f3/tmrl_a_1961908_f0008_oc.jpg)
The physics behind the lithosphere’s patterns is rooted in distortion of the shape of geological bodies (contiguous masses of rock with similar composition [Citation120]). Under forces acting in the solid Earth crust, geological bodies deform plastically and get fractured. An important, and oftentimes decisive, role in this process is played by the phenomenon of strain localization [Citation122]. Owing to bulk compression, adjacent geological bodies penetrate the fractured one through the ruptures that form. This holds the pieces together and leads to mixing of the lithosphere’s constituents. As a result, vortices, folds, and other bizarre formations emerge. To use an art analogy, mixing of colors occurs and, as if copied from a Van Gogh painting, vortices come into being.
In a striking semblance with patterns exemplified by Figure , similar characteristic features are also found in specimens of engineering materials deformed to very large shear strains under high pressure [Citation119]. Such processes, collectively labeled severe plastic deformation (SPD) [Citation123], have become popular as a means of achieving outstanding mechanical properties of metallic materials through extreme grain refinement [Citation124]. The similarity between the structures found in these two realms of matter is not fortuitous. It is caused by the commonality of the underlying physical processes. Despite the obvious difference between metals and rocks (and the length scales of the patterns they develop), they can be described by similar rheological models [Citation125] and obey a common thermodynamic principle of maximum rate of dissipation of mechanical energy [Citation126] that governs the formation of meso structures during plastic deformation.
Literature on high pressure torsion (HPT)—one of the most popular SPD techniques—abounds with examples of patterns in multilayer metallic assemblies akin to those found in the lithosphere, cf., e.g. [Citation127–131]. Research in this area is on the rise, and its current status is captured in a recent review [Citation132]. This research aims at synthesizing bulk nanocrystalline alloys, and in this context the spontaneously emerging lithomimetic structures are considered just as being transient on the way of the system to spatial uniformity. If the aim of the HPT processing is not to achieve full mixing of the components of an assemblage, but rather to emulate patterns occurring in Earth’s lithosphere, then the art of lithomimetics is to find the right processing conditions that furnish that.
While the nature of the lithomimetic structures is obviously stochastic, they contain certain characteristic elements (such as those in Figure ) whose volume fraction in a specimen with a fixed composition and given HPT parameters is determined by the magnitude of strain.
Figure 9. Schematics of several characteristic elements of lithomimetic structures induced by HPT of assemblies of stacked alternating layers of two different metals: (a) initial structure, (b) folds, (c) vortices, (d) boudinage, (e) fine lamellar structure, (f) vortex in a fine lamellar structure. (Adapted from Refs. [Citation119,Citation133–136].) In all figures, the harder of the two constituent layers is shown in green.
![Figure 9. Schematics of several characteristic elements of lithomimetic structures induced by HPT of assemblies of stacked alternating layers of two different metals: (a) initial structure, (b) folds, (c) vortices, (d) boudinage, (e) fine lamellar structure, (f) vortex in a fine lamellar structure. (Adapted from Refs. [Citation119,Citation133–136].) In all figures, the harder of the two constituent layers is shown in green.](/cms/asset/e27784d6-d55a-4ef7-bfd6-b3b5d21c58a8/tmrl_a_1961908_f0009_oc.jpg)
To synthesize uniform materials mechanically, the constituents of the assembly need to come in sufficiently close contact for diffusion to become effective. This requires a fair amount of mixing, as exemplified by fine lamellar structures depicted in Figure (e,f). Unfortunately, it does not happen often that a good mixing is achieved by HPT, even if many anvil revolutions, and hence gigantic shear strains, are applied. Indeed, consider as an example the case when a ‘hard inclusions in a soft matrix’ structure is formed as a result of processing, cf. Figure (c). This puts certain conditions on the subsequent co-deformation of the constituents necessary for continued mixing. In the case when the difference in the flow stresses of the two phases is large and the volume fraction of the hard phase is small, the hard inclusions will ‘float’ in the matrix as rafts of undeformed material. Further deformation of the assembly will not increase the degree of mixing.
Determining the conditions for full mixing of the constituents of an assemblage by HPT and the evolution of the inner architecture towards this state is of paramount significance for synthesis of hybrid nanostructured alloys. Solving this problem requires the knowledge of how lithomimetic structures are formed. At present, this knowledge is practically missing. There is currently just a single article [Citation135] where the evolution of such structures is treated numerically, based on the nonlinear viscous fluid model [Citation134], whilst several publications hypothesize about the mechanisms of the emergence of vortices during HPT [Citation136–138]. There is a need to investigate lithomimetic structures dictated by the growing interest in mechanically induced synthesis of hybrid nanostructured alloys.
At this point we would like to mention the principal difference between the geomimetic approach proposed in [Citation139] and the lithomimetic one championed in our work. The former focuses on hydrothermal synthesis occurring in the Earth’s crust—without involvement of deformation—as a range of processes to be mimicked in producing inorganic, organic, or inorganic/organic hybrid materials. The essence of the lithomimetic principle is the use of the deformation-driven processes creating pattern morphologies of interest.
What makes metallic SPD-derived materials with expressly lithomimetic architecture (LA) particularly attractive? While the full picture is not yet clear, one can dare the assertion that the components of LA materials will have an ultrafine grain structure—a hallmark of SPD processing—thus enhancing mechanical strength of the material. One can also expect good bonding between the components—not only at the atomic scale but also at the meso scale, owing to mechanical interlocking at the interfaces due to swirls formed there, cf. Figure (b,c,f). This kind of geometrical interlocking differs from the topological interlocking discussed in Section 2, but its beneficial effect in terms of enhancement of mechanical strength and fracture toughness may be considerable as well. It is this combination of the effects of structure variation at micro and meso scale potentially achievable through lithomimetic architecturing that gives promise for materials design. An additional advantage is associated with back stresses arising from plastic incompatibility between the different components of the assemblage that is discussed in Section 6. The co-existence of hard and soft constituents within the material is also conducive for good tensile ductility. Structures containing folds of a hard material (Figure (b)) give rise to geometry-induced strain hardening [Citation140]. Structures composed of alternating thin layers with different strength (Figure (e,f)) can be used to produce materials with reduced sensitivity to tensile overloads [Citation141]. Crack propagation in such structures is also hindered [Citation142], which causes their high fracture resistance. Blocky structures, such as vortices (Figure (c)) or chocolate boudinage (Figure (d)), may prove to be useful for various physical applications. For example, one can reduce the energy losses due to eddy currents in electric machines and transformers [Citation143] by creating material architectures where ferromagnetic blocks are separated by layers of a non-magnetic material with a low electrical conductivity.
By virtue of their morphology, LA materials are richer in the degrees of freedom than metals and alloys with a uniform inner structure. This is the key to the potential advantages of the LA materials [Citation144]. Creating novel materials with improved properties is not the ultimate goal of research, however. Materials are the stuff from which things are manufactured, which is done by such processes as cutting, metal forming, or consolidation of powders. Metal forming is known to change the structure of materials at all length scales, which alters their properties. While for conventional metals and alloys these processes have been extensively studied and are largely understood, no such studies have been conducted for LA materials. It is therefore not known at this stage what properties will be imparted to articles from lithomimetic materials by metal forming processes. The lack of knowledge in this area calls for studies into the effect of different deformation processes on the meso structure and properties of bulk lithomimetic materials. Obtaining the full gamut of characteristics of such materials, including the flow curves for different deformation modes, yield surfaces, fracture criteria, etc., which are required for design of manufacturing processes, is thus the order of the day.
To conclude this section, we would also like to mention the possibility of using LA materials in the form of powders. To that end, one will first need to produce planar blanks of such materials, e.g. by high-pressure torsion or high-pressure sliding [Citation145]. These blanks are to be crushed to powders, which can be done by employing, for example, a swarf crusher. From the LA powders thus produced, various structural members can be manufactured by traditional powder technologies or by 3D printing.
Admittedly, being a very new approach, lithomimetics is still in its infancy, and it is to be seen whether this strategy for creating novel materials will come to fruition in terms of practical applications. But the potential is there, and it is worth being explored and exploited.
6. Heterostructured materials
Since the first report [Citation146] on the superior mechanical properties of heterostructured materials that cannot be explained in terms of conventional materials science, they have been rapidly developing to a hot research area. Heterostructured materials are defined as materials consisting of heterogenous zones that have radically different mechanical and physical properties (>100%) and exhibit significant synergy that surpasses the prediction by the rule of mixtures [Citation147]. The fundamentals of heterostructured materials have been systematically investigated over the last few years and significant progress, reported in a suit of papers, has been made [Citation146–155]. One of the most important advantages of heterostructured materials is that they can be processed by current industrial facilities, making it conducive to industrial production at low cost [Citation154]. Thus, a common problem with real-world application faced by most new materials is avoided. This section provides a brief introduction to heterostructured materials.
Many materials systems can be classified as heterostructured materials (see Figure ), including heterogeneous lamellae structured materials (Figure (a)) [Citation146], laminate structured materials (Figure (b)) [Citation149,Citation156–169], gradient structured materials (Figure (c)) [Citation152,Citation153,Citation170–173], harmonic (core–shell) materials (Figure (d)) [Citation174–176], dual/multi-phase structured materials [Citation177–179], multi-modal materials [Citation180–183], etc. As seen in Figure , these materials have very diverse microstructures that can be hardly classified into one common category. Nevertheless, they are all referred to as heterostructured materials because their superior mechanical properties are derived from the same scientific principle: hetero-deformation induced (HDI) strengthening and HDI strain hardening [Citation147,Citation148]. The HDI strengthening acts to enhance the yield strength, while the HDI strain hardening acts to help retain the ductility.
Figure 10. Four typical heterostructures [Citation147]: (a) heterogeneous lamellar structure [Citation146], (b) laminate structure, (c) gradient structure, and (d) harmonic (core–shell) structure (adapted from [Citation146,Citation147]). In these schematic sketches the scale depends on the nature of the respective fabrication process, the smallest features being typically at nanoscale.
![Figure 10. Four typical heterostructures [Citation147]: (a) heterogeneous lamellar structure [Citation146], (b) laminate structure, (c) gradient structure, and (d) harmonic (core–shell) structure (adapted from [Citation146,Citation147]). In these schematic sketches the scale depends on the nature of the respective fabrication process, the smallest features being typically at nanoscale.](/cms/asset/02c49041-c288-4fc1-9732-e852ec13916b/tmrl_a_1961908_f0010_oc.jpg)
HDI stress is caused by the plastic incompatibility between hard and soft zones in heterostructured materials [Citation147,Citation148]. As shown in Figure , geometrically necessary dislocations (GNDs) with the same Burgers vector are emitted from a Frank-Read source within a soft zone and pile up against a boundary with the adjacent hard zone. These GNDs produce a long-range back stress in the soft zone to obstruct the glide of trailing GNDs, which effectively makes the soft zone apparently stronger. The direction of the back stress is opposite to that of the applied stress. At the same time, the piling up of GNDs produces a stress concentration of nτa at the zone boundary, where n is the total number of GNDs in a pileup and τa is the applied shear stress. A forward stress, with the same magnitude of nτa, but opposite to the direction of the back stress is generated at the hard zone side of the boundary to balance the back stress. In other words, the back stress and the forward stress cancel each other at the zone boundary. However, the forward stress and the back stress decay in a different way at distances away from the boundary, and therefore cannot cancel each other. Consequently, they collectively produce a hetero-deformation induced (HDI) stress.
Figure 11. Schematics of the piling up of geometrically necessary dislocations in the soft zone producing a back stress in the soft zone and a forward stress in the hard zone [Citation147].
![Figure 11. Schematics of the piling up of geometrically necessary dislocations in the soft zone producing a back stress in the soft zone and a forward stress in the hard zone [Citation147].](/cms/asset/6dc74e8e-ebfa-4055-924b-04987e5c07ed/tmrl_a_1961908_f0011_oc.jpg)
The HDI stress enhances the yield strength of the heterostructured materials before yielding, while the continuous increase of HDI stress after yielding produces strain hardening to retain or even increase the ductility. This is the key advantage of the HDI effect, which can simultaneously increase the yield strength and strain hardening [Citation147,Citation148]. Most strengthening mechanisms in conventional homogeneous materials reduce the strain hardening capability, which produces a typical tradeoff between the strength and ductility [Citation147]. It is noted that before yielding, the HDI stress rises due to the increase in the back stress while the forward stress is still not high enough to soften the hard zones. Therefore, it can be argued that the enhancement of the yield strength can be largely attributed to the back stress strengthening.
The best demonstration of the advantage of heterostructured materials is presented in Figure [Citation146], which shows that the heterostructured lamellar Ti has the strength of nanostructured Ti, while its ductility is even slightly higher than that of the coarse-grained Ti. This is what would be believed impossible according to our textbook knowledge. Not all heterostructured materials exhibit such a great heterostructural effect, though. That is why a targeted design of heterostructures is needed for achieving the best properties. A better understanding of the deformation fundamentals of heterostructured materials is required before we can effectively design and predict their mechanical properties.
Figure 12. A superior combination of strength and ductility of heterostructured lamellar (HL) Ti as compared with that of ultrafine-grained (UFG) Ti and coarse-grained (CG) Ti (adapted from [Citation146]).
![Figure 12. A superior combination of strength and ductility of heterostructured lamellar (HL) Ti as compared with that of ultrafine-grained (UFG) Ti and coarse-grained (CG) Ti (adapted from [Citation146]).](/cms/asset/f50a5c7f-b06b-4d5c-84fc-2d6d6cac699b/tmrl_a_1961908_f0012_oc.jpg)
Extensive, highly dispersed localized strain bands (LSBs) have been observed in several types of heterostructured materials, including gradient [Citation184,Citation185], bi-modal grain structured [Citation186], and laminated samples [Citation150]. It appears that the formation of dispersed LSBs may be an intrinsic deformation feature of heterostructured materials [Citation147]. Formation of dispersed LSBs is a mechanism for the hard zones, which typically have low strain hardening rate, to accommodate more plastic strain without leading to catastrophic failure of the whole sample. Dispersed LSBs are stabilized by the higher strain hardening rate of the soft zones, the recovery of strain hardening capability in the LSBs, as well as the local strain gradient near the propagating fronts of the LSBs [Citation150,Citation184–186]. The mechanisms of nucleation and propagation of LSBs are still not well understood, and this has become a fundamental issue with heterostructured materials. Particularly, the observations of shear bands on the surface of the samples are so far at macroscopic scale (micrometers to millimeters). It is critical to understand the nucleation and propagation of LSBs at the dislocation level. A critical issue here is the relationship between the LSB formation and the piling up and interactions of geometrically necessary dislocations at the zone boundaries.
Like for several other sections of this article, it can be said that the field of heterostructured materials is still in its infancy, although several industrial techniques have been used to produce such materials with encouraging successes. The processing of heterostructured materials is still by trial and error, however. It is therefore important to develop predictive models and theories to design heterostructures for the best properties, which in turn needs a better understanding of their deformation physics. It is also important to develop new technologies that can produce desired heterostructures in a controlled and economic manner, thus facilitating production of heterostructured materials at industry scale.
7. Cluster and nanoparticle assembly towards architectured materials
Clusters and nanoparticles are possible building blocks for the assembly of architectured materials. In our terminology, clusters are structural entities consisting of a few to a few hundred atoms each, corresponding to the size range up to 3 nm in diameter, while nanoparticles are typically considered to be in the size range above the largest cluster sizes. The differentiation between the terms cluster and nanoparticle is not exactly defined and is based more on the differences of atomic structure and properties, than on the size alone.
The assembly of nanoparticles using controlled compaction at high pressures under extremely clean vacuum conditions has been the innovative idea in the early 1980s leading to nanocrystalline (nc) materials [Citation187,Citation188] and later to nanoglasses [Citation189]. The compaction of nanoparticles with average sizes in the range of 10–20 nm results in the formation of interfacial regions. In the case of crystalline particles, grain boundaries are formed and, due to the nanometer size of the particles, the grain boundaries become a substantial fraction of the material. If the particles are amorphous, it has been found that the interfacial regions are amorphous as well, but with an atomic structure distinctly different from that of the inner parts of the amorphous nanoparticles. The idea to combine nanoparticle synthesis with ‘powder metallurgy’, i.e. compaction and sintering, for different types of particle structure has led to an enormous growth of the field. In particular, the idea of assembling nanoparticles opens up opportunities for the controlled design of novel materials with unprecedented mechanical and functional properties.
At the smaller end of the size range of particles, isolated clusters have been extensively studied motivated by the strong size dependence of their structure and functional properties leading to quantum confinement phenomena for the case of small numbers of atoms per cluster. Clusters of pure elements and compounds can be synthesized using physical and chemical methods, resulting in narrow size distributions or even atomically precise sizes, as bare clusters or those protected by organic molecules. The structure of such clusters is well known based on electron and X-ray diffraction and first principle Discrete Fourier Transform (DFT) calculations [Citation190,Citation191]. Size-selected clusters of many metals have been reported, including Au7, Au19 and Au20 [Citation192] and 55-atom transition metal clusters [Citation193], atomically precise unprotected (bare) or protected metal clusters, such as Au55(PPh3)12Cl6 and [Au25(PET)18] [Citation194], metal chalcogenides [Citation195], and many more varieties. Clusters can be handled as charged species in vacuum, as clusters in liquid solvents, or embedded in frozen inert gases. In all operations with clusters, even when stabilized using ligands, it needs to be considered that the clusters remain extremely reactive. As an example, using mass spectroscopy, it has been shown that protected clusters of noble metals, each with the identical number of atoms, in a solvent react with each other, by continuously exchanging atoms. The kinetics of such intercluster reactions between atomically precise [Ag25(DMBT)18]− and [Au25(PET)18]− clusters yields a wide distribution of product clusters [AgmAu25−m]− (m = 1−24) [Citation196].
Single crystals of atomically precise clusters with sizes reaching millimeters can be formed. Typically, such single crystals are used for structure determination and property measurements [Citation195]. However, only few reports are available on 2D- or 3D-arrangements of clusters or integration into matrix materials to exploit the cluster properties for engineering applications. The use of clusters, or at larger sizes, nanoparticles as building blocks opens new ways to architecture functional materials from the bottom up and represents a paradigm shift from established synthesis methods, such as thin film deposition using atomic species. In particular, cluster or nanoparticle assembly allows to transfer the size-dependent properties, including quantum phenomena, into the assembled structures, and to integrate the large fractions of interfaces into the design of advanced materials.
A wealth of possibilities arises from the variation of the characteristics of the building blocks, i.e. clusters or nanoparticles, crystalline or amorphous, atomically precise or with a size distribution, for the final architecture of the resulting material. The grain boundaries in nc-materials represent disorder of the crystalline lattice and thus high energy defects, leading to a strong tendency for grain growth. The effects of nanometer-sized grains have been exploited in the field of nanocrystalline materials, both for metals and oxides, with superior mechanical and functional properties being reported [Citation188,Citation197]. In contrast, the amorphous interfaces formed in metallic nanoglasses, have been described as regions of increased medium-range order and enhanced free volume, most likely exhibiting lower energy compared to the grain interiors with the amorphous structure characteristic for rapidly quenched metallic glasses. That is to say, in a nanoglass the presence of the interfaces lowers the free energy of the entire system [Citation197,Citation198].
In recent years, an increasing interest in cluster-assembled materials, instead of the study of isolated clusters, is noticed. Two examples are to be mentioned. (1) By using C58 fullerenes as perfect mono-sized building blocks, micrometer-thick films have been formed on inert surfaces and subsequently, their mechanical properties have been measured [Citation199]; (2) a nano-inorganic layered hybrid material, composed of bovine serum albumin (BSA)-protected atomically precise Au30 clusters and aminoclay sheets was synthesized and its luminescence properties were studied and applied in a strain sensor [Citation200]. The availability of well-defined clusters in sufficient quantities opens up opportunities for the design of novel materials structures, as will be described in the following paragraphs.
Thin film deposition, where layers are grown from atomic species using physical (MBE, sputtering, PLD) or chemical (CVD, ALD) methods, has seen a wide distribution from basic science studies to large scale industrial processes. As an extension of thin film growth, the use of well-defined clusters as building blocks for layers or bulk structures offers new functionalities by the possibility of integrating favorable cluster properties into usable material structures.
Irrespective of the preparation method, some prerequisites need to be fulfilled, such as availability of sufficient quantities of well-defined clusters, and chemical or physical processing methods for the integration of clusters into the desired material structures. Many options to architecture the final morphology and geometry of 2D and 3D cluster-assembled materials are available: (i) integration of clusters into pre-existing structures that provide the space for the cluster integration; (ii) deposition of clusters on a substrate under controlled conditions; and (iii) co-deposition of clusters and a matrix.
For the case of growth using physical methods, Figure summarizes the wide range of possibilities using cluster assembly, assuming that the system is capable of producing simultaneously a cluster beam with size selection and of providing a flux of matrix atoms onto a substrate. For all possible cases, a large number of variables can be freely selected, such as size and size distribution of clusters, structure of clusters, i.e. crystalline or amorphous, material and type of bonding, i.e. metallic, ionic or covalent, charge state of clusters, and impact energy on substrate. Two general groups can be distinguished, pure cluster-deposited materials (denoted A), which are formed by the controlled deposition of only clusters on a substrate, and cluster-matrix composites (denoted B, C, D), formed by the co-deposition of clusters and of a matrix. In the latter case, both clusters and matrix can consist of any combination of materials with metallic, ionic or covalent bonds.
Figure 13. Schematic of architectured materials made possible by cluster assembly. On the right side, possible variations of cluster-matrix composites are shown, amorphous (blue), crystalline (green) or mixed clusters, also with different sizes, embedded in a continuous matrix (grey), which can be crystalline or amorphous, and metallic or non-metallic. The variability offers an enormous number of possible combinations, even more if cluster size and impact energy are considered as additional parameters. On the left side variations of systems are shown, prepared solely by cluster deposition, i.e. without any matrix deposition. The bottom (blue) shows cluster-assembled metallic glasses, the middle (green) nanocrystalline materials with extremely small grain sizes, and the top (mixed green and blue) the possibility for cluster-assembled nanocomposites with different chemical compositions. Porosity can be an additional component of the cluster-assembled structure, as shown in the figure, but can also be prevented by using appropriate processing conditions.
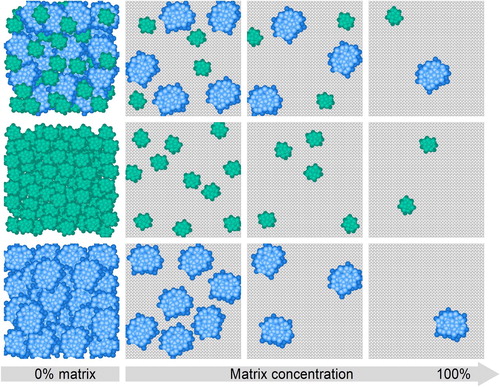
For cluster-matrix composites, the co-deposition allows the growth of any volume fraction of clusters in any matrix, irrespective of the equilibrium phase diagram. As an example, even for fully miscible systems, such as Nix-Cu (x denoting the number of atoms per cluster), it is possible to stabilize Ni-clusters in a Cu-matrix and to freely choose the volume fraction of clusters by the ratio of cluster flux and matrix atom flux. In addition. several systems of immiscible combinations, such as Fex-Ag [Citation201], Fex-Cr [Citation202] and Fex-Ge [Citation203] have shown interesting magnetic and magnetoelectric properties. Even applications in quantum technology for magnetic Josephson junctions are being considered [Citation204].
Pure cluster-deposited materials have been prepared using amorphous Fe80Sc20 clusters deposited at different impact energies from 50 to 500 eV per cluster [Citation205]. The structural motifs of the amorphous structure determined from extended X-ray absorption fine structure (EXAFS) measurements vary strongly with impact energy. At the highest impact energy, the structural motifs are identical to those of the rapidly quenched control sample yet are altered systematically at lower energies. The change of the magnetic Curie temperature follows the change of the structure, which demonstrates the ability to control functional properties by the parameters of cluster deposition, and to grow amorphous structures not considered previously.
It’s still early days, but it has already been demonstrated for cluster-assembled materials that unique structures with unexpected properties can be prepared. The uniqueness of the new synthesis processes with the possibility to transfer the richness of the size-dependent properties of individual clusters to bulk materials will undoubtedly enrich materials science.
8. Conclusion
In this article, we outlined six promising areas of research devoted to improving the properties and functionalities of materials through their architecturing. These areas are far from maturity, but the advancements achieved so far are encouraging. Among the features of the architectured materials that transpired is their ability to provide function with less chemical diversity than conventional materials. Archimats are, therefore, more easily recycled, as less effort is needed in separating their different components. Some types of architectured materials, for example interlocking materials or trusses and lattices, may even be reconfigured to provide new functions. For this reason, we expect that the development of architectured materials will gain increasing momentum with the growing need for a sustainable materials economy.
As stated in the Introduction, the juxtaposition of the subjects presented here is not exhaustive. Rather, it is based on our individual research interests and, to some extent, on our idiosyncrasies. While our research preferences may be different, we all share the view that each of these areas is interesting in its own way, and we hope to have attracted the attention of the readers to the great potential they have. We trust that this essay will stimulate research into the principles and methods of designing architectured materials. Outcomes of this research may one day become part of the engineering practice, so it is worthwhile watching this space!
Acknowledgements
YE appreciates the hospitality of the Max Planck Institute for Colloids and Interfaces (Potsdam, Germany) he enjoyed during his stay there as a senior visiting researcher.
Disclosure statement
No potential conflict of interest was reported by the author(s).
Additional information
Funding
References
- Ashby MF. Designing architectured materials. Scr Mater. 2013;68:4–7.
- Estrin Y, Bréchet Y, Dunlop J, et al. Architectured materials in nature and engineering. Cham, Switzerland: Springer Nature; 2019.
- Haken H. Information and self-organization. A macroscopic approach to complex systems. Berlin: Springer; 2006.
- Kanit T, Forest S, Galliet I, et al. Determination of the size of the representative volume element for random composites: statistical and numerical approach. Int J Solids Struct. 2003;40(13–14):3647–3679.
- Imry Y. Introduction to mesoscopic physics (mesoscopic physics and nanotechnology). New York: Oxford University Press; 2008.
- Beygelzimer Y, Spuskanyuk A. The thick yield surface: an idea and approach for investigating its structure. Phil Mag A. 1999;79:2437–2459.
- Thom R. Structural stability and morphogenesis. London: W.A. Benjamin; 1975.
- Sass SL. The substance of civilization: materials and human history from the stone age to the age of silicon. New York: Arcade; 1998.
- Cahn RW. The coming of materials science. Pergamon Materials Series. New York: Pergamon; 2001.
- Fleck NA, Deshpande VS, Ashby MF. Micro-architectured materials: past, present, and future. Proc Roy Soc A. 2010;466:2495–2516.
- Greer JR, Deshpande VS. Three-dimensional architected materials and structures: design, fabrication, and mechanical behavior. MRS Bull. 2019;44:750–757.
- Ashby MF. Materials selection in mechanical design. Burlington (MA): Butterworth-Heinemann Elsevier; 2011.
- Dyskin AV, Estrin Y, Kanel-Belov A, et al. A new concept in design of materials and structures: assemblies of interlocked tetrahedron-shaped elements. Scr Mater. 2001;44:2689–2694.
- Dyskin AV, Estrin Y, Kanel-Belov A, et al. Toughening by fragmentation—how topology helps. Adv Eng Mater. 2001;3(11):885–888.
- Estrin Y, Dyskin AV, Pasternak E. Topological interlocking as a material design concept. Mater Sci Eng C. 2011;31:1189–1194.
- Dyskin AV, Estrin Y, Belov-Kanel A, et al. Topological interlocking of platonic solids: a way to new materials and structures. Phil Mag Lett. 2003;83(3):197–203.
- Kanel-Belov A, Dyskin AV, Estrin Y, et al. Interlocking of convex polyhedra: towards a geometric theory of fragmented solids. Moscow Math J. 2010;10:337–342.
- Weizmann M, Amir O, Grobman YJ. Topological interlocking in buildings: a case for the design and construction of floors. Autom Constr. 2016;72:18–25.
- Vella IM, Kotnik T. Geometric versatility of abeille vault. A stereotomic, topological interlocking assembly. 34th Annual eCAADe. 2016;34:391–397.
- Bejarano A, Hoffmann C. A generalized framework for designing topological interlocking configurations. Int J Archit Comput. 2019;17:53–73.
- Viana V. Topological interlocking of convex regular polyhedra. In: Leopold C, Robeller C, Weber U, editors. RCA 2018, Conference book; September 27-28. TU Kaiserslautern, Germany. 2018:255–257.
- Piekarski M. Floor slabs made from topologically interlocking prefabs of small size. Build. 2020;10(4):76.
- Subramanian SG, Eng M, Krishnamurthy VR, et al. Delaunay lofts: a biologically inspired approach for modeling space filling modular structures. Comp Graph. 2019;82:73–83.
- Krishnamurthy VR, Akleman E, Subramanian SG, et al. Geometrically interlocking space-filling tiling based on fabric weaves. 2021; in press.
- Estrin Y, Krishnamurthy V, Akleman E. Design of architectured materials based on topological and geometrical interlocking. J Mater Res Techn. 2021; in press.
- Krause T, Molotnikov A, Carlesso M, et al. Mechanical properties of topologically interlocked structures with elements produced by freeze gelation of ceramic slurries. Adv Eng Mater. 2012;14:335–341.
- Khandelwal S, Siegmund T, Cipra RJ, et al. Transverse loading of cellular topologically interlocked materials. Int J Solids Struct. 2012;49:2394–2403.
- Mirkhalaf M, Zhou T, Barthelat F. Simultaneous improvements of strength and toughness in topologically interlocked ceramics. PNAS. 2018;115(37):9128–9133.
- Feng Y, Siegmund T, Habtour E, et al. Impact mechanics of topologically interlocked material assemblies. Intl J Impact Eng. 2015;75:140–149.
- Djumas L, Simon GP, Estrin Y, et al. Deformation mechanics of non-planar topologically interlocked assemblies with structural hierarchy and varying geometry. Sci Rep. 2017;7:11844.
- Molotnikov A, Estrin Y, Dyskin AV, et al. Percolation mechanism of failure of a planar assembly of interlocked osteomorphic elements. Eng Fract Mech. 2007;74(8):1222–1232.
- Ashby M, Brechet Y. Designing hybrid materials. Acta Mater. 2003;51(19):5801–5821.
- Carlesso MV, Giacomelli RO, Krause T, et al. Improvement of sound absorption and flexural compliance of porous alumina-mullite ceramics by engineering the microstructure and segmentation into topologically interlocked blocks. J European Ceram Soc. 2013;33:2549–2558.
- Meyers MA, Chen PY, Lin YM, et al. Biological materials: structure and mechanical properties. Prog Mater Sci. 2008;53:1–206.
- Valdevit L, Jacobsen AJ, Greer JR, et al. Protocols for the optimal design of multi-functional cellular structures: from hypersonics to micro-architected materials. J Am Ceram Soc. 2011;94:15–34.
- Gibson LJ, Ashby MF. Cellular solids, structure and properties. New York: Cambridge University Press; 1997.
- Ashby MF. The properties of foams and lattices. Phil Trans R Soc A. 2006;364:15–30.
- Benedetti M, Plessis A, Ritchie RO, et al. Architected cellular materials: a review on their mechanical properties towards fatigue-tolerant design and fabrication. Mater Sci Eng R. 2011;144:100606.
- Zheng X, Smith W, Jackson J, et al. Multiscale metallic metamaterials. Nature Mater. 2016;15:1100–1106.
- Schwaiger R, Meza LR, Li X. The extreme mechanics of micro- and nanoarchitected materials. MRS Bull. 2019;44:758–765.
- Kadic M, Milton GW, Hecke M, et al. 3D metamaterials. Nat Rev Phys. 2019;1:198–210.
- Phani AS, Hussein MI. Dynamics of lattice materials. Chichester: Wiley; 2017.
- Bauer J, Meza LR, Schaedler TA, et al. Nanolattices: an emerging class of mechanical metamaterials. Adv Mater. 2017;29(40):1701850.
- Ziemke P, Frenzel T, Wegener M, et al. Tailoring the characteristic length scale of 3D chiral mechanical metamaterials. Extr Mech Lett. 2019;32:100553.
- Findeisen C, Hohe J, Kadic M, et al. Characteristics of mechanical metamaterials based on buckling elements. J Mech Phys Solids. 2017;102:151–164.
- Fernandes MC, Aizenberg J, Weaver JC, et al. Mechanically robust lattices inspired by deep-sea glass sponges. Nat Mater. 2021;20:237–241.
- Ryvkin M, Slesarenko V, Cherkaev A, et al. Fault-tolerant elastic–plastic lattice material. Phil Trans R Soc A. 2020;10:20190107.
- Cabras L, Brun M. A class of auxetic three-dimensional lattices. J Mech Phys Solids. 2016;91:56–72.
- Carta G, Cabras L, Brun M. Continuous and discrete microstructured materials with null Poisson’s ratio. J Eur Ceram Soc. 2016;36:2183–2192.
- Shaat M, Wagih A. Hinged-3D metamaterials with giant and strain-independent Poisson’s ratios. Sci Rep. 2020;10:2228.
- Pham MS, Liu C, Todd I, et al. Damage-tolerant architected materials inspired by crystal microstructure. Nature. 2019;565:305–311.
- Ronellenfitsch H, Stoop N, Yu J, et al. Inverse design of discrete mechanical metamaterials. Phys Rev Mater. 2019;3:095201.
- Kulagin R, Beygelzimer Y, Estrin Y, et al. Architectured lattice materials with tuneable anisotropy: design and analysis of the material property space with the aid of machine learning. Adv Eng Mater. 2020;22:2001069.
- Bellman RE. Adaptive control processes: a guided tour. New Jersey: Princeton University Press; 1961.
- Nilsson NJ. Principles of artificial intelligence. Berlin: Morgan Kaufmann; 2014.
- Huber N. Connections between topology and macroscopic mechanical properties of three-dimensional open-pore materials. Front Mater. 2018;5:69.
- Xia X, Afshar A, Yang H, et al. Electrochemically reconfigurable architected materials. Nature. 2019;573:205–213.
- Masic M, Skelton RE, Gill PE. Algebraic tensegrity form-finding. Int J Solids Struct. 2005;42:4833–4858.
- Beloshenko VA, Varyukhin VN, Voznyak YV. The shape memory effect in polymers. Russ Chem Rev. 2005;74(3):265–283.
- Pasini D, Guest J. Imperfect architected materials: mechanics and topology optimization. MRS Bull. 2019;44(10):766–772.
- Milton GW, Cherkaev AV. Which elasticity tensors are realizable? ASME J Eng Mater Technol. 1995;117(4):483–493.
- Sigmund O. Materials with prescribed constitutive parameters: an inverse homogenization problem. Int J Solids Struct. 1994;31:2313–2329.
- Mao Y, He Q, Zhao X. Designing complex architectured materials with generative adversarial networks. Sci Adv. 2020;6:4169.
- Xue T, Wallin TJ, Menguc Y, et al. Machine learning generative models for automatic design of multi-material 3D printed composite solids. Extr Mech Lett. 2020;41:100992.
- Cadman JE, Zhou S, Chen Y, et al. On design of multi-functional microstructural materials. J Mater Sci. 2013;48:51–66.
- Glass CW, Oganov AR, Hansen N. USPEX—evolutionary crystal structure prediction. Comp Phys Comm. 2006;175:713–720.
- Garcia-Santiago X, Burger S, Rockstuhl C, et al. Bayesian optimization with improved scalability and derivative information for efficient design of nanophotonic structures. J Light Technol. 2021;39:167.
- Hashin Z, Shtrikman S. A variational approach to the theory of the elastic behaviour of multiphase materials. J Mech Phys Solids. 1963;11:127–140.
- Wadley HNG. Multifunctional periodic cellular metals. Phil Trans R Soc A. 2006;364:31–68.
- Khoda B, Ahsan AMMN, Shovon AN, et al. 3D metal lattice structure manufacturing with continuous rods. Sci Rep. 2021;11:434.
- Eder M, Amini S, Fratzl P. Biological composites-complex structures for functional diversity. Science. 2018;362:543–547.
- Fratzl P. Biomimetic materials research: what can we really learn from nature’s structural materials? J R Soc Interface. 2007;4(15):637–642.
- Fratzl P, Weinkamer R. Nature’s hierarchical materials. Prog Mater Sci. 2007;52(8):1263–1334.
- Harrington MJ, Fratzl P. Natural load-bearing protein materials. Prog Mater Sci. 2021;120:100767.
- Liu KS, Jiang L. Bio-inspired design of multiscale structures for function integration. Nano Today. 2011;6(2):155–175.
- Xia F, Jiang L. Bio-inspired, smart, multiscale interfacial materials. Adv Mater. 2008;20(15):2842–2858.
- Yang XY, Chen LH, Li Y, et al. Hierarchically porous materials: synthesis strategies and structure design. Chem Soc Rev. 2017;46(2):481–558.
- Yao HB, Fang HY, Wang XH, et al. Hierarchical assembly of micro-/nano-building blocks: bio-inspired rigid structural functional materials. Chem Soc Rev. 2011;40(7):3764–3785.
- Barthelat F, Yin Z, Buehler MJ. Structure and mechanics of interfaces in biological materials. Nature Rev Mater. 2016;1:16007.
- Dunlop JWC, Weinkamer R, Fratzl P. Artful interfaces within biological materials. Mater Today. 2011;14(3):70–78.
- Fratzl P, Kolednik O, Fischer FD, et al. The mechanics of tessellations – bioinspired strategies for fracture resistance. Chem Soc Rev. 2016;45(2):252–267.
- Dunlop JWC, Fratzl P. Biological composites. Ann Rev Mater Res. 2010;40:1–24.
- Estroff LA, Hamilton AD. At the interface of organic and inorganic chemistry: bioinspired synthesis of composite materials. Chem Mater. 2001;13(10):3227–3235.
- Nudelman F, Sommerdijk N. Biomineralization as an inspiration for materials chemistry. Angewandte Chem Inter Edition. 2012;51(27):6582–6596.
- Sanchez C, Julian B, Belleville P, et al. Applications of hybrid organic-inorganic nanocomposites. J Mater Chem. 2005;15(35-36):3559–3592.
- Studart AR. Towards high-performance bioinspired composites. Adv Mater. 2012;24(37):5024–5044.
- Foerster S, Antonietti M. Amphiphilic block copolymers in structure-controlled nanomaterial hybrids. Adv Mater. 1998;10(3):195–217.
- Wegst UGK, Bai H, Saiz E, et al. Bioinspired structural materials. Nature Mater. 2015;14(1):23–36.
- Bouville F, Maire E, Meille S, et al. Strong, tough and stiff bioinspired ceramics from brittle constituents. Nature Mater. 2014;13(5):508–514.
- Ritchie RO. The conflicts between strength and toughness. Nature Mater. 2011;10(11):817–822.
- Speck T, Burgert I. Plant stems: functional design and mechanics. Annu Rev Mater Res. 2011;41:169–193.
- Plessis A, Broeckhoven C, Yadroitsava I, et al. Beautiful and functional: a review of biomimetic design in additive manufacturing. Addit Manuf. 2019;27:408–427.
- Bhushan B, Jung YC. Natural and biomimetic artificial surfaces for superhydrophobicity, self-cleaning, low adhesion, and drag reduction. Prog Mater Sci. 2011;56(1):1–108.
- Koch K, Bhushan B, Barthlott W. Multifunctional surface structures of plants: an inspiration for biomimetics. Prog Mater Sci. 2009;54(2):137–178.
- Liu MJ, Wang ST, Jiang L. Nature-inspired superwettability systems. Nature Rev Mater. 2017;2:17036.
- Yao X, Song YL, Jiang L. Applications of bio-inspired special wettable surfaces. Adv Mater. 2011;23(6):719–734.
- Wang B, Liang WX, Guo ZG, et al. Biomimetic super-lyophobic and super-lyophilic materials applied for oil/water separation: a new strategy beyond nature. Chem Soc Rev. 2015;44(1):336–361.
- Wong TS, Kang SH, Tang SKY, et al. Bioinspired self-repairing slippery surfaces with pressure-stable omniphobicity. Nature. 2011;477(7365):443–447.
- Kreder MJ, Alvarenga J, Kim P, et al. Design of anti-icing surfaces: smooth, textured or slippery? Nature Rev Mater. 2016;1:15003.
- Ma PX. Biomimetic materials for tissue engineering. Adv Drug Deliv Rev. 2008;60(2):184–198.
- Shin H, Jo S, Mikos AG. Biomimetic materials for tissue engineering. Biomater. 2003;24(24):4353–4364.
- Tadepalli S, Slocik JM, Gupta MK, et al. Bio-optics and bio-inspired optical mater. Chem Rev. 2017;117(20):12705–12763.
- Zhao YJ, Xie ZY, Gu HC, et al. Bio-inspired variable structural color materials. Chem Soc Rev. 2012;41(8):3297–3317.
- Gur D, Palmer BA, Weiner S, et al. Light manipulation by guanine crystals in organisms: biogenic scatterers, mirrors, multilayer reflectors and photonic crystals. Adv Funct Mater. 2017;27:1603514.
- Stefik M, Guldin S, Vignolini S, et al. Block copolymer self-assembly for nanophotonics. Chem Soc Rev. 2015;44(15):5076–5091.
- Liu YQ, He K, Chen G, et al. Nature-inspired structural materials for flexible electronic devices. Chem Rev. 2017;117(20):12893–12941.
- Sangwan VK, Hersam MC. Neuromorphic nanoelectronic materials. Nature Nanotech. 2020;15(7):517–528.
- Jeon SJ, Hauser AW, Hayward RC. Shape-morphing materials from stimuli-responsive hydrogel hybrids. Acc Chem Res. 2017;50(2):161–169.
- Mazzolai B, Tramacere F, Fiorello I, et al. The bio-engineering approach for plant investigations and growing robots. A mini-review. Front Robot AI. 2020;7:130.
- Ionov L. Soft microorigami: self-folding polymer films. Soft Matter. 2011;7(15):6786–6791.
- Fratzl P, Barth FG. Biomaterial systems for mechanosensing and actuation. Nature. 2009;462(7272):442–448.
- Laschi C, Mazzolai B, Cianchetti M. Soft robotics: technologies and systems pushing the boundaries of robot abilities. Sci Robot. 2016;1:3690.
- Cianchetti M, Laschi C, Menciassi A, et al. Biomedical applications of soft robotics. Nature Rev Mater. 2018;3(6):143–153.
- Palagi S, Fischer P. Bioinspired microrobots. Nature Rev Mater. 2018;3(6):113–124.
- Harrington MJ, Speck O, Speck T, et al. Biological archetypes for self-healing materials. In: Hager M, van der Zwaag S, Schubert U, editors. Self-healing materials. Advances in polymer science. Cham, Switzerland: Springer; 2015. p. 307–344.
- Sedo J, Saiz-Poseu J, Busque F, et al. Catechol-based biomimetic functional materials. Adv Mater. 2013;25(5):653–701.
- Wu DY, Meure S, Solomon D. Self-healing polymeric materials: a review of recent developments. Prog Polym Sci. 2008;33(5):479–522.
- Merindol R, Walther A. Materials learning from life: concepts for active, adaptive and autonomous molecular systems. Chem Soc Rev. 2017;46(18):5588–5619.
- Beygelzimer Y, Kulagin R, Fratzl P, et al. Earth’s lithosphere inspires materials design. Adv Mater. 2021;33:2005473.
- Fossen H. Structural geology. Cambridge: Cambridge University Press; 2010.
- Available from: http://myweb.facstaff.wwu.edu/~talbot/cdgeol/Localities/Switzerland.html
- Rice JR. The localization of plastic deformation. In: WT Koiter, editor. Theoretical and applied mechanics. Amsterdam: North-Holland Publishing Co; 1976. p. 207–220.
- Valiev RZ, Estrin Y, Horita Z, et al. Producing bulk ultrafine-grained materials by severe plastic deformation. JOM. 2006;58:33–39.
- Estrin Y, Vinogradov A. Extreme grain refinement by severe plastic deformation: a wealth of challenging science. Acta Mater. 2013;61:782–817.
- Nadai AL. Theory of flow and fracture of solids. New York: McGraw-Hill; 1963.
- Ziegler H. An introduction to thermomechanics. Amsterdam: Elsevier North-Holland; 1983.
- Höppel HW, May J, Göken M. Enhanced strength and ductility in ultrafine-grained aluminium produced by accumulative roll bonding. Adv Eng Mat. 2004;6:781–784.
- Bazarnik P, Bartkowska A, Romelczyk-Baishya B, et al. Superior strength of tri-layered Al-Cu-Al nano-composites processed by high-pressure torsion. J Alloys Comp. 2020;846:156380.
- Estrin Y, Beygelzimer Y, Kulagin R. Design of architectured materials based on mechanically-driven structural and compositional patterning. Adv Eng Mater. 2019;21:1900487.
- Rogachev SO, Nikulin SA, Khatkevich VM, et al. Structure formation and hardening of the hybrid material based on vanadium and zirconium alloys during high-pressure torsion. Rus Metall. 2018;4:372–376.
- Han JK, Herndon T, Jang J, et al. Synthesis of hybrid nanocrystalline alloys by mechanical bonding through high-pressure torsion. Adv Eng Mater. 2020;22:1901289.
- Beygelzimer Y, Kulagin R, Estrin Y. Severe plastic deformation as a way to produce architectured materials. In: Estrin Y, Bréchet Y, Dunlop J, et al., editors. Architectured materials in nature and engineering. Cham, Switzerland: Springer Nature; 2019. p. 231–255.
- Kulagin R, Beygelzimer Y, Bachmaier A, et al. Benefits of pattern formation by severe plastic deformation. App Mater Today. 2019;15:236–241.
- Kulagin R, Beygelzimer Y, Ivanisenko Y, et al. Instabilities of interfaces between dissimilar metals induced by high pressure torsion. Mater Lett. 2018;222:172–175.
- Pouryazdan M, Kaus BJP, Rack A, et al. Mixing instabilities during shearing of metals. Nat Commun. 2017;8:1611.
- Kulagin R, Beygelzimer Y, Ivanisenko Y, et al. Modelling of high pressure torsion using FEM. Proced Eng. 2017;207:1445–1450.
- Kulagin R, Beygelzimer Y, Ivanisenko Y, et al. High pressure torsion: from laminar flow to turbulence. IOP Conf Series Mater Sci Eng. 2017;194:012045.
- Cao Y, Wang YB, Figueiredo RB, et al. Three-dimensional shear-strain patterns induced by high-pressure torsion and their impact on hardness evolution. Acta Mater. 2011;59:3903–3914.
- Unterlass MM. Geomimetics and extreme biomimetics inspired by hydrothermal systems—what can we learn from nature for materials synthesis? Biomim. 2017;2(2):8.
- Bouaziz O. Geometrically induced strain hardening. Scr Mater. 2013;68:28–30.
- Beygelzimer Y, Estrin Y, Kulagin R. Synthesis of hybrid materials by severe plastic deformation: a new paradigm of SPD processing. Adv Eng Mater. 2015;17:1853–1861.
- Cherepanov GP. Fracture mechanics of composite materials. Moscow: Nauka; 1983. Russian.
- Fitzgerald AE, Kingsley Jr C, Umans SD. Electric machinery. New York: McGraw-Hill; 2003.
- Brechet Y, Embury JD. Architectured materials: expanding materials space. Scr Mater. 2013;68:1–3.
- Fujioka T, Horita Z. Development of high-pressure sliding process for microstructural refinement of rectangular metallic sheets. Mater Trans. 2009;50:930–933.
- Wu XL, Yang MX, Yuan FP, et al. Heterogeneous lamella structure unites ultrafine-grain strength with coarse-grain ductility. Proc Natl Acad Sci USA. 2015;112:14501–14505.
- Zhu YT, Ameyama K, Anderson PM, et al. Heterostructured materials: superior properties from hetero-zone interaction. Mater Res Lett. 2021;9:1–30.
- Zhu YT, Wu XL. Perspective on heterogeneous deformation induced (HDI) hardening and back stress. Mater Res Lett. 2019;7:393–398.
- Ma XL, Huang CX, Moering J, et al. Mechanical properties in copper/bronze laminates: role of interfaces. Acta Mat. 2016;116:43–52.
- Huang CX, Wang YF, Ma XL, et al. Interface affected zone for optimal strength and ductility in heterogeneous laminate. Mater Today. 2018;17:713–719.
- Zhou H, Huang CX, Sha XC, et al. In-situ observation of dislocation dynamics near heterostructured interfaces. Mater Res Lett. 2019;7:376–382.
- Wu XL, Jiang P, Chen L, et al. Synergetic strengthening by gradient structure. Mater Res Lett. 2014;2:185–191.
- Wu XL, Jiang P, Chen L, et al. Extraordinary strain hardening by gradient structure. Proc Natl Acad Sci USA. 2014;111:7197–7201.
- Wu XL, Zhu YT. Heterogeneous materials: a new class of materials with unprecedented mechanical properties. Mater Res Lett. 2017;5:527–532.
- Yang MX, Li RG, Jiang P, et al. Residual stress provides significant strengthening and ductility in gradient structured materials. Mater Res Lett. 2019;7:433–438.
- Beyerlein IJ, Mayeur JR, Zheng SJ, et al. Emergence of stable interfaces under extreme plastic deformation. Proc Natl Acad Sci USA. 2014;111:4386–4390.
- Nix WD. Mechanical-Properties of thin-films. Metall Trans A Phys Metall Mater Sci. 1989;20:2217–2245.
- Barnett SA, Shinn M. Plastic and elastic properties of compositionally modulated thin-films. Ann Rev Mater Sci. 1994;24:481–511.
- Anderson PM, Foecke T, Hazzledine PM. Dislocation-based deformation mechanisms in metallic nanolaminates. Mrs Bull. 1999;24:27–33.
- Schwaiger R, Kraft O. High cycle fatigue of thin silver films investigated by dynamic microbeam deflection. Scr Mater. 1999;41:823–829.
- Wang YC, Misra A, Hoagland RG. Fatigue properties of nanoscale Cu/Nb multilayers. Scripta Mater. 2006;54:1593–1598.
- Misra A. Mechanical behavior of metallic nanolaminates. In: Hannink RH, Hill AJ, editors. Nanostructure control of materials. Cambridge: Woodhead; 2006. p. 146–176.
- Carpenter JS, Misra A, Uchic MD, et al. Strain rate sensitivity and activation volume of Cu/Ni metallic multilayer thin films measured via micropillar compression. Appl Phys Lett. 2012;101:051901.
- Carpenter JS, Misra A, Anderson PM. Achieving maximum hardness in semi-coherent multilayer thin films with unequal layer thickness. Acta Mater. 2012;60:2625–2636.
- Carpenter JS, Vogel SC, LeDonne JE, et al. Bulk texture evolution of Cu-Nb nanolamellar composites during accumulative roll bonding. Acta Mater. 2012;60:1576–1586.
- Wang J, Kang K, Zhang RF, et al. Structure and property of interfaces in ARB Cu/Nb laminated composites. Jom. 2012;64:1208–1217.
- Gram MD, Carpenter JS, Payzant EA, et al. X-ray diffraction studies of forward and reverse plastic flow in nanoscale layers during thermal cycling. Mater Res Lett. 2013;1:233–243.
- Carpenter JS, Zheng SJ, Zhang RF, et al. Thermal stability of Cu-Nb nanolamellar composites fabricated via accumulative roll bonding. Philos Mag. 2013;93:718–735.
- Zheng SJ, Beyerlein IJ, Carpenter JS, et al. High-strength and thermally stable bulk nanolayered composites due to twin-induced interfaces. Nat Commun. 2013;4:1696.
- Lu K. Making strong nanomaterials ductile with gradients. Science. 2014;345:1455–1456.
- Fang TH, Li WL, Tao NR, et al. Revealing extraordinary intrinsic tensile plasticity in gradient nano-grained copper. Science. 2011;331:1587–1590.
- Chen AY, Liu JB, Wang HT, et al. Gradient twinned 304 stainless steels for high strength and high ductility. Mater Sci Eng A. 2016;667:179–188.
- Wei YJ, Li YQ, Zhu LC, et al. Evading the strength- ductility trade-off dilemma in steel through gradient hierarchical nanotwins. Nature Comm. 2014;5:1–8.
- Sawangrat C, Kato S, Orlov D, et al. Harmonic-structured copper: performance and proof of fabrication concept based on severe plastic deformation of powders. J Mater Sci. 2014;49:6579–6585.
- Zhang Z, Vajpai SK, Orlov D, et al. Improvement of mechanical properties in SUS304L steel through the control of bimodal microstructure characteristics. Mater Sci Eng A. 2014;598:106–113.
- Vajpai SK, Ota M, Watanabe T, et al. The development of high performance Ti-6Al-4V alloy via a unique microstructural design with bimodal grain size distribution. Metall Mater Trans A. 2015;46:903–914.
- Calcagnotto M, Adachi Y, Ponge D, et al. Deformation and fracture mechanisms in fine- and ultrafine-grained ferrite/martensite dual-phase steels and the effect of aging. Acta Mater. 2011;59:658–670.
- Li ZM, Pradeep KG, Deng Y, et al. Metastable high-entropy dual-phase alloys overcome the strength-ductility trade-off. Nature. 2016;534:227.
- Park K, Nishiyama M, Nakada N, et al. Effect of the martensite distribution on the strain hardening and ductile fracture behaviors in dual-phase steel. Mater Sci Eng A. 2014;604:135–141.
- Wang YM, Chen MW, Zhou FH, et al. High tensile ductility in a nanostructured metal. Nature. 2002;419:912–915.
- Han BQ, Huang JY, Zhu YT, et al. Strain rate dependence of properties of cryomilled bimodal 5083 Al alloys. Acta Mater. 2006;54:3015–3024.
- Han BQ, Lee Z, Witkin D, et al. Deformation behavior of bimodal nanostructured 5083 Al alloys. Metall Mater Trans A. 2005;36a:957–965.
- Zhao YH, Topping T, Bingert JF, et al. High tensile ductility and strength in bulk nanostructured nickel. Adv Mater. 2008;20:3028–3033.
- Wang YF, Huang CX, Li YS, et al. Dense dispersed shear bands in gradient-structured Ni. Int J Plast. 2020;124:186–198.
- Yuan FP, Yan DS, Sun JD, et al. Ductility by shear band delocalization in the nano-layer of gradient structure. Mater Res Lett. 2019;7:12–17.
- Wang YF, Huang CX, He Q, et al. Heterostructure induced dispersive shear bands in heterostructured Cu. Scr Mater. 2019;170:76–80.
- Birringer R, Gleiter H, Klein HP, et al. Nanocrystalline materials an approach to a novel solid structure with gas-like disorder. Phys Lett A. 1984;102:365–369.
- Gleiter H. Nanocrystalline materials. Prog Mater Sci. 1989;33:223–315.
- Jing J, Kramer A, Birringer R, et al. Modified atomic-strucure in a Pd-Fe-Si nanoglass – a Mössbauer study. J Non Cryst Solids. 1989;113:167–170.
- Furche F, Ahlrichs R, Weis P, et al. The structures of small gold clusters as determined by a combination of ion mobility measurements and density functional calculations. J Chem Phys. 2002;117:6982–6990.
- Schooss D, Blom MN, Parks JH, et al. The structures of Ag-55 (+) and Ag-55 (-): trapped ion electron diffraction and density functional theory. Nano Lett. 2005;10:1972–1977.
- Gruene P, Rayner DM, Redlich B, et al. Structures of neutral Au-7, Au-19 and Au-20 clusters in the gas phase. Science. 2008;321:674–676.
- Rapps T, Ahlrichs R, Waldt E, et al. On the structures of 55-atom transition-metal clusters and their relationship to the crystalline bulk. Angewandte Chemie Internat Ed. 2013;52:6102–6105.
- Chakraborty I, Pradeep T. Atomically precise clusters of noble metals: emerging link between atoms and nanoparticles. Chem Rev. 2012;117:8208–8271.
- Fuhr O, Dehnen S, Fenske D. Chalcogenide clusters of copper and silver from silylated chalcogenide sources. Chem Soc Rev. 2013;42:1871–1906.
- Neumaier M, Baksi A, Weis P, et al. Kinetics of intercluster reactions between atomically precise noble metal clusters [Ag25(DMBT)18]− and [Au25(PET)18]− in room temperature solutions. J Am Chem Soc. 2021;143:6969–6980.
- Gleiter H, Schimmel T, Hahn H. Nanostructured solids – from nanoglasses to quantum transistors. Nano Today. 2014;9:17–68.
- Ivanisenko Y, Kübel C, Nandam SH, et al. Structure and properties of nanoglasses. Adv Eng Mater. 2018;20(12):1800404.
- Ulas S, Bundschuh S, Jester SS, et al. Mechanical properties of C58 materials and their dependence on thermal treatment. Carbon N Y. 2014;68:125–137.
- Ghosh D, Ganayee MA, Som A, et al. Hierarchical assembly of atomically precise metal clusters as a luminescent strain sensor. ACS Appl Mater Interfaces. 2021;13:6496–6504.
- Fischer A, Kruk R, Hahn H. A versatile apparatus for the fine-tuned synthesis of cluster-based materials. Rev Sci Instrum. 2015;86:023304.
- Fischer A, Kruk R, Wang D, et al. Magnetic properties of iron cluster/chromium matrix nanocomposites. Beilstein J Nanotechnol. 2015;6:1158–1163.
- Gack N, Iankevich G, Benel C, et al. Magnetotransport properties of ferromagnetic nanoparticles in a semiconductor matrix studied by precise size-selective cluster ion beam deposition. Nanomaterials. 2020;10:2192.
- Benel C, Reisinger T, Kruk R, et al. Cluster-assembled nanocomposites: functional properties by design. Adv Mater. 2018;31(26):1806634.
- Benel C, Fischer A, Zimina A, et al. Controlling the structure and magnetic properties of cluster-assembled metallic glasses. Mater Horiz. 2019;6:727–732.