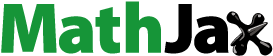
Abstract
In this study, Ti6Al7Nb alloy produced by twin-wire arc additive manufacturing was oxidized at 800°C to identify the oxidation difference induced by heat-affected bands (HABs), which have been widely reported in additive manufactured titanium alloys. The oxidation kinetics proved that HABs with compact β laths have stronger oxidation resistance compared with that of the non-HAB zone. Nb element enriched in β phase promoted Ti3Al to precipitate at the original position of β laths after oxidation, having a similar spacing to the β laths. The formation of compact Ti3Al on HAB beneficially inhibits oxygen diffusion across the oxide scale/matrix interface.
GRAPHICAL ABSTRACT
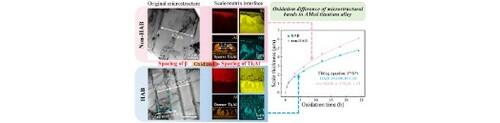
IMPACT STATEMENT
Oxidation difference induced by microstructural bands in additive manufactured titanium alloy was identified, and the stronger oxidation resistance of heat-affected bands was attributed to the more compact β laths.
Introduction
Additive manufacturing (AM) is a promising method that offers many advantages over the conventional manufacturing processes, some of which include high flexibility for complex-shaped component design, reduction in cost, and savings in materials [Citation1–3]. Significant progress has been obtained in the utilization of AM in processing titanium alloys, as their features of high raw material cost and difficulty-to-machine made them strong candidates for AM techniques [Citation4–6]. During the layer-by-layer deposition process of AM, the repeated translation of the heat source can lead to multiple heating and cooling cycles with gradually decreasing peak temperature [Citation7–9]. A unique microstructural variation will occur in the thermal cycle with a specific peak temperature and cooling rate, forming a heat-affected zone in the previously deposited titanium alloy [Citation10,Citation11]. The heat-affected zone presents a series of parallel bands known as heat-affected bands (HABs), in the etched cross-section of the additively manufactured single-track wide walls. HABs are more noticeable in wire arc additive manufacturing (WAAM) and directed laser deposition (DLD) processes due to their thicker deposition layers [Citation12,Citation13]. The existence of HABs was first reported on the Ti6Al4 V sample produced by the DLD process, and subsequent studies have focused on the formation mechanism of HABs [Citation14,Citation15]. The formation of HABs was recently determined to be by the migration of α/β phase interfaces, where the peak temperature approaches the β transition temperature [Citation16]. The mechanical properties of HABs have been examined to include higher hardness [Citation17] and efficient inhibition of fatigue crack propagation [Citation18], but little is known about the oxidation behavior of HABs. In this work, Ti6Al7Nb (Ti67) alloy produced by the WAAM process was oxidized at 800°C for up to 24 h. Oxide scales grown on HAB and non-HAB zone were characterized separately and compared in detail to determine the difference in oxidation resistance. The possible mechanism of oxidation difference was discussed in terms of elemental distribution and original microstructure.
Experimental
The Ti67 alloy was prepared by a twin-wire arc additive manufacturing technology combined with in-situ alloying as shown in Figure (a), using the same process parameters as reported in a previous study [Citation19]. The oxidation specimens with dimensions of 30 × 15 × 3 mm3 were cut from the deposited wall in the YOZ plane, then ground up to grit No. 7000 and ultrasonically cleaned in acetone before the oxidation tests. The elemental distribution of original oxidation specimens was revealed by the electron probe microanalyzer (EPMA, Shimadzu 1720H). Isothermal oxidation tests were carried out in a muffle furnace at 800°C in the air for 0.5, 1, 3, 6, 12, 18, and 24 h, respectively. The phase structure of the oxidization specimens was identified with X-ray diffraction (XRD, Bruker D8 Advance) using Cu Kα (λ=1.5418 Å) radiation. Microstructural characterization of the oxide scale was performed by scanning electron microscopy (SEM, JSM-7800F) and transmission electron microscopy (TEM, JEM-2100F) equipped with the energy dispersive spectroscope (EDS). To measure scale thickness, the cross-section of the oxidized samples was wrapped by the resin, then ground up to grit No. 7000, polished, and etched using Kroll’s reagent (1 vol.% HF, 3 vol.% HNO3, and 94 vol.% water) to distinguish HAB and non-HAB zones. The scale thickness was measured on HAB and non-HAB zones 10 times through SEM, respectively, and the average value was taken. For high-resolution characterization of the oxide scale and the oxide scale/matrix interface, focused ion beam (FIB) technology was used to prepare the TEM sample.
Results and discussion
The TEM analysis in Figure (b) proved that the Ti67 alloy was primarily composed of α matrix phase, separated by nano-scaled β laths. Periodic HABs could be observed on the etched surface of the oxidation specimen (Figure (c)), in which the average spacing of β laths was 0.87µm. In comparison, the β laths were spaced far apart in the non-HAB zone with an average spacing of 2.73 µm, as seen in Figure (d,e). The formation of compact β laths in HAB was because the secondary α heterogeneously nucleated on the residual α phase when the reheating temperature was just below the β transition temperature [Citation16,Citation19]. The chemical composition difference between HAB and the non-HAB zone was detected by EPMA mapping and the result presented in Figure (f), which revealed that the HABs are rich in Nb and Al elements. The concentrations of Nb and Al in HABs were 7.42 wt. % and 6.37 wt. %, and it reduced to 6.51 wt. % and 6.21 wt.% in the non-HAB zone, respectively. This reduction was attributed to thermally induced diffusion during the formation process of the HABs [Citation19]. It should be noted that the addition of Nb and Al as alloying elements has proven to be effective in improving the oxidation resistance of titanium alloy [Citation20–22].
Figure depicts the surface morphology, phase structure and the thickness of the oxide scale on the specimens oxidized at different time intervals. The local appearance of the specimen after being repolished to remove the etched surface and oxidized for 24 h was presented in Figure (a). The oxidation difference between the HAB and non-HAB zone was indicated by several parallel dark bands located at the site of HABs. The morphologies of the oxide scale on HAB and non-HAB zone after oxidization for 0.5, 6, and 24 h were shown in Figure (b–g). As the oxidation time increased, the oxide particles increased in size with statistics presented in Table . The oxide particles on HAB are notably smaller than those on the non-HAB areas regardless of the oxidation time. It was reported that the formation of finer oxide particles indicated greater oxidation resistance of titanium alloy [Citation23]. Thus, HAB covered by finer oxide particles had stronger oxidation resistance than the non-HAB zone.
Figure 2. Characterization of oxide scales on specimens oxidized at 800°C for different times: (a) photograph of the surface shown in Figure c after being oxidized for 24 h, (b-d) surface morphologies of HAB oxidized for 0.5 h, 6 h and 24 h, respectively, (e-g) surface morphologies of non-HAB zone oxidized for 0.5, 6, and 24 h, respectively, (h) XRD spectra of the original Ti67 alloy and the specimens oxidized for different times, and (i) oxidation kinetics of HAB and non-HAB zone.
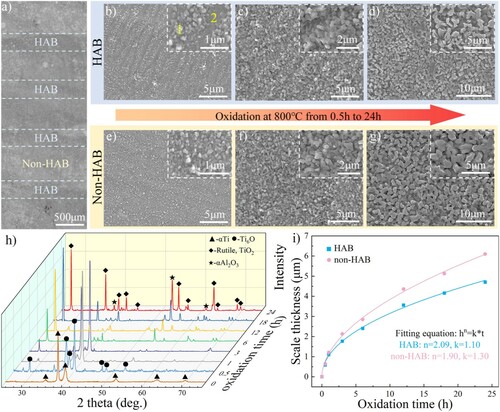
Table 1. The average particle size of the oxide at various oxidation times (unit: nm).
The oxide particles on the HAB presented a lamellar distribution after 0.5 h oxidation (Figure (b)), which might be related to the lamellar α/β microstructure of the original Ti67 alloy. High magnification of the lamellar characterization revealed a mixture of coarse oxide particles (point 1) and fine oxide particles (point 2). EDS analysis of these points presented in Table indicated that the fine particles contained more Nb and less Al than the coarse particles. The formation of lamellar oxide distribution was attributed to the preferential oxidation nucleation of α or β phase induced by the chemical composition difference [Citation24]. Since Nb is enriched in the β phase as a solid stabilizing element that can reduce the solid solubility of oxygen in the titanium alloy [Citation25], the oxide is presumed to nucleate at the α phase first, forming coarse oxide particles with lower Nb content. Subsequently, the fine oxide particles grow on the initial β phase with stronger oxidation resistance. For the non-HAB region with lamellar α/β microstructure, the distribution of oxides was uniform rather than lamellar, with coarse oxide particles covering the surface. In this phenomenon, the wide α phase between sparse β laths provides more nucleation sites for the oxide formation and promotes the rapid growth of oxide particles, resulting in uniform oxide on the non-HAB zone. When the oxidation time reaches 6 h, the lamellar oxide on HAB was covered by subsequent growing oxide particles.
Table 2. EDS analysis of the points in Figure (at. %).
Figure (h) shows the phase structure of the deposited Ti67 alloy and the oxidized surface for different holding times. The diffraction peaks of the α phase dominated the XRD pattern of the original Ti67 alloy, while the β phase was absent due to its nano-scale dimension. Ti6O was formed at the initial oxidation stage, while the weak peak of Rutile-TiO2 at 27.5° was enhanced with the extension of oxidation time. When the oxidation time was extended to 6 h, the oxide was composed mainly of TiO2, while Ti6O disappeared in the XRD pattern. The α-Al2O3 peaks were first detected at the oxidation time of 12 h and increased with increasing oxidation time. The variation of oxide thickness as a function of time was shown in Figure (i), where HAB was covered by thinner scales than the non-HAB zone at all the oxidation times. The thickness of the oxide scale remarkably decreased by 23% from 6.1µm on the non-HAB zone to 4.7µm on HAB after 24 h oxidation. To identify the law of the oxidation kinetics on HAB and non-HAB zone, the following equation was used to fit the thickness of the oxide scales:
(1)
(1) where h is the thickness of the oxidation layer (µm), n is the oxidation exponent, k is the oxidation rate constant (µmn/h) and t is the oxidation time (h). The fitting curve was plotted, and the oxidation exponents (n) of the HAB and non-HAB zone were 2.09 and 1.90, respectively. Both HAB and non-HAB zone obeyed parabolic growth kinetics (n≈2) at 800°C exposing. The oxidation rate constant (k) of the non-HAB zone was 1.30µm2/h, and it decreased to 1.10µm2/h on HAB, indicating a stronger oxidation resistance of HAB, which is consistent with the finer oxide particles developed on HAB.
The elemental distributions of the cross-sectional oxide scales on HAB and non-HAB zone evaluated by FIB-TEM were shown in Figure . The oxide scale and the titanium matrix on HAB were collected by FIB milling, but only part of the oxide scale was obtained from the non-HAB zone. The oxide scales primarily contained TiO2 as well as some Al2O3 particles, as confirmed by the elemental distribution and selected area electron diffraction (SAED) patterns. A similar multilayer structure was observed in the oxide scales on both HAB and non-HAB zone, consisting of three layers: a porous TiO2 outermost layer, a thin Al2O3/Ti2O mixture layer and a TiO2 innermost layer. TiO2 and Al2O3 were the most thermodynamically stable phases in the Ti-Al–O system [Citation26], but the TiO2 grew faster at 800°C [Citation27], thus, TiO2 occupied the largest volume in the oxide scale. TiO2 grew by consuming Ti in the matrix, leading to the formation of a Ti-poor and Al-rich zone under the TiO2 layer, which promoted the diffusion of Al through the TiO2 and reacting with oxygen to form Al2O3. The enrichment of Al also resulted in precipitation of the Ti3Al phase due to the limited solid solubility of Al in αTi (approximately 10 at. % [Citation28]). Therefore, the oxide scale/matrix interface on HAB was composed of Ti3Al with high Nb content and αTi.
Figure 3. TEM analysis of Ti67 alloy after oxidation for 24h: (a) TEM image of the oxide scale and matrix on HAB; (b) TEM image of the oxide scale on non-HAB zone; (c,d) EDS elemental mappings for the selected area in a and b and (e-h) SAED patterns of different phases.
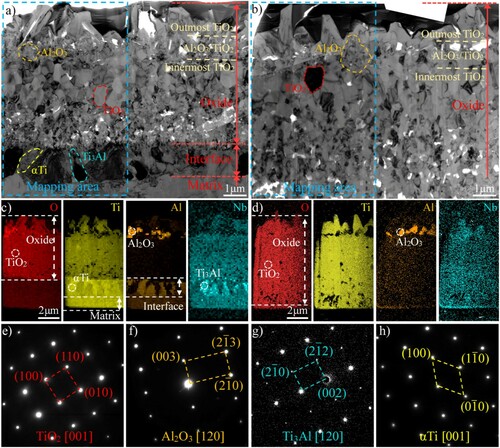
It is worth noting that Nb could be soluble in TiO2, which was beneficial to inhibit the oxygen diffusion across the already formed TiO2 layer by reducing the oxygen vacancy concentration, thereby decreasing the growth rate of TiO2 [Citation29,Citation30]. The Nb content in HAB was slightly higher than that in the non-HAB zone, which promoted the dissolving of Nb into the TiO2 and enhanced the oxidation resistance of HAB. In consequence, the average Nb content in TiO2 was 2.1 wt. % on HAB which is slightly higher than that on the non-HAB zone (1.5wt. %) through TEM-EDS. In addition to elemental content, the unique original microstructure of the HAB also contributed to the oxidation differences. To identify the effect of the original microstructure on the oxidation resistance, the oxide scale/matrix interface on non-HAB was additionally observed by FIB-TEM and presented in Figure (a), showing a complete contrast with HAB. Ti3Al with high Nb content was also found to precipitate from the αTi under the oxide scale. It has been reported that Ti3Al alloy has stronger oxidation resistance than titanium alloy [Citation31,Citation32], and increasing the volume fraction of the Ti3Al phase can also improve the oxidation resistance of the Ti-Ti3Al composite [Citation33]. Thus, the precipitation of Ti3Al phase in the scale/matrix interface was beneficial to the oxidation resistance of Ti67 alloy. The elemental content provided in Table confirmed a lower oxygen content in Ti3Al than that in αTi, indicating a stronger diffusion of oxygen in αTi. Hence, the boundary of oxides was convex to αTi. Previous investigations have concluded that more compact Ti3Al precipitation and less αTi in contact with the oxide scale were conducive to the antioxidant properties by inhibiting oxygen diffusion. The spacing of Ti3Al precipitation was about 2.7µm on the non-HAB zone while it was less than 0.9µm on HAB, so the denser Ti3Al precipitation is another factor contributing to the stronger oxidation resistance of HAB.
Figure 4. The influencing mechanism of original microstructure on oxidation resistance: (a) TEM image of the oxide scale/matrix interface on non-HAB zone after oxidation at 800°C for 24h6, (b) EDS elemental mappings for a, (c) original microstructure of HAB, (d) original microstructure of non-HAB zone and (e) schematic diagrams illustrating the Ti3Al precipitation process on HAB and non-HAB zone.
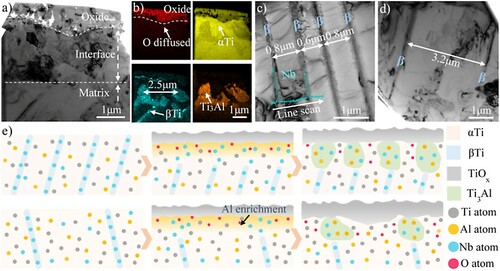
Table 3. Elemental content of Ti3Al and αTi adjacent with oxide scale in Figure (at. %).
The denser Ti3Al precipitation was considered to be related to the compact β laths in the original microstructure of HAB. The spacing of β laths in the original microstructure was about 0.7µm in Figure (c), which was close to the spacing of Ti3Al precipitation on HAB. Similarly, the spacing of the β laths (3.2µm) was close to that of Ti3Al in the non-HAB zone. A possible mechanism illustrating the approximate equivalent relationship between the spacing of β laths and Ti3Al precipitation was shown schematically in Figure (e). As confirmed by the XRD analysis, titanium firstly reacts with oxygen to form oxide in the early oxidation stages, resulting in the enrichment of Al under the oxidation layer. Meanwhile, oxygen atoms diffuse through the oxide scale into the matrix. With increasing contents of O and Al, which are α-stabilizing elements, the β→α transformation occurs in the oxide scale/matrix interface, while the Nb element rich in β remains near the original β laths due to its low diffusion coefficient. The lattice distortion caused by the Nb solution can induce Ti3Al precipitation [Citation34,Citation35]. Therefore, Ti3Al forms near the positions of original β laths and contain high Nb content, owning a similar spacing to the β laths.
Conclusion
In summary, the oxidation behavior of HAB, a region with unique microstructural variation during the multiple thermal cycles in the additive manufacturing process of titanium alloy, was firstly revealed in this study. After oxidation at 800°C for up to 24 h, finer oxide particles and thinner scales were formed on HAB, indicating stronger oxidation resistance of HAB than the non-HAB area. TiO2 was found to be the main component of the oxide scale, with a small amount of Al2O3 located under the surface of the oxide scale after 24 h oxidation. With the depletion of Ti in the matrix by TiO2, the oxide/matrix interface was enriched with Al, promoting Ti3Al to precipitate on either HAB or non-HAB zone. The stronger oxidation resistance of HAB was attributed to the slightly higher Nb content and the compact β laths in the original microstructure by promoting the denser Ti3Al precipitation, which was beneficial for inhibiting oxygen diffusion. This work provided a simple approach to improve the oxidation resistance of titanium alloy by controlling β laths spacing.
Declaration of interest statement
No potential competing interest was reported by the authors.
Disclosure statement
No potential conflict of interest was reported by the author(s).
Additional information
Funding
References
- DebRoy T, Wei HL, Zuback JS, et al. Additive manufacturing of metallic components - process, structure and properties. Prog Mater Sci. 2018;92:112–224.
- Wu B, Pan Z, Ding D, et al. A review of the wire arc additive manufacturing of metals: properties, defects and quality improvement. J Manuf Process. 2018;35:127–139.
- Oliveira JP, Santos TG, Miranda RM. Revisiting fundamental welding concepts to improve additive manufacturing: from theory to practice. Prog Mater Sci. 2020;107:100590.
- Wang J, Lin X, Wang J, et al. Grain morphology evolution and texture characterization of wire and arc additive manufactured Ti-6Al-4V. J Alloys Compd. 2018;768:97–113.
- Bermingham MJ, Kent D, Zhan H, et al. Controlling the microstructure and properties of wire arc additive manufactured Ti–6Al–4 V with trace boron additions. Acta Mater. 2015;91:289–303.
- Wang J, Pan Z, Ma Y, et al. Characterization of wire arc additively manufactured titanium aluminide functionally graded material: microstructure, mechanical properties and oxidation behaviour. Mater Sci Eng A. 2018;734(SEP.12):110–119.
- Herzog D, Seyda V, Wycisk E, et al. Additive manufacturing of metals. Acta Mater. 2016;117:371–392.
- Sames WJ, List IIIFA, Pannala S, et al. The metallurgy and processing science of metal additive manufacturing. Int Mater Rev. 2016;61:315–360.
- Wang F, Williams S, Colegrove P, et al. Microstructure and mechanical properties of wire and Arc additive manufactured Ti-6Al-4V. Metall Mater Trans A. 2013;44(2):968–977.
- Baufeld B, Brandl E, van der Biest O. Wire based additive layer manufacturing: comparison of microstructure and mechanical properties of Ti–6Al–4 V components fabricated by laser-beam deposition and shaped metal deposition. J Mater Process Technol. 2011;211(6):1146–1158.
- Åkerfeldt P, Antti M-L, Pederson R. Influence of microstructure on mechanical properties of laser metal wire-deposited Ti-6Al-4V. Mater Sci Eng A. 2016;674:428–437.
- Martina F, Colegrove PA, Williams SW, et al. Microstructure of interpass rolled wire + Arc additive manufacturing Ti-6Al-4V components. Metall Mater Trans A. 2015;46(12):6103–6118.
- Zhu Y, Tian X, Li J, et al. Microstructure evolution and layer bands of laser melting deposition Ti–6.5Al–3.5Mo–1.5Zr–0.3Si titanium alloy. J Alloys Compd. 2014;616:468–474.
- Kobryn PA, Semiatin SL. Microstructure and texture evolution during solidification processing of Ti–6Al–4 V. J Mater Process Technol. 2003;135(2):330–339.
- Kelly SM, Kampe SL. Microstructural evolution In laser-deposited multilayer Ti-6Al-4V builds: part I. microstructural characterization. Metall Mater Trans A. 2004;35(6):1861–1867.
- Ho A, Zhao H, Fellowes JW, et al. On the origin of microstructural banding In Ti-6Al4 V wire-arc based high deposition rate additive manufacturing. Acta Mater. 2019;166:306–323.
- Lin J, Guo D, Lv Y, et al. Heterogeneous microstructure evolution In Ti-6Al-4V alloy thin-wall components deposited by plasma arc additive manufacturing. Mater Des. 2018;157:200–210.
- Wang Y, Chen R, Cheng X, et al. Effects of microstructure on fatigue crack propagation behavior In a bi-modal TC11 titanium alloy fabricated via laser additive manufacturing. J Mater Process Technol. 2019;35(2):403–408.
- Yang Z, Liu Q, Wang Y, et al. Fabrication of multi-element alloys by twin wire arc additive manufacturing combined with In-situ alloying. Mater Res Lett. 2020;8(12):477–482.
- Jiang H, Hirohasi M, Lu Y, et al. Effect of Nb on the high temperature oxidation of Ti–(0–50 at. %)Al. Scr Mater. 2002;46(9):639–643.
- Lin JP, Zhao LL, Li GY, et al. Effect of Nb on oxidation behavior of high Nb containing TiAl alloys. Intermetallics. 2011;19(2):131–136.
- Dai J, Wang L, Wu X, et al. Effects of alloying elements on the stability of TiO2 and their diffusion properties studied by first principles calculations. Mater Today Commun. 2018;17:40–45.
- Guo W, Wang H, Peng P, et al. Effect of laser shock processing on oxidation resistance of laser additive manufactured Ti6Al4 V titanium alloy. Corros Sci. 2020;170:108655.
- Du W, Yao Z, Zhang S, et al. The effect of B doping on the oxidation resistance of Ti6Al4 V by EBF3. Corros Sci. 2020;173:108766.
- Xu J-Y, Shi Z-Z, Zhang Z-B, et al. Significant enhancement of high temperature oxidation resistance of pure titanium via minor addition of Nb and Si. Corros Sci. 2020;166:108430.
- Seifert HJ, Kussmaul A, Aldinger F. Phase equilibria and diffusion paths In the Ti–Al–O–N system. J Alloys Compd. 2001;317-318:19–25.
- Qu SJ, Tang SQ, Feng AH, et al. Microstructural evolution and high-temperature oxidation mechanisms of a titanium aluminide based alloy. Acta Mater. 2018;148:300–310.
- Namboodhiri TKG. On the Ti-Al phase diagram. Mater Sci Eng. 1983;57(1):21–22.
- Dai J, Zhu J, Chen C, et al. High temperature oxidation behavior and research status of modifications on improving high temperature oxidation resistance of titanium alloys and titanium aluminides: A review. J Alloys Compd. 2016;685:784–798.
- Cui Y, Aoyagi K, Koizumi Y, et al. Effect of niobium addition on tensile properties and oxidation resistance of a titanium-based alloy. Corros Sci. 2021;180:109198.
- Lui HX, Zhang XW, Jiang YH, et al. Microstructure and high temperature oxidation resistance of In-situ synthesized TiN/Ti3Al intermetallic composite coatings on Ti6Al4 V alloy by laser cladding process. J Alloys Compd. 2016;670:268–274.
- Li ZW, Gao W, Ying DY, et al. Improved oxidation resistance of Ti with a thermal sprayed Ti3Al(O)–Al2O3 composite coating. Scr Mater. 2003;48(12):1649–1653.
- Wang J, Pan ZX, Ma Y, et al. Characterization of wire arc additively manufactured titanium aluminide functionally graded material: microstructure, mechanical properties and oxidation behaviour. Mater Sci Eng A. 2018;734:110–119.
- Dear FF, Kontis P, Gault B, et al. Mechanisms of Ti3Al precipitation In hcp α-Ti. Acta Mater. 2021;212:116811.
- Bagot PAJ, Radecka A, Magyar AP, et al. The effect of oxidation on the subsurface microstructure of a Ti-6Al-4V alloy. Scr Mater. 2018;148:24–28.