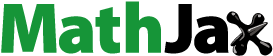
Abstract
The (FeCoNi)86Ti7Al7 multi-principal-element alloy with a dual heterogeneous microstructure was successfully fabricated by selective laser melting, exhibiting an excellent combination of strength (ultimate tensile strength, 1085.2 ± 23.2 MPa) and ductility (30.5 ± 2.6%). It is evidenced that the joint effects of the hetero-deformation induced hardening from grains with heterogeneous geometrically necessary dislocations densities, in-situ formed B2 phase, and the coherent precipitation hardening from in-situ formed nano L12 phase were responsible for the strength. This work sheds light on the feasibility of simplifying the production of multi-mechanism strengthened alloys within one step and paves a new avenue to produce high-performance complex-shaped components.
GRAPHICAL ABSTRACT
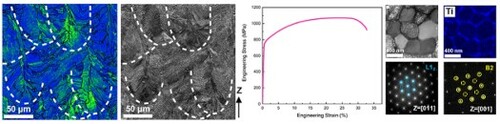
IMPACT STATEMENT
(FeCoNi)86Ti7Al7 multi-principal-element alloy exhibiting heterogeneity on the grains structure and in-situ precipitation was successfully fabricated by selective laser melting. It shows both good tensile strength and ductility.
1. Introduction
The idea of multi-principal-element alloy (MPEA) has been considered to be a breakthrough to the traditional single-principal-based alloy design strategy, and hence potentially to further extend the up-limit of strength-ductility combination [Citation1–3]. In particular, the face-centered-cubic (fcc) MPEAs often show high work-hardening capability due to the intrinsically activated multiple dislocation slip system during straining, leading to good resistance to crack propagation and the consequent descent tensile ductility [Citation2]. However, most fcc-MPEAs generally present low strength [Citation2], making strengthening fcc-MPEAs a quite hot topic.
Inducing precipitation of the L12 phase and introducing heterogeneous grain structure are both effective and widely employed strengthening methods for fcc-MPEAs. The coherent interface between the L12 phase and the fcc matrix relieves the interfacial stress concentration, significantly improving the strength without sacrificing too much ductility [Citation4–10]. While the heterogeneous grain structure can induce a gradient distribution of strain around interfaces, triggering an extra work-hardening effect [Citation11–15]. For further improvement on the mechanical performance, the precipitation hardening and heterogeneous grain structure have been simultaneously employed in MPEAs with complex processing methods that involve multi-pass rolling and annealing [Citation16–19]. During the annealing, the significant difference in the driving force provided by the heterogeneous matrix usually causes heterogeneity in the phase, morphology, and distribution of precipitates, which enables the formation of a dual heterogeneous microstructure (heterogeneous grain structure and heterogeneous precipitates) and achieves an even better strength-ductility combination [Citation16,Citation17]. However, tuning the dual heterogeneous microstructure by thermomechanical treatments is still too inconvenient for a wide industrial application. Fortunately, additive manufacturing, a recently developed fabrication route, seems to provide a possible solution to this dilemma. Additive manufacturing (AM) is a one-step near-net manufacturing method that can produce parts with complex geometry, while the complex thermal cycles during processing give rise to the tendency to form in-situ precipitation and microstructure in different degrees of heterogeneity [Citation20–23], making it a promising method to combine the precipitation and heterogeneous grain structure within one step.
In this work, by alloying a high amount of Ti and Al simultaneously, we designed an MPEA with a composition of (FeCoNi)86Ti7Al7 (at.%) that refers from the literature [Citation9] with good mechanical performance yet only after complex processing. The SLMed alloy exhibits a heterogeneous matrix, which presents grains with different geometrically necessary dislocations (GNDs) densities, and the pronounced heterogeneity on the precipitation, which relates to the B2 phase and L12 phase. This dual-heterogeneity endows the alloy with a decent combination of strength and ductility, without any in-following thermomechanical process. The strengthening mechanism was discussed in accompany with microstructure analyses.
2. Materials and methods
The pre-alloyed (FeCoNi)86Ti7Al7 (in at. %) powders were produced by gas atomization, and the particle size ranges from 8 to 45 µm with a mean value of 29.8 µm (Figure S1, Supporting information). The SLM process was conducted on a commercial machine (FS271M, Farsoon, China), with a laser power of 400 W and a scanning speed of 1200 mm/s. The beam size is 90 µm, the hatching space is 110 µm, and the layer thickness is 0.04 mm. Argon atmosphere was used to prevent oxidation during SLM. The laser was rotated 67° in-between each scanning layer. The geometry of the as-built material block was designed in dog-bone shape, with a gauge length of 9.525 mm, a width of 2 mm, and a thickness of 10 mm. The specimens for tensile tests were prepared via slicing the as-built blocks by wire-electrode. Each tensile specimen has a thickness of ∼2 mm after polishing. The density of the as-built block was measured three times by the Archimedes method.
The phase constitution of the as-built (FeCoNi)86Ti7Al7 HEA was identified by an X-ray diffractometer (XRD, Rigaku D/MAX-2250, Japan) with a Cu Kα radiation. Electron backscatter diffraction (EBSD) characterization was conducted using an SEM (Zeiss Supra 55) equipped with an EBSD Detector. Electron channeling contrast imaging (ECCI) was conducted on a scanning electron microscope (SEM, Carl Zeiss SMT AG, Germany) with a Gemini-type field emission gun electron column. Conventional TEM characterizations were performed by transmission electron microscope (TEM, JEOL-2100F, Japan) equipped with an energy dispersive spectrometer (EDS). Elemental distribution was further characterized by another TEM (Thermo Fisher Talos 200X) equipped with a super EDS.
All tensile tests were conducted at room temperature by using an Autograph AGS-X 50 kN tester with an extensometer. The test was repeated three times to ensure the reproducibility. The strain rate of conventional tensile tests is 1×10−3 s−1. The loading-unloading-reloading (LUR) tensile tests were performed at room temperature with a strain rate of 1×10−3 s−1. In each LUR cycle, the sample was first stretched to a predefined strain at a constant strain rate of 1×10−3 s −1 and then unloaded in a load-control mode to 50 N. Subsequently, the sample was stretched again at a strain rate of 1×10−3 s −1 before the next unloading.
3. Results and discussion
The bulk density is measured to be 7.718 ± 0.001 g/cm3. The low magnification SEM characterization and EDS mapping of the undeformed sample are presented in Figure S2, showing no macroscopic voids and homogeneous element distribution. Figure (a, b, d, e) present the hierarchical microstructure and heterogeneous grains morphology resulted from the layer-by-layer fabrication mode and the accompanied remelting [Citation24,Citation25]. Overlapped melt tracks are observed in Figure (f). The scanning strategy is shown in Figure (j). Slanted columnar grains (white arrows) grow perpendicular to the melt pool boundaries due to the sizeable and directional thermal gradient, while relatively finer grains (black arrow in Figure (b)) may form at regions near multiple melt pool boundaries (marked with dashed lines in Figure (c)) due to the multiple remelting and reheating brought by overlapping of melt pools [Citation26].
Figure 1. EBSD characterization of the (FeCoNi)86Ti7Al7 alloy. (a) EBSD inverse pole figure (IPF) map on XZ plane; (b) Enlarged view in (a); (c) Integrated forward scatter detector (FSD) map of (b); (d) EBSD IPF map on XY plane; (e)Enlarged view in (d); (f) Integrated forward scatter detector (FSD) map of (e); (g) KAM map corresponding to (a) (step size = 0.5 µm); (h) KAM map corresponding to (d) (step size = 0.5 µm); (i) XRD pattern of the investigated alloy; (j) Schematic diagram of the scanning strategy in SLM process.
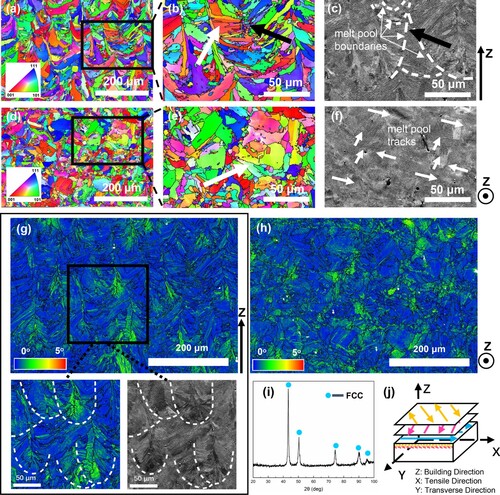
Figure (g and h) show the local misorientations on XZ plane and XY plane. Previous investigations have confirmed that the density of geometrically necessary dislocations (GND) is positively proportional to the KAM value [Citation27]: .
is the average local misorientation, b is the Burger’s vector and u is the unit length (step size used in EBSD characterization). Figure (g) exhibits an inherent heterogeneity in the local misorientations, reflecting more severe strains and higher densities of GNDs from the centre to the bottom of melt pools. The initial strain and the high densities of GNDs in materials produced by AM are ascribed to the expansion/contraction heterogeneities produced by the localized heating/cooling [Citation28]. The unstable solidification process enables uneven initial stress and strain among grains, thus GNDs are generated to coordinate the microscopic deformation and maintain the continuity [Citation29]. Furthermore, the shrinkage of the whole melt pool area will be restricted by the heat affected area beneath the melt pool, leading to even intenser strain localization, which is consistent with the phenomenon that there is higher GNDs density around grains at the bottom and centre area of melt pools [Citation28,Citation30]. It is worth noting that except for GNDs, there may also be statistically stored dislocations (SSD) in the alloy, but the distribution of SSDs cannot be displayed via KAM map since they have no cumulative effect on the local misorientation [Citation31,Citation32]. Most of SSDs may be annihilated under cyclic heating, and GNDs may be dominant in the remaining dislocations, so more attention is paid to the GNDs. The XRD pattern in Figure (i) shows a single fcc crystalline structure, yet no additional peaks can be identified for other phases.
Figure (a, b, e, f) present that all grains are composed of fully-developed sub-grain cellular structures or columnar structures (Figure (f)), respectively. According to the references [Citation33–36], the cellular structures are columnar structures that are displayed cross-sectionally. To facilitate discussion, both of them are denoted as ‘cellular structures’ hereafter. Figure (b–d) present the obvious discrepancy in the size of cellular structures and inter-cellular precipitates from region to region. Moreover, the size of inter-cellular precipitates shows a positive dependent relationship with the size of cellular structures. Figure (g-h) exhibit more details about precipitates. High-density dislocations are observed around the inter-cellular precipitates as well as to lie along the cellular boundaries as shown in Figure (h).
Figure 2. SEM (a-d) and ECC images (e-h) of the XY plane of the investigated alloy: (a), (e) Grains composed of cellular structures; (b), (c), and (d) cellular substructures in different sizes; (f) Cellular structures exhibited in columnar morphology; (g) Precipitates distributed along cellular structures boundaries; (h) A close-up on precipitates with dislocations around.
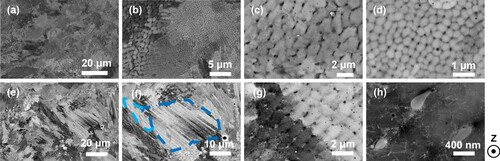
To further uncover the constituent phase structure, TEM characterizations were carried out. The failure to characterize precipitates in XRD pattern may be probably due to the small amount (volume fraction of 3.6%) of the inter-cellular precipitates, slightly below the detectable limit of the XRD technique. Figure (d), the selected area electron diffraction (SAED) pattern of the circled area in Figure (a), reveals that the inter-cellular precipitate is a B2 phase, which is frequently observed in the other Al/Ti containing MPEAs [Citation37–39]. Figure (c) shows the columnar structures, which is the cellular structure exhibited in another view. The inter-cellular B2 precipitate corresponding to Figure (c–d, g–h) are observed along the boundaries as circles indicate, and there are tangled high-density dislocations around the cellular structure boundaries. Figure (e), the SAED pattern of the circled area in Figure (b) also shows that the matrix is an fcc structure. Interestingly, the appearance of the ordered superlattice that marked by the dash lined circles indicates the formation of the L12 precipitates. Figure (f) shows that the L12 precipitates are pretty small, mostly below 5 nm, consistent with the weak superlattice spots. Figure (g) reveals that there are Ti segregation and Fe depletion along the cellular structure boundaries.
Figure 3. (a, b) Bright-field image of the investigated alloy; (c) Bright-field image of cell substructures decorated with dislocations and B2 precipitates along boundaries; (d, e) SAED patterns corresponding to the circled areas in (a) and (b), respectively; (f) Dark-field image of the L12 precipitate inside; (g) Bright-field image and TEM-EDS mapping of cellular structures.
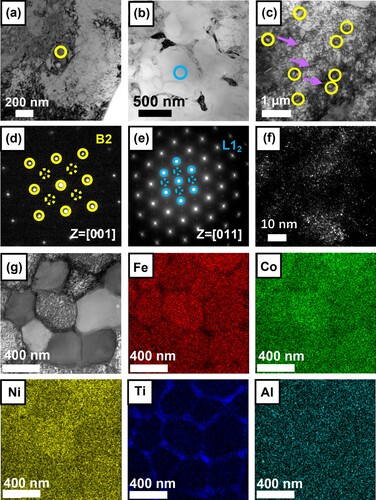
In summary, the SLMed (FeCoNi)86Ti7Al7 alloy displays a dual heterogeneous microstructure both in the matrix and the precipitates. The matrix containing grains in different morphologies exhibits an inherent GNDs variation from region to region. The precipitates include the B2 phase in size ranging from tens to hundreds of nanometers distributing along cellular structure boundaries, and L12 in size below 5 nm inside cellular structures.
The remelting and reheating fabrication mode brings about the variation of the solidification rate and cooling rate, plays a similar effect of aging, subsequently inducing the heterogeneous precipitation of the B2 phase and L12 phase. As Figure S3 and Table S1 and Table S2 show, the matrix where the size of cellular structures are finer contains more Ti and Al, and the inter-cellular precipitates also exhibit finer size and lower content of Ti and Al. This local composition difference may also result from the remelting and varied cooling rate, which also enhances the heterogeneity of microstructure. As the substitutional solute, Ti atoms tend to move to the loosely packed region like the cellular structure boundaries due to its relatively larger size [Citation40]. The high Ti/Al ratio along cellular structure boundaries promotes the formation of the B2 phase, while the L12 phase precipitates inside the cellular where there is a lower Ti/Al ratio [Citation41]. Since the interface between the B2 phase and the fcc matrix is incoherent [Citation42], the inter-cellular boundaries, which are kind of defects, can act as an excellent position for precipitation to lower the lattice distortion.
As for the cellular structures, the formation mechanism is still incompletely revealed. Previous studies have ascribed it to the cellular solidification accompanied by solutes redistribution or segregation induced by constitutional supercooling and vertex inside melt pool [Citation43]. The local composition variations among cellular structures in different sizes in the SLMed (FeCoNi)86Ti7Al7 alloy indicates that redistribution of solutes does happen while the formation of cellular structures. The addition of Ti and Al may facilitate the constitutional supercooling and furtherly promote cellular solidification. But how solute segregation interacts with the inherent dislocations, and whether it is one of the origins of dislocations are still questions. It has been verified that there still is a high density of dislocations and cellular structures inside additive manufactured pure Cu [Citation28]. So the microscopic compression-tension brought by the periodic heating and cooling is regarded as one of the origins of dislocations [Citation28,Citation44,Citation45], which also agrees with the GNDs distribution here. Moreover, Ti-6Al-4V, which exhibits inherent weak elemental segregation and fast phase transition, shows no cellular structures even with a large density of dislocations inside when fabricated via additive manufacturing [Citation44]. This phenomenon indicates that the elemental composition and crystal structure have an effect on the formation of cellular structure since they influence the solidification microstructure and the intrinsic moving behavior of dislocations.
Figure (a) shows the representative tensile curves of the as-built (FeCoNi)86Ti7Al7 alloy tested at room temperature. The alloy shows a yield strength (YS) of 773.4 ± 18.1 MPa, an ultimate tensile strength (UTS) of 1085.2 ± 23.2 MPa, a uniform elongation (UE) of 24.0 ± 1.6%, and a total elongation to fracture (TE) of 30.5 ± 2.6%. The corresponding true stress-true strain curve and strain-hardening rate curve reveal that our present alloy can keep enough strain-hardening rate to avoid the plastic instability even when the true strain exceeds 20%, as shown in Figure (b). Figure (c-d) is a comparison of our present alloy with other excellent SLMed MPEAs [Citation21–23,Citation27,Citation29,Citation34,Citation36,Citation46–56], showing the superiority in the combination of strength and ductility. It is worth noting that the size of tensile test samples may affect the mechanical properties [Citation57].
Figure 4. (a) Representative tensile curve of SLMed (FeCoNi)86Ti7Al7 alloy; (b) The true stress-true strain curve and strain-hardening rate curve corresponding to (a); (c and d) Comparisons of the tensile properties of our present alloy with other excellent SLMed MPEAs; (e) LUR true stress-strain curve; (f) Evolution of σHDI and σeff with increasing true strain.
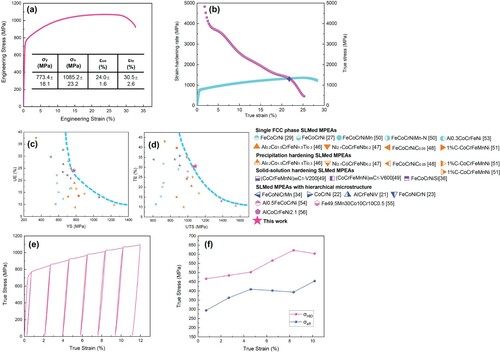
LUR test was also carried out, as shown in Figure (e). The distinct occurrence of hysteresis loops indicates a strong Bauschinger effect [Citation11]. The flow stress of the alloy at a specific strain can be divided into the HDI stress () and the effective stress (
) [Citation58], both showing a growing trend with the increasing strain, as Figure (f) exhibited.
Since the higher KAM value indicates a higher density of geometrically necessary dislocations (GNDs) and a severer strain, the regions with higher GNDs density may have experienced stronger work hardening compared with the regions with lower GNDs density. The region with a higher KAM value shows higher Vickers hardness as the nanoindentation results presented in Figure S5 and Table 3. Hence, the region with higher GNDs density are hard domains, regions with lower GNDs density are soft domains. The strain incapability between soft and hard domains can bring out the HDI hardening.
Figure presents the EBSD IPF maps, KAM maps, and FSD maps of microstructures on the XZ plane before and after the tensile test. Microstructures after deformation are picked at regions 5, 3, and 1 mm away from the fracture to represent microstructure with different degrees of strain, which is illustrated in Figure (o). As Figure (a-c) show, in undeformed microstructure, the grains at the bottom area or centre area of melt pools show evident higher misorientations, which is consistent with Figure (g). In the region 5 mm away from the fracture (Figure (d-f)), the KAM concentration phenomenon becomes less obvious, indicating that soft regions (regions with less initial GNDs) start to deform first at the initial stage of deformation. In the region 3 mm away from the fracture (Figure (g-i)), the KAM concentration phenomenon was enhanced. The grains near the centre and bottom of melt pools show even stronger local misorientations, indicating that when the strain increases, the hard domain is also activated. Finally, the region 1 mm away from the fracture (Figure (j-l)) shows much severer orientations changes compared to the initial state, suggesting the severe deformation near the fracture.
Figure 5. EBSD IPF map, KAM map, and FSD map of microstructure on XZ plane (step size µ = 0.1 µm): (a–c) undeformed area; (d–f) 5 mm from the fracture; (g–i) 3 mm from the fracture; (j–l) 1 mm from the fracture; (m–n) SEM images showing the fractographic features of the investigated HEAs; (o) Illustration of the regions picked for the characterization.
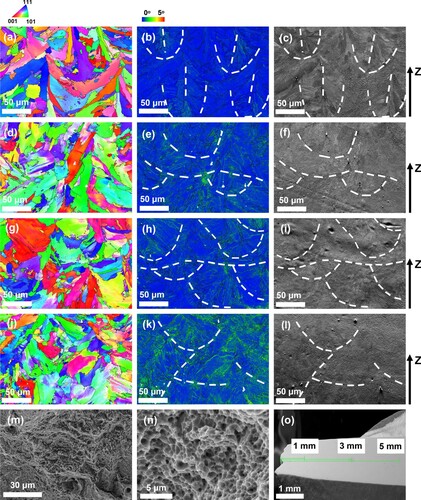
At the initial deforming stage, soft domain is firstly activated. To maintain the strain continuity, GNDs would be generated and pile up near the interface between soft and hard domains. The accumulated GNDs produce the long-range internal stress that reduces the applied effective resolved shear stress for dislocation slip [Citation58], leading to an increase of the yield strength. As the deformation proceeding, GNDs keep accumulating, thus provide a persistent long-range internal stress and the subsequent high strain hardening, stabilizing the plastic deformation and leading to good ductility [Citation11,Citation59,Citation60]. Pronounced dimples can be observed at the fracture surface as Figure (m and n) show, exhibiting a ductile fracture.
The is the directional long-range internal stress provided by the pile-up and accumulation of GNDs against barriers including dislocation walls, dislocation cells, grain boundaries, and incoherent interfaces. The
is usually attributed to the interaction between the moving dislocations, pre-existed dislocation forest, and coherent precipitates [Citation16]. As the interface between B2 precipitates and the matrix is incoherent [Citation42], dislocations pile up at the interface, or bow out and leave dislocation loops when passing [Citation61,Citation62]. B2 precipitates, and the following piled dislocations, and dislocation loops actually also provide long-range internal stress [Citation18,Citation63], playing the same reducing effect on the applied effective resolved shear stress for dislocation slip as which the GNDs accumulation induced by heterogeneous deformation provides. Thus, the strengthening contribution from B2 precipitates is also part of the HDI hardening [Citation64]. In contrast, due to the small size of L12 particles and low misfit between the L12 particles and the matrix, dislocations can shear the L12 particles during the deformation [Citation5]. Therefore, the interaction between moving dislocations and the L12 phase contributes to effective stress.
The strengthening contribution from HDI hardening, solid-solution hardening, and precipitation hardening are calculated to be around 466.7, 33.4, and 170.1 MPa, respectively (detailed calculations are presented in Supplementary information). The calculation values indicate the HDI hardening makes the most contribution, suggesting the superiority of the dual heterogeneous structure.
4. Conclusion
In this study, the (FeCoNi)86Ti7Al7 alloy accompanied by a dual-heterogeneous microstructure was successfully fabricated through a selective laser melting process. It exhibits a good combination of both the strength and ductility. The excellent mechanical properties result from the HDI hardening and precipitation hardening. Introducing the dual-heterogeneous microstructure via selective laser melting sheds light on the feasibility of simplifying the production of dual heterogeneous microstructure, and the capability to produce high-performance complex-shaped components within one step.
Supplemental Material
Download MS Word (4.9 MB)Disclosure statement
No potential conflict of interest was reported by the author(s).
Data availability
The raw/processed data required to reproduce these findings cannot be shared at this time as the data also forms part of other ongoing studies.
Additional information
Funding
References
- Yeh JW, Chen SK, Lin SJ, et al. Nanostructured high-entropy alloys with multiple principal elements: Novel alloy design concepts and outcomes. Adv Eng Mater. 2004;6:299–303.
- Wu Z, Bei H, Pharr GM, et al. Temperature dependence of the mechanical properties of equiatomic solid solution alloys with face-centered cubic crystal structures. Acta Mater. 2014;81:428–441.
- Liu WH, Lu ZP, He JY, et al. Ductile CoCrFeNiMox high entropy alloys strengthened by hard intermetallic phases. Acta Mater. 2016;116:332–342.
- Zhao YL, Yang T, Tong Y, et al. Heterogeneous precipitation behavior and stacking-fault-mediated deformation in a CoCrNi-based medium-entropy alloy. Acta Mater. 2017;138:72–82.
- Zhao YY, Chen HW, Lu ZP, et al. Thermal stability and coarsening of coherent particles in a precipitation-hardened (NiCoFeCr)(94)Ti2Al4 high-entropy alloy. Acta Mater. 2018;147:184–194.
- Fan L, Yang T, Luan JH, et al. Control of discontinuous and continuous precipitation of γ'-strengthened high -entropy alloys through nanoscale Nb segregation and partitioning. J Alloys Compd. 2020;832:154903.
- He JY, Wang H, Huang HL, et al. A precipitation-hardened high-entropy alloy with outstanding tensile properties. Acta Mater. 2016;102:187–196.
- He JY, Wang H, Wu Y, et al. Precipitation behavior and its effects on tensile properties of FeCoNiCr high-entropy alloys. Intermetallics. 2016;79:41–52.
- Yang T, Zhao YL, Tong Y, et al. Multicomponent intermetallic nanoparticles and superb mechanical behaviors of complex alloys. Science. 2018;362:933–937.
- Lu W, Luo X, Yang Y, et al. Heterogeneous precipitates facilitate excellent mechanical properties in non-equiatomic medium-entropy alloy. Intermetallics. 2021;129:107036.
- Wu X, Yang M, Yuan F, et al. Heterogeneous lamella structure unites ultrafine-grain strength with coarse-grain ductility. P Natl Acad Sci USA. 2015;112:14501–14505.
- Yang M, Yan D, Yuan F, et al. Dynamically reinforced heterogeneous grain structure prolongs ductility in a medium-entropy alloy with gigapascal yield strength. P Natl Acad Sci USA. 2018;115:7224–7229.
- Wu SW, Wang G, Wang Q, et al. Enhancement of strength-ductility trade-off in a high-entropy alloy through a heterogeneous structure. Acta Mater. 2019;165:444–458.
- Yin F, Hu S, Xu R, et al. Ultrastrong medium entropy alloy with simultaneous strength-ductility improvement via heterogeneous nanocrystalline structures. Mater Sci Eng A. 2021;823:141631.
- Zheng XY, Xie WB, Zeng LF, et al. Achieving high strength and ductility in a heterogeneous-grain-structured CrCoNi alloy processed by cryorolling and subsequent short-annealing. Mater Sci Eng A. 2021;821:141610.
- Li W, Chou T-H, Yang T, et al. Design of ultrastrong but ductile medium-entropy alloy with controlled precipitations and heterogeneous grain structures. Appl Mater Today. 2021;23:101037.
- Du XH, Li WP, Chang HT, et al. Dual heterogeneous structures lead to ultrahigh strength and uniform ductility in a Co-Cr-Ni medium-entropy alloy. Nature Comm. 2020;11:2390.
- Shukla S, Choudhuri D, Wang T, et al. Hierarchical features infused heterogeneous grain structure for extraordinary strength-ductility synergy. Mater Res Lett. 2018;6:676–682.
- Sathiyamoorthi P, Asghari-Rad P, Park JM, et al. Exceptional cryogenic strength-ductility synergy in Al0.3CoCrNi medium-entropy alloy through heterogeneous grain structure and nano-scale precipitates. Mat Sci Eng A. 2019;766:138372.
- Wang Z, Lin X, Kang N, et al. Strength-ductility synergy of selective laser melted Al-Mg-Sc-Zr alloy with a heterogeneous grain structure. Addit Manuf. 2020;34:101260.
- Yao H, Tan Z, He D, et al. High strength and ductility AlCrFeNiV high entropy alloy with hierarchically heterogeneous microstructure prepared by selective laser melting. J Alloys Compd. 2020;813:152196.
- Han B, Zhang C, Feng K, et al. Additively manufactured high strength and ductility CrCoNi medium entropy alloy with hierarchical microstructure. Mat Sci Eng A. 2021;820:141545.
- Song M, Zhou R, Gu J, et al. Nitrogen induced heterogeneous structures overcome strength -ductility trade-off in an additively manufactured high-entropy alloy. Appl Mater Today. 2020;18:100498.
- Akram J, Chalavadi P, Pal D, et al. Understanding grain evolution in additive manufacturing through modeling. Addit Manuf. 2018;21:255–268.
- Sunny S, Gleason G, Mathews R, et al. Simulation of laser impact welding for dissimilar additively manufactured foils considering influence of inhomogeneous microstructure. Mater Design. 2021;198:109372.
- Xiong ZH, Liu SL, Li SF, et al. Role of melt pool boundary condition in determining the mechanical properties of selective laser melting AlSi10Mg alloy. Mater Sci Eng A. 2019;740:148–156.
- Lin D, Xu L, Han Y, et al. Structure and mechanical properties of a FeCoCrNi high-entropy alloy fabricated via selective laser melting. Intermetallics. 2020;127:106963.
- Wang G, Ouyang H, Fan C, et al. The origin of high-density dislocations in additively manufactured metals. Mater Res Lett. 2020;8:283–290.
- Lin D, Xu L, Jing H, et al. Effects of annealing on the structure and mechanical properties of FeCoCrNi high-entropy alloy fabricated via selective laser melting. Addit Manuf. 2020;32:101058.
- Mirkoohi E, Dobbs JR, Liang SY. Analytical mechanics modeling of in-process thermal stress distribution in metal additive manufacturing. J Manuf Process. 2020;58:41–54.
- Moussa C, Bernacki M, Besnard R, et al. About quantitative EBSD analysis of deformation and recovery substructures in pure Tantalum; proceedings of the 36th Riso International Symposium on Materials Science, Riso, DENMARK, F 2015 Sep 07-11, 2015.
- Betanda YA, Helbert A-L, Brisset F, et al. Measurement of stored energy in Fe–48%Ni alloys strongly cold-rolled using three approaches: Neutron diffraction, Dillamore and KAM approaches. Mater Sci Eng A. 2014;614:193–198.
- Brif Y, Thomas M, Todd I. The use of high-entropy alloys in additive manufacturing. Scripta Mater. 2015;99:93–96.
- Zhu ZG, Nguyen QB, Ng FL, et al. Hierarchical microstructure and strengthening mechanisms of a CoCrFeNiMn high entropy alloy additively manufactured by selective laser melting. Scripta Mater. 2018;154:20–24.
- Nartu MSKKY, Jagetia A, Chaudhary V, et al. Magnetic and mechanical properties of an additively manufactured equiatomic CoFeNi complex concentrated alloy. Scripta Mater. 2020;187:30–36.
- Lin D, Xu L, Li X, et al. A Si-containing FeCoCrNi high-entropy alloy with high strength and ductility synthesized in situ via selective laser melting. Addit Manuf. 2020;35:101340.
- Tang Z, Gao MC, Diao H, et al. Aluminum alloying effects on lattice types, microstructures, and mechanical behavior of high-entropy alloys systems. Jom. 2013;65:1848–1858.
- Choudhuri D, Alam T, Borkar T, et al. Formation of a huesler-like L21 phase in a CoCrCuFeNiAlTi high-entropy alloy. Scripta Mater. 2015;100:36–39.
- Li RD, Niu PD, Yuan TC, et al. Selective laser melting of an equiatomic CoCrFeMnNi high-entropy alloy: processability, non-equilibrium microstructure and mechanical property. J Alloys Compd. 2018;746:125–134.
- Yang T, Zhao YL, Fan L, et al. Control of nanoscale precipitation and elimination of intermediate-temperature embrittlement in multicomponent high-entropy alloys. Acta Mater. 2020;189:47–59.
- Chen D, He F, Han B, et al. Synergistic effect of Ti and Al on L1(2)-phase design in CoCrFeNi-based high entropy alloys. Intermetallics. 2019;110:106476.
- Li Z, Fu L, Peng J, et al. Improving mechanical properties of an FCC high-entropy alloy by γ' and B2 precipitates strengthening. Mater Charact. 2020;159:109989.
- Asta M, Beckermann C, Karma A, et al. Solidification microstructures and solid-state parallels: recent developments, future directions. Acta Mater. 2009;57:941–971.
- Murr LE, Esquivel EV, Quinones SA, et al. Microstructures and mechanical properties of electron beam-rapid manufactured Ti-6Al-4V biomedical prototypes compared to wrought Ti-6Al-4V. Mater Charact. 2009;60:96–105.
- Bertsch KM, de Bellefon GM, Kuehl B, et al. Origin of dislocation structures in an additively manufactured austenitic stainless steel 316L. Acta Mater. 2020;199:19–33.
- Lin WC, Chang YJ, Hsu TH, et al. Microstructure and tensile property of a precipitation strengthened high entropy alloy processed by selective laser melting and post heat treatment. Addit Manuf. 2020;36:101601.
- Zhou KX, Wang ZJ, He F, et al. A precipitation-strengthened high-entropy alloy for additive manufacturing. Addit Manuf. 2020;35(12):101410.
- Zhou R, Liu Y, Liu B, et al. Precipitation behavior of selective laser melted FeCoCrNiC0.05 high entropy alloy. Intermetallics. 2019;106:20–25.
- Park JM, Choe J, Kim JG, et al. Superior tensile properties of 1%C-CoCrFeMnNi high-entropy alloy additively manufactured by selective laser melting. Mater Res Lett. 2020;8:1–7.
- Zhao DD, Yang Q, Wang DW, et al. Ordered nitrogen complexes overcoming strength-ductility trade-off in an additively manufactured high-entropy alloy. Virtual Phys Prototy. 2020;15:532–542.
- Park JM, Kim ES, Kwon H, et al. Effect of heat treatment on microstructural heterogeneity and mechanical properties of 1%C-CoCrFeMnNi alloy fabricated by selective laser melting. Addit Manuf. 2021;47:102283.
- Park JM, Choe J, Park HK, et al. Synergetic strengthening of additively manufactured (CoCrFeMnNi)(99)C-1 high-entropy alloy by heterogeneous anisotropic microstructure. Addit Manuf. 2020;35:101333.
- Peyrouzet F, Hachet D, Soulas R, et al. Selective laser melting of Al0.3CoCrFeNi high-entropy alloy: printability, microstructure, and mechanical properties. Jom. 2019;71:3443–3451.
- Zhou PF, Xiao DH, Wu Z, et al. Al0.5FeCoCrNi high entropy alloy prepared by selective laser melting with gas-atomized pre-alloy powders. Mat Sci Eng A. 2019;739:86–89.
- Zhu ZG, An XH, Lu WJ, et al. Selective laser melting enabling the hierarchically heterogeneous microstructure and excellent mechanical properties in an interstitial solute strengthened high entropy alloy. Mater Res Lett. 2019;7:453–459.
- Wang S, Li Y, Zhang D, et al. Microstructure and mechanical properties of high strength AlCoCrFeNi2.1 eutectic high entropy alloy prepared by selective laser melting (SLM). Mater Lett. 2022;310:131511.
- Wang P, Goh MH, Li Q, et al. Effect of defects and specimen size with rectangular cross-section on the tensile properties of additively manufactured components. Virtual Phys Prototy. 2020;15:251–264.
- Feaugas X. On the origin of the tensile flow stress in the stainless steel AISI 316L at 300 K: Back stress and effective stress. Acta Mater. 1999;47:3617–3632.
- Yang MX, Pan Y, Yuan FP, et al. Back stress strengthening and strain hardening in gradient structure. Mater Res Lett. 2016;4:145–151.
- Gao HJ, Huang YG. Geometrically necessary dislocation and size-dependent plasticity. Scripta Mater. 2003;48:113–118.
- Kim SH, Kim H, Kim NJ. Brittle intermetallic compound makes ultrastrong low-density steel with large ductility. Nature. 2015;518:77–79.
- Song HJ, Yoo J, Kim SH, et al. Novel ultra-high-strength Cu-containing medium-Mn duplex lightweight steels. Acta Mater. 2017;135:215–225.
- Kies F, Wu XX, Hallstedt B, et al. Enhanced precipitation strengthening of multi-principal element alloys by kappa- and B2-phases. Mater Design. 2021;198:109315.
- Liu XL, Xue QQ, Wang W, et al. Back-stress-induced strengthening and strain hardening in dual-phase steel. Materialia. 2019;7:100376.