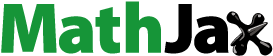
Abstract
The achievement of fine equiaxed β grain with conventional intragranular (α-Ti+β-Ti) microstructure in additive manufacturing titanium alloy remains a big challenge. We conquer this challenge by synergistically controlling β-grains during both solidification and subsequent thermal-cycles of laser directed energy deposition (DED), and a solution + quenching heat-treatment. Both the strength and plasticity of heat-treated Ti6Al4V3Ni0.05B are superior to those reported new DED titanium alloy and comparable to that of DED Ti6Al4V, because of the fine-equiaxed β-grains with intragranular (α-Ti+β-Ti) microstructure. These findings provide new insight into the grain structure control and the composition design of AM titanium alloy.
GRAPHICAL ABSTRACT
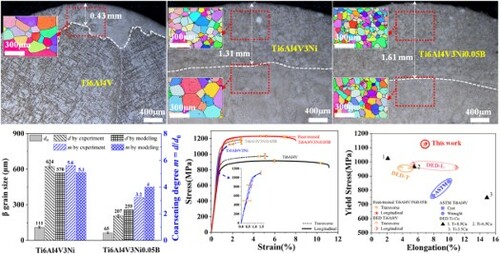
IMPACT STATEMENT
The synergetic control of β-grain during both solidification and subsequent thermal-cycling is essential for achieving fully-equiaxed fine β-grains in additively manufactured titanium alloys.
1. Introduction
Additive manufacturing (AM) is a revolutionary technology that offers a promising approach for the near-net shape and flexible design of components [Citation1–4]. Titanium-based alloys are one of the most mature alloys for the application in AM processing [Citation5–8]. However, the intrinsic high cooling rates and high thermal gradients in AM often produce coarse columnar β-grains and continuous grain-boundary α-phases up to several centimeters long, along the deposition direction in titanium alloy, resulting in a pronounced anisotropy in mechanical properties [Citation9,Citation10] and poor low-cycle fatigue properties [Citation11–15]. Therefore, the achievement of equiaxed fine β-grains is imperative for fabricating high-quality AM titanium alloy parts.
Generally, it is believed that the equiaxed fine β-grains in AM titanium alloy are more easily obtained under large constitutional-supercooling (CS) because it can not only facilitate the columnar to equiaxed transition (CET), but restrict the grain-growth during solidification [Citation16–18]. In addition, the development rate of a CS zone is proportional to the value of growth restriction factor Q (=Qn*c0) [Citation19,Citation20]. Thus, the elements with a large normalized growth restriction factor (Qn) in Ti, such as B [Citation21–23] and Si [Citation24], were preferentially selected as the alloying elements in AM Ti or titanium alloy. Researches have showed that these elements are highly-effective in refining the β-grains by restricting the grain-growth during solidification, but they fail to produce fully-equiaxed β-grains due to the limited maximum-solubility c0-max in Ti does not provide sufficient CS to promote nucleation. To solve this problem, the fast-eutectoid element Cu and Ni, with a large c0-max and medium Qn were added to Ti and Ti6Al4V, and the fully-equiaxed fine β-grains were achieved under relative low deposition efficiency (˂2 g/min) fabricated by laser directed energy deposition (DED) [Citation6,Citation25]. Nevertheless, the eutectoid phase is harmful to the ductility of Ti alloys, thus, the addition amount of the fast-eutectoid element must be deliberated. Apparently, achieving the equiaxed fine grains with (α+β) two-phase microstructure under traditional deposition efficiency (6–12 g/min) in AM titanium alloys is still challenging.
In fact, the final β-grain structure in the as-built AM titanium alloy depends not only on the grain nucleation and growth during solidification but also on the grain-coarsening during subsequent thermal-cycles. Regrettably, most studies have focused on the former to control β-grains, while very little attention has been paid to the latter. Recently, our research [Citation26] has proved that the β-grains can be coarsened by 3–9 times under single instantaneous high-temperature thermal-cycles (<1 s) during DED titanium alloy. Undisputedly, such coarsening also must be inhibited for refining β-grains. Therefore, a synergetic control of grain structure during both solidification and subsequent thermal-cycling is essential for achieving equiaxed fine β-grains in AM titanium alloy.
To this end, alloy-composition modification probably is an effective solution. The fast-eutectoid element Ni and B were selected as the alloying elements, based on the following facts: (i) Ni has a large c0-max in Ti and a larger Qn than Cu [Citation27]; (ii) B has the second-largest Qn in Ti; and (iii) B can inhibit the grain-boundary migration in titanium alloys during conventional heat-treatment. On the one hand, the co-addition of Ni and B in titanium alloy can reduce the amount of Ni addition alone for controlling β-grains during solidification; on the other hand, B could also probably limit the grain-coarsening during subsequent thermal-cycles of DED.
Thereby, the low-content Ni and trace B were chosen as the alloying elements in DED Ti6Al4V to synergistically control the β-grain structure during both solidification and subsequent thermal-cycles. The morphology and size of the β-grains in DED Ti6Al4VxNiyB after solidification and subsequent thermal-cycling were respectively investigated by combining experimental observations with finite element thermal simulation. Also, the tensile properties and their anisotropy were analyzed.
2. Experimental details
The pre-alloyed Ti6Al4V, Ni spherical-powder (diameter: 80∼150 µm) and B powder (diameter: 1 µm) were mixed with the nominal compositions of Ti6Al4V3Ni and Ti6Al4V3Ni0.05B (wt%) by a planetary ball milling. A series of single-walls (110 × 6 × 110 mm3) were deposited on the forged Ti6Al4V substrates using a reciprocating scanning strategy.
Details of the DED equipment was described in [Citation21]. The processing parameters are shown in Table .
Table 1. Processing parameters for DED.
The β-reconstructed electron-backscattered-diffraction maps (area: 800 × 600 µm2, step size: 1.4 µm, acceleration voltage: 20KV, working distances:21 mm) and optical microscope maps were used to measure the β-grain size at the top and middle of the deposits, respectively.
Details about obtaining the β-grain coarsening parameters in Ti6Al4V3Ni-xB and the thermal simulation were described in Supplementary Materials.
The heat treatment for Ti6Al4V3Ni0.05B deposit is 990°C for 15 min followed by water quenching.
Two types of room-temperature tensile samples parallel (longitudinal) and perpendicular (transverse) to the deposition direction with a gage dimension of 24 × 6 × 2 mm3 were machined from the middle of each single-wall deposit and were tested with a constant crosshead displacement rate of 1 mm/min using an Instron-3382 machine.
3. Results and discussion
The last-layer at the top of the deposit exhibits the solidification microstructure without experiencing any thermal-cycling. The β-grains at the top of the Ti6Al4VxNiyB deposits and the schematic diagrams of their formation mechanism are shown in Figure . In the last layer, the as-built microstructure in Ti6Al4V consists of the columnar and equiaxed β-grains, while the microstructures are fully-equiaxed β-grains in both Ti6Al4V3Ni and Ti6Al4V3Ni0.05B. The thickness of the top equiaxed fine-grain zone in three samples is 0.43, 1.31 and 1.61 mm, respectively. Compared with Ti6Al4V, the average size d0 of the equiaxed fine-grains in the last-layer in Ti6Al4V3Ni and Ti6Al4V3Ni0.05B is decreased by 48% and 69% down to 111 and 65 µm, respectively. Compared with Ti6Al4V3Ni, Ti6Al4V3Ni0.05B obtains a larger zone containing finer equiaxed-grains.
Figure 1. The β-grains at the top of Ti6Al4VxNiyB and the initial solidification mechanism of the last layer. (a), (d) Ti6Al4V; (b), (e) Ti6Al4V3Ni; (c), (f) Ti6Al4V3Ni0.05B; (g) grain size d0 plotted against the inverse Q. (The dashed white lines in a-c separate the equiaxed grains obtained only by solidification from the ones subjected to subsequent thermal-cycling. TE is the equilibrium liquidus temperature and ΔTn is the critical undercooling for nucleation).
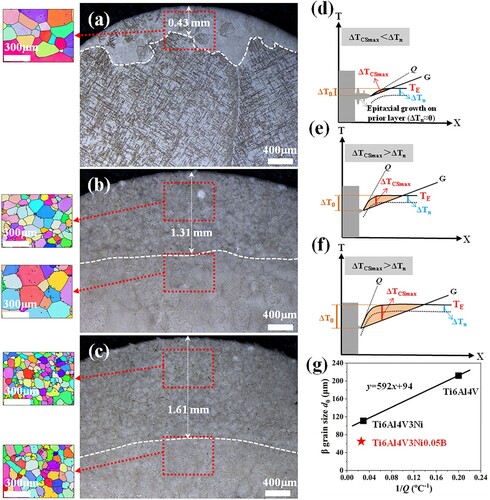
The formation criterion of CS ahead of the solid–liquid interface is given by Equation (1) [Citation21]. A large degree of CS (ΔTcs) can be obtained from a large value of the right side of Equation (1).
(1)
(1) where G is the temperature gradient, V is the solidification rate,
, ml is the liquidus slop, c0 is the normal solute concentration in wt%, k is the solute partition coefficient, ΔT0 is the equilibrium solidification temperature range and D is the liquid solute diffusivity. The Q and ΔT0 represent the developing rate and degree of CS, respectively. For multi-component alloys,
. Table shows Q and ΔT0 for three alloys, and the values of ml, k and Qi of Al, V, Ni, B elements in each alloy, calculated using the Thermo-Calc software with TTTI titanium alloy database.
Table 2. The Q, ΔT0, ml, k and Qi.
Referring to Ti6Al4V, Q in Ti6Al4V3Ni and Ti6Al4V3Ni0.05B increases by approximately 5.8 and 6.8 times, while ΔT0 increases by about 19.7 and 33.9 times, respectively. Compared with Ti6Al4V3Ni, the synergy of Ni and B in Ti6Al4V3Ni0.05B prominently increases Q and ΔT0, resulting in a more rapid buildup of a larger ΔTcs ahead of the solid–liquid interface.
During the initial solidification process of the last layer of the Ti6Al4VxNiyB deposits, the prior β-grains at the molten-pool bottom grow epitaxially from the previous layer (ΔTn ≈ 0°C) and, at the same time, the partitioned solute is discharged into the liquid, triggering a CS zone ahead of the solid–liquid interface (Figure (d–f)). Compared with Al and V, Ni has a larger partitioning in the liquid during the solidification of titanium alloy. The larger Q and ΔT0 in Ti6Al4V3Ni allow the rapid achievement of the larger ΔTcs and, thus, plenty of new grains can nucleate only after a slight extent of epitaxial growth of prior β-grains due to ΔTcs>ΔTn, and the equiaxed-grains form at the molten-pool bottom. Consequently, the fully-equiaxed-grains are obtained in Ti6Al4V3Ni. Similar process also happens in Ti6Al4V3Ni0.05B, except that the synergy of Ni and B can more rapidly produce a larger ΔTcs, leading to a larger zone containing finer equiaxed-grains.
It is conventionally believed that the size of the grains directly obtained from the solidification is inversely proportional to Q of titanium alloy. However, in this study the synergy of Ni and B pronouncedly reduces the d0 value in Ti6Al4V3Ni0.05B to nearly 50% that in Ti6Al4V3Ni, leading to a much finer grain than the one predicted by the linear relationship of 1/Q previously reported (Figure (g)) [Citation19,Citation24,Citation28]. Dramatically, an enhanced synergetic effect on grain refinement is achieved, similarly to previous report in aluminum systems [Citation29]. Notably, the Q value calculated by the simple summation of Qi for each single-element probably cannot account for this synergistic mechanism during solidification and, thus, it must be further studied.
Different from the last-layer in the deposit top, the previously deposited layers experience a series of thermal-cycling responsible for the final microstructures, as shown in Figure (a,b). Note that the microstructures in the middle of the Ti6Al4V3Ni and Ti6Al4V3Ni0.05B deposits are fully-equiaxed β-grains. Correspondingly, the average size d of β-grains is 624 and 207 µm, respectively; the β-grain coarsening degree m (m = d/d0) is 5.6 and 3.2, respectively, referring to the β-grain size in the last-layer. Notably, only 0.05 wt% B indeed reduces m of Ti6Al4V3Ni0.05B to nearly half that of Ti6Al4V3Ni, resulting in a prominent reduction of d (by 67%) in Ti6Al4V3Ni0.05B.
Figure 2. The β-grains at the middle of the Ti6Al4V3NiyB deposits. (a) Ti6Al4V3Ni, (b) Ti6Al4V3Ni0.05B; (c) β-grain size and coarsening degree m; (d) the function of the simulated m with regard to d0, and the symbols represent the experimental value; the simulated δdi, d = d0+Σδdi, δMi and M = ΣδMi with regard to the thermal-cycling number (Tβ˂Tp˂Ts) in (e) Ti6Al4V3Ni and (f) Ti6Al4V3Ni0.05B. (Ts and Tβ are calculated using Thermo-Calc.).
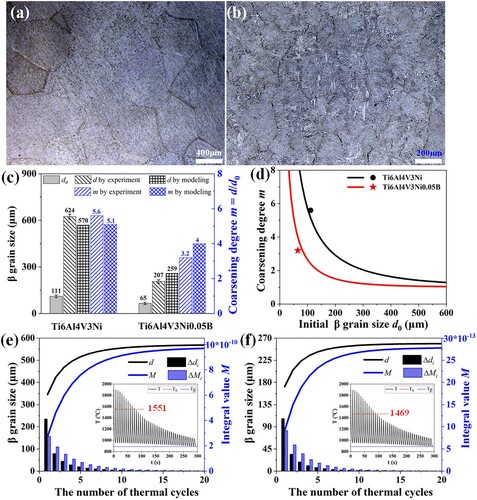
According to the classic grain-coarsening model [Citation30], a modified model suitable for the instantaneous temperature T during DED is given as:
(2)
(2)
(3)
(3) where n is the grain-coarsening exponent, k0 is a constant, M is an integral value related with temperature T(t) and time t, th(Tβ) and tc(Tβ) are the time when the heating and cooling temperature reaches the β-transus (Tβ = 887.3°C for Ti6Al4V3NiyB), respectively; q is the grain-coarsening activation energy and R is the gas constant (8.314 J/(mol·K)). Only the thermal-cycles with a peak-temperature Tp satisfying Tβ˂Tp˂Ts (alloy melting-temperature) can induce grain coarsening. The grain-coarsening parameters for Ti6Al4V3Ni and Ti6Al4V3Ni0.05B are: n = 2.45, k0 = 11.36 m2.45/s, q = 319.9 KJ/mol; and n = 2.56, k0 = 229.5 m2.56/s, q = 390 KJ/mol, respectively. Thereby, the grain coarsening at the middle of the Ti6Al4V3NiyB deposits can be predicted through Equations (2) and (3) once the corresponding temperature field is known.
According to the calculated temperature field (Figure (e,f)), the predicted values of m with respect to different d0 for Ti6Al4V3Ni and Ti6Al4V3Ni0.05B are shown in Figure (d). The predicted and measured results show a better agreement. In addition, the smaller the d0, the larger the m for the same alloy. Here, the measured d0 in the Ti6Al4V3Ni0.05B (65 µm) is about half of that in the Ti6Al4V3Ni (111 µm). However, the m value of the coarsened-grain at the middle of Ti6Al4V3Ni0.05B deposit (3.2) is much smaller than that of Ti6Al4V3Ni (5.6). This is because that trace B can significantly curb the β-grain coarsening during multiple instantaneous high-temperature thermal-cycles (˂1 s for each loading) by increasing q and n as shown above. Therefore, Ti6Al4V3Ni0.05B achieves the much finer equiaxed-grains than Ti6Al4V3Ni. This reveals for the first time that trace B plays an equally important role in refining β-grains of DED titanium alloy during reheat-cycles and solidification process.
The final β-grains at the middle of the deposit result from the coarsening of the initial solidified β-grains during successive multiple thermal-cycles (Tβ˂Tp˂Ts). Figure (e,f) shows the contribution of each thermal-cycling to the size of the coarsened β-grain δdi and to the corresponding integral area δMi for Ti6Al4V3Ni and Ti6Al4V3Ni0.05B. For both alloy deposits, the d value of the nth layer (black curve) firstly rises rapidly with the thermal-cycling number, and then remains unchanged. This is because as the number of the deposited layers increases, the temperature that the nth layer suffers from each subsequent thermal-cycling gradually decreases, leading to the reduction of δMi and δdi. Strikingly, the d value is mainly affected by a few high-temperature thermal-cycles (<10) when depositing the subsequent layers adjacent the nth layer. Consequently, only the adjacent several re-heating high-temperature thermal-cycles (Tβ˂Tp˂Ts) are mainly responsible for the grain-coarsening of the nth layer in DED titanium alloy.
As shown in Figure , compared with Ti6Al4V, the addition of Ni causes the formation of Ti2Ni (139 nm) and reduces the aspect ratio of the α-laths (1.6 µm in width) in Ti6Al4V3Ni. Besides a lot of Ti2Ni between the α-laths, some TiB phase is also formed, and the α-laths (1 µm in width) are refined in Ti6Al4V3Ni0.05B. For the heat-treated Ti6Al4V3Ni0.05B, Ni is almost completely dissolved into the β-matrix, forming (α-Ti+β-Ti) intragranular-microstructure with a little amount of residual Ti2Ni (˂0.01 vol.%), and the width of α-laths is significantly reduced to 0.219 µm.
Figure 3. The microstructures at the middle of the Ti6Al4VxNiyB deposits. As-built: (a) Ti6Al4V, (b) Ti6Al4V3Ni, and (c) Ti6Al4V3Ni0.05B, (d) heat-treated Ti6Al4V3Ni0.05B.
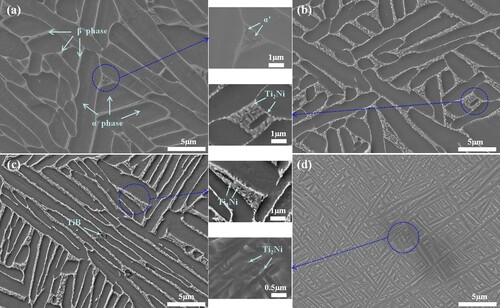
As shown in Figure (a), compared with Ti6Al4V, both the yield strength (YS) and the ultimate tensile strength (UTS) are increased, while the fracture elongation (EL) is decreased for as-built Ti6Al4V3Ni and Ti6Al4V3Ni0.05B. This should be attributed to the strengthening and embrittlement effect of Ti2Ni. Compared with Ti6Al4V3Ni, all YS, UTS and EL in as-built Ti6Al4V3Ni0.05B are improved, especially the longitudinal EL is increased by ∼3.4 times (2.1%). This may be attributed to the weakened detrimental-effect of the relatively dispersed Ti2Ni caused by the finer equiaxed-grains and α-laths. After the heat-treatment for Ti6Al4V3Ni0.05B, a significantly increased EL with slightly higher UTS (transverse: 6.87%, 1231Mpa; longitudinal: 6.97%, 1230Mpa) without mechanical anisotropy are both achieved (Figure (a,c)). The significant enhancement of EL is attributed to the near-complete disappearance of Ti2Ni, which favors the movement of dislocations and deformation compatibility of different phases. The improvement of UTS is due to the strengthen of refiner α-laths and solid-solution strengthening of Ni [Citation31].
Figure 4. Mechanical properties of Ti6Al4VxNiyB alloys. (a) Representative engineering stress–strain curves; the error bars (UTS and EL) represent one standard deviation. (b) Tensile properties for heat-treated Ti6Al4V3Ni0.05B are comparable with Ti-Cu [Citation6] and Ti6Al4V [Citation10] by DED and the ASTM standard for Ti6Al4V [Citation32]. (c) Anisotropy (the calculation method is shown in [Citation21]).
![Figure 4. Mechanical properties of Ti6Al4VxNiyB alloys. (a) Representative engineering stress–strain curves; the error bars (UTS and EL) represent one standard deviation. (b) Tensile properties for heat-treated Ti6Al4V3Ni0.05B are comparable with Ti-Cu [Citation6] and Ti6Al4V [Citation10] by DED and the ASTM standard for Ti6Al4V [Citation32]. (c) Anisotropy (the calculation method is shown in [Citation21]).](/cms/asset/b268df6f-33c5-4ab3-8988-f4c7f0a1fe5c/tmrl_a_2115323_f0004_oc.jpg)
As shown in Figure (b), compared with Ti–Cu alloys manufactured by DED [Citation6], the mechanical properties of the heat-treated Ti6Al4V3Ni0.05B exhibit a much higher strength with comparable plasticity. Compared with DED Ti6Al4V [Citation10], the YS of the heat-treated Ti6Al4V3Ni0.05B is significantly higher, and the EL is between the transverse and longitudinal EL of Ti6Al4V. Also, the comprehensive tensile properties of the heat-treated Ti6Al4V3Ni0.05B are comparable to that of ASTM standard for cast and wrought Ti6Al4V [Citation32].
As shown in , the fracture surface of Ti6Al4V is a ductile-fracture with dimples. While an obvious intergranular brittle-fracture is presented in Ti6Al4V3Ni. The as-built Ti6Al4V3Ni0.05B shows a mixed ductile-brittle fracture because of its finer equiaxed-grains and the grain-boundary strengthening by B [Citation23]. The heat-treated Ti6Al4V3Ni0.05B exhibits ductile fracture with small dimples, which is consistent with its improved ductility ().
4. Conclusions
In summary, an alloy design method for achieving fully-equiaxed fine β-grains with good comprehensive tensile properties in AM titanium alloy is demonstrated, by synergistically controlling the β-grains during both solidification and subsequent thermal-cycle, and a solution + quenching heat-treatment. The fully-equiaxed β-grains are obtained in both Ti6Al4V3Ni and Ti6Al4V3Ni0.05B due to the significantly increased constitutional supercooling by Ni. Compared with Ti6Al4V3Ni, the grain size of Ti6Al4V3Ni0.05B is firstly reduced by ∼50% during the initial solidification owing to the larger Q caused by the synergy of Ni and B, and then the grain-coarsening degree during thermal-cycles is further reduced by ∼50% because of the increased grain-coarsening exponent and activation energy by trace B. This reveals for the first time that a 1 + 1 > 2 grain-refinement effect can be achieved in solidified equiaxed-grains by co-addition of Ni and B, and trace B plays an equally important role in refining β-grains during reheat-cycles and solidification process. Both the strength and plasticity of heat-treated Ti6Al4V3Ni0.05B are improved and comparable to that of DED Ti6Al4V, due to the fine fully-equiaxed β-grains with intragranular (α-Ti+β-Ti) microstructure. These findings provide new insight into the grain structure control and the composition design of AM titanium alloy.
Supplemental Material
Download MS Word (5.3 MB)Disclosure statement
No potential conflict of interest was reported by the author(s).
Additional information
Funding
References
- DebRoy T, Wei HL, Zuback JS, et al. Additive manufacturing of metallic components – process, structure and properties. Prog Mater Sci. 2018;92:112–224.
- Herzog D, Seyda V, Wycisk E, et al. Additive manufacturing of metals. Acta Mater. 2016;117:371–392.
- Martin JH, Yahata BD, Hundley JM, et al. 3D printing of high-strength aluminium alloys. Nature. 2017;549:365–369.
- Panwisawas C, Tang YT, Reed RC. Metal 3D printing as a disruptive technology for superalloys. Nat Commun. 2020;11:2327.
- Zhang T, Huang Z, Yang T, et al. In situ design of advanced titanium alloy with concentration modulations by additive manufacturing. Science. 2021;374:478–482.
- Zhang D, Qiu D, Gibson MA, et al. Additive manufacturing of ultrafine-grained high-strength titanium alloys. Nature. 2019;576:91–95.
- Todaro CJ, Easton MA, Qiu D, et al. Grain structure control during metal 3D printing by high-intensity ultrasound. Nat Commun. 2020;11:142.
- Barriobero-Vila P, Gussone J, Stark A, et al. Peritectic titanium alloys for 3D printing. Nat Commun. 2018;9:3426.
- Carroll BE, Palmer TA, Beese AM, et al. Anisotropic tensile behavior of Ti-6Al-4V components fabricated with directed energy deposition additive manufacturing. Acta Mater. 2015;87:309–320.
- Kok Y, Tan XP, Wang P, et al. Anisotropy and heterogeneity of microstructure and mechanical properties in metal additive manufacturing: a critical review. Mater Des. 2018;139:565–586.
- Ren YM, Lin X, Guo PF, et al. Low cycle fatigue properties of Ti-6Al-4V alloy fabricated by high-power laser directed energy deposition: experimental and prediction. Int J Fatigue. 2019;127:58–73.
- Sterling A, Torries B, Shamsaei N, et al. Fatigue behavior and failure mechanisms of direct laser deposited Ti–6Al–4V. Mater Sci Eng A. 2016;655:100–112.
- Sterling A, Shamsaei N, Torries B, et al. Fatigue behaviour of additively manufactured Ti-6Al-4V. Procedia Eng. 2015;133:576–589.
- Zhang ZB, Hao YL, Li SJ, et al. Fatigue behavior of ultrafine-grained Ti–24Nb–4Zr–8Sn multifunctional biomedical titanium alloy. Mater Sci Eng A. 2013;577:225–233.
- Saitova LR, Höppel HW, Göken M, et al. Cyclic deformation behavior and fatigue lives of ultrafine-grained Ti-6AL-4V ELI alloy for medical use. Int J Fatigue. 2009;31:322–331.
- Chao Q, Mateti S, Hodgson PD, et al. Nanoparticle-mediated ultra grain refinement and reinforcement in additively manufactured titanium alloys. Addit Manuf. 2021;46:102173.
- Tian X, Zhu Y, Zhang K, et al. Isotropic and improved tensile properties of Ti-6Al-4V achieved by in-situ rolling in direct energy deposition. Addit Manuf. 2021;46:102151.
- Zhang G, Lu X, Lin X, et al. In-situ grain structure control in directed energy deposition of Ti6Al4V. Addit Manuf. 2022;55:102865.
- StJohn DH, Qian M, Easton MA, et al. The interdependence theory: the relationship between grain formation and nucleant selection. Acta Mater. 2011;59:4907–4921.
- Easton MA, StJohn DH. A model of grain refinement incorporating alloy constitution and potency of heterogeneous nucleant particles. Acta Mater. 2001;49:1867–1878.
- Xue A, Lin X, Wang L, et al. Influence of trace boron addition on microstructure, tensile properties and their anisotropy of Ti6Al4V fabricated by laser directed energy deposition. Mater Des. 2019;181:107943.
- Bermingham MJ, Kent D, Zhan H, et al. Controlling the microstructure and properties of wire arc additive manufactured Ti–6Al–4V with trace boron additions. Acta Mater. 2015;91:289–303.
- Singh G, Ramamurty U. Reprint: boron modified titanium alloys. Prog Mater Sci. 2021;120:100815.
- Mereddy S, Bermingham MJ, StJohn DH, et al. Grain refinement of wire arc additively manufactured titanium by the addition of silicon. J Alloy Compd. 2017;695:2097–2103.
- Sui S, Chew Y, Weng F, et al. Study of the intrinsic mechanisms of nickel additive for grain refinement and strength enhancement of laser aided additively manufactured Ti–6Al–4V. Int J Extrem Manuf. 2022;4:035102.
- Xue A, Lin X, Wang L, et al. Heat-affected coarsening of β grain in titanium alloy during laser directed energy deposition. Scripta Mater. 2021;205:114180.
- Bermingham MJ, McDonald SD, StJohn DH, et al. Beryllium as a grain refiner in titanium alloys. J Alloys Compd. 2009;481:L20–L23.
- Bermingham MJ, StJohn DH, Krynen J, et al. Promoting the columnar to equiaxed transition and grain refinement of titanium alloys during additive manufacturing. Acta Mater. 2019;168:261–274.
- Gröbner J, Mirković D, Schmid-Fetzer R. Thermodynamic aspects of grain refinement of Al–Si alloys using Ti and B. Mater Sci Eng A. 2005;395:10–21.
- Semiatin SL, Soper JC, Sukonnik IM. Short-time beta grain growth kinetics for a conventional titanium alloy. Acta Mater. 1996;44:1979–1986.
- Xiong Z, Pang X, Liu S, et al. Hierarchical refinement of nickel-microalloyed titanium during additive manufacturing. Scripta Mater. 2021;195:113727.
- Zhang D, Sun S, Qiu D, et al. Metal alloys for fusion-based additive manufacturing. Adv Eng Mater. 2018;20:1700952.