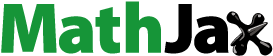
Abstract
High strain hardening rate is usually pursued for high ductility. Here we report that moderate strain hardening rate is desired for producing better ductility and high yield strength, which is demonstrated in a medium carbon TRIP steel. By adjusting the temperature for bainitic transformation, the morphology, carbon content and residue stress of retained austenite were tuned to tailor the TRIP kinetics during tensile tests, which produced moderated but long-lasting strain hardening for high ductility while at the same time resulted in high yield strength. This strategy should work well for most materials, which usually have a limited ultimate strength.
GRAPHICAL ABSTRACT
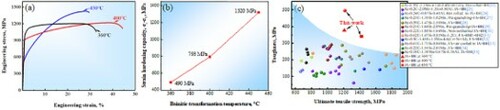
IMPACT STATEMENT
A principle is proposed and verified that an optimized moderate strain hardening rate is desired to produce the best mechanical properties for metallic materials.
1. Introduction
Metallic materials have been the main materials for advanced manufacturing and structural applications due to their good balance of high strength and ductility. However, these two properties are often mutually exclusive: an increase in strength is often accompanied by a sacrifice in ductility, leading to the well-known strength-ductility tradeoff [Citation1–5]. For instance, bulk nanostructured materials are usually several times stronger than their coarse-grained counterparts, but their ductility is typically very low [Citation3]. This is because the small grains of nanostructured materials make it difficult to generate Frank-Read dislocation sources in the grain interior. Consequently, dislocations are usually nucleated on grain boundaries, glide across the grains and then annihilated at grain boundaries on the opposite side without accumulation, which leads to low or no strain hardening [Citation4]. Therefore, the key to obtaining good ductility is to improve the strain hardening rate, which can delay the necking under tensile testing [Citation5]. Many strategies for designing alloys have been proposed to enhance the strain hardening rate, so as to achieve good high strength while retaining a reasonable ductility [Citation5–11]. For example, fine second-phase particles are introduced into nanostructured materials, which can increase dislocation storage capability and resist dislocation slip [Citation5]. Another example is the extra strain hardening in heterogeneous structural materials, which is responsible for their good ductility [Citation9,Citation10]. High strain hardening rate is usually pursued for improving the ductility of metallic materials.
It is well known from the Considère criterion [Citation12] that the necking instability will not happen during a tensile testing if
(1)
(1) where σ is true stress, ε is true strain, and the
is strain hardening rate (the tangent slope of the true stress–strain curve). The most direct and common interpretation of Equation (1) is that higher strain hardening rate is desired for better ductility. Therefore, in the literature researchers often report strategies on how to raise the strain hardening rate in order to improve ductility [Citation4,Citation9,Citation10,Citation13,Citation17]. Some good examples include using TRIP and TWIP effects on β-Ti alloys to achieve high ductility by stabilizing the plastic flow as formulated by Considère [Citation15–17]. Meanwhile, the increase of hardening rate is necessary in BCC alloy systems where the hardening rate is intrinsically low. A question arises: is the higher the strain hardening rate, the better?
In this paper we report that the moderate strain hardening rate is beneficial for achieving the best combination of high Ductility and good yield strength, which is demonstrated in a medium carbon TRIP steel. The adjustment of strain hardening rate in TRIP steels can be realized by tuning the stability of retained austenite (RA). The transformation of RA into martensite is accompanied by local shear strain and volume expansion, generating dislocations and compressive stress in the austenitic matrix, which consequently enhances strain hardening [Citation18,Citation19]. Moreover, the strain hardening rate of TRIP steels can be controlled by adjusting the stability and volume fraction of RA. The moderate strain hardening rate was obtained by adjusting the TRIP kinetics during tensile tests, which made the moderated strain hardening rate last longer for high ductility while at the same time the yield strength can be raised without significantly affect the ductility. This strategy is applicable to materials with a limited ultimate strength or a limited strain hardening capacity, which are true for most metallic materials. In this study, the RA stability was tuned by varying the bainite transformation temperature to tailor the volume fraction, morphology, grain size, and carbon content of RA.
2. Materials and methods
A steel with a nominal composition of Fe-0.51C-0.49Si-1.78Mn-1.60Al-1.46Cu-0.12Ti-0.21Mo-0.037 V (wt.%) was used in this study. The cast ingot was forged and homogenized at 1200°C for 2 h, hot rolled by 93% from 80 mm to 6 mm via 6 passes, and warm rolled to a thickness of 1.5 mm at 750°C by 6 passes. Phase transformation temperatures A1 and A3 of the studied steel were obtained by JMatPro-v10 as 735.1°C and 844.1°C, respectively. The specimens were annealed at 820°C for 5 min, followed by an isothermal holding in a salt bath at 360°C, 400°C, or 450°C for 30 min. Finally, the specimens were cooled in air to room temperature. The uniaxial tensile specimens with a gage dimension of 15 × 5 × 1.5 mm3 were machined along the rolled direction, and tensile tests were performed on a 100 kN AG-X plus testing system at a strain rate of 2 × 10−3 s−1. The volume fraction and carbon content of RA were measured by XRD equipped with a graphite bent crystal monochromator using Cu Kα radiation. The scanning range was 45–94° and the scan step was 0.03° per second. The carbon content in RA can be calculated from Equation (2) [Citation20], assuming that the diffusion effect of substitutional elements can be ignored during heat treatment process [Citation21],
(2)
(2) where C, Mn, Si, Al, Cu, Mo, Ti, and V are the corresponding concentration of element (wt.%) in studied steel [Citation21, Citation22]. aγ is the average lattice parameters of (200)γ, (220)γ, and (311)γ in Å. Cγ is the average carbon content in RA.
The aγ can be calculated by the followed equation:
(3)
(3) where h, k, l are the Miller indices of the crystal plane, and dhkl is the corresponding interplanar spacing.
The volume fraction of RA was calculated by the following equation [Citation23, Citation24]:
(4)
(4) where Vγ is the volume fraction of RA, Iγ and Iα are the average integral intensity of (200) γ, (220) γ, and (311) γ austenite peaks as well as the (200) α and (211) α ferrite peaks, respectively.
The microstructures were characterized by using a JSM-7001F scanning electron microscope (SEM) at a voltage of 20 kV. The samples for SEM observation were etched in 4% nital solution after mechanical grinding and polishing. Electron-backscatter-diffraction (EBSD) analyses were performed on an SEM (Zeiss crossbeam 550) equipped with an EBSD detector, operating at 20 kV with a step size of 50 nm, and the EBSD data were analyzed by HKL Channel 5. The specimens were prepared via mechanical polishing and electro-polishing using 10 vol% perchloric acid and 90% alcohol solution. TEM studies were performed in a field emission gun (FEG) JEM 2100F at 200 kV. The TEM specimens were prepared by electro-polishing in a solution of 8% perchloric and 92% acid-alcohol solution by using a twin jet electron-polisher operated at 26 V and −25°C.
3. Results and discussion
The engineering stress–strain curves of three steel specimens treated at various bainitic transformation temperatures are shown in Figure (a), and the corresponding mechanical properties are listed in Table . For simplicity, the specimens treated at 360°C, 400°C and 450°C are here after referred to as the 360°C specimen, 400°C specimen, and 450°C specimen, respectively. As shown in Figure (a), the ultimate strength (σUTS) increased from 1200 to 1430 MPa with increasing treatment temperature, while the yield strength (σY) decreased remarkably from 1010 to 510 MPa.
Figure 1 (a) Engineering stress - strain curves of the medium carbon TRIP steels after bainitic holding at 360°C, 400°C and 450°C. (b) Increasing strain hardening capacity with increasing bainitic holding temperature. (c, d) Comparison of mechanical properties in this study with the previously reported TRIP assisted steels in literatures [Citation21, Citation25–Citation35]. IA: intercritical annealing, FA: full austenitized, BH: bainitic holding.
![Figure 1 (a) Engineering stress - strain curves of the medium carbon TRIP steels after bainitic holding at 360°C, 400°C and 450°C. (b) Increasing strain hardening capacity with increasing bainitic holding temperature. (c, d) Comparison of mechanical properties in this study with the previously reported TRIP assisted steels in literatures [Citation21, Citation25–Citation35]. IA: intercritical annealing, FA: full austenitized, BH: bainitic holding.](/cms/asset/5f5ac79d-8fee-4f7d-a48d-77737b969045/tmrl_a_2116295_f0001_oc.jpg)
Table 1. Mechanical properties of medium carbon TRIP steels after bainitic holding.
Here we define a new terminology, strain hardening capacity, as the difference between the true stress (σt) at the point of necking onset point and the yield true strength (σy), to be used in the following discussion. The true stress at the point of necking onset point can be calculated as σt = σu (δ+1), where σu and δ are the ultimate (tensile) strength and ductility, respectively, from the engineering stress–strain curve. Figure (b) shows that the strain hardening capacity dramatically increased with increasing bainitic holding temperature. Table reveals that although the strain hardening capacity of the 450°C specimen (the blue curve) is 1.7 times of that of the 400°C specimen (the red curve), the uniform elongation of the 450°C specimen is only 74% of that of the 400°C specimen. This is because the 400°C specimen has a moderate strain hardening rate that lasted longer before consuming its lower strain hardening capacity. For the same reason, the 360°C specimen has a good ductility of 25% although its total strain hardening capability is only 37% of that of the 450°C specimen.
As shown in Figure and Table , the 450°C specimen has the highest strain hardening rate, lowest ductility, lowest yield strength and lowest toughness, while the 400°C specimen has a moderate strain hardening rate, the highest ductility, a high yield strength and the highest toughness (Figure (c,d)). The toughness, which is the area under the stress–strain curve, can be considered as a good indicator of the comprehensive mechanical property because it takes both high strength and high ductility to produce high toughness. Therefore, there exists an optimum moderate strain hardening rate that produces the best comprehensive mechanical property. If the strain hardening rate is too high, the total strain hardening capacity will be exhausted quickly, leading to low ductility. Furthermore, if the yield strength is very high, the strain hardening capacity may be reduced, also leading to lower ductility at the same strain hardening rate.
The related mechanical properties of the three specimens are summarized in Figure (c,d), and compared with the reported TRIP steels [Citation21,Citation25–35]. As shown, using the moderate strain hardening rate strategy we have produced mechanical properties that are much superior to those reported in the literature for TRIP steels.
Figure (a–c) shows the SEM micrographs of the three specimens. The microstructures consist of ferrite, bainite, RA, and martensite. It is clear that the martensitic blocks increase gradually with increasing transformation temperature. The carbon content and volume fraction of RA was measured by XRD (Figure (d)). As shown, the peak position of (200)γ gradually shifts to the right with increasing isothermal temperatures from 360°C to 450°C. This indicates that spacing of (200)γ planes decreased and the corresponding carbon content in RA decreased with increasing temperature. The calculated RA volume fractions are comparable, 29%, 31%, and 31% for the 360°C specimen, 400°C specimen and 450°C specimen. However, the corresponding carbon content decreased, which are 1.6%, 1.4%, and 1.1%, respectively. It is known that the RA becomes less stable with decreasing carbon content [Citation26].
Figure 2. SEM images of medium carbon TRIP steels. (a) 360°C specimen, (b) 400°C specimen and (c) 450°C specimen. (d) The corresponding XRD patterns, and inset showing the magnified (200)Y peak. RA: retained austenite, B: bainite, F: ferrite, M: martensite.
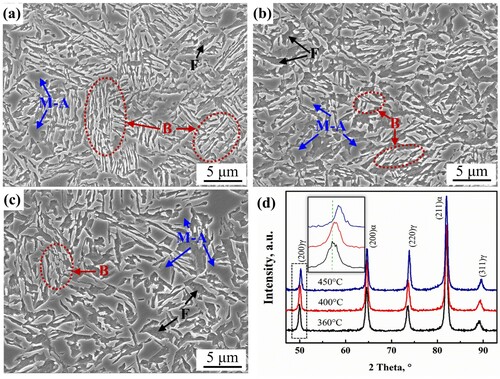
Figure (a–c) shows deviation angle from the K-S relationship across the interface between RA and surrounding phases in the 360°C specimen, 400°C specimen and 450°C specimen. In the micrograph, FCC and BCC phases are indicated in white and gray. The boundaries with a deviation angle of θ ≤ 10°, 10°< θ ≤ 20°, 20°< θ ≤ 30°, and 30°< θ are indicated in red, green, blue and cyan, respectively. As shown, the blocky RA (in the blue rectangle) are mostly located along the grain boundaries of primary austenite while film-like RA (in the yellow rectangle) are always located at the boundaries of bainitic ferrite. Moreover, the RA lamellae show a near K-S orientation relationship with the bainitic ferrite. However, blocky RAs exhibit a slight deviation with the parent phase. In fact, it was reported that blocky RA with a larger size always distributes along high-angle grain boundaries. In contrast, small film-like RAs are often observed near the low-angle grain boundaries [Citation14].
Figure 3. Interface characterization of medium carbon TRIP steels. (a) 360°C specimen, (b) 400°C specimen, and (c) 450°C specimen. (d) The corresponding average grain sizes of RA (d). LAGB: low angle grain boundary, HAGB: high angle grain boundary.

As shown in Figure (d), the proportion of large-sized RA gradually increases with increasing bainitic transformation temperature. Statistical results show that the average grain size of RA increased from 320 ± 20 nm to 410 ± 20 nm with increasing temperatures from 360°C to 450°C. It is known that RA with larger grain size and lower carbon content becomes less stable [Citation26]. This led to the decrease of RA stability with increasing bainitic temperature from 360°C to 450°C.
To verify and understand the adjustment of RA stability and its effect on strain hardening rate during tensile testing, the evolution of RA volume fraction under different interrupted tensile strain were analyzed by XRD (Figure ). It is revealed that the RA fraction gradually decreased with increasing applied strain. RA stability can be used to estimate the martensite transformation rate, as described by [Citation36]:
(5)
(5) where f0 is the volume fraction of RA before tensile deformation, f is the volume fraction of RA at a specific true strain (ε). In general, a higher k value represents faster transformation to martensite, i.e. lower RA stability. The k value of TRIP and Q&P steels usually lies in the range of 1–20 [Citation37]. Based on the exponential fitting, the k values of the 360°C specimen, 400°C specimen and 450°C specimen were calculated as 6.42, 6.35, and 13.58, respectively. This indicates that the 360°C specimen, 400°C specimen were clearly more stable than 450°C specimen, which can be attributed to the lower carbon content and larger grain size of the 450°C specimen.
Figure 4. Evolution of RA volume fraction as a function of true strain for medium carbon TRIP steels after bainitic holding at 360°C, 400°C, and 450°C.
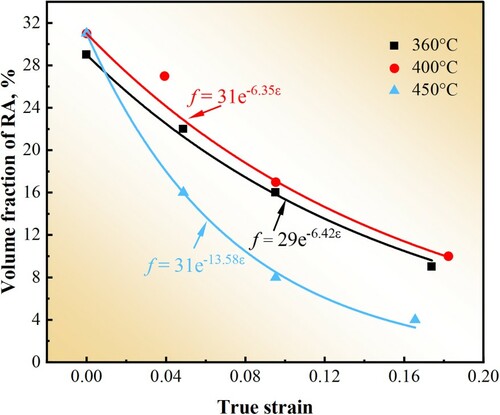
The three specimens have the similar initial fraction RA (29–31%) and the similar average grain size of RA. Thus, evolution of the RA volume fraction with tensile straining led to the distinct differences in their strain hardening behaviors, yield strengths, and tensile strengths. Due to the high RA stability of 360°C specimen, the transformation from RA into martensite is suppressed, and the transformed RA is only 23% after fracture, so its strain hardening capacity is limited, which led to the lowest strain hardening rate but the highest yield strength of 1010 MPa. In contrast, a large fraction of RA was transformed into martensite in the beginning of deformation in the 450°C specimen, which subsequently promotes rapid multiplication of dislocations and enhancing strain hardening rate. The transformed RA is largest (29%) in the 450°C specimen, giving it the highest strain hardening rate, which resulted in the highest tensile strength of 1430 MPa, but the lowest yield strength of 510 MPa and the lowest ductility of 29%, which was caused by its lowest RA stability. Consequently, the strain hardening capacity was consumed quickly in the early stage of tensile deformation despite of its highest strain hardening capacity.
As mentioned earlier, the strain hardening capacity of a material is related to both its yield strength and ultimate strength [Citation38]. If the strain hardening capacity of a material is too high, it will inevitably lead to low yield strength. In turn, if the yield strength is too high, it will lead to insufficient strain hardening capacity, resulting in limited ductility. In this study, the strain hardening capacity of the 450°C specimen is 920 MPa, which is higher than that the 360°C specimen. As a result, the 450°C specimen has the lowest yield strength of 510 MPa, and the 360°C specimen has the highest yield strength of 1010 MPa. Compared with the 360°C specimen and 450°C specimen, the TRIP kinetic of the 400°C specimens has an optimum strain hardening rate, which made it last to high tensile strains while at the same time produced a high yield strength of 890 MPa.
4. Summary
In summary, we have proposed and verified a principle in designing the strain hardening rate for the best mechanical properties of metallic materials. Very high strain hardening rate is often associated with low yield strength and/or low ductility. Very low strain hardening rate leads to low ductility. A moderate optimized strain hardening rate would produce the best combination of yield strength and ductility. We also proposed a new concept of strain hardening capacity, which is the difference between the ultimate strength and yield strength. Metallic materials with high yield strength usually have low strain hardening capacity, making it more critical to moderate the strain hardening rate, making it just high enough to prevent early necking. The proposed principle is verified using a medium carbon TRIP steel as a model material, whose strain hardening rate was adjusted by tuning the stability of retained austenite. Superior combinations of yield strengths and high uniform elongations were obtained using the moderate strain hardening rate strategy. This strategy should be applicable to most metallic materials.
Supplemental Material
Download MS Word (1.2 MB)Disclosure statement
No potential conflict of interest was reported by the author(s).
Additional information
Funding
References
- Kong HJ, Yang T, Chen R, et al. Breaking the strength-ductility paradox in advanced nanostructured Fe-based alloys through combined Cu and Mn additions. Scripta Mater. 2020;186:213–218.
- Wu XL, Zhu YT, Lu K. Ductility and strain hardening in gradient and lamellar structured materials. Scripta Mater. 2020;186:321–325.
- Zhao YH, Bingert JF, Liao XZ, et al. Simultaneously increasing the ductility and strength of ultra-fine-grained pure copper. Adv Mater. 2006;18:2949–2953.
- Ovid’ko IA, Valiev RZ, Zhu YT. Review on superior strength and enhanced ductility of metallic nanomaterials. Prog Mater Sci. 2018;94:462–540.
- Zhao YH, Liao XZ, Cheng S, et al. Simultaneously increasing the ductility and strength of nanostructured alloys. Adv Mater. 2006;18:2280–2283.
- Luo ZC, Huang MX. The role of interstitial carbon atoms on the strain-hardening rate of twinning-induced plasticity steels. Scripta Mater. 2020;178:264–268.
- Niu MC, Yang K, Luan JH, et al. Cu-assisted austenite reversion and enhanced TRIP effect in maraging stainless steels. J Mater Sci Technol. 2022;104:52–58.
- Yang Z, Jiang F, Wang Y, et al. Making composite steel higher strength and higher ductility via introducing carbon diffusion strategy. Mater Res Let. 2021;9:391–397.
- Wu XL, Jiang P, Chen L, et al. Synergetic strengthening by gradient structure. Mater Res Let. 2014;2:185–191.
- Cheng Z, Zhou H, Lu Q, et al. Extra strengthening and work hardening in gradient nanotwinned metals. Science. 2018;362:eaau1925.
- Park JM, Yang DC, Kim HJ, et al. Ultra-strong and strain-hardenable ultrafine-grained medium-entropy alloy via enhanced grain-boundary strengthening. Mater Res Let. 2021;9:315–321.
- Meyers M, Chawla K. Mechanical behavior of materials. 2nd ed. Cambridge University Press; 2009. p. 177.
- Ma E, Zhu T. Towards strength-ductility synergy through the design of heterogeneous nanostructures in metals. Mater Today. 2017;20:323–331.
- Zhu YT, Ameyama K, Anderson PM, et al. Heterostructured materials: superior properties from hetero-zone interaction. Mater Res Lett. 2021;9:1–30.
- Zhang J, Fu Y, Wu B, et al. Hierarchical {332}<113 >twinning in a metastable β Ti-alloy showing tolerance to strain localization. Mater Res Lett. 2020;8:247–253.
- Sun F, Zhang JY, Marteleur M, et al. Investigation of early stage deformation mechanisms in a metastable β titanium alloy showing combined twinning-induced plasticity and transformation-induced plasticity effects. Acta Mater. 2013;61:6406–6417.
- Qian B, Lilensten L, Zhang J, et al. On the transformation pathway in TRIP/TWIP Ti–12Mo alloy. Mater Sci Eng A. 2021;822:141672.
- Ennis BL, Jimenez-Melero E, Atzema EH, et al. Metastable austenite driven work-hardening behaviour in a TRIP-assisted dual phase steel. Int J Plast. 2017;88:126–139.
- Tan X, Xu Y, Yang X, et al. Microstructure-properties relationship in a one-step quenched and partitioned steel. Mater Sci Eng A. 2014;589:101–111.
- Dyson D, Holmes B. Effect of alloying additions on the lattice parameter of austenite. J Iron Steel Inst. 1970;208:469–474.
- Wang J, Wang Z, Wang X, et al. Strengthening effect of nanoscale precipitation and transformation induced plasticity in a hot rolled copper-containing ferrite-based lightweight steel. Scripta Mater. 2017;129:25–29.
- Dong XX, Shen YF, Yin TW. Strengthening a medium-carbon steel to 2800 MPa by tailoring nanosized precipitates and the phase ratio. Mater Sci Eng A. 2019;759:725–735.
- Lee YK, Shin HC, Jang YC, et al. Effect of isothermal transformation temperature on amount of retained austenite and its thermal stability in a bainitic Fe-3%Si-0.45%C-X steel. Scripta Mater. 2002;47:805–809.
- Dong XX, Shen YF, Jia N, et al. Improving mechanical properties and retained-austenite stability of a medium carbon Q&P steel by adjusting phase ratio. Mater Sci Eng A. 2022;833:142580.
- Peng F, Xu Y, Gu X, et al. Microstructure characterization and mechanical behavior analysis in a high strength steel with different proportions of constituent phases. Mater Sci Eng A. 2018;734:398–407.
- Grajcar A, Skowronek A, Radwański K. Mechanical behavior and stability of dispersed retained austenite in thermomechanically rolled and isothermally-treated TRIP-aided multiphase steel. Mater Sci Eng A. 2022;830:142300.
- Xie ZJ, Liu ZF, Misra RDK, et al. Retained austenite stabilisation in low carbon high silicon steel during isothermal holding. Mater Sci Technol. 2018;35:45–54.
- Zhou Y, Hojo T, Koyama M, et al. Effect of austempering treatment on the microstructure and mechanical properties of 0.4C-1.5Si-1.5Mn TRIP-aided bainitic ferrite steel. Mater Sci Eng A. 2021;819:141479.
- Gu XL, Xu YB, Wang X, et al. Austenite formation and mechanical behavior of a novel TRIP- assisted steel with ferrite/martensite initial structure. Mater Sci Eng A. 2020;803:140468.
- Gu XL, Xu YB, Peng F, et al. Role of martensite/austenite constituents in novel ultra-high strength TRIP-assisted steels subjected to non-isothermal annealing. Mater Sci Eng A. 2019;754:318–329.
- Liu N, Zhang X, Ding J, et al. Microstructure and mechanical properties of nanobainitic steel subjected to multiple isothermal heat treatments. J Iron Steel Res Int. 2018;25:1062–1067.
- Zhou SB, Hu F, Zhou W, et al. Effect of retained austenite on impact toughness and fracture behavior of medium carbon submicron-structured bainitic steel. J Mater Res Techol. 2021;14:1021–1034.
- Varshney A, Mondal K, Sangal S. Cold work induced stability of retained austenite at elevated temperature in a medium carbon high silicon steel. Mater Sci Eng A. 2022;832:142455.
- Chen ZY, Qi JJ, Liu HQ, et al. Bainitic transformation and mechanical properties of low-carbon high-strength bainitic steels with Mo addition. J Mater Eng Perform. 2020;29:2428–2439.
- Tang ZY, Huang JN, Ding H, et al. Austenite stability and mechanical properties of a low-alloyed ECAPed TRIP-aided steel. Mater Sci Eng A. 2018;724:95–102.
- Sugimoto KI, Kobayashi M, Hashimoto SI. Ductility and strain-induced transformation in a high-strength transformation induced plasticity-aided dual-phase steel. Metall Trans A. 1992;23:3085–3091.
- Sugimoto K, Tsunezawa M, Hojo T, et al. Ductility of 0.1-0.6C-1.5Si-1.5Mn ultra high-strength TRIP-aided sheet steels with bainitic ferrite matrix. ISIJ Int. 2004;44:1608–1614.
- Luo J, Mei Z, Tian W, et al. Diminishing of work hardening in electroformed polycrystalline copper with nano-sized and uf-sized twins. Mater Sci Eng A. 2006;441:282–290.