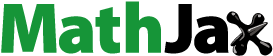
Abstract
A novel idea of precisely constructing gradient heterogeneous microstructure was proposed to greatly improve the formability of Al-Zn-Mg-Cu alloy by coupling multi-process firstly. After coupling control of the heterogeneous distribution of precipitates, strain energy storage and dislocation number density, a gradient distribution of coarse/fine grains can be constructed in the pre-aged alloy, resulting in a greatly enhanced average plastic strain ratio of 0.716. This work opens up a new frontier for achieving super-high room temperature formability without sacrificing the high strengths for Al-Zn-Mg-Cu alloys.
GRAPHICAL ABSTRACT
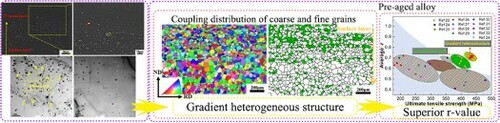
IMPACT STATEMENT
This paper reports a gradient heterogeneous structure in Al-Zn-Mg-Cu alloys by coupling control of precipitates, strain energy storage and dislocation number density, resulting in a greatly enhanced average plastic strain ratio of 0.716.
1. Introduction
For the traditional 7xxx series alloys (Al-Zn-Mg-Cu alloys), the room temperature formability is poor, and the high temperature forming process is complicated and high cost, which limit the possibility of their wide applications as automotive structure parts [Citation1–4]. If new 7xxx Al alloys can be widely used as transportation structural parts [Citation5,Citation6], their better room temperature formability is undoubtedly required. In the field of traditional metallic materials, the increase in strengths inevitably leads to a decrease in formability or plasticity at room temperature [Citation7–10]. This problem is particularly acute for 7xxx Al alloys [Citation11–13]. How to solve this common problem has become the key issue limiting the 7xxx Al alloys to be widely used in automotive fields. A large amount of literature [Citation14–18] points out that the design of heterogeneous microstructure can overcome the strength-ductility trade-off, such as the formation of heterogeneous lamellar structure, bimodal grain structure, gradient microstructure, etc., which can improve ductility of alloys with high strengths. For example, in high entropy alloys [Citation19,Citation20], different heat treatments of the alloys were designed to control the distribution of second phase particles and dislocation number density to prepare lamellar or gradient grain structures [Citation21,Citation22], effectively overcoming the strength-ductility trade-off and obtaining advanced alloys with both high strength and high ductility. Especially, in our previous study, we prepared a microdomain heterogeneous structure with coarse grains surrounded by fine grains using Fe-rich phase particles coupled with solute element concentrations, which greatly enhanced the formability of the alloys [Citation23]. However, the formation of the Fe-rich phase consumed Cu atoms, resulting in a slight decrease in the strengths of the alloys. Promisingly, if a new type of heterostructure, such as gradient grain structure, can be designed and constructed in Al-Zn-Mg-Cu alloys, it is expected that both high strength and high formability can be obtained. However, no study on constructing a gradient microstructure in Al-Zn-Mg-Cu alloys by thermomechanical processing route has been reported.
Therefore, this paper focuses on study on designing and constructing gradient microstructure in Al-Zn-Mg-Cu alloys to significantly improve their room temperature formability. Hopefully, it could provide a new strategy for the design and construction of gradient microstructure in other Al alloys with high strength and high formability.
2. Materials and methods
The composition of the experimental alloy was designed as follows: Al-5Zn-1.5Mg-1.5Cu-0.1Mn-0.1Ti-0.03Ni (wt.%). In order to substantially break and further control the evolution and final distribution of the precipitated phases in the alloy, the as-cast alloy was designed to be hot-rolled directly. The strain storage energy generated around the coarse precipitated phase during hot rolling can be used to accelerate the diffusion of solute elements during homogenization, which can reduce the production cost of Al-Zn-Mg-Cu alloys used in the automotive industry. Accordingly, the final detailed thermomechanical processing route is as follows, ingot → hot rolling from 90 mm to 7 mm → homogenization at 460°C for 15 h. Since the recrystallization microstructure is mainly influenced by strain energy storage and dispersion particles, it is considered that rolling deformation at different temperatures can induce corresponding changes in strain energy storage within the matrix, and a suitable intermediate annealing process can effectively control the distribution of precipitates. Therefore, in order to precisely construct a gradient structure of coarse and fine grains, the deformation rolling processes at different temperatures were designed in this work, combined with an intermediate annealing process. And finally, a significant improvement in the room temperature formability of the alloy sheets can be achieved. Accordingly, #A alloy: 7 mm homogenized sheet → room temperature cold rolling to 5 mm → 430°C/1 h intermediate annealing → room temperature cold rolling to 3.5 mm → 430°C/1 h intermediate annealing → room temperature cold rolling to 2 mm gauge → 475°C/10 min solution treatment → 120°C/1 h pre-aging treatment; #B alloy: 7 mm homogenized sheet → ultra-low temperature cold rolling to 4 mm at an initial temperature of liquid nitrogen and a finish temperature in the range of −30 to −10°C → 200°C/1 h + 430°C/1 h intermediate annealing → ultra-low temperature cold rolling to 2 mm → 200°C/1 h + 475°C/10 min solution treatment → 120°C/1 h pre-aging treatment.
Tensile properties of pre-aged alloy specimens were measured using an MTS-810 testing machine at room temperature. The microstructures and precipitate distribution were characterized by a SUPRA 55 field emission scanning electron microscope (SEM) with an X-ray energy dispersive spectroscopy (EDS) and Tecnai G2F30 field emission transmission electron microscopy (TEM). After mechanical thinning, the TEM test samples with a thickness of approximately 70 μm were prepared by electrolytic double-spraying in a solution of 70% vol. methanol and 30% vol. nitric acid at −25°C. The grain structure of the pre-aged alloy was performed Electron backscatter diffraction (EBSD) analysis in a SUPRA 55 field emission scanning electron microscope system operating at an acceleration voltage of 20 kV, a working distance of 15 mm, and a scanning step of 2.5 μm.
3. Results and discussion
As expected, the heterogeneous grain structures were prepared by the designed rolling process with different temperatures, as presented in Figure . It is clear that the surface layer of #A alloy forms a microstructure of fine sized grains, while the central layer has a relatively coarse sized grain structure, and in the vertical rolling direction, an obvious gradient grain structure is formed, as shown in Figure (b). However, the fine grains layer of #B alloy is distributed in the central region of the alloy, while the coarse grains layer in the surface layer, as shown in Figure (c). A precise size division of the grain size was performed, as shown in Figure (d)(e), showing grains with grain sizes smaller than the average grain size in green and grains with sizes higher than the average size in white. Obviously, the surface area of the pre-aged #A alloy forms a fine grain layer with smaller grain size, while the central area is a coarse grain layer with larger size, and the coupling distribution of coarse and fine grains shows a gradient structure characteristic. Accordingly, the #B alloy also exhibits a heterogeneous gradient structure with the fine grain layer in the center and the coarse grain layer on the surface. The grain size distributions of the gradient heterogenous structure are shown in Figure (f)(g), and the schematic diagram of grain size statistics is shown in Figure S1. From the surface layer to the central layer, the number density of fine grains of #A alloy gradually decreases and the distribution of fine/coarse grains presents a gradient heterostructure, while the gradient distribution trend of #B alloy is just opposite. This indicates that the distribution of fine grain layers can be controlled by designing a reasonable thermomechanical processing route, such as the routes used in the #A and #B alloys, to prepare Al-Zn-Mg-Cu alloys with a gradient structure of coupled coarse and fine grain distribution.
Figure 1. EBSD characterization of Al-Zn-Mg-Cu alloy in pre-aged state (a) a schematic diagram of the specimen extracted for viewing EBSD, (b) (c) Inverse pole figure (IPF), (d) (e) coarse/fine grain gradient coupling distribution, where green grains indicate fine grains with less than average grain size 26.6 μm and white grains indicate coarse grains, (f) (g) grain size distribution of gradient heterogenous structure (b) (d) (f): #A alloy, (c) (e) (g): #B alloy.

Figure shows the tensile mechanical properties curves, as well as the high level average plastic strain ratio r-values of the advanced series Al alloys for comparison. The detailed mechanical properties are shown in . It is worth noting that the formation of the heterogeneous structure results in a high plastic strain ratio even at the high strength level. For example, the average plastic strain ratio r of #A alloy can reach the value of 0.716. As shown in Figure (d), although in our previous study, the alloy formability was improved using multi-scale Fe-rich particles or the microdomain heterogeneous structure of coarse grains surrounded by fine grains, and the r value can be increased to the value of 0.719 [Citation23], the strengths of Fe-containing Al-Zn-Mg-Cu alloys were reduced due to the consumption of Cu element for the formation of Fe-rich phases. In comparison, the formation of the gradient structure in the Fe-free Al-Zn-Mg-Cu alloy not only can increase the average r value to the same high level (r = 0.716), but can also remain the high level of strengths due to without forming Fe-rich phases and no consumption of added Cu element in forming them. This should be attributed to the positive effect of the gradient distribution of the coarse/fine grain in the alloy. The gradient grain structure can induce plastic incompatibilities in the layers of different grain sizes during tensile deformation [Citation35]. Moreover, the gradient microstructure can also increase the yield strength of alloys along the direction of grain gradient distribution due to an extended elastic-plastic transformation induced by different layers. However, the 0° direction exhibits stress changes due to interlayer coupling between coarse and fine grain layers throughout the tensile deformation process, and its strength is lower than that of the 90° direction. Accordingly, the high elongation of the two alloys stem mainly from the strain dispersion effect induced by the coarse/fine grain coupling interaction. As shown in Figure (c), the strain hardening rate θ curves of the two alloys, present a typical two work hardening stages: the elastic-plastic transition stage with a steep decrease at small strain and the steady-state stage with a gentle decrease at large strain. The detailed SEM fracture images can be found in Figure S2, and the coordinated deformation of gradient heterogeneous microstructure is revealed in Figure S3. Eventually, the formation of gradient structure helps to overcome the strength-formability trade-off of the alloys, resulting in a combination of high strength, high plasticity and high formability.
Figure 2. Tensile mechanical properties of Al-Zn-Mg-Cu alloys in the pre-aging state (a) (b) tensile stress-strain curves. (c) strain hardening rate vs. true strain. (d) r values for different strength levels of advanced series aluminum alloys [Citation23–34].
![Figure 2. Tensile mechanical properties of Al-Zn-Mg-Cu alloys in the pre-aging state (a) (b) tensile stress-strain curves. (c) strain hardening rate vs. true strain. (d) r values for different strength levels of advanced series aluminum alloys [Citation23–34].](/cms/asset/68442a07-40af-48d6-8d34-165fcd4e7d42/tmrl_a_2122752_f0002_oc.jpg)
Table 1. Mechanical properties of alloys in the pre-aging state.
Additionally, as shown in Figure , compared with ultra-low temperature small deformation rolling, room temperature rolling can control the distribution of fine grain layer on the surface layer of the alloy. When the fine grain layer is distributed in the surface layer of the alloy and the coarse grain is distributed in the central layer, the coupling distribution of coarse and fine grains presents a gradient structure, which is conducive to the coordinated deformation between coarse/fine grains to improve the mechanical properties of the alloy [Citation36–39]. Accordingly, the #A alloy with the heterogeneous gradient structure can exhibit a high average plastic strain ratio of 0.716, but the #B alloy with a different heterogeneous structure (i.e. a fine grain layer in the center of sheet) has a slightly reduced r value of 0.699 (as shown in ). Therefore, it is necessary to investigate the microstructure control and formation mechanism of the gradient structures in Al-Zn-Mg-Cu alloys.
The sides of the 2 mm cold-rolled alloys in the rolling direction were observed using SEM, as shown in Figure . There are a large number of precipitates distributed along the rolling direction near the surface layer of the 2 mm alloy sheet, while there are fewer precipitates in the central layer of the #A alloy, as shown in Figure (a)(b). Combined with EDS analysis, as shown in Figure (e)(f), these precipitates are mostly AlZnMgCu quaternary phases, and a small number of particles are AlCuNi. Accordingly, the cold-rolled microstructure images of the #B alloy are given to show the fine grain zones formed by small deformation rolling process at the ultra-low temperature, as shown in Figure (c)(d). It can be confirmed that the heterogeneous distribution of the precipitates can be formed in the cold rolled alloy by coupling control of thermomechanical processing parameters, such as the different gradient distributions of precipitates in the #A and #B alloy sheets.
Figure 3. Precipitates distribution. (a) SEM microstructure of #A alloy in the cold rolled state, (b): local high magnification SEM image in (a), (c) SEM microstructure of #B alloy in the cold rolled state, (d): local high magnification SEM image in (c), (e): EDS pattern of particle A in (b), (f): EDS pattern of particle B in (b).

Furthermore, in order to accurately characterize the distribution of precipitates in the surface and central layers of the alloy, and to verify the heterogeneous distribution phenomenon observed in the SEM images, TEM identification along the <110 > Al zone axes was performed on the 3.5 mm annealed #A alloy sheet with gradient structure, as shown in Figure . In the surface layer of #A alloy, a large number of precipitates with fine sizes can be found in the sample, while the distribution of precipitates in the central layer is very sparse, which is consistent with the findings observed in the SEM images. Moreover, a large number of dislocations can be found around the precipitates in the surface layer, which indicates both the deformation zone around the precipitates and high strain energy storage have been formed in the surface layer. And then, the presence of dislocations and strain energy storage can further promote the rapid occurrence of recrystallization in the alloy during the high temperature heat treatment. Overall, the alloy surface layer has a high number density of precipitates and high strain energy storage, while the central layer has a lower number density of precipitates and strain energy storage. Accordingly, when the alloy is subjected to solid solution treatment, a large number of fine recrystallized grains can be formed in the surface layer, while a small number of coarse recrystallized grains can be produced in the central layer, resulting in a gradient grain structure as shown in Figure .
Figure 4. (a) Precipitates and dislocation distribution in the surface layer of 3.5 mm annealed sheet by TEM, (b) corresponding distribution in the center of 3.5 mm annealed sheet.

Additionally, in order to better reveal the forming mechanism of gradient structure of the developed Al-Zn-Mg-Cu alloy, a schematic diagram of gradient heterostructure formation controlled by room temperature rolling combined with double annealing process is given, as shown in Figure . Moreover, the mechanism on the formation of gradient heterostructures induced by the ultra-low temperature rolling process is presented in Supplementary Material. During rolling of the alloy at room temperature, a strong shear strain is generated between the contact surface of the roll and the alloy plate due to friction, however, owing to geometric symmetry, it is weakened or disappears in the central layer, resulting in a higher strain in the surface layer than in the central layer. This strain gradient induces different precipitation behaviors during the annealing process, resulting in a higher number density of precipitates in the surface layer, as shown in Figure (d)(e). And then, if cold rolling deformation of the alloy is continued, the stress gradient distribution characteristics existing between the surface and central layers are substantially enhanced, and a high strain energy storage and a large amount of dislocation distribution present in the surface layer of the alloy (as shown in Figure TEM images). A suitable intermediate annealing treatment can effectively regulate the stress distribution and control the distribution of precipitates in the alloy matrix. As shown in Figure (g), after intermediate annealing treatment (430°C/1 h), precipitates with heterogeneous distribution between the surface and central layers have been formed in the alloy with a thickness of 3.5 mm. With further cold rolling, the gradient stress distribution characteristics from the surface layer to the center layer in the alloy sheet become more obvious. Accordingly, the final 2 mm cold-rolled alloy sheet possesses a more pronounced surface-to-center layer gradient distribution feature. The formed strain storage energy can provide the driving force for the different recrystallization processes on the surface and central layers. And finally, the gradient distribution of precipitates and strain energy storage contributes to the formation of gradient recrystallization grain structure in solid solution treatment. Eventually, the surface layer with higher strain energy storage and higher number density of precipitates produces a large number of fine recrystallized grains during high temperature solution treatment, while the central layer of the alloy forms coarse grains with a smaller number of recrystallized grains, which ends up with a microstructure of recrystallized grains tending to a gradient distribution.
Figure 5. Schematic diagram of gradient formation with room temperature regulation (a) cast state, (b) 7 mm hot rolled state, (c) homogenized state, (d) 5 mm cold rolled state, (e) 5 mm intermediate annealed state, (f) 3.5 mm cold rolled state, (g) 3.5 mm intermediate annealed state, (h) 2 mm final cold rolled state, (i) solid solution recrystallization.
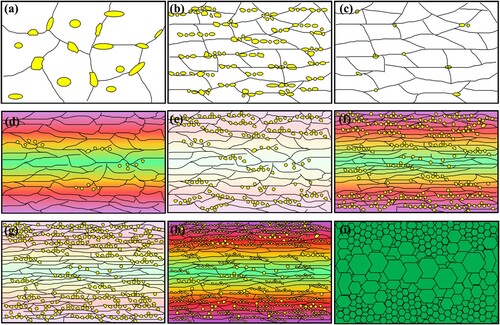
4. Conclusions
In summary, a novel thermomechanical processing was designed to effectively control the distribution of fine grains zones by coupling the heterogeneous distribution of precipitated phase particles, strain energy storage and dislocation density in the alloy. A heterogeneous microstructure with a gradient distribution of coarse/fine grains was constructed, resulting in a greatly enhanced average plastic strain ratio (reaching 0.716) in the pre-aged alloy. The forming mechanism of coupling coarse/fine grains with gradient distribution characteristics and its corresponding high formability mechanism were proposed.
Supplemental Material
Download MS Word (1.1 MB)Data availability
The raw/processed data required to reproduce these findings cannot be shared at this time due to technical or time limitations.
Disclosure statement
No potential conflict of interest was reported by the author(s).
Additional information
Funding
References
- Maeno T, Mori K, Yachi R. Hot stamping of high-strength aluminium alloy aircraft parts using quick heating. CIRP Ann. 2017;66:269–272.
- Hu JL, Wu XJ, Bo H. Dislocation density model and microstructure of 7A85 aluminum alloy during thermal deformation. J Cent South Univ. 2021;28:2999–3007.
- Zheng KL, Politis DJ, Wang LL, et al. A review on forming techniques for manufacturing lightweight complex—shaped aluminium panel components. Int J Lightweight Mater Manuf. 2018;1:55–80.
- Wang H, Luo YB, Friedman P, et al. Warm forming behavior of high strength aluminum alloy AA7075. Trans Nonferrous Met Soc China. 2012;22:0–7.
- Tisza M, Czinege I. Comparative study of the application of steels and aluminium in lightweight production of automotive parts. Int J Lightweight Mater Manuf. 2018;1:229–238.
- Benedyk JC. Mater Des Manuf Lightweight Veh. Woodhead Publishing Limit; 2010; 79–113.
- Wu XL, Jiang P, Chen L, et al. Extraordinary strain hardening by gradient structure. Proc Natl Acad Sci USA. 2014;111:7197–7201.
- Oliaei M, Jamaati R. Improvement of the strength-ductility-toughness balance in interstitial-free steel by gradient microstructure. Mater Sci Eng A. 2022;845:143237.
- Zhu Y, Ameyama K, Anderson PM, et al. Heterostructured materials: superior properties from hetero-zone interaction. Mater Res Lett. 2021;9(1):1–31.
- Yuan LL, Guo MX, Habraken AM, et al. Extremely improved formability of Al-Zn-Mg-Cu alloys via micro-domain heterogeneous structure. Mater Sci Eng A. 2022;837:142737.
- Xiong ZF, Jiang Y, Yang M, et al. Achieving superior strength and ductility in 7075 aluminum alloy through the design of multi-gradient nanostructure by ultrasonic surface rolling and aging. J Alloys Compd. 2022;165669.
- Yuan LL, Guo MX, Liu ZY, et al. Enhanced stiffness of Al-Zn-Mg-Cu alloys via heterogeneous structure of soft and hard microdomains. Mater Sci Eng A. 2022;841:143028.
- Pan T, Ysa B, Hja B, et al. Effect of Zn content on the microstructure and mechanical properties of as-cast Al-Zn-Mg-Cu alloy with medium Zn content. J Mater Res Technol. 2022;18:2620–2630.
- Bae JW, Moon J, Jang MJ. Trade-off between tensile property and formability by partial recrystallization of CrMnFeCoNi high-entropy alloy. Mater Sci Eng A. 2017;20:323–331.
- Shukla S, Wang TH, Cotton S. Hierarchical microstructure for improved fatigue properties in a eutectic high entropy alloy. Scr Mater. 2018;156:105–109.
- Wang YM, Ma E. Three strategies to achieve uniform tensile deformation in a nanostructured metal. Acta Mater. 2004;52:1699–1709.
- Ma E, Zhu T. Towards strength-ductility synergy through the design of heterogeneous nanostructures in metals. Mater Today. 2017;20:323–331.
- Wu XL, Yang MX, Yuan FP. Heterogeneous lamella structure unites ultrafine-grain strength with coarse-grain ductility. Proc Natl Acad Sci USA. 2015;112:14501–14505.
- He JY, Wang H, Huang HL, et al. A precipitation-hardened high-entropy alloy with outstanding tensile properties. Acta Mater. 2016;102:187–196.
- Zhang W, Ma ZC, Zhao HW, et al. Refinement strengthening, second phase strengthening and spinodal microstructure-induced strength-ductility trade-off in a high-entropy alloy. Mater Sci Eng A. 2022;847:143343.
- Wu XL, Zhu YT. Gradient and lamellar heterostructures for superior mechanical properties. MRS Bull. 2021;46(3):244–249.
- Fan J, Zhu L, Lu J, et al. Theory of designing the gradient microstructured metals for overcoming strength-ductility trade-off. Scr Mater. 2020;184:41–45.
- Yuan LL, Guo MX, Habraken AM, et al. Extremely improved formability of Al-Zn-Mg-Cu alloys via micro-domain heterogeneous structure. Mater Sci Eng A. 2022;837:142737.
- Yuan LL, Guo MX, Zhang JS, et al. Synergy in hybrid multi-scale particles for the improved formability of Al-Zn-Mg-Cu alloys. J Mater Res Technol. 2021;10:1143–1157.
- Shabadi R, Suwas S, Kumar S, et al. Texture and formability studies on AA7020 Al alloy sheets. Mater Sci Eng A. 2012;558:439–445.
- Jeon JG, Shin JH, Shin SE, et al. Improvement in the anisotropic mechanical properties and formability of Al–Si–Mg–Cu-based alloy sheets. Mater Sci Eng A. 2021;799:140199.
- Dong GJ, Zhao CC, Peng YX, et al. Hot granules medium pressure forming process of AA7075 conical parts. Chin J Mech Eng. 2015;28(3):580–591.
- Wang XF, Guo MX, Chapuis A, et al. Effect of solution time on microstructure, texture and mechanical properties of Al–Mg–Si–Cu alloys. Mater Sci Eng A. 2015;644:137–151.
- Chen Y, Clausen AH, Hopperstad OS, et al. Stress–strain behaviour of aluminium alloys at a wide range of strain rates. Int J Solids Struct. 2009;46(21):3825–3835.
- Reyes A, Hopperstad OS, Lademo OG, et al. Modeling of textured aluminum alloys used in a bumper system: material tests and characterization. Comput Mater Sci. 2006;37(3):246–268.
- Tajally M, Emadoddin E. Mechanical and anisotropic behaviors of 7075 aluminum alloy sheets. Mater Des. 2011;32(3):1594–1599.
- Wang XF, Liu H, Tang XB. A comparison study of microstructure, texture and mechanical properties between two 6xxx aluminum alloys. Metall Res Technol. 2021;118:211.
- Huang J, Jiang YG, Jiang FQ, et al. The improved mechanical anisotropy of a commercial Al–Cu–Mg–Mn–Si (2017) aluminum alloy by cross rolling. Adv Eng Mater. 2022;24(3):2100831.
- Sidor J, Petrov R H, Kestens L AI. Deformation, recrystallization and plastic anisotropy of asymmetrically rolled aluminum sheets. Mater Sci Eng A. 2010;528(1):413–424.
- Wu XL, Yang MX, Li RG, et al. Plastic accommodation during tensile deformation of gradient structure. Sci China Mater. 2021;64(6):1534–1544.
- Wu X, Zhu Y, Lu K. Ductility and strain hardening in gradient and lamellar structured materials. Scr Mater. 2020;186:321–325.
- Wu X L, Jiang P, Chen L, et al. Synergetic strengthening by gradient structure. Mater Res Lett. 2014;2(4):185–191.
- Fang XT, Li ZK, Wang YF, et al. Achieving high hetero-deformation induced (HDI) strengthening and hardening in brass by dual heterostructures. J Mater Sci Technol. 2022;98:244–247.
- Yang M, Pan Y, Yuan F, et al. Back stress strengthening and strain hardening in gradient structure. Mater Res Lett. 2016;4(3):145–151.