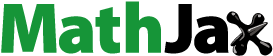
ABSTRACT
Deformation incompatibility in Ti/Nb laminates under uniaxial tension was revealed by in-situ neutron diffraction. During uniform deformation of the bulk laminates, the hard Nb constrained by the soft Ti showed moderate work hardening and only slightly decreased flow stress. The mechanical incompatibility accumulated in both elastic and elasto-plastic regimes between the metals lead to pronounced hetero-deformation induced (HDI) strengthening, and the HDI stress was comparable to the maximum phase-to-phase interaction. The HDI hardening and interphase stress showed consistent evolution trends, implying that the interaction between dissimilar metals can be used as an important indicator for evaluating HDI strengthening and hardening.
GRAPHICAL ABSTRACT
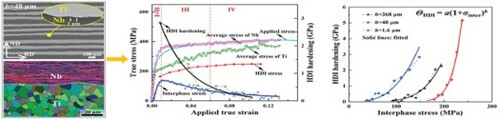
IMPACT STATEMENT
The phase-to-phase interaction is found to be an important indicator for evaluating the HDI strengthening and hardening in heterogeneous laminates, and the microstress analysis can guide the design of heterostructures.
Introduction
Heterogeneous structure, also known as heterostructure, is attracting ever-increasing attention as an effective strategy to overcome the strength-ductility trade-off [Citation1–4]. Heterostructured materials contain hard and soft domains with dramatically different mechanical properties, such as ultrafine-grained (UFG)/nano-grained (NG) domains with the higher strength and coarse-grained (CG) domains with the lower strength. Several types of heterostructures, including gradient [Citation5–9], bimodal [Citation10,Citation11], laminated [Citation12–15], heterogeneous lamellar [Citation1,Citation16], harmonic [Citation17,Citation18] structures, etc., have been proposed to obtain superior strength-ductility synergy and enhanced work hardening. Although the microstructural characteristics in those materials are different, the fundamental deformation physics, namely the micromechanical behavior regulated by deformation incompatibility and strain/stress partitioning across the soft/hard domain interfaces is universal [Citation2].
The strengthening and work hardening in heterostructured materials are attributed to the hetero-deformation induced (HDI) strengthening and hardening, respectively [Citation19,Citation20]. The HDI hardening is defined as:
(1)
(1) where σHDI is the HDI stress and ϵ is the applied true strain, and ΘHDI is the slope of the HDI stress-true strain curve. This mechanism is closely associated with the accumulation of geometrically necessary dislocations (GNDs) that are induced by plastic heterogeneity [Citation19]. When a deformed material is in the regime of elasto-plastic transition, namely that plastic deformation takes place preferentially in the soft domain while the hard domain still deforms elastically, GNDs will be accumulated at the domain interfaces. The GND pile-up produces a long-range internal stress, i.e. back stress in the soft domain. Concurrently, the stress concentration at the head of the GND pile-up exerts strong forward stress in the adjacent hard domain. Therefore, HDI stress is a combined effect of back stress and forward stress. When the bulk material yields, strain partitioning between the different domains will occur, and the soft domain sustains the higher plastic strains than the hard domain [Citation21,Citation22]. Correspondingly, GNDs are accumulated inevitably owing to the plastic strain gradient across the domain interfaces, leading to the HDI hardening and the enhanced ductility for the material. Specifically, the HDI strengthening/hardening are closely related to the mechanical incompatibility between the neighboring domains. This then raises one question, i.e. how is the evolution of deformation incompatibility within a heterostructured material related to the HDI strengthening and hardening? On the other hand, the accumulation of GNDs during deformation leads to the development of internal stress, which changes the stress state and mechanical response of different domains and enables dynamic stress/strain transfer between the domains [Citation21,Citation23–25]. However, it is still unclear that how the constituent domains interact and coordinate with each other during co-deformation. In particular, the quantitative relationship between the interaction of soft and hard domains and HDI strengthening/hardening remains an open issue. Solving these problems is a prerequisite for understanding the deformation micromechanisms in heterostructured materials and designing materials with high performances.
In that context, it is urgent to accurately reveal the stress/strain partitioning in heterostructured materials under external loading together with its effect on micromechanical behaviors and global properties with the help of advanced characterization techniques. Wang et al. designed a prestraining-peeling-retesting procedure to quantitatively estimate stress–strain behavior of the NG brass layers in a Cu/brass laminate [Citation26]. Based on the in-situ synchrotron based high-energy X-ray diffraction technique, Wu et al. obtained the lattice strain evolutions in an interstitial-free steel that is processed by the surface mechanical attrition treatment, through the layer-by-layer measurements [Citation21]. Accordingly, the evolution of plastic accommodation in the gradient structure was clarified. However, the application of those techniques in revealing the correlation between macro- and micro- mechanical behaviors in heterostructured materials is very limited. Here, we select the multilayered Ti/Nb composites with the simple lamellar structure as the model materials. By employing in-situ neutron diffraction technique, the stress–strain responses of respective constituents and the corresponding deformation incompatibility in the laminates under uniaxial tension are characterized quantitatively. Surprisingly, the Nb layers with ultra-fine grain thickness exhibit unique work hardening behaviors and sustainable tensile strains. Further microstress analysis reveals that deformation incompatibility within the laminates is closely related to the evolution of HDI stress in bulk materials. This work provides direct evidence for the source of HDI strengthening and hardening in heterogeneous laminates.
Experimental
The laminates consisting of alternatively stacked pure titanium (Ti) and pure niobium (Nb) plates with a thickness of 1 mm were fabricated by accumulative roll bonding (see details in Ref. [Citation25]). Then the laminates were annealed at 575°C for 1 h. In this paper, to obtain universal conclusions three laminates with the nominal layer thickness (h) of 368, 48 and 1.6 μm were investigated, where the nominal layer thickness is defined as the total thickness of each laminate divided by the number of constituent metal layers. The volume fraction of Nb (fNb) and the number of layers in each laminate are listed in Supplementary Table S1. Microstructures of the laminates were observed using a JEOL JSM-7001F scanning electron microscope (SEM) and a Zeiss Crossbeam 550 microscope equipped with the electron backscatter diffraction (EBSD) detector. In-situ neutron diffraction tests during room-temperature uniaxial tension were performed on the VULCAN diffractometer at the Spallation Neutron Source (SNS), Oak Ridge National Laboratory (ORNL), with the experimental setup and sample geometry detailed in Ref [Citation27]. To make sure that deformation occurs in the sample center, a tapered gauge dimension with total length of 15 mm and width of 2.6 mm was designed. The gauge thickness was in a range of 1.74∼2.45 mm. In-situ uniaxial tensile tests were carried out at a nominal strain rate of ∼5 × 10−6 s−1 to ensure good data statistics and minimize fitting statistics error. Throughout the continuous loading, neutron diffraction patterns were recorded successively and subsequently chopped into 7 min intervals using the VULCAN Data Reduction and Interactive Visualization software (VDRIVE). Single peak fitting was used to track the orientation-specific lattice spacing (dhkl), and then the corresponding lattice strain and average engineering stress of each individual metal (a stress averaged over the differently oriented grains relative to their volume fractions) were evaluated, respectively (Note (i) in Supplementary material). Further, interphase stress within one laminate was calculated as the difference in stress between the constituent metals [Citation28–30]. To quantitatively evaluate the evolution of HDI stress, loading-unloading-reloading (LUR) tests [Citation19] were performed on a Shimadzu AG-Xplus machine at a loading strain rate of 10−3 s−1 and an unloading rate of 250 N·min−1 to the minimum load of 80 N. Dog-bone shaped tensile samples with a gauge length of 12 mm and a width of 3 mm were used.
Results and discussion
Figure (a–c) are SEM images showing clear Ti/Nb interfaces in the laminates. Our previous study on the ARB processed Ti/Nb laminates has shown that the heterophase interfaces are sharp and without amorphization and intermetallic compounds formed at the interfaces [Citation25]. Microstructures in each individual metal across the interfaces were further characterized by EBSD, as shown in Figure (d–f). The Ti layers are featured by the recrystallized coarse grains with an average grain size of several tens of microns. In contrast, in Nb layers with the higher thermal stability, non-recrystallized grains with dense dislocations are found, and the thickness of Nb grains in the laminates with h = 48 μm and h = 1.6 μm is ultrafine (below 1 μm). Such a dramatic microstructure heterogeneity is expected to produce strong constraints between the neighboring metals in the deformed bulk laminates [Citation23,Citation31].
Figure 1. Typical lamellar morphology and detailed microstructure across heterophase interfaces in the Ti/Nb laminates: (a) h = 368 μm (b) h = 48 μm and (c) h = 1.6 μm. The insets in (a)–(c) are high-magnification micrographs showing the sharp interfaces. The white dotted lines in (d)–(f) represent the heterophase interfaces between the Ti and Nb constituents. fNb is the volume fraction of Nb.
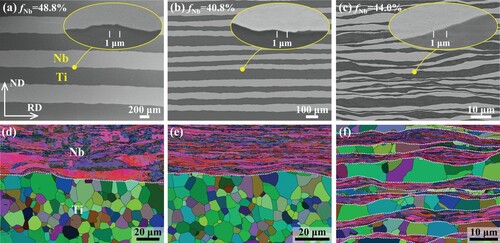
Figure (a) shows the true stress–strain curves obtained during in-situ neutron diffraction tests. The laminates with nominal layer thicknesses of 368 and 48 μm display similar combinations of yield strength (∼270 MPa) and uniform elongation (∼10%). When the layer thickness decreases to 1.6 μm, yield strength of the laminate increases dramatically, and is comparable to that of Ti-28at.%Nb alloy [Citation32]. However, uniform elongation terminates prematurely before the significant necking occurs, due to the strain localization caused by macroscopic shear bands (to be discussed below). Based on the lattice strains measured by in-situ neutron diffraction, the evolution of average engineering stress in respective metals with the applied strain can be derived [Citation25,Citation33]. Further, as shown in Figure (b–d), the true stress (vertical axis) is calculated by multiplying average engineering stress with (1+ϵ), where ϵ is the applied strain. Three typical mechanical behaviors are found in the Nb constituent with ultra-fine grain thickness. First, the Nb layers show the higher flow stress and moderate work hardening, which is in sharp contrast to that of UFG Nb alloys [Citation34]. UFG/NG metals generally exhibit very limited uniform elongation and unstable work hardening under tensile loading [Citation35]. Here, taking the laminate with a nominal layer thickness of 48 μm as an example, during plastic deformation the true stress increases slowly from 356 MPa to 412 MPa (corresponding to 0.13 true strain). Second, in all laminates the Nb constituent displays decent uniform elongations (even for the laminate with a nominal layer thickness of 1.6 μm, Figure S1 in Supplementary material), which is attributed to the delayed strain localization by constraints between the constituent metals. Third, during uniform elongation of the bulk laminates, Nb shows the continuously decreased flow stress (Figure S1, Supplementary material), indicating the gradually decreased ability to bear load in this metal. In contrast, in homogeneous metals the ever-increasing flow stress is a prerequisite for maintaining the uniform elongation during tensile deformation [Citation36]. The mechanical properties of Nb layers in the studied Ti/Nb laminates agree well with that of UFG brass layers in the Cu/brass laminates under tensile loading [Citation26].
Figure 2. (a) True stress–strain curves of the Ti/Nb laminates obtained from in-situ neutron diffraction tests. The stress–strain curves of initial pure metals and Ti-28at.%Nb alloy[Citation32] obtained from conventional tensile tests are also provided. (b)–(d) Evolutions of average true stress of each constituent metal and interphase stress as a function of applied true strain in the laminates with initial layer thicknesses of 368, 48 and 1.6 μm.
![Figure 2. (a) True stress–strain curves of the Ti/Nb laminates obtained from in-situ neutron diffraction tests. The stress–strain curves of initial pure metals and Ti-28at.%Nb alloy[Citation32] obtained from conventional tensile tests are also provided. (b)–(d) Evolutions of average true stress of each constituent metal and interphase stress as a function of applied true strain in the laminates with initial layer thicknesses of 368, 48 and 1.6 μm.](/cms/asset/2159a33c-083e-4604-9f5c-4de702f8aaae/tmrl_a_2128916_f0002_oc.jpg)
In addition, Figure (b–d) also present the phase-to-phase interaction i.e. the interphase stress (σinter, indicated by the blue circle symbols). The blue solid lines are the fitted flow curves showing the evolution tendency. Due to the elastic mismatch, mechanical incompatibility between two constituent metals is expected to occur in the elastic regime, and thus the interphase stress increases with the elevated strain (stage I). When micro-yielding occurs in the Ti layers, a load transfer from ‘soft' Ti to ‘hard' Nb becomes apparent, resulting in the mild development of interphase stress (stage II). After macro-yielding of the Ti/Nb laminates (∼0.01 true strain), the Ti layers are hardened remarkably, and the deformation incompatibility between Ti and Nb becomes less significant. Therefore, the interphase stress decreases significantly (stage III). When the applied true strain reaches ∼0.06, interphase stress in each laminate decreases moderately, and the value comes to a plateau in the late stage of deformation (stage IV). As all metal layers in the laminates are subjected to the same applied tensile strain along the loading direction [Citation14,Citation37], the decreasing interphase stress after macro-yielding indicates the decreasing difference of plastic strains between the constituent metals, i.e. the occurrence of plastic accommodation. In fact, plastic accommodation and deformation incompatibility are often coupled in heterogeneous materials, and plastic accommodation occurs soon after yielding and continues throughout the whole deformation [Citation21].
Further, LUR tests were performed to evaluate the evolution of HDI stress in each laminate, as displayed in Figure . To clearly show the trends, the HDI stress of an additional Ti/Nb laminate with the initial layer thickness of 5 μm is also presented. Figure (a) shows the true stress–strain curves of the laminates during the LUR tests. The equation proposed by Yang et al. [Citation38] is used to calculate the HDI stress, i.e.
(2)
(2) where σu and σr are the elastic limit during unloading and reloading, respectively, as defined in the inset of Figure (b). As shown in this figure, in four laminates the evolutions of HDI stress with the increasing strain are consistent. Namely, at low plastic strains (<0.06 true strain), the HDI stress increases significantly with deformation, due to the significant strain partitioning between constituent metals. However, at higher strain levels, the HDI stress tends to be saturated due to the weakened interaction between the metals. Fang et al. also found in a brass with heterogeneous lamellar structure that under high plastic strains, conventional forest dislocation hardening dominates the strain hardening [Citation20]. Moreover, under one constant applied strain, the HDI stress of the Ti/Nb laminates increases monotonically with decreasing layer thickness and the laminate with the initial layer thickness of 1.6 μm shows the highest HDI stress. This is in good accordance with the significant increment of interface constraint effects with the reduced layer thickness in Ti/Al multilayered composites as revealed by the combination of in-situ neutron diffraction and digital image correlation (DIC) techniques [Citation14]. The trend also agrees with that in the Cu/brass laminates predicted by constitutive models [Citation39].
Figure 3. (a) LUR curves of the laminates with different initial layer thicknesses. (b) Evolution of HDI stress as a function of true strain deduced from the LUR curves. The inset in (b) is the schematic of an unloading-reloading loop.

When comparing the evolutions of HDI stress and interphase stress with straining in the Ti/Nb laminates, several common features can be captured (Figure (a)). First, at the macroscopic yield point (corresponding to ∼0.01 true strain, i.e. the starting point of stage III), the HDI stress is comparable to the interphase stress, which is corresponding to the maximum interphase stress. This means that the mechanical incompatibility accumulated in elastic and elasto-plastic deformation regimes leads to pronounced HDI strengthening, and determines the HDI stress in the current laminates. Second, with increasing plastic strain (stage III and IV), evolution rate of HDI stress and interphase stress gradually decrease, and the both values come to a plateau at the late stage of deformation. In order to identify the relationship between deformation incompatibility and HDI strengthening, the evolution of HDI hardening as a function of applied true strain is also plotted in Figure (a). It is evident that the HDI hardening decreases with the decreasing interphase stress, namely, the hardening induced by heterostructures decreases with the deformation accommodation between constituent metals. Figure (b) shows the curves of HDI hardening and the interphase stress evolution rate with deformation. The interphase stress evolution rate is the derivative of interphase stress with respect to the applied true strain. When Ti/Nb laminates yield, the HDI hardening drops remarkably, while the evolution rate of interphase stress decreases gradually. When entering stage IV, the evolution rate of interphase stress becomes stable and even converges to zero. Concomitantly, the HDI hardening remains almost unchanged. This means that HDI hardening shows the consistent evolution trend as interphase stress. The quantitative relationship between interphase stress (σinter) and HDI hardening (ΘHDI) for the studied laminates can be represented by a nonlinear formula, i.e. , where a and b are fitting parameters (Table S2, Supplementary material). As shown in Figure (c), in all plastically deformed laminates the HDI hardening decreases exponentially with decreasing interphase stress. This implies that HDI hardening has a direct relationship with deformation incompatibility between the constituent metals. Therefore, the phase-to-phase interaction could be served as an important indicator for evaluating the HDI strengthening and hardening for the laminated composites.
Figure 4. (a) Evolution of interphase stress, HDI stress and HDI hardening as a function of applied true strain in the laminates. (b) Comparison of HDI hardening and interphase stress evolution rate with tensile deformation. The dashed lines with solid circles denote HDI hardening, and the solid lines are fitted curves indicating evolution trends of the data. The open circles denote evolution rates of interphase stress. (c) Plot of the HDI hardening vs. the interphase stress for the studied laminates. The solid lines are the fitted lines using a power function, and the grey arrows indicate the direction of the increased tensile loading.
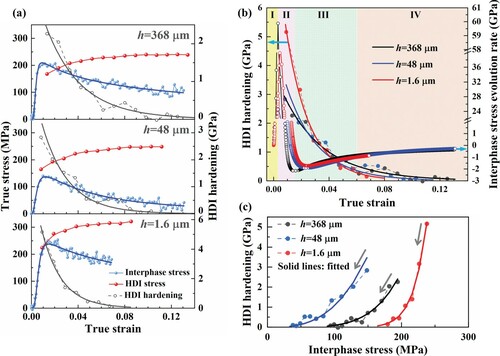
Conclusion
In summary, to quantitatively reveal deformation incompatibility in the laminates composed of coarse-grained Ti and Nb with ultra-fine grain thickness under tensile loading, mechanical responses of each constituent metal are characterized by in-situ neutron diffraction. The Nb layers constrained by the softer Ti layers show moderate work hardening and only slightly reduced flow stress during uniform deformation, which is distinctly different from that of UFG Nb alloys with uniform structures. When the laminates yield, the mechanical incompatibility accumulated in both elastic and elasto-plastic deformation regimes leads to pronounced HDI strengthening, and the HDI stress value is comparable to the maximum interphase stress. As the applied strain increases, HDI hardening and interphase stress show the similar evolution trend, indicating that HDI hardening is directly related to deformation incompatibility between the constituent Ti and Nb. Therefore, the interaction between dissimilar metals, i.e. interphase stress, could be served as an important indicator for evaluating the HDI strengthening and hardening for laminated composites. These findings provide crucial insight into the strengthening and toughening mechanisms caused by inhomogeneous deformation in heterostructured laminates, and potentially guide the development of high-performance structural materials.
Supplemental Material
Download MS Word (177.1 KB)Acknowledgements
The authors would like to thank Dr. Ke An and Dr. Yan Chen at the BL-7 beamline at the Spallation Neutron Source (SNS) at Oak Ridge National Laboratory (ORNL) for assistance with the neutron diffraction measurements. Neutron diffraction work was carried out at the Spallation Neutron Source (SNS), a DOE Office of Science User Facility operated by the Oak Ridge National Laboratory.
Disclosure statement
No potential conflict of interest was reported by the author(s).
Additional information
Funding
References
- Wu XL, Yang MX, Yuan FP, et al. Heterogeneous lamella structure unites ultrafine-grain strength with coarse-grain ductility. Proc Natl Acad Sci USA. 2015;112(47):14501–14505. DOI:10.1073/pnas.1517193112.
- Wu XL, Zhu YT. Heterogeneous materials: a new class of materials with unprecedented mechanical properties. Mater Res Lett. 2017;5(8):527–532. DOI:10.1080/21663831.2017.1343208.
- Zhu YT, Ameyama K, Anderson PM, et al. Heterostructured materials: superior properties from hetero-zone interaction. Mater Res Lett. 2021;9(1):1–31. DOI:10.1080/21663831.2020.1796836.
- Yu YS, Hu B, Gao ML, et al. Determining role of heterogeneous microstructure in lowering yield ratio and enhancing impact toughness in high-strength low-alloy steel. Int J Miner Metall Mater. 2021;28:816–825. DOI:10.1007/s12613-020-2235-5.
- Fang TH, Li WL, Tao NR, et al. Revealing extraordinary intrinsic tensile plasticity in gradient nano-grained copper. Science. 2011;331(6024):1587–1590. DOI:10.1126/science.1200177.
- Wei Y, Li Y, Zhu L, et al. Evading the strength–ductility trade-off dilemma in steel through gradient hierarchical nanotwins. Nat Commun. 2014;5:3580. DOI:10.1038/ncomms4580.
- Wu XL, Jiang P, Chen L, et al. Extraordinary strain hardening by gradient structure. Proc Natl Acad Sci USA. 2014;111(20):7197–7201. DOI:10.1073/pnas.1324069111.
- Cheng Z, Zhou H, Lu Q, et al. Extra strengthening and work hardening in gradient nanotwinned metals. Science. 2018;362:6414. DOI:10.1126/science.aau1925.
- Wang YF, Huang CX, Wang MS, et al. Quantifying the synergetic strengthening in gradient material. Scripta Mater. 2018;150:22–25. DOI:10.1016/j.scriptamat.2018.02.039.
- Wang Y, Chen M, Zhou F, et al. High tensile ductility in a nanostructured metal. Nature. 2002;419:912–915. DOI:10.1038/nature01133.
- Liu YF, Cao Y, Mao QZ, et al. Critical microstructures and defects in heterostructured materials and their effects on mechanical properties. Acta Mater. 2020;189:129–144. DOI:10.1016/j.actamat.2020.03.001.
- Beyerlein IJ, Mayeur JR, Zheng S, et al. Emergence of stable interfaces under extreme plastic deformation. Proc Natl Acad Sci USA. 2014;111(12):4386–4390. DOI:10.1073/pnas.1319436111.
- Ma XL, Huang CX, Xu WZ, et al. Strain hardening and ductility in a coarse-grain/nanostructure laminate material. Scripta Mater. 2015;103:57–60. DOI:10.1016/j.scriptamat.2015.03.006.
- Huang CX, Wang YF, Ma XL, et al. Interface affected zone for optimal strength and ductility in heterogeneous laminate. Mater Today. 2018;21(7):713–719. DOI:10.1016/j.mattod.2018.03.006.
- Wang YF, Yang MX, Ma XL, et al. Improved back stress and synergetic strain hardening in coarse-grain/nanostructure laminates. Mater Sci Eng A. 2018;727:113–118. DOI:10.1016/j.msea.2018.04.107.
- Li J, Cao Y, Gao B, et al. Superior strength and ductility of 316L stainless steel with heterogeneous lamella structure. J Mater Sci. 2018;53(14):10442–10456. DOI:10.1007/s10853-018-2322-4.
- Sawangrat C, Kato S, Orlov D, et al. Harmonic-structured copper: performance and proof of fabrication concept based on severe plastic deformation of powders. J Mater Sci. 2014;49(19):6579–6585. DOI:10.1007/s10853-014-8258-4.
- Park HK, Ameyama K, Yoo J, et al. Additional hardening in harmonic structured materials by strain partitioning and back stress. Mater Res Lett. 2018;6(5):261–267. DOI:10.1080/21663831.2018.1439115.
- Zhu YT, Wu XL. Perspective on hetero-deformation induced (HDI) hardening and back stress. Mater Res Lett. 2019;7(10):393–398. DOI:10.1080/21663831.2019.1616331.
- Fang XT, He GZ, Zheng C, et al. Effect of heterostructure and hetero-deformation induced hardening on the strength and ductility of brass. Acta Mater. 2020;186:644–655. DOI:10.1016/j.actamat.2020.01.037.
- Wu X, Yang M, Li R, et al. Plastic accommodation during tensile deformation of gradient structure. Sci China Mater. 2021;64:1534–1544. DOI:10.1007/s40843-020-1545-2.
- Estrin Y, Beygelzimer Y, Kulagin R, et al. Architecturing materials at mesoscale: some current trends. Mater Res Lett. 2021;9(10):399–421. DOI:10.1080/21663831.2021.1961908.
- Huang M, Xu C, Fan GH, et al. Role of layered structure in ductility improvement of layered Ti-Al metal composite. Acta Mater. 2018;153:235–249. DOI:10.1016/j.actamat.2018.05.005.
- Wan T, Cheng Z, Bu L, et al. Work hardening discrepancy designing to strengthening gradient nanotwinned Cu. Scripta Mater. 2021;201:113975. DOI:10.1016/j.scriptamat.2021.113975.
- Jiang S, Peng Lin R, Hegedűs Z, et al. Micromechanical behavior of multilayered Ti/Nb composites processed by accumulative roll bonding: An in-situ synchrotron X-ray diffraction investigation. Acta Mater. 2021;205:116546. DOI:10.1016/j.actamat.2020.116546.
- Wang Y, Wei Y, Zhao Z, et al. Mechanical response of the constrained nanostructured layer in heterogeneous laminate. Scripta Mater. 2022;207:114310. DOI:10.1016/j.scriptamat.2021.114310.
- Magagnosc DJ, Field DM, Meredith CS, et al. Superior strength and ductility in a low density duplex steel studied by in situ neutron diffraction. Mater Sci Eng A. 2021;799:140252. DOI:10.1016/j.msea.2020.140252.
- Jia N, Peng Lin R, Wang YD, et al. Interactions between the phase stress and the grain-orientation-dependent stress in duplex stainless steel during deformation. Acta Mater. 2006;54(15):3907–3916. DOI:10.1016/j.actamat.2006.04.019.
- Jia N, Peng Lin R, Wang YD, et al. Micromechanical behavior and texture evolution of duplex stainless steel studied by neutron diffraction and self-consistent modeling. Acta Mater. 2008;56(4):782–793. DOI:10.1016/j.actamat.2007.10.040.
- Cui YM, Li CH, Zhang CS, et al. Effect of initial microstructure on the micromechanical behavior of Ti-55531 titanium alloy investigated by in-situ high-energy X-ray diffraction. Mater Sci Eng A. 2020;772:138806. DOI:10.1016/j.msea.2019.138806.
- Wang Y, Huang C, Li Z, et al. Shear band stability and uniform elongation of gradient structured material: role of lateral constraint. Extreme Mech Lett. 2020;37:100686. DOI:10.1016/j.eml.2020.100686.
- Kim HY, Hashimoto S, Kim JI, et al. Mechanical properties and shape memory behavior of Ti-Nb alloys. Mater Trans. 2004;45(7):2443–2448. DOI:10.2320/matertrans.45.2443.
- Johansson J, Odén M, Zeng XH. Evolution of the residual stress state in a duplex stainless steel during loading. Acta Mater. 1999;47(9):2669–2684. DOI:10.1016/S1359-6454(99)00149-4.
- Niendorf T, Canadinc D, Maier HJ, et al. Microstructure–mechanical property relationships in ultrafine-grained NbZr. Acta Mater. 2007;55(19):6596–6605. DOI:10.1016/j.actamat.2007.08.015.
- Ovid'ko IA, Valiev RZ, Zhu YT. Review on superior strength and enhanced ductility of metallic nanomaterials. Prog Mater Sci. 2018;94:462–540. DOI:10.1016/j.pmatsci.2018.02.002.
- Zhu YT, Wu XL. Ductility and plasticity of nanostructured metals: differences and issues. Mater Today Nano. 2018;2:15–20. DOI:10.1016/j.mtnano.2018.09.004.
- Wang YF, Wang MS, Fang XT, et al. Extra strengthening in a coarse/ultrafine grained laminate: role of gradient interfaces. Int J Plast. 2019;123:196–207. DOI:10.1016/j.ijplas.2019.07.019.
- Yang M, Pan Y, Yuan F, et al. Back stress strengthening and strain hardening in gradient structure. Mater Res Lett. 2016;4(3):145–151. DOI:10.1080/21663831.2016.1153004.
- Zhao J, Zaiser M, Lu X, et al. Size-dependent plasticity of hetero-structured laminates: A constitutive model considering deformation heterogeneities. Int J Plast. 2021;145:103063. DOI:10.1016/j.ijplas.2021.103063.