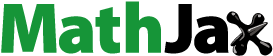
Abstract
WC is an indispensable constituent when producing Ti(C, N)-based cermets, yet its role on microstructure and the mechanism remain blurred. Herein, based on the CALPHAD approach, we designed and synthesized the cermets containing unsaturated and supersaturated WC. Formation of a macro-gradient structure was observed, encompassing an undissolved WC area, a WC dissolution area, and a (Ti, W)(C, N) solid-solution area. Such a unique structure has not been reported in cermet systems, which originates from the denitrification-induced W solubility change in Ti(C, N), as clarified computationally. Thus, this work shows the usefulness of thermodynamic calculations in establishing composition-microstructure relationships in cermets.
GRAPHICAL ABSTRACT
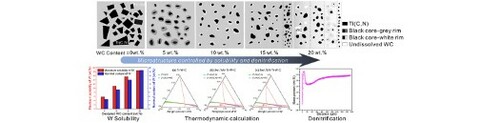
IMPACT STATEMENT
Novel macro-gradient structures in the Ti(C, N)-based cermet systems were observed for the first time, and the thermodynamic mechanisms were elucidated from the perspective of denitrification-induced W solubility change.
1. Introduction
Due to the environmental and cost concerns, lightweight Ti(C, N)-based cermets have drawn much industrial interests and appeared to outperform the WC-Co hard metals when machining cast iron and steel workpieces [Citation1–3]. At the same time, the addition of WC can practically improve the densification of Ti(C, N)-based cermets [Citation3, Citation4], which stimulates the interests to investigate the use of WC as an indispensable constituent when producing high-quality Ti(C, N)-based cermets. In recent years, extensive experimental efforts on WC induced microstructural changes in Ti(C, N)-based cermets have been conducted [Citation5–10]. Typically, a core-rim structure forms on the ceramic phase as a result of the WC addition, where the core is undissolved Ti(C, N) while the rim is (Ti, W)(C, N) solid-solution [Citation5]. In addition, the rim can be further differentiated into the light-contrast inner rim (also referred to as the inner white rim) with a high W content and the dark-contrast outer rim (also referred to as the outer grey rim) incorporating less W, based on the contrast difference under electron microscope. Lindahl et al. [Citation6] have reported that with the rise of WC content in a TiC-TiN-WC-Ni system, the difference between the inner white rim and outer grey rim vanishes, accompanying the simultaneous generation of undissolved white WC particles. Through covering a wide range of WC content (5–75 wt.%), Jung and Kang [Citation7] have observed the disappearance of grey rims in a Ti(C, N)-WC-Ni system once WC content exceeds 50 wt.%, a point at which W reaches the upper limit of solubility in both the Ni binder and the (Ti, W)(C, N) rim. Ahn et al. [Citation10] have suggested that the rim composition is predominantly affected by the maximum quantity of solutes available in the liquid binder at the sintering temperature, rather than the nominal carbide content. Although a degree of consensus has been reached on the WC addition and its resultant microstructural variations, the underlying thermodynamic mechanism remains to be explored.
Based on the above-mentioned experimental evidences, it can be inferred that the formation of (Ti, W)(C, N) rim phase is controlled by a two-step iterative process, namely the dissolution of W solutes in liquid Ni and their precipitation onto undissolved Ti(C, N) particles. As such, the solubility limit of W in liquid Ni could be a critical parameter that determines the morphology of Ti(C, N)-based cermets. This can be readily studied using thermodynamic calculations, while the relationships between composition and microstructure can serve as useful guidelines to further optimizations of Ti(C, N)-based cermets.
2. Materials and methods
In this work, the CALPHAD (CALculation of PHAse Diagrams) approach, being widely used in predicting phase constitutions and interpreting phase transitions [Citation11–15], was employed to design the cermet compositions based on the thermodynamic database CSUTDCC1 [Citation16]. To potentially amplify the changes in the core-rim structures that are governed by the dissolution-precipitation process during liquid-phase sintering, a high Ni binder content of 50 wt.% was selected on purpose. As shown in Figure , the maximum solubility of W in liquid Ni phase varies with the change of WC content in a Ti(C, N)-WC-50 wt.% Ni system, increasing from a solubility of 5.8 wt.% at a WC addition of 5.0 wt.% to that of 18.7 wt.% at a WC addition of 20.0 wt.%. Thus, the cermet system with 20.0 wt.% WC addition should reach the supersaturated condition.
Figure 1. Thermodynamically calculated solubility limits of W in liquid Ni binder phase in Ti(C, N)-WC-50 wt.% Ni system incorporating different WC contents (from 5.0 wt.% to 20.0 wt.%) at 1450°C. The nominal concentration of W at each WC content is also given for reference.

In this context, four groups of Ti(C, N)-WC-50 wt.% Ni cermets with different nominal WC contents (varying from 5.0 wt.% to 20.0 wt.%) were prepared from a powder mixture of WC, Ti(C, N), and Ni (See Table S1 in Supplementary Material for detailed information on raw powders used). After milling and drying, the raw powders were pressed and sintered under a vacuum condition at a maximum temperature of 1450 °C for 1 h (See Figure S1 in Supplementary Material for the temperature profile used). The denitrification behavior of cermets during sintering was investigated using a thermal analysis instrument (STA449F5-QMS403, Netzsch, Germany). The microstructure of cermets was studied using a scanning electron microscope (SEM, MIRA 3 LMH/LMU, TESCAN, Czech). The elemental distribution profiles of cermets were measured using a glow discharge emission spectrometer (GDA 750HP, Spectruma Analytik GmbH, Germany). Prior to the measurement, the surfaces of samples were cleaned by Ar (≥99.995%). The results obtained were calibrated using the nominal compositions of samples. The measured element concentration was quantified using Equations (1)–(4):
(1)
(1)
(2)
(2)
(3)
(3)
(4)
(4) where
is the element concentration,
is the sputtering rate,
is a constant,
is the light intensity,
is the element mass, m is the total mass, t is the measurement time,
is the element density, A is the measurement area, and h is the measurement depth. As the values of
, A,
and
are fixed, the relationship between h and t is established based on Equation (4).
3. Results and discussion
The as-sintered microstructure of cermets with the WC content varying from 5.0 wt.% to 20.0 wt.% is shown in Figure . In total five different contrasts can be detected in the interior of these cermets (A1 of Figure (a), B1 of Figure (b), C1 of Figure (c), and D1 of Figure (d)), namely the black core, the white rim, the grey rim, the white WC grain, and the light-grey Ni binder, which are consistent with previous studies [Citation6–8, Citation17–19]. Rimless grains which are absent in the cermet containing 5.0 wt.% WC (A1 of Figure (a)) start to emerge in the ones with higher WC concentrations (B1 of Figure (b), C1 of Figure (c), and D1 of Figure (d)). It has been suggested [Citation7] that formation of the W-rich white rim occurs at a temperature lower than the dissolution of Ti(C, N), thus the encapsulation effect brought by the white rim can hinder the subsequent generation of the Ti-rich grey rim. As the iterations of dissolution and precipitation continue, the W concentration of the rim phase can eventually reach an equilibrium with that of the binder phase, thus the contrast difference between the rim and binder diminishes and the visually ‘rimless' grains form. In addition, the presence of undissolved white WC grains at 20.0 wt.% WC addition (D1 of Figure (d)) suggests the attainment of supersaturated condition, which agrees well with the thermodynamic design (Figure ).
Figure 2. Scanning electron microscope (SEM) images of as-sintered Ti(C, N)-based cermets with different WC concentrations: (a) 5.0 wt.%, (b) 10.0 wt.%, (c) 15.0 wt.%, and (d) 20.0 wt.%. High-magnification images showing the details of microstructures in different regions from center to surface are also provided.

Through the comparison between the interior and subsurface microstructures of different cermets, it is also interesting to note that the ones with increased WC contents exhibit a high propensity towards the formation of macro-gradient structures. To be specific, it can be seen from A1 and A2 of Figure (a) that the core-rim structure in the interior region exhibits a spherical shape whereas it reveals a polyhedral shape in the subsurface region. Likewise, the shape difference also occurs in B1 and B2 of Figure (b), but the rim structure in B2 is brighter than that in B1, implying its higher concentration of W. With the WC addition rising to 15.0 wt.%, unlike a large number of rimless grains in C1 of Figure (c), most of the black cores in C2 of Figure (c) are wrapped with white rims. Eventually in the cermet with supersaturated WC (20.0 wt.%), it is surprising that the undissolved oval-shaped WC grains only exist in the interior region (as shown in D1 of Figure (d)), whereas WC grains can be barely detectable both in the intermediate region (D2 of Figure (d)) and the subsurface region (D3 of Figure (d)). Meanwhile, large quantities of black core-white rim structures appear again in the subsurface region (D3 of Figure (d)). Here it is also pertinent to mention that at high WC concentrations (15.0 and 20.0 wt.%), aggregated Ti(C, N) layers seemingly form in the immediate subsurface region with different thicknesses (C2 of Figure (c) and D3 of Figure (d)).
Thus far, it is clear that the rise of WC content (from unsaturated to supersaturated condition) brings about the microstructural change from a typical core-rim structure to the emergence and enrichment of rimless grains and to the preservation of undissolved WC grains. Nevertheless, the formation mechanism of macro-gradient structures, a distinct feature observed in the cermet with high WC concentrations, remains to be unraveled. Enlightened by the functionally graded cemented carbides that have been fabricated through the deliberate control of the inward or outward diffusion of N via the adjustment of N pressure of sintering atmosphere [Citation20–23], the following paragraphs will discuss the denitrification behavior and its influence on solubility to rationalize the generation of macro-gradient structures, using the cermet sample with 20 wt.% WC as an example.
The gas evolution behavior and the mass change of the cermet containing 20 wt.% WC during sintering are shown in Figure (a). According to the result, the cermet keeps suffering from mass loss in a temperature range of 1100–1450°C; meanwhile, in consideration of the constituent elements (Ti, W, C, N, Ni) of the cermet and the relative mass (14) of the gas molecules detected during heating, the N2 escape can be identified, and the apex of which occurs at ∼1350°C. This is consistent with the literature report [Citation24] that once WC is added, Ti(C, N) becomes thermodynamically unstable, which facilitates the denitrification during high-temperature sintering. The concentration profile of N along with the increase of distance from top surface is shown in Figure (b). The N concentration reveals firstly an increase in the subsurface region, then a sharp decrease in the intermediate region and finally a gradual rise to reach a plateau in the interior region. In the enlarged view in Figure (c), it can be seen that Ti, N, and Ni elements accumulate on the surface (corresponding to a depth range of 0–0.2 μm); Ni concentration decreases but Ti and N concentrations slowly increase with the depth increasing from 0.2 to 3 μm; W concentration reaches the maximum in the depth range of 0.2–1.5 μm and then gradually decrease in the range of 1.5–3 μm. From Figure (d), it is further noted that Ti and N contents continue to increase in the depth range of 3–12 μm, which arrive the maximum values in the range of 7–9 μm; Ni content keeps rising in the range of 3–40 μm, whereas W content shows a downward trend in the range of 3–10 μm and stabilizes afterwards (in the range of 10–40 μm). During the denitrification of Ti(C, N), N atoms escape in the form of N2, and the remnant Ti atoms dissolve into the Ni binder. Propelled by the strong thermodynamic affinity between Ti and N, Ti atoms are prone to diffuse inwardly where the N concentration is high [Citation25]. Thus, Ti and N elements show similar distributions, with their maximum concentrations detected in the depth of 3–12 μm. The synchronous increase of Ti and N in the immediate subsurface region may be the reason for the presence of an aggregated Ti(C, N) layer, however, the potential factors that influence its thickness remain to be studied. The variations of W and Ni contents, on the other hand, may be attributed to the diffusion of W and Ni atoms to fill the vacancies left in place after the inward diffusion of Ti [Citation26, Citation27]. The complex elemental profiles in the subsurface and intermediate regions (corresponding to a depth range of 0–40 μm) are generally consistent with the experimental evidences and kinetic simulations reported in the WC-Ti(C, N)-Co gradient cemented carbide system [Citation26–29], which is believed to be controlled by the chemical potential of each element as well as the chemical affinity between different elements.
Figure 3. (a) N ion-current curve and thermogravimetric curve of Ti(C, N)-20 wt.% WC-50 wt.% Ni cermet in the temperature range of 1100–1450°C. (b) N distribution along with the increase of distance from the top surface to a depth of 200 μm. Enlarged views of N, Ti, W, and Ni distributions in the depth ranges of (c) 0–3 μm and (d) 3–40 μm. Note that the concentrations of N, Ti, W, and Ni in (c) were normalized after excluding the interference of C contamination on the cermet surface.
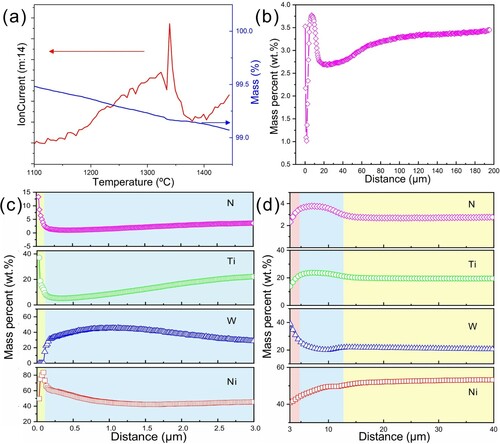
It is also worth noting that the N concentration in Figure (b) shows an upward trend from 40 to 200 μm, which means on a larger scale a N gradient forms in the cermet as a result of the denitrification reaction. With the premise that N exhibits extremely low solubility in the liquid Ni binder phase [Citation30], the denitrification affects predominantly the precipitation step of a typical dissolution-precipitation process, thus the potential change of W solubility due to the reduction of N content can be considered within the Ti-W-C-N quaternary system. To qualitatively describe the thermodynamic tendency of W solubility change in response to N content variation, the isothermal sections of Ti-W-C ternary system with 0, 3, and 5 wt.% N additions at 1450 °C were established as shown in Figure . Initially W has a maximum solubility of ∼60 wt.% in (Ti, W)C of the Ti-W-C system, which decreases to ∼49 wt.% in (Ti, W)(C, N) of the Ti-W-C-3 wt.% N system, and further drops to ∼35 wt.% in (Ti, W)(C, N) of the Ti-W-C-5 wt.% N system. These results indicate that for the cermet containing supersaturated WC, the reduced N content due to denitrification could facilitate a larger quantity of W solutes precipitated from the liquid Ni onto the Ti(C, N), leading to the disappearance of undissolved WC particles in the intermediate and subsurface regions.
Figure 4. Isothermal sections of Ti-W-C system with different N additions at 1450°C: (a) Ti-W-C, (b) 3 wt.% N-Ti-W-C, (c) 5 wt.% N-Ti-W-C.
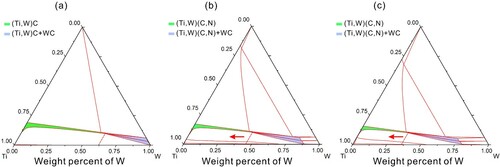
Here, it is pertinent to note that the gradient of N content induced by denitrification also exists in the cermets containing unsaturated WC. Using A1 and A2 of Figure (a) as an example, the denitrification in the subsurface region increases the solubility of W in the (Ti, W)(C, N) phase, contributing to a sufficient but slow growth of the rim phase showing a typical polyhedral shape, while the rim phase in the interior forms via the rapid precipitation of solutes in the Ni binder during the liquid cooling stage [Citation31, Citation32], the shape of which tends to be spherical.
4. Conclusions
In summary, Ti(C, N)-WC-Ni cermets with varying the WC concentration from unsaturated to supersaturated conditions were specifically designed in this work based on thermodynamic calculations. Through experimental characterizations combined with theoretical approaches, the role of WC addition on cermet microstructure and the governing thermodynamic mechanism were elucidated. Our results show that the rise of WC content induces the microstructural change from a typical core-rim structure, to the generation of rimless grains, and ultimately to the preservation of undissolved WC. The instability of Ti(C, N) during sintering results in the denitrification, with the loss of N especially in the intermediate and subsurface regions. According to isothermal sections established, reduced N concentration causes an increased solubility of W in the (Ti, W)(C, N) rim phase, which contributes to the formation of macro-gradient structures that are most pronounced in the cermet with supersaturated WC. Thus, this work shows the usefulness of thermodynamic calculations in establishing composition-microstructure relationships of WC incorporated Ti(C, N)-based cermets, which is expected to facilitate future optimization of cermet tools.
Supplemental Material
Download MS Word (103.6 KB)Disclosure statement
No potential conflict of interest was reported by the author(s).
Additional information
Funding
References
- Lou M, Chen X, Xu K, et al. Temperature-induced wear transition in ceramic-metal composites. Acta Mater. 2021;205:116545.
- Park S, Kang S. Toughened ultra-fine (Ti,W)(CN)-Ni cermets. Scripta Mater. 2005;52(2):129–133.
- Ettmayer P, Kolaska H, Lengauer W, et al. Ti(C,N) cermets—metallurgy and properties. Int J Refract Met Hard Mater. 1995;13:343–351.
- Lengauer W, Scagnetto F. Ti(C,N)-based cermets: critical review of achievements and recent developments. Solid State Phenom. 2018;274:53–100.
- Zheng Z, Lv J, Lou M, et al. Mechanical and tribological properties of WC incorporated Ti(C, N)-based cermets. Ceram Int. 2022;48:10086–10095.
- Lindahl P, Gustafson P, Rolander U, et al. Microstructure of model cermets with high Mo or W content. Int J Refract Met Hard Mater. 1999;17:411–421.
- Jung J, Kang S. Effect of ultra-fine powders on the microstructure of Ti(CN)-xWC-Ni cermets. Acta Mater. 2004;52:1379–1386.
- Li Y, Liu N, Zhang X, et al. Effect of WC content on the microstructure and mechanical properties of (Ti,W)(C, N)-Co cermets. Int J Refract Met Hard Mater. 2008;26:33–40.
- Kim S, Zuo J, Kang S. Effect of WC or NbC addition on lattice parameter of surrounding structure in Ti(C0.7,N0.3)-Ni cermets investigated by TEM/CBED. J Eur Ceram Soc. 2010;30:2131–2138.
- Ahn SY, Kang S. Formation of core/rim structures in Ti(C,N)-WC-Ni cermets via a dissolution and precipitation process. J Am Ceram Soc. 2010;83:1489–1494.
- Lou M, Xu K, Chen L, et al. Development of robust surfaces for harsh service environments from the perspective of phase formation and transformation. J Mater Inform. 2021;1:5.
- Qin Z, Wang Z, Wang Y, et al. Phase prediction of Ni-base superalloys via high-throughput experiments and machine learning. Mater Res Lett. 2021;9:32–40.
- Jagetia A, Nartu M, Dasari S, et al. Ordering-mediated local nano-clustering results in unusually large Hall-Petch strengthening coefficients in high entropy alloys. Mater Res Lett. 2021;9:213–222.
- Chen L, Zhang Z, Lou M, et al. High-temperature wear mechanisms of TiNbWN films: role of nanocrystalline oxides formation. Friction. 2022: 1–13. DOI:10.1007/s40544-022-0621-x.
- Peng Y, Zhou P, Du Y, et al. Thermodynamic evaluation of the C-Ta-Ti system and extrapolation to the C-Ta-Ti-N system. Int J Refract Met Hard Mater. 2013;40:36–42.
- Peng Y, Du Y, Zhou P, et al. CSUTDCC1—A thermodynamic database for multicomponent cemented carbides. Int J Refract Met Hard Mater. 2014;42:57–70.
- Park C, Nam S, Kang S. Carbide/binder interfaces in Ti(C,N)-(Ti,W)C/(Ti,W)(C,N)-based cermets. J Alloys Compd. 2016;657:671–677.
- Xiong H, Wu Y, Li Z, et al. Comparison of Ti(C, N)-based cermets by vacuum and gas-pressure sintering: microstructure and mechanical properties. Ceram Int. 2018;44:805–813.
- Liu N, Yin W, Zhu L. Effect of TiC/TiN powder size on microstructure and properties of Ti(CN)-based Cermets. Mater Sci Eng A. 2007;445–446:707–716.
- Glühmann J, Schneeweiß M, Van Den Berg H, et al. Functionally graded WC-Ti(C,N)-(Ta,Nb)C-Co hardmetals: metallurgy and performance. Int J Refract Met Hard Mater. 2013;36:38–45.
- Janisch DS, Lengauer W, Eder A, et al. Nitridation sintering of WC-Ti(C,N)-(Ta,Nb)C-Co hardmetals. Int J Refract Met Hard Mater. 2013;36:22–30.
- Lengauer W. Diffusional control of the near-surface microstructure in functional gradient hardmetals. Materialwiss Werkstofftech. 2005;36:460–466.
- Lengauer W, Dreyer K. Tailoring hardness and toughness gradients in functional gradient hardmetals (FGHMs). Int J Refract Met Hard Mater. 2006;24:155–161.
- Chen L, Lengauer W, Ettmayer P, et al. Fundamentals of liquid phase sintering for modern cermets and functionally graded cemented carbonitrides (FGCC). Int J Refract Met Hard Mater. 2000;18:307–322.
- Li N, Wang Q, Zhang W, et al. Development of multilayer graded cemented carbides with Ti-Zr carbonitride miscibility gaps. Ceram. Int. 2021;47:7521–7527.
- Zhang W, Du Y, Peng Y, et al. Experimental investigation and simulation of the effect of Ti and N contents on the formation of fcc-free surface layers in WC-Ti(C,N)-Co cemented carbides. Int J Refract Met Hard Mater. 2013;41:638–647.
- Zhang W, Peng Y, Zhou P, et al. Experimental investigation and computer simulation of gradient zone formation in WC-Ti(C,N)-TaC-NbC-Co cemented carbides. J Phase Equilib Diffus. 2013;34:202–210.
- Li N, Li X, Zhang W, et al. Relation between the nitrogen gas pressure and structure characteristics of WC-Ti(C, N)-Co graded cemented carbides. J Alloys Compd. 2020;831:154764.
- Zhang W, Du Y, Zhou P, et al. A new type of double-layer gradient cemented carbides: preparation and microstructure characterization. Scripta Mater. 2016;123:73–76.
- Garcia J. Influence of Fe-Ni-Co binder composition on nitridation of cemented carbides. Int J Refract Met Hard Mater. 2012;30:114–120.
- Xiong H, Li Z, Gan X, et al. Morphology evolution of TiC-based cermets via different sintering schedules. Ceram Int. 2017;43:5805–5812.
- Nie J, Wu Y, Li P, et al. Morphological evolution of TiC from octahedron to cube induced by elemental nickel. CrystEngComm. 2012;14:2213–2221.