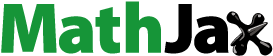
ABSTRACT
By introducing heterogeneous lamella-structure, we obtained a superior strength-ductility synergy in Mg-alloy associated with excellent strain-hardening ability, i.e. yield strength of ∼251 MPa, tensile strength of ∼393 MPa and elongation of ∼23%. By using advanced characterization techniques, we showed that strengthening was mainly caused by the non-uniform distribution of hetero-deformation induced (HDI) stress associated with grain-boundary disclinations, which are mediated by heterogeneous multi-grain interactions. Induced by grain-boundary disclinations and intergranular slip transfers, a variety of abnormal deformation modes have been activated,which contributed significantly to enhanced ductility. This work suggests a new avenue to evade strength-ductility trade-off dilemma in Mg-alloys.
GRAPHICAL ABSTRACT

IMPACT STATEMENT
The heterogeneous lamella-structure leads to sustained strain-hardenability in Mg-alloy with unique accommodating deformation modes (extensive abnormal <c+a> slips and feather-shaped twins), induced by grain-boundary disclinations and intergranular slip transfers.
1. Introduction
As the lightest metallic materials with low density and high specific strength, magnesium (Mg) alloys have attracted considerable attentions with extensive application prospects in the transportation, aerospace and electronics industries [Citation1,Citation2]. However, one of the critical issues in high-strength Mg-alloys is the lack of ductility, which is due to limited easily activated slip modes in hexagonal close-packed (HCP) magnesium. To achieve high strength in Mg-alloys, conventional strengthening methods include precipitation hardening, grain refinement and introducing strong basal texture, but all of them are at the expense of ductility [Citation3]. For typical high-strength Mg-alloys with ultimate strength of around 400 MPa (such as AZ80 [Citation4,Citation5] and AZ91 [Citation6,Citation7]), their ductility usually ranges from ∼2 to 13%. It is a great challenge to develop Mg-alloys with superior synergy of strength and ductility.
One of the most promising design strategies to evade the strength-ductility dilemma is introducing microstructural heterogeneities in materials [Citation8]. One typical example is gradient-structured steel, which exhibits not only a large tensile fracture elongation of ∼55%, comparable to that of the homogeneous coarse-grained (CG) sample, but also yield strength of ∼200 MPa that is ∼2.6 times as high [Citation9]. Caused by multi-grain inhomogeneity and strain gradient near domain interfaces, high strength and high ductility can be achieved simultaneously with hetero-deformation induced (HDI) stress strengthening and hardening [Citation8]. However, due to the lack of activedeformation modes, hetero-structured Mg-alloys can hardly achieve more than ∼18% elongation [Citation10–12]. For example, the yield strength and ultimate tensile strength of gradient-structured AZ31 Mg-alloy can reach ∼240 and ∼325 MPa, respectively (compared with ∼188 and ∼260 MPa for uniform CG counterpart), with a significant downgrade of fracture elongation from ∼17% to ∼6% [Citation11]. In particular, when the hetero-structured Mg-alloys possess high yield strength and tensile strength of ∼250 and ∼350 MPa, their ductility will prominently decrease to ∼10%, close to that of high strength fine-grained (FG) Mg-alloys [Citation13–15]. Even though efficient strengthening can be realized in hetero-grain structured Mg-alloys, it is still difficult to enhance ductility effectively, which usually requires the activation of a large variety of deformation modes in both CGs and FGs, such as non-basal slips or slip systems with low Schmid factor.
In the present work, we obtained a novel heterogeneous lamella-structured Mg-9Al-1Zn-1Sn alloy (denoted as HL-Mg-alloy) using simple rolling and precisely controlled annealing process. The HL-Mg-alloy features alternating micro CG and FG layers, and exhibits impressive strength-ductility synergy, i.e. a high yield strength of ∼251 MPa, tensile strength of ∼393 MPa and superior ductility of ∼23%. Through scanning electron microscope (SEM), quasi-in-situ electron backscattered diffraction (EBSD) and transmission electron microscope (TEM) characterizations, the strain gradient near hetero-interface/grain-boundaries (GBs) has been quantified by calculating GB disclinations. It has been found that strengthening is mainly caused by the non-uniform distribution of intragranular dislocations and HDI-stress associated with disclinations, which are mediated by heterogeneous multi-grain interactions. A large amount of abnormal deformation modes has been activated, e.g. low Schmid factor pyramidal <c+a> slips and inhomogeneous feather-shaped twins, induced by GB disclinations and intergranular slip transfers, which are critical to accommodate both global and local strain (e.g. between CGs and FGs). By introducing lamellar hetero-grain structure to control inter/intra-grain defect distributions (e.g. dislocations, disclinations and twins), our work provides a new insight into the design of Mg-alloys possessing both high strength and high ductility.
2. Materials and methods
The hard-plate rolling (HPR) process that added hard plates (made of hardened steel ∼50 HRC, thickness of 1 mm) between rolls and sample during rolling [Citation16] was applied to prepare the HL-Mg-alloy. The commercial extruded Mg-9Al-1Zn-1Sn (wt.%) sheet of 5 mm thick was preheated at 573 K for 15 min and rolled to 1 mm with one-pass reduction of 80% using HPR, followed by annealing at 573 K for 290 s, to prepare the HL-Mg-alloy. Details of tensile tests and microstructural characterizations including SEM, EBSD and TEM are presented in Section 1 of Supplementary Material. For comparison, the Mg-alloy with the same composition was prepared by multi-pass rolling followed by varying annealing parameters to obtain CG and FG counterparts (Supplementary Figure S1, Section 2 of Supplementary Material).
3. Results and discussion
3.1. Heterogeneous lamella-structure and tension properties
Here we report a heterogeneous lamella-structure in an Mg-9Al-1Zn-1Sn alloy prepared by HPR and precisely controlled annealing. Figure (a) displays a typical low-magnification inverse pole figure (IPF) map of the annealed sample, showing a heterogeneous lamella-structure, consisting of FGs interspersed with CG layers. The average grain-sizes of CG and FG layers are ∼8.9 and ∼1.6 µm, respectively (Figure (b)). The CG and FG layers exhibit similar basal-type texture spreading along rolling direction (RD) and comparable maximum intensity of ∼9–11 multiple random distribution (m.r.d.) (Figure (c)). The special HL structure is formed by the interplay of heterogeneous dynamic recrystallization (Figure (d,e)) and inhomogeneous pinning effect caused by Mg17Al12 formed along GBs. That is the high-density Mg17Al12 particles at GBs in the FG layer, compared with the low-density Mg17Al12 particles in CG layer (Figure (f–i)). The formation mechanism of special heterogeneous lamella-structure is further discussed in Section 3 of Supplementary Material. For comparison, the microstructure of CG and FG samples are shown in Supplementary Figure S1.
Figure 1. (a) The low-magnification IPF map of HL-Mg-alloy; (b) The grain-size distribution in FG and CG layers. (c) The (0002) PFs of the FG and CG layers, respectively. (d) and (e) The IPF maps of as-rolled sample and as-annealed sample. (f) and (g) The high-magnification IPF and corresponding SEM microstructure of typical region. (h) and (i) TEM analysis showing Mg17Al12 particles mainly distributed along GBs of FGs.
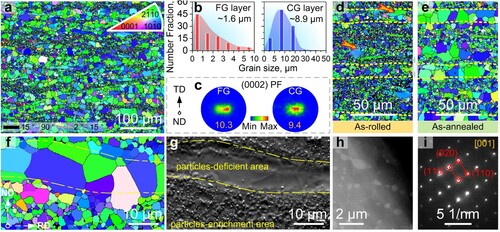
Figure (a) shows engineering stress–strain curves at room temperature of the HL-Mg-alloy, together with uniform CG and FG counterparts. The HL sample exhibits not only a large elongation (ϵ ∼23 ± 1.1%) that is superior to the CG counterpart, but also a high yield strength (σ0.2 ∼251 ± 3 MPa) and ultimate strength (σUS ∼393 ± 5 MPa). Furthermore, the large ultimate-yield strength difference (σUS-σ0.2) up to ∼140 MPa suggests a strong strain-hardening ability, which even exceeds the CG counterpart (Figure (a)). Despite a relatively high alloying content (>9 wt.%), the present HL-Mg-alloy is more ductile than those FG Mg-alloys with similar yield strength (Figure (b)), being especially promising for developing reliable engineering materials. Also, the remarkable strength-ductility combination is superior to the gradient- and bimodal-structured Mg-Al-Zn alloys [Citation10–12,Citation15,Citation17–21] (Figure (b)).
Figure 2. (a) Engineering stress–strain (σ–ϵ) curves of CG, FG and HL samples and LUR σ–ϵ curve of HL sample under tension along RD; the inset of a shows HDI-stress and HDI/strain-hardening curves of HL sample. (b) Comparison of yield strengths and fracture elongations of the present HL-Mg-alloy (indicated by star) with representative AZ91 Mg-alloys processed by accumulative rolling bonding (ARB) [Citation24,Citation25], equal channel angular process (ECAP) [Citation26–28], extrusion [Citation29–31], high-ratio differential speed rolling (HRDSR) [Citation6,Citation7], and wrought AZ80 [Citation4,Citation5,Citation32], AZ31 [Citation33–36], gradient-structured [Citation10–12] and bimodal-structured Mg-Al-Zn alloys [Citation19–21] reported in literature.
![Figure 2. (a) Engineering stress–strain (σ–ϵ) curves of CG, FG and HL samples and LUR σ–ϵ curve of HL sample under tension along RD; the inset of a shows HDI-stress and HDI/strain-hardening curves of HL sample. (b) Comparison of yield strengths and fracture elongations of the present HL-Mg-alloy (indicated by star) with representative AZ91 Mg-alloys processed by accumulative rolling bonding (ARB) [Citation24,Citation25], equal channel angular process (ECAP) [Citation26–28], extrusion [Citation29–31], high-ratio differential speed rolling (HRDSR) [Citation6,Citation7], and wrought AZ80 [Citation4,Citation5,Citation32], AZ31 [Citation33–36], gradient-structured [Citation10–12] and bimodal-structured Mg-Al-Zn alloys [Citation19–21] reported in literature.](/cms/asset/e431caa5-bebb-4168-99cd-6e1624e7a2d5/tmrl_a_2133976_f0002_oc.jpg)
From the unloading–reloading hysteresis loop (Figure (a)), we can calculate the HDI-stress () values to evaluate the contribution of HL structure to strengthening and hardening. The method was proposed by Zhu and Yang et al. [Citation22], and
is defined as the average value of
and
, where
is the unloading yield stress and
is the reloading yield stress at unloading–reloading loop, respectively. Each yield point is defined as the point which has a 5% reduction in slope from the effective elastic modulus [Citation22]. As follows:
(1)
(1) The inserted graph in Figure (a) presents the
with increasing strain, as well as the total strain-hardening rate (
= d
) and HDI-hardening rate curve (
= d
). According to literature [Citation23], it is more reasonable to employ
(
denotes flow stress) for evaluating the contribution of
to strengthening (insert in Figure (a)). The high average
value approaching to ∼56% suggests substantial HDI-strengthening effect in the HL structure. Meanwhile, the sustained and prominent HDI hardening associated with GNDs accumulation during hetero-deformation, especially at early stage, is beneficial for excellent strain-hardening ability (Figure (a)). The above results demonstrate that HDI strengthening and hardening contribute significantly to the superior mechanical properties in present HL sample, in addition to Hall–Peth effect [Citation35].
3.2. Analyses of microstructural defects and activated deformation modes
Based on the above analyses, it is clear that the hetero-grain structure is critical in determining its superior mechanical properties. Theoretically, because of the inhomogeneous microstructure, various kinds of crystalline defects with non-uniform distribution can be induced upon deformation, which leads to large strain gradient and HDI-stress near different types of GBs [Citation37]. By using the orientation maps from quasi-in-situ EBSD data, the densities of geometrically necessary dislocations (GNDs) and disclinations were calculated in order to quantify the strain gradient in present HL microstructure. According to topological defect theory in physics, dislocation and disclination are the two basic types of topological defects in crystals [Citation38]. A disclination can be quantified by its Frank vector (a rotation vector), whose direction is rotation axis and magnitude is rotation angle. Similar to the role of intragranular GND, disclinations are required to accommodate lattice curvature near GBs arising from non-uniform strain (e.g. strain gradient). Because the misorientation of a GB is not directly dictated by crystal symmetry, disclinations at GBs are usually partial disclinations. Based on Nye tensor theory, the disclination density tensor can be determined from the curl of elastic curvature tensor (more details can be found in Section 4 in Supplementary Material).
Figure shows the evolutions of IPF, disclination density and GND density through quasi-in-situ EBSD characterization before and after ∼3.5% tension. The scalar disclination density of undeformed specimen (Figure (b)) features low level in both the CG and FG layers. Tensor components of disclination density and GND density tensor are included in Supplemental Material, Supplementary Figures S1 and S3. In contrast, the disclination density increases significantly in FG layers,especially near the interface between the CG and FG layers (Figure (e)). By examining Figure (c,f), the high-density GND intensively develops in FG layers. While only the regions near hetero-interface inside the CGs accumulate substantial GNDs, which indicates apparent strain gradient along different layers [Citation8]. Intuitively, large-size grains possess more room to accommodate GNDs, and dislocations are only required to pile up around the hetero-interface for compensating strain gradient rather than other GBs. In contrast, within FGs, local stress concentration can be established near GBs because of the interactions between GBs and dislocations, which is necessary for the activation of non-basal slips in FGs [Citation39]. As supported by Figure (e), the interactions between dislocations and GBs lead to the formation of disclinations, indicating high-stress concentration among the FGs. Furthermore, the disclinations along hetero-interface also imply large strain gradient between layers, rationalizing the interlayer interaction and corresponding well with measured significant HDI-stress. We suggest the interaction between hetero-layers is mainly caused by different GB-strengthening effects, according to the literature [Citation40]. Besides, the disperse high-density Mg17Al12 particles can further strengthen FG layers although they distribute mainly at GBs [Citation41]. In addition, due to the submicron size, substantial dynamic precipitates in present HL-Mg-alloy do not significantly deteriorate the ductility [Citation42].
Figure 3. (a) The IPF map, (b) scalar disclination density (in rad μm−2) and (c) scalar GND density (in μm−1) of the undeformed HL-Mg-alloy; (d) The IPF map, (e) scalar disclination density (in rad μm−2) and (f) scalar GND density (in μm−1) of the ∼3.5% strained HL-Mg-alloy.

To identify the activated dislocation modes during tensile deformation, the microstructure of deformed HL samples has been further investigated through TEM characterizations (Figure ) and slip trace analyses (Figure and Supplementary Figure S4). About 200 grains were counted for statistically sound conclusions. Burgers vectors of dislocations can be identified according to g·b = 0 invisible criterion [Citation43]. As shown in the dark-field TEM image viewed from [] zone axis under the two-beam condition of g = [
] (Figure (a)), high-density basal <a> dislocations (examples are indicated by white arrows) were observed inside the typical FG after an applied tensile strain of ∼13%. Figure (b,c) presents bright-field and dark-field images under the g = [
] condition of b and c regions marked by orange dashed rectangles in Figure (a), respectively, where many dislocations with Burgers vectors having c-components are clearly discerned, as indicated by red arrows. It reveals that both <c+a> and <a> dislocations are activated in FGs to coordinate plastic deformation. Besides, substantial dislocation lines containing <c> type Burgers vectors (marked by red arrows, Figure (d)) are visible in a typical grain interior at strain of ∼23% under g = [
] condition. The frequently observed pyramidal <c+a> slips in FGs in TEM images (Figure ) can be further validated by slip trace analyses (Supplementary Figure S4(a)).
Figure 4. (a) The dark-field TEM image of typical FG after ∼13% tensile deformation under the two-beam condition of g = [].(b) The bright-field TEM image of region (b) in (a) using g = [
]; (c) the dark-field TEM image of region (c) in (a) using g = [
]. (d) The dark-field TEM image of typical FG after ∼23% tensile deformation using g = [
].
![Figure 4. (a) The dark-field TEM image of typical FG after ∼13% tensile deformation under the two-beam condition of g = [101¯0].(b) The bright-field TEM image of region (b) in (a) using g = [0002]; (c) the dark-field TEM image of region (c) in (a) using g = [0002]. (d) The dark-field TEM image of typical FG after ∼23% tensile deformation using g = [0002].](/cms/asset/929d66a3-ef41-4ff1-ae60-d739b780f995/tmrl_a_2133976_f0004_oc.jpg)
Figure 5. (a) The statistical results of the identified slip activity in CG and FG layers. Relative frequencies of activated pyramidal <c+a> slips with high m values (>0.2, above the blue line) and low m values (<0.2, below the blue line) are marked in (a). (b) The slip transfers in a typical region of CG layer. (c)–(f) The IPF, scalar disclination density (in rad µm−2), scalar GND density (in µm−1) and SEM of representative CG near hetero-interface, with feather-shaped tension twinning activated. The white numbers represent values (Schmid factor) under uniaxial loading.
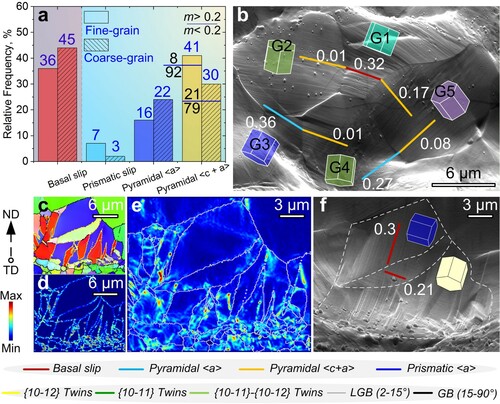
Moreover, among all the activated dislocation slip modes identified by slip traces, a high fraction of non-basal slips have occurred in both CG and FG layers, e.g. ∼55% in CG and ∼64% in FG (Figure (a)). In particular, the proportions of pyramidal <c+a> slips in CG and FG layers are determined as ∼30% and ∼41%, respectively. Note that the activated slip systems do not necessarily have a high Schmid factor value as expected. Surprisingly, the proportion of pyramidal <c+a> slips with low Schmid factor values (m < 0.2) are as high as ∼80% and ∼90% in CG and FG layers (out of total pyramidal <c+a> slips), respectively (Figure (a)). Both TEM observations and slip trace analyses suggest that highly activated <c+a> slips are significant contributor to high ductility and strain-hardenability for their essential role on strain accommodation (Figure (a)), facilitating deformation at high stress level [Citation44].
As shown in Figure (e,f), intragranular dislocations and GB disclinations can be found even at the early stage of deformation, which suggests a large strain gradient and HDI-stress developed near GBs within FG layer. Since local stress concentration near those GBs plays an important role in selecting slip systems, <c+a> slips with low Schmid factor (determined by external load) can be easily activated in FGs to accommodate local strain gradient, which could benefit macroscopic plasticity [Citation39].
Meanwhile, within CG layers, intergranular slip transfer can be frequently observed (Figure (b) and Supplementary Figure S4(b,c)). Detailed analyses show that the low-Schmid factor <c+a> slips are accompanied with dislocation interactions at GBs (such as G1-G2, G1-G5, G4-G5, and G3-G4 in Figure (b)), i.e. slip transfer. In many cases, as shown in Figure (b), a pair of ‘connected’ slip traces in neighboring grains (indicating slip transfer) usually belong to different types of slip systems: one belongs to an easily activated slip system (e.g. basal slip in G1 or high-Schmid Factor non-basal slips in G3 and G4), while the other belongs to a hardly activated slip system (e.g. low-Schmid Factor pyramidal <c+a> slips in G2, G4 and G5). Slip transfer can be considered as a mechanism to relieve local stress concentration caused by the interaction between dislocations and GBs. When gliding dislocations in one grain are impeded by a GB, they may either stop at the GB (resulting in a large disclination), or ‘transmit’ through the GB into another slip system in the neighboring grain (resulting in a small remnant disclination). A typical example of remnant disclination has been determined in Supplementary Figure S5, which directly results from slip transfer. In the latest report on Mg-Gd alloy laminate with dual-heterostructure grain size and texture [Citation45], the slip transfer induced by hetero-structure was also considered to play an important role in strain accommodation. Hence, the enhanced strain hardenability of present HL-Mg-alloy can be attributed to both the intragranular dislocations (including a variety of slip systems) and GB disclinations, caused by heterogeneous multi-grain interactions.
Besides the activation of low Schmid factor pyramidal <c+a> slip in both FGs and CGs, additional deformation modes have also been observed especially near the interface (Figure (c–f) and Supplementary Figure S6). Inhomogeneous feather-shaped twins are observed in several CGs near hetero-interfaces (Figure (c–f) and Supplementary Figure S6). Those feather-shaped twins usually grow from FG/CG interface towards the interior of CGs. Additional GB disclination analyses (Figure (d)) show GB disclinations with large strain gradient at FG/CG interface, indicating significant HDI-stress and inducing twin nucleation. By comparing GNDs density map and corresponding SEM image with slip traces (Figure (e,f) and Supplementary Figure S7), it is found that dislocations are also activated in both parent and twin grains, which suggests the interplay between twinning boundaries and dislocations/disclinations, being beneficial for the strain-hardenability.
Mediated by the heterogeneous distribution and interaction of FG and CG layers, dislocations interact with GBs in different layers, resulting in inhomogeneous disclination distribution at GBs. The strain gradient and HDI-stress associated with inhomogeneous disclinations are responsible for the activation of a large variety of accommodating deformation modes (e.g. low Schmid factor pyramidal <c+a> slip and inhomogeneous feather-shaped twins). In other words, multiple types of crystalline defects, e.g. dislocations, disclinations and twins, have been activated to accommodate local strain gradient caused by microstructural heterogeneity, which interact with each other and contribute to sustained strain-hardening and enhanced ductility [Citation9].
4. Conclusions
Here we report superior strength-ductility synergy obtained in a heterogeneous lamella-structured (HL) Mg-alloy with alternating coarse-grained (∼8.9 µm) and fine-grained (∼1.6 µm) layers. The present HL-Mg-alloy possesses appreciable strain-hardening and superior strength-ductility synergy, i.e. an elongation of ∼23%, yield strength of 251 MPa and tensile strength of ∼393 MPa. The high yield strength is mainly caused by the non-uniform distribution of HDI-stress, which is mediated by heterogeneous multi-grain interactions. The large ductility benefits from the activation of a variety of abnormal deformation modes, e.g. low Schmid factor pyramidal <c+a> slips and inhomogeneous feather-shaped twins, induced by GB disclinations and intergranular slip transfers, which accommodate both the global strain and the local strain between CGs/FGs. These accommodating deformation modes not only render effective strain accommodation at high-stress level, but also subsequently facilitates dislocation accumulation and interaction, finally leading to high HDI/strain-hardenability and high tensile strength. By introducing a lamellar hetero-grain structure to control inter/intra-grain defect distributions (e.g. dislocations, disclinations and twins), our work provides a new insight into the design of high-strength, high-ductility Mg-alloys.
Supplemental Material
Download MS Word (4 MB)Acknowledgement
We would like to thank Prof. Chao Xu from Harbin Institute of Technology for the TEM work.
Disclosure statement
No potential conflict of interest was reported by the author(s).
Additional information
Funding
References
- Yan Z, Yu Y, Qian J, et al. Fabrication of high-strength Mg–Gd–Nd–Zn–Sn–Zr alloy via extrusion and aging. Met Mater Int. 2021;27:4182–4194.
- Diqing W, Houbin W, Jiajun H, et al. Effect of the secondary phase on mechanical and damping properties of Mg–Zn–Y–Si alloy. Met Mater Int. 2021;27:838–842.
- Jian WW, Cheng GM, Xu WZ, et al. Ultrastrong Mg alloy via nano-spaced stacking faults. Mater Res Lett. 2013;1:61–66.
- Zhao X, Li SC, Zheng YS, et al. The microstructure evolution, texture weakening mechanism and mechanical properties of AZ80 Mg alloy processed by repetitive upsetting-extrusion with reduced deformation temperature. J Alloy Compd. 2021;883:160871.
- Tang LL, Zhao YH, Islamgaliev RK, et al. Enhanced strength and ductility of AZ80 Mg alloys by spray forming and ECAP. Mater Sci Eng A. 2016;670:280–291.
- Kim WJ, Hong SI, Kim YH. Enhancement of the strain hardening ability in ultrafine grained Mg alloys with high strength. Scr Mater. 2012;67:689–692.
- Kim WJ, Park JD, Kim WY. Effect of differential speed rolling on microstructure and mechanical properties of an AZ91 magnesium alloy. J Alloy Compd. 2008;460:289–293.
- Wu XL, Zhu YT. Heterogeneous materials: a new class of materials with unprecedented mechanical properties. Mater Res Lett. 2017;5:527–532.
- Wu X, Jiang P, Chen L, et al. Extraordinary strain hardening by gradient structure. PNAS. 2014;111:7197–7201.
- Chen L, Yuan F, Jiang P, et al. Mechanical properties and deformation mechanism of Mg-Al-Zn alloy with gradient microstructure in grain size and orientation. Mater Sci Eng A. 2017;694:98–109.
- Meng X, Duan M, Luo L, et al. The deformation behavior of AZ31 Mg alloy with surface mechanical attrition treatment. Mater Sci Eng A. 2017;707:636–646.
- Ning J, Xu B, Sun M, et al. Strain hardening and tensile behaviors of gradient structure Mg alloys with different orientation relationships. Mater Sci Eng A. 2018;735:275–287.
- Wei XX, Jin L, Wang FH, et al. High strength and ductility Mg-8Gd-3Y-0.5Zr alloy with bimodal structure and nano-precipitates. J Mater Sci Technol. 2020;44:19–23.
- Zhang H, Wang HY, Wang JG, et al. The synergy effect of fine and coarse grains on enhanced ductility of bimodal-structured Mg alloys. J Alloy Compd. 2019;780:312–317.
- Oh-ishi K, Mendis CL, Homma T, et al. Bimodally grained microstructure development during hot extrusion of Mg-2.4 Zn-0.1 Ag-0.1 Ca-0.16 Zr (at.%) alloys. Acta Mater. 2009;57:5593–5604.
- Wang H-Y, Yu Z-P, Zhang L, et al. Achieving high strength and high ductility in magnesium alloy using hard-plate rolling (HPR) process. Sci Rep. 2015;5:17100.
- Zhang Y, Rong W, Wu YJ, et al. Achieving ultra-high strength in Mg-Gd-Ag-Zr wrought alloy via bimodal-grained structure and enhanced precipitation. J Mater Sci Technol. 2020;54:160–170.
- Peng P, Tang AT, She J, et al. Significant improvement in yield stress of Mg-Gd-Mn alloy by forming bimodal grain structure. Mater Sci Eng A. 2021;803:140569.
- Park SH, Kim SH, Kim YM, et al. Improving mechanical properties of extruded Mg-Al alloy with a bimodal grain structure through alloying addition. J Alloy Compd. 2015;646:932–936.
- Cubides Y, Karayan AI, Vaughan MW, et al. Enhanced mechanical properties and corrosion resistance of a fine-grained Mg-9Al-1Zn alloy: the role of bimodal grain structure and beta-Mg17Al12 precipitates. Materialia. 2020;13:100840.
- Li YK, Zha M, Jia HL, et al. Tailoring bimodal grain structure of Mg-9Al-1Zn alloy for strength-ductility synergy: co-regulating effect from coarse Al2Y and submicron Mg17Al12 particles. J Magnes Alloy. 2021;9:1556–1566.
- Yang M, Pan Y, Yuan F, et al. Back stress strengthening and strain hardening in gradient structure. Mater Res Lett. 2016;4:145–151.
- Wu X, Yang M, Yuan F, et al. Heterogeneous lamella structure unites ultrafine-grain strength with coarse-grain ductility. PNAS. 2015;112:14501–14505.
- Pérez-Prado MT, Del Valle JA, Ruano OA. Achieving high strength in commercial Mg cast alloys through large strain rolling. Mater Lett. 2005;59:3299–3303.
- Pérez-Prado MT, Valle D, Ruano OA. Grain refinement of Mg–Al–Zn alloys via accumulative roll bonding. Scr Mater. 2004;51:1093–1097.
- Khani S, Aboutalebi MR, Salehi MT, et al. Microstructural development during equal channel angular pressing of as-cast AZ91 alloy. Mater Sci Eng A. 2016;678:44–56.
- Máthis K, Gubicza J, Nam NH. Microstructure and mechanical behavior of AZ91 Mg alloy processed by equal channel angular pressing. J Alloy Compd. 2005;394:194–199.
- Yang Z, Ma A, Liu H, et al. Managing strength and ductility in AZ91 magnesium alloy through ECAP combined with prior and post aging treatment. Mater Charact. 2019;152:213–222.
- Kim S-H, Lee JU, Kim YJ, et al. Improvement in extrudability and mechanical properties of AZ91 alloy through extrusion with artificial cooling. Mater Sci Eng A. 2017;703:1–8.
- Kim YJ, Kim YM, Hong SG, et al. Comparative study of tensile and high-cycle fatigue properties of extruded AZ91 and AZ91-0.3Ca-0.2Y alloys. J Mater Sci Technol. 2021;93:41–52.
- Liu SS, Zhang BX, Liu H, et al. Achieving strength-ductility synergy of AZ91 extruded sheet by balancing dual-heterostructure of grain size and precipitates. Mater Sci Eng A. 2021;827:141989.
- Huang XS, Suzuki K, Saito N. Microstructure and mechanical properties of AZ80 magnesium alloy sheet processed by differential speed rolling. Mater Sci Eng A. 2009;508:226–233.
- Zeng ZR, Zhu YM, Liu RL, et al. Achieving exceptionally high strength in Mg-3Al-1Zn-0.3Mn extrusions via suppressing intergranular deformation. Acta Mater. 2018;160:97–108.
- Kim WJ, Lee YG, Lee MJ, et al. Exceptionally high strength in Mg-3Al-1Zn alloy processed by high-ratio differential speed rolling. Scr Mater. 2011;65:1105–1108.
- Mehranpour MS, Heydarinia A, Emamy M, et al. Enhanced mechanical properties of AZ91 magnesium alloy by inoculation and hot deformation. Mater Sci Eng A. 2021;802:140667.
- Azghandi SHM, Weiss M, Arhatari BD, et al. A rationale for the influence of grain size on failure of magnesium alloy AZ31: An in situ X-ray microtomography study. Acta Mater. 2020;200:619–631.
- Bouaziz O, Kim HS, Lee J, et al. Bauschinger effect or kinematic hardening: bridging microstructure and continuum mechanics. Met Mater Int. 2022. doi:10.1007/s12540-022-01227-3
- Mermin ND. The topological theory of defects in ordered media. Rev Mod Phys. 1979;51:591–648.
- Li JL, Wu D, Chen RS, et al. Anomalous effects of strain rate on the room-temperature ductility of a cast Mg-Gd-Y-Zr alloy. Acta Mater. 2018;159:31–45.
- Park HK, Ameyama K, Yoo J, et al. Additional hardening in harmonic structured materials by strain partitioning and back stress. Mater Res Lett. 2018;6:261–267.
- Kim WJ, Jeong HG, Jeong HT. Achieving high strength and high ductility in magnesium alloys using severe plastic deformation combined with low-temperature aging. Scr Mater. 2009;61:1040–1043.
- Wang J, Niu L, Zhang Y, et al. Is Mg17Al12 ductile or brittle? A theoretical insight. J Magnes Alloy. 2021. doi:10.1016/j.jma.2021.06.006.
- Ko KK, Bae HJ, Park EH, et al. A feasible route to produce 1.1 GPa ferritic-based low-Mn lightweight steels with ductility of 47%. J Mater Sci Technol. 2022;117:225–237.
- Liu BY, Liu F, Yang N, et al. Large plasticity in magnesium mediated by pyramidal dislocations. Science. 2019;365:73–75.
- Liu S, Xia D, Yang H, et al. Mechanical properties and deformation mechanism in Mg-Gd alloy laminate with dual-heterostructure grain size and texture. Int J Plasticity. 2022;157:103371.