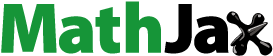
Abstract
Interface characteristics are of great importance in mechanical performance for multi-phases heat-resistant Al alloys. Herein, Al3Sc precipitates were created at both Al/Al9FeNi interface and Al matrix inside Al–Fe-Ni eutectic alloy by microalloyed Sc. Critically, Al3Sc interface precipitates were found to alleviate local lattice distortion at the Al/Al9FeNi interface to improve interface stability. Therefore, this alloy showed superior creep properties over available reports. The underlying mechanisms were quantitatively elucidated by elevated load transfer effect from interface precipitates and enhanced threshold stress from matrix precipitates. Generally, this work provided a solid understanding to optimize the creep property of eutectic Al alloys by manipulating interface structures.
GRAPHICAL ABSTRACT

IMPACT STATEMENT
This work reports that Al3Sc precipitates at Al/Al9FeNi interface can enhance load transfer effect of eutectic phase from microscopic/macroscopic factors, illustrating fundamental mechanisms for creep improvement of eutectic Al alloy.
1. Introduction
Heat-resistant Al alloys have been widely used in aerospace and automotive fields because they are lightweight and have high strength [Citation1–3]. Traditionally, Al–Si(-Cu) heat-resistant Al alloys are mostly used at ∼200°C, subjected to the rapid diffusion rates of Si and/or Cu in the Al matrix [Citation4–6]. This cannot meet increasing demands from practical applications. Therefore, the design of heat-resistant Al alloys with improved microstructure stability is vital to optimizing their high-temperature performances.
Introducing slow diffusion elements into the Al matrix, there are two types of newly developed heat-resistant Al alloys divided by a major strengthening phase: (I) Eutectic structure reinforced Al alloys. Since elements (i.e. Fe, Ni, La and Ce) have slower diffusion rates in the Al matrix [Citation7], their eutectic Al alloys (i.e. Al-Ni [Citation1], Al–Fe-Ni [Citation8,Citation9], Al-La [Citation10] and Al-Ce [Citation11]) show good performance at 300–400°C. (II) Precipitates strengthened Al alloys. The highly stable precipitates are introduced into the Al matrix by microalloying elements (i.e. Sc, Zr or Mn) [Citation12,Citation13]. For example, microalloying Sc is widely applied, and Al3Sc precipitates are created in the Al matrix to improve the thermal stability of Al alloys at 300°C [Citation14,Citation15]. Meanwhile, Al3Sc precipitates can impede dislocation movement to improve the creep resistance of Al alloys [Citation16,Citation17]. Furthermore, Sc is used to optimize the interface structure of multi-phases in Al alloys, elevating their thermal stability [Citation18]. For example, Chen and Gao [Citation19,Citation20] studied Al-Cu-Sc alloy and found there was a stable Sc-containing layer at the Al/θ` interface, ensuring θ` phase stability at 300 °C and impeding dislocation movement at the interface [Citation20].
Eutectic alloys have been widely discussed because of their excellent mechanical properties and application prospects [Citation21]. The investigation and analysis of the abundant metal/intermetallic interface structure are helpful to understand and optimize the mechanical properties of eutectic alloys. Zhou [Citation22] revealed the structure features of the Al/Al2Cu interface and explained the formation mechanism of lattice dislocations. Based on this, Liu [Citation23] prepared laser surface remelted Al-Al2Cu eutectic alloy and elucidated that the performance of high strength and plasticity depends on the metal/intermetallic heterointerface. Furthermore, the modeling of interface strengthening in Al–Si eutectic alloys [Citation24] and the research on laser rapid solidified Al–Si fibrous eutectics [Citation25] demonstrated that synergistic enhancement of strength and plasticity of Al–Si can be achieved by coordinating the soft Al matrix and hard nano-scale Si eutectic phase through the heterogeneous interface. Therefore, the optimizing interface structure in eutectic alloys can improve their mechanical performance.
In combination with eutectic structures with the microalloying method, Sc is added to eutectic Al alloys to tune their creep performance [Citation26,Citation27]. For example, the increased Sc addition can cause a higher load transfer effect of the eutectic phase in Al-Ni-Sc alloy [Citation26]. However, there is a lack of in-depth discussion on microstructure-mechanical property relationship for these novel heat-resistant Al alloys, including (1) Microstructure characteristics involved Sc addition to eutectic alloys; (2) Strengthening mechanisms controlled by Sc-induced microstructures to alloy creep properties.
Therefore, the creep behavior of Al-1.75wt%Fe-1.25wt%Ni-0.2wt%Sc eutectic alloy (i.e. AlFeNi-0.2Sc alloy) was studied to show the influence of induced microstructure features by microalloying Sc. In comparison with the creep behavior of the AlFeNi alloy, the controlling creep mechanisms for the AlFeNi-0.2Sc alloy were quantitatively modeled and discussed. Specifically, Al3Sc precipitates at the Al/Al9FeNi interface were characterized to explain the corresponding load transfer effect, which was beneficial to optimizing creep properties.
2. Experiments
The AlFeNi-0.2Sc eutectic alloy was prepared by conventional gravity cast, as detailed in our previous work [Citation8,Citation9]. Before microstructure characterization and mechanical test, the as-cast alloy was heat treated at 300°C@4 h as the peak-aged state. The microstructure was characterized by Scanning Electron Microscope (SEM), and the element distribution was acquired by energy dispersive spectroscopy (EDS). The precipitates inside the Al matrix or at the Al/Al9FeNi interface were analyzed by Transition Electron Microscope (TEM) or Scanning Transition Electron Microscope (STEM). Meanwhile, the high-resolution TEM (HRTEM) image was acquired to demonstrate the lattice structure of precipitates. Based on the HRTEM image, the lattice strain nearby the interface was analyzed by Geometric Phase Analysis (GPA) [Citation28]. Besides, the electronic creep testing machine (RDL50) was used for the creep test. The applied creep stress was in the range of 20–60 MPa.
3. Results and discussions
AlFeNi is a typical eutectic alloy with the Al9FeNi and Al matrix as the main eutectic structure (Figure (a)). Comparably, AlFeNi-0.2Sc shows a similar microstructure (Figure (b)). Therefore, the eutectic structure can be divided into three sub-divisions according to microstructure features (Figure (a,b)), including primary Al (Sub-division I), eutectic boundary Al (Sub-division II) and eutectic internal Al (Sub-division III). Although microalloying 0.2 wt% Sc hardly affects the basic macro-morphology of eutectic structure (Figure (b)), it has promoted the formation of primary Al (Sub-division I), which is rare in eutectic AlFeNi alloy (Figure (a)).
Figure 1. Microstructure characteristics: (a) AlFeNi; (b) AlFeNi-0.2Sc. (c) Sc concentration in different areas. Al3Sc distribution in different zones of the AlFeNi-0.2Sc alloy at peak-aged state: (d) Eutectic boundary Al; (e) Eutectic internal Al.
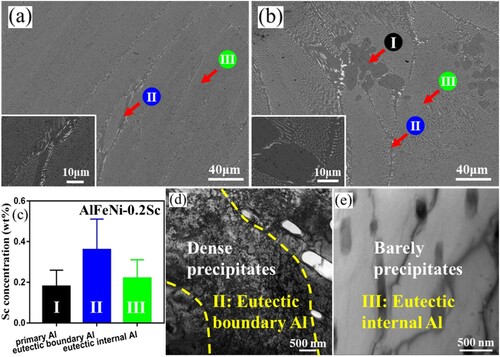
Sc mainly dissolves in the Al matrix of the AlFeNi-0.2Sc alloy. Influenced by element distribution during solidification in the AlFeNi-0.2Sc alloy, Sc tends to gather at grain boundaries [Citation29]. In detail, more Sc is pushed by the Al9FeNi phase to the eutectic boundary Al [Citation30], where the EDS result for Sc concentration is much higher than other sub-divisions (Figure (c)). Therefore, aggregated Al3Sc precipitates inside eutectic boundary Al are revealed (Figure (d)), and these precipitates are called matrix precipitates. The average diameter of these matrix precipitates is ∼5 nm [Citation16]. However, matrix precipitates are rarely seen inside the eutectic grains (Figure (e)). Herein, the precipitation behavior of Sc inside the eutectic grain may be changed, and we have identified precipitates at the Al/Al9FeNi interface by EDS and TEM analyses. For instance, a typical Al9FeNi phase with surrounding elements distribution is shown (Figure (a–b)), and the Sc element is rich at the Al/Al9FeNi interface.
Figure 2. (a, c) Eutectic phase inside grains of the AlFeNi-0.2Sc alloy at peak-aged state; (b) Element distributions around the eutectic phase; (d) Overall morphology of the precipitate at Position A near the Al/Al9FeNi interface; (e) HRTEM image at Position A.
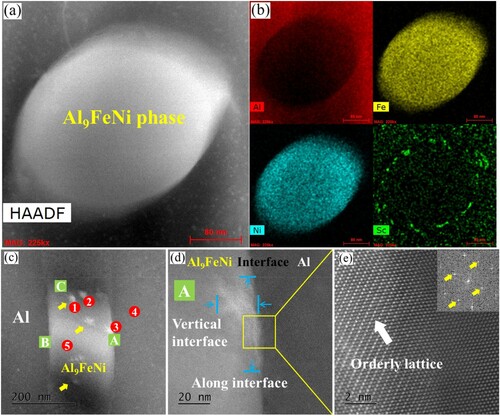
Observed at another Al9FeNi phase, several irregular patches with higher contrast are seen at the Al/Al9FeNi interface (Figure (c)). Then, five featured positions are selected to make the EDS test, and the results are shown in Table . Accordingly, Positions 1–3 should be precipitates containing Sc. Meanwhile, Sc is rarely detected in the Al matrix (Position 4) and eutectic phase (Position 5).
Table 1. Element contents (at%) of featured points at the eutectic phase and surrounding area of AlFeNi-0.2Sc alloy at peak-aged state.
Furthermore, Position A near the precipitate (Position 3) on the Al/Al9FeNi interface is characterized by an HRTEM image (Figure (d)). Herein, such precipitate size reaches tens of nanometers, and its shape presents irregular dendritic morphology. Besides, the cross-section of this precipitate is provided in SM (Supplementary Materials)-Part 1. The thickness of this precipitate is ∼5 nm, and the length is ∼30 nm in the direction along the interface. Its thickness is similar to the diameter of Al3Sc matrix precipitates, but the length is much longer than the size of matrix precipitates under a peak-aged state. The precipitate has an ordered lattice structure, and the superlattice diffraction pattern is shown in a Fourier Fast Transform image (Figure (e)). Therefore, the precipitate is referred to the L12-Al3Sc phase. This Al3Sc precipitate at the Al/Al9FeNi interface is called interface precipitate. Also, HRTEM images of Positions B and C are provided in SM-Part 2 to confirm the wide existence of interface precipitates.
To reveal characteristic structures at Al/Al9FeNi, Figure (a) identifies a certain orientation relationship (OR) between Al9FeNi and the Al matrix. The zone axis for the Al matrix is determined as [011]Al, and for the Al9FeNi phase is [00]Al9FeNi (Figure (a)). Under these parallel zone axes, the nearly paralleling planes are (11
)Al and (00
)Al9FeNi, although there is a ∼4.5° orientation difference between them. Then, the corresponding OR1 is written as
(1)
(1)
According to OR1, the (0
0)Al9FeNi plane is parallel to the (011)Al plane, and the interface is constructed using an Edge-to-Edge manner. The [100]Al9FeNi direction on the (0
0)Al9FeNi surface is nearly parallel to the [2
1]Al direction on the (011)Al surface. Therefore, the interface perpendicular to the image section is constructed by both (00
)Al9FeNi and (11
)Al planes. The schematic diagram of OR1 is shown in Figure (c).
Figure 3. (a) Al/Al9FeNi interface and crystalline orientation of each phase under this axis; (b) Lattice structure of Al9FeNi under the [00] axis; (c) Schematic diagram of OR1; (d) Lattice structure of (11
)Al; (e) Lattice structure of (00
)Al9FeNi; (f) Interface structure from the side view; (g) Schematic diagram of Sc precipitation in the interface structure.
![Figure 3. (a) Al/Al9FeNi interface and crystalline orientation of each phase under this axis; (b) Lattice structure of Al9FeNi under the [01¯0] axis; (c) Schematic diagram of OR1; (d) Lattice structure of (111¯)Al; (e) Lattice structure of (001¯)Al9FeNi; (f) Interface structure from the side view; (g) Schematic diagram of Sc precipitation in the interface structure.](/cms/asset/46541618-1360-434c-9d1f-9a8f5520e801/tmrl_a_2136016_f0003_oc.jpg)
Meanwhile, the Al9FeNi structure viewed from [00]Al9FeNi is shown in Figure (b). The distributions of Fe and Ni atoms in the structure are consistent with the TEM observation (Inset in Figure (b)). Herein, the marked section is (00
)Al9FeNi plane. According to the crystal structure, Al atoms on the plane can be classified into three types:A, B and C (Figure (b)). Type A atoms are on the plane, and type B and C atoms are on two sides of the plane. Therefore, the rotation angle between (00
)Al9FeNi and (11
)Al planes may ensure more atom coplanar and the interface stability can be improved.
The top views of both (11)Al and (00
)Al9FeNi planes are presented in Figure (d,e), respectively. Thus, the vertical interface structure from [11
]Al view is exhibited in Figure (f). Herein, the lattice structure is well matched at the local position (i.e. [2
0]Al9FeNi // [10
]Al), and the local mismatch is low (∼2%). However, there are some larger mismatches at another interface (i.e. ∼10% between [010]Al9FeNi and [011]Al), and the relatively larger lattice distortion and higher storage distortion energy should exist at these positions. Thus, the Al lattice structure (Lower elastic modulus phase) should be stretched and affected by the Al9FeNi lattice structure (Higher elastic modulus phase).
Accordingly, Figure (g) shows the interface structure after Sc precipitated at the Al/Al9FeNi interface. Since Sc has the larger atomic size, its segregation at these locations (Indicated by Black Arrows) can alleviate local distortions. Correspondingly, this may also be the vital reason for the interface precipitation of Al3Sc. During the heat treatment of the AlFeNi-0.2Sc alloy, Sc is attracted to precipitate at the Al/Al9FeNi interface to reduce local distortion and improve interface stability [Citation18,Citation31].
Experienced 300°C creep test, both AlFeNi and AlFeNi-0.2Sc alloys exhibit optimized creep performance. The detailed creep results are provided in SM-Parts 3 and 4. In comparison with creep properties of reported heat-resistant Al alloys at peak-aged and over-aged states [Citation16,Citation17,Citation20,Citation26,Citation27,Citation32–35], the AlFeNi alloy shows similar creep ability with Al-Ni [Citation32] and Al-Cu-Sc [Citation20] alloys (Figure (a)). Critically, the creep resistance of AlFeNi-0.2Sc alloy at a peak-aged state is highly improved. For instance, it has a steady-state creep rate of 9.6 × 10−10 s−1 at 300°C@40 MPa, which is 1–4 orders of magnitude lower than other heat-resistant Al alloys. Although the creep property of AlFeNi-0.2Sc is inferior to that of Al-Ni-0.2Sc [Citation21], the main reason is ascribed to the difference from the heat treatment method. This phenomenon can be explained by the research on the creep performance of Al-0.2Sc alloy treated in 300°C@6 h (Peak-aged state) or 24 h (Over-aged state) (Blue triangle in Figure (a)). Besides, the improved creep performance of Al-Ni-0.4Sc (Black hollow square in Figure (a)) over Al-Ni-0.2Sc alloy was also clear [Citation26], which was ascribed to the higher precipitation strengthening effect to creep improvement induced by more Al3Sc precipitates with higher Sc addition. Meanwhile, Ref. [Citation26] also contained a result that can support that the added Sc can cause a higher load transfer effect of the eutectic phase in the creep of the Al-Ni-Sc alloy, and this was not emphasized originally. However, this phenomenon complied well with our following in-depth analyses.
Figure 4. (a) Comparison of the creep behavior of Al alloys at 300°C; (b) Comparison of the dislocation creep behavior of AlFeNi alloy at 300°C; (c) Schematic diagram of Al3Sc precipitates under peak aging; (d) Interaction between dislocation and matrix precipitates; (e) FEM Simulation of stress distribution after the formation of transition layer around the eutectic phase; (f) Al3Sc precipitate layer around the eutectic phase and the lattice strain around the interface calculated by GPA: (g) Vertical interface; (h) Along interface (The white arrow points at the Al/Al9FeNi interface; the red circle marks the Al3Sc interface precipitate).
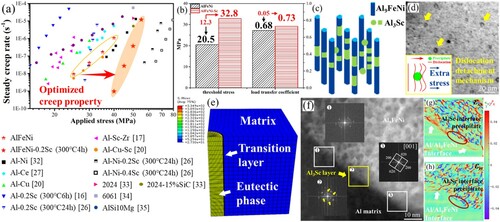
This work attempts to reveal the mechanism of Sc improving the creep properties of eutectic alloys. Therefore, the creep constitutive equation for dislocation creep of AlFeNi alloy at 300 °C (SM-Part 3) is modeled using a coupling modification [Citation36] by introducing both threshold stress (σth) and load transfer coefficient (α):
(2)
(2)
where σth-1 = 20.5 MPa; α1 = 0.68 (Figure (b)). Herein, the threshold stress originates from the interaction between Al9FeNi and dislocations to impede creep. Besides, the load transfer effect is the main way of Al9FeNi strengthens the matrix, due to its larger volume fraction and higher modulus [Citation37].
Similarly, the creep constitutive equation of the AlFeNi-0.2Sc alloy at 300°C is calculated at SM-Part 4, and provided as
(3)
(3)
where σth-2 = 32.8 MPa; α2 = 0.73 (Figure (b)). In addition to AlFeNi eutectic structures, Al3Sc precipitates should offer an intensive strengthening effect on creep.
For threshold stress, AlFeNi-0.2Sc alloy has a much higher value than AlFeNi alloy. Since AlFeNi-0.2Sc alloy has a similar eutectic structure, the interaction between Al9FeNi and dislocations for creep improvement is inherited thereby. Furthermore, the Al3Sc precipitate also has a superior ability to hinder dislocation movement. For example, Seidman [Citation16] found that the Al-0.2Sc alloy showed an increased creep performance than pure Al, and its threshold stress was ∼14 MPa at 300°C. Similarly, Al3Sc matrix precipitates (Figure (d)) can effectively impede dislocation movement (Inset in Figure (d)) in an alloy matrix. Generally, the threshold stress of AlFeNi-0.2Sc (32.8 MPa) is nearly equal to the sum of threshold stresses caused by eutectic phase (20.5 MPa (σth-1)) and Al3Sc precipitates (14 MPa [Citation16]).
Regarding the load transfer coefficient, the AlFeNi-0.2Sc alloy (α2 = 0.73) has a higher value over AlFeNi alloy (α1 = 0.68), indicating its higher contribution to creep. Since both alloys have similar eutectic structures, more attention is paid to the Al3Sc precipitate in the AlFeNi-0.2Sc alloy. For Al3Sc matrix precipitate, there is available analysis confirming its ever contribution by the load transfer effect [Citation16]. Therefore, the elevated load transfer coefficient should be accounted for more by Al/Al9FeNi interface structure with interface precipitates, i.e.:
Macroscopically, Al3Sc interface precipitates are regarded as part of the eutectic phase (Figure (c)), which is equivalent to an increased eutectic phase volume fraction. Meanwhile, finite element modeling (FEM) is to discuss stress distribution at the Al/Al9FeNi interface with/without interface precipitates. In the AlFeNi-0.2Sc alloy, the Al3Sc interface precipitates exhibit a certain length and thickness by microstructure characterization (Figure (c–e) and Figure S1). Although these interface precipitates do not form a continuous layer at the interface, they precipitate in large quantities hereby (Figure (a,b)). To discuss stress distribution around the Al9FeNi/Al3Sc/Al structure related to the load transfer effect of creep, the situation is very complicated. Therefore, the Al3Sc interface precipitates are assumed to be a continuous layer for simplicity in the FEM model. Furthermore, a detailed discussion on this issue is included in SM-Part 5. The result shows that the eutectic structure with interface precipitates shares higher stress than only the eutectic structure during deformation (Figure (e) and Figure S5).
Microscopically, Al3Sc interface precipitates can alter the Al/Al9FeNi interface structure to affect the load transfer effect. Before the external stress applies to the alloy, there are differences in lattice parameters between Al9FeNi and Al matrix that contributed to interface mismatch at interface structure (Figure (f–h)). Since both the lattice parameter and elastic modulus of the Al9FeNi phase are larger than the Al matrix, the Al lattice is subjected to tensile stress to cause corresponding tensile strain through the interface structure. During transferring load process, the applied external stress causes the deformation of the Al matrix initially. Then, the eutectic Al9FeNi phase sustains the load transferred by the interface structure. From coordination deformation, the eutectic phase co-shares the load from the matrix to restrain matrix deformation, and the actual matrix strain becomes smaller. Therefore, the initial tensile stress at the Al/Al9FeNi interface reduces load transfer efficiency. When Al3Sc precipitates at the interface, Sc tends to aggregate at the position under tensile stress because an Sc atom has a slightly larger size than Al (Figure (g)). Furthermore, an HRTEM image of the Al/Al9FeNi interface with interface precipitates (Position 2) (Positions 1 and 3 are Al matrix) is shown (Figure (f)), and related lattice strains are calculated by GPA (Geometric Phase Analysis, Figure (g–h)). Herein, the Al matrix presents tensile stress, and it is alleviated by the Al3Sc precipitate. Besides, the lattice strain around the Al3Sc interface precipitate characterized by STEM and GPA analyses is made in SM-Part 6, which also supports the conclusion from Figure (f–h). Therefore, the Al3Sc interface precipitate can optimize load transfer efficiency, and the load transfer coefficient is increased accordingly.
4. Conclusion
Microalloying Sc into AlFeNi eutectic can induce the formation of Al3Sc precipitates at both the Al/Al9FeNi interface and Al matrix. Therefore, this novel AlFeNi-0.2Sc alloy shows superior creep properties over available reports. By coupling modification analyses on the creep constitutive equation, both threshold stress and load transfer coefficient are quantitatively acquired. In detail, threshold stress is increased by the Al3Sc matrix precipitates by impeding dislocation movement, and the load transfer coefficient is improved by interface precipitates. Specifically, both microscopic and macroscopic factors for the interface structure with interface precipitates are analytically discussed to enhance the load transfer effect. Generally, this work provides a solid understanding to improve the creep property of eutectic heat-resistant Al alloys by manipulating eutectic phase/matrix interface structure.
Supplemental Material
Download MS Word (3.6 MB)Acknowledgments
Zeyu Bian: Conceptualization, Investigation, Validation, Data curation, Formal analysis, Writing-original draft. Chen Yang: Investigation, Data curation, Formal analysis, Writing-review & editing. Hongyi Zhu: Data curation, Formal analysis, Writing-review & editing. Dechao Zhao: Formal analysis, Writing-review & editing. Mingliang Wang: Conceptualization, Funding acquisition, Formal analysis, Writing- review & editing. Huawei Zhang: Conceptualization, Resources, Formal analysis, Writing-review & editing. Zhe Chen: Resources, Writing-review & editing. Haowei Wang: Supervision, Writing-review & editing.
Disclosure statement
No potential conflict of interest was reported by the author(s).
Additional information
Funding
References
- Pandey P, Makineni SK, Gault B, et al. On the origin of a remarkable increase in the strength and stability of an Al rich Al-Ni eutectic alloy by Zr addition. Acta Mater 2019;170:205–217.
- Wang LY, Ye B, Bai Y, et al. Effect of Zr and Sc micro-additions on the microstructure and mechanical properties of as-cast Al-5Ce alloy. Mater Sci Eng A. 2021;822:141654.
- Tiwary CS, Pandey P, Sarkar S, et al. Five decades of research on the development of eutectic as engineering materials. Prog Mater Sci 2021;9:100793.
- Du Y, Chang YA, Huang B, et al. Diffusion coefficients of some solutes in fcc and liquid Al: critical evaluation and correlation. Mater Sci Eng A. 2003;363(1–2):140–151.
- Zuo LJ, Ye B, Feng J, et al. Effect of ε-Al3Ni phase on mechanical properties of Al–Si–Cu–Mg–Ni alloys at elevated temperature. Mater Sci Eng A. 2020;772:1387.
- Poplawsky JD, Milligan BK, Allard LF, et al. The synergistic role of Mn and Zr/Ti in producing L12 co-precipitates in Al-Cu alloys. Acta Mater 2020;194:577–586.
- Knipling KE, Dunand DC, Seidman DN. Criteria for developing castable, creep resistant aluminum-based alloys-a review. Z Für Met. 2006;97(3):246–265.
- Bian ZY, Dai SH, Wu L, et al. Thermal stability of Al-Fe-Ni alloy at high temperatures. J Mater Res Technol. 2019;8(3):2538–2548.
- Bian ZY, Liu YT, Dai SH, et al. Regulating microstructures and mechanical properties of Al-Fe-Ni alloys. Prog Nat Sci Mater Int. 2020;30:54–62.
- Liu YT, Bian ZY, Chen Z, et al. Effect of Mn on the elevated temperature mechanical properties of Al-La alloys. Mater Char. 2019;155:109821.
- Sims ZC, Rios OR, Weiss D, et al. High performance aluminum-cerium alloys for high-temperature applications. Mater Horiz 2017;4:1070–1078.
- Gladman T. Precipitation hardening in metals. Mater Sci Technol 1999;15(1):30–36.
- Li YJ, Muggerud AMF, Olsen A, et al. Precipitation of partially coherent α-Al(Mn,Fe)Si dispersoids and their strengthening effect in AA 3003 alloy. Acta Mater 2012;60:1004–1014.
- Jia QB, Zhang F, Rometsch P, et al. Precipitation kinetics, microstructure evolution and mechanical behavior of a developed Al–Mn–Sc alloy fabricated by selective laser melting. Acta Mater 2020;193:239–251.
- Spierings AB, Dawson K, Uggowitzer PJ, et al. Influence of SLM scan-speed on microstructure, precipitation of Al3Sc particles and mechanical properties in Sc- and Zr-modified Al-Mg alloys. Mater Des 2018;140:134–143.
- Seidman DN, Marquis EA, Dunand DC. Precipitation strengthening at ambient and elevated temperatures of heat-treatable Al(Sc) alloys. Acta Mater 2002;50:4021–4035.
- Fuller CB, Seidman DN, Dunand DC. Mechanical properties of Al(Sc,Zr) alloys at ambient and elevated temperatures. Acta Mater 2003;51(16):4803–4814.
- Biswas A, Siegel DJ, Seidman DN. Simultaneous segregation at coherent and semicoherent heterophase interfaces. Phys Rev Lett 2010;105:076102.
- Chen BA, Liu G, Wang RH, et al. Effect of interfacial solute segregation on ductile fracture of Al–Cu–Sc alloys. Acta Mater 2013;61:1676–1690.
- Gao YH, Yang C, Zhang JY, et al. Stabilizing nanoprecipitates in Al-Cu alloys for creep resistance at 300°C. Mater Res Lett. 2019;7(1):18–25.
- Chanda B, Potnis G, Jana PP, et al. A review on nano-/ultrafine advanced eutectic alloys. J Alloys Compd 2020;827:154226.
- Zhou Q, Hua DP, Du Y, et al. Atomistic study of atomic structures and dislocation nucleation at Al/Al2Cu interfaces. Int J Plast 2019;120:115–126.
- Liu GS, Wang SJ, Misra A, et al. Interface-mediated plasticity of nanoscale Al-Al2Cu eutectics. Acta Mater 2020;186:443–453.
- Wu WQ, Gong MY, Wei BQ, et al. Atomistic modeling of interface strengthening in Al-Si eutectic alloys. Acta Mater 2022;225:117586.
- Wei BQ, Wu WQ, Xie DY, et al. In situ characterization of tensile behavior of laser rapid solidified Al-Si heterogeneous microstructures. Mater Res Lett. 2021;9:507–515.
- Suwanpreecha C, Toinin JP, Michi RA, et al. Strengthening mechanisms in Al-Ni-Sc alloys containing Al3Ni microfibers and Al3Sc nanoprecipitates. Acta Mater 2019;164:334–346.
- Yi M, Zhang P, Yang C, et al. Improving creep resistance of Al-12 wt.% Ce alloy by microalloying with Sc. Script Mater. 2021;198:113838.
- Hÿtch MJ, Snoeck E, Kilaas R. Quantitative measurement of displacement and strain fields from HREM micrographs. Ultramicroscopy. 1998;74:131–146.
- Knipling KE, Dunand DC, Seidman DN. Ambient- and high-temperature mechanical properties of isochronally aged Al-0.06Sc, Al-0.06Zr and Al-0.06Sc -0.06Zr (at. %) alloys. Acta Mater 2011;59(3):943–954.
- Bian ZY, Xiao YK, Hu L, et al. Stimulated heterogeneous distribution of Sc element and its correlated local hardening effect in Al-Fe-Ni-Sc alloy. Mater Sci Eng A. 2020;771:138650.
- Nie JF, Zhu YM, Liu JZ, et al. Periodic segregation of solute atoms in fully coherent twin boundaries. Science. 2013;340:957–960.
- Himbeault DD, Cahoon JR. Creep regimes for directionally solidified Al-Al3Ni eutectic composite. Metall Trans A. 1993;24(12):2721–2730.
- Spigarelli S, Cabibbo M, Evangelista E, et al. Creep properties of an Al-2024 composite reinforced with SiC particulates. Mater Sci Eng A. 2002;328:39–47.
- Ma Y, Langdon TG. Creep behavior of an Al-6061 metal matrix composite produced by liquid metallurgy processing. Mater Sci Eng A. 1997;230:183–187.
- Glerum JA, Mogonye J, Dunand DC. Creep properties and microstructure evolution at 260–300 °C of AlSi10Mg manufactured via laser powder-bed fusion. Mater Sci Eng A. 2022;843:143075.
- Fernández R, González-Doncel G. Threshold stress and load partitioning during creep of metal matrix composites. Acta Mater 2008;56:2549–2562.
- Chen CL, Richter A, Thomson RC. Investigation of mechanical properties of intermetallic phases in multi-component Al–Si alloys using hot-stage nanoindentation. Intermetallics. 2010;18:499–508.