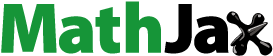
Abstract
This study investigates the evolutions of microstructure and performance of TiNbZrTaHf-based alloys from equiatomic high-entropy alloys to Ti-rich dilute alloys. A novel biocompatible alloy, Ti50Nb12.5Zr12.5Ta12.5Hf12.5, was developed with a high yield strength of 839 ± 12 MPa, low modulus of 61.5 GPa, low magnetic susceptibility of ∼1.99 × 10−6 cm3g−1, and unprecedented tensile plasticity of 28.7 ± 2.2%. The study discusses the underlying mechanisms responsible for these superior performances, attributing the exceptional plasticity to the activation of cross-slip dislocations, enhanced dynamic recovery and high resistance to crack propagation. The findings provide new insights into the development of biomedical titanium alloys.
GRAPHICAL ABSTRACT
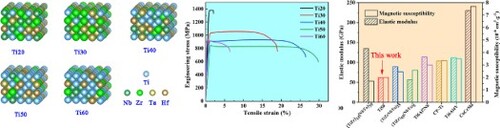
IMPACT STATEMENT
This study introduces a novel biocompatible concentrated alloy with high strength, low modulus and unprecedented ductility, providing new insights for developing high-performance biomedical titanium alloys.
1. Introduction
In recent years, there has been significant progress in the development of beta-type titanium alloys for biomedical applications, with a focus on non-toxic and allergy-free alloys [Citation1–3]. Among them, Ti-35Nb-7Zr-5Ta (TNZT) is considered one of the most promising candidates for the next generation of implant materials due to its extremely low elastic modulus of about 55 GPa [Citation4]. However, the newly developed beta-type titanium alloys, including TNZT, have relatively low yield strength (400-800 MPa) and medium tensile plasticity (<15%) [Citation4,Citation5]. To address this issue, many alloy strengthening and toughening strategies have to be taken into account in processes [Citation5,Citation6]. Recently, a new alloy design concept, termed high-entropy alloys (HEAs) or concentrated alloys, has been presented [Citation7–9]. Among the newly developed alloys, many body-centered cubic (BCC) HEAs containing refractory metal elements have demonstrated excellent biocompatibility [Citation10,Citation11], but their high elastic modulus and relatively low plasticity always limit their use in biomedical applications [Citation8,Citation9]. Recently, high strength and toughness TiNbZrTa-based HEAs were reported [Citation12–14]. Unlike conventional alloys, such as TNZT, these biocompatible HEAs are typically composed of multiple principal alloying elements or have (near) equiatomic concentrations [Citation7–9], thus have relatively high density. Despite having a crystalline order similar to traditional metals, the HEAs are compositionally disordered and always exhibit local chemical short-range order (CSRO) [Citation15–20]. The experimental investigation on the TiNbZrTa-based HEAs showed that CSRO or local chemical fluctuation contributes to the increment in both strength and ductility due to strongly promoted local double cross-slips of dislocations [Citation13], which is different from the deformation mechanism of traditional homogeneous beta-type titanium alloys, such as TRIP (Transformation-Induced Plasticity) and TWIP (Twinning-Induced Plasticity) effect [Citation21]. Therefore, it would be of great engineering and academic value to develop heterogeneous TiNbZrTa-based HEAs into TNZT-like single-principal biocompatible titanium alloys with improved performance by introducing similar structure and deformation mechanism with parent HEAs.
Motivated by this idea, we studied TiNbZrTaHf-based HEA alloys with increasing Ti content. We discovered that a novel Ti-rich biocompatible Ti50Nb12.5Zr12.5Ta12.5Hf12.5 concentrated alloy, with a composition between equiatomic HEAs and commercial TNZT alloys, possesses a unique combination of high plasticity, high yield strength, low modulus, and low magnetic susceptibility, making it a promising material for use in next-generation medical implants.
2. Materials and methods
Alloy ingots with nominal compositions of Tix(NbTaHfZr)100-x (at. %, x = 20, 30, 40, 50 and 60) (referred to as Ti20, Ti30, Ti40, Ti50 and Ti60) were prepared by arc-melting a mixture of pure metals (purity >99.9%). The alloy ingots were re-melted at least five times to ensure compositional homogeneity. The as-cast ingots were hot-rolled into a sheet with a thickness of 8 mm (thickness reduction of approximately 30%) at 1223 K and then cold-rolled to a final thickness of 1 mm. The rolled sheets were then subjected to recrystallisation annealing at 1073 K for 4 h in a vacuum sintering furnace, followed by furnace cooling. The phase constitution of the samples was characterized by X-ray diffraction (XRD) (X'pert Powder, PANalytical, Netherlands). The microstructure was investigated by A transmission electron microscope (TEM, FEI Talos F200X, America) and scanning electron microscopy (SEM, Carl Zeiss Gemini 300 microscope) equipped with an Oxford Symmetry S2 electron backscatter diffraction (EBSD) detector. To evaluate the mechanical properties, uniaxial tensile tests were performed along the rolling direction and on dog-bone-shaped samples with a gauge section 3 mm in width, 1 mm in thickness, and 14 mm in length at a strain rate of 5 × 10−4 s−1 using a universal testing machine (Instron 8860, USA). Strain values were measured using an electronic extensometer. The detailed methodology for the first-principles calculations of TiNbZrTaHf-based alloys is available in the supplementary materials.
3. Results and discussion
The XRD patterns of cool-rolled and annealed TiNbZrTaHf-based alloys with varying Ti contents are shown in Figure a. Samples with Ti contents not exceeding 50 at.% primarily exhibit a single-phase BCC structure. However, when the Ti content increases to 60 at.%, a trace of HCP α-Ti phase is detected, indicating that higher Ti content induces phase instability in the TiNbZrTaHf-based alloys. Notably, unlike the cast TiNbZrTaHf HEA [Citation14,Citation22], the major peak of the deformed and annealed samples shifted from the (110) plane to the (211) plane. EBSD analyses reveal this is mainly due to formation of weak textures. Figure b-f presents the inverse pole figures of the cool-rolled and annealed samples. Abundant deformation bands are clearly observed in the Ti20 sample, indicating no recrystallisation (Figure b). The inverse pole figure and corresponding local orientation map of Ti30 sample demonstrate a partial recrystallisation structure with a bimodal distribution of grain size (Figure c and Figure h). With a further increase in Ti content, Ti40, Ti50 and Ti60 are completely recrystallised (Figure d-f and Figure i-k). The average size of completely recrystallised grains for the Ti30, Ti40,Ti50 and Ti60 is determined to be 15.2 ± 2.3 µm, 20.6 ± 3.0 µm, 24.4 ± 4.2 µm and 28.4 ± 3.3 µm, respectively. The increasing grain size with increase of Ti content is primarily ascribed to higher diffusion coefficient of Ti element at 1073 K comparing with other elements [Citation27], as well as decreasing recrystallisation temperature. Furthermore, SEM-energy dispersive X-ray (EDX), high-angle annular dark-field (HAADF) images and corresponding elemental distribution maps reveal homogeneous composition distribution in all crystallized samples (Figure l-q and Fig.S2). The selected area electron diffraction (SAED) pattern along the [110] direction confirms that the alloy Ti30 is a single-phase BCC solid solution without the precipitation of second phases or phase separation (Figure l).
Figure 1. (a) XRD patterns of TiNbZrTaHf alloys with different Ti contents; Inverse pole figures from EBSD of Ti20 (b), Ti30 (c), Ti40 (d), Ti50 (e) and Ti60 (f), and the corresponding local misorientation maps (g-k); (l) HAADF image and (m-q) corresponding STEM-EDX elemental distribution maps from Ti30 alloy after recrystallisation annealing at 1073 K, inset in (l) is corresponding SAED pattern along [110] direction.
![Figure 1. (a) XRD patterns of TiNbZrTaHf alloys with different Ti contents; Inverse pole figures from EBSD of Ti20 (b), Ti30 (c), Ti40 (d), Ti50 (e) and Ti60 (f), and the corresponding local misorientation maps (g-k); (l) HAADF image and (m-q) corresponding STEM-EDX elemental distribution maps from Ti30 alloy after recrystallisation annealing at 1073 K, inset in (l) is corresponding SAED pattern along [110] direction.](/cms/asset/6f432c9d-b271-40b5-a7e7-87b73c606bd6/tmrl_a_2197942_f0001_oc.jpg)
Figure 2. (a) Tensile stress–strain curves of the TiNbZrTaHf based alloys with different Ti contents; (b) comparison of the developed Ti-rich TiNbZrTaHf concentrated alloys with conventional TNZT alloys [Citation4,Citation5,Citation23–35] and BCC refractory HEAs [Citation12,Citation13,Citation36–41]; (c) magnetization variation as a function of applied magnetic field at room temperature; (d) comparison of magnetic susceptibilities and Young's elastic modulus of alloys Ti50 with some BCC HEAs, titanium alloys and alloys commonly used in medical devices [Citation12,Citation45,Citation46].
![Figure 2. (a) Tensile stress–strain curves of the TiNbZrTaHf based alloys with different Ti contents; (b) comparison of the developed Ti-rich TiNbZrTaHf concentrated alloys with conventional TNZT alloys [Citation4,Citation5,Citation23–35] and BCC refractory HEAs [Citation12,Citation13,Citation36–41]; (c) magnetization variation as a function of applied magnetic field at room temperature; (d) comparison of magnetic susceptibilities and Young's elastic modulus of alloys Ti50 with some BCC HEAs, titanium alloys and alloys commonly used in medical devices [Citation12,Citation45,Citation46].](/cms/asset/391eb46a-7f5a-41bb-ac12-be2a9869868a/tmrl_a_2197942_f0002_oc.jpg)
Figure a shows the room-temperature tensile engineering stress–strain curves of the TiNbZrTaHf-based alloys with different Ti contents. The equiatomic TiNbZrTaHf HEA (Ti20) demonstrates an ultrahigh yield strength but limited tensile plasticity due to high-density dislocation and internal stress in the unrecrystallized sample. As the Ti content increases from 20% to 50%, the yield strength decreases from 1378 ± 20 MPa to 839 ± 12 MPa, while the corresponding elongation increases from 2.1 ± 0.2% to 28.7 ± 2.2%, respectively. In the case of Ti60 alloy, the formation of a minor HCP phase results in decreased plasticity and increased yield strength. Notably, the Ti50 alloy exhibits a remarkable combination of strength and plasticity. Figure b presents a comparison of the newly developed alloys with conventional TNZT beta-Ti alloy and BCC HEAs. Evidently, the newly developed alloys (Ti30, Ti40 and Ti50) achieve unprecedented levels of strength and ductility. In particular, the plasticity of the Ti50 alloy surpasses that of commercial TNZT alloys [Citation4,Citation5,Citation23–35] and most BCC refractory HEAs [Citation12,Citation13,Citation36–41].
To prevent the stress-shielding effect in biomaterials, a low elastic modulus is necessary. In this study, the Young's elastic modulus is derived from stress–strain curves. The results indicate that the Young's elastic modulus decreases from 127.86 GPa to 61.54 GPa as the Ti content increases from 20 at.% to 50 at.%, but sharply increases to 87.21 GPa when the Ti60 alloy forms an HCP phase. The Young's elastic modulus is an intrinsic property of materials, closely related to their crystal structure. For example, BCC-structured Ti generally has a lower Young's elastic modulus than HCP-structured Ti [Citation42]. The increase in the Young's elastic modulus in the Ti60 alloy is due to the formation of the HCP phase. Valence electron concentration (VEC) is an important factor used to determine the phase structure and stability of metals, such as Ti alloys [Citation43] and some HEAs [Citation7–9]. VEC for a multi-component alloy can be estimated by equation: , where
is the valence electron concentration of the
th element [Citation12]. However, it is still necessary to further verify whether VEC can be used to determine the phase stability of Ti-rich BCC HEAs and establish its correlation with Young's elastic modulus. In this study, the VEC values for Ti20, Ti30, Ti40, Ti50, and Ti60 are determined to be 4.40, 4.35, 4.30, 4.25, and 4.20, respectively. According to the XRD results (Figure a), it can be concluded that the TiNbZrTaHf based alloys retained a single BCC structure when VEC ≥ 4.25. The critical VEC of 4.25 for the transition between the HCP and BCC structures is close to the previously reported value of 4.18 [Citation12]. The results confirmed that VEC can be used to predict the structure of Ti-rich HEAs. In this regime with VEC ≥ 4.25, Young’s elastic modulus decreased monotonically with decreasing VEC. This trend can be explained by the fact that the Young's modulus in the <100> direction of BCC crystals is typically lowered by reducing c11-c12 [Citation12,Citation42], which generally decreases with decreasing d + s valence electrons (i.e. VEC) for transitional metals with BCC structure [Citation44]. Therefore, the low elastic modulus achieved in Ti-50 alloy is mainly due to its small VEC while simultaneously maintaining the BCC structure.
To ensure accurate magnetic resonance imaging (MRI) measurements, it is important for implants to have a low magnetic susceptibility. Figure c illustrates the magnetic variation of TiNbZrTaHf-based alloys with respect to the applied magnetic field. Linear fitting of this data shows that the magnetic susceptibilities of these alloys monotonically increase from 1.4517–2.2526 × 10−6 cm3g−1 as the Ti content increases (as shown in the inset of Figure c). Figure d compares the Young's elastic modulus and magnetic susceptibility of sample Ti50 with those of several representative biomechanical materials, including Co-Cr-Mo, CP-Ti, Ti-6Al-4 V, Ti-6Al-7Nb alloys and typical BCC HEAs [Citation12,Citation45–47]. The results show that the elastic modulus of Ti50 (∼61.54 GPa) and its magnetic susceptibility (1.99 × 10−6 cm3g−1) are lower than those of the aforementioned alloys [Citation12,Citation45–47]. The low elastic modulus, low magnetic susceptibility, high yield strength, and exceptional plasticity of the developed Ti50 alloy make it highly suitable for use in next-generation medical implantations.
While most refractory HEAs with a BCC structure are recognized for their high strength and limited ductility [Citation9], the Ti50 alloy developed in this study demonstrates exceptional plasticity. To understand the source of this plasticity, the deformation mechanism of the Ti50 alloy was examined. When a tensile strain of 6% was applied to the sample, straight slip traces with uniform spacing of about 20.1 µm were formed uniformly in the entire deformed region, indicating the dominance of planar slips of dislocations in the early stage of plastic deformation, as shown in Figure a-1. Moreover, cross-slipped bands were occasionally observed in some regions (Figure a-2), indicating the activation of multiple slip systems [Citation13,Citation48]. As the tensile strain reached 24%, necking occurred (Figure b-1), and closer inspection revealed wavy slips with spacing of approximately 0.8 µm dominating the middle and final stages of plastic deformation (Figure b-2, Figure b-3, and Figure b-4). When the sample broke, on the fracture surface shown in Figure c, numerous cross-slip bands were observed at the tips of the cracks (Figure c-1 and Figure c-2). Additionally, high-density flat-shaped dimples with a diameter of about 5.1 µm covered most of the fracture surface (Figure c-3), resembling the Taylor meniscus instability pattern [Citation49]. This type of pattern is often found in amorphous materials such as metallic glasses [Citation50], polymers [Citation51], and liquid interfaces [Citation52]. More recently, these patterns were also observed on the fracture surfaces of high-strength and toughness metastable Ti–Mo alloys [Citation53]. The presence of Taylor patterns suggests a significant temperature rise in the slip bands or cracks, resulting in the formation of a viscous layer [Citation49]. The conversion of mechanical energy to heat, adiabatic heating, and frictional heating are the possible reasons for the localized temperature increase.
Figure 3. Evolution of the microstructure of Ti50 sample during deformation; (a) microstructure of sample with 6% tensile strain, a-1 and a-2 is the surface morphology from the different region of sample, respectively, a-3 and a-4 is the SEM image and corresponding EBSD of microcrack; (b) microstructure of sample with 24% tensile strain, b1-b3 present necking and cracking of sample, b4 shows wavy deformation bands; (c) microstructure of sample after fracture, c-1 is the surface morphology of the sample near the crack, c-2 shows the detail of deformation bands, c-3 indicates fractorgraphy; (d) schematic illustration showing the change in dislocation structures during deformation.
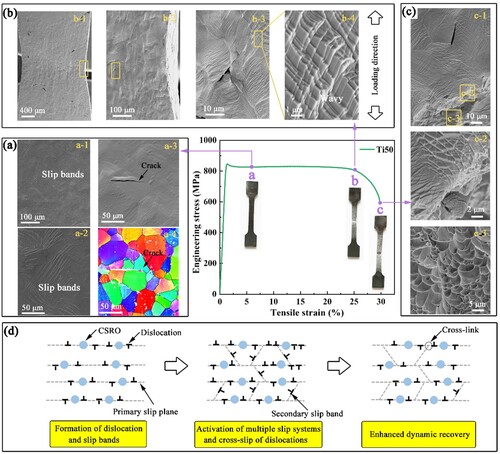
Based on above deformation mechanism, the exceptional plasticity of Ti50 alloy can be rationalized. When stress is applied to Ti50, dislocations of the primary slip system may begin to operate first, forming straight slip bands (Figure a). For further deformation, a secondary slip system is activated, resulting in cross or wavy slip bands, which form cross-links (Figure b-4) [Citation48]. Because of the cross-links of slip bands and possible CSRO [Citation15–17,Citation54], dislocation motion would be impeded. For further deformation, dislocation cross slips may occur, transferring the planar slips of the dislocation into various atomic planes (Figure d). Cross-slips of dislocations decrease the dislocation density on a certain atomic plane, thus effectively avoiding the dislocation tangles and stress concentration of planar slips [Citation13]. Therefore, a slight stress increase was observed in the stress–strain curve during the plastic deformation stage (Figure a). Another possible mechanism is that such secondary slip or cross-slip dislocations may be easily annihilated, that is, dynamic recovery may occur significantly, thus resulting in a consistently low dislocation density during deformation. With increase of deformation, the dynamic recovery may be more significant because of the decreasing space for dislocation motion by forming high-density cross-links and the temperature rise in the slip bands [Citation55]. Both the enhanced dynamic recovery and cross-slips of dislocations would suppress dislocation pile-up, leading to the release of local concentrated stress, which delays the formation of cracks.
The Ti50 alloy showed remarkable plasticity, but microcracks were unexpectedly observed at the grain boundary in samples with a tensile strain of only 6% (Figure a-3 and Figure a-4). Generally, the formation of cracks during deformation indicates that the material is approaching failure [Citation56]. However, the Ti50 alloys demonstrated an ultimate plastic strain of 28.7 ± 2.2%, which is at least four times the strain of the initial crack formation (<6%). The fact that microcracks formed long before the material fractured suggests that the Ti50 alloy has an exceptionally high resistance to crack propagation. The resistance to crack propagation in solid solution alloys depends on the competition between dislocation emissions and the propagation of cleavage near the crack tip [Citation44,Citation57]. The cleavage propagation and dislocation emissions near the crack tip closely relate to the surface energies (γsurf) of cleavage planes and unstable stacking fault energies (γusf) of specific slip systems, respectively [Citation58]. Approximately, an alloy with a higher ratio of γsurf /γusf can be considered to have a higher likelihood of being intrinsically ductile [Citation58,Citation59]. For BCC-structured materials, 110<111> is one of the most common slip systems during plastic deformation [Citation9,Citation59]. In order to determine the surface energies and unstable stacking fault (γsurf and γusf) of a TiNbZrTaHf-based alloy with varying Ti compositions, density functional theory (DFT) calculations were conducted using the VASP code [Citation58]. The resulting values for γusf of the (110) < 11 > slip systems and γsurf of (110) plane are presented in Figure a. The data shows that γusf decreases from 0.411 J/m2 to 0.367 J/m2 with an increase in Ti content from 20 at. % to 60 at. % in the TiNbZrTaHf alloy, while γsurf remains relatively constant at a value of 1.55 ± 0.55 J/m2 for all alloy compositions (Figure a). The ratio between the two types of stress intensity factors, γsurf/γusf, is displayed in Figure b, which indicates an increasing trend with increasing Ti content. The Ti50 alloy has a high γsurf/γusf of 3.95, which is located in the ductility zone compared with previous studies and larger than most of the quaternary alloys screened in the 10-component compositional space [Citation58]. The trend of γsurf/γusf suggests that increasing the Ti content in TiNbZrTaHf based alloy improves dislocation mobility but has little effect on cleavage fracture propagation. When the dislocations at the crack tip are easily activated or have high mobility, they blunt the cracks and delay extension (Figure c). Although EBSD and XRD tests revealed some degree of texture in the samples, the Schmid factors of samples with varying titanium contents showed no significant change as the titanium content increased (Fig.S3). In other words, the weak texture in this study does not play a decisive role in the plasticity. The increased plasticity for the TiNbZrTaHf-based alloy with increasing Ti content results from the increasing resistance to crack propagation. This explains why the Ti50 alloy exhibits higher tensile plasticity than cast or completely recrystallized equiatomic TiNbZrTaHf HEA (28.7% vs. 18.5% [Citation22]). These results offer valuable insights into the underlying mechanisms governing the mechanical properties of TiNbZrTaHf-based alloys, and suggest potential avenues for optimizing their performance in various applications.
Figure 4. (a) Unstable stacking fault energy (γusf) and surface energy (γsurf) of TiNbZrTaHf based alloys predicted from DFT calculations. The above and below inset is the supercell for calculations of surface energies and unstable stacking fault energy, respectively. These figures show a projection along the [−112] direction; (b) evolution of γsurf/γusf in TiNbZrTaHf based alloys with different Ti contents; (c) schematic of crack evolution during deformation, showing extension of cracking under loading, and sharp crack is blunted crack by the dislocation emission.
![Figure 4. (a) Unstable stacking fault energy (γusf) and surface energy (γsurf) of TiNbZrTaHf based alloys predicted from DFT calculations. The above and below inset is the supercell for calculations of surface energies and unstable stacking fault energy, respectively. These figures show a projection along the [−112] direction; (b) evolution of γsurf/γusf in TiNbZrTaHf based alloys with different Ti contents; (c) schematic of crack evolution during deformation, showing extension of cracking under loading, and sharp crack is blunted crack by the dislocation emission.](/cms/asset/c1bbbf49-fb8c-42ac-b46a-17e801a2848c/tmrl_a_2197942_f0004_oc.jpg)
4. Conclusions
In this study, a novel biocompatible Ti50Nb12.5Zr12.5Ta12.5Hf12.5 concentrated alloy with a high yield strength of 839 ± 12 MPa, low modulus of 61.5 GPa, low magnetic susceptibility of ∼1.99 × 10−6 cm3g−1 and unprecedented tensile plasticity of 28.7 ± 2.2% was developed by tuning the Ti content of equal-atomic-ratio TiNbZrTaHf high-entropy alloys. The high plasticity of the Ti50Nb12.5Zr12.5Ta12.5Hf12.5 alloy may originate from the enhanced dynamic recovery, cross-slips of dislocations and high resistance to crack propagation. The newly developed alloy has enormous potential to be the next generation of biological implant materials.
Supplemental Material
Download MS Word (2.9 MB)Acknowledgments
Special thanks to Sinoma Institute of Materials Research (Guang Zhou) Co., Ltd (SIMR) for its support in TEM testing.
Disclosure statement
No potential conflict of interest was reported by the author(s).
Data availability statement
The data that support the findings of this study are available from the corresponding author upon reasonable request.
Additional information
Funding
References
- Li J, Qin L, Yang K, et al. Materials evolution of bone plates for internal fixation of bone fractures: A review. J Mater Sci Technol. 2020;36:190–208. doi:10.1016/j.jmst.2019.07.024.
- Batalha RL, Batalha WC, Deng L, et al. Processing a biocompatible Ti–35Nb–7Zr–5Ta alloy by selective laser melting. J Mater Res. 2020;35(9):1143–1153. doi:10.1557/jmr.2020.90.
- Rack HJ, Qazi JI. Titanium alloys for biomedical applications. Mater Sci Eng: C. 2006;26(8):1269–1277. doi:10.1016/j.msec.2005.08.032.
- Luo JP, Sun JF, Huang YJ, et al. Low-modulus biomedical Ti-30Nb-5Ta-3Zr additively manufactured by Selective Laser Melting and its biocompatibility. Mater Sci Eng C Mater Biol Appl. 2019;97:275–284. doi:10.1016/j.msec.2018.11.077.
- Luo X, Liu LH, Yang C, et al. Overcoming the strength–ductility trade-off by tailoring grain-boundary metastable Si-containing phase in β-type titanium alloy. J Mater Sci Technol. 2021;68:112–123. doi:10.1016/j.jmst.2020.06.053.
- Luo X, Yang C, Li RY, et al. Effect of silicon content on the microstructure evolution, mechanical properties, and biocompatibility of β-type TiNbZrTa alloys fabricated by laser powder bed fusion. Biomater Adv. 2022;133:112625.
- George EP, Raabe D, Ritchie RO. High-entropy alloys. Nat Rev Mater. 2019;4:515–534.
- George EP, Curtin WA, Tasan CC. High entropy alloys: A focused review of mechanical properties and deformation mechanisms. Acta Mater. 2020;188:435–474. doi:10.1016/j.actamat.2019.12.015.
- Li W, Xie D, Li D, et al. Mechanical behavior of high-entropy alloys. Prog Mater Sci. 2021;118:100777.
- Hori T, Nagase T, Todai M, et al. Development of non-equiatomic Ti-Nb-Ta-Zr-Mo high-entropy alloys for metallic biomaterials. Scripta Mater. 2019;172:83–87. doi:10.1016/j.scriptamat.2019.07.011.
- Todai M, Nagase T, Hori T, et al. Novel TiNbTaZrMo high-entropy alloys for metallic biomaterials. Scripta Mater. 2017;129:65–68.
- Yuan Y, Wu Y, Yang Z, et al. Formation, structure and properties of biocompatible TiZrHfNbTa high-entropy alloys. Mater Res Lett. 2019;7:225–231. doi:10.1080/21663831.2019.1584592.
- Bu Y, Wu Y, Lei Z, et al. Local chemical fluctuation mediated ductility in body-centered-cubic high-entropy alloys. Mater Today. 2021;46:28–34. doi:10.1016/j.mattod.2021.02.022.
- Senkov ON, Scott JM, Senkova SV, et al. Microstructure and room temperature properties of a high-entropy TaNbHfZrTi alloy. J Alloy Compd. 2011;509:6043–6048. doi:10.1016/j.jallcom.2011.02.171.
- Seol JB, Ko W-S, Sohn SS, et al. Mechanically derived short-range order and its impact on the multi-principal-element alloys. Nat Commun. 2022;13(1):6766. doi:10.1038/s41467-022-34470-8.
- Huang X, Liu L, Duan X, et al. Atomistic simulation of chemical short-range order in HfNbTaZr high entropy alloy based on a newly-developed interatomic potential. Mater Des. 2021;202:109560.
- Yin S, Zuo Y, Abu-Odeh A, et al. Atomistic simulations of dislocation mobility in refractory high-entropy alloys and the effect of chemical short-range order. Nat Commun. 2021;12:4873.
- Yin YZ, Lu Y, Zhang TP, et al. Nanoindentation avalanches and dislocation structures in HfNbTiZr high entropy alloy. Scripta Mater. 2023;227:115312. doi:10.1016/j.scriptamat.2023.115312..
- Zhang B, Ding J, Ma E. Chemical short-range order in body-centered-cubic TiZrHfNb high-entropy alloys. Appl Phys Lett. 2021;119(20):201908. doi:10.1063/5.0069417.
- Xun K, Zhang B, Wang Q, et al. Local chemical inhomogeneities in TiZrNb-based refractory high-entropy alloys. J Mater Sci Technol. 2023;135:221–230. doi:10.1016/j.jmst.2022.06.047.
- Marteleur M, Fan S, Gloriant T, et al. On the design of new β-metastable titanium alloys with improved work hardening rate thanks to simultaneous TRIP and TWIP effects. Scripta Mater. 2012;66:749–752. doi:10.1016/j.scriptamat.2012.01.049.
- Senkov ON, Pilchak AL, Semiatin SL. Effect of cold deformation and annealing on the microstructure and tensile properties of a HfNbTaTiZr refractory high entropy alloy. Metall Mater Trans A. 2018;49:2876–2892. doi:10.1007/s11661-018-4646-8.
- Stráský J, Harcuba P, Václavová K, et al. Increasing strength of a biomedical Ti-Nb-Ta-Zr alloy by alloying with Fe, Si and O. J Mech Behav Biomed Mater. 2017;71:329–336. doi:10.1016/j.jmbbm.2017.03.026.
- Elias LM, Schneider SG, Schneider S, et al. Microstructural and mechanical characterization of biomedical Ti–Nb–Zr (–Ta) alloys. Mater Sci Eng A. 2006;432(1-2):108–112. doi:10.1016/j.msea.2006.06.013.
- Guo W, Quadir MZ, Moricca S, et al. Microstructural evolution and final properties of a cold-swaged multifunctional Ti–Nb–Ta–Zr–O alloy produced by a powder metallurgy route. Mater Sci Eng A. 2013;575:206–216. doi:10.1016/j.msea.2013.03.029.
- Talling RJ, Dashwood RJ, Jackson M, et al. Determination of (C11-C12) in Ti–36Nb–2Ta–3Zr–0.3 O (wt.%)(Gum metal). Scripta Mater. 2008;59(6):669–672. doi:10.1016/j.scriptamat.2008.05.022.
- Xu YF, Yi DQ, Liu HQ, et al. Effects of cold deformation on microstructure, texture evolution and mechanical properties of Ti–Nb–Ta–Zr–Fe alloy for biomedical applications. Mater Sci Eng A. 2012;547:64–71. doi:10.1016/j.msea.2012.03.081.
- Plaine AH, Silva M, Bolfarini C. Tailoring the microstructure and mechanical properties of metastable Ti–29Nb–13Ta-4.6Zr alloy for self-expansible stent applications. J Alloy Compd. 2019;800:35–40. doi:10.1016/j.jallcom.2019.06.049.
- Niinomi M. Mechanical properties of biomedical titanium alloys. Mater Sci Eng A. 1998;243(1–2):231–236. doi:10.1016/S0921-5093(97)00806-X.
- Zhang LC, Chen LY. A review on biomedical titanium alloys: recent progress and prospect. Adv Eng Mater. 2019;21(4):1801215. doi:10.1002/adem.201801215.
- Niinomi M, Nakai M. Titanium-based biomaterials for preventing stress shielding between implant devices and bone. Int J Biomater. 2011;2011:836587. doi:10.1155/2011/836587.
- Qazi J I, Rack H J, Marquardt B. High-strength metastable beta-titanium alloys for biomedical applications. JOM. 2004;56:49–51. doi:10.1007/s11837-004-0253-9.
- Kopova I, Stráský J, Harcuba P, et al. Newly developed Ti–Nb–Zr–Ta–Si–Fe biomedical beta titanium alloys with increased strength and enhanced biocompatibility. Mater Sci Eng C. 2016;60:230–238. doi:10.1016/j.msec.2015.11.043.
- Li Z, Zheng B, Wang Y, et al. Ultrafine-grained Ti–Nb–Ta–Zr alloy produced by ECAP at room temperature. J Mater Sci. 2014;49:6656–6666. doi:10.1007/s10853-014-8337-6.
- Li Q, Niinomi M, Hieda J, et al. Deformation-induced ω phase in modified Ti–29Nb–13Ta–4.6 Zr alloy by Cr addition. Acta Biomater. 2013;9(8):8027–8035. doi:10.1016/j.actbio.2013.04.032.
- Huang H, Wu Y, He J, et al. Phase-transformation ductilization of brittle high-entropy alloys via metastability engineering. Adv Mater. 2017;29(30):1701678. doi:10.1002/adma.201701678.
- Senkov O N, Semiatin S L. Microstructure and properties of a refractory high-entropy alloy after cold working. J Alloy Compd. 2015;649:1110–1123. doi:10.1016/j.jallcom.2015.07.209.
- Lei Z, Liu X, Wu Y, et al. Enhanced strength and ductility in a high-entropy alloy via ordered oxygen complexes. Nature. 2018;563(7732):546–550.
- Juan C C, Tsai M H, Tsai C W, et al. Simultaneously increasing the strength and ductility of a refractory high-entropy alloy via grain refining. Mater Lett. 2016;184:200–203. doi:10.1016/j.matlet.2016.08.060.
- Wu YD, Cai YH, Wang T, et al. A refractory Hf25Nb25Ti25Zr25 high-entropy alloy with excellent structural stability and tensile properties. Mater Lett. 2014;130:277–280. doi:10.1016/j.matlet.2014.05.134.
- Lilensten L, Couzinié J P, Bourgon J, et al. Design and tensile properties of a bcc Ti-rich high-entropy alloy with transformation-induced plasticity. Mater Res Lett. 2017;5(2):110–116. doi:10.1080/21663831.2016.1221861.
- Ikehata H, Nagasako N, Furuta T, et al. First-principles calculations for development of low elastic modulus Ti alloys. Phys Rev B. 2004;70:174113.
- Abdel-Hady M, Hinoshita K, Morinaga M. General approach to phase stability and elastic properties of β-type Ti-alloys using electronic parameters. Scripta Mater. 2006;55:477–480. doi:10.1016/j.scriptamat.2006.04.022.
- Sheikh S, Shafeie S, Hu Q, et al. Alloy design for intrinsically ductile refractory high-entropy alloys. J Appl Phys. 2016;120(16):164902. doi:10.1063/1.4966659.
- Li H, Zhou F, Li L, et al. Design and development of novel MRI compatible zirconium-ruthenium alloys with ultralow magnetic susceptibility. Sci Rep. 2016;6:1–10. doi:10.1038/s41598-016-0001-8.
- Taniguchi S, Tebble R, Williams D. The magnetic susceptibilities of some transition metal alloys and the corresponding density of states curves. Proc Royal Soc Lond Series: A Math Phys Sci. 1962;265:502–518.
- Diao HY, Feng R, Dahmen KA, et al. Fundamental deformation behavior in high-entropy alloys: An overview. Curr Opin Solid St M. 2017;21:252–266. doi:10.1016/j.cossms.2017.08.003.
- Wen X, Huang H, Wu H, et al. Enhanced plastic deformation capacity in hexagonal-close-packed medium entropy alloys via facilitating cross slip. J Mater Sci Technol. 2023;134:1–10. doi:10.1016/j.jmst.2022.05.059.
- Taylor GI. The instability of liquid surfaces when accelerated in a direction perpendicular to their planes. I. Proc Royal Soc Lond Series: A Math Phys Sci. 1950;201:192–196.
- Liu L, Ma J, Yu C, et al. Determination of forming ability of high pressure die casting for Zr-based metallic glass. J Mater Process Tech. 2017;244:87–96. doi:10.1016/j.jmatprotec.2017.01.015.
- Conley K, Gu W, Ritter J, et al. Observations on finger-like crack growth at a urethane acrylate/glass interface. J Adhesion. 1992;39:173–184. doi:10.1080/00218469208030461.
- Harth K, Eremin A, Stannarius R. A gallery of meniscus patterns of free-standing smectic films. Ferroelectrics. 2012;431:59–73. doi:10.1080/00150193.2012.684630.
- Choisez L, Ding L, Marteleur M, et al. High temperature rise dominated cracking mechanisms in ultra-ductile and tough titanium alloy. Nat Commun. 2020;11:2110. doi:10.1038/s41467-020-15772-1.
- Zhou X, He S, Marian J. Cross-kinks control screw dislocation strength in equiatomic bcc refractory alloys. Acta Mater. 2021;211:116875.
- Kamikawa N, Abe Y, Miyamoto G, et al. Tensile behavior of Ti, Mo-added low carbon steels with interphase precipitation. Isij Int. 2014;54:212–221. doi:10.2355/isijinternational.54.212.
- Liu L, Yang C, Wang F, et al. Ultrafine grained Ti-based composites with ultrahigh strength and ductility achieved by equiaxing microstructure. Mater Des. 2015;79:1–5. doi:10.1016/j.matdes.2015.04.032.
- Mak E, Yin B, Curtin WA. A ductility criterion for bcc high entropy alloys. J Mech Phys Solids. 2021;152:104389.
- Hu YJ, Sundar A, Ogata S, et al. Screening of generalized stacking fault energies, surface energies and intrinsic ductile potency of refractory multicomponent alloys. Acta Mater. 2021;210:116800.
- Chan KS. A computational approach to designing ductile Nb-Ti-Cr-Al solid-solution alloys. Metall Mater Trans A. 2001;32:2475–2487. doi:10.1007/s11661-001-0037-6.