Abstract
A novel variable temperature rolling (VTR) and annealing process was conducted on a metastable austenitic stainless steel. Strain softening occurred during tensile straining in both cold rolled and cryogenic rolled-annealed steels, leading to low uniform elongations of only 2-3%. In contrast, thanks to the metastable dual-phase heterogeneous lamellar structure achieved via the VTR process, a ultra-high strength of over 1 GPa was obtained, and strain hardening led to a remarkable increase of uniform elongation up to 10%. The high strength and ductility are attributed to the significant work-hardening derived from the superior heterogeneous deformation-induced hardening and sustained transformation-induced plasticity effect.
IMPACT STATEMENT
We identify a new variable temperature rolling and annealing process to achieve a metastable dual-phase heterogeneous lamellar structure, which overcomes strength-ductility trade-off by coupling of HDI hardening and TRIP effect.
1. Introduction
Austenitic stainless steels (ASSs) were widely used in kitchenware, transportation, petrochemical engineering, nuclear power engineering, aerospace, and other civil and defense applications [Citation1,Citation2]. However, the grain size of conventionally rolled and solution-treated ASSs was very coarse at 20–120 μm, leading to low yield strengths in the range of 150–300 MPa [Citation3,Citation4]. The low yield strength seriously limited their application in high-strength components under load-bearing, dynamic loading, and high pressure conditions. To meet the demand for lightweight structures and for improving safety, it became an urgent issue to develop advanced ASSs with a combination of high strength and ductility.
Grain refinement is the most effective way to improve yield strength without increasing the alloying cost. However, when the grains were homogeneously refined to the submicron or even nanometer scale, the strain hardening rate would be significantly reduced [Citation5,Citation6], resulting in low ductility. At the same time, nanocrystalline and equiaxed austenitic grains suppressed the transformation-induced plasticity (TRIP) effect [Citation7], leading to strain concentration, non-uniform deformation, and premature failure. Therefore, it is of great practical significance to enhance the strain hardening ability of nanostructured ASSs for good ductility.
Recently, heterostructures provided a new paradigm for solving the tradeoff between the strength and ductility of metals by invoking hetero-deformation induced (HDI) hardening [Citation8,Citation9]. Zhu and Wu et al. [Citation10,Citation11] proposed that the origin of HDI hardening in heterostructures is the interactive coupling near hetero-zone boundaries via the piling up of geometrically necessary dislocations (GNDs). Recent studies have found that the rolling and annealing process was effective and feasible in refining 304 ASS [Citation1,Citation12], in which cold rolling strain induced martensite, and the reverse transformation of austenite and recrystallization during annealing caused the grain refinement [Citation13], resulting in nanocrystalline (<100 nm)/ultra-fine grains (100–500 nm) structures. The yield strength of annealed steel was 1157 MPa and had an obvious yield drop and long Lüders band during deformation. Decreasing the rolling temperature stimulated the martensitic transformation, and cryogenic rolling at −196 °C produced a higher amount of martensite than cold rolling [Citation14], and lath martensite changed into martensite with dislocation cells at the subsequent rolling stage. Thus, the grain size of reversely transformed austenite was homogeneously nano-crystalline after annealing. The yield strength of the annealed steel was 1250 MPa and strain softening occurred during deformation. Cold rolling or cryogenic rolling followed by annealing could significantly refine grains and improve the yield strength but unfortunately at the expense of ductility. Moreover, the high rolling force and the severe edge cracking of steel plate made it hard for industrial applications. It was discovered that the deformation mechanisms changed from martensitic transformation to deformation twins during warm rolling at 200 °C, and recrystallization enabled modestly refined grains to form relatively coarse grains (>1 μm)/submicron grains (500–1000 nm) during annealing, but remarkable strength increment was not achieved and the yield strength of the annealed steel was only 540 MPa [Citation15]. It was also proposed that the TRIP kinetics during tensile deformation could be tailored by tuning the stability of retained austenite, and the resulted moderate but sustained strain hardening was conductive to realizing the combination of high strength and excellent ductility [Citation16]. At present, the combined rolling modes with variable rolling temperatures have not been considered, and the nucleation and transformation mechanisms are unclear. It is meaningful to develop a new fabricating method to tailor the metastable heterostructure and break the strength-ductility dilemma.
In the present study, a novel processing route of variable temperature rolling (VTR) and annealing was conducted on the 304 ASS, and the phase transformation behavior and subsequent microstructures were characterized to reveal the forming mechanism of the metastable dual-phase heterogeneous lamellar structure. The contribution of HDI hardening and TRIP effect on strain hardening and their interaction will be discussed. The finding in this work demonstrates that the nano-scale heterogeneous structure can overcome the strength-ductility dilemma.
2. Materials and methods
The experimental steel was a 5 mm thick commercially available 304 austenitic stainless steel plate produced by hot-rolling and solution treatment. The grain size in the initial solid solution state is coarse at ∼30–40 μm, and the yield strength is 295 MPa. The nominal chemical composition in wt.% is 0.04C, 0.41Si, 1.11Mn, 18.26Cr, 8.00Ni, 0.04N, and balance Fe. Schematics of rolling and annealing processes are shown in the Supplementary Materials Fig. S1. For cold rolling and cryogenic rolling procedures, the steel plates were rolled to a plate of 2.5 mm on a laboratory rolling mill at room temperature and cryogenic temperature (−196 °C), respectively. For the variable temperature rolling procedure, the steel plate was first warm rolled to a plate of 3.5 mm at 300 °C, and cryogenically rolled to a plate of 2.5 mm. Warm rolling was conducted at 300 °C to avoid martensitic transformation, and to produce a large number of deformation twins. The total rolling reduction ratio of steel plates was 50% in all conditions. Subsequently, the cold-rolled steel, cryogenic-rolled steel, and variable temperature-rolled steel were annealed at 650 °C for 3 min, which were termed CR-A steel, CCR-A steel, and VTR-A steel. Annealing was done at 650 °C to trigger the reverse transformation from a large amount of martensite to austenite, and to prevent grain coarsening.
Transmission electron microscope (TEM) studies were conducted using FEI Tecnai G2 F20 TEM at an accelerating voltage of 200 kV. The volume fraction of austenite was determined by a Rigaku SmartLab 9 kW X-ray diffractometer (XRD) using a Cu-Kα radiation source and obtained by a direct comparison method of the integrated intensities of the (200)γ, (220)γ, (311)γ, (200)α, and (211)α diffraction peaks in the 2θ-range tested [Citation17]. Tensile tests were conducted at room temperature at a crosshead speed of 3 mm/min using an INSTRON5969 universal testing machine. The gauge length of tensile specimens was 25 mm, and the width and thickness were 6.25 and 2.5 mm, respectively, according to ASTM standard. Load-unload-reload (LUR) tensile tests were conducted at room temperature at an engineering strain interval of 2%.
3. Results and discussion
XRD spectra and phase volume fraction statistics of rolled and annealed experimental steels are shown in Figure . Martensitic transformation occurred during rolling at room temperature, and 26% austenite remained in the CR steel. Due to the higher driving force of martensitic transformation at −196 °C [Citation18], full martensite was formed in the CCR and VTR steels (Figure (a,c)). Martensite underwent a reverse transformation to form austenite during annealing at 650 °C, increasing the austenite volume fraction. As a result, a dual-phase structure was obtained in CR-A, CCR-A, and VTR-A steels with martensite volume fractions of 11%, 20%, and 18%, respectively (Figure (b,d)).
Figure 1. XRD spectra and phase content statistics of experimental steels: (a)(c) CR, CCR, and VTR steels; and (b)(d) CR-A, CCR-A, and VTR-A steels.

The microstructures of rolled steels are shown in Figure . The red circle in the micrographs is the area where diffraction patterns were taken. The CR steel consisted of lath martensite and coarse retained austenite with a high density of dislocations (Figure (a,b)). During cryogenic rolling, the coarse grain austenite was first transformed into lath martensite, and with larger deformation, martensite with dislocation cells structure was formed due to the destruction of the lath martensitic structure (Figure (c,d)). The stacking fault energy of the material decreased and the driving force of martensitic transformation increased at −196 °C, which resulted in the direct transformation of γ to α′ martensite [Citation19]. There were a large number of deformation twins in the coarse-grained austenite matrix of VTR (3.5) steel (Figure (e,f)), which formed a lamellar lath martensite structure in the VTR (2.5) steel due to nucleation and growth of martensite along the deformation twins during cryogenic rolling (Figure (g,h)).
Figure 2. TEM micrographs of rolled steels with low and high magnifications: (a)(b) CR steel; (c)(d) CCR steel; (e)(f) VTR (3.5) steel by warm rolling to 3.5 mm; and (g)(h) VTR (2.5) steel by warm rolling to 3.5 mm and cryogenic rolling to 2.5 mm.
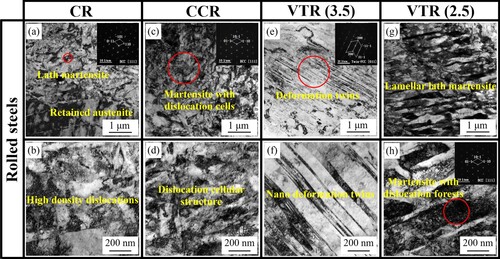
TEM micrographs presenting the microstructure of annealed steels are shown in Figure . It was a mixed structure of micron coarse grains (∼1–2 μm), submicron grains (∼500–1000 nm) and ultra-fine grains (∼100–500 nm) that formed in the CR-A steel. Retained austenite in the cold rolled steel increased during annealing, forming micron-sized coarse grains and submicron grains [Citation20]. Moreover, lath martensite underwent a reverse transformation to form lath ultra-fine austenitic grains (Figure (a,b)). Due to the formation of uniform martensite with dislocation cells structure in the CCR steel, martensite with dislocation cells during annealing underwent a reverse transformation to form uniform equiaxed ultra-fine grains (∼100–500 nm) structure in the CCR-A steel [Citation14] (Figure (c,d)). VTR-A steel formed a heterogeneous lamellar structure with an alternating distribution of lath martensite and lath austenite. The lamellar structure was nanoscale (∼50–200 nm) in width and microns (∼1–3 μm) in length. Lath martensite growing along deformation twins during cryogenic rolling of the VTR steel underwent a reverse transformation during annealing, forming lath austenite due to morphology inheritance. As a result, lath austenite and residual lath martensite together formed a heterogeneous lamellar structure (Figure (e,f)).
Figure 3. TEM micrographs of annealed steels with low and high magnifications: (a)(b) CR-A steel; (c)(d) CCR-A steel; and (e)(f) VTR-A steel.
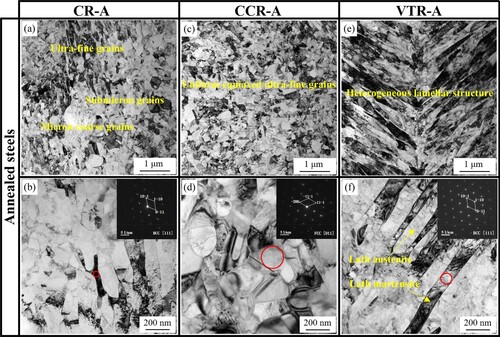
The tensile properties of the annealed steels are shown in Figure . The yield strength of the CR-A steel was 994 MPa due to the grain refinement of austenite and the introduction of a small amount of martensite. But strain softening immediately occurred, and the low strain hardening ability led to only 3% uniform elongation. Nano-crystallization of grains increased the yield strength of the CCR-A steel to 1164 MPa. However, strain softening was intensified under tensile straining, and uniform elongation was reduced to 2%. The yield strength of the VTR-A steel reached 1048 MPa. Moreover, the strain hardening rate was remarkably enhanced, and continuous strain hardening postponed the necking, resulting in much improved uniform elongation to 10%.
Figure 4. Tensile properties of annealed steels: (a) engineering stress-strain curves; (b) true stress-strain curves and work hardening rate curves; (c) yield strength; and (d) uniform elongation.

Variations of HDI stress and austenite volume fraction of annealed steels under tensile strain are shown in Figure . The HDI stress was calculated according to the method of Yang et al. [Citation21] (Figure (a,b)). The HDI stress gradually increased during deformation of the VTR-A steel (Figure (c)). Another hardening contribution, the TRIP effect, was probed by interrupted tensile tests. Variation of austenite volume fraction as a function of engineering strain is shown in Figure (d). Austenite to martensite transformation occurred under tensile deformation. The martensite volume fractions of the CR-A steel and VTR-A steel increased by 1% and 10% at an engineering strain of 3%, respectively, and the martensite volume fraction of the VTR-A steel continuously increased by 20% at an engineering strain of 12%. Therefore, the remarkable and sustained TRIP effect was found in the VTR-A steel (Figure (d)).
Figure 5. HDI stress and TRIP effect of annealed steels: (a) the load-unload-reload engineering stress-strain curves; (b) the load-unload-reload true stress-strain curves; (c) variation of HDI stress with true strain; and (d) variation of austenite phase content with engineering strain.
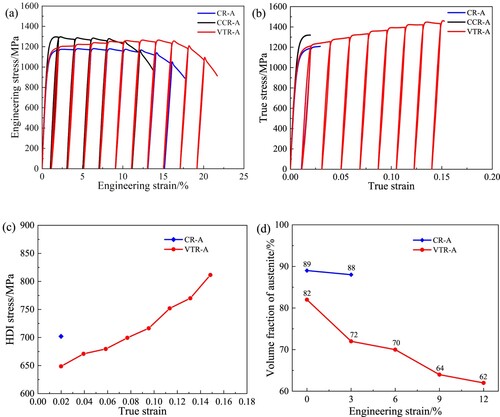
Transformation and deformation mechanisms of the VTR-A steel are shown in Supplementary Materials Fig. S2. As to the transformation mechanism of metastable dual-phase heterogeneous structure, a large number of deformation twins were produced during the warm rolling process, which made the martensite grow along the deformation twins during cryogenic rolling, resulting in the formation of lamellar lath martensite structure. Part of lath martensite underwent reverse transformation to form lath austenite during annealing, while other lath martensite retained, and the dual-phase heterogeneous lamellar structure with alternating distribution of lath martensite and lath austenite was obtained in the VTR-A steel (Fig. S2a-d). During straining, deformation induced GNDs accumulation and martensitic transformation occurred, leading to HDI hardening and sustained TRIP effect (Fig. S2e). The reason for metastable dual-phase heterogeneous lamellar structure to overcome the strength-ductility dilemma could be summarized into three aspects. Firstly, the hardness distribution of the dual-phase structure was not uniform. Plastic deformation of the soft phase was effectively constrained by the surrounding hard phase, which produced back stress in the soft phase and promoted HDI strain hardening [Citation21]. Nanoscale dual-phase heterogeneous lamellar structure had high density of phase boundaries, in which GNDs could be accumulated to enhance back stress [Citation22]. Secondly, lamellar morphology could produce higher strain hardening than equiaxed morphology, especially when its long axis was parallel to the loading direction [Citation23]. The geometry of this structure made mutual restriction between different phases more effective, which could generate higher back stress [Citation9]. Finally, back stress would stimulate martensite transformation in the soft phase austenite region together with the applied stress, and fresh martensite could enhance HDI hardening combined with surrounding austenite. As a result, the HDI hardening and TRIP effect promoted each other.
4. Conclusions
In summary, a novel procedure of variable temperature rolling and annealing was conducted on the 304 austenitic stainless steel for tailoring the transformation pathways and optimizing the mechanical properties. Nano-scaled deformation twins were produced under warm rolling, which further stimulated the martensite nucleation and constrained its growth along the deformation twins during cryogenic rolling. Some lath martensite underwent a reverse transformation to form lath austenite during the subsequent annealing, leading to a unique dual-phase heterogeneous lamellar structure containing alternately distributed lath martensite and lath austenite. The resultant ultra-high strength and superior uniform elongation were attributed to the significant strain hardening derived from the coupling of remarkable HDI hardening and sustained TRIP effect.
Declaration of interest statement
The authors declare that they have no known competing financial interests or personal relationships that could have appeared to influence the work reported in this paper.
Supplemental Material
Download MS Word (1,022.7 KB)Acknowledgments
This work was financially supported by the National Natural Science Foundation of China (grant number 52071066).
Disclosure statement
No potential conflict of interest was reported by the author(s).
Additional information
Funding
References
- Lo KH, Shek CH, Lai JKL. Recent developments in stainless steels. Mater Sci Eng R. 2009;65(4):39–104.
- Wang YM, Voisin T, McKeown JT, et al. Additively manufactured hierarchical stainless steels with high strength and ductility. Nat Mater. 2018;17(1):63–71.
- Wang JL, Huang MH, Xi XH, et al. Characteristics of nucleation and transformation sequence in deformation-induced martensitic transformation. Mater Charact. 2020;163:110234.
- Shen YF, Li XX, Sun X, et al. Twinning and martensite in a 304 austenitic stainless steel. Mater Sci Eng A. 2012;552:514–522.
- Song R, Ponge D, Raabe D, et al. Overview of processing, microstructure and mechanical properties of ultrafine grained bcc steels. Mater Sci Eng A. 2006;441(1):1–17.
- Yu CY, Kao PW, Chang CP. Transition of tensile deformation behaviors in ultrafine-grained aluminum. Acta Mater. 2005;53(15):4019–4028.
- Shen YF, Jia N, Wang YD, et al. Suppression of twinning and phase transformation in an ultrafine grained 2 GPa strong metastable austenitic steel: Experiment and simulation. Acta Mater. 2015;97:305–315.
- Pan QS, Zhang LX, Feng R, et al. Gradient cell-structured high-entropy alloy with exceptional strength and ductility. Science. 2021;374(6570):984–989.
- Wu XL, Yang MX, Yuan FP, et al. Heterogeneous lamella structure unites ultrafine-grain strength with coarse-grain ductility. Proc Natl Acad Sci. 2015;112(47):14501–14505.
- Wu XL, Yang MX, Yuan FP, et al. Combining gradient structure and TRIP effect to produce austenite stainless steel with high strength and ductility. Acta Mater. 2016;112:337–346.
- Zhu YT, Wu XL. Heterostructured materials. Prog Mater Sci. 2023;131:101019.
- Sun GS, Du LX, Hu J, et al. Ultrahigh strength nano/ultrafine-grained 304 stainless steel through three-stage cold rolling and annealing treatment. Mater Charact. 2015;110:228–235.
- Sun GS, Du LX, Hu J, et al. Microstructural evolution and recrystallization behavior of cold rolled austenitic stainless steel with dual phase microstructure during isothermal annealing. Mater Sci Eng A. 2018;709:254–264.
- Shi JT, Hou LG, Zuo JR, et al. Effect of cryogenic rolling and annealing on the microstructure evolution and mechanical properties of 304 stainless steel. Int J Miner Metall Mater. 2017;24(6):638–645.
- Sun GS, Du LX, Hu J, et al. On the influence of deformation mechanism during cold and warm rolling on annealing behavior of a 304 stainless steel. Mater Sci Eng A. 2019;746:341–355.
- Dong XX, Shen YF, Zhu YT. Moderating strain hardening rate to produce high ductility and high strength in a medium carbon TRIP steel. Mater Res Lett. 2023;11(1):69–75.
- Ding R, Dai ZB, Huang MX, et al. Effect of pre-existed austenite on austenite reversion and mechanical behavior of an Fe-0.2C-8Mn-2Al medium Mn steel. Acta Mater. 2018;147:59–69.
- Kwon H, Sathiyamoorthi P, Karthik GM, et al. 2.3 GPa cryogenic strength through thermal-induced and deformation-induced body-centered cubic martensite in a novel ferrous medium entropy alloy. Scripta Mater. 2021;204:114157.
- Tang L, Magdysyuk OV, Jiang FQ, et al. Mechanical performance and deformation mechanisms at cryogenic temperatures of 316L stainless steel processed by laser powder bed fusion: In situ neutron diffraction. Scripta Mater. 2022;218:114806.
- Naghizadeh M, Mirzadeh H. Microstructural evolutions during annealing of plastically deformed AISI 304 austenitic stainless steel: martensite reversion, grain refinement, recrystallization, and grain growth. Metall Mater Trans A. 2016;47(8):4210–4216.
- Yang MX, Pan Y, Yuan FP, et al. Back stress strengthening and strain hardening in gradient structure. Mater Res Lett. 2016;4(3):145–151.
- Xie L, Huang TL, Zhang L, et al. Managing both strength and ductility in duplex stainless steel with heterogeneous lamella structure. Mater Sci Eng A. 2018;738:190–193.
- Tanaka K, Mori T. The hardening of crystals by non-deforming particles and fibres. Acta Metall. 1970;18(8):931–941.