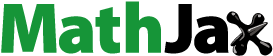
Abstract
Constructing heterostructures in particulate reinforced titanium matrix composites (PRTMCs) to evade the strength-ductility trade-off dilemma is much more difficult than in metals. Here, we proposed a novel and controllable strategy of simple powder assembly to fabricate bimodal-grained PRTMCs, this customized strategy makes coarse grains (CGs) surrounded by ultrafine-grained (UFG) matrices, conferring a superior strength-ductility combination not achievable by their traditional homogeneous counterparts. We found that such heterostructures appear to promote storage of mostly<c+a> dislocations in CGs and accumulation near the CG/UFG boundaries. Moreover, hybrid reinforcements also activate multiple hardening mechanisms, inducing high ductility.
GRAPHICAL ABSTRACT
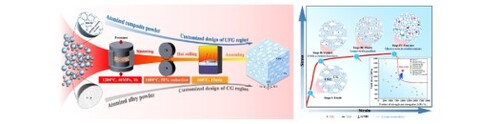
IMPACT STATEMENT
We proposed a novel and controllable strategy of simple powder assembly to fabricate heterostructured metal matrix composites for breaking the strength-ductility trade-off dilemma and revealed the enhanced <c+a> dislocation activity.
Introduction
Making metals stronger and tougher has been the primary endeavor of scientists and engineers, but classical strengthening mechanisms, including solid solution strengthening, dislocation hardening, precipitation hardening, and dispersion strengthening, etc., are achieved by impeding the motion of dislocations, which defeats the purpose of promoting ductility by multiplication, accumulation, and storage of dislocations, resulting in a dilemma known as the strength-ductility trade-off [Citation1,Citation2]. In recent years, heterostructured metals with both soft and hard domains have been widely investigated by advanced manufacturing techniques to obtain superior strength-ductility synergy and enhanced work hardening, which are related to the generation, accumulation, and interaction of geometrically necessary dislocations (GNDs) near hetero-zone boundaries [Citation2–8]. On the one hand, pile-up of GNDs produces the back stress in the soft domains, which induces the forward stress in the hard domains. The coupling of back and forward stresses increases the global yield strength and contributes to the extra hardening, which is referred to as ‘hetero-deformation induced (HDI) strengthening and hardening’ [Citation7,Citation9]. On the other hand, the nucleation of GNDs accelerates the statistical storage of dislocations during deformation, which is beneficial for additional hardening [Citation2,Citation8]. As an example, a three-dimensional (3D) core–shell nanostructures with highly tunable shell thickness and grain size distributions in pure copper was fabricated by mechanical milling and subsequent sintering, which obtained superior strength–ductility synergy. The experimental and simulation results reveal that the GNDs near the core–shell interface play a pivotal role in accommodating the strain gradient and sustaining a high strain-hardening rate during plastic deformation [Citation10]. However, it is much more difficult to construct heterogeneous zones in particulate reinforced metal matrix composites (PRMMCs) than in metals, which is attributed to the presence of hybrid reinforcements that limit the grain growth, making it difficult to controllably design the heterogeneous zones with significant differences in grain size. Moreover, the soft/hard zone interface prone to fail due to the lower plasticity of hard zone, easily causing voids or cracks at the zone boundaries [Citation9]. Therefore, it is meaningful to develop a new fabricating method to achieve controllable introduction of heterostructures into PRMMCs and to overcome the strength-ductility dilemma, ultimately facilitating their development and application.
To solve the above dilemmas, we proposed a novel strategy and controllable way of simple powder assembly to design the heterogenous structure in metal matrix composites (MMCs). Starting from the fabrication of composite powder, which plants nano-/microparticles with ultra-fine network and without the pollution of reinforcements caused by ball milling, and controls the primary grain size below 10 μm on the basis of rapid solidification theory [Citation11], then assembling the optional powder with controllable powder ratio or particle size at the powder source followed by hot rolling, to further aggravate the deformation incoherence between the coarse grains (CG) and ultrafine-grained (UFG) zones. The heterogenous structure would promote a strong <c+a> dislocation hardening and thus improve the mechanical properties of titanium matrix composites (TMCs). This study provides a novel and controllable strategy to construct heterogeneous structures in PRMMCs for breaking the strength-ductility trade-off dilemma.
Materials and methods
Figure schematically illustrated the customized strategy to develop the heterostructured titanium matrix composites (TMCs). The new atomized 5 vol. % (TiB +TiC)/Ti6Al4 V composite powders (TiB: TiC = 1:1, diameter in 53∼165 µm) embedded with ultra-fine network structure (network size ≤10 μm) (Supplementary Materials Fig. S1), and Ti6Al4 V powders (15∼65 µm) with coarse grain size (52.51 μm) were the supporting materials. Firstly, assembly mixed these two types of powders in the planetary ball milling with the powder ratio of 7:3, using the rotating speed of 200 rpm for 4 h, and setting the reinforcement content as 3.5 Vol. %. Then, hot pressed the assemble powders at 1200℃/40 MPa (HP, ZT-30-15Y, China) for 1 h at a heating rate of 10 ℃/min, followed by hot rolling at 1000℃ (α+β region) to reach a final height reduction of 50%. All rolled sheets were held for 5 min at the temperature of 1000 ℃ before rolling, then annealed the final hot rolled sheets at 600 ℃ for 15 min. For comparison, the matrix Ti6Al4 V alloy was also prepared with the same process parameters. The dog-bone-shaped tensile specimens with a gauge section of 15 × 3 × 1.8 mm oriented along the rolling direction (RD). Both normal and load-unload-reload (LUR) tests were carried out at room temperature at a strain rate of 10−3 s−1 using a universal tensile testing machine (Zwick, Roell Z020, Germany), and each test was repeated for at least 3 samples to ensure data reproducibility. The scanning electron microscope (SEM, RISE-MAGNA, Czech Republic) equipped with an energy dispersive spectrometer (EDS) was used to characterize the microstructure. The rolled TMCs were also characterized by electron back-scattered diffraction (EBSD) in a SEM (Mira 3, Czech Republic) equipped with an automatic orientation acquisition system, and the EBSD data was post-processed using AztecCrystal software. A transmission electron microscope (TEM, JEM-2100, Japan) operated at 200 kV was employed to reveal the microstructural features.
Results and discussion
Figure (a) shows the typical engineering tensile stress–strain curves of the rolled Ti6Al4 V and TMC. Interestingly, the heterostructured TMC exhibited a significant increase in yield strength (YS) and ultimate tensile strength (UTS) by ∼218 MPa and ∼127 MPa, respectively, and simultaneously improved the elongation by 17%, which achieved a promising strength-ductility synergy. Figure (b) shows the true stress–strain curves and corresponding strain hardening rate of the heterostructured TMC and the rolled Ti6Al4 V. The strain hardening rate of the TMC decreased more slowly than Ti6Al4 V after the larger strain of 2%, which indicated a large amount of dislocation storage. As a result, the heterostructured TMC exhibited a higher strain to failure. To better understand the high yield strength and strain hardening, we conducted the load-unload-reload (LUR) tests, as shown in Figure (c). The TMC exhibited a hysteresis loop, which reveals the existence of Bauschinger effect [Citation12]. It also shows the back stress of the rolled TMC was non-negligibly high, and steadily increased with the higher load, which quantitatively explains that the larger back stress is primarily responsible for the obtained high yield strength [Citation13]. The high back stress is considered as long-range internal stress associated with local strain, allowing long-range interaction with movable dislocations, which strengthens the soft zone, and finally increases the global yield strength [Citation13–15]. Note that the HDI stress of the Ti6Al4 V alloy increased sharply at the initial stage of deformation, because the interface may absorb some GND pileups and consequently do not contribute to HDI hardening with increasing strain gradient [Citation4,Citation16]. Figure (d) shows a comparison of tensile properties of the rolled heterostructured TMC with previously reported TMCs [Citation17–26], the strength-elongation product, which is scaled by the area under the tensile stress–strain curve [Citation27], distinguishes our TMC from all previous rolled TMCs in terms of ‘toughness’, which is the energy consumed in the tensile test to undergo plastic deformation and ultimately break the material. In other words, the current rolled TMC are separated from the general trend for conventional metallic materials, suggesting a favorable combination of strength and ductility.
Figure 2. (a) Tensile engineering stress-strain curves of the Ti6Al4V and the heterostructured TMC, (b) True stress-strain curves and strain hardening rate versus true strain curves, (c) LUR stress-strain curves and the corresponding back stress-strain curves, (d) A comparison of the YS and the product of UTS and elongation of the rolled heterostructured TMC with other as-rolled TMCs.
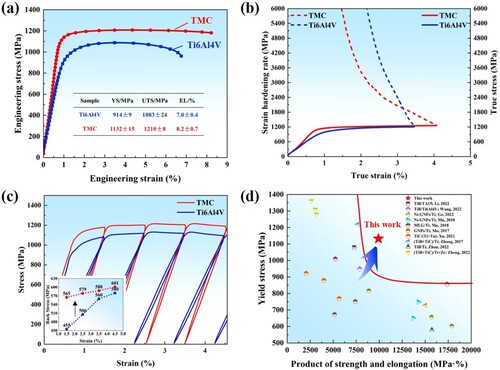
Figure (a) shows the IPF map of the heterostructured TMC. It is suggested that the heterostructured TMC mostly consists of elongated coarse grains (CGs) which are surrounded by a chain of equiaxed ultrafine-grained (UFGs) (Figure (b) and Supplementary Materials Fig. S2) with an average size of 4.58 and 0.84 μm, respectively (Figure (g)). Furthermore, the elongated CGs developed from Ti6Al4 V powders present slender morphology, while those developed from atomized Ti6Al4 V composite powders show a shorter shape, because the grain growth is hindered by the reinforcement during the hot rolling and heat treatment, as shown in Figure (d) and Supplementary Materials Fig. S3. The kernel average misorientation (KAM) map (Figure (f)) shows that most of the UFGs store low dislocations, while the CGs store higher dislocations, and the closer distance to the CG/UFG boundaries, the higher the dislocation density is, which presents a significant strain gradient. In other words, the larger grain size is, the higher GND density or the greater plastic deformation possess. The way in which bimodal grains are formed is responsible for this dislocation distribution characteristic. The UFGs are formed due to the dynamic recrystallization (DRX) of the α-Ti grains by new grain’s nucleation and growth during the hot rolling process, so the DRX consumes the storage energy of dislocations multiplication and pile-up [Citation28], while the CGs generate from the deformation and rotation of α-grains during the rolling process, which will be further analyzed later. Besides, the heterostructured TMC exhibits almost no significant texture with a relatively low maximum intensity of 3.31 (Figure (c)), indicating the weak influence of texture on the comprehensive mechanical property, and the deformation mechanism of the heterostructured TMC in this study is different from the previous reported bimodal microstructure in metals [Citation28,Citation29]. Additionally, it is interesting to note that the polar figures of CGs and UFGs show different characteristics, where the UFGs present a weak texture with a maximum intensity of 3.06, while the CGs show a strong texture with a maximum intensity of 6.33, which is attributed to the most of the UFGs originated from the DRX, there is no obvious orientation, while CGs are produced by deformation and rotation of α-grains during rolling, providing a greater texture. The grain boundary distribution map (Figure (e)) indicates that these elongated CGs have small misorientation angles (θ < 15°), as denoted by the gray lines, which further illustrates that the dynamic recovery (DRV) and DRX would also occur on these deformed grains during the rolling process [Citation30]. As a result, the deformation process and DRV/DRX are concomitant in the current TMC. Specifically, the severe deformation induced high dislocations, which would be rearranged by the high driving force in high temperature, then polygonized and further transformed into sub-grain boundaries, forming the UFGs [Citation30]. Figure (h) presents the grain boundary misorientation. The proportion of high-angle grain boundaries (HAGBs) with misorientation greater than 15° in the rolled TMC was approximately 72.2%. Such a large volume fraction of HAGBs could store more dislocations [Citation31], which may increase the likelihood of induced GNDs [Citation32], and thus obtaining better ductility. Figure (i) shows that the average Schmid factors (SFs) of slips corresponding to basal <a> (0002 <110>), prismatic <a> (10
0 <11
0>) and pyramidal <c+a> (
22 <11
3>) are 0.31, 0.33 and 0.35, respectively. The average SF of pyramidal <c+a> slips is highest, indicating that pyramidal <c+a> slips were easily activated and promote the migration of dislocations. Thus, the inhomogeneous deformation of such bimodal-grained structure as well as the hybrid reinforcements and the consequent dislocation behavior are considered to be the critical reasons for the improvement of work-hardening capacity and ductility rather than the texture.
Figure 3. Microstructures of the heterostructured TMC. (a) IPF map, (b) TEM micrographs for the bimodal grains, (c) Pole figures, (d) Grain map, (e) Grain boundary distribution map, (f) KAM map, (g) Grain size distributions, (h) Misorientation angle distribution (MAD), (i) SFs of slips corresponding to basal <a>, prismatic <a> and pyramidal<c+a>, respectively.
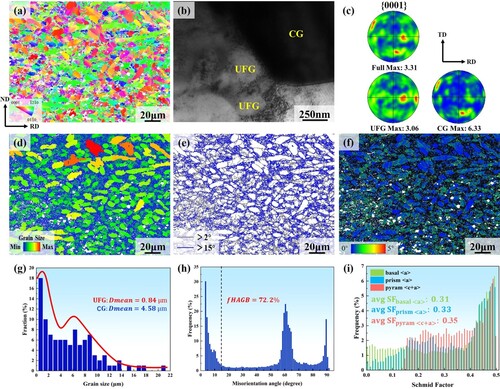
Figure (a–c) shows the SEM images of heterostructured TMC at different strains during the tensile test and the slip trace analyses (Figure (a-b) and Supplementary Materials Fig. S5). At 3% strain, only activated a small number of slip systems in the grains, including basal <a> slip, prismatic <a> slip, and pyramidal <c+a> slip. Further, increased the strain to 6%, as observed by slip trace analysis, several slip systems were activated during the deformation, and most of them are <c+a> slips. Until fracture, a large number of dimples appeared on the fracture surface, showing a ductile fracture morphology. In addition, cracks appear in the reinforcement, indicating a good load-transfer effect of the hybrid reinforcements. Dislocation behaviors were further characterized by two-beam conditions by TEM. Based on the invisibility criterion of defects, if the , the dislocations would be invisible [Citation33]. Therefore, the dislocation type could be determined by using different two-beam conditions. Comparing the special microstructure in the TEM images under different two-beam conditions, plenty of GNDs pile-ups and stored in the CGs, as shown in Figure (d), both <c+a> dislocations and <a> dislocations are visible. In the α-Ti, prismatic <a> dislocation slip is the easiest mode, due to its relatively low critical resolved shear stress (CRSS) for prismatic slip at room temperature [Citation34]. But the uniform distribution between UFGs and CGs produces HDI hardening effect. Moreover, the HDI causes extra<c+a> dislocations piling ups, which produce enough and extra strain hardening to enhance the ductility [Citation35]. TEM images (Figure (e-f)) present a large number of high-density <c+a> dislocations, especially the region nearby the TiB and TiC for the heterostructured TMC, which would activate multiple hardening mechanisms. First, the hybrid reinforcements promote plastic deformation incompatibility between reinforcement-rich and reinforcement-poor regions, inducing more HDI hardening and extra <c+a> dislocations, ultimately enabling the composites to achieve strength-ductility synergy. Second, the hybrid reinforcements can highly redistribute and suppress the stress concentrations and avoid the occurrence of potential strain localization, further inducing higher strain-hardening rate before failure [Citation36,Citation37]. Moreover, the reinforcements would inhibit DRV and increase the dislocation storage, thereby increasing strain hardening rate [Citation38]. Above results reveal that the heterogeneous grains and reinforcements in this study provided additional impetus for the activation of <c+a> dislocations, which was beneficial for the improvement of ductility and promotion of work hardening [Citation39,Citation40]. This allowed the deformation to persist at high stress levels even while maintaining high tensile strength.
Figure 4. SEM images of the heterostructured TMC at different deformation stages of (a) ϵ = 3%, (b) ϵ = 6%, (c) Fracture, (d∼f) TEM images in two-beam condition with g = 011 or g = 0002 of the rolled TMCs after tensile tests. (d) In CGs, (e) Region nearby the TiB, (f) Region nearby the TiC.
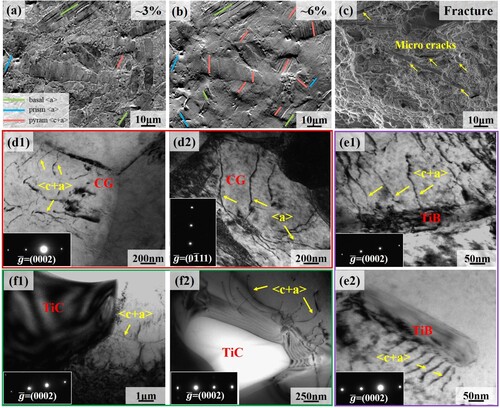
On the basis of the above results and analysis, we summarized the deformation mechanism for the heterostructured titanium matrix composites, as illustrated in Figure . After yielding, both CGs and UFGs will deform plastically. However, the CGs are compatible to deform, thus bearing more plastic strain than the UFGs, and further appears more strain gradient [Citation13]. Meanwhile, not only in the CGs, but also at the CG/UFG boundaries, the strain gradient will build up in this case [Citation3,Citation9,Citation41]. The strain gradient become larger as deformation continues, requiring more GNDs and leading to high back-stress hardening. The same strain gradient and back-stress hardening also formed at the reinforcement/matrix boundaries [Citation9]. It’s reported that the GNDs accumulated around the interface, not only contributing to the strengthening via promoting the kinematic hardening process, but also producing extra strain hardening, which accommodates the mechanical incompatibility across the interface [Citation35,Citation42]. Furthermore, the reinforcements induced the crack initiation, due to the higher load-transfer effect at high strain, thus absorbing more active energy for crack propagation during the tensile deformation [Citation31]. Consequently, they are the joint contributor to the observed high work hardening.
Some models are also proposed to investigate the back-stress hardening or HDI strengthening of heterogeneous metals, which would further provide theoretical support for the bimodal-grained structure in this study [Citation14,Citation43,Citation44]. For example, Li et al. [Citation14] calculated the back stress based on the configuration of GND pile-ups at the phase boundaries in the heterogeneous Cu, and found the extraordinary enhancement of ductility compared with CG Cu is due to the strong strain hardening capability obtained by back stress. However, unlike the other heterogeneous metals, the superior properties of the heterogeneous composites in this study are related to the customized tailoring of the matrix grain sizes, the reinforcements, and the extra <c+a> dislocations, which will require more subsequent simulations to illustrate in the future. Recently, a deformation mechanism-based plasticity model was also developed for heterostructure materials, and the result showed that the key principle of optimizing strength-ductility combination is to maximize the hetero-zone boundary affected region (Hbar) effects by building dispersed zone configuration rather than clustered or lamella, improving the degree of mechanical incompatibility and adopting the microstructure configuration with soft zones distributed in hard matrix rather than the opposite [Citation43,Citation44], which was consistent with our experimental results and discussion. For example, the width of Hbar is approximately estimated to be 1.83 μm (Supplementary Materials Note S1), which is conducive to achieving an optimum condition. Besides, the microstructure configuration is shown in Figure and Supplementary Materials Fig. S3, the enhanced mechanical incompatibility is due to the difference in CGs/UFGs and reinforcements/matrix, and the above factors ultimately achieved a higher product of YS and elongation. This indicates that the strength-ductility of heterogeneous composites is not only superior to that of conventional homogeneous metals, but more importantly, represents a breakthrough in the performance of heterogeneous metals, as shown in the inset of Figure .
Conclusions
To summarize, we fabricated a bimodal-grained PRTMC in which CGs were surrounded by UFGs via customized strategy of simple powder assembly, which provides the Ti6Al4 V composite with an outstanding synergy of yield strength of 1132 MPa, tensile strength of 1210 MPa and elongation of 8.2%. The results showed that bimodal grains would promote HDI strengthening and hardening, thus contributing to the storage of mostly <c+a> dislocations in CGs and accumulation near the zone boundaries. Furthermore, hybrid reinforcements also activate multiple hardening mechanisms, which are beneficial for the improvement of ductility and work hardening. Our promising strategy of assembling the optional powder with controllable powder ratio or particle size at the powder source can intentionally manipulate the grain size and volume fraction of CG/UFG regions over a wide range in heterostructured materials, and it should be extendable to other MMCs for solving the severe engineering challenges caused by the low ductility and strain hardening capacity.
Supplemental Material
Download MS Word (7 MB)Acknowledgements
The authors are thankful for the kind help of Lili at the teaching Laboratory center for School of Materials Science and Engineering for the guidance of the usage of Scanning Electron Microscope equipment (or other equipment).
Disclosure statement
No potential conflict of interest was reported by the author(s).
Additional information
Funding
References
- Wu H, Fan G. An overview of tailoring strain delocalization for strength-ductility synergy. Prog Mater Sci. 2020;113:100675. doi:10.1016/j.pmatsci.2020.100675
- Jiang J, Chen Z, Ma H, et al. Strength-ductility synergy in heterogeneous-structured metals and alloys. Matter. 2022;5(8):2430–2433. doi:10.1016/j.matt.2022.05.023
- Ma E, Zhu T. Towards strength–ductility synergy through the design of heterogeneous nanostructures in metals. Mater Today. 2017;20(6):323–331. doi:10.1016/j.mattod.2017.02.003
- Wang YF, Huang CX, Fang XT, et al. Hetero-deformation induced (HDI) hardening does not increase linearly with strain gradient. Scr Mater. 2020;174:19–23. doi:10.1016/j.scriptamat.2019.08.022
- Ma E, Wu X. Tailoring heterogeneities in high-entropy alloys to promote strength-ductility synergy. Nat Commun. 2019 Dec 9;10(1):5623. doi:10.1038/s41467-019-13311-1
- Zhu YT, Ameyama K, Anderson PM, et al. Heterostructured materials: superior properties from hetero-zone interaction. Mater Res Lett. 2021;9(1):1–31. doi:10.1080/21663831.2020.1796836
- Li X, Lu L, Li J, et al. Mechanical properties and deformation mechanisms of gradient nanostructured metals and alloys. Nature Rev Mater. 2020;5(9):706–723. doi:10.1038/s41578-020-0212-2
- Li J, Zhang Q, Huang R, et al. Towards understanding the structure–property relationships of heterogeneous-structured materials. Scr Mater. 2020;186:304–311. doi:10.1016/j.scriptamat.2020.05.013
- Zhu YT, Wu XL. Heterostructured materials. Prog Mater Sci. 2023;131:101019. doi:10.1016/j.pmatsci.2022.101019
- Li G, Jiang J, Ma H, et al. Superior strength–ductility synergy in three-dimensional heterogeneous-nanostructured metals. Acta Mater. 2023;256:119143. doi:10.1016/j.actamat.2023.119143
- Li SP, Wang XY, Le JW, et al. Towards high strengthening efficiency by in-situ planting nano-TiB networks into titanium matrix composites. Compos Part B: Eng. 2022;245:110169. doi:10.1016/j.compositesb.2022.110169
- Yang MX, Pan Y, Yuan FP, et al. Back stress strengthening and strain hardening in gradient structure. Mater Res Lett. 2016;4(3):145–151. doi:10.1080/21663831.2016.1153004
- Shi P, Ren W, Zheng T, et al. Enhanced strength-ductility synergy in ultrafine-grained eutectic high-entropy alloys by inheriting microstructural lamellae. Nat Commun. 2019 Jan 30;10(1):489. doi:10.1038/s41467-019-08460-2
- Li J, Lu W, Chen S, et al. Revealing extra strengthening and strain hardening in heterogeneous two-phase nanostructures. Int J Plast. 2020;126:102626. doi:10.1016/j.ijplas.2019.11.005
- Sumin S, Chaoyi Z, Cheng Z, et al. Extraordinary strength-ductility synergy in a heterogeneous-structured β -Ti alloy through microstructural optimization. Mater Res Lett. 2019;7(11):467–473. doi:10.1080/21663831.2019.1652856
- He F, Yang Z, Liu S, et al. Strain partitioning enables excellent tensile ductility in precipitated heterogeneous high-entropy alloys with gigapascal yield strength. Int J Plast. 2021;144:103022. doi:10.1016/j.ijplas.2021.103022
- Li Z, Kang Q, Wang G, et al. Microstructure evolution during hot-packed rolling and mechanical properties anisotropy of as-rolled network-structured TiBw/TA15 composites. Mater Sci Eng A. 2022;849:143518. doi:10.1016/j.msea.2022.143518
- Wang S, Huang L, Liu B, et al. Microstructure and mechanical properties of Ti6Al4V based laminated composites at various rolling reductions. Compos Commun. 2022;33:101212. doi:10.1016/j.coco.2022.101212
- Ge YX, Zhang HM, Cheng XW, et al. Towards high performance in Ti-based composite through manipulating nickel coatings on graphene reinforcement. J Alloys Compd. 2022;893:162240. doi:10.1016/j.jallcom.2021.162240
- Mu XN, Cai HN, Zhang HM, et al. Uniform dispersion and interface analysis of nickel coated graphene nanoflakes/ pure titanium matrix composites. Carbon. 2018;137:146–155. doi:10.1016/j.carbon.2018.05.013
- Mu XN, Cai HN, Zhang HM, et al. Interface evolution and superior tensile properties of multi-layer graphene reinforced pure Ti matrix composite. Mater Des. 2018;140:431–441. doi:10.1016/j.matdes.2017.12.016
- Mu XN, Zhang HM, Cai HN, et al. Microstructure evolution and superior tensile properties of low content graphene nanoplatelets reinforced pure Ti matrix composites. Mater Sci Eng A. 2017;687:164–174. doi:10.1016/j.msea.2017.01.072
- Xu S, Lu T, Qiu J, et al. Microstructure and mechanical properties of Ti-Ta based composites enhanced by in-situ formation of TiC particles. Mater Charact. 2021;178:111241. doi:10.1016/j.matchar.2021.111241
- Zhang C, Li X, Zhang S, et al. Effects of direct rolling deformation on the microstructure and tensile properties of the 2.5 vol% (TiB w +TiC p )/Ti composites. Mater Sci Eng A. 2017;684:645–651. doi:10.1016/j.msea.2016.12.113
- Zhou Y, Yang F, Chen C, et al. Mechanical property and microstructure of in-situ TiB/Ti composites via vacuum sintering and hot rolling. J Alloys Compd. 2022;911:165042. doi:10.1016/j.jallcom.2022.165042
- Zheng Z, Kong F, Wang X, et al. Microstructure evolution, mechanical properties and strengthening mechanism of titanium matrix composite sheets. Mater Sci Eng A. 2022;860:144256. doi:10.1016/j.msea.2022.144256
- Li H, Zong H, Li S, et al. Uniting tensile ductility with ultrahigh strength via composition undulation. Nature. 2022 Apr;604(7905):273–279. doi:10.1038/s41586-022-04459-w
- Fu W, Dang PF, Guo SW, et al. Heterogeneous fiberous structured Mg-Zn-Zr alloy with superior strength-ductility synergy. J Mater Sci Technol. 2023 Jan 20;134:67–80. doi:10.1016/j.jmst.2022.06.021
- Zhang Z, Zhang JH, Wang WK, et al. Unveiling the deformation mechanism of highly deformable magnesium alloy with heterogeneous grains. Scr Mater. 2022;221:114963. doi:10.1016/j.scriptamat.2022.114963
- Dong Z, Ma Z, Yu L, et al. Achieving high strength and ductility in ODS-W alloy by employing oxide@W core-shell nanopowder as precursor. Nat Commun. 2021 Aug 20;12(1):5052. doi:10.1038/s41467-021-25283-2
- Wei Z, Han Y, Li S, et al. Interfacial modification strategy to break through the strength and ductility trade-off in multi-walled carbon nanotubes reinforced titanium matrix composites. Mater Sci Eng A. 2023;880:145284. doi:10.1016/j.msea.2023.145284
- Fang XT, He GZ, Zheng C, et al. Effect of heterostructure and hetero-deformation induced hardening on the strength and ductility of brass. Acta Mater. 2020;186:644–655. doi:10.1016/j.actamat.2020.01.037
- Wang T, Zha M, Du C, et al. High strength and high ductility achieved in a heterogeneous lamella-structured magnesium alloy. Mater Res Lett. 2023;11(3):187–195. doi:10.1080/21663831.2022.2133976
- Gong J, Wilkinson AJ. Anisotropy in the plastic flow properties of single-crystal α titanium determined from micro-cantilever beams. Acta Mater. 2009;57(19):5693–5705. doi:10.1016/j.actamat.2009.07.064
- Gu L, Meng A, Chen X, et al. Simultaneously enhancing strength and ductility of HCP titanium via multi-modal grain induced extra <c+a> dislocation hardening. Acta Mater. 2023;252:118949. doi:10.1016/j.actamat.2023.118949
- Chen J, Han Y, Li S, et al. Evading the strength and ductility trade-off dilemma in titanium matrix composites through designing bimodal grains and micro-nano reinforcements. Scr Mater. 2023;235:115625. doi:10.1016/j.scriptamat.2023.115625
- Sun H, Saba F, Fan GL, et al. Micro/nano-reinforcements in bimodal-grained matrix: a heterostructure strategy for toughening particulate reinforced metal matrix composites. Scr Mater. 2022;217:114774. doi:10.1016/j.scriptamat.2022.114774
- Zhao YH, Liao XZ, Cheng S, et al. Simultaneously increasing the ductility and strength of nanostructured alloys. Adv Mater. 2006;18(17):2280–2283. doi:10.1002/adma.200600310
- Liu BY, Liu F, Yang N, et al. Large plasticity in magnesium mediated by pyramidal dislocations. Science. 2019 Jul 5;365(6448):73–75. doi:10.1126/science.aaw2843
- Chong Y, Bhattacharjee T, Tian YZ, et al. Deformation mechanism of bimodal microstructure in Ti-6Al-4V alloy: The effects of intercritical annealing temperature and constituent hardness. J Mater Sci Technol. 2021;71:138–151. doi:10.1016/j.jmst.2020.08.057
- Qin S, Yang MX, Jiang P, et al. Designing structures with combined gradients of grain size and precipitation in high entropy alloys for simultaneous improvement of strength and ductility. Acta Mater. 2022;230:117847. doi:10.1016/j.actamat.2022.117847
- Hu J, Li XY, Zhang ZM, et al. Overcoming the strength-ductility trade-off in metastable dual-phase heterogeneous structures using variable temperature rolling and annealing. Mater Res Lett. 2023 Aug 3;11(8):648–654. doi:10.1080/21663831.2023.2209596
- Chou TH, Li WP, Chang HW, et al. Quantitative analysis of hetero-deformation induced strengthening in heterogeneous grain structure. Int J Plast. 2022;159:103482. doi:10.1016/j.ijplas.2022.103482
- Wang Y, Zhu Y, Yu Z, et al. Hetero-zone boundary affected region: a primary microstructural factor controlling extra work hardening in heterostructure. Acta Mater. 2022;241:118395. doi:10.1016/j.actamat.2022.118395