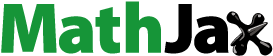
Abstract
In this study, we investigate the influence of dislocation strengthening in the metastable parent phase on the deformation-induced martensitic transformation behavior of a face-centered cubic (fcc) Co20Cr20Fe34Mn20Ni6 high-entropy alloy. Annealed and hot-swaged specimens were prepared. In-situ neutron diffraction experiments captured an accelerated transformation kinetics in the hot-swaged specimen due to accumulated dislocations. The phase-specific macrostress development showed that the hexagonal close-packed -martensite predominantly accommodated the macroscopic plastic deformation of the annealed counterpart. Conversely, the matrix dislocation strengthening promoted cooperative plasticity of the
-matrix and the
-martensitic phase, thus enhancing yield stress while preserving ductility.
IMPACT STATEMENT
This paper firstly uncovers the role and significance of matrix dislocation strengthening on the mechanical behavior of metastable high-entropy alloys via in-situ neutron diffraction experiments.
1. Introduction
High-entropy alloys (HEAs) are multicomponent alloys composed of five or more elements in approximately equimolar proportions [Citation1–3]. The enhanced configurational entropy associated with this unique alloying concept stabilizes solid solutions [Citation4], such as in face-centered cubic (fcc) [Citation2,Citation5,Citation6], body-centered cubic [Citation7,Citation8], and hexagonal close-packed (hcp) [Citation9,Citation10] structures. Moreover, HEAs exhibit exceptional properties, such as outstanding solid-solution strengthening [Citation3,Citation11–14], excellent damage tolerance [Citation5,Citation15], and good corrosion resistance [Citation16–19], thereby attracting considerable attention in the materials science community. Recent studies have introduced precipitation strengthening in HEAs, achieving exceptional high strength [Citation20–24].
Among HEAs, Cantor alloy, an equimolar fcc CoCrFeMnNi HEA [Citation2,Citation5], has been widely studied. This alloy consists of a single-phase fcc -microstructure and exhibits dislocation-mediated plasticity [Citation25]. Li et al. [Citation26–28] proposed an alternative design strategy of combining transformation-induced plasticity (TRIP) effect [Citation29–31] with HEAs by introducing non-equimolar compositions to reduce the staking fault energy (SFE). TRIP-assisted dual-phase (TRIP-DP) HEAs, such as Fe50Mn30Co10Cr10 [Citation26,Citation28] and Co20Cr20Fe34Mn20Ni6 [Citation27], undergo
(fcc)-to-
(hcp) deformation-induced martensitic transformation (DIMT) to demonstrate an exceptional combination of strength and ductility. This outcome is attributed to their inherent solid-solution strengthening characteristics and the TRIP effect, which delays the onset of plastic instability under tensile loading. Despite their outstanding ductility, the yield strength of these HEAs (approximately 200−300 MPa at room temperature [Citation26–28,Citation32–34]) is even lower than that of the Cantor alloy, which restricts their application as structural materials.
Thermomechanical processing (TMP) has emerged as a promising treatment to optimize the microstructure and resulting mechanical properties of HEAs [Citation35–39]. The grain size dependence of the mechanical behavior of metastable HEAs has been investigated. Li et al. [Citation26] highlighted that a finer grain size of ∼4.5 µm results in a superior strength–ductility combination of Fe50Mn30Co10Cr10 alloys. In another study, the grain refinement of a TRIP-DP Cr20Mn6Fe34Co34Ni6 HEA to 3−10 µm was reported to increase its yield stress to higher than that of Cantor alloy [Citation40]. Chen et al. [Citation41] indicated an accelerated →
DIMT in metastable Fe40Co20Cr20Mn10Ni10 HEAs upon increasing the grain size from 12 to 41 µm. TMP, which is performed at elevated temperatures at which the parent phase is mechanically stable, could strengthen metastable
-matrices via grain refinement and dislocation hardening [Citation42]. However, the effect of initial dislocation substructures in the
-matrix on the DIMT behavior remains poorly understood.
Therefore, the aim of this study is to examine the interplay between the initial dislocation substructure and DIMT and clarify the multiphase mechanical behavior of a model TRIP-assisted metastable Co20Cr20Fe34Mn20Ni6 HEA [Citation27], focusing on the stress partitioning between the parent -matrix and
-martensitic phases and transformation kinetics. To this end, in-situ neutron diffraction (ND) experiments were conducted under tensile loading, and the macrostress [Citation43] for each phase and phase fraction were analyzed via Rietveld texture analysis (RTA) [Citation44–46]. The results demonstrated that the dislocation strengthening of the metastable
-matrix phase enhances cooperative plasticity during DIMT, improving the yield stress while maintaining excellent strain hardening and ductility.
2. Materials and methods
A 30-kg ingot of Co20Cr20Fe34Mn20Ni6 alloy was produced using conventional high-frequency vacuum induction melting. The purities of the raw materials were ≥ 99.9% for Co and Fe, ≥ 99% for Cr and Mn, and ≥ 99.99% for Ni. Table summarizes the chemical composition of the prepared alloy. The ingot was homogenized at 1200 °C for 4 h, hot forged, and subjected to hot caliber rolling to produce bars with a diameter of approximately 15 mm. Additionally, several hot-swaged bars were annealed at 1100 °C for 30 min in vacuum, followed by Ar gas quenching.
Table 1. Chemical composition of the studied alloy (at.%).
The microstructure was analyzed using field-emission scanning electron microscopy (FE-SEM; JSM-7100F, JEOL, Japan) at 15 kV. Electron backscatter diffraction (EBSD) measurements were obtained using HKL Channel 5 software (Oxford Instruments, UK). Elemental maps were acquired using a field-emission electron probe microanalyzer (FE-EPMA; JXA-8430F, JEOL, Japan) operated at 15 kV. Standard metallographic procedure was followed to prepare the samples for the microstructural characterizations. The dislocation substructures of the specimens were examined through transmission electron microscopy (TEM; JEM-2000EXII, JEOL, Japan) at 200 kV. Samples were extracted from specimens subjected to nominal strains () of 20% and 40%. TEM thin foils were prepared by ion-beam milling (Model 1010, Fischione, USA).
Uniaxial tensile tests were conducted at room temperature. Samples with a gauge diameter of 2.5 mm and length of 12.5 mm were prepared following the ASTM E8M Standard. Each specimen was strained to failure at an initial strain rate of 1.3 × 10−4 s−1 using an Instron 5969 dual-column tensile testing system. The strain during tensile deformation was measured using a non-contacting video extensometer (AVE2, Instron, USA). Each specimen underwent a minimum of three sets of tensile tests to confirm reproducibility.
In-situ time-of-flight (TOF) ND experiments during tensile deformation were performed at iMATERIA (BL20) [Citation47] in the Japan Proton Accelerator Research Complex (J-PARC). Tensile specimens with a gauge diameter of 6 mm and length of 12 mm were installed in the sample chamber, enabling uniaxial deformation perpendicular to the incident beam [Citation48,Citation49]. ND data were continuously acquired while the samples were strained at an initial strain rate of 1.0 × 10−4 s−1. The phase fraction and macrostress for each phase at different strains were quantified by RTA [Citation44–46] based on the Materials Analysis Using Diffraction (MAUD) software [Citation50]. The peak shifts due to external stress for both the parent - and martensite
-phases were fitted using the moment pole stress model [Citation48], which calculates the bulk elastic modulus from the stiffness of a single crystal, considering the texture of the sample. Specifically, we used the weighted Hill model in MAUD to correlate the bulk and single crystalline elastic moduli. The elastic constants for the
- and
-phases of the Co20Cr20Fe34Mn20Ni6 alloy were extracted from the literature [Citation51].
3. Results
Figure shows the specimen microstructures prior to tensile loading. Both the annealed and hot-swaged specimens exhibited equiaxed grains with annealing twins, as observed in the SEM-backscattered electron (BSE) images (Figure (a, d)). No precipitates were detected except for minor oxide inclusions. The inverse pole figure (IPF) maps (Figure (b, e)) indicated that the texture did not change significantly during subsequent annealing, consistent with the RTA results based on the ND data (Figure S1(a, b)). The phase maps (Figure (c, f)) indicate that the -phase was stable in the investigated specimens, although small amounts of the
-martensite were detected. The
-grain sizes for the annealed and hot-swaged specimens were approximately 52.6 and 40.5 µm, respectively. Figure (g−i) show the TEM bright-field (BF) image, selected area electron diffraction (SAED) pattern, and dark-field (DF) images of the hot-swaged specimen. The TEM-DF images were obtained leveraging the 〈002〉
reflection. A dislocation substructure showing a fringe contrast of stacking faults (SFs) was observed. The TEM-DF image (Figure (i)) obtained using the 〈0001〉
reflection indicated the presence of a small amount of
-martensite, formed upon cooling of the hot-swaged specimens. Figure S2 demonstrates a homogeneous distribution of alloying elements across the microstructure.
Figure 1. (a, d) SEM-BSE images; (b, e) IPF maps; (c, f) phase maps of the (a−c) annealed and (d−f) hot-swaged specimens prior to tensile loading. (g) TEM-BF and TEM-DF images for the (h) -matrix and (i)
-martensite phases in the hot-swaged alloy. The zone axis for the SAED pattern (inset) is parallel to the [110]
direction.
![Figure 1. (a, d) SEM-BSE images; (b, e) IPF maps; (c, f) phase maps of the (a−c) annealed and (d−f) hot-swaged specimens prior to tensile loading. (g) TEM-BF and TEM-DF images for the (h) γ-matrix and (i) ε-martensite phases in the hot-swaged alloy. The zone axis for the SAED pattern (inset) is parallel to the [110]γ direction.](/cms/asset/935975c4-ca04-4e60-82d1-aab28a780237/tmrl_a_2281593_f0001_oc.jpg)
Figure (a) shows the nominal stress−nominal strain curves of the alloy specimens. Table summarizes the tensile properties of the specimens. The 0.2% proof stress and ultimate tensile strength (UTS) of the annealed alloy were 202 ± 13 and 708 ± 8 MPa, respectively. These values were higher than the ones reported previously (155 ± 10 MPa and 545 ± 11 MPa, respectively) [Citation27], which can be attributed to differences in the alloy manufacturing process. The hot-swaged specimen exhibited an improved yield stress (245 ± 14 MPa) and comparable UTS. Both specimens exhibited considerable ductility (i.e. > 50% in uniform elongation and >60% in total elongation) with that of the annealed specimen being slightly higher. Figure (b) shows the true stress (t)−true strain (
t) curves and corresponding strain-hardening rate (d
t/d
t) curves as a function of
t of the alloy specimens. Both specimens exhibited similar behaviors, characterized by significant strain hardening during tensile deformation. Failure occurred when Considère criterion (d
t/d
t ≤
t) was satisfied. However, the annealed specimen displayed a slightly higher strain-hardening rate in the initial stage of tensile deformation (
t ∼ 0.1), eventually reaching similar stress levels as the deformation progressed.
Figure 2. (a) Nominal stress−nominal strain curves and (b) corresponding true stress and strain-hardening rate as a function of the true strain of the annealed and hot-swaged specimens.
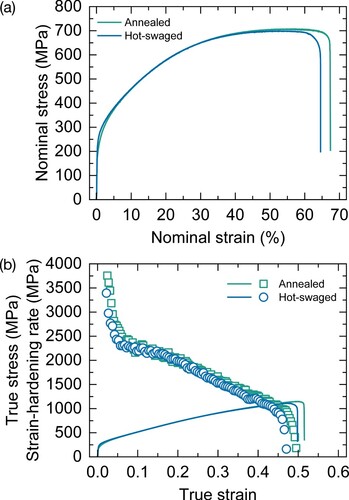
Table 2. Tensile properties of the studied alloy.
Figure shows the SEM-BSE and EBSD results for both alloys strained to 20% and 40%. The SEM-BSE images indicated the presence of numerous intragranular boundaries within the matrix of both specimens after tensile deformation. The magnified EBSD results captured the formation of a plate-like -phase, as confirmed by the TEM observations (Figure ). The SAED patterns exhibited two sets of diffraction spots corresponding to the hcp
-phase, which displays the Shoji−Nishiyama orientation relationship with the surrounding fcc
-matrix:
. This finding demonstrated the
→
DIMT in the alloy during tensile loading [Citation27]. Streaks in the SAED patterns indicated the formation of SFs in the
-matrix. Several
-martensite plates underwent distortion owing to further straining after the transformation [Citation52], as indicated by the phase maps (Figure ). Overall, the ex-situ EBSD and TEM analyses could not capture any significant difference in the DIMT behavior between the annealed and hot-swaged specimens.
Figure 3. (a, d, g, j) SEM-BSE images, (b, e, h, k) IPF maps, and (c, f, i, l) phase maps of the (a−f) annealed and (g−l) hot-swaged specimens subjected to tensile straining to (a−c, g−i) = 20% and (d−f, j−l) 40%.
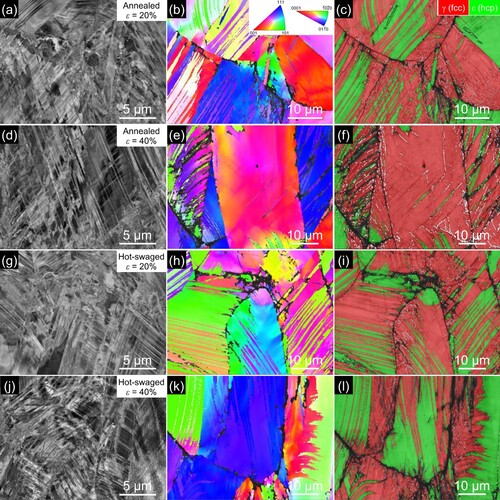
Figure 4. (a, d) TEM-BF and TEM-BF images for the (b, e) -matrices and (c, f)
-martensite plates in the (a–c) annealed and hot-swaged specimens subjected to tensile straining to
= 20%. The insets show the corresponding SAED patterns with the diffraction spots used for capturing the TEM-DF images.
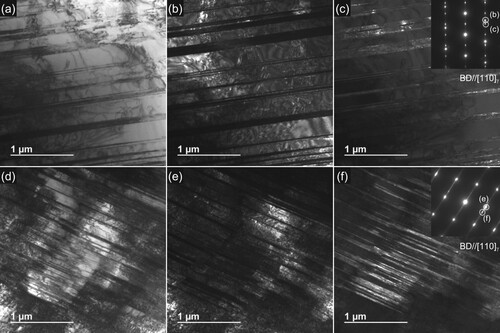
During the in-situ ND experiments under tensile loading, the peaks associated with -martensite became more pronounced as the applied strain increased (Figure S3). Additionally, an increase in the applied strain led to peak broadening, thereby decreasing the peak intensity of the
-matrix. Figure (a) shows the evolution of the martensite fraction as a function of the applied strain, as obtained through the RTA of the ND profiles. Although the hot-swaged specimen showed higher
-martensite fractions in the initial stage, both specimens exhibit similar behaviors involving the continuous progress of DIMT with the
-martensite fraction saturated at ∼60%. Figure (b) and (c) show the phase-specific macrostress (
22 along the tensile direction) as a function of applied strain for the annealed and hot-swaged specimens, respectively. The total macrostress
total (Equation Equation1
(1)
(1) ), based on the rule of mixtures [Citation53], was consistent with the experimentally determined
t, demonstrating the accuracy of the analysis.
(1)
(1) where
and
denote the macrostress for the
-matrix and
-martensite, respectively, and f
is the fraction of the
-phase. As shown in Figure (b),
of the annealed specimen was considerably lower than
. Specifically,
of the annealed specimen continuously increased to >2 GPa, whereas
increased and then decreased to zero as the applied strain increased. This observation suggested that the plastic deformation of the annealed specimen was governed by high-strength
-martensite and the stress partition between the parent
- and martensitic
-phases became negligible with increasing
. The hot-swaged specimen exhibited a different behavior. Here, the macrostress of both the
-matrix and
-martensite increased with strain, although
-martensite remained the harder phase. This indicates that the
-matrix also contributed to macroscopic plastic deformation in the hot-swaged specimen. Moreover, prior hot deformation of the
-matrix altered the plasticity in the duplex microstructure in a more cooperative manner, although the RTA revealed similar texture evolution during tensile loading (Figure S1).
4. Discussion
In this study, we investigated the tensile deformation behavior and corresponding microstructural evolution of a TRIP-aided metastable HEA in both annealed and hot-swaged conditions. Notably, hot swaging did not compromise the strain-hardening capability or the resultant ductility relative to the annealed alloy (Figure ). Given that hot swaging elevated the yield stress of the alloy, this approach could be employed to improve the strength–ductility balance in metastable HEAs.
In a duplex microstructure, stress and strain partitioning, which varies throughout the deformation process, plays a key role in strain hardening. The significant strain hardening in TRIP steels can be ascribed to the evolution of the stress and strain partitioning with the appearance of the hard martensite phase [Citation54]. We characterized the macrostress of each phase by in-situ ND measurements. Consequently, we established that the flow stress of the annealed specimen was dominated by the -martensitic phase during tensile loading (Figure (b)). Thus, the
-matrix in the annealed specimen did not act as a stress-bearing phase, and the external load partitioned to it was exclusively used for
-martensite production, resulting in further strain hardening.
Conversely, we observed that the external stress applied to the hot-swaged specimen was partitioned to the -martensite and metastable
-matrix (Figure (c)), demonstrating the cooperative deformation between the
-matrix and
-martensite. Thus, the dislocation substructure developed during hot swaging, i.e. dislocation strengthening, rendered the
-matrix a load-bearing phase alongside the
-martensite. This phenomenon altered the phase-specific plasticity, in which
→
DIMT played a key role.
The influence of the microstructure on the DIMT and TRIP effect has been extensively investigated. In steels, grain refinement increases the mechanical free energy required for the transformation of martensite to austenite [Citation55]. Conversely, the TRIP-DP-HEA, Fe50Mn30Co10Cr10, exhibited enhanced strain hardening responses, which are associated with accelerated DIMT kinetics in the presence of a finer grain size [Citation26]. In contrast, dislocation strengthening typically results in reduced ductility and heightened brittleness [Citation56]. Notably, the hcp -martensite phase is formed by the overlap of intrinsic SFs on alternate 111
planes [Citation57]. Consequently, the formation of SFs was observed through the TEM images (Figure ). Mori et al. [Citation58] reported that the
→
DIMT behavior in biomedical Co–Cr–Mo alloys is accelerated through the consumption of lattice defects, including dislocations and SFs [Citation59], introduced upon hot rolling. Similarly, the DIMT kinetics of the hot-swaged specimen was accelerated by the accumulated dislocations in the
-matrix, also contributing to the strain hardening. However, in spite of the lower
-martensite fraction, the enhanced strain hardening behavior at the initial stage of the annealed specimen indicates a higher dislocation accumulation in the
-matrix of the specimen than that of the hot-swaged specimen during tensile loading.
Recently, Liu et al. [Citation60] reported that hot rolling can elevate both the yield stress and ductility of AISI301 austenitic steel. This enhancement is attributed to an increase in the initial dislocation density and dislocation plasticity. Another study on additively manufactured austenitic steel pointed towards an improved strength–ductility synergy stemming from the formation of a dislocation network, which acts as a soft barrier against dislocation slip [Citation61]. The results of our study demonstrate the correlation between the →
DIMT and the initial dislocation structure, a relationship not previously established with certainty. The DIMT behavior and subsequent strain hardening are possibly shaped by multiple aspects of dislocation substructures, including their distribution and the extent of dislocation dissociation. This indicates that by fine-tuning the dislocation substructure via the alloy composition, the DIMT behavior can be effectively modulated.
5. Conclusions
In this study, we clarified the stress partitioning between the fcc -matrix and hcp
-martensite during DIMT in metastable Co20Cr20Fe34Mn20Ni6 HEAs. In-situ ND measurements and RTA demonstrated that hot swaging of the alloy promoted its deformation with the
-martensite, whereas
-martensite predominantly governs the flow stress during DIMT in the annealed specimen. Furthermore, dislocation accumulation in the metastable
-matrix enhanced the DIMT kinetics and increased the yield stress, while maintaining excellent strain hardening and tensile ductility of the alloy. These findings highlight a promising approach involving lattice defect engineering for enhancing strength–ductility synergy.
Supplemental Material
Download PDF (10.5 MB)Acknowledgments
The authors thank Masahiro Yamazaki, Eiwa Co., Ltd., for assisting in sample preparation, and Issei Narita, Shun Ito, and Fuyuki Sakamoto, Institute for Materials Research, Tohoku University, for providing technical assistance. EPMA analysis was performed under the GIMRT Program of the Institute for Materials Research, Tohoku University (Proposal No. 19G0414). The neutron experiment at J-PARC was performed as per proposal 2019PM2006.
Disclosure statement
No potential conflict of interest was reported by the author(s).
Additional information
Funding
References
- Yeh J-W, Chen S-K, Lin S-J, et al. Nanostructured high-entropy alloys with multiple principal elements: Novel alloy design concepts and outcomes. Adv Eng Mater. 2004;6:299–303. doi:10.1002/adem.200300567
- Cantor B, Chang ITH, Knight P, et al. Microstructural development in equiatomic multicomponent alloys. Mater Sci Eng A. 2004;375–377:213–218.
- Zhang Y, Zuo TT, Tang Z, et al. Microstructures and properties of high-entropy alloys. Prog Mater Sci. 2014;61:1–93. doi:10.1016/j.pmatsci.2013.10.001
- Zhang Y, Zhou YJ, Lin JP, et al. Solid-solution phase formation rules for multi-component alloys. Adv Eng Mater. 2008;10:534–538. doi:10.1002/adem.200700240
- Gludovatz B, Hohenwarter A, Catoor D, et al. A fracture-resistant high-entropy alloy for cryogenic applications. Science. 2014;345:1153–1158. doi:10.1126/science.1254581
- Yao MJ, Pradeep KG, Tasan CC, et al. A novel, single phase, non-equiatomic FeMnNiCoCr high-entropy alloy with exceptional phase stability and tensile ductility. Scr Mater. 2014;72–73:5–8.
- Senkov ON, Wilks GB, Miracle DB, et al. Refractory high-entropy alloys. Intermetallics. 2010;18:1758–1765. doi:10.1016/j.intermet.2010.05.014
- Senkov ON, Scott JM, Senkova SV, et al. Microstructure and room temperature properties of a high-entropy TaNbHfZrTi alloy. J Alloys Compd. 2011;509:6043–6048. doi:10.1016/j.jallcom.2011.02.171
- Feuerbacher M, Heidelmann M, Thomas C. Hexagonal high-entropy alloys. Mater Res Lett. 2015;3:1–6. doi:10.1080/21663831.2014.951493
- Zhao YJ, Qiao JW, Ma SG, et al. A hexagonal close-packed high-entropy alloy: The effect of entropy. Mater Des. 2016;96:10–15. doi:10.1016/j.matdes.2016.01.149
- Oh HS, Ma D, Leyson GP, et al. Lattice distortions in the FeCoNiCrMn high entropy alloy studied by theory and experiment. Entropy. 2016;18:321, doi:10.3390/e18090321
- Li J, Yamanaka K, Chiba A. Calculation-driven design of off-equiatomic high-entropy alloys with enhanced solid-solution strengthening. Mater Sci Eng A. 2021;817:141359, doi:10.1016/j.msea.2021.141359
- Yoshida S, Bhattacharjee T, Bai Y, et al. Friction stress and Hall-Petch relationship in CoCrNi equi-atomic medium entropy alloy processed by severe plastic deformation and subsequent annealing. Scr Mater. 2017;134:33–36. doi:10.1016/j.scriptamat.2017.02.042
- Lee C, Song G, Gao MC, et al. Lattice distortion in a strong and ductile refractory high-entropy alloy. Acta Mater. 2018;160:158–172. doi:10.1016/j.actamat.2018.08.053
- Zhang Z, Mao MM, Wang J, et al. Nanoscale origins of the damage tolerance of the high-entropy alloy CrMnFeCoNi. Nat Commun. 2015;6:10143, doi:10.1038/ncomms10143
- Shi Y, Yang B, Liaw PK. Corrosion-resistant high-entropy alloys: A review. Metals (Basel). 2017;7:43, doi:10.3390/met7020043
- Luo H, Li Z, Mingers AM, et al. Corrosion behavior of an equiatomic CoCrFeMnNi high-entropy alloy compared with 304 stainless steel in sulfuric acid solution. Corros Sci. 2018;134:131–139. doi:10.1016/j.corsci.2018.02.031
- Fujieda T, Shiratori H, Kuwabara K, et al. CoCrFeNiTi-based high-entropy alloy with superior tensile strength and corrosion resistance achieved by a combination of additive manufacturing using selective electron beam melting and solution treatment. Mater Lett. 2017;189:148–151. doi:10.1016/j.matlet.2016.11.026
- Pao L, Nishimoto M, Muto I, et al. Electrochemical surface modification of Al8Co19Cr23Fe32Ni18 in H2SO4: A high-entropy alloy with high pitting corrosion resistance and high oxidation resistance. Mater Trans. 2023;64:2286–2295. doi:10.2320/matertrans.MT-M2023088
- Guo JM, Zhou BC, Qiu S, et al. Achieving ultrahigh strength and ductility in high-entropy alloys via dual precipitation. J Mater Sci Technol. 2023;166:67–77. doi:10.1016/j.jmst.2023.05.021
- Cao B, Yang T, Liu W, et al. Precipitation-hardened high-entropy alloys for high-temperature applications: A critical review. MRS Bull. 2019;44:854–859. doi:10.1557/mrs.2019.255
- He JY, Wang H, Huang HL, et al. A precipitation-hardened high-entropy alloy with outstanding tensile properties. Acta Mater. 2016;102:187–196. doi:10.1016/j.actamat.2015.08.076
- Yang C, Bian H, Aoyagi K, et al. Synergetic strengthening in HfMoNbTaTi refractory high-entropy alloy via disordered nanoscale phase and semicoherent refractory particle. Mater Des. 2021;212:110248, doi:10.1016/j.matdes.2021.110248
- Yang C, Bian H, Zhang F, et al. Competition between solid solution and multi-component Laves phase in a dual-phase refractory high-entropy alloy CrHfNbTaTi. Mater Des. 2023;226:111646, doi:10.1016/j.matdes.2023.111646
- Lee S, Duarte MJ, Feuerbacher M, et al. Dislocation plasticity in FeCoCrMnNi high-entropy alloy: quantitative insights from in situ transmission electron microscopy deformation. Mater Res. Lett. 2020;8:216–224. doi:10.1080/21663831.2020.1741469
- Li Z, Pradeep KG, Deng Y, et al. Metastable high-entropy dual-phase alloys overcome the strength–ductility trade-off. Nature. 2016;534:227–230. doi:10.1038/nature17981
- Li Z, Körmann F, Grabowski B, et al. Ab initio assisted design of quinary dual-phase high-entropy alloys with transformation-induced plasticity. Acta Mater. 2017;136:262–270. doi:10.1016/j.actamat.2017.07.023
- Li Z, Tasan CC, Pradeep KG, et al. A TRIP-assisted dual-phase high-entropy alloy: Grain size and phase fraction effects on deformation behavior. Acta Mater. 2017;131:323–335. doi:10.1016/j.actamat.2017.03.069
- Herrera C, Ponge D, Raabe D. Design of a novel Mn-based 1 GPa duplex stainless TRIP steel with 60% ductility by a reduction of austenite stability. Acta Mater. 2011;59:4653–4664. doi:10.1016/j.actamat.2011.04.011
- Frommeyer G, Brüx U, Neumann P. Supra-ductile and high-strength manganese-TRIP/TWIP steels for high energy absorption purposes. ISIJ Int. 2003;43:438–446. doi:10.2355/isijinternational.43.438
- Grässel O, Krüger L, Frommeyer G, et al. High strength Fe–Mn–(Al, Si) TRIP/TWIP steels development — properties — application. Int J Plast. 2000;16:1391–1409. doi:10.1016/S0749-6419(00)00015-2
- Otto F, Dlouhy A, Ch S, et al. The influences of temperature and microstructure on the tensile properties of a CoCrFeMnNi high-entropy alloy. Acta Mater. 2013;61:5743–5755. doi:10.1016/j.actamat.2013.06.018
- Laplanche G, Kostka A, Horst OM, et al. Microstructure evolution and critical stress for twinning in the CrMnFeCoNi high-entropy alloy. Acta Mater. 2016;118:152–163. doi:10.1016/j.actamat.2016.07.038
- Joo SH, Kato H, Jang MJ, et al. Tensile deformation behavior and deformation twinning of an equimolar CoCrFeMnNi high-entropy alloy. Mater Sci Eng A. 2017;689:122–133. doi:10.1016/j.msea.2017.02.043
- Otto F, Hanold NL, George EP. Microstructural evolution after thermomechanical processing in an equiatomic, single-phase CoCrFeMnNi high-entropy alloy with special focus on twin boundaries. Intermetallics. 2014;54:39–48. doi:10.1016/j.intermet.2014.05.014
- Haghdadi N, Primig S, Annasamy M, et al. Dynamic recrystallization in AlXCoCrFeNi duplex high entropy alloys. J Alloys Compd. 2020;830:154720, doi:10.1016/j.jallcom.2020.154720
- Wani IS, Bhattacharjee T, Sheikh S, et al. Tailoring nanostructures and mechanical properties of AlCoCrFeNi2.1 eutectic high entropy alloy using thermo-mechanical processing. Mater Sci Eng A. 2016;675:99–109. doi:10.1016/j.msea.2016.08.048
- Stepanov ND, Shaysultanov DG, Chernichenko RS, et al. Effect of thermomechanical processing on microstructure and mechanical properties of the carbon-containing CoCrFeNiMn high entropy alloy. J Alloys Compd. 2017;693:394–405. doi:10.1016/j.jallcom.2016.09.208
- Santos LA, Singh S, Rollett AD. Microstructure and texture evolution during thermomechanical processing of Al0.25CoCrFeNi high-entropy alloy. Metall Mater Trans A. 2019;50:5433–5444. doi:10.1007/s11661-019-05399-3
- Chen S, Oh HS, Gludovatz B, et al. Real-time observations of TRIP-induced ultrahigh strain hardening in a dual-phase CrMnFeCoNi high-entropy alloy. Nat Commun. 2020;11:826, doi:10.1038/s41467-020-14641-1
- Chen W, An X, Wang Z, et al. Grain size dependent deformation behavior of a metastable Fe40Co20Cr20Mn10Ni10 high-entropy alloy. J Alloys Compd. 2021;883:160876, doi:10.1016/j.jallcom.2021.160876
- Mori M, Yamanaka K, Sato S, et al. Strengthening of biomedical Ni-free Co–Cr–Mo alloy by multipass “low-strain-per-pass” thermomechanical processing. Acta Biomater. 2015;28:215–224. doi:10.1016/j.actbio.2015.09.016
- Lutterotti L, Chateigner D, Ferrari S, et al. Texture, residual stress and structural analysis of thin films using a combined X-ray analysis. Thin Solid Films. 2004;450:34–41. doi:10.1016/j.tsf.2003.10.150
- Onuki Y, Sato S, Nakagawa M, et al. Strain-induced martensitic transformation and texture evolution in cold-rolled Co–Cr alloys. Quantum Beam Sci. 2018;2:11, doi:10.3390/qubs2020011
- Wenk H-R, Lutterotti L, Vogel SC. Rietveld texture analysis from TOF neutron diffraction data. Powder Diffr. 2010;25:283–296. doi:10.1154/1.3479004
- Onuki Y, Hoshikawa A, Nishino S, et al. Rietveld texture analysis for metals having hexagonal close-packed phase by using time-of-flight neutron diffraction at iMATERIA. Adv Eng Mater. 2018;20:1700227, doi:10.1002/adem.201700227
- Ishigaki T, Hoshikawa A, Yonemura M, et al. IBARAKI materials design diffractometer (iMATERIA)—Versatile neutron diffractometer at J-PARC. Nucl Instrum Methods Phys Res A. 2009;600:189–191. doi:10.1016/j.nima.2008.11.137
- Onuki Y, Sato S. In situ observation for deformation-induced martensite transformation (DIMT) during tensile deformation of 304 stainless steel using neutron diffraction. PART I: mechanical response. Quantum Beam Sci. 2020;4:31, doi:10.3390/qubs4030031
- Onuki Y, Sato S. In situ observation for deformation-induced martensite transformation during tensile deformation of SUS 304 stainless steel by using neutron diffraction PART II: transformation and texture formation mechanisms. Quantum Beam Sci. 2021;5:6, doi:10.3390/qubs5010006
- Lutterotti L, Matthies S, Wenk HR, et al. Combined texture and structure analysis of deformed limestone from time-of-flight neutron diffraction spectra. J Appl Phys. 1997;81:594–600. doi:10.1063/1.364220
- Li X, Irving DL, Vitos L. First-principles investigation of the micromechanical properties of fcc-hcp polymorphic high-entropy alloys. Sci Rep. 2018;8:11196, doi:10.1038/s41598-018-29588-z
- Mori M, Yamanaka K, Chiba A. Cold-rolling behavior of biomedical Ni-free Co–Cr–Mo alloys: Role of strain-induced ε martensite and its intersecting phenomena. J Mech Behav Biomed Mater. 2016;55:201–214. doi:10.1016/j.jmbbm.2015.10.021
- Kwon H, Harjo S, Kawasaki T, et al. Work hardening behavior of hot-rolled metastable Fe50Co25Ni10Al5Ti5Mo5 medium-entropy alloy: in situ neutron diffraction analysis. Sci Technol Adv Mater. 2022;23:579–586. doi:10.1080/14686996.2022.2122868
- Jacques PJ. Transformation-induced plasticity for high strength formable steels. Curr Opin Solid State Mater Sci. 2004;8:259–265. doi:10.1016/j.cossms.2004.09.006
- Lee S, Lee S-J, Cooman D, et al. Austenite stability of ultrafine-grained transformation-induced plasticity steel with Mn partitioning. Scr Mater. 2011;65:225–228. doi:10.1016/j.scriptamat.2011.04.010
- Lu K, Lu L, Suresh S. Strengthening materials by engineering coherent internal boundaries at the nanoscale. Science. 2009;324:349–352. doi:10.1126/science.1159610
- Talonen J, Hänninen H. Formation of shear bands and strain-induced martensite during plastic deformation of metastable austenitic stainless steels. Acta Mater. 2007;55:6108–6118. doi:10.1016/j.actamat.2007.07.015
- Mori M, Yamanaka K, Sato S, et al. Tuning strain-induced γ-to- ε martensitic transformation of biomedical Co–Cr–Mo alloys by introducing parent phase lattice defects. J Mech Behav Biomed Mater. 2019;90:523–529. doi:10.1016/j.jmbbm.2018.10.038
- Yamanaka K, Mori M, Sato S, et al. Stacking-fault strengthening of biomedical Co–Cr–Mo alloy via multipass thermomechanical processing. Sci Rep. 2017;7:10808, doi:10.1038/s41598-017-10305-1
- Liu J, Jin Y, Fang X, et al. Dislocation strengthening without ductility trade-off in metastable austenitic steels. Sci Rep. 2016;6:35345, doi:10.1038/srep35345
- Liu L, Ding Q, Zhong Y, et al. Dislocation network in additive manufactured steel breaks strength–ductility trade-off. Mater Today. 2018;21:354–361. doi:10.1016/j.mattod.2017.11.004