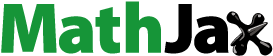
Abstract
Metals and alloys with heterogeneous microstructures exhibit an enhanced combination of strength and ductility, compared to their counterparts with homogeneous microstructures. Additive manufacturing (AM) techniques offers a new opportunity to induce heterogeneous microstructures in a wide range of metals and alloys, thereby optimizing their mechanical properties. In this review article, we focus on four types of heterogeneous microstructures induced by AM: lamellar, gradient, laminated, and harmonic ones. We will introduce (i) the tailored generation of heterogeneous microstructures, (ii) the effects of characteristic solidification conditions, and (iii) the intricate phase transformation in laser-based AM process. Furthermore, we discuss the features, advantages, and potential applications of the metals and alloys with heterogeneous microstructures made by AM. To conclude, we discuss current challenges and future opportunities in this field.
IMPACT STATEMENT
Additive manufacturing offers the opportunity of creating heterogeneous microstructures that enhance the strength-ductility synergy in metals and alloys. We review generation methods, solidification effects, heat treatment, and potential applications.
1. Introduction
Heterostructured materials, or materials with heterogeneous microstructures, are characterized by distinct zones with significantly different mechanical and physical properties [Citation1–3]. These materials are reported to achieve an excellent combination of strength and ductility, effectively overcoming the traditional strength-ductility trade-off (Figure (a)). This exceptional combination of strength and ductility results from the interactions between these heterogeneous zones [Citation1–3]. During the deformation of heterostructured materials, the formation of pileups of geometrically necessary dislocations (GNDs) occurs at the boundaries between soft and hard zones [Citation4–6]. GNDs have two primary strengthening effects: (i) their accumulation contributes to hetero-deformation induced (HDI) hardening, which involves the development of back stress strengthening in the soft domain and forward stress in the hard domain [Citation7,Citation8]; (ii) GNDs increase the total dislocation density, contributing to the strength of materials [Citation9]. HDI stress represents a long-range internal stress, which can be observed through the Bauschinger effect and experimentally measured during loading-unloading operations in tension tests [Citation10]. In general, metals and alloys also exhibit a certain degree of heterogeneity such as second-phase particles. To enhance the interaction between these heterogeneous zones, the heterogeneities should possess specific characteristics, including appropriate sizes, geometries, and distributions [Citation2]. Based on the literature, materials with certain microstructure characteristics such as lamellar structures, laminated structures, gradient structures, and harmonic (core–shell) structures (Figure (b–e)) are typically classified as heterostructured materials [Citation1].
Figure 1. (a) Materials with heterogeneous microstructures mitigating the strength-ductility trade-off. (b)–(e) Examples of typical lamellar, laminated, gradient, and harmonic [Citation1] heterogeneous microstructures (reprinted with permission from Refs. [Citation25]). Schematics of (f) DED and (g) LPBF (reprinted with permission from Ref. [Citation26]).
![Figure 1. (a) Materials with heterogeneous microstructures mitigating the strength-ductility trade-off. (b)–(e) Examples of typical lamellar, laminated, gradient, and harmonic [Citation1] heterogeneous microstructures (reprinted with permission from Refs. [Citation25]). Schematics of (f) DED and (g) LPBF (reprinted with permission from Ref. [Citation26]).](/cms/asset/28bb1195-5722-4b30-9afb-0dcd62705d5e/tmrl_a_2305261_f0001_oc.jpg)
Additive manufacturing (AM) technologies construct components from a 3D model, usually layer by layer, distinguishing themselves from subtractive and formative manufacturing methodologies [Citation11]. Most popular laser-based AM technologies include directed energy deposition (DED) (Figure (f)) and laser powder bed fusion (LPBF) (Figure (g)). The main difference between DED and LPBF lies in the way stock materials are fed: DED employs a coaxial powder or wire feeding approach [Citation12], while LPBF uses a powder bed deposition method [Citation13]. As a result, the DED process can be used to build new metal parts and also add materials to existing components, such as for coatings, repairs, and hybrid manufacturing applications [Citation12,Citation14]. Laser-based AM technology shows numerous unique process characteristics: (i) AM fabricates parts using a computer-aided design model and layer-by-layer technology, which offers the freedom to design complex geometries for structural applications [Citation15]; (ii) Highly localized melting pools, high-temperature gradients, and solidification-front velocities enable the tuning of the fine non-equilibrium microstructures compared with counterparts made by conventional methods such as casting and rolling [Citation16]; (iii) With the high-energy input of the laser beam, AM can be used to fabricate materials with high melting points, such as nickel-based superalloys and refractory alloys [Citation17,Citation18].
Over the recent years, there have been significant advancements in enhancing the mechanical properties of additively manufactured metals with heterogeneous microstructures. For example, Damascus steel with alternating soft and hard layers, created by pausing during the fabrication process, exhibited 1.3 GPa ultimate tensile strength without sacrificing ductility [Citation19]. These advancements have been made possible through various strategies employed in laser-based AM to create heterogeneous microstructures. Table summarizes the key strategies, resulting heterogeneous microstructures, and types of heterogeneity. Several factors contribute to these achievements: (i) Customized process characteristics: The layer-by-layer nature of AM allows for the modification of printing parameters and material compositions, spanning from individual melt pools to entire parts [Citation20]. Additionally, complementary methods can be integrated to further process the fabricated part after each hatch or layer [Citation21]. (ii) Manipulating solidification conditions: Different locations within each melt pool experience varying thermal conditions during solidification, leading to distinct microstructures, particularly along melt-pool boundaries and within melt pools [Citation22]. Meanwhile, the criteria for grain nucleation and growth during solidification can be adjusted to generate variations in grain sizes, morphologies, and orientations [Citation22,Citation23]. This can generate a combination of coarse and fine grains, columnar and equiaxed grains, or alternations in textures. (iii) Complex cyclic heat treatment: The cyclic reheating associated with successive laser passes introduces microstructural alterations and intricate phase transformations during the fabrication process, offering new opportunities for tailoring and tuning heterogeneous microstructures [Citation19].
Table 1. Typical heterogeneous microstructures fabricated by laser-based AM methods.
Over the past decade, a few review papers have been published to consolidate various aspects of AM, including the intricacies of heterogeneity introduced by AM [Citation22,Citation24]. To the best of the authors’ knowledge, however, there remains a gap in the literature concerning heterogeneous microstructures fabricated by AM with optimized strength-and-ductility synergy, according to the principal classification of heterogeneous microstructures shown in Figure (b–e) [Citation1]. In this article, we present a comprehensive review of heterostructured AM-produced metallic materials, with an emphasis on their tensile properties. We discuss the generation of heterogeneous microstructures via tailored fabrication methods for each melt pool, solidification characteristics, and the intrinsic heat treatment that contributes to heterogeneity. We also delve into the distinctive features, advantages, and potential applications of such microstructures. Finally, we conclude by summarizing the existing challenges and outlining the promising future opportunities in this rapidly evolving field.
2. AM processes to achieve heterogeneous microstructures
2.1. Layer-by-layer fabrication
The layer-by-layer processing approach inherent in AM provides the ability to tailor the material and microstructure of each melt pool, in contrast to the traditional subtractive manufacturing methods [Citation11,Citation27]. This enables manufacturers to build material systems with more intelligent, rapid, and integrated designs for multipurpose functionalities. Several strategies enable the fabrication of heterogeneous microstructures within AM: (i) the modification of process parameters or compositions for each melt pool to generate heterogeneity [Citation28,Citation29]; (ii) the gradual alteration of the composition and structure of the material to produce functional graded materials (FGMs) [Citation30]; (iii) the combination of AM and in situ processing after the creation of each hatch or layer to yield heterogeneous microstructures [Citation31]. This section describes the effect and optimization of several AM processing parameters by researchers for the layer-by-layer fabrication of metallic components. The heterogeneous microstructures of these materials is further characterized based on the desired enhancement of tensile properties.
2.1.1. Controlling microstructures of melt pools
The DED process offers a convenient means of depositing layered structures with desired architectures by controlling the powder feeding rate or types [Citation32,Citation33]. The technical difficulty of spreading multi-material powders during LPBF limits its application to printing components only from a single material [Citation34]. Recently, multi-material manufacturing in LPBF was achieved by using two or more dissimilar material powders and then adjusting the composition and print orientation along the 3D axes to obtain a layered microstructure [Citation20]. Simultaneously, we can blend different materials in situ to fabricate multi-material alloys. Apart from the heterogeneity introduced by chemical composition, we can also alter the AM processing parameters of each melt pool to introduce heterogeneity. The manipulation of each melt pool to fabricate heterogeneous microstructures is discussed in this section.
Extensive efforts have been made in DED to modify the chemical composition of each melt pool, aiming to create layered heterogeneous microstructures. Precise deposition of C300 maraging steel powder and austenitic 316L stainless steel (SS) powder in pre-designed patterns demonstrated the formation of both voxelized and layer-wise heterogeneous structures, as shown in Figure (a–c) [Citation29]. The voxelized heterostructured component displayed a complex hierarchical phase distribution on the micrometer-scale, with a three-dimensional distribution of different materials within and between layers (Figure (b)). The layer-wise heterostructured sample exhibited characteristic layer-wise features (Figure (c)). Besides fabricating different structures, for a specific type of heterogeneous microstructure, such as layer-wise heterogeneous microstructures, the deposition distance between two different materials (e.g. C300 maraging steel and 420 SS [Citation35]) could be adjusted to tailor the mechanical properties. Furthermore, the chemical compositions of the materials could be meticulously designed to produce dual-phase alloys composed of face-centered cubic (fcc) and body-centered cubic (bcc) phases, such as the cases of CrMnFeCoNi and AlCoCrFeNiTi0.5 laminated-HEA components [Citation36]. In LPBF, changing the powder composition is a typical challenge in manufacturing multi-material metallic materials [Citation37]. Innovations to address this challenge include the use of self-designed and homemade setup to print CoCrFeMnNi-HEA alloy matrix composites, 316L/IN718, and 316L/Cu10Sn alloys [Citation38,Citation39]. Another approach to produce heterostructured materials using AM involves in situ blending of different alloys. For example, the introduction of a small amount of 316L SS into the Ti6Al4V alloy resulted in alloys featuring micrometer-scale concentration variations of the elements present in 316L SS within the Ti6Al4V matrix [Citation28]. Besides changes in chemical compositions, adjustments in printing parameters play a role in generating heterogeneous microstructures. The manipulation of scan speed and energy density between melt pools of the same material produced heterogeneous microstructures, such as lamellar and rectangular core configuration, in the case of austenitic 316L SS [Citation40].
Figure 2. (a) The DED fabrication processes of producing martensitic grade 300 maraging steel and 316L voxelized heterostructured materials. (b) 3D optical microscope image of voxelized heterostructured materials (VHM). (c) Optical microscope image of layerwise heterostructured materials (LHM). (d) Engineering stress-strain curves for both VHM and LHM samples, along with true stress-strain curves and load-unload-reload behavior for the VHM sample. Reprinted with permission from Ref. [Citation29].
![Figure 2. (a) The DED fabrication processes of producing martensitic grade 300 maraging steel and 316L voxelized heterostructured materials. (b) 3D optical microscope image of voxelized heterostructured materials (VHM). (c) Optical microscope image of layerwise heterostructured materials (LHM). (d) Engineering stress-strain curves for both VHM and LHM samples, along with true stress-strain curves and load-unload-reload behavior for the VHM sample. Reprinted with permission from Ref. [Citation29].](/cms/asset/be24fbeb-4a81-4037-827f-10c2149059fc/tmrl_a_2305261_f0002_oc.jpg)
For the heterogeneous microstructures formed by combining martensitic grade 300 maraging steel powder with austenitic 316L SS powder, the voxelized heterostructured samples demonstrated better tensile properties than the layer-wise heterostructured samples [Citation29] (Figure (d)). This resulted from the effective backstress generated between the hard and soft domains in voxelized heterostructured components [Citation29]. In a sample with alternating CrMnFeCoNi and AlCoCrFeNiTi0.5 lamellae, a more favorable combination of compressive yield strength and macroscopic plasticity was achieved in comparison to high-strength bulk HEAs [Citation35]. Furthermore, a multi-scale layer-wise architecture, combining C300 maraging steel and 420 SS alloys, achieved a considerable ultimate tensile strength and elongation [Citation36]. This improvement was attributed to numerous unique deformation bands and HDI strengthening, distinguishing it from the homogeneous materials [Citation36]. Regarding the CoCrFeMnNi-HEA alloy matrix composites with an artificially designed bimodal grain structure, a 22% higher strength with superior ductility was observed in the split Hopkinson pressure bar test compared to homogeneous HEAs [Citation39,Citation41]. For heterostructured austenitic 316L SS with both lamellar and rectangular core architectures, the heterostructured samples showed a superior combination of strength and elongation with respect to properties reported in the literature and the homogeneous reference material [Citation40]. The abundant development of GNDs and enhanced twinning activity in the heterostructured samples were instrumental in achieving an enhanced strength-ductility synergy [Citation40]. The heterostructured Ti6Al4V material, in situ blended with 316L SS, exhibited a progressive transformation-induced plasticity effect, resulting in ∼1.3 GPa ultimate tensile strength with ∼9% uniform elongation, coupled with an impressive work-hardening capacity exceeding 300 MPa [Citation28].
2.1.2. Compositional gradient materials
Functional graded materials (FGM) are a class of advanced structural materials with changing compositions and properties such as strength and ductility throughout the geometry, as per the functional requirements [Citation42]. Compared with traditional composite materials, which are homogeneous mixtures or laminates of multiple materials (Figure (a)), FGMs are characterized by a gradient structure between the two materials (Figure (b)) [Citation43]. Materials with gradient structures can achieve an optimal balance of high strength and enhanced ductility by preventing strain localization, restraining shear banding, avoiding accumulation of dislocations, and suppressing cracking [Citation10,Citation44]. The layer-by-layer building characteristics and flexible design in AM processes provide an avenue for manufacturing FGM components with specific designs and gradient structures. This new method has been coined by researchers as functionally graded additive manufacturing [Citation45], which involves the strategical control of density and directionality of material deposition and produces monolithic components by varying the deposition density and orientations [Citation46]. The complexity of FGM design patterns as approached by AM processes and their influence on the tensile properties have been discussed below.
Figure 3. Schematic of (a) a conventional composite material and (b) functional gradient materials (reprinted with permission from [Citation43]). (c) Illustration of the TiO-reinforced Ti6Al4 V/316 L FGM with varying volume percentages of Ti6Al4 V and 316 L SS in different regions. (d)-(f) Electron backscatter diffraction (EBSD) images showing the grain distributions in the bottom, middle, and top regions. (g) The engineering stress-strain curve of in situ TiO-reinforced Ti6Al4 V/316 L FGM. (c) to (g) are reprinted with permission from Ref. [Citation30].
![Figure 3. Schematic of (a) a conventional composite material and (b) functional gradient materials (reprinted with permission from [Citation43]). (c) Illustration of the TiO-reinforced Ti6Al4 V/316 L FGM with varying volume percentages of Ti6Al4 V and 316 L SS in different regions. (d)-(f) Electron backscatter diffraction (EBSD) images showing the grain distributions in the bottom, middle, and top regions. (g) The engineering stress-strain curve of in situ TiO-reinforced Ti6Al4 V/316 L FGM. (c) to (g) are reprinted with permission from Ref. [Citation30].](/cms/asset/89fe4386-5bcb-4b9b-acc6-752386d882aa/tmrl_a_2305261_f0003_oc.jpg)
Several FGMs have been manufactured by the DED process. A FGM was fabricated with in situ TiO-reinforced Ti6Al4V/316L SS alloy powders. This FGM consisted of three layers, each containing varying volumes of 316L SS powder, as shown in Figure (c) [Citation30]. Besides the composition change, the component showed a spatial heterogeneous microstructure. The microstructure featured a transition from columnar grains at the bottom (Figure (d)), to large equiaxed grains in the middle (Figure (e)), and small equiaxed grains at the top (Figure (f)) [Citation30]. A crack-free TiCp/Ti6Al4V FGM composite was successfully fabricated with the TiC volume fraction changing gradually from 0% to 50% [Citation47]. Other than Ti-based FGMs, stainless steel-based FGMs are widely investigated due to their high strength and toughness using DED. A FGM consisting of 316L SS and IN718, with varying compositional gradients, was investigated [Citation48], which revealed that FGMs with lower compositional gradients experienced grain coarsening, primarily attributed to heat accumulation during the fabrication process. A defect-free sandwich 316L SS/IN625 FGM specimen with an intermediate composition consisting of a 50–50 mixture of 316L SS-IN625 alloys was fabricated [Citation49]. The microstructure transformed from a cellular structure at the bottom to a mixed cellular/columnar structure in the intermediate layer and subsequently transitioned into a columnar structure of IN625 alloy at the top. Hybrid manufacturing is another category of FGMs including the laser deposition of material on a wrought substrate of either the same or different composition. Ti6Al4V and Ti6.5Al3.5Mo1.5Zr0.3Si alloys deposited under such circumstances showed a gradient microstructure from the substrate to the laser melted zone through the interface region [Citation50,Citation51]. Similarly, a crack-free γ-TiAl/Ti2AlNb graded metallic alloy was fabricated by depositing γ-TiAl powder on a Ti2AlNb alloy substrate [Citation15]. Using LPBF to fabricate FGMs requires multiple feeders to control the heterogeneous metal composition. A mild steel-copper FGM was fabricated using LPBF which showed ultrahigh bonding strength due to interfacial strengthening [Citation52]. Grain-size gradients and heterogeneous microstructures were introduced in 316L SS/CuCrZr FGM [Citation53]. The gradient microstructure was identified by the presence of ultrafine equiaxed grains in the diffusion zone, which was sandwiched between columnar grains on the two sides of 316L SS and CuCrZr alloys. In addition to multi-material-based FGMs, DED and LPBF have also provided avenues to process high-yield strength metallic lightweight structures with varying spatial density [Citation54,Citation55].
The in situ TiO reinforced Ti6Al4V/316L SS alloy FGM, characterized by variations in both composition and grain size, demonstrated superior ultimate tensile strength and elongation (Figure (g)) than Ti6Al4V/316 L SS in the literature [Citation30]. The tensile yield strength of 316L SS/IN625 FGM was similar to that of pure IN625 alloy processed by AM, although its ultimate tensile strength was closer to that of the 316L SS alloy [Citation49]. Necking occurred on the 316L SS side, as IN625 showed a much higher strength. The heat affected zone (HAZ) formed between the wrought substrate and the deposited part controls the quality of metallurgical bonding and hence the mechanical behavior of hybrid FGMs. However, the coarse and brittle colonies formed in either the HAZ or wrought region tend to decrease the elongation of the hybrid FGMs compared to either wrought or laser deposited part [Citation50,Citation51]. The interfacial shear strength of the 316L/CuCrZr samples was higher than that of the CuCrZr sample and other reported steel/copper samples, which can be attributed to the ultrafine equiaxed grains and heterogeneous microstructure [Citation53]. The ultimate tensile strength of the 316L/CuCrZr sample was similar to that of the CuCrZr sample manufactured by LPBF [Citation53].
2.1.3. Influence of in situ processing
External energy introduced into melt pools may influence both the solidification and subsequent thermal cycling processes, thereby facilitating the formation of equiaxed grains [Citation21,Citation56]. For instance, in additively manufactured IN625, by toggling high-intensity ultrasound on and off, a distinct pattern emerged, with alternating primary γ grains consisting of columnar structures measuring 500 µm in length and 150 µm in width, and equiaxed primary γ grains, which were significantly smaller, measuring only a few micrometers in size [Citation21]. The introduction of ultrasound leads to the creation of acoustic cavitation and streaming within the liquid metal, resulting in the solidification of small equiaxed grains (Figure (a)). A similar effect was observed in the IN718 alloy. The resulting hybrid sample, with an alternation of columnar and small equiaxed grains (Figure (b)), exhibited higher strength than the counterpart without ultrasound (Figure (c)) [Citation31]. When assisted by ultrasonic vibration, the fabricated 321 SS exhibited a heterogeneous microstructure along the build direction. The microstructure transitioned from a region with columnar dendritic grains to an intermediate region featuring a mixture of columnar and equiaxed dendritic grains, ultimately culminating in a region dominated by equiaxed dendritic grains [Citation57]. Simultaneously, there was a declining trend in hardness from the substrate to the upper surface. In comparison to a homogeneous counterpart fabricated without ultrasonic vibration, the yield strength increased by ∼11.9%, and the ultimate tensile strength improved by ∼2.6% [Citation57]. Another approach that incorporates ultrasound in AM involves subsequent cyclic thermal influence. This method entailed the application of ultrasonic impact after each layer deposition to introduce intense plastic deformation into the solidified structure. Subsequently, during the heating of successive deposition layers, recrystallization took place, resulting in the formation of fine equiaxed grains. This approach has been successfully applied to achieve a microstructure consisting of fine columnar and equiaxed grains in a LPBF Ti6Al4V [Citation56].
Figure 4. (a) A schematic showing the process of DED onto an ultrasound sonotrode. The high-intensity ultrasound leads to the creation of acoustic cavitation and streaming within the liquid metal. These effects vigorously agitate the molten material during solidification, resulting in the significant modification and refinement of the microstructure [Citation21]. (b) The EBSD inverse pole figure map along the build direction for the sample produced using the hybrid deposition strategy with the ultrasound on and off. This map reveals the heterogeneous microstructure with small equiaxed grains formed by ultrasound. (c) Tensile properties of IN718 part manufactured through both the hybrid deposition and conventional DED methods. (b) and (c) are reprinted with the permission from Ref. [Citation31].
![Figure 4. (a) A schematic showing the process of DED onto an ultrasound sonotrode. The high-intensity ultrasound leads to the creation of acoustic cavitation and streaming within the liquid metal. These effects vigorously agitate the molten material during solidification, resulting in the significant modification and refinement of the microstructure [Citation21]. (b) The EBSD inverse pole figure map along the build direction for the sample produced using the hybrid deposition strategy with the ultrasound on and off. This map reveals the heterogeneous microstructure with small equiaxed grains formed by ultrasound. (c) Tensile properties of IN718 part manufactured through both the hybrid deposition and conventional DED methods. (b) and (c) are reprinted with the permission from Ref. [Citation31].](/cms/asset/14fe0a3e-0f5c-48d1-9288-1f11bed80df9/tmrl_a_2305261_f0004_oc.jpg)
By controlling the dislocation density and thermal stability of an alloy fabricated by AM, recrystallization can be deliberately induced during heat treatment to create heterogeneous microstructures [Citation58,Citation59]. In the case of 316L SS, a smaller hatch distance resulted in a higher number of GNDs due to increased cumulative plastic strain. Additionally, remelting each layer promotes local chemical composition homogenization through solid-state diffusion. Both factors facilitate recrystallization during heat treatment. The authors show their ability to fabricate heterogeneous microstructures with alternating recrystallized and non-recrystallized regions. This heterogeneity leads to materials with superior tensile performance compared to those featuring a monolithic microstructure due to HDI strengthening [Citation58].
2.2. Solidification characteristics
In laser-material interaction, the intensity of the laser beam is highest at the center and diminishes towards the edges, leading to a radial temperature gradient within the melt pool. This results in a characteristic cross-sectional shape with deeper centers and shallower edges. Following melting, cooling primarily occurs through heat conduction towards the substrate, with cooling rates reaching up to 105–106 K/s [Citation60,Citation61]. The rapid and directional cooling inherent in AM processes imparts distinctive grain and cellular or dendritic structures to the as-fabricated parts. The solidification process is chiefly governed by two factors: thermal gradient (G) and growth rate (R), as shown in Figure (a) [Citation22]. G represents the temperature difference over a specific distance (dT/dx), while R is the product of the speed of the moving heat source (v) and the cosine of θ, where θ denotes the angle between the growth direction and the direction of heat source. Both G and R exhibit variations across time and location within the melt pool. The product of G and R determines the growth rate, which in turn dictates the fineness of the microstructure—the higher the G R value, the finer the resulting microstructure. The ratio G / R plays a crucial role in determining the solidification mode, ranging from planar to cellular, columnar dendritic, or equiaxed dendritic structure (in descending order of G / R values). This variation in G and R across the melt pool results in different grain morphologies and variations in cell/dendrite size, offering control over heterogeneous structural characteristics. Furthermore as depicted in Figure (b), undercooling is primarily induced by constitutional supercooling, which promotes columnar-to-equiaxed transition transformation [Citation22,Citation23]. As a result, it is possible to regulate constitutional supercooling by adjusting the composition. Additionally, the growth direction in AM follows specific criteria, providing opportunities to customize the textures of as-fabricated parts.
Figure 5. (a) Impact of growth rate (R) and temperature gradient (G) on solidification microstructure size and morphology. (b) Undercooling and constitutional supercooling as functions of arc length for a DED process. The area under the Gaussian distribution represents the probability of heterogeneous nucleation. Arc length indicates the distance from the top to bottom of the melt pool along the solid/liquid interface. Reproduced with permission from Ref. [Citation22].
![Figure 5. (a) Impact of growth rate (R) and temperature gradient (G) on solidification microstructure size and morphology. (b) Undercooling and constitutional supercooling as functions of arc length for a DED process. The area under the Gaussian distribution represents the probability of heterogeneous nucleation. Arc length indicates the distance from the top to bottom of the melt pool along the solid/liquid interface. Reproduced with permission from Ref. [Citation22].](/cms/asset/e4adb7fb-3b51-45ed-83f2-6767d8c58e68/tmrl_a_2305261_f0005_oc.jpg)
2.2.1. Microstructure differences between melt pool boundaries and interiors
Some additively manufactured alloys show differences between the interiors and boundaries of melt pools. In the literature, two prevailing explanations for the formation of this specific pattern have been widely discussed: (i) Some reports attribute it to the difference in G and R between the interiors and boundaries of melt pools during the solidification process [Citation62,Citation63]. (ii) An alternative viewpoint suggests that these distinctions are due to the reheating that occurs during the melting of the subsequent hatch or layer [Citation64–66]. The dissimilarity between melt pool interiors and boundaries is evident in titanium alloys with a high content of β stabilizing elements. For instance, in the case of DED Ti5Al5Mo5V1Cr1Fe near β titanium alloy, a unique microstructural pattern was observed: beneath the melt pool boundaries, there were layer bands with a duplex microstructure with low hardness, while the regions between layer bands displayed an ultra-fine basket-weave microstructure with high hardness [Citation65]. A similar observation has been made in a DED Ti6.5Al3.5Mo1.5Zr0.3Si alloy, where the interlayer bands formed in the narrow region just below each layer [Citation66].
AM-produced AlSi10Mg alloys typically show a distinct microstructure consisting of fine cells/dendrites within the melt pools, coarse cells/dendrites along the melt pool boundaries, and a thin layer of heat affected zone beneath the melt pool boundaries [Citation62,Citation67–75]. Tensile tests on the Al–Si alloy samples reveal that the material exhibits anisotropic strength and ductility characteristics. Previous studies indicate that the fracture behavior of such LPBF alloys is primarily linked to the generation and propagation of microvoids and cracks within the melt pool boundaries [Citation74]. These defects are induced by strain incompatibilities between melt pool interiors and boundaries [Citation70,Citation73,Citation74].
When Zirconium (Zr) and Scandium (Sc) are introduced into additively manufactured Al alloys, the resulting microstructure exhibits a distinctive pattern. It comprises fine equiaxed grains along the boundaries of the melt pools, while within the melt pools, coarse columnar grains grow along the thermal gradient. This phenomenon is observed in various alloy compositions, including the AlCuMgZr alloy [Citation76], Scalmalloy alloy [Citation77–82], AlMgScZr alloy [Citation83–90], and AlMnSc alloy [Citation91,Citation92]. The harmonic grain distribution observed in these alloys primarily results from the presence of a significant number of Al3(Sc, Zr) particles, which act as nuclei for the solidification of the Al matrix. These particles also serve as grain growth inhibitors, leading to the formation of a fine-grained microstructure along the melt pool boundaries. Inside the hot melt pool region, most of these particles dissolve, and the precipitation of Al3(Sc, Zr) is effectively suppressed due to the non-equilibrium solidification process. As a result, the growth of coarse columnar crystals occurs within the melt pools. The harmonic pattern was reported for the LPBF AlSi10Mg alloy when employing bidirectional scanning patterns [Citation67]. When Si was added to an AA7075 alloy, ultrafine equiaxed grains tended to form along the melt pool boundaries, while elongated coarse columnar grains developed within the melt pools [Citation93]. The harmonic pattern was closely linked to the uneven distribution of Si within the matrix, suggesting that the presence of Si encouraged the solidification of finer grains in those regions.
The application of laser-based AM in Al alloys with the addition of Zr or Sc enables the achievement of a harmonic grain size distribution, resulting in an outstanding combination of strength and ductility. Figure (e) shows a summary of the yield strength and elongation to failure for various aluminium alloys, including additively manufactured Al alloys with the addition of Zr or Sc [Citation79–83,Citation86–92,Citation94–104], additively manufactured AlSi10Mg alloys [Citation62,Citation70,Citation73,Citation74,Citation105–111], cast Al alloys [Citation112], and rolled AlMgSc alloys [Citation113,Citation114]. The comparison reveals that AM-produced AlSi10Mg alloys show superior strength compared to cast Al alloys, while maintaining similar levels of elongation. However, in comparison to rolled AlMgSc alloys, the AM-produced alloys tend to be more brittle but exhibit slightly greater strength. Among these four categories, additively manufactured Al alloys with the addition of Zr or Sc demonstrate the most favorable combination of strength and ductility. In the case of LPBF AlCuMgZr alloy, the yield strength has been found to increase by 76.3% compared to LPBF AlCuMg alloy, due to the addition of Zr [Citation76]. Similarly, the LPBF AlMgZr alloy showed superior ductility, a benefit attributed to the harmonic grain size distribution, which induced HDI strengthening that stabilized the tensile deformation [Citation95]. Moreover, LPBF AlMgScZr samples exhibited an improved yield strength, about 2.8 times that of a fully equiaxed grain structured AlMgScZr sample produced using DED. This increase was attributed to additional back stress hardening and improved strain hardening ability [Citation83]. AlMgScZr alloys processed via DED with air cooling (AC) or water cooling (WC) substrates showed differing grain structures: the AC sample showed an equiaxed grain structure while the WC sample showed a heterogeneous grain structure. The WC sample demonstrated a yield strength ∼1.4 times that of the AC sample, while maintaining comparable uniform elongation [Citation86]. Furthermore, LPBF Al7075+Zr alloy produced using different powders consistently exhibited superior strength and ductility when compared to plate AA7075 and AM AA7075 alloys. Additionally, yield strength, ultimate tensile strength, and strain-at-failure for as-built Zr-modified AA6061 were determined to be superior to the tensile properties of AA6061 alloys in annealed or as-cast conditions [Citation96].
Figure 6. (a) Schematic diagram depicting the formation of three zones during LPBF of AlSi10Mg, where TL is the liquidus temperature and TS is the solidus temperature (reprinted with permission from Ref. [Citation64]). (b) Scanning electron microscopy (SEM) image revealing coarse cells along melt pool boundaries and fine cells within melt pools in AMed AlSi10Mg alloys (reprinted with permission from Ref. [Citation74]). (c) Schematic illustration showing equiaxed grain nucleation caused by Al3(Sc, Zr) precipitates along melt pool boundaries during solidification of AMed Al alloys (reproduced with permission from Ref. [Citation94]). (d) Inverse polar figure displaying the distribution of fine grains along melt pool boundaries and coarse columnar grains inside melt pools in AMed Al alloys with Sc and Zr additions (reprinted with permission from Ref. [Citation83]). (e) Comparative analysis of ultimate strength and elongation among cast Al alloys, AMed AlSi10Mg alloys, rolled AlMgSc alloys, and AMed Al alloys with Sc/Zr additions.
![Figure 6. (a) Schematic diagram depicting the formation of three zones during LPBF of AlSi10Mg, where TL is the liquidus temperature and TS is the solidus temperature (reprinted with permission from Ref. [Citation64]). (b) Scanning electron microscopy (SEM) image revealing coarse cells along melt pool boundaries and fine cells within melt pools in AMed AlSi10Mg alloys (reprinted with permission from Ref. [Citation74]). (c) Schematic illustration showing equiaxed grain nucleation caused by Al3(Sc, Zr) precipitates along melt pool boundaries during solidification of AMed Al alloys (reproduced with permission from Ref. [Citation94]). (d) Inverse polar figure displaying the distribution of fine grains along melt pool boundaries and coarse columnar grains inside melt pools in AMed Al alloys with Sc and Zr additions (reprinted with permission from Ref. [Citation83]). (e) Comparative analysis of ultimate strength and elongation among cast Al alloys, AMed AlSi10Mg alloys, rolled AlMgSc alloys, and AMed Al alloys with Sc/Zr additions.](/cms/asset/b5efe962-b4df-4d6c-8437-305a1453b2f5/tmrl_a_2305261_f0006_oc.jpg)
2.2.2. Control of nucleation and grain growth
Control of the G and R through the process parameters such as laser power, laser speed, substrate temperature, and beam diameter, can yield either columnar or equiaxed grain morphologies [Citation115]. High G with low R typically favors directional epitaxial growth, while low G and high R leads to equiaxed grain formation (Figure (a)) [Citation116]. In DED, an alternating arrangement of equiaxed and columnar grains can be achieved by fine-tuning G and R parameters. For instance, DED IN718 samples exhibited a banded grain structure, with fine grains between the layers of inclined columnar grains [Citation115,Citation117,Citation118]. The gradient laser power deposition method, which uniformly decreases laser power layer-by-layer with increasing deposition height, resulting in a mixed structure of equiaxed and fine elongated columnar grains [Citation119]. A similar grain morphology was observed in a CO2 laser formed Cu38Ni alloy, where large grains traversed the AM layers, and the layer boundaries consisted of fine grains [Citation120]. In Ti alloys, such as Ti5Al5Mo5V1Cr1Fe, large columnar grains were prominent at the overlap zone between adjacent tracks due to epitaxial growth, while small columnar and equiaxed grains formed at the top of individual tracks, resulting in a ‘bamboo’-like grain morphology (Figure (a)) [Citation65,Citation121]. As a result, the heterogeneous microstructure included three types of β grains: large columnar, small columnar, and equiaxed (Figure (b)). Similar observations were made for a Ti6.5Al3.5Mo1.5Zr0.3Si alloy, where an alternately arranged grain morphology of columnar and equiaxed grains was found, with columnar grains at the overlap of melt pools and equiaxed grains at the center of melt pools where no overlap occurs [Citation122]. A ‘steel-bar reinforced concrete’-like mixed grain structure consisting of coarse continuous columnar grains and fine inter-pillar equiaxed grains was also reported for Ti6.5Al3.5Mo1.5Zr0.3Si [Citation123]. In other titanium alloys as studied in the Refs [Citation124–127], different strategies have been employed to achieve a mix of columnar and equiaxed grains. DED IN718 stand out with the gradient laser power deposition method, which yielded a blend of equiaxed and elongated columnar grains, enhancing both strength and ductility [Citation119]. In contrast, the Ti6.5Al3.5Mo1.5Zr0.3Si alloy displayed alternating columnar and equiaxed grains, offering elevated strength but reduced ductility in the DED state [Citation122]. Similarly, a Ti5Al2Sn2Zr4Mo4Cr alloy with a mixed prior β grain structure showed higher strength but decreased ductility in its as-deposited form [Citation128]. Lastly, the Ti5Al5Mo5V3Cr1Zr alloy reveals anisotropic tensile properties with excellent elongation but relatively low yield strength and ultimate tensile strength, primarily due to the absence of α phase reinforcement in the prior β grains [Citation129].
Figure 7. (a) Schematic representation of the formation process of β grains, with small equiaxed grains developing at the top of melt pools. (b) Corresponding morphology of β grains in a DED Ti5Al5Mo5V1Cr1Fe alloy, showing a heterogeneous grain distribution with alternating columnar and equiaxed grains. Reprinted with permission from [Citation65]. 3D crystal orientation maps obtained by SEM-EBSD for 316L SS specimens fabricated under conditions of (c) low energy density and (d) high energy density. (e) True stress–true strain curves at room temperature for specimens from (c) (referred to as SLM-CLM) and (d) (referred to as SLM-single), along with a reference plate [Citation137].
![Figure 7. (a) Schematic representation of the formation process of β grains, with small equiaxed grains developing at the top of melt pools. (b) Corresponding morphology of β grains in a DED Ti5Al5Mo5V1Cr1Fe alloy, showing a heterogeneous grain distribution with alternating columnar and equiaxed grains. Reprinted with permission from [Citation65]. 3D crystal orientation maps obtained by SEM-EBSD for 316L SS specimens fabricated under conditions of (c) low energy density and (d) high energy density. (e) True stress–true strain curves at room temperature for specimens from (c) (referred to as SLM-CLM) and (d) (referred to as SLM-single), along with a reference plate [Citation137].](/cms/asset/37c13eed-ab18-4385-927c-158af17b0e9b/tmrl_a_2305261_f0007_oc.jpg)
The LPBF process can be used to fabricate heterogeneous microstructures and crystallographic orientations depending on the material and specific parameters. In LPBF Ni-25at.% Mo alloys, the combination of a small melt pool and high energy density resulted in a pronounced tendency for a combination of long columnar grains at the center of melt pools that span several melt pools and inclined columnar or small grains away from the center [Citation130]. LPBF IN718 exhibited a heterogeneous microstructure consisting of long columnar grains and irregular grains [Citation131,Citation132]. An alternating fine and coarse grain structure was identified in a LPBF CM247LC alloy due to the island scan strategy [Citation133]. Ti6Al4V samples fabricated under 200 and 300 W conditions exhibited a distinctive sandwich structure with alternating layers of fine and coarse grains, while the 100 W condition resulted in a unimodal distribution [Citation134]. LPBF 316L SS parts fabricated without any rotation resulted in a unique crystallographic orientation, primarily featuring large <101> oriented grains separated by thin bands of small <100> oriented grains with respect to the building direction. The introduction of a rotated scan pattern eliminated these bands [Citation135]. In LPBF-produced 316L SS processed with high power, approximately 100 μm thick rectangular beam-shaped grains coexisted with equiaxed grains in the microstructure. Equiaxed grains originated at the center of the melt pool and developed from the last fraction of liquid to solidify [Citation136]. In another study, 316L SS specimens fabricated under low energy density exhibited a layered microstructure with alternating differently oriented grains (Figure (d)) [Citation137]. In contrast, specimens fabricated under high energy density displayed a single crystal-like structure (Figure (d)). LPBF 316L SS exhibited unique macroscopic textures due to specific laser scanning patterns, forming mosaic-type macrostructures with tesserae measuring 100–150 µm in size. Each tessera showed distinct crystallographic orientations compared to adjacent ones, with smaller recrystallized grains between the tesserae [Citation138]. Furthermore, in LPBF 316L SS fabrication, the ability to vary the laser scanning angle enables the production of stainless-steel samples with controlled crystallographic textures. The resulting microstructures can range from strongly textured blocks of arbitrary thickness and shape to gradient crystallographic textures [Citation139]. The enhanced strain hardening and ductility observed in the Ti6Al4V sample with a bimodal sandwich microstructure, in comparison to the unimodal sample, can be attributed to HDI strengthening [Citation134]. LPBF-fabricated 316L SS parts characterized by a heterogeneous microstructure exhibited exceptional mechanical properties. These included the highest yield strength (449 ± 2.4 MPa), ultimate tensile strength (527 ± 5.4 MPa), and ductility (58 ± 1.3%), surpassing samples with random grain morphologies [Citation135]. The lamellar-structured 316L SS was observed to exhibit higher strength and ductility compared to both the single crystal-like structured counterpart and reference commercial part (Figure (e)) [Citation137]. Additionally, mosaic-type macrostructures in ferritic steel led to superior mechanical properties, including high strength and microhardness, when compared to various stainless-steel grades, including austenitic, ferritic, and duplex types. Notably, the ferritic steel also demonstrated remarkable ductility, with over 45% elongation, a significant improvement over counterparts with 30–40% elongation [Citation138].
Microalloying modifications can effectively promote the formation of equiaxed grains during the deposition process, thus generating heterogeneous microstructures. The addition of certain elements increases undercooling, promoting the nucleation of equiaxed grains ahead of the solid/liquid interface during solidification, potentially leading to the columnar-to-equiaxed transition with varying grain fractions depending on undercooling levels [Citation140]. For instance, when boron was added to the LPBF Ti6Al4V alloy, a noticeable increase in the volume fraction of equiaxed dendrites was observed once the boron content surpasses 0.17 wt.%. This alteration resulted in a microstructure characterized by alternating columnar and equiaxed dendrites [Citation140]. With the addition of 2wt.% La to pure Ti, an alternating microstructure was observed, featuring extensive distributions of large tortuous α grains interspersed with fine-equiaxed α grains [Citation141]. Similarly, the incorporation of titanium Carbide (TiC) into 316L SS resulted in nanocomposite samples exhibiting a bimodal grain structure, comprising large areas of elongated columnar grains adjacent to regions containing fine grains [Citation142].
2.3. Cyclic intrinsic heat treatment
Components fabricated by laser-based AM have a specific thermal history, which leads the parts to undergo rapid quenching and subsequent intrinsic heat treatment (IHT) [Citation19]. The layer-by-layer characteristic further allows local tailoring of the designed microstructure by IHT. The deposition process can be temporarily paused after specific layers to facilitate IHT and create targeted heterogeneous microstructures. Alternatively, it is possible to adjust the processing parameters to form heterogeneous layer patterns during the fabrication process without requiring interruptions [Citation143].
A 120-second pause after deposition of every four layers (Figure (a)) triggered martensitic transformation and NiAl precipitation in a Fe19Ni5Ti (wt.%) maraging steel, forming a hierarchical structure with alternating soft and hard layers resembling Damascus steel (Figure (b)) [Citation19]. The hard layers containing nanoscale precipitates showed higher hardness in comparison to the soft layers devoid of any nanoprecipitates. The layered Damascus steel exhibited an exceptional combination of 1.3 GPa ultimate tensile strength with 10% elongation (Figure (c)), surpassing both its homogeneous counterpart (Figure (c)) and ancient Damascus steel [Citation19]. The study also emphasized that process parameters such as laser power, scan speed, external heating and cooling, and their combination can highly influence the AM heterostructures. A similar ‘pause’-strategy was also implemented which indicated that the IHT may eliminate the post-printing heat treatment required for maraging steel [Citation144]. By investigating the aging curves of MAR60HRC and a faster aging response of the DED system, the study designed intrinsic aging scenarios to apply the age-hardening effect during the deposition process. The cooling caused during a pause, triggered localized martensitic transformation at each layer, thereby enhancing the age-hardening. IHT was also demonstrated to be able to induce precipitation of NiAl nanoparticles in Fe19NixAl maraging steel [Citation145].
Figure 8. (a) A schematic of the fabrication process. After the construction of each four layers, the process was paused for 120 s to enable sample cooling. The temperature profile with the Martensite starting temperature (Ms) indicated is shown on the right. (b) A light optical micrograph displaying a dark band at the location where the pause was introduced. The overlay of the hardness curve reveals peaks in hardness corresponding to each dark band. (c) Tensile stress-strain curves of layered Damascus steel and the homogeneous counterpart manufactured without interruptions during the fabrication process. Reprinted with permission from [Citation19].
![Figure 8. (a) A schematic of the fabrication process. After the construction of each four layers, the process was paused for 120 s to enable sample cooling. The temperature profile with the Martensite starting temperature (Ms) indicated is shown on the right. (b) A light optical micrograph displaying a dark band at the location where the pause was introduced. The overlay of the hardness curve reveals peaks in hardness corresponding to each dark band. (c) Tensile stress-strain curves of layered Damascus steel and the homogeneous counterpart manufactured without interruptions during the fabrication process. Reprinted with permission from [Citation19].](/cms/asset/63b77cda-64dc-45a2-a888-c836f864cb64/tmrl_a_2305261_f0008_oc.jpg)
In the case of AM fabrication without pausing for titanium alloys with a high content of β-stabilizing elements (e.g. Ti6Al2Sn2Zr3Mo1.5Cr2Nb), the cyclic reheating led to the formation of layer bands within the material [Citation143]. In Ti alloys, there are two types of layer bands: one is the narrower band located at the bottom of the melt pool, which has been discussed in section 2.2.2; the other is the heat-affected band, which does not correspond to the melt pool boundaries, and this is a focal point of the discussion in this section. For the DED Ti6.5Al3.5Mo1.5Zr0.3Si alloy, two distinct zones were observed. The layer bands exhibited a unique bimodal microstructure, consisting of fork-like primary α (αp) and fine lamellar β transformed matrix [Citation66] or martensitic α′ with longer plates of α phase [Citation146]. Regions between layer bands presented a similar basket-weave microstructure. Interestingly, layer bands and regions between the layer bands exhibited similar micro-hardness values [Citation66,Citation146]. In the case of the LPBF Ti6.5Al2ZrMoV alloy, the dual- and quadruple-laser processed samples exhibited layer bands compared to the single-laser processed sample, resulting from reheating of the substrate material to temperatures near the β transus temperature [Citation147]. For the DED Ti6Al4V alloy, layer-band region promoted the formation and growth of the α colonies[Citation148–151] or showed coarse microstructure [Citation152]. These layer bands are typically observed in materials manufactured with DED and are absent in those produced with LPBF [Citation153]. Additionally, the LPBF Ti6Al4V alloy may also exhibit layer bands [Citation154]. Between the layer bands of the Ti7Al3Zr2V alloy, the microstructure contained oriented α Widmanstätten laths within a remnant β matrix. Within the layer bands, ultrafine basket-weave microstructures were composed of stripe-like α and remnant β [Citation155]. For Ti48Al2Nb2Cr and Ti47Al2Cr2V titanium aluminide intermetallic alloys, a narrow region just below the melt pool is reheated to high temperatures, thus enhancing the precipitation of new equiaxed grains (Figure (a)), and finally formed a unique layered microstructure comprised of alternating duplex regions and nearly lamellar regions (Figure (b,c), respectively) [Citation156,Citation157]. In a DED Zr45Ti31.5Nb13.5Al10 HEA, the material exhibited melt pools with a bcc structure and heat-affected zones featuring a mixed structure of bcc + ordered bcc (B2) nanoprecipitates, arranged in a lamellar structure [Citation158].
Figure 9. (a) A schematic illustrating the DED process of the Ti48Al2Nb2Cr titanium aluminide intermetallic alloy, highlighting the evolution of the heterogeneous microstructure. (b) EBSD map showing the nearly lamellar region with α2/γ lamellae and a massive γ phase (γm). (c) EBSD map showing the duplex region with equiaxed grains containing lamellae and randomly distributed γm grains. (d) Tensile stress–strain curves of the specimens tested at room temperature and 760°C. Reproduced with the permission from Ref. [Citation156].
![Figure 9. (a) A schematic illustrating the DED process of the Ti48Al2Nb2Cr titanium aluminide intermetallic alloy, highlighting the evolution of the heterogeneous microstructure. (b) EBSD map showing the nearly lamellar region with α2/γ lamellae and a massive γ phase (γm). (c) EBSD map showing the duplex region with equiaxed grains containing lamellae and randomly distributed γm grains. (d) Tensile stress–strain curves of the specimens tested at room temperature and 760°C. Reproduced with the permission from Ref. [Citation156].](/cms/asset/ae291c92-4949-4803-a1ef-1618887b2310/tmrl_a_2305261_f0009_oc.jpg)
In materials with layer bands, the orientation of the bands can influence the mechanical properties. For example, in a DED Ti6.5Al3.5Mo1.5Zr0.3Si alloy, the sample parallel to the deposition direction exhibited lower ultimate tensile strength but better elongation compared to the sample oriented perpendicular to the deposition direction [Citation146]. In a Ti6Al4V alloy with layer bands, tensile tests revealed different strain distributions between layer bands and other regions [Citation159,Citation160], with significant strain heterogeneities increasing with applied strain [Citation161]. Strain localization is more pronounced on layer bands [Citation161,Citation162], although there is no strong evidence of the influence of layer bands on the fracture of the sample [Citation162]. In the case of Ti48Al2Nb2Cr and Ti47Al2Cr2V titanium aluminide intermetallic alloys with alternating microstructures, regions with nearly lamellar structures exhibited higher hardness than the duplex regions [Citation157], and the samples tended to fracture in the near-lamellar region [Citation156]. The deposited samples exhibited good tensile properties at both room temperature and high temperature (760°C), with the ductility at high temperature being comparable to that at room temperature (Figure (d)). Additionally, in a DED Zr45Ti31.5Nb13.5Al10 HEA with a bcc structure inside the melt pools and a bcc matrix with B2 nanoprecipitates in the heat-affected zones, the heterogeneous lamellar structure within the melt pool and heat-affected zone helped mitigate stress concentration and enhanced flow stresses. Consequently, this sample demonstrates higher compressive strength and ductility compared to the as-cast sample [Citation158].
3. Features, advantages, and applications
AM is a disruptive technology, not only because it enables the production of components with complex geometries, but also because it provides unique opportunities for microstructure control and materials design [Citation13,Citation19]. In contrast to conventional manufacturing technologies, such as casting, forging, and hot rolling, AM offers additional degrees of freedom to ‘architect’ the material microstructure across many length scales. Owing to this unique capability, both beam-based processes, LPBF and DED, unlock new opportunities for tailoring microstructures and their related mechanical and functional properties of metals and alloys [Citation19,Citation30]. Understanding the intricate relationships between these complex microstructures and the consequential mechanical and functional properties is key to developing novel material designs. Laser or e-beam based AM allows for precise control over the microstructure within each melt pool and the overall global microstructures. By adjusting process parameters, it allows for tailoring localized microstructures, enabling the customization of distinct heterogeneous zone sizes and specific mechanical properties.
The use of laser-based AM for creating heterogeneous microstructures offers several distinct advantages. Firstly, it allows to produce heterogeneous microstructures that are difficult or impossible to achieve with traditional manufacturing techniques. Secondly, it shows the ability to tune material compositions, volume fractions, and spatial distributions of heterogeneity that leads to HDI hardening, resulting in enhanced mechanical properties. This ability optimizes the stress–strain distribution, achieving a balance of strength and ductility. Table S1 in the Supplementary Information summarizes the tensile properties of the alloys studied in this review article. Furthermore, laser-based AM reduces waste and manufacturing time compared to conventional methods, as it produces near-net shape structures without the need for extensive post-processing and machining, making it a more efficient and sustainable fabrication approach.
AM of heterostructured materials offers the potential to fabricate heterogeneous, multi-material components with superior mechanical properties for aerospace, automobile, biomedical, and electronics applications. Research is currently focussed on introducing material heterogeneities on a multi-dimensional scale, i.e. both temporal and spatial distribution [Citation24]. Some potential aerospace applications are shown in Figure (a–b), including a one-piece rocket [Citation163] and a blisk in turbine engines [Citation15]. Additional applications comprise aerospace heat exchangers [Citation165], combustion chambers for space applications [Citation166], and dual-metal components [Citation165,Citation167]. Specifically, the Ti6Al4V alloy is widely used in the aerospace industry due to its excellent high-temperature performance and high specific density, but suffers from relatively low hardness, low wear resistance, and high chemical reactivity [Citation8,Citation168,Citation169]. Depending on specific application, graded Ti alloys with a spatial change in composition and microstructure can be fabricated using the AM methods. The material design and combination primarily depend upon the application of the component. The Ti-Ni-C graded composites were printed using a DED system, showing increased high-temperature resistance and enhanced surface wear resistance by altering the gradient composition [Citation170]. In extreme environments with high temperatures and corrosive conditions, as encountered by the aerospace or nuclear industries, combinations of Ti- and Ni-based alloys into gradient materials can be beneficial due to their high thermal creep and oxidation resistance [Citation171]. The concept of FGMs can be also used to reduce the sudden change in the coefficient of thermal expansion for two or more distinct materials when gradually bonded together. This can prevent catastrophic failures which arise due to easier crack generation at the composition transition interfaces. FGMs by AM could be used in the automotive industry such as for automotive valve stems. In high-performance automobiles, valves are traditionally made from IN625 and friction-welded to a stainless-steel stem [Citation163]. Figure (c) shows a potential gradient valve stem fabricated by AM [Citation163]. The gradient from 304L SS to IN625 spans 2.5 cm in the neck, yet the entire part consists of a single austenite phase. AM shows the potential to mitigate failure in these components due to friction by eliminating abrupt transitions in the neck.
Figure 10. (a) A one-piece rocket where the body is made of low-density Ti6Al4V, but the nozzle, where the majority of the heat load is experienced, is a high-melting temperature refractory metal (Nb). Reprinted with permission from Ref. [Citation163]. (b) A schematic showing the DED fabrication of the γ-TiAl/Ti2AlNb graded alloy, potentially as a whole blisk with the Ti2AlNb as the disk and the γ-TiAl as the blades. Reprinted with permission from Ref. [Citation15]. (c) The fabrication of 304L to IN625 automotive valve stems where the valve is high-temperature IN625 and the stem is 304L stainless steel. Reprinted with permission from Ref. [Citation163]. (d) A novel porous titanium craniofacial part that had a graded porosity and density ideal for patient-specific implants [Citation164]. (e) A multimaterial object with a 3D gradient distribution of different materials within and between deposited layers. An example is the LPBF smart femoral hip stem with an embedded sensor in the printed carrier structure. (f) A multimaterial structure with a 2D gradient distribution of different materials between deposited layers. Examples include temperature sensor structures on a glass insulation layer (blue) on a stainless-steel substrate (gray). Both (e) and (f) are reprinted with permission from Ref. [Citation26].
![Figure 10. (a) A one-piece rocket where the body is made of low-density Ti6Al4V, but the nozzle, where the majority of the heat load is experienced, is a high-melting temperature refractory metal (Nb). Reprinted with permission from Ref. [Citation163]. (b) A schematic showing the DED fabrication of the γ-TiAl/Ti2AlNb graded alloy, potentially as a whole blisk with the Ti2AlNb as the disk and the γ-TiAl as the blades. Reprinted with permission from Ref. [Citation15]. (c) The fabrication of 304L to IN625 automotive valve stems where the valve is high-temperature IN625 and the stem is 304L stainless steel. Reprinted with permission from Ref. [Citation163]. (d) A novel porous titanium craniofacial part that had a graded porosity and density ideal for patient-specific implants [Citation164]. (e) A multimaterial object with a 3D gradient distribution of different materials within and between deposited layers. An example is the LPBF smart femoral hip stem with an embedded sensor in the printed carrier structure. (f) A multimaterial structure with a 2D gradient distribution of different materials between deposited layers. Examples include temperature sensor structures on a glass insulation layer (blue) on a stainless-steel substrate (gray). Both (e) and (f) are reprinted with permission from Ref. [Citation26].](/cms/asset/46ff3e02-c265-4d0f-b018-fa68da140a17/tmrl_a_2305261_f0010_oc.jpg)
The ability of AM to print any type of material leads to its increased biomedical applications such as orthopedic implants, muscle tissues, cranium, etc. These materials, however, usually require varying levels of porosity throughout the structure [Citation172]. Compared to traditional methods of fabricating foam or powder metallurgy for producing open-cell porous metals, the layer-by-layer building strategy of AM has significant design advantages [Citation24,Citation172]. An example of this is a novel porous titanium craniofacial component with graded porosity and density, making it an ideal choice for patient-specific implants (Figure (d)) [Citation164].
AM has also demonstrated the capability to integrate electronics into printed parts within the designed volume. By embedding sensors into the printing component during a pause of fabrication, AM shows a potential for full encapsulation of sensors for working in harsh environments or the human body [Citation173]. For instance, by embedding the inductor into the implants during laser beam melting fabrication, researchers were able to analyze the change of load on the implant outside the human body [Citation173]. Non-intrusive placement of sensors in the component body by AM significantly increases the life span and flexibility of sensors [Citation174]. Some electronic applications for heterostructured materials are shown in Figure (e–f), including smart femoral hip stem with the embedded sensor in the printed carrier structure [Citation173] and temperature sensor structures on a stainless-steel substrate [Citation175].
4. Challenges and future opportunities
In situ mechanical testing to fundamentally understand deformation mechanisms:
Conducting in situ SEM / TEM mechanical testing provides valuable insights such as the stress–strain distribution behavior across different regions during tensile testing, further supporting the HDI strengthening theory. More importantly, there remain numerous unexplored aspects regarding heterogeneous microstructures produced through AM. For instance, the impact of layer bands on the mechanical properties of Ti alloys and TiAl alloys needs to be assessed from the perspective of heterogeneous microstructures. Moreover, there is a significant need to investigate the heterogeneity of grains, residual stress and their contributions to the mechanical properties of additively manufactured metals. These areas represent opportunities for further research and experimentation.
Forward and inverse machine learning for heterogeneous microstructure optimization:
Machine learning offers the potential to not only predict mechanical properties based on known microstructures but also to enable inverse design, optimizing heterogeneous microstructures to achieve targeted strength and ductility. A significant challenge still lies in effectively and accurately combining various characteristics of laser additively manufactured metals with numerous facets of heterogeneity. Inversely, the microstructure that is designed by machine learning should be achievable through AM.
Combination of multiple heterogeneous microstructures:
The integration of multiple levels of heterogeneity in AM holds significant potential to enhance HDI strengthening. This approach includes altering the composition within each hatch or layer, as well as introducing variations in grain sizes throughout the fabricated part. Meanwhile, optimizing the regular change in residual stress distribution within the part can further improve the control and performance. Implementing these multifaceted approaches could result in superior performance and control in additively manufactured metals with heterogeneous microstructures.
Exploration of process window for heterogeneous microstructures:
Additive manufacturing still faces challenges in achieving fully dense parts, particularly for nickel-based superalloys or high-strength aluminum. This issue may become even more pronounced when attempting to create various heterogeneous microstructures, such as those with abrupt changes in compositions. Achieving these components without cracks necessitates a thorough investigation into the process window for such heterogeneous microstructures.
Non-beam AM processes of heterogeneous microstructures:
Non-beam AM processes, including binder jetting, materials jetting, sheet lamination, cold spray [Citation176], electrodeposition [Citation177], and additive friction stir deposition [Citation178], also offer opportunities to create materials with both chemical and microstructural heterogeneity. For example, cold spray and electrodeposition can be used to produce samples made of different materials or microstructures, which may contribute to the strength-ductility synergy. A comprehensive understanding and effective utilization of these techniques could expand the current spectrum of materials accessible for AM production.
Supplemental Material
Download MS Word (78.5 KB)Disclosure statement
No potential conflict of interest was reported by the author(s).
Correction Statement
This article has been corrected with minor changes. These changes do not impact the academic content of the article.
Additional information
Funding
References
- Zhu Y, Ameyama K, Anderson PM, et al. Heterostructured materials: superior properties from hetero-zone interaction. Mater Res Lett. 2021;9:1–31. doi:10.1080/21663831.2020.1796836
- Wu X, Zhu Y. Heterogeneous materials: a new class of materials with unprecedented mechanical properties. Mater Res Lett. 2017;5:527–532. doi:10.1080/21663831.2017.1343208
- Zhu Y, Wu X. Heterostructured materials. Prog Mater Sci. 2023;131:101019. doi:10.1016/j.pmatsci.2022.101019
- Shi P, Li R, Li Y, et al. Hierarchical crack buffering triples ductility in eutectic herringbone high-entropy alloys. Science. 2021;373:912–918. doi:10.1126/science.abf6986
- Liu Y, Xu M, Xiao L, et al. Dislocation array reflection enhances strain hardening of a dual-phase heterostructured high-entropy alloy. Mater Res Lett. 2023;11:638–647. doi:10.1080/21663831.2023.2208166
- Wu X, Yang M, Yuan F, et al. Heterogeneous lamella structure unites ultrafine-grain strength with coarse-grain ductility. Proc Natl Acad Sci USA. 2015;112:14501–14505. doi:10.1073/pnas.1517193112
- Liu Y, Cao Y, Mao Q, et al. Critical microstructures and defects in heterostructured materials and their effects on mechanical properties. Acta Mater. 2020;189:129–144. doi:10.1016/j.actamat.2020.03.001
- Zhu Y, Wu X. Perspective on hetero-deformation induced (HDI) hardening and back stress. Mater Res Lett. 2019;7:393–398.
- Ashby MF. The deformation of plastically non-homogeneous materials. Philos Mag. 1970;21:399–424. doi:10.1080/14786437008238426
- Yang M, Pan Y, Yuan F, et al. Back stress strengthening and strain hardening in gradient structure. Mater Res Lett. 2016;4:145–151. doi:10.1080/21663831.2016.1153004
- Nematollahi M, Jahadakbar A, Mahtabi MJ, et al. 12 – additive manufacturing (AM). In: Niinomi M, editor. Metals for biomedical devices (Second Edition) [Internet]. Woodhead Publishing; 2019 [cited 2023 Nov 5]. p. 331–353. Available from: https://www.sciencedirect.com/science/article/pii/B9780081026663000122.
- Liu Z, He B, Lyu T, et al. A review on additive manufacturing of titanium alloys for aerospace applications: directed energy deposition and beyond Ti-6Al-4V. JOM. 2021;73:1804–1818. doi:10.1007/s11837-021-04670-6
- Yap CY, Chua CK, Dong ZL, et al. Review of selective laser melting: materials and applications. Appl Phys Rev 2015;2:041101. doi:10.1063/1.4935926
- Dávila JL, Neto PI, Noritomi PY, et al. Hybrid manufacturing: a review of the synergy between directed energy deposition and subtractive processes. Int J Adv Manuf Technol. 2020;110:3377–3390. doi:10.1007/s00170-020-06062-7
- Chen H, Liu Z, Cheng X, et al. Laser deposition of graded γ-TiAl/Ti2AlNb alloys: microstructure and nanomechanical characterization of the transition zone. J Alloys Compd. 2021;875:159946. doi:10.1016/j.jallcom.2021.159946
- Wang YM, Voisin T, McKeown JT, et al. Additively manufactured hierarchical stainless steels with high strength and ductility. Nat Mater. 2018;17:63–71. doi:10.1038/nmat5021
- Mostafaei A, Ghiaasiaan R, Ho I-T, et al. Additive manufacturing of nickel-based superalloys: a state-of-the-art review on process-structure-defect-property relationship. Prog Mater Sci. 2023;136:101108. doi:10.1016/j.pmatsci.2023.101108
- Wang T, Tang H-B, Zhu Y-Y, et al. Laser additive manufacturing of new α+β titanium alloy with high strength and ductility. J Mater Res Technol. 2023;26:7566–7582. doi:10.1016/j.jmrt.2023.09.113
- Kürnsteiner P, Wilms MB, Weisheit A, et al. High-strength Damascus steel by additive manufacturing. Nature. 2020;582:515–519. doi:10.1038/s41586-020-2409-3
- Wei C, Li L. Recent progress and scientific challenges in multi-material additive manufacturing via laser-based powder bed fusion. Virtual Phys Prototyp. 2021;16:347–371. doi:10.1080/17452759.2021.1928520
- Todaro CJ, Easton MA, Qiu D, et al. Grain structure control during metal 3D printing by high-intensity ultrasound. Nat Commun. 2020;11:142. doi:10.1038/s41467-019-13874-z
- Karthik GM, Kim HS. Heterogeneous aspects of additive manufactured metallic parts: a review. Met Mater Int. 2021;27:1–39. doi:10.1007/s12540-020-00931-2
- Liu P, Wang Z, Xiao Y, et al. Insight into the mechanisms of columnar to equiaxed grain transition during metallic additive manufacturing. Addit Manuf. 2019;26:22–29. doi:10.1016/j.addma.2018.12.019
- Li B, Fu J, Feng J, et al. Review of heterogeneous material objects modeling in additive manufacturing. Vis Comput Ind Biomed Art. 2020;3:6. doi:10.1186/s42492-020-0041-6
- Li X, Lu L, Li J, et al. Mechanical properties and deformation mechanisms of gradient nanostructured metals and alloys. Nat Rev Mater. 2020;5:706–723. doi:10.1038/s41578-020-0212-2
- Gu D, Shi X, Poprawe R, et al. Material-structure-performance integrated laser-metal additive manufacturing. Science [Internet]. 2021 [cited 2021 May 28];372. Available from: https://science.sciencemag.org/content/372/6545/eabg1487
- Gibson I, Rosen D, Stucker B, et al. Additive manufacturing technologies [Internet]. Cham: Springer International Publishing; 2021 [cited 2023 Oct 19]. Available from: https://link.springer.com/10.1007978-3-030-56127-7.
- Zhang T, Huang Z, Yang T, et al. In situ design of advanced titanium alloy with concentration modulations by additive manufacturing. Science. 2021;374:478–482. doi:10.1126/science.abj3770
- Tan C, Liu Y, Weng F, et al. Additive manufacturing of voxelized heterostructured materials with hierarchical phases. Addit Manuf. 2022;54:102775. doi:10.1016/j.addma.2022.102775
- Xu G, Song C, Zhang H, et al. Spatially heterogeneous microstructure in in-situ TiO-reinforced Ti6Al4V/316L functionally graded material fabricated via directed energy deposition. Addit Manuf. 2022;59:103178. doi:10.1016/j.addma.2022.103178
- Yang Z, Wang S, Zhu L, et al. Manipulating molten pool dynamics during metal 3D printing by ultrasound. Appl Phys Rev. 2022;9:021416. doi:10.1063/5.0082461
- Nie MH, Zhou YX, Jiang PF, et al. Achieving illustrious friction on a directed energy deposition 316/NiTi heterogeneous alloy with bionic Ni interlayer. Appl Surf Sci. 2023;638:158107. doi:10.1016/j.apsusc.2023.158107
- Yeoh YC, Macchi G, Jain E, et al. Multiscale microstructural heterogeneity and mechanical property scatter in Inconel 718 produced by directed energy deposition. J Alloys Compd. 2021;887:161426. doi:10.1016/j.jallcom.2021.161426
- Wei C, Li L. Multi-material 3D printing based on modified LPBF. Laser Systems Europe. 2020:26–28.
- Guan S, Wan D, Solberg K, et al. Additively manufactured CrMnFeCoNi/AlCoCrFeNiTi0.5 laminated high-entropy alloy with enhanced strength-plasticity synergy. Scr Mater. 2020;183:133–138. doi:10.1016/j.scriptamat.2020.03.032
- Tan C, Chew Y, Duan R, et al. Additive manufacturing of multi-scale heterostructured high-strength steels. Mater Res Lett. 2021;9:291–299. doi:10.1080/21663831.2021.1904299
- Wei C, Chueh Y-H, Zhang X, et al. Easy-to-remove composite support material and procedure in additive manufacturing of metallic components using multiple material laser-based powder bed fusion. J Manuf Sci Eng. 2019;141:071002. doi:10.1115/1.4043536
- Wei C, Li L, Zhang X, et al. 3D printing of multiple metallic materials via modified selective laser melting. CIRP Ann. 2018;67:245–248. doi:10.1016/j.cirp.2018.04.096
- Li B, Zhang W, Shen J, et al. Micro-laminated CoCrFeMnNi−TiNp/CoCrFeMnNi high-entropy alloy matrix composite with bimodal grain structure via multi-material selective laser melting (MM-SLM) additive manufacturing. Comp Comm. 2022;36:101366. doi:10.1016/j.coco.2022.101366
- Jeong SG, Karthik GM, Kim ES, et al. Architectured heterogeneous alloys with selective laser melting. Scr Mater. 2022;208:114332. doi:10.1016/j.scriptamat.2021.114332
- Li B, Qian B, Xu Y, et al. Fine-structured CoCrFeNiMn high-entropy alloy matrix composite with 12 wt% TiN particle reinforcements via selective laser melting assisted additive manufacturing. Mater Lett. 2019;252:88–91. doi:10.1016/j.matlet.2019.05.108
- Ghanavati R, Naffakh-Moosavy H. Additive manufacturing of functionally graded metallic materials: a review of experimental and numerical studies. J Mater Res Technol. 2021;13:1628–1664.
- Loh GH, Pei E, Harrison D, et al. An overview of functionally graded additive manufacturing. Addit Manuf. 2018;23:34–44. doi:10.1016/j.addma.2018.06.023
- Fan J, Zhu L, Lu J, et al. Theory of designing the gradient microstructured metals for overcoming strength-ductility trade-off. Scr Mater. 2020;184:41–45. doi:10.1016/j.scriptamat.2020.03.045
- Loh GH, Pei E, Harrison D, et al. An overview of functionally graded additive manufacturing. Addit Manuf. 2018;23:34–44. doi:10.1016/j.addma.2018.06.023
- Oxman N. Variable property rapid prototyping: inspired by nature, where form is characterized by heterogeneous compositions, the paper presents a novel approach to layered manufacturing entitled variable property rapid prototyping. Virtual Phys Prototyp. 2011;6:3–31. doi:10.1080/17452759.2011.558588
- Li L, Wang J, Lin P, et al. Microstructure and mechanical properties of functionally graded TiCp/Ti6Al4V composite fabricated by laser melting deposition. Ceram Int. 2017;43:16638–16651. doi:10.1016/j.ceramint.2017.09.054
- Su Y, Chen B, Tan C, et al. Influence of composition gradient variation on the microstructure and mechanical properties of 316 L/Inconel718 functionally graded material fabricated by laser additive manufacturing. J Mater Process Technol. 2020;283:116702. doi:10.1016/j.jmatprotec.2020.116702
- Zhang X, Chen Y, Liou F. Fabrication of SS316L-IN625 functionally graded materials by powder-fed directed energy deposition. Sci Technol Weld Joining. 2019;24:504–516. doi:10.1080/13621718.2019.1589086
- Ma J, Zhang Y, Li J, et al. Microstructure and mechanical properties of forging-additive hybrid manufactured Ti-6Al-4V alloys. Mater Sci Eng A. 2021;811:140984. doi:10.1016/j.msea.2021.140984
- Zhu Y, Li J, Tian X, et al. Microstructure and mechanical properties of hybrid fabricated Ti-6.5Al-3.5Mo-1.5Zr-0.3Si titanium alloy by laser additive manufacturing. Mater Sci Eng A. 2014;607:427–434. doi:10.1016/j.msea.2014.04.019
- Tan C, Chew Y, Bi G, et al. Additive manufacturing of steel–copper functionally graded material with ultrahigh bonding strength. J Mater Sci Technol. 2021;72:217–222. doi:10.1016/j.jmst.2020.07.044
- Hu Z, Ma Z, Yu L, et al. Functionally graded materials with grain-size gradients and heterogeneous microstructures achieved by additive manufacturing. Scr Mater. 2023;226:115197. doi:10.1016/j.scriptamat.2022.115197
- Caiazzo F, Alfieri V, Campanelli SL, et al. Additive manufacturing and mechanical testing of functionally-graded steel strut-based lattice structures. J Manuf Process. 2022;83:717–728. doi:10.1016/j.jmapro.2022.09.031
- Trevisan F, Calignano F, Aversa A, et al. Additive manufacturing of titanium alloys in the biomedical field: processes, properties and applications. J Appl Biomater Funct Mater. 2018;16:57–67. doi:10.5301/jabfm.5000371
- Zhang M, Liu C, Shi X, et al. Residual stress, defects and grain morphology of Ti-6Al-4V alloy produced by ultrasonic impact treatment assisted selective laser melting. Appl Sci. 2016;6:304. doi:10.3390/app6110304
- Yuan D, Sun X, Sun L, et al. Improvement of the grain structure and mechanical properties of austenitic stainless steel fabricated by laser and wire additive manufacturing assisted with ultrasonic vibration. Mater Sci Eng A. 2021;813:141177. doi:10.1016/j.msea.2021.141177
- Gao S, Li Z, Van Petegem S, et al. Additive manufacturing of alloys with programmable microstructure and properties. Nat Commun. 2023;14:6752. doi:10.1038/s41467-023-42326-y
- Zou Z, Simonelli M, Katrib J, et al. Refinement of the grain structure of additive manufactured titanium alloys via epitaxial recrystallization enabled by rapid heat treatment. Scr Mater. 2020;180:66–70. doi:10.1016/j.scriptamat.2020.01.027
- Svetlizky D, Das M, Zheng B, et al. Directed energy deposition (DED) additive manufacturing: physical characteristics, defects, challenges and applications. Mater Today. 2021;49:271–295. doi:10.1016/j.mattod.2021.03.020
- Scipioni Bertoli U, Guss G, Wu S, et al. In-situ characterization of laser-powder interaction and cooling rates through high-speed imaging of powder bed fusion additive manufacturing. Mater Des. 2017;135:385–396. doi:10.1016/j.matdes.2017.09.044
- Van Cauwenbergh P, Samaee V, Thijs L, et al. Unravelling the multi-scale structure–property relationship of laser powder bed fusion processed and heat-treated AlSi10Mg. Sci Rep. 2021;11:6423. doi:10.1038/s41598-021-85047-2
- Ho A, Zhao H, Fellowes JW, et al. On the origin of microstructural banding in Ti-6Al4V wire-arc based high deposition rate additive manufacturing. Acta Mater. 2019;166:306–323. doi:10.1016/j.actamat.2018.12.038
- Liu X, Zhao C, Zhou X, et al. Microstructure of selective laser melted AlSi10Mg alloy. Mater Des. 2019;168:107677. doi:10.1016/j.matdes.2019.107677
- Liu CM, Tian XJ, Tang HB, et al. Microstructural characterization of laser melting deposited Ti–5Al-5Mo–5V–1Cr–1Fe near β titanium alloy. J Alloys Compd. 2013;572:17–24. doi:10.1016/j.jallcom.2013.03.243
- Zhu Y, Tian X, Li J, et al. Microstructure evolution and layer bands of laser melting deposition Ti–6.5Al–3.5Mo–1.5Zr–0.3Si titanium alloy. J Alloys Compd. 2014;616:468–474. doi:10.1016/j.jallcom.2014.07.161
- Thijs L, Kempen K, Kruth J-P, et al. Fine-structured aluminium products with controllable texture by selective laser melting of pre-alloyed AlSi10Mg powder. Acta Materialia [Internet]. 2013 [cited 2020 Oct 2]; Available from: http://journals.scholarsportal.info/detailsundefined
- Wu J, Wang XQ, Wang W, et al. Microstructure and strength of selectively laser melted AlSi10Mg. Acta Mater. 2016;117:311–320. doi:10.1016/j.actamat.2016.07.012
- Chen B, Moon SK, Yao X, et al. Strength and strain hardening of a selective laser melted AlSi10Mg alloy. Scr Mater. 2017;141:45–49. doi:10.1016/j.scriptamat.2017.07.025
- Liu Q, Wu H, Paul MJ, et al. Machine-learning assisted laser powder bed fusion process optimization for AlSi10Mg: new microstructure description indices and fracture mechanisms. Acta Mater. 2020;201:316–328. doi:10.1016/j.actamat.2020.10.010
- Delahaye J, Tchuindjang JT, Lecomte-Beckers J, et al. Influence of Si precipitates on fracture mechanisms of AlSi10Mg parts processed by selective laser melting. Acta Mater. 2019;175:160–170. doi:10.1016/j.actamat.2019.06.013
- Macías JGS, Douillard T, Zhao L, et al. Influence on microstructure, strength and ductility of build platform temperature during laser powder bed fusion of AlSi10Mg. Acta Mater. 2020;201:231–243. doi:10.1016/j.actamat.2020.10.001
- Paul MJ, Liu Q, Best JP, et al. Fracture resistance of AlSi10Mg fabricated by laser powder bed fusion. Acta Mater. 2021;211:116869. doi:10.1016/j.actamat.2021.116869
- Chen H, Patel S, Vlasea M, et al. Enhanced tensile ductility of an additively manufactured AlSi10Mg alloy by reducing the density of melt pool boundaries. Scr Mater. 2022;221:114954. doi:10.1016/j.scriptamat.2022.114954
- Shi S, Lin X, Wang L, et al. Investigations of the processing–structure–performance relationships of an additively manufactured AlSi10Mg alloy via directed energy deposition. J Alloys Compd. 2023;944:169050. doi:10.1016/j.jallcom.2023.169050
- Zhang H, Zhu H, Nie X, et al. Effect of Zirconium addition on crack, microstructure and mechanical behavior of selective laser melted Al-Cu-Mg alloy. Scr Mater. 2017;134:6–10. doi:10.1016/j.scriptamat.2017.02.036
- Microstructural features of Sc- and Zr-modified Al-Mg alloys processed by selective laser melting – ScienceDirect [Internet] [cited 2023 Sep 25]. Available from: https://www-sciencedirect-com.myaccess.library.utoronto.ca/science/article/pii/S0264127516314277.
- Nezhadfar PD, Thompson S, Saharan A, et al. Structural integrity of additively manufactured aluminum alloys: effects of build orientation on microstructure, porosity, and fatigue behavior. Addit Manuf. 2021;47:102292. doi:10.1016/j.addma.2021.102292
- Shakil SI, González-Rovira L, Cabrera-Correa L, et al. Insights into laser powder bed fused Scalmalloy®: investigating the correlation between micromechanical and macroscale properties. J Mater Res Technol. 2023;25:4409–4424. doi:10.1016/j.jmrt.2023.06.228
- Kuo CN, Peng PC, Liu DH, et al. Microstructure evolution and mechanical property response of 3D-printed Scalmalloy with different heat-treatment times at 325°C. Metals (Basel). 2021;11:555. doi:10.3390/met11040555
- Cabrera-Correa L, González-Rovira L, de Dios López-Castro J, et al. Effect of the heat treatment on the mechanical properties and microstructure of Scalmalloy® manufactured by Selective Laser Melting (SLM) under certified conditions. Mater Charact. 2023;196:112549. doi:10.1016/j.matchar.2022.112549
- Awd M, Tenkamp J, Hirtler M, et al. Comparison of microstructure and mechanical properties of Scalmalloy® produced by selective laser melting and laser metal deposition. Materials (Basel). 2018;11:17. doi:10.3390/ma11010017
- Wang Z, Lin X, Kang N, et al. Strength-ductility synergy of selective laser melted Al-Mg-Sc-Zr alloy with a heterogeneous grain structure. Addit Manuf. 2020;34:101260. doi:10.1016/j.addma.2020.101260
- Spierings AB, Dawson K, Dumitraschkewitz P, et al. Microstructure characterization of SLM-processed Al-Mg-Sc-Zr alloy in the heat treated and HIPed condition. Addit Manuf. 2018;20:173–181. doi:10.1016/j.addma.2017.12.011
- Yang KV, Shi Y, Palm F, et al. Columnar to equiaxed transition in Al-Mg(-Sc)-Zr alloys produced by selective laser melting. Scr Mater. 2018;145:113–117. doi:10.1016/j.scriptamat.2017.10.021
- Wang Z, Lin X, Kang N, et al. Directed energy deposition additive manufacturing of a Sc/Zr-modified Al–Mg alloy: effect of thermal history on microstructural evolution and mechanical properties. Mater Sci Eng A. 2021;802:140606. doi:10.1016/j.msea.2020.140606
- Wang D, Feng Y, Liu L, et al. Influence mechanism of process parameters on relative density, microstructure, and mechanical properties of low Sc-content Al-Mg-Sc-Zr alloy fabricated by selective laser melting. Chin J Mech Eng Addit Manuf Front. 2022;1:100034. doi:10.1016/j.cjmeam.2022.100034
- Wang Z, Lin X, Kang N, et al. Laser powder bed fusion of high-strength Sc/Zr-modified Al–Mg alloy: phase selection, microstructural/mechanical heterogeneity, and tensile deformation behavior. J Mater Sci Technol. 2021;95:40–56. doi:10.1016/j.jmst.2021.03.069
- Spierings AB, Dawson K, Uggowitzer PJ, et al. Influence of SLM scan-speed on microstructure, precipitation of Al3Sc particles and mechanical properties in Sc- and Zr-modified Al-Mg alloys. Mater Des. 2018;140:134–143. doi:10.1016/j.matdes.2017.11.053
- Wang Z, Lin X, Wang J, et al. Remarkable strength-impact toughness conflict in high-strength Al-Mg-Sc-Zr alloy fabricated via laser powder bed fusion additive manufacturing. Addit Manuf. 2022;59:103093. doi:10.1016/j.addma.2022.103093
- Jia Q, Rometsch P, Cao S, et al. Towards a high strength aluminium alloy development methodology for selective laser melting. Mater Des. 2019;174:107775. doi:10.1016/j.matdes.2019.107775
- Jia Q, Rometsch P, Kürnsteiner P, et al. Selective laser melting of a high strength Al Mn Sc alloy: alloy design and strengthening mechanisms. Acta Mater. 2019;171:108–118. doi:10.1016/j.actamat.2019.04.014
- Montero-Sistiaga ML, Mertens R, Vrancken B, et al. Changing the alloy composition of Al7075 for better processability by selective laser melting. J Mater Process Technol. 2016;238:437–445. doi:10.1016/j.jmatprotec.2016.08.003
- Sun J, Gao L, Liu Q, et al. Novel isotropic mechanical properties of laser powder-bed fusion Sc/Zr modified Al alloy. Mater Sci Eng A. 2023;872:145003. doi:10.1016/j.msea.2023.145003
- Croteau JR, Griffiths S, Rossell MD, et al. Microstructure and mechanical properties of Al-Mg-Zr alloys processed by selective laser melting. Acta Mater. 2018;153:35–44. doi:10.1016/j.actamat.2018.04.053
- Mehta A, Zhou L, Huynh T, et al. Additive manufacturing and mechanical properties of the dense and crack free Zr-modified aluminum alloy 6061 fabricated by the laser-powder bed fusion. Addit Manuf. 2021;41:101966. doi:10.1016/j.addma.2021.101966
- Wang Y, Li R, Yuan T, et al. Microstructure and mechanical properties of Al-Fe-Sc-Zr alloy additively manufactured by selective laser melting. Mater Charact. 2021;180:111397. doi:10.1016/j.matchar.2021.111397
- Yang Z, Chen C, Li D, et al. An additively manufactured heat-resistant Al-Ce-Sc-Zr alloy: microstructure, mechanical properties and thermal stability. Mater Sci Eng A. 2023;872:144965. doi:10.1016/j.msea.2023.144965
- Zhou L, Hyer H, Park S, et al. Microstructure and mechanical properties of Zr-modified aluminum alloy 5083 manufactured by laser powder bed fusion. Addit Manuf. 2019;28:485–496. doi:10.1016/j.addma.2019.05.027
- Yang W, Jung Y-G, Kwak T, et al. Microstructure and mechanical properties of an Al–Mg–Si–Zr alloy processed by L-PBF and subsequent heat treatments. Materials (Basel). 2022;15:5089. doi:10.3390/ma15155089
- Li R, Wang M, Li Z, et al. Developing a high-strength Al-Mg-Si-Sc-Zr alloy for selective laser melting: crack-inhibiting and multiple strengthening mechanisms. Acta Mater. 2020;193:83–98. doi:10.1016/j.actamat.2020.03.060
- Zhu Z, Ng FL, Seet HL, et al. Superior mechanical properties of a selective-laser-melted AlZnMgCuScZr alloy enabled by a tunable hierarchical microstructure and dual-nanoprecipitation. Mater Today. 2022;52:90–101. doi:10.1016/j.mattod.2021.11.019
- Zhang H, Zhu H, Nie X, et al. Effect of Zirconium addition on crack, microstructure and mechanical behavior of selective laser melted Al-Cu-Mg alloy. Scr Mater. 2017;134:6–10. doi:10.1016/j.scriptamat.2017.02.036
- Zhou L, Pan H, Hyer H, et al. Microstructure and tensile property of a novel AlZnMgScZr alloy additively manufactured by gas atomization and laser powder bed fusion. Scr Mater. 2019;158:24–28. doi:10.1016/j.scriptamat.2018.08.025
- Aboulkhair NT, Maskery I, Tuck C, et al. The microstructure and mechanical properties of selectively laser melted AlSi10Mg: the effect of a conventional T6-like heat treatment. Mater Sci Eng A. 2016;667:139–146. doi:10.1016/j.msea.2016.04.092
- Hadadzadeh A, Amirkhiz BS, Mohammadi M. Contribution of Mg2Si precipitates to the strength of direct metal laser sintered AlSi10Mg. Mater Sci Eng A. 2019;739:295–300. doi:10.1016/j.msea.2018.10.055
- Li W, Li S, Liu J, et al. Effect of heat treatment on AlSi10Mg alloy fabricated by selective laser melting: microstructure evolution, mechanical properties and fracture mechanism. Mater Sci Eng A. 2016;663:116–125. doi:10.1016/j.msea.2016.03.088
- Wei P, Wei Z, Chen Z, et al. The AlSi10Mg samples produced by selective laser melting: single track, densification, microstructure and mechanical behavior. Appl Surf Sci. 2017;408:38–50. doi:10.1016/j.apsusc.2017.02.215
- Hadadzadeh A, Baxter C, Amirkhiz BS, et al. Strengthening mechanisms in direct metal laser sintered AlSi10Mg: comparison between virgin and recycled powders. Addit Manuf. 2018;23:108–120. doi:10.1016/j.addma.2018.07.014
- Kempen K, Thijs L, Humbeeck JV, et al. Processing AlSi10Mg by selective laser melting: parameter optimisation and material characterisation. Mater Sci Technol. 2015;31:917–923. doi:10.1179/1743284714Y.0000000702
- EOS Aluminium AlSi10Mg Material Data Sheet. EOS.
- Aluminium die casting alloys: alloy composition, microstructure, and properties-performance relationships [Internet]. [cited 2023 Sep 25]. Available from: https://www.tandfonline.com/doi/epdf/10.1179imr.1995.40.6.221?needAccess=true.
- Filatov Y, Yelagin VI, Zakharov VV. New Al–Mg–Sc alloys. Mater Sci Eng A. 2000;280:97–101. doi:10.1016/S0921-5093(99)00673-5
- Polmear I, StJohn D, Nie J-F, et al. 4 – wrought aluminium alloys. In: Polmear I, StJohn D, Nie J-F, et al., editors. Light alloys (Fifth Edition) [Internet]. Boston: Butterworth-Heinemann; 2017 [cited 2023 Sep 25]. p. 157–263. Available from: https://www.sciencedirect.com/science/article/pii/B978008099431400004X.
- Parimi LL, Ravi G, Clark D, et al. Microstructural and texture development in direct laser fabricated IN718. Mater Charact. 2014;89:102–111. doi:10.1016/j.matchar.2013.12.012
- Huang W, Lin X. Research progress in laser solid forming of high-performance metallic components at the state key laboratory of solidification processing of China. 3D Print Addit Manuf. 2014;1:156–165. doi:10.1089/3dp.2014.0016
- Blackwell PL. The mechanical and microstructural characteristics of laser-deposited IN718. J Mater Process Technol. 2005;170:240–246. doi:10.1016/j.jmatprotec.2005.05.005
- Yeoh YC, Macchi G, Jain E, et al. Multiscale microstructural heterogeneity and mechanical property scatter in Inconel 718 produced by directed energy deposition. J Alloys Compd. 2021;887:161426. doi:10.1016/j.jallcom.2021.161426
- Xu L, Chai Z, Zhang X, et al. A new approach to improve strength and ductility of laser powder deposited Inconel 718 thin-wall structure. Mater Sci Eng A. 2022;855:143871. doi:10.1016/j.msea.2022.143871
- Bhattacharya S, Dinda GP, Dasgupta AK, et al. A comparative study of microstructure and mechanical behavior of CO2 and diode laser deposited Cu–38Ni alloy. J Mater Sci. 2014;49:2415–2429. doi:10.1007/s10853-013-7883-7
- He B, Li J, Cheng X, et al. Brittle fracture behavior of a laser additive manufactured near-β titanium alloy after low temperature aging. Mater Sci Eng A. 2017;699:229–238. doi:10.1016/j.msea.2017.05.050
- Zhu Y, Liu D, Tian X, et al. Characterization of microstructure and mechanical properties of laser melting deposited Ti–6.5Al–3.5Mo–1.5Zr–0.3Si titanium alloy. Mater Des. 2014;56:445–453. doi:10.1016/j.matdes.2013.11.044
- Wang T, Zhu YY, Zhang SQ, et al. Grain morphology evolution behavior of titanium alloy components during laser melting deposition additive manufacturing. J Alloys Compd. 2015;632:505–513. doi:10.1016/j.jallcom.2015.01.256
- Zhang Q, Chen J, Lin X, et al. Grain morphology control and texture characterization of laser solid formed Ti6Al2Sn2Zr3Mo1.5Cr2Nb titanium alloy. J Mater Process Technol. 2016;238:202–211. doi:10.1016/j.jmatprotec.2016.07.011
- Qiu C, Ravi GA, Attallah MM. Microstructural control during direct laser deposition of a β-titanium alloy. Mater Des. 2015;81:21–30. doi:10.1016/j.matdes.2015.05.031
- Qi M, Huang S, Ma Y, et al. Columnar to equiaxed transition during β heat treatment in a near β alloy by laser additive manufacture. J Mater Res Technol. 2021;13:1159–1168. doi:10.1016/j.jmrt.2021.05.057
- Zhu Y-Y, Tang H-B, Li Z, et al. Solidification behavior and grain morphology of laser additive manufacturing titanium alloys. J Alloys Compd. 2019;777:712–716. doi:10.1016/j.jallcom.2018.11.055
- Zhu Y, Chen B, Tang H, et al. Influence of heat treatments on microstructure and mechanical properties of laser additive manufacturing Ti-5Al-2Sn-2Zr-4Mo-4Cr titanium alloy. Trans Nonferrous Met Soc China. 2018;28:36–46. doi:10.1016/S1003-6326(18)64636-9
- Deng H, Chen L, Qiu W, et al. Microstructure and mechanical properties of as-deposited and heat treated Ti–5Al–5Mo–5V–3Cr–1Zr (Ti-55531) alloy fabricated by laser melting deposition. J Alloys Compd. 2019;810:151792. doi:10.1016/j.jallcom.2019.151792
- Sun S-H, Hagihara K, Nakano T. Effect of scanning strategy on texture formation in Ni-25 at.% Mo alloys fabricated by selective laser melting. Mater Des. 2018;140:307–316. doi:10.1016/j.matdes.2017.11.060
- Wan HY, Zhou ZJ, Li CP, et al. Effect of scanning strategy on mechanical properties of selective laser melted Inconel 718. Mater Sci Eng A. 2019;753:42–48. doi:10.1016/j.msea.2019.03.007
- Choi J-P, Shin G-H, Yang S, et al. Densification and microstructural investigation of Inconel 718 parts fabricated by selective laser melting. Powder Technol. 2017;310:60–66. doi:10.1016/j.powtec.2017.01.030
- Carter LN, Martin C, Withers PJ, et al. The influence of the laser scan strategy on grain structure and cracking behaviour in SLM powder-bed fabricated nickel superalloy. J Alloys Compd. 2014;615:338–347. doi:10.1016/j.jallcom.2014.06.172
- Alabort E, Tang YT, Barba D, et al. Alloys-by-design: a low-modulus titanium alloy for additively manufactured biomedical implants. Acta Mater. 2022;229:117749. doi:10.1016/j.actamat.2022.117749
- Leicht A, Yu CH, Luzin V, et al. Effect of scan rotation on the microstructure development and mechanical properties of 316L parts produced by laser powder bed fusion. Mater Charact. 2020;163:110309. doi:10.1016/j.matchar.2020.110309
- Montero-Sistiaga ML, Godino-Martinez M, Boschmans K, et al. Microstructure evolution of 316L produced by HP-SLM (high power selective laser melting). Addit Manuf. 2018;23:402–410. doi:10.1016/j.addma.2018.08.028
- Sun S-H, Ishimoto T, Hagihara K, et al. Excellent mechanical and corrosion properties of austenitic stainless steel with a unique crystallographic lamellar microstructure via selective laser melting. Scr Mater. 2019;159:89–93. doi:10.1016/j.scriptamat.2018.09.017
- Saeidi K, Kevetkova L, Lofaj F, et al. Novel ferritic stainless steel formed by laser melting from duplex stainless steel powder with advanced mechanical properties and high ductility. Mater Sci Eng A. 2016;665:59–65. doi:10.1016/j.msea.2016.04.027
- Sofinowski KA, Raman S, Wang X, et al. Layer-wise engineering of grain orientation (LEGO) in laser powder bed fusion of stainless steel 316L. Addit Manuf. 2021;38:101809. doi:10.1016/j.addma.2020.101809
- Xue A, Lin X, Wang L, et al. Influence of trace boron addition on microstructure, tensile properties and their anisotropy of Ti6Al4V fabricated by laser directed energy deposition. Mater Des. 2019;181:107943. doi:10.1016/j.matdes.2019.107943
- Barriobero-Vila P, Gussone J, Stark A, et al. Peritectic titanium alloys for 3D printing. Nat Commun. 2018;9:3426. doi:10.1038/s41467-018-05819-9
- AlMangour B, Grzesiak D, Yang J-M. Scanning strategies for texture and anisotropy tailoring during selective laser melting of TiC/316L stainless steel nanocomposites. J Alloys Compd. 2017;728:424–435. doi:10.1016/j.jallcom.2017.08.022
- Zhang Q, Chen J, Zhao Z, et al. Microstructure and anisotropic tensile behavior of laser additive manufactured TC21 titanium alloy. Mater Sci Eng A. 2016;673:204–212. doi:10.1016/j.msea.2016.07.040
- Amirabdollahian S, Deirmina F, Harris L, et al. Towards controlling intrinsic heat treatment of maraging steel during laser directed energy deposition. Scr Mater. 2021;201:113973. doi:10.1016/j.scriptamat.2021.113973
- Kürnsteiner P, Wilms MB, Weisheit A, et al. Massive nanoprecipitation in an Fe-19Ni-xAl maraging steel triggered by the intrinsic heat treatment during laser metal deposition. Acta Mater. 2017;129:52–60. doi:10.1016/j.actamat.2017.02.069
- Liu Z, Qin Z-X, Liu F, et al. The microstructure and mechanical behaviors of the Ti–6.5Al–3.5Mo–1.5Zr–0.3Si alloy produced by laser melting deposition. Mater Charact. 2014;97:132–139. doi:10.1016/j.matchar.2014.09.002
- Li S, Yang J, Wang Z. Multi-laser powder bed fusion of Ti-6.5Al-2Zr-Mo-V alloy powder: defect formation mechanism and microstructural evolution. Powder Technol. 2021;384:100–111. doi:10.1016/j.powtec.2021.02.010
- Szost BA, Terzi S, Martina F, et al. A comparative study of additive manufacturing techniques: residual stress and microstructural analysis of CLAD and WAAM printed Ti–6Al–4V components. Mater Des. 2016;89:559–567. doi:10.1016/j.matdes.2015.09.115
- Kelly SM, Kampe SL. Microstructural evolution in laser-deposited multilayer Ti-6Al-4V builds: part I. Microstructural characterization. Metall Mater Trans A. 2004;35:1861–1867. doi:10.1007/s11661-004-0094-8
- Carroll BE, Palmer TA, Beese AM. Anisotropic tensile behavior of Ti–6Al–4V components fabricated with directed energy deposition additive manufacturing. Acta Mater. 2015;87:309–320. doi:10.1016/j.actamat.2014.12.054
- Nassar AR, Reutzel EW. Additive manufacturing of Ti-6Al-4V using a pulsed laser beam. Metall Mater Trans A. 2015;46:2781–2789. doi:10.1007/s11661-015-2838-z
- Zhai Y, Lados DA, Brown EJ, et al. Understanding the microstructure and mechanical properties of Ti-6Al-4V and Inconel 718 alloys manufactured by laser engineered net shaping. Addit Manuf. 2019;27:334–344. doi:10.1016/j.addma.2019.02.017
- Neikter M, Åkerfeldt P, Pederson R, et al. Microstructural characterization and comparison of Ti-6Al-4V manufactured with different additive manufacturing processes. Mater Charact. 2018;143:68–75. doi:10.1016/j.matchar.2018.02.003
- Chen J, Fabijanic D, Zhang T, et al. Deciphering the transformation pathway in laser powder-bed fusion additive manufacturing of Ti-6Al-4V alloy. Addit Manuf. 2022;58:103041. doi:10.1016/j.addma.2022.103041
- Zhu Z, Liu T, Dong C, et al. Achieving high-temperature strength and plasticity in near-α Ti-7Al-3Zr-2V alloy using cluster formula design. J Mater Res Technol. 2022;18:2582–2592. doi:10.1016/j.jmrt.2022.03.158
- Wang J, Luo Q, Wang H, et al. Microstructure characteristics and failure mechanisms of Ti-48Al-2Nb-2Cr titanium aluminide intermetallic alloy fabricated by directed energy deposition technique. Addit Manuf. 2020;32:101007. doi:10.1016/j.addma.2019.101007
- Wu Y, Zhang S, Cheng X, et al. Investigation on solid-state phase transformation in a Ti-47Al-2Cr-2V alloy due to thermal cycling during laser additive manufacturing process. J Alloys Compd. 2019;799:325–333. doi:10.1016/j.jallcom.2019.05.337
- Ouyang D, Zhang P, Zhang C, et al. High-strength lamellar high-entropy alloys in-situ synthesized by laser additive manufacturing. Mater Sci Eng A. 2023;867:144745. doi:10.1016/j.msea.2023.144745
- Yvinec T, Naït-Ali A, Mellier D, et al. Tensile properties of Ti-6Al-4V as-built by laser metal deposition: the relationship between heat affected zone bands, strain localization and anisotropy in ductility. Addit Manuf. 2022;55:102830. doi:10.1016/j.addma.2022.102830
- Lee J-R, Lee M-S, Yeon SM, et al. Unravelling anisotropic deformation behaviour of Ti-6Al-4V ELI fabricated by powder bed fusion additive manufacturing. Mater Charact. 2023;202:113017. doi:10.1016/j.matchar.2023.113017
- Foehring D, Chew HB, Lambros J. Characterizing the tensile behavior of additively manufactured Ti-6Al-4V using multiscale digital image correlation. Mater Sci Eng A. 2018;724:536–546. doi:10.1016/j.msea.2018.03.091
- Ty A, Balcaen Y, Mokhtari M, et al. Influence of deposit and process parameters on microstructure and mechanical properties of Ti6Al4V obtained by DED-W (PAW). J Mater Res Technol. 2022;18:2853–2869. doi:10.1016/j.jmrt.2022.03.169
- Hofmann DC, Kolodziejska J, Roberts S, et al. Compositionally graded metals: a new frontier of additive manufacturing. J Mater Res. 2014;29:1899–1910. doi:10.1557/jmr.2014.208
- Li Y, Feng Z, Hao L, et al. A review on functionally graded materials and structures via additive manufacturing: from multi-scale design to versatile functional properties. Adv Mater Technol. 2020;5:1900981. doi:10.1002/admt.201900981
- Nazir A, Gokcekaya O, Md Masum Billah K, et al. Multi-material additive manufacturing: a systematic review of design, properties, applications, challenges, and 3D printing of materials and cellular metamaterials. Mater Des. 2023;226:111661. doi:10.1016/j.matdes.2023.111661
- Multi-material metal parts by Powder Bed Fusion [Internet]. Metal AM magazine. 2022 [cited 2023 Oct 21]. Available from: https://www.metal-am.com/articles/multi-material-metal-parts-by-powder-bed-fusion-new-application-opportunities/.
- Meyer I, Oel M, Ehlers T, et al. Additive manufacturing of multi-material parts – design guidelines for manufacturing of 316L/CuCrZr in laser powder bed fusion. Heliyon. 2023;9:e18301. doi:10.1016/j.heliyon.2023.e18301
- Liu S, Shin YC. Additive manufacturing of Ti6Al4V alloy: a review. Mater Des. 2019;164:107552. doi:10.1016/j.matdes.2018.107552
- Singh P, Pungotra H, Kalsi NS. On the characteristics of titanium alloys for the aircraft applications. Mater Today Proc. 2017;4:8971–8982. doi:10.1016/j.matpr.2017.07.249
- Wang J, East D, Morozov EV, et al. Microstructure and hardness variation of additively manufactured Ti–Ni–C functionally graded composites. J Alloys Compd. 2021;865:158976. doi:10.1016/j.jallcom.2021.158976
- Han J, Lu L, Xin Y, et al. Microstructure and mechanical properties of a novel functionally graded material from Ti6Al4V to Inconel 625 fabricated by dual wire + arc additive manufacturing. J Alloys Compd. 2022;903:163981. doi:10.1016/j.jallcom.2022.163981
- Wang X, Xu S, Zhou S, et al. Topological design and additive manufacturing of porous metals for bone scaffolds and orthopaedic implants: a review. Biomaterials. 2016;83:127–141. doi:10.1016/j.biomaterials.2016.01.012
- Töppel T, Lausch H, Brand M, et al. Structural integration of sensors/actuators by laser beam melting for tailored smart components. JOM. 2018;70:321–327. doi:10.1007/s11837-017-2725-8
- Hossain MS, Gonzalez JA, Hernandez RM, et al. Fabrication of smart parts using powder bed fusion additive manufacturing technology. Addit Manuf. 2016;10:58–66. doi:10.1016/j.addma.2016.01.001
- Laser-based functionalization of electronic multi-material-layers for embedded sensors | Journal of Laser Applications | AIP Publishing [Internet]. [cited 2023 Oct 21]. Available from: https://pubs.aip.org/lia/jla/article-abstract/29/2/022603/96892/Laser-based-functionalization-of-electronic-multi.
- Zou Y. Cold spray additive manufacturing: microstructure evolution and bonding features. Acc Mater Res. 2021;2:1071–1081. doi:10.1021/accountsmr.1c00138
- Haché MJR, Tam J, Erb U, et al. Electrodeposited nanocrystalline medium-entropy alloys – an effective strategy of producing stronger and more stable nanomaterials. J Alloys Compd. 2022;899:163233. doi:10.1016/j.jallcom.2021.163233
- Yu HZ, Jones ME, Brady GW, et al. Non-beam-based metal additive manufacturing enabled by additive friction stir deposition. Scr Mater. 2018;153:122–130. doi:10.1016/j.scriptamat.2018.03.025