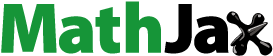
Abstract
Strength and electrical conductivity (EC) are key properties for heat-resistant Al-Zr-based alloy wires used as overhead transmission lines. Developing high-strength conductors with EC over 61.0% IACS has been a long-standing issue for heat-resistant Al conductive wires. In this work, a new design idea involving the coupling design of deformation and ageing was innovatively proposed to produce ultra-heat-resistant Al-0.2Zr-0.06Sc wires. The desired combination of high strength (195 ± 2 MPa) and good EC (61.2% IACS) was successfully achieved without annealing treatment. The strength residual rate of cold-drawn Al-0.2Zr-0.06Sc wire is as high as 94.0% after heat exposure of 280°C/1 h.
1. Introduction
Today, with the rise of service temperature of Al cables due to the ever-increasing demand in the electric power transmission, the usage of good heat-resistant Al-Zr alloy cables has significantly increased. Al-Zr-based alloys are dominant materials for overhead transmission lines due to their advantages of high specific strength and electrical conductivity (EC), which are closely related to service safety and energy-saving, respectively [Citation1–3]. It is an urgent challenge to develop a new generation of Al-Zr-based wires with high strength (over 160 MPa), high EC (over 61.0% IACS, International annealed copper standard, 100% IACS = 58 MS/m) and good heat resistance in the electrical conductor industries.
A significant amount of studies have been conducted in order to improve strength and EC for Al-Zr-based conductive wires synchronously, and adding alloy element Sc catches more attention [Citation4–8]. Adjusting alloying contents and/or optimizing preparation processes can improve the strength and EC of Al-Zr-Sc alloys effectively. Unfortunately, almost all Al-Zr-based conductive wires produced by cold drawing exhibit high strength and low EC (less than 60.0%IACS) due to the fact that the high-density dislocations introduced by deformation bring significant dislocation strengthening at the expense of scattering electrons, and thereby damaging the EC severely. Cold drawing followed by annealing treatment has always been used to improve the EC, but the trade-off between strength and EC is hard to break, due to the sacrificed strength. As reported by Liu et al. [Citation9], the cold-drawn Al-0.23Zr-0.06Sc wire (1.5 mm in diameter) exhibits a very low EC of 57.6% IACS, though a high strength of 199 MPa is achieved. After annealing at 400°C for 5 h, the EC of the Al-0.23Zr-0.06Sc wire increases from 57.6 to 59.7% IACS but the strength decreases from 199 to 192 MPa. Guan et al. [Citation10] reported that by greatly improving Sc content, high strength of 210 MPa and 60.2% IACS are obtained in the cold-drawn Al-0.2Zr-0.35Sc wire of 3.0 mm diameter. However, on the one hand, increasing Sc content raises cost significantly. On the other hand, the requirement of good EC (≥61.0% IACS) for urgent conductors cannot be satisfied without annealing.
It is reported that Al-Zr-Sc alloy with the addition of Er element can further improve the strength and EC. The addition of Er element promotes the precipitation of Zr-rich phases and the formation of Al3Er and Al3(Er,Sc,Zr) nano-scale precipitates [Citation11–13]. However, the addition of Er element cannot resolve the disproportionate matching between strength and EC, and annealing treatment is still needed. Additionally, the addition of Sc elements should be controlled below 0.1%, considering the production cost. In this case, the well-combined properties are harder to achieve by traditional processing methods. The aim of this study is to provide a novel processing path for heat-resistant Al conductive wires based on the dilute Al-Zr-Sc system, to achieve the desired combination of high strength (≥160 MPa) and good EC (≥61.0% IACS) without annealing treatment.
Here we provide an effective approach via the process of continue casting direct rolling (CCDR) → ageing treatment → cold drawing, and the Al-0.2Zr-0.06Sc wire with a diameter of 4.0 mm (total length: 18.3 km) was successfully produced. By such a simple production process, high-quality Al-0.2Zr-0.06Sc wire with high strength (195 ± 2 MPa) and good EC (61.2% IACS) could be directly produced. This approach simplifies the production process and keeps costs within an acceptable level. Furthermore, the microstructure evolution of Al-0.2Zr-0.06Sc wires during the processing path was characterized by electron backscatter diffraction (EBSD) and scanning transmission electron microscope (STEM). The mechanisms of the combination of high strength and good EC were quantitatively revealed. Consequently, our findings contribute a novel approach for developing heat-resistant Al-Zr-based conductive wires strengthened by precipitation and dislocation strengthening for potential applications in overhead transmission lines.
2 Materials and methods
The raw materials for casting consisted of electrolytic aluminium melt (Al: 99.9 wt.%), Al-5Zr and Al-2Sc master alloys. Firstly, the electrolytic aluminium melt, Al-5Zr and Al-2Sc master alloys were melted in a medium-frequency induction furnace at 750–780°C and subsequently poured into the crystallization wheel. Then the ingot was transferred to the continuous rolling mill via the crystallization wheel. The rolling parameters are as follows: rolling-in temperature is 400∼420°C; rolling-out temperature is 250∼280°C; flow rate of cooling water is 14 L/min; rods are rewound at a speed of 8–9 m/s. Finally, the ingot was produced to Al rods (total weight: ∼800 kg) with a diameter of 9.5 mm by CCDR for 12 passes. The Al rods were aged at 250°C for 24 h, subsequently two-stage ageing at 395°C for 48, 120 and 168 h, respectively, which are denoted by aged/48h-rod, aged/120h-rod and aged/168h-rod. The rods were further deformed into wires by cold drawing to reach a diameter of 4.0 mm after 7 passes processing. Correspondingly, these wires are defined as aged/48h-wire, aged/120h-wire and aged/168h-wire, respectively. The chemical composition (wt.%) of the cold-drawn Al wire is Zr ∼0.1963, Sc ∼0.0599, Fe ∼0.0993, Si ∼0.0465 and Al bal., which were measured by the inductively coupled plasma-optical emission spectrometer technique (ICP-OES, Horiba Ultima Expert, Japan).
The STEM observations were conducted on the Talos F200X equipment under an acceleration voltage of 200 kV equipped with Energy Dispersive spectrometry (EDS, Super-X G2 EDS detector). The TEM foils were first mechanically polished to 60 μm thick and then double jet thinned using an electrolyte of 10% perchloric acid and 90% alcohol with 15 V at about −25℃. Then, the foils were cleaned by ion-milling with an angle of 2° at 3 kV for 10 mins. The EBSD samples were electropolished in 90% ethanol and 10% perchloric at 13 V for 25 s. The EBSD observations were conducted on the field emission scanning electron microscope (FE-SEM, FEI Nova Nano SEM 450) equipped with the EBSD detector (EDAX Hikari Plus).
The measured resistance value can be adjusted to the standard one (at 20℃) using the following equation:
(1)
(1) where R20 and RT are the resistance value at 20℃ and testing temperature (℃), respectively, and α is the temperature coefficient of resistance:
(2)
(2)
(3)
(3) where K20 is the EC (in %IACS), ρ20 is resistance rate, Ω mm2/m, S is the cross-sectional area, mm2, and L is the length of 1 m.
3 Results and discussion
Figure shows the STEM results of Al-0.2Zr-0.06Sc alloys observed from the axial sections taken along [101] crystal direction. After CCDR processing, the microstructure of the Al-0.2Zr-0.06Sc alloy rod consists of grains elongated along rolling direction and fine recrystallized grains, as shown in Figure (a1). Only diffraction spots of Al matrix were characterized from the selected area electron diffraction (SAED) pattern, which demonstrates that Zr and Sc atoms are well dissolved in the Al matrix. From Figure (b1–d1), many Al-Fe-Si phases distributed on the grain boundaries (GBs) because the impurity elements (Fe, Si) are difficult to be completely eliminated during the production process. After long-term ageing, grains are coarsened and the deformed features become blurry, as shown in Figure (a2). A large number of white spherical precipitates with a mean diameter of ∼6.23 ± 1.52 nm are clearly observed (Figure (b2)), which are proven to be Al3(Zr, Sc) particles by the fast-fourier-transform (FFT) image (Figure (d2)). Figure (a3) shows that grains are significantly elongated along the drawing direction and massive dislocations are introduced after cold drawing. From Figure (b3) and (d3), the type and size of the precipitates are almost un-changed after cold drawing. Based on the EDS mapping results, the Al3(Zr,Sc) precipitate shows a core–shell structure approximately (Figure (a4–d4)).
Figure 1. STEM results of Al-0.2Zr-0.06Sc alloys produced by different processes: (a1–a3) Bright-field micrographs; (b1–d1) Al-Fe-Si impurity phase and EDS mapping of Fe and Si elements; (b2 and b3) Dark-field micrographs and their corresponding particle size distribution in (c2 and c3); (d2, d3) High-resolution transmission electron microscope (HRTEM) micrographs and their corresponding FFT images; (a4–d4) High-angle annular dark field (HAADF) micrograph of Al3(Zr,Sc) precipitates and EDS mapping. Among them, (a2–d2) rods are aged at 250°C/24 h + 395°C/168 h.
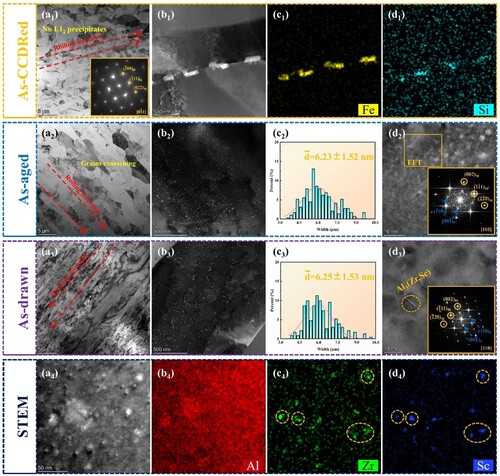
Figure shows the EBSD results of Al-0.2Zr-0.06Sc alloys observed by radial and axial sections. Most of the radial grains after CCDR processing exhibit <111> orientation, but <001> orientation is also found in some grains (Figure (a1)). After ageing, the grain structure is coarsened together with the decreased proportion of <111> oriented grains and increased proportion of <001> and <101> oriented grains (Figure (a2)). It is indicated from Figure (a3) that <111> orientation is dominate with a few <001> orientation after cold drawing. In Figure (c1–c3), the axial grains are finer and longer, but fine recrystallized grains increase the fraction of GBs.
Figure 2. The orientation distribution maps of Al-0.2Zr-0.06Sc alloys: (a1–c1) as-CCDRed sample; (a2–c2) as-aged sample at 250°C/24 h + 395°C/168 h; (a3–c3) as-drawn sample; (a1–a3) radial direction; (b1–b3) grain size distributions; (c1–c3) axial direction. (d) Schematic diagram of sample observation; (e) Statistical results corresponding to the grain lengths and widths. DD: Deformation direction; RD: Rolling direction.
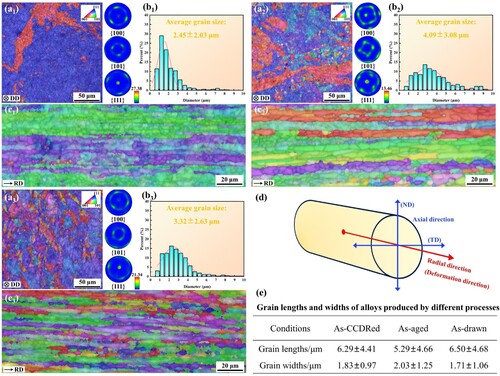
Furthermore, the quantitative statistical results of grain structure were conducted and presented in Figure (b1–b3) and (e). The average radial grain size of as-CCDRed alloy is ∼2.45 ± 2.03 μm, which grows to ∼4.09 ± 3.08 μm after ageing treatment and refines to ∼3.32 ± 2.63 μm after cold drawing. The axial grain length decreases from 6.29 ± 4.41 to 5.29 ± 4.66 μm after ageing and then increases to 6.50 ± 4.68 μm after cold drawing. The above results indicate that grains are coarsened during ageing, but elongated again after cold drawing.
Figure shows the strengths and EC of heat-resistant Al alloys prepared by different processes, and the ultimate tensile strength (UTS) and EC of Al-0.2Zr-0.06Sc alloy wires are compared with other heat-resistant Al conductors. During long-term ageing, the UTS of rods decreases slightly with the increase in the ageing time. After cold drawing, the strengths are improved and EC is reduced, which are related to the grain refinement and the increased dislocation density. The UTS and EC of Al-0.2Zr-0.06Sc wire (aged/168 h) are 195 ± 2 MPa and 61.2% IACS, respectively, which exhibits an excellent combination of mechanical properties and EC. According to the ASTM B941-2016 standard specification of ultra-heat-resistant Al-Zr alloy wires for electrical purposes, heat resistance tests shall indicate strengths not less than 90% of the values for individual tests after heat exposure of 280°C/1 h. A high strength residual rate of ∼94.0% is obtained in the aged/168h-wire, which is mainly attributed to the pinning effect of Al3(Zr,Sc) precipitates dispersed on the Al matrix.
Figure 3. UTS and EC of Al-0.2Zr-0.06Sc alloy wires were compared with other heat-resistant Al conductors produced by different processes. (CD: Cold drawing; A: Ageing treatment; HR: Hot rolled; CR: Cold rolled; AN: Annealing treatment; and HPT: High pressure torsion) [Citation9,Citation14–22].
![Figure 3. UTS and EC of Al-0.2Zr-0.06Sc alloy wires were compared with other heat-resistant Al conductors produced by different processes. (CD: Cold drawing; A: Ageing treatment; HR: Hot rolled; CR: Cold rolled; AN: Annealing treatment; and HPT: High pressure torsion) [Citation9,Citation14–22].](/cms/asset/84e66d61-2512-45d7-8ce7-43a41f9dbe57/tmrl_a_2360161_f0003_oc.jpg)
For Al-0.2Zr-0.06Sc alloys, the strengthening mechanisms are the combined effects of GB strengthening, precipitation strengthening, dislocation strengthening and solid-solution strengthening. The phenomenological superposition approximation is used to calculate obstacles of similar strengths [Citation23]:
(4)
(4) Therefore, the yield strength (YS) can be presented as [Citation24]:
(5)
(5) The contribution of GB strengthening can be described by the Hall–Petch relation [Citation25]:
(6)
(6) where k is the Hall-Petch coefficient (is 60 MPa·μm−1/2 for Al); σ0 (∼10 MPa) is the inherent friction stress, and dave is the average grain size. Since the tensile direction of the wire is parallel to the axial direction, the dislocation slip is mainly hindered by the axial GBs. Thus, the dave is equivalent to the grain width in this study.
The strengthening contribution of precipitates σpre can be given using the Orowan mechanism [Citation26]:
(7)
(7) here, M is the Tayor factor with a value of 3.06; v is the Poisson's ratio of Al with a value of 0.345; G = 25.4 GPa is the shear modulus; b = 0.286 nm is the Burgers vector. The mean radius of a circular cross-section in a random plane for a spherical precipitate
and the edge-to-edge inter-precipitate spacing λ can be estimated as [Citation27]:
(8)
(8)
(9)
(9) where r is the average particle size of spherical precipitates and fv is the volume fraction of the precipitates.
The strengthening contribution provided by dislocations can be calculated as follows [Citation28]:
(10)
(10) In this equation, α is a dimensionless constant related to the dislocation interaction, which is reported to be 0.3 for Al, and Ddis is the dislocation density. For CCDR-A method, most dislocations recover after long-term ageing treatment, so the dislocation strengthening is inconspicuous.
The contribution of solid-solution strengthening can be calculated using the Labysch’s model [Citation29]:
(11)
(11) In this model, kAl-Zr is the solid-solution strengthening coefficient (9 MPa. wt%−2/3 for Al-Zr alloy) and CZr is the concentration of solute Zr. For Al-0.2Zr-0.06Sc alloys in this study, the solid-solution strengthening effect is as small as ∼3 MPa (as-CCDRed condition), because the solute atoms precipitate significantly after ageing treatment.
The quantitative strengthening contributions estimated by Equation (4-11) are shown in Figure . Clearly, the high strength of Al-0.2Zr-0.06Sc wire are provided by precipitation strengthening (∼49%), dislocation strengthening (∼25%) and GB strengthening (∼26%) in Figure (a). Since the GB strengthening and precipitation strengthening are similar for as-aged and as-drawn samples, the dislocation strengthening is essential to achieve higher strength. The theoretically calculated YS of cold-drawn Al-0.2Zr-0.06Sc wire is 173 MPa, which is approached with the experimental results of 182 MPa (Figure (b)). Therefore, cold drawing is an effective way to increase the YS due to the introduction of dislocations strengthening and grain refinement.
Figure 4. The strengthening contribution provided by different mechanisms was calculated using Equations (4)–(11) in (a); and difference between calculated and experimental results in (b).
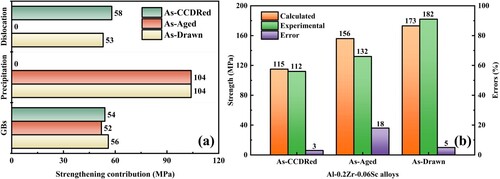
According to Matthiessen’s rule, the total electrical resistivity of Al-0.2Zr-0.06Sc alloys can be expressed as [Citation30]:
(12)
(12) where ρAl is the resistivity of pure Al (2.7 μΩ·cm); ρss, ρgb, ρdis, ρpre, and ρvac are the electrical resistivity provided by solute atoms, GBs, dislocations, precipitates and vacancies. In addition, it is well accepted that the influence of precipitates with good coherence relationship with the Al matrix on the electrical resistivity can be ignored [Citation9]. Since the electrical resistivity contribution of vacancies after ultra-severe plastic deformation is usually as small as 0.02 μΩ·cm, the ρvac can also be negligible [Citation26]. As a result, the key factors that influencing the electrical resistivity of Al-0.2Zr-0.06Sc alloy wire are the solute atoms, GBs and dislocations.
The contribution of solute atoms on the electrical resistivity can be expressed as follows [Citation30]:
(13)
(13) where Δρiss is the resistivity per unit contribution of i-th solute atom (ΔρZrss is 6.103 μΩ·cm·at%−1 and ΔρScss is 3.4 μΩ·cm·at%−1) and Ciss is the concentration of ith solute atom.
The contribution of GBs on electrical resistivity can be estimated as follows [Citation31]:
(14)
(14) Here, SGBs (m−1) ≈ 3/dave is the bulk density of GBs with an average grain size of dave, and ΔρGBs is the resistivity per unit concentration of GBs, which is 2.6 × 10−16 Ωm2 for Al. For the Al wire, the conductive direction is parallel to the axial direction. The scattering effect of the GBs vertical to the axial direction on electrons during conduction is dominate. Therefore, the grain width is used to estimate ρGBs.
The contribution of dislocations on the electrical resistivity can be expressed by Equation (12). For the aged alloy before cold drawing, the ρdis can be ignored due to the recovery of dislocations after ageing, so the ρss of aged alloys can also be obtained by Equation (12).
Figure shows the electrical resistivity contributions calculated by Equation (12-14) and the change of aged/168h-wire on the EC during the processing path. For the as-CCDRed alloy, the main contribution to the electrical resistivity comes from the solute atoms (∼79%), as shown in Figure (a). The GBs and dislocations influencing the electrical resistivity are ∼7% and ∼14%, respectively. After long-term ageing, the electrical resistivity of as-aged alloy is significantly reduced because of the precipitation of solute atoms and the recovery of dislocations. Cold drawing refines the grain structure and introduces dislocations, but the change of electrical resistivity is mainly attributed by dislocations instead of GBs. Additionally, we found that the UTS and EC of wires after cold drawing increase ∼30 MPa and reduce ∼1.2% IACS for different processes, respectively, in Figure and Figure (b). This is mainly due to the fact that cold drawing has similar abilities to refine grains and introduce dislocations at the same deformation process without affecting the solute atoms. Based on this analysis, the strength and EC of Al-Zr-Sc wires can be predicted by the properties of rods.
Figure 5. The influence of different mechanisms on the electrical resistivity was calculated using Equations (12)–(14) in (a); The change of aged/168h-wire on the EC during processing paths in (b).
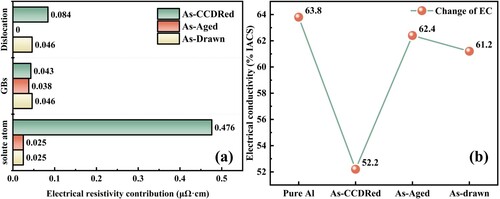
Compared with the quantitative results reported by Fan et al. [Citation21], the key to improve the EC is weakening the adverse effects of Zr atoms. Guan et al. [Citation5] reported that the EC of Al-0.2Zr-0.35Sc alloy after cold drawing from 10.0 to 3.0 mm is reduced by 0.5% IACS, which is smaller than our study (∼1.2%IACS). So, the greater deformation volume during cold drawing is more beneficial to keep the good EC of Al-Zr-Sc alloy wires. Therefore, the key factors to achieve well-combined properties for Al-Zr-Sc conductive wires are the full precipitation of solute atoms and greater cold deformation volume.
4. Conclusion
In summary, the Al-0.2Zr-0.06Sc wire with high UTS (195 ± 2 MPa) and good EC (61.2% IACS) was successfully prepared by the CCDR → Ageing treatment → Cold drawing processing method. Increasing ageing time ensures the high EC due to the precipitation of solute atoms and recovery of dislocations introduced by rolling. After cold drawing, the precipitation strengthening, GB strengthening and dislocation strengthening provide the remarkable strength. The EC decreased by dislocations can be improved through fully precipitation of solute atoms, while the dislocation strengthening compensates for the reduced precipitation strengthening due to over-ageing. Undoubtedly, excellent combination of strength and EC can be achieved for Al-Zr-Sc wires by this processing path, breaking the trade-offs of strength and EC during traditional annealing processing method. The heat-resistant of Al wires meets the ASTM B941-2016 standard specification of ultra-heat-resistant Al-Zr alloy wires for electrical purposes. This optimized processing path will also provide a guidance for other Al-Zr-based alloy conductive wires.
Disclosure statement
No potential conflict of interest was reported by the author(s).
Correction Statement
This article has been corrected with minor changes. These changes do not impact the academic content of the article.
Additional information
Funding
References
- Souza PHL, Oliveira CASd, Quaresma JMdV. Precipitation hardening in dilute Al–Zr alloys. J Mater Res Technol. 2018;7:66–72. doi:10.1016/j.jmrt.2017.05.006
- Wang WY, Pan QL, Lin G, et al. Internal friction and heat resistance of Al, Al-Ce, Al-Ce-Zr and Al-Ce-(Sc)-(Y) aluminum alloys with high strength and high electrical conductivity. J Mater Res Technol. 2021;14:1255–1274. doi:10.1016/j.jmrt.2021.07.054
- Ekaputra CN, Rakhmonov JU, Weiss D, et al. Microstructure and mechanical properties of cast Al-Ce-Sc-Zr-(Er) alloys strengthened by Al11Ce3 micro-platelets and L12 Al3(Sc,Zr,Er) nano-precipitates. Acta Mater. 2022;240:118354. doi:10.1016/j.actamat.2022.118354
- Zhang J, Wang B, Wang H, et al. Improvement in compressive creep resistance of Al-0.2Zr alloy with L12 structured Sc-enriched precipitates. Mater Charact 2020;159:110024. doi:10.1016/j.matchar.2019.110024
- Guan RG, Jin HM, Jiang W, et al. Quantitative contributions of solution atoms, precipitates and deformation to microstructures and properties of Al-Sc-Zr alloys. Trans Nonferrous Metals Soc China. 2019;29(5):907–918. doi:10.1016/S1003-6326(19)65000-4
- Zhou WW, Cai B, Li WJ, et al. Heat-resistant Al-0.2Sc-0.04Zr electrical conductor. Mat Sci Eng A-Struct. 2012;552:353–358. doi:10.1016/j.msea.2012.05.051
- Kong Y, Pu Q, Jia Z, et al. Microstructure and property evolution of Al-0.4Fe-0.15Zr-0.25Er alloy processed by high pressure torsion. J Alloy Compd. 2020;824:153949. doi:10.1016/j.jallcom.2020.153949
- Zhang JY, Wang HX, Yi DQ, et al. Comparative study of Sc and Er addition on microstructure, mechanical properties, and electrical conductivity of Al-0.2Zr-based alloy cables. Mater Charact 2018;145:126–134. doi:10.1016/j.matchar.2018.08.037
- Liu L, Jiang JT, Zhang B, et al. Enhancement of strength and electrical conductivity for a dilute Al-Sc-Zr alloy via heat treatments and cold drawing. J Mater Sci Technol 2019;35:962–971. doi:10.1016/j.jmst.2018.12.023
- Guan R, Shen Y, Zhao Z, et al. A high-strength, ductile Al-0.35Sc-0.2Zr alloy with good electrical conductivity strengthened by coherent nanosized-precipitates. J Mater Sci Technol 2017;33:215–223. doi:10.1016/j.jmst.2017.01.017
- Liu L, Jiang JT, Cui XY, et al. Correlation between precipitates evolution and mechanical properties of Al-Sc-Zr alloy with Er additions. J Mater Sci Technol 2022;99:61–72. doi:10.1016/j.jmst.2021.05.031
- Booth-Morrison C, Seidman DN, Dunand DC. Effect of Er additions on ambient and high-temperature strength of precipitation-strengthened Al-Zr-Sc-Si alloys. Acta Mater. 2012;60:3643–3654. doi:10.1016/j.actamat.2012.02.030
- Luca AD, Dunand DC, Seidman DN. Microstructure and mechanical properties of a precipitation-strengthened Al-Zr-Sc-Er-Si alloy with a very small Sc content. Acta Mater. 2018;144:80–91. doi:10.1016/j.actamat.2017.10.040
- Orlova TS, Latynina TA, Mavlyutov AM, et al. Effect of annealing on microstructure, strength and electrical conductivity of the pre-aged and HPT-processed Al-0.4Zr alloy. J Alloy Compd. 2019;784:41–48. doi:10.1016/j.jallcom.2018.12.324
- Orlova TS. Influence of severe plastic deformation on microstructure, strength and electrical conductivity of aged Al-0.4Zr (wt.%) alloy. Rev Adv Mater Sci 2018;55:92–101. doi:10.1515/rams-2018-0032
- Pozdniakov AV, Barkov RY, Prosviryakov AS, et al. Effect of Zr on the microstructure, recrystallization behavior, mechanical properties and electrical conductivity of the novel Al-Er-Y alloy. J Alloy Compd. 2018;765:1–6. doi:10.1016/j.jallcom.2018.06.163
- Kong Y, Jia Z, Liu Z, et al. Effect of Zr and Er on the microstructure, mechanical and electrical properties of Al-0.4Fe alloy. J Alloy Compd. 2021;857:157611. doi:10.1016/j.jallcom.2020.157611
- Zhang Y, Gu J, Tian Y, et al. Microstructural evolution and mechanical property of Al–Zr and Al–Zr–Y alloys. Mat Sci Eng. A-Struct. 2014;616:132–140. doi:10.1016/j.msea.2014.08.017
- Barkov RY, Mikhaylovskaya AV, Yakovtseva OA, et al. Effects of thermomechanical treatment on the microstructure, precipitation strengthening, internal friction, and thermal stability of Al–Er-Yb-Sc alloys with good electrical conductivity. J Alloy Compd. 2021;855:157367. doi:10.1016/j.jallcom.2020.157367
- Gorlov LE, Loginova IS, Glavatskikh MV, et al. Novel precipitation strengthened Al-Y-Sc-Er alloy with high mechanical properties, ductility and electrical conductivity produced by different thermomechanical treatments. J Alloy Compd. 2022;918:165748. doi:10.1016/j.jallcom.2022.165748
- Fan SY, Li ZH, Xiao WL, et al. Effects of processing paths on the microstructure, mechanical properties and electrical conductivity of dilute Al-Zr-Sc alloy conductive wires. J Mater Sci Technol 2024;188:202–215. doi:10.1016/j.jmst.2023.11.060
- Pozdniakov AV, Barkov RY. Microstructure and mechanical properties of novel Al-Y-Sc alloys with high thermal stability and electrical conductivity. J Mater Sci Technol 2020;36:1–6. doi:10.1016/j.jmst.2019.08.006
- Starink MJ, Wang SC. A model for the yield strength of overaged Al-Zn-Mg-Cu alloys. Acta. Mater. 2003;51:5131–5150. doi:10.1016/S1359-6454(03)00363-X
- Knipling KE, Seidman DN, Dunand DC. Ambient- and high-temperature mechanical properties of isochronally aged Al-0.06Sc, Al-0.06Zr and Al-0.06Sc-0.06Zr (at.%) alloys. Acta Mater 2011;59:943–954. doi:10.1016/j.actamat.2010.10.017
- Fan SY, Guo XM, Jiang QW, et al. Microstructure evolution and mechanical properties of Ti and Zr micro-alloyed Al-Cu alloy fabricated by wire + arc additive manufacturing. JOM-US. 2023;75:4115–4127. doi:10.1007/s11837-023-05900-9
- Mohammadi A, Enikeev NA, Murashkin MY, et al. Developing age-hardenable Al-Zr alloy by ultra-severe plastic deformation: significance of supersaturation, segregation and precipitation on hardening and electrical conductivity. Acta Mater. 2021;203:116503. doi:10.1016/j.actamat.2020.116503
- Fuller CB, Seidman DN, Dunand DC. Mechanical properties of Al(Sc,Zr) alloys at ambient and elevated temperatures. Acta Mater. 2003;51:4803–4814. doi:10.1016/S1359-6454(03)00320-3
- Hansen N, Huang X. Microstructure and flow stress of polycrystals and single crystals. Acta Mater. 1998;46:1827–1836. doi:10.1016/S1359-6454(97)00365-0
- Myhr OR, Grong O, Andersen SJ. Modelling of the age hardening behaviour of Al-Mg-Si alloys. Acta Mater. 2001;49:65–75. doi:10.1016/S1359-6454(00)00301-3
- Sauvage X, Bobruk EV, Murashkin MY, et al. Optimization of electrical conductivity and strength combination by structure design at the nanoscale in Al-Mg-Si alloys. Acta Mater. 2015;98:355–366. doi:10.1016/j.actamat.2015.07.039
- Karolik AS, Luhvich AA. Calculation of electrical resistivity produced by dislocations and grain boundaries in metals. J Phys Condens Matter 1994;6:873–886. doi:10.1088/0953-8984/6/4/007