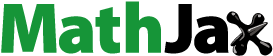
Abstract
Overcoming the trade-off relationship between strength and ductility has always been a challenge. In this article, a neatly arranged ultrafine bainite that is composed of multi-scale retained austenite was obtained by introducing weak chemical heterogeneity in low-alloy steel. The optimized microstructure makes transformation-induced plasticity (TRIP) behavior and coordinating deformation behavior between each phase to be smoother. This results in better comprehensive properties, with 28.5% and 9% increases in uniform elongation and toughness, respectively, and a similar strength. This study provides a new way to improve the properties of low-alloy steels.
IMPACT STATEMENT
A strategy of weak chemical heterogeneity has been proposed in low-alloy steel, which effectively optimizes the microstructure and enhances the plasticity and toughness of steel.
1. Introduction
In recent years, researchers have found that introducing chemical heterogeneity into steel can regulate microstructure and effectively improve mechanical properties [Citation1–4]. The formation of chemical heterogeneity usually depends on Mn-rich phases, such as cementite, in the initial microstructure. After rapid heat treatment, the microstructure of steel inherits the enrichment of alloying elements. An increase in Mn content effectively reduces the martensitic transformation temperature of the sample. As a result, the phase transformation behavior at the Mn-rich area is different from that at the Mn-poor area. Research shows that chemical heterogeneity regulates microstructure morphology, and increases the content and stability of retained austenite [Citation5,Citation6]. This is beneficial for improving the mechanical properties of material, especially the plasticity and toughness. Kim et al. [Citation7] designed the chemical heterogeneity of Fe-0.18C-3.5Mn steel and obtained a large amount of nanoscale Mn-rich austenite and thus achieved an increase in elongation. Gu et al. [Citation8] introduced chemical heterogeneity in quenched partitioned (Q&P) steel, which then exhibited tensile properties that were comparable to those of steels with higher Mn content.
Mn content is an important factor that affects chemical heterogeneity. The application of chemical heterogeneity in steel is summarized in Table S1. As seen, researchers generally apply chemical heterogeneity in medium-Mn steel. The enrichment of the Mn element in cementite or austenite of medium-Mn steel is high enough (more than 10 wt.%). The content of the Mn element in the Mn-rich area after rapid heat treatment is much higher than the average content of Mn. This makes it easier to retain austenite in the area enriched with Mn elements [Citation9,Citation10]. However, the high content of alloying elements in steel is not conducive to develop the industry. Reduction of the amount of alloying elements is conducive to achieving the goal of sustainable development [Citation11]. Mn content is low in many commercial steels; for example, it is generally less than 2 wt.% in Q&P steel [Citation12]. Therefore, developing a method for improving the performance of low-alloy steel with chemical heterogeneity is greatly significant. In recent years, researchers have promoted the diffusion of C into austenite by generating a large number of ferrites, thus achieving chemical heterogeneity in low-carbon steel [Citation2,Citation9]. However, a large amount of ferrite in the microstructure limits its application. In this paper, weak chemical heterogeneity was successfully exploited to regulate microstructure in low-alloy steel. Ultrafine bainite with multi-scale retained austenite was constructed, and the ductility and toughness were simultaneously improved.
2. Experimental procedure
The chemical composition of the investigated steel is Fe-0.70C-2.42Si-0.47Cr-0.66Mn (wt.%). The steel was obtained by vacuum smelting and further forged at high temperature to obtain a cylindrical steel bar with a diameter of 60 mm. The heat treatment process was divided into a preheating treatment and a final heating treatment. First, the content distribution of alloying elements can be controlled by changing the preheating treatment process. The preheating treatment needed heating the sample at 900°C for 1 h, and then isothermal steps at 600°C and 350°C for 2 h, respectively. Finally, lamellar pearlite (LP) with a lamellar distribution of alloying elements and ultrafine bainite (UB) with uniform composition was obtained. Subsequently, the LP samples and UB samples were heated to 920°C and 900°C at a heating rate of 100°C/s, respectively. For the two microstructures under rapid heating, the austenitizing temperature was determined according to Ac3’ +50°C. Then, an isothermal step was conducted in a salt bath furnace at 350°C for 2 h. In addition, to observe the compositional distribution of the sample after rapid heat treatment, the samples were quenched to room temperature at a cooling rate of 30°C/s. The heat treatment processes are shown in Figure S1. The samples were labeled according to the initial microstructure and austempering temperature. The sample that had an initial pearlite transformation, rapid heating to reaustenitization and austempering at 350°C was denoted as the LP-350 sample.
Microstructures were characterized using an SU-5000 field emission scanning electron microscope (SEM), electron backscatter diffraction (EBSD) instrument and FEI-Talos 200 FX transmission electron microscope (TEM). The distribution of alloying elements was measured using an energy dispersive spectrometer (EDS) that was equipped with the SEM. A standard round bar tensile sample that had a gauge diameter of 5 mm and a length of 30 mm was used. Tensile tests were carried out at a strain rate of 2 × 10−3 s−1 on an MTS tensile testing machine. A JB-300 pendulum impact tester was used to conduct room temperature impact tests. The dimensions of the samples were 10 × 10 × 55 mm3 with a U notch. The hardness of the sample was measured on a Rockwell hardness tester.
3. Results and discussion
Figure (a,b) show microstructure images of ultrafine bainite with chemical heterogeneity and uniform distribution of alloying elements, respectively. It can be seen from the SEM images in Figure (a1, b1) that the microstructure of the LP-350 sample is significantly coarser than that of the UB-350 sample. There is a large amount of parallel-arranged retained austenite in the LP-350 sample. Although the morphologies of bainitic ferrite are similar (Figure (a2, 3, b2, 3)), there are obvious differences in the morphologies of the retained austenite. Moreover, some of the thicker filmy retained austenite has a parallel arrangement in the LP-350 sample. This corresponds to the morphology of retained austenite in SEM images. The thicker filmy retained austenite is interspersed with several bainitic ferrite laths and thinner filmy retained austenite. A comparison of Figure (a,c) shows that the arrangement of these thicker filmy retained austenite in the LP-350 sample is similar to that of the cementite plate in LP. A detailed comparison of the size and content of each phase is provided in Figure .
Figure 1. SEM image of LP-350 sample with weak chemical heterogeneity (a1); TEM bright field image and selected area electron diffraction (SAED) patterns in the LP-350 sample (a2, a3). SEM image of the UB-350 sample with uniform distribution of alloying elements (b1); TEM bright field image and SAED patterns in the UB-350 sample (b2, b3). SEM image of the LP sample after pretreatment (c1); TEM bright field image and SAED patterns in the LP sample (c2, c3). Note: BF is bainitic ferrite, RA-B is blocky retained austenite, RA-F is filmy retained austenite and F is ferrite.
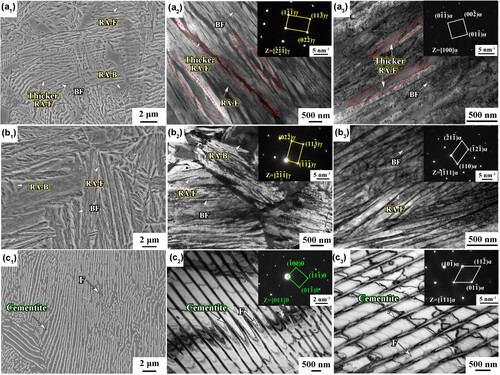
Figure 2. Thicknesses of bainitic ferrites (a). The equivalent diameter of the blocky retained austenite (b). The thickness of the filmy retained austenite and cementite (c). Lamellar spacing of the thicker filmy retained austenite and cementite (d). XRD patterns of different samples (e). Grain size of parent austenite (f). Note: The measured microstructure size of the sample has been visually corrected according to reference [Citation13].
![Figure 2. Thicknesses of bainitic ferrites (a). The equivalent diameter of the blocky retained austenite (b). The thickness of the filmy retained austenite and cementite (c). Lamellar spacing of the thicker filmy retained austenite and cementite (d). XRD patterns of different samples (e). Grain size of parent austenite (f). Note: The measured microstructure size of the sample has been visually corrected according to reference [Citation13].](/cms/asset/f40452fe-4ba9-4995-a9b7-e9b2a840b5cc/tmrl_a_2366875_f0002_oc.jpg)
Figure (a) shows the lath thickness distribution of bainitic ferrite. The average lath thickness of bainitic ferrite is 48.4 nm in the LP-350 sample. This is slightly less than that of the corresponding thickness in the UB-350 sample (59.5 nm). The sizes of the blocky retained austenite are similar between the two samples, as seen in Figure (b). The thickness distribution of filmy retained austenite is shown in Figure (c). It can be seen that the average thickness of the filmy retained austenite of the LP-350 sample is 37.6 nm. This is significantly greater than that of the UB-350 sample (17.6 nm). The thickness distribution of filmy-retained austenite in the LP-350 sample exhibits a bimodal shape. The average thickness of thicker filmy retained austenite is 96.8 nm and that of thinner one is 17.6 nm. Interestingly, the thickness distribution of the thicker filmy retained austenite is similar to that of cementite in LP. In addition, the spacing between the thicker filmy retained austenite is 0.25 µm in the LP-350 sample, and this is also smaller than that between cementite (0.21 µm) in the LP sample (Figure (d)). This is because the thicker filmy retained austenite is not formed at the position of some cementite plate. Therefore, it can be deduced that there is probably an inheritance relationship between the thicker filmy retained austenite in the LP-350 sample and the cementite in the LP sample.
As shown in Figure (e), XRD results show that the contents of retained austenite are similar in the UB-350 sample and the LP-350 sample. The peak positions of (200)γ are similar, and this indicates that the carbon contents in the retained austenite are similar. This is different from the conventional understanding that the content of retained austenite increases after chemical heterogeneity is introduced [Citation14–16]. The reason for the negligible change in the content of retained austenite is related to weak chemical heterogeneity in low-alloying steel, specifically the low enrichment of Mn. During the bainite isothermal process, Mn-rich austenite requires a large amount of carbon for its chemical stability to be improved and thus the Mn-rich austenite can be retained. As shown in Figure (f), the grain size of parent austenite in the LP-350 sample is lower than that in the UB-350 sample. This is because cementite plays a pinning role in the austenite grain boundaries [Citation17,Citation18]. Therefore, the grain size of the parent austenite of the LP-350 sample is relatively small.
It can be seen from Figure (a), these thicker filmy austenite are enriched in Mn and Cr in the LP-350 sample. This is similar to the alloy element distribution of the LP sample and LP-0 sample (quenched sample) shown in Figure (b,c), respectively. Since no elements diffuse during the rapid quenching process, the composition distribution of the quenched sample can be regarded as the distribution of chemical elements in the sample after the rapid heating process. Mn and Cr are carbide-forming alloying elements and thus are enriched in the cementite plate. The diffusion coefficients of Mn and Cr alloying elements are much lower than that of C. Therefore, the diffusion of these alloying elements is insufficient during the short austenitization time [Citation19]. This results in a slightly reduced enrichment of Mn and Cr. The laminar distribution of alloying elements in the initial microstructure is partially retained. The enrichment degree of Mn and Cr is much lower compared with previous studies on chemical heterogeneity of traditional medium-Mn steel, as researched by Zhang et al. [Citation20] and Sun et al. [Citation21].
Figure 3. Microstructure and elemental distribution by line scanning of the LP-350 sample (a), the LP sample (b) and the LP-0 sample (directly quenched) (c).
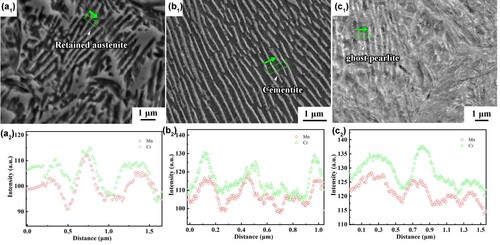
Therefore, the formation of thicker filmy retained austenite is related to the chemical heterogeneity that is inherent in initial cementite. An increase in Mn decreases the driving force of bainitic transformation (ΔGγ→α) [Citation22–24]. The effect that Cr has on bainitic transformation is similar to that of Mn [Citation25]. Therefore, the enrichment of Mn and Cr stabilizes the austenite and inhibits the nucleation of bainitic ferrite. This results in the preferential occurrence of bainite transformation in the matrix with relatively lower alloy content. With an increase in transformation time, the carbon in bainitic ferrite diffuses to untransformed austenite [Citation26,Citation27]. This causes the chemical stability of the untransformed austenite to continue increasing, making it difficult for further phase transformation. Finally, the thicker filmy retained austenite is obtained in these lamellar areas enriched with Mn and Cr.
In previous studies on chemical heterogeneity, the Mn content was higher than 10 wt.% in the area enriched with alloying elements [Citation1,Citation5]. High Mn content significantly reduces the Ms temperature in the area enriched with alloying elements, and the phase transformation is different. However, in this paper, the chemical heterogeneity is weak. The martensitic phase transformation does not undergo significant phase separation during the continuous cooling process, as shown in Figure S2. There are primarily two reasons why weak chemical heterogeneity can regulate microstructure in low alloy steel. First, the area enriched with Mn and Cr elements hinders the nucleation and growth of bainitic ferrite. Second, carbon enrichment during the bainite isothermal process in these areas further improves the stability of the enriched austenite.
Figure (a,b) show the tensile and work hardening curves of the LP-350 sample and the UB-350 sample, respectively. The strengths of the LP-350 sample and UB-350 sample are similar. Among them, the yield strength of the LP-350 sample is slightly lower, and the work hardening ability is better than that of the UB-350 sample. The elongation of the LP-350 sample is significantly higher than that of the UB-350 sample, specifically, the uniform elongation increased by 28.5%. As seen in Figure (b), the LP-350 sample has a continuous work hardening ability. It can be seen from the illustration that the work-hardening rate of the LP-350 sample is slightly higher than that of the UB-350 sample. At 8% strain, the work hardening rate of the LP-350 sample is increased by 7.7% compared with the UB-350 sample. The mechanical properties of the UB-350 sample were used as a standard, and the measured mechanical property data were normalized and plotted to obtain the radar model diagram shown in Figure (c). It can be seen that in addition to strength and elongation, the impact toughness of the LP-350 sample with weak chemical heterogeneity is significantly improved by 9%. From an area evaluation of the radar chart model, the comprehensive mechanical properties of the LP-350 sample, which has chemical heterogeneity, are improved by 21% compared to those of the UB-350 sample.
Figure 4. Tensile curves (a) and work hardening curves (b). Radar model diagram of normalized mechanical properties (c). Relationship between the volume fraction of retained austenite and true strain of the LP-350 sample and UB-350 sample (d). TEM bright field image of LP-350 sample in the tensile uniform section (e). SEM image of the LP-350 sample in the tensile necking area (f).
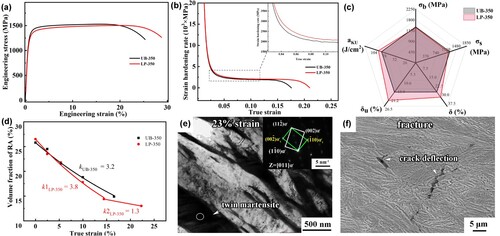
The multi-scale retained austenite induced via weak chemical heterogeneity and should play an important role in the increased comprehensive properties. Figure (c) shows how the retained austenite content varies with strain for different samples. The stability of retained austenite was evaluated using the following formula [Citation28]:
(1)
(1) where
is the initial volume fraction of retained austenite; V is the volume fraction of retained austenite when the true strain is ϵ; ϵ is the degree of strain and k is a constant. The value of k represents the mechanical stability of retained austenite. When the value of k is smaller, the mechanical stability of retained austenite is higher. It can be seen that the stability of retained austenite in the LP-350 sample is slightly lower than that in the UB-350 sample when the true strain is lower than 15%. This is corroborated by the higher work-hardening rate of the LP-350 sample. However, ultimately, it is improved during the later tensile stage of the LP-350 sample.
It is generally recognized that plasticity and toughness that is enhanced by chemical heterogeneity stems from its effect on retained austenite. In particular, an increase in chemical elements contributes to the content and mechanical stability of retained austenite [Citation9,Citation16]. It is generally believed that the improved stability of retained austenite and its continuous transformation behavior is beneficial for improving the plasticity and toughness of steel [Citation29–31]. Enrichment of Mn and Cr effectively enhances the stability of retained austenite. However, the present results show a reduced initial stability of retained austenite. Except for the element content in retained austenite, the larger size of retained austenite reduces its mechanical stability because of the reduced compressive stress that results from the bainitic ferrite on both sides [Citation28]. Therefore, compared to the stability of filmy retained austenite in the UB-350 sample, the thicker filmy retained austenite in the LP-350 sample possesses a relatively lower stability and the thinner filmy retained austenite possesses a higher stability. As shown in Figure (e), the thicker filmy retained austenite undergoes a martensitic phase transition after tensile to 23%. The thicker filmy retained austenite has a good transition effect between blocky retained austenite and thinner retained austenite, making the TRIP effect smoother.
Except for the stability change of multi-scale retained austenite that results from weak chemical heterogeneity, optimization of the microstructure also plays a key role in the improved comprehensive properties of the LP-350 sample. First, refinement of the grain size of parent austenite and the lath of bainitic ferrite in the LP-350 sample are both beneficial for improving plasticity and toughness [Citation32]. Second, the presence of thicker filmy retained austenite facilitates the TRIP effect as discussed above; also, it relieves the stress concentration and improves the coordinated deformation ability during the plastic deformation process [Citation33–36], due to its neat arrangement to form a layered structure. As shown in Figure (f), when a crack intersects with the layered microstructure, the crack deflects. Therefore, the improved comprehensive properties of the LP-350 sample mainly come from the multi-scale retained austenite that results from weak chemical heterogeneity.
4. Conclusions
The present study provides a strategy for weak chemical heterogeneity in low-alloy steel that results in a finer neatly arranged microstructure, with a multi-scale retained austenite in it. The uniform ductility and toughness of the sample with chemical heterogeneity increased by 28.5% and 9%, respectively, with similar strength; also, the comprehensive mechanical properties ultimately increased by 21%. Introducing weak chemical heterogeneity does not increase the content of retained austenite and its mechanical stability, but makes TRIP behavior and coordinating deformation between each phase smoother, this facilitates an improvement of the mechanical properties of the steel. This study provides a new way to improve the properties of low-alloy steels.
Supplemental Material
Download MS Word (187 KB)Disclosure statement
No potential conflict of interest was reported by the author(s).
Additional information
Funding
References
- Liu G, Dai ZB, Yang ZG, et al. Kinetic transitions and Mn partitioning during austenite growth from a mixture of partitioned cementite and ferrite: role of heating rate. J Mater Sci Technol. 2020;49:70–80. doi:10.1016/j.jmst.2020.01.051
- Ding R, Zhang C, Wang Y, et al. Mechanistic role of Mn heterogeneity in austenite decomposition and stabilization in a commercial quenching and partitioning steel. Acta Mater. 2023;250:118869. doi:10.1016/j.actamat.2023.118869
- Hu B, Zheng Q, Lu Y, et al. Stabilizing austenite via intercritical Mn partitioning in a medium Mn steel. Scr Mater. 2023;225:115162. doi:10.1016/j.scriptamat.2022.115162
- Wang Y, Ding R, Franke C, et al. Flash annealing of a chemically heterogeneous medium Mn steel. Scr Mater. 2024;242:115923. doi:10.1016/j.scriptamat.2023.115923
- Ding R, Yao YJ, Sun BH, et al. Chemical boundary engineering: a new route toward lean, ultrastrong yet ductile steels. Sci Adv. 2020;6(13):eaay1430. doi:10.1126/sciadv.aay1430
- Zhang C, Xiong Z, Li Z, et al. On the role of chemical heterogeneity in carbon diffusion during quenching and partitioning. Acta Mater. 2024;271:119902. doi:10.1016/j.actamat.2024.119902
- Kim JH, Gu G, Kwon M, et al. Microstructure and tensile properties of chemically heterogeneous steel consisting of martensite and austenite. Acta Mater. 2022;223:117506. doi:10.1016/j.actamat.2021.117506
- Gu G, Kim JH, Lee HH, et al. Room temperature quenching and partitioning (RT-Q&P) processed steel with chemically heterogeneous initial microstructure. Mater Sci Eng A. 2022;851:143651. doi:10.1016/j.msea.2022.143651
- Zhang C, Liu C, Guo H, et al. Chemical heterogeneity enables austenite stabilization in a Si-/Al-free Fe-0.2C-2Mn steel. Scr Mater. 2022;218:114822. doi:10.1016/j.scriptamat.2022.114822
- Lee S, Lee S, De Cooman BC. Austenite stability of ultrafine-grained transformation-induced plasticity steel with Mn partitioning. Scr Mater. 2011;65(3):225–228. doi:10.1016/j.scriptamat.2011.04.010
- Li X, Lu K. Improving sustainability with simpler alloys. Science. 2019;364(6442):733–734. doi:10.1126/science.aaw9905
- Ranjan R, Singh SB. Isothermal bainite transformation in low-alloy steels: mechanism of transformation. Acta Mater. 2021;202:302–316. doi:10.1016/j.actamat.2020.10.048
- Zhao JL, Lv B, Zhang FC, et al. Effects of austempering temperature on bainitic microstructure and mechanical properties of a high-C high-Si steel. Mater Sci Eng A. 2019;742:179–189. doi:10.1016/j.msea.2018.11.004
- Kim JH, Kwon M, Gu G, et al. Quenching and partitioning (Q&P) processed medium Mn steel starting from heterogeneous microstructure. Materialia. 2020;12:100757. doi:10.1016/j.mtla.2020.100757
- Kim JH, Gu G, Koo M, et al. Enhanced ductility of as-quenched martensite by highly stable nano-sized austenite. Scr Mater. 2021;201:113955. doi:10.1016/j.scriptamat.2021.113955
- Chai Z, Wang L, Wang Z, et al. Cr-enriched carbide induced stabilization of austenite to improve the ductility of a 1.7 GPa−press-hardened steel. Scr Mater. 2023;224:115108. doi:10.1016/j.scriptamat.2022.115108
- Fang F, Dai SF, Zhang YX, et al. Role of inhibitor behavior in abnormal growth of Goss grain in grain-oriented silicon steel: experiments and modeling. J Mater Res Technol. 2023;24:2918–2934. doi:10.1016/j.jmrt.2023.03.179
- Erişir E, Bilir OG, Gezmişoğlu AE. A study of carbide dissolution in bearing steels using computational thermodynamics and kinetics. IOP Conf Ser: Mater Sci Eng. 2017;179(1):012021. doi:10.1088/1757-899X/179/1/012021
- Bhadeshia HKDH. Cementite. Int Mater Rev. 2020;65(1):1–27. doi:10.1080/09506608.2018.1560984
- Zhang C, Xiong ZP, Yang DZ, et al. Heterogeneous quenching and partitioning from manganese-partitioned pearlite: retained austenite modification and formability improvement. Acta Mater. 2022;235:118060. doi:10.1016/j.actamat.2022.118060
- Sun WW, Wu YX, Yang SC, et al. Advanced high strength steel (AHSS) development through chemical patterning of austenite. Scr Mater. 2018;146:60–63. doi:10.1016/j.scriptamat.2017.11.007
- Morawiec M, Opara J, Garcia-Mateo C, et al. Effect of Mn on the chemical driving force and bainite transformation kinetics in medium-manganese alloys. J Therm Anal Calorim. 2023;148(4):1567–1576. doi:10.1007/s10973-022-11664-2
- Leach L, Kolmskog P, Höglund L, et al. Critical driving forces for formation of bainite. Metall Mater Trans A. 2018;49(10):4509–4520. doi:10.1007/s11661-018-4819-5
- Gao GH, Liu ZY, Feng C, et al. Acceleration of bainitic transformation through chemical patterning of austenite. Metall Mater Trans A. 2023;54(8):2975–2981. doi:10.1007/s11661-023-07084-y
- Kim JH, Gu G, Hong S, et al. Acceleration of bainitic transformation in 0.28C-3.8Mn-1.5Si steel utilizing chemical heterogeneity. Scr Mater. 2024;239:115779. doi:10.1016/j.scriptamat.2023.115779
- Królicka A, Żak AM, Caballero FG. Enhancing technological prospect of nanostructured bainitic steels by the control of thermal stability of austenite. Mater Des. 2021;211:110143–110143. doi:10.1016/j.matdes.2021.110143
- Li K, Qian L, Wei C, et al. Effects of above- or below-a austenitization on bainite transformation behavior, microstructure and mechanical properties of carbide-free bainitic steel. Mater Sci Eng A. 2023;888:145814. doi:10.1016/j.msea.2023.145814
- Wang X, Zhang X, Fang Q, et al. Effect of tempering on stability of retained austenite and tensile properties of nanostructured bainitic steel. Mater Sci Eng A. 2022;856:143958. doi:10.1016/j.msea.2022.143958
- Hu J, Li X, Meng Q, et al. Tailoring retained austenite and mechanical property improvement in Al–Si–V containing medium Mn steel via direct inter critical rolling. Mater Sci Eng A. 2022;855:143904. doi:10.1016/j.msea.2022.143904
- Zhao JL, Zhang FC, Lv B, et al. Inconsistent effects of austempering time within transformation stasis on monotonic and cyclic deformation behaviors of an ultrahigh silicon carbide-free nanobainite steel. Mater Sci Eng A. 2019;751:80–89. doi:10.1016/j.msea.2019.01.100
- Yang DP, Wang T, Miao ZT, et al. Effect of grain size on the intrinsic mechanical stability of austenite in transformation-induced plasticity steels: the competition between martensite transformation and dislocation slip. J Mater Sci Technol. 2023;162:38–43. doi:10.1016/j.jmst.2023.03.013
- Dong HY, Hu CY, Wu GH, et al. Effect of nickel on hardening behavior and mechanical properties of nanostructured bainite-austenite steels. Mater Sci Eng A. 2021;817:141410. doi:10.1016/j.msea.2021.141410
- Niu G, Ding C, Liu Z, et al. Achieving high strength and high ductility of dual-phase steel via alternating lamellar microstructure. Mater Sci Eng A. 2024:892:146072. doi:10.1016/j.msea.2024.146072
- Nie J, Chen Y, Song L, et al. Enhancing strength and ductility of Al-matrix composite via a dual-heterostructure strategy. Int J Plast. 2023;171:103825. doi:10.1016/j.ijplas.2023.103825
- Wu X, Zhu Y. Gradient and lamellar heterostructures for superior mechanical properties. MRS Bull. 2021;46(3):244–249. doi:10.1557/s43577-021-00056-w
- Zou Y, Xu YB, Hu ZP, et al. High strength-toughness combination of a low-carbon medium-manganese steel plate with laminated microstructure and retained austenite. Mater Sci Eng A. 2017;707:270–279. doi:10.1016/j.msea.2017.09.059