Abstract
In this paper, the effect of Deep Cryogenic Treatment (DCT) soaking duration on tungsten carbide end mill cutters on cutting forces and power consumption during machining P20 mold steel in CNC milling machine is investigated and optimized the process parameters. The data collected for the study are based on Box–Behnken design of response surface methodology. Cutting forces and power consumption are considered as important performance measures which are functions of decision variables viz. cutting speed, feed, depth of cut, and end milling cutting tools subjected to different soaking duration. The percentage contribution is calculated based on ANOVA to identify most influencing parameter on cutting forces and power consumption. The study revealed that cryogenic soaking duration exhibits most significant effect on cutting forces and power consumption followed by cutting speed, feed, and depth of cut. Regression analysis is carried out to relate the process variables and performance measures. Finally, a non-dominated sorting Algorithm (NSGA-II) is proposed to optimize the process variable to obtain the desired optimal solutions. The results indicate DCT tool soaked for longer duration is minimizing the cutting forces and power consumption when compared to untreated tool.
1. Introduction
CNC milling machines finds extensive application in manufacturing industry. CNC milling machines are widely used to make slots, pocket, and complex surface shapes (Kondayya & Krishna, Citation2012). Tungsten carbide end mill cutting tools are generally used in industry for machining of hard materials in CNC milling process. Tungsten carbide is having higher wear resistance, high hardness. Due to high hardness it is able to machine high strength to weight ratio materials. In machining the cutting tools are subjected to high heat and fluctuating loads. Cutting tools used for machining should withstand that high heat and fluctuating loads without deformation and wearing. While machining due to high heat generation, cutting tool material gets softened which leads to tool wear and higher cutting forces are generated on the cutting tools (Gill, Singh, Singh, & Singh, Citation2011; Pilligrin, Asokan, Jerald, & Kanagaraj, Citation2017a). In order to increase productivity, it is necessary to reduce the cutting forces and power consumption. In the past, much work has been done for reducing the surface roughness and to improve tool life. But optimizing power consumption and cutting forces with cryogenic-treated tools had not received any considerable attention till now in the literature. Reducing the power consumption of CNC machine can extensively improve the ecological act of manufacturing processes. In order to increase the life of the tools, to reduce the cutting forces and power consumption, cryogenic treatment on cutting tools is the best solution (Pilligrin, Asokan, Jerald, & Kanagaraj, Citation2017b; Podgornik, Paulin, Zajec, Jacobson, & Leskovšek, Citation2016; Singh, Singh, & Singh, Citation2011; Yan & Li, Citation2013). The motivation behind cryogenic treatment is to transform retained austenite phase to martensite phase and raise the hardness of the structure (Gao, Luo, Bai, Zhu, & Ouyang, Citation2016; Perez & Belzunce, Citation2014; Sobotova, Jurci, & Dlouhy, Citation2016). Austenite (a soft form of iron) is formed only for HSS materials during the quenching phase of metal production, which is a solid solution of iron and carbon. Austenite is weak and undesirable since it contains some molecular interfaces to help hold the metal together. When metal is cryogenically treated, the austenite phase is gradually changed into a very composed grain structure called martensite phase, a body centered tetragonal crystal structure. Martensite is a better and harder structure that brings high wear resistance.
1.1. Cryogenic treatment
A cryogenic treatment is the process of treating cutting tools to cryogenic temperatures (i.e. below −190 °C) consecutively to eliminate residual stresses and get better wear resistance on steels. In addition to seeking improved stress relief or wear resistance, cryogenic treatment is also having capability to improve corrosion resistance by precipitating micro-fine eta carbides. The process has a wide range of applications from industrial tooling to the improvement of musical signal transmission. Improvement in toughness, hardness, and ductility is high due to cryogenic treatment (Dieringa, Citation2017; Xie, Huang, Tang, & GU, Citation2015). The typical increase in life of cutting tool is 35–50%. Another advantage of cryogenic treatment is increasing the thermal conductivity which results in high dissipation of heat (Chopra & Sargade, Citation2015; Li, Min, Li, & Xiaochun, Citation2013). In addition, better dimensional stability and refined grain structure is obtained in cryogenic-treated materials (Singh et al., Citation2011).
The input parameters concerned to cryogenic treatment process to improve tool life and productivity are soaking duration, lowering temperature, cooling and heating rates, and quenching and tempering processes. Few studies analyzed on cryogenic soaking duration and lowering temperature (Li, Yan, Liang, Hong, & Li, Citation2016) However, effect of soaking duration on machining performance of CNC milling process is extremely rare in the literature.
2. Literature review
In the last decade, CNC end milling process has emerged as one the major topic of research interest by the researchers. To enhance the productivity of the process numerous studies reported until now by the researchers have been summarized in the following lines. Many researchers have attempted to incorporate cryogenic cooling during machining using liquid nitrogen as coolant on to the machining zone (Giasin, Ayvar-Soberanis, & Hodzic, Citation2016; Kalyan Kumar & Choudhury, Citation2008; Khan & Ahmed, Citation2008; Nalbant & Yildiz, Citation2011; Safari, Sharif, Izman, Jafari, & Kurniawan, Citation2014; Sartori, Moro, Ghiotti, & Bruschi, Citation2016; Wang, Liu, & Shu, Citation2017). However, using liquid nitrogen as a coolant, the brittleness of the tool is increased. Due to brittleness, the tool may get micro-cracks at higher cutting speeds and flank wear during machining (Khan & Ahmed, Citation2008). Recently, cryogenic treatment on cutting tools has resulted in successful application to reduce cutting forces, power consumption and tool wear for machining different materials in CNC turning process (Aggarwal, Singh, Kumar, & Singh, Citation2008; Ghosh & Rao, Citation2017; Özbek, Çiçek, Gülesin, & Özbek, Citation2015; Sreerama Reddy, Sorna Kumar, Venkatarama Reddy, & Venkatram, Citation2009a; Sreerama Reddy, Sorna Kumar, Venkatarama Reddy, Venkatram, & Senthil Kumar, Citation2009b; Thamizhmanii, Mohideen, Zaidi, & Hasan, Citation2015).
To enhance the machining process few researchers have studied the effect of cryogenic treatment on cutting forces and tool life. Yong, Seah, and Rahman (Citation2007) studied the performance of cryogenically treated and untreated tungsten carbide tool inserts while machining medium carbon steel work material in CNC milling. The study revealed that crogenically treated tungsten carbide inserts can enhance the tool life by 28.9–38.6% in comparison with untreated tool inserts. Abou-El-Hossein, Kadirgama, and Hamdi (Citation2007) studied the effect of cutting speed, feed rate, radial depth, and axial depth of cut by developing first-order and second-order cutting force equations using response surface methodology (RSM) and predictive analysis was done by Minitab software. Close agreement has been achieved between predicted and experimental values. Kadirgama, Abou-El-Hossein, Mohammad, AL-Ani, and Noor (Citation2008) used FEA method and RSM method to find the effect of milling parameters such as cutting speed, feed rate, and axial depth in machining of Hastelloy C-22HS with 90o holder to optimize the cutting force. Based on the Analysis of Variance (ANOVA) they found that feed rate is the most significant parameter affecting cutting force. Optimized cutting force equations are generated using RSM and simulated using FEA. Kalsi, Segal, and Sharma (Citation2010) studied the effect of cryogenic treatment on different types of steel and other materials. It is observed that cryogenic treatment of materials has significant improvement in their properties like wear resistance, reduced residual stresses, hardness, fatigue resistance, toughness, and better thermal conductivity. Thamizhmanii, Nagib, and Sulaiman (Citation2011) analyzed the tool performance of cryogenically treated and untreated PVD inserts in the milling process on Inconel 718 material. The analysis revealed that cryogenic-treated PVD inserts showed better performance in terms of tool life and flank wear than untreated inserts.
A very few researchers have investigated experimentally and statistically on reduction of cutting forces in CNC end milling process. Turgut, Cxinici, and Sxahin (Citation2011) analyzed the effect of cutting speed, feed rates, and different cutting tool types (coated and uncoated) on cutting forces and surface roughness in face milling operation. They found that main cutting force (Fx) is increasing with increasing in feed rate and depth of cut whereas it is decreasing with increasing cutting speed. They also found that good surface roughness is obtained with increasing cutting speed for both coated and uncoated tools. Jaya kumar, Mathew, and Joseph (Citation2012) investigated on SiC particle- reinforced metal matrix composites using central composite experimental design by varying cutting speed, feed, and depth of cut to identify the responses such as cutting force, tool–work interface temperature. The results showed that higher cutting force is required during machining process with increase in % volume of SiCp reinforcement over the matrix. Karabulut (Citation2015) studied the effect of the cutting parameters while machining of AA7039 based metal matrix composites reinforced with Al2O3 on cutting force and surface roughness using neural networks and Taguchi method. They found that material structure is the most significant factor on surface roughness and feed rate is the most dominant factor affecting cutting force.
Theoretically and analytically, many studies have been reported on predicting the cutting force. The theoretical and analytical methods are purely based on assumptions that are not in the analysis. Reliability of the calculated values may reduce based on these methods. These methods may be successfully applicable to only certain ranges of cutting conditions (Campatelli & Scippa, Citation2012; Li & Li, Citation2002; Yun & Cho, Citation2001). Many studies reported purely experimental approaches to study the relationship between cutting force and process parameters. This may increase the total cost of the machining by increasing the number of experiments (Suresh Kumar Reddy & Venkateswara Rao, Citation2006; Zheng, Chiou, & Liang, Citation1996).
However, as far as CNC end milling process is concerned limited number of studies has been reported until now. Several studies aim to achieve optimal level of machining parameters for CNC milling process by the application of artificial intelligence (AI) techniques viz. genetic algorithm (GA), artificial neural network (ANN), and fuzzy logic. Mostly researchers have optimized commonly used input parameters like cutting speed, feed rate, and depth of cut to achieve improved machining efficiency. However, minimal number of studies has been reported until now for achieving optimal level of machining parameters by considering cryogenic treatment soaking duration as the process parameter. Few studies report application of deep cryogenic treatment (DCT) to enhance the tool life. However, their application severely limited to the number of single objective like tool wear and flank wear. It is also observed that little effort has been made to study the effect of cryogenic treatment on the micro-structural changes occurring in the tool material. Therefore, there exists a vital need to propose an efficient technological model which will lead to enhance the productivity of the process. So to bridge this gap, experimental investigation, minimization, and micro-structural analysis are carried out to study the effect deep cryogenic-treated end mill cutter on cutting force and power consumption in machining of P20 steel in CNC end milling process. P20 steel is selected as work material because these steels are capable of being machined into complex and large dies and molds. CNC end milling experiments were conducted on vertical CNC milling machine. Tungsten carbide end milling cutters were treated with DCT for various soaking durations. Scanning Electron Microscope (SEM) analysis was conducted to analyze the grain changes in the microstructure of the DCT-treated tools and untreated tools. ANOVA is used to find the significant process parameters influencing cutting forces and power consumption. Regression analysis is conducted to relate the process variables viz. cutting speed, feed, depth of cut, and cryogenic soaking duration with the cutting forces and power consumption. Finally, a non-dominated sorted Genetic Algorithm (NSGA-II) is used to obtain the optimal set of solutions because when compared with other methods, Genetic Algorithm (GA) technique is the best technique in multi-objective minimization and showed much attention by the researchers.
3. Response surface methodology
The design of experiments (DOE) technique is powerful work tool which allows us to model and analyze the influence of determined process variables over the specified variables, which are generally known as response variables. These response variables are unknown functions of the previous design variables, also known as design factors. Within the DOE, there are different types of methods that can be considered. One of the most widely known ones is the RSM. Using RSM the number of experimental runs can be reduced to a large extent and both effects of factors and their possible interactions can be studied and predictive equations can be generated and statistically validated. Generally, a second-order model shown in the Equation (1) is employed in RSM.
where Y is the output variable, X i ’s are input parameters, X i 2 and X i X j are the square and interaction terms of parameters, respectively. β 0, β i , β ii , and β ij are the unknown regression coefficients and ε is the error. The least square technique is being used to fit a model equation containing the input variables by minimizing the residual error measured by the sum of square deviations between the actual and estimated responses. The calculated coefficients or the model equations, however, need to be tested for statistical significance. ANOVA is used to check the adequacy of the model for the responses in the experimentation. F-ratio is the ratio between the regression mean square and the mean square error is calculated by ANOVA. If the calculated value of F-ratio is higher than the tabulated value of F-ratio for cutting force, then the model is adequate at desired significance level α to represent the relationship between machining response and the machining parameters.
To analyze the importance of individual parameters, the model is optimized by adding or deleting parameters through backward elimination, forward addition or stepwise elimination or addition. It involves the determination of value of p or probability of significance that relates the risk of erroneously rejecting a given hypothesis. If the value of p is less or equal to the selected α-level, then the effect of the variable is significant. If the value of p is greater than the selected α-value, then it is considered that the variable is insignificant. Sometimes the individual variables may not be significant. If the effect of interaction terms is significant, then the effect of each factor is different at different levels of the other factors. In the present study, ANOVA for cutting force and power consumption are carried out using Design Expert 10 software.
In this paper, the Box–Behnken design in RSM is used to design the experiments. The Box–Behnken design is an independent quadratic design, in that it does not contain an embedded factorial or fractional factorial design. In this design, the treatment combinations are at the midpoints of edges of the process space and at the center. Box–Behnken designs require fewer treatment combinations than a Central Composite Design for problems involving 3 or 4 factors (Vishnu Vardhan, Sankaraiah, & Yohan, Citation2017a).
4. Multi-objective optimization
In a single objective optimization problem, there is only one output criterion and such work has been studied over the past 50 years. When there is more than one objective, a different treatment is required. Real-world problems require simultaneous optimization of several incommensurable and often conflicting objectives. Often, there is no single optimal solution; rather, there is a set of alternative solutions. These solutions are optimal in the wider sense that no other solutions in the search space are superior to another when all objectives are considered. They are known as Pareto-optimal solutions. Mostly to obtain the best solutions for various design problems with different input data-sets minimization techniques are necessary. The multi-objective problems come up in the industries like design and manufacturing and aerospace applications. It is observed that, all the practical problems concerning multi-objective criterion with different constraints are creating a lot of interest toward the multi-objective minimization. These problems could be effectively solved with less computational effort and high accuracy. There are two goals in a multi-objective minimization: (i) convergence to the Pareto-optimal set; and (ii) maintenance of diversity and distribution in solutions. Compared to other methods Genetic Algorithm (GA) technique is the best technique in multi-objective minimization and showed much attention by the researchers. Genetic Algorithm (GA) is the prominent among the most popular Multi-Objective Evolutionary Algorithm (MOEA); a natural method of evolution with eminence on reproduction and the survival of the fittest. Genetic Algorithm’s simulates the survival of fittest among individuals over a successive generation to solve the problem. The individuals in the population are then made to experience a process of evolution. First, a preliminary population is arbitrarily created; the genetic algorithm has three operators:
(a) | Selection operator which compares to survival of the fittest; | ||||
(b) | Crossover operator which resembles mating between individuals; | ||||
(c) | Mutation operator represents arbitrary modifications. |
These operators provide the search way toward a GA. The Genetic Algorithm flow chart is shown in .
A non-dominated sorting genetic algorithm II (NSGA II) is a MOEA derived from non-dominated sorting. To find the non-dominated set of solutions; this algorithm utilizes elitist non-dominated sorting. Constrained multi-objective minimization problems are handled by this algorithm through binary codes and actual parameter. Here, variables are coded by a suitable objective function. Once a definite number of generations are completed, this algorithm produces the non-dominated solution set out of the total population. The non-dominated solution set, i.e. Pareto-front solution set, is obtained from the convergence of the algorithm. Based on ranking and crowding distance, with the help of crowded-comparison operator optimal solution set is selected (Vishnu Vardhan, Sankaraiah, & Yohan, Citation2017b).
5. Experimental procedure
A Box–Behnken design of RSM is used to collect data for the study because it performs non-sequential experiments having fewer design points (Kadirgama et al., Citation2008). It works in the safe operating zone for the process as such a design does not have axial points. It helps to create a suitable functional relationship between input parameters on output. The cutting tool selected for the present investigation was tungsten carbide end mill cutter with four flutes by the recommendations of manufacturer. Tungsten Carbide end mill cutter is used for machining hard materials. The commercially available tungsten carbide end mill cutter with 12 mm diameter, 40 mm long (ISO specification) with four flutes were procured for machining of P20 steel with dimensions 100 × 100 × 10 mm. They have the hardness in the range of 28–37 HRC. Tungsten carbide has a high melting point at 2870 °C, a boiling point of 6000 °C when under a pressure equivalent to 1 standard atmosphere (100 kPa), a thermal conductivity of 110 Wm−1 K−1.
The flow chart of the experimentation is shown in . Three different tungsten carbide end mill cutters were procured as one Untreated tool (UT), and two DCT tools subjected to various soaking duration. Cutting tools have been subjected to DCT in which they were cryotreated in the indigenously developed cryotreatment system for 24 and 36 h at 98 K with 3 h of cooling and 8 h of warm up to room temperature as shown in . The cryogenic treatment system is shown in .
The main aim of the machining experiment is to study the effect of cryogenically treated tungsten carbide end mill cutting tools on cutting forces and power consumption while machining P20 steel material in CNC milling process. The machining parameters used were selected based on the recommendation of manufacturer’s catalog and ISO standards are shown .
Table 1. Machining parameters and their level used.
CNC end milling experiments was performed at Central Institute of Tool Design (CITD), Hyderabad on a vertical CNC milling machine with boron based water soluble solution is used as a coolant as shown in . The experiments were performed to investigate the effect of cutting speed, feed, depth of cut, and cryogenic soaking duration on performance measures viz. cutting forces, Power consumption. The P20 steel work material and tungsten carbide end mill cutting tools used in the experiment are shown in .
Twenty-nine experiments were conducted based on Box–Behnken design from RSM as shown in . Each experimental run is continued for 10 min. and the time is recorded with a stopwatch. During machining, force measurements are generally taken by means of a table mounted dynamometer. These dynamometers determine the cutting forces in three mutually perpendicular directions. A Kistler RCD type 9171A Piezo electric dynamometer was mounted on the table using fixture and P20 steel work piece was clamped on to the dynamometer directly. The force components in x, y , and z directions is collected by amplifier and Dynoware software. Similar calculation is done somewhere else (Jaya kumar et al., Citation2012). The resultant force F r is calculated based on the Equation (2).
Table 2. Experimental results.
A set of Wattmeter’s were used to quantify power consumption and the readings were noted after multiplying by an appropriate multiplying factor to obtain power consumption in Watts.
6. Results and discussions
As mentioned earlier, cryogenic treatment trials were conducted on the tungsten carbide end mill cutters. The experimental results are tabulated in . The analysis was done on the experimental data collected based on Box–Behnken design to establish the connection of various input parameters on the performance measures using ANOVA at a significant level of .05.
shows ANOVA for cutting force after eliminating the insignificant parameters. The parameters cutting speed, feed, depth of cut, and cryogenic soaking duration, and square terms feed, and depth of cut are found to be the most significant parameters. shows ANOVA for power consumption after eliminating the insignificant parameters. The parameters such as cutting speed, feed, and cryogenic soaking duration, and interactions terms cutting speed x Cryogenic soaking duration, feed x cryogenic soaking duration are found to be the most significant parameters. The Percentage contribution is also shown in ANOVA table. From the ANOVA table, it is observed that most significant parameter influencing the cutting force and power consumption is DCT soaking duration.
Table 3. ANOVA table for cutting force.
Table 4. ANOVA for power consumption.
The coefficient of determination (R2), adjusted R2, and Pred R-Squared values are 85.3, 77.7, 64.65% for cutting force and 96.08, 94.51, 90.8% for power consumption; it is observed that the lack of fit is not significant to the response, meaning there is a no missing term in the model.
(a) shows the surface plot of variation in cutting force with cutting speed and cryogenic soaking duration. The advantage of deep cryogenic-treated tool over untreated tool can be clearly seen in the (a). Cutting force is less when machined with DCT tool with soaking duration for 36 and 24 h compared to untreated tool (Sreerama Reddy et al., Citation2009a). In between the two different cryo-treated soaking duration tools, 36-h-soaked tool showed better performance than 24-h-soaked tool. Cryogenic treatment contributes appreciably in cooling the tool tip by dissipating heat to the surroundings by enhancing the thermal conductivity of the tool (Sreerama Reddy, Sorna Kumar, Venkatarama Reddy, & Venkatram, Citation2008). So if cutting speed increases, the heat generated in the shear zone cannot be conducted away from work piece during the very short time. So, the temperature rise softens the work material aiding grain boundary dislocation and thus reduces cutting forces (Dhananchezian, Pradeep Kumar, & Sorna Kumar, Citation2011). Thus, cutting force is decreasing with increase in cutting speed. (b) shows the surface plot of variation in cutting force with cutting speed and feed. Cutting force is increasing with increase in feed.
Figure 7. Surface plot of cutting force with (a) Cutting speed and cryogenic soaking duration. (b) Cutting speed and feed. (c) Feed and depth of cut. (d) Feed and cryogenic soaking duration.
(c) shows the surface plot of variation in cutting force with feed and depth of cut. It is clear from the (c) that cutting force increases with increase in feed. The cutting force is directly proportional to the feed. Cutting force was observed to be greater at higher feed. This is because at higher feeds more material is to be removed; as a result, more energy is required. This causes an increase in the cutting force. Cutting force is also increasing with increase in depth of cut (Karabulut, Citation2015). (d) shows the surface plot of variation in cutting force with feed and cryogenic soaking duration. It is clearly seen from surface plot that with DCT tool, cutting forces acting on machining is reduced.
(a) shows the surface plot of variation in power consumption with cutting speed and feed. It is clear from the surface plot that power consumption is increasing with increase in cutting speed and feed. It is due to fact that with increase in cutting speed, less time available for the work piece material to adhere or weld temporarily on the tool tip, the power consumption falls down, and again increases as usual with increased depth of cut shown in surface plot (b) (Aggarwal et al., Citation2008). All the main effect plots show that the major effect on the responses is due to cutting speed and very little effect due to feed rate and depth of cut. (c) shows the surface plot of variation in power consumption with depth of cut and feed. The Figures and shows the normal plot of residuals and contour plots of cutting force and power consumption. The normal probability plot is a graphical method to recognize substantive departures from normality. Normal probability plots are prepared from raw data, residuals from model fits, and estimated parameters. A contour plot is a graphical method of representing a 3D surface by plotting contours on a 2D surface. The micro-structural analysis on tungsten carbide cutting tools was conducted using ZEISS scanning electron microscope (SEM) at DRDL, Hyd. The microstructure of DCT and untreated tungsten carbide cutting tool is shown in (a) and (b). The main phases can be observed in the microstructure of tungsten carbides are α-phase (WC), β phase (Cobalt binder), and η phase (multiple carbide tungsten and at least one metal binder). Gray angular shaped grains represent α-phase, white grains represent β phase, dark gray grains represents η phase. γ phase (TaC, TiC, etc.) phase is not seen because of less presence of TiC and TaC (Singh et al., Citation2011). The η phase is a carbon deficient form of tungsten carbide that results in a harder, more brittle tungsten carbide part. The fine η particles are formed during the long exposure to DCT as clearly seen in (a) and (b). These fine η particles form a denser and tougher matrix in the material. The cryogenic treatment lowers the β phase, i.e. cobalt binder. This causes the increase in tool life and reduces the tool wear and hence reduces the cutting force (Sreerama Reddy et al., Citation2009b).
Figure 8. Surface plots of power consumption with (a) Cutting speed and feed. (b) Depth of cut and cryogenic soaking duration. (c) Feed and depth of cut.
Figure 11. SEM microstructures (a) DCT tungsten carbide tools (36 h soaking duration). (b) Untreated tool.
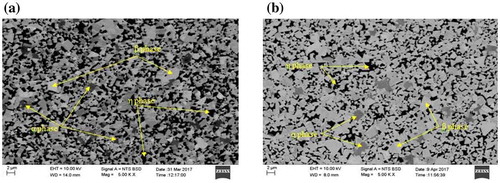
Surface morphology of the P20 work material was tested using JEOL JSM 5500 Scanning Electron Microscope (SEM) at Ruska labs, Hyderabad. (a) and (b) show SEM micrographs of machined surface with DCT with soaking duration of 36 h and untreated tool. It is clearly seen from the SEM graphs that DCT tool performed machining effectively when compared to untreated tool. Surface quality is also improved.
Figure 12. SEM micrographs of Machined surface (a) A = 85 mm/min, B = .15 mm/tooth, C = 1 mm, D = DCT 36 h (b) A = 85 mm/min, B = .15 mm/tooth, C = 1 mm, D = DCT 0 h (untreated tool).
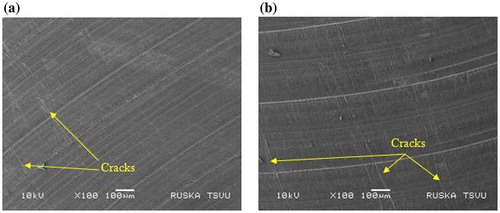
In this paper, two responses such as cutting force and power consumption are considered. The final relation between input parameters and output responses in terms of actual factors formed from the RSM method is utilized as an objective function to solve the minimization problem.
In this study, the goals are minimization of cutting forces and power consumption. The relations obtained in Equations (3) and (4) between input parameters and output responses are utilized as functional relations. NSGA II algorithm is used in MATLAB to solve the minimization problems:
Minimize {f(x), g(x)}
Subject to
The functions of f(x) and g(x) represents the cutting force and power consumption, which are unknown and to be fitted from the experimental values and A, B, C, and D represent cutting force, feed, depth of cut, and cryogenic soaking duration (1 represents untreated, 2 represents 24-h-treated, and 3 represents 36-h-treated tool).
At this point a primary population size of 70 is considered and minimization is performed. Based on NSGA-II algorithm, rankings and sorting of solutions are done and the final Pareto-optimal solutions set are shown in . is drawn to judge the Pareto front of cutting force vs. power consumption. It is eminent that all the solutions are simultaneously excellent and any solution set of process parameters can be taken to attain the equivalent response values depending upon machining conditions.
Table 5. Pareto-optimal solutions.
7. Conclusions
Based on the experimental investigation and analysis of results, it can be concluded that:
Cutting speed, feed, depth of cut, and cryogenic soaking duration are found to be the significant parameters influencing cutting force and power consumption.
From ANOVA table of cutting force it is observed that cryogenic soaking duration is the most significant parameter influencing the cutting force with 55% followed by feed with 14%, depth of cut with 11%, and cutting speed with 8%.
From ANOVA table of Power consumption it is observed that cutting speed is the most significant parameter influencing the power consumption with 57% followed by cryogenic soaking duration with 37%, depth of cut with 1.69%, and feed with 1.65%.
Cutting force is decreasing with increase in cutting speed, and it is increasing with increase in feed and depth of cut. Power consumption is increasing with increase in cutting speed, feed, and depth of cut.
While machining, it is observed that cutting force is less with 36-h-soaked DCT cutting tool compared with 24-h-soaked DCT tool and untreated cutting tools. So DCT-36 h soaking duration cutting tool is most favorable for machining of P20 steel than DCT-24 h soaking duration cutting tools and untreated tools.
It is also observed that power consumption is less while machining with DCT cutting tools compared to untreated tools especially with 36-h-soaked cutting tool.
It can be noticed from micro-structural analysis that, subjecting tool to DCT results in increased thermal conductivity of the tungsten carbide material due to proper alignment of grains in the structure, resulting in decrease in tool tip temperature and improved surface quality during milling operation.
So it can be concluded from the experimental results and micro-structural analysis that DCT on tungsten carbide cutting tools reduced the cutting forces acting on the tool and also reduced the power consumption during machining.
Effect of cryogenic treatment soaking duration of tools on responses such as tool wear rate, flank wear, material removal rate, surface roughness and tool life need to be studied for further enhancement of machining process.
Disclosure statement
No potential conflict of interest was reported by the authors.
Acknowledgements
The authors hereby thank Mr. Durgesh Nadig, Senior Scientific Officer, Indian Institute of Science Bangalore, India for cryogenic treatment of cutting tools. Authors also acknowledge the support of Dr. Parthoghosal, Scientist F, DMRL Hyderabad, India for SEM analysis.
References
- Abou-El-Hossein, K. A., Kadirgama, K., & Hamdi, M. (2007). Prediction of cutting force in end milling operation of modified AISI P20 tool steel. Journal of Materials Processing Technology, 182(1–3), 241–247.10.1016/j.jmatprotec.2006.07.037
- Aggarwal, A., Singh, H., Kumar, P., & Singh, M. (2008). Minimization of multiple quality characteristics for CNC turning under cryogenic cutting environment using desirability function. Journal of Materials Processing Technology, 205, 42–50.10.1016/j.jmatprotec.2007.11.105
- Campatelli, G., & Scippa, A. (2012). Prediction of milling cutting force coefficients for Aluminum 6082-T4. 5th CIRP Conference on High Performance Cutting, Zurich, Switzerland.
- Chopra, S. A., & Sargade, V. G. (2015). Metallurgy behind the Cryogenic Treatment of Cutting Tools: An overview. Materials Today: Proceedings, 2, 1814–1824. doi:10.1016/j.matpr.2015.07.119
- Dhananchezian, M., Pradeep Kumar, M., & Sorna Kumar, T. (2011). Cryogenic turning of AISI 304 stainless steel with modified tungsten carbide tool inserts. Materials and Manufacturing Processes, 26, 781–785.10.1080/10426911003720821
- Dieringa, H. (2017). Influence of cryogenic temperatures on the microstructure and mechanical properties of magnesium alloys: A review. Metals, 7, 38. doi:10.3390/met7020038
- Giasin, K., Ayvar-Soberanis, S., & Hodzic, A. (2016). Evaluation of cryogenic cooling and minimum quantity lubrication effects on machining GLARE laminates using design of experiments. Journal of Cleaner Production, 135, 533–548. doi:10.1016/j.jclepro.2016.06.098
- Ghosh, C. S., & Rao, P. V. (2017). Performance evaluation of deep cryogenic processed carbide inserts during dry turning of Nimonic 90 aerospace grade alloy. Tribology International, 115, 397–408. doi:10.1016/j.triboint.2017.06.013
- Gao, Y., Luo, B. H., Bai, Z. H., Zhu, Z., & Ouyang, S. (2016). Effects of deep cryogenic treatment on the microstructure and properties of WC-Fe-Ni tungsten carbides. International Journal of Refractory Metals and Hard Materials, 58, 42–50. doi:10.1016/j.ijrmhm.2016.03.010
- Gill, S. S., Singh, H., Singh, R., & Singh, J. (2011). Flank wear and machining performance of cryogenically treated tungsten carbide inserts. Materials and Manufacturing Processes, 26, 1430–1441.10.1080/10426914.2011.557128
- Jaya kumar, K., Mathew, J., & Joseph, M. A. (2012). An investigation of cutting force and tool–work interface temperature in milling of Al–SiCp metal matrix composite. Proceedings of the Institution of Mechanical Engineers, Part B: Journal of Engineering Manufacture, 227(3), 362–374.
- Kadirgama, K., Abou-El-Hossein, K. A., Mohammad, B., AL-Ani, H., & Noor, M. M. (2008). Cutting force prediction model by FEA and RSM when machining Hastelloy C-22HS with 90○ holder. Journal of Scientific & Industrial Research, 67, 521–427.
- Kalsi, N. S., Segal, R., & Sharma, V. S. (2010). Cryogenic Treatment of Tool Materials: A Review. Materials and Manufacturing Processes, 25(10), 1077–1100.10.1080/10426911003720862
- Kalyan Kumar, K. V. B. S., & Choudhury, S. K. (2008). Investigation of tool wear and cutting force in cryogenic machining using design of experiments. Journal of Materials Processing Technology, 203, 95–101.10.1016/j.jmatprotec.2007.10.036
- Karabulut, S. (2015). Minimization of surface roughness and cutting force during AA7039/Al2O3 metal matrix composites milling using neural networks and Taguchi method. Measurement, 66, 139–149.10.1016/j.measurement.2015.01.027
- Khan, A. A., & Ahmed, M. I. (2008). Improving tool life using cryogenic cooling. Journal of Materials Processing Technology, 196(1–3), 149–154.10.1016/j.jmatprotec.2007.05.030
- Kondayya, D., & Krishna, G. A. (2012). An integrated evolutionary approach for modeling and minimization of CNC end milling process. International Journal of Computer Integrated Manufacturing, 25(11), 1069–1084.10.1080/0951192X.2012.684718
- Li, H. Z., & Li, X. P. (2002). Milling force prediction using a dynamic shear length model. International Journal of Machine Tools and Manufacture, 42, 277–286.10.1016/S0890-6955(01)00098-0
- Li, S., Min, N., Li, J., & Xiaochun, W. (2013). Internal friction measurements of phase transformations during the process of deep cryogenic treatment of a tool steel. Cryogenics, 57, 1–5. doi:10.1016/j.cryogenics.2013.03.003
- Li, J., Yan, X., Liang, X., Hong, G., & Li, D. Y. (2016). Influence of different cryogenic treatments on high-temperature wear behaviour of M2 steel. Wear, 376, 1112–1121. doi:10.1016/j.wear.2016.11.041
- Nalbant, M., & Yildiz, Y. (2011). Effect of cryogenic cooling in milling process of AISI 304 stainless steel. Transactions of Nonferrous Metals Society of China, 21, 72–79.10.1016/S1003-6326(11)60680-8
- Özbek, N. A., Çiçek, A., Gülesin, M., & Özbek, O. (2015). Effect of cutting conditions on wear performance of cryogenically treated tungsten carbide inserts in dry turning of stainless steel. Tribology International, 94, 223–233. doi:10.1016/j.triboint.2015.08.024
- Perez, M., & Belzunce, F. J. (2014). The effect of deep cryogenic treatments on the mechanical properties of AISI H13 steel. Materials Science & Engineering A, 624, 32–40. doi:10.1016/j.msea.2014.11.051
- Pilligrin, C. J., Asokan, P., Jerald, J., & Kanagaraj, G. (2017a). Tool speed and polarity effects in micro-EDM drilling of 316L stainless steel. Production & Manufacturing Research, 5(1), 99–117.10.1080/21693277.2017.1357055
- Pilligrin, C. J., Asokan, P., Jerald, J., & Kanagaraj, G. (2017b). Effects of electrode materials on performance measures of electrical discharge micro-machining. Materials and Manufacturing Processes, 33(6),1–10. doi:10.1080/10426914.2017.1364757
- Podgornik, B., Paulin, I., Zajec, B., Jacobson, S., & Leskovšek, V. (2016). Deep cryogenic treatment of tool steels. Journal of Materials Processing Technology, 229, 398–406. doi:10.1016/j.jmatprotec.2015.09.045
- Safari, H., Sharif, S., Izman, S., Jafari, H., & Kurniawan, D. (2014). Cutting force and surface roughness characterization in cryogenic high-speed end milling of Ti–6Al-4 V ELI. Materials and Manufacturing Processes, 29, 350–356.10.1080/10426914.2013.872257
- Sartori, S., Moro, L., Ghiotti, A., & Bruschi, S. (2016). On the tool wear mechanisms in dry and cryogenic turning Additive Manufactured titanium alloys. Tribiology International, 105, 264–273. doi:10.1016/j.triboint.2016.09.034
- Singh, S., Singh, S., & Singh, J. (2011). Improvement in tool life of M2HSS tools by cryogenic treatment. Journal of Metallurgical Engineering, 1, 47–61.
- Sobotova, J., Jurci, P., & Dlouhy, I. (2016). The effect of subzero treatment on microstructure, fracture toughness, and wear resistance of Vanadis 6 tool steel. Materials Science & Engineering A, 652, 192–204. doi:10.1016/j.msea.2015.11.078
- Sreerama Reddy, T. V., Sorna Kumar, T., Venkatarama Reddy, M., & Venkatram, R. (2008). Machining performance of low temperature treated P-30 tungsten carbide cutting tool inserts. Cryogenics, 48, 458–461.10.1016/j.cryogenics.2008.06.001
- Sreerama Reddy, T. V., Sorna Kumar, T., Venkatarama Reddy, M., Venkatram, R., & Senthil Kumar, A. (2009a). Turning studies of deep cryogenic treated p-40 tungsten carbide cutting tool inserts – technical communication. Machining Science and Technology, 13, 269–281.10.1080/10910340902979754
- Sreerama Reddy, T. V., Sorna Kumar, T., Venkatarama Reddy, M., & Venkatram, R. (2009b). Machinability of C45 steel with deep cryogenic treated tungsten carbide cutting tool inserts. International Journal of Refractory Metals and Hard Materials, 27, 181–185.10.1016/j.ijrmhm.2008.04.007
- Suresh Kumar Reddy, N., & Venkateswara Rao, P. (2006). Experimental investigation to study the effect of solid lubricants on cutting forces and surface quality in end milling. International Journal of Machine Tools & Manufacture, 46, 189–198.10.1016/j.ijmachtools.2005.04.008
- Thamizhmanii, S., Mohideen, R., Zaidi, A. M. A., & Hasan, S. (2015). Surface roughness and tool wear on cryogenic treated CBN insert on titanium and inconel 718 alloy steel. IOP Conference Series: Materials Science and Engineering, 100, 012058. doi:10.1088/1757-899X/100/1/012058
- Thamizhmanii, S., Nagib, M., & Sulaiman, H. (2011). Performance of deep cryogenically treated and non-treated PVD inserts in milling. Journal of Achievements in Materials and Manufacturing Engineering, 49(2), 460–466.
- Turgut, Y., Cxinici, H., & Sxahin, I. (2011). Study of cutting force and surface roughness in milling of Al/SiC metal matrix composites. Sci Res Essays, 6(10), 2056–2062.
- Vishnu Vardhan, M., Sankaraiah, G., & Yohan, M. (2017a). Optimization of parameters in CNC milling of P20 steel using response surface methodology and Taguchi method. Materials Today: Proceedings, 4, 9163–9169.10.1016/j.matpr.2017.07.273
- Vishnu Vardhan, M., Sankaraiah, G., & Yohan, M. (2017b). Performance evaluation of deep cryogenic treated tools at different temperatures in CNC milling. ARPN Journal of Engineering and Applied Sciences, 12, 7262–7273.
- Wang, F., Liu, J., & Shu, Q. (2017). Minimization of cryogenic milling parameters for AFRP. International Journal of Advanced Manufacturing Technology, 91, 3243–3252. doi:10.1007/s00170-017-0003-0
- Xie, C.-H., Huang, J.-W., Tang, Y.-F., & GU, L.-N. (2015). Effects of deep cryogenic treatment on microstructure and properties of WC−11Co tungsten carbides with various carbon contents. Transactions of Nonferrous Metals Society of China, 25, 3023–3028. doi:10.1016/S1003-6326(15)63929-2
- Yan, X. G., & Li, D. Y. (2013). Effects of the sub-zero treatment condition on microstructure, mechanical behavior and wear resistance of W9Mo3Cr4 V high speed steel. Wear, 302, 854–862. doi:10.1016/j.wear.2012.12.037
- Yong, A. Y. L., Seah, K. H. W., & Rahman, M. (2007). Performance of cryogenically treated tungsten carbide tools in milling operations. The International Journal of Advanced Manufacturing Technology, 32(7–8), 638–643.10.1007/s00170-005-0379-0
- Yun, W. S., & Cho, D. W. (2001). Accurate 3-D cutting force prediction using cutting condition independent coefficients in end milling. International Journal of Machine Tools and Manufacture, 41, 463–478.10.1016/S0890-6955(00)00097-3
- Zheng, L., Chiou, Y. S., & Liang, S. Y. (1996). Three dimensional cutting force analysis in end milling. International Journal of Mechanical Sciences, 38(3), 259–269.10.1016/0020-7403(95)00057-7