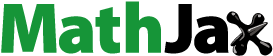
ABSTRACT
High-entropy ceramics have emerged as a research hotspot in the field of ceramics due to their single-crystal structure and excellent physicochemical properties. In this paper, an innovative approach is adopted to synthesize high-entropy nitride ceramics (TiVCrNbZr1-x)Ny. To achieve this, the non-stoichiometric compound TiN0.3 was introduced as a sintering additive and the Spark Plasma Sintering (SPS) technique was employed. By adding TiN0.3, successfully preparing high-entropy nitride ceramics at 1500°C, which introduces vacancy defects that provide additional space for the diffusion and migration of atoms, allowing for more efficient migration and diffusion within the crystal structure, thereby accelerating the sintering process. The (TiVCrNbZr1-x)Ny- xZrO2 samples achieved outstanding mechanical properties when sintered at 1700°C, owing to the mechanisms of solid solution strengthening and second-phase diffusion toughening. Specifically, the samples exhibited a hardness of 25.42 ± 1.58 GPa, a flexural strength of 888 ± 32 MPa, and a fracture toughness of 6.23 ± 0.27 MPa·m1/2. This innovative sintering route provides an efficient method for preparing high-entropy nitride ceramics at relatively low temperatures without sacrificing quality. This approach not only enhances production efficiency but also expands the potential practical applications of these ceramics.
1. Introduction
Materials science currently faces the great challenge of continuously searching for advanced materials that can meet the demands of rapidly developing new technologies. This challenge arises from the need to step out of the confines of traditional material design concepts and explore new materials from a fresh perspective. Such exploration represents both a trend in scientific and technological development and a means for overcoming the limitations of existing materials’ performance [Citation1,Citation2]. High-entropy materials, a recently emerging class of materials, defy traditional material design concepts. These new materials consist of a diverse range of elements in roughly equal proportions, forming a unique type of multi-principal element material. This breakthrough in material design opens up new possibilities for innovative material development [Citation3].
As research progresses, the design concept of High-Entropy Alloys has extended into the field of ceramics. In 2014, Murty [Citation4] highlighted the presence of the high-entropy effect in ceramics and introduced the concept of “High-Entropy Ceramics”. Subsequently, in 2015, Rost [Citation5] successfully synthesized (Mg0.2Co0.2Ni0.2Zn0.2Cu0.2)O oxide high-entropy ceramics, marking significant progress in this area [Citation6]. Unlike high-entropy alloys, high-entropy ceramics are intricate structures comprising multiple components such as cations, anions, and defects at specific locations, providing greater flexibility for component design and performance optimization. High-entropy ceramics demonstrate exceptional hardness and modulus, good oxidation resistance, and low thermal conductivity, positioning them at the forefront of ceramic research [Citation7].
Research on high-entropy nitrides is still in its early stages. As early as 2004, Yeh’s team [Citation8] conducted research involving high-entropy alloy thin-film materials, demonstrating excellent mechanical properties for thin-film applications. Subsequent studies on high-entropy nitride thin films have been limited to thin-film materials [Citation8–11]. However, in 2018, Jin et al. [Citation12] proposed a new method for preparing high-entropy metal nitride (VCrZrNbMo)N powders using a mechanically soft urea method, synthesizing them from metal chloride and urea precursors at 800°C, and demonstrating excellent electrochemical properties. In 2020, Dmitry Moskovskikh et al. [Citation13] successfully obtained high-entropy nitride phases through the combustion reaction of mechanically activated nanostructured metal precursors in nitrogen, producing bulk high-entropy nitride (Hf0.2Nb0.2Ta0.2Ti0.2Zr0.2)N via discharge plasma sintering, exhibiting exceptional hardness and fracture toughness surpassing expected properties based on mixing rules. More recently, Lu Youjun’s team [Citation14] proposed a “soft mechanochemical-assisted nitride thermal reduction method” to prepare high-entropy nitride ceramics (HENCs) using metal oxides that can be converted to corresponding metal nitrides by reacting with Si3N4, successfully producing (HfZrTiNbTa)N high-entropy powders in complete solid solution. Despite being at an early stage, this research shows promise for the mechanical and electrochemical application of high-entropy nitrides. Future research will further advance the preparation, property optimization, and application areas of high-entropy nitrides.
The high-entropy effect in high-entropy materials involves increasing conformational entropy within the material system by introducing diverse group elements. This promotes the formation of solid solution phases, leading to a more complex and diverse crystal structure. This complexity enhances the material’s possibilities and diversities, ultimately improving its performance. In multifunctional material systems, each atom is surrounded by a variety of atoms, experiencing simultaneous lattice strain and stress. This dual influence results in significant distortions in the lattice structure, potentially impacting the material’s mechanical properties. This phenomenon offers novel insights and approaches for material design and application, expanding the realm of materials science research and unlocking new avenues for optimizing and innovating material properties.
In this study, a homemade non-stoichiometric compound TiN0.3 was utilized as a sintering aid, mixed equimolarly with VN, CrN, NbN, and ZrN in a 1:1:1:1:1 ratio. Spark Plasma Sintering (SPS) technique was employed with a holding time of 20 minutes to investigate the impact of various sintering temperatures on the structural and mechanical properties of the sample. X-ray diffraction (XRD) and microstructural characterization of (TiVCrNbZr1-x)Ny-xZrO2 HENCs confirmed their synthesis and revealed the influence of different sintering temperatures on their structure and properties.
2. Experiments
2.1. Raw materials
TiN0.3 was obtained by mechanical alloying reaction of Ti and TiN in the ratio of 2:1, and the other raw materials used were VN, CrN, NbN, ZrN, with a purity of 99.9% and a particle size of 3 ~ 10 μm (purchased from Shanghai Nano Technology Co., Ltd. (China)).
2.2. Sintering of samples
TiN0.3, along with VN, CrN, NbN, and ZrN in an equimolar ratio of 1:1:1:1:1, was added to a ball milling tank with a ball-to-material ratio of 10:1 and milled for 10 hours. The resulting mixture was dried at 90°C and subjected to high-temperature vacuum sintering in an SPS furnace. The sintering temperature, temperature increase rate, holding time, and pressure were 1400–1800°C, 50℃/min, 20 minutes, and 50 MPa, respectively. (TiVCrNbZr1-x)Ny-xZrO2 synthesized at different temperatures, namely N5–1400, N5–1500, N5–1600, N5–1700, and N5–1800, were investigated. illustrates the synthesis of TiN0.3 as well as the sintering of the samples and performance testing flowchart. The experimental procedure is described as follows:
2.3. Characterization of samples
The sintered high-entropy ceramic samples underwent grinding and polishing using a diamond polishing machine. The physical phase compositions of TiN0.3 and the high-entropy ceramics were analyzed via X-ray diffraction (XRD) (X’Pert PRO, Panalytical, the Netherlands). Microstructures and elemental maps of the high-entropy nitride ceramic sections were examined using scanning electron microscopy (SEM, S-4800, Hitachi High-Tech/Oxford Instruments, Japan/UK) in combination with its Energetic Dispersive Spectrometer (EDS). The bending strength of the sintered samples was measured using a three-point bending test method on a universal mechanical testing machine (AG-150 KN, Shimadzu, Japan); the Vickers microhardness of the polished samples was determined with a microhardness tester (EV-1000 L, Shanghai Hengyi Precision Instruments Co., Ltd.) under an applied load of 3 kgf and an indentation time of 10 seconds. Fracture toughness was evaluated based on the length of indentation-induced crack extension and calculated using the empirical formula [Citation15]:
where P is the indentation load value; a is the diagonal crack length.
The flexural strength of the sintered samples was tested on a universal mechanical testing machine (AG-150 KN, Shimadzu, Japan) using the three-point flexural testing method, and the three-point flexural strength was calculated using the following formula:
Where, σf-bending strength (MPa), L-span (mm), F-bending loading pressure, h-sample thickness (mm), B-sample diameter (mm).
3. Results and discussions
The XRD diffraction peaks of HENCs, prepared by SPS densification and sintering using non-stoichiometric TiN0.3 and stoichiometric VN, CrN, NbN, and ZrN powders (mixed in equimolar ratio of 1:1:1:1:1:1) as starting materials, are shown in . At 1400°C, the compounds did not completely solidify to form a single phase. However, with continued sintering at 1500°C, the compounds completely solidified and obtained HENCs with face-centered-cubic (FCC) structure as the main phase, with the space group Fmm. On the other hand, the sintered bodies synthesized with stoichiometric TiN as the precursor under the same synthetic process at 1600°C did not exhibit a single-phase structure. In addition to the face-centered cubic phase, there were incompletely reacted VN, ZrN, and NbN residues in the sintered body. The presence of nitrogen vacancy defects accelerated the formation of single-phase face-centered cubic (FCC) HENCs and lowered the synthesis temperature. Besides the FCC structure, the impurity phase ZrO2 was also present due to the oxidation of ZrN during high-temperature sintering [Citation16,Citation17]. The oxides were introduced because of unavoidable oxidative contamination during sintering under low-vacuum conditions.
Figure 2. XRD data of five transition metal nitrides under Cu Kα radiation after SPS at different temperatures.
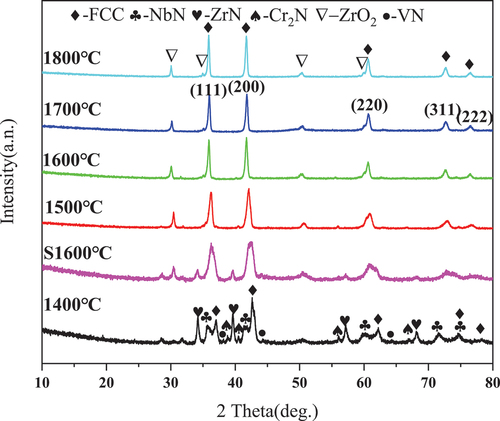
Nitrogen vacancies can promote the formation of HENCs at lower temperatures for two main reasons. First, from a thermodynamic perspective, the introduction of anionic vacancies increases the entropy of mixing and reduces the enthalpy of mixing, thereby maximizing the reduction in the system’s Gibbs free energy and improving its thermodynamic stability. Second, from a diffusion kinetics analysis perspective, vacancies lower the activation energy for metal atom diffusion, leading to accelerated atomic diffusion and the promotion of single-phase solid solution formation (Nitrogen vacancies effectively lower the activation energy required for metal atom diffusion, thus enhancing their mobility within the crystal lattice. As metal atoms traverse through the lattice, they encounter nitrogen vacancies, enabling them to swiftly transition to adjacent sites. Consequently, the presence of nitrogen vacancies accelerates the diffusion kinetics of metal atoms, thereby fostering the formation of metal crystals and facilitating phase transitions.) [Citation18,Citation19]. Additionally, the presence of nitrogen vacancies results in the formation of metallic Ti-Ti bonds between adjacent Ti atoms in TiNx and a decrease in the strong covalent bonding properties of TiNx [Citation20,Citation21]. This change in covalent bonding properties lowers the melting point of TiNx and enhances its sintering ability [Citation22,Citation23].
Based on the table, it is evident that the ZrO2 content exhibits a gradual decrease with rising temperature. Elevated temperatures can alter the reaction equilibrium constants, causing a shift in the equilibrium position toward the conversion of ZrO2 into other compounds, thereby reducing the ZrO2 content. Specifically, high temperatures may induce reactions between ZrO2 and other elements or compounds, resulting in the formation of new compounds or solid solutions. These newly formed entities may diminish the original ZrO2 content, leading to a declining trend as temperature increases. However, the extent of conversion to other oxides might be minimal and undetectable through XRD analysis.
Table 1. Weight percentage of ZrO2 at different temperatures.
The SEM images in reveal significant differences in the fracture surfaces of the HENCs. Control group A sintered at 1600°C exhibited poor sintering with noticeable air holes, while the addition of vacancies at the same temperature facilitated material diffusion during sintering, resulting in significantly improved sintering performance, nearly invisible pores, and denser crystal structures. Comparison of shows a gradual reduction in pore size as temperature increases, accompanied by improved crystallinity and larger grain size. Additionally, the fracture surface appears relatively flat, suggesting predominantly through-crystalline fracture.
Figure 3. SEM schematic of SPS sintered samples at different temperatures: A: S1600°C, B: 1400°C, C: 1500°C, D: 1600°C, E: 1700°C, F: 1800°C.
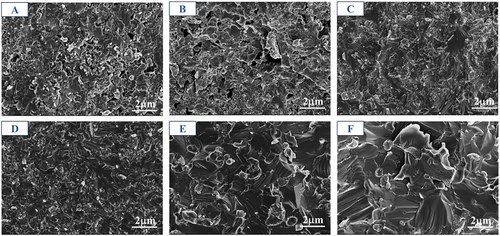
Elemental analysis was conducted on the samples sintered at 1700°C using EDS to obtain their elemental distribution. illustrates the elemental distribution, while presents the elemental content and spectrograms obtained by scanning the small particles at distinct points. Additionally, provides the statistics of the face-scanning elemental content data for the samples in –F). In , uniform distribution of Ti, V, Nb, and Cr elements was observed, whereas Zr elements appeared to be more enriched. Further point scanning of small particles, such as point 1 in , was performed, through which a high content of O and Zr elements was found (as shown in ). Consequently, it is speculated that these small particles consisted of ZrO2, consistent with the X-ray diffraction (XRD) test results in . indicates the element content in the samples at 1400℃-1800°C, showing that the atomic percentage of Ti, V, Cr, Zr, and Nb was nearly 1:1:1:1:1. Due to unavoidable oxygen contamination during mixing and sintering, the samples also contained a small amount of oxygen element.
Figure 5. Point scanning of small particle point 1 in (A): (B) elemental content distribution map, (C) spectrograms.
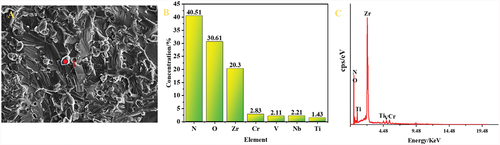
Table 2. Elemental content under EDS surface scanning at different sintering temperatures.
The microstructure of the sintered body at the nanoscale was analyzed using Scanning Transmission Electron Microscopy (STEM), as illustrated in . presents a bright field image (BF-STEM) plot of the (TiVCrNbZr1-x)Ny-xZrO2 sintered body at a sintering temperature of 1700°C, which indicates good sintering condition and absence of porosity at the nanoscale. displays an electron diffraction (SAED) pattern in the [001] band axis, which confirms the face-centered cubic structure of the sample and is consistent with the XRD results in . shows a High-Resolution Transmission Electron Microscopy (HRTEM) image of the sample, revealing clear observation of the lattice stripes, while also displaying noticeable lattice torsion and distortion within the crystal [Citation23]. These lattice defects are likely due to differences in metal atom sizes at the cation nodes, caused by interdiffusion during high-temperature sintering of non-stoichiometric compounds and transition metal nitrides, resulting in the formation of a replacement solid solution. Random occupation of cation nodes by atoms with differing atomic radii leads to lattice distortion in the solid solution [Citation19]. These fractional defects increase resistance to dislocation motion and hinder dislocation slip, thereby increasing the strength of the solid solution. and (E) display the Inverse Fourier Transform (IFFT) plots of the red and blue boxes in , respectively. shows that the crystal face spacing of the FCC phase (111) face of the sample is 2.406 Å, which closely matches the data obtained for the FCC phase in XRD (2.494 Å). Similarly, the crystal face spacing displayed in is 2.522 Å, which is similar to the (200) crystal face spacing of ZrO2 (2.555 Å).
Figure 6. TEM analysis of the 1700°C samples: (A) BF-STEM image of the samples; (B) Spectral Array of Electron Diffraction (SAED) image under the [010] crystallographic band axis; (C) High Resolution Transmission Electron Microscopy (HRTEM) image; (D) and (E) IFFT images of the FCC phase and the ZrO2 phase, respectively.
![Figure 6. TEM analysis of the 1700°C samples: (A) BF-STEM image of the samples; (B) Spectral Array of Electron Diffraction (SAED) image under the [010] crystallographic band axis; (C) High Resolution Transmission Electron Microscopy (HRTEM) image; (D) and (E) IFFT images of the FCC phase and the ZrO2 phase, respectively.](/cms/asset/5f865d5d-e216-4609-bdbb-475fb3601ae0/tace_a_2360248_f0006_oc.jpg)
The hardness, fracture toughness, and flexural strength of the HENCs samples were evaluated on the polished surface, as depicted in . The results indicate that, with increasing sintering temperature, the flexural strength and hardness initially increased and then decreased. The samples exhibited maximum flexural strength and hardness values of 888 ± 32 MPa and 25.42 ± 1.58 GPa, respectively, at 1700°C. However, further temperature elevation led to excessive sintering energy, resulting in grain growth and reduced grain boundaries. According to the theory of fine-grain reinforcement [Citation24], increased grain size corresponds to decreased material strength and hardness. The rise in hardness primarily resulted from the solid solution strengthening effect [Citation25]. Furthermore, the uniform distribution of Ti, V, Cr, Nb, and Zr metal atoms in HENCs () caused significant lattice distortion within the crystal due to the large difference in atomic radii. This distortion increased resistance to dislocation motion, impeding dislocation slipping and ultimately enhancing the hardness of the HENCs sintered body.
The fracture toughness (KIC) of HENCs samples was determined using the indentation method with a 3 kgf load, and the results showed that the fracture toughness reached a maximum value of 6.23 ± 0.27 MPa·m1/2 at a sintering temperature of 1700°C. In comparison to the previously studied the high-entropy bulk nitride ceramics (HfZrTiNbTa)N, which had a Vickers hardness 21.00 ± 0.94GPa and a fracture toughness of 3.18 ± 0.16MPa·m1/2 [Citation14],the fracture toughness of this sample has significantly improved. This improvement can be attributed to two main factors.
Firstly, the presence of vacancy defects allows for a new type of bonding in non-stoichiometric compounds, specifically metal-vacancy-metal bonding. This type of bonding increases the metallicity of the system, which, under applied stress, promotes plastic deformation of covalently bonded materials [Citation20,Citation26]. This serves to weaken and disperse the stress concentration at the crack tip, thereby increasing the applied stress required for the crack to propagate through the lattice and ultimately promoting material toughening.
Additionally, the observation of small particles distributed in the sample, identified as ZrO2, suggests toughening by dispersed particles of the second phase. When these dispersed particles are distributed in the matrix material, the mismatch between the coefficients of thermal expansion of the second phase and the matrix phase, along with the modulus of elasticity, leads to the formation of a complex stress field inside the material. This stress field interacts with the crack-tip stress concentration, resulting in reduced and dispersed crack propagation. The change in the crack propagation state increases the resistance to crack propagation and consumes the energy needed for the crack to continue expanding, thus achieving toughening of the ceramic material [Citation27–29].
However, as the temperature increased to 1800°C, the fracture toughness tended to decrease. According to Griffith’s microcrack theory [Citation30], the fracture strength of a material is more closely related to the size of internal cracks than to the number of cracks generated. When cracks continue to propagate and exceed the critical size, they will rapidly expand, resulting in brittle fracture of the ceramic material.
4. Conclusions
In summary, high-entropy nitride ceramics with the composition HENCs were successfully synthesized at 1500°C. The synthesis involved the addition of the non-stoichiometric compound TiN0.3 as a sintering additive, which introduced vacancy defects, providing more space for the diffusion and migration of atoms, thus facilitating the sintering process. This novel sintering pathway not only enables high-quality preparation at relatively low temperatures, but also improves production efficiency. Subsequent preparation at 1700°C resulted in HENCs samples with excellent mechanical properties achieved through solid solution strengthening and a second-phase diffuse toughening mechanism. The hardness, flexural strength, and fracture toughness of the samples reached 25.42 ± 1.58 GPa, 888 ± 32 MPa, and 6.23 ± 0.27MPa·m1/2, respectively. These results suggest a promising application for the prepared high-entropy nitride ceramics.
CRediT authorship contribution statement
Peixun Wang: Conceptualization, Methodology, Data Curation, Writing-Original Draft, Writing-Review & Editing and Visualization. Jiuyang Li: Validation, Formal analysis, Investigation. Luyu Yang: Formal analysis, Investigation. Peicheng Mo: Formal analysis, Investigation. Yi Wu: Supervision, Project administration, Funding acquisition
Data and code availability
Data will be made available on request.
Acknowledgments
This work was supported by the National Foundation Regional Science Foundation Project (52062010) and “Key Laboratory of New Processing Technology for Nonferrous Metal & Materials, Ministry of Education/Guangxi Key Laboratory of Optical and Electronic Materials and Devices, Guilin University of Technology, Guilin 541004, China” Open Fund Grant (Contract No. 22AA-9). We would like to thank the staff of the Key Laboratory of New Processing Technology for Nonferrous Metal & Materials, Ministry of Education for their help in testing.
Disclosure statement
No potential conflict of interest was reported by the author(s).
Additional information
Funding
References
- Senkov O, Miller J, Miracle D, et al. Accelerated exploration of multi-principal element alloys with solid solution phases. Nat Commun. 2015;6(1):6529. doi: 10.1038/ncomms7529
- Xiaopeng W, Fantao K. Resent development in high-entropy alloys and other high-entropy materials. J Aeronaut Mater. 2019;39(6):1–19. doi: 10.11868/j.issn.1005-5053.2019.000170
- Yeh JW, Chen SK, Lin SJ, et al. Nanostructured high‐entropy alloys with multiple principal elements: novel alloy design concepts and outcomes. Adv Eng Mater. 2004;6(5):299–303. doi: 10.1002/adem.200300567
- Murty BS, Yeh JW, Ranganathan S. A Brief History of Alloys and the Birth of High-Entropy Alloys. HEA. 2014:1–12. doi: 10.1016/B978-0-12-800251-3.00001-8
- Rost CM, Sachet E, Borman T, et al. Entropy-stabilized oxides. Nat Commun. 2015;6(1):8485. doi: 10.1038/ncomms9485
- Oses C, Toher C, Curtarolo S. High-entropy ceramics. Nat Rev Mater. 2020;5(4):295–309. doi: 10.1038/s41578-019-0170-8
- Wright AJ, Luo J. A step forward from high-entropy ceramics to compositionally complex ceramics: a new perspective. J Mater Sci. 2020;55(23):9812–9827. doi: 10.1007/s10853-020-04583-w
- Chen T, Shun T, Yeh J, et al. Nanostructured nitride films of multi-element high-entropy alloys by reactive DC sputtering. Surf Coat Technol. 2004;188:193–200. doi: 10.1016/j.surfcoat.2004.08.023
- Ren B, Liu Z, Shi L, et al. Structure and properties of (AlCrMnMoNiZrB0.1) Nx coatings prepared by reactive DC sputtering. Appl Surf Sci. 2011;257(16):7172–7178. doi: 10.1016/j.apsusc.2011.03.083
- Feng X, Tang G, Ma X, et al. Characteristics of multi-element (ZrTanbtiW)n films prepared by magnetron sputtering and plasma based ion implantation. Nucl Instrum Methods Phys Res B. 2013;301:29–35. doi: 10.1016/j.nimb.2013.03.001
- Sobol O, Andreev A, Gorban V, et al. Reproducibility of the single-phase structural state of the multielement high-entropy Ti-V-Zr-Nb-Hf system and related superhard nitrides formed by the vacuum-arc method. Tech Phys Lett. 2012;38(7):616–619. doi: 10.1134/S1063785012070127
- Jin T, Sang X, Unocic RR, et al. Mechanochemical-Assisted Synthesis of High-Entropy Metal Nitride via a Soft Urea Strategy. Adv Mater. 2018;30(23):1707512. doi: 10.1002/adma.201707512
- Moskovskikh D, Vorotilo S, Buinevich V, et al. Extremely hard and tough high entropy nitride ceramics. Sci Rep. 2020;10(1):19874. doi: 10.1038/s41598-020-76945-y
- Liu X, Lu Y, Xu Q, et al. Synthesis of (HfZrtinbta) N powders via nitride thermal reduction with soft mechano-chemical assistance. JAC. 2023;12(3):565–577. doi: 10.26599/JAC.2023.9220705
- Hu X, Zhong S, Geng J, et al. In situ synthesis of PcBN composites from Sialon–TiN–TiB 2 binder and cBN under high temperature and pressure. Int J Appl Ceram Technol. 2023;20(4):2183–2193. doi: 10.1111/ijac.14362
- Harrison RW, Lee WE, Jacobson N. Mechanism and kinetics of oxidation of ZrN ceramics. J Am Ceram Soc. 2015;98(7):2205–2213. doi: 10.1111/jace.13575
- Qi Z, Wu Z, Liang H, et al. In situ and ex situ studies of microstructure evolution during high-temperature oxidation of ZrN hard coating. Scr Mater. 2015;97:9–12. doi: 10.1016/j.scriptamat.2014.10.024
- Peng C, Tang H, He Y, et al. A novel non-stoichiometric medium-entropy carbide stabilized by anion vacancies. J Mater Sci Technol. 2020;51:161–166. doi: 10.1016/j.jmst.2020.02.049
- Peng C, Gao X, Wang M, et al. Diffusion-controlled alloying of single-phase multi-principal transition metal carbides with high toughness and low thermal diffusivity. Appl Phys Lett. 2019;114(1):011905. doi: 10.1063/1.5054954
- Guemmaz M, Mosser A, Parlebas J-C. Electronic changes induced by vacancies on spectral and elastic properties of titanium carbides and nitrides. J Electron Spectros Relat Phenom. 2000;107(1):91–101. doi: 10.1016/S0368-2048(00)00091-8
- Guemmaz M, Mosser A, Ahuja R, et al. Theoretical and experimental investigations on elastic properties of substoichiometric titanium nitrides: Influence of lattice vacancies. IJIM. 2001;3(8):1319–1321. doi: 10.1016/S1466-6049(01)00151-9
- Xu S, Wang M, Qiao L, et al. Influence of nitrogen vacancy defects incorporation on densification behaviour of spark plasma sintered non-stoichiometric TiN1-x. Adv Appl Ceram. 2015;114(5):256–260. doi: 10.1179/1743676114Y.0000000216
- Xu S, Wang M, Qiao L, et al. Enhancing the sintering ability of TiNx by introduction of nitrogen vacancy defects. Ceram Int. 2015;41(8):9514–9520. doi: 10.1016/j.ceramint.2015.04.009
- Manna R, Mukhopadhyay NK, Sastry GVS. Strengthening Behavior of Bulk Ultra Fine Grained Aluminum Alloys. Mater Sci forum. 2012;710:241–246. doi: 10.4028/www.scientific.net/MSF.710.241
- Gild J, Zhang Y, Harrington T, et al. High-entropy metal diborides: a new class of high-entropy materials and a new type of ultrahigh temperature ceramics. Sci Rep. 2016;6(1):37946. doi: 10.1038/srep37946
- Skala L, Capkova P. Nitrogen vacancy and chemical bonding in substoichiometric vanadium nitride. J Phys Condens Matter. 1990;2(42):8293. doi: 10.1088/0953-8984/2/42/007
- Becher PF. Microstructural design of toughened ceramics. J Am Ceram Soc. 1991;74(2):255–269. doi: 10.1111/j.1151-2916.1991.tb06872.x
- Evans AG, Faber KT. Toughening of ceramics by circumferential microcracking. J Am Ceram Soc. 1981;64(7):394–398. doi: 10.1111/j.1151-2916.1981.tb09877.x
- Zhang G, Yue X, Jin Z, et al. In-situ synthesized TiB2 toughened SiC. J Eur Ceram Soc. 1996;16(4):409–412. doi: 10.1016/0955-2219(95)00116-6
- Sneddon I, Elliot H. The opening of a Griffith crack under internal pressure. Q Appl Math. 1946;4(3):262–267. doi: 10.1090/qam/17161