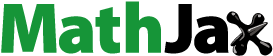
ABSTRACT
WC-Co composites are widely used in cutting tools but are expensive and harmful due to Co in the composites. Alternatives, such as WC-Ni composites have inferior mechanical properties, as a result, WC-Co composites are used in most cutting tools. This study investigated whether adding yttrium oxide (Y2O3) to WC-Ni composites, fabricated from recycled tungsten carbide (WC) and Ni, improved their mechanical properties. Changes in the composites’ microstructure and mechanical properties depended on the amount of Y2O3 added. Y2O3 reacted with WC during sintering, promoting the formation of W and reducing the proportion of C in the composite. The added Y2O3 accelerated the dissolution of W in the Ni matrix, and increased the fractions of the eta phase and solid solution phase. Ni is strengthened by the dissolution of W in Ni, thereby supplementing the low toughness of the eta phase and ultimately yielding WC – Ni with improved hardness and fracture toughness (HV: max. 15.4 GPa, KIC: max. 13.4 MPa∙m1/2) compared to WC – Ni without Y2O3 (HV: 13.5 GPa, KIC: 12.7 MPa∙m1/2). The method for improving the properties of WC – Ni composites by the addition of Y2O3 has a high possibility of commercialization because it does not necessitate process changes.
1. Introduction
Tungsten carbide (WC) – metal composites are widely used as cutting tool materials owing to their excellent wear resistance, chemical stability, and high thermal conductivity [Citation1–3]. The high hardness of WC ensures appropriate wear resistance, and the ductility of the metallic phase improves the fracture toughness of the WC-metal composite. Therefore, WC and the metallic phase impart particular properties to the composite, which originate from their unique properties [Citation2].
Cobalt metal is the most widely used material in the metallic phase of WC-metal composites owing to its high resistance to plastic deformation and low reactivity with WC [Citation4]. Martensitic transformation (a hexagonal close-packed (HCP) structure to a face-centered cubic (FCC) structure without a body-centered cubic (BCC) structure) occurs in the cooling stage of Co after heating, and the martensitic transformation of Co, which is a unique phenomenon found in Co, strengthens Co [Citation5]. This explains why despite its harmfulness to the human body and high cost, Co has not been replaced by other metallic elements such as Ni and Fe in WC – metal composites [Citation4]. In general, WC – metal composites using Ni have approximately 80%–90% lower hardness and strength than composites using Co and are particularly inferior in hardness by approximately 100 to 200 HV [Citation6–8].
To replace Co in WC – metal composites, research has focused on improving the composites’ properties using other metals, particularly Ni. A few studies attempted to enhance composite properties by reducing the WC particle size [Citation9–11], but reinforcing the Ni with solutes such as Co, Fe, Cr, and Mo was found to be more effective [Citation10–20]. Co and Fe are added in the form of metal while Cr and Mo are added in the form of carbides (Cr3C2 and Mo2C) in Ni for a solid solution metallic binder. The solid solution metallic binder in the composite has its intrinsic properties improved by solid solution strengthening, the same as that of the bulk metal [Citation21]. As a result, the mechanical properties of the composite containing the solid solution metallic binder are enhanced.
However, the addition of metal elements to strengthen the metallic binder in the WC-Ni composites has disadvantages and limitations. Even though Cr3C2 and Mo2C effectively improve the mechanical properties of WC-Ni composites, it is difficult to suppress the formation of free C in the microstructure due to the higher solubility of Cr and Mo compared to C in Ni [Citation20,Citation22]. Furthermore, Co with Ni is not complete replacements for Co, and Fe is highly susceptible to oxidation in the presence of heat and moisture [Citation2].
In the WC – metal composite, the amount of carbon affects the formation of a ternary carbide called the eta phase, and if the amount of carbon is insufficient, phases such as CoxWyC or NixWyC (x+y = 6 or 12) appear [Citation23,Citation24]. The eta phase is considered an undesirable phase because it is highly brittle and reduces the fracture toughness of the WC – metal composite [Citation23–26]. Therefore, when the eta phase exists at the WC and metal phase interface, the properties of the composite deteriorate owing to the weakening of the interface properties [Citation27]. However, contrary research results show that the wear resistance properties of WC – metal composites improve when the eta phases are uniformly distributed in the microstructure [Citation26]. The eta phase has a high hardness and can have a positive effect on the hardness and wear resistance of WC – metal composites.
In this study, the mechanical properties were improved by the formation of a hard eta phase and strengthened solid solution (Ni,W) in the WC – Ni composite. Y2O3 was added to WC – Ni composite, and the carbon content of WC – Ni was reduced through a reaction between Y2O3 and WC during sintering. It was expected that the eta phase was formed from WC, Ni, W metal, and the W dissolved in the Ni matrix, forming the (Ni,W) solid solution phase. The eta phase increases the hardness, and the strengthening (Ni,W) plays a role in enhancing the toughness. Ultimately, a WC – Ni composite with high hardness and toughness without using Co as the metallic phase was successfully obtained by the addition of Y2O3.
2. Materials and methods
2.1. Preparation of WC and Ni by recycling of WC–Co hardmetal sludge and waste nickel
The WC and Ni used in the fabrication of the WC-Ni composite were prepared from waste resources such as hardmetal sludge and waste Ni to reduce the raw material costs, as shown in . Hardmetal sludge is generated in the machining step of the manufacturing process and the waste Ni was obtained from spent catalysts for desulfurization. To obtain high-purity WC powder, the hardmetal sludge from which the cutting oil was removed was first mixed with sodium carbonate (Na2CO3) in a mass ratio of sludge to Na2CO3 of 1:0.6, and the mixture was melted at 930°C for 5 h. When the melt was added to distilled water, only water-soluble sodium tungstate (Na2WO4) was dissolved, and the impurities contained in the sludge were removed through filtration and washing. The inorganic acids were then added to the sodium tungstate solution to produce tungstic acid. After purification, high-purity tungstic acid (H2WO4) powder was obtained by drying and crushing. H2WO4 powder and graphite (Alfa Aesar, 7–10 μm, >99%) were mixed together using horizontal ball milling. Tungsten carbide balls were used to prepare the H2WO4–C mixture at a ball-to-powder weight ratio of 10:1. All the milling processes were conducted in a stainless-steel container at a rotation speed of 150 rpm for 24 h in air. Tungsten carbide powder was synthesized by the carbothermal reduction of the mixture at 1200°C in a vacuum for 3 h [Citation28].
Figure 1. Recycling process of hardmetal sludge and waste Ni for the preparation of WC and Ni powders.
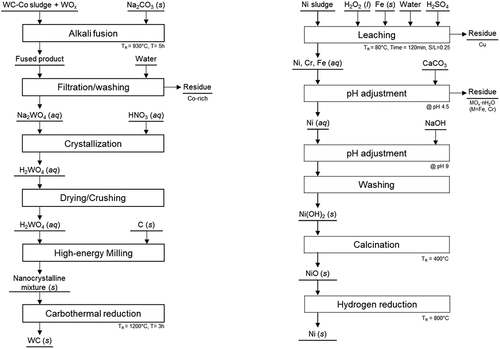
For the preparation of high-purity nickel powder, copper was first removed by sulfuric acid (H2SO4) leaching of waste nickel at 80°C. After leaching, Cr and Fe were removed by adding calcium carbonate (CaCO3) and maintaining a pH of 4.5, and the pH was adjusted to 9 using sodium hydroxide (NaOH). The formed nickel hydroxide (Ni(OH)2) was transformed to nickel oxide (NiO) by calcination at 400°C and finally, nickel powder was prepared by hydrogen reduction at 800°C.
2.2. Thermodynamic analysis of phase fractions by carbon loss in the WC–Ni system
The change in the phase fraction according to the amount of carbon loss, compared to the chemically equivalent amount of carbon in the WC – Ni with a mass ratio of 9:1 (WC:Ni), was analyzed through thermodynamic calculations. FactSage 8.3 (THERMFACT Ltd., Canada) was used as the thermodynamic calculation program, and FTlite and FSstel were used as thermodynamic databases to determine the equilibrium states in the WC – Ni system. Thermodynamic calculations were performed at 1400°C, the sintering temperature for the WC – Ni composite, and the change in phase fraction was determined using an equilibrium module of the FactSage program.
2.3. High-energy ball milling of WC – Ni – Y2O3 mixtures and sintering of the milled powders
High-energy ball-milling was used to obtain mixtures of WC, Ni, and Y2O3 with nanosized crystallites. The recycled WC and Ni were mixed with Y2O3 (Sigma Aldrich, 5–10 μm, 99.9%) to prepare WC – Ni – Y2O3 mixtures. In each mixture, the weight ratio of WC to Ni was 9:1, and Y2O3 was added to the WC – Ni mixtures at weight percentages of 0, 1, 1.5, and 2.0. The mixed powders were subjected to high-energy ball milling using a planetary mill (Pulverisette 5; Fritsch, Germany). Tungsten carbide balls were used to mill the WC – Ni – Y2O3 mixtures in a ball-to-powder weight ratio of 20:1. All the milling processes were conducted in a stainless-steel container at a rotation speed of 200 rpm for 20 h in Ar. For comparison, an unmilled mixture of WC and Ni was prepared by horizontal ball milling.
The milled WC – Ni – Y2O3 mixtures were compacted into discs under a pressure of 125 MPa for Pressureless Vacuum Sintering (PVS) and sintered at 1400°C for 1 h. The milled mixtures were then sintered at 1200°C for 5 min using Spark Plasma Sintering (SPS) to identify the intermediate phases formed by Y2O3 during sintering. The unmilled mixture of WC and Ni powders was also sintered using the same process so that the microstructure and properties of the milled powders could be compared with those of the unmilled powder.
2.4. Phase analysis and mechanical property evaluation of the sintered WC – Ni – Y2O3 composites
The phase analysis of the sintered bodies was performed by X-ray diffraction (XRD; Smartlab, Rigaku, Japan) using monochromatic Cu-Kα radiation (λ = 1.5418 Å); Si (SRM640D, NIST, USA) was used as a standard to calibrate the diffractometer. The sintered WC – Ni – Y2O3 composites were polished, and the microstructures of the sintered specimens were observed using field-emission scanning electron microscopy (FE-SEM; Quanta 650, FEI, Oregon, USA). The grain size of each sintered specimen was analyzed using image analysis software (i-Solution DT-L, Image & Microscope Technology Inc., Korea). Field-emission transmission electron microscopy (FE-TEM; JEM-2100F, JEOL, Tokyo, Japan) and energy-dispersive X-ray spectroscopy (EDS) were used to determine the regional compositions of the sintered bodies. The carbon contents of the sintered WC – Ni – Y2O3 samples were measured using a CS determinator (CS-600, LECO Corporation). To measure the amount of total carbon, the carbon present in the sintered bodies was oxidized to carbon dioxide (CO2) and swept by an oxygen carrier. Carbon was detected as CO2 using a second pair of NDIR cells.
Vickers hardness was measured using a Vickers Hardness Tester (HV-110, Mitutoyo, Tokyo, Japan) with a load of 30 kg. The fracture toughness was calculated using the expression derived by Shetty et al. [Citation29]. The dwell time for the indentation was 15 s, and the reported values represent the average of five measurements. The fracture toughness was estimated from the length of the cracks using the following equation:
where c is the trace length of the crack measured from the center of the indentation, a is half the average length of the two indent diagonals, and Hv is the Vickers hardness.
3. Results and discussion
3.1. Prediction of phase change in the WC–Ni according to carbon loss
shows the change in the phase fraction according to the carbon loss compared to that of a chemically equivalent amount of carbon (5.52 wt.%) of WC – Ni with 10 wt.% Ni at 1400°C through thermodynamic calculations. As the carbon loss increased, the WC ratio decreased because Ni2W4C, a carbide with a relatively low C/W, was formed. Therefore, when carbon loss occurred, the proportion of the phase with relatively low carbon content increased. In the case of the metal phase, there was no significant change in the phase ratio due to carbon loss; however, the amount of dissolved W increased. Therefore, if a decarburization process occurs during the sintering of the WC – Ni composite, it can be predicted that the eta phase ratio will increase, and the dissolved amount of W in the Ni matrix will increase [Citation30].
3.2. Phase change in the WC–Ni composite by addition of Y2O3
shows a schematic of the microstructural changes that occurred during the WC – Ni sintering process. In a typical WC – Ni sintering process, liquefaction of Ni and rearrangement of WC particles are observed in the early stage of liquid-phase sintering. As the liquid-phase sintering progressed, the WC particles dissolved in the Ni matrix, and the WC particles changed into a round shape. Afterward, as the dissolved W and C components reprecipitated, crystallized WC particles were formed, and the microstructure of the WC – Ni composite, including the particle shape and grain size, was determined. If the WC – Ni composite contains an oxide that causes a decarburization process through a reaction with WC, the microstructure may be different from that of the WC – Ni composite without the oxide, as shown in . The oxide that can react with carbon in the WC, such as Y2O3, reduces the amount of carbon that generates CO gas in the WC – Ni composite. During the decarburization process, some WC particles are converted into W, and an eta phase is formed through the reaction between W, WC, and Ni [Citation2,Citation31]. Consequently, the final microstructure of the composite was expected to consist of WC, a metal phase, and an eta phase.
shows the XRD patterns of WC – Ni – Y2O3 sintered by SPS at 1200°C and PVS at 1400°C. A W metal phase was observed in WC – Ni – Y2O3 sintered at 1200°C for 5 min by SPS, suggesting that decarbonization occurred by the addition of Y2O3 in WC – Ni, and the WC was partially transformed into W. The formed W was then dissolved in Ni, resulting in a (Ni,W) solid solution phase. Thus, the peak position of the (Ni,W) phase shifted to a lower angle as the content of Y2O3 was increased, indicating the dissolution of more W in Ni by the decarbonization of WC. The eta phase was also observed, and the peaks from the eta phase increased as the content of Y2O3 rose in WC – Ni – Y2O3. The eta phase is found in cemented carbides where decarbonization occurs [Citation31]. Clearly, Y2O3 played a role in reducing the carbon content by triggering a reaction between Y2O3 and WC in WC – Ni, and forming the eta phase and (Ni,W) during sintering. The following equations are considered:
Figure 4. XRD patterns of WC – Ni – Y2O3 composites fabricated by (a) SPS at 1200°C for 5 min and (b) PVS at 1400°C for 1 h.
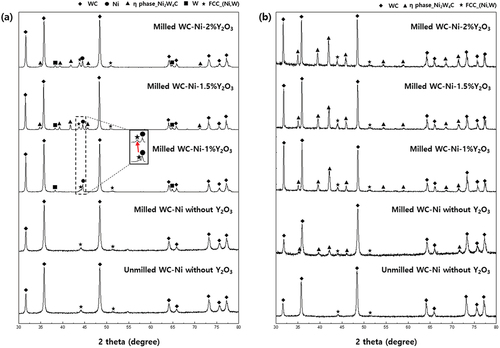
Decarbonization by Y2O3 was clearer when WC – Ni – Y2O3 was sintered at 1400°C for 1 h than in the case of the WC – Ni – Y2O3 sintered at 1200°C for 5 min. As seen in , the Ni phase is not observed, and only the (Ni,W) solid solution phase exists as a metallic phase in the WC – Ni – Y2O3 sintered at 1400°C. We suggest that the amount of the (Ni,W) phase is higher here as a consequence of the high sintering temperature and the passage of sufficient sintering time for the decarbonization of WC and reaction/dissolution of W in Ni to occur, as predicted by thermodynamic calculations from . We also found that three kind of phases – WC, eta phase, and (Ni,W) solid solution phase – existed in the WC – Ni – Y2O3 sintered by PVS at 1400°C for 1 h.
The decarbonization of WC by Y2O3 was confirmed by determining the carbon content of the sintered WC – Ni – Y2O3. As shown in , the amount of carbon decreased as the amount of Y2O3 increased. Decarbonization of WC by Y2O3 then caused the formation of an eta phase and a (Ni,W) solid solution phase with the increase in Y2O3 when a sufficient reaction time was available, as shown in .
Table 1. Carbon content in the sintered WC–Ni with Y2O3 and intensity ratios of the main peaks of the eta phase/WC and the (Ni,w)/wc.
3.3. Microstructure change in the WC–Ni composite by the addition of Y2O3
shows the microstructure of the WC – Ni – Y2O3 sintered by PVS at 1400°C. As shown in the low-magnification images (insets), the sintered bodies had a porosity of A2B2 or higher [Citation32]. It is clear that the sintered bodies prepared from the milled mixtures have relatively smaller grains in the microstructure compared to those of the conventionally mixed WC – Ni. It was expected that the dissolved amount of Y in Ni would be limited, as predicted by the phase diagram, with the result that Y does not affect grain growth behavior during liquid-phase sintering at 1400°C for 1 h [Citation27]. The limited dissolution of Y was confirmed by TEM-EDS results (). It was found that Y was segregated and located in both the WC grains and Ni matrix, and the solubility of Y in the Ni matrix was very low, as can be seen from the quantitative analysis results. Therefore, it is thought that the coalescence of the WC particles could be interrupted by the addition of Y2O3 during sintering, with the result that the grain size of WC becomes small as the amount of Y2O3 increases (1% Y2O3:3.80 ± 0.1 μm, 1.5% Y2O3:3.39 ± 0.06 μm, and 2% Y2O3:2.75 ± 0.04 μm).
3.4. Change in the mechanical properties of the WC–Ni composite by adding Y2O3
shows the variation in the grain size of WC and the mechanical properties of the sintered WC – Ni – Y2O3 together with the previous results for WC – metal composites with 10 wt.% metal phases. The mechanical properties of WC-metal composites vary depending on the grain size of the WC [Citation2]. This tendency was also observed for the WC – metal composites with 10 wt.% metal phases as shown in , where the smaller the particle size, the better the hardness properties, and the larger the particle size, the higher the fracture toughness. The differences in the mechanical properties of WC – metal composites with equal particle sizes are probably caused by differences in the properties of the materials themselves and the metallic phases ultimately determine the properties of the WC – metal composites. The WC particle size in the WC–10Ni – Y2O3 composites prepared in this study is within the range of 2.75–3.8 μm, which shows that it is superior in hardness compared to previously reported WC – metal composites with 10 wt.% metal phases as well as WC-10Ni composites with similar WC particle size [Citation10,Citation11,Citation14–17] The hardness of WC–10Ni – Y2O3 is 13 to 15.4 GPa, which is superior to WC–10Ni (11.8–13.5 GPa). This is attributed to the effect of the high-hardness eta phase formed by the addition of Y2O3. As shown in , in the sample to which Y2O3 was added, a high hardness eta phase formed during sintering, and as the amount of Y2O3 added increased, the proportion of the eta phase in the sample increased. In other words, in the case of the WC-10Ni sintered body with Y2O3 added, the hardness is superior due to the high hardness eta phase even though the WC grain size is larger compared to the sintered body without added Y2O3. Meanwhile, the fracture toughness of WC–10Ni – Y2O3 composites was up to 14.2 MPa∙m1/2, which was inferior to those of the WC – metal composites with Co or alloyed binder (NiCo and NiFe). In the WC – Ni – Y2O3 composites, the (Ni,W) solid solution phase was formed with the addition of less than 2% Y2O3; thus, the solid solution strengthening of the metal phase is believed to be very limited. This appears to be the reason why the fracture toughness is inferior to that of the WC – metal composites using alloy binders. However, the fracture toughness of the WC–10Ni – Y2O3 composite was higher than that (11.4 MPa∙m1/2) of the WC–10Ni composite. It is believed that the toughness did not degrade owing to the strengthening effect of the metallic binder despite the presence of a highly brittle eta phase in the WC – Ni – Y2O3 composite. Therefore, it was concluded that both the hardness and fracture toughness of the WC – Ni composite could be enhanced by the addition of Y2O3 through the formation of a hard eta phase and strengthening (Ni,W) [Citation30].
Figure 7. (a) Vickers hardness and (b) fracture toughness of the WC – metal composites with different WC grain sizes and metallic binder [Citation10,Citation11,Citation14–17].
![Figure 7. (a) Vickers hardness and (b) fracture toughness of the WC – metal composites with different WC grain sizes and metallic binder [Citation10,Citation11,Citation14–17].](/cms/asset/6f68e611-9492-4863-8334-a7556e94ed2e/tace_a_2361992_f0007_oc.jpg)
4. Conclusion
In this study, the microstructure and mechanical properties of a WC – Ni composite were controlled by the addition of Y2O3, which can react with WC to form an eta phase and a solid solution metallic binder. Y2O3 reacted with WC, with the result that decarbonization occurred during sintering and the eta phase and (Ni,W) solid solution phase were formed by a reaction between W, WC, and Ni during the sintering. The eta phase and (Ni,W) solid solution phase affected the hardness and fracture toughness of the WC – Ni composites, respectively. The eta phase formed by the addition of Y2O3 had an intrinsically high hardness and played a role in improving the hardness properties of the WC – Ni composites. Moreover, the solid-solution strengthening of the metallic phase maintained high fracture toughness in the WC – Ni – Y2O3 composites even though the brittle eta phase increased with the amount of Y2O3. Therefore, it is concluded that the addition of Y2O3 can be an effective way to improve the mechanical properties, such as the hardness and fracture toughness, of WC – Ni composites by forming a hard eta phase and a solution-strengthened metallic phase in the microstructure. The method for improving the properties of WC – Ni composites presented in this paper has a high possibility of commercialization because it does not necessitate process changes.
Disclosure statement
No potential conflict of interest was reported by the author(s).
Data availability statement
Data will be made available on request.
Additional information
Funding
References
- Toth LE, Margrave JL. Transition metal carbides and nitrides. 1st ed. (NY) and London: Academic Press; 1971. p. 9–10.
- Ettmayer P. Hardmetals and cermets. Annu Rev Mater Sci. 1989;19(1):145–164. doi: 10.1146/annurev.ms.19.080189.001045
- Kieffer R R, Ettmayer P, Freundhofeier M. New sintered nitride and carbonitride hard metals. Powder Metall. 1971;25:1335–1342.
- Holmstrom E E, Lizarraga R, Linder D. High entropy alloys: Substituting for cobalt in cutting edge technology. Appl Mater Today. 2018;12:322–329. doi: 10.1016/j.apmt.2018.07.001
- Wang W, Jinke Y, Qijie Z. Co-doping effect on the martensitic transformation and magnetic properties of Ni49Mn39Sn12 alloy. J Magn Magn Mater. 2013;346:103–106. doi: 10.1016/j.jmmm.2013.07.025
- Suzuki H, Hayashi K, Yamamoto T. Relations between some properties of Sintered WC-10%Ni alloy and its binder phase composition. J Jpn Soc Powder Metal. 1966;13(6):290–295. doi: 10.2497/jjspm.13.290
- Suzuki H, Hayashi K, Terada O. Room-temperature transverse-rupture strength of WC-10%Ni cemented carbide. J Jpn Inst Metals. 1977;41(6):559–563. doi: 10.2320/jinstmet1952.41.6_559
- Human AM, Exner HE. The relationship between electrochemical behaviour and in-service corrosion of WC based cemented carbides. Int J Refract Met Hard Mater. 1997;15(1–3):65–71. doi: 10.1016/S0263-4368(96)00014-5
- Suzuki H, Terada O, Ike H. Mechanical properties of micro-grained WC-Ni cemented carbide. J Jpn Soc Powder Metal. 1995;42(11):1345–1349. doi: 10.2497/jjspm.42.1345
- Jia K, Fischer TE, Gallois B. Microstructure, hardness and toughness of nanostructured and conventional WC-Co composites. NanoStruct Mater. 1998;10(5):875–891. doi: 10.1016/S0965-9773(98)00123-8
- Silva EN, Santos AAA, Nascimento RM. Investigation of characteristics and properties of spark plasma sintered ultrafine WC-6.4Fe3.6Ni alloy as potential alternative WC-Co hard metals. Int J Refract Met Hard Mater. 2021;101:105669. doi: 10.1016/j.ijrmhm.2021.105669
- Walbrühl M, Linder D, Agren J. Diffusion modeling in cemented carbides: solubility assessment for Co, Fe and Ni binder systems. Int J Refract Met Hard Mater. 2017;68:41–48. doi: 10.1016/j.ijrmhm.2017.06.006
- Steinlechner R, Calderon R, Koch T. A study on WC-Ni cemented carbides: constitution, alloy compositions and properties, including corrosion behaviour. Int J Refract Met Hard Mater. 2022;103:105750. doi: 10.1016/j.ijrmhm.2021.105750
- Almond EA, Roebuck B. Identification of optimum binder phase compositions for improved WC hard metals. Mater Sci Eng A. 1988;105(106):237–248. doi: 10.1016/0025-5416(88)90502-2
- Zhang X, Zhou J, Lin N. Effects of Ni addition and cyclic sintering on microstructure and mechanical properties of coarse-grained WC–10Co cemented carbides. Int J Refract Met Hard Mater. 2016;57:64–69. doi: 10.1016/j.ijrmhm.2016.02.008
- Jiang H, Tong J, Zhan Z. Comparative study on the densification, microstructure and properties of WC-10(Ni, Ni/Co) cemented carbides using electroless plated and coprecipitated powders. Mater. 2023;16(5):1977. doi: 10.3390/ma16051977
- Gonzalez R, Echeberria J, Sanchez JM. WC-(Fe,ni,c) hardmetals with improved toughness through isothermal heat treatments. J Mater Sci. 1995;30(13):3435–3439. doi: 10.1007/BF00349891
- Rocha AMF, Bastos AC, Cardoso JP. Corrosion behaviour of WC hardmetals with nickel-based binders. Corros Sci. 2019;147:384–393. doi: 10.1016/j.corsci.2018.11.015
- Santos RF, Rocha AMF, Bastos AC. Microstructural characterization and corrosion resistance of WC-Ni-Cr-Mo composite – The effect of Mo. Int J Refract Met H. 2020;86:105090. doi: 10.1016/j.ijrmhm.2019.105090
- Li G, Peng Y, Yan L. Effects of Cr concentration on the microstructure and properties of WC-Ni cemented carbides. J Mater Res Technol. 2020;9(1):902–907. doi: 10.1016/j.jmrt.2019.11.030
- Walbruhl M, Linder D, Agren J. Alternative Ni-based cemented carbide binder – Hardness characterization by nano-indentation and focused ion beam. Int J Refract Met H. 2018;73:204–209. doi: 10.1016/j.ijrmhm.2018.02.017
- Walbruhl M, Linder D, Agren J. Diffusion modelling in cemented carbides: Solubility assessment for Co, Fe and Ni binder systems. Int J Refract Met H. 2017;68:41–48. doi: 10.1016/j.ijrmhm.2017.06.006
- Pollock CB, Stadelmaier HH. The eta carbides in the Fe−W−C and Co−W−C systems. Metall Trans. 1970;1(4):767–770. doi: 10.1007/BF02811752
- Guillermet AF. Thermodynamic properties of the Co-W-C system. Trans A. 1989;20(5):935–956. doi: 10.1007/BF02651660
- Cho KH, Lee JW, Chung IS. A study on the formation of anomalous large WC grain and the eta phase, mater. Sci Eng A. 1996;209(1–2):298–301. doi: 10.1016/0921-5093(95)10104-7
- Formisano A, Minutolo FC, Caraviello A. Influence of eta-phase on wear behavior of WC-Co carbides. Adv Tribol. 2016;2016:1–6. doi: 10.1155/2016/5063274
- Eso O, Fang ZZ, Griffo A. Kinetics of cobalt gradient formation during the liquid phase sintering of functionally graded WC–co. Int J Refract Met Hard Mater. 2007;25(4):286–292. doi: 10.1016/j.ijrmhm.2006.07.002
- Kwon H, Shin J. Preparation and characterization of tungsten carbide using products of hard metal sludge recycling process. Resour Recycl. 2022;31(4):19–25. doi: 10.7844/kirr.2022.31.4.19
- Shetty DK, Wright IG, Mincer PN. Indentation fracture of WC-Co cermets. J Mater Sci. 1985;20(5):1873–1882. doi: 10.1007/BF00555296
- Kwon H, Suh CY, Kim W. Microstructure and mechanical properties of (Ti,w)c–Ni cermet prepared using a nano-sized TiC–WC powder mixture. J Alloys Compd. 2015;639:21–26. doi: 10.1016/j.jallcom.2015.03.115
- Akesson L. Science of Hard Materials. (NY): Springer; 1983. p. 71–82.
- Park S, Kang S. Toughened ultra-fine (Ti,w)(cn)–Ni cermets. Scripta Mater. 2005;52(2):129–133. doi: 10.1016/j.scriptamat.2004.09.017