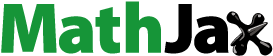
Abstract
Automobile production plants have advanced the utilization of stainless steel alloys for the production of exhaust mufflers due to corrosion failures associated with their operating lifespan and conditions of application. Corrosion vulnerability of as received and heat treated (500oC and 1000oC) 439 L ferritic stainless in 3.5 M H2SO4 electrolyte at 0% to 6% NaCl concentration was evaluated with potentiodynamic polarization, potentiostatic measurement, open circuit potential measurement, and optical microscopy characterization. Potentiodynamic polarization results show heat treatment improved the general corrosion resistance of the steel. Heat treated 439 L steel at 500°C displayed the lowest corrosion rate trailed by the heat treated steel at 1000°C. However, potentiostatic measurement shows that heat treatment decreases the resistance of the steel to localized corrosion deterioration from inspection of the metastable pitting current and passivation potential values. Results from open circuit potential measurement show heat treatment increases the thermodynamic tendency for 439 L steel to corrosion while improving its corrosion resistance. Optical images of the as-receive and heat treated steels show the presence of numerous corrosion pits and corrosion along the grain boundaries. However, the extent of deterioration is significantly higher for the as-received steel.
PUBLIC INTEREST STATEMENTS
The economic impact and problems resulting from corrosion have drawn strong attention from scientists and engineers worldwide. Corrosion in industrial environments is a major concern in chemical processing plants, oil and gas industry, manufacturing, automobile industry, marine operations, boiler plants and power generation plants due to the considerable cost involved in the replacement of metallic parts in their various applications. The consequence often leads to plant shutdowns, breakdown of industrial equipment, reduced efficiency, industrial downtime, high maintenance cost due to replacement of damaged part, wastage of valuable resources and expensive overdesign. Appropriate selection of engineering with desirable corrosion-resistant properties significantly reduce corrosion damage thus prolonging the lifespan of the material and subsequently reducing cost of corrosion prevention.
1. Introduction
Automobile production plants are one of the most significant sectors of a nation’s economy (Vaz et al., Citation2017). Automobile exhaust system is an important component of an automobile vehicle. The automobile exhaust structure consists of parts such as exhaust manifold, muffler, catalytic converter and extension pipes. Exhaust manifold connects to the engine cylinder, collecting the exhaust gas from each cylinder into the exhaust collector (Seabra et al., Citation2016). It operates under astringent conditions, alternating between high and room temperature. The exhaust system is prone to problems such as high-temperature oxidation, localized corrosion, stress corrosion cracking and intergranular corrosion (Zhang & Cen, Citation2011). The major factor responsible for the premature failure and limited lifespan of an automobile exhaust system is the cognate debilitating impact of corrosion and fatigue. The system is subject to thermal stress coupled with surface oxidation and vulnerability to corrosive anions from the toxic waste gases and environment (Valarmathi et al., Citation2017). The corrosion mechanisms are divided into two, (a) internal corrosion due to condensation of harmful acid constituents and (b) external corrosion due to chlorides, sulphates, etc., especially in coastal areas and high levels of acid rain. The hot end of the exhaust system is where oxidation breakdown of the surface oxide layer is a major problem. At this end formation of porous oxide occurs leading to accelerated deterioration of the material. At the cold end, localized corrosion deterioration is prevalent and condensation of gaseous products produces (H2SO4 and small concentrations of HCl acid) create environmental conditions which results in corrosion of the inner components (Dai et al., Citation2011; Douthett, Citation2006). The exhaust component is exposed to high temperatures (950°C and above), NaCl and exhaust precipitates during automobile engine operation (Sarda & Bindu, Citation2014). Choice of material for application in automobile exhaust system is crucially important. The material with the least tendency to react with its operating environment while maintaining its mechanical, metallurgical and physical properties is most likely to have a longer lifespan. However, it must be noted that selected materials have threshold limits to corrosion, stress and high temperature (Aniekan et al., Citation2017). Other factors such as cost, expected lifespan, warranty requirements, prevailing market trends, customer demands, etc., influence the choice of materials for the manufacture of automobile exhaust system (Varma et al., Citation2011). Carbon steel was previously the material of choice. However, its poor corrosion resistance limited it durability especially when exposed to chlorides and exhaust condensate. Alloys such as aluminized carbon steel, ferritic chromium steels and ferritic chromium molybdenum steels are presently used in the manufacture of exhaust mufflers. The earlier steels mentioned are metallic alloys resistant to corrosion due to the initiation and growth of a protective, inert and impenetrable oxide on its surface. Collapse of the oxide by corrosive anions such as chlorides, sulphates, etc., at sufficiently positive anodic potential and temperature lead to gradual metallurgical deterioration and mechanical failure of the steels. 409 and 304 stainless steels are used in exhaust mufflers because they are cost effective and with good weldability. However, operating temperature conditions most often go beyond their oxidation limit resulting in shortened operational lifespan. 439 L ferritic steel is a Ti stabilized, 18% percent Cr alloy with the specific purpose of resisting corrosion in oxidizing environments. The steel has very low vulnerability to H2 embrittlement, excellent weldability, high thermal conductivity and minimal thermal expansion properties. The steel is gradually replacing the conventional stainless steels and other alloys as the material of choice in automobile exhaust system due to its high oxidation resistance. The steel has threshold limit to chloride-sulphate attack prevalent in simulated exhaust working conditions which has been established to a certain degree (Loto, Citation2019, Citation2017; Loto & Loto, Citation2018; Loto & Oghenerukewe, Citation2016). However, details are scarce on the corrosion behaviour of the steel when subjected to conditions that alter the metallurgical and microstructural properties of the steel. This research focuses on the corrosion resistance of 439 L ferritic stainless steel subjected to high temperature variation of 500°C and 1000°C in Cl–SO42- solution.
2. Experimental methods
The elemental (wt. %) content () of 439 L ferritic stainless steel (439ST) plates obtained from McMaster University, Ontario, Canada was determined with PhenomWorld scanning electron microscope at Covenant University, Ota, Nigeria. As received 439ST was cut into four samples, each with mean surface area of 1 cm2 before embedding in vercocit resin mounts. Another two sets of 439ST (four samples each) underwent heat treatment processing in a muffle furnace. One set of samples was heated to 1000°C and the other set was heated to 500°C. Both sets were maintained at the particular temperature of 30 min and allowed to cool down to 37°C. The temperature was regulated with inbuilt control (accuracy ± 10°C) linked to a thermocouple (K-Type) to achieve the desired temperature condition. The steel surface underwent metallographic preparation with SiC papers (80–1000 grits), 6 µm diamond solution, distilled H2O and C3H6O. 200 mL of 3.5 M H2SO4 at 0%, 2%, 4% and 6% NaCl concentration were formulated from standard grade solution of the H2SO4 (98% purity) and NaCl (recrystallized). Potentiodynamic polarization technique and open circuit potential measurements were done with a triple electrode configuration (encased 439ST electrodes, Ag/AgCl reference electrode and Pt counter electrode) inside a glass container holding 100 mL of the electrolyte solution and linked to Digi-Ivy 2311 potentiostatic device (interfaced with a laptop). Potentiodynamic polarization curves were obtained at sweep estimate of 0.0015 V/s between from −1 V and +1.25 V. Corrosion current density CD (A/cm2) and corrosion potential CP (V) values were obtained from Tafel extrapolation of anodic-cathodic polarization curves. Corrosion rate, CR (mm/y) was calculated from the mathematical relationship;
Table 1. Elemental content (wt. %) of 439ST
EQ illustrates equivalent weight (g) of 439ST, 0.00327 represents corrosion rate constant for dimension and time conversion in mm/y and D represents the density (g). Open circuit potential measurements on 439ST placed within 200 ml of 3.5% H2SO4 solution at 0%, 2% and 6% NaCl concentration was done at step potential of 0.1 V/s for 3600 s with double-electrode cell consisting configuration (Ag/AgCl reference electrode and encased 439ST electrode) connected to Digi-Ivy 2311 potentiostatic device. Optical representations of 439ST steel samples prior to and after heat treatment were obtained with the used Omax trinocular metallurgical microscope for characterization.
3. Results and discussion
Potentiodynamic polarization studies
Potentiodynamic polarization data of untreated and heat treated 439ST corrosion in 3.5 M H2SO4 solution at 0%—6% NaCl concentration is shown in . The polarization curves are depicted from to . depicts the polarization curves of untreated 439ST (UN-439ST). shows the polarization curves of heat treated 439ST at 500°C (500–439ST) while shows the polarization curves of heat treated 439ST at 1000°C (1000–439ST). The corrosion rate of UN-439ST increased with increase in Cl− ion concentration. At 0% Cl− ion concentration, the corrosion rate is 0.374 mm/y which correlates to corrosion current density of 3.48 × 105 A/cm2 and polarization resistance of 738.4 Ω. The result is due to the reactivity of SO42- ions in the acid solution which chemically displaced the adsorbed O2 molecules causing the passivation of the steel (Kruger et al., Citation1975; Maurice & Marcus, Citation2018; Raja & Jones, Citation2006; Uhlig, Citation1958). The SO42- ions react with the substrate Fe leading to anodic degradation of the steel. Increase in Cl− ion concentration to 2% results in proportional increase in corrosion rate to 0.512 mm/y coupled with decrease in polarization resistance value to 539.0 Ω. At optimal concentration of 6% Cl− ion concentration, the corrosion rate peaked at 0.695 mm/y.
Figure 1. Potentiodynamic polarization curves of untreated 439ST corrosion in 3.5 M H2SO4 solution at 0%—6% NaCl concentration
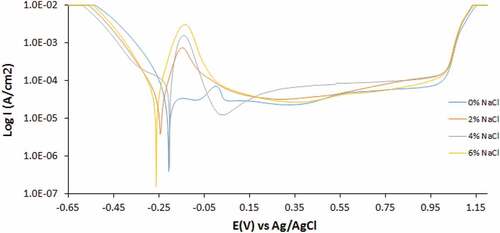
Figure 2. Potentiodynamic polarization curves of 500–439ST corrosion in 3.5 M H2SO4 solution at 0%—6% NaCl concentration
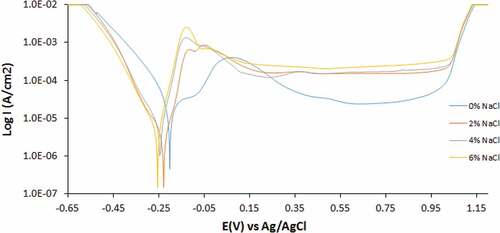
Figure 3. Potentiodynamic polarization curves of 1000–439ST corrosion in 3.5 M H2SO4 solution at 0%—6% NaCl concentration
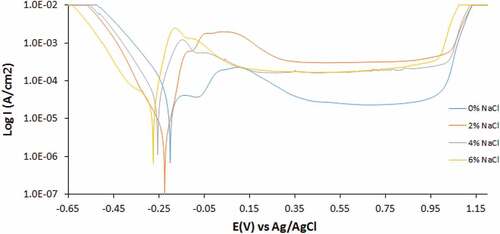
Table 2. Potentiodynamic polarization outputs of untreated and heat treated 439ST corrosion in 3.5 M H2SO4 solution at 0%—6% NaCl concentration
These observations show that the combined action of SO42- and Cl− ions is deleterious to the corrosion resistance of untreated 439ST. Heat treatment of 500–439ST to recrystallization temperature of 500°C altered the microstructural properties of steel, hence its electrochemical properties were also altered. Corrosion rate values of the steel show that heat treatment processes significantly improved the corrosion resistance of 439ST coupled with the unlikely phenomenon of decrease in corrosion rate with increase in Cl− ion concentration. At 0% Cl− ion concentration, the corrosion rate of 500–439ST is 0.265 mm/y compared to the higher value of 0.374 mm/y for UN-439ST. The corrosion rate of 500–439ST decreased with increase in Cl− ion concentration, attaining peak value of 0.115 mm/y at 6% Cl− ion concentration. In summary, heat treatment of 439ST improved its corrosion resistance by 29.11%, 57.79%, 75.82% and 83.44% with respect to Cl− ion concentration in 3.5 M H2SO4 solution. While the corrosion potential of UN-439ST varied between anodic and cathodic shift analogous to Cl− ion concentration. The corrosion potential of 500–439ST shifted to cathodic values from −0.206 V at 0% Cl− ion concentration to −0.259 V at 6% concentration indicating the dominant effect of reduction reactions on the corrosion reaction mechanism. The same phenomenon occurred for 1000–439ST where the corrosion potential of the steel shifted from −0.204 V at 0% Cl− ion concentration to −0.280 V at 6% concentration.
Increase in temperature to 1000°C substantially influenced the corrosion resistance of 1000–439ST (). The corrosion rate of 1000–439ST at 0% Cl− ion concentration increased to 0.397 mm/y compared to 0.265 mm/y for 500–439ST and 0.374 mm/y for UN-439ST. Optimal value of 0.580 mm/y at 6% Cl− ion concentration was obtained at 1000°C. The % variation on corrosion rate compared to the UN-439ST is −6.29%, 16.22%, 10.36% and 16.46%. These observations indicate there is no uniform consensus on the effect of exhaust operating conditions on the corrosion resistance of 439ST. Each part of an automobile exhaust system varies in operating conditions with in turn strongly influence the corrosion resistance and lifespan of 439ST.
Metastable pitting and passivation studies
depicts the potentiostatic output obtained from the corrosion polarization studies of untreated and heat treated 439ST. Corrosion potential, metastable pitting potential/current and passivation potential/current values are presented analogous to Cl− ion concentration in 3.5 M H2SO4 solution. Observation of the metastable pitting potentials of UN-439ST, 500–439ST and 1000–439ST at 0% Cl− ion concentration show that the effect of SO42- ions only in the electrolyte solution delays the formation of transient corrosion pits on untreated and heat treated 439ST. However, observation of the polarization curves at this Cl− ion concentration in shows the delay in transient pit formation is due to short-term passivation and disintegration of the protective oxide on the steel’s surface following anodic polarization of the steel. While the anodic polarization reactions are related to anodic dissolution and oxidation of the steel leading to surface degradation, the extent and potential span of the anodic dissolution of UN-439ST is significantly shorter than is observed for 500–439ST and 1000–439ST due to substantial changes in the microstructural properties of heat treated 439ST. depicts the metastable pitting potential of UN-439ST is 0.00 V compared to the values of 0.10 V obtained for 500–439ST and 1000–439ST. The anodic polarization plot preceding the onset of metastable corrosion pits is shorter for 1000–439ST compared to 500–439ST despite the relatively lower corrosion rate values for 500–439ST earlier obtained. While heat treatment at 500°C and 1000°C improves the corrosion resistance by 439ST, it undoubtedly increases its susceptibility to localized corrosion deterioration. The metastable pitting current values prove this assertion. The values increase with increase in heat treatment process signifying higher susceptibility as earlier mentioned. The polarization curves in show increasing anodic polarization curves with increase in Cl− ion concentration which simultaneously increased the metastable pitting portion of the polarization plots. The presence of chlorides heightened the susceptibility of the steel to pitting corrosion. Though comparison of the relative effect for the heat treated and untreated steel is negligible after 2% Cl− ion concentration as shown in the metastable pitting values in . In agreement with the earlier discussion on increased vulnerability of heat treated 439ST to localized corrosion compared to untreated 439ST, the passivation potential values for UN-439ST at 0.03 V (0% Cl− ion concentration) is significantly lower compared to 500–439ST and 1000–439ST and 0.36 V and 0.39 V. At higher Cl− ion concentration, the same phenomenon occurred where UN-439ST passivated at lower potentials compared to the heat treated counterparts, i.e., heat treated processes hinder the capacity of 439ST to quickly passivate probably due to precipitation of Cr at the grain boundary. The passivation potential value for 500–439ST at 2% chloride concentration is lower than the value obtained for 1000–439ST. However, the beyond this concentration, the values are relatively the same. Heat treatment enhances the general corrosion resistance of 439ST, however, the steel becomes more vulnerable to localized corrosion deterioration as it decreases the capacity of the steel to passivate and sustain its passive film over wide potentials in the presence of corrosive ions.
Table 3. Potentiostatic output for untreated and heat treated 439ST corrosion in 3.5 M H2SO4 solution at 0%—6% NaCl concentration
Open circuit potential measurement (OCP)
Open circuit potential studies for UN-439ST, 500–439ST and 1000–439ST were performed in 3.5 M H2SO4 solution at 0%, 2% and 6% NaCl solution for 3600s shows the OCP curves versus exposure time for UN-439ST, 500–439ST and 1000–439ST. The curves for UN-439ST vary significantly analogous to Cl− ion concentration (). The curve at 0% Cl− ion concentration initiated at −0.215 V and shifted to relative anodic potentials throughout with final OCP value of 0.377 V. The anodic shift is due to the gradual formation Cr2O4 oxide on the steel. Hence the steel becomes more corrosion resistant in the presence of SO42- ions. Addition of chlorides to the acid solution at 2% and 6% increased the tendency for UN-439ST to corrode. Cathodic shift in corrosion potential occurred relative to the OCP curve at 0% NaCl concentration. The curve for UN-439ST at 2% and 6% NaCl concentration initiated at −0.271 V and −0.270 V (0s). However, the curve at 6% NaCl attained thermodynamic stability at −0.268 V (80s), while the curve at 2% NaCl concentration showed the presence of potential transients for the first 200s of exposure before attaining relative stability at 400s (−0.231 V). Generally, the curves for UN-439ST show that Cl− ions increase the tendency for the steel to corrode compared to the curve at 0% NaCl concentration. However, in the presence of chlorides the steel is thermodynamically stable though the visible potential transients’ shows sites of active/passive behaviour of the steel surface.
Figure 4. Open circuit potential curves of for UN-439ST in 3.5 M H2SO4 solution at 0%, 2% and 6% NaCl concentration
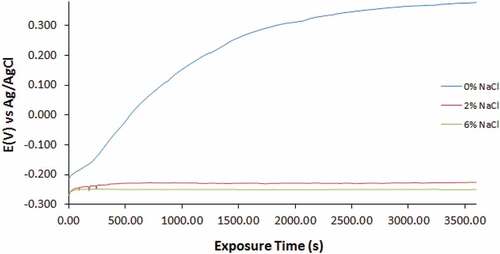
Figure 5. Open circuit potential curves of for 500–439ST in 3.5 M H2SO4 solution at 0%, 2% and 6% NaCl concentration
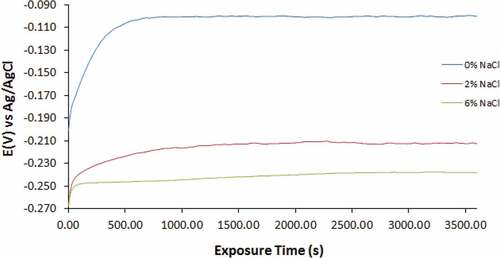
Figure 6. Open circuit potential curves of for 1000–439ST in 3.5 M H2SO4 solution at 0%, 2% and 6% NaCl concentration
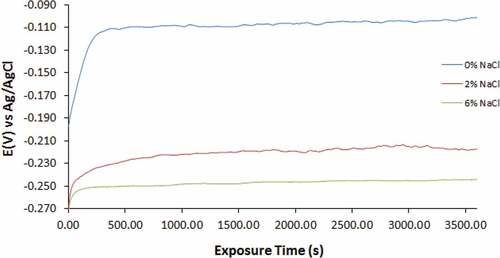
The OCP curves for 500–439ST and 1000–439ST at 0%, 2% and 6% NaCl concentration are generally similar. Observation also shows the curves for 500–439ST and 1000–439ST (0% NaCl) shifted to relative anodic potentials due to formation of the corrosion resistant protective oxide on the steel surfaces. At this concentration, the OCP curves initiated at −0.201 V and −0.197 V and shifted to −0.103 V (600s) and −0.114 V (300s) attaining the thermodynamic stability and improved corrosion resistance. However, comparing the potentials at which the curves for UN-439ST, 500–439ST and 1000–439ST (0% NaCl concentration) attained thermodynamic stability (0.287 V, −0.103 V and −0.114 V); it clearly evident that heat treatment increases the thermodynamic tendency for 439ST to corrode. Comparing the potentials at which UN-439ST, 500–439ST and 1000–439ST attained thermodynamic stability in the acid electrolyte at 2% and 6% NaCl concentration, values of −0.231 V and −0.257, −0.216 V and −0.248, and −0.223 and −0.251 were obtained. The values show heat treatment of 439ST slightly boosts the general corrosion resistance of the steel.
Optical microscopy studies
Optical microscopic images (mag. x100) of 439ST before corrosion, and after corrosion from 3.5 M H2SO4 solution at 0%, 2% and 6% NaCl concentration are shown from to ). shows the optical image of 439ST before corrosion. ) to (c) shows the optical images of UN-439ST after corrosion. ) to (c) displays the optical representations of 500–439ST after corrosion while ) to (b) depict the optical images of 1000–439ST after corrosion. ) to (c) showed the presence of corrosion pits while ) to 10(c) depicts both corrosion pits and intergranular degradation due to the electrochemical action of chlorides and sulphates on the steel surfaces. Analogous to the results from potentiodynamic polarization test, the extent of deterioration on UN-439ST surface [ c)] is much higher compared to the images shown from ) to ). Large corrosion pits are distinguishable in ) due to localized deterioration of UN-439ST resulting from the action of SO42- ions in the electrolyte. On ) the number of corrosion has increased significantly due to the combined electrochemical action of SO42- and Cl− ions resulting in accelerated deterioration of the steel surface. The image in ) shows greater occurrence of micro-pits due to increased concentration of Cl− ions at 6% volumetric concentration. The micro-pits cover the entire steel surface, hence increasing the vulnerability of the steel to localized corrosion deterioration as earlier discussed from passivation studies. The hardened surface of 500–439ST and 1000–439ST from ) to 10(c) decreased the occurrence of corrosion pits compared to ); nevertheless intergranular corrosion is clearly visible on the images due to enlargement of the steel’s grain structure resulting from the heat treatment processes. As a result, deterioration along the grain boundaries due to Cr depletion occurred.
Figure 8. Optical images of UN-439ST after corrosion in 3.5 M H2SO4 solution at (a) 0% NaCl, (b) 2% NaCl and (c) 6% NaCl concentration
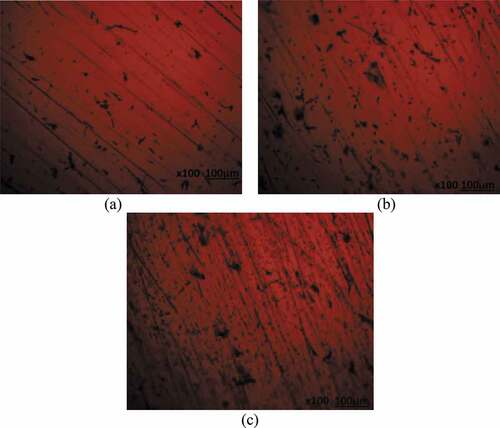
4. Conclusion
Heat treatment strongly influenced the corrosion resistance of 439 L ferritic steel in acid chloride solution. Alteration of the microstructural properties at 500oC and 1000oC improved the general corrosion resistance of the steel. However, results showed the heat treated steel was more vulnerable to localized corrosion deterioration. The thermodynamic tendency of the steel to corrode increased after heat treatment. Hence during application while the steel may not show visible sign of deterioration, pitting and intergranular corrosion of the steel occurs gradually as proven from optical microscopic characterization.
Acknowledgements
The author thanks Covenant University for their support and provision of research facilities
Disclosure statement
Authors declare no conflict of interest.
Additional information
Funding
Notes on contributors
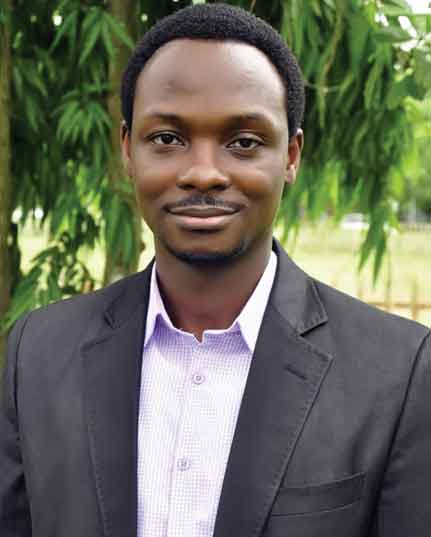
Roland Tolulope Loto
oto Roland Tolulope is a Professor at the Department of Mechanical Engineering, Covenant University, Ogun State, Nigeria. He is the head of the corrosion and materials research cluster. Roland has over one hundred and ninety190 (190) research publications including reviews in top international journals and has consistently served as reviewer in respectable journals due to his in-depth knowledge and technical expertise. He has a lot of experience in research experimentation basically aimed at proffering solutions to the current depreciating effect of metallic degradation and failure in various engineering applications. He is a registered member of the Council for the Regulation of Engineering in Nigeria, South African Institute of Mining and Metallurgy and the Corrosion Institute of Southern Africa.
References
- Aniekan, I., Kelly, O. E., & Abdulsamad, G. (2017). Engineering material selection for automotive exhaust systems using CES software. International Journal of Engineering Technologies, 3(2), 50–14. https://doi.org/10.19072/ijet.282847
- Dai, Z., He, H., & Xu, D. (2011). Failure mode analysis of automotive exhaust system hot end. SAE Technical Paper. https://doi.org/10.4271/2011-01-0787
- Douthett, J. 2006. Automotive exhaust system corrosion, corrosion: Environments and industries, ASM Handbook, Vol. 13C, 519–530.
- Kruger, J., Ambrose, J. R., & Kodama, T. 1975. The role of passive film growth kinetics and properties in stress corrosion and crevice corrosion susceptibility (NBSIR 75–916), Institute for Materials Research, National Bureau of Standards. https://nvlpubs.nist.gov/nistpubs/Legacy/IR/nbsir75-916.pdf
- Loto, R. T. (2017). Electrochemical corrosion characteristics of 439 ferritic, 301 austenitic, s32101 duplex and 420 martensitic stainless steel in sulfuric acid/NaCl solution. Journal of Bio- & Tribo Corrosion, 3(2), 24. https://doi.org/10.1007/s40735-017-0084-1
- Loto, R. T. (2019). Comparative study of the pitting corrosion resistance, passivation behavior and metastable pitting activity of NO7718, NO7208 and 439L super alloys in chloride/sulphate media. Journal of Materials Research and Technology, 8(1), 623–629. https://doi.org/10.1016/j.jmrt.2018.05.012
- Loto, R. T., & Loto, C. A. (2018). Corrosion behaviour of S43035 ferritic stainless steel in hot sulphate/chloride solution. Journal of Materials Research and Technology, 7(3), 231–239. https://doi.org/10.1016/j.jmrt.2017.07.004
- Loto, R. T., & Oghenerukewe, E. (2016). Inhibition studies of rosmarinus officinalis on the pitting corrosion resistance 439LL ferritic stainless steel in dilute sulphuric acid. Oriental Journal of Chemistry, 32(5), 2813–2832. https://doi.org/10.13005/ojc/320557
- Maurice, V., & Marcus, P. (2018). Progress in corrosion science at atomic and nanometric scales. Progress in Materials Science, 95, 132–171. http://doi.org/10.1016/j.pmatsci.2018.03.001
- Raja, K. S., & Jones, D. A. (2006). Effects of dissolved oxygen on passive behavior of stainless alloys. Journal for electrochemistry. Corrosion Science, 48(7), 1623–1638. https://doi.org/10.1016/j.corsci.2005.05.048
- Sarda, S., & Bindu, R. S. (2014). Exhaust transfer connection material selection meeting critical qualification requirements in automotive application. International Journal of Mechanical and Production Engineering, 2(6), 87–91.
- Seabra, A. S., Pereira, A. L., Moreira, M. A. R., Pereira, M. L. B., Santos, T. R. S., & Marcelino, T. A. L. (2016). Production process of an automotive exhaust. Journal of Management and Technology, 4(2). https://doi.org/10.24279/jmgmt.v4i2.633
- Uhlig, H. H. (1958). The adsorption theory of passivity and the flade potential. Society for physical chemistry,62(6–7). https://doi.org/10.1002/bbpc.19580620603
- Valarmathi, S., Nathc, R., & Kumar, P. (2017). Experimental analysis of exhaust manifold with ceramic coating for reduction of heat dissipation, IOP Conf. Series: Materials Science and Engineering, 197, 012051. http://doi.org/10.1088/1757-899X/197/1/012051
- Varma, A., Newman, D., Kay, D., Gibson, G., Beevor, J., Peter, S. I., & Wells, P. Effect of regulations and standards on vehicle prices, Report for Directorate-General Climate Action, European Commission, 2011;ED56221. https://ec.europa.eu/clima/sites/clima/files/transport/vehicles/cars/docs/report_effect_2011_en.pdf
- Vaz, C. R., Rauen, T. R. S., & Lezana, A. G. R. (2017). Sustainability and innovation in the automotive sector: A structured content analysis. MDPI Sustainability, 9(6), 880. https://doi.org/10.3390/su9060880
- Zhang, Q., & Cen, S. (2011). Multiphysics applications in automotive engineering. Multiphysics Modeling. http://doi.org/10.1016/C2021-0-01330-0