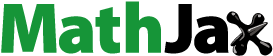
Abstract
The microstructural characteristics and mechanical behaviour of aluminium matrix composites reinforced with Si-based refractory compounds (SRC) derived from rice husk were investigated. The reinforcement materials (SRC) were synthesized using a carbothermal processing technique. The reinforcement was used to prepare a 10 wt.% Al-Mg-Si alloy-based composite using a double stir casting process. The composites produced were characterized using microhardness, tensile properties, scanning electron microscopy (SEM), and X-ray diffractometer (XRD). From the results, A1650, C1650, and A1600 grades of the samples show more resistance to indentation due to the high proportion of hard SRC in the reinforced materials. Superior elongation values were observed for these composites A1650, C1650 and A1600 grades, respectively. The grades A1250, B1250, and C1250 series had the least toughness values within the range of 20–37% as compared to the control sample. For all composites under examination, the percent porosity was noted to be less than 4% and the strain to fracture was within 24–38%. Higher intensity of SiC was observed from the XRD spectrum and the formation of intermetallic materials. The tensile fracture surface morphologies of the composites produced were similar, showing a ductile dimple-like structure. The formation of a micro-crack and micro-void was also observed along the interphase.
PUBLIC INTEREST STATEMENT
Incremental research documents are available on the use of synthetic materials in the development of aluminium metal matrix composites. Unfortunately, there are enormous quantity of agro-wastes materials not completely employed in Nigeria. The current study is a contribution to our previous report on the development of silicon-based refractory compounds (SRC) from agro-wastes. In this work, we report the use of this SRC in the development of aluminium matrix composites. The microstructural characteristics and mechanical behaviour of the composites developed were evaluated in the study. A double stir casting route was used for the composites development. The results obtained showed a good potential application in transport structural parts.
1. Introduction
The choice of aluminium matrix composites (AMCs) in aerospace, structural, and automobile industries has been attributed to their unique properties, such as good wear resistance, low fabrication cost, low density, and high strength weight ratio (Shaikh et al., Citation2019; Singh & Chauhan, Citation2016; Suthar & Patel, Citation2018; Adediran et al., Citation2020). Besides, the characteristic attributes such as good corrosion resistance, lightweight, high thermal conductivity, and low processing cost make aluminium a choice material for metal matrix (Natarajan et al., Citation2006). Researchers over the years have deployed agro-waste as reinforcement material in the design of AMCs. Some utilized them as partial replacement along with synthetic ceramic reinforcement materials (Bodunrin et al., Citation2015; Alaneme et al., Citation2018); also, with other synthetic materials (Alaneme et al., Citation2018; Verma & Vettivel, Citation2018) or in the development of hybrid composites (Shaikh et al., Citation2019; Alaneme et al., Citation2013a). Synthetic reinforcements such as silicon carbide (SiC) were previously synthesized using the Acheson process (Acheson, Citation1893). Silica sand and carbon were used simultaneously as source materials in an electric furnace-based reactor. However, the challenge in accessing these starting materials in the developing countries is of concern, coupled with the high processing techniques involved. Other processing routes such as carbothermal reduction of silica (Adediran et al., Citation2018); chemical vapour deposition (Zhang et al., Citation2016); powder mixing (Pezzotti & Sakai, Citation1994); sol-gel processes (Ebrahimpour et al., Citation2014); laser pyrolysis (Coupe et al., Citation2012) have been reported by the authors. The state-of-the-art facilities and the energy burden associated with the aforementioned processing routes pose a challenge to the developing countries. Carbothermal synthesis route is a cost-effective process for producing Si-based refractory compounds. Agro-waste materials containing high silica materials are easily and readily found within Nigeria. The environmental impact their disposal causes can be harnessed by converting them to Si-based refractory compounds (Adediran et al., Citation2019, Citation2018). Furthermore, the motivation behind the use of agro-waste as reinforcement is informed by the low-density property, low cost, and accessibility of these materials. Studies have shown that agro-wastes can either be used as precursor materials (Adediran et al., Citation2018) or processed into ash before further synthesis (Prasad et al., Citation2011; Alaneme et al., Citation2013a; Edoziuno et al., Citation2021; Madakson et al., Citation2012). These processed ashes were added as complementary reinforcement using different processing routes in the development of AMCs. Some of these are processes are liquid infiltration, rheocasting, double stir casting, compocasting, among others (Alaneme et al., Citation2018; Kala et al., Citation2014; Shabani & Mazahery, Citation2013). However, double stir casting has been widely used over the years by researchers owing to its flexibility, simplicity, and viability (Prasad & Krishna, Citation2011; Alaneme et al., Citation2018; Ramanathan et al., Citation2019; Singh & Chauhan, Citation2017).
The challenge of accessing synthetic reinforcement materials in developing countries has been a concern for researchers (Prasad, Citation2016; Alaneme & Ajayi, Citation2017). To this end, agro-waste materials are highly sort after as potential materials for the synthesis of Si-based refractory compounds. In the previous work, Adediran et al. (Citation2018) have successfully synthesized Si-based refractory compounds (SRC) from rice husk (RHs) via a carbothermal processing route. This SRC comprises a good percentage of silicon carbide and other refractory compounds in their structures. Thus, making them a potential reinforcement material in the design of AMCs (Akbar et al., Citation2020). Also, RHs possesses a good percentage of silica, hematite and alumina as major refractory oxides in its structure (Dinaharan et al., Citation2017). However, the elastic modulus of silicon carbide (SiC) ranges between 50 and 70 GPa, which is relatively in line with that of aluminium (60 GPa) (Chakrapani & Suryakumari, Citation2020). Similarly, the elastic modulus of alumina ranges between 320 and 380 GPa, while that of silicon carbide is between 400 and 450 GPa (Alaneme et al., Citation2013a). There appears to be a sparse literature on the characterization of AMCs reinforced with Si-based refractory compounds derived from RHs. The current study attempts to explore the mechanical and microstructural characteristics of aluminium metal matrix composites developed from Si-based refractory compounds of RHs. The data from these findings would add to the existing database of cost-effective and technically efficient secondary reinforcement phase to improve aluminium metal matrix composites.
2. Materials and methods
2.1. Materials
Al-Mg-Si alloy (AA 6063) was used as a matrix in the composite production, and the elemental composition is presented in . Rice husks used as precursor materials were sourced from Igbemo Ekiti, Ekiti State, Nigeria. A carbothermal processing technique was used for the production of the Si-based refractory compounds (SRC) at a temperature window of 900–1650°C at a heating rate of 10°C/min in a controlled environment as described by Adediran et al. (Citation2018). The morphology of the reinforcements is presented in , b, c, d, e, f, and g, respectively. The average particle size of the reinforcements varied from 40 to 50 μm. Details about the constituents of the reinforcement phases are as presented in respectively. The products from these reaction systems were used as reinforcement in the composite production. shows the chemical composition of the rice husk used.
Figure 1. Showing the scanning electron image of reinforcements used for the production of the composite (a) A1 (b) B1 (c) C1 (d) A (e) B (f) D and (g) conventional SiC used for the development of D1
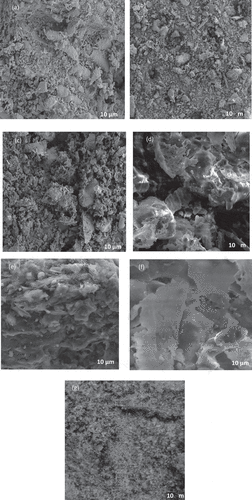
Table 1. Elemental composition of Al-Mg-Si alloy
Table 2. Elemental composition of rice husk ash
Table 3. Variation in yield of selected Si-based refractory compounds processed at higher temperature interphase used for composites reinforcement (Adediran et al., Citation2018)
Table 4. Variation in yield of selected silica-based polytypes processed at 1250°C temperature interphase used for composites reinforcement (Adediran et al., Citation2019)
2.2. Composites production
The production of the Al-Mg-Si alloy matrix composites reinforced with Si-based refractory compounds from rice husk was performed using a two-step stir casting process as reported by Alaneme and Sanusi (Citation2015). The process began with the determination of the amount of Si-based refractory (SRC) required to produce 10 wt.% particle reinforced composites. The variations in the yield of selected Si-based refractory compounds processed at higher temperature interphase used for composite reinforcement are presented in , respectively. The SRC were preheated before the casting process at a temperature of 200–280°C to eradicate dampness and improve the wettability of the molten matrix following Alaneme and Aluko (Citation2012). The Al-Mg-Si alloys were then charged into the crucible furnace (gas-fired with a temperature probe) and heated to a temperature of 710°C ± 30°C to ensure a complete melt. The melt was allowed to cool to a semi-solid state at a temperature of about 610°C and stirred manually for 10 min. The semi-solid mixture was again heated to 710°C ± 30°C and stirred with a mechanical stirrer operated at 350 rpm for another 5–10 min before casting into sand moulds with metallic chills around the mould. The composites designation and the processing history of the reinforcement are detailed in .
Table 5. Sample designation, reinforcement in 10 wt.% and reinforcement history
2.3. Composite density & percentage porosity
The evaluation of the composites theoretical density was done using the relation stated by Alaneme et al. (Citation2013a) which implies that:
where is the composite density,
is the weight fraction of Al-Mg-Si alloy,
is the density of Al-Mg-Si alloy,
is the wt. fraction of Si-based refractory compounds from rice husk,
is the density of the Si-based refractory compounds.
The experimental density of each composite produced was evaluated by dividing the measured weight of each sample by its measured volume using a digital weighing balance (GK 320-GS 2202) with a tolerance of ± 0.001.
The percentage porosity for each of the composites was computed using the values of the experimental density and the theoretical density following Alaneme et al., Citation2014.
Where is the theoretical density (g/cm3), and
is the experimental density (g/cm3).
2.4. Mechanical properties
2.4.1. Hardness measurement
The microhardness test was evaluated on the composites developed using a standard procedure. The samples were machined and polished to obtain a smooth plane surface before the test was conducted following ASTM E92-17 standard (Astm, Citation2017). A microhardness tester FM-800 was used at 100 gf load at 15 s dwell time, and an average of 10 indentations were taken within the margin of ±2%.
2.4.2. Tensile testing
The tensile properties of the composites developed were determined at room temperature using an Instron universal testing machine. A strain rate of 10 −3/s was used with a specimen dimension of gauge length 30 mm and diameter of 5 mm following Alaneme and Odoni (Citation2016) The test procedures were guided by the recommendation of ASTM E8/E8M-16a standard (ASTM E8/ E8M-16a, Citation2016). Triplicate tests were performed for each composite to ascertain the repeatability of the results.
2.4.3. Fracture toughness
Circumferential notch tensile (CNT) testing method was used for the fracture toughness determination as reported by Alaneme (Citation2011). Samples for the test were machined to a gauge length of 30 mm, with a specimen diameter of 6 mm, a notch diameter of 4.2 mm, and 60° notched angle. The samples were later subjected to tensile loading to fracture using a universal tensile testing machine. The fracture toughness calculation was done from the fracture load (pf) obtained from the CNT specimens load-extension plots. The equation provided by Dieter (Citation1988) was used in the final determination of the fracture toughness as corroborated by Alaneme and Ajayi (Citation2017). Triplicate tests were done for each sample to ensure their reproducibility.
where D and d are the specimen diameter and the diameter of the notched section, respectively. Plane strain conditions and by extension, the validity of the fracture toughness values obtained was determined using the relations by Nath and Das (Citation2006)
2.5. XRD Characterization
X-Ray Diffraction (XRD) analysis was done on the composites to determine the phases present in the composites produced. The XRD was operated at 40 kV, and at 45 mA, samples were scanned at a speed of 2°/min in the range of 2θ from 10° to 90°. The samples were prepared for XRD analysis using a backloading preparation method (Ramezani et al., Citation2021). They were analyzed with a PANalytical Empyrean diffractometer with PIXcel detector and fixed slits with Fe filtered Co-Kα radiation (λ = 1.54060). The phases were identified using X’Pert High Score Plus software.
2.6. Microstructural characterization
Optical microscope (Olympus BX51M) was used for analyzing the microstructural features of the composites produced. Additionally, the surface morphology and fracture surface determination, and elemental composition were determined using JSM-7800 F extreme resolution analytical field emission scanning electron microscope equipped with an energy-dispersive spectroscope (EDS). The scanning electron microscope was operated at 15 kV and a working distance of 15 mm (Ramezani et al., Citation2020; Hoseinzadeh et al., Citation2017). Selected areas of interest were focused and micrographs were taken for samples requiring SEM and EDS analysis (Ramezani et al., Citation2021; Hoseinzadeh et al., Citation2017). Before the microscopic examination, the samples were metallographically prepared using a series of grinding and polishing steps. Samples were then etched using Keller’s reagent (1.0 ml HF, 1.5 ml HCl, 2.5 ml HNO3, 95 ml water).
3. Results and discussion
3.1. Microstructure
Representative SEM micrographs and EDS analysis of the composites produced are shown in . The Si-based refractory compounds (reinforcement) were fairly dispersed in the matrix (Al-Mg-Si alloy). The EDS spectra also show the peaks of Si (silicon), Mg (magnesium), Al (aluminium), C (carbon), and O (oxygen). The presence of these elements confirm that SiC and Al-Mg-Si alloys are the main reinforcement and matrix, respectively. However, the presence of oxygen among others shows that it is partly from the silica phase of the rice husk. Similar observation has been reported by Alaneme and Sanusi (Citation2015). From , representative optical microscope images for A1250, B1250, C1250, and D are shown. shows a higher dispersion of Si-based refractory in the matrix. The grain boundaries were, however, obvious in , while (f) shows a relative dispersion of the reinforcement within the Al-matrix. However, there were few cracks noticed in the structure.
Figure 2. (a). Representative secondary electron mode images of A1650 showing the dispersion of the Si-based refractory compounds in the Al-Mg-Si alloy; (b) showing a pronounced phase of the reinforcement in the matrix for C1650; (c) showing the grain boundaries and the reinforcement phase of A1600 with the EDS spectra; (d) distribution of the reinforcement phase for A1250 in the matrix; (e) showing the optical image of B1250 with a network of the reinforcement in the matrix; (f) showing clearly the reinforcement particles in the Al-Mg-Si matrix for C1250. (b) showing a pronounced phase of the reinforcement in the matrix for C1650; (c) showing the grain boundaries and the reinforcement phase of A1600 with the EDS spectra; (d) distribution of the reinforcement phase for A1250 in the matrix; (e) showing the optical image of B1250 with a network of the reinforcement in the matrix; (f) showing clearly the reinforcement particles in the Al-Mg-Si matrix for C1250
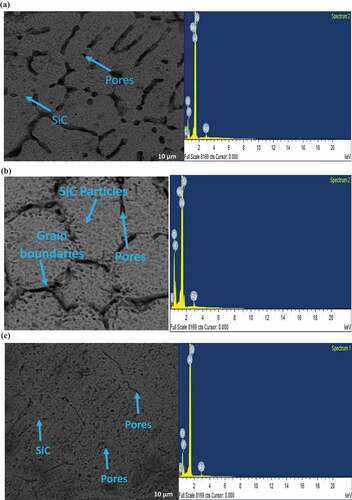
3.2. Structural characterization
The XRD result is as presented in . It shows the various diffraction patterns of the phases formed at varying 2theta values.
shows the variation in phases in the composites developed at different two theta values. The presence of SiC was evident in the phases identified in the XRD analysis and were characterized by high peak intensities. It is evident that the constituent elements in the matrix reacted with the Si-based refractory compounds, thus forming different phases in the composites developed. It is noted that there are other phases with lower intensity such as wustite (Fe30O36), spinel (MgAl16O32), and periclase (Mg4O4) also identified in the spectra. The role played by intermetallic compounds during the solidification of the composites developed has been reported by Yildirim and Ozyurek (Citation2013) and Zulfia et al. (Citation2007). Estatite with chemical formula Mg14.56 Fe1.20 Si15.76 Al0.24 O48 and manganese silicide (Mn10Si6) have noticeable peaks in the phases for the compound identified in the spectrum. The formation of these compounds implies that there was an interface/chemical reaction between the elemental constituents in the composite matrix and the SRC.
3.3. Mechanical behaviour
3.3.1. Microhardness
The variations in the microhardness values are as presented in .
It is noted that from , the A1650, C1650, and A1600 grades of composites developed had higher hardness values implying more resistance to indentation due to the high proportion of hard SRC in the reinforced materials (). The SRC withstands the major load transferred by the matrix in the composites developed. Similar behaviour was reported by Ravikumar et al. (Citation2017). It is ultimately inferred that the increment in the hardness values observed in A1650 sample might be attributed to the high proportion of SiC polytypes in the refractory compounds used as reinforcement () for the production of the composite (Adediran et al., Citation2018). However, the presence of silica polytypes partly appearing as cristobalite phase (softer material) resulted in the reduction in hardness value, as observed in series A1250, B1250, and C1250, thus impeding the hardness level. A similar report was observed by different authors on the influence of silica phase on the harness value of composite materials (Alaneme & Sanusi, Citation2015; Shaikh et al., Citation2019). It is noted that the variations in the harness value are due to the different elastic behaviour of the reinforcement (SRC) and the matrix.
3.3.2. Tensile values
The representative variations in the ultimate tensile strength and the yield strength are as presented in .
Figure 5. (a) Variation of the ultimate tensile strength of the composites. (b) Variation of yield strength of the composites
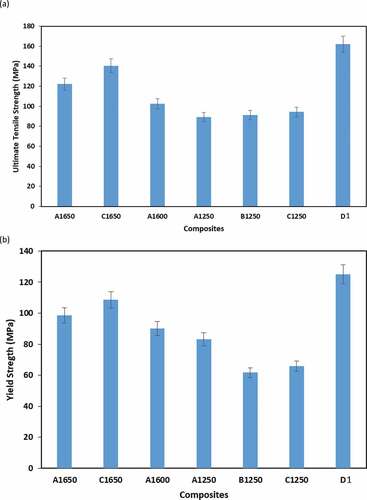
The representative ultimate tensile strength and yield strength values are as presented in . It is noted that the yield strength to some extent follows the trend in the hardness (). The ultimate tensile strength (UTS) of C1650 gave the optimum value (for the composites developed) which is about 13.25% reduction when compared to the sample designated D1. Moreover, A1650 and A1600 had a range of 24–37.5% reduction in UTS for D1. This might be due to the interfacial bonding between the Al-Mg-Si alloy matrix and the relatively hard Si-based refractory compounds since there were variations in the yield of SiC in the reinforcement. It is worth noting that A1250, B1250, and C1250 all gave the lowest ultimate tensile value. Specifically, A1250 showed the least value with an approximate value of 44.92% reduction in the ultimate tensile strength. A similar trend was reported by Ravikumar et al. (Citation2017) and Alaneme and Sanusi (Citation2015). From , it was observed that as the yield of the Si-based refractory compounds increases in the matrix (), there appeared to be a corresponding reduction in the ultimate tensile strength. This trend was corroborated by Ravikumar et al. (Citation2018); Singh and Chauhan (Citation2016). It is evident that the strengthening is a result of the greater load-carrying capacity of the reinforcement, thus leading to higher work-hardening capacity and increase in resistance to plastic deformation in the composites developed (Chawla & Shen, Citation2001). An indirect strengthening occurred due to the variation in the thermal coefficient between the matrix and the SRC (Si-based refractory compounds) during cooling (Gladston et al. (Citation2015); Chawla and Shen (Citation2001). It is worth noting that there was a marginal variation in the ultimate tensile strength in A1250 and B1250 compositions.
3.3.3. Strain to fracture, fracture toughness and porosity values
The variation of strain to fracture and fracture toughness values of the composites are presented in , respectively.
From the variation in strain to fracture results presented in , it is observed that C1650 grade shows a superior strain to fracture among the composite batches. However, when compared with D1 (control), it had about 52.9% increase in strain value. It is evident that this composite grade was able to sustain plastic deformation; thus, it possesses a good ductility. However, composites A1250, B1250, C1250, and A1650 all had a strain to fracture increment ranging from 25% to 40% as compared to D1. Similarly, composite A1600 had about 2.9% reduction in strain value as compared to D1. shows the fracture toughness values of the composites produced, C1650 grade had about 15.3% increase in fracture toughness value when compared to D1 (control). However, previous work reported by Alaneme and Adewale (Citation2013c) using 10 wt.% SiC in developing AMC showed a range of 6–7 MPam1/2 fracture toughness values. This value was however attained after cold deformation was carried out on the samples to remove the deformity inherent after casting. It is noted that A1600, A1250, and C1250 recorded the least toughness values ranging from 20% to 37% when compared with sample C1650. However, they had a range of 13–26% reduction when compared with sample D1. The high proportion of Si-based refractory compounds in the matrix of the Al-Mg-Si alloy used as the matrix contribute to the reduction in the fracture toughness value observed in the composites developed. Additionally, SiC constitutes part of the reaction products in the Si-based refractory compounds. It is a hard ceramic reinforcement material that is liable to rapid crack propagation.
The variation in the density values for the composites developed is presented in . It is observed that the theoretical density had higher values as against the experimental, an indication that there were porosities in the composites developed. It was noted that for all composites, the percentage porosity was less than 4% which has been reported to be the maximum permissible in cast metal matrix composites (Alaneme & Sanusi, Citation2015).
Table 6. Composite density and estimated percent porosity
Since the fractography image of the fractured surface of the composites developed shows an identical shape, a representative image showing the surface morphology of the fractured surface is presented in , b, and c. It is however noted from that the fractured surface showed a ductile form of dimple structure likely due to shearing. The structure also showed some debris, pits and plastic deformation regions (), while a large burr due to plastic deformation and a continuous groove is shown in at higher magnification. It is apparent that within the reinforcement-matrix interphase, there is a micro-crack and micro-void formation which might be due to debonding along this interphase (Chawla & Shen, Citation2001). Furthermore, it is evident that the cracks noticed on the fractured surface might have been as a result of the stress induced during tensile loading on the samples. This in turn creates a potential site for propagation before the final failure occurs. The fracture micro-mechanism of the reinforced AMCs is attributed to interfacial cracking, particle cracking and debonding. Equally of note is that this observation might have contributed to the reduction in the strength values observed in the composites produced. A similar trend was corroborated by Yildirim and Ozyurek (Citation2013); Thirugnanam et al. (Citation2007).
4. Conclusions
The microstructural characteristics and mechanical behaviour of aluminium matrix compositesreinforced with Si-based refractory compounds derived from rice husk was investigated in the current work. The results show that samples such as A1650, C1650, and A1600 showed more resistance to indentation due to the high proportion of hard Si-based refractory compounds in the reinforced materials. The Si-based refractory compounds withstand the major load transferred by the matrix in the composites developed and the strain to fracture for all composites were within the range of 15–46%. The tensile fracture surface morphology of all composites produced showed a ductile dimple structure. Intermetallic compounds were identified from the XRD pattern which play a significant role in the strength of the composites developed.
Acknowledgement
The authors appreciate the funding support for the APC from Pan African University for Life and Earth Sciences Institute, Ibadan, Nigeria.
Additional information
Funding
Notes on contributors
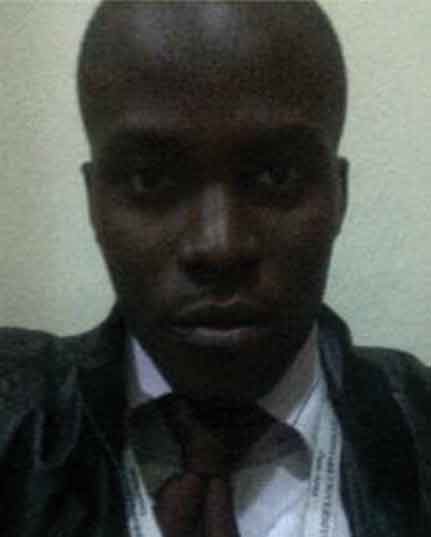
Adeolu Adesoji Adediran
Adediran A.A (PhD) is a Lecturer in the Department of Mechanical Engineering, Landmark University, Omu-Aran, Kwara State Nigeria. He is a registered Engineer with the Council for the Regulation of Engineering in Nigeria (COREN) and a member of several Professional bodies. His research interest is in advanced materials.
Alaneme K.K is a Full Professor in Metallurgical and Materials Engineering Department, Federal University of Technology, Akure. He is a visiting Professor at the University of Johannesburg, South Africa. His interest is in Physical Metallurgy, Mechanical Behavior of Materials, Composite Materials, Fracture Mechanics and Failure Analysis. He has supervised several undergraduates and post-graduates students and has published both in local and international journals.
Oladele I.O is an Associate Professor in Metallurgical and Materials Engineering Department, Federal University of Technology, Akure. His interest is in Composites Material Development and Production in Metallurgy. He has published in both local and international journals.
References
- Acheson, E. G. (1893). Carborundum: Its history, manufacture and uses. Journal of the Franklin Institute, 136(3), 194–16. https://doi.org/10.1016/0016-0032(93)90311-H
- Adediran, A. A., Alaneme, K. K., Oladele, I. O., & Akinlabi, E. T. (2019). Structural Characterization of Silica based Carbothermal Derivatives of Rice Husk. Procedia Manufacturing, 35, 436–441. https://doi.org/10.1016/j.promfg.2019.05.063
- Adediran, A. A., Alaneme, K. K., Oladele, I. O., Akinlabi, E. T., & Bayode, B. L. (2020). Effects of milling time on the structural and morphological features of Si-based refractory compounds derived from selected Agro-Wastes. Materials Today: Proceedings, 38(2), 928-933. https://doi.org/10.1016/j.matpr.2020.05.416
- Adediran, A. A., Alaneme, K. K., Oladele, I. O., & Akinlabi, E. T. (2018). Processing and structural characterization of Si-based carbothermal derivatives of rice husk. Cogent Engineering, 5(1), 1–12. https://doi.org/10.1080/23311916.2018.1494499
- Akbar, H. I., Surojo, E., & Ariawan, D. (2020). Investigation of Industrial and Agro Wastes for Aluminum Matrix Composite Reinforcement. Procedia Structural Integrity, 27, 30–37. https://doi.org/10.1016/j.prostr.2020.07.005
- Alaneme, K. K. (2011). Fracture Toughness (K1C) evaluation for dual phase medium carbon low alloy steels using circumferential notched tensile (CNT) specimens. Materials Research, 14(2), 155–160. https://doi.org/10.1590/S1516-14392011005000028
- Alaneme, K. K., Adewale, T., & Olubambi, P. (2014). Corrosion and wear behaviour of Al–Mg–Si alloy matrix hybrid composites reinforced with rice husk ash and silicon carbide. . Journal of Materials Research and Technology, 3(1), 9–16. https://doi.org/10.1016/j.jmrt.2013.10.008
- Alaneme, K. K., & Adewale, T. M. (2013c). Influence of rice husk ash–silicon carbide weight ratios on the mechanical behaviour of Al–Mg–Si alloy matrix hybrid composites. Tribol. Ind, 35(2), 163–172. https://www.tribology.rs/journals/2013/2013-2/10.pdf
- Alaneme, K. K., & Ajayi, O. J. (2017). Microstructure and mechanical behavior of stir-cast Zn–27Al based composites reinforced with rice husk ash, silicon carbide, and graphite. Journal of King Saud University - Engineering Sciences, 29(2), 172–177. https://doi.org/10.1016/j.jksues.2015.06.004
- Alaneme, K. K., Akintunde, I. B., Olubambi, P. A., & Adewale, T. M. (2013a). Fabrication characteristics and mechanical behaviour of rice husk ash – Alumina reinforced Al-Mg-Si alloy matrix hybrid composites. Journal of Materials Research and Technology, 2(1), 60–67. https://doi.org/10.1016/j.jmrt.2013.03.012
- Alaneme, K. K., & Aluko, A. O. (2012). Fracture toughness (KIC) and tensile properties of as-cast and age-hardened aluminium (6063)–silicon carbide particulate composites. Scientia Iranica, Transactions A: Civil Engineering, 19(4), 992–996. https://doi.org/10.1016/j.scient.2012.06.001
- Alaneme, K. K., Ekperusi, J. O., & Oke, S. R. (2018). Corrosion behaviour of thermal cycled aluminium hybrid composites reinforced with rice husk ash and silicon carbide. Journal of King Saud University – Engineering Sciences, 30(4), 391–397. https://doi.org/10.1016/j.jksues.2016.08.001
- Alaneme, K. K., & Odoni, B. U. (2016). Mechanical properties, Wear and Corrosion Behavior of Copper Matrix Composites Reinforced with Steel Machining Chips. Engineering Science and Technology, an International Journal, 19(3), 1593–1599. https://doi.org/10.1016/j.jestch.2016.04.006
- Alaneme, K. K., & Sanusi, K. O. (2015). Mechanical and wear behaviour of rice husk ash-alumina-graphite hybrid reinforced aluminium based composite. Eng. Sci. Technol. Int. J, 18, 416–422. https://doi.org/10.1016/j.jestch.2015.02.003
- ASTM E8/ E8M-16a, standard test methods for tension testing of metallic materials. ASTM International 2016, www.astm.org
- Astm, E.92–17, Standard Test Methods for Vickers Hardness and Knoop Hardness of Metallic Materials, ASTM International 2017, www.astm.org
- Bodunrin, M. O., Alaneme, K. K., Chown, L. H. (2015). Aluminium matrix hybrid composites: a review of reinforcement philosophies; mechanical, corrosion and tribological characteristics. Journal of Materials Research and Technology, 4(4), 434-445. https://doi.org/10.1016/j.jmrt.2015.05.003
- Chakrapani, P., & Suryakumari, T. S. A. (2020). Mechanical properties of aluminium metal matrix composites-A review. Materials Today Proceedings. https://doi.org/10.1016/j.matpr.2020.09.247(in press).
- Chawla, N., & Shen, Y. (2001). Mechanical Behavior of Particle Reinforced Metal Matrix Composites. . Advanced Engineering Materials, 3(6), 357–370. https://doi.org/10.1002/1527-2648(200106)3:6<357::AID-ADEM357>3.0.CO;2-I
- Coupe, A., Maskrot, H., Buet., E., Renault., A., Fontaine, P. J., & Chaffron, L. (2012). Dispersion behaviour of laser-synthesized silicon carbide nanopowders in ethanol for electrophoretic infiltration. Journal of the European Ceramic Society, 32(14), 3837–3845. https://doi.org/10.1016/j.jeurceramsoc.2012.05.022
- Dieter, G. E. (1988). Mechanical metallurgy. McGraw-Hill.
- Dinaharan, I., Kalaiselvan, K., & Murugan, N. (2017). Influence of rice husk ash particles on microstructure and tensile behavior of AA6061 aluminum matrix composites produced using friction stir processing. Composites Communications, 3, 42–46. https://doi.org/10.1016/j.coco.2017.02.001
- Ebrahimpour, O., Dubois, C., & Chaouki, J. (2014). Fabrication of mullite-bonded porous SiC ceramics via a sol–gel assisted in situ reaction bonding. Journal of the European Ceramic Society, 34(2), 237–247. https://doi.org/10.1016/j.jeurceramsoc.2013.08.028
- Edoziuno, F. O., Adediran, A. A., Odoni, B. U., Utu, O. G., & Olayanju, A. (2021). Physico-chemical and morphological evaluation of palm kernel shell particulate reinforced aluminium matrix composites. Materials Today: Proceedings, 38(2), 652-657. https://doi.org/10.1016/j.matpr.2020.03.641
- Gladston, J. A. K., Sheriff, N. M., Dinaharan, I., & Selvam, J. D. R. (2015). Production and characterization of rice husk ash particulate reinforced AA6061 aluminium alloy composites by compocasting. 25, 683–691. https://doi.org/10.1016/S1003-6326(15)63653-6
- Hoseinzadeh, S., Ghasemiasl, R., Bahari, A., & Ramezani, A. H. (2017). n-type WO3 semiconductor as a cathode electrochromic material for ECD devices. Journal of Materials Science: Materials in Electronics Volume, 28, 14446–14452.
- Kala, H., Mer, K. K. S., & Kumar, S. (2014). A Review on Mechanical and Tribological Behaviors of Stir Cast Aluminum Matrix Composites.. Procedia Materials Science, 6, 1951–1960. https://doi.org/10.1016/j.mspro.2014.07.229
- Madakson, P. B., Yawas, D. S., & Apasi, A. (2012). Characterization of coconut shell ash for potential utilization in metal matrix composites for automotive applications. Int. J Eng. Sci. Technol, 3(4), 1190–1198. http://www.idc-online.com/technical_references/pdfs/mechanical_engineering/Characterization%20of%20Coconut%20Shell%20Ash%20for.pdf
- Natarajan, N., Vijayarangan, S., Rajendran, I. (2006) Wear behaviour of A356/25SiCp aluminium matrix composites sliding against automobile friction materials. Wear, 261, 812–822
- Nath, S. K., & Das, U. K. (2006). Effect of microstructure and notches on the fracture toughness of medium carbon steel. Journal of Naval Architecture and Marine Engineering, 3(1), 15–22. https://doi.org/10.3329/jname.v3i1.925
- Pezzotti, G., & Sakai, M. (1994). Effect of a Silicon Carbide “Nano-Dispersion” on the Mechanical Properties of Silicon Nitride. Journal of the American Ceramic Society, 77(11), 3039–3041. https://doi.org/10.1111/j.1151-2916.1994.tb04545.x
- Prasad, S. D., & Krishna, R. A. (2011). Production and mechanical properties of A356.2/RHA composites. Int. J. Adv. Sci. Technol, 33, 51–58. http://article.nadiapub.com/IJAST/vol33/5.pdf
- Ramanathan, A., Krishnan, P. K., & Muraliraja, R. (2019). A review on the production of metal matrix composites through stir casting – Furnace design, properties, challenges, and research opportunities. Journal of Manufacturing Processes, 42, 213–245. https://doi.org/10.1016/j.jmapro.2019.04.017
- Ramezani, A. H., Hoseinzadeh, S., & Ebrahiminejad, Z. (2020). Statistical and fractal analysis of nitrogen ion implanted tantalum thin films. Applied Physics A, 126(6), 6. https://doi.org/10.1007/s00339-020-03671-7.
- Ramezani, A. H., Hoseinzadeh, S., Ebrahiminejad, Z., Hantehzadeh, M. R., & Shafiee, M. (2021). The study of mechanical and statistical properties of nitrogen ion-implanted Tantalum bulk. Optik, 225, 165628. https://doi.org/10.1016/j.ijleo.2020.165628
- Ravikumar, K., Kiran, K., & Sreebalaji, V. S. (2017). Characterization of mechanical properties of aluminium/tungsten carbide composites. Measurement, 102, 142–149. https://doi.org/10.1016/j.measurement.2017.01.045
- Ravikumar, K., Pridhar, T., & Sreebalaji, V. S. (2018). Mechanical properties and characterization of zirconium oxide (ZrO2) and coconut shell ash(CSA) reinforced aluminium (Al 6082) matrix hybrid composite. Journal of Alloys and Compounds, 765, 171–179. https://doi.org/10.1016/j.jallcom.2018.06.177
- Shabani, M. O., & Mazahery, A. (2013). The synthesis of the particulates Al matrix composites by the compocasting method. Ceramics International, 39(2), 1351–1358. https://doi.org/10.1016/j.ceramint.2012.07.073
- Shaikh, M. B. N., Arif, S., Aziz, T., Waseem, A., Shaikh, M. A. N., & Ali, M. (2019). Microstructural, mechanical & tribological behaviour of powder metallurgy processed SiC & RHA reinforced Al-based composites. Surfaces & Interfaces, 15, 166–179. https://doi.org/10.1016/j.surfin.2019.03.002
- Singh, J., & Chauhan, A. (2016). Characterization of hybrid aluminum matrix composites for advanced applications – A review. Journal of Materials Research and Technology, 5(2), 159–169. https://doi.org/10.1016/j.jmrt.2015.05.004
- Singh, J., & Chauhan, A. (2017). Fabrication characteristics & tensile strength of novel Al2024/SiC/red mud composites processed via stir casting route. Transactions of Nonferrous Metals Society of China, 27(12), 2573–2586. https://doi.org/10.1016/S1003-6326(17)60285-1
- Suthar, J., & Patel, K. M. (2018). Processing issues, machining, and applications of aluminum metal matrix composites. Materials and Manufacturing Processes, 33(5), 499–527. https://doi.org/10.1080/10426914.2017.1401713
- Thirugnanam, A., Sukumaran, K., Pillai, U. T. S., Raghukandan, K., & Pai, B. C. (2007). Effect of Mg on the fracture characteristics of cast Al–7Si–Mg alloys. Mater. Sci. Eng. A, 445-446, 405–414. https://doi.org/10.1016/j.msea.2006.09.063
- Verma, N., & Vettivel, S. C. (2018). Characterization and experimental analysis of boron carbide and rice husk ash reinforced AA7075 aluminium alloy hybrid composite. Journal of Alloys and Compounds, 741, 981–998. https://doi.org/10.1016/j.jallcom.2018.01.185
- Yildirim, M., & Ozyurek, D. (2013). The effects of Mg amount on the microstructure and mechanical properties of Al–Si–Mg alloys. Materials & Design, 51, 767–774. https://doi.org/10.1016/j.matdes.2013.04.089
- Zhang, J.-P., Fu, Q.-G., Qu, J.-L., Yuan, R.-M., & Li, H.-J. (2016). Blasting treatment and chemical vapor deposition of SiC nanowires to enhance the thermal shock resistance of SiC coating for carbon/carbon composites in combustion environment. Journal of Alloys and Compounds, 666, 77–83. https://doi.org/10.1016/j.jallcom.2016.01.124
- Zulfia, A., Zhakiah, T., & Dhaneswara, D. (2007). Characteristics of Al-Si-Mg reinforced SiC composites produced by stir casting route. Materials Sci. & Engr, 202, 0102089. https://iopscience.iop.org/article/ 10.1088/1757-899X/202/1/012089