Abstract
Adaptation of alternative and novel materials in place of traditional metals and alloys is getting higher attention in all domains of life. Tailored or customized fiber reinforced composite materials offer multiple advantages such as lighter systems with adequate strength, cost-effectiveness, and easier handling during fabrication and service time. In this review paper, attempts are made to comprehensively look into property improvement, fabrication, and characterization followed by researchers for natural fiber reinforced, natural fiber-synthetic fiber reinforced and hybrid natural fibers reinforced polymer-based composites. Composites having natural fibers as reinforcements had improved sound absorption and vibration damping properties. A combination of natural and synthetic fiber was found to be ideal for obtaining improved mechanical properties.
1. Introduction
In recent times, the use of composite materials in different structures has become popular since composites are well known for their excellent mechanical properties which makes them the material of choice for lightweight structures (Chawla, Citation2012). Classification of fiber reinforced composites based on the type of fiber as reinforcement is shown in .
Hybrid fiber reinforced polymer matrix composites are composites that have a polymer matrix reinforced by two or more different fibers. Low modulus fibers like glass and kevlar make the composites more resistant to impact while the high modulus fibers like boron and carbon improve the load bearing capacities and composite solidness (Bhatia et al., Citation2021; Forintos & Czigany, Citation2019; Priyanka et al., Citation2017). Stiffness, strength, fatigue resistance, impact resistance and fracture toughness can be improved by hybridizing. In general, the purpose of bringing two fiber types in a single composite is to maintain the advantages of both fibers and lessen some disadvantages. For instance, replacing carbon fibers in the middle of a laminate by cheaper glass fibers can significantly reduce the cost, while the flexural properties remain almost unaffected. Hybrid fiber reinforced composites are of three types: natural fiber reinforced hybrid composites like bamboo/kenaf, jute/sisal fiber reinforced hybrid composites, synthetic fiber reinforced hybrid composites like carbon/Kevlar, glass/aramid fiber reinforced composites and natural-synthetic fiber reinforced hybrid composites like bamboo/carbon, sisal/Kevlar fiber reinforced composites. The fibers can be put together in a wide variety of ways. depicts the three most significant configurations. The layers of two fiber types are layered on top of one another in the interlayer arrangement illustrated in . It is the simplest and direct way of hybridization. As seen in , two fiber types are blended inside the layers in intralayer configurations. Parallel bundles and other intralayer arrangements are also feasible. Additionally, the two fiber types can be combined or blended at the fiber level to create an intrayarn hybrid, as shown in . Combining two of these three setups will result in more intricate configurations (Supian et al., Citation2018; Swolfs et al., Citation2014).
Figure 2. The main hybrid composites configurations (a) interlayer (b) intralayer and (c) intrayarn. (Reproduced with permission from Elsevier)(Swolfs et al., Citation2014).
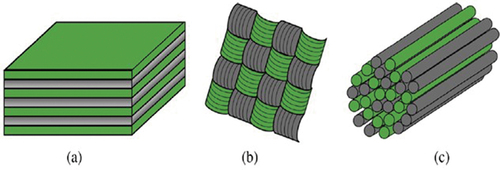
Khieng et al. (Khieng et al., Citation2021) summarized the effect of strain rates on the mechanical properties of natural fiber reinforced polymer matrix composites. The effect of strain rates on the failure of behaviour of composites were also analysed. The results of the methods or procedures utilised for characterising strain rates have been summarised in this study. It was observed that the mechanical characteristics, quantity and size of natural filler, as well as the kinds of polymer matrix, were the main determinants of how well the composite performed at varied strain rates.
Given the importance of fiber reinforced polymer matrix composites in various applications in automotive and aerospace industries, this present review aims at studying the effects of using natural fibers as reinforcement instead of or along with synthetic fibers . This article compares the physical properties, thermal stability, mechanical properties, sound absorption, vibration damping and aging properties of natural fiber reinforced composites, natural fiber reinforced hybrid composites, natural/synthetic fiber reinforced hybrid composites and synthetic fiber reinforced hybrid composites. The methodology of the work is depicted in .
2. Fabrication of polymer matrix composites
The different methods used to fabricate fiber-reinforced polymer matrix composites are Hand lay-up method, compression moulding, Injection moulding, Vacuum Bagging, Resin transfer moulding, Pultrusion, Filament winding as shown in . The different fabrication techniques of composites as per the literatures studied are shown in .
Table 1. Advantages and disadvantages of different fabrication methods of polymer matrix composites (Chawla, Citation2012; Liu, Citation2012)
Table 2. Fabrication techniques used as per the literatures studied
3. Physical characterization
The mechanical qualities of a composite are mostly determined by its physical properties. Fick’s law of moisture diffusion assumes that moisture concentration gradient is the potential for mass transfer through a unit area of a section of a material, moisture diffusion follows a single free-phase absorption model in which the water molecules are not combined with the absorbing material, and diffusion occurs in a single direction perpendicular to the plane of the absorbing material (Apeagyei et al., Citation2015).
3.1. Natural fiber reinforced composites
When polymer matrix composites are exposed to moisture or water, absorption of water takes place by diffusion through the matrix. When composites are exposed to moisture for several days, the moisture concentration increases with time and reaches equilibrium. The absorption rate is much lesser than the desorption rate. Dhakal et al. (Dhakal et al., Citation2007) compared the quantity of water absorbed of composites having different fiber volume fractions of hemp fiber as reinforcements. Because there were more voids and cellulose in composites with a high fiber volume percentage, the quantity of moisture absorbed was the largest. Cracks in the composite aid in flow of water molecules. The tensile and flexural strength reduced with moisture absorption. The SEM images showing the effect of water molecules are shown in .
Figure 4. Failure of composite by (a) Matrix cracking (b) Fracture along the interface (c) Fiber-matrix debonding caused due to attack by water molecules (Reproduced with permission from Elsevier)(Dhakal et al., Citation2007).
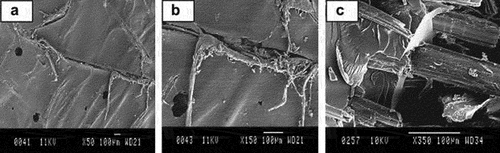
Thakur et al. (Thakur & Singha, Citation2010) studied mechanical and thermal properties along with swelling behaviour, moisture absorption and chemical resistance of phenol formaldehyde matrix composites having pine needles as reinforcement. Pine needles of different sizes were used. Long fiber composites had highest moisture absorption. Composites had better wear resistance, compressive strength and flexural strength than phenol formaldehyde resin. Mahesha et al. (Mahesha et al., Citation2016) compared the density and amount of water absorbed by Grewia Serulata fiber reinforced polyester composites having different percentages of fibers. Composites with high fiber volume fraction had higher percentage of voids. Composites with 20% fiber volume fraction absorbed more amount of water than neat resin specimen.
3.2. Natural fiber-reinforced hybrid composites
Moisture by weight is used to measure the moisture absorbed in the composite. The moisture content is measured by weighing the composite at ambient conditions then it is drying and reweighing. The weight change due to moisture content is found by calculating the difference between the two. Venkateshwar et al. (Venkateshwaran et al., Citation2011) calculated the amount of water absorbed by banana/sisal fiber reinforced hybrid composites. The composites strength improved slightly after hybridization. Hybridization reduced moisture absorption.
The mechanical properties, thermal properties, strength and fatigue resistance and corrosion resistance of composites are affected if voids are present in the composite. Voids can be the site where cracks are initiated in a composite and also can allow moisture to penetrate. Boopalan et al. (Boopalan et al., Citation2013) evaluated the amount of moisture absorbed by composites having jute and banana fibers as reinforcements. Composites with 50:50 Jute/banana fiber weight ratio showed minimum moisture absorption. Devireddy and biswas (Devireddy & Biswas, Citation2016) compared the density, void content and moisture absorption properties of composites having different weight fractions of banana and jute fibers. The experimentally measured density values are lower than the theoretically calculated values due to voids. As the fiber percentage increased, the number of voids and amount of water absorbed increased. Composites reinforced with more percentage of banana fibers absorbed more amount of water. Asim et al. (Asim et al., Citation2018) compared the density, number of voids and water absorption of composites having silane treated and untreated kenaf and pineapple fiber as reinforcement. Hybrid composites having treated fibers had the highest density, the lowest void content and lowest water absorption when compared to untreated hybrid composites. Kumar et al. (S. Kumar et al., Citation2021) fabricated Grewia optiva and hybrid G. optiva/Bauhinia vahlii fiber reinforced composites and studied their dry sliding wear behaviour and mechanical properties. Increase in void content, water absorption and decrease in density occurred due to increase in Grewia optiva and hybrid G. optiva/Bauhinia vahlii content. Ramlee et al. (Azlina Ramlee et al., Citation2021) compared the amount of water absorbed and void content of oil palm/bagasse fiber reinforced hybrid composites subjected to different surface treatments. Least amount of water absorbed and void content was observed for silane treated composite having 30 wt.% oil palm fiber and 35 wt.% bagasse fiber as reinforcement. Composites that underwent silane treatment had better properties than composites that were treated with hydrogen peroxide. Ibrahim et al. (Ibrahim et al., Citation2020) calculated the density, moisture content, water absorption rate and studied the morphological properties of cornhusk and sugar palm fiber reinforced hybrid composites. Hybridization showed a reduction in density, moisture content and water absorption rate.
3.3. Natural fiber/synthetic fiber reinforced hybrid composites
Zahari et al. (Zahari et al., Citation2015) calculated the tensile strength and amount of water absorbed by treated and untreated polypropylene/Ijuk fiber composites. Silane treatment was done by immersing the specimen in vinyltrimethoxy silane. Higher strength and high value of young’s modulus were found for silane treated composites. Silane treatment showed slight decrease in amount of water absorbed by the composite as shown in . Composite with high fiber content absorbed highest amount of water.
Figure 5. Water absorption percentage of treated and untreated composites of different fiber weight fractions as a function of time (Reproduced with permission from Elsevier)(Zahari et al., Citation2015).
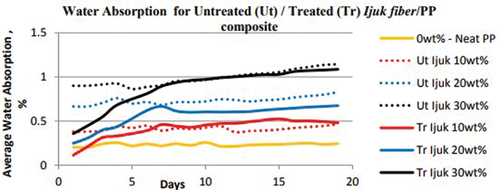
Espert et al. (Espert et al., Citation2004) analysed the characteristics of water absorption of natural fiber/polypropylene composites. The process of water absorption was said to follow Fick’s theory. The Young’s modulus and stress at maximum load were both very low due to water uptake. Higher values of strain were observed for water saturated composites with low fiber content. Atiqah et al. (Atiqah et al., Citation2019) analysed the impact of various treatments, as well as combinations of treatments, on the physical and thermal characteristics of composites having sugar palm and glass fibers as reinforcement. Composites that were combined 6% alkaline and 2% saline treated had the lowest density and water absorption rate. Safri et al. (Safri et al., Citation2020) evaluated the change in physical, mechanical and thermal properties due to benzoylation treatment and addition of glass fibers of sugarpalm fiber reinforced composites. The water absorption rate reduced due to hybridization with glass fibers and due to benzoylation treatment. Hybridization and benzoyl treatment increased the density of the composite. Afzaluddin et al. (Afzaluddin et al., Citation2019) studied the physical and mechanical properties of sugar palm/glass fiber reinforced hybrid composites. Composites of 40 wt.% were fabricated. Composites with 30 wt.% and 10 wt.% sugar palm had reduced water absorption, thickness swelling and higher density.
3.4. Synthetic fiber reinforced hybrid composites
Monticeli et al. (Monticeli et al., Citation2019) investigated the effect of stacking sequence on the porosity of carbon/glass fiber reinforced hybrid composites. Improvement in impregnation quality and reduction in porosity could be achieved through 3-D microstructure model. The composite having glass fiber concentration in the middle had good impregnation and thus had less voids. Li et al. (Li et al., Citation2019) studied the influence of temperature, salt concentration and temperature on water absorption and mechanical properties of carbon/glass fiber reinforced composite rod in salty solutions. Water absorption increased on the application of hydraulic pressure and as the temperature increased. Water absorption mainly occurred in the longitudinal direction. The diffusion coefficient and water absorption of composites as per the literature studied are shown in .
Table 3. Water absorption properties of different composites
4. Thermal properties of composites
4.1. Natural fiber reinforced composites
Krishnudu et al. (Mohana Krishnudu et al., Citation2020) conducted Thermogravimetric analysis (TGA), differential thermal analysis (DTA) and Fourier transform infrared spectroscopy (FTIR) on Abutilon Indicum fiber reinforced composites. Alkali treated composites showed improved thermal stability. Presence of C = O, -COO, C-O-C and -OH functional groups were found in the composite through FTIR. Tajvidi et al. (Tajvidi & Takemura, Citation2010) conducted TGA, DTA and Differential Scanning Calorimetry (DSC) on various natural fiber reinforced composites. Rice hulls reinforced composites had the least thermal stability. Addition of compatibilizer reduced the thermal stability of the composites.
4.2. Natural fiber reinforced hybrid composites
Jawaid et al. (Jawaid et al., Citation2015) investigated the thermal resistance of chemically treated oil palm empty fruit brunch/jute fiber reinforced hybrid composites. Fibers were chemically treated to increase fiber-matrix adhesion, resulting in stiffer hybrid composites. High thermal stability was observed for treated composites. Chee et al. (Chee et al., Citation2019) compared the thermal stability of composites having different weight fractions of bamboo and kenaf fibers as reinforcements. The highest thermal stability was for composites reinforced with bamboo fibers. Increased bamboo content increased the thermal stability and thermal oxidative stability. Nimanpure et al. (Nimanpure et al., Citation2019) evaluated the changes in the thermal behavior of composites having alkali treated sisal and kenaf fibers as reinforcement. The thermal stability of the composites was increased through hybridization. The thermal stability of the hybrid composite was increased by alkali treatment of the fibers. Karthi et al. (Karthi et al., Citation2021) calculated the thermal stability and wear rate of composites having banana and jute fibers reinforcement. The composites thermal stability was increased through hybridization.
4.3. Natural/synthetic fiber reinforced hybrid composites
Atiqah et al. (Atiqah et al., Citation2018) conducted Thermogravimetric analysis (TGA) of composites reinforced with sugar palm and glass fibers. Increase in onset and maximum decomposition temperature was observed for composite with high content of sugar palm fiber. The inclusion of glass fibers enhanced the TGA properties of the composites. Naveen et al. (Naveen et al., Citation2019) analysed the thermal behaviour of cocos nucifera sheath (CNS)/Kevlar fiber reinforced hybrid composites by TGA, DMA and DSC. Highest thermal stability was observed for kevlar fiber reinforced composite. Hybrid composite having 75% kevlar and 25% CNS had highest thermal stability among hybrid composites and high char residue. Raja et al. (Raja et al., Citation2021) examined the thermal stability and degradation characteristics of composites having bamboo and glass fiber as reinforcement and nanoparticles as fillers. When coconut shell powder is added to hybrid composites, their thermal stability is diminished. Angrizani et al. (Angrizani et al., Citation2017) evaluated the thermal stability of curaua/glass fiber reinforced hybrid composites. The thermal stability of the composite increased due to the presence of glass fibers. Composites reinforced with glass fibers had higher glass transition temperature. Braga and Magalhaes (Braga & Magalhaes, Citation2015) conducted TGA of composites having jute and glass fibers as reinforcement. TGA revealed that composites with a higher proportion of jute fiber lost greater mass whereas composite having more percentage of glass fiber lost less weight with rise in temperature.
4.4. Synthetic fiber reinforced hybrid composites
Ghouti et al. (Ghouti, Citation2018) monitored the thermal degradation of composites having kevlar and carbon fibers as reinforcement. The hybrid composites had excellent resistance to thermal degradation as shown in . The use of carbon fibers increased the thermal characteristics of the composites.
Figure 6. Thermal resistance of kevlar and carbon fiber reinforced composites, adapted from Ghouti et al (Ghouti, Citation2018).
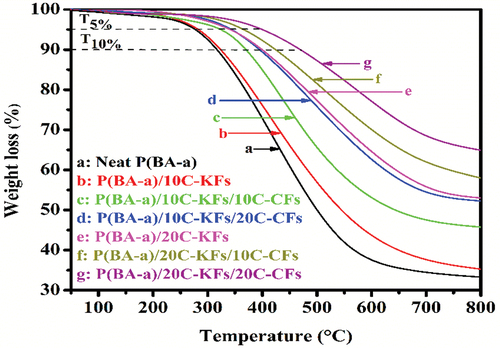
Zegaoui et al. (Zegaoui et al., Citation2019) fabricated kevlar/glass fibers reinforced with cyanate ester/benzoxazine resin matrix hybrid composites and evaluated their thermal behaviour. The degradation temperature, char yields and thermal stability were improved for hybrid composites. From FTIR and SEM, it was evident that enhanced dispersion and interfacial adhesion also led to improvement in properties.
5. Mechanical characterization
The mechanical testing of materials relies on certain logical variables. These variables help in better understanding and to facilitate the progress in assessing the different processes. Mechanical properties, for example, tensile, flexural, compressive and shear properties of a material are the fundamental design data in numerous applications.
5.1. Natural fiber reinforced composites
Tensile strength, tensile modulus and Poisson’s ratio are measured through tensile testing. The inter-laminar shear strength of a laminate, shear modulus, shear strength, tensile and compression moduli along with flexural and shear stiffness are determined by flexural testing. Sathishkumar et al. (Sathishkumar et al., Citation2012) investigated the tensile and flexural properties of snake grass reinforced polyester composites and compared them with other natural fiber reinforced composites. After the physical testing, the specimen that fractured were investigated for fiber pull-out. The tensile properties of snake grass fiber were better than other natural fibers. Maximum mechanical properties were observed for 25% fiber volume fraction. Franco and Gonzalez (Herrera-Franco & Valadez-González, Citation2005) studied the changes in mechanical properties of short henequen fiber reinforced composites due to fiber matrix adhesion. The tensile strength was greatly enhanced after alkaline treatment, saline treatment, and resin pre-impregnation. Flexural strength increased only when silane treatment was performed. Shear strength was increased when fibers underwent silane treatment. Singh et al. (Singh et al., Citation2018) analysed the changes in mechanical properties of jute fiber reinforced composites cured at different temperatures. The impact strength of the composite decreased with increase in curing temperature whereas tensile and flexural strength increased till 100°C and then decreased. At 100°C, best overall strength of the composite was achieved. Gupta et al. (Sharan Gupta et al., Citation2021) examined the influence of fiber orientation of natural fiber reinforced composites on their mechanical properties. Minimum stress for tensile test was observed at 0° orientation of fibers. Best flexural test results were observed for fibers at 90° orientation. In Brinell hardness test, the best results were obtained for 45° fiber orientation. Sarikaya et al. (Sarikaya et al., Citation2019) examined the mechanical characteristics of palm, birch, and eucalyptus fiber reinforced polymer matrix composites. When compared to mechanically treated fibers, chemically treated fibers have better characteristics. Composites reinforced with eucalyptus fibers had highest tensile strength and bending stress, whereas composites reinforced with palm fiber had the highest impact energy as seen in .
Figure 7. Mechanical properties of birch, eucalyptus and palm fiber reinforced composites (Reproduced with permission from Elsevier)(Sarikaya et al., Citation2019).
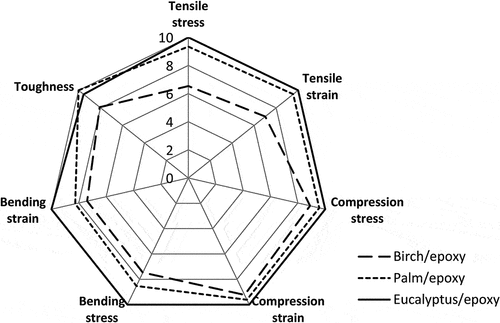
Sain et al. (Sain et al., Citation2005) compared the mechanical characteristics of old newsprint, kraft pulp and hemp fiber reinforced composites. Kraft pulp and hemp fiber reinforced composites outperformed glass fiber reinforced composites in terms of impact strength, tensile strength, and flexural strength. Costa et al. (Costa et al., Citation2020) evaluated the impact and flexural properties of mallow fiber reinforced composites. Composites with 30% mallow fiber had the highest flexural strength and absorbed the most impact energy as seen in .
Figure 8. Impact energy vs volume% of mallow fibers (Reproduced with permission from Elsevier)(Costa et al., Citation2020).

Rana et al. (Rana et al., Citation2003) looked at how adding a compatibilizer and an impact modifier to jute fiber reinforced composites affected their tensile, flexural, and impact strength. Composites that had impact modifiers were observed to have improved impact strength. The addition of a compatibilizer increased the tensile and impact characteristics while lowering the flexural qualities. shows the comparison of tensile and flexural properties of natural fiber reinforced composites.
Figure 9. Comparison of tensile and flexural properties of natural fiber reinforced composites (Sarikaya et al., Citation2019; Sathishkumar et al., Citation2012; Singh et al., Citation2018).
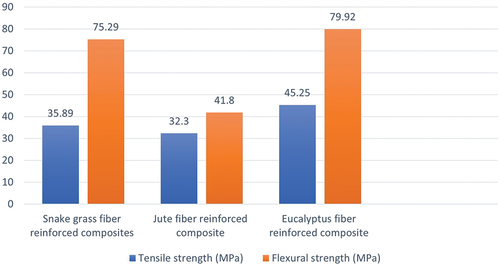
5.2. Natural fiber reinforced hybrid composites
Devireddy et al. (Devireddy & Biswas, Citation2017) evaluated the mechanical behaviour of composites reinforced with banana and jute fibers. About 30 wt.% of fiber loading had improved tensile strength, flexural strength and interlaminar shear strength. Fiber loading increased the void content of composites. Chaudhary et al. (Chaudhary et al., Citation2018) evaluated the mechanical properties of jute/hemp/flax fiber reinforced hybrid composites. Highest tensile strength, modulus and impact strength were observed for hybrid composites reinforced with jute, hemp and flax fibers. The flexural strength of the jute/hemp fiber reinforced composite was the highest.
5.3. Natural fiber/ synthetic fiber reinforced hybrid composites
Ramnath et al. (Vijaya Ramnath et al., Citation2014) evaluated the shear, tensile, impact and flexural properties of composites having intra-layer abaca-jute-glass fiber as the reinforcement. The impact, tensile, and flexural strength of the composites enhanced as the abaca percentage increased. Bhoopathi et al. (Bhoopathi et al., Citation2014) calculated the tensile strength, impact strength and flexural strength of banana, hemp and glass fiber reinforced hybrid composites. The banana/glass fiber reinforced hybrid composites had the maximum tensile strength. The flexural and impact strength of banana/hemp/glass fiber reinforced hybrid composites were the highest. Harish et al. (Harish et al., Citation2009) compared the mechanical characteristics of coir fiber reinforced composites and glass fiber reinforced composites. The impact strength, flexural strength and tensile strength were much lower for composites having coir as reinforcement. They suggested hybridization of coir with glass fibers to develop composites with new application. Ghasemzadeh-barvarz et al. (Ghasemzadeh-Barvarz et al., Citation2015) analysed the mechanical behaviour of flax/glass fiber reinforced composites. Composites having glass and flax fibers as reinforcement showed improved tensile strength, tensile modulus, impact strength and hardness. Ramesh and Anand (Ramesh & Anand, Citation2020) evaluated the effect of stacking sequence of fibers on the flexural and tensile characteristics of Kevlar/basalt fiber reinforced hybrid composites. Best tensile and flexural properties were observed for Kevlar-basalt-Kevlar-basalt-Kevlar-basalt-Kevlar composite.
5.4. Synthetic fiber reinforced hybrid composites
Guermazi et al. (Guermazi et al., Citation2014) examined the physical, thermal, and mechanical characteristics of composites having glass and carbon fibers as reinforcement. Composites reinforced with carbon fibers showed higher tensile strength (242–312 MPa) compared to hybrid composites (210 MPa) and composites having glass fibers as reinforcement (186 MPa). When compared to other composites, glass fiber reinforced composites have a substantially greater wear rate. Karthik et al. (Karthik et al., Citation2020) compared the tensile properties of Kevlar/glass/carbon fiber reinforced hybrid composites of different stacking sequences. The tensile strength of composites with three carbon fiber layers and two Kevlar layers was 385.09 MPa which was the highest. Song (Song, Citation2015) compared the mechanical properties of glass/carbon fiber reinforced hybrid composites and aramid/carbon fiber reinforced hybrid composites. The tensile behaviour of glass/carbon fiber reinforced hybrid composites and aramid/carbon fiber reinforced hybrid composites was quite similar, implying that carbon fiber presence impacted the tensile characteristics as seen in .
Figure 10. Stress–strain curve of (a) carbon/glass fiber reinforced composite and (b) carbon/aramid fiber reinforced composite (Reproduced with permission from Elsevier)(Song, Citation2015).
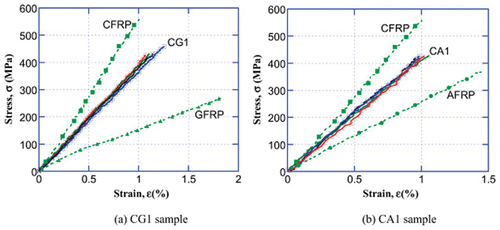
Batra and Dikshit (Batra & Dikshit, Citation2019) calculated the hardness, tensile and flexural strength of glass/carbon/aramid fiber reinforced hybrid composites. The flexural and tensile strength of composites having carbon fibers as reinforcement was the greatest. Carbon fiber content was increased, which improved the composite’s flexural and tensile strength. The tensile and flexural strength of natural fiber reinforced hybrid composites and synthetic fiber reinforced hybrid composites are shown in .
Table 4. Comparison of tensile and flexural strength of Hybrid fiber reinforced composites
6. Aging characteristics
Composites have many advantages which make them the ideal choice in many industrial, aerospace, structural and automotive applications but because of their unknown long-term properties when exposed to loads, high temperatures and environmental conditions, researchers are reluctant to use them in these applications. Continuous exposure to heat, moisture, chemicals, fatigue, loads and combinations of these factors can affect the stiffness and strength of material.
6.1. Natural fiber reinforced composites
Huang and Young (Huang & Bin Young, Citation2019) evaluated the mechanical properties and interfacial strength of bamboo fiber reinforced composites subjected to hygrothermal aging. Resin transfer moulding was used to fabricate the composite. Alkaline treatment of fibers increased the tensile strength of the composites. Improvements in tensile properties were observed as the diameter of fiber was reduced. Bamboo fiber reinforced composites were highly sensitive to moisture absorption which reduced the mechanical properties. Wang et al. (Wang et al., Citation2019) inspected the creep behaviour of composites having treated flax fibers as reinforcement subjected to hygrothermal aging. Acetylation, silanization, and alkalization treatments improved the composite’s mechanical characteristics. The treated specimen had lower water uptake than the untreated group. The chemically treated fiber composites had lower creep deformation. Liao et al. (Liao et al., Citation2012) studied the weight change mechanism of deep dried and naturally dried jute fiber reinforced composites. Ultrasonic wave inspection was used to study internal deterioration. Deep dried and naturally dried samples showed similar weight gain and loss ascending trend. Jute fiber played an important role for JFRP’s weight change mechanism during aging. Scida et al. (Scida et al., Citation2013) investigated the damage behaviour of hygrothermally aged flax fiber reinforced composites that underwent mechanical testing. The composites were manufactured using a hot press. Tensile test was carried out for both aged and non-aged samples. Tensile test samples were subjected to hygrothermal aging. First, the samples were dried for 24 hours then they were kept in a test chamber with relative humidity of 90% at temperature of 20°C and 40°C. During aging experiment at certain periods, the specimen were taken out and weighed. Weighing of specimen was stopped when weight reached saturation point. A significant reduction in stiffness was found whereas reduction in strength was much less. Acoustic emission study was done on the specimen to monitor the chronology of various damage mechanisms and also to characterize evolution of chronology. SEM observations allowed a better understanding of this evolution. Zain et al. (Zain et al., Citation2011) examined the mechanical characteristics of ageing composites having banana pseudo stem fiber as reinforcement. The composites flexural and impact strength were improved as a result of ageing. For tensile test, strength of composite reduced after aging. Chaudhary et al. (Chaudhary et al., Citation2020) examined the mechanical characteristics of aged plant fiber reinforced composites. Hardness of the composite was unaffected due to moisture uptake. Moisture absorption reduced the tensile properties. Due to moisture uptake, the flexural strength and modulus showed a huge reduction. The hydrophilic characteristic of natural fibers enhanced the quantity of moisture absorbed.
6.2. Natural fiber/Synthetic fiber reinforced hybrid composites
Thwe and Liao (Thwe & Liao, Citation2002) explored tensile and flexural capabilities of bamboo/glass fiber reinforced hybrid polypropylene composites (BGRP). By increasing the glass fiber content in BGRP, the tensile and flexural characteristics were improved. Hybrid BGRP composites experienced a massive reduction in tensile properties than composites reinforced with bamboo fibers. Fiore et al. (Fiore et al., Citation2017) evaluated the resistance of jute/basalt fiber reinforced hybrid composites to aging. Sandwich laminates had better resistance to aging than laminates with intercalated fiber layups. Laminate with basalt fiber as outer layers had better aging resistance due to the fact that basalt protects the inner layers of jute fiber from degradation. Akil et al. (Akil et al., Citation2014) explored the characteristics of glass/jute fiber reinforced hybrid composites that had been environmentally aged. After aging, composites reinforced with jute fibers and hybrid composites both lost 54% and 34% of their tensile strength, respectively. Calabrese et al. (Calabrese et al., Citation2019) examined the mechanical characteristics and ageing resistance of composites having glass and flax fibers as reinforcement. Addition of flax fibers to the composite increased the aging resistance of the composite.
6.3. Natural fiber reinforced hybrid composites
Ugochukwu et al. (Ugochukwu et al., Citation2021) monitored the scratch resistance of thermally aged kenaf, hemp and jute fiber reinforced hybrid composites. Thermally aged Jute fiber reinforced composites had higher coefficient of friction than thermally aged kenaf and hemp fiber reinforced composites. Due to thermal aging, jute fiber reinforced epoxy composites had highest fracture toughness and lowest penetration depth. Thermally aged jute fiber reinforced composites have very high scratch resistance. Fiore et al. (Fiore et al., Citation2017) analysed the properties of salt-fog aged basalt/jute fiber reinforced composites. Hybrid composites had high resistance to aging. Composites having basalt fibers as the external layers had the highest resistance to aging. Kufel and kuciel (Kufel & Kuciel, Citation2020) tested the mechanical characteristics of basalt/hazelnut shell fiber reinforced hybrid composites subjected to thermal aging. Tensile properties were improved for composites having fillers. Water absorption did not show much effect on mechanical properties. Significant decrease in tensile properties was observed for thermally aged samples as shown in .
Figure 11. Tensile strength of unaged and aged composites of different fiber weight percentage, adapted from Kufel and Kuciel (Kufel & Kuciel, Citation2020).
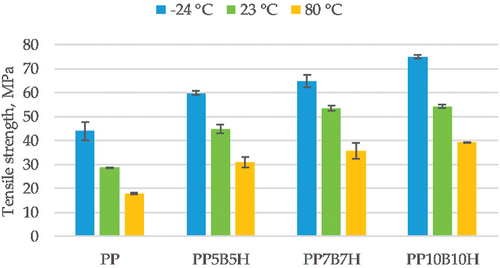
Yorseng et al. (Yorseng et al., Citation2020) analyzed the mechanical, thermal and water absorption characteristics of kenaf/sisal fiber reinforced bioepoxy composites subjected to accelerated aging. The mechanical properties did not vary much after aging. Composite had lower tensile properties than neat epoxy system.
6.4. Synthetic fiber reinforced Hybrid composites
Felipe et al. (Felipe et al., Citation2019) investigated the environmental aging effects on glass/kevlar fiber reinforced hybrid composites of different fiber types. Aging caused severe damage in all the laminates. Microbuckling and kevlar fiber fraying was observed. Jesthi and Nayak (Jesthi & Nayak, Citation2019) compared the properties of sea water aged carbon/glass fiber reinforced hybrid composites of different stacking sequences. Hybrid composites absorbed least amount of water. The mechanical properties were improved by both dry aging and sea water aging. Abd El-baky (Abd El-baky, Citation2019) compared the impact performance of sea water aged and distilled water aged glass/polypropylene hybrid composites to non-aged specimen. Hybridizing glass fiber reinforced composite with polypropylene fibers improved its impact strength and increased the amount of water absorbed. Composites absorbed more amount of distilled water than sea water. Dasari et al. (Dasari et al., Citation2021) studied the influence of cryogenic aging on the flexural properties of glass/carbon fiber reinforced hybrid composites of different stacking sequence. Cryogenic conditioning of 4 hours or 8 hours improves the flexural properties of the composites. Composites having two carbon fibers on the tensile side had the highest flexural strength, whereas composite having carbon fibers on each side of layers of glass fibers had the highest flexural modulus. The aging type and aging parameters used for different composites are highlighted in .
Table 5. Aging parameters data used by authors
7. Sound absorption characteristics
Noise control and its standards assume a significant function in establishing an acoustically satisfying environment. This can be accomplished when intensity of sound is brought down to a level that is not harmful to the human ears. Accomplishing a satisfying environment can be acquired by utilizing different strategies. One such method is sound retention or absorption. Sound absorption is the process by which a material, structure or item takes in sound energy when sound waves are experienced as opposed to reflecting it. Sound transmission loss is the ratio of sound energy passed through a material and the sound energy on incident side of material. Sound absorption coefficient and sound transmission loss are measured using the impedance tube and reverberation chamber method.
7.1. Natural fiber reinforced composites
The ratio of absorbed energy to incident energy, known as the sound absorption coefficient, defines how much energy is absorbed by a material. High value of sound absorption indicates that most of the sound is being absorbed and less is being reflected. Jayamani et al. (Jayamani et al., Citation2016) compared the sound absorption coefficients of betel nut fiber reinforced with polypropylene (thermoplastics) and unsaturated polyester (thermosets) matrix composites with different fiber loading and frequencies. The composites were fabricated in a hot press. Lowest sound absorption coefficient was observed for composites having polypropylene as the matrix. Composites with high fiber content had higher sound absorption coefficient. Taban et al. (Taban et al., Citation2019) compared the experimental results to the mathematical model of date palm fiber reinforced composites. Increase in thickness of sample and introduction of air gap improves the sound absorption property. Johnson-Champoux-Allard model was consistent with experimental results. Koruk et al. (Koruk et al., Citation2021) compared the sound absorption characteristics of composites having jute fiber as reinforcement and composites having luffa fiber as reinforcements having different thickness and fiber volume fractions. The sound absorption coefficient (SAC) enhanced as the fiber volume percent increased, while the sound transmission loss dropped for both composites. As the thickness increased the sound transmission loss (STL) also increased linearly. Hassan et al. (Hassan, Citation2020) evaluated the behaviour of cotton, coconut and sugarcane fiber reinforced composites when subjected to thermal, mechanical and acoustic testing. Coconut fiber reinforced composite had better sound absorption property than cotton fiber reinforced composite and sugarcane fiber reinforced composite. Sound absorption increases with increasing the fiber content. Hariprasad et al. (Hariprasad et al., Citation2020) compared the sound absorption behaviour of milkweed, kusha grass, sisal, banana and hay fiber reinforced composites. In the 500–2000 Hz range, a constant increase in sound absorption coefficient was observed for milkweed and hay fiber reinforced composites of 20 mm thickness. At higher frequency, increase in thickness has not much effect on sound absorption coefficient. Zhang et al. (Zhang et al., Citation2018) fabricated composites having plant fibers as reinforcement and assessed the sound absorption capabilities. Because of lumen and cell wall structure of plant fibers, plant fibers reinforced composites were discovered to have greater sound absorption capabilities than glass and carbon fiber reinforced composites. The sound absorption coefficients of different natural fiber reinforced composites are shown in .
Figure 12. Comparison of sound absorption coefficient of natural fiber reinforced composites (Jayamani et al., Citation2016; Koruk et al., Citation2021).
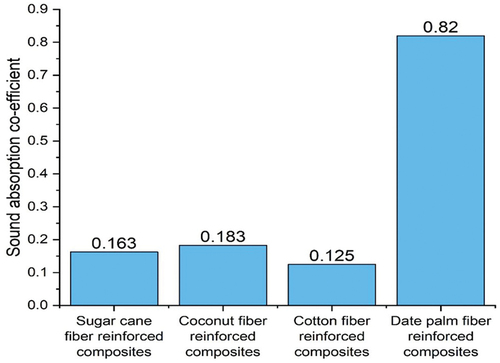
7.2. Natural fiber/synthetic fiber reinforced hybrid composites
Prabhakaran et al. (Prabhakaran et al., Citation2014) assessed the coefficient of absorption of composites having glass and flax fibers as reinforcement. Composites having flax fiber as reinforcement had a sound absorption coefficient that was 21.42% greater at 2000 Hz and 25% higher at 100 Hz than composites having glass fiber as reinforcement. Prabhu et al. (Prabhu et al., Citation2020) analyzed the sound absorption capabilities of composites having industrial waste tea leaf, kenaf and E-glass fibers as reinforcement. The sound absorption capabilities of composites containing 25% waste tea leaf fiber and 5% kenaf fiber were the best. Lee et al. (Lee et al., Citation2017) calculated the coefficient of sound absorption of composites having glass and flax fibers as reinforcement. At frequencies below 500 Hz, there was no sound absorbed. This is because as the frequency is low, the wavelength of sound is longer. Flax fiber reinforced epoxy composites are better at sound absorption than composites having glass fiber as reinforcement. Haris et al. (Haris et al., Citation2019) compared the sound transmission loss of flax/carbon fiber reinforced hybrid composite and aluminium. Flax fiber reinforced composite had higher sound transmission loss property than aluminium. Moreover, it was observed that hybridizing flax fiber reinforced composite with carbon fiber improved the sound transmission loss even more. Peng et al. (Peng et al., Citation2015) analyzed the mechanical and sound absorption characteristics of composites having wood and polyester fibers as reinforcement. At higher frequency, the sound absorption coefficients were high. Prabhu et al. (Prabhu et al., Citation2020) assessed the acoustic and mechanical characteristics of composites having snake grass and waste tea leaf fibers as reinforcement with glass fibers. Composite with 25% waste tea leaf fiber, 5% snake grass fiber and 10% glass fiber had the best sound absorption property and best mechanical property. Gokulkumar et al. (Gokulkumar et al., Citation2021) analyzed the mechanical and acoustical characteristics of pineapple fiber, waste tea leaf fiber and glass fiber reinforced hybrid composites having different fiber volume fractions. Composite with 25% waste tea leaf fiber has best sound absorption property.
7.3. Natural fiber reinforced hybrid composites
Ismail et al. (Ismail et al., Citation2019) compared the void content, tensile, vibration and sound absorption behaviour for composites having different volume fractions of kenaf and bamboo fibers as reinforcement. Hybrid composites of ratio 50:50 had highest tensile strength and modulus. 30:70 bamboo/kenaf composite had the highest damping factor and natural frequency. Hybrid composites of 50:50 ratio had slightly better damping properties. The composites overall characteristics were enhanced as a result of hybridization. Marichelvam et al. (Marichelvam et al., Citation2020) analyzed the sound absorption capabilities of composites having different volume fractions of bagasse and coconut coir fibers as reinforcement. Composite with 20% bagasse and 40% coir fiber reinforced hybrid composite had best sound absorption property. Singh and Mukhopadhyay (Singh & Mukhopadhyay, Citation2020) tested the sound transmission loss of composites having banana and coir fiber as reinforcement. The sound transmission loss increased with increase in content of fibers. Hybrid composites had highest sound transmission loss. Dhandapani and Megalingam (Dhandapani & Megalingam, Citation2021) compared the mechanical characteristics and coefficient of sound absorption of composites having different weight fractions of sisal and palm fibers as reinforcement. Highest sound absorption coefficient was observed for composite having 20 wt% of sisal and 15 wt% of palm fiber. Saravanan and Prakash (Saravanan & Prakash, Citation2021) investigated the sound absorption coefficient and noise reduction coefficient of jute/chicken feather fiber reinforced hybrid composites. Increase in wt.% of chicken feather fiber in the composite increases the noise absorption coefficient. The highest noise reduction coefficient of 0.6 was observed for the composite having 100% chicken feather fiber as the reinforcement. The sound absorption coefficient of natural fiber reinforced hybrid composites is shown in .
Table 6. Comparison of Sound absorption coefficients of Hybrid fiber reinforced composites
8. Vibration damping characteristics
Damping ability of composite and the natural frequency of the composite are the two main factors that decide the vibration characteristics of the system. Damping is the ability of a material to dissipate vibrations. Damping is measured by damping factor ζ. A high value of damping factor is desirable for reducing the resonance amplitude of vibration in a structure. Damping is important in mechanical equipment which are subjected to variable speeds to reduce the level of noise in the system. The damping factor is determined by the kind of fiber and resin used, the fiber’s orientation, the possibility of sliding at the matrix-reinforcement interface, any defects such as cracks or voids, and the viscoelastic nature of the fiber and resin.
8.1. Natural fiber reinforced composites
Composites having natural fibers as reinforcement are viscoelastic which aids in their damping properties. Viscoelastic materials can dissipate energy through mechanical deformation. By employing materials with high energy dissipation capacity, the structural damping of the system can be increased. Rajamanickam et al. (Rajamanickam et al., Citation2019) evaluated the mechanical characteristics and vibration damping ability of composites having kenaf fiber as reinforcement. A low value of damping factor was observed for composites having high content of fibers. For 35% fiber weight fraction, the damping factor was at its lowest value. Etaati et al. (Etaati et al., Citation2014) compared the vibration damping behaviour of coupled and uncoupled hemp fiber reinforced composites. Composite with 2.5 wt% anhydride-grafted polyethylene octane was the coupling agent and 30 wt% fiber had the highest damping ratio. Ramakrishnan et al. (Ramakrishnan et al., Citation2021) examined the free vibration behaviour of untreated and treated jute/nano-clay hybrid composites. The free vibration characteristics were studied by impulse hammer method. Treatment of fibers with 5% NaOH showed better natural frequency values. These properties were improved further by adding 5 wt. % nano clay. Kumar et al. (G. R. Kumar et al., Citation2021) studied the free vibration performances of phoenix sp./nano clay reinforced composites. Phoenix sp. fiber reinforced composites had improved vibration damping characteristics. NaOH treated fibers improved the vibration damping characteristics. Bulut et al. (Bulut et al., Citation2020) analyzed the mechanical and vibration damping characteristics of composites having basalt fiber as reinforcement and nano clay fillers. Composites having 2 wt% of nanoclay particles had improved damping and natural frequency but for 3 wt% of nanoclay particles the damping and natural frequency decreased. The damping factor of natural fiber reinforced composites is shown in .
Table 7. Comparison of Damping factor of Natural fiber reinforced composites
8.2. Natural fiber reinforced hybrid composites
Kumar et al. (Senthil Kumar et al., Citation2014) analysed the influence of weight percentage and length of fibers on free vibration behaviour and mechanical characteristics of short sisal fiber-reinforced composites and short banana fiber reinforced composites. Composites reinforced with sisal fibers exhibited better mechanical properties and free vibration characteristics than composites having banana fibers as reinforcement. Increasing the fiber content has a greater impact on mechanical qualities and vibration characteristics than varying the fiber length. Rajesh et al. (Rajesh et al., Citation2016) analyzed the vibration characteristics of composites reinforced with treated banana and sisal fibers. The method used to fabricate the composite was compression molding method. Composites having treated fibers as reinforcement showed increased stiffness and modulus. Murugan et al. (Murugan et al., Citation2019) tested the mechanical properties and vibration damping abilities of composites having different stacking sequences of flax and sisal fiber as reinforcement. Composite having flax fibers as the outer layers had better vibration damping properties than the composite with sisal fibers as the outer layers. This was further proved by finite element analysis. Bennet et al. (Bennet et al., Citation2015) analyzed the vibration characteristics of composites having Sansevieria cylindrica/coconut sheath fibers as reinforcement. Hybridization of Sansevieria cylindrica with coconut sheath fiber significantly improved the free vibration properties. The free vibration characteristics of pure and hybrid composites were enhanced by chemical treatment. When compared to other composites, those with coconut sheath fiber as the outer layers showed a greater natural frequency. Kumar et al. (K. S. Kumar et al., Citation2014) evaluated the tensile, impact, and vibration characteristics of different stacking sequences of coconut sheath/sisal fiber reinforced hybrid composites. Improved properties were observed for composites with silane-treated coconut sheath fibers as the outer layer. High natural frequencies are seen when identical fibers are piled together in composites.
8.3. Natural fiber/synthetic fiber reinforced hybrid composites
Flynn et al. (Flynn et al., Citation2016) evaluated the effects of hybridizing flax fiber with carbon fiber on the composite’s tensile, flexural, impact and vibration properties. In comparison to the other two samples, the Hybrid samples had the best vibrational properties. Assarar et al. (Assarar et al., Citation2015) compared the vibration damping behaviour of carbon/flax fiber reinforced hybrid composites of different stacking sequence. Laminates with flax layers outside and carbon layers inside had higher damping but slightly less bending modulus. Cihan et al. (Cihan et al., Citation2019) tested the mechanical characteristics and vibration damping ability of flax/E-glass fiber reinforced hybrid composites. An increase in damping is observed for hybrid composite having flax fibers placed on the outside, whereas tensile properties were significantly reduced. Hybrid composites having flax fibers as the outer layers had improved vibration damping properties and reduced tensile strength. Guen et al. (Le Guen et al., Citation2016) assessed the modulus of elasticity and damping capacity of flax/carbon fiber reinforced hybrid composites. Composites having flax fibers as reinforcement had four times higher damping capacity than composites reinforced with carbon fibers. Bozkurt et al. (Bozkurt & Gökdemir, Citation2018) tested the tensile characteristics and vibration damping ability of basalt/carbon fiber reinforced hybrid composites. The vibration damping capabilities of hybrid composites were enhanced. The damping property increased as the volume fraction of basalt fibers increased.
8.4. Synthetic fiber reinforced hybrid composites
Bulut et al. (Bulut et al., Citation2019) investigated the effect of hybridizing carbon/aramid fiber reinforced composites with glass fibers on the vibration damping properties. Samples having outer layers as S-glass and inner layers as carbon/aramid fibers reinforced polymers showed greater loss modulus. The addition of glass fibers to carbon/aramid fiber reinforced polymer composites improved the vibration damping. Bulut et al. (Bulut et al., Citation2016) studied the effect of changing fiber volume fractions of kevlar and glass fibers on the vibration damping and tensile strength of the hybrid composites. Kevlar fiber reinforced composite had the highest damping ratio, loss modulus and storage modulus. Among hybrid composites, composite having eight layers of kevlar and two layers of glass had the highest damping ratio, loss modulus and storage modulus. Alsaadi et al. (Alsaadi et al., Citation2020) studied the effect of inclusion of nanoclay particles on the vibration damping and mechanical properties of carbon/aramid intraply fiber reinforced composites. At nanoclay content of 1 and 2 wt%, the loss modulus and storage modulus are very high values. For every inclusion of nanoclay particles, the damping ratio decreased. The damping factors of hybrid fiber reinforced composites are shown in .
Table 8. Comparison of damping factor of Hybrid fiber reinforced composites
9. Applications
Natural fibers are replacing many synthetic fibers in composites. This is mainly due to low cost, easy availability and biodegradability of natural fibers. Reasonable mechanical properties are observed for composites reinforced with natural fibers, whereas composites reinforced with synthetic fibers have excellent mechanical properties. So, a combination of natural and synthetic fiber is ideal for applications where the cost of the material needs to be low and the composite needs to have reasonable mechanical properties. In applications where the main priority is excellent mechanical properties rather than the cost, synthetic fiber/synthetic fiber reinforced hybrid composites are ideal to be used. Another advantage of natural fibers are their visco-elastic nature which becomes useful in applications where vibration damping and sound absorption are a priority. So natural fiber/natural fiber reinforced hybrid composites tend to have excellent sound absorption and vibration damping properties.
Natural fibers possess the disadvantage of water absorption and degradation which affects the properties of the fiber and also the composite. Natural fibers are hydrophilic in nature. High moisture absorption, weak fiber-matrix interfacial adhesion, and poor fiber dispersion are all impacts of this hydrophilic characteristic. Natural fibers are extremely flammable, which restricts their use. By eliminating contaminants from the fiber’s surface, surface treatment increases the bonding characteristics of fibers with the matrix and increases the surface adhesion of natural fibers (Nurazzi et al., Citation2021). The applications of fiber reinforced polymer matrix composites are depicted in .
The following are some of the applications:
Aerospace and aeronautical: kevlar, glass and carbon fiber reinforced composites and combinations of them are mainly used in aerospace and aeronautical field due to their mechanical characteristics and resistance to thermal degradation.
Marine: Hybrid fiber reinforced composites tend to absorb less water than composites reinforced by single type of fiber (Jesthi & Nayak, Citation2019). Composites having basalt fibers as the external layers increase the resistance of composites to salt fog (Fiore et al., Citation2017). Boat and ship hulls are made of hybrid fiber reinforced composites.
Interior design: Composites reinforced with natural fibers good vibration damping and sound absorption property, making them ideal for sound proofing applications like auditoriums, theatres, music studios, etc. False ceilings, doors, partitions are made of hybrid fiber reinforced composites.
Automotive: Polymer matrix composites have various automobile applications. Metal components in automobiles are being replaced by hybrid composites due to good strength to weight ratio which could aid in reducing the amount of fuel consumed. Composites reinforced with natural fibers have many applications in automobiles like dash boards, door panels, trunk floor, glove box, etc. Composites having natural and synthetic fibers as reinforcement and composites having natural fiber as reinforcement are used to make Anti-roll bars in cars (Ravishankar et al., Citation2019).
Figure 13. Applications of fiber reinforced polymer matrix composites (Balakrishnan et al., Citation2016).; Mansor et al., Citation2019; Ravishankar et al., Citation2019; Sahu & Gupta, Citation2020).
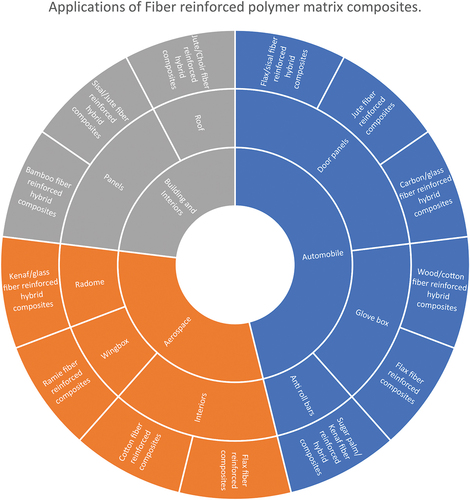
10. Conclusions
Composite materials are replacing conventionally used materials such as alloys and metals in most of the present day applications. Composite materials can be lighter than conventional materials making them superior with regard to strength to weight ratio. Hybrid fiber reinforced composites can have better properties than composites reinforced with a single type of fiber. Composites having a combination of natural and synthetic fiber as reinforcement are ideally used. From the literature studied,
Compression moulding and Hand lay-up method are the most commonly used methods to fabricate fiber reinforced polymer matrix composites and fiber reinforced hybrid polymer matrix composites.
Hybridization reduced the amount of water absorbed by the composites. Increase in fiber volume fraction, increase the amount of water absorbed by natural fiber reinforced composites and natural fiber reinforced hybrid composites.
Chemical treatment of fibers reduced the water absorption property of natural fiber reinforced composites, natural fiber reinforced hybrid composites and natural-synthetic fiber reinforced hybrid composites.
Chemical treatment of natural fibers improved the overall mechanical property of the composites. Composites reinforced with two types of natural fibers had better tensile and flexural properties than composites reinforced with a single type of natural fiber. Moreover, replacing one of the natural fibers with a synthetic fiber improved the tensile and flexural properties of the hybrid composites even more.
Surface treatment of fibers and addition of nano particles in the matrix improved the vibration damping properties. Addition of natural fibers significantly improved the vibration damping of the composite than the addition of synthetic fibers. Natural-synthetic fibers reinforced hybrid composites with natural fibers as the outer layers had better vibration damping properties.
Natural fibers are replacing synthetic fibers in composites as they have been found to reduce the overall weight and cost of the composite while obtaining reasonable properties.
Notes on Contributor
Dr Dayananda Pai is working as a Professor and Head of Department of Aeronautical and Automobile Engineering, Manipal Institute of Technology, Manipal Academy of Higher Education, Manipal. He holds B.E. (Mechanical), M. Tech.(Production Management) and Ph.D. (Mechanical Engg) degrees. He has 30 years of teaching experience. His areas of interest includes Materials - Composites, Manufacturing, Design and Optimization. ORCID ID: 0000-0003-0334-8718.
Dr Mahesha GT is an Associate Professor in the Department of Aeronautical and Automobile Engineering, Manipal Institute of Technology, Manipal Academy of Higher Education, Manipal. He holds B.E. (Mechanical), M. Tech. (Energy Systems) and Ph. D. (Composite Materials) degrees. He has 25 years of teaching experience. His areas of interest are Bio degradable composites, Internal combustion engines, Alternative fuels, Electric and Hybrid Vehicles. ORCID ID: 0000-0001-9477-8996.
Mr Abhijit Kudva is a research scholar from Department of Aeronautical and Automobile Engineering, Manipal Institute of Technology, Manipal Academy of Higher Education, Manipal.
Disclosure statement
No potential conflict of interest was reported by the author(s).
Additional information
Funding
References
- Abd El-baky, M. A. (2019, May). Experimental investigation on impact performance of glass–polypropylene hybrid composites: Effect of water aging. Journal of Thermoplastic Composite Materials, 32(5), 657–30. https://doi.org/10.1177/0892705718772876
- Afzaluddin, A., Jawaid, M., Salit, M. S., & Ishak, M. R. (2019, January). Physical and mechanical properties of sugar palm/glass fiber reinforced thermoplastic polyurethane hybrid composites. Journal of Materials Research and Technology, 8(1), 950–959. https://doi.org/10.1016/j.jmrt.2018.04.024
- Akil, H. M., Santulli, C., Sarasini, F., Tirillò, J., & Valente, T. (2014, April). Environmental effects on the mechanical behaviour of pultruded jute/glass fibre-reinforced polyester hybrid composites. Composites Science and Technology, 94, 62–70. https://doi.org/10.1016/j.compscitech.2014.01.017
- Alsaadi, M., Erkliğ, A., & Abbas, M. (2020, July). Effect of clay nanoparticles on the mechanical and vibration characteristics of intraply aramid/carbon fiber reinforced epoxy composite. Polymer Composites, 41(7), 2704–2712. https://doi.org/10.1002/pc.25568
- Angrizani, C. C., Ornaghi, H. L., Zattera, A. J., & Amico, S. C. (2017, March). Thermal and mechanical investigation of interlaminate glass/curaua hybrid polymer composites. Journal of Natural Fibers, 14(2), 271–277. https://doi.org/10.1080/15440478.2016.1193091
- Apeagyei, A. K., Grenfell, J. R. A., & Airey, G. D. (2015, May). Application of Fickian and non-Fickian diffusion models to study moisture diffusion in asphalt mastics. Materials and Structures/Materiaux Et Constructions, 48(5), 1461–1474. https://doi.org/10.1617/s11527-014-0246-2
- Asim, M., Paridah, M. T., Saba, N., Jawaid, M., Alothman, O. Y., Nasir, M., & Almutairi, Z. (2018, October). Thermal, physical properties and flammability of silane treated kenaf/pineapple leaf fibres phenolic hybrid composites. Composite Structures, 202, 1330–1338. https://doi.org/10.1016/j.compstruct.2018.06.068
- Assarar, M., Zouari, W., Sabhi, H., Ayad, R., & Berthelot, J. M. (2015, November). Evaluation of the damping of hybrid carbon-flax reinforced composites. Composite Structures, 132, 148–154. https://doi.org/10.1016/j.compstruct.2015.05.016
- Atiqah, A., Jawaid, M., Sapuan, S. M., Ishak, M. R., & Alothman, O. Y. (2018, October). Thermal properties of sugar palm/glass fiber reinforced thermoplastic polyurethane hybrid composites. Composite Structures, 202, 954–958. https://doi.org/10.1016/j.compstruct.2018.05.009
- Atiqah, A., Jawaid, M., Sapuan, S. M., Ishak, M. R., Ansari, M. N. M., & Ilyas, R. A. (2019, September). Physical and thermal properties of treated sugar palm/glass fibre reinforced thermoplastic polyurethane hybrid composites. Journal of Materials Research and Technology, 8(5), 3726–3732. https://doi.org/10.1016/j.jmrt.2019.06.032
- Azlina Ramlee, N., Jawaid, M., Abdul Karim Yamani, S., Syams Zainudin, E., & Alamery, S. (2021, March). Effect of surface treatment on mechanical, physical and morphological properties of oil palm/bagasse fiber reinforced phenolic hybrid composites for wall thermal insulation application. Construction and Building Materials, 276, 122239. https://doi.org/10.1016/j.conbuildmat.2020.122239
- Bakhori, S. N. M., Hassan, M. Z., Bakhori, N. M., Rashedi, A., Mohammad, R., Daud, M. Y. M., Aziz, S. A., Ramlie, F., Kumar, A., & J, N. (2022, June). Mechanical properties of PALF/kevlar-reinforced unsaturated polyester hybrid composite laminates. Polymers (Basel), 14(12), 2468. https://doi.org/10.3390/polym14122468
- Balakrishnan, P., John, M. J., Pothen, L., Sreekala, M. S., & Thomas, S. (2016). Natural fibre and polymer matrix composites and their applications in aerospace engineering. In Advanced Composite Materials for Aerospace Engineering (pp. 365–383). Woodhead Publishing. https://doi.org/10.1016/b978-0-08-100037-3.00012-2
- Batra, N. K., & Dikshit, I. (2019). Evaluation of mechanical properties of polytherimide reinforced carbon/glass/aramid hybrid composites. Materials Today: Proceedings, 33 3 , 1472–1476. https://doi.org/10.1016/j.matpr.2020.02.009
- Bennet, C., Rajini, N., Jappes, J. W., Siva, I., Sreenivasan, V. S., & Amico, S. C. (2015, February). Effect of the stacking sequence on vibrational behavior of Sansevieria cylindrica/coconut sheath polyester hybrid composites. Journal of Reinforced Plastics and Composites, 34(4), 293–306. https://doi.org/10.1177/0731684415570683
- Bhatia, S., Angra, S., & Khan, S. (2021). A review on mechanical and tribological characterization of boron carbide reinforced epoxy composite. Advanced Composite Materials, 30(4), 307–337. https://doi.org/10.1080/09243046.2020.1759482
- Bhoopathi, R., Ramesh, M., & Deepa, C. (2014). Fabrication and property evaluation of banana-hemp-glass fiber reinforced composites. Procedia Engineering, 97, 2032–2041. https://doi.org/10.1016/j.proeng.2014.12.446
- Boopalan, M., Niranjanaa, M., & Umapathy, M. J. (2013, August). Study on the mechanical properties and thermal properties of jute and banana fiber reinforced epoxy hybrid composites. Composites Part B: Engineering, 51, 54–57. https://doi.org/10.1016/j.compositesb.2013.02.033
- Bozkurt, Ö. Y., & Gökdemir, M. E. (2018, December). Effect of basalt fiber hybridization on the vibration-damping behavior of carbon fiber/epoxy composites. Polymer Composites, 39(S4), E2274–E2282. https://doi.org/10.1002/pc.24606
- Braga, R. A., & Magalhaes, P. A. A. (2015, June). Analysis of the mechanical and thermal properties of jute and glass fiber as reinforcement epoxy hybrid composites. Materials Science and Engineering C, 56, 269–273. https://doi.org/10.1016/j.msec.2015.06.031
- Bulut, M., Alsaadi, M., Erkliğ, A., & Alrawi, H. (2019, May). The effects of S-glass fiber hybridization on vibration-damping behavior of intraply woven carbon/aramid hybrid composites for different lay-up configurations. Proceedings of the Institution of Mechanical Engineers, Part C: Journal of Mechanical Engineering Science, 233(9), 3220–3231. https://doi.org/10.1177/0954406218813188
- Bulut, M., Bozkurt, Ö. Y., Erkliğ, A., Yaykaşlı, H., & Özbek, Ö. (2020, February). Mechanical and dynamic properties of basalt fiber-reinforced composites with nanoclay particles. Arabian Journal for Science and Engineering, 45(2), 1017–1033. https://doi.org/10.1007/s13369-019-04226-6
- Bulut, M., Erkliǧ, A., & Yeter, E. (2016, June). Experimental investigation on influence of kevlar fiber hybridization on tensile and damping response of kevlar/glass/epoxy resin composite laminates. Journal of Composite Materials, 50(14), 1875–1886. https://doi.org/10.1177/0021998315597552
- Calabrese, L., Fiore, V., Scalici, T., & Valenza, A. (2019, April). Experimental assessment of the improved properties during aging of flax/glass hybrid composite laminates for marine applications. Journal of Applied Polymer Science, 136(14). https://doi.org/10.1002/app.47203
- Chandrasekar, M., Siva, I., Kumar, T. S. M., Senthilkumar, K., Siengchin, S., & Rajini, N. (2020, November). Influence of fibre inter-ply orientation on the mechanical and free vibration properties of banana fibre reinforced polyester composite laminates. Journal of Polymers and the Environment, 28(11), 2789–2800. https://doi.org/10.1007/s10924-020-01814-8
- Chaudhary, V., Bajpai, P. K., & Maheshwari, S. (2018, January). Studies on mechanical and morphological characterization of developed jute/hemp/flax reinforced hybrid composites for structural applications. Journal of Natural Fibers, 15(1), 80–97. https://doi.org/10.1080/15440478.2017.1320260
- Chaudhary, V., Bajpai, P. K., & Maheshwari, S. (2020, January). Effect of moisture absorption on the mechanical performance of natural fiber reinforced woven hybrid bio-composites. Journal of Natural Fibers, 17(1), 84–100. https://doi.org/10.1080/15440478.2018.1469451
- Chawla, K. K. (2012). Composite materials: Science and engineering (3rd ed.). Springer. https://doi.org/10.1007/978-0-387-74365-3
- Chee, S. S., Jawaid, M., Sultan, M. T. H., Alothman, O. Y., & Abdullah, L. C. (2019, July). Evaluation of the hybridization effect on the thermal and thermo-oxidative stability of bamboo/kenaf/epoxy hybrid composites. Journal of Thermal Analysis and Calorimetry, 137(1), 55–63. https://doi.org/10.1007/s10973-018-7918-z
- Cihan, M., Sobey, A. J., & Blake, J. I. R. (2019, March). Mechanical and dynamic performance of woven flax/E-glass hybrid composites. Composites Science and Technology, 172, 36–42. https://doi.org/10.1016/j.compscitech.2018.12.030
- Costa, U. O., Nascimento, L. F. C., Garcia, J. M., Bezerra, W. B. A., & Monteiro, S. N. (2020, January). Evaluation of Izod impact and bend properties of epoxy composites reinforced with mallow fibers. Journal of Materials Research and Technology, 9(1), 373–382. https://doi.org/10.1016/j.jmrt.2019.10.066
- Dasari, S., Lohani, S., Gangineni, P. K., & Prusty, R. K. (2021, September). Effects of cryogenic aging on flexural behavior of advanced inter-ply hybrid fiber-reinforced polymer composites. Transactions of the Indian Institute of Metals, 74(9), 2171–2183. https://doi.org/10.1007/s12666-021-02288-5
- Devireddy, S. B. R., & Biswas, S. (2016, August). Physical and thermal properties of unidirectional banana-jute hybrid fiber-reinforced epoxy composites. Journal of Reinforced Plastics and Composites, 35(15), 1157–1172. https://doi.org/10.1177/0731684416642877
- Devireddy, S. B. R., & Biswas, S. (2017, July). Physical and mechanical behavior of unidirectional banana/jute fiber reinforced epoxy based hybrid composites. Polymer Composites, 38(7), 1396–1403. https://doi.org/10.1002/pc.23706
- Dhakal, H. N., Zhang, Z. Y., & Richardson, M. O. W. (2007, June). Effect of water absorption on the mechanical properties of hemp fibre reinforced unsaturated polyester composites. Composites Science and Technology, 67(7–8), 1674–1683. https://doi.org/10.1016/j.compscitech.2006.06.019
- Dhandapani, N., & Megalingam, A. (2021). Mechanical and sound absorption behavior of sisal and palm fiber reinforced hybrid composites. Journal of Natural Fibers, 1–14. https://doi.org/10.1080/15440478.2020.1863893
- Espert, A., Vilaplana, F., & Karlsson, S. (2004, November). Comparison of water absorption in natural cellulosic fibres from wood and one-year crops in polypropylene composites and its influence on their mechanical properties. Composites Part A: Applied Science and Manufacturing, 35(11), 1267–1276. https://doi.org/10.1016/j.compositesa.2004.04.004
- Etaati, A., Mehdizadeh, S. A., Wang, H., & Pather, S. (2014, February). Vibration damping characteristics of short hemp fibre thermoplastic composites. Journal of Reinforced Plastics and Composites, 33(4), 330–341. https://doi.org/10.1177/0731684413512228
- Felipe, R. C. T. S., Felipe, R. N. B., Batista, A. C. M. C., & Aquino, E. M. F. (2019, October). Influence of environmental aging in two polymer-reinforced composites using different hybridization methods: Glass/kevlar fiber hybrid strands and in the weft and warp alternating kevlar and glass fiber strands. Composites Part B: Engineering, 174, 106994. https://doi.org/10.1016/j.compositesb.2019.106994
- Fiore, V., Sanfilippo, C., & Calabrese, L. (2019, December). Influence of sodium bicarbonate treatment on the aging resistance of natural fiber reinforced polymer composites under marine environment. Polymer Testing, 80, 106100. https://doi.org/10.1016/j.polymertesting.2019.106100
- Fiore, V., Scalici, T., Badagliacco, D., Enea, D., Alaimo, G., & Valenza, A. (2017, January). Aging resistance of bio-epoxy jute-basalt hybrid composites as novel multilayer structures for cladding. Composite Structures, 160, 1319–1328. https://doi.org/10.1016/j.compstruct.2016.11.025
- Fiore, V., Scalici, T., Sarasini, F., Tirilló, J., Calabrese, L. (2017, May). Salt-fog spray aging of jute-basalt reinforced hybrid structures: Flexural and low velocity impact response. Composites Part B: Engineering, 116, 99–112. https://doi.org/10.1016/j.compositesb.2017.01.031
- Flynn, J., Amiri, A., & Ulven, C. (2016, July). Hybridized carbon and flax fiber composites for tailored performance. Materials and Design, 102, 21–29. https://doi.org/10.1016/j.matdes.2016.03.164
- Forintos, N., & Czigany, T. (2019, April 1). Multifunctional application of carbon fiber reinforced polymer composites: Electrical properties of the reinforcing carbon fibers – A short review. Composites Part B: Engineering, 162, 331–343. Elsevier Ltd. https://doi.org/10.1016/j.compositesb.2018.10.098
- Ghasemzadeh-Barvarz, M., Duchesne, C., & Rodrigue, D. (2015, December). Mechanical, water absorption, and aging properties of polypropylene/flax/glass fiber hybrid composites. Journal of Composite Materials, 49(30), 3781–3798. https://doi.org/10.1177/0021998314568576
- Ghouti, H. A. (2018, November). Multifunctional hybrid composites with enhanced mechanical and thermal properties based on polybenzoxazine and chopped Kevlar/carbon hybrid fibers. Polymers (Basel), 10(12), 1308. https://doi.org/10.3390/polym10121308
- Gokulkumar, S., Thyla, P. R., Prabhu, L., & Sathish, S. (2021). Characterization and comparative analysis on mechanical and acoustical properties of camellia sinensis/ananas comosus/glass fiber hybrid polymer composites. Journal of Natural Fibers, 18(7), 978–994. https://doi.org/10.1080/15440478.2019.1675215
- Guermazi, N., Haddar, N., Elleuch, K., & Ayedi, H. F. (2014). Investigations on the fabrication and the characterization of glass/epoxy, carbon/epoxy and hybrid composites used in the reinforcement and the repair of aeronautic structures. Materials and Design, 56, 714–724. https://doi.org/10.1016/j.matdes.2013.11.043
- Hariprasad, K., Ravichandran, K., Jayaseelan, V., & Muthuramalingam, T. (2020). Acoustic and mechanical characterisation of polypropylene composites reinforced by natural fibres for automotive applications. Journal of Materials Research and Technology, 9(6), 14029–14035. https://doi.org/10.1016/j.jmrt.2020.09.112
- Haris, N. I. N., Ilyas, R. A., Mohamad Zaki Hassan, S. M. S., Afdzaluddin, A., Rijal Jamaludin, K., Ahmad Zaki, S., & Ramlie, F. (2021). Dynamic Mechanical Properties and Thermal Properties of Longitudinal Basalt/Woven Glass Fiber Reinforced Unsaturated Polyester Hybrid Composites. Polymers, 13(19), 3343. https://doi.org/10.3390/polym13193343
- Haris, A., Kureemun, U., Tran, L. Q. N., & Lee, H. P. (2019, July). Noise reduction capability of hybrid flax fabric-reinforced polypropylene-based composites. Advanced Composite Materials, 28(4), 335–346. https://doi.org/10.1080/09243046.2018.1533347
- Harish, S., Michael, D. P., Bensely, A., Lal, D. M., & Rajadurai, A. (2009, January). Mechanical property evaluation of natural fiber coir composite. Materials Characterization, 60(1), 44–49. https://doi.org/10.1016/j.matchar.2008.07.001
- Hassan, T. (2020, March). Acoustic, mechanical and thermal properties of green composites reinforced with natural fiberswaste. Polymers (Basel), 12(3), 654. https://doi.org/10.3390/polym12030654
- Herrera-Franco, P. J., & Valadez-González, A. (2005, December). A study of the mechanical properties of short natural-fiber reinforced composites. Composites Part B: Engineering, 36(8), 597–608. https://doi.org/10.1016/j.compositesb.2005.04.001
- Huang, J. K., & Bin Young, W. (2019, June). The mechanical, hygral, and interfacial strength of continuous bamboo fiber reinforced epoxy composites. Composites Part B: Engineering, 166, 272–283. https://doi.org/10.1016/j.compositesb.2018.12.013
- Ibrahim, M. I. J., Sapuan, S. M., Zainudin, E. S., & Zuhri, M. Y. M. (2020, January). Preparation and characterization of cornhusk/sugar palm fiber reinforced cornstarch-based hybrid composites. Journal of Materials Research and Technology, 9(1), 200–211. https://doi.org/10.1016/j.jmrt.2019.10.045
- Ismail, A. S., Jawaid, M., & Naveen, J. (2019, July). Void content, tensile, vibration and acoustic properties of kenaf/bamboo fiber reinforced epoxy hybrid composites. Materials, 12(13), 2094. https://doi.org/10.3390/ma12132094
- Jawaid, M., Alothman, O. Y., Saba, N., Tahir, P. M., & Khalil, H. P. S. A. (2015, September). Effect of fibers treatment on dynamic mechanical and thermal properties of epoxy hybrid composites. Polymer Composites, 36(9), 1669–1674. https://doi.org/10.1002/pc.23077
- Jayamani, E., Hamdan, S., Bin Bakri, M. K., Kok Heng, S., Rahman, M. R., & Kakar, A. (2016, May). Analysis of natural fiber polymer composites: Effects of alkaline treatment on sound absorption. Journal of Reinforced Plastics and Composites, 35(9), 703–711. https://doi.org/10.1177/0731684415620046
- Jesthi, D. K., & Nayak, R. K. (2019, October). Evaluation of mechanical properties and morphology of seawater aged carbon and glass fiber reinforced polymer hybrid composites. Composites Part B: Engineering, 174, 106980. https://doi.org/10.1016/j.compositesb.2019.106980
- Karthi, N., Kumaresan, K., Rajeshkumar, G., Gokulkumar, S., & Sathish, S. (2021). Tribological and thermo-mechanical performance of chemically modified musa acuminata/corchorus capsularis reinforced hybrid composites. Journal of Natural Fibers, 1–14. https://doi.org/10.1080/15440478.2020.1870614
- Karthik, K., Rajamani, D., Manimaran, A., & Udayaprakash, J. (2020). Evaluation of tensile properties on glass/carbon/kevlar fiber reinforced hybrid composites. Materials Today: Proceedings, 39, 1655–1660. https://doi.org/10.1016/j.matpr.2020.06.049
- Khieng, T. K., Debnath, S., Ting Chaw Liang, E., Anwar, M., Pramanik, A., & Basak, A. K. (2021, May 1). A review on mechanical properties of natural fibre reinforced polymer composites under various strain rates. Journal of Composites Science, 5(5), 130. MDPI AG. https://doi.org/10.3390/jcs5050130
- Koruk, H., Ozcan, A. C., Genc, G., & Sanliturk, K. Y. (2021). Jute and luffa fiber-reinforced biocomposites: Effects of sample thickness and fiber/resin ratio on sound absorption and transmission loss performance. Journal of Natural Fibers, 1–16. https://doi.org/10.1080/15440478.2021.1907832
- Kufel, A., & Kuciel, S. (2020, January). Hybrid composites based on polypropylene with basalt/hazelnut shell fillers: The influence of temperature, thermal aging, and water absorption on mechanical properties. Polymers (Basel), 12(1). https://doi.org/10.3390/polym12010018
- Kumar, G. R., Hariharan, V., & Saravanakumar, S. S. (2021). Enhancing the Free Vibration Characteristics of Epoxy Polymers Using Sustainable phoenix Sp. Fibers and nano-clay for machine tool applications. Journal of Natural Fibers, 18(4), 531–538. https://doi.org/10.1080/15440478.2019.1636740
- Kumar, S., Patel, V. K., Mer, K. K. S., Gangil, B., Singh, T., & Fekete, G. (2021). Himalayan natural fiber-reinforced epoxy composites: Effect of grewia optiva/bauhinia vahlii fibers on physico-mechanical and dry sliding wear behavior. Journal of Natural Fibers, 18(2), 192–202. https://doi.org/10.1080/15440478.2019.1612814
- Kumar, K. S., Siva, I., Rajini, N., Jeyaraj, P., & Jappes, J. W. (2014, October). Tensile, impact, and vibration properties of coconut sheath/sisal hybrid composites: Effect of stacking sequence. Journal of Reinforced Plastics and Composites, 33(19), 1802–1812. https://doi.org/10.1177/0731684414546782
- le Guen, M. J., Newman, R. H., Fernyhough, A., Emms, G. W., & Staiger, M. P. (2016, March). The damping-modulus relationship in flax-carbon fibre hybrid composites. Composites Part B: Engineering, 89, 27–33. https://doi.org/10.1016/j.compositesb.2015.10.046
- Lee, H. P., Ng, B. M. P., Rammohan, A. V., & Tran, L. Q. N. (2017, January). An investigation of the sound absorption properties of flax/epoxy composites compared with glass/epoxy composites. Journal of Natural Fibers, 14(1), 71–77. https://doi.org/10.1080/15440478.2016.1146643
- Li, C., Xian, G., & Li, H. (2019, July). Combined effects of temperature, hydraulic pressure and salty concentration on the water uptake and mechanical properties of a carbon/glass fibers hybrid rod in salty solutions. Polymer Testing, 76, 19–32. https://doi.org/10.1016/j.polymertesting.2019.02.034
- Liao, M., Yang, Y., Yu, Y., & Hamada, H. (2012). HYDROTHERMAL AGEING MECHANISM OF NATURAL FIBER REINFORCED COMPOSITE IN HOT WATER. Proceedings of the ASME 2012 International Mechanical Engineering Congress and Exposition. Volume 3: Design, Materials and Manufacturing, Parts A, B, and C, ASME, Houston, Texas, USA, November 9-15, 2012. 1371–1378. Available: http://www.asme.org/about-asme/terms-of-use
- Liu, S.-J. (2012). Injection molding in polymer matrix composites. In Manufacturing Techniques for Polymer Matrix Composites (Pmcs) (pp. 15–46). Woodhead publishing series in Composite Science and Engineering. https://doi.org/10.1533/9780857096258.1.13
- Mahesha, G. T., Satish, S. B., Vijaya, K. M., & Bhat, K. S. (2016, September). Preparation of unidirectional grewia serrulata fiber-reinforced polyester composites and evaluation of tensile and flexural properties. Journal of Natural Fibers, 13(5), 547–554. https://doi.org/10.1080/15440478.2015.1081575
- Mansor, M. R., Nurfaizey, A. H., Tamaldin, N., & Nordin, M. N. A. (2019). Natural fiber polymer composites: Utilization in aerospace engineering. In Biomass, Biopolymer-Based Materials, and Bioenergy: Construction, Biomedical, and Other Industrial Applications (pp. 203–224). Woodhead publishing series in Composite Science and Engineering. https://doi.org/10.1016/B978-0-08-102426-3.00011-4
- Marichelvam, M. K., Kandakodeeswaran, K., & Geetha, M. (2020). Mechanical and acoustic properties of bagasse–coconut coir based hybrid reinforced composites. Journal of Natural Fibers, 1–10. https://doi.org/10.1080/15440478.2020.1854143
- Mejri, M., Toubal, L., Cuillière, J. C., & François, V. (2018, March). Hygrothermal aging effects on mechanical and fatigue behaviors of a short- natural-fiber-reinforced composite. International Journal of Fatigue, 108, 96–108. https://doi.org/10.1016/j.ijfatigue.2017.11.004
- Mohana Krishnudu, D., Sreeramulu, D., & Reddy, P. V. (2020, December). Alkali treatment effect: Mechanical, Thermal, Morphological, and Spectroscopy Studies on Abutilon Indicum Fiber-Reinforced Composites. Journal of Natural Fibers, 17(12), 1775–1784. https://doi.org/10.1080/15440478.2019.1598917
- Monticeli, F. M., Ornaghi, H. L., Cornelis Voorwald, H. J., & Cioffi, M. O. H. (2019, October). Three-dimensional porosity characterization in carbon/glass fiber epoxy hybrid composites. Composites Part A: Applied Science and Manufacturing, 125, 105555. https://doi.org/10.1016/j.compositesa.2019.105555
- Munde, Y. S., Ingle, R. B., & Siva, I. (2018, October). Investigation to appraise the vibration and damping characteristics of coir fibre reinforced polypropylene composites. Advances in Materials and Processing Technologies, 4(4), 639–650. https://doi.org/10.1080/2374068X.2018.1488798
- Murugan, R., Nithyanandan, N., & Sathya, V. (2019). Influence of Stacking Sequence on Free Vibration Characteristics of Epoxy-Based Flax/Sisal Composite Beams. In Advances in Materials and Metallurgy (pp. 171–183). Lecture notes in Mechanical Engineering, Springer. https://doi.org/10.1007/978-981-13-1780-4_18
- Nanthakumar, K., Yeng, C. M., & Chun, K. S. (2020, March). Tensile and water absorption properties of solvent cast biofilms of sugarcane leaves fibre-filled poly(lactic) acid. Journal of Thermoplastic Composite Materials, 33(3), 289–304. https://doi.org/10.1177/0892705718805526
- Naveen, J., Jawaid, M., Zainudin, E. S., Sultan, M. T. H., & Yahaya, R. (2019, January). Mechanical and moisture diffusion behaviour of hybrid Kevlar/Cocos nucifera sheath reinforced epoxy composites. Journal of Materials Research and Technology, 8(1), 1308–1318. https://doi.org/10.1016/j.jmrt.2018.07.023
- Naveen, J., Jawaid, M., Zainudin, E. S., Sultan, M. T. H., Yahaya, R., & Abdul Majid, M. S. (2019, July). Thermal degradation and viscoelastic properties of kevlar/cocos nucifera sheath reinforced epoxy hybrid composites. Composite Structures, 219, 194–202. https://doi.org/10.1016/j.compstruct.2019.03.079
- Nimanpure, S., Hashmi, S. A. R., Kumar, R., Bhargaw, H. N., Kumar, R., Nair, P., & Naik, A. (2019, February). Mechanical, electrical, and thermal analysis of sisal fibril/kenaf fiber hybrid polyester composites. Polymer Composites, 40(2), 664–676. https://doi.org/10.1002/pc.24706
- Norhasnan, N. H. A., Hassan, M. Z., Nor, A. F. M., Zaki, S. A., Dolah, R., Jamaludin, K. R., & Aziz, S. A. (2021, April). Physicomechanical properties of rice husk/coco peat reinforced acrylonitrile butadiene styrene blend composites. Polymers (Basel), 13(7), 1171. https://doi.org/10.3390/polym13071171
- Nurazzi, N. M., Asyraf, M. R. M., Fathimah, Athiyah S, Shazleen, S. S., Rafiqah, S. A., Harussani, M. M., Kamarudin, S. H., Razman, M. R., Rahmah, M, Zainuddin, E. S., Ilyas, R. A., Aisyah, H. A., Norrrahim, M. N. F., Abdullah, N, Sapuan, S. M., & Khalina, A. (2021, July 1). A review on mechanical performance of hybrid natural fiber polymer composites for structural applications. Polymers, 13(13), 1–47. MDPI AG. https://doi.org/10.3390/polym13132170.
- Palanikumar, K., & Subbiah, V. (2019, May). Bio caryota fiber reinforced polymer composites: Mechanical properties and vibration behavior analysis. Journal of Bionic Engineering, 16(3), 480–491. https://doi.org/10.1007/s42235-019-0039-y
- Peng, L., Song, B., Wang, J., & Wang, D. (2015). Mechanic and acoustic properties of the sound-absorbing material made from natural fiber and polyester. Advances in Materials Science and Engineering, 2015, 1–5. https://doi.org/10.1155/2015/274913
- Prabhakaran, S., Krishnaraj, V., Senthil Kumar, M., & Zitoune, R. (2014). Sound and vibration damping properties of flax fiber reinforced composites. Procedia Engineering, 97, 573–581. https://doi.org/10.1016/j.proeng.2014.12.285
- Prabhu, L., Krishnaraj, V., Gokulkumar, S., Sathish, S., Sanjay, M. R., & Siengchin, S. (2020). Mechanical, chemical and sound absorption properties of glass/kenaf/waste tea leaf fiber-reinforced hybrid epoxy composites. Journal of Industrial Textiles, 1–27. https://doi.org/10.1177/1528083720957392
- Prabhu, L., Krishnaraj, V., Sathish, S., Gokulkumar, S., Sanjay, M. R., & Siengchin, S. (2020, December). Mechanical and acoustic properties of alkali-treated sansevieria ehrenbergii/camellia sinensis fiber–reinforced hybrid epoxy composites: Incorporation of glass fiber hybridization. Applied Composite Materials, 27(6), 915–933. https://doi.org/10.1007/s10443-020-09840-4
- Priyanka, P., Dixit, A., & Mali, H. S. (2017, November). High-Strength hybrid textile composites with carbon, kevlar, and e-glass fibers for impact-resistant structures. A review. Mechanics of Composite Materials, 53(5), 685–704. https://doi.org/10.1007/s11029-017-9696-2
- Raja, D. B. P., Vettivel, S. C., & Prabhu, A. S. (2021, January). Influence of nanoparticles on thermal, mechanical and 3D analysis of hybrid bamboo/glass fibre-reinforced polymer composites. Transactions of the Indian Institute of Metals, 74(1), 179–193. https://doi.org/10.1007/s12666-020-02111-7
- Rajamanickam, S. K., Ravichandran, V., Sattanathan, S., Ganapathy, D., Arockia Dhanraj, J., & Hindustan Institute of Technology and Science, Sri Krishna College of Engineering and Technology. (2019). Experimental investigation on mechanical properties and vibration damping frequency factor of kenaf fiber reinforced epoxy composite. International Conference on Advances in Design, Materials, Manufacturing and Surface Engineering for Mobility, SAE International. https://doi.org/10.4271/2019-28-0167
- Rajesh, M., Pitchaimani, J., & Rajini, N. (2016). Free vibration characteristics of banana/sisal natural fibers reinforced hybrid polymer composite beam. Procedia Engineering, 144, 1055–1059. https://doi.org/10.1016/j.proeng.2016.05.056
- Ramakrishnan, S., Krishnamurthy, K., Rajeshkumar, G., & Asim, M. (2021, April). Dynamic mechanical properties and free vibration characteristics of surface modified jute fiber/nano-clay reinforced epoxy composites. Journal of Polymers and the Environment, 29(4), 1076–1088. https://doi.org/10.1007/s10924-020-01945-y
- Ramesh, V., & Anand, P. (2020). Evaluation of mechanical properties on Kevlar/Basalt fiber reinforced hybrid composites. Materials Today: Proceedings, 39, 1494–1496. https://doi.org/10.1016/j.matpr.2020.05.406
- Rana, A. K., Mandal, A., & Bandyopadhyay, S. (2003). Short jute fiber reinforced polypropylene composites: Effect of compatibiliser, impact modifier and fiber loading. Composites Science and Technology, 63 (6), 801–806. Available. www.elsevier.com/locate/compscitech
- Ravishankar, B., Nayak, S. K., & Kader, M. A. (2019, September). Hybrid composites for automotive applications – A review. Journal of Reinforced Plastics and Composites, 38(18), 835–845. https://doi.org/10.1177/0731684419849708
- Safri, S. N. A., Sultan, M. T. H., & Shah, A. U. M. (2020). Characterization of benzoyl treated sugar palm/glass fibre hybrid composites. Journal of Materials Research and Technology, 9(5), 11563–11573. https://doi.org/10.1016/j.jmrt.2020.08.057
- Sahu, P., & Gupta, M. K. (2020, January 1). A review on the properties of natural fibres and its bio-composites: Effect of alkali treatment. Proceedings of the Institution of Mechanical Engineers, Part L: Journal of Materials: Design and Applications, 234(1), 198–217. SAGE Publications Ltd. https://doi.org/10.1177/1464420719875163
- Sain, M., Suhara, P., Law, S., & Bouilloux, A. (2005). Interface modification and mechanical properties of natural fiber-polyolefin composite products. Journal of Reinforced Plastics and Composites, 24(2), 121–130. https://doi.org/10.1177/0731684405041717
- Saravanan, K., & Prakash, C. (2021). Study of acoustic properties of chicken feather fibre (CFF) and its hybrid composites. Journal of Natural Fibers, 18(4), 502–509. https://doi.org/10.1080/15440478.2019.1629560
- Sarikaya, E., Çallioğlu, H., & Demirel, H. (2019, June). Production of epoxy composites reinforced by different natural fibers and their mechanical properties. Composites Part B: Engineering, 167, 461–466. https://doi.org/10.1016/j.compositesb.2019.03.020
- Sathishkumar, T. P., Navaneethakrishnan, P., & Shankar, S. (2012, June). Tensile and flexural properties of snake grass natural fiber reinforced isophthalic polyester composites. Composites Science and Technology, 72(10), 1183–1190. https://doi.org/10.1016/j.compscitech.2012.04.001
- Scida, D., Assarar, M., Poilâne, C., & Ayad, R. (2013, May). Influence of hygrothermal ageing on the damage mechanisms of flax-fibre reinforced epoxy composite. Composites Part B: Engineering, 48, 51–58. https://doi.org/10.1016/j.compositesb.2012.12.010
- Senthil Kumar, K., Siva, I., Jeyaraj, P., Winowlin Jappes, J. T., Amico, S. C., & Rajini, N. (2014). Synergy of fiber length and content on free vibration and damping behavior of natural fiber reinforced polyester composite beams. Materials and Design, 56, 379–386. https://doi.org/10.1016/j.matdes.2013.11.039
- Sharan Gupta, U., Dharkar, A., Dhamarikar, M., Choudhary, A., Wasnik, D., Chouhan, P., Tiwari, S., & Namdeo, R. (2021). Study on the effects of fiber orientation on the mechanical properties of natural fiber reinforced epoxy composite by finite element method. Materials Today: Proceedings, 45, 7885–7893. https://doi.org/10.1016/j.matpr.2020.12.614
- Singh, V. K., & Mukhopadhyay, S. (2020). Studies on the effect of hybridization on sound insulation of coir-banana-polypropylene hybrid biocomposites. Journal of Natural Fibers. https://doi.org/10.1080/15440478.2020.1745116
- Singh, J. I. P., Singh, S., & Dhawan, V. (2018, September). Effect of curing temperature on mechanical properties of natural fiber reinforced polymer composites. Journal of Natural Fibers, 15(5), 687–696. https://doi.org/10.1080/15440478.2017.1354744
- Song, J. H. (2015, April). Pairing effect and tensile properties of laminated high-performance hybrid composites prepared using carbon/glass and carbon/aramid fibers. Composites Part B: Engineering, 79, 61–66. https://doi.org/10.1016/j.compositesb.2015.04.015
- Supian, A. B. M., Sapuan, S. M., Zuhri, M. Y. M., Zainudin, E. S., & Ya, H. H. (2018, August 1). Hybrid reinforced thermoset polymer composite in energy absorption tube application: A review. Defence Technology, 14(4), 291–305. China Ordnance Society. https://doi.org/10.1016/j.dt.2018.04.004
- Swolfs, Y., Gorbatikh, L., & Verpoest, I. (2014). Fibre hybridisation in polymer composites: A review. Composites Part A: Applied Science and Manufacturing, 67, 181–200. Elsevier Ltd. https://doi.org/10.1016/j.compositesa.2014.08.027
- Taban, E., Khavanin, A., Jafari, A. J., Faridan, M., & Tabrizi, A. K. (2019, June). Experimental and mathematical survey of sound absorption performance of date palm fibers. Heliyon, 5(6), e01977. https://doi.org/10.1016/j.heliyon.2019.e01977
- Tajvidi, M., & Takemura, A. (2010, May). Thermal degradation of natural fiber-reinforced polypropylene composites. Journal of Thermoplastic Composite Materials, 23(3), 281–298. https://doi.org/10.1177/0892705709347063
- Thakur, V. K., & Singha, A. S. (2010, January). Mechanical and water absorption properties of natural fibers/polymer biocomposites. Polymer - Plastics Technology and Engineering, 49(7), 694–700. https://doi.org/10.1080/03602551003682067
- Thwe, M. M., & Liao, K. (2002). Effects of environmental aging on the mechanical properties of bamboo ± glass ®ber reinforced polymer matrix hybrid composites. Composite Part A: Applied Science and Manufacturing, 33 (1), 43–52. Available. www.elsevier.com/locate/compositesa
- Ugochukwu, S., Ridzuan, M. J. M., Abdul Majid, M. S., Cheng, E. M., Razlan, Z. M., & Marsi, N. (2021, April). Effect of thermal ageing on the scratch resistance of natural-fibre-reinforced epoxy composites. Composite Structures, 261, 113586. https://doi.org/10.1016/j.compstruct.2021.113586
- Venkateshwaran, N., ElayaPerumal, A., Alavudeen, A., & Thiruchitrambalam, M. (2011, August). Mechanical and water absorption behaviour of banana/sisal reinforced hybrid composites. Materials and Design, 32(7), 4017–4021. https://doi.org/10.1016/j.matdes.2011.03.002
- Vijaya Ramnath, B., Manickavasagam, V. M., Elanchezhian, C., Vinodh Krishna, C., Karthik, S., & Saravanan, K. (2014). Determination of mechanical properties of intra-layer abaca-jute-glass fiber reinforced composite. Materials and Design, 60, 643–652. https://doi.org/10.1016/j.matdes.2014.03.061
- Wang, X., Petrů, M., & Yu, H. (2019, May). The effect of surface treatment on the creep behavior of flax fiber reinforced composites under hygrothermal aging conditions. Construction and Building Materials, 208, 220–227. https://doi.org/10.1016/j.conbuildmat.2019.03.001
- Yorseng, K., Rangappa, S. M., Pulikkalparambil, H., Siengchin, S., & Parameswaranpillai, J. (2020, February). Accelerated weathering studies of kenaf/sisal fiber fabric reinforced fully biobased hybrid bioepoxy composites for semi-structural applications: Morphology, thermo-mechanical, water absorption behavior and surface hydrophobicity. Construction and Building Materials, 235, 117464. https://doi.org/10.1016/j.conbuildmat.2019.117464
- Zahari, W. Z. W., Badri, R. N. R. L., Ardyananta, H., Kurniawan, D., & Nor, F. M. (2015). Mechanical properties and water absorption behavior of polypropylene/ijuk fiber composite by using silane treatment. In 2nd International Materials, Industrial, and Manufacturing Engineering Conference, 4-6 February, Bali, Indonesia, 2, 573–578. https://doi.org/10.1016/j.promfg.2015.07.099
- Zain, S. N. Z. M., Ismarrubie, Z. N., & Zainudin, E. S. (2011). The effect of aging temperature on mechanical properties of banana pseudostem fiber reinforced polymer composite. Key Engineering Materials, 471–472, 444–448. https://doi.org/10.4028/www.scientific.net/KEM.471-472.444
- Zegaoui, A., Derradji, M., Dayo, A. Q., Medjahed, A., Zhang, H.-Y., Cai, W.-A., Liu, W.-B., Ma, R.-K., & Wang, J. (2019, August). High-performance polymer composites with enhanced mechanical and thermal properties from cyanate ester/benzoxazine resin and short kevlar/glass hybrid fibers. High Performance Polymers, 31(6), 719–732. https://doi.org/10.1177/0954008318793181
- Zhang, S., Li, Y., & Zheng, Z. (2018, December). Effect of physiochemical structure on energy absorption properties of plant fibers reinforced composites: Dielectric, thermal insulation, and sound absorption properties. Composites Communications, 10, 163–167. https://doi.org/10.1016/j.coco.2018.09.006