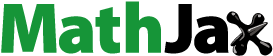
Abstract
Nanotechnology has opened up new avenues for industrial efficiency and performance. The Al2O3-Cu/water hybrid nanofluid with and without insert is analyzed numerically and validated to show heat transfer enhancement. A circular duct with inserts, a tube length of 3 m, a hydraulic diameter of 0.01 m, tube wall with a constant heat flux of 20 kW/m2, and a twist ratio of 125 were used to examine Al2O3-Cu/water hybrid nanofluid in turbulent regime. At Re = 20,000, due to insertion of twisted tape, there is an additional mixing of fluid that takes place, leading towards increase in temperature of around 1–1.75% when compared with that of without inserts. The Nusselt number is improved for plain twisted tape tube by 1.5–2.0% higher than plain tube as revealed in the result. Moreover, there is a 1.01 times improvement in performance evaluation criteria when twisted tape is inserted instead of plain tube.
1. Introduction
The world’s temperature is steadily rising above pre-industrial levels due to an increase in energy demand, and the release of radiation and toxic gases has resulted in extreme weather conditions (Harish Kumar et al., Citation2022). As a result, the use and development of several heat transfer enhancement techniques was prompted by the engineering understanding of the need to improve the thermal performance of heat exchanger in order to effect energy, cost, material, as well as a consequential mitigation of environmental degradation (Emad et al., Citation2017). Due to their superior qualities, research on various nanofluids for improving performance in thermal applications has attracted a lot of attention in recent years (Ahmed et al., Citation2012; Pehlivan et al., Citation2013). One of the most difficult issues that thermal engineers face is improving heat transfer in heat exchangers. As technology advances, the demand for faster and more efficient heat transfer from smaller regions or across smaller temperature differences grows. Because water, oil, and ethylene glycol mixtures lack sufficient heat transfer qualities to fulfill the increasing demand for improved heat transmission (Hamdi et al., Citation2019; Jiat Kendrick Wong, Citation2021; Moghaddami et al., Citation2012).
Nanotechnology has opened up new avenues for industrial efficiency and performance. The use of nanofluids to improve heat transfer performance is one of the suggested petitions. To increase the effectiveness of temperature exchangers, nanofluids are frequently employed. The thermal conductivity of nanoparticles, size, diameter, and volume concentration were all factors in determining the rate of heat transfer (Kumar & Dr, Citation2017; Mehrjou et al., Citation2015). Cars, energy storage, electronic component cooling, solar absorbers, and nuclear reactors (Nasrin et al., Citation2021) are among the most common uses of nanofluids. In flowing fluid, mechanical and heat transfer qualities are of particular interest due to their numerous industrial uses in chemicals, energy, machinery, and other industries. To boost heat transfer efficiency, nanoparticles are included in the base fluid in this example (Arjun , K. S., Rakesh , K., Citation2020). The advent of nanotechnology has forced numerous fields of basic science and engineering to confront new problems (Lin et al., Citation2022). In engineering thermal systems, convective heat transfer must be increased in order to reduce heat exchanger size, weight, and cost. It is being tried multiple times to improve heat transfer by using roughened surfaces. A variety of rib-groove channel layouts and temperature gradients have been researched during the past few decades by researchers (Abdulwahab, Citation2014). M. E. Nakhchi and J. A. Esfahani (Navaei et al., Citation2015) examined the heat transfer and friction factor of CuO nanoparticles dispersed in water/propylene blend in a plain tube (PT) with and without twisted tape inserts. As the volume concentration of nanoparticles in the base fluid rises, the Nusselt number of CuO nanofluids increases significantly over that of the base fluids. Nanofluids have a negligible effect of friction on the base fluid in a planar tube. It is possible to improve heat transfer in CuO nanofluids by using tape inserts with several twists, which reduce friction while improving heat transfer. S. Aljabair et al. (Nakhchi & Esfahani, Citation2020) numerically examined H2O-Al2O3 nanofluid heat transfer by natural convection inside symmetrical and asymmetrical corrugated annuli at various nanoparticle volume fractions and Rayleigh numbers. The stream function intensity and heat transfer rate increase with increasing nanoparticle volume fraction and Rayleigh number. In contrast to symmetrical annuli, unsymmetrical annuli have a higher rate of heat transfer.
H. Shiravi et al. (Aljabair et al., Citation2020) carried out an experimental investigation using carbon nanofluid in turbulent regime to assess the variation of CHTC, Nusselt number, and pressure drop in concentrations of 0 to 0.4 mass% of nanofluid. The result shows that the value of CHTC enhanced with increasing nanofluid concentration up to 0.21% and then reduced. Moreover, increasing Reynolds leads to improvement in both Nusselt number and the CHTC, but friction factor is decreased.
A.A. Rabienataj Darzi et al. (Hossein Shiravi et al., Citation2020) conducted experiments to analyze the effect of nanofluid on turbulent heat transfer and pressure drop inside concentric tubes using base fluid (H2O) and nanoparticle (SiO2) with mean diameter of 30 nm, respectively. Study was performed for both PT and five roughened tubes with different heights and pitches of corrugations. Thus, the results show that adding the nanoparticles in tube with high height and small pitch of corrugations enhances the heat transfer with a minimum pressure drop penalty.
For nanofluid flow, S. Kumar et al. (Rabienataj Darzi et al., Citation2012) and A. S. Navaei et al. (Kumar et al., Citation2017) evaluated the turbulent heat transfer in square channels with protruding rib morphologies varying from 4000 to 18,000 Reynolds numbers. In addition, nanoparticles (Al2O3, CuO, and ZnO) of various concentrations () and sizes (dnp) are disseminated in water (base fluid). The results demonstrate that Al2O3 nanofluid has the highest average Nusselt number value in comparison to other nanofluids. As concentration increases, the average Nusselt number rises, while the average particle diameter decreases. Increases in volume fraction, roughness height, and Reynolds number all contributed to a rise in the Nusselt number. However, when the nanoparticles diameter increased, it dropped. After glycerin and ethylene glycol, water-SiO2 was found to have the lowest Nusselt number, followed by water and glycerin. Ashkan Vatani and H.A. Mohammed (Navaei et al., Citation2015) and Sh.M. Vanaki et al. (Ashkan & Mohammed, Citation2013) also come to similar conclusions.
Nanofluid flow through a thermally growing, hydraulically developing pipe was studied numerically by Masoud Ziaei-Rad and Maryam Beigi (Sh et al., Citation2014). According to experimental results, with increasing nanoparticle volume fraction, the thermal entrance length is reduced and heat transfer rises as a result. Increasing the volume fraction of nanoparticles by 10% increases the average Nusselt number by a whopping 15%.
According to the experiments of A. Moghadassi et al. (Ziaei-Rad & Beigi, Citation2016) and S. Suresh et al. (Moghadassi et al., Citation2015), the Nusselt number was increased by 13.56% at a Reynolds number of 1730 compared to the water Nusselt number. According to the experimental results, Al2O3-Cu/water nanofluids have a slightly greater friction factor than Al2O3/water nanofluids. There is a good match between experimental data and the empirical correlations for the friction factor and Nusselt number.
Ing Jiat Kendrick Wong and Ngieng Tze Angnes Tiong (Hamdi et al., Citation2019) show that the heat transfer performance of circular pipes is superior and the pressure drop is greater than that of noncircular ducts. As a result of lack of sharp edges in circular pipe, the heat transfer rate was increased. A hybrid nanofluid of Al2O3-Cu and water has a higher pressure drop than water. The hybrid nanofluid pressure drop in a circular duct can be 4.79 times greater than water. The increased viscosity of the hybrid nanofluid is responsible for the increased pressure drop.
Recep Ekiciler et al. (Suresh et al., Citation2012) analyzed the flow of Al2O3/water nanofluid and Al2O3-Cu/water nanofluid 1% volume concentration nanoparticle in a duct with ellipse, square, and triangular rib under turbulent flow condition. The result reveals that adding Al2O3/water nanoparticle and Al2O3-Cu/water nanoparticle into the base fluid enhances the rate of heat transfer in all cases. Moreover, some of the related literatures are listed in .
Table 1. Summary of some of the related literatures review
The above studies show that nanofluids are a promising method for heat transfer enhancement by increasing thermal conductivity even for small volume fraction of suspended nanoparticles. Thus, this research work studied numerically for further enhancement of heat transfer by adding twisted tape insert. Thermal power plants, process industries, and evaporator heating and cooling can all benefit from mixed method of heat transfer augmentation that is both active and passive method. There will be an added advantage of enhancement of heat transfer due to two methods adopted; however, pressure drop must be considered during flow. An efficient heat exchanger can be designed with the above method of adoption. An existing heat exchanger can benefit from these strategies. Thus, the current research aims to increase heat transfer by adding twisted tap insert in PT using working fluid hybrid nanofluid (Al2O3-Cu) with base fluid of water.
2. Materials and methods
2.1. Physical modeling
The geometries examined in this study were circular tube and plain twisted tape (PTT) tube. To guarantee that the flow was hydrodynamically and thermally fully developed, the length of the tube was adjusted to 3 m, and the hydraulic diameter was 0.01 m, as shown in Figure based on the work of Ing Jiat Kendrick Wong and Ngieng Tze Angnes Tiong (Hamdi et al., Citation2019). Further, to intensify heat transfer, we have adopted passive method along with active method; for this, it has been provided with twisted strip for a full-length tube. Further, the tube of 3 m length has been extruded 5 mm on either side of the tube in order to avoid back flow during analysis and a twist ratio of ( has been provided for a twist tape.
2.2. Thermophysical properties of water and hybrid nanofluids
Copper and alumina hybrid nanofluids were used in this investigation. Studies have demonstrated that as particle loading rises, Al2O3-Cu/water accelerates heat transfer (Hamdi et al., Citation2019). Table displays the characteristics of water and hybrid nanofluids at various volume concentrations. For our analysis, thermophysical properties of hybrid nanofluid Al2O3-Cu/water with volumetric concentration of 1% have been chosen and it has been validated with Ing Jiat Kendrick Wong and Ngieng Tze Angnes Tiong (Hamdi et al., Citation2019); further, to intensify heat transfer, passive method has been adopted by inserting twisted tape into PT.
Table 2. Thermophysical properties of water and hybrid nanofluid Al2O3-Cu/water (Hamdi et al., Citation2019)
3. Mathematical model and Numerical method
3.1. Governing equations and boundary conditions
In this article, alumina–copper–water (Al2O3–Cu/H2O) hybrid nanofluid is viewed as an incompressible boundary layer and steady-state flow. The equations of conservation of mass, momentum, and energy for boundary layer approximations can be stated as follows, given specific physical hypotheses:
Conservation of mass
Momentum equation
Energy equation
where (k + kt) is the effective thermal conductivity, (kt) is the turbulent thermal conductivity, T is the temperature, v and u are the velocity components, P is the static pressure, μ is the viscosity, is the Kronecker delta, h is the sensible enthalpy, and
is the fluid density. To resolve the turbulent kinetic energy, ƙ, and dissipation rate, ɛ, the standard–turbulence model with enhanced wall treatment was chosen.
where t is the time, ui is the velocity component, is the viscosity,
and
are the turbulent Prandtl numbers for the kinetic energy and dissipation rate of the turbulent flow, respectively, Gk is the turbulent kinetic energy generated by the mean velocity gradient,
is fluid’s Eddy viscosity, and I is turbulence intensity. For the transport equations, the constants C are 1.44 for
, 1.92 for
, and 0.09 for
.
The range of 0.1–2% was given for the volume fraction of hybrid nanoparticles. At a weight percentage ratio of 9:1, Al2O3-Cu hybrid nanoparticles were used in the simulations. The density () and heat capacity (Cp) of hybrid nanofluid were calculated using EquationEqs. 8
(8)
(8) –Equation12
(12)
(12) . The subscripts bf, hnf, and nf, respectively, stand for the base fluid (water), hybrid nanofluid, and single-particle nanofluid. The hybrid nanofluid volume fraction is denoted by
in EquationEq. (12)
(12)
(12) .
Boundary conditions
The governing equations were solved in accordance with the provided boundary conditions. The fluid entered the domain with a uniform velocity profile because its flow was parallel to the border. The axial velocity of nanofluid was determined using the Reynolds number. It was required that the inlet temperature be 300 K. The outflow boundary condition was applied to the outlet border. There was no slip boundary condition imposed on the tube walls. Following a study by Ing Jiat Kendrick Wong and Ngieng Tze Angnes Tion (Hamdi et al., Citation2019), the above boundary condition and tube wall of constant heat flux of 20 kW/m2 were chosen.
3.2. Numerical method
A tool for commercial computational fluid dynamics software ANSYS-Fluent is utilized. Fluent employs the finite volume technique to solve the governing equations and boundary conditions given above. The thermo-hydraulic properties of a tetrahedral mesh element with a small significant center and an inflating layer are used to produce thin elements that record velocity and temperature gradients near no-slip barriers. The Navier–Stokes and energy equations are discretized in the model using standard pressure and second-order upwind discretization. The simple method is used to handle the pressure–velocity relationship. There are also convergence conditions of 10−6 and 10−8 for the continuity and velocity components, respectively. Figure shows the grid resolution test, and the temperature value in cells 2602844 (model 1) and 3364281 (model 3) differs by 1−1.5% from that in cell 3114836 up to section S5. As a result, the grid with the number of cells of 3114836 (Model 2, Figure c) was chosen for the PTT tube for Re = 20,000.
3.3. Data reduction
The average convective heat transfer coefficient (hav), Nusselt number (Nu), and the Reynolds number (Re) of the fluid were determined using EquationEq. (5)(5)
(5) .
Figure 2. Grid resolution test for PTT tube. (a) Cell_ 26028449 (Model 1). (b) Cell_3364281 (Model 3). (c) Cell_3114836 (Model 2).
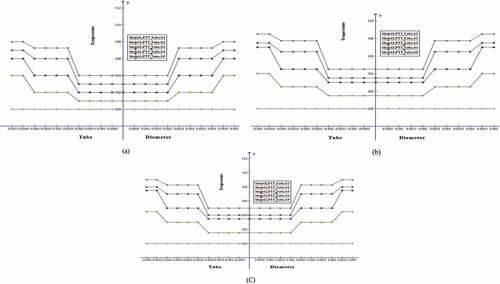
where A is the cross-sectional area, P is the perimeter, Tw is the wall temperature, Tf is the film temperature, Tin is the intake temperature, Tout is the outlet temperature, and q″ is the heat flux. To compute the friction factor (f) and pressure drop (P) for the flow behavior of hybrid nanofluid, the formulas listed below are used. Additionally, thermal performance factors of hybrid nanofluid were assessed using performance evaluation criteria (PEC) according to EquationEq. (20)(20)
(20) .
Nusselt number of water was calculated for validation reasons using the Dittus–Boelter correlation, and water’s friction factor was determined using EquationEq. (23)(23)
(23) . The Dittus–Boelter correlation has validity ranges of 0.6 ≤ Pr ≤ 160, Re ≥ 10,000, and
> 10, whereas EquationEq. (23
(23)
(23) ) has validity ranges of 3000 ≤ Re ≤ 5 × 106 (Ekiciler & Samet Ali Çetinkaya, Citation2021).
4. Result and discussions
4.1. Flow field investigation
shows velocity contour plot for circular tube/PT for Al2O3-Cu/water, Re = 20,000, at different axial locations. Because plain tube is not induced by twisted tape naturally, where there is no obstacle, velocity will be maximal at that place, as shown in , and there is a 1% to 1.25% variation between present work and previous work of Ing Jiat Kendrick Wong and Ngieng Tze Angnes Tiong (Hamdi et al., Citation2019).
shows velocity contour plot for PTT tube for Al2O3-Cu/water, Re = 20,000, at different axial locations. Thus, it has been observed that there is a decrease in velocity during the flow near towards tape wall due to swirling action but, there is an increase in velocity which can be observed as shown in Figure . However, there is a decrease in velocity along the path flow, and results of velocity contours have been shown in sections S1 to S5 (inlet, 1 m, 1.5 m, 2 m, 2.5 m, and 3 m).
4.2. Temperature contours for circular tube and PTT tube
Figure shows temperature contour plot for PT for water, Re = 20,000, at different axial locations, and it can be observed that there is an increase in temperature along the flow path. Due to boundary layer formation at the wall, there is an increase in pressure which leads to temperature raise which can be seen in Figure .
Figure shows temperature contour plot for PT for Al2O3-Cu/water, Re = 20,000, at different axial locations. Due to active method adoption of hybrid nanofluid, there is an increase in temperature from 1% to 1.5% when compared with of water which can be seen along the path from section S1 to S5.
Figure shows temperature contour plot for PTT for Al2O3-Cu/water, Re = 20,000, at different axial locations. There is an intensification of temperature of around 1% to 1.75% when compared with that of without inserts. This is due to a mixed method of active and passive employed in this analysis. Due to insertion of twisted tape, an additional mixing of fluid takes place, leading towards increase in temperature near towards wall of both pipe domain and twisted tape domain. These results can be observed along the path which has been shown between sections S1 and S5.
4.3. Heat transfer and friction factor
Using the numerical data gathered by Ing Jiat Kendrick Wong and Ngieng Tze Angnes Tiong (Hamdi et al., Citation2019), the current numerical analysis for PT validated the results of the Al2O3-Cu/water hybrid nanofluid at 1% as illustrated in Figure . Therefore, there is a good agreement between the current findings and those of Ing Jiat Kendrick Wong and Ngieng Tze Angnes Tiong (Hamdi et al., Citation2019).
The validated hybrid 1% Al2O3-Cu/water nanofluid in PT has a good agreement when compared to Nusselt number of Ing Jiat Kendrick Wong and Ngieng Tze Angnes Tiong (Hamdi et al., Citation2019), as shown in Figure . The slop of Nusselt number for the water is more linear than that of the Al2O3-Cu/water hybrid nanofluid as it is revealed in Figure . By adding a small amount, copper nanoparticles can dramatically improve the thermal properties of an Al2O3 nanofluid. A hybrid Al2O3-Cu/water nanofluid has a superior thermal conductivity than water because of the higher conductivity of metallic copper nanoparticles. When compared to base fluid and mono nanofluid, hybrid nanofluid can dramatically raise the Nusselt number, especially at higher Reynolds numbers. This result is highly agreed with Behrouz Takabi and Hossein Shokouhmand (Takabi & Shokouhmand, Citation2015) too as shown in Figure .
Further to enhance the heat transfer, a passive method is adopted for hybrid fluid flow in PT by inserting twisted tape. An increase of 1.5% to 2% heat transfer can be observed as shown in Figure . It clearly shows that due to flow disruption and formation of swirl, there is an increase in Nusselt number which leads to the augmentation of heat transfer.
Figure compares the Darcy friction factor (f) of the current investigation to those of Ing Jiat Kendrick Wong and Ngieng Tze Angnes Tiong (Hamdi et al., Citation2019) to establish the validity of hydrodynamic results for 1% hybrid nanofluid in the range of Reynolds number. A good agreement was found between the computed friction factor and those obtained from these correlations. Moreover, the same report is also reported by Behrouz Takabi and Hossein Shokouhmand (Takabi & Shokouhmand, Citation2015) as shown in Figure .
Further due to increase in pressure drop in PTT tube, there is a rise in friction factor when compared with that of without inserts. Clearly from Figure , it can be seen that there is a drop of friction factor with rise in Reynolds number.
4.4. Thermal performance factor
Hybrid nanofluids with PEC ratios higher than 1 demonstrate that the overall heat transfer capability of fluid predominates over flow resistance because water has a PEC ratio of 1 at all Reynolds numbers.
The merits of nanofluids for heat transfer enhancement depend on the compromise between thermal conductivity increase and viscosity increase. In this objective, Figure shows the evolution of this energetic criterion with the Reynolds number in the case of nanofluids for PT and PTT tube. We can notice that all measurements lead to PEC values under those corresponding to the case of water in the study by Ing Jiat Kendrick Wong and Ngieng Tze Angnes Tiong (Hamdi et al., Citation2019). Clearly due to insertion of twisted tape, there is a rise in PEC of 1.01 times than in the work of Ing Jiat Kendrick Wong and Ngieng Tze Angnes Tiong (Hamdi et al., Citation2019) PT.
Figure 7. Temperature contour plot for PT for Al2O3-Cu/water, Re = 20,000, at different axial locations.
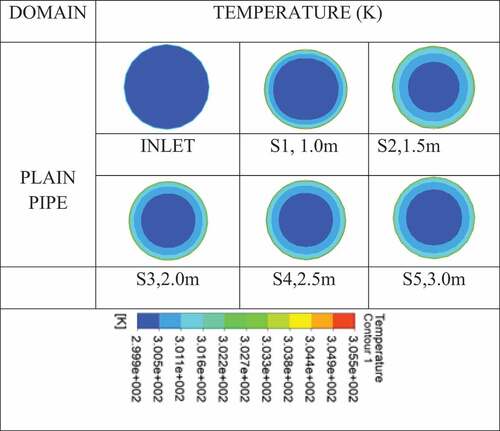
Figure 8. Velocity contour plot for PT for Al2O3-Cu/water, Re = 20,000, at different axial locations.
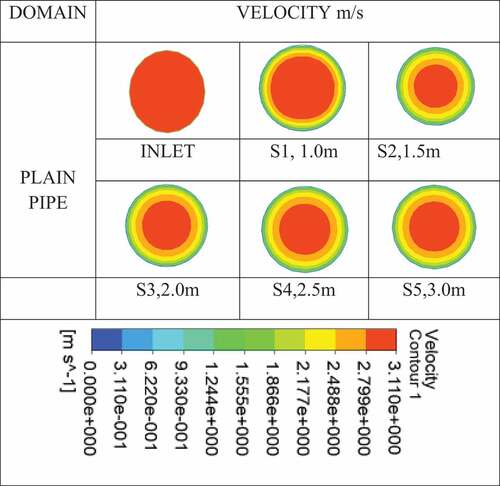
5. Conclusions
In the present study, turbulent thermal performance factor of Al2O3-Cu/water hybrid nanofluid in circular tube/PT ducts was numerically investigated. The following conclusions can be drawn based on the current study:
Due to insertion of twisted tape, an additional mixing of fluid takes place, leading towards increase in temperature of around 1% to 1.75% when compared with that of without inserts at Re = 20,000.
Heat transfer is further enhanced by adopting passing method for hybrid fluid flow in PT by inserting twisted tape. An increase of 1.5% to 2% heat transfer can be observed due to flow disruption and formation of swirl.
Twisted tape inserts have a higher heat transfer rate due to enhanced fluid mixing along the tube wall.
Due to insertion of twisted tape, there is a rise in PEC of 1.01 times than in the work of Ing Jiat Kendrick Wong and Ngieng Tze Angnes Tiong (Hamdi et al., Citation2019) PT.
Nomenclatures
Table
Data availability
The data used to support this study are included within the article.
Acknowledgements
The authors would like to thank Ing Jiat Kendrick Wong and Ngieng Tze Angnes Tiong, whose paper “Simulation approach on turbulent thermal performance factor of Al2O3‑Cu/water hybrid nanofluid in circular and non‑circular ducts” was used as a reference paper for validating the numerical results.
Additional information
Funding
References
- Abdollahi, A., Mohammed, H. A., Vanaki, M., Osia, A., & Haghighi, M. R. G. (2017). Fluid flow and heat transfer of nanofluids in microchannel heat sink with V-type inlet/outlet arrangement. Alexandria Engineering Journal, I. https://doi.org/10.1016/j.aej.2016.09.019
- Abdulwahab, M. R. (2014). A numerical investigation of turbulent magnetic nanofluid flow inside square straight channel. Journal of Advanced Research in Fluid Mechanics and Thermal Sciences, 1. https://semarakilmu.com.my/index.php/journals/article/view/1790
- Ahmed, M. A., Shuaib, N. H., & Yusoff, M. Z. (2012). Numerical investigations on the heat transfer enhancement in a wavy channel using nanofluid. International Journal of Heat and Mass Transfer, 55(21–22), 5891–17. https://doi.org/10.1016/j.ijheatmasstransfer.2012.05.086
- Aljabair, S., Akeel Abdullah Mohammed, I. A., & Alesbe, I. (2020). Natural convection heat transfer in corrugated annuli with H2O-Al2O3 nanofluid. Heliyon, 6(11), e05568. https://doi.org/10.1016/j.heliyon.2020.e05568
- Arjun , K. S., & Rakesh , K. (2020). Heat transfer in magnetohydrodynamic nanofluid flow past a circular cylinder. Physics of Fluids. https://doi.org/10.1063/5.0005095
- Ashkan, V., & Mohammed, H. A. (2013). Turbulent nanofluid flow over periodic Rib-Grooved channels. Engineering Applications of Computational Fluid Mechanics, 7(3), 369–381. https://doi.org/10.1080/19942060.2013.11015478
- Ekiciler, R., & Samet Ali Çetinkaya, M. (2021). A comparative heat transfer study between monotype and hybrid nanofluid in a duct with various shapes of ribs. Thermal Science and Engineering Progress. https://doi.org/10.1016/j.tsep.2021.100913
- Emad, M.-S. E.-S., Abdulaziz, M., & Mohamed, M. A. (2017). A numerical investigation on heat transfer enhancement and the flow characteristics in a new type plate heat exchanger using helical flow duct. Cogent Engineering, 4(1), 1396638. https://doi.org/10.1080/23311916.2017.1396638
- Hamdi, E. A., Salman, B. H., & Sh Kerbeet, A. (2019). Heat transfer enhancement of turbulent forced nanofluid flow in a duct using triangular rib. International Journal of Heat and Mass Transfer, 134. https://doi.org/10.1016/j.ijheatmasstransfer.2018.12.163
- Harish Kumar, L., Kazi, S. N., Masjuki, H. H., & Zubir, M. N. M. (2022). A review of recent advances in green nanofluids and their application in thermal systems. Chemical Engineering Journal, 429. https://doi.org/10.1016/j.cej.2021.132321
- Hossein Shiravi, A., Firoozzadeh, M., Bostani, H., & Bozorgmehrian, M. (2020). Experimental study on convective heat transfer and entropy generation of carbon black nanofluid turbulent flow in a helical coiled heat exchanger. Journal of Thermal Analysis and Calorimetry. https://doi.org/10.1007/s10973-020-09729-1
- Jiat Kendrick Wong, I. (2021). Ngieng Tze Angnes Tiong. Simulation approach on turbulent thermal performance factor of Al2O3‑Cu/water hybrid nanofluid in circular and non‑circular ducts. SN Applied Sciences. https://doi.org/10.1007/s42452-021-04317-w
- Kumar, S., Darshan Kothiyal, A., Singh Bisht, M., & Kuma, A. (2017). Turbulent heat transfer and nanofluid flow in a protruded ribbed square passage. Results in Physics, 7, 3603–3618. https://doi.org/10.1016/j.rinp.2017.09.023
- Kumar, P., & Dr, K. M. P. (2017). Effect on heat transfer characteristics of nanofluids flowing under laminar and turbulent flow regime – a review. IOP Conf Series: Materials Science and Engineering 225, 012168. https://doi.org/10.1088/1757-899X/225/1/012168
- Lin, W., Shi, R., & Lin, J. (2022). Heat transfer and pressure drop of nanofluid with rod-like particles in turbulent flows through a curved pipe. Entropy, 24(3), 416. https://doi.org/10.3390/e24030416
- Mehrjou, B., Zeinali Heris, S., & Mohamadifard, K. (2015). Experimental study Of CuO/Water Nanofluid turbulent convective heat transfer in square cross-section duct. Experimental Heat Transfer, 28(3), 282–297. https://doi.org/10.1080/08916152.2013.871606
- Moghadassi, A., Fahime Parvizian, E. G., & Parvizian, F. (2015). A numerical study of water based Al2O3 and Al2O3-Cu hybrid nanofluid effect on forced convective heat transfer. International Journal of Thermal Sciences, 92, 50–57. https://doi.org/10.1016/j.ijthermalsci.2015.01.025
- Moghaddami, M., Ehsan Shahidi, S., & Siavashi, M. (2012). Entropy generation analysis of nanofluid flow in turbulent and laminar regimes. Journal of Computational and Theoretical Nanoscience, 9(10), 1–10. https://doi.org/10.1166/jctn.2012.2249
- Nakhchi, M. E., & Esfahani, J. A. (2020). Numerical investigation of turbulent CuO–water nanofluid inside heat exchanger enhanced with double V‑cut twisted tapes. Journal of Thermal Analysis and Calorimetry. https://doi.org/10.1007/s10973-020-09788-4
- Nasrin, R., Sweety, S. A., & Zahan, I. (2021). Turbulent nanofluid flow analysis passing a shell and tube thermal exchanger with Kays-Crawford model. Journal of Nanofluids, 10(4), 518–537. https://doi.org/10.1166/jon.2021.1803
- Navaei, A. S., Mohammed, H. A., Munisamy, K. M., Yarmand, H., & Gharehkhani, S. (2015). Heat transfer enhancement of turbulent nanofluids flow over various types of internally corrugated channels. Powder Technology, 286, 332–341. https://doi.org/10.1016/j.powtec.2015.06.009
- Pehlivan, H., Taymaz, I., & İslamoğlu, Y. (2013). Experimental study of forced convective heat transfer in a different arranged corrugated channel. International Communications in Heat and Mass Transfer, 46, 106–111. https://doi.org/10.1016/j.icheatmasstransfer.2013.05.016
- Peyghambarzadeh, S. M., Hashemabadi, S. H., Chabi, A. R., & Salimi, M. (2014). Performance of water-based CuO and Al2O3 nanofluids in a Cu–Be alloy heat sink with rectangular microchannels, energy conversion and management 86, 28–38. https://www.sciencedirect.com/science/article/abs/pii/S0196890414004245
- Rabienataj Darzi, A. A., Sedighi, K., Shafaghat, R., Zabihi, K., & Zabihi, K. (2012). Experimental investigation of turbulent heat transfer and flow characteristics of SiO2/water nanofluid within helically corrugated tubes. International Communications in Heat and Mass Transfer, 39(9), 1425–1434. https://doi.org/10.1016/j.icheatmasstransfer.2012.07.027
- Raei, B., Shahraki, F., & Mohammad Jamialahmadi, S. M. P. (2016). Experimental study on the heat transfer and flow properties of -Al2O3/water nanofluid in a double-tube heat exchanger. Journal of Thermal Analysis and Calorimetry. https://doi.org/10.1007/s10973-016-5868-x
- Sakanova, A., Yin, S., Zhao, J., Wu, J. M., & Leong, K. C. (2014). Optimization and comparison of double-layer and double-side micro-channel heat sinks with nanofluid for power electronics cooling. Applied Thermal Engineering, 65(1–2), 124–134. https://doi.org/10.1016/j.applthermaleng.2014.01.005
- Sh, M. V., Mohammed, H. A., Ayoub Abdollahi, M. A. W., & Wahid, M. A. (2014). Effect of nanoparticle shapes on the heat transfer enhancement in a wavy channel with different phase shifts. Journal of Molecular Liquids, 196, 32–42. https://doi.org/10.1016/j.molliq.2014.03.001
- Suresh, S., Venkitaraj, K. P., Selvakumar, P., & Chandrasekar, M. (2012). Effect of Al2O3–Cu/water hybrid nanofluid in heat transfer. Experimental Thermal and Fluid Science, 38, 54–60. https://doi.org/10.1016/j.expthermflusci.2011.11.007
- Takabi, B., & Shokouhmand, H. (2015). Effects of Al2 O3 – Cu/water hybrid nanofluid on heat transfer and flow characteristics in turbulent regime. International Journal of Modern Physics C, 26(4), 1550047. https://doi.org/10.1142/S0129183115500473
- Xia, G. D., Liu, R., Wang, J., & Du, M. (2016). The characteristics of convective heat transfer in microchannel heat sinks using Al2O3 and TiO2 nanofluids. International Communications in Heat and Mass Transfer, 76, 256–264. https://doi.org/10.1016/j.icheatmasstransfer.2016.05.034
- Ziaei-Rad, M., & Beigi, M. (2016). Numerical study of turbulent nanofluid flow at the entrance region of a ribbed pipe. Physica Scripta, 91(3), 034004. https://doi.org/10.1088/0031-8949/91/3/034004