ABSTRACT
Through technological advancements, medical devices have evolved in their designs and have become more complex in both their design and materials of construction. Medical grade biocompatible epoxies are widely used in reusable medical devices. Choosing an epoxy that maintains its performance characteristics when subjected to repeated sterilization throughout the reusable medical device’s lifespan is a known challenge for medical device manufacturers. This study evaluated the material compatibility of seven cured 2-part and 1-part epoxies used in medical devices following exposure to 100 cycles in a low temperature vaporized hydrogen peroxide sterilizer. Six of the seven epoxies tested were found to be compatible with vaporized hydrogen peroxide sterilization based on qualitative, hardness and weight measurements conducted post exposure to 100 VHP cycles. The epoxies deemed to be compatible displayed no visual signs of physical defects, minimal reduction in hardness (≤2%) and total weight gain (≤2.9%). One of the epoxy samples did not maintain its texture and exhibited 17% loss in hardness post exposure to 100 VHP sterilization cycles and was found to be incompatible with the low temperature vaporized hydrogen peroxide process. This study verifies the need for material compatibility evaluations of epoxies prior to designing and developing a medical device while keeping in mind the application, lifecycle and intended use of medical devices.
1. Introduction
Medical device manufacturers (MDMs) are often challenged to design medical devices that meet device application needs, biocompatibility requirements and maintain functionality throughout the device’s lifecycle. Materials used to construct medical devices include but are not limited to metals,[Citation1] ceramics,[Citation2] plastics, and polymers,[Citation3] and the compatibility of these materials has been studied across sterilization modalities.[Citation4–9] Medical grade epoxies find their use in a variety of medical devices such as implantable devices, endoscopes, optical systems, catheters, prosthetics, surgical equipment, etc. [Citation8–13] Selecting a medical grade epoxy is an integral part of designing some medical devices. Medical grade epoxy compositions are proprietary and vary among epoxy manufacturers. Due to variability in composition, epoxies are not identified on sterilizer manufacturer material compatibility lists, which is a challenge for MDMs during the design phase of a medical device. Understanding the epoxy’s compatibility with a sterilization modality prior to designing a medical device will help MDMs make better choices around choosing the best epoxy for the intended use of the medical device.
Although steam sterilization/moist heat has been a conventional choice of sterilization for well over 100 years, it has certain limitations. High temperatures, humidity and high pressures have been known to be deleterious to heat-sensitive instruments, biomaterials, polymer-based materials, and may cause rust as some instruments remain wet after sterilization.[Citation14–17] To overcome limitations presented by steam sterilization, alternative terminal sterilization modalities such as low temperature vaporized hydrogen peroxide sterilization, have gained popularity in the healthcare facilities. The use of hydrogen peroxide (a strong oxidizing agent)[Citation18] in gas (or vapor) form for disinfection[Citation19–21] and sterilization has continued to increase due to several advantages that include broad spectrum antimicrobial efficacy,[Citation22] shorter processing times, environmentally friendly by-products (water and oxygen) and good material compatibility.[Citation18] Vaporized hydrogen peroxide (VHP™) can be produced by vaporizing liquid hydrogen peroxide under sub-atmospheric conditions in a closed chamber. It has good to excellent material compatibility with most polymers (thermosets or thermoplastics), metals, ceramics, silicones and elastomers[Citation23] and it can be used to sterilize electronic medical devices, and materials that are heat and moisture sensitive.[Citation18] VHP sterilizers operate at lower temperatures, under 60°C, and medical devices are available for immediate use, whereas steam sterilizers operate at 121–135°C and devices must cool after processing. Currently marketed low temperature vaporized hydrogen peroxide cycles differ in sterilant contact times, chamber pre-injection set points, device claims and sterilant contact times.[Citation24,Citation25]
There are many types of adhesive chemistries such as acrylics, silicones, urethanes, and epoxies. Among them, epoxies offer a combination of excellent heat as well as chemical resistance. This is one of the reasons why epoxies are used in medical device applications which may be exposed to high temperatures or chemical sterilants. Epoxies can be characterized into two classes based upon their cure mechanism, two-part and one-part epoxies. Two-part epoxies are composed of a resin and a hardener – these two materials must be mixed thoroughly in the manufacturer recommended ratio prior to use. Most two-part epoxies can cure at room temperature, although the cure rate and extent of cure can be increased at higher temperatures. One-part epoxies require no mixing and generally have an “unlimited” working life at room temperature. These one-part systems, due to their inherent stability at ambient temperatures, require high temperature to deactivate the inhibitors and to provide a high degree of cure.[Citation10] In addition to temperature, there are UV-curable epoxies that cure rapidly when exposed to a high-intensity UV light source of an appropriate spectral output. Recent developments in the epoxy formulation have also led to the introduction of dual-cure epoxies, which can be cured with exposure to UV irradiation or temperature. Selection of a medical grade epoxy is often influenced by medical device design, manufacturing process, application requirements, and the epoxy’s ability to bond with different substrates.
While there is some general compatibility data available,[Citation18,Citation26] specific information about epoxies and low temperature vaporized hydrogen peroxide compatibility is lacking. A collaboration was initiated to determine the compatibility of Master Bond epoxies with STERIS low-temperature Vaporized Hydrogen Peroxide sterilization systems. For this material compatibility study, epoxies used in the manufacture of medical devices were chosen.[Citation27] The seven Master Bond epoxies used in this study are biocompatible and are identified as compliant with ISO 10993–5[Citation28] and/or USP Class VI.[Citation29] The adhesive systems selected represent a sampling of the different cure chemistries. These included two-part epoxies, a one-part thermal curing epoxy, a one-part UV curing epoxy, and a dual-cure epoxy. EP42HT-2MED is a two-part epoxy with a phenol novolac resin and a cycloaliphatic/aromatic amine blend, EP42HT-4AOMED Black has a similar base chemistry with an aluminum oxide filler for enhanced thermal conductivity and lower thermal expansion properties. EP62-1HTMED is based on a phenol novolac resin and an imidazole curing agent, whereas EP41S-5MED utilizes a phenol novolac resin and a high functionality aliphatic amine curing agent. EP4CL-80MED is a one component, heat curing, cycloaliphatic epoxy with an extremely low viscosity, whereas UV10TKMED is a UV curing epoxy acrylate chemistry for applications requiring a very fast cure with UV light. UV15DC80MED is an epoxy-based, cationic curing chemistry with a dual curing, i.e., UV + heat curing mechanism. This product can be cured with heat (above 80℃) after an initial UV light exposure. More details about the cure schedule used for all these products are mentioned in . To expose the epoxy test articles to VHP, the Lumen Cycle of the V-PRO® s2 Sterilizer was chosen as a worst-case for material exposure as this cycle has the highest theoretical dose of VHP among V-PRO Sterilizers. The cured epoxy test articles were exposed to 100 VHP cycles. Qualitative, weight and hardness evaluations were used to understand cured epoxy sample material compatibility pre- and post-exposure to repeated VHP cycles.
Table 1: Product details and Cure Schedules of the seven epoxies used in this study
2. Materials and methods
The epoxy test articles used throughout the study were prepared, cured, and provided by Master Bond. The cured epoxy test articles were then exposed to 100 VHP cycles at STERIS. Post sample processing, qualitative and weight assessments were performed at STERIS and the epoxy test articles were shipped back to Master Bond for hardness measurements.
2.1. Epoxy test article preparation
Seven cured epoxy test articles were used for this study, namely EP42HT-2Med, EP42HT-4AOMed Black, EP62-1HTMed, EP41S-5Med, EP4CL-80Med, UV10TKMed and UV15DC80Med. For the two-part epoxy types, the resin and hardener were measured and mixed according to the mix ratios on the technical data sheets (see for details) and manufacturer instructions.
To prepare the test articles, the two-part or one-part systems were poured into molds. The cured discs were 2 inches in diameter and around 0.25 inches thick. Mold release agents were not used in the process. The samples were cured as recommended by the manufacturer (see ). A forced air oven was used for heat curing some of the products. The UV curing was performed using a broad spectrum floodlamp i.e., the Uvitron Intelliray 600 that offered evenly distributed 175 mW/cm[Citation2] UVA light. The First Weigh Model CK10 Scale, Fisherbrand Isotemp 60 L Oven FA and the UV lamp used were calibrated prior to use.
2.2. Vaporized hydrogen peroxide sterilization process
VHP sterilization was performed at STERIS using the V-PRO® s2 Low Temperature Sterilization System. All the test articles were exposed to 100 V-PRO® s2 Sterilizer Lumen Cycles. VAPROX® HC Sterilant, 59% Hydrogen Peroxide (STERIS part # PB011) was used as the sterilant. Each Lumen Cycle delivers a total theoretical sterilant dose of 346 mg-min/L. The sterilizer chamber operating temperature is approximately 50°C. Celerity™ HP Chemical Indicator, a Type 1 process indicator (STERIS part # PCC075), was used to confirm hydrogen peroxide exposure, and cycle tapes were used to monitor cycle completion.[Citation30] The epoxy test articles were processed in an unwrapped open STERIS Sterilization Tray Model No. VP0004. The samples were processed continuously during a regular workday, followed by overnight breaks and testing was completed over the course of 4 weeks.
2.3. Qualitative assessments
All test articles were evaluated qualitatively for appearance. Test articles were photographed prior to processing to allow for visual inspection of epoxy compatibility with the vaporized hydrogen peroxide sterilizer. Post exposure to 100 VHP cycles, test articles were assessed for changes in color, texture (smoothness, tackiness), and the potential presence of defects such as cracking, and flaking.
2.4. Hardness measurements
The cured discs were quantitatively tested per ASTM D2240 for hardness both before and after exposure to 100 V-PRO® s2 Sterilizer Lumen Cycles.[Citation31] Durometer Stand Model 320 with the Durometer Model 307 L, PTC instruments was used for the measurement of the Shore D hardness values.
2.5. Weight measurements
The cured discs were weighed pre- and post-processing after 10, 25, 50 and 100 cycles to evaluate for weight changes. Weight measurements were conducted with a calibrated analytical scale Sartorius Analytic Model No. CP224S.
3. Results
3.1. Qualitative assessments
No signs of changes to texture such as cracking, flaking, or other defects, were observed with six of the seven epoxies after exposure to 100 VHP cycles. The EP42HT-2Med sample displayed a minor cosmetic color change as it darkened in color post exposure to 100 VHP cycles (see ). The UV15DC80Med test article displayed changes in both texture and color progressively post exposure to
Figure 1. Schematic representation of the experimental process and evaluations conducted to determine material compatibility of the seven epoxy test articles.

VHP (see ). No changes to color or texture were noted with the other five epoxy samples. A summary of the qualitative assessments is presented in .
Table 2: Master Bond Epoxies Material Evaluation Pre- and Post-exposure to 100 VHP cycles
3.2. Hardness measurements
Changes to cured disc sample hardness were evaluated before and after exposure to 100 VHP cycles. details the hardness measurements for the seven epoxy samples tested. Upon evaluation, all seven epoxy test articles displayed an overall loss in hardness ranging from 1% to 17%. Six of the seven epoxies exhibited less than 2% change in hardness, while the one-part UV/Heat cured UV15DC80Med epoxy sample’s hardness decreased by 17% (). A percent change of ≥5% to hardness of the epoxy test articles was considered significant for this study.
3.3. Weight measurements
The cured discs were weighed pre-processing and post-completion of 10, 25, 50 and 100 VHP cycles to evaluate for weight changes. Percent weight gained vs. number of VHP cycles is presented in . Weight gain was noted with all the seven epoxy samples tested. The weight gain observed for all the seven epoxy test articles tested was minimal and ranged from 0.5% to 3.0% post-exposure to 100 VHP cycles. The percent weight gain for five of the seven epoxy test articles was 1% or less. The highest weight change of 3.0% was observed with the UV15DC80Med test article (see ). A percent weight change of ≥5% for an epoxy test article was considered significant for this study.
4. Discussion
Medical devices can vary vastly in terms of their complexity, intended use, and sterilization requirements. Material and epoxy considerations are very different for disposable/single-use or reusable/long term use medical devices.[Citation32] Disposable, single-use medical devices are generally high-volume manufactured articles that require rapid assembly, simplified application, and experience limited exposure to sterilization. On the other hand, reusable medical devices undergo repeated processing that includes cleaning, packaging, sterilization, storage, etc., throughout the lifespan of the device. Furthermore, during cleaning and sterilization, reusable medical devices are repeatedly subjected to process-specific variables such as cleaning chemicals, pressure variations, temperature, humidity, sterilant, pH, etc. This makes the choice of epoxy for a medical device complex and critical. When selecting an epoxy for a reusable medical device, one must factor in the substrate used,[Citation33] intended use of the device, reprocessing loop,[Citation34] compatibility with cleaning chemistries and sterilization requirements.[Citation35,Citation36]
In this study, VHP sterilization compatibility of the epoxies was determined based on changes to appearance/texture, hardness, and weight post exposure to 100 VHP cycles. Hardness is an indicator of an epoxy’s mechanical property, and a significant change in the hardness of the epoxy indicates deterioration of epoxy’s mechanical properties. The epoxy samples with the least amount of hardness change tend to perform best mechanically. A percent change of ≥5% in hardness of the epoxy test articles was considered significant for this study, since such a change would implicate changes to mechanical properties and surface texture of the epoxy. This in turn could potentially impact functionality of the epoxy and cause a deterioration in strength or stability of a bonded joint when used in a medical device. Changes to weight could indicate either chemical absorption or etching of the cured epoxy matrix. A weight change of ≥5% for an epoxy test article is considered a failure as higher the weight change, the higher the likelihood of leakage, cracking, or swelling in a bonded joint or a sealed assembly. For this study, a passing criterion of 5% was established for both weight and hardness. Products that met both weight and hardness criteria were deemed compatible with the VHP sterilization process.
Upon a combined evaluation of the aforementioned characteristics, six of the seven epoxies were found to be compatible with VHP. These included one-part, two-part and UV-curable epoxies, namely EP42HT-2Med, EP42HT-4AOMed Black, EP62-1HTMed, EP41S-5Med, EP4CL-80Med, and UV10TKMed. These six epoxies were non-tacky and displayed no visual signs of physical defects such as cracking or flaking post exposure to 100 VHP cycles. Additionally, they displayed minimal reduction in hardness (≤2%) and total weight gain (≤2.9%). Although there was a color change observed with the EP42HT-2Med epoxy post exposure to VHP cycles, this was considered cosmetic. The six epoxies found to be compatible with VHP offer excellent physical strength properties and bond well with a variety of substrates including metals, ceramics, glass, and different plastics. They may find use in a variety of medical devices including catheters, endoscopes, implantable devices, ultrasound devices, diagnostic instruments, surgical instruments, respiratory equipment, orthopedic and prosthetic devices, etc.
Although UV15DC80Med is widely used in medical devices, this epoxy sample () did not maintain its texture, and the first occurrence of bubbling, softening and tackiness was observed after five cycles in the test articles. In addition, this epoxy sample exhibited 17% loss in hardness and a weight gain of 2.9% post exposure to 100 VHP sterilization cycles. Even though the weight gain observed with UV15DC80Med epoxy is considered minimal, the weight gain should not be used as the sole measure to determine compatibility. Overall, the mechanical properties such as hardness and/or the mechanical integrity of the epoxy test articles must be evaluated along with the weight changes to understand the material compatibility of adhesives. A 17% drop in hardness could point to a change in the material’s mechanical integrity due to the softening of the product. Based on the above assessments the UV15DC80Med epoxy was found to be incompatible with the low temperature vaporized hydrogen peroxide process.
Figure 3. Percent weight gain of the seven cured epoxy test articles post -exposure to 10, 25, 50, 100 VHP cycles.
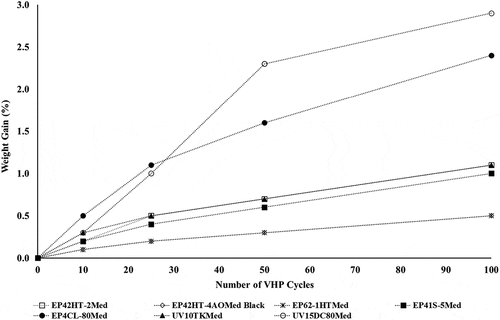
Post exposure to 100 VHP cycles, all seven epoxy test articles exhibited a weight gain of ≤2.9%, and the percent weight assessment results did not exclude any epoxy from use consideration. All the compatible test articles displayed a weight gain of ≤1.6% post-exposure to the first 50 VHP cycles. The maximum weight gain of 2.3% was observed with the UV15DC80Med sample. Post-exposure to the next round of 50 VHP cycles, a weight gain of ≤0.7% was observed with all the test articles. The maximum weight gain of 0.7% was observed with the EP4CL-80MED sample. The rate of weight gain slowed down for all epoxy samples after exposure to the first 50 VHP cycles as shown in .
In a previous study conducted by Master Bond, four epoxies, EP42HT-4AOMed Black, EP42HT-2MED, UV10TKMED and UV15DC80Med exhibited a weight gain of 2%, 2.5%, 2% and 3% when subjected to 100 steam sterilization cycles and were deemed compatible with steam sterilization (see ). A weight change of <5% was established as a passing criterion post exposure to 100 steam sterilization cycles. The steam sterilization cycles were conducted at 121°C, 15 psi and lasted approximately 20 min.[Citation38] The weight gain observed in this study with the corresponding samples was 0.5%, 1.1%, 1.1% and 2.9%, respectively, when subjected to 100 repeated VHP cycles (see ) which is less than what was observed with steam sterilization.
Table 3: Master Bond Epoxies Material Evaluation Post-exposure to 100 Steam Sterilization Cycles[Citation37]
As evident from the comparison of and and different sterilization modalities could have slightly different impacts on the physical properties of medical-grade epoxies. While there are several studies that report the effects of different sterilization modalities such as Ethylene Oxide, Gamma radiation, Steam, etc., on polymers used in medical device industry,[Citation39–41] there is limited information available on material compatibility of epoxies and current sterilization methods.[Citation42–44] This study evaluated the compatibility of epoxy test articles with a VHP sterilizer. It provides information on physical assessments to consider when selecting an epoxy for a reusable medical device intended for VHP sterilization. However, different substrates, sterilization modalities, device geometries, curing methods, repeated processing, etc., may influence the performance of epoxies in turn impacting the functionality of the final medical device. Hence, the compatibility of epoxies must be reevaluated by the MDM within the finished medical device. Given the variability in epoxy compositions and compatibility with sterilization processes, the MDM should work with the epoxy and sterilizer manufacturers to find the best solution for their needs. Understanding the substrate and material compatibility of the epoxies whilst considering the intended use of the medical device prior to designing it will help the MDM choose the best epoxy during the development phase of the medical device.
5. Conclusion
This study evaluated the material compatibility of seven USP Class VI and/or ISO 10993–5 compliant Master Bond epoxies to 100 VHP sterilization cycles. The study determined that six of the seven Master Bond epoxies tested were compatible with VHP sterilization process. The Master Bond EP42HT-2Med, EP42HT-4AOMed Black, EP62-1HTMed, EP41S-5Med, EP4CL-80Med and UV10TKMed epoxies are compatible with low temperature vaporized hydrogen peroxide, as they maintained their surface texture, exhibited less than 2% change in hardness, and displayed less than a 2.5% weight gain post exposure to 100 VHP cycles. The study shows that changes in weight alone may not be sufficient to determine material compatibility of epoxies. The one-part UV and heat cure epoxy, UV15DC80Med was incompatible with the VHP sterilization cycles but might find other applications outside the scope of this study.
In the medical device design process, sterilization may many a times be an afterthought. There is an unmet need for material compatibility evaluations of medical-grade epoxies with relevance to the sterilization modality in healthcare industry. This study highlights the importance of conducting material compatibility studies, and continued collaborations (among MDMs, sterilizer manufacturers and epoxy manufacturers/suppliers) during the early stages of medical device development to ensure a successful reusable medical device that will withstand repeated sterilization.
MB_supporting information_5124.docx
Download MS Word (23.7 KB)Acknowledgments
The authors acknowledge the support of Jodi Alt, Ph.D. and Jean-Luc Lemyre, Ph.D. for their support with the review process.
Disclosure statement
No potential conflict of interest was reported by the author(s).
Supplementary data
Supplemental data for this article can be accessed online at https://doi.org/10.1080/25740881.2024.2376209
Additional information
Notes on contributors
Shruti Padhee
Dr. Shruti Padhee is a Senior scientist at STERIS R&D with over 15 years of research experience. She holds B. Pharm., M.S and Ph. D in Chemistry. Over the past 15years, held a variety of positions and has a breadth of research experience ranging from low-temperature hydrogen peroxide sterilizers, peptide chemistry infectious diseases, to translational research.
Christine Fingar
Christine Fingar has a bachelor’s degree in chemical engineering, is an Application Engineer at Master Bond. She is HAZMAT trained and actively involved in new product development testing as well as ensuring quality compliance of various Master Bond products. She has over 7 years of experience in analyzing application-oriented issues and provides product solutions for companies in the aerospace, electronics, medical, optical, and oil/chemical industries.
Ankit Patel
Ankit Kumar Patel has a M. S in Chemistry, has is a Manger of Production, R&D, Safety at Master Bond Inc. with more than 13 years of experience in technical mixing of complex adhesive formulations, Quality control testing of finished products as well as incoming Raw Materials, developing new products and customizing existing formulations to meet customer needs.
Randal Eveland
Dr. Randal Eveland received his Ph.D. in Chemistry from Northwestern University and has over 20 years’ experience with STERIS developing low-temperature hydrogen peroxide sterilizers and sterilizer accessories. He is a Senior Principal Scientist in the Research and Development group. He is actively involved in standards development with AAMI (Association for the Advancement of Medical Instrumentation) and has extensive experience collaborating with medical device manufacturers.
Jordan Rantucci
Jordan Rantucci holds a bachelor’s degree in Pharmaceutical Science and is a Scientist I with 12 years of experience at STERIS specializing in Research and Development within STERIS Device Testing. His primary expertise lies in microbiology, particularly focusing on the material compatibility and validation of medical devices across various STERIS modalities, including vaporized hydrogen peroxide.
Tawana Ward
Tawana Ward is a Laboratory Technician III at STERIS Corporation with over 8 years of experience specializing in low temperature sterilization and chemical indicators. Her expertise lies in preparing and analyzing samples for material compatibility testing within various low-temperature sterilization processes, particularly focusing on vaporized hydrogen peroxide (VHP).
Venkat Nandivada
Venkat Nandivada holds a M.S in chemical engineering and is the Manager of Technical Support at Master Bond. He has 14 years of experience in analyzing application-oriented issues and provides product solutions for companies in the aerospace, electronics, medical, optical, OEM, and oil & gas industries. He has extensive experience in editing technical content for various whitepapers and technical tips.
Rohit Ramnath
Rohit Ramnath received his M.S in chemical engineering and is a Senior Product Engineer with 12 years of experience at Master Bond where he manages new product development right from concept development to procurement to product launch via numerous marketing channels such as news releases, and case studies. He troubleshoots customer adhesive application challenges in the medical, aerospace, electronics, optical, OEM, and oil & gas industries.
References
- Williams, C. The 11 Most Important Metals Used in Medicine. n.d. https://www.starrapid.com/blog/the-6-most-important-metals-used-in-medicine/ (accessed Feb 1, 2024).
- Webster, S. What Do OEMs Need to Consider When Using Ceramics for Medical Devices? https://www.nsmedicaldevices.com/analysis/ceramics-medical-devices/ (accessed Feb 1, 2024).
- George, E. R. An Introduction to Polymeric Materials for Medical Devices. An Introduction to Polymeric Materials for Medical Devices (Meddeviceonline.Com) (accessed Feb 1, 2024).
- Rogers, W. J. Steam and Dry Heat Sterilization of Biomaterials and Medical Devices. In Sterilisation of Biomaterials and Medical Devices, 1st ed.; Lerouge, S. Simmons, A., Eds.; Woodhead Publishing: Oxford, Philadelphia, 2012; pp. 20–55.
- Rogers, W. J. Sterilisation Techniques for Polymers. In Sterilisation of Biomaterials and Medical Devices, 1st ed.; Lerouge, S. Simmons, A., Eds.; Woodhead Publishing: Oxford, Philadelphia, 2012; pp. 151–211.
- Rogers, W. J.;the Effects of Sterilization on Medical Materials and Welded Devices. In Joining and Assembly of Medical Materials and Devices, 1st ed.; Zhou, Y. N. Breyen, M. D., Eds.; Woodhead Publishing: Cambridge, UK, 2013; pp. 79–130.
- Zhang, Y. Z.; Bjursten, L. M.; Freij-Larsson, C.; Kober, M.; Wesslen, B. Tissue Response to Commercial Silicone and Polyurethane Elastomers After Different Sterilization Procedures. Biomaterials 1996, 17(23), 2265–2272. DOI: 10.1016/0142-9612(96)00055-5.
- Rai, R.; Tallawi, M.; Roether, J. A.; Detsch, R.; Barbani, N.; Rosellini, E.; Kaschta, J.; Schubert, D. W.; Boccaccini, A. R. Sterilization Effects on the Physical Properties and Cytotoxicity of Poly (Glycerol Sebacate). Mater. Lett. 2013, 105, 32–35. DOI: 10.1016/j.matlet.2013.04.024.
- Tipnis, N. P.; Burgess, D. J. Sterilization of Implantable Polymer-Based Medical Devices: A Review. Int. J. Pharm. 2018, 544, 455–460. DOI: 10.1016/j.ijpharm.2017.12.003.
- Frick, L. Epoxies for Medical Device Applications. https://www.machinedesign.com/fastening-joining/article/21833540/epoxies-for-medical-device-applications. (accessed Feb 1, 2024).
- MASTERBOND. EP30Med: Utilized As Sensor Encapsulant in Prosthetic Device. https://www.masterbond.com/case-study/ep30med-utilized-sensor-encapsulant-prosthetic-device (accessed Feb 6, 2024).
- EPO-TEK®. Biocompatible/Medical Device Grade Products. https://www.epotek.com/docs/en/Related/EPO-TEK%C2%AE%20Biocompatible%20Medical%20Device%20Grade%20Products.pdf (accessed Feb 6, 2024).
- Joung, Y. Development of Implantable Medical Devices: From an Engineering Perspective. Int. Neurourol. J. 2013, 17(3), 98–106. DOI: 10.5213/inj.2013.17.3.98.
- Baier, R. E.; Meyer, A. E.; Akers, C. K.; Natiella, J. R.; Meenaghan, M.; Carter, J. M. Degradative Effects of Conventional Steam Sterilization on Biomaterial Surfaces. Biomaterials 1982, 3(4), 241–245. DOI: 10.1016/0142-9612(82)90027-8.
- Harrington, R. E.; Guda, T.; Lambert, B.; Martin, J. ed.; Wagner, W. R.; Sakiyama-Elbert, S. E.; Zhang, G. Sterilization and Disinfection of Biomaterials for Medical Devices. In Biomaterials Science, 4th ed.; Yaszemski, M. J., Ed.; Academic Press, an imprint of Elsevier: London, United Kingdom; San Diego, CA, 2020; pp. 1431–1446.
- Mubarak, M. T.; Ozsahin, I.; Ozsahin, D. U. Evaluation of Sterilization Methods for Medical Devices. Adv. Sci. Eng. Technol. Int. Conf 2019, 1–4. DOI: 10.1109/ICASET.2019.8714223.
- Rutala, W. A.; Weber, D. J. Disinfectants Used for Environmental Disinfection and New Room Decontamination Technology. Am. J. Infect. Control 2013, 41(5), S36–S41. DOI: 10.1016/j.ajic.2012.11.006.
- Eveland, R. W. Disinfection and Sterilization with Hydrogen Peroxide. In Block’s Disinfection, Sterilization, and Preservation, 6th ed.; McDonnell, G. Hansen, J., Eds.; Wolters Kluwer: Philadelphia, PA, USA, 2020; pp. 671–683.
- Fu, T. Y.; Gent, P.; Kumar, V. Efficacy, Efficiency and Safety Aspects of Hydrogen Peroxide Vapour and Aerosolized Hydrogen Peroxide Room Disinfection Systems. J. Hosp. Infect. 2012, 80, 199–205. DOI: 10.1016/j.jhin.2011.11.019.
- Pottage, T.; Macken, S.; Giri, K.; Walker, J. T.; Bennett, A. M. Low-Temperature Decontamination with Hydrogen Peroxide or Chlorine Dioxide for Space Applications. Appl. Environ. Microbiol 2012, 78(12), 4169–4174. DOI: 10.1128/AEM.07948-11.
- Meszaros, J. E.; Antloga, K.; Justi, C.; Plesnicher, C.; McDonnell, G. Area Fumigation with Hydrogen Peroxide Vapor. Appl. Biosaf 2005, 10(2), 91–100. DOI: 10.1177/153567600501000206.
- Alfa, M. J.; DeGagne, P.; Olson, N.; Puchalski, T. Comparison of Ion Plasma, Vaporized Hydrogen Peroxide, and 100% Ethylene Oxide Sterilizers to the 12/88 Ethylene Oxide Gas Sterilizer. Infect Control. Hosp Epidemiol 1996, 17(2), 92–100. DOI: 10.1086/647252.
- Association for the Advancement of Medical instrumentation (AAMI). AAMI TIR17: 2017/(R) 2023 Compatability of Materials Subject to Sterilization. Annex E. AAMI 2017.
- STERIS. M4067EN V-PRO Comparison Matrix -MaX2, 60, STERRAD 100NX, STERRAD 100S and STERRAD NX. V-PRO MaX 2 Low Temperature Sterilization System | STERIS. (accessed Feb 6, 2024).
- STERIS. M4176EN V-PRO Family Brochure. V-PRO S2 Low Temperature Sterilization System | STERIS. (accessed Feb 6, 2024).
- Compatability of Medical devices and Materials with Low- Temperature Hydrogen Peroxide Gas Plasma. https://www.mddionline.com/news/compatibility-medical-devices-and-materials-low-temperature-hydrogen-peroxide-gas-plasma (accessed Feb 6, 2024).
- MASTERBOND. Biocompatible Adhesives. https://www.masterbond.com/properties/biocompatible-adhesives. (accessed Feb 1, 2024).
- International organization for Standards (ISO). BS EN ISO 10993-5: 2009 Biological Evaluation of Medical Devices- Tests for in vitro Cytotoxicity. https://compliancenavigator.bsigroup.com/doc/000000000030160958 (accessed Feb 7, 2024).
- STERIS. 10660555 V-PRO S2 LOW Temperature Sterilization System. V-PRO S2 Low Temperature Sterilization System | STERIS (accessed Feb 6, 2024).
- STERIS. 10778508 V-PRO S2 LOW Temperature Sterilization System. V-PRO S2 Low Temperature Sterilization System | STERIS (accessed Feb 6, 2024).
- STERIS. M10425EN-CA V-PRO Consumables Brochure. https://www.steris.com/healthcare/products/v-pro-sterilizers/pro-lite-sterilization-trays#Literature (accessed Feb 6, 2024).
- SYENSQO. Material Considerations for Single-Use Vs Reusable Medical Devices. https://www.solvay.com/en/chemical-categories/specialty-polymers/healthcare/material-considerations-for-single-use-vs-reusable-medical-devices. (accessed Feb 1, 2024).
- Tavakoli, M. The Adhesive Bonding of Medical Devices. The Adhesive Bonding of Medical Devices (Mddionline.Com) (accessed Feb 1, 2024).
- STERIS. What Is Medical Device Reprocessing? https://www.steris.com/healthcare/knowledge-center/infection-prevention/what-is-medical-device-reprocessing (accessed Feb 1, 2024).
- MASTERBOND. Q & A: Adhesive Considerations for Medical Device Manufacturers. https://www.masterbond.com/q-and-a/adhesive-considerations-medical-device-manufacturers (accessed Feb 1, 2024).
- Singh, A. B.; Khandelwal, C.; Dangayach, G. S. Advancements in Healthcare Materials: Unraveling the Impact of Processing Techniques on Biocompatibility and Performance. Polym. Technol. Mater. 2024, 63(12), 1608–1644. DOI: 10.1080/25740881.2024.2350026.
- MASTERBOND. Autoclaving Resistance of Medical Adhesives. https://www.masterbond.com/articles/autoclave-resistance-medical-adhesives (accessed Feb 1, 2024).
- Hirata, N.; Matsumoto, K.-I.; Inishita, T.; Takenaka, Y.; Suma, Y.; Shintani, H. Gamma-Ray Irradiation, Autoclave and Ethylene Oxide Sterilization to Thermosetting Polyurethane: Sterilization to Polyurethane. Radiat. Phys. Chem. 1995, 46(3), 377–381. DOI: 10.1016/0969-806X(94)00134-6.
- Brétagnol, F.; Rauscher, H.; Hasiwa, M.; Kylian, O.; Ceccone, G.; Hazell, L.; Paul, A. J.; Lefranc, O.; Rossi, F. The Effect of Sterilization Processes on the Bioadhesive Properties and Surface Chemistry of a Plasma-Polymerized Polyethylene Glycol Film: XPS Characterization and L929 Cell Proliferation Tests. Acta Biomater 2008, 4(6), 1745–1751. DOI: 10.1016/j.actbio.2008.06.013.
- Nikousaleh, M. A.; Giesen, R. U.; Heim, H. P.; Hartung, M. MC-Injection Molding with Liquid Silicone Rubber (LSR) and Acrylonitrile Butadiene Styrene (ABS) for Medical Technology. Polymers. 2023, 15(19), 3972. DOI: 10.3390/polym15193972.
- Fenton, M. D. Impact of Radiation Processing on Materials and Adhesives Selection. Presented at the Polymers, Laminations and Coatings Conference, Nashville, TN, USA, Sep 15–17, 1986; pp 33–39.
- Ramaraju, H.; McAtee, A. M.; Akman, R. E.; Verga, A. S.; Bocks, M. L.; Hollister, S. J. Sterilization Effects on Poly(glycerol Dodecanedioate): A Biodegradable Shape Memory Elastomer for Biomedical Applications. J. Biomed. Mater. Res. Part B Appl. Biomater. 2023, 111(4), 958–970. DOI: 10.1002/jbm.b.35205.
- Fenton, M. D. Impact of Radiation Processing on Materials and Adhesives Selection. Presented at the Polymers, Laminations and Coatings Conference, Nashville, TN, Sep 15–17, 1986; pp 33–39.
- Nair, P. D. Currently Practised Sterilization Methods–Some Inadvertent Consequences. J. Biomater. Appl. 1995, 10(2), 121–135. DOI: 10.1177/088532829501000203.