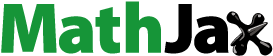
Abstract
The mainstream polishing methods were reviewed in light of polycrystalline CVD diamond wafer with large area. The principles, equipment, and processes of the mainstream polishing methods were reviewed, and the processing characteristics of these methods were compared. The material removal rate (MRR), polishing rate (PR), and minimum surface roughness (Ra) obtained by each polishing method were summed up. The non-contact method has a relatively higher MRR than the contact method, while the contact method has a relatively smaller final roughness than the non-contact method. Two factors, K (K = ΔRa/Δm, ΔRa is the reduction of the surface roughness, Δm is the mass loss) and CI (CI = K/t, t is the total polishing time), were proposed to evaluate the influence of the polishing parameters on the polishing course in the contact polishing methods and to describe the feature of each polishing method, respectively. The variation of the K value indicated that the polishing load and the polishing plate speed did not always influence the polishing effect monotonically in every contact polishing method, and it should be optimized to obtain fine surface roughness with the tiny mass loss. The CI value showed that the non-contact polishing method possessed the feature of high roughness improvement with low mass loss in the unit polishing time. These results reveal how to move forward on the path to polishing large area polycrystalline CVD diamond wafer.
1. Introduction
Chemical vapor deposition (CVD) diamond has been grown to 200 mm in diameter of the polycrystalline wafer [Citation1] and 4 inches in diameter of the single crystal wafer [Citation2]. Polycrystalline CVD diamond wafers are widely used in applications such as integrated circuits [Citation3], heat sinks [Citation4], and microelectromechanical systems [Citation5] due to their larger area, lower costs, and gentler production conditions than single crystal diamonds [Citation6, Citation7]. The electrical performances of large-grain-size polycrystalline diamond FETs with (110) highly oriented grains are comparable or even better in drain current density and high-frequency application than those of single crystal diamond FETs [Citation8].
For fabrication of the reliable diamond-based device, the wafer surface smoothness with Ra < 0.5 µm and less surface damage are essentially demanded [Citation9, Citation10]. Therefore, many polishing methods for CVD diamond were developed and created in the past tens of years, and the graphitization mechanism [Citation11–15], the material removal rate (MRR) [Citation16–30], the polishing rate (PR) [Citation31–33], the polishing damage [Citation34–37] of these methods were studied in detailed and systematically. If deeply considering these studies, some confusing questions would be raised. For example, MRR is originally defined as the thickness reduction during 15 min, and its unit is µm/hr [Citation18]. From this initial definition, MRR is the removal rate of the thickness during 15 min. However, the polishing time was used as the total polishing time instead of 15 min in most parts of the studies (MRR = Δh/Δt) [Citation19–27]. This causes the different values of MRR for the same sample by the same polishing method, e.g. it can be from several nm/hr to tens of µm/hr in mechanical polishing (MP) [Citation20, Citation28–30], resulting in difficultly to evaluate the polishing procedure. In some studies, MRR was defined as the ratio of the improvement of surface roughness and the total polishing time [Citation38], in which MRR and polishing rate (PR) are easily confused. The polishing rate is defined as the ratio of wafer surface roughness variation to time before and after polishing (PR = ΔRa/Δt). Whilst, in some other studies, MRR was defined as the mass loss per unit polishing time with the unit of mg/hr [Citation39–42] or even, as the mass loss per unit polishing time and per unit polishing area with the unit of mg/(hr.cm2) [Citation43]. The meaning of this “MRR” is absolutely not the one of the initial MRR. It seems much more like the mass loss of row crystal (MLRC) as one of the economic factors to evaluate the polishing method because the economic factors, like efficiency, cost of supply material, and loss of row crystal are the main issues in wafer surface smoothing [Citation44]. This indicates that the researcher has realized the importance of the economy in CVD diamond wafer polishing because the CVD diamond wafer with large area is very expensive to grow by the present manufacturing technique [Citation45]. As yet, there is no clear definition of “the large area diamond.” From a series of articles, we have found that this definition will vary depending on the type of diamond product. Circular polycrystalline diamond with a diameter of 50 mm (area: 1963 mm2) was referred to as large area in the existing literature [Citation46], whereas square single crystal diamond with a side length of 5 mm (area: 25 mm2) was referred to as large area [Citation47].
Regretfully, the new MRR (MRR = Δh/Δt) as the mass loss divided by the product of the polishing area and the polishing time was not able to properly evaluate the polishing effect. These questions and problems seriously block the selection of polishing method in CVD diamond wafer smoothing. On the other hand, the as-grown surface of both the polycrystalline and the single crystal CVD diamond wafer is certainly covered by polycrystalline diamond grains [Citation48]. So, it must first sweep away the polycrystalline grains in the beginning to smooth the as-grown surface of CVD diamond wafer. This means that the first selected smoothing procedure of as-grown CVD diamond wafer is to smooth the polycrystalline CVD diamond wafer. The process of smoothing is often referred to as grinding and polishing, and there are somewhat differences between them. Grinding for polycrystalline diamond wafer typically involves the removal of rough polycrystalline grains and the exposure of relatively flat substrates. Grinding for single crystal diamond wafer is usually the process of removing the polycrystalline structure associated with the surface of diamond. Polishing is the process of getting a smoother surface and is often done after grinding. In some literature, the entire polishing process is divided into two processes: grinding (rough polishing) and polishing (fine polishing) [Citation49–51]. In some other literature, grinding and polishing are not usually deliberately distinguished, and they are often combined with each other, as the integrated engineering of grinding and polishing for diamond processing [Citation30, Citation52]. The MRR for the mechanical grinding process of polycrystalline diamond film is approximately 6.67 μm/hr [Citation49]. Random crystal surfaces are encountered when polishing polycrystalline diamond wafers, and additional challenges arise during polycrystalline CVD diamond wafer polishing if non-uniformities are encountered in film thickness and intrinsic stresses as a result of the particular CVD synthesis process. Polishing large area polycrystalline CVD diamond wafer has always been a worldwide problem that needs to be solved urgently [Citation29]. Therefore, in light of the large area polycrystalline CVD diamond wafer polishing, this article reviews the present mainstream polishing methods, like mechanical polishing (MP), chemical mechanical polishing (CMP), thermo-chemical polishing (TCP), dynamic friction polishing (DFP), laser polishing (LP), ion beam polishing (IBP), and plasma assisted polishing (PAP) [Citation53]. The MRR as defined initially and PR of each method are clearly distinguished. A parameter, K = ΔRa/Δm (here within, ΔRa is the improvement of the surface roughness, Δm is the mass loss during the whole polishing time), is defined to analyze the influence of the polishing parameters on the polishing course. Another parameter, CI = K/t (here within, t is the total polishing time), is introduced as a “comprehensive indicator” to evaluate the polishing efficiency and the economy of each polishing method.
2. Mechanical polishing (MP)
Mechanical polishing (MP) is a contact polishing method that is developed from gem diamond polishing. It is highly accurate and commonly used for single crystal diamond polishing instead of polycrystalline diamond. The efficiency of MP is affected very much by the crystallographic orientation of the diamond surface being polished and the direction of sliding because of the polishing resistance. The easily polished crystallographic planes are the (100) and (110) planes, but it is extremely difficult to polish the (111) planes. Even on the easily polished crystallographic planes, the polishing should be performed along the ‘soft direction’ or ‘easy direction,’ avoiding the ‘hard direction.’ The ‘soft direction’ refers to polishing in < 100 > or < 110 > direction on (100) and (110) planes, whilst all directions on the (111) surface are termed as ‘hard direction’ [Citation29, Citation36, Citation54]. Due to the anisotropy, polishing polycrystalline diamond by MP often takes longer. For polycrystalline diamond films with an original roughness of 15 µm, the suitable polishing time is 36 h [Citation55].
The schematic MP equipment and characterization results are shown in . The material removal rate is influenced by some key factors, like the relative sliding speed, the load (hence of pressure) exerted on the polished surface, the diamond grit’s size and its concentration on the Scaife, and the polishing environmental conditions. The removal rate increases linearly with the increase of the relative sliding speed at the medium speed of 100 m/s (sometimes, using rotation per minute as the unit), and non-linearly with the increase of the relative sliding speed at low and/or very high speed, respectively, because of the property change in iron-casted scaife. The increase of the load may increase the removal rate, which is due to the change of the friction coefficient in different directions. The larger diamond powder can obtain a higher removal rate rather than the finer powder. In regard to the concentration, recharging makes no significant difference in an easy < 100 > direction. To obtain a high removal rate and fine finishing surface, manual skill is also important because the soft direction on the easily polished crystallographic planes needs to examine by the experience.
Figure 1. Mechanical polishing (MP): (a) Schematic diagram of the setup for MP experiments; (b) Optical images of MP [Citation56]; (c) Typical AFM roughness image of MP [Citation49]; (d) Scanning electron microscope images of MP [Citation19].
![Figure 1. Mechanical polishing (MP): (a) Schematic diagram of the setup for MP experiments; (b) Optical images of MP [Citation56]; (c) Typical AFM roughness image of MP [Citation49]; (d) Scanning electron microscope images of MP [Citation19].](/cms/asset/dc0b7d9e-e8ea-4178-a689-464153c9196f/tfdi_a_2246495_f0001_c.jpg)
The polishing rate is calculated based on the published papers and listed in . It can be seen that PR is different from MRR. For polishing polycrystalline CVD diamond by MP method, the maximum MRR is up to 70.32 µm/hr [Citation57], the maximum PR is up to 32.00 nm/min [Citation56], the finest surface is up to 0.278 nm [Citation49], and the maximum wafer size is 2827 mm2 [Citation57]. If it is ultrasonic-assisted mechanical polishing, the maximum MRR is up to 180 µm/hr [Citation20], and the maximum PR is up to 900 nm/min [Citation20]. Mechanical polishing has the advantage of simple equipment and long history, however, two difficulties with the application of mechanical polishing in the direction of polishing large polycrystalline diamond wafer are that, on the one hand, the time required is too costly, on the other hand, mechanical removal causes damage to the wafer. Even if a smooth, crack-free surface to the naked eye is obtained after polishing, cracks have already developed on its sub-surface [Citation55]. In severe cases, the cracks become unstable and expand, leading to the cracking of the wafer, which causes a reduction in the yield of the polished products.
Table 1. Evaluation of different polishing methods for polycrystalline CVD diamond wafer.
From , it can be seen that MRR is different from PR. In some polishing methods, like TCP, the long polishing time and the high polishing temperature would result in a high removal rate, but the surface roughness becomes worse [Citation72]. Therefore, the difference between MRR and PR should be clarified. The reason why MRR and PR are often confused in CVD diamond wafer polishing maybe lie in that polishing CVD diamond wafer is different from other semiconductors, like Si. Usually, the surface smoothing procedure of Si and other semiconductors includes grinding, lapping, and polishing [Citation73, Citation74]. After smoothing procedure, the treated surface of wafer should be characterized by a degree of crystalline perfection, defect, microstructure, surface/subsurface damage, global surface planarization, uniform thickness/total thickness variation (TTV), residual stresses, and roughness. MRR is suitable to describe the grinding/lapping procedure. As TTV is an inspected factor, MRR is an essential value to be measured and calculated individually. However, the grinding/lapping procedure is mixed with polishing procedure in CVD diamond smoothing procedure, especially in smoothing thin diamond film on the substrate. Furthermore, diamond-based device is not too much applied rather than Si-based device, thus, the tested factor, like TTV, is not exactly measured and calculated individually. So, MRR in smoothing CVD diamond wafer is much similar to PR.
Generally speaking, the polishing procedure undergoes two courses as the grinding and the polishing. In the grinding course, the mass loss is main, and the roughness reduction dominates the polishing course. Therefore, PR should be applied to describe the polishing course as it is defined as the ratio of the surface roughness improvement to the polishing time. MRR should be used in the grinding course. For the homogenous material, the density of the polished material is uniform everywhere. MRR is thus, equivalent to the mass loss per unit polishing time. However, it is not the one for polycrystalline CVD diamond because the polycrystalline CVD diamond is not the homogenous material. MRR is not in a fixed proportion to the mass loss per unit polishing time. Thus, MRR can not exactly evaluate the efficiency and the economy of the polishing method for polycrystalline CVD diamond.
Another important point is that the reduction of the wafer thickness does not mean that the surface roughness is improved. This phenomenon has been found in several polishing methods [Citation75–77]. In other words, some polishing parameters influence complicatedly on the surface roughness [Citation58, Citation78, Citation79]. To make it clear, a parameter, K, was defined as ΔRa/Δm to evaluate the influence of polishing parameters on the polishing effect. A larger value of K means that a larger improvement in roughness can be obtained with a smaller loss of mass. The present CVD diamond polishing methods are divided into two kinds, as contact method and non-contact method [Citation53]. However, how to choose these polishing methods in a certain polishing case and how to evaluate these polishing methods in light of economy and the polishing efficiency is not very clear yet. So, we define a parameter, CI = K/t = (ΔRa)/(tΔm) (here within, ΔRa is the improvement of the surface roughness; t is the total polishing time to obtain the surface roughness improvement; Δm is the total mass loss during t.), as a “comprehensive indicator” to evaluate the polishing efficiency and the economy of each polishing method. According to the definition of CI, a high CI value means that it can quickly obtain a large improvement of surface roughness with few mass loss in unit polishing time. Otherwise, the small improvement of roughness is obtained with much mass loss in unit polishing time. In MP, K takes values from 2.129 × 10−4 to 0.331 m/g, and CI takes values from 0.013 to 2.560 μm/(g·s) [Citation19, Citation56, Citation80–82].
3. Chemical mechanical polishing (CMP)
Chemical mechanical polishing (CMP), also known as thermal oxidation polishing, is another contact polishing method. During CMP, the diamond surface is treated by a rotating polishing plate, assisted by oxidizing chemicals at elevated temperatures as well as the predetermined load. The entire surface of the diamond is covered with molten oxidizing reagent in the polishing process, but polishing occurs only on peaks that are in contact with the polishing plate. Usually, the polishing rate for CMP is in the order of 10 nm/min, and the minimum Ra could be even less than 10 nm in the local area [Citation83]. For polishing polycrystalline CVD diamond by CMP method, the maximum MRR is up to 120.20 µm/hr [Citation30], the maximum PR is up to 92.20 nm/min [Citation43], the finest surface is up to 0.187 nm [Citation41], and the maximum wafer size is 7853 mm2 [Citation70]. K takes values from 2.173 × 10−4 to 0.002 m/g, and CI takes values from 0.015 to 0.275 μm/(g·s) [Citation41, Citation43, Citation84].
The material removal rate is dependent on the oxidization reagent used and the corresponding polishing temperature, the applied load (pressure), and sliding speed. The chemical agents are selected from a group of oxidizing agents, such as NaNO3, KNO3, KOH, KClO3, K2Cr2O7, H2O2, HClO, HNO3, H2SO4, AgO, Cr2O3, MnO2, BaO2, PdO2, and their mixtures. The commonly used ones are NaNO3, KNO3, and KOH. Their melting temperatures are 308, 324, and 360 °C, respectively. The mixtures of oxidizing agents with lower melting points have also been used in the polishing process, such as LiNO3 + KNO3 which has a melting point at 130 °C. During a polishing operation, the polishing plate needs to be maintained at a constant temperature over the melting point of oxidizing chemicals dispersed onto its surface. The higher temperature results in a higher removal rate as the rate of chemical reaction increases faster at higher temperatures. The higher sliding speed and applied load result in the higher removal rate. A typical polishing parameter is a sliding speed of approximately 40 m/s (at 2800 rpm), pressure 1.4 MPa (load 13 N on 3 × 3 mm2 specimen).
It can be seen that CMP combines the MP with the chemical etching to enhance the material removal rate and improve surface quality. The difference between CMP and MP with the enhancement of oxidation reaction is the temperature which is determined by the added chemicals during the polishing. Moreover, surface damages caused by CMP are less rather than those caused by MP and take a shorter process time. Also, CMP is ideally suited to obtaining very fine sample surfaces. The disadvantage is that the build-up of chemical reaction products can cause dirty and messy polishing equipment. The schematic diagram of the CMP instrument and characterization results are shown in , and the MRR and PR are listed in .
Figure 2. Chemical mechanical polishing (CMP): (a) Schematic diagram of the setup for CMP experiments (Adapted from ref. [Citation43]); (b) Typical AFM roughness image of CMP [Citation41]; (c) Surface optical images of CMP [Citation41].
![Figure 2. Chemical mechanical polishing (CMP): (a) Schematic diagram of the setup for CMP experiments (Adapted from ref. [Citation43]); (b) Typical AFM roughness image of CMP [Citation41]; (c) Surface optical images of CMP [Citation41].](/cms/asset/7654b1d3-a8b4-4db4-8931-88d71b7a2fd2/tfdi_a_2246495_f0002_c.jpg)
4. Thermo-chemical polishing (TCP)
Thermo-chemical polishing (TCP) is also a contact polishing method, during which the diamond surface is pressed against a rotating transition metal plate at elevated temperatures from 700 to 1000 °C. The hot transition metals include iron, Mn, lanthanum (La), cerium (Ce), and their alloys. It includes two courses, like the hot metal plate polishing and the thermo diffusion etching which is based on the atomic dissolution of carbon into the hot metal/alloy foils, molten or partially molten metal/alloy, the transformation of diamond into graphite, and diamond oxidation. As no high pressure is exerted on the diamond wafer, micro-cracks or other defects on the polished diamond surfaces are not easily generated after polishing. For polishing polycrystalline CVD diamond by TCP method, the maximum MRR is up to over 400 μm/h [Citation23], the maximum PR is up to 69.30 nm/min [Citation61], the finest surface is up to 1.3 nm [Citation66], and the maximum wafer size is 225 mm2 [Citation58]. K takes values from 6.274 × 10−5 to 4.730 × 10−4 m/g, and CI takes values from 0.015 to 0.240 μm/(g·s) [Citation23, Citation32, Citation58, Citation72].
The material removal rate and polished surface quality are influenced by the polishing temperature, pressure exerted on the diamond, surrounding atmosphere, sliding speed, and crystallographic orientations. Among these parameters, the polishing temperature and the degree of contact between the polishing plate and the diamond surfaces profoundly influence the material removal rate. There exists a critical polishing temperature, e.g. 700°C, polishing does not proceed because of insufficient chemical reactivity. Vacuum may be the most atmosphere for TCP because polishing rate is the highest one among those obtained in the atmosphere of hydrogen, argon, helium, and nitrogen, respectively. Among those gas atmospheres, a significantly high value is obtained in hydrogen. This may be due to the effect of decarburization of the iron disk by hydrogen via methane molecule formation, thus keeping the disk in an active state. Therefore, a gas mixture comprising 4% hydrogen and 96% argon has also been used as ambient atmosphere in polishing for safety reasons and to obtain a very fine surface. The other parameters, pressure, sliding speed, and crystallographic orientations, do influence the polishing efficiency and quality of the surface, but not too significant. Polishing is more effective in liquid alloys compared to the solid metal/alloys. Although increasing temperature and time can significantly improve the material removal rate and surface finish of diamond films, very high temperatures and too much time will make the surface rougher due to preferred etching at the boundary. TCP has good prospects in the field of polishing large area of polycrystalline diamond wafer due to the short polishing times. However, the equipment costs are high due to the strong dependence on high temperature conditions. The costs are exacerbated when transition and rare earth metals are used for polishing. In addition, the severe loss of material during polishing does not mean that a smooth surface can be obtained, which is a necessary consideration for polishing large area of polycrystalline diamond wafer. The schematic diagram of the instrument and characterization results are shown in , and the MRR and PR are listed in .
Figure 3. Thermo-chemical polishing (TCP): (a) Schematic diagram of the setup for TCP experiments. (Adapted from ref. [Citation58]); (b) Typical AFM roughness image of TCP [Citation85]; (c) Surface optical images of TCP [Citation85].
![Figure 3. Thermo-chemical polishing (TCP): (a) Schematic diagram of the setup for TCP experiments. (Adapted from ref. [Citation58]); (b) Typical AFM roughness image of TCP [Citation85]; (c) Surface optical images of TCP [Citation85].](/cms/asset/5e499dcf-2061-4935-8f0e-917598128086/tfdi_a_2246495_f0003_b.jpg)
5. Dynamic friction polishing (DFP)
Dynamic friction polishing (DFP), as the contact polishing technique, is an abrasive-free process that utilizes the frictional heating between a diamond specimen and a rotating catalytic metal disk. As the thermo-chemical reaction is activated, the conversion of diamond into non-diamond carbon, diffusion, oxidation, and mechanical abrasion take place to achieve an efficient material removal. The significant features of the DFP method and its potential superiority over the other existing methods include 1) Abrasive free polishing by simply pressing a diamond workpiece to a metal disk rotating at a high speed to generate frictional heat. 2) Polishing at room temperature, effective use of polishing-generated frictional heating, and not requiring special equipment for heating the polishing disk and diamond specimen. 3) Polishing in a dry atmospheric environment and not requiring a vacuum chamber. 4) Short polishing time (in the order of a few tens of seconds to a few minutes), material removal rate is up to 480 μm/min for single crystal diamond which is 100 times faster than the other polishing techniques. 5) Surface roughness values of the order of 50 nm Ra for single crystal diamond. Thus, it is a very promising method for CVD diamond single crystal polishing. For polishing polycrystalline CVD diamond by DFP method, the maximum MRR is up to 1260 μm/h [Citation38], the maximum PR is up to 1166.70 nm/min [Citation62], the finest surface is up to 0.1 nm [Citation67], and the maximum wafer size is 126.6 mm2 [Citation38]. K takes values from 7.143 × 10−5 to 0.001 m/g, and CI takes values from 0.198 to 5.368 μm/(g·s) [Citation38, Citation42].
The material removal rate is depending on the polishing parameters, like the disk material, pressure exerted on the diamond, rotating speed/sliding speed, and polishing environments. Among these parameters, the pressure pressing on the diamond is a key factor, i.e. there is a threshold value of pressure to start the polishing at a certain rotating speed/sliding speed. If the pressure is lower than the threshold value, DFP won’t start. Blowing oxygen or air to the polishing point will enhance the polishing rate if polishing is starting. The DFP equipment is also simple. It differs from MP in that DFP is an abrasive-free method and does not suffer from anisotropy, resulting in a larger MRR and shorter polishing times. However, DFP requires the use of experimental parameters such as high pressure to ensure that the wafers are at high temperatures (usually over 700 °C), and the suitability of these experimental parameters becomes a challenge when polishing large areas of polycrystalline diamond wafers, as the high pressure increases the risk of wafer cracking and can lead to reduced yields.
The schematic diagram of the setup for DFP and characterization results are shown in , and the MRR and PR are listed in .
Figure 4. Dynamic friction polishing (DFP): (a) Schematic diagram of the setup for DFP. (Adapted from ref. [Citation86]); (b) Typical AFM roughness image of DFP [Citation67]; (c) Scanning electron microscope images of DFP [Citation87].
![Figure 4. Dynamic friction polishing (DFP): (a) Schematic diagram of the setup for DFP. (Adapted from ref. [Citation86]); (b) Typical AFM roughness image of DFP [Citation67]; (c) Scanning electron microscope images of DFP [Citation87].](/cms/asset/5f3d0c76-465a-419c-8eea-0e9413c66420/tfdi_a_2246495_f0004_c.jpg)
6. Laser polishing (LP)
Laser polishing (LP) is a non-contact polishing technique, which performs the ablation by focusing the scanning laser beam on the diamond surface. LP is based on the direct interaction between the laser photon and the diamond surface atoms, causing the ablation due to the pitching and graphitization. For polishing polycrystalline CVD diamond by LP method, the maximum MRR is up to 10 μm/h [Citation58], the maximum PR is up to 3592 nm/min [Citation63], and the finest surface is up to 22 nm [Citation68], and the maximum wafer size is 225 mm2 [Citation58]. K takes values from 1.339 × 10−5 to 4.464 × 10−5 m/g, and CI takes values from 0.111 to 1.110 μm/(g·s) [Citation58, Citation63].
The polishing efficiency of LP is dependent on the operating parameters of laser beam and the properties of the polished diamond. The former include wavelength (nm), energy density fluence (J/cm2), pulse length (nanosecond), repetition rate (Hz), angle of incidence (deg.), and spot size as well as scanning speed, focal plane position, assist gas type, and pressure. While, the later includes the spectral absorptivity at the laser beam wavelength, thermal diffusivity, and purity (constituent phases, defects, and surface cleanliness).
Photon Energy of laser light is a function of frequency f (or wavelength λ) and speed of light and the energy E in a photon is given by
where h is Planck’s constant (6.63 × 10−34 J·s), c is the speed of light (= 3.00 × 108 m/s), while 1 eV = 1.602 × 10−19 J.
As the wavelength λ of the laser increases, the energy E decreases. If the photon energy E of the incident laser exceeds the band gap of diamond (=5.5 eV), ablation can take place directly by the interaction of the laser light with the diamond [Citation88]. Required by 5.5 eV of the diamond band gap, the wavelength should be shorter than 2.2 µm for the incident laser. If the wavelength were longer, the incident laser easily transmits pure diamond without any ablation. The strong absorption takes place only in lattice defects and impurities. This strong absorption enables to result in the graphitic layer which enhances the absorption. Like the limit of the wavelength of incident laser, there exists threshold value of laser fluencies (energy density). For example, it is about 7 J/cm2 for natural Ia-type diamond crystal.
Under the condition of using the incident laser with the wavelength shorter than 2.2 µm and the laser fluencies (energy density) over the threshold value, the material removal rate is determined by the thermal conductivity and diamond crystalline quality because these two properties influence the light absorption of diamond. In summary, LP is a highly efficient non-contact polishing technique with no wafer area limitations and is suitable for small areas and can be extended to large areas. Polishing can be done in air at a low cost. LP is ideally suited to the rough polishing of large area diamond wafer without the cracking associated with pressure.
The instrument and characterization results of LP are shown in , and the MRR and PR are listed in .
Figure 5. Laser polishing (LP): (a) Schematic diagram of the setup for LP (Adapted from ref. [Citation89]); (b) Typical AFM roughness image of LP [Citation88]; (c) Scanning electron microscope images of LP [Citation90].
![Figure 5. Laser polishing (LP): (a) Schematic diagram of the setup for LP (Adapted from ref. [Citation89]); (b) Typical AFM roughness image of LP [Citation88]; (c) Scanning electron microscope images of LP [Citation90].](/cms/asset/9d62bd24-f72c-42a7-b494-e6b2fcc79eee/tfdi_a_2246495_f0005_b.jpg)
7. Ion beam polishing (IBP)
Ion beam polishing (IBP) is a non-contact polishing technique, also called high energy beam polishing, which applies the principle of bombardment of the diamond surface with reactive/non-reactive ion beams to ablate diamond atoms by sputtering. Two courses result in the carbon atoms removal. First, the heating due to the bombardment of incident ion makes the host lattice atoms sublimated. Second, the incident ion can simply knock off a host atom by sputtering. For polishing polycrystalline CVD diamond by IBP method, the maximum MRR is up to 8.60 μm/h [Citation59], the maximum PR is up to 24.90 nm/min [Citation64], the finest surface is up to 1.9 nm [Citation69], and the maximum wafer size is 100 mm2 [Citation64]. K takes values from 0.005 to 2.640 m/g, and CI takes values from 0.208 to 36.667 μm/(g·s) [Citation59, Citation69, Citation91].
The material removal rate can be enhanced by utilizing the oxidation and etching in reactive ion etching (RIE), i.e., the reactive channels wherein O, O2, O3, OH, H, etc., interact and remove carbon from the diamond surface via heterogeneous chemical reactions. In ion beam polishing, the polishing rates and the surface finish are dependent on the incidence angle of ion irradiation with respect to the diamond surface, energy power of irradiating, the type of ion beam and gap flow, and chamber vacuum pressure. As the polishing rate is not very fast, IBP can be regarded as the polishing method for surface fine fish of single crystal diamond wafer instead of coarse polycrystalline diamond film. It means that IBP is not suitable for polycrystalline grain removal in production of single crystal diamond wafer. The instrument of IBP and characterization results are shown in , and the MRR and PR are listed in .
Figure 6. Ion beam polishing (IBP): (a) An ion beam machining apparatus equipped with a high-voltage discharge-type ion source (Adapted from ref. [Citation92]); (b) Typical AFM roughness image of IBP [Citation93]; (c) Scanning electron microscope images of IBP [Citation91].
![Figure 6. Ion beam polishing (IBP): (a) An ion beam machining apparatus equipped with a high-voltage discharge-type ion source (Adapted from ref. [Citation92]); (b) Typical AFM roughness image of IBP [Citation93]; (c) Scanning electron microscope images of IBP [Citation91].](/cms/asset/1ba9a94d-8baf-426b-802c-91e47fe87ca8/tfdi_a_2246495_f0006_b.jpg)
8. Plasma assisted polishing (PAP)
Plasma assisted polishing (PAP) is also a non-contact polishing method. It is based on the plasma etching of the diamond surface to complete the polishing. The polishing process significantly depends on the plasma processing parameters, such as the working gas, the chamber pressure, the exciting electromagnetic wave frequency, and the power of plasma. The working gasses are selected from Ar, H2, O2, F2, and SiF6, or their mixture, such as Ar-H2, Ar-O2, SiF6-O2. The chamber pressure is less than 102 Pa. The plasma can be generated as the radio frequency (RF) plasma and DC plasma by RF dipole electrodes and DC bias, respectively. The frequency is adjusted around 2 MHz with the RF voltage varying in a range from 100 V to 250 V. For DC bias, it is varied in a range from –400 V to -600 V. A standard experimental set up and characterization results are shown in , and the MRR and PR are listed in .
Figure 7. Plasma assisted polishing (PAP): (a) Plasma polishing system with parallel stainless steel rods (Adapted from ref. [Citation26]); (b) Optical images of PAP [Citation9]; (c) Typical AFM roughness image of PAP [Citation49]; (d) Scanning electron microscope images of PAP [Citation9].
![Figure 7. Plasma assisted polishing (PAP): (a) Plasma polishing system with parallel stainless steel rods (Adapted from ref. [Citation26]); (b) Optical images of PAP [Citation9]; (c) Typical AFM roughness image of PAP [Citation49]; (d) Scanning electron microscope images of PAP [Citation9].](/cms/asset/8a3f7c1d-04b9-418b-a824-a513b487ceb6/tfdi_a_2246495_f0007_c.jpg)
For polishing polycrystalline CVD diamond by PAP method, the maximum MRR is up to 120 µm/hr [Citation60], the maximum PR is up to 8.24 nm/min [Citation65], the finest surface is up to 1.79 nm [Citation49], and the maximum wafer size is 100 mm2 [Citation71]. K takes values from 1.425 to 1.943 m/g, and CI takes values from 1187 to 1618 μm/(g·s) [Citation94].
The MRR of PAP is faster than IBP, but due to the heating of the plasma, the surface of the diamond wafer is susceptible to contamination. In addition, for polishing large area of polycrystalline diamond, the dilemma with PAP is the expensive auxiliary equipment required to obtain the same large area of plasma.
9. Other polishing methods
There are some other methods for polishing diamond, such as electrical discharge machining (EDM), abrasive liquid jet polishing, aero-lap polishing, float polishing, spark erosion, and so on. These methods are not suitable for high quality CVD diamond wafer polishing. For example, the EDM polishing method is suitable for electrically conductive PCD, instead of non-electrically conductive CVD polycrystalline and single crystalline diamond films/wafers.
10. Discussion
10.1. Comparison of various methods
The characteristics of various methods for polishing diamond materials are listed in . Each of these methods has both advantages and disadvantages. CMP, TCP, LP may be more suitable for polishing large area polycrystalline diamond wafer. The present CVD diamond polishing methods are divided into two kinds, as contact method and non-contact method [Citation53]. The non-contact method has a relatively higher MRR than the contact method, while the contact method has a relatively smaller final roughness than the non-contact method.
Table 2. Comparison of various methods for polishing diamond materials.
10.2. Insight into the polishing course
In our previous work on DFP in , it is found that the DFP procedure can be divided into two parts, one part is to remove the mass, and the other part is to improve the surface roughness. From the , it can be seen that the polishing parameters, like the polishing load and the polishing time, do not benefit for the roughness improvement every time. If the polishing load is over one value, the roughness improvement reduces whilst the mass loss increases. It is the same tendency as that in the polishing time. Only the polishing speed monotonically improve the surface roughness according to the K value. It means that the polishing time and the polishing load should be selected carefully. is the comparation of the load vs. K and/or rotation speed vs. K in each contact polishing method. It shows that each polishing method possesses different K value zone, and the K varies in different way. If compared the K value of each polishing method, the maximum K value occurs in MP method. also indicates that the selection of polishing parameters can be based on the K value as a reference, i.e. the polishing procedure should be designed with the high K value.
Figure 8. K values depending on polishing parameters in DFP: (a) K vs polishing time; (b) K vs polishing load; (c) K vs polishing plate linear velocity [Citation86].
![Figure 8. K values depending on polishing parameters in DFP: (a) K vs polishing time; (b) K vs polishing load; (c) K vs polishing plate linear velocity [Citation86].](/cms/asset/83afac3d-ddc5-4fe9-93fb-47f5e54b49ea/tfdi_a_2246495_f0008_b.jpg)
Figure 9. (a) Polishing load vs. K; (b) Polishing plate linear velocity vs. K. (MP: [Citation80, Citation95], CMP: [Citation43], DFP: [Citation86], TCP: [Citation23, Citation32, Citation72]).
![Figure 9. (a) Polishing load vs. K; (b) Polishing plate linear velocity vs. K. (MP: [Citation80, Citation95], CMP: [Citation43], DFP: [Citation86], TCP: [Citation23, Citation32, Citation72]).](/cms/asset/c99de466-439c-4fb7-a463-dbd06b9a5b46/tfdi_a_2246495_f0009_c.jpg)
10.3. Feature of each polishing method with K and CI
K and CI of each polishing method calculated based on data in references are shown in . From , it can be seen that there exists the distribution of K value of each polishing method. For polycrystalline CVD diamond polishing, the relatively high K exists in IBP and PAP. The relatively low K exists in LP, TCP, DFP, MP, and CMP. A higher value of K means that a higher improvement in roughness can be obtained with a smaller loss of mass. From , it can be seen that there exists the distribution of CI value of each polishing method. For polycrystalline CVD diamond polishing, the relatively high CI exists in LP, DFP, IBP, and PAP. The relatively low CI exists in MP, CMP, and TCP. This indicates that the non-contact methods possess high CI rather than the contact methods.
Figure 10. (a) K of each polishing method calculated based on data in references; (b) CI of each polishing method calculated based on data in references. (MP: [Citation19, Citation56, Citation80–82], CMP: [Citation41, Citation43, Citation84], TCP: [Citation23, Citation32, Citation58, Citation72], DFP: [Citation38, Citation42], LP: [Citation58, Citation63], IBP: [Citation59, Citation69, Citation91], PAP: [Citation94]).
![Figure 10. (a) K of each polishing method calculated based on data in references; (b) CI of each polishing method calculated based on data in references. (MP: [Citation19, Citation56, Citation80–82], CMP: [Citation41, Citation43, Citation84], TCP: [Citation23, Citation32, Citation58, Citation72], DFP: [Citation38, Citation42], LP: [Citation58, Citation63], IBP: [Citation59, Citation69, Citation91], PAP: [Citation94]).](/cms/asset/28a912b5-5afe-4139-8e47-d599b3ed127a/tfdi_a_2246495_f0010_c.jpg)
The non-contact methods tend to be hybrid with each other or with the contact method. For example, LP hybrid PAP can arrive at a very smooth surface with a surface roughness of 0.53 nm Sq and a flatness of less than 1 μm [Citation96]. LP hybrid MP can arrive at 40 nm after 10 min LP and 20 min MP. This hybrid polishing method must meet the requirements of obtaining the best roughness with the lowest quality loss in the shortest polishing time. Although the contact method can be performed in the whole polishing procedure, i.e., grinding and polishing, the subsurface damage can not be ignored. A mixture of contact and non-contact polishing methods could be a promising approach for polishing large area polycrystalline diamond wafer.
11. Conclusion
Based on the above review, we can draw the following conclusion:
MRR and PR are different factors in a certain polishing course. The initial definition of MRR is not able to evaluate the efficiency and the economy of the polishing method for polycrystalline CVD diamond polishing.
The non-contact method has a relatively higher MRR than the contact method, while the contact method has a relatively smaller final roughness than the non-contact method.
The parameter K can work as a role to distinguish the influence of each parameter on the polishing course of a certain polishing method. The higher the K value, the less mass loss with more improvement of surface roughness occurs.
CI parameter is defined as a parameter to evaluate the polishing efficiency and economy of each method. CI value indicates that the non-contact polishing method possesses the feature of high roughness improvement with low mass loss in the per polishing time.
To polish the as-grown CVD diamond wafer, it is suggested to start the polishing from the polycrystalline CVD diamond wafer polishing. The polishing procedure is suggested to be the hybrid of contact method and the non-contact method.
Disclosure statement
No potential conflict of interest was reported by the authors.
Additional information
Funding
Notes on contributors
Haochen Zhang
Haochen Zhang: Conceptualization, Investigation, Data collection, Writing-original draft, Visualization.
Zengyu Yan
Zengyu Yan: Data collection, Investigation, Theoretical analysis, Visualization.
Zhipeng Song
Zhipeng Song: Resources, Supervision, Conceptualization, Methodology, Project administration, Funding acquisition.
Shuai Zhou
Shuai Zhou: Methodology, Formal analysis.
Zilong Zhang
Zilong Zhang: Supervision, Conceptualization, Methodology, Formal analysis.
Guo Chen
Guo Chen: Supervision, Conceptualization, Methodology, Formal analysis.
Meiyong Liao
Meiyong Liao: Supervision, Conceptualization, Methodology, Formal analysis.
Guangchao Chen
Guangchao Chen: Writing-review & editing, Visualization, Supervision, Conceptualization, Methodology, Project administration, Funding acquisition.
Reference
- Chae K-W, Baik Y-J, Park J-K, et al. The 8-inch free-standing CVD diamond wafer fabricated by DC-PACVD. Diamond Relat Mater. 2010;19(10):1–15.
- Schreck M, Gsell S, Brescia R, et al. Ion bombardment induced buried lateral growth: the key mechanism for the synthesis of single crystal diamond wafers. Sci Rep. 2017;7(1):44462.
- Zhu X, Shao S, Chan S, et al. High performance of normally‐on and normally‐off devices with highly boron‐doped source and drain on H‐terminated polycrystalline diamond. Adv Elect Materials. 2023;9(3):2201122.
- Chernykh MY, Andreev AA, Ezubchenko IS, et al. GaN-based heterostructures with CVD diamond heat sinks: a new fabrication approach towards efficient electronic devices. Appl Mater Today. 2022;26:101338.
- Buijnsters JG, Tsigkourakos M, Hantschel T, et al. Effect of boron doping on the wear behavior of the growth and nucleation surfaces of micro- and nanocrystalline diamond films. ACS Appl Mater Interfaces. 2016;8(39):26381–26391.
- Alcantar-Pena JJ, de Obaldia E, Tirado P, et al. Polycrystalline diamond films with tailored micro/nanostructure/doping for new large area film-based diamond electronics. Diamond Relat Mater. 2019;91:261–271.
- Francis D, Kuball M. 14 - GaN-on-diamond materials and device technology: a review. In: Tadjer MJ, Anderson TJ, editors. Thermal management of gallium nitride electronics. Cambridge, England: Woodhead Publishing; 2022. p. 295–331.
- Imanishi S, Horikawa K, Oi N, et al. 3.8W/mm RF power density for ALD Al2O3-based two-dimensional hole gas diamond MOSFET operating at saturation velocity. IEEE Electron Device Lett. 2019;40(2):279–282.
- Yunata EE, Aizawa T, Tamaoki K, et al. Plasma polishing and finishing of CVD-diamond coated WC (Co) dies for dry stamping. International Conference on the Technology of Plasticity (ICTP), Cambridge, England, 2017, pp. 2197–2202.
- Hicks ML, Pakpour-Tabrizi AC, Jackman RB. Polishing, preparation and patterning of diamond for device applications. Diamond Relat Mater. 2019;97:107424.
- Wang HC, Jin ZJ, Li XH, et al. Insight into the graphitization mechanism of the interface between iron and diamond: a DFT study. Diamond Relat Mater. 2022;127:109213.
- Shubin WB, Yujing SJ, Shi T. Surface graphitization analysis of cerium-polished HFCVD diamond films with micro-raman spectra. J Rare Earths. 2008;26(3):362–366.
- Yan XB, Wei JJ, An K, et al. High temperature surface graphitization of CVD diamond films and analysis of the kinetics mechanism. Diamond Relat Mater. 2021;120:108647.
- Lee CK. Effects of hydrogen and oxygen on the electrochemical corrosion and wear-corrosion behavior of diamond films deposited by hot filament chemical vapor deposition. Appl Surf Sci. 2008;254(13):4111–4117.
- Shi Z, Jin Z, Guo X, et al. Insights into the atomistic behavior in diamond chemical mechanical polishing with OH environment using ReaxFF molecular dynamics simulation. Comput Mater Sci. 2019;166:136–142.
- Kubota A, Nagae S, Touge M. Improvement of material removal rate of single-crystal diamond by polishing using H2O2 solution. Diamond Relat Mater. 2016;70:39–45.
- Chen Y, Nguyen T, Zhang LC. Polishing of polycrystalline diamond by the technique of dynamic friction-Part 5: quantitative analysis of material removal. Int J Machine Tools & Manufacture. 2009;49(6):515–520.
- Le X, Peterson ML. Material removal rate in flat lapping. J Manuf Syst. 1999;18(2):71–78.
- Zhou L, Huang ST, Xu LF. An efficient super-high speed polishing method for CVD diamond films. Int J Refractory Metals & Hard Mater. 2011;29(6):698–704.
- Ralchenko VG, Ashkinazi EE, Zavedeev EV, et al. High-rate ultrasonic polishing of polycrystalline diamond films. Diamond Relat Mater. 2016;66:171–176.
- Kubota A, Nagae S, Motoyama S. High-precision mechanical polishing method for diamond substrate using micron-sized diamond abrasive grains. Diamond Relat Mater. 2020;101:107644.
- Yang H, Jin Z, Niu H, et al. A novel visible-light catalyzed assisted single crystal diamond chemical mechanical polishing slurry and polishing mechanism. Mater Today Commun. 2022;33:104249.
- Sun Y, Wang S, Tian S, et al. Polishing of diamond thick films by Ce at lower temperatures. Diamond Relat Mater. 2006;15(9):1412–1417.
- Johnson CE. Chemical polishing of diamond. Surf Coat Technol. 1994;68-69/(69):374–377.
- Liu N, Sugawara K, Yoshitaka N, et al. Damage-free highly efficient plasma-assisted polishing of a 20-mm square large mosaic single crystal diamond substrate. Sci Rep. 2020;10(1):19432.
- Yamamura K, Emori K, Sun R, et al. Damage-free highly efficient polishing of single-crystal diamond wafer by plasma-assisted polishing. CIRP Ann. 2018;67(1):353–356.
- Yang HP, Jin ZJ, Niu L, et al. Visible-light catalyzed assisted chemical mechanical polishing of single crystal diamond. Diamond Relat Mater. 2022;125:108982.
- Xiao C, Hsia F-C, Sutton-Cook A, et al. Polishing of polycrystalline diamond using synergies between chemical and mechanical inputs: a review of mechanisms and processes. Carbon. 2022;196:29–48.
- Schuelke T, Grotjohn TA. Diamond polishing. Diamond Relat Mater. 2013;32:17–26.
- Xu H, Zang J, Tian P, et al. Surface conversion reaction and high efficient grinding of CVD diamond films by chemically mechanical polishing. Ceram Int. 2018;44(17):21641–21647.
- Thomas ELH, Nelson GW, Mandal S, et al. Chemical mechanical polishing of thin film diamond. Carbon. 2014;68:473–479.
- Li J, Wang S, Sun Y, et al. Diamond films by CVD and high rate polishing at low temperature with partially molten Ce-Fe alloy. Rare Metal Mater Engin. 2007;36(5):933–936.
- Zaitsev AM, Kosaca G, Richarz B, et al. Thermochemical polishing of CVD diamond films. Diamond Relat Mater. 1998;7(8):1108–1117.
- Nguyen VT, Fang TH. Phase transformation and subsurface damage formation in the ultrafine machining process of a diamond substrate through atomistic simulation. Sci Rep. 2021;11(1):17795.
- Zhang M, Xu H. Controllability and mechanism investigation on the subsurface damage of CVD diamond film by Fe-containing vitrified bond wheel. Tribol Int. 2021;155:106774.
- Zheng YT, Ye HT, Thornton R, et al. Subsurface cleavage of diamond after high-speed three-dimensional dynamic friction polishing. Diamond Relat Mater. 2020;101:107600.
- Kononenko TV, Pivovarov PA, Khomich AA, et al. Processing of polycrystalline diamond surface by IR laser pulses without interior damage. Optics and Laser Technol. 2019;117:87–93.
- Chen Y, Zhang LC. Polishing of polycrystalline diamond by the technique of dynamic friction, part 4: establishing the polishing map. Int J Machine Tools & Manufacture. 2009;49(3–4):309–314.
- Xu HQ, Zang JB, Yang GP, et al. High-efficiency grinding CVD diamond films by Fe-Ce containing corundum grinding wheels. Diamond Relat Mater. 2017;80:5–13.
- Hocheng H, Chen CC. Chemical-assisted mechanical polishing of diamond film on wafer. In: Jywe W, Chen CL, Fan KC, et al., editors. Progress on advanced manufacture for micro/nano technology 2005, Pt 1 and 2. Stafa, Switzerland: Trans Tech Publications Ltd, 2006. pp. 1225–1230.
- Yuan Z, Jin Z, Zhang Y, et al. Chemical mechanical polishing slurries for chemically vapor-deposited diamond films. J Manuf Sci Eng. 2013;135(4):041006.
- Feng HB, Chen YQ, Zhang LC. Polishing of CVD diamond wafers and films. International Conference on Materials Science and Nanotechnology (ICMSN 2012), Guangzhou, PEOPLES R CHINA, 2012, pp. 373–376.
- Wang CY, Zhang FL, Kuang TC, et al. Chemical/mechanical polishing of diamond films assisted by molten mixture of LiNO3 and KNO3. Thin Solid Films. 2006;496(2):698–702.
- Sharonov GV, Petrov SA. Superfinishing polish of diamond substrates for epitaxial technology. J Eng Phys Thermophy. 2011;84(5):1188–1191.
- Xiu LF, Chengming L. Thirty years of chemical vapor deposition (CVD) diamond films research in China. J Synthetic Crystals. 2022;51(5):753–758.
- Li B, Han B, Lu XY, et al. IR transmittance of large-sized free-standing transparent diamond films prepared by MWPCVD. New Carbon Mater. 2008;23(3):245–249.
- Mao YM, Gao J, Zheng K, et al. Optimization for solderability of large-size single-crystal diamond with heterogeneity alloys by tantalum coating. Surface & Coatings Technol. 2022;437:128382.
- Chen G, Liu H, Li J, et al. Preparation method of CVD diamond and novel ideas for increasing growth rate. JES. 2017;09(06):538–546.
- Huang XR, Zhou CJ, Wu B, et al. Wafer-scale polishing of polycrystalline MPACVD-diamond. Surfaces. 2022;5(1):155–164.
- Liu N, Sugimoto K, Yoshitaka N, et al. Highly efficient finishing of large-sized single crystal diamond substrates by combining nanosecond pulsed laser trimming and plasma-assisted polishing. Ceram Int. 2023;49(11):19109–19123.
- Kubota A, Nagae S, Motoyama S, et al. Two-step polishing technique for single crystal diamond (100) substrate utilizing a chemical reaction with iron plate. Diamond Relat Mater. 2015;60:75–80.
- Wen H, Lu J, Li C, et al. Research on integrated processing of grinding and polishing for large-size single crystal diamond. J Synthetic Crystals. 2022;51(05):941–947.
- Liao MY, Shen B, Wang ZG. Ultra-wide bandgap semiconductor materials. Amsterdam, Netherlands: Elsevier; 2019.
- Zong WJ, Li D, Cheng K, et al. The material removal mechanism in mechanical lapping of diamond cutting tools. Int J Machine Tools & Manufacture. 2005;45(7-8):783–788.
- Ollison CD, Brown WD, Malshe AP, et al. A comparison of mechanical lapping versus chemical-assisted mechanical polishing and planarization of chemical vapor deposited (CVD) diamond. Diamond Relat Mater. 1999;8(6):1083–1090.
- Tang CJ, Neves AJ, Fernandes AJS, et al. A new elegant technique for polishing CVD diamond films. Diamond Relat Mater. 2003;12(8):1411–1416.
- Xu HQ, Zang JB, Tian PF, et al. Rapid grinding CVD diamond films using corundum grinding wheels containing iron. Int J Refractory Metals & Hard Materials. 2018;71:147–152.
- Tsai HY, Ting CJ, Chou CP. Evaluation research of polishing methods for large area diamond films produced by chemical vapor deposition. Diamond Relat Mater. 2007;16(2):253–261.
- Izak T, Kromka A, Babchenko O, et al. Comparative study on dry etching of polycrystalline diamond thin films. Vacuum. 2012;86(6):799–802.
- Zheng YT, Ye HT, Liu JL, et al. Surface morphology evolution of a polycrystalline diamond by inductively coupled plasma reactive ion etching (ICP-RIE). Mater Lett. 2019;253:276–280.
- Fu Y, Lu F, Wang J, et al. Polishing of thick free standing films by rare earth metals. Chinese High Technology Letters. 1996;(1):1–5.
- Tang FZ, Chen YQ, Zhang LC. Analysis of polished polycrystalline diamond using dual beam focused ion beam microscopy. Philos Mag. 2012;92(13):1680–1690.
- Ozkan AM, Malshe AP, Brown WD. Sequential multiple-laser-assisted polishing of free-standing CVD diamond substrates. Diamond Relat Mater. 1997;6(12):1789–1798.
- Leech PW, Reeves GK, Holland AS, et al. Ion beam etching of CVD diamond film in Ar, Ar/O-2 and Ar/CF4 gas mixtures. Diamond Relat Mater. 2002;11(3-6):833–836.
- Wu J, Ma Z-B, Shen W-L, et al. Influence of nitrogen in diamond films on plasma etching. Acta Phys Sin. 2013;62(7):075202.
- Weima JA, Fahrner WR, Zaitsev AM, et al. Surface characterization of thermochemically polished CVD diamond films. 3rd International Micro Materials Conference, Berlin, Germany, 2000, pp. 880–883.
- Liang YF, Zheng YT, Wei JJ, et al. Effect of grain boundary on polycrystalline diamond polishing by high-speed dynamic friction. Diamond Relat Mater. 2021;117:108461.
- Ogawa Y, Ota M, Nakamoto K, et al. A study on machining of binder-less polycrystalline diamond by femtosecond pulsed laser for fabrication of micro milling tools. Cirp Annals-Manufacturing Technol. 2016;65(1):245–248.
- Yoshida A, Deguchi M, Kitabatake M, et al. Atomic level smoothing of CVD diamond films by gas cluster ion beam etching, nuclear. Instruments & Methods in Physics Research Section B-Beam Interactions with Materials and Atoms. 1996;112(1-4):248–251.
- Mallik AK, Bhar R, Bysakh S. An effort in planarising microwave plasma CVD grown polycrystalline diamond (PCD) coated 4 in. Si wafers. Mater Sci Semicond Process. 2016;43:1–7.
- Zheng XF, Ma ZB, Zhang L, et al. Investigation on the etching of thick diamond film and etching asa pretreatment for mechanical polishing. Diamond Relat Mater. 2007;16(8):1500–1509.
- Sun Y, Wang S, Tian S, et al. A low-temperature polishing technique for CVD diamond films by Ce-Mn alloys. Rare Metal Mater Engin. 2007;36:892–895.
- Gogotsi Y, Baek C, Kirscht F. Raman microspectroscopy study of processing-induced phase transformations and residual stress in silicon. Semicond Sci Technol. 1999;14(10):936–944.
- Pei ZJ, Fisher GR, Liu J. Grinding of silicon wafers: a review from historical perspectives. Int J Machine Tools & Manufacture. 2008;48(12–13):1297–1307.
- Ali B, Litvinyuk IV, Rybachuk M. Femtosecond laser micromachining of diamond: current research status, applications and challenges. Carbon. 2021;179:209–226.
- Wei C, Ma YP, Han Y, et al. Study on femtosecond laser processing characteristics of nano-crystalline CVD diamond coating. Appl Sci-Basel. 2019;9(20):4273.
- Yan B, Chen N, He N, et al. Surface modeling and component analysis of picosecond laser ablation of CVD diamond. Diamond Relat Mater. 2021;111:108191.
- Toros A, Kiss M, Graziosi T, et al. Reactive ion etching of single crystal diamond by inductively coupled plasma: state of the art and catalog of recipes. Diamond Relat Mater. 2020;108:107839.
- Yuan Z, Jin Z, Wang K, et al. High-productivity ultraprecise polishing technique of CVD diamond film. Nanotechnol Precis Eng. 2011;9(5):451–458.
- Huang ST, Zhou L, Xu LF, et al. A super-high speed polishing technique for CVD diamond films. Diamond Relat Mater. 2010;19(10):1316–1323.
- Roy S, Balla VK, Mallik A, et al. A comprehensive study of mechanical and chemo-mechanical polishing of CVD diamond. International Conference on Functional Nanomaterials (IC-FNM), Howrah, India, 2016, pp. 9846–9854.
- Wang J, Wang J. Mechanical lapping thick CVD diamond films. J Wuhan Institute of Technol. 2005;27(5):39–41.
- Cheng CY, Tsai HY, Wu CH, et al. An oxidation enhanced mechanical polishing technique for CVD diamond films. Diamond Relat Mater. 2005;14(3–7):622–625.
- Kuhnle J, Weis O. Mechanochemical superpolishing of diamond using NaNO3 or KNO3 as oxidizing agents. Surf Sci. 1995;340(1–2):16–22.
- Weima JA, Zaitsev AM, Job R, et al. Investigation of non-diamond carbon phases and optical centers in thermochemically polished polycrystalline CVD diamond films. J Solid State Electrochem. 2000;4(8):425–434.
- Zhang H, Xu K, Yan Z, et al. Study on dynamic friction polishing of single crystal diamond. J Univ Chinese Acad Sci. 2023:78.
- Chen Y, Zhang LC, Arsecularatne JA. Polishing of polycrystalline diamond by the technique of dynamic friction. Part 2: material removal mechanism. Int J Mach Tools Manuf. 2007;47(10):1615–1624.
- Gloor S, Luthy W, Weber HP, et al. UV laser polishing of thick diamond films for IR windows. Appl Surf Sci. 1999;138–139:135–139.
- Chen C, Tsai H-L. Fundamental study of the bulge structure generated in laser polishing process. Opt Lasers Eng. 2018;107:54–61.
- Prieske M, Vollertsen F. Picosecond-laser polishing of CVD-diamond coatings without graphite formation. Mater Today: Proc. 2021;40:1–4.
- Grogan DF, Zhao T, Bovard BG, et al. Planarizing technique for ion-beam polishing of diamond films. Appl Opt. 1992;31(10):1483–1487.
- Hirata A, Tokura H, Yoshikawa M. Smoothing of chemically vapour deposited diamond films by ion beam irradiation. Thin Solid Films. 1992;212(1–2):43–48.
- Ilias S, Sene G, Moller P, et al. Planarization of diamond thin film surfaces by ion beam etching at grazing incidence angle. Diamond Relat Mater. 1996;5(6–8):835–839.
- Sirineni GMR, Naseem HA, Malshe AP, et al. Reactive ion etching of diamond as a means of enhancing chemically-assisted mechanical polishing efficiency. Diamond Relat Mater. 1997;6(8):952–958.
- Zhou L, Huang ST, Wang XL, et al. High-speed mechanical lapping of CVD diamond films using diamond wheel. Int J Refractory Metals & Hard Mater. 2012;35:185–190.
- Wang R, Chen N, Yan B, et al. Inert ambiance-assisted laser ablation of CVD diamond leads to enhanced surface quality and grindability. Ceram Int. 2023;49(1):1154–1164.