Abstract
Nanocomposite Si/SiOx powders were produced by plasma spray physical vapor deposition (PS-PVD) at a material throughput of 480 g h−1. The powders are fundamentally an aggregate of primary ∼20 nm particles, which are composed of a crystalline Si core and SiOx shell structure. This is made possible by complete evaporation of raw SiO powders and subsequent rapid condensation of high temperature SiOx vapors, followed by disproportionation reaction of nucleated SiOx nanoparticles. When CH4 was additionally introduced to the PS-PVD, the volume of the core Si increases while reducing potentially the SiOx shell thickness as a result of the enhanced SiO reduction, although an unfavorable SiC phase emerges when the C/Si molar ratio is greater than 1. As a result of the increased amount of Si active material and reduced source for irreversible capacity, half-cell batteries made of PS-PVD powders with C/Si = 0.25 have exhibited improved initial efficiency and maintenance of capacity as high as 1000 mAh g−1 after 100 cycles at the same time.
Introduction
Lithium ion batteries have already been used in various portable devices as high-density rechargeable energy sources. However, further increase in capacity is needed to meet demands from mobile vehicle industries. From a material point of view, especially for negative electrodes, Si is a promising candidate to replace the conventional graphite, as it possesses volumetric and gravimetric capacities that are nearly 10 times greater. However, this material is also known to experience a huge volume change of up to 400% associated with lithiation–delithiation reaction during the charge–discharge process. This causes pulverization of Si particles and loss of electric path within the electrode, which inevitably results in a capacity decay in short recharge cycles [Citation1]. Substantial research on this issue has identified that the structural control of Si anodes is effective in making the best of their high theoretical specific capacity, such as nanosized [Citation1, Citation2], porous [Citation3, Citation4], composite structure, and coating with electric conducting agents [Citation5].
SiO is also considered as a potential alternative to Si because batteries using SiO as a negative electrode generally attain a stable cycle capacity retention due mainly to its adaptable amorphous structure and also to the formation of Li2O that may act as buffer for dilation [Citation6]. In addition, this material is also known to transform into Si and SiO2 through disproportionation reaction [Citation7, Citation8]. This has been promisingly used as a host for the spontaneous composite structure having nanosized Si precipitates within the SiO2 matrix, proving its structural effectiveness, especially with the addition of the secondary element [Citation9, Citation10]. However, the inevitable formation of Li–O and Li–Si–O phases literally consumes lithium during lithiation as part of irreversible capacity [Citation11], which reduces the initial efficiency significantly. This is another major issue of this material, along with enhancement of the specific capacity itself.
Meanwhile, as an industrial-compatible approach that is capable of production of nanostructured powders at high throughputs, we have employed plasma spraying physical vapor deposition [Citation12]. Nanoparticles of several tens of nm in size were produced at >360 g h−1 from metallurgical-grade Si powders and the improvement in the specific capacity retention was confirmed for batteries with these powders as the negative electrode. The fundamental process in this approach is, in brief, characterized by evaporation of injected raw powders for formation of the vapor phase in the thermal plasma jet where the core temperature in general exceeds 10 000 K, and also by the consecutive rapid condensation of such high temperature Si vapors for nanoparticle formation in the low-temperature region of the jet tail. Even for nanoparticle production, the elemental physical process in the plasma is essentially similar to that for film deposition. This approach is therefore conventionally called plasma spray physical vapor deposition (PS-PVD) [Citation13].
If one uses SiO as feedstock for PS-PVD with an Ar + H2 plasma jet, reduction of SiO is expected to some extent, as has been demonstrated for the reduction of silicon oxide [Citation14–Citation17]. That is, the decrease in the oxygen content, x, in the raw Si1O x to less than 1 readily increases the relative number of Si atoms, which could contribute to an increase in the electric capacity by decreasing the irreversible capacity associated with Li–O formation. In addition, there would be technical advantage for this SiO and PS-PVD combination. According to the literature, SiO(s) sublimates at a temperature around 2200 K, lower than the 3500 K boiling point of Si, and the total energies required for formation of the vapor phase (SiO(g)) from solid SiO is estimated to be approximately 399 kJ mol−1, which is less than the total enthalpy of 523 kJ mol−1 required for evaporation of solid Si [Citation18]. This means that if one considers forming SiO vapor by complete decomposition of SiO powders, compared to the use of Si feedstock, less energy is required to produce the same amount of vapor, or a higher quantity of SiO vapor can be produced at a fixed input power to the plasma. Furthermore, the vapor pressure of SiO is roughly three orders of magnitude higher than that of Si at least at temperatures below 2000 K [Citation19, Citation20]. It is thus anticipated that if the grain growth after nucleation is effectively suppressed by introducing appropriate quenching, many smaller particles could form preferentially compared to the case of Si.
Introduction of the secondary element together with SiO powder into the plasma leads potentially to various gas phase formation and subsequent co-condensation to certain alloy phases. This suggests that the structure of the nanoparticles can be controlled topologically and compositionally by selection of the overall composition and the quenching protocol. Consider here the addition of CH4 together with SiO powder injection; the effectiveness of the addition of C to SiO for battery performance has been reported in [Citation5–Citation7]. Figures (a) and (b) compare the calculated equilibrium plasma chemistries in the Ar–H–O–Si and Ar–H–O–Si–C system with molar ratio corresponding to the actual PS-PVD condition shown in the following section. In this calculation, formation of molecular H2 is ignored since the amount of the atomic hydrogen is expected to be high in the thermal plasma jet [Citation21].
Figure 1 Calculated equilibrium chemistries in the (a) Ar–H–O–Si and (b) Ar–H–O–Si–C system under the conditions equivalent to the experiment shown in table .
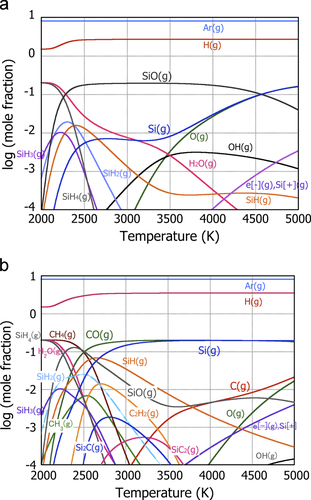
In the case of no CH4 addition (figure (a)), SiO vapor exists as the most stable Si-containing phase at temperatures ranging from 2500 K to ∼4500 K. Si(g) is the second stable phase in this temperature region but with its molar ratio smaller by one order of magnitude than SiO(g). This indicates that the SiO is not significantly reduced in the Ar and H2 environment, even with the preferential formation of atomic H. This contrasts with the case of CH4 addition (figure (b)). When CH4 is introduced at the relative molar ratio C/Si = 1, Si(g) becomes the most stable Si-containing phase instead, and SiO(g) is the third stable, due to high stability of CO(g) especially at high temperature. As such, addition of CH4 is effective at least in reducing x in SiO x at its vapor phase. However, it is also found that Si2C(g) and SiC2(g), the major species in SiC(s) formation, are formed together with various hydrocarbon molecules. Since SiC(s) is not the active material as anode, formation of SiC is favorably suppressed in order not to reduce the amount of Si active material. Phase equilibria therefore suggest that reduced SiO(s) and Si(s) could form as condensed phases by rapid quenching of these high-temperature CH4 added vapor mixtures. However, the amount needs to be optimized so as not to form SiC(s) and not to induce excessive reduction of SiO to make the most of the unique structural characteristics of SiO. Under such a condition, inclusion of free carbon in the PS-PVD powder is less likely.
In this work, we have therefore attempted PS-PVD starting with SiO raw powders to produce SiO nanocomposites and analyzed the capacity cycle performance of the batteries using these plasma-processed powders. The effect of CH4 addition to cycle performance is also discussed from a structural point of view.
Experimental
PS-PVD was carried out using a plasma spray system equipped with a dc-RF hybrid inductively coupled plasma torch. Details of this system can be found in [Citation22]. The reaction chamber was first evacuated to a base pressure of 10−2 Torr and then filled with Ar to a process pressure of 400 Torr. Plasma was generated with Ar and H2 gas at an input RF power of 90 kW and dc power of 8 kW. The metallurgical-grade raw SiO powders used were primarily amorphous as identified by the x-ray diffraction (XRD) pattern shown later in figure . Crushed raw SiO powders were first sieved to a mean diameter of 165 μm. These powders were fed from the top of the dc torch such that the powders passed through the highest temperature zone in the plasma jet preferentially. The powder feeding rate was adjusted to 8 g min−1 at the maximum, taking into account of the thermal load for the complete evaporation of the Si powders under the present plasma condition [Citation12]. CH4 gas was also introduced to the plasma from the top of the plasma torch to maintain overall C/Si molar ratios of 0.25, 1 and 1.5. The plasma jet was immediately quenched by placing a water-cooled vessel underneath the plasma flame. High-temperature Si vapors were thus condensed and the nucleated nanoparticles attached to the vessel wall were collected after the plasma was turned off. The conditions of PS-PVD are listed in detail in table . These powders were characterized by static laser light scattering (wavelength 375 nm) for particle size distribution, XRD for identification and quantitative analysis of existing phases, and field emission scanning electron microscopy (FE-SEM), high resolution transmission electron microscopy (HR-TEM) and scanning TEM (STEM) with electron energy loss spectroscopy (EELS) for particle structural analysis.
Table 1. List of the plasma spray conditions.
These PS-PVD powders were ground by pestle and then sieved to cut off particles larger than 40 μm. In order to understand the effect of the different PS-PVD powders on battery performance, all the PS-PVD powders with different C/Si ratios were mixed identically with a binder and carbon black powders at a fixed amount; Si active material : conducting carbon : binder = 60 : 15 : 25. The slurry was applied to Cu foil to a thickness of 75 μm, which was further reduced to 21 μm after being oven-dried under ambient conditions. Using this as anode, half coin cells were assembled in a globe box filled with Ar, together with lithium metal as the counter electrode and 1 M LiPF6 dissolved with ethylene carbonate and diethyl carbonate (1:1 vol.%) as the electrolyte. The test cell was charged at a constant current of 0.1 mA for the first three cycles and at 0.5 mA for the rest of the cycles, which roughly correspond to 0.02 C and 0.1 C, respectively. All the tests were conducted at a controlled temperature of 23 °C.
Results and discussion
PS-PVD powder characteristics
Figure shows the FE-SEM image of (a) raw SiO powder, (b) PS-PVD and (c) its magnified image. It is seen that the raw powders are several hundred micrometers in size and have rather sharp surfaces. Once they are processed by PS-PVD, the particles are changed to fine particles, far smaller than the raw particles, although some of them are agglomerated. From the magnified image of figure (c), the particles are found to have an agglomerated structure 100 nm in size on average, and further are composed of particles as small as several tens of nanometers. Fundamentally similar powder appearance was observed also for the powders with different C/Si ratios. This clearly indicates that the particles are produced through evaporation and condensation by PS-PVD.
Figure 2 FE-SEM images of the raw SiO (a), plasma sprayed (PS-PVD) powder with CH4 addition (C/Si = 1) (b) and its higher magnitudes (c).
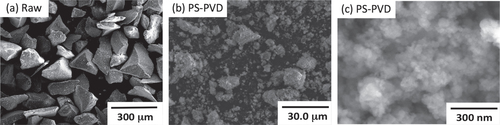
Figure shows the size distribution of these powders (frequency in the volume) analyzed by static laser light scattering, assuming a constant refractive index of 2.15-0.2i for SiO. It is clearly seen that once the powders are processed by PS-PVD, all exhibit a similarly broad-sized distribution ranging from 0.1 to 10 μm. This confirms that the particles are composed fundamentally of variously sized agglomerates; the size decreases slightly on CH4 addition although there is no significant effect for the different C/Si ratios.
Figure 3 Comparison of the particle size distribution of the PS-PVD powders between the powders produced with different CH4 additions (volumetric frequency basis).
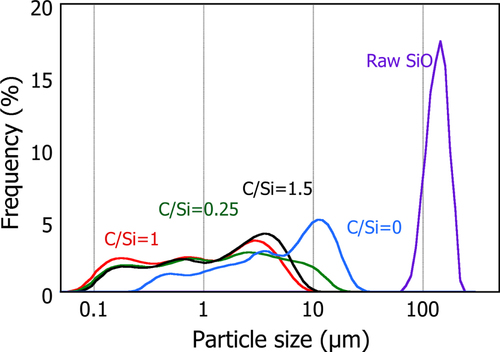
Figure shows HR-TEM images of the PS-PVD powders with (a) C/Si = 0 and (b) C/Si = 0.25. For both powders with and without CH4, the primary particle is seen to be around 10–20 nm on average and a crystalline lattice structure 5–15 nm in size exists within the amorphous particle. Such core–shell particles can be found in places over a wider region too. When CH4 was added, the size of the core crystalline region seems to become large and also these core–shell particles are observed more frequently in the image, as indicated by the dotted red circles.
Figure 4 HR-TEM images of the PS-PVD SiO powders processed (a) without and (b) with 1.1 slm CH4 gas addition.
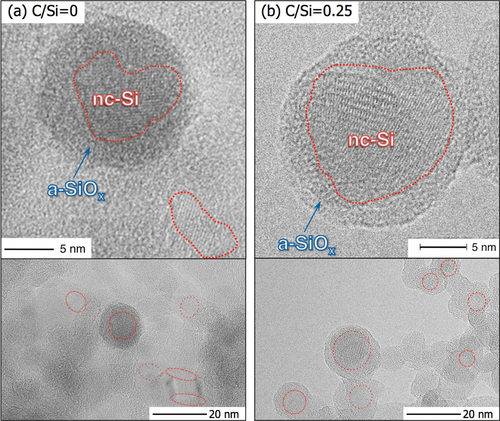
The EEL spectra of the Si–L edge at different positions within the particles for C/Si = 0 and 0.25 was then analyzed, as shown in figure . The position of the EELS measurement is indicated in the STEM high-angle annular dark field (HAADF) image. For both PS-PVD powders, the spectrum at the center of the particle (#3 for C/Si = 0 and #4 for C/Si = 0.25) shows the first peak with the edge onset near 99 eV that is characteristic of the crystalline Si. As the position gets closer to the edge of the particle, the secondary peak near 110 eV becomes strong while the first peak becomes small; the EELS at the edge (#1) then resembles that of SiO2. Although the EELS spectrum of SiO is reported to be similar to that of a mixture of Si and SiO2 [Citation8], for both PS-PVD powders, the center of the particle is highly likely to be crystalline Si and it is surrounded by a SiO x shell where the oxygen content, x, increases towards the outer region of the shell. Precipitation of Si within amorphous SiOx(a-SiOx) matrix is a characteristic structure of SiO after disproportionation reaction. Therefore, it is reasonable to consider that the core Si with SiOx shell structure is produced by the disproportionation reaction of the SiO nanoparticle. This in turn suggests that, during PS-PVD, the SiOx vapor condenses first to form SiOx nanoparticles at around 2000 °C near the sublimation temperature of SiOx and these particles are then subject to disproportionation reaction at lower temperatures despite the total millisecond reaction time within the plasma jet.
Figure 5 Change in the EEL spectra of the Si–L edge within the SiOx particle of the PS-PVD powders processed with and without CH4 gas addition. The positions of the EELS analysis are indicated in the STAM HAADF images.
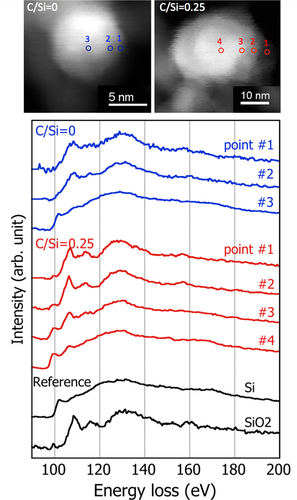
The XRD patterns of the PS-PVD powders with different C/Si ratios are summarized in figure . The raw SiO is seen to have only a broad peak at around 20–30° with no appreciable peak of crystalline Si (c-Si), suggesting that the raw powders are amorphous SiO x and not a mixture of crystalline Si and SiO2. Once this powder was processed by PS-PVD (with no CH4), the crystalline Si peaks are clearly detected, while the broad peak is also still observed. Even when CH4 was added at C/Si = 0.25, the pattern of the peaks is not significantly changed except for a slight increase in the Si intensity relative to the SiO x broad peak. At C/Si = 1, the broad peak associated with SiOx becomes small and the 3C-SiC peak emerges instead, and this tendency becomes significant as C/Si increases to 1.5. Therefore, addition of CH4 up to C/Si = 0.25 produces solely the nanocrystalline-Si(nc-Si)/a-SiO x core–shell powders, in which the oxygen is effectively removed, whereas further increase in CH4 produces a mixture of core–shell nc-Si/SiOx, and individual nc-Si and 3C-SiC powders.
The mass fraction of the existing phases, nc-Si, a-SiOx and 3C-SiC, was quantified by Rietveld analysis of the XRD patterns using the commercial software TOPAS, as listed in table . The goodness-of-fit indicator, S, for all the analyses was in the range between 1.14 and 1.38, which is considered to be mostly within the reasonable fitting range [Citation23]. The PS-PVD powder with C/Si = 0 is estimated to include nc-Si at 8.6 wt% in the powder mixture and its average size to be 15 nm. For the powder with C/Si = 0.25, the total amount of nc-Si is estimated to be 30 wt%, in which nc-Si particles of 7 nm and 29 nm average size are present as the majority in nearly equal quantity. With further increase in the C/Si ratio, nc-Si becomes as the major phase instead of SiO x in the powder mixture. The tendency of the nc-Si size and its fraction estimated by XRD seems to be roughly in agreement with that observed locally in the TEM image shown in figure . Considering that reduction of SiO x proceeds primarily in its vapor phase prior to condensation, the oxygen content of the overall composition is estimated as x in SiOx, by summation of the mass fraction of all the phases, to be 0.87, 0.58 and 0.31 for the C/Si = 0, 0.25 and 1, respectively. It is thus clear that the combination of plasma and CH4 addition promotes reduction significantly.
Table 2. Relative amount (wt%) of phases present in the PS-PVD powder mixture, estimated by Rietveld analysis of the XRD patterns shown in figure .
Furthermore, for the case of C/Si = 0.25, given that all the nc-Si composes the core–shell particle (having a 15 nm core in a 20 nm particle, as observed in the TEM image shown in figure (b)) and also that there are no individual nc-Si particles, 28 wt% of the particle mixture is estimated to be individual a-SiO particles. On the other hand, for the powders with C/Si = 1, the SiO reduction is considered to proceed excessively such that CH4 interacts not only with oxygen but also with Si atoms to form SiC. In this case, suppose that all the a-SiOx are at the shell of the core–shell particle (with the same dimensions described above): 20.6 wt% of the powder mixture is estimated to be individual nc-Si particles with no SiOx shell structure.
Battery performance
Figure compares the initial capacity change with voltage for the batteries using PS-PVD powders with different C/Si ratios. It is seen that the maximum charged capacity changes with C/Si: the batteries with C/Si = 0.25 and 1 have a relatively high capacity of ∼3000 mAh g−1, while the cells with C/Si = 0 and 1.5 attain 2000 mAh g−1, which is smaller than that with the raw SiO. Discharged capacity also shows a similar tendency with the C/Si ratio. That is, the cells with C/Si = 0.25 and 1 attain a relatively large capacity whereas the cells with C/Si = 0 and 1.5 return Li less compared to that with raw SiO. As a result, the initial efficiency, the amount of the discharged capacity relative to the charged capacity, decreased from 58% to 53% by employing PS-PVD (C/Si = 0) as compared to the case of the raw SiO. Since the PS-PVD powders are composed of nanosized particles with a greater specific surface area than that of the raw SiO, the irreversible phase formation on surfaces may inevitably increase. However, as the PV-PVD particle is nc-Si/a-SiO x (x ∼ 2) core–shell structured because of the SiOx reduction and disproportionation reaction, the overall Li consumed for formation of the irreversible phases can be reduced. Furthermore, lithium silicate, such as Li4SiO4, could form around the core nc-Si upon the initial lithiation as Li diffuses from the outer shell of the particle. The stable Li4SiO4 phase expands only 200% upon the full lithiation of SiO [Citation24], which potentially hinders the expansion of the nc-Si up to a maximum ∼400%, resulting in the reduced charged capacity and so the discharged capacity.
Figure 7 Change in the initial capacity with voltage for the PS-PVD powders with different C/Si ratios. The battery was charged at a constant current of 0.1 mA, and the cut-off voltage was set to 0 V. The initial efficiency (%) is shown next to the C/Si.
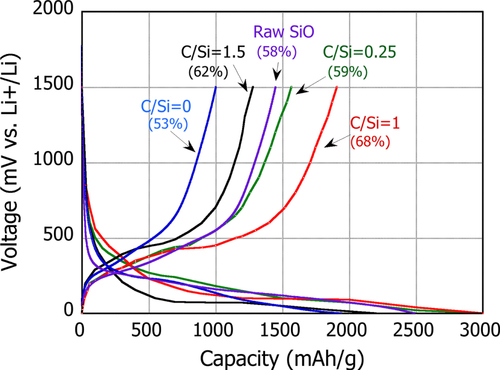
Once the SiOx reduction is promoted by the CH4 addition, as the relative volume of the core nc-Si is increased whereas that of the shell a-SiOx is reduced as listed in table , the charged capacity could be greater than that of the raw SiO and conversely the discharge capacity can be reduced because of the decreased SEI amount. In fact, when CH4 was added at C/Si = 0.25 or 1, the initial capacity efficiency was improved appreciably to 59% and 68%, respectively, despite nanosized particles. However, if the C/Si ratio further increases to 1.5, although the initial capacity is improved from the raw SiO battery, the charged capacity is essentially reduced because of the increase in the inactive SiC particle in the PS-PVD powder mixture. These results therefore confirm that the addition of CH4 needs to be optimized to attain high initial efficiency, based on the balance between promotion of SiO reduction and suppression of SiC formation.
The capacities retained at longer cycles are shown in figure , comparing these cells with different C/Si ratios. (The capacity shows rather noisy behavior with cycles, because roll-press was not applied during anode preparation. Also, as a general tendency for all the cells, the capacity is seen to drop rather significantly for the first several cycles before exhibiting less steep behavior afterwards. This may be associated with the various sized PS-PVD particles, as shown in figure . Therefore, it is likely that several cycles are required for all particle surfaces to be wetted by the electrolyte neatly and attain stable surfaces. Nevertheless, the difference in the tendency of the cycle performance is clearly distinguished.)
Figure 8 Capacity change with number of cycle for PS-PVD powders processed with different CH4 gas additions. The battery was charged at a constant current of 0.1 mA for the first three cycles and at 0.5 mA for the rest of the cycles.
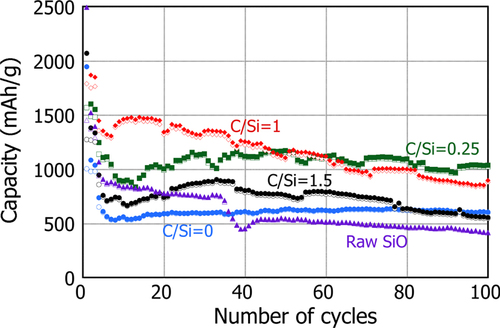
It is seen as a benchmark of this series that the cell with raw SiO shows a gradual decay from 1000 mAh g−1 at the 5th cycle to 400 mAh g−1 after 100 cycles. However, once the powder was plasma processed only (C/Si = 0), the capacity was reasonably well retained at least up to 100 cycles, although the initial capacity efficiency was reduced. When CH4 was added at C/Si = 0.25, the capacity increased to greater than 1000 mAh g−1 on average and it was somewhat maintained for 100 cycles. In contrast, for the case of C/Si = 1, the capacity was increased to an even higher value of ∼1500 mAh g−1 after the initial drop. However, it decays gradually with cycles even faster than the C/Si = 0.25. With further increase in the C/Si to 1.5, the capacity after the initial drop is reduced further to less than 1000 mAh g−1 and it also exhibits a gradual tendency to decrease. The coulombic efficiency of these batteries, shown in figure , is also classified similarly. The batteries with raw SiO and PS-PVD with C/Si = 0 and 0.25 attain an efficiency of around 99%, whereas a decrease in efficiency was apparent when CH4 was introduced at C/Si = 1 and 1.5. As described in the previous section, the reduction of SiO in the powders with C/Si = 1 and 1.5 is potentially significant so that individual nc-Si particles with no a-SiO x shell structure are additionally formed. Therefore, these batteries exhibit appreciable tendency for decreasing capacity that is commonly observed for the battery with Si particles. The difference in capacity between C/Si = 1 and 1.5 can be reasonably explained by the difference in the amount of SiC, i.e., the active Si particle, included in each powder mixture. In contrast to these, since no individual nc-Si particle is expected in the PS-PVD powder mixture with C/Si = 0 and 0.25, the coulombic efficiency can be kept high due to the presence of a-SiO x .
Figure 9 Coulombic efficiency change with cycle for the PS-PVD powders processed with different CH4 gas additions.
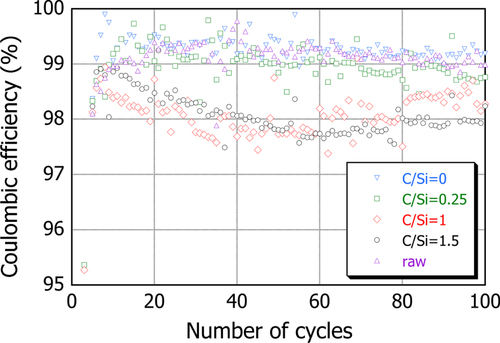
Figure compares the differential capacity of these batteries. As a general tendency, although the peaks are observed at different voltages between batteries in the first cycle, each peak for all the batteries is found at roughly the same voltage after 100 cycles. This suggests that the structure of the pristine anode is different but it becomes fundamentally similar after cycling in terms of the electrochemical reaction.
Figure 10 Change in the differential capacity with voltage for the PS-PVD powders processed with different CH4 gas additions at the 1st cycle. Inset: at the 100th cycle.
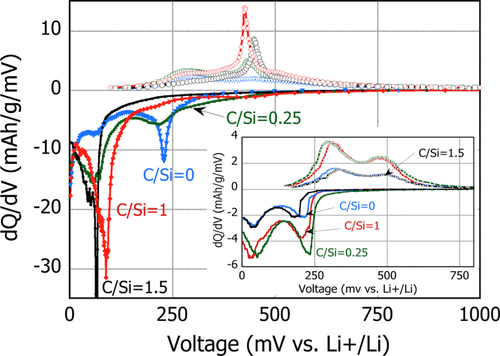
During the first lithiation, the peaks are observed at 240 mV only in the cell with C/Si = 0 and 0.25, and the peak intensity for C/Si = 0 is greater than that of C/Si = 0.25. The peak appearing at this voltage is reportedly ascribed to the formation of amorphous Si–Li alloy [Citation25, Citation26]. In fact, the a-SiO x is confirmed as the major phase in these powders, and the relative amount of this phase is higher in the C/Si = 0 powder, as qualitatively listed in table . Therefore, this attests to the formation of amorphous Si–Li–O phase, such as Li4SiO4 from a-SiOx, that contributes to the initial capacity in these powders. As lithiation proceeds, another major peak is observed at around 90 mV for all the specimens. It is a strong and major peak for C/Si = 1 and 1.5, a second peak with an intermediate intensity for C/Si = 0.25, and a quite small peak for C/Si = 0. The peak at this voltage range is commonly observed at the initial stage of the cycles for the battery using nc-Si, and is attributed to the formation of the crystalline Li–Si alloy phase. Again, the difference in this peak intensity between C/Si ratios is at least qualitatively in agreement with the relative amount of nc-Si in these powders, as listed in table . Therefore, this suggests that there is a large contribution of this reaction from individual nc-Si particles to the initial capacity for the batteries with C/Si = 1 and 1.5, but a limited contribution of this reaction for C/Si = 0 and 0.25.
After 100 cycles, all of the cells show similar peaks at 240 mV and 90 mV. The peak intensity of the cell with C/Si = 0 decreases significantly, possibly because of the initial irreversible capacity loss associated with the a-SiO x particles. Meanwhile, it is interesting to note that the intensity of the peak at 240 mV for the cells with C/Si = 0.25 seems to be maintained although a certain amount of individual a-SiO x particles is also expected in this powder mixture. This suggests that the nc-Si at the core of the composite particles changes into amorphous Si (a-Si) after several cycles and contributes to an increase in the intensity at 240 mV constantly. In contrast, for the batteries with C/Si = 1 and 1.5, a peak emerged at 240 mV and the peak around 100 mV is significantly decreased after 100 cycles. This is an indication that some of the individual nc-Si particles in the pristine powder are changed into a-Si during the cycles. However, the coulombic efficiency of these powders is found to be less than that of C/Si = 0.25. These results suggest that although the individual nc-Si particle with no SiOx shell is less stable even after the structural change from crystalline into amorphous, if nc-Si is surrounded by the SiOx to form a core–shell structure, they are anticipated to be reasonably stable in maintaining their structure and thus retaining capacity. This is probably because the Li–O alloy phase acts as buffer as reported [Citation6], and also because the a-SiOx shell changes into Si–Li–O during lithiation and provides an electrically conducting web connecting directly the nc-Si particles [Citation27].
Conclusion
Production of nanosized Si/SiOx composite powders has been demonstrated at throughputs of 480 g h−1 by plasma spray physical vapor deposition (PS-PVD) using SiO powders as feedstock. Reduction and disproportionation reaction of SiO can be undertaken during a single continuous process of nanoparticle production and nc-Si/a-SiOx core–shell composite particles are produced. Addition of CH4 to PS-PVD promotes SiO reduction and thereby increases the volume of the core nc-Si and decreases the SiOx shell thickness, although the excessive CH4 addition with C/Si molar ratio >1 results in the formation of nc-Si with no shell and also the SiC phase particle. The amount of CH4 addition at C/Si = 0.25 seems to be in the optimal range to produce an enlarged nc-Si core with a reduced SiOx shell while suppressing inactive SiC formation. As a result of the increased amount of active Si and reduced source for irreversible capacity, this composite structure was shown to improve the initial efficiency and maintain high capacity for longer cycles at the same time.
Acknowledgement
This work is partly supported by the Funding Program for Next Generation World-Leading Researchers (NEXT Program) of Japan.
References
- LiuX HZhongLHuangSMaoS XZhuTHuangJ Y 2012 ACS Nano 6 1522 1531 1522–31 10.1021/nn300436b
- GraetzJAhnC CYazamiRFultzB 2003 Electrochem. Solid-State Lett. 6 A194 A197 A194–7 10.1149/1.1596917
- ChanC KPengHLiuGMcIlwrathKZhangX FHugginsR ACuiY 2008 Nat. Nanotechnology 3 31 35 31–5 10.1038/nnano.2007.411
- MagasinskiADixonPHertzbergBKvitAAyalaJYushinG 2010 Nat. Mater. 9 353 358 353–8 10.1038/nmat2725
- NgS-HWangJWexlerDKonstantinovKGuoZ-PLiuH-K 2006 Angew. Chem. Int. Ed. 45 6896 6899 6896–9 10.1002/(ISSN)1521-3773
- DohC-HShinH-MKimD-HHaY-CJinB-SKimH-SmoonS-IVeluchamyA 2008 Electrochem. Commun. 10 233 237 233–7 10.1016/j.elecom.2007.11.034
- MamiyaMTakeiHKikuchiMUyedaC 2001 J. Cryst. Growth 229 457 461 457–61 10.1016/S0022-0248(01)01202-7
- WangJWangX FLiQHryciwAMeldrumA 2007 Philos. Mag. 87 11 27 11–27 10.1080/14786430600863047
- ParkC-MChoiWHwaYKimJ-HJeongGSohnH-J 2010 J. Mater. Chem. 20 4854 4860 4854–60 10.1039/b923926j
- KimJ-HSohnH-JKimHJeongGChoiW 2007 J. Power Sources 170 456 459 456–9 10.1016/j.jpowsour.2007.03.081
- MiyachiMYamamotoHKawaiHOhtaTShirakataM 2005 J. Electrochem. Soc. 152 A2089 A2091 A2089–91 10.1149/1.2013210
- KambaraMHideshimaTHommaKKagaMSheemK-YIshidaSYoshidaT 2014 J. Appl. Phys. 115 143302 10.1063/1.4870600
- YoshidaT 1994 Pure Appl. Chem. 66 1223 1230 1223–30 10.1351/pac199466061223
- BibikovM BDemkinS AZhivotovV KZaitsevS AMoskovskiiA SSmirnovR VFateevV N 2010 High Energy Chem. 44 58 62 58–62 10.1134/S0018143910010091
- ColdwellD MRoquesR A 1977 J. Electrochem. Soc. 124 168 169 168–9 10.1149/1.2133137
- HuczkoAMeubusP 1989 Plasma Chem. Plasma Process 9 371 386 371–86 10.1007/BF01083673
- MexmainJ MMorvanDBourdinEAmourouxJFauchaisP 1983 Plasma Chem. Plasma Process 3 393 420 393–420 10.1007/BF00564627
- SchnurreS MGrobnerJSchmid-FetzerR 2004 J. Non-Cryst. Solids 336 1 25 1–25 10.1016/j.jnoncrysol.2003.12.057
- FergusonF TNuthJ A III 2008 J. Chem. Eng. Data 53 2824 2832 2824–32 10.1021/je800560b
- MargraveJ L 1967 The Characterization of High-Temperature Vapors New York Wiley
- TakamuraYHayashiKTerashimaKYoshidaT 1996 Plasma Chem. Plasma Process 16 S141 S156 S141–56 10.1007/BF01512632
- HuangHEguchiKKambaraMYoshidaT 2006 J. Thermal Spray Technol. 15 83 91 83–91 10.1361/105996306X92640
- YoungR A 1993 The Rietveld Method Oxford Oxford University Press
- WeastR C 1992 Handbook of Chemistry and Physics 73rd edn Boca Raton, FL CRC
- KangKLeeH-SHanD-WKimG-SLeeDLeeGKangY MJoM H 2010 Appl. Phys. Lett. 96 053110 10.1063/1.3299006
- KagaMHideshimaTKambaraM 2014 JPS Conf. Proc. 1 015073 10.7566/jpscp.1.015073
- KambaraMOdaNHommaK 2014 submitted