ABSTRACT
Heterostructured materials are an emerging class of materials with superior performances that are unattainable by their conventional homogeneous counterparts. They consist of heterogeneous zones with dramatic (>100%) variations in mechanical and/or physical properties. The interaction in these hetero-zones produces a synergistic effect where the integrated property exceeds the prediction by the rule-of-mixtures. The heterostructured materials field explores heterostructures to control defect distributions, long-range internal stresses, and nonlinear inter-zone interactions for unprecedented performances. This paper is aimed to provide perspectives on this novel field, describe the state-of-the-art of heterostructured materials, and identify and discuss key issues that deserve additional studies.
IMPACT STATEMENT
This paper delineates heterostructured materials, which are emerging as a new class of materials with unprecedented properties, new materials science and economic industrial production.
GRAPHICAL ABSTRACT
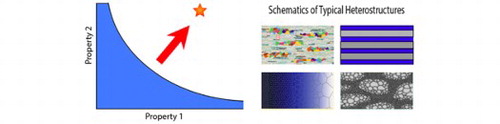
Acknowledgements
The authors wish to thank Prof. David Embury for his insightful and constructive comments and suggestions on the elastoplastic deformation of heterostructured materials. YTZ acknowledge the support by the National Key R&D Program of China (2017YFA0204403), the National Natural Science Foundation of China (51931003); KA acknowledges the support by the Japan Society for the Promotion of Science (JSPS) Grant-in-Aid for Scientific Research (S) JP18H05256; PMA acknowledges support by the US Department of Energy, Office of Basic Energy Sciences under grant number DE-SC0001258; IJB acknowledges financial support from the National Science Foundation (NSF CMMI-1728224); HG acknowledges support by the National Science Foundation through grant DMR-1709318; HSK was supported by the National Research Foundation of Korea (NRF) grant funded by the Korea government (MSIP) (NRF-2017R1A2A1A17069427); SNM acknowledges support from the U.S. National Science Foundation CMMI (grants 1554632, 1150986, and 1463679), and the Laboratory Directed Research and Development program at Pacific Northwest National Laboratory (PNNL) as part of the Solid Phase Processing Science initiative; ROR acknowledges support from the Director, Office of Science, Office of Basic Energy Sciences, Materials Sciences and Engineering Division, of the U.S. Department of Energy (Contract No. DE-AC02-05-CH11231). NT was supported by the Grant-in-Aid for Scientific Research (A) (No. 20H00306) from Japan Society for Promotion of Science (JSPS), and JST-CREST (No. JPMJCR1994) from Japan Science and Technology Agency (JST). XYZ acknowledges the support by the National Natural Science Foundation of China (51931007, 51971196). XLW was funded by the Ministry of Science and Technology, PR China, 2017YFA02044-01/-02/-03, the NSFC Basic Science Center Program for ‘Multiscale Problems in Nonlinear Mechanics’ (grant number 11988102), the NSFC (Grant Nos. 11972350), and the CAS (grant number XDB22040503).
Disclosure statement
No potential conflict of interest was reported by the author(s).