Figures & data
Table 1. An overview of the state-of-art related researches
Table 2. Summary of recent studies in underactuated robot
Figure 2. Model of inverted pendulum (a) stable position, (b) marginal position, (c) impact position.
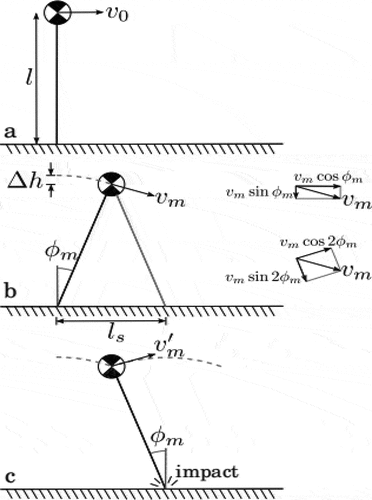
Table 3. List of dimensional values for wheel-legged mechanism
Figure 12. 3D model of hybrid mechanism, (a) component assembly, (b) motion state in wheel mode and (c) motion state in leg mode.
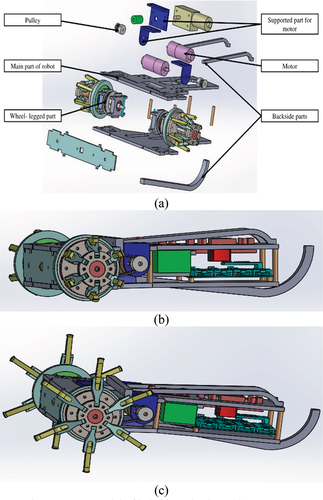
Table