ABSTRACT
Biodegradable blends of kefiran with various contents (10–40 wt%) of waterborne polyurethane were successfully synthesized via the casting method. When waterborne polyurethane content is lower than 30 wt%, good compatibility and miscibility were observed; otherwise, phase separation occurs between them. These phenomena can be attributed to intermolecular interactions, which were confirmed by Fourier transform infrared, X-ray diffraction, differential scanning calorimetry analysis, and scanning electron microscopy. Compared with kefiran film, the blends increased in thickness, tensile strength, elongation at break, yellowness, and opacity when the waterborne polyurethane content was increased. Meanwhile, the water vapor permeability and moisture absorption significantly decreased (p < 0.05).
Introduction
The popularity of synthetic polymeric films is on the rise because of various features such as softness, transparency, and lightness. However, concern has recently been voiced, since petroleum is a non-renewable source and can irreparably cause major environmental issues.[Citation1] Many scholars attempt to overcome such challenges through biodegradable and natural alternatives to petrochemical-based materials. Kefiran as an exocellular polysaccharide synthesized by lactic acid bacteria (LAB) can be used as biopolymer films to regulate the transfer of gas, aroma, flavor, and oils in a food system and to increase the shelf life and quality of food products.[Citation1,Citation2]
Kefiran is a secondary metabolite that can be obtained from the microbial flora of kefir grains of deproteinized whey at high yields.[Citation2] This heteropolysaccharide has water-soluble properties, containing branched hexa- or hepta-saccharide repeating units (i.e. D-glucose and D-galactose in a molar ratio of 0.94:1.1).[Citation3] Kefiran can improve the rheological features and, similar to most of the polysaccharides-based films, is edible and transparent, with a pleasing appearance.[Citation1] Moreover, it shows antitumor, antibacterial activities, and therapeutic benefits like modulating the gut immune system.[Citation3]
On the other hand, this filmognic material has poor mechanical characteristics when compared to synthetic polymers. In addition, its hydrophilic nature causes sensitivity to water and increases water vapor permeability. Several methods have been investigated to overcome such challenges, one of which develops a mixture of biopolymers (starch, whey protein, and chitosan) and synthetic polymers.[Citation4,Citation5] Polyurethane (PU)—as a unique synthetic polymer—possesses a wide range of physical and chemical properties from a high-performance elastomer to a tough thermoplastic polymer.[Citation6] The reaction of a diisocyanate, either aliphatic or aromatic, with a polyol (i.e. polyester or polyether) forms polyurethanes.[Citation7] Owing to environmental and health concerns of organic solvent-borne PU, low-cost and environmentally friendly waterborne polyurethane (WPU)[Citation8] has been developed to provide most of the features of solvent-borne ones with advantages of non-toxicity, good compatibility, and low viscosity at high molecular weight.[Citation9] More to the point, WPU films present superior mechanical properties, non-flammability, and low water uptake.[Citation10]
The aim of this study was to improve the drawbacks of low-cost kefiran film which can be obtained from the kefir grains of deproteinized whey at high yields. To overcome such challenges, mixtures of biopolymers and synthetic polymers have been developed. Among synthetic polymers we have chosen low-cost and environmentally friendly waterborne polyurethane. This method has been successfully used in previous studies by blending starch[Citation11], soy protein isolate[Citation10], soy meal protein[Citation12], lignin[Citation13], alginate[Citation14], casein[Citation15], and guar gum[Citation16] with WPU. To the best of our knowledge, there is no reported study aimed at applying WPU as a method for improving the water vapor permeability and mechanical properties of kefiran films. In the present study, a blend of kefiran and WPU was prepared with polyester as the soft segment on account of greater susceptibility to biodegradation, higher thermal stability, and stronger mechanical properties.[Citation10] A series of blend films of kefiran/WPU with WPU content—ranging from 10 to 40 wt%—was made by casting-evaporation methods. The physicochemical and mechanical properties of the blends with different WPU contents were investigated well. In detail: to determine the microstructural characteristics of the resultant films, using different methodologies like FTIR spectroscopy, scanning electron microscopy (SEM), differential scanning calorimetry (DSC), and X-ray diffraction (XRD), and to discuss the possibility of applications as packaging material in the food industry.
Materials and methods
Materials
Kefir grains were purchased from a household in Tehran, Iran. Analytical grade chemicals including isophorone diisocyanate (IPDI), polycaprolactone (PCL) (Capa 225), dimethylolpropionic acid (DMPA), triethylamine (TEA), 1, 4-Butanediol, ethanol, glycerol (99.5% purity), calcium chloride, calcium nitrite, calcium sulphate, and sodium chloride were purchased from Sigma-Aldrich Chemical Company.
Isolation and purification of kefiran
Kefir grains were maintained in skimmed milk at ambient temperature (20–22°C). The culture medium was replaced every day to retain the viability of the grains. After seven days, when their growth diameter reached 2 cm, the grains were considered active. For extraction and purification of exopolysaccharides, kefir grains were initially dissolved in boiling water (in a weight ratio of 1:10) for 30 min. Thereafter, the mixture was centrifuged at 10,000 g for 30 min and decanted from the undissolved portion. An equal amount of chilled ethanol was subsequently mixed to precipitate the polysaccharides and kept at −18°C for 24 h. In order to collect the pellets, the mixture underwent another centrifugation at 1000 g for 30 min at 4°C. The precipitates were rinsed with water three times to remove impurities. At the end of this process, the obtained white curds polysaccharide was known as kefiran. The phenol-sulfuric method was performed to determine the total polysaccharide in kefiran.[Citation4]
Synthesis of WPU dispersion
As for the synthesis of WPU, IPDI (4.03 g) and PCL (12.5 g) were charged into a four-necked flask equipped with a mechanical stirrer, condenser, nitrogen inlet, and thermometer. The reaction occurred at 90°C under a nitrogen atmosphere while being stirred vigorously for 3 h. DMPA (1.02 g) was added to the mixture as an emulsifier and then stirred at 200 rpm and 70°C for 30 min. To neutralize the carboxylic group in DMPA and expand the polymer chain, 0.5 g of TEA and 40 mL of butanediol were respectively added to the mixture. A 40 mL of deionized water was added under vigorous stirring at 900 rpm to yield WPU dispersions.
Preparation of kefiran/WPU blend films
An aqueous solution containing 2 wt% of kefiran was prepared under stirring condition to obtain a homogenous solution. A 35 wt% of glycerol was incorporated into the kefiran solution as plasticizer to achieve more flexible films. Afterward, WPU dispersions were mixed with the kefiran solution in different ratios and then stirred for 2 h. The mixture was cast into a Teflon mold and dried in an oven at 50°C and 50% relative humidity overnight. A series of kefiran/WPU blend films was prepared through changes in the WPU content 0, 10, 20, 30, 40, and 100 wt%, films coded respectively as K, KPU10, KPU20, KPU30, KPU40, and WPU. The conditioning films were obtained by using a desiccator containing calcium nitrite solution at ambient temperature for a week to ensure a relative humidity of 55%. These then underwent various characterizations.
Characterization
Fourier transform infrared
The FTIR analysis of the films was performed at ambient temperature by applying a Thermo Nicolet FTIR spectrometer (Nexus 870, United States) to determine the chemical structure of the films. Over 16 scans with a resolution of 4 cm−1 were carried out to obtain the spectra at 400–4000 cm−1.
X-ray diffraction analysis
The X-ray diffraction (XRD) patterns of the study samples were recorded at room temperature over a diffraction angle (2θ) of 5–40° with a scanning rate of 0.02°/min. The Cu Kα radiation (λ = 0.15418 nm) was produced at 40 kV and 30 mA using a XRD 3003 PTS (Seifert, Germany). The average crystallite size of the polymer specimens was calculated in accordance with Scherrer’s Equation (1):
where D is the crystallite size, is the diffraction angle for the first peak, and
is the full width at half maximum of the most intense diffraction peak.
Differential scanning calorimetry
The thermal features of the films were analyzed by means of a DSC SETARAM 131 apparatus (France) based on ASTM standard method D 3418–08. Purge gas was nitrogen at a flow rate of 20 mL/min. Each film (10 mg) was cut and put into a pan. An empty aluminum pan was served as the reference sample. The specimens were subsequently scanned three times at a temperature of −20–100°C and a heating rate of 10°C/min. The glass transition temperatures (Tg) of the samples were measured at the half-variation in heat capacity occurring at the glass-rubber transition.
Scanning electron microscopy
The microstructure and morphology of the films were investigated with a field emission scanning electron microscopy (FE-SEM; KYKY-EM3200 model, China). Examinations were conducted by using an accelerating beam at 15 kV. For observing the cross-section of the films, specimens were cryofractured by immersion in liquid nitrogen. All films were initially sputtered with a thin layer of gold, employing a KYKY-SBC-12 sputter coater (KYKY, China).
Thickness
The thickness of each film was randomly measured by a digital micrometer at 10 different points to the nearest 0.001 mm. The average values were calculated and used in further tests on water vapor permeability (WVP) and mechanical properties.
Water vapor permeability
The films’ WVP was gravimetrically investigated by the cup method[Citation17] with minor modification at 25°C and 50% RH gradient. Firstly, every film was conditioned in a desiccator at 25°C and 50% RH for 24 h. Afterward, cups filled with calcium chloride (0% RH) were covered by films and placed into a desiccator containing a saturated solution of sodium chloride to reach 75% RH at 25°C. The difference in RH between two sides of the film led to a driving force of 1753.55 Pa, named as water vapor partial pressure difference (∆P). The weight loss or gain was periodically recorded every 1 h throughout 24 h, having an accuracy of 0.0001 g.
The water vapor transmission rate (WVTR) of the films was obtained from the slope (S) of the weight vs. time plot (R2 ≥ 0.986), transferred through the effective film area (A) (Equation 2). The WVP [(g.m)/(m2.s.Pa)] was calculated as follows (Equation 3):
where X (m) is the average film thickness. This test for each sample was conducted to the average of at least three determinations.
Moisture absorption
As for moisture absorption (MA), the catted samples (20 mm × 20 mm) were conditioned in a desiccator containing calcium sulfate at 0% RH and 25°C overnight. Thereafter, the films were weighed repeatedly to ensure an RH of 55% by using a desiccator containing the saturated solution of calcium nitrate at 25°C. Until they reached an equilibrium state, films were weighted at specific intervals. MA was calculated as follows[Citation4]:
where W1 and W2 are the initial weights of the sample and the weights of the specimen respectively, after equilibration at 55% RH. All experiments were done at least in three replicates.
Mechanical properties
Tensile strength (TS) and elongation at break (EB) were explored by a texture analyzer (Gotech, Taiwan) in accordance with ASTM method D882-02.[Citation18] The cutting ribbons of 10 mm × 100 mm were conditioned at RH 50% and 25°C for at least 48 h. The initial grip distance and crosshead speed were 50 mm and 50 mm/min respectively. At the end of the test, the results were shown on the monitor of instron. All experiments were done at least three times for each specimen. The TS and EB were calculated as follows (Equations 5 and 6 respectively):
Color and opacity measurement
Hunter color lightness (L) and chromaticity parameters a (red-green) and b (yellow-blue) values of the films were measured using a colorimeter (Hunter-lab model D25/DP-9000, USA). All samples were placed on a white standard plate with color parameter values L* = 92.22, a* = −1.28 and b* = 1.17. The measurements were performed in three replicates. The total color difference (ΔE), whiteness index (WI), and yellowness index (YI) were calculated using Equations (7)–(9)[Citation4]:
For determining the opacity degree (OD) of the films, UV/VIS spectrophotometer (OPTIZEN 2120uv plus mecasys, Korea) was used. The films were cut into rectangles and placed in the spectrophotometer cell. The absorbance of the films was recorded at 600 nm and the empty cell was used as a reference.[Citation5] ODs of the films were calculated by Equation 10. All measurements were performed in triplicates.
Statistical analysis
Significant differences among kefiran/WPU films were examined by the analysis of variance (ANOVA) using SPSS software (Version 11.5; SPSS Inc., USA). Duncan’s multiple range tests were subsequently utilized to determine pairwise comparisons between mean values of samples’ properties. The p-value of 0.05 was considered a significant level.
Results and discussion
Fourier transform infrared
Considering the frequency shift of the groups, FTIR is an accurate instrument for the investigation of the hydrogen bonding.[Citation16] In two compatible polymers, appearing or disappearing, intensity changed, and displacement of the peak can be seen in the FTIR spectrum of their blends.[Citation15] The KPU blends as well as kefiran and WPU were first characterized through FTIR to confirm the structure and interaction between them ().
As can be seen in , the characteristic absorption peak of WPU was observed at 1746 cm−1, which was attributed to the stretching of free urethane carbonyl groups, while the band at 3395 cm−1 was assigned to hydrogen-bonded –NH in urethane group. Kefiran displayed characteristic broad band at 3499 cm−1 and distinct band at 1424 cm−1 attributed to the –OH group and C–O group respectively. In the FTIR spectrum of KPU10, when WPU was added to kefiran, two new bands appeared: a sharp characteristic band for carbonyl group at 1735 cm−1 and another distinct band for C–N group at 1563 cm−1. With increasing WPU content in blends from 10 wt% to 40 wt%, the stretching vibration of carbonyl group shifted to a higher wave number, from 1735 cm−1 to 1750 cm−1. This observed blue shift indicated an enhancement of the free C = O group fraction in the blend films, which could imply intermolecular hydrogen bonding between carbonyl groups of WPU and hydroxyl carbonyl groups of kefiran. Similar results were reported for studies on blend films composed of SPI and polypropylene glycol-based WPU.[Citation8]
X-ray diffraction analysis
The diffractograms and crystallite size of the films are demonstrated in . Kefiran film XRD pattern showed two peaks at 2 Ɵ= 7.3 and 15.26ᵒ. The first peak was sharp and clear, and was used to calculate the crystallite size of films. The second peak appeared broadly with low intensity. In line with previous reports, the semi-crystalline nature of kefiran was observed in this study.[Citation4]
Figure 2. XRD profiles of the kefiran WPU and kefiranWPU films. The value in parenthesis is crystallite size.
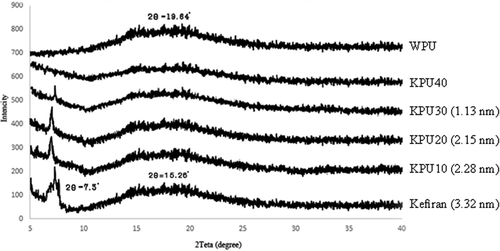
PLC—with its semi-crystalline thermoplastic nature[Citation19]—was utilized as a soft segment of WPU. However, the amorphous nature of WPU film was indicated by only a broad diffraction hump at 2 Ɵ= 19.64. The leading cause behind such phenomenon is that PCL with molecular weight below 2000 typically does not possess crystallinity, since the molecular chain is not long enough to complete the process of chain folding.[Citation19]
When it comes to the blend films, not only was there no new characteristic crystalline peak, but the first peak also disappeared in KPU40. Accordingly, the crystallite size could not be calculated by using Scherrer’s equation for WPU and KPU40. In KPU10, KPU20 and KPU30, it could be seen that the intensity of the first peak and crystallite size decreased on increasing the WPU content. It can be concluded that incorporating WPU into the films destroyed the semi-crystalline structure of kefiran and changed the type and intensity of peaks that appeared in the XRD patterns. It was in good agreement with the results from FTIR. Changing the natural structure of kefiran in blend films was caused by the blue shift in FTIR spectrum of blend films which indicated intermolecular hydrogen bonding between kefiran and WPU.
Differential scanning calorimetry
To further understand the structure, confirm the interactions and miscibility of polymers, DSC studies of the specimens were performed. shows the thermograms of the films. The Tgs—the temperatures at which the polymer undergoes a structural transition from an amorphous solid state (glassy) to a more viscose rubbery state[Citation20]—of the pure kefiran and WPU were 13.95 and 27.22°C respectively. According to Lu et al., if the components Tgs are higher than 20°C apart, it is possible to differentiate a phase-separated system from a miscible one by DSC.[Citation9] Fortunately, distinct differences in the chemical structures of WPU and kefiran resulted in two different Tgs and, detection of individual polymer by DSC. Moreover, the Tgs of the blends were shifted to higher temperatures by increasing the WPU content. This evidence highlighted the point that kefiran participates have synergistic chemical interactions and thus higher miscibility with WPU. It is well known that miscible polymers show only one Tg lying between the Tgs of the components apart whereas immiscible polymers have two distinguishable Tgs, corresponding to the individual polymer.[Citation9] In all specimens, regardless of KPU40, only a single Tg was observed by an endothermic peak. Two different Tgs of KPU40 indicated that phase separation occurred between two polymers. DSC results can be able to prove by SEM micrograph which was discussed in following section.
Scanning electron microscopy
In an attempt to determine the morphological changes in the films, SEM—as a very useful tool—was conducted to visualize the micrograph for all film samples.[Citation21] SEM topography images of upper surface of the films are shown in the . As observed by SEM, kefiran film looks like a thin film with a smooth surface and homogenous morphology. SEM observations of blend films with different WPU concentrations illustrated structural differences. The homogeneous and compact structure, without cracks and free of air bubbles of KPU10, KPU20, and KPU30 films is an indicator of the structural integrity and good miscibility of two polymers, in contrast with that strong interfacial adhesion, about KPU40 film had seen an inhomogeneous structure, suggesting at least a partial separation of phases, indicating poorer compatibility. With a further increase in the WPU content, the continuous phase of kefiran could not be miscible with dispersed WPU phase and appeared as a typical “sea-island” structure (islands of WPU particles dispersed in the sea of the kefiran). This effect had led to thermodynamically immiscible blends, which has been confirmed by DSC analysis. In the other hand, as it is shown in thermograms of miscible films with one Tg have homogenous SEM images.
illustrates SEM images of the cross-section for films. The WPU and kefiran pure films showed uniform morphology without pores or cracks. The fracture cross-sections of KPU10, KPU20, and KPU30 appeared one-phase microstructure with no irregularities, such as breaks or voids. However, continuous fractionate surface of those films meant good interfacial adhesion between the two phases. The sample prepared with 40 wt% WPU show discontinue structure and some bumps associated with the formation of two phases in the matrix which indicated the poorer compatibility between 40 wt% WPU and kefiran. Overall, the blending of WPU with kefiran would lead to improve barrier and mechanical properties as discussed below. Similar results have been observed earlier on the surface of WPU-carboxymethylated guar gum blend films[Citation16] and in plasticized starch modified with poly (ε-caprolactone)-based WPU films.[Citation19]
Thickness
The thicknesses for different ratios of kefiran/WPU films are presented in . Kefiran pure films had lowest thickness which had undesirable effect on water vapor permeability and mechanical property. Moreover the handing of this film was hard. Compared to kefiran film, the thickness of composite films is significantly increased by the addition of WPU (p < 0.05). This might be attributed to the existing differences in the matrix and molecular size of these two polymers. However, there was no considerable difference in the thickness of blend films (p < 0.05). It is important to note that thickness of the WPU film was significantly higher than blend films (p < 0.05). Adding WPU content in the composite films was improved thickness of kefiran film. In contrast to this finding, it was shown that the thickness of kefiran composite film decreased significantly with the addition of starch. The hydrogen bond formed between these two biopolymers might create new chains, leading to more a closely packed structure and thereby reducing the thickness.[Citation1]
Table 1. Thickness, WVP, MA, and mechanical properties of kefiran/WPU films (means ± standard deviation)a.
Water vapor barrier property
WVP is one of the critical properties for packaging materials in the food industry, especially in a humid atmosphere. Owing to the hydrophilicity of kefiran, the WVP was high. This drawback was gradually reduced by interactions with WPU (). This was corroborated in the study by Zhang et al.[Citation10], who concluded that an increase in the WPU concentration decreased the WVP of blend films based on soy protein isolate through strong interactions between two component chains.
The WPU content less than 40 wt% in the composite films was shown to be efficient in keeping the WVP sufficiently below 4.9 ± 0.2 × 10–11 g/m.s.Pa, which might occur as a result of phase separation revealed by DSC and SEM; or, in other words, the matrix of KPU40 contains possible paths for diffusion of molecules. This phenomenon has been observed in kefiran/starch films as well. It was reported that the WVP of blend films reduced with increases in the starch content from 0% to 50%. Therefore, the interaction between kefiran and starch could prevent water molecules from diffusing through the films. Nevertheless, the high content of starch as well as its insufficient dispersals in the matrix caused an increase in the WVP.[Citation1]
Moisture absorption
Another defect of biopolymer materials—the same as kefiran with its hydrophilic nature—is the tendency to absorb moisture. Hence, any improvement in water resistance plays a significant role in their usage.[Citation22] shows the effects of WPU content on the MA of films. It can be easily seen that the WPU is basically waterproof and absorbs water at a very low level, while the kefiran is water-sensitive and absorbs water. Compared with kefiran film, MA of blends significantly decreased with the increase in WPU content (p < 0.05). Meanwhile, the hydrogen bonding interactions which were observed in FTIR spectrum between the high water-resistant WPU with kefiran might be responsible for the reduction in the MA.
Similar results have been reported in an earlier study on the addition of WPU to soy meal protein. In that study, the reason for the decrease in MA was explained by the strong hydrogen bonding interaction between two polymers.[Citation12]
Mechanical properties
Comparing mechanical properties of kefiran with commercial films like LDPE and HDPE shows, TS of kefiran very lower than LDPE (16.2 Mpa) and HDPE (27.8 Mpa) and in case EB, kefiran and LDPE had same value (68.8%) but HDPE (150%)[Citation23] is higher than them. These comparisons determined mechanical properties defects of pure kefiran film. As can be observed in , the EB and TS values of the blend films were positively affected by the WPU addition from 10 to 40 wt% as compared with kefiran film. The WPU exhibited the characteristic of a flexible polymer with maximum TS and EB among all specimens in this study. WPU exhibited much more EB (737.15%) compare with commercial films. The improvement in the mechanical features of the composite films can be attributed to the hydrogen bonding interaction of WPU with kefiran which was observed in FTIR results. However, the film containing 40 wt% WPU showed poor mechanical properties despite having the highest content of WPU. Akin to the WVP, the sharp drop in TS and EB of KPU40, as it was discussed in DSC and SEM sections, were induced by phase separation in the matrix.
Considering these results, it was concluded that KPU30 displayed the critical ratio for the TS and EB values of the blend films, and, accordingly, the greatest integrity of the film-forming constituents. Mechanical properties of blend films especially EB of KPU30 were remarkable improved in compare with LDPE and HDPE. A similar trend was also evident in thermoplastic starch (TPS)/WPU blend films. The highest values of TS and EB for the composite films were respectively observed at 15 wt% and 10 wt% of WPU. The additional WPU was thereafter associated with a decline in mechanical properties. The probable cause behind such behavior was the fractionation of two starting components into two various phases.[Citation6]
Color and opacity measurement
The final appearance of the product and its acceptability to consumers can be influenced by the opacity and color characteristics of films and coatings.[Citation2,Citation20] The effects of WPU addition on films’ color and opacity are displayed in . Both of kefiran and WPU do not have red or green pigments. Therefore, a (redness/greenness) value of the films did not change and no significant differences between blend films were observed. ΔE, YI, and b (yellowness/blueness) values increased as a result of the increasing WPU content in blend films. In contrast, L (lightness/darkness) and WI values decreased significantly (p < 0.05). The OD of the film specimens significantly increased (p < 0.05) with increasing WPU content. In food packaging systems, an increase in OD created a better barrier to UV that can postpone fat oxidation.[Citation5] Blending with WPU caused yellower and darker films, which can be explained by the development of cross-linking between two polymers.
Table 2. Hunter color values (L, a, and b), total color difference (ΔE), whiteness index (WI), yellowness index (YI), and opacity degree of kefiran/WPU filmsa.
Conclusion
The glycerol plasticized kefiran blended with WPU by casting method. We successfully prepared a series of new biodegradable films based on kefiran with improved water resistance and physical properties. When WPU content was lower than 30 wt%, fine compatibility, homogeneous structure and improvement of kefiran drawback were observed, as a result of the strong interaction with kefiran. Further increases in WPU caused phase separation, immiscibility and destroyed the properties that had improved. The results of FTIR, XRD, DSC and SEM explained these phenomena and indicated the intermolecular interactions between them. Compared with the pure kefiran films, the kefiran/WPU blends show lower WVP and moisture absorption. Meanwhile, higher values of tensile strength, elongation at break, yellowness, and opacity were obtained. It is interesting to produce kefiran/WPU blend films with biodegradable materials, which have a potential application in the food industry.
Acknowledgments
The authors gratefully acknowledge the facilities, support and technical assistance provided by Islamic Azad University, Science and Research Branch, of Iran.
References
- Motedayen, A. A.; Khodaiyan, F.; Salehi, E. A. Development and Characterisation of Composite Films Made of Kefiran and Starch. Food Chem. 2013, 136(3), 1231–1238.
- Piermaria, J.; Bosch, A.; Pinotti, A.; Yantorno, O.; Garcia, M. A.; Abraham, A. G. Kefiran Films Plasticized with Sugars and Polyols: Water Vapor Barrier and Mechanical Properties in Relation to Their Microstructure Analyzed by ATR/FT-IR Spectroscopy. Food Hydrocoll. 2011, 25(5), 1261–1269.
- Pop, C.; Rotar, A. M.; Salanțӑ, L. C.; Semeniuc, C. A.; Socaciu, C.; Sindic, M. Fingerprint Profiling of Polysaccharide Kefiran Extracted from Kefir Grains Biomass. J. Agroaliment. Proc. Tech. 2015, 21(2), 207–212.
- Shahabi-Ghahfarrokhi, I.; Khodaiyan, F.; Mousavi, M.; Yousefi, H. Effect of γ-Irradiation on the Physical and Mechanical Properties of Kefiran Biopolymer Film. Int. J. Biol. Macromol 2015, 74, 343–350.
- Sabaghi, M.; Maghsoudlou, Y.; Habibi, P. Enhancing Structural Properties and Antioxidant Activity of Kefiran Films by Chitosan Addition. Food Struct. 2015, 5, 66–71.
- Lu, Y.; Tighzert, L.; Dole, P.; Erre, D. Preparation and Properties of Starch Thermoplastics Modified with Waterborne Polyurethane from Renewable Resources. Polymer (Guildf). 2005, 46(23), 9863–9870.
- Barikani, M.; Mohammadi, M. Synthesis and Characterization of Starch-Modified Polyurethane. Carbohydr. Polym. 2007, 68(4), 773–780.
- Tian, H.; Wang, Y.; Zhang, L.; Quan, C.; Zhang, X. Improved Flexibility and Water Resistance of Soy Protein Thermoplastics Containing Waterborne Polyurethane. Ind. Crops Prod. 2010, 32(1), 13–20.
- Lu, Y.; Tighzert, L.; Berzin, F.; Rondot, S. Innovative Plasticized Starch Films Modified with Waterborne Polyurethane from Renewable Resources. Carbohydr. Polym. 2005, 61(2), 174–182.
- Zhang, M.; Song, F.; Wang, X.-L.; Wang, Y.-Z. Development of Soy Protein Isolate/Waterborne Polyurethane Blend Films with Improved Properties. Coll. Surf. B. 2012, 100, 16–21.
- Zia, F.; Zia, K. M.; Zuber, M.; Kamal, S.; Aslam, N. Starch Based Polyurethanes: A Critical Review Updating Recent Literature. Carbohydr. Polym. 2015, 134, 784–798.
- Tong, X.; Luo, X.; Li, Y. Development of Blend Films from Soy Meal Protein and Crude Glycerol-Based Waterborne Polyurethane. Ind. Crops Prod. 2015, 67, 11–17.
- Ciobanu, C.; Ungureanu, M.; Ignat, L.; Ungureanu, D.; Popa, V. Properties of Lignin–Polyurethane Films Prepared by Casting Method. Ind. Crops Prod. 2004, 20(2), 231–241.
- Zia, K. M.; Zia, F.; Zuber, M.; Rehman, S.; Ahmad, M. N. Alginate Based Polyurethanes: A Review of Recent Advances and Perspective. Int. J. Biol. Macromol. 2015, 79, 377–387.
- Ma, J.; Xu, Q.; Gao, D.; Zhou, J.; Zhang, J. Blend Composites of Caprolactam-Modified Casein and Waterborne Polyurethane for Film-Forming Binder: Miscibility, Morphology and Properties. Polym. Degrad. Stab. 2012, 97(8), 1545–1552.
- Huang, Y.; Yu, H.; Xiao, C. Effects of Ca 2+ Crosslinking on Structure and Properties of Waterborne Polyurethane-Carboxymethylated Guar Gum Films. Carbohydr. Polym. 2006, 66(4), 500–513.
- Intl, A.S.T.M. Standard Test Methods for Water Vapor Transmission of Material E 95-96 Annual Book of ASTM Standards; ASTM Intl.: Philadelphia, PA, 1995; pp. 785–792.
- Intl, A.S.T.M. Standard Test Method for Tensile Properties of Thin Plastic Sheeting D 882-01 Annual Book of ASTM Standards; ASTM Intl.: Philadelphia, PA, 2001; pp. 162–170.
- Cao, X.; Chang, P. R.; Huneault, M. A. Preparation and Properties of Plasticized Starch Modified with Poly (ε-caprolactone) Based Waterborne Polyurethane. Carbohydr. Polym. 2008, 71(1), 119–125.
- Ghasemlou, M.; Khodaiyan, F.; Oromiehie, A.; Yarmand, M. S. Development and Characterisation of a New Biodegradable Edible Film Made from Kefiran, an Exopolysaccharide Obtained from Kefir Grains. Food Chem. 2011, 127(4), 1496–1502.
- Ahmed, Z.; Wang, Y.; Anjum, N.; Ahmad, A.; Khan, S. T. Characterization of Exopolysaccharide Produced by Lactobacillus Kefiranofaciens ZW3 Isolated from Tibet kefir–Part II. Food Hydrocoll. 2013, 30(1), 343–350.
- Zolfi, M.; Khodaiyan, F.; Mousavi, M.; Hashemi, M. Development and Characterization of the Kefiran-Whey Protein isolate-TiO 2 Nanocomposite Films. Int. J. Biol. Macromol. 2014, 65, 340–345.
- Piermaria, J. A.; Pinotti, A.; Garcia, M. A.; Abraham, A. G. Films Based on Kefiran, an Exopolysaccharide Obtained from Kefir Grain: Development and Characterization. Food Hydrocoll. 2009, 23(3), 684–690.