ABSTRACT
Laser powder bed fusion (LPBF) is a promising additive manufacturing technique that allows layer-by-layer fabrication of metallic powders. Distinguished thermal dynamics result in the microstructure of intrinsic features. This review aims to provide a thorough insight into the solidification fundamentals and the microstructural tailoring during LPBF. It begins with the introduction of the LPBF and the challenges of its applications with aluminium alloys. The thermal dynamics and its influence on the microstructure in LPBF were thereafter discussed. The attempts to tailor microstructures by refinement in LPBF fabrication of various aluminium alloys were summarised. Finally, the review provides a conclusive remark on the microstructural controlling and an outlook on the remaining challenges and potential research topics in LPBF with Al alloys.
1. Introduction
Laser powder bed fusion (LPBF) is a disruptive additive manufacturing (AM) technology that selectively melts and consolidates thin layers of metallic powders with a focused high-energy laser beam to build components directly based on a computer-aided design model (Hojjatzadeh et al. Citation2019; Leung et al. Citation2018). The typical manufacturing routes are usually completed in a chamber purged with inert gas (typically argon) to prevent oxidation, as shown in (a and b). During LPBF, the periodic heating and cooling cycles result in a unique processing–structure–property relationship (Thampy et al. Citation2020; Gu et al. Citation2021). The rapid melting and solidification of localised materials accompany with steep thermal gradients and high cooling rates (∼104–107 K·s−1) (Sohrabpoor et al. Citation2021), which further result in extremely fine and columnar grains oriented along the building direction (Kuo et al. Citation2020) as well as high solid solubility (Sohrabpoor et al. Citation2021). Consequently, increased strength, reduced ductility and increased microstructure and mechanical property anisotropy are prominent features in LPBF manufactured components. Besides, high residual stress and the accompanying risk of cracking have been a thorny issue over decades because plenty of alloys were therefore considered unsuitable for the technique (Pant et al. Citation2022; Platl et al. Citation2022). A wider selection of materials with sound LPBF fabrication and an improvement of mechanical properties are the ultimate goals for all kinds of applications (Martin et al. Citation2017). Since LPBF has been mainly employed to fabricate certain commercial alloy powders, the main processing parameters, i.e. laser power, scanning speed, hatch spacing and layer thickness, as shown in (c), have been well investigated among these materials (Cunningham et al. Citation2019; Nayak et al. Citation2020; Khorasani et al. Citation2020). In recent years, the research focus has been shifted to the compositional modification to improve the printability of alloys that can be well manufactured with conventional technologies (Wang et al. Citation2022). An expectation that the overall performance can be further improved is counted on.
Figure 1. Schematic of (a) a typical LPBF machine, (b) gas circulation system, and (c) LPBF process parameters. Reproduced from Wen et al. (Citation2019) (a and b) and Yap et al. (Citation2015) (c).
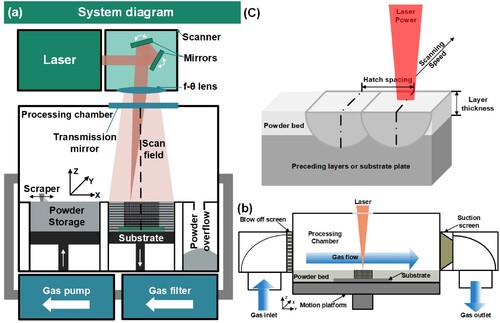
Aluminium alloys have been extensively used as lightweight structural materials owing to their excellent specific strength and corrosion resistance (Joshi and Sheikh Citation2015). Although LPBF technology enables improved properties and resultant potentials of aluminium alloys for applications in aerospace, automobile and defence industries, great challenges have been encountered in practice (Choong et al. Citation2020). LPBF can only be adopted to fabricate limited Al–Si series casting aluminium alloys such as AlSi10Mg (Maleki et al. Citation2022) and AlSi12 (Kimura et al. Citation2020), which show insufficient strength for aerospace and automotive applications (Liu et al. Citation2022). Other series aluminium alloys especially high-strength aluminium alloys manufactured via LPBF have drawn increasing attention worldwide (Qi et al. Citation2021; Bradford et al. Citation2021). Due to their high sensitivity to solidification crack, huge amount of work is currently in progress intended to improve their printability (Mair et al. Citation2022; Sabzi et al. Citation2020; Yu et al. Citation2022). An in-depth understanding of the as-built microstructure is crucial for the modification methodology. illustrates the formation of the as-built microstructure. The heating (melting), cooling (solidification) and the post-remelting and intrinsic heat treatment develop the ultimate microstructure (Jiang et al. Citation2020).
Figure 2. The illustration of the as-built microstructure formation. Revised from Zhang et al. (Citation2022), Pérez-Ruiz et al. (Citation2021), Thijs et al. (Citation2013), Pantawane et al. (Citation2020).
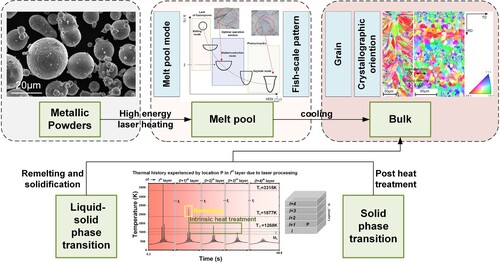
Although recent reviews (Leirmo Citation2021; Fiocchi, Tuissi, and Biffi Citation2021; Yu et al. Citation2019) have discussed the development of aluminium alloys fabricated with LPBF, few were focused on the microstructure evolution associated with the solidification process. This review provides an overview of recent advances in as-built microstructure manipulation, especially by compositional modification in aluminium alloys via the LPBF process. After a brief introduction, the solidification behaviour, the thermal history in LPBF and the consequent typical microstructure will be comprehensively described. The methods for microstructure manipulation in different aluminium alloys will be discussed thereafter. An outlook on the remaining challenges and potential research topics will be provided finally.
2. Solidification behaviour in LPBF
Small volumes of materials in the LPBF process melt and solidify due to the rapid scanning of focused laser beam on the powder bed (Li et al. Citation2021; Coen, Goossens, and Van Hooreweder Citation2022). Therefore, of significant importance is the in-depth understanding of the solidification mechanisms. During solidification, disordered atoms are converted into an ordered solid crystal via nucleation and growth (Boettinger et al. Citation2000). According to classical nucleation theories (Bai and Li Citation2006), the nucleation process was initiated by stable clusters (i.e. the nuclei) formation due to density fluctuations in the melts. The critical nuclei radius is inversely proportional to the nucleation undercooling, which is composed of thermal undercooling and constitutional undercooling (Prasad et al. Citation2020). The thermal undercooling, assumed to be large in the LPBF process, is induced by the lag in the growth of the solid/liquid (S/L) interface at high cooling rates (Ghoncheh et al. Citation2021). The constitutional undercooling is yielded by the solute elemental accumulation in front of the S/L interface (Prasad et al. Citation2020; Shu et al. Citation2011). Conversely, a high cooling rate associated with the LPBF process would generate a reduced diffusion layer at the S/L interface, limiting and even eliminating constitutional undercooling (Schimbäck et al. Citation2022). Therefore, whether sufficient undercooling can exceed the critical nucleation undercooling in the LPBF remains up for further investigation and discussion. Tan et al. (Citation2022) demonstrated that solute addition was essential for activating heterogeneous nucleation upon solidification to achieve high grain refinement efficiency and attributed it to the lag in dendrite growth induced by solute rejection during solidification. After nucleation, the crystals grow until all the grains impinge upon each other. Preferred growth orientation of the crystals is an important characteristic of alloys that makes contribution to the crystallographic texture. The overall heat flow direction within the component being built and the growth direction, influenced by the thermal input, are the other two factors (Qin et al. Citation2018). To control the microstructure of the parts, a thorough understanding of solidification conditions is crucial. In this section, the thermal histories and the distinguished microstructure will be discussed.
2.1. Thermal history
In the LPBF process, the scanning of a laser beam with a diameter ranging from tens to hundreds of micrometres (Qu et al. Citation2021; Makoana et al. Citation2018; Vrancken, Ganeriwala, and Matthews Citation2020) on a small volume of materials yields extremely high heating rate followed by rapid cooling (104–107 K/s). The track-by-track and layer-by-layer building processes result in the fact that each region in the parts goes through a distinct and unique thermal history. These thermal histories manifest into various thermal processes, including multiple melting, annealing and tempering heat treatment, which consequently generate different microstructure depending on where it is located (Yavari et al. Citation2021). Monitoring the temperature of certain location has been attempted (Zhang, Vallabh, and Zhao Citation2022; Megahed et al. Citation2019; Yavari et al. Citation2021). However, due to the facts that (1) there are very localised laser–material interaction regions, (2) these small regions undergo extremely high thermokinetics (high temperature and high heating/cooling rates), and (3) the materials plume and/or plasma in the laser–material interaction regions may obstruct the monitoring process (Pantawane et al. Citation2020), computational efforts on developing the understanding of the laser–material interaction have been performed consistently (Zhang et al. Citation2021).
Pantawane et al. (Citation2020) conducted computational simulation through the finite element modelling (FEM) on the thermal evolution in a single laser track, single layer with bi-directional strategies and multiple layers of Ti6Al4V alloy parts, with the laser power 150 W and scanning speed 800 mm/s. The results can also apply to other alloys. illustrates the computationally predicted time-temperature relationship in the solid and liquid regions in a single laser track. The laser-interaction zone was divided into three zones, i.e. molten (during heating), molten + vapour (during heating) and molten (during cooling) states. When the powder materials are subjected to high energy laser, the surface temperature rapidly rises and develops a melt pool. At the vaporisation temperature (3315 K for Ti6Al4V), there is some material loss, causing evaporative cooling effect (Megahed et al. Citation2019). Besides, vapours generate recoil pressure, which may influence the vaporisation temperature (Ye et al. Citation2019). Consequently, the surface temperature fluctuates around the vaporisation temperature. During the cooling process, the cooling rates vary within specific temperature ranges, indicated by the slope of the curve. The cooling rate is highest in the range from vaporisation to liquidus temperature. As the temperature falls into the zone between liquidus and solidus, a gradual decrease in the cooling rates can be witnessed due to the release of the latent heat associated with the mushy state of the alloy (Marola et al. Citation2020). After complete solidification, the cooling rate of the solid regains a higher value and continues decreasing until the beginning of the next laser track.
Figure 3. The computationally predicted thermal pattern in a single laser track. Reproduced from Pantawane et al. (Citation2020).
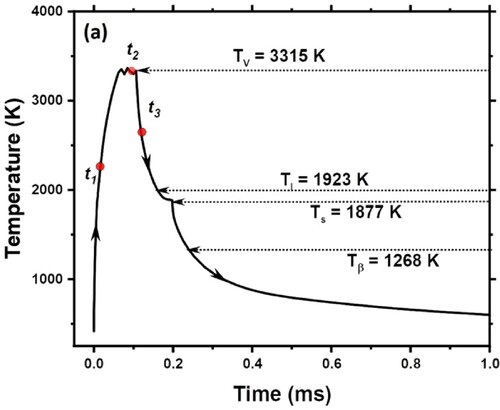
In , the temperature at one specific location P in single layer was captured. It shows the preheating and postheating effects due to multiple laser scanning. The prior neighbouring laser tracks individually contribute to the rise in the temperature of location P due to heat transfer from these laser tracks at the extents proportional to their relative distances from location P. In Pantawane's work associated with Ti6Al4V alloy under certain processing parameters, only four prior neighbouring tracks can significantly contribute to a temperature rise over 400 K, above which microstructural effects are expected. Other prior laser tracks leading to a temperature rise of less than 400 K may only affect the temperature-dependent thermophysical properties. Similarly, the laser scanning caused post-heat treatment is effective within the neighbouring four tracks. No remelting in the melt pool centre was found in the time-temperature plot. Apart from heat treatment, reduced cooling rates are expected to relieve the residual stresses to some extent due to the post-heating.
Figure 4. The computationally predicted thermal pattern of position P in a single layer. Reproduced from Pantawane et al. (Citation2020).
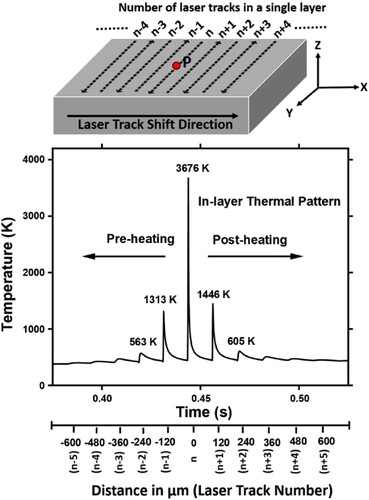
The temperature evolution at certain location P in a multilayer structure was probed and shown in . The thermal pattern of preheating–(remelting)–postheating with relatively lower peak temperatures in later deposited layers was illustrated. With the temperature above solidus, the remelting occurs in the subsequent one layer, i.e. the (l +1)th layer on layer l in . Generally, this is intentionally designed so that a metallurgically sound interface forms between consecutive built layers during the LPBF process (Ghosh et al. Citation2018). While deeper penetration depth was reported (Qin et al. Citation2018), depending on the processing parameters and materials characteristics. Scanning of other layers results in temperature lower than solidus temperature, which generates intrinsic thermal treatment substantially and is likely to influence microstructural and phase evolution along with the state of stress in the component. For example, Moyle et al. (Citation2022) demonstrated that a higher degree of Cu clustering and precipitation in 17–4 precipitate hardening stainless steel led to higher hardness at a higher energy input. The authors attributed it to the more effective intrinsic heat treatment and foresaw the prospect of mitigating post-fabrication heat treatments. Another example associated with a hardness decrease due to intrinsic heat treatment was also reported (Damon et al. Citation2019). Therefore, it depends on the material characteristics and needs to be well controlled.
Figure 5. The computationally predicted overall thermal history of location P on the surface of lth layer in multiple layer fabrication. Reproduced from Pantawane et al. (Citation2020).

Apart from bi-directional scanning, various scanning strategies add the complexity of the thermal histories (Yu et al. Citation2019; Zhang et al. Citation2021), e.g. the duration and sequence of the melting, remelting, and heat treatment process. More generally, the thermal histories depend significantly on the materials and processing parameters (Ashby et al. Citation2022; Lough et al. Citation2020), summarised in . Although the monitoring of thermal histories encountered challenges, the characterisation of materials and the determination of processing parameters offer a good indication for decision making. The typical microstructure and crystallographic texture in the aluminium components will be discussed in the following section.
2.2. Solidified microstructure
The hierarchical structures associated with the thermal histories are illustrated in . (a) exhibits the mode of melt pools, from balling mode, conduction mode to the keyhole mode, with volumetric energy density (VED) increasing. The microstructure in LPBF parts differs significantly from that in the bulk components manufactured via traditional manufacturing processes (Avateffazeli et al. Citation2022). A typical fish scale pattern shown in (b) consists of dual-half elliptical melt pools aligned along the building direction (Bosio et al. Citation2021). (c) displays the crystal morphology along with the crystallographic orientation in two perpendicular views for an AlSi10Mg LPBF part. An emphasis will be focused on this aspect in the section.
Figure 7. (a) The melt pool morphology varying with VED; (b) the illustrations of fish scale pattern in conduction and keyhole melt pool; (c) representative EBSD orientation maps of the front view (left) and top view (right) for an AlSi10Mg alloy LPBF part. Reproduced from Pérez-Ruiz et al. (Citation2021) (a and b) and Thijs et al. (Citation2013) (c).
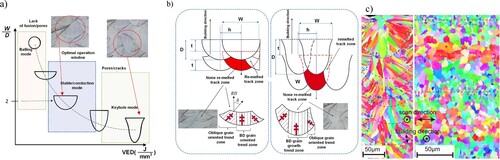
The crystalline distribution relies on the solidification inside the melt pool and subsequent intrinsic heat treatment (Wang et al. Citation2021). A common phenomenon in solidification of melt pool during LPBF is epitaxial growth (Yuan et al. Citation2022; Guo et al. Citation2022), which results from the remelting of the previously built layers, as mentioned in Section 2.1. Due to the insufficient nuclei at the S/L interface, bulk heterogenous nucleation events make room for epitaxial growth, a process in which crystallographic orientations are inherited from the partially melted parental grains in the underlying layer because the layer being built is of the same material with the substrate or the previously deposited layer (Liu et al. Citation2022). Competitive growth occurs between the grains better aligned with the local temperature gradient and less aligned ones (Liu and To Citation2017). The former grains outgrow the latter ones and form columnar grains, usually propagating across layers, as shown in (c). It was reported that both epitaxial growth (as termed as epitaxial nucleation) and the bulk nucleation are possible in the melt pool. When epitaxial growth dominates and no bulk nucleation is activated (the maximum nuclei density N0 = 0), the grain structure is occupied by columnar grains, perpendicular to the moving solidification front (indicated by the dashed lines in ) (Li and Tan Citation2018). With bulk nucleation activated, equiaxed grains are formed on top of the melt pool. Increasing N0 for bulk nucleation, growing number of finer equiaxed grains is expected.
Figure 8. The grain structures at the centre plane in LPBF parts with different N0 with undercooling ΔTc being kept as 5 K. Reproduced from Li and Tan (Citation2018).
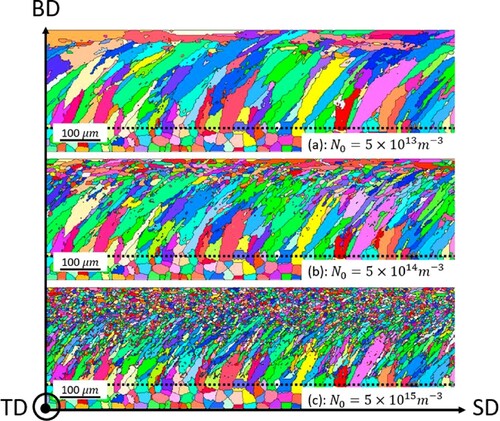
As demonstrated in , the number of equiaxed grains grows along the building direction. The grain size and morphology manipulation have always been the task of materials fabrication. To describe the relationship between grain morphology and size, the solidification map (Van Cauwenbergh et al. Citation2021) was developed, in which the parameters, thermal gradient (G) and solidification rate (R) are involved. As exhibited in (a), the morphology of the microstructure is up to the parameter G/R, while the grain size depends on the cooling rate G·R. Fine to coarse grains take shape as the cooling rate G·R decreases. With the decreasing values of parameter G/R, a gradual change in grain morphology appears from planar, cellular, columnar dendritic to equiaxed dendritic shape. The G/R value distribution in the melt pool indicates that columnar and equiaxed grains tend to form at the bottom and top of the melt pool, respectively, while in between columnar to equiaxed transition (CET, if it occurs) is expected (Karimi et al. Citation2021). Although equiaxed grain near the top of the melt pool may take shape, will it be observed only when a large fraction of them is assured because remelting of the previously deposited layers may erase them (Li and Tan Citation2018). The G–V map is another strategy for predicting the dominant morphology. According to the G–V map, the grain structure will transform from columnar to equiaxed as the G decreases and the V increases. The melt pool bottom marked out by the blue triangle exhibits columnar grains while the melt pool tail indicated by the circle is in the equiaxed grain zone, as illustrated in (b).
Figure 9. (a) Solidification map and (b) a representative G–V map. Reproduced from Van Cauwenbergh et al. (Citation2021) (a) and Li and Tan (Citation2018) (b).
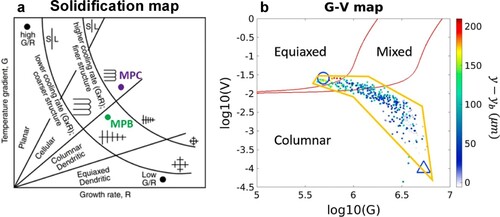
A deeper insight into the microstructure is focused on the crystallographic orientations. For aluminium alloys with a face-centred-cubic (FCC) crystal structure, the <100> directions are usually aligned with local maximum temperature gradient (Collins et al. Citation2016). In multiple scanning printed bulks, the texture is influenced by the processing parameters and material modifications. Scanning strategies are of primary importance. Orientation of the primary dendrites was found at 60° for all deposited layers with unidirectional laser scanning. While it was revealed to be 90° in the neighbouring layers for bidirectional laser scanning (Dinda, Dasgupta, and Mazumder Citation2012). A zigzag orientation and tortuous grain shapes were therefore formed (Metelkova et al. Citation2021). A chessboard scanning strategy and bidirectional scanning with rotation of 67° between adjacent layers were reported to weaken the overall crystallographic texture (Qin et al. Citation2018; Thijs et al. Citation2013). The laser parameters will determine the remelting portion of the underlying layer and the adjacent tracks, making the texture incomplete. VED-related parameters could be manipulated, for example by varying the hatch spacing and the layer thickness (Thijs et al. Citation2013), to modify the texture. Grain refinement via inoculation treatment was also demonstrated to yield a microstructure with random texture (Mair et al. Citation2021). To sum up, a comprehensive relationship among LPBF microstructure properties is illustrated in , which is an updated version based on reference (Pérez-Ruiz et al. Citation2021).
Figure 10. Interactions between LPBF parameters-microstructure-properties. Revised from Pérez-Ruiz et al. (Citation2021).
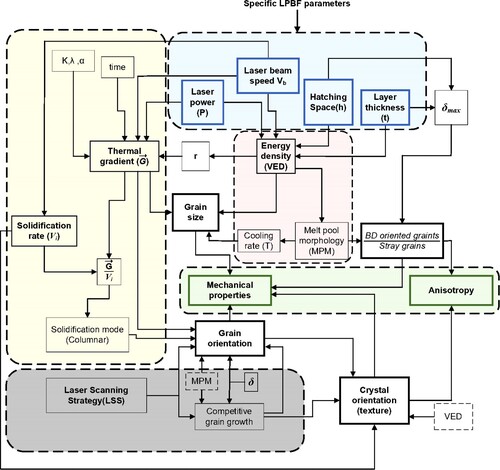
3. Grain refinement attempts in aluminium alloys via LPBF
Analogous to the traditional manufacturing processes, AM technology was proven to rely on grain microstructure refinement to improve mechanical properties such as strength and plasticity (Guan and Tie Citation2017; Ramirez et al. Citation2008). Meanwhile, migration of anisotropy of parts fabricated via LPBF has been studied since the advent of this technique (Somlo et al. Citation2022). Equiaxed fine grains offer a preferred solution. In this section, the microstructure and various grain refinement attempts in different aluminium alloys will be discussed.
3.1. Al–Si alloys
Al–Si series alloys are the most widely adopted aluminium alloys for LPBF. However, only near eutectic alloys were reported to have good processibility (Lefebvre et al. Citation2021). The silicon content has a significant impact on the fluidity of the liquid, therefore affecting the printability via LPBF. Kimura et al. (Citation2017) carried out an experimental investigation in Al–xSi binary alloys (x = 0, 1, 4, 7, 10, 12 and 20 wt%) and found that Al–1Si alloy exhibits a high density of solidification cracks, which cannot be eliminated by manipulating processing parameters. Hyer et al. (Citation2021) later calculated the maximum cracking susceptibility of Al–xSi alloys based on the criterion |dT/dfS1/2| proposed by Kou (Citation2015). The variables T and fs are the temperature and the mass fraction of solid, respectively. It was claimed that the maximum cracking was expected in Al–0.5Si alloy without considering any diffusion in solid while it shifts to higher silicon concentration (1 wt%) when taking solid diffusion into account. Therefore, Al–Si alloys with silicon content over 4 wt%, especially 7–12 wt% are popular for LPBF. Minor additions of Mg enable precipitation of Mg2Si and thus hardenability by natural or artificial ageing. Therefore, AlSi7Mg (Casati et al. Citation2021) and AlSi10Mg (Ramoni et al. Citation2021) are widely used and studied in LPBF. Inspiringly, recent research interest has been focused on other near eutectic alloys, such as Al–Ce alloys (Hesselmann et al. Citation2022; Zhou et al. Citation2020).
Typical microstructure of Al–xSi alloys via LPBF has been revealed, as shown in . In pure aluminium, dispersed granular microstructures dominate and microstructural anisotropy in different direction was not observed. When silicon content increases, the granular eutectic silicon and microstructural anisotropy emerge gradually. With the silicon concentration above 4 wt%, the web-like Al–Si eutectic structure and the elongated cells parallel to the stacking direction become better defined (Kimura et al. Citation2017).
Figure 11. SEM images of etched top (−1) and side (−2) of Al–xSi LPBF samples fabricated with the optimal processing parameters. (a) Al–0Si, (b) Al–1Si, (c) Al–4Si, (d) Al–7Si, (e) Al–10Si, (f) Al–12Si, and (g) Al–20Si. Reproduced from Kimura et al. (Citation2017).
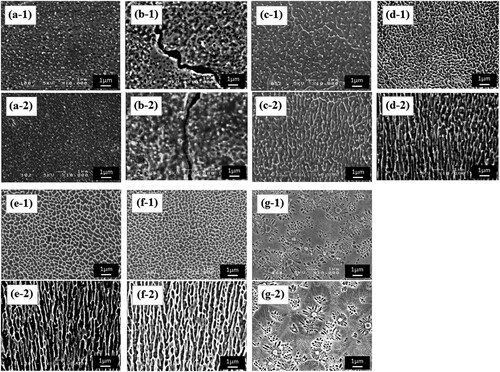
The α-Al grain and sub-grain eutectic structure are the typical microstructure of hypoeutectic Al–Si alloy. Both along with the fraction of secondary phase (i.e. Si precipitation) are essential to the mechanical properties. Kempf and Hilgenberg (Citation2020) demonstrated a negative correlation between strength properties and the sub-cell size. The as-build AlSi10Mg alloys with fine sub-grain cell size as small as 420 nm exhibit ultimate tensile stress (UTS) as high as 492 MPa. The authors further ascribed the strength reduction caused by heat treatment to the sub-cells coarsening and break-up without changing the grain size. Liu et al. (Citation2020) verified the impact of sub-cell and proposed two newly defined morphology indices, i.e. dimensional-scale index Id and shape index Is, to quantify the influence of the sub-cell structure on the mechanical properties in AlSi10Mg alloys. The dimensional-scale index Id describes the structure size (i.e. area, major axis length and perimeter) and shape fullness (i.e. roundness and convexity). While the shape index Is index is related to shape (e.g. aspect ratio and eccentricity) and boundary details (e.g. tortuosity). A microstructure with larger Id and smaller Is indicating bigger cells with more convex hull structure tend to lead to more local stress concentration, deteriorating the mechanical strength. However, neither the grain size nor the two new morphology indices alone can fully explain the mechanical differences among parts. A combination of them can do a better job for quantification.
Previous research has been focused on the improved microstructure and mechanical properties for near eutectic Al–Si alloys by an investigation into LPBF processing window. Manipulation of laser power, scanning speed, hatch spacing, layer thickness, scanning strategies, gas atmosphere, pre-heating treatment, storage conditions, etc. has been well performed (Riener et al. Citation2021; Xiao et al. Citation2022; Yang et al. Citation2020). However, limitation for the application has been encountered. The yield strength was well reviewed by Rometsch et al. (Citation2022) and was found in the range of 150–300 MPa, failing to meet the increasing demand of high strength. Apart from the extensive investigation on parameters, a growing number of studies have been conducted on materials modification or design although it was believed that Al–Si alloys have good printability. Inoculation treatments have been commercially practiced in foundries for decades and are now regarded as a new approach to achieve high strength in LPBF. Grain refining inoculants promote heterogeneous nucleation events during solidification so that equiaxed microstructures can be obtained in LPBF Al parts. Analogous to the traditional manufacturing techniques, an edge-to-edge model was well adopted to select the grain refiners. Al3X (X = Sc, Zr, Er, …) compounds with L12 structure and YB6 (Y = Ca, La, Ce, …) compounds with cubic structure (CsCl-type) have produced encouraging results (Tan et al. Citation2020). Sc was proven to be able to refine both α-Al and the eutectic silicon in cast alloys (Lu et al. Citation2019). Adopted in LPBF, both the grain size and the sub-grain size expected to be refined. In the investigation of Chen et al. (Citation2021), the sub-cell size from approximately 1.2 to 0.7 μm was obtained by modifying AlSi10Mg alloy with Sc, achieving a UTS as high as 438 MPa at the as-built condition. Zhang et al. (Citation2022) used Er, which introduces Al3Er in the molten pool, to improve the mechanical properties of AlSi7Mg alloy by refining the average size from approximately 40 to 11.4 μm. The ultrafine sub-cell structure and silicon particles were expected to benefit the mechanical properties as well. An UTS of 438 MPa and yield strength of 296 MPa were achieved at as-built condition. Other nanoparticles such as TiB2 (Xiao et al. Citation2019) and TiC (Fan et al. Citation2021) have been attempted to refine the microstructure of AlSi10Mg alloys. Ultrafine equiaxed sub-cell structure exhibiting no anisotropy can be obtained. An extreme high UTS over 520 MPa was made possible. An alternative approach to optimise the microstructure is via reinforced Al matrix composite (Zhao et al. Citation2019; Jiang et al. Citation2018; Li et al. Citation2019; Konopatsky et al. Citation2021). With TiCN as a reinforcement, the microstructure with an average grain size of 1.56 µm and a sub-cell size of 0.97 µm was obtained (He et al. Citation2022). Nevertheless, the weak interfacial bonding between the Al matrix and reinforcements, leading to insufficient strength, requires further improvement. Some researchers also explored alloying with Ni (Jandaghi et al. Citation2022) and Cu (Garmendia et al. Citation2020) elements to enhance mechanical properties although a comprehensive understanding and manipulation are needed.
Apart from near eutectic Al–Si alloys, the majority of other aluminium alloys can be classified as the category with poor printability, such as Al–Mg, Al–Cu, Al–Zn–Mg alloys. The microstructure manipulation will be addressed in the following sections.
3.2. Al–Mg alloys
Al–Mg alloys, which are intrinsically not heat treatable and printable via LPBF, have drawing extensive attention since the Scalmalloy® concept was pioneered by Frank Palm at Airbus (Schmidtke et al. Citation2011). As moderate-strength alloys, they have shown potential as structural materials. With Sc and/or Zr addition in AlMg alloys, Al3Sc, Al3Zr and /or Al3(Scx, Zr1–x) have been demonstrated in the literature (Wang et al. Citation2022). The consequent grain refinement makes it possible for columnar to equiaxed transition of grains in the melt pool and improves the feasibility of LPBF. Moreover, these precipitates allow the alloys to be heat treatable, further improving the mechanical properties (Zhang, Gu, and Dai Citation2022). However, the material modification was not sufficient to assure a uniform and fine microstructure as the number density of the precipitates is not uniform throughout the microstructure. A bimodal microstructure, which consists of ultrafine grains along the melt pool boundary and relatively coarse grains inside the melt pool, has been in the majority of published works (Spierings et al. Citation2017; He et al. Citation2021; Zhou et al. Citation2019; Ma et al. Citation2020), as shown in . As Al3Sc was characterised by TEM, a schematic of how the bimodal microstructure forms was illustrated in . Spierings et al. (Citation2017) attributed the phenomenon to the dissolution of Al3(Sc,Zr) particles at a temperature of over 800°C based on the Scheil simulation. It was further confirmed that the precipitation of Al3(Scx,Zr1–x) particles occurs at low laser scan speeds while at high scanning speeds Sc and Zr are mainly in solid solution (Spierings et al. Citation2018). Yang et al. (Citation2018) demonstrated similar microstructure in their investigation. The authors claimed that the fully equiaxed grain structure can be achieved in the remelting zone of the melt pool because of a larger population of potential nuclei. Therefore, they obtained the microstructure with equiaxed grains fraction increasing from 64.2% to 100% by raising the applied VED from 77.1 to 154.2 J/mm3. Ekubaru et al. (2022) attempted to tune the microstructure via decreasing hatch spacing to increase the track-track melt pool boundary. Decreasing the hatch spacing from 100 μm down to 60 μm, the volume fraction of ultrafine grains increased from 34.6% to 59.5%, resulting in an increase of UTS from 296 to 380 MPa. Other researchers made efforts to achieve high fraction of equiaxed grains via materials preparation. Li et al. (Citation2022) claimed that modification by ScH3 and ZrH2 was more efficient than pre-alloying under the same process parameters although high porosity was generated. For the moment, systematic investigation is still on the way.
Figure 12. Microstructure of the as-built Al-5024 alloy fabricated by LPBF. (a) EBSD orientation map indicating the bimodal structure. (b) HAADF-STEM image of a fine equiaxed grain region with corresponding EDX elemental mapping. (c) Bright-field TEM image within a fine Al equiaxed grain region. (d) The selected area diffraction (SAD) from a single Al grain shown in (c), indicating single-phase Al in the [001] orientation. Reproduced from He et al. (Citation2021).
![Figure 12. Microstructure of the as-built Al-5024 alloy fabricated by LPBF. (a) EBSD orientation map indicating the bimodal structure. (b) HAADF-STEM image of a fine equiaxed grain region with corresponding EDX elemental mapping. (c) Bright-field TEM image within a fine Al equiaxed grain region. (d) The selected area diffraction (SAD) from a single Al grain shown in (c), indicating single-phase Al in the [001] orientation. Reproduced from He et al. (Citation2021).](/cms/asset/86b6395c-1987-4946-9ba3-1dc3472c6f76/nvpp_a_2125880_f0012_oc.jpg)
Figure 13. Schematic of early-stage and later-stage solidification within the melt pool, indicating how Sc atom distribution leads to a bimodal structure in the melt pool. Reproduced from He et al. (Citation2021).
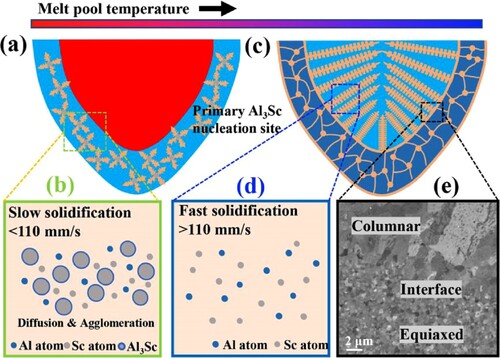
The optimum of Sc and/or Zr content has not been well investigated due to the high cost of powder preparation and difficulty in composition control. Zhou et al. (Citation2021) proved that 1 wt% of Zr alloying broadened the LPBF processing window compared to the 0.7 wt% of Zr alloying and increased UTS of the LPBF Zr-modified AA5083 alloy. However, the optimum of Zr content was not given. Besides, since Sc has been classified as a critical raw material by European Commission due to its high cost and supply risk (Belelli et al. Citation2022), researchers have been working on new compositions with low content of Sc and alternative alloying elements (Guo et al. Citation2022; Rakhmonov, Weiss, and Dunand Citation2022) in recent years.
3.3. Al–Cu alloys and Al–Zn–Mg alloys
The high strength Al alloys, including 2xxx and 7xxx alloys, have shown significant potential for applications in aerospace industries. However, they have shortcomings for printing due to the solidification cracking. Three main solutions were attempted and summarised as follows.
The processing parameters especially substrate pre-heating (Uddin et al. Citation2018; Kaufmann et al. Citation2016) and supportive structure construction (Karg et al. Citation2017) were found to relieve the thermal stress of the built parts and eliminate the cracks. Extremely high and low VED can lead to the dramatic reduction in crack density because of the stress release caused by the large number of keyhole or lack of fusion pores (Li et al. Citation2022; Wang et al. Citation2022). Large columnar grains dominate the microstructure under these conditions.
A second method is narrowing down the freezing intervals. Inspired by the research on Al–Si alloy, silicon additives were of primary choice. In the study of Li et al. (Citation2021), 3.74 wt% Si was claimed to result in a minimum crack susceptibility, while Otani and Sasaki (Citation2020) demonstrated that 5 wt% was the optimum content. Zhou et al. (Citation2020) further cooperate Si and TiB2 and eliminated the cracks, achieving a UTS of 556 MPa as nucleation was enhanced meanwhile. Yang et al. (Citation2022) reported that the cellular Al–Mg2Si eutectic resulting from the segregation contributes to the low hot-tearing susceptibility of LPBF Al–Mg–Zn–Si alloys. Y was also revealed as an effective alloying element for the solidification crack elimination, which is mainly attributed to the combination of the narrowed brittle temperature range, the decreased solidification crack susceptibility index, and the refined grains (Chen et al. Citation2022).
The last approach is the most effective one, i.e. modification with solute elements or introduction of inoculants. Sc and Zr are still the most popular and effective elements as equiaxed fine grains in the melt pool can be assured with proper parameters. Thapliyal et al. (Citation2020) established a closed-loop integrated computational material engineering (ICME) anchored methodology to develop new high-strength aluminium alloys which can be fabricated with the LPBF technique. Finalisation of Al–1.5Cu–0.8Sc–0.4Zr composition and prediction of solidification behaviour and mechanical properties were done using calculation of phase diagrams (CALPHAD) and analytical tools and further verified experimentally (Agrawal et al. Citation2021). Recently, more and more alloying elements and particles have been investigated, such as Ti (Tan et al. Citation2021; Tan et al. Citation2020), Ta (Li et al. Citation2022), Er (Zhang et al. Citation2022), CaB6 (Mair et al. Citation2021) and so on. However, fully equiaxed fine grains require special attention for powder preparation (Zhang et al. Citation2022).
4. Conclusion and an outlook
In summary, growing attention has been drawn to the uptake of LPBF for the fabrication of aluminium alloys. The thermal dynamics of LPBF allows rapid melting and solidifying of powder materials and the subsequent intrinsic heat treatment. Typical microstructure includes columnar grains along the building direction and strong crystallographic texture, which results in anisotropy in the mechanical properties of the parts. Grain refinement resulting in more fraction of equiaxed grains favour the mechanical performance. For aluminium alloys with low strength, the major study on near eutectic Al–Si alloys with good printability was focused on processing parameters previously. Recently growing number of studies were performed on the columnar to equiaxed transition to achieve high UTS and isotropy. Grain refining by inoculants, the introduction of reinforced aluminium matrix composite, and alloying with Ni and Cu elements were explored. For moderate strength Al–Mg alloys, solidification crack was mainly eliminated by Sc and/or Zr alloying. A bimodal microstructure was reported and tailored by parameter manipulation. For high strength Al–Cu and Al–Zn–Mg alloys, three approaches were attempted to refine the grain and improve the feasibility of LPBF: (1) optimising parameters by extremely high or low energy input, substrate preheating and supportive structure construction; (2) narrowing down the freezing range; (3) inoculants treatments.
For future research prospects, the manipulation of the solidification process especially heterogeneous nucleation will be increasingly promising for aluminium applications via LPBF fabrication. Although various elements or ex-situ inoculants have been studied, how to achieve a uniform distribution of nuclei in the melt pool and to increase the nucleation efficiency is still challenging. To solve this issue, the solidification behaviour must be thoroughly understood as the melt pool exists locally within very short time. Materials design for LPBF is also vital for a wider application. The solidification path of these newly designed materials requires intensive research.
Disclosure statement
No potential conflict of interest was reported by the author(s).
Additional information
Funding
Notes on contributors
Zhen Xiao
Zhen Xiao is a lecturer at the School of Transportation and Vehicle Engineering, Shandong University of Technology. His research interests cover additive manufacturing and vehicle dynamics control.
Wenhui Yu
Wenhui Yu is a lecturer at the Shandong Provincial Key Laboratory of Precision Manufacturing and Non-traditional Machining, School of Mechanical Engineering, Shandong University of Technology. Her research interests include additive manufacturing and laser manufacturing.
Hongxun Fu
Hongxun Fu is an associate professor at the School of Transportation and Vehicle Engineering, Shandong University of Technology. His research interests cover additive manufacturing and vehicle dynamics control.
Yaoji Deng
Yaoji Deng is a lecturer at the School of Mechanical Engineering, Yangzhou University. His main research interests include non-pneumatic/smart tires and vehicle dynamics control.
Yongling Wu
Yongling Wu is a professor at Shandong Provincial Key Laboratory of Precision Manufacturing and Non-traditional Machining, School of Mechanical Engineering, Shandong University of Technology. Her research area is in surface engineering and characterisation of materials.
Hongyu Zheng
Hongyu Zheng is the dean of the School of Mechanical Engineering, Shandong University of Technology. His research interests include laser micro/nano-manufacturing, surface engineering and additive manufacturing.
References
- Agrawal, Priyanka, Sanya Gupta, Saket Thapliyal, Shivakant Shukla, Ravi Sankar Haridas, and Rajiv S. Mishra. 2021. “Additively Manufactured Novel Al–Cu–Sc–Zr Alloy: Microstructure and Mechanical Properties.” Additive Manufacturing 37: 101623. doi:10.1016/j.addma.2020.101623.
- Ashby, Ava, Gabe Guss, Rishi K. Ganeriwala, Aiden A. Martin, Philip J. DePond, Dave J. Deane, Manyalibo J. Matthews, and Clara L. Druzgalski. 2022. “Thermal History and High-Speed Optical Imaging of Overhang Structures During Laser Powder Bed Fusion: A Computational and Experimental Analysis.” Additive Manufacturing 53: 102669. doi:10.1016/j.addma.2022.102669.
- Avateffazeli, M., P. E. Carrion, B. Shachi-Amirkhiz, H. Pirgazi, M. Mohammadi, N. Shamsaei, and M. Haghshenas. 2022. “Correlation Between Tensile Properties,: Microstructure, and Processing Routes of an Al–Cu–Mg–Ag–TiB2 (A205) Alloy: Additive Manufacturing and Casting.” Materials Science and Engineering: A 841: 142989. doi:10.1016/j.msea.2022.142989.
- Bai, Xian-Ming, and Mo Li. 2006. “Calculation of Solid–Liquid Interfacial Free Energy: A Classical Nucleation Theory Based Approach.” The Journal of Chemical Physics 124 (12): 124707. doi:10.1063/1.2184315.
- Belelli, F., R. Casati, C. Andrianopoli, F. Cuccaro, and M. Vedani. 2022. “Investigation and Characterization of an Al–Mg–Zr–Sc Alloy with Reduced Sc Content for Laser Powder bed Fusion.” Journal of Alloys and Compounds 924: 166519. doi:10.1016/j.jallcom.2022.166519.
- Boettinger, W. J., S. R. Coriell, A. L. Greer, A. Karma, W. Kurz, M. Rappaz, and R. Trivedi. 2000. “Solidification Microstructures: Recent Developments,: Future Directions.” Acta Materialia 48 (1): 43–70. doi:10.1016/S1359-6454(99)00287-6.
- Bosio, Federico, Haopeng Shen, Yang Liu, Mariangela Lombardi, Paul Rometsch, Xinhua Wu, Yuman Zhu, and Aijun Huang. 2021. “Production Strategy for Manufacturing Large-Scale AlSi10Mg Components by Laser Powder Bed Fusion.” JOM Journal of the Minerals Metals and Materials Society 73 (3): 770–780. doi:10.1007/s11837-020-04523-8.
- Bradford, Robyn L., Li Cao, Don Klosterman, Fred Herman, Lewis Forman, and Charles Browning. 2021. “A Metal–Metal Powder Formulation Approach for Laser Additive Manufacturing of Difficult-to-Print High-Strength Aluminum Alloys.” Materials Letters 300: 130113. doi:10.1016/j.matlet.2021.130113.
- Casati, R., M. Coduri, S. Checchia, and M. Vedani. 2021. “Insight Into the Effect of Different Thermal Treatment Routes on the Microstructure of AlSi7Mg Produced by Laser Powder bed Fusion.” Materials Characterization 172: 110881. doi:10.1016/j.matchar.2021.110881.
- Chen, Yuming, Linzhi Wang, Zhongxue Feng, and Wanneng Zhang. 2021. “Effects of Heat Treatment on Microstructure and Mechanical Properties of SLMed Sc-Modified AlSi10Mg Alloy.” Progress in Natural Science: Materials International 31 (5): 714–721. doi:10.1016/j.pnsc.2021.08.003.
- Chen, Ying, Chuangwei Xiao, Shang Zhu, Zhiwen Li, Wenxin Yang, Feng Zhao, Shengfu Yu, and Yusheng Shi. 2022. “Microstructure Characterization and Mechanical Properties of Crack-Free Al-Cu–Mg–Y Alloy Fabricated by Laser Powder bed Fusion.” Additive Manufacturing 58: 103006. doi:10.1016/j.addma.2022.103006.
- Choong, Yu Ying Clarrisa, Hong Wei Tan, Deven C. Patel, Wan Ting Natalie Choong, Chun-Hsien Chen, Hong Yee Low, Ming Jen Tan, Chandrakant D. Patel, and Chee Kai Chua. 2020. “The Global Rise of 3D Printing During the COVID-19 Pandemic.” Nature Reviews Materials 5 (9): 637–639. doi:10.1038/s41578-020-00234-3.
- Coen, Viktor, Louca Goossens, and Brecht Van Hooreweder. 2022. “Methodology and Experimental Validation of Analytical Melt Pool Models for Laser Powder bed Fusion.” Journal of Materials Processing Technology 304: 117547. doi:10.1016/j.jmatprotec.2022.117547.
- Collins, P. C., D. A. Brice, P. Samimi, I. Ghamarian, and H. L. Fraser. 2016. “Microstructural Control of Additively Manufactured Metallic Materials.” Annual Review of Materials Research 46 (1): 63–91. doi:10.1146/annurev-matsci-070115-031816.
- Cunningham, Ross, Cang Zhao, Niranjan Parab, Christopher Kantzos, Joseph Pauza, Kamel Fezzaa, Tao Sun, and Anthony D. Rollett. 2019. “Keyhole Threshold and Morphology in Laser Melting Revealed by Ultrahigh-Speed x-ray Imaging.” Science 363 (6429): 849–852. doi:10.1126/science.aav4687.
- Damon, James, Robin Koch, Daniel Kaiser, Gregor Graf, Stefan Dietrich, and Volker Schulze. 2019. “Process Development and Impact of Intrinsic Heat Treatment on the Mechanical Performance of Selective Laser Melted AISI 4140.” Additive Manufacturing 28: 275–284. doi:10.1016/j.addma.2019.05.012.
- Dinda, G. P., A. K. Dasgupta, and J. Mazumder. 2012. “Texture Control During Laser Deposition of Nickel-Based Superalloy.” Scripta Materialia 67 (5): 503–506. doi:10.1016/j.scriptamat.2012.06.014.
- Ekubaru, Yusufu, Ozkan Gokcekaya, Takuya Ishimoto, Kazuhisa Sato, Koki Manabe, Pan Wang, and Takayoshi Nakano. 2022. “Excellent Strength–Ductility Balance of Sc–Zr–Modified Al–Mg Alloy by Tuning Bimodal Microstructure via Hatch Spacing in Laser Powder bed Fusion.” Materials & Design 221: 110976. doi:10.1016/j.matdes.2022.110976.
- Fan, Zhenhua, Xingchen Yan, Zhiyong Fu, Ben Niu, Junfu Chen, Yongjun Hu, Cheng Chang, and Jianglong Yi. 2021. “In Situ Formation of D022-Al3Ti During Selective Laser Melting of Nano-TiC/AlSi10Mg Alloy Prepared by Electrostatic Self-Assembly.” Vacuum 188: 110179. doi:10.1016/j.vacuum.2021.110179.
- Fiocchi, J., A. Tuissi, and C. A. Biffi. 2021. “Heat Treatment of Aluminium Alloys Produced by Laser Powder bed Fusion: A Review.” Materials & Design 204: 109651. doi:10.1016/j.matdes.2021.109651.
- Garmendia, X., S. Chalker, M. Bilton, C. J. Sutcliffe, and P. R. Chalker. 2020. “Microstructure and Mechanical Properties of Cu-Modified AlSi10Mg Fabricated by Laser-Powder Bed Fusion.” Materialia 9: 100590. doi:10.1016/j.mtla.2020.100590.
- Ghoncheh, M. H., M. Sanjari, A. Shojaei Zoeram, E. Cyr, B. Shalchi Amirkhiz, A. Lloyd, M. Haghshenas, and M. Mohammadi. 2021. “On the Microstructure and Solidification Behavior of new Generation Additively Manufactured Al–Cu–Mg–Ag–Ti–B Alloys.” Additive Manufacturing 37: 101724. doi:10.1016/j.addma.2020.101724.
- Ghosh, Abhi, Xianglong Wang, Anne-Marie Kietzig, and Mathieu Brochu. 2018. “Layer-by-Layer Combination of Laser Powder bed Fusion (LPBF) and Femtosecond Laser Surface Machining of Fabricated Stainless Steel Components.” Journal of Manufacturing Processes 35: 327–336. doi:10.1016/j.jmapro.2018.08.016.
- Gu, Dongdong, Xinyu Shi, Reinhart Poprawe, David L. Bourell, Rossitza Setchi, and Jihong Zhu. 2021. “Material-structure-performance Integrated Laser-Metal Additive Manufacturing.” Science 372 (6545): eabg1487. doi:10.1126/science.abg1487.
- Guan, Ren-Guo, and Di Tie. 2017. “A Review on Grain Refinement of Aluminum Alloys: Progresses,: Challenges and Prospects.” Acta Metallurgica Sinica (English Letters) 30 (5): 409–432. doi:10.1007/s40195-017-0565-8.
- Guo, Meng, Kai Liu, Jingjia Sun, and Dongdong Gu. 2022. “Laser Powder Bed Fusion of a Novel Nano-Modified Tungsten Alloy with Refined Microstructure and Enhanced Strength.” Materials Science and Engineering: A 843: 143096. doi:10.1016/j.msea.2022.143096.
- Guo, Yanwu, Wu Wei, Wei Shi, Xiaorong Zhou, Shengping Wen, Xiaolan Wu, Kunyuan Gao, et al. 2022. “Microstructure and Mechanical Properties of Al–Mg–Mn–Er–Zr Alloys Fabricated by Laser Powder bed Fusion.” Materials & Design 222: 111064. doi:10.1016/j.matdes.2022.111064.
- He, Peidong, Qian Liu, Jamie J. Kruzic, and Xiaopeng Li. 2022. “Machine-learning Assisted Additive Manufacturing of a TiCN Reinforced AlSi10Mg Composite with Tailorable Mechanical Properties.” Materials Letters 307: 131018. doi:10.1016/j.matlet.2021.131018.
- He, Peidong, Richard F. Webster, Vladislav Yakubov, Hui Kong, Qin Yang, Shuke Huang, Michael Ferry, Jamie J. Kruzic, and Xiaopeng Li. 2021. “Fatigue and Dynamic Aging Behavior of a High Strength Al-5024 Alloy Fabricated by Laser Powder bed Fusion Additive Manufacturing.” Acta Materialia 220: 117312. doi:10.1016/j.actamat.2021.117312.
- Hesselmann, Marcel, Daniel Knoop, Jérémy Epp, Volker Uhlenwinkel, Axel von Hehl, and Anastasiya Toenjes. 2022. “Effect of Precipitation-Forming Elements in a Near-Eutectic Al–Ce Alloy for Laser Powder Bed Fusion.” Additive Manufacturing 57: 102959. doi:10.1016/j.addma.2022.102959.
- Hojjatzadeh, S., H. Mohammad, Niranjan D. Parab, Wentao Yan, Qilin Guo, Lianghua Xiong, Cang Zhao, Minglei Qu, et al. 2019. “Pore Elimination Mechanisms During 3D Printing of Metals.” Nature Communications 10 (1): 3088. doi:10.1038/s41467-019-10973-9.
- Hyer, Holden, Le Zhou, Abhishek Mehta, Sharon Park, Thinh Huynh, Shutao Song, Yuanli Bai, Kyu Cho, Brandon McWilliams, and Yongho Sohn. 2021. “Composition-dependent Solidification Cracking of Aluminum-Silicon Alloys During Laser Powder bed Fusion.” Acta Materialia 208: 116698. doi:10.1016/j.actamat.2021.116698.
- Jandaghi, Mohammad Reza, Alberta Aversa, Diego Manfredi, Flaviana Calignano, Luca Lavagna, and Matteo Pavese. 2022. “In Situ Alloying of AlSi10Mg–5 wt% Ni Through Laser Powder bed Fusion and Subsequent Heat Treatment.” Journal of Alloys and Compounds 904: 164081. doi:10.1016/j.jallcom.2022.164081.
- Jiang, L. Y., T. T. Liu, C. D. Zhang, K. Zhang, M. C. Li, T. Ma, and W. H. Liao. 2018. “Preparation and Mechanical Properties of CNTs-AlSi10Mg Composite Fabricated via Selective Laser Melting.” Materials Science and Engineering: A 734: 171–177. doi:10.1016/j.msea.2018.07.092.
- Jiang, Runbo, Amir Mostafaei, Ziheng Wu, Ann Choi, Pin-Wen Guan, Markus Chmielus, and Anthony D. Rollett. 2020. “Effect of Heat Treatment on Microstructural Evolution and Hardness Homogeneity in Laser Powder bed Fusion of Alloy 718.” Additive Manufacturing 35: 101282. doi:10.1016/j.addma.2020.101282.
- Joshi, Sunil C., and Abdullah A. Sheikh. 2015. “3D Printing in Aerospace and its Long-Term Sustainability.” Virtual and Physical Prototyping 10 (4): 175–185. doi:10.1080/17452759.2015.1111519.
- Karg, Michael Cornelius Hermann, Bhrigu Ahuja, Sebastian Wiesenmayer, Sergey Vyacheslavovich Kuryntsev, and Michael Schmidt. 2017. “Effects of Process Conditions on the Mechanical Behavior of Aluminium Wrought Alloy EN AW-2219 (AlCu6Mn) Additively Manufactured by Laser Beam Melting in Powder Bed.” Micromachines 8 (1): 23. doi:10.3390/mi8010023.
- Karimi, Paria, Esmaeil Sadeghi, Joakim Ålgårdh, Ali Keshavarzkermani, Reza Esmaeilizadeh, Ehsan Toyserkani, and Joel Andersson. 2021. “Columnar-to-equiaxed Grain Transition in Powder bed Fusion via Mimicking Casting Solidification and Promoting in Situ Recrystallization.” Additive Manufacturing 46: 102086. doi:10.1016/j.addma.2021.102086.
- Kaufmann, N., M. Imran, T. M. Wischeropp, C. Emmelmann, S. Siddique, and F. Walther. 2016. “Influence of Process Parameters on the Quality of Aluminium Alloy EN AW 7075 Using Selective Laser Melting (SLM).” Physics Procedia 83: 918–926. doi:10.1016/j.phpro.2016.08.096.
- Kempf, A., and K. Hilgenberg. 2020. “Influence of sub-Cell Structure on the Mechanical Properties of AlSi10Mg Manufactured by Laser Powder bed Fusion.” Materials Science and Engineering: A 776: 138976. doi:10.1016/j.msea.2020.138976.
- Khorasani, Amir Mahyar, Ian Gibson, AmirHossein Ghasemi, and Alireza Ghaderi. 2020. “Modelling of Laser Powder bed Fusion Process and Analysing the Effective Parameters on Surface Characteristics of Ti–6Al–4V.” International Journal of Mechanical Sciences 168: 105299. doi:10.1016/j.ijmecsci.2019.105299.
- Kimura, Masaaki, Akihiro Hirayama, Junya Yoshioka, Hosei Maekawa, Masahiro Kusaka, Koichi Kaizu, and Tsuyoshi Takahashi. 2020. “Mechanical Properties of AlSi12 Alloy Manufactured by Laser Powder Bed Fusion Technique.” Journal of Failure Analysis and Prevention 20 (6): 1884–1895. doi:10.1007/s11668-020-00998-4.
- Kimura, Takahiro, Takayuki Nakamoto, Masataka Mizuno, and Hideki Araki. 2017. “Effect of Silicon Content on Densification, Mechanical and Thermal Properties of Al-xSi Binary Alloys Fabricated Using Selective Laser Melting.” Materials Science and Engineering: A 682: 593–602. doi:10.1016/j.msea.2016.11.059.
- Konopatsky, Anton S., Dmitry G. Kvashnin, Shakti Corthay, Ivan Boyarintsev, Konstantin L. Firestein, Anton Orekhov, Natalya Arkharova, Dmitry V. Golberg, and Dmitry V. Shtansky. 2021. “Microstructure Evolution During AlSi10Mg Molten Alloy/BN Microflake Interactions in Metal Matrix Composites Obtained Through 3D Printing.” Journal of Alloys and Compounds 859: 157765. doi:10.1016/j.jallcom.2020.157765.
- Kou, Sindo. 2015. “A Criterion for Cracking During Solidification.” Acta Materialia 88: 366–374. doi:10.1016/j.actamat.2015.01.034.
- Kuo, C. N., C. K. Chua, P. C. Peng, Y. W. Chen, S. L. Sing, S. Huang, and Y. L. Su. 2020. “Microstructure Evolution and Mechanical Property Response via 3D Printing Parameter Development of Al–Sc Alloy.” Virtual and Physical Prototyping 15 (1): 120–129. doi:10.1080/17452759.2019.1698967.
- Lefebvre, Williams, Grégory Rose, Pauline Delroisse, Eric Baustert, Fabien Cuvilly, and Aude Simar. 2021. “Nanoscale Periodic Gradients Generated by Laser Powder bed Fusion of an AlSi10Mg Alloy.” Materials & Design 197: 109264. doi:10.1016/j.matdes.2020.109264.
- Leirmo, Julie Langedahl. 2021. “High Strength Aluminium Alloys in Laser-Based Powder Bed Fusion – a Review.” Procedia CIRP 104: 1747–1752. doi:10.1016/j.procir.2021.11.294.
- Leung, Chu Lun Alex, Sebastian Marussi, Robert C. Atwood, Michael Towrie, Philip J. Withers, and Peter D. Lee. 2018. “In Situ X-ray Imaging of Defect and Molten Pool Dynamics in Laser Additive Manufacturing.” Nature Communications 9 (1): 1355. doi:10.1038/s41467-018-03734-7.
- Li, Chonggui, Shuai Sun, Youfeng Zhang, Chuanming Liu, Peiran Deng, Ming Zeng, Feifei Wang, Pan Ma, Wenge Li, and You Wang. 2019. “Effects of Laser Processing Parameters on Microstructure and Mechanical Properties of Additively Manufactured AlSi10Mg Alloys Reinforced by TiC.” The International Journal of Advanced Manufacturing Technology 103 (5): 3235–3246. doi:10.1007/s00170-019-04001-9.
- Li, E. L., L. Wang, A. B. Yu, and Z. Y. Zhou. 2021. “A Three-Phase Model for Simulation of Heat Transfer and Melt Pool Behaviour in Laser Powder bed Fusion Process.” Powder Technology 381: 298–312. doi:10.1016/j.powtec.2020.11.061.
- Li, Gan, Xinwei Li, Chuan Guo, Yang Zhou, Qiyang Tan, Wenying Qu, Xinggang Li, Xiaogang Hu, Ming-Xing Zhang, and Qiang Zhu. 2022. “Investigation Into the Effect of Energy Density on Densification, Surface Roughness and Loss of Alloying Elements of 7075 Aluminium Alloy Processed by Laser Powder bed Fusion.” Optics & Laser Technology 147: 107621. doi:10.1016/j.optlastec.2021.107621.
- Li, Guichuan, Suraj Dinkar Jadhav, Arturo Martín, Maria L. Montero-Sistiaga, Jeroen Soete, Maria San Sebastian, Carmen M. Cepeda-Jiménez, and Kim Vanmeensel. 2021. “Investigation of Solidification and Precipitation Behavior of Si-Modified 7075 Aluminum Alloy Fabricated by Laser-Based Powder Bed Fusion.” Metallurgical and Materials Transactions A 52 (1): 194–210. doi:10.1007/s11661-020-06073-9.
- Li, Xiang, Yunzhong Liu, and Zhiguang Zhou. 2022. “Grain Refinement and Performance Enhancement of Laser Powder bed Fusion in-Situ Processed Al-Mg Alloy Modified by ScH3 and ZrH2.” Materials Characterization 190: 112068. doi:10.1016/j.matchar.2022.112068.
- Li, Xinwei, Dawang Li, Gan Li, and Qizhou Cai. 2022. “Microstructure, Mechanical Properties, Aging Behavior, and Corrosion Resistance of a Laser Powder bed Fusion Fabricated Al–Zn–Mg–Cu–Ta Alloy.” Materials Science and Engineering: A 832: 142364. doi:10.1016/j.msea.2021.142364.
- Li, Xuxiao, and Wenda Tan. 2018. “Numerical Investigation of Effects of Nucleation Mechanisms on Grain Structure in Metal Additive Manufacturing.” Computational Materials Science 153: 159–169. doi:10.1016/j.commatsci.2018.06.019.
- Liu, Jian, and Albert C. To. 2017. “Quantitative Texture Prediction of Epitaxial Columnar Grains in Additive Manufacturing Using Selective Laser Melting.” Additive Manufacturing 16: 58–64. doi:10.1016/j.addma.2017.05.005.
- Liu, Mengna, Kaiwen Wei, Runsen Zhou, Xiaoze Yue, and Xiaoyan Zeng. 2022. “Microstructure and Mechanical Property of High Power Laser Powder bed Fusion AlSi10Mg Alloy Before and After T6 Heat Treatment.” Virtual and Physical Prototyping 17 (4): 749–767. doi:10.1080/17452759.2022.2068294.
- Liu, Qian, Hongkun Wu, Moses J. Paul, Peidong He, Zhongxiao Peng, Bernd Gludovatz, Jamie J. Kruzic, Chun H. Wang, and Xiaopeng Li. 2020. “Machine-learning Assisted Laser Powder bed Fusion Process Optimization for AlSi10Mg: New Microstructure Description Indices and Fracture Mechanisms.” Acta Materialia 201: 316–328. doi:10.1016/j.actamat.2020.10.010.
- Lough, Cody S., Xin Wang, Christopher C. Smith, Robert G. Landers, Douglas A. Bristow, James A. Drallmeier, Ben Brown, and Edward C. Kinzel. 2020. “Correlation of SWIR Imaging with LPBF 304L Stainless Steel Part Properties.” Additive Manufacturing 35: 101359. doi:10.1016/j.addma.2020.101359.
- Lu, Zhao, Lijun Zhang, Jiang Wang, Qingrong Yao, Guanghui Rao, and Huaiying Zhou. 2019. “Understanding of Strengthening and Toughening Mechanisms for Sc-Modified Al-Si-(Mg) Series Casting Alloys Designed by Computational Thermodynamics.” Journal of Alloys and Compounds 805: 415–425. doi:10.1016/j.jallcom.2019.07.069.
- Ma, Rulong, Chaoqun Peng, Zhiyong Cai, Richu Wang, Zhaohui Zhou, Xiaogeng Li, and Xuanyang Cao. 2020. “Effect of Bimodal Microstructure on the Tensile Properties of Selective Laser Melt Al–Mg–Sc–Zr Alloy.” Journal of Alloys and Compounds 815: 152422. doi:10.1016/j.jallcom.2019.152422.
- Mair, Philipp, Valerie Sue Goettgens, Tobias Rainer, Nikolaus Weinberger, Ilse Letofsky-Papst, Stefan Mitsche, and Gerhard Leichtfried. 2021. “Laser Powder bed Fusion of Nano-CaB6 Decorated 2024 Aluminum Alloy.” Journal of Alloys and Compounds 863: 158714. doi:10.1016/j.jallcom.2021.158714.
- Mair, Philipp, Lukas Kaserer, Jakob Braun, Janko Stajkovic, Christian Klein, David Schimbäck, Lukas Perfler, Evgeny Zhuravlev, Olaf Kessler, and Gerhard Leichtfried. 2022. “Dependence of Mechanical Properties and Microstructure on Solidification Onset Temperature for Al2024–CaB6 Alloys Processed Using Laser Powder bed Fusion.” Materials Science and Engineering: A 833: 142552. doi:10.1016/j.msea.2021.142552.
- Makoana, Nkutwane Washington, Ina Yadroitsava, Heinrich Möller, and Igor Yadroitsev. 2018. “Characterization of 17-4PH Single Tracks Produced at Different Parametric Conditions Towards Increased Productivity of LPBF Systems—The Effect of Laser Power and Spot Size Upscaling.” Metals 8 (7): 475.
- Maleki, E., S. Bagherifard, S. M. J. Razavi, M. Bandini, A. du Plessis, F. Berto, and M. Guagliano. 2022. “On the Efficiency of Machine Learning for Fatigue Assessment of Post-Processed Additively Manufactured AlSi10Mg.” International Journal of Fatigue 160: 106841. doi:10.1016/j.ijfatigue.2022.106841.
- Marola, Silvia, Dario Gianoglio, Federico Bosio, Alberta Aversa, Massimo Lorusso, Diego Manfredi, Mariangela Lombardi, and Livio Battezzati. 2020. “Alloying AlSi10Mg and Cu Powders in Laser Single Scan Tracks, Melt Spinning, and Laser Powder Bed Fusion.” Journal of Alloys and Compounds 821: 153538. doi:10.1016/j.jallcom.2019.153538.
- Martin, John H., Brennan D. Yahata, Jacob M. Hundley, Justin A. Mayer, Tobias A. Schaedler, and Tresa M. Pollock. 2017. “3D Printing of High-Strength Aluminium Alloys.” Nature 549 (7672): 365–369. doi:10.1038/nature23894.
- Megahed, Mustafa, Hans-Wilfried Mindt, Jöerg Willems, Paul Dionne, Lars Jacquemetton, James Craig, Piyush Ranade, and Alonso Peralta. 2019. “LPBF Right the First Time—the Right Mix Between Modeling and Experiments.” Integrating Materials and Manufacturing Innovation 8 (2): 194–216. doi:10.1007/s40192-019-00133-8.
- Metelkova, Jitka, Lars Vanmunster, Han Haitjema, and Brecht Van Hooreweder. 2021. “Texture of Inclined up-Facing Surfaces in Laser Powder bed Fusion of Metals.” Additive Manufacturing 42: 101970. doi:10.1016/j.addma.2021.101970.
- Moyle, M. S., N. Haghdadi, W. J. Davids, X. Z. Liao, S. P. Ringer, and S. Primig. 2022. “Evidence of in-Situ Cu Clustering as a Function of Laser Power During Laser Powder bed Fusion of 17–4 PH Stainless Steel.” Scripta Materialia 219: 114896. doi:10.1016/j.scriptamat.2022.114896.
- Nayak, S. K., S. K. Mishra, C. P. Paul, A. N. Jinoop, and K. S. Bindra. 2020. “Effect of Energy Density on Laser Powder bed Fusion Built Single Tracks and Thin Wall Structures with 100 µm Preplaced Powder Layer Thickness.” Optics & Laser Technology 125: 106016. doi:10.1016/j.optlastec.2019.106016.
- Otani, Yuki, and Shinya Sasaki. 2020. “Effects of the Addition of Silicon to 7075 Aluminum Alloy on Microstructure,: Mechanical Properties, and Selective Laser Melting Processability.” Materials Science and Engineering: A 777: 139079. doi:10.1016/j.msea.2020.139079.
- Pant, Prabhat, Filomena Salvemini, Sebastian Proper, Vladimir Luzin, Kjell Simonsson, Sören Sjöström, Seyed Hosseini, Ru Lin Peng, and Johan Moverare. 2022. “A Study of the Influence of Novel Scan Strategies on Residual Stress and Microstructure of L-Shaped LPBF IN718 Samples.” Materials & Design 214: 110386. doi:10.1016/j.matdes.2022.110386.
- Pantawane, Mangesh V., Yee-Hsien Ho, Sameehan S. Joshi, and Narendra B. Dahotre. 2020. “Computational Assessment of Thermokinetics and Associated Microstructural Evolution in Laser Powder Bed Fusion Manufacturing of Ti6Al4V Alloy.” Scientific Reports 10 (1): 7579. doi:10.1038/s41598-020-63281-4.
- Pérez-Ruiz, José David, Luis Norberto López de Lacalle, Gorka Urbikain, Octavio Pereira, Silvia Martínez, and Jorge Bris. 2021. “On the Relationship Between Cutting Forces and Anisotropy Features in the Milling of LPBF Inconel 718 for Near net Shape Parts.” International Journal of Machine Tools and Manufacture 170: 103801. doi:10.1016/j.ijmachtools.2021.103801.
- Platl, Jan, Sabine Bodner, Christina Hofer, Andreas Landefeld, Harald Leitner, Christoph Turk, Marc-André Nielsen, et al. 2022. “Cracking Mechanism in a Laser Powder bed Fused Cold-Work Tool Steel: The Role of Residual Stresses, Microstructure and Local Elemental Concentrations.” Acta Materialia 225: 117570. doi:10.1016/j.actamat.2021.117570.
- Prasad, Arvind, Lang Yuan, Peter Lee, Mitesh Patel, Dong Qiu, Mark Easton, and David StJohn. 2020. “Towards Understanding Grain Nucleation Under Additive Manufacturing Solidification Conditions.” Acta Materialia 195: 392–403. doi:10.1016/j.actamat.2020.05.012.
- Qi, Yang, Zhiheng Hu, Hu Zhang, Xiaojia Nie, Changchun Zhang, and Haihong Zhu. 2021. “High Strength Al–Li Alloy Development for Laser Powder bed Fusion.” Additive Manufacturing 47: 102249. doi:10.1016/j.addma.2021.102249.
- Qin, Hong, Vahid Fallah, Qingshan Dong, Mathieu Brochu, Mark R. Daymond, and Mark Gallerneault. 2018. “Solidification Pattern, Microstructure and Texture Development in Laser Powder Bed Fusion (LPBF) of Al10SiMg Alloy.” Materials Characterization 145: 29–38. doi:10.1016/j.matchar.2018.08.025.
- Qu, Shuo, Junhao Ding, Jin Fu, Mingwang Fu, Baicheng Zhang, and Xu Song. 2021. “High-precision Laser Powder bed Fusion Processing of Pure Copper.” Additive Manufacturing 48: 102417. doi:10.1016/j.addma.2021.102417.
- Rakhmonov, Jovid U., David Weiss, and David C. Dunand. 2022. “Solidification Microstructure, Aging Evolution and Creep Resistance of Laser Powder-bed Fused Al–7Ce–8Mg (wt%).” Additive Manufacturing 55: 102862. doi:10.1016/j.addma.2022.102862.
- Ramirez, A., Ma Qian, B. Davis, T. Wilks, and D. H. StJohn. 2008. “Potency of High-Intensity Ultrasonic Treatment for Grain Refinement of Magnesium Alloys.” Scripta Materialia 59 (1): 19–22. doi:10.1016/j.scriptamat.2008.02.017.
- Ramoni, Monsuru, Ragavanantham Shanmugam, Nimel Sworna Ross, and Munish Kumar Gupta. 2021. “An Experimental Investigation of Hybrid Manufactured SLM Based Al–Si10–Mg Alloy Under Mist Cooling Conditions.” Journal of Manufacturing Processes 70: 225–235. doi:10.1016/j.jmapro.2021.08.045.
- Riener, Kirstin, Steffen Oswald, Michael Winkler, and Gerhard J. Leichtfried. 2021. “Influence of Storage Conditions and Reconditioning of AlSi10Mg Powder on the Quality of Parts Produced by Laser Powder bed Fusion (LPBF).” Additive Manufacturing 39: 101896. doi:10.1016/j.addma.2021.101896.
- Rometsch, Paul A., Yuman Zhu, Xinhua Wu, and Aijun Huang. 2022. “Review of High-Strength Aluminium Alloys for Additive Manufacturing by Laser Powder bed Fusion.” Materials & Design 219: 110779. doi:10.1016/j.matdes.2022.110779.
- Sabzi, Hossein Eskandari, Suhyun Maeng, Xingzhong Liang, Marco Simonelli, Nesma T. Aboulkhair, and Pedro E. J. Rivera-Díaz-del-Castillo. 2020. “Controlling Crack Formation and Porosity in Laser Powder bed Fusion: Alloy Design and Process Optimisation.” Additive Manufacturing 34: 101360. doi:10.1016/j.addma.2020.101360.
- Schimbäck, D., P. Mair, M. Bärtl, F. Palm, G. Leichtfried, S. Mayer, P. J. Uggowitzer, and S. Pogatscher. 2022. “Alloy Design Strategy for Microstructural-Tailored Scandium-Modified Aluminium Alloys for Additive Manufacturing.” Scripta Materialia 207: 114277. doi:10.1016/j.scriptamat.2021.114277.
- Schmidtke, K., F. Palm, A. Hawkins, and C. Emmelmann. 2011. “Process and Mechanical Properties: Applicability of a Scandium Modified Al-Alloy for Laser Additive Manufacturing.” Physics Procedia 12: 369–374. doi:10.1016/j.phpro.2011.03.047.
- Shu, Da, Baode Sun, J. Mi, and P. S. Grant. 2011. “A Quantitative Study of Solute Diffusion Field Effects on Heterogeneous Nucleation and the Grain Size of Alloys.” Acta Materialia 59 (5): 2135–2144. doi:10.1016/j.actamat.2010.12.014.
- Sohrabpoor, H., V. Salarvand, R. Lupoi, Q. Chu, W. Li, B. Aldwell, W. Stanley, et al. 2021. “Microstructural and Mechanical Evaluation of Post-Processed SS 316L Manufactured by Laser-Based Powder bed Fusion.” Journal of Materials Research and Technology 12: 210–220. doi:10.1016/j.jmrt.2021.02.090.
- Somlo, K., B. H. Frodal, C. V. Funch, K. Poulios, G. Winther, O. S. Hopperstad, T. Børvik, and C. F. Niordson. 2022. “Anisotropic Yield Surfaces of Additively Manufactured Metals Simulated with Crystal Plasticity.” European Journal of Mechanics - A/Solids 94: 104506. doi:10.1016/j.euromechsol.2022.104506.
- Spierings, A. B., K. Dawson, T. Heeling, P. J. Uggowitzer, R. Schäublin, F. Palm, and K. Wegener. 2017. “Microstructural Features of Sc- and Zr-Modified Al-Mg Alloys Processed by Selective Laser Melting.” Materials & Design 115: 52–63. doi:10.1016/j.matdes.2016.11.040.
- Spierings, A. B., K. Dawson, P. J. Uggowitzer, and K. Wegener. 2018. “Influence of SLM Scan-Speed on Microstructure,: Precipitation of Al3Sc Particles and Mechanical Properties in Sc- and Zr-Modified Al-Mg Alloys.” Materials & Design 140: 134–143. doi:10.1016/j.matdes.2017.11.053.
- Tan, Qiyang, Zhiqi Fan, Xiaoqin Tang, Yu Yin, Gan Li, Danni Huang, Jingqi Zhang, et al. 2021. “A Novel Strategy to Additively Manufacture 7075 Aluminium Alloy with Selective Laser Melting.” Materials Science and Engineering: A 821: 141638. doi:10.1016/j.msea.2021.141638.
- Tan, Qiyang, Yu Yin, Arvind Prasad, Gan Li, Qiang Zhu, David Henry StJohn, and Ming-Xing Zhang. 2022. “Demonstrating the Roles of Solute and Nucleant in Grain Refinement of Additively Manufactured Aluminium Alloys.” Additive Manufacturing 49: 102516. doi:10.1016/j.addma.2021.102516.
- Tan, Qiyang, Jingqi Zhang, Ning Mo, Zhiqi Fan, Yu Yin, Michael Bermingham, Yingang Liu, Han Huang, and Ming-Xing Zhang. 2020. “A Novel Method to 3D-Print Fine-Grained AlSi10Mg Alloy with Isotropic Properties via Inoculation with LaB6 Nanoparticles.” Additive Manufacturing 32: 101034. doi:10.1016/j.addma.2019.101034.
- Tan, Qiyang, Jingqi Zhang, Qiang Sun, Zhiqi Fan, Gan Li, Yu Yin, Yingang Liu, and Ming-Xing Zhang. 2020. “Inoculation Treatment of an Additively Manufactured 2024 Aluminium Alloy with Titanium Nanoparticles.” Acta Materialia 196: 1–16. doi:10.1016/j.actamat.2020.06.026.
- Thampy, Vivek, Anthony Y. Fong, Nicholas P. Calta, Jenny Wang, Aiden A. Martin, Philip J. Depond, Andrew M. Kiss, et al. 2020. “Subsurface Cooling Rates and Microstructural Response During Laser Based Metal Additive Manufacturing.” Scientific Reports 10 (1): 1981. doi:10.1038/s41598-020-58598-z.
- Thapliyal, Saket, Mageshwari Komarasamy, Le Zhou Shivakant Shukla, Holden Hyer, Sharon Park, Yongho Sohn, and Rajiv S. Mishra. 2020. “An Integrated Computational Materials Engineering-Anchored Closed-Loop Method for Design of Aluminum Alloys for Additive Manufacturing.” Materialia 9: 100574. doi:10.1016/j.mtla.2019.100574.
- Thijs, Lore, Karolien Kempen, Jean-Pierre Kruth, and Jan Van Humbeeck. 2013. “Fine-structured Aluminium Products with Controllable Texture by Selective Laser Melting of pre-Alloyed AlSi10Mg Powder.” Acta Materialia 61 (5):1809-1819. doi:10.1016/j.actamat.2012.11.052.
- Uddin, Syed Z., Lawrence E. Murr, Cesar A. Terrazas, Philip Morton, David A. Roberson, and Ryan B. Wicker. 2018. “Processing and Characterization of Crack-Free Aluminum 6061 Using High-Temperature Heating in Laser Powder bed Fusion Additive Manufacturing.” Additive Manufacturing 22: 405–415. doi:10.1016/j.addma.2018.05.047.
- Van Cauwenbergh, P., V. Samaee, L. Thijs, J. Nejezchlebová, P. Sedlák, A. Iveković, D. Schryvers, B. Van Hooreweder, and K. Vanmeensel. 2021. “Unravelling the Multi-Scale Structure–Property Relationship of Laser Powder bed Fusion Processed and Heat-Treated AlSi10Mg.” Scientific Reports 11 (1): 6423. doi:10.1038/s41598-021-85047-2.
- Vrancken, Bey, Rishi K. Ganeriwala, and Manyalibo J. Matthews. 2020. “Analysis of Laser-Induced Microcracking in Tungsten Under Additive Manufacturing Conditions: Experiment and Simulation.” Acta Materialia 194: 464–472. doi:10.1016/j.actamat.2020.04.060.
- Wang, Di, Linqing Liu, Guowei Deng, Cheng Deng, Yuchao Bai, Yongqiang Yang, Weihui Wu, et al. 2022. “Recent Progress on Additive Manufacturing of Multi-Material Structures with Laser Powder bed Fusion.” Virtual and Physical Prototyping 17 (2): 329–365. doi:10.1080/17452759.2022.2028343.
- Wang, Tingting, Yilong Wang, Xu Yang, Baijin Chen, and Haihong Zhu. 2022. “Cracks and Process Control in Laser Powder bed Fusion of Al–Zn–Mg Alloy.” Journal of Manufacturing Processes 81: 571–579. doi:10.1016/j.jmapro.2022.06.066.
- Wang, Xiang, Lin-Jie Zhang, Jie Ning, Sen Li, and Suck-Joo Na. 2021. “Effect of Addition of Micron-Sized Lanthanum Oxide Particles on Morphologies, Microstructures and Properties of the Wire Laser Additively Manufactured Ti–6Al–4 V Alloy.” Materials Science and Engineering: A 803: 140475. doi:10.1016/j.msea.2020.140475.
- Wang, Zihong, Xin Lin, Jingfeng Wang, Nan Kang, Yunlong Hu, Danqian Wang, Hongyun Li, Weidong Huang, and Fushen Pan. 2022. “Remarkable Strength-Impact Toughness Conflict in High-Strength Al-Mg-Sc-Zr Alloy Fabricated via Laser Powder bed Fusion Additive Manufacturing.” Additive Manufacturing 59: 103093. doi:10.1016/j.addma.2022.103093.
- Wen, Peng, Yu Qin, Yanzhe Chen, Maximilian Voshage, Lucas Jauer, Reinhart Poprawe, and Johannes Henrich Schleifenbaum. 2019. “Laser Additive Manufacturing of Zn Porous Scaffolds: Shielding gas Flow, Surface Quality and Densification.” Journal of Materials Science & Technology 35 (2): 368–376. doi:10.1016/j.jmst.2018.09.065.
- Xiao, Y. K., Z. Y. Bian, Y. Wu, G. Ji, Y. Q. Li, M. J. Li, Q. Lian, Z. Chen, A. Addad, and H. W. Wang. 2019. “Effect of Nano-TiB2 Particles on the Anisotropy in an AlSi10Mg Alloy Processed by Selective Laser Melting.” Journal of Alloys and Compounds 798: 644–655. doi:10.1016/j.jallcom.2019.05.279.
- Xiao, Yunmian, Yongqiang Yang, Shibiao Wu, Di Wang Jie Chen, and Changhui Song. 2022. “Microstructure and Mechanical Properties of AlSi10Mg Alloy Manufactured by Laser Powder Bed Fusion Under Nitrogen and Argon Atmosphere.” Acta Metallurgica Sinica (English Letters) 35 (3): 486–500. doi:10.1007/s40195-021-01354-7.
- Yang, Feipeng, Jianying Wang, Tao Wen, Lei Zhang, Xixi Dong, Dong Qiu, Hailin Yang, and Shouxun Ji. 2022. “Developing a Novel High-Strength Al–Mg–Zn–Si Alloy for Laser Powder bed Fusion.” Materials Science and Engineering: A 851: 143636. doi:10.1016/j.msea.2022.143636.
- Yang, Kun V., Yunjia Shi, Frank Palm, Xinhua Wu, and Paul Rometsch. 2018. “Columnar to Equiaxed Transition in Al–Mg(–Sc)–Zr Alloys Produced by Selective Laser Melting.” Scripta Materialia 145: 113–117. doi:10.1016/j.scriptamat.2017.10.021.
- Yang, Tao, Tingting Liu, Wenhe Liao, Eric MacDonald, Huiliang Wei, Changdong Zhang, Xiangyuan Chen, and Kai Zhang. 2020. “Laser Powder bed Fusion of AlSi10Mg: Influence of Energy Intensities on Spatter and Porosity Evolution, Microstructure and Mechanical Properties.” Journal of Alloys and Compounds 849: 156300. doi:10.1016/j.jallcom.2020.156300.
- Yap, C. Y., C. K. Chua, Z. L. Dong, Z. H. Liu, D. Q. Zhang, L. E. Loh, and S. L. Sing. 2015. “Review of Selective Laser Melting: Materials and Applications.” Applied Physics Reviews 2 (4): 041101. doi:10.1063/1.4935926.
- Yavari, R., A. Riensche, E. Tekerek, L. Jacquemetton, H. Halliday, M. Vandever, A. Tenequer, et al. 2021. “Digitally Twinned Additive Manufacturing: Detecting Flaws in Laser Powder bed Fusion by Combining Thermal Simulations with in-Situ Meltpool Sensor Data.” Materials & Design 211: 110167. doi:10.1016/j.matdes.2021.110167.
- Yavari, Reza, Ziyad Smoqi, Alex Riensche, Ben Bevans, Humaun Kobir, Heimdall Mendoza, Hyeyun Song, Kevin Cole, and Prahalada Rao. 2021. “Part-scale Thermal Simulation of Laser Powder bed Fusion Using Graph Theory: Effect of Thermal History on Porosity, Microstructure Evolution, and Recoater Crash.” Materials & Design 204: 109685. doi:10.1016/j.matdes.2021.109685.
- Ye, Jianchao, Saad A. Khairallah, Alexander M. Rubenchik, Michael F. Crumb, Gabe Guss, Jim Belak, and Manyalibo J. Matthews. 2019. “Energy Coupling Mechanisms and Scaling Behavior Associated with Laser Powder Bed Fusion Additive Manufacturing.” Advanced Engineering Materials 21 (7): 1900185. doi:10.1002/adem.201900185.
- Yu, W. H., S. L. Sing, C. K. Chua, C. N. Kuo, and X. L. Tian. 2019. “Particle-reinforced Metal Matrix Nanocomposites Fabricated by Selective Laser Melting: A State of the art Review.” Progress in Materials Science 104: 330–379. doi:10.1016/j.pmatsci.2019.04.006.
- Yu, Wenhui, Swee Leong Sing, Chee Kai Chua, and Xuelei Tian. 2019. “Influence of re-Melting on Surface Roughness and Porosity of AlSi10Mg Parts Fabricated by Selective Laser Melting.” Journal of Alloys and Compounds 792: 574–581. doi:10.1016/j.jallcom.2019.04.017.
- Yu, Wenhui, Zhen Xiao, Xuhui Zhang, Yetao Sun, Peng Xue, Shuai Tan, Yongling Wu, and Hongyu Zheng. 2022. “Processing and Characterization of Crack-Free 7075 Aluminum Alloys with Elemental Zr Modification by Laser Powder bed Fusion.” Materials Science in Additive Manufacturing 1 (1): 4. doi:10.18063/msam.v1i1.4.
- Yuan, Weihao, Hui Chen, Shuai Li, Yuhua Heng, Shuo Yin, and Qingsong Wei. 2022. “Understanding of Adopting Flat-top Laser in Laser Powder bed Fusion Processed Inconel 718 Alloy: Simulation of Single-Track Scanning and Experiment.” Journal of Materials Research and Technology 16: 1388–1401. doi:10.1016/j.jmrt.2021.12.077.
- Zhang, Bo, Wu Wei, Wei Shi, Yanwu Guo, Shengping Wen, Xiaolan Wu, Kunyuan Gao, Li Rong, Hui Huang, and Zuoren Nie. 2022. “Effect of Heat Treatment on the Microstructure and Mechanical Properties of Er-Containing Al–7Si–0.6 Mg Alloy by Laser Powder bed Fusion.” Journal of Materials Research and Technology 18: 3073–3084. doi:10.1016/j.jmrt.2022.04.023.
- Zhang, Han, Dongdong Gu, and Donghua Dai. 2022. “Laser Printing Path and its Influence on Molten Pool Configuration, Microstructure and Mechanical Properties of Laser Powder bed Fusion Processed Rare Earth Element Modified Al-Mg Alloy.” Virtual and Physical Prototyping 17 (2): 308–328. doi:10.1080/17452759.2022.2036530.
- Zhang, Haolin, Chaitanya Krishna Prasad Vallabh, and Xiayun Zhao. 2022. “Registration and Fusion of Large-Scale Melt Pool Temperature and Morphology Monitoring Data Demonstrated for Surface Topography Prediction in LPBF.” Additive Manufacturing 58: 103075. doi:10.1016/j.addma.2022.103075.
- Zhang, Xing, Bo Mao, Leslie Mushongera, Julia Kundin, and Yiliang Liao. 2021. “Laser Powder bed Fusion of Titanium Aluminides: An Investigation on Site-Specific Microstructure Evolution Mechanism.” Materials & Design 201: 109501. doi:10.1016/j.matdes.2021.109501.
- Zhang, Xuan, Hao Xu, Zhongjie Li, Anping Dong, Dafan Du, Liming Lei, Guodong Zhang, Donghong Wang, Guoliang Zhu, and Baode Sun. 2021. “Effect of the Scanning Strategy on Microstructure and Mechanical Anisotropy of Hastelloy X Superalloy Produced by Laser Powder Bed Fusion.” Materials Characterization 173: 110951. doi:10.1016/j.matchar.2021.110951.
- Zhang, Xuhui, Zhen Xiao, Wenhui Yu, Chee Kai Chua, Lihua Zhu, Zongshen Wang, Peng Xue, Shuai Tan, Yongling Wu, and Hongyu Zheng. 2022. “Influence of Erbium Addition on the Defects of Selective Laser-Melted 7075 Aluminium Alloy.” Virtual and Physical Prototyping 17 (2): 406–418. doi:10.1080/17452759.2021.1990358.
- Zhao, Zhanyong, Peikang Bai, R. D. K. Misra, Mengyao Dong, Renguo Guan, Yanjun Li, Jiaoxia Zhang, et al. 2019. “AlSi10Mg Alloy Nanocomposites Reinforced with Aluminum-Coated Graphene: Selective Laser Melting, Interfacial Microstructure and Property Analysis.” Journal of Alloys and Compounds 792: 203–214. doi:10.1016/j.jallcom.2019.04.007.
- Zhou, Le, Thinh Huynh, Sharon Park, Holden Hyer, Abhishek Mehta, Shutao Song, Yuanli Bai, Brandon McWilliams, Kyu Cho, and Yongho Sohn. 2020. “Laser Powder bed Fusion of Al–10 wt% Ce Alloys: Microstructure and Tensile Property.” Journal of Materials Science 55 (29): 14611–14625. doi:10.1007/s10853-020-05037-z.
- Zhou, Le, Holden Hyer, Jinfa Chang, Abhishek Mehta, Thinh Huynh, Yang Yang, and Yongho Sohn. 2021. “Microstructure, Mechanical Performance, and Corrosion Behavior of Additively Manufactured Aluminum Alloy 5083 with 0.7 and 1.0 wt% Zr Addition.” Materials Science and Engineering: A 823: 141679. doi:10.1016/j.msea.2021.141679.
- Zhou, Le, Holden Hyer, Sharon Park, Hao Pan, Yuanli Bai, Katherine P. Rice, and Yongho Sohn. 2019. “Microstructure and Mechanical Properties of Zr-Modified Aluminum Alloy 5083 Manufactured by Laser Powder bed Fusion.” Additive Manufacturing 28: 485–496. doi:10.1016/j.addma.2019.05.027.
- Zhou, S. Y., Y. Su, H. Wang, J. Enz, T. Ebel, and M. Yan. 2020. “Selective Laser Melting Additive Manufacturing of 7xxx Series Al-Zn-Mg-Cu Alloy: Cracking Elimination by co-Incorporation of Si and TiB2.” Additive Manufacturing 36: 101458. doi:10.1016/j.addma.2020.101458.