ABSTRACT
Metal additive manufacturing is gaining immense research attention. Some of these research efforts are associated with physics, statistical, or artificial intelligence-driven process modelling and optimisation, structure–property characterisation, structural design optimisation, or equipment enhancements for cost reduction and faster throughputs. In this review, the focus is drawn on the utilisation of topology optimisation for structural design in metal additive manufacturing. First, the symbiotic relationship between topology optimisation and metal additive manufacturing in aerospace, medical, automotive, and other industries is investigated. Second, support structure design by topology optimisation for thermal-based powder-bed processes is discussed. Third, the introduction of capabilities to limit manufacturing constraints and generate porous features in topology optimisation is examined. Fourth, emerging efforts to adopt artificial intelligence models are examined. Finally, some open-source and commercial software with capabilities for topology optimisation and metal additive manufacturing are explored. This study considers the challenges faced while providing perceptions on future research directions.
GRAPHICAL ABSTRACT

1. Introduction
Metal Additive Manufacturing (MAM) has attracted increasing attention because it realises geometrically complex, fully functional metallic structures that are hard to produce by traditional processes (du Plessis et al. Citation2019; Fayazfar et al. Citation2018; Bacciaglia, Ceruti, and Liverani Citation2020; Plocher and Panesar Citation2019; Zhang et al. Citation2020a; Townsend et al. Citation2016; Bhavar et al. Citation2017; Blakey-Milner et al. Citation2021; Pan, Karnati, and Liou Citation2020b; DebRoy et al. Citation2018; Gisario et al. Citation2019; Lewandowski and Seifi Citation2016; Frazier Citation2014; Kok et al. Citation2018). Most traditional manufacturing methods limit topological design complexities of parts which are considerably feasible by Additive Manufacturing (AM) processes. Topology optimisation (TO) establishes the best material or structural layout with a predetermined design domain by optimising an objective parameter against one or a set of constraints. Due to this design freedom TO offers, organic shapes having intricately connected features are common. Although optimum designs are obtainable compared to other structural optimisation methods, TO was largely theoretical in the past because of limitations on manufacturing techniques to actualise such designs. This narrative is fast-changing, and in the last decade, there have been enormous efforts to consider TO in the design workflow of various components due to the advancement of AM processes. Classifications of popular TO and MAM methods are shown in . To indulge the reader, there are several reviews on equipment-focused AM (Frazier Citation2014; Kok et al. Citation2018; Gisario et al. Citation2019), microstructure and mechanical properties of AM parts (Fayazfar et al. Citation2018; Bhavar et al. Citation2017; DebRoy et al. Citation2018; Frazier Citation2014; Gisario et al. Citation2019; Gu et al. Citation2012; Yap Citation2015; Bourell et al. Citation2017; Zhai, Lados, and LaGoy Citation2014; du Plessis, Yadroitsava, and Yadroitsev Citation2020; Kok et al. Citation2018; Lewandowski and Seifi Citation2016; Townsend et al. Citation2016), cost models (Gisario et al. Citation2019; Ahn Citation2016), and simulation of AM processes (Bandyopadhyay and Traxel Citation2018; Megahed et al. Citation2016; Gatsos et al. Citation2019; Srivastava et al. Citation2020a; Kouraytem et al. Citation2021; Bayat et al. Citation2021; Hashemi et al. Citation2021). Some TO-specific reviews can be seen in Wang et al. (Citation2021c), Xia et al. (Citation2016), van Dijk et al. (Citation2013), Rozvany (Citation2008), and Reddy et al. (Citation2016a) while TO for AM is observed in Gao et al. (Citation2015), Meng et al. (Citation2019), Abdulaziz et al. (Citation2020), Liu et al. (Citation2018a), Blakey-Milner et al. (Citation2021), and Plocher and Panesar (Citation2019).
Figure 1. Summary of major topology optimisation and metal additive manufacturing techniques. Metal AM portion adapted from (Kok et al. Citation2018).

Although there are now a plethora of methods to topologically optimise structures, they can be categorised into 4 major methods as shown in : density-based, evolutionary, boundary variation, and non-gradient-based methods. Density-based methods make use of pseudo-density variables as the optimisation’s design variables with limits placed on this parameter usually to establish material phases (e.g. solid, void, fluid., etc.). There are two popular density-based methods: Solid Isotropic Material with Penalisation (SIMP) and the Rational Approximation of Material Properties (RAMP) (Bendsøe et al. Citation2011; Toyserkani et al. Citation2021). These methods are defined by the material interpolation function, while SIMP uses a power-law function, RAMP utilises a rational function. The evolutionary methods enable the successive removal, in the case of ESO, or successive removal and addition, in the case of Bi-directional ESO (BESO), of material during the optimisation process. In the boundary variation methods, level and phase functions are used to identify solid, void, or boundary regions. In nascent times, non-gradient-based have been gaining some popularity especially because of the advancements of artificial intelligence models. Other non-gradient-based methods which have been used for topology optimisation as listed in are Genetic Algorithm (GA), Particle Swarm Optimisation (PSO), etc.
While Powder Bed Fusion (PBF), Direct Energy Deposition (DED), and Binder Jetting (BJ) form the most popular MAM technologies as pointed out by Toyserkani et al. (Citation2021), in this study, most MAM technologies are first broadly classified as either powder-bed, directed energy deposition, or sheet lamination. MAM processes can also be identified or classified by their working mechanisms such as lasers, electron beams, optical systems, material delivery, etc. The classifications in are according to how the feedstock material is being consolidated. Within powder bed processes, Laser Fusion (LF) often called Laser Powder Bed Fusion (LPBF) and Electron Beam Melting (EBM) are popular fusion processes while Binder Jetting (BJ) is a unique metal powder bed process that requires a binder to consolidate powder particles to form a ‘green’ part which needs to be heat treated for binder removal and curing. For DED processes, feedstock materials are either powder-fed or wire-fed. While materials that are powder-fed cannot be consolidated by electron beams because vacuum conditions will be required, wire-fed materials can be worked upon by either lasers or electron beams. Direct Metal Deposition (DMD) and Electron Free-Form Fabrication (EF3) are popular laser and electron beam DED technologies respectively. In sheet lamination, thin sheets of metal are joined together in a solid-state manner usually by ultrasonic consolidation (Toyserkani et al. Citation2021). Sheet lamination can be beneficial because joining is done at much lower temperatures than the material’s melting temperature, consequently, the microstructure of the final part closely matches that of the parent material. However, there are limitations on compatible materials possible and design complexities.
AM’s flexibility makes it ideal for its integration with TO (Bendsøe and Kikuchi Citation1988; Bendsøe et al. Citation2011). However, TO results are not always AM-friendly (Liu et al. Citation2018b; Meng et al. Citation2019; Mirzendehdel and Suresh Citation2016), so it is critical to incorporate AM limitations into TO to fully improve the integration between design and fabrication in actual applications (Wu et al. Citation2018; Mhapsekar, McConaha, and Anand Citation2018; Zegard and Paulino Citation2016; Zhu et al. Citation2021b). To that purpose, great effort has been considered in the design stage to optimise support structures (Li et al. Citation2016a; Xiong et al. Citation2020; Zhou and Zhang Citation2019), reduce thermal accumulation (Allaire and Bogosel Citation2018; Wang and Qian Citation2020; Zhou, Liu, and Lin Citation2019a; Miki and Nishiwaki Citation2022), ease residual stress and deformation (Cheng and To Citation2019; Cheng et al. Citation2019a; Bartsch et al. Citation2019; Zhang et al. Citation2020a; Misiun et al. Citation2021; Allaire and Jakabčin Citation2018; Allaire, Bihr, and Bogosel Citation2020; Pellens et al. Citation2020), and so on.
This review focuses on the intervention of TO methods in MAM design workflow, especially within the technical research space. The review is targeted to address two broad scopes: industry applications of TO and MAM, and the use of TO within the Design for Additive Manufacturing (DfAM) framework considering metals. In the first scope, the extent to which the symbiosis between TO and MAM has assisted industry-specific design applications for improved functionalities, ease of manufacturability, and general freedom of design expression is discussed in Section 2. The second scope elaborates on the use of topology optimisation to fulfil aspects of the design for metal additive manufacturing framework. Under this scope, the role of TO in the design of support structures prevalent in thermal-based powder-bed processes is examined in Section 3. Thermal-based powder-bed technologies form the most utilised MAM and support structures are inevitable for most of them. As will be explained in this review, many research efforts have shown that TO can assist in generating optimal support structures while limiting material usage. Since MAM processes present manufacturability constraints, this review in Section 4, will examine the various TO algorithms that have captured design-based constraints, such as overhang elimination, cavity-filling, feature size limits, and process-based constraints such as residual stresses and deformation. Furthermore, an aspect of design for additive manufacturing (DfAM) that has gained popularity is lightweighting through porous structures. In Section 5, this review will explore the significance of TO in generating porous structures through latticing or infill strategies while recognising the considerations that should be made for MAM processes. In Section 6, the influence of nascent artificial intelligence models on the effectiveness and versatility of TO algorithms are discussed, and finally, some commercial and open-source software for TO and MAM are investigated in Section 7. A pertinent aspect of this review is the exploration of the status of these techniques and their effectiveness while identifying the inherent challenges and opportunities for future developments. Regarding the graphical abstract, the inner square shows the first scope of this study which reviews the adoption of TO and MAM in the industry covered in Section 2, while the outer circular ring reveals the second scope of TO and MAM within the DfAM framework which is covered from Sections 3 to 7.
2. Industry-related design and application
In simple terms, the entire purpose of design and manufacturing is to cater to individual or commercial market needs. While a variety of these needs are being addressed by several traditional and/or conventional manufacturing processes, AM has found immense application in some major industries. Developing metal parts through MAM poses unique design- and process-related challenges, unlike other polymer-based processes. TO has been a viable tool to address these challenges, although some of these algorithms are still in their infancy. In this section, the use of TO and MAM targeted for specific industrial purposes is studied.
2.1. Aerospace
Topology optimisation of structures related to aircrafts and spacecrafts will be considered under aerospace in this study. A review of TO applied in aircraft and aerospace structures was done by Zhu et al. (Citation2021b). Although they briefly discussed the role AM could play in advancing structural designs, there was no elaborate discussion on MAM processes. However, an important conclusion they made is the fact that TO has been widely accepted for the design of aerospace structures, although with several manufacturability concerns. To investigate the symbiosis between TO and MAM within the aerospace industry, this study looks at several efforts within the past decade with some of these efforts shown in . To demonstrate this, Süß et al. (Citation2016) topologically optimised the main gearbox of a helicopter and adopted EBM (Ti-6Al-4V – material) as the chosen AM process. Three major objectives were targeted: weight savings, part consolidation, and the satisfaction of requirements for mechanical properties such as tensile, yield, and fatigue strength. Two optimisation solutions were obtained using different initial design domains, and separate redesigning strategies were utilised to reconstruct the topologies. One striking challenge was the intricacy and time spent reconstructing the topologies. Nonetheless, they achieved over 40% material reduction after reconstruction in both optimisation cases in addition to other objectives they accomplished. Seabra et al. (Citation2016) leveraged TO and LPBF to design and manufacture a lightweight aircraft bracket shown in (a) while maintaining functional stress levels. The general workflow is similar to (Süß et al. Citation2016); however, parts produced by LPBF are more prone to porosities and residual stresses compared to EBM if optimum process parameter selections are not made; therefore they performed Hot Isostatic Pressing (HIP) after printing. A 28% reduction in weight was achieved even though the bracket’s material was changed to a Titanium alloy from an aluminum alloy. Another application is observed in Magerramova, Vasilyev, and Kinzburskiy (Citation2016), where turbine blades were designed by a TO formulation consisting of a strain energy minimisation as the objective function and two constraints: a double reduction in material volume (from the original design domain) and a limit on the first 6 eigenfrequencies. Constraining the eigenfrequencies is necessary to detune the resonance frequency in the design of low-pressure turbines (LPT). It should be noted that due to the tomography of turbine blades, there could be very thin features in the design that will pose a manufacturing challenge. To circumvent this challenge, a minimum feature thickness of 0.15 mm was imposed during the design. Representative small-sized blades were printed using a Nickel-based superalloy via LPBF. The popular GE Aircraft Engine bracket was redesigned and manufactured by Direct Metal Laser Sintering (DMLS) in López-Castro et al. (Citation2017) as shown in (b). The aim was to reduce the weight of previous versions of this bracket by printing an optimised alternative using Stainless Steel AISI 15-5PH as opposed to Ti-6Al-4V. To adhere to geometric constraints for the AM process, a minimum feature size limit of 9 mm was placed during TO, and a 56% reduction in weight was realised while keeping close functional stress and deformation profiles with the original design. Other areas that explored the use of TO and MAM for metal aircraft components without exploring manufacturability can be seen in the aircraft landing gear and engine mount in Munk et al. (Citation2019), tesla valve in Gaymann, Montomoli, and Pietropaoli (Citation2017), and aircraft brackets in Gebisa and Lemu (Citation2017a) and Fetisov and Maksimov (Citation2018).
Figure 2. The application of TO and MAM in the development of aircraft brackets as developed by (a) (Seabra et al. Citation2016). Reproduced with permission from Ref. (Seabra et al. Citation2016). Copyright 2016, Elsevier, and (b) (López-Castro et al. Citation2017). Reproduced with permission from Ref. (López-Castro et al. Citation2017). Copyright 2017, Elsevier.
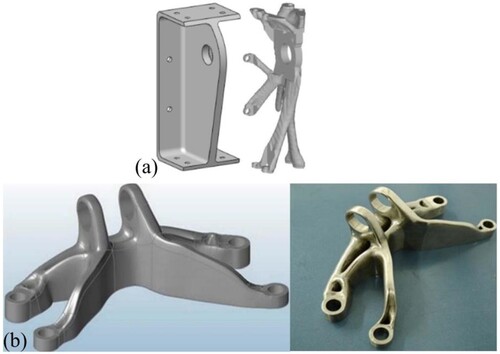
For space-related applications, the design of mirrors using TO and MAM was explored by Herzog et al. (Citation2015). Mirrors find a useful application in spaceflight, therefore, there were critical properties required, such as good structural rigidity, quality surface finish, and the ability to withstand severe vibrational effects. In light of this, an initial CAD file placed under appropriate load and boundary conditions was optimised for stiffness maximisation and placed under a material volume and a 250 Hz natural frequency constraint. The mirror was printed using two MAM processes: EBM with Ti-6Al-4V and DMLS with AlSi10Mg. Due to the unique specifications required by the mirror, several post-processing steps were taken such as HIP to reduce porosity, and preliminary machining with a mill for resurfacing, grinding and polishing. The last two processes are important phases in general optical fabrication. Although the mirrors printed successfully using both materials, the aluminum mirror was more successful with fewer porosities and a better micro roughness. Another space mirror was developed by Hu et al. (Citation2017) by topology and sizing optimisation. No manufacturability study was performed; however, extrusion (Ishii and Aomura Citation2004; Zhou et al. Citation2002), and void filling (Liu et al. Citation2015) constraints were included in the TO step. . Orme et al. (Citation2017) designed and manufactured a mock framework (consisting of 4 legs and a hub) of a lunar spacecraft. As seen in (c), a design domain (in grey) was obtained and optimised for minimal mass while limiting the natural frequency and stress to >60 Hz and <115 MPa respectively. The optimised framework was printed using an EOS M290 using AlSi10Mg as material and due to the framework’s size relative to the machine, it was designed to have 4 identical legs. Due to the limitations of the optimisation software used, CAD interpretation of the optimised topology was necessary for post-optimisation FEA, support minimisation, and overall printability.
A critical aspect of the aerospace industry is certification and standardisation of air/space-crafts and important components such as engines/engine parts, and structural frameworks which, oftentimes, take time. Without certification and standardisation, these components are prone to failure leading to catastrophic events and losses. The United States Federal Aviation Administration mentioned that they spent 5 years certifying the Boeing 737 MAX between 2012 and 2017 (Airworthiness Certification Citation2022). Most of the aerospace-related efforts reviewed in this study are within the last 6 years with little to no mention of the homologation process for the designed or redesigned components. The reason could be that these new designs are still more theoretical than practical as further experimental studies need to be done to certify their performances. A study that considered part qualification is the work done by Willner et al. (Citation2020). For spacecraft components, a technology readiness level (TRL) of 7 is required for the final system test, launch, and operations. In Willner et al. (Citation2020), it was opined that their topologically optimised and additively manufactured spacecraft bracket was eligible for TRL 3 as is, with a qualification process increasing this level to TRL 5. However, to raise this certification level to TRL 7, testing of the assembled system including the bracket needed to be done. This action was beyond the scope of their study and therefore limited the homologation process. Singamneni et al. (Citation2019) stated that the certification and standardisation of AM parts is the most difficult stage for the aircraft industry due to several limitations which can be summarised as the current evolution of the manufacturing technology. Since most MAM technologies are still evolving, obtaining widely acceptable standards for AM materials, processes, quality control, and assessment, and design is still lacking. This is a key contributing factor that hinders the homologation of the many newly designed aerospace components. This hindrance is further exacerbated by the cost and length of time for these certification and standardisation procedures.
2.2. Medical
Over the past decade, the need and relevance of AM for medical purposes have greatly increased. For example, in 2011 in Belgium, Dr. Jules Poukens and his team implanted the world’s first additively manufactured mandible in a patient (Xillo Citation2011). The achievement of this milestone is significant in many ways because it has revealed opportunities in the design and manufacture of medical implants (Leary Citation2018), such as patient-tailored implants (Shidid et al. Citation2016) or lattice-based implants with mechanical and geometric properties closely similar to the host’s bone (Wang et al. Citation2016; Reinhart and Teufelhart Citation2011). Other than lattice structure design, one popular approach in designing patient-tailored implants is through TO or a combination of TO and lattice structures which will be the focus of this section. In the design of implant devices and bone tissue engineering (Bose, Vahabzadeh, and Bandyopadhyay Citation2013; Wang et al. Citation2016), bone remodelling is a core aspect that involves the adaptation of the bone’s internal structure to adequately support external loading conditions. To achieve this, the principal stress paths of the implant’s structure have to be optimally re-organized to maximise structural rigidity (Goda et al. Citation2019). Additionally, an undesirable phenomenon that occurs in an inappropriately matched bone-implant assembly is stress shielding where a much stiffer implant compared to its neighbouring bone region results in inaccurate bone remodelling (Haase and Rouhi Citation2013; Park, Lee, and Sutradhar Citation2019). Several efforts have employed TO and MAM to address these aspects.
Al-Tamimi et al. (Citation2019) studied the re-design of metallic bone plates in the treatment of bone fractures. To combat stress shielding, the plates were topologically optimised to obtain an equivalent stiffness comparable to that of a cortical bone. The optimised plates were printed via EBM using Ti6Al4V and several characterisations were done to observe their tensile, hardness, and surface roughness properties. The results of tensile tests revealed close matches to numerical results. In-vitro testing of the plates was done to understand the speed and quality of biological bonding with surrounding tissue, and it was found that rough surfaces of the EBM plates contributed to better bonding compared to smoother commercially produced plates. Contrary to previous related studies, they concluded that rougher EBM plates without any post-processing contributed to higher cell binding and proliferation. In a similar vein, He et al. (Citation2018) combated stress-shielding in LPBF-manufactured Ti6Al4 V hip prosthesis through a combination of TO and lattice design. Although no in-vitro biological testing was done, it was noticed that the stress shielding increase (SSI) (Weinans et al. Citation2000; Fraldi et al. Citation2010) was reduced by over 50% in the optimised design and could last longer than 107 life cycles compared to the generic implant. Some bottlenecks identified in this study are the absence of the influence of the bone-implant interface which often results in aseptic loosening and the a priori approach taken to obtain the unit cell type and size for lattice structures.
To design a patient-tailored mandibular implant, Cheng et al. (Citation2019b) developed a Titanium implant through a 3D reconstruction of the patient’s defective mandibular and TO. Two broad functionalities were considered: aesthetics and functionality. For functionality, four objectives were specified: fixation, support, bone ingrowth, and chewing. After TO, micro-pores were introduced to inhibit stress-shielding and encourage bone ingrowth. The implant was printed via LPBF using Ti6Al4V, but neither mechanical nor in-vitro testing was done. A multi-objective TO model to optimise stiffness under various functional routines was utilised to design a pelvic implant by Iqbal et al. (Citation2019). This design strategy was fulfilled for four initial design domains obtained from different resection types as observed in . The implant was printed using EBM in Ti6Al4V and was implanted in a patient in China. Some challenges and assumptions were the adoption of less realistic static loading conditions, the exclusion of the effects of connecting muscles and ligaments, and performance evaluation based on numerical analysis only without experimental mechanical test validations. For future developments, the numerical model can be strengthened by using dynamic loading inputs which will more closely match the natural physiological routine.
Figure 3. Topology-optimised prostheses for four resection types. Reproduced with permission from Ref. (Iqbal et al. Citation2019). Copyright 2019, Elsevier.
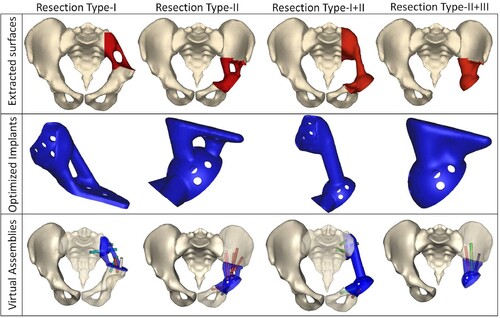
In this paragraph, three major TO approaches for implant designs are summarised. While the general formulation and implementation of TO can be found here (Andreassen et al. Citation2011; Ibhadode et al. Citation2021),
The first popular approach is the use of a multi-objective functional, usually compliance or strain energy (Iqbal et al. Citation2019; Guo and Yin Citation2019; Liu, Jiang, and Lin Citation2020b; Jiang et al. Citation2017). Here, since the daily routine of the physiological region exerts several load types on the implant’s structure, a consolidated compliance function is expressed as the summation of the weighted individual load compliances. Consolidation is facilitated by introducing weight factors associated with the compliances where the value of a weight factor depends on the priority given to the functional load.
A second approach is stress-based TO. Instead of going with a multi-objective function, global compliance resulting from the summed effects of the loads is maintained as the objective while a stress constraint is imposed to limit the structure’s failure (Al-Ali et al. Citation2017; Deaton and Grandhi Citation2016).
In the third approach, infill and perimeter TO frameworks are developed to generate structures that nearly model the venous or porous nature of bone structures (Wu et al. Citation2018; Zhao and Zhang Citation2021a, Citation2021b; Park et al. Citation2018). This involves the addition of one or more constraints that control the distribution of the pseudo-density field during optimisation. The applications of TO and MAM in medicine can mainly be seen in the development of implants and prostheses for mandibles, craniums and facials, hips, dental implants, and spines as shown in .
Figure 4. Major applications of TO and MAM in medicine: mandibles (reproduced with permission from Ref. (Li et al. Citation2020a). Copyright 2020, Elsevier), cranium and facial (Park et al. Citation2021), pelvic and hip (reproduced with permission from Ref. (Iqbal et al. Citation2019). Copyright 2019, Elsevier), dental (reproduced with permission from Ref. (Park et al. Citation2019). Copyright 2019, Elsevier), and spine (reproduced with permission from Ref. (Wang et al. Citation2020a). Copyright 2020, Elsevier).
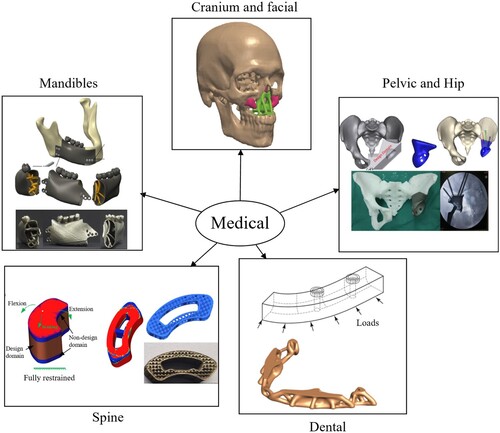
There are several other non-metallic additively manufactured implant designs developed in the past years (Park, Lee, and Sutradhar Citation2019; Jiang et al. Citation2017; Živčák et al. Citation2018; Gómez Pérez, Medellín-Castillo, and Espinosa-Castañeda Citation2017; Sutradhar et al. Citation2015, Citation2010; Moussa et al. Citation2020; Hu et al. Citation2019; Li, Wu, and Lin Citation2020a).
2.3. Automotive
In a bid to push up the efficiencies of modern automobiles, several advanced techniques such as turbocharging, advanced spark ignitions, better emission control, fuel consumption, advanced braking, steering and suspension systems, etc. have been devised. To achieve these technologies, ingenious design and manufacturing techniques must be adopted. Several research efforts are beginning to introduce TO and additive manufacturing into the design workflows for these automobile components and systems. It is particularly observed that many case studies focus on parts in and around the suspension/wheel system and engine. In Dalpadulo, Pini, and Leali (Citation2020a), Walton and Moztarzadeh (Citation2017), Vaverka, Koutny, and Palousek (Citation2019), Reddy et al. (Citation2016b), and Bikas et al. (Citation2016a), wheel knuckles or uprights for Formula race cars were studied. While Bikas et al. (Citation2016a), Dalpadulo, Pini, and Leali (Citation2020a), and Vaverka, Koutny, and Palousek (Citation2019) printed topology-optimised samples using AlSi10Mg by LPBF, Walton and Moztarzadeh (Citation2017) and Reddy et al. (Citation2016b) printed optimised samples using Ti6Al4V by EBM and LPBF respectively. In all the listed studies, significant weight savings were attained while maintaining decent performances, however, in Walton’s study, the cost of EBM against the machined alternative was over 700%. Since the manufacturing costs for EBM or LPBF parts are still comparatively high, it is pertinent that these manufacturing methods are reserved for high-priority or sensitive parts where performance is given higher consideration than cost. Moreover, although most thermal-based MAM processes are meant for low-volume or customised productions, it is highly recommended that more studies investigate the cost of MAM in comparison with alternative production processes. Dalpadulo, Pini, and Leali (Citation2020a) went further to explore several workflows for part simulation, print preparation, and process simulation in Catia’s 3DExperience. For efforts that compare MAM to other manufacturing processes, Großmann et al. (Citation2020) compared a topologically optimised riveting tool printed via LPBF to an optimised version constrained for milling and an original milled. Amongst others, their weights, manufacturing costs, time, simulated maximum displacements, equivalent stresses, and waste material were compared. The optimised MAM part outperformed the others in weight, waste material, and equivalent stress; however, it performed less in manufacturing time and cost. With research and development, it is expected that time and cost for MAM parts will be reduced; however, relatively simple parts such as the riveting tool might be easier and cost-effective to manufacture using traditional processes. Furthermore, as mentioned previously, if the part is not meant for high performance or safety such that precise functional requirements over production costs are justified, non-thermal-based MAM such as Binderjetting (BJ), material extrusion, or traditional production processes are recommended.
Tyflopoulos, Lien, and Steinert (Citation2021) redesigned the front and back brake callipers that were printed using Ti6V4Al by LPBF in (a) while Bici, Broggiato, and Campana (Citation2016) topologically optimised a suspension wishbone attachment without printing it although they opined that it was a good candidate for MAM. Junk, Fleig, and Fink (Citation2017) redesigned a brake mount through TO and prototyped it via BJ. After refinements and smoothing, the final part was printed via LPBF using AlSi10Mg. An interesting aspect was the relationship established between the weight reduction in the brake mount and the carbon footprint. It was estimated that an 81 g reduction in the mass could lead to a reduction of 855 mg/100 km of CO2; Barbieri et al. (Citation2018) proposed that steel pistons could be adopted in place of their contemporary aluminum counterparts because they can take more mechanical and thermal loads. Steel pistons were redesigned by TO resulting in a 9% increase in weight, further design studies were recommended to ensure the redesigned pistons meet the functional requirements. Unfortunately, neither manufacturability nor experimental mechanical tests were done to validate the design solution. Other applications of TO and MAM can be seen in the gearbox housing redesign by Barreiro et al. (Citation2019) printed using AlSi10Mg by LPBF, race-car upright design by Hunar et al. (Citation2020) in (b), diesel engine support by Marchesi et al. (Citation2015) in (c), steering column support by Mantovani, Campo, and Ferrari (Citation2020), and automotive fixtures by Naik et al. (Citation2019); they are all summarised in Table S1.
Figure 5. Applications of TO and MAM in the automotive industry: (a) brake calliper (Tyflopoulos et al. Citation2021), (b) upright design (Hunar et al. Citation2020), (c) diesel engine support (Marchesi et al. Citation2015).
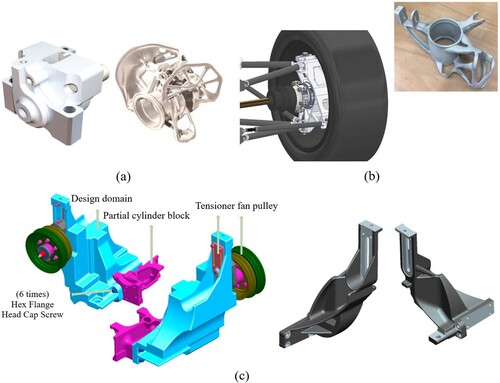
2.4. Others
Several other industries have benefited from the symbiotic relationship enjoyed by TO and MAM although not as much as the industries listed above. As far back as 2007, Ngim reported the design of axisymmetric components using a material minimisation, stress-constrained TO process (Ngim, Liu, and Soar Citation2007). The design strategy was reported to be suitable for a range of components such as brake disks, flywheels, pressure vessels, etc. Although a prototype was printed of the optimised design using a nylon material via SLS, it was reported that metallic materials could be used as they will have properties similar to carbon steel which was used during the simulation. Herbin, Grzesiak, and Krolikowski (Citation2017) considered a 7-Degree of Freedom ExoArm for lightweighting since the weight of the components of the ExoArm impacts the power on the drives. First, the original material specification Ti-6Al-4V was replaced with 7075 aluminum and steel for weight reduction. Next, TO and lattice structures were applied to further reduce the weights of the ExoArm clamps. The clamps were printed using LPBF achieving a material reduction of 45% and above for all parts optimised. TO and MAM have also been explored in the construction industry. Huang, Deng, and Lam (Citation2021) investigated the performance of additively manufactured topology-optimised tubular joints with their hollow square-section welded counterparts. Several mechanical tests were performed, and some important conclusions drawn are: a 1.6% difference in the Young’s Modulus between the printed and welded tubular joints, the printed joints gave more symmetric stress distributions compared to the welded joints, the maximum stress was decreased by 49% when TO was utilised to design the printed parts. Using TO, Lynch et al. (Citation2013) proposed some guidelines for the design and optimisation of parts to be manufactured by cold-spray AM. The design guidelines include the consideration of planar features, smooth transition between surfaces for continuous spraying, deposition angle and cross-sectional geometry, feature thickness limitations based on cold spray parameters, etc. Wu et al. (Citation2017) worked on the redesign of a plastic injection tool using a thermo-mechanical TO model and lattices. Steuben et al. (Citation2017) investigated the redesign of an unmanned underwater vessel by a meta-material TO model with acoustic tunability. Other applications can be found in and Table S1 in the supplementary file.
Figure 6. Application of TO and MAM in other industries (a) redesign of a welding jig (reproduced with permission from Ref. (Schuh et al. Citation2020). Copyright 2020, Elsevier) design of a phase change material-based heat sink (reproduced with permission from Ref. (Ho et al. Citation2021). Copyright 2021, Elsevier).
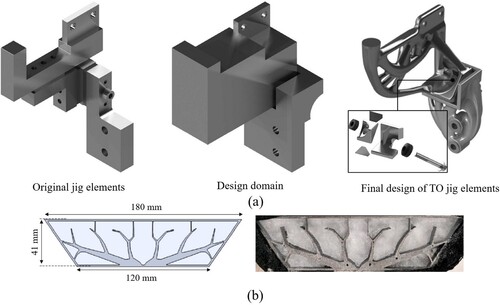
2.5. Sustainability
In the aerospace and automotive industries, strict requirements on the final part quality are usual. Often, the application of TO and MAM can produce lightweight parts that meet certain operational requirements such as structural rigidity. However, there are other precise specifications required by these industries in terms of surface finishes, tolerances, etc., which might be difficult to attain by MAM only. It is, therefore, important to understand how MAM compares to conventional manufacturing or machining in terms of cost and energy demands especially when attempts are made to ensure a part meets up with these additional requirements. Furthermore, in light of this study, the influence of TO to contribute to more sustainable additively manufactured parts is important to point out. In Priarone et al. (Citation2017), the cost and energy demand of a hybrid process of EBM and finish machining (FM) are compared to conventional machining (CM). As illustrated in , the study showed that when an initial part is lightweighted by 25% (part 2) or 75% (part 3), the cost and energy required to produce the parts by CM increases slightly and this might be attributed to the resulting structural complexities compared to the original part. It is expected that this cost increase will become significant with much greater structural complexities. However, with EBM+FM, the cost of producing part 3, which is 75% lighter and more complex than part 1, is reduced by over 60% while the energy input required is reduced by over 50%. Although the cost of producing all parts using EBM+FM is considerably larger than that used by CM, TO plays a great role in ensuring MAM parts are not only optimally functional but more sustainable because of its lightweighting ability. Moreover, it is observed that energy demands by EBM+FM become less than CM for part 3. It is important to add that in Priarone et al. (Citation2017), the additional cost and energy demand from FM were marginal compared to the overall demand by the hybrid process. In addition to MAM’s material reusability, MAM minimises energy and cost consumption substantially compared to CM when the part is designed with optimum material usage regardless of structural complexity. Note that the breakdown of the cost and energy components in is not shown, please refer to Priarone et al. (Citation2017) for this. In a similar study, Tang, Mak, and Zhao (Citation2016) estimated a 58% decrease in CO2 emissions when binderjetting (BJ) was used to produce an optimised aerospace bracket compared to a computer numerically controlled (CNC) designed and produced bracket.
Figure 7. Cost and energy estimations for producing three parts using conventional machining (CM) and a hybrid electron beam melting (EBM) and finish machining (FM). Adopted from (Priarone et al. Citation2017).
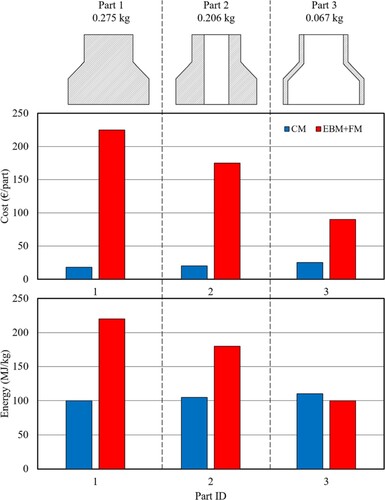
In a study by Donofrio (Citation2016), it was mentioned that 3D-printed topologically optimised structural steel joints developed by Arup had the potential to reduce transportation and storage costs compared to the original bulkier versions as the optimised structures were smaller and lighter. Studies by Munk and Miller (Citation2022) and Gebisa and Lemu (Citation2017b) also show that TO and MAM contribute to improving the product supply chain and minimising cost and environmental impact within several industries.
2.6. Remarks
TO has been extensively utilised in the design of parts for MAM, especially in the aerospace, medical, and automotive industries, however, it is observed that compared to the automobile industry, a wider range of applications has been considered in aviation and medicine.
In Table S1 in the supplementary file, 103 case studies on the application of TO and MAM in major industries drawn from several research efforts are presented. 29 of these case studies are categorised under aerospace (Süß et al. Citation2016; Seabra et al. Citation2016; Magerramova, Vasilyev, and Kinzburskiy Citation2016; López-Castro et al. Citation2017; Munk et al. Citation2019; Gaymann, Montomoli, and Pietropaoli Citation2017; Gebisa and Lemu Citation2017a; Fetisov and Maksimov Citation2018; Herzog et al. Citation2015; Orme et al. Citation2017; Willner et al. Citation2020; Song et al. Citation2021; Smith et al. Citation2016; Senck et al. Citation2020; Saudan et al. Citation2018; Muir et al. Citation2013; Li et al. Citation2016c; Ferro et al. Citation2017; Ferro et al. Citation2016; Faskhutdinov et al. Citation2017; Dagkolu, Gokdag, and Yilmaz Citation2021; Cucinotta, Raffaele, and Salmeri Citation2019; Galvao et al. Citation2021; Hu et al. Citation2017; Fan et al. Citation2021; Suárez et al. Citation2022; Chen et al. Citation2021b; Caivano et al. Citation2022; Leary et al. Citation2021; Berrocal et al. Citation2019), 25 under medical (Wu et al. Citation2018; Park, Lee, and Sutradhar Citation2019; Al-Tamimi et al. Citation2019; Cheng et al. Citation2019b; Iqbal et al. Citation2019; Gómez Pérez, Medellín-Castillo, and Espinosa-Castañeda Citation2017; Sutradhar et al. Citation2015; Moussa et al. Citation2020; Min et al. Citation2017; Deng et al. Citation2015; Bergmann et al. Citation2016; Li, Wu, and Lin Citation2020a; Liu et al. Citation2017; Carnicero et al. Citation2021; Kang et al. Citation2012; Lang et al. Citation2021; Bittredge et al. Citation2022; Liu et al. Citation2021b; Seebach et al. Citation2020; Seebach et al. Citation2017; Dai et al. Citation2018; Liu, Jiang, and Lin Citation2020b; Al-Tamimi et al. Citation2017; Al-Tamimi, Peach, and Bartolo Citation2018; Wang et al. Citation2020a; Lin et al. Citation2021), 25 under automotive (Dalpadulo, Pini, and Leali Citation2020a; Walton and Moztarzadeh Citation2017; Vaverka, Koutny, and Palousek Citation2019; Reddy et al. Citation2016b; Bikas et al. Citation2016a; Großmann et al. Citation2020; Tyflopoulos, Lien, and Steinert Citation2021; Bici, Broggiato, and Campana Citation2016; Junk, Fleig, and Fink Citation2017; Barbieri et al. Citation2017; Barbieri et al. Citation2018; Barreiro et al. Citation2019; Hunar et al. Citation2020; Marchesi et al. Citation2015; Mantovani, Campo, and Ferrari Citation2020; Mesicek et al. Citation2021; Ahn et al. Citation2021; Bujny et al. Citation2021; Cecchel Citation2020; DeBoer et al. Citation2021; Dalpadulo, Pini, and Leali Citation2021c; Dalpadulo, Pini, and Leali Citation2021a; Dalpadulo, Pini, and Leali Citation2021b; Abdi, Ashcroft, and Wildman Citation2018), and 23 under others (Ngim, Liu, and Soar Citation2007; Herbin, Grzesiak, and Krolikowski Citation2017; Lynch et al. Citation2013; Steuben et al. Citation2017; Ye et al. Citation2021; McEwen et al. Citation2018; Dalpadulo et al. Citation2020b; Nourbakhsh et al. Citation2016; Xiao et al. Citation2018; Xu et al. Citation2017; Pilagatti et al. Citation2021; See et al. Citation2022; Ueno et al. Citation2021; Alexandersen, Sigmund, and Aage Citation2016; Alexandersen et al. Citation2018; Dede, Joshi, and Zhou Citation2015; Hayes and Whiting Citation2021; Kanyilmaz et al. Citation2020; Mirzendehdel, Behandish, and Nelaturi Citation2022; Yan et al. Citation2022; Raz, Chval, and Stepanek Citation2022; Schuh et al. Citation2020; Ho et al. Citation2021). The major areas identified in these studies are the adopted TO model, optimisation objective, material, and MAM process. In (a), the gradient-based density methods (SIMP, RAMP) are the most utilised and this is not far-fetched from the understanding that several current TO software tools are based on these methods. It is important to note that some non-gradient methods are gaining popularity, taking 10% of the total, in contrast to the comparatively more established evolutionary and level-set methods. Volume and compliance minimisation are equally popular as optimisation objectives in (b). For material usage, 43% of the case studies use Ti6Al4V and other Ti-alloys in (c) and although it takes the largest portion overall, (e) reveals that the popularity of Ti-alloys is localised to the medical industry while there is a more even distribution of the usage of Ti-alloys, Al-alloys and Steel alloys in the aerospace and automotive industries. LPBF is the most used MAM process across all industries in (d) and within the various specific industries in (f). The BJAM process requires no support structures and typically performs better with geometrically simpler and bulkier shapes compared to LPBF, DMLS/SLS, and EBM. Considering the intricate results produced by TO, it is no surprise that it is the least used MAM process as observed in (d,f). It should be stated that powder-fed processes received no attention in the case studies investigated. This is also no surprise because they require much simpler structural designs to be applicable; therefore, the rest of this study focuses on powder-bed processes.
Figure 8. Chart organisation of (a) topology optimisation models, (b) optimisation objectives, (c,e) materials, and (d,f) MAM processes across the aerospace, medical, automotive, and other industries.
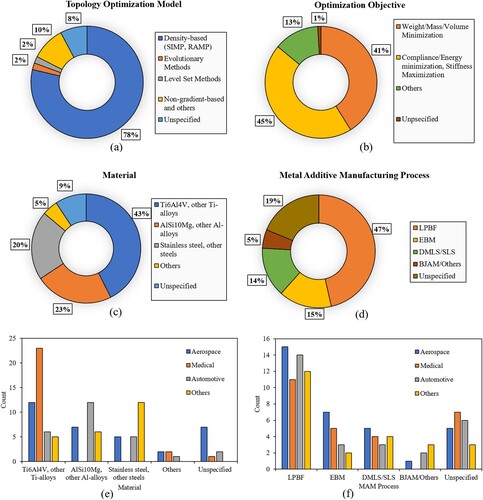
In most case studies, the integration of AM constraints within TO is either not done or not reported. While only a few works (Orme et al. Citation2017; Mantovani, Campo, and Ferrari Citation2020) consider minimum feature size, overhangs, and build orientation optimisation during the design phase, a much larger portion of studies do not account for any MAM-related constraints which are widely developed in TO-AM research studies. Furthermore, void limitation/elimination is not observed to be implemented in any study. These constraints are developed to enable a more seamless and efficient design for manufacturability workflow. However, their lack of use might be attributed to either their absence or limited effectiveness within many commercially available TO software, designers do not consider them critical during the design process, or something else. A study on this dichotomy is important to understand the reasons for it and ways to ensure painstakingly developed TO-AM constraints are beneficial to designers during the DfAM process.
With the benefits of TO, it is expected that MAM will be widely adopted in more industries when two significant challenges are addressed: the high cost of MAM technologies (especially laser and electron beam techs, both initial and running costs) and limited build volumes and speed. Fortunately, Barnes (Citation2021a), Barnes (Citation2021b) showed that these challenges are being addressed with the introduction of multi-laser PBF systems. They showed that moving from a medium build volume single laser system to a large build volume quad laser system, production rates of a control arm increased by almost 100% while costs were reduced by almost 50%.
For many of the case studies amongst the major industries investigated and others, experimental validation studies for functionality are limited. It is important to benchmark the performance of candidate parts suitable for MAM based on functionality in addition to cost and manufacturability. Common functionalities such as stiffness/strength, frequency, heat transfer, pressure drop, surface roughness, etc., depending on the application, should be investigated, and evaluated against the performances of their counterpart designs made from traditional manufacturing processes.
3. Support structure design
AM components often require temporary support material to avoid collapse or warping during fabrication (Zhang, Yang, and Zhao Citation2020b; Blakey-Milner et al. Citation2021; Liu et al. Citation2018b; Mirzendehdel and Suresh Citation2016; Hussein et al. Citation2013; Strano et al. Citation2012; Calignano Citation2014; Hu, Jin, and Wang Citation2015; Langelaar Citation2016a; Cacace, Cristiani, and Rocchi Citation2017; Jiang, Xu, and Stringer Citation2018; Leary et al. Citation2019; Han et al. Citation2018). No matter how these support materials are removed chemically or mechanically, the use of sacrificial material increases total material usage, build time, and clean-up cost. For example, the largest portion of the cost for MAM, besides the equipment cost that is amortised, is the material cost of about 18% (Thomas and Gilbert Citation2014). Besides, the cost of support structure removal can make up for about 8% of the total product cost (Thomas and Gilbert Citation2014). Furthermore, research on support structures for MAM is important because support structures play a critical role in MAM by eliminating cracks, curls, sags, or shrinkages (Jiang, Xu, and Stringer Citation2018; Leary et al. Citation2019; Han et al. Citation2018). For example, in PBF, a high-power laser/electron beam selectively scans over metal powder to form a solidified metal layer to form parts layer-by-layer. PBF is known to contribute to residual stresses, distortion, and heat accumulation issues, which are due to the thermal stresses induced by the high and rapid heat input. To reduce these problems, PBF parts are commonly printed with support structures that are suitably designed to hold overhanging features, dissipate heat to prevent overheating, and anchor the parts to the substrate to reduce unwanted distortions and residual stresses (Mezzadri, Bouriakov, and Qian Citation2018; Zhou, Liu, and Lin Citation2019a; Cheng et al. Citation2019a; Bartsch et al. Citation2019; Zhang et al. Citation2020a).
For the reasons stated previously, support structure optimisation and minimisation are of significant interest within the AM community. Many researchers have used DfAM to optimise the design for the best manufacturing quality, minimising material for support structures and post-processing requirements (Thomas and Gilbert Citation2014; Blakey-Milner et al. Citation2021). As one of the most important DfAM tools, TO has been widely used due to its extensibility and attainability in optimising material distribution in a structure (Liu et al. Citation2018b; Meng et al. Citation2019; Mirzendehdel and Suresh Citation2016; Zhu et al. Citation2021b; Wang et al. Citation2016; Gardan and Schneider Citation2015; Zegard and Paulino Citation2016).
However, TO results are usually not AM-friendly (Liu et al. Citation2018b; Meng et al. Citation2019; Mirzendehdel and Suresh Citation2016), so it is critical to incorporate AM limitations into TO to improve this integration between design and fabrication in actual applications (Mhapsekar, McConaha, and Anand Citation2018; Zhu et al. Citation2021b; Zegard and Paulino Citation2016). To that end, great effort has been put in the design stage to eliminate enclosed voids and support structures (Li et al. Citation2016a; Xiong et al. Citation2020; Zhou and Zhang Citation2019), reduce thermal accumulation (Allaire and Bogosel Citation2018; Wang and Qian Citation2020; Zhou et al. Citation2019a; Miki and Nishiwaki Citation2022), ease residual stress and deformation (Cheng and To Citation2019; Cheng et al. Citation2019a; Bartsch et al. Citation2019; Zhang et al. Citation2020a; Misiun et al. Citation2021; Allaire and Jakabčin Citation2018; Allaire et al. Citation2020; Pellens et al. Citation2020), and so on. Among these constraints, designing structures and/or support structures with overhang angle control is considered an important AM constraint needed in TO and has drawn increasing attention to reduce the amount of support material usage and avoid printing failures (Mirzendehdel and Suresh Citation2016; Li et al. Citation2016a; Xiong et al. Citation2020; Strano et al. Citation2012; Gaynor and Guest Citation2016; van de Ven et al. Citation2020) or even get support-free structures (Zhou and Zhang Citation2019; Mezzadri et al. Citation2018; Guo et al. Citation2017; Langelaar Citation2018; Liu and To Citation2017; Zeng et al. Citation2015; Allaire et al. Citation2004; Liu and Yu Citation2020).
Besides support structures’ elimination, another related aspect is to design them for other loading conditions other than their weight, e.g. thermal loads or residual-stress-induced loads. Even though eliminating support material is beneficial and necessary, support structures are usually required in MAM, e.g. powder bed fusion (PBF) technique (Hussein et al. Citation2013; Strano et al. Citation2012; Jiang et al. Citation2018; Zeng et al. Citation2015). The functionalities of support structures, such as heat dissipation and part anchoring to counter residual stress and distortion, should not be ignored. The inclusion of support structures may alleviate the locally accumulated heat, as the underlying powder (e.g. powder bed fusion) does not conduct sufficient heat away, thereby reducing the possibility for residual stress and warping (Blakey-Milner et al. Citation2021).
The design of an effective support structure relies on its ability to contribute to print success without any support-related in-process errors while utilising the least amount of powder to produce those supports. Amongst all the design techniques, TO is one of the most important due to its versatility and ability to generate conceptual designs (Rozvany Citation2008; Bendsøe and Kikuchi Citation1988; Bendsøe et al. Citation2011; Meng et al. Citation2019; Liu et al. Citation2018b; Zegard and Paulino Citation2016; Zhu et al. Citation2021b; Allaire et al. Citation2020; Wang et al. Citation2021b; Kuo and Cheng Citation2019; Allaire et al. Citation2017; Zhou et al. Citation2016). Thus, researchers have been using TO to either design optimum support structures for AM or eliminate them as much as possible. Based on the different loading conditions, the optimisation of support structures can be classified into 3 categories: support structure for gravity load, thermal load, and residual-stress-induced load.
3.1. Support structure for gravity load
The primary role of support structures in AM is to support overhanging areas against gravity loads. In , five types of support structures are shown: vertical strut-type, honeycomb, porous-type, contact-free, and topology-optimised supports. These temporary supports ensure a component does not collapse or warp during fabrication (Blakey-Milner et al. Citation2021; Liu et al. Citation2018b; Jiang et al. Citation2018; Leary et al. Citation2019; Han et al. Citation2018; Vouga et al. Citation2012).
Figure 9. Types of support structures under overhang areas in different parts. (a) vertical strut-type supports (b) honeycomb supports (Zhang et al. Citation2020a) (c) porous-type support (obtained with permission from GE Additive) (d) contact-free support (Cooper et al. Citation2017) (e) topology-optimised support (Langelaar Citation2019).
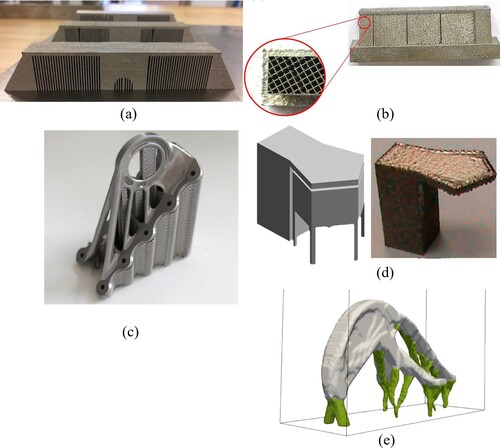
3.1.1. Support minimisation and optimisation
The importance of support structures for thermal-based MAM technologies has been elaborated on in the previous section. Notwithstanding, if support structures are not optimised or minimised, they can significantly increase build time, material, cost, removal time, and energy. Over the past years, many studies have implemented overhang elimination or self-supporting algorithms to ensure parts to be printed utilise minimal support structures. While several of these methodologies are elaborated in Section 4.1, some works that minimise and/or optimise support structures considering gravity loads are highlighted here. Pandey et al. (Citation2004) proposed a weighted-averaging multi-criteria genetic algorithm to minimise support structure and build time while improving surface quality. Calignano (Citation2014) investigated the manufacturability and geometrical precision of LPBF structures. The objective was achieved in two steps: first, understanding the limitation of construction without support structures, and second, optimising support structures by using experimental-driven statistical design (Taguchi L36 design). A complex structure can be manufactured successfully by using the proposed method. To minimise the overall volume of support in a build, Leary et al. (Citation2014) proposed a method to design ‘internal’ support-free optimal structures. First, a topologically optimised structure is derived and then the proposed method is employed to modify infeasible domains by adding extra material to their boundary to achieve self-supporting structures. In addition to optimising a part and its orientation, Hu et al. (Citation2015) employed a shape optimisation model to trim down support structures.
3.1.2. Optimal build orientation
AM build orientation can have a significant influence on the final printed parts as well as support structures (DebRoy et al. Citation2018; Di Angelo et al. Citation2020; Keshavarzkermani et al. Citation2019; Sun et al. Citation2021; Zeng Citation2015). Different spatial orientations of a part cause different overhang areas over a substrate and consequently, different volumes of support structures are needed to fabricate the part, as shown in (a).
Figure 10. (a) Different orientations resulting in different support structure volumes (Di Angelo et al. Citation2020). Optimisation of build orientation to minimise residual stresses using cubic lattice structure, (b) optimal orientation with cubic lattices (c) normalised residual stresses after process simulation. Reproduced with permission from Ref. (Cheng and To Citation2019). Copyright 2019, Elsevier.
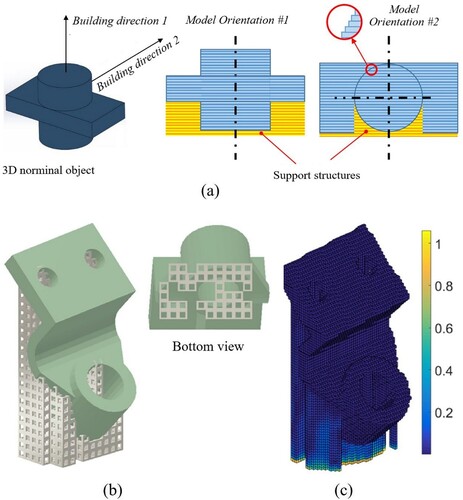
Zhang et al. (Citation2015a) developed a perceptual model to find optimal printing directions that can preserve important visual features. Hu et al. (Citation2015) proposed a method to optimise an original model and its orientation to make it more self-supported. Zhang et al. (Citation2015b) developed a multi-part orientation optimisation method, which is based on a genetic algorithm to find the minimal total build time and cost at an optimal global level.
The optimisation of support structures is important because it can minimise not only the material used but scan time (Dunbar Citation2016). Cheng and To (Citation2019) proposed a method to minimise residual stress and support volume by optimising the build orientation – (a,b). Di Angelo et al. (Citation2020) provided a comprehensive review of the optimal build direction in AM and how the orientation influences part quality, surface quality, support structure, build time, manufacturing cost, and mechanical properties. Therefore, for more information on the build orientation optimisation, the reader is referred to (Di Angelo et al. Citation2020).
3.2. Support structures for thermal load
Support structures can help dissipate process heat and alleviate locally accumulated heat; therefore, they have the potential to minimise geometrical distortions caused by thermal stress (Blakey-Milner et al. Citation2021; Zhou et al. Citation2019a; Calignano Citation2014; Cheng and Chou Citation2020).
Leary et al. (Citation2019) investigated the mechanical strength and thermal properties of AlSi10Mg LPBF support structures and found that the strength of a support structure is inversely proportional to its height and the heat transfer capability increases with smaller support spacings. Ganesh-Ram et al. (Citation2021) found that unsupported overhangs can have effects on the microstructures of the printed parts as well as the hardness due to the different heat accumulation and dissipation. Moreover, support structures influence the fatigue strength of LPBF parts. Kajima et al. (Citation2018) found that adding support structures can improve the fatigue strength of LPBF parts. The improvement is two folds: first, support structures reduced the residual strain which helped to prevent micro-cracks, second, support structures could dissipate heat faster which enabled the formation of finer microstructures contributing to better fatigue strength of the part.
To prevent overheating and increase heat dissipation, researchers have also employed TO to design optimum support structures for PBF. Traditionally, heat transfer TO has been widely used to design heat sinks based on various boundary conditions and objectives (Bendsøe et al. Citation2011; Alexandersen et al. Citation2016; Dede et al. Citation2015; Bruns Citation2007; Gao et al. Citation2008; Dbouk Citation2017; Lohan et al. Citation2019). However, there are much fewer works for AM. Allaire and Bogosel (Citation2018) proposed a level-set TO approach to optimise the heat dissipation and cooling effects of support structures by using a spectral model. Zhou et al. (Citation2019a) proposed the integration of a transient heat transfer model into density-based TO to design support structures shown in (a) to efficiently transfer laser-induced heat to a prescribed heat sink, where an overhang constraint was incorporated to avoid overhang features in both supports and parts. Wang and Qian (Citation2020) proposed a quasi-static boundary-dependent heat conduction model that only applies heat flux to overhanging areas to simplify the layer-by-layer process and employed density-based TO to generate optimal self-support support structures. Recently, Miki and Nishiwaki (Citation2022) developed a model to design support structures to improve heat dissipation in the printing process. They incorporated a computationally inexpensive analytical model that uses the volume heat flux as a heat source for TO; their optimised support structure is shown in (b).
Figure 11. Optimised support structures considering maximum heat dissipation, (a) results from Zhou et al. (Zhou et al. Citation2019a). Reproduced with permission from Ref. (Zhou et al. Citation2019a). Copyright 2019, Elsevier., (b) results from Miki and Nishiwaki (Miki and Nishiwaki Citation2022). Reproduced with permission from Ref. (Miki and Nishiwaki Citation2022). Copyright 2022, Elsevier.
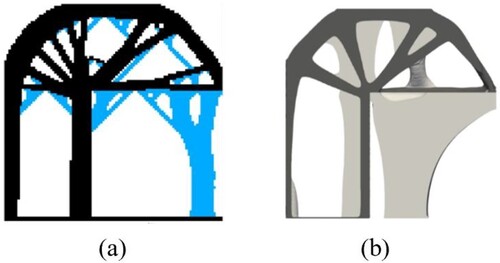
3.3. Support structure for residual-stress load
The importance of support structures also manifests in preventing part distortion in MAM. Thermal-based MAM is similar to a welding process where there is a moving heat source that moves along the laser or electron beam scanning path (Luo and Zhao Citation2018; Zhang et al. Citation2019a). Therefore, the melting and solidification phenomena happening on the material can lead to high thermal stress and part distortion (Frazier Citation2014). Residual stress is reported to induce cracking, delamination, and distortion in MAM (Fang et al. Citation2020; Mercelis and Kruth Citation2006; Vrancken et al. Citation2014), typically spawned by the uneven rapid heating and cooling process. In-situ distortion could cause part-recoater collision and failure of printing. To consider the residual stress and distortion in the design stage, MAM process numerical modelling is significant.
The MAM numerical modelling can be categorised into micro-structure modelling (Sahoo and Chou Citation2014; Körner et al. Citation2020; Li et al. Citation2020c), particle-level modelling (Megahed et al. Citation2016; Stavropoulos and Foteinopoulos Citation2018; Cook and Murphy Citation2020) and continuum modelling (Srivastava et al. Citation2020a; Bayat et al. Citation2021; Luo and Zhao Citation2018). However, the first two are too time-consuming to be used in TO because TO would require hundreds of LPBF process simulations in its iterative process. Therefore, macro-scale models have enjoyed increasing attention in TO due to their shorter simulation times and acceptable prediction accuracies. Wildman and Gaynor (Citation2017) incorporated a macro-scale thermomechanical model into TO to minimise the compliance of structures under the process-induced thermal load.
Moreover, one of the most famous macro-scale methods is the Inherent Strain Method (ISM), which was first proposed by Ueda et al. (Citation1988), and it has been widely employed because of its efficiency and accuracy in predicting MAM parts’ deflections (Keller and Ploshikhin Citation2014; Siewert et al. Citation2019; Yaghi et al. Citation2018; Li et al. Citation2016b). It is also based on the element-birth method; it requires experimentally calibrated inherent strain values and a pure elastic mechanical simulation instead of a thermomechanical simulation, resulting in high computational efficiency. By incorporating ISM into TO, researchers have designed higher-performance structures that can reduce structural distortions and/or recoater-collision failure during the MAM process (Cheng et al. Citation2019a; Bartsch et al. Citation2019; Zhang et al. Citation2020a; Misiun Citation2021). Bartsch et al. (Citation2019) proposed a two-step approach to design support structures in LPBF. The maximum forces obtained by a printing simulation in Amphyon® were transferred into the TO model in Comsol® to reduce the distortions in the LPBF manufacturing process. Cheng et al. (Citation2019a) developed a stress-constraint-based methodology to design lattice support structures to reduce the maximum residual stress caused during LPBF. An in-house code and Simufact® were used to establish the workflow shown in , and the results were validated by experiments.
Figure 12. Workflow process for the implant component. (a) Specimen for printing, (b) voxel-based mesh for analysis, (c) Optimised density profile of support structure, and (d) Optimal lattice support along with CAD model of the component. Reproduced with permission from Ref (Cheng et al. Citation2019a). Copyright 2019, Elsevier.
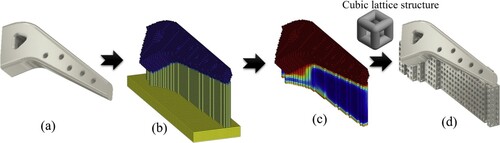
Pellens et al. (Citation2020) invented a method that employs ISM to get the vertical deformations and added the deformations of each printing layer as constraints in TO to achieve distortion reduction. Allaire et al. (Citation2020) also considered two loading situations: gravity and thermoelastic load and the thermoelastic load only. Simufact Additive® software was used to simulate the AM process. Zhang et al. (Citation2020b) proposed a support structure design method by using parallel-computing TO based on the inherent strain method, as shown in , and found that the deflection of printed cantilevers can be reduced to over 60% compared to the original equipment manufacturer’s support structures. It was concluded that a stiffer support structure in terms of residual stress loading can lead to a lower deflection. An analytical explanation was also provided and is in good agreement with the numerical and experimental results.
Figure 13. Support TO results designed by Zhang et al. (Citation2020a) considering the MAM process to reduce part deflection. (a) Original Equipment Manufacturer support, (b) support optimised for part gravity load only, (c) support optimised for both part gravity and residual stress from AM process. Reproduced with permission from Ref (Zhang et al. Citation2020a). Copyright 2020, Springer Nature.
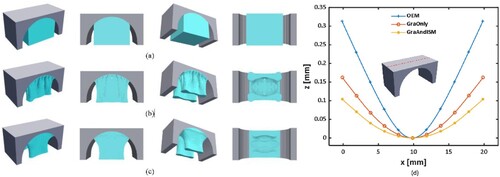
In the following brief discussion, the reasons why the aforementioned efforts can reduce the distortion of a part in its as-built condition and after support removal is presented.
van Belle et al. (Citation2013) found that support structures in MAM can significantly influence the residual stresses in the printed parts. The influence of the support structures on the printed part’s residual stresses was investigated and it was found that a thinner support structure could induce larger residual stress. Hussein et al. (Citation2013) studied the effects of different lattice support structures on part deformation and different volume fractions and cell sizes were also investigated experimentally. It was found that smaller cell sizes and larger volume fractions (stiffer support structures) can lead to smaller deformations. Morand (Citation2021) investigated the influence of supports on MAM parts. Several support patterns were pre-designed and compared. It was observed that the Y-shaped structure could reduce both part deformation and material usage significantly. It is interesting to note that this Y-shaped support structure is of great similarity compared to the support structures derived by Zhang et al. (Citation2020b) using TO, as shown in . Pan et al. (Citation2020a) examined the effects of support structures on part deformation and found that the support hatch spacing and support contact spacing are dominant in the deformation of the final built parts. It was observed that a smaller support hatch spacing and a larger support contact spacing led to smaller deflections which implied that stiffer support structures lead to reductions in deformation. Recently, Xie et al. (Citation2021) and Xie et al. (Citation2018) proposed a constraining force theory to explain the distortions in laser additive manufacturing and applied it to investigate the influence of support structures on cantilever distortions. It was noted that a stiffer support structure could reduce the distortion of printed parts because a stiffer support structure influences lower strains on the previously deposited material induced by the newly deposited layer. This leads to a smaller bending moment and, thus, a smaller distortion after support removal. This is in agreement with the work of Zhang et al. (Citation2020b). Finally, efforts on support structure TO are summarised in .
Table 1. Summary of efforts on support structure TO.
In addition to considering process-induced residual stresses in TO using ISM or its variants, the hatching pattern which can significantly influence thermal gradients has been studied. Takezawa et al. (Citation2022) and Chen et al. (Citation2021a) studied the optimisation of hatching orientation and the use of an island scanning strategy, respectively, together with an ISM for residual stress prediction to alleviate in-situ and ex-situ deformations. The same authors, Takezawa et al. (Citation2020) and Takezawa et al. (Citation2021), also investigated the integration of ISM in a homogenisation-based TO model to obtain variable density lattice structures that limit process deformation. To design process-tailored self-supported structures, Xu et al. (Citation2022) introduced Langelaar’s AM filter Langelaar (Citation2016b) within an ISM-based residual stress-constrained TO approach.
There are a few studies that have focused on considering in-process residual stresses and/or deformation within TO of both the support structure and entire part geometry. Allaire and Jakabčin (Citation2018) proposed residual stress constraints to prevent inducing these undesired effects and incorporated them into a level set TO algorithm by using an adjoint method. Yasin et al. (Citation2018) investigated the minimisation of process-induced warpage in a protector cover using TO and the results showed a significant warpage reduction in the printed product. Miki and Yamada (Citation2021) developed an analytical solution that accounts for the distortion in the TO approach. A two-dimensional design model is utilised for validation of their methodology. Misiun et al. (Citation2021) considered recoater collision and part deformation constraints in their optimisation approach for the cantilever geometry shown in .
Figure 14. Topology optimised cantilever design with distortion and recoater collision constraints (far left), x and y displacement plots of the resulting topology (middle and far right image respectively) (Misiun et al. Citation2021).
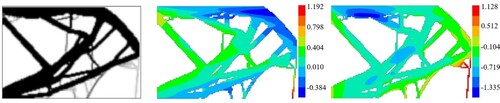
To our best knowledge, most researchers have investigated residual stress and deformation constraints derived from inherent strain process modelling and incorporated them into TO. Moving forward, it will be beneficial to investigate the result of integrating detailed thermo-mechanical process models in TO to ascertain how viable current simplified inherent strain models are in capturing the residual stress and/or deformation constraints.
3.4. Remarks
Support structures in MAM have significant effects on the success and/or quality of printed parts. Support structures have potential influences on the mechanical properties of MAM parts, including quasi-static properties (tension, hardness, torsion, impact strength, fracture toughness, creep), environmental effects (stress corrosion, hydrogen embrittlement, and corrosion fatigue), and dynamic properties (low/high cycle fatigue, creep-fatigue, and fatigue crack growth) (Lewandowski and Seifi Citation2016).
Research on manufacturability-based numerical modelling of TO parts should be further investigated. For instance, support structure modelling is key in attaining a robust MAM process model because support structures significantly influence the formation, or lack thereof, of cracks, curls, sags, or shrinkages (Jiang et al. Citation2018). Multi-physics multi-scale models of MAM are of importance to better understand the manufacturing process by providing feedback on the viability of the structural and material design. Therefore, they assist in mitigating issues such as geometric errors, potentially large residual stresses, porosities, cracks, and poor material properties (Michopoulos et al. Citation2021).
Recently, there has been an increasing number of review papers on MAM modelling. summarises a list of available review papers on the modelling and simulation of MAM process simulation, a large portion of which was published recently in 2020 and 2021. In , review papers are categorised into 3 groups based on the model scale: microstructure modelling, particle-level modelling, and continuum modelling.
Table 2. Summary of review papers on MAM modelling.
To link the MAM process simulation to TO, accelerated models should be considered in the future. Besides the ISM models that can accelerate the simulation, analytical models (Huang et al. Citation2019a; Huang et al. Citation2016; Huang et al. Citation2019b; Flint et al. Citation2018; Mirkoohi et al. Citation2018; Ning et al. Citation2019; Steuben et al. Citation2019; Mirkoohi et al. Citation2020a; Mirkoohi et al. Citation2020b; Mirkoohi et al. Citation2021; Bacciaglia et al. Citation2019; Carraturo et al. Citation2020; Yang et al. Citation2018; Yang, van Keulen, and Ayas Citation2020) are faster and could be considered in the future. The benefit of these analytical models over ISM is that they can generate the temperature distribution, which may be very helpful when considering a TO strategy related to the temperature gradient and cooling rates.
Besides the analytical models, parallel computing is a powerful tool to further accelerate numerical modelling (Zhang et al. Citation2020a; Borrvall and Petersson Citation2001; Fernández et al. Citation2020; Zhang et al. Citation2021). Moreover, machine-learning-based TO is a direction that accelerates optimisation and has acquired increasing attention from both academia and industry (Lei et al. Citation2019; Guo et al. Citation2021; Chandrasekhar and Suresh Citation2021). Lastly, the CAD software for designing support structures and how to design them are two main challenges to consider for future efforts because support structures are of complex shapes, usually lattice structures, which are not very suitable for most CAD tools (Bacciaglia et al. Citation2020; Torigaki and Fujitani Citation2000; Aremu et al. Citation2017). The voxel-based representation is advantageous in a double-pronged way: to obtain fast geometry manipulation and transfer topology-optimised results to a post-process simulation, e.g. MAM process simulation (Bacciaglia et al. Citation2020; Bacciaglia et al. Citation2019). The main advantage of voxelization lies in the possibility to perform design-through-analysis within a single, yet effective numerical environment and without the need to generate finite element meshes that conform to the boundary of the simulated artifact (Zhang et al. Citation2020a; Carraturo et al. Citation2020).
4. Manufacturability considerations
4.1. Overhang elimination
As identified in the previous section, in most thermal-based powder-bed MAM technologies, there needs to be enough material to act as support for successive layers to be printed. If there are regions with unsupported material (overhangs), removable supports will be added. However, this procedure adds material, takes more time, and also requires supports to be removed which then requires additional polishing and/or other post-processing methods. Therefore, substantial efforts have been exerted to minimise the need for support structures or generate support-free structures (Gaynor and Guest Citation2016; van de Ven et al. Citation2020; Wang et al. Citation2021b; Gaynor and Guest Citation2014; Qian Citation2017; Johnson and Gaynor Citation2018; van de Ven et al. Citation2018; Barroqueiro et al. Citation2019; Wang et al. Citation2018b; Zhou et al. Citation2021; Langelaar Citation2016b). Researchers have developed several methods that can be broadly categorised into two groups: implicit methods and explicit methods.
First, the implicit methods are designed to generate support-free structures by using overhang filters or constraint functions to impose a surface slope constraint. Many researchers studied overhang constraints and incorporated them into TO to design overhang-controlled parts. The implicit methods can be classified into two major groups: (a) overhang filters, where element densities are filtered layer by layer based on elementally coordinative relations (Gaynor and Guest Citation2016; van de Ven et al. Citation2020; Langelaar Citation2018; Gaynor and Guest Citation2014; Qian Citation2017; Johnson and Gaynor Citation2018; van de Ven et al. Citation2018; Barroqueiro et al. Citation2019; Wang et al. Citation2018b; Langelaar Citation2016b) or filtered as a whole to generate printable density field (van de Ven et al. Citation2020; van de Ven et al. Citation2018); (b) overhang constraint functions which use specific constraints formulas to suppress the overhang angles larger than a threshold value (Wang et al. Citation2021b; Kuo and Cheng Citation2019; Allaire et al. Citation2017; Qian Citation2017; Mezzadri and Qian Citation2020; Garaigordobil et al. Citation2018; Garaigordobil et al. Citation2019; Zhang et al. Citation2019b; Zhang and Cheng Citation2020; Luo et al. Citation2020; Wang et al. Citation2018a). The overhang constraint methods align with the filter methods as they also use the layer-wise idea to generate their functions. To be specific, they aggregate local constraints (point- or element-wise constraints) to form a global overhang angle regulation, where the local constraints rely on the density gradient information and the elementally coordinative relations. For instance, (Qian Citation2017; Mezzadri and Qian Citation2020; Luo et al. Citation2020) used a Heaviside-projected density gradient while (Garaigordobil et al. Citation2019; Zhang et al. Citation2019b; Zhang and Cheng Citation2020) estimated the boundary normal based on local elemental density. Several other efforts have also utilised the Heaviside density projection or versions of it (Qian Citation2017; Garaigordobil et al. Citation2018; Osanov and Guest Citation2017; da Silva et al. Citation2019).
Recently, (Wang et al. Citation2021b) utilised B-spline parameterisation to generate the gradient of the density field and proposed the use of two constraints for overhang angle control and V-shaped areas. The schematics of the two constraints are shown in (a). Bi et al. (Citation2020) developed a layer-wise geometric constraint to eliminate overhangs based on the BESO framework. (b) shows the application of the constraint in designing an industrial frame compared to an optimised version without the constraint.
Figure 15. The application of overhang or self-supporting constraints in (a) the B-spline parameterised TO. Reproduced with permission from (Wang et al. Citation2021b). Copyright 2021, Elsevier, (b) the BESO-based TO. Reproduced with permission from (Bi et al. Citation2020). Copyright 2020, Elsevier.
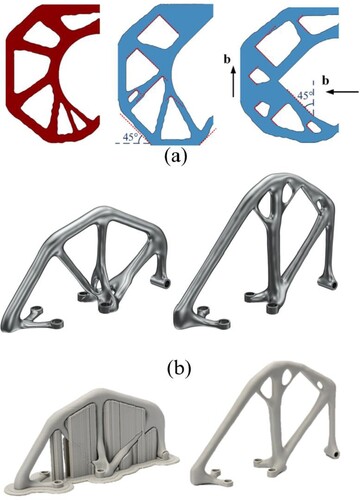
Moreover, level-set methods provide another approach to identifying topological boundaries and imposing overhang constraints using level-set functions (Liu and To Citation2017; Allaire et al. Citation2017; Wang et al. Citation2018a). For example,Liu and To (Citation2017) addressed the self-support manufacturability constraint through a multi-level set modelling to represent the different layers, ensuring each layer is self-supported.
Furthermore, explicit methods, which are also called feature-driven methods, are methodologies that consider the boundaries of an optimised structure as explicit boundary representations (Zhou et al. Citation2016; Guo et al. Citation2017; Zhou et al. Citation2021; Wang et al. Citation2018a; Zhang et al. Citation2015d; Zhang et al. Citation2017; Zhang and Zhou Citation2018; Wein et al. Citation2020). Guo et al. (Citation2017) proposed the use of moving morphable components and moving morphable voids to solve the support-free problem in a geometrically explicit way. Zhang and Zhou (Citation2018) proposed the use of polygonal features (basic primitive) to perform 2D self-supporting structure design. Recently, they extended their work to 3D structures and solved the well-known design problems with V-shaped regions by limiting the positions of solid features (Zhou et al. Citation2021). Wang et al. (Citation2018b) created a constraint using the element (pixels) densities. Any pixel with not enough pixels under it is penalised.
For moving morphable components, the same definitions are reused from the previous section however the constraints are changed. Instead of the size constraints, the overhang constraints are adapted.
Some other efforts to control the formation of overhangs are presented. Jankovics et al. (Citation2018) developed a code where they defined a surface area sensitivity that is a derivative of the surface area of each element with respect to its density. The surface area sensitivities are added to the compliance sensitivities to obtain a final topology.
Li et al. (Citation2016a) developed a way to constrain low-inclined surfaces and avoid unprintable circles by converting them into ellipses. In their case, the constraint is applied after the optimisation. Mass and Amir (Citation2017) restricted the minimum angle of features in a structure using truss optimisation, their procedure works as follows: a ground structure within the design space is optimised with a minimum angle restriction for all the struts. The resulting optimal truss is used as a skeleton onto which they create the continuum structure (based on FE). Only certain elements located at a certain distance from the skeleton are considered. Thore et al. (Citation2019) opted for a penalty regulation to control overhangs. They slightly extend Langelaar’s approach by adding weight factors to penalise sharp corners within resulting topologies. van de Ven et al. (Citation2018) created a filter that eliminates overhang zones. They achieved this using a continuous front propagation scheme to study the progression of the edges. Mirzendehdel and Suresh (Citation2016) transformed the support structures elimination problem into a multi-objective multi-material TO problem by considering both part performance and support structure material function in a consolidated objective function. Cacace et al. (Citation2017) developed a method to generate ad hoc chamfers to reduce the number of support structures based on the level-set method.
Pellens et al. (Citation2018) investigated the combination of the minimum length scale and maximum overhang angle to demonstrate that the overhang angle can be controlled along with the minimum length scale. The paper presents two ways of going about it, the first way is by implementing a minimum length feature followed by a maximum overhang angle filter and the second way is by doing the same thing in reverse. Zhao et al. (Citation2020a) used a convolution function to detect overhanging areas, and with that, generated support-free topology-optimised results. The time efficiency of their proposed convolution method is reported higher than the traditional enumeration method.
4.2. Process-, design-based geometrical considerations (minimum, maximum feature, and length control)
Enforcing a minimum feature size is a common constraint within TO (Mhapsekar et al. Citation2018; Gardan and Schneider Citation2015; Osanov and Guest Citation2017; Sigmund Citation2001; Zhang et al. Citation2016; Zhao et al. Citation2019; Zhou et al. Citation2015; Liu et al. Citation2019; Vatanabe et al. Citation2016; Carstensen and Guest Citation2013; Guest Citation2009a; Zhang et al. Citation2014; Guest et al. Citation2004; Weiss et al. Citation2021). The minimum feature size is enforced during optimisation to enable mesh independency and is also necessary to fulfil the requirements of the manufacturing process. Depending on the manufacturing process, some sizes are not attainable, and it is therefore important to enforce a restriction on such sizes.
To evaluate minimum and maximum feature controls, it is important to define filtering and projection in TO. Filtering is attributing a weight function to an element based on the neighbouring elements or nodes; the amount of neighbouring elements or nodes to consider is given by the minimum size provided by the user. Therefore, the actual density of an element can be rewritten based on the density of the neighbouring elements/nodes (Guest et al. Citation2004; Zhou et al. Citation2015). One typical way the minimum feature size is reached is by first applying a filter and then imposing the filter for every iteration. The minimum size which is imposed during filtering is achieved by deciding how far the last element will affect the current element. Filtering can be done using nodal densities instead of element densities. The main benefit of using nodal densities instead of element densities is the computational cost. In the case of nodal densities, filtering is used to define an element’s density based on the densities of the nodes which are located within a certain radius from that element. For a certain minimum feature size, it is possible to control the number of nodes that have to be considered. However, in the case where elements are used, elements cannot be skipped. This is because there needs to be a density for all of them. Hence, nodal techniques might improve the computational cost for specific conditions (Hussein et al. Citation2013).
Projection refers to classifying continuous inputs into a finite number of outputs (Sigmund Citation2001). In the TO context, the inputs are the densities of the elements of a discretized design with continuous volume fractions between 0 and 1 and the outputs are elements with volume fractions equal to 0 (void) or 1 (solid). Projection is achieved through functions like the Heaviside and Sigmoid or level-set functions.
Zhao et al. (Citation2019) worked on developing porous structures with minimum feature sizes. The authors map topologically optimised geometry on top of unit cells. The TO algorithm they used includes filters that get rid of the need for support structures and another filter to impose a minimum feature size. The specificity of their algorithm is that the elements’ densities are referred to as unit cell volume fractions and when the cell becomes smaller, the volume fraction becomes greater. Qian (Citation2017) used Helmholtz’s partial differential equation (PDE) to impose a minimum feature size. Gardan and Schneider (Citation2015) designed an optimisation workflow to ensure that parts were properly printed. They derived a set of guidelines to couple T.O. with AM by introducing a penalisation factor to impose maximum thicknesses for different walls. Lazarov and Wang (Citation2017) came up with a bandpass filter to restrict the appearance of too-thick or too-thin features. They used bandpass filters, originally used to limit frequencies, to limit the density of elements in the optimisation problem. Mhapsekar et al. (Citation2018) offered a set of guidelines to minimise the number of thin features, support structures, and thus overhangs. While a density filter was utilised to minimise thin features, they applied a weighted multi-objective approach to minimise compliance and support structures.
Liu et al. (Citation2019) discussed the implementation of minimum feature size for multiscale TO. In their words, multi-scale T.O. is ‘an adaptation of the homogenisation-based TO technique to design the local micro or mesoscale structural details of a part or without concurrently optimising the macro-scale structural geometry’. To observe how unit cells would behave, they experimented and concluded that the unit cell size should be selected to be considerably smaller than the part to ensure the homogenisation-based simulation’s accuracy but at the same time, it should be larger than the minimum length scale limit to reduce the impact of the length scale constraint. Osanov and Guest (Citation2017) adjusted the Heaviside projection function to better consider the nature of the layer-by-layer AM process. They transformed the space of influence of neighbourhood elements/nodes from a sphere to a cylindrical shape. Vatanabe et al. (Citation2016) studied the effect of a few manufacturing constraints on the final compliance of the optimised part. The constraints they considered are the minimum member size, and minimum hole size, amongst others. Guest et al. developed a projection method incorporating the nodal volume fractions instead of using the elemental volume fraction (Guest et al. Citation2004), the nodal volume fractions are then projected back onto the element’s centroid.
A TO framework that was developed to ensure a minimum feature size constraint is the moving morphable components (MMC) (Zhang et al. Citation2016). A similar method is moving morphable voids (MMV). The MMC method treats the design space as a set of components or geometrical features which can first be parameterised, then moved, and/or morphed. To satisfy the minimum length/size constraint, restrictions are applied on the minimum size, as well as the minimum intersection between two components.
The different MAM technologies offer different minimum size restrictions. Design guidelines for parts to be printed by LPBF, EBM, and BJ as outlined in Toyserkani et al. (Citation2021) and Diegel et al. (Citation2019) show that the resolvable minimum feature sizes should be 0.1 mm (0.3 mm for vertical walls), 0.5 mm (0.6 mm for vertical walls), and 1 to 3.2 mm (vertical walls inclusive), respectively. However, several variables can cause these minimum sizes to be inapplicable in a practical design case. In a design example shown in , a structure that supports a thin feature in the printed framework has a delaminated support area as shown in the red box on the left image. The framework was printed by LPBF using Hastelloy X as material. Just before delamination, during printing, the aspect ratio of the underlying support structure was small as its width was significantly smaller than its height. The machine’s recoater had sufficient momentum to cause this slender support structure to shift its top position on the powder bed. This shift created a ditch in the region of the powder bed around the top of the slender support structure contributing to its delamination. This delamination contributed to poor heat conduction from the top layers to the substrate, inducing high residual stresses, and thereby resulting in a crack in the boss of the framework during support removal as shown in the right image of . Therefore, it is insufficient to restrict a design to contain unsupported features with sizes close to the minimum allowable by the manufacturing technology as other variables such as support structure length, width, type, build orientation, etc, can adversely affect the build outcome. Lattice cells with strut or wall diameters close to the minimum allowable sizes are typically not seriously impacted by recoater movements since the strut aspect ratios are usually at acceptable values that limit flexing. Metrological experiments (McGregor et al. Citation2019; Rathore et al. Citation2021; Dallago et al. Citation2019; Noronha et al. Citation2022; Colosimo et al. Citation2022) conducted on as-printed strut-based lattices compared to as-designed models show that lattices with strut diameter sizes of 0.5 mm and aspect ratios of over 0.15 are printable without any major defects, however, with ‘overprints’ and ‘underprints’ at different locations.
Unlike maximum size control, minimum size control is critical from two standpoints: optimisation and manufacturability. For optimisation, it is implemented for mesh independency and to eliminate checkerboarding features; for manufacturability, it is implemented to guarantee feature resolution by a given manufacturing technology. Maximum size control, however, is important to give the designer better control of the structural features being formed. In 2009, Guest (Citation2009b) considered the maximum length scale in mechanical and fluid-flow optimisation problems by placing a constraint on the phase composition of circular local regions throughout the design domains. Carstensen and Guest (Citation2018) extended this work by providing nonlinear weighting functions to implement a two-phase minimum and maximum length scale control with the capabilities of actively projecting either the solid or void phases during the optimisation. In quite similar veins, Fernández et al. (Citation2019) and Fernández et al. (Citation2020) implemented maximum length controls as initially proposed by Guest (Citation2009b) by projecting the void phases during optimisation. Lazarov and Wang (Citation2017) used so-called morphological operators to impose a maximum length scale on designs during optimisation. In an attempt to eliminate the discrepancies that can arise between density-based TO results and reconstructed models, Costa et al. (Citation2019) employed Non-Uniform Rational Basis splines (NURBS) hyper-surfaces to formulate the maximum length scale control.
4.3. Enclosed void elimination
Another important constraint is enclosed voids, and although less popular than the previous constraints presented, it has gotten some attention (Li et al. Citation2016a; Zhou and Zhang Citation2019; Liu et al. Citation2015; Zhou et al. Citation2019c; Zhou et al. Citation2019b). Such a constraint targets powder bed MAM such as laser and electron-beam powder bed fusion, binder jetting, etc where there are risks of entrapped powder particles within the printed optimised part. Establishing void connectivities is an approach to resolving enclosed voids. Succinctly expressed, imposing the connectivity of voids is akin to treating the outside of the structure as a ‘void’ and ensuring all internal voids are connected to it. Imposing a constraint on enclosed voids can be done through the Virtual Temperature Method (VTM) described by Liu et al. (Citation2015). The VTM is inspired by heat transfer concepts and treats all enclosed cavities as heat sources, while the solid parts around the cavities are treated as insulators. They applied the enclosed void constraint in the optimisation of torsional cantilevers. They also optimised and printed the cantilever without the constraint; this resulted in the retention of internal support structures and powder as revealed in the sectioned cantilever. However, with the inclusion of the enclosed void constraint, the optimised structure ensured that the internal void was connected to the ‘outer void’ guaranteeing the removal of internal support structures and powder. Other efforts to exclude voids in parts designed by TO can be seen in Xiong et al. (Citation2020), Luo et al. (Citation2020), and Wang (Citation2021a).
4.4. Remarks
In overhang elimination methods, there is one prevailing issue. An arbitrary minimum angle can be imposed during TO, however, this will not necessarily ensure acceptable manufacturability especially when the thicknesses or sizes of features within the printed part are considered. Some more effort should be placed to qualify the manufacturability of overhanging regions through a physics- or data-driven approach. Some algorithms such as the MMC, modify the geometry after the optimisation process, however, these modifications can potentially have undesirable changes on the optimisation objective. Some effort should be placed into investigating the resulting deviations.
5. Porous feature design
There are many forms of porous structures. Often, the results of many TO methods yield varying levels of structural porosities. Sometimes, pores are inserted voluntarily into a structure for lightweighting or other application-specific purposes. The structures that are discussed in this section follow this case. Porous structures can be divided into two broad categories. When holes are introduced with a clear repetitive pattern vs. when holes are introduced with no clear pattern. The sub-category of porous structures that exhibit a repetitive pattern is cellular structures and (Nsiempba et al. Citation2021) discusses them in detail. A subcategory of cellular structures is lattices.
5.1. Porous design strategies based on topology optimisation
This section will review specific TO methods for lightweighting, that produce solutions that functionally have similar features as those produced through latticing. In this context, latticing refers to filling the design volume with repeating unit cells.
Some approaches first use TO, followed by a post-processing step that adds lattices as done in Abdi et al. (Citation2018). The work in Abdi et al. (Citation2018) was done using the Isoline-Extended Finite Element Method (Iso-XFEM) to obtain smoother boundaries in conjunction with BESO (likened to a discrete implementation of the SIMP method Plocher and Panesar (Citation2019)). The BESO method can be used to optimise lattices by assigning the degrees of freedom as the lattice thicknesses to optimise the lattice for maximum stiffness and a fixed mass (Tang et al. Citation2015).
The use of cellular structures through latticing as displayed in literature is mainly for light-weighting and to meet up with design objectives such as heat transfer and energy dissipation (Plocher and Panesar Citation2019). Heterogeneous periodic lattices can be optimised for maximum stiffness by homogenising unit cells into representative volume finite elements (Khanoki and Pasini Citation2012). The same type of lattices can also be designed by mapping the obtained density obtained by the SIMP method to a lattice cell with a certain volume fraction (Alzahrani et al. Citation2015).
A way of generating features in a structure like a heterogeneous and pseudo-periodic lattice is the volume constraint modified SIMP method that implicitly considers a maximum volume fraction in a prescribed local region within the design domain done by Wu et al. (Citation2018). The application for this method was for infill design for AM parts with a fixed external shell. In this method, the global volume constraint typically used in the SIMP method is replaced by a local volume constraint, that has a similar form to the typical SIMP local filtering function but with a weighting of 1 for all neighbourhood cells (Wu et al. Citation2018). Another observation made was that the pseudo-periodic lattice struts have an alignment along stress trajectories, also seen in the human femur bone. The article highlights two features of the SIMP method used to produce a pseudo-periodic lattice, and only for load-bearing applications; robustness to local failure and force variations, which often occur in practical load cases. The robustness to local failure was shown clearly by locally removing material along a vertical line. It was also shown that a pseudo-periodic lattice that is conformal to the stress field has better compliance as well as robustness to local failure compared to a periodic lattice.
Different values of the constants used in the optimisation problem can be used to suppress the formation of wall-like structures instead of trusses. The results given in Wu et al. (Citation2018) are qualitatively similar to the ones that can be obtained using the commercially available ParaMatters software (Bogomolny Citation2018). The work by Wu et al. (Citation2019) extends the work in Wu et al. (Citation2018), by generating a lattice with constant cross-section trusses, having more of them in higher principal stress regions. This is argued to generate results that are more manufacturable by AM. It is also comparatively faster to compute than the local volume constraint method described in Wu et al. (Citation2018) since one finite element corresponds to a lattice cell.
Based on the observation in Wu et al. (Citation2018) that the resulting TO result produces lattice struts aligned with the stress trajectories, another avenue of research is to use the stress trajectories themselves to produce a pseudo-periodic lattice directly; this requires solving only one FEA step to obtain the stress field and would be easier to manufacture by using standard strut geometries. The first article using this approach is by Reinhart and Teufelhart (Citation2013). The method is summarised as follows:
Run an FEA simulation with the design space and the design loading conditions.
From the obtained data calculate the principal stresses for each node.
Using the designer’s input decide on initial points close to the applied loads and from it calculate a line of force or flux line such that its path is always parallel to an interpolated principal stress direction.
Using designer’s input, join the lines of force and add cross trusses to make a lattice structure.
Using an optimisation method adjust the thickness of the struts such that the structure’s compliance and/or maximum Von Misses stresses are minimised.
A structure obtained using the proposed method was very similar to a Michell strut system. As described, the method was applied to a horizontal beam with a downward end load and the algorithm requires user intervention. Another work done by Daynes et al. (Citation2017) follows the same procedure. The method uses Altair OptiStruct 13.0® to calculate the stress field in the design space after topology optimisation without an interpolation function, the lattice is constructed in MATLAB and the resulting lattice is size optimised also using OptiStruct. The force lines are found by manually specifying the initial points and integrating them using interpolated stress field values from finite elements and the Euler method. The key difference here from (Reinhart and Teufelhart Citation2013) is that the stress distribution is from a resulting topology-optimised solution, using no interpolation to promote a high-contrast solution. Another observed difference is that the resulting quadrilateral lattice cells were subsequently filled with another truss cell design. A graphical abstract of the method from (Daynes et al. Citation2017) is shown in . In addition to the use of force lines or stress fields, another popular approach to implementing infill TO-MAM structures is the variable density cellular approach, used by Zhang et al. (Citation2015c) and Cheng et al. (Citation2017) for stiffness maximisation and Takezawa et al. (Citation2019) for effective liquid cooling.
Figure 17. Force line method and resulting lattice for a beam in bending as described in Daynes et al. (Citation2017). Reproduced with permission from (Daynes et al. Citation2017). Copyright 2022, Elsevier.
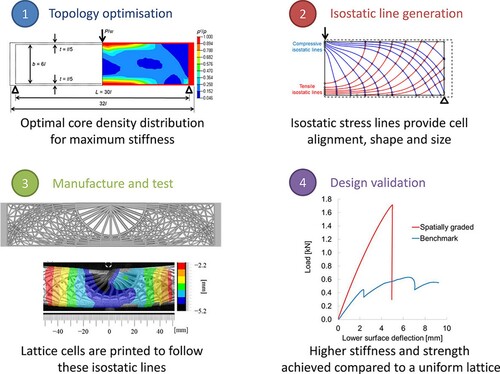
More recent work by Arora et al. (Citation2019) automatically extracts a Michell truss structure from the stress field. This is done by ‘smoothing’ the stress field obtained from linear tetrahedral elements before using the field to produce the lattice. This is done by generating a quadrilateral mesh with a custom mesh generation algorithm and using the stress field as an input. The resulting quadrilateral element edges are also aligned with the stress field. The obtained structures are also very similar to a Michell strut system. The method only extracts a lattice structure with a uniform thickness and does not do sizing optimisation as a final step. The resulting lattices from these methods can be further optimised by adjusting the thickness of the struts. Although the optimised porous structures gene, (Reinhart and Teufelhart Citation2013; Daynes et al. Citation2017) were validated by printing the resulting geometries, they were only printed in plastic which is less challenging than printing them in metal. Although much work has been done to improve the printability of TO-generated geometries and repeating lattices, there are ample research opportunities for further optimisation. The strut dimensions can be further optimised as a post-processing step; possibly using a gradient-based method like in SIMP for example but with the optimisation variables being the strut thicknesses, and using an FEA solution for a frame structure with fixed lattice nodes. Additionally, LPBF fabrication constraints can either be integrated within the algorithms or introduced as post-processing steps.
Other efforts to consider strut-like porous structures within topology optimisation for metal additive manufacturing can be seen in the work by Lin et al. (Citation2007) who adopted a dual TO approach. The dual approach consisted of a macroscopic or first-scale TO to obtain the density design field while the second approach involved a homogenisation method to design the microstructure and come up with effective and specific elastic properties across the porous design. In the study, lumbar interbody fusion cages were printed via LBPF using Ti6Al4V to show the potential of the proposed methodology. In a similar effort by Xiao et al. (Citation2013), the homogenisation method was used to design load-bearing bone implants having high stiffness and relatively large porosities to encourage bone ingrowth. Results showed improvements in the computationally tested elastic modulus of the optimised scaffolds compared to more standardised cubic scaffolds. Schwerdtfeger et al. (Citation2011) and Takezawa et al. (Citation2017) also utilise homogenisation-based TO to implement auxetic and porous structures, for compliant mechanisms and to obtain high stiffness and strength steels respectively, through powder-bed AM processes.
Another research effort within the past couple of years is the combination of TO and surface-based or triply periodic minimal surface (TPMS) lattices to obtain functionally graded porous structures. Although this area is beyond the scope of this work considering TO is typically not used to directly generate the minimal surfaces, some recent works are noteworthy. Strömberg (Citation2022) proposed a TO framework that provides a macro layout for the design problem and a relative density field for an infill surface lattice structure. To gain more control over TPMS lattices, Hu et al. (Citation2022) utilised TO to optimise the scale distribution of graded shell-infill walled gyroid structures. A novelty in this study is the functions that were developed to represent, analyse, optimise, and store information thereby avoiding remeshing the structure upon a design change. Relative density mapping to manipulate unit cell volume fractions is one of the most popular approaches in obtaining graded TPMS designs as observed in Zhang et al. (Citation2022), el Khadiri et al. (Citation2022), Alkebsi et al. (Citation2021), and Ren et al. (Citation2021) while the use of TO and TPMS for thermo-fluid/thermal-based applications is conducted in Wang et al. (Citation2022) and Yeranee et al. (Citation2022). Most of the aforementioned efforts were conducted within the last 2 years and understandably, they are mostly numerical/theoretical with little or no experimental verification. While these methodologies are in their infancy, it is a good practice to commence manufacturability and mechanical studies on resulting designs early on to tweak the algorithms where necessary. For example, results from the study by Hu et al. (Citation2022) often give ‘stretched’ and/or thin wall surfaces that might not be well supported against gravity or well connected for heat conduction for a build orientation perpendicular to their longitudinal axes.
5.2. Remarks
One challenge of leveraging TO for metal 3D printing is making sure the topologically optimised design is manufacturable. A recent work that attempts to find an optimised shape that is designed not to fail during printing is (Misiun et al. Citation2021) which included an inherent strain mechanical model to take into account distortion after separation from the build plate and re-coater collisions. A review of a similar previous technique referred to as ‘space-time’ TO for wire-fed directed energy deposition is described in Wang et al. (Citation2020b). These techniques use a simpler model to take into account the self-weight of intermediate structures, process-dependent loads, and time-dependent mechanical properties such as a curing process. More efforts in this direction are expected in the future, especially with the increase in powerful computing resources. The use of models inspired by the physics of the printing process might be more beneficial rather than an observation-driven metric such as overhang constraint angles (Leary et al. Citation2014).
6. Artificial intelligence-assisted design
The conventional TO process usually requires several iterations in the order of tens to hundreds to arrive at an optimal design and each iteration can be computationally expensive, especially for high-resolution applications. Machine Learning (ML) models, especially deep learning, can be used to drastically reduce the computational time since when well-trained, can compute several design problems quickly without undergoing the iterative process of conventional TO methods. Several researchers have employed deep learning-based methods for TO: Sosnovik and Oseledets (Citation2019) employed a convolutional neural network (autoencoder-type network) trained with intermediate topologies received from conventional TO approaches. The optimisation problem was modelled as an image segmentation task with the inputs into the network consisting of two greyscale images (2-channel image) with one channel containing the density distribution of an iterated solution from a regular TO solver. The second channel contained the last gradient update of the densities of the last performed iteration. The model prediction is a greyscale image of the predicted final structure; their proposed model is shown in (a). The results showed that the encoder-decoder architecture could predict optimised structures up to 20 times faster with few pixel-wise changes compared to the standard simplified isotropic material with penalisation (SIMP) approach. The methodology was also shown to solve heat conduction problems, outperforming SIMP results both in speed and binary accuracy-wise with thresholding. Banga et al. (Citation2018) extended the encoder-decoder CNN architecture to generate 3D structures. Their approach involves the use of an FEA-based TO software, TopOpt (Aage et al. Citation2015), based on the SIMP method to generate structures from the initial TO iterations. The optimisation process is then stopped at an intermediate stage after which the current structure from the process is fed into the CNN network to predict the final structure. The input into the network includes the 3D density distribution of the conventional TO, gradient voxel densities between iterations, forces, and boundary conditions along x, y, and z directions. The results showed that a trained network architecture can predict the final structures instantaneously with an average binary accuracy of 96.2%- and 40%-time reduction as compared to solely using the FEA-based SIMP method. In Abueidda et al. (Citation2020), they also utilised CNNs to predict optimised structures for a given set of boundary conditions, loads and optimisation constraints. They considered materials with hyper-elastic responses having material and geometric nonlinearities. The dataset used in training the model is composed of optimised designs and their corresponding boundary conditions, load, and volume constraint from conventional topology optimisers. Preliminarily results showed CNN could derive optimised results with much less computational costs.
Figure 18. Application of deep-learning-based models (a) CNN used for prediction of optimised structures from intermediate topologies (Sosnovik and Oseledets Citation2019) (b) GANs for TO (Rawat and Shen Citation2018).
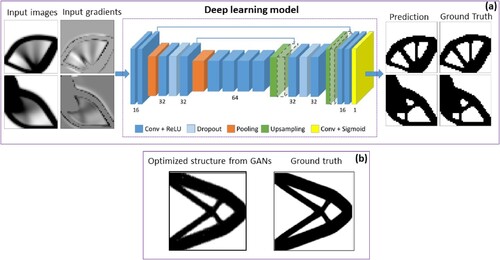
Generative modelling (Creswell et al. Citation2018) is a very exciting field that has several diverse applications. Generative Adversarial Networks (GANs) are unsupervised machine learning methods that automatically find parameters that model high-dimensional data and generate new data from sampling the distribution. Yu et al. (Citation2018) applied a deep learning-based approach to generative modelling. This was done by applying GANs to generate optimised structures without TO iterations. They used a type of generative network called the variational autoencoder (VAE). The encoder section of their network extracted relevant features from the input space to derive the mean and variance latent variables that enabled several optimised structures. Although their model to predict test cases was devoid of gradient-based TO processes, all training data was generated from the SIMP TO method. The drawback of this approach is the computational time required in generating the training data. Rawat and Shen (Citation2018) also employed GANs to generate optimised structures for certain constraints and conditions. The training dataset was also gotten from a conventional TO code which uses the SIMP model. In comparison to other existing conventional algorithms, their approach showed the capability of generating sub-optimal topology with a relatively small training dataset. An optimised topology from their GAN model compared to a reference ground truth is shown in (b).
Another application of machine learning in TO is parameter tuning. Lynch et al. (Citation2019) introduced a machine-learning framework to derive optimal parameters in TO. The framework involves a two-step process where a recommendation of parameters is first derived from similar domain problems to serve as the training data for the next step which involves using Bayesian optimisation to refine the parameters for a specific TO problem. The authors developed a quality metric to quantify the robustness of the solution and applied it to simple optimisation problems. The approach was shown to be less computationally expensive, and the application to more complex TO problems was reserved for future work.
The aforementioned efforts focused on optimising structures without manufacturing considerations. A research effort oriented to part manufacturability by LPBF is seen in the work by Naresh et al. (Citation2021). They applied a 3D-Unet CNN-based attention architecture to optimise LPBF-manufactured parts against in-process cracking; their methodology is expressed in . Their approach involved formulating the optimisation task as a segmentation problem where training inputs were derived from conventional TO methods or simulators. These inputs were fed into a 3D attention Unet architecture to predict optimised structures in compliance with either the maximum shear strain index (MSSI), strain failure index (SFI), or total strain energy density index (TSI), with the conclusion of MSSI as the best index for predicting the likelihood of cracks. The unique aspect of their approach involves the use of weights from the penultimate network layer to generate maps that focused on regions most relevant to accurate crack index estimation. Their framework demonstrated the effectiveness of CNN-based methods to derive optimised structural parts for LPBF with reduced MSSI values and minimal computational time.
Figure 19. A PATO framework to integrate additive manufacturability in the part design process through a deep neural network predictor (Naresh et al. Citation2021).
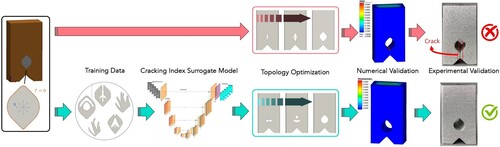
In the background of these aforementioned successes, a recent robust and critical review on the use of artificial intelligence in topology optimisation was done by Woldseth et al. (Citation2022) from the famous TopOpt group led by Ole Sigmund. An important observation made was the many direct AI design models for TO in literature and it was argued that these models often generate poor designs which are costly to obtain with a limited problem and mesh generality. It was suggested that the use of AI to attempt to provide iteration-free TO models should be abandoned while the focus should be placed on alleviating the computational cost of portions within the iterative process. The study also suggested that investments should be made in improving physics-informed neural networks (PINNs) for TO and neural network models for result post-processing.
In reflection, deep-learning methods especially CNNs are quite promising in deriving optimal structures with minimal computation time. These methods are heavily dependent on the numerical solutions from conventional TO methods thus the accuracy of these deep-learning approaches is limited to the quality of the dataset used in training these models. Nevertheless, they show high potential for practical use cases and thus require further studies. Consequently, in the short term, the focus should be placed on physics-influenced models such that there is less dependence on the results of conventional TO methods as sole ML inputs. Rather, the physics governing the TO problem and objective/constraint sensitivity analysis can be captured within the ML model. There is also the need to explore high-resolution 2D and 3D structural problems that will ensure these models become useful within the DfAM framework. In the long term, the aim will be to allow AI-driven TO models to solve structural design problems for part performance as well as manufacturability.
7. Simulation and software capabilities
Several software tools can now assist in the DfAM workflow by addressing at least one of its stages as shown in . The first stage in the DfAM workflow shown is pre-processing, which involves creating a three-dimensional (3D) model and defining the design space, after which TO can be set up and run. Once an optimal design is generated, its 3D model can be modified and refined in the post-processing step to meet any form, fit, function, and DfAM requirements. The final steps involve validation of the model via numerical or analytical approaches, after which the optimisation may be redefined and repeated as desired, or the design can be finalised. Simulation of MAM processes can also be used to predict any fabrication issues and inform design changes. In this section, we present and compare a range of software tools for TO and MAM process simulation.
Figure 20. TO workflow with major steps. (a) Pre-processing design space and boundary condition defining using a color-coding representation (Ibhadode et al. Citation2021) and a voxelization approach (Zhang et al. Citation2021) (reproduced with permission from (Zhang et al. Citation2021). Copyright 2021, Springer Nature) (b) topology optimised models (Ibhadode et al. Citation2021; Zhang et al. Citation2021) (c) Post-processing step to smoothen a topology optimised connecting rod model generated in nTopology (nTopology Citation2023) (d) Different length scales and models required to model MAM processes. Reproduced with permission from (Francois et al. Citation2017). Copyright 2017, Elsevier. (e) Prediction of hot and cold defects for PBF processes using a probability of thermal errors. Reproduced with permission from (Moran et al. Citation2021). Copyright 2021, Elsevier.
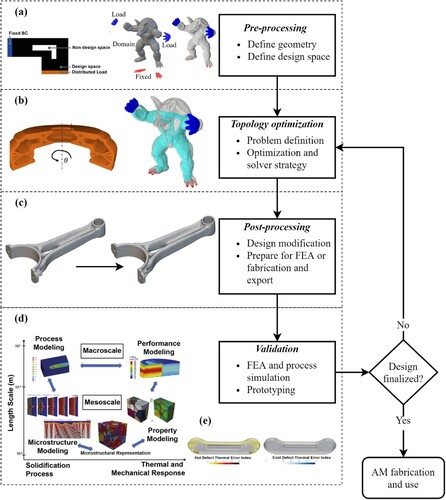
7.1. Open-source software and frameworks
There are several open-source tools with complete workflows for TO (Aage et al. Citation2015; Zhang et al. Citation2021; Aranda et al. Citation2020; Kambampati et al. Citation2018; Vogiatzis et al. Citation2017). Some provide a nice user interface (UI) and allow defining two-dimensional (2D) or three-dimensional (3D) problems for objective functions such as compliance minimisation (Zhang et al. Citation2021; Aranda et al. Citation2020; Smith and Norato Citation2020) and global temperature minimisation (Zhang et al. Citation2021). Ease of use and accessibility are typically prioritised so new users can familiarise themselves with TO and its workflows quickly. However, open-source tools that address workflow steps in a modular approach, such that they can be coupled with other tools, are particularly advantageous (Kambampati et al. Citation2018; Talischi et al. Citation2012). By creating tools that address discrete parts of a workflow, they can be interchanged conveniently to give developers fast access to recent developments in TO research. Here, examples of open-source software that address at least one of these steps in TO workflows are reviewed: pre-processing, TO, post-processing, and AM simulation.
7.1.1. Pre-processing tools
Pre-processing for TO involves a preliminary definition of the optimisation problem by creating a 3D model and designating the design space. This step can be mainly satisfied by general open-source CAD (Hennes Citation2022; Kintel Citation2022; Kazakov Citation2022) and meshing tools (Kazakov Citation2022; Geuzaine and Remacle Citation2009; Si Citation2015; Mahadevan et al. Citation2022), so open-source pre-processing tools made specifically for TO workflows are rare. One pre-processing tool developed by Ibhadode et al. (Citation2021) provides a colour-coded visual UI to improve accessibility. Both the design space and boundary conditions (BCs) for structural optimisation problems are definable using a color-coding representation in a 2D grid, see (a). As problem complexity increases for 3D geometries with many multi-physics constraints, the utility of this representation increases its convenience for helping the user identify and edit constraints. However, this requires effective communication of BCs to any downstream tools. As well, Zhang et al. (Citation2021) developed a parallel computing TO framework named TopADD, which expands on Aage et al’s framework (Aage et al. Citation2015) and provides classes for pre-processing, see (a,b). These classes provide functionality for importing and voxelizing design domains as STL files and accommodate 2D and 3D dimensionality. This gives the designer freedom in initialising complex design domains beyond simple solid geometry primitives (cubes, spheres, etc.). This framework expansion is designed to handle linear compliance and heat conduction design problems. Similarly, Aranda et al. (Citation2020) developed a pre-processing tool for linear compliance and volume minimisation TO problems with their software TOptimiz3D. This requires a design domain mesh to be generated before importing to TOptimiz3D, where constraints, boundary conditions, material properties, and optimisation parameters can be defined. Since these pre-processing tools are limited to linear FEA, more complex bending loads will be harder to simulate, leading to less accurate optimisation results.
7.1.2. Topology optimisation: PDE solvers and processing tools
Many open-source codes implementing new TO strategies are made available in literature and have recently been reviewed in Zhang et al. (Citation2021), Ribeiro et al. (Citation2021), and Deng et al. (Citation2021). These codes generally implement a new technique and solve several benchmark problems to characterise their effectiveness, though they can be adapted to different problems. Open-source codes that focus on implementing AM-specific constraints (feature size, build direction, overhang constraints, etc.) were investigated in literature and found to be rare. One example is a tool developed in C++ (Amir and Amir Citation2021), which minimises compliance while improving printability by adding lattice supports. Several example structures are completed in 3D for different build directions, and lattices are only added when they do not significantly alter compliance (Amir and Amir Citation2021). Overall, there is a current need for more open-source codes implementing AM constraints in TO.
To enable solving applications of greater complexity and scale (e.g. 3D multi-physics optimisation), powerful tools for PDE solving are needed. Open-source toolkits and libraries can be implemented for these purposes, which should address requirements such as efficiency, speed, and accuracy (Meng et al. Citation2020; Morse et al. Citation2021; Li and Chen Citation2018). Ideally, they also allow users to develop custom objective functions and constraints for specialised problems. To meet these criteria while achieving modularity, open-source PDE solvers such as FEniCS (Alnæs et al. Citation2015) and FreeFEM (le Hyaric et al. Citation2022) are currently very popular in TO research, being used recently in Laurain (Citation2018), Sá et al. (Citation2021), Alonso et al. (Citation2019), Sun et al. (Citation2020), Miki and Nishiwaki (Citation2022), Kim et al. (Citation2020), Zhu et al. (Citation2021a), Jung et al. (Citation2021), Li et al. (Citation2021), and Li et al. (Citation2022), respectively. These PDE solvers offer high-performance computing (HPC) and parallel processing to enhance their solution speed and handle computationally demanding problems. A similar powerful PDE solver is deal.II (Arndt et al. Citation2021), which also offers parallel processing capability for many varieties and orders of FE elements. However, some more modern functionalities such as HPC are not yet provided by deal.II. Another advanced PDE solver toolkit is MFEM (Anderson et al. Citation2021), which enables parallel scalable processing to thousands of cores, efficient high-performance computing (HPC), graphics processing unit (GPU) acceleration, and strong, diverse meshing capabilities. These tools present a significant incentive for MFEM’s use in TO research, which has been done in White et al. (Citation2020) and White et al. (Citation2018). To enable parallel processing and GPU acceleration, the PDE toolkit is PETSc (Balay et al. Citation2021) is very popular, having been used for TO applications in structural and DfAM applications (Amir and Amir Citation2021), fluid dynamics (Høghøj et al. Citation2020; Lazarov et al. Citation2018), and heat transfer problems (Zhang et al. Citation2021; Høghøj et al. Citation2020; Lazarov et al. Citation2018). For more flexible multi-physics coupling using different solvers, the coupling library preCICE (Bungartz et al. Citation2016) can be used to facilitate communication, and already has official adapters for several popular solvers. A great advantage of this library is its intentional modularity in its design, which allows simple coupling with black box solvers without requiring significant solver code changes. This enables easy incorporation of custom in-house tools. For examples of other open-source toolkits and libraries, we refer the reader to OpenMDAO (Gray et al. Citation2019), DUNE (Bastian et al. Citation2021), OpenFOAM (OpenCFD and ESI Group Citation2021), and libMesh (Kirk et al. Citation2006).
7.1.3. Post-processing and AM simulation
Post-processing involves altering and exporting the optimised geometry so that it can be re-designed, modelled for validation, and manufactured (Subedi et al. Citation2020). Surface-based representations generated by TO tools regularly require secondary operations such as smoothing or remeshing to improve surface quality. In addition to the open-source meshing tools mentioned in 7.1.1, CGAL (Project Citation2021) and TTK (Bin Masood et al. Citation2021) offer many powerful capabilities including polygonal reconstruction, mesh segmentation, simplification, and conversion to skeleton forms. (c) shows geometry smoothing from an optimised solution in the commercial software nTopology (nTopology Citation2023). GIBBON (Moerman Citation2018) also provides smoothing, refinement, and remeshing functionality. A disadvantage of the surface representations that conventional TO tools generate is that they are difficult to convert to an editable 3D CAD model (STEP, IGES, etc.). Recent TO research on isogeometric analysis techniques employ geometry representations such as non-uniform rational basis spline (NURBS) (Costa et al. Citation2021; Montemurro and Refai Citation2021), and T-Splines (Zhao et al. Citation2020b) to overcome this issue. While they show promise for simplified conversion to an editable 3D CAD model (Costa and Montemurro Citation2020), to our knowledge no open-source tools currently exist that can reliably do this conversion from 3D isogeometric representations.
After traditional smoothing and remeshing operations, the CAD model can be prepared further by considering MAM process modelling. Besides considering AM constraints previously discussed (e.g. feature size and supportless geometries), simulating MAM processes is a non-trivial problem that requires the coupling of models at different length scales (Francois et al. Citation2017; DebRoy et al. Citation2021; Wei et al. Citation2021) (see (d) for overview of model coupling). Thorough reviews of the state of MAM process simulation are provided in Francois et al. (Citation2017), DebRoy et al. (Citation2021) and Wei et al. (Citation2021), which also reference many commercial and open-source software tools. Here we refer the reader to some additional open-source tools and research conducted recently. Moran et al. (Citation2021) developed a tool that models thermal stresses during powder bed fusion (PBF), using thermal fields to predict defect occurrences. For a sample part studied in (e), they demonstrated that geometry, layer elevation, and scan strategy can influence defect generation, due to inadequate or excessive thermal energy (Moran et al. Citation2021). Also, Rodgers et al. (Citation2021) developed the Potts Monte Carlo tool SPPARKS to simulate grain growth mechanics during PBF processing. To prepare designs for MAM fabrication, process models are ideally coupled with scan path optimisation techniques and they have been studied recently in Liu et al. (Citation2021a), Liu et al. (Citation2020a), and Boissier et al. (Citation2020). To enable greater tool path control and geometric freedom, Gleadall (Citation2021) developed a flexible path planning open-source tool. Both non-extruding and extruding paths can be controlled, and non-planar print paths, feed rates, speeds, etc. can be defined. Overall, advanced path planning and optimisation techniques can still be developed further (Zhao and Guo Citation2020) and coupled with AM process simulation for their effective deployment in software tools.
7.2. Commercial software
Seven different commercial TO tools that offer complete workflows (including pre- and post-processing functionalities) are compared in based on their functionality. Desired functionalities for MAM are considered, such as functionally graded latticing, overhang, and feature size constraints. Fusion 360 (Autodesk Citation2022) uses a generative design tool that employs machine learning methods and cloud-based solving to enhance its TO features. While being a unique alternative to other commercial tools, it lacks some tools for enabling AM designs. Conversely, some of the tools with more AM functionality include nTopology (nTopology Citation2023), ANSYS Mechanical (Ansys Inc Citation2022), Optistruct (Altair Engineering Citation2021a), and Inspire (Altair Engineering Citation2021b). nTopology’s (nTopology Citation2023) unique capabilities include many lattice design tools, implicit modelling, and field-based designs. Optistruct (Altair Engineering Citation2021a) is one of the most-developed software tools for TO, allowing more complex multi-physics definitions and providing SIMP, RAMP, polynomial, and level-set TO methods. ANSYS Mechanical (Ansys Inc Citation2022) also provides similar powerful features including allowing build direction definitions, SIMP and level-set methods, and multiple solver types including sequential quadratic programming (SQP) and optimality criteria (OC). Inspire (Altair Engineering Citation2021b) is a more user-friendly version of Optistruct (Altair Engineering Citation2021a), with some of the advanced user functions removed in exchange for a simpler UI.
Table 3. Commercial TO software with multiple functionalities of interest.
We note that while multi-material (MM) metal TO methods have been implemented in research (Bohrer and Kim Citation2021; Kazemi et al. Citation2020; Sha et al. Citation2021), none of the seven commercial tools here possess this functionality. Just as the advent of practical AM processes sparked renewed interest in TO (Gebisa and Lemu Citation2017a), we expect TO software progression to be partially dictated by AM’s technological development. Ongoing research in the field of MM MAM shows great promise for increasing design flexibility more suitable for TO. For example, Wei et al. (Citation2019) produced parts with a MM continuous gradient between Cu10Sn and 316L stainless steel (SS) using selective laser melting. These continuous gradient designs would be well-suited to mesh-based TO, which naturally produces material gradients (Zegard and Paulino Citation2016) (which are normally penalised for single material optimizations). However, MM MAM parts are still only being produced in laboratory settings and require more development to reliably produce MM topology-optimised geometries (Schneck et al. Citation2021; Gralow et al. Citation2020). We expect that future demand, development, and commercialisation of MM TO tools will increase as MM MAM processes become more practical.
8. Conclusion
In this work, the symbiosis between TO and MAM has been amply examined. This investigation has covered industry-related applications, support structure designs, manufacturability-oriented designs, porous considerations, artificial intelligence-assisted modelling, and software availability. This study has shown that several advancements have been made to address future considerations suggested by Liu et al. (Citation2018) in 2018 such as process-induced residual stress/deformation integrated into TO and combined support-free and build orientation TO. In addition to these, in the past 5 years, we have observed hundreds of research efforts go into the design or redesign of components in the aerospace, automotive, medical, and other industries using TO and MAM. There have also been model considerations for enclosed cavities and process-influenced geometrical constraints. An interesting and nascent field of study is the use of machine and deep learning approaches to either generate topology-optimised structures or realise a wider DfAM spectrum. A former major hindrance to actualising practical or working designs in DfAM is software capabilities, however, the past few years have revealed new or enhanced open-source and commercial frameworks which either consider parallel computing or utilise new modelling strategies such as implicit and field-driven concepts.
Even with the immense progress achieved in TO for MAM, there are still several boxes that need to be checked. A foremost challenge is validating and standardising the several algorithms developed such that they become widely applicable. We observe that in the industrial case studies, very few studies included the many manufacturability-constrained TO approaches. The disconnect between these algorithms and DfAM for practical use cases needs to be studied and worked upon. Artificial intelligence-assisted models need to be extended to large-scale, high-resolution TO problems while considering additive manufacturing limitations. Notwithstanding, the immense research effort being put into these areas and the promising results obtained already only affirm the prosperous future of TO for MAM as forecasted by Liu et al. (Citation2018).
Supplemental Material
Download MS Word (150.6 KB)Disclosure statement
No potential conflict of interest was reported by the author(s).
Correction Statement
This article has been corrected with minor changes. These changes do not impact the academic content of the article.
Additional information
Funding
Notes on contributors
Osezua Ibhadode
Dr. Osezua Ibhadode is an assistant professor in Mechanical Engineering at the University of Alberta, Edmonton, Canada, and directs the new Multifunctional Design and Additive Manufacturing lab. His research is focused on design for additive manufacturing for multiphysics and multidisciplinary applications. He obtained his Ph.D. in Mechanical Engineering and completed a postdoctoral fellowship in the Multiscale Additive Manufacturing (MSAM) lab at the University of Waterloo.
Zhidong Zhang
Dr. Zhidong Zhang is a leading researcher who specializes in the study of high-performance computing for additive manufacturing-oriented structural optimization. He received his Ph.D. in Mechanical Engineering from the University of Waterloo, Canada. His research interests include heat source modeling, structural topology optimization, and parallel computing for metal additive manufacturing. His research has been published in many academic journals and he has presented his findings at recognized conferences around the globe.
Jeffrey Sixt
Mr. Jeffrey Sixt holds a MA.Sc in Mechanical and Mechatronics Engineering from the University of Waterloo. During his degree he specialized in leveraging AM for vibration strain sensing wearable devices and developed design optimization algorithms for AM-based designs. He now works at an augmented reality startup designing light engines.
Ken M. Nsiempba
Mr. Ken M. Nsiempba holds a MA.Sc. in Mechanical and Mechatronics Engineering from the University of Waterloo. During his degree program, he focused on studying how to effectively manage the coupling of geometrical constraints in additive manufacturing within the topology optimization process. He possesses extensive expertise in computational geometry and currently serves as a data scientist at a medical startup, where he specializes in analyzing medical images.
Joseph Orakwe
Mr. Joseph Nonso Orakwe is a Ph.D. student at the University of Waterloo's Mechanical & Mechatronics Engineering department, conducting research on design optimization for additive manufacturing at the Multi-Scale Additive Manufacturing Lab (MSAM). He completed his bachelor's studies at the University of Benin, Nigeria and his Master's degree at the Technical University of Ingolstadt, Germany.
Alexander Martinez-Marchese
Dr. Alexander Martinez-Marchese obtained his Bachelor's and Master's degrees from the University of Toronto in mechanical engineering. After his master's Alexander worked as a research engineer at Dyson Technology Ltd., where he specialized in gas-particle separation technologies, experimental fluid dynamics, and CFD, and obtained an international patent on a low-energy particle separation system. Afterward, he completed a Ph.D. at the Multiscale Additive Manufacturing (MSAM) lab, University of Waterloo, where he researched laser ultrasonics, and developed and obtained a patent for a novel technology for directed energy deposition called ultrasound particle lensing. He is currently a Postdoctoral Fellow at the MSAM lab.
Osazee Ero
Mr. Osazee Ero is a Ph.D. candidate at the University of Waterloo's Mechanical & Mechatronics Engineering department, conducting research on artificial intelligence for quality assurance in additive manufacturing at the Multi-Scale Additive Manufacturing (MSAM) lab. He completed his Bachelor's studies in Electrical/Electronics Engineering at the University of Benin and his Master's degree in Systems Engineering at the University of Lagos, both in Nigeria.
Shahriar Imani Shahabad
Dr. Shahriar Imani Shahabad completed his Ph.D. at the University of Waterloo in the Multiscale Additive Manufacturing (MSAM) lab. His main research is on the multi-physics modeling of additive manufacturing processes, especially Laser Powder-bed Fusion (L-PBF) and Electron Beam Powder-bed Fusion (E-BPBF) processes. He is involved in an industrial project related to the topology optimization of fluid channels in heat exchanger components.
Ali Bonakdar
Dr. Ali Bonakdar is an Advanced Manufacturing Technology Lead at Siemens Energy Canada Limited, Gas and Power Division, responsible for the strategic development of various advanced manufacturing processes with a particular focus on additive manufacturing. In addition to his industrial role, he is an Adjunct Professor at Concordia University, University of Waterloo, Western University, and École de technologie supérieure (ÉTS); leading several industrial-academic research projects.
Ehsan Toyserkani
Dr. Ehsan Toyserkani is a professor in Mechanical and Mechatronics Engineering, at the University of Waterloo. He holds the Canada Research Chair position in Additive Manufacturing (AM) and has over 20 years of experience in different aspects of AM research and development, from mechatronics AM system development to AM applications in medicine and engineering. He established the first AM laboratory at a Canadian university - the Multi-Scale Additive Manufacturing (MSAM) Laboratory – which focuses on the development of the next generation of AM processes and applications.
References
- Aage, N., E. Andreassen, and B. S. Lazarov. 2015. “Topology Optimization Using PETSc: An Easy-to-Use, Fully Parallel, Open Source Topology Optimization Framework.” Structural and Multidisciplinary Optimization 51 (3): 565–572. doi:10.1007/s00158-014-1157-0.
- Abdi, M., I. Ashcroft, and R. D. Wildman. 2018. “Design Optimization for an Additively Manufactured Automotive Component.” International Journal of Powertrains 7 (1–3): 142–161. doi:10.1504/IJPT.2018.090371.
- Abdulaziz, A., A. Tamimi, H. Almeida, and P. Bartolo. 2020. “Structural Optimisation for Medical Implants Through Additive Manufacturing.” Progress in Additive Manufacturing 0123456789, doi:10.1007/s40964-020-00109-7.
- Abueidda, D. W., S. Koric, and N. A. Sobh. 2020. “Topology Optimization of 2D Structures with Nonlinearities Using Deep Learning.” Computers & Structures 237: 106283. doi:10.1016/j.compstruc.2020.106283.
- Ahn, D.-G. 2016. “Direct Metal Additive Manufacturing Processes and Their Sustainable Applications for Green Technology: A Review.” International Journal of Precision Engineering and Manufacturing-Green Technology 3 (4): 381–395. doi:10.1007/s40684-016-0048-9.
- Ahn, H., M. B. Gingerich, R. Hahnlen, M. J. Dapino, and F. Pourboghrat. 2021. “Numerical Modeling of Mechanical Properties of UAM Reinforced Aluminum Hat Sections for Automotive Applications.” International Journal of Material Forming 14 (5): 917–928. doi:10.1007/s12289-020-01607-3.
- Airworthiness Certification. 2022. “Airworthiness Certification.” Federal Aviation Administration. Accessed December 25, 2022. https://www.faa.gov/aircraft/air_cert/airworthiness_certification#:~:text=Amended type certificates typically take, between 5 and 9 years.
- Al-Ali, M. A., M. A. Al-Ali, A. Takezawa, and M. Kitamura. 2017. “Topology Optimization and Fatigue Analysis of Temporomandibular Joint Prosthesis.” World Journal of Mechanics 7 (12): 323–339. doi:10.4236/wjm.2017.712025.
- Al-Tamimi, A. A., P. R. A. Fernandes, C. Peach, G. Cooper, C. Diver, and P. J. Bartolo. 2017. “Metallic Bone Fixation Implants: A Novel Design Approach for Reducing the Stress Shielding Phenomenon.” Virtual and Physical Prototyping 12 (2): 141–151. doi:10.1080/17452759.2017.1307769.
- Al-Tamimi, A. A., B. Huang, C. Vyas, M. Hernandez, C. Peach, and P. Bartolo. 2019. “Topology Optimised Metallic Bone Plates Produced by Electron Beam Melting: A Mechanical and Biological Study.” The International Journal of Advanced Manufacturing Technology 104 (1–4): 195–210. doi:10.1007/s00170-019-03866-0.
- Al-Tamimi, A. A., C. Peach, and P. Bartolo. 2018. “Topology Optimization of Metallic Locking Compression Plates Produced Using Electron Beam Melting.” Proceedings of the International Conference on Progress in Additive Manufacturing 2018-May: 364–369. doi:10.25341/D41G66.
- Alexandersen, J., O. Sigmund, and N. Aage. 2016. “Large Scale Three-Dimensional Topology Optimisation of Heat Sinks Cooled by Natural Convection.” International Journal of Heat and Mass Transfer 100: 876–891. doi:10.1016/j.ijheatmasstransfer.2016.05.013.
- Alexandersen, J., O. Sigmund, K. E. Meyer, and B. S. Lazarov. 2018. “Design of Passive Coolers for Light-Emitting Diode Lamps Using Topology Optimisation.” International Journal of Heat and Mass Transfer 122: 138–149. doi:10.1016/j.ijheatmasstransfer.2018.01.103.
- Alkebsi, E. A. A., H. Ameddah, T. Outtas, and A. Almutawakel. 2021. “Design of Graded Lattice Structures in Turbine Blades Using Topology Optimization.” International Journal of Computer Integrated Manufacturing 34 (4): 370–384. doi:10.1080/0951192X.2021.1872106.
- Allaire, G., M. Bihr, and B. Bogosel. 2020. “Support Optimization in Additive Manufacturing for Geometric and Thermo-Mechanical Constraints.” Structural and Multidisciplinary Optimization 61 (6): 2377–2399. doi:10.1007/s00158-020-02551-1.
- Allaire, G., and B. Bogosel. 2018. “Optimizing Supports for Additive Manufacturing.” Structural and Multidisciplinary Optimization 58 (6): 2493–2515. doi:10.1007/s00158-018-2125-x.
- Allaire, G., C. Dapogny, R. Estevez, A. Faure, and G. Michailidis. 2017. “Structural Optimization Under Overhang Constraints Imposed by Additive Manufacturing Technologies.” Journal of Computational Physics 351: 295–328. doi:10.1016/j.jcp.2017.09.041.
- Allaire, G., and L. Jakabčin. 2018. “Taking into Account Thermal Residual Stresses in Topology Optimization of Structures Built by Additive Manufacturing.” Mathematical Models and Methods in Applied Sciences 28 (12): 2313–2366. doi:10.1142/s0218202518500501.
- Allaire, G., F. Jouve, and A.-M. Toader. 2004. “Structural Optimization Using Sensitivity Analysis and a Level-Set Method.” Journal of Computational Physics 194 (1): 363–393. doi:10.1016/j.jcp.2003.09.032.
- Alnæs, M., J. Blechta, J. Hake, A. Johansson, B. Kehlet, A. Logg, C. Richardson, J. Ring, M. Rognes, and G. N. Wells. 2015. “The FEniCS Project Version 1.5.” Archive of Numerical Software 3 (100). doi:10.11588/ans.2015.100.20553.
- Alonso, D. H., L. F. N. de Sá, J. S. R. Saenz, and E. C. N. Silva. 2019. “Topology Optimization Based on a Two-Dimensional Swirl Flow Model of Tesla-Type Pump Devices.” Computers & Mathematics with Applications (1987) 77 (9): 2499–2533. doi:10.1016/j.camwa.2018.12.035.
- Altair Engineering. 2021a. “Altair Optistruct.” Version 20.2 [Software]. Accessed February 7, 2023. [Online]. https://www.altair.com/optistruct.
- Altair Engineering. 2021b. “Altair Inspire.” Version 2021.2 [Software]. Accessed February 7, 2023. [Online]. https://www.altair.com/inspire.
- Alzahrani, M., S.-K. Choi, and D. W. Rosen. 2015. “Design of Truss-Like Cellular Structures Using Relative Density Mapping Method.” Materials and Design 85: 349–360. doi:10.1016/j.matdes.2015.06.180.
- Amir, E., and O. Amir. 2021. “Concurrent High-Resolution Topology Optimization of Structures and Their Supports for Additive Manufacturing.” Structural and Multidisciplinary Optimization 63 (6): 2589–2612. doi:10.1007/s00158-020-02835-6.
- Anderson, R., et al. 2021. “MFEM: A Modular Finite Element Methods Library.” Computers & Mathematics with Applications (1987) 81 (C): 42–74. doi:10.1016/j.camwa.2020.06.009.
- Andreassen, E., A. Clausen, M. Schevenels, B. S. Lazarov, and O. Sigmund. 2011. “Efficient Topology Optimization in MATLAB Using 88 Lines of Code.” Structural and Multidisciplinary Optimization 43 (1): 1–16. doi:10.1007/s00158-010-0594-7.
- Ansys Inc. 2022. “ANSYS Mechanical.” Version 2021 R21 [Software]. Accessed February 7, 2023. [Online]. https://www.ansys.com/products/structures/ansys-mechanical.
- Aranda, E., J. C. Bellido, and A. Donoso. 2020. “Toptimiz3D: A Topology Optimization Software Using Unstructured Meshes.” Advances in Engineering Software (1992) 148: 102875. doi:10.1016/j.advengsoft.2020.102875.
- Aremu, A. O., et al. 2017. “A Voxel-Based Method of Constructing and Skinning Conformal and Functionally Graded Lattice Structures Suitable for Additive Manufacturing.” Addit Manuf 13: 1–13. doi:10.1016/j.addma.2016.10.006.
- Arndt, D., et al. 2021. “The Deal.II Library, Version 9.3.” Journal of Numerical Mathematics, doi:10.1515/jnma-2021-0081.
- Arora, R., et al. 2019. “Volumetric Michell Trusses for Parametric Design & Fabrication.” Proceedings of the ACM Symposium on Computational Fabrication, Art. no. 6.
- Autodesk. 2022. “Fusion 360.” Version 2.0.13162 [Software]. Accessed February 7, 2023. [Online]. https://www.autodesk.com/products/fusion-360.
- Bacciaglia, A., A. Ceruti, and A. Liverani. 2019. “A Systematic Review of Voxelization Method in Additive Manufacturing.” Mechanics & Industry 20 (6): 630. doi:10.1051/meca/2019058.
- Bacciaglia, A., A. Ceruti, and A. Liverani. 2020. “Additive Manufacturing Challenges and Future Developments in the Next Ten Years.” Design Tools and Methods in Industrial Engineering, 891–902. doi:10.1007/978-3-030-31154-4_76.
- Balay, S., et al. 2021. PETSC/TAO Users Manual. Argonne: Argonne National Laboratory.
- Bandyopadhyay, A., and K. D. Traxel. 2018. “Invited Review Article: Metal-Additive Manufacturing – Modeling Strategies for Application-Optimized Designs.” Addit Manuf 22: 758–774. doi:10.1016/j.addma.2018.06.024.
- Banga, S., L. Gehani, H. Bhilare, S. Patel, and S. Kara, 2018. “3D Topology Optimization Using Convolutional Neural Networks.” arXiv preprint arXiv:1808.07440, doi:10.1063/pt.5.028530.
- Barbieri, S. G., M. Giacopini, V. Mangeruga, and S. Mantovani. 2017. “A Design Strategy Based on Topology Optimization Techniques for an Additive Manufactured High Performance Engine Piston.” Procedia Manuf 11: 641–649. doi:10.1016/j.promfg.2017.07.162.
- Barbieri, S. G., M. Giacopini, V. Mangeruga, and S. Mantovani. 2018. “Design of an Additive Manufactured Steel Piston for a High Performance Engine: Developing of a Numerical Methodology Based on Topology Optimization Techniques.” SAE Int J Engines 11 (6): 1139–1150. doi:10.4271/2018-01-1385.
- Barnes, J. E. 2021a. “Speed is Relative in AM: A Data-Driven Comparison of Multi-Laser Powder Bed Fusion and Binder Jet Processing.” Additive Manufacturing Magazine. Accessed December 19, 2021. https://www.additivemanufacturing.media/articles/speed-is-relative-in-am-a-data-driven-comparison-of-multi-laser-powder-bed-fusion-and-binder-jet-processing.
- Barnes, J. E. 2021b. “Making a Slow Decision on a Fast Technology: Evaluating the Business Case for Multi-Laser Powder Bed Fusion.” Additive Manufacturing Magazine. Accessed December 19, 2021. https://www.additivemanufacturing.media/articles/making-a-slow-decision-on-a-fast-technology-evaluating-the-business-case-for-multi-laser-powder-bed-fusion.
- Barreiro, P., A. Bronner, J. Hoffmeister, and J. Hermes. 2019. “New Improvement Opportunities Through Applying Topology Optimization Combined with 3D Printing to the Construction of Gearbox Housings.” Forschung im Ingenieurwesen 83 (3): 669–681. doi:10.1007/s10010-019-00374-1.
- Barroqueiro, B., A. Andrade-Campos, and R. A. F. Valente. 2019. “Designing Self Supported SLM Structures via Topology Optimization.” Journal of Manufacturing and Materials Processing 3 (3): 68. doi:10.3390/jmmp3030068.
- Bartsch, K., F. Lange, M. Gralow, and C. Emmelmann. 2019. “Novel Approach to Optimized Support Structures in Laser Beam Melting by Combining Process Simulation with Topology Optimization.” Journal of Laser Applications 31 (2): 22302. doi:10.2351/1.5096096.
- Bastian, P., et al. 2021. “The Dune Framework: Basic Concepts and Recent Developments.” Computers & Mathematics with Applications 81: 75–112. doi:10.1016/j.camwa.2020.06.007.
- Bayat, M., W. Dong, J. Thorborg, A. C. To, and J. H. Hattel. 2021. “A Review of Multi-Scale and Multi-Physics Simulations of Metal Additive Manufacturing Processes with Focus on Modeling Strategies.” Addit Manuf 47: 102278. doi:10.1016/j.addma.2021.102278.
- Bendsøe, M. P., and N. Kikuchi. 1988. “Generating Optimal Topologies in Structural Design Using a Homogenization Method.” Computer Methods in Applied Mechanics and Engineering 71 (2): 197–224. doi:10.1016/0045-7825(88)90086-2.
- Bendsøe, M. P., O. Sigmund, M. P. Bendsoe, O. Sigmund, M. P. Bendsøe, and O. Sigmund. 2011. Topology Optimization: Theory, Methods, and Applications. Berlin, Heidelberg: Springer.
- Bergmann, G., A. Bender, J. Dymke, G. Duda, and P. Damm. 2016. “Standardized Loads Acting in Hip Implants.” PLoS One 11 (5): e0155612–e0155612. doi:10.1371/journal.pone.0155612.
- Berrocal, L., et al. 2019. “Topology Optimization and Additive Manufacturing for Aerospace Components.” Progress in Additive Manufacturing 4 (2): 83–95. doi:10.1007/s40964-018-0061-3.
- Bhavar, V., P. Kattire, V. Patil, S. Khot, K. Gujar, and R. Singh. 2017. “A Review on Powder Bed Fusion Technology of Metal Additive Manufacturing.” Additive Manufacturing Handbook. CRC Press, 251–253. doi:10.1201/9781315119106-15.
- Bi, M., P. Tran, and Y. M. Xie. 2020. “Topology Optimization of 3D Continuum Structures Under Geometric Self-Supporting Constraint.” Addit Manuf 36 (May): 101422. doi:10.1016/j.addma.2020.101422.
- Bici, M., G. B. Broggiato, and F. Campana. 2016. “Topological Optimization in Concept Design: Starting Approach and a Validation Case Study.” Lecture Notes in Mechanical Engineering. Springer International Publishing, 289–299. doi:10.1007/978-3-319-45781-9_30.
- Bikas, H., J. Stavridis, P. Stavropoulos, and G. Chryssolouris. 2016a. “A Design Framework to Replace Conventional Manufacturing Processes with Additive Manufacturing for Structural Components: A Formula Student Case Study.” Procedia CIRP 57: 710–715. doi:10.1016/j.procir.2016.11.123.
- Bikas, H., P. Stavropoulos, and G. Chryssolouris. 2016b. “Additive Manufacturing Methods and Modeling Approaches: A Critical Review.” International Journal of Advanced Manufacturing Technology 83 (1–4): 389–405. doi:10.1007/s00170-015-7576-2.
- Bin Masood, T., et al. 2021. “An Overview of the Topology ToolKit.” Topological Methods in Data Analysis and Visualization VI, 327–342.
- Bittredge, O., et al. 2022. “Fabrication and Optimisation of Ti-6Al-4V Lattice-Structured Total Shoulder Implants Using Laser Additive Manufacturing.” Materials (Basel) 15 (9): 3095. doi:10.3390/ma15093095.
- Blakey-Milner, B., et al. 2021. “Metal Additive Manufacturing in Aerospace: A Review.” Materials and Design 209: 110008. doi:10.1016/j.matdes.2021.110008.
- Bogomolny, M. 2018. “Paramatters Releases CogniCAD 2.0 Topology Optimiser for Lightweighting.” Metal AM Magazine. [Online]. https://www.metal-am.com/paramatters-releases-cognicad-2-0-topology-optimiser-for-lightweighting/.
- Bohrer, R., and I. Y. Kim. 2021. “Multi-material Topology Optimization Considering Isotropic and Anisotropic Materials Combination.” Structural and Multidisciplinary Optimization 64 (3): 1567. doi:10.1007/s00158-021-02941-z.
- Boissier, M., G. Allaire, and C. Tournier. 2020. “Additive Manufacturing Scanning Paths Optimization Using Shape Optimization Tools.” Structural and Multidisciplinary Optimization 61 (6): 2437–2466. doi:10.1007/s00158-020-02614-3.
- Borrvall, T., and J. Petersson. 2001. “Large-Scale Topology Optimization in 3D Using Parallel Computing.” Computer Methods in Applied Mechanics and Engineering 190 (46–47): 6201–6229. doi:10.1016/s0045-7825(01)00216-x.
- Bose, S., S. Vahabzadeh, and A. Bandyopadhyay. 2013. “Bone Tissue Engineering Using 3D Printing.” Materials Today 16 (12): 496–504. doi:10.1016/j.mattod.2013.11.017.
- Bourell, D., et al. 2017. “Materials for Additive Manufacturing.” CIRP Annals 66 (2): 659–681. doi:10.1016/j.cirp.2017.05.009.
- Bruns, T. E. 2007. “Topology Optimization of Convection-Dominated, Steady-State Heat Transfer Problems.” International Journal of Heat and Mass Transfer 50 (15–16): 2859–2873. doi:10.1016/j.ijheatmasstransfer.2007.01.039.
- Bujny, M., M. Olhofer, N. Aulig, and F. Duddeck. 2021. “Topology Optimization of 3D-Printed Joints Under Crash Loads Using Evolutionary Algorithms.” Structural and Multidisciplinary Optimization 64 (6): 4181–4206. doi:10.1007/s00158-021-03053-4.
- Bungartz, H.-J., et al. 2016. “preCICE – a Fully Parallel Library for Multi-Physics Surface Coupling.” Computers & Fluids 141: 250–258. doi:10.1016/j.compfluid.2016.04.003.
- Cacace, S., E. Cristiani, and L. Rocchi. 2017. “A Level Set Based Method for Fixing Overhangs in 3D Printing.” Applied Mathematical Modelling 44: 446–455. doi:10.1016/j.apm.2017.02.004.
- CAESS. 2022. “ProTOp.” Version 6.2 [Software]. Accessed February 7, 2023. [Online]. https://caess.eu/.
- Caivano, R., et al. 2022. “Defect-Driven Topology Optimisation: TopFat Algorithm Validation via 3D Components re-Design for Real Industrial Applications.” Procedia Structural Integrity 39: 81–88. doi:10.1016/j.prostr.2022.03.075.
- Calignano, F. 2014. “Design Optimization of Supports for Overhanging Structures in Aluminum and Titanium Alloys by Selective Laser Melting.” Materials and Design 64: 203–213. doi:10.1016/j.matdes.2014.07.043.
- Carnicero, A., A. Peláez, A. Restoy-Lozano, I. Jacquott, and R. Perera. 2021. “Improvement of an Additively Manufactured Subperiosteal Implant Structure Design by Finite Elements Based Topological Optimization.” Scientific Reports 11 (1): 15390. doi:10.1038/s41598-021-94980-1.
- Carraturo, M., J. Jomo, S. Kollmannsberger, A. Reali, F. Auricchio, and E. Rank. 2020. “Modeling and Experimental Validation of an Immersed Thermo-Mechanical Part-Scale Analysis for Laser Powder Bed Fusion Processes.” Addit Manuf 36: 101498. doi:10.1016/j.addma.2020.101498.
- Carstensen, J. V., and J. K. Guest. 2013. “Improved Two-Phase Projection Topology Optimization.” In Proceedings of the 10th World Congress on Structural and Multidisciplinary Optimization, 1–8. Orlando, FL.
- Carstensen, J. v., and J. K. Guest. 2018. “Projection-Based Two-Phase Minimum and Maximum Length Scale Control in Topology Optimization.” Structural and Multidisciplinary Optimization 58 (5): 1845–1860. doi:10.1007/s00158-018-2066-4.
- Cecchel, S. 2020. “Materials and Technologies for Lightweighting of Structural Parts for Automotive Applications: A Review.” SAE International Journal of Materials and Manufacturing 14 (1), doi:10.4271/05-14-01-0007.
- Chandrasekhar, A., and K. Suresh. 2021. “Multi-Material Topology Optimization Using Neural Networks.” CAD Computer Aided Design 136: 1135–1149. doi:10.1016/j.cad.2021.103017.
- Chen, Q., et al. 2021a. “Island Scanning Pattern Optimization for Residual Deformation Mitigation in Laser Powder bed Fusion via Sequential Inherent Strain Method and Sensitivity Analysis.” Addit Manuf 46: 102116. doi:10.1016/j.addma.2021.102116.
- Chen, Y., et al. 2021b. “Topology Optimization Design and Experimental Research of a 3D-Printed Metal Aerospace Bracket Considering Fatigue Performance.” Applied Sciences 11 (15): 6671. doi:10.3390/app11156671.
- Cheng, B., and K. Chou. 2020. “A Numerical Investigation of Support Structure Designs for Overhangs in Powder bed Electron Beam Additive Manufacturing.” Journal of Manufacturing Processes 49: 187–195. doi:10.1016/j.jmapro.2019.11.018.
- Cheng, L., X. Liang, J. Bai, Q. Chen, J. Lemon, and A. To. 2019a. “On Utilizing Topology Optimization to Design Support Structure to Prevent Residual Stress Induced Build Failure in Laser Powder bed Metal Additive Manufacturing.” Addit Manuf 27: 290–304. doi:10.1016/j.addma.2019.03.001.
- Cheng, K., Y. Liu, C. Yao, W. Zhao, and X. Xu. 2019b. “A Personalized Mandibular Implant with Supporting and Porous Structures Designed with Topology Optimization – a Case Study of Canine.” Rapid Prototyping Journal 25 (2): 417–426. doi:10.1108/rpj-11-2017-0231.
- Cheng, L., and A. To. 2019. “Part-scale Build Orientation Optimization for Minimizing Residual Stress and Support Volume for Metal Additive Manufacturing: Theory and Experimental Validation.” Computer-Aided Design 113: 1–23. doi:10.1016/j.cad.2019.03.004.
- Cheng, L., P. Zhang, E. Biyikli, J. Bai, J. Robbins, and A. To. 2017. “Efficient Design Optimization of Variable-Density Cellular Structures for Additive Manufacturing: Theory and Experimental Validation.” Rapid Prototyping Journal 23 (4): 660–677. doi:10.1108/RPJ-04-2016-0069.
- Colosimo, B. M., M. Grasso, F. Garghetti, and B. Rossi. 2022. “Complex Geometries in Additive Manufacturing: A New Solution for Lattice Structure Modeling and Monitoring.” Journal of Quality Technology 54 (4): 392–414. doi:10.1080/00224065.2021.1926377.
- Cook, P. S., and A. B. Murphy. 2020. “Simulation of Melt Pool Behaviour During Additive Manufacturing: Underlying Physics and Progress.” Addit Manuf 31: 100909. doi:10.1016/j.addma.2019.100909.
- Cooper, K., P. Steele, B. Cheng, and K. Chou. 2017. “Contact-Free Support Structures for Part Overhangs in Powder-Bed Metal Additive Manufacturing.” Inventions 3 (1): 2. doi:10.3390/inventions3010002.
- Costa, G., and M. Montemurro. 2020. “Eigen-frequencies and Harmonic Responses in Topology Optimisation: A CAD-Compatible Algorithm.” Engineering Structures 214: 110602. doi:10.1016/j.engstruct.2020.110602.
- Costa, G., M. Montemurro, and J. Pailhès. 2021. “NURBS Hyper-Surfaces for 3D Topology Optimization Problems.” Mechanics of Advanced Materials and Structures 28 (7): 665–684. doi:10.1080/15376494.2019.1582826.
- Costa, G., M. Montemurro, J. Pailhès, and N. Perry. 2019. “Maximum Length Scale Requirement in a Topology Optimisation Method Based on NURBS Hyper-Surfaces.” CIRP Annals 68 (1): 153–156. doi:10.1016/j.cirp.2019.04.048.
- Creswell, A., T. White, V. Dumoulin, K. Arulkumaran, B. Sengupta, and A. A. Bharath. 2018. “Generative Adversarial Networks: An Overview.” IEEE Signal Processing Magazine 35 (1): 53–65. doi:10.1109/msp.2017.2765202.
- Cucinotta, F., M. Raffaele, and F. Salmeri. 2019. “A Topology Optimization of a Motorsport Safety Device.” Lecture Notes in Mechanical Engineering. Springer International Publishing, 400–409. doi:10.1007/978-3-030-31154-4_34.
- da Silva, G. A., A. T. Beck, and O. Sigmund. 2019. “Stress-Constrained Topology Optimization Considering Uniform Manufacturing Uncertainties.” Computer Methods in Applied Mechanics and Engineering 344: 512–537. doi:10.1016/j.cma.2018.10.020.
- Dagkolu, A., I. Gokdag, and O. Yilmaz. 2021. “Design and Additive Manufacturing of a Fatigue-Critical Aerospace Part Using Topology Optimization and L-PBF Process.” Procedia Manuf 54: 238–243. doi:10.1016/j.promfg.2021.07.037.
- Dai, N., et al. 2018. “Design of a Maxillofacial Prosthesis Based on Topology Optimization.” Journal of Mechanics in Medicine and Biology 18 (3): 1850024. doi:10.1142/s0219519418500240.
- Dallago, M., S. Raghavendra, V. Luchin, G. Zappini, D. Pasini, and M. Benedetti. 2019. “Geometric Assessment of Lattice Materials Built via Selective Laser Melting.” Materials Today: Proceedings 7: 353–361. doi:10.1016/j.matpr.2018.11.096.
- Dalpadulo, E., F. Gherardini, F. Pini, and F. Leali. 2020b. “Integration of Topology Optimisation and Design Variants Selection for Additive Manufacturing-Based Systematic Product Redesign.” Applied Sciences 10 (21): 7841. doi:10.3390/app10217841.
- Dalpadulo, E., F. Pini, and F. Leali. 2020a. “Integrated CAD Platform Approach for Design for Additive Manufacturing of High Performance Automotive Components.” International Journal on Interactive Design and Manufacturing (IJIDeM) 14 (3): 899–909. doi:10.1007/s12008-020-00684-7.
- Dalpadulo, E., F. Pini, and F. Leali. 2021a. “Optimization of an Engine Piston Through CAD Platforms and Additive Manufacturing Based Systematic Product Redesign.” Lecture Notes in Mechanical Engineering. Springer International Publishing, 486–493. doi:10.1007/978-3-030-91234-5_49.
- Dalpadulo, E., F. Pini, and F. Leali. 2021b. “Design for Additive Manufacturing of a Topology Optimized Brake Caliper Through CAD-Platform-Based Systematic Approach.” Lecture Notes in Mechanical Engineering. Springer International Publishing, 92–97. doi:10.1007/978-3-030-70566-4_16.
- Dalpadulo, E., F. Pini, and F. Leali. 2021c. “Assessment of Computer-Aided Design Tools for Topology Optimization of Additively Manufactured Automotive Components.” Applied Sciences 11 (22): 10980. doi:10.3390/app112210980.
- Dassault Systemes. 2021. “Abaqus Simulia.” Version 2021 [Software]. Accessed February 7, 2023. [Online]. https://www.3ds.com/products-services/simulia/.
- Daynes, S., S. Feih, W. F. Lu, and J. Wei. 2017. “Optimisation of Functionally Graded Lattice Structures Using Isostatic Lines.” Materials and Design 127: 215–223. doi:10.1016/j.matdes.2017.04.082.
- Dbouk, T. 2017. “A Review About the Engineering Design of Optimal Heat Transfer Systems Using Topology Optimization.” Applied Thermal Engineering 112: 841–854. doi:10.1016/j.applthermaleng.2016.10.134.
- Deaton, J. D., and R. v. Grandhi. 2016. “Stress-Based Design of Thermal Structures via Topology Optimization.” Structural and Multidisciplinary Optimization 53 (2): 253–270. doi:10.1007/s00158-015-1331-z.
- DeBoer, B., N. Nguyen, F. Diba, and A. Hosseini. 2021. “Additive, Subtractive, and Formative Manufacturing of Metal Components: A Life Cycle Assessment Comparison.” The International Journal of Advanced Manufacturing Technology 115 (1–2): 413–432. doi:10.1007/s00170-021-07173-5.
- DebRoy, T., et al. 2018. “Additive Manufacturing of Metallic Components – Process, Structure and Properties.” Progress in Materials Science 92: 112–224. doi:10.1016/j.pmatsci.2017.10.001.
- DebRoy, T., T. Mukherjee, H. L. Wei, J. W. Elmer, and J. O. Milewski. 2021. “Metallurgy, Mechanistic Models and Machine Learning in Metal Printing.” Nat Rev Mater 6 (1): 48–68. doi:10.1038/s41578-020-00236-1.
- Dede, E. M., S. N. Joshi, and F. Zhou. 2015. “Topology Optimization, Additive Layer Manufacturing, and Experimental Testing of an Air-Cooled Heat Sink.” Journal of Mechanical Design 137 (11), doi:10.1115/1.4030989.
- Deng, H., P. S. Vulimiri, and A. C. To. 2021. “An Efficient 146-Line 3D Sensitivity Analysis Code of Stress-Based Topology Optimization Written in MATLAB.” Optimization and Engineering, doi:10.1007/s11081-021-09675-3.
- Deng, X., Y. Wang, J. Yan, T. Liu, and S. Wang. 2015. “Topology Optimization of Total Femur Structure: Application of Parameterized Level Set Method Under Geometric Constraints.” Journal of Mechanical Design 138 (1), doi:10.1115/1.4031803.
- Di Angelo, L., P. Di Stefano, and E. Guardiani. 2020. “Search for the Optimal Build Direction in Additive Manufacturing Technologies: A Review.” Journal of Manufacturing and Materials Processing 4 (3): 71. doi:10.3390/jmmp4030071.
- Diegel, O., A. Nordin, and D. Motte. 2019. A Practical Guide to Design for Additive Manufacturing. Singapore: Springer Singapore. doi:10.1007/978-981-13-8281-9.
- Donofrio, M. 2016. “Topology Optimization and Advanced Manufacturing as a Means for the Design of Sustainable Building Components.” Procedia Engineering 145: 638–645. doi:10.1016/j.proeng.2016.04.054.
- du Plessis, A., et al. 2019. “Beautiful and Functional: A Review of Biomimetic Design in Additive Manufacturing.” Addit Manuf 27: 408–427. doi:10.1016/j.addma.2019.03.033.
- du Plessis, A., I. Yadroitsava, and I. Yadroitsev. 2020. “Effects of Defects on Mechanical Properties in Metal Additive Manufacturing: A Review Focusing on X-Ray Tomography Insights.” Materials and Design 187: 108385. doi:10.1016/j.matdes.2019.108385.
- Dunbar, A. J. 2016. “Analysis of the Laser Powder Bed Fusion Additive Manufacturing Process Through Experimental Measurement and Finite Element Modeling.” Department of Mechanical Engineering Doctor of (May): 176.
- el Khadiri, I., et al. 2022. “TPMS Lattice Structure Derived Using Topology Optimization for the Design of Additive Manufactured Components.” in 2022 8th International Conference on Optimization and Applications (ICOA), 1–4. doi:10.1109/ICOA55659.2022.9934649.
- Fan, Y., et al. 2021. “Research and Experimental Verification on Topology-Optimization Design Method of Space Mirror Based on Additive-Manufacturing Technology.” Machines (MDPI) 9 (354), doi:10.3390/machines9120354.
- Fang, Z.-C., Z.-L. Wu, C.-G. Huang, and C.-W. Wu. 2020. “Review on Residual Stress in Selective Laser Melting Additive Manufacturing of Alloy Parts.” Optics & Laser Technology 129 (15): 106283. doi:10.1016/j.optlastec.2020.106283.
- Faskhutdinov, R. N., A. S. Dubrovskaya, K. A. Dongauzer, P. V. Maksimov, and N. A. Trufanov. 2017. “Topology Optimization of a Gas-Turbine Engine Part.” IOP Conf Ser Mater Sci Eng 177: 12077. doi:10.1088/1757-899x/177/1/012077.
- Fayazfar, H., et al. 2018. “A Critical Review of Powder-Based Additive Manufacturing of Ferrous Alloys: Process Parameters, Microstructure and Mechanical Properties.” Materials and Design 144: 98–128. doi:10.1016/j.matdes.2018.02.018.
- Fernández, E., M. Collet, P. Alarcón, S. Bauduin, and P. Duysinx. 2019. “An Aggregation Strategy of Maximum Size Constraints in Density-Based Topology Optimization.” Structural and Multidisciplinary Optimization 60 (5): 2113–2130. doi:10.1007/s00158-019-02313-8.
- Fernández, E., K. Yang, S. Koppen, P. Alarcón, S. Bauduin, and P. Duysinx. 2020. “Imposing Minimum and Maximum Member Size, Minimum Cavity Size, and Minimum Separation Distance Between Solid Members in Topology Optimization.” Computer Methods in Applied Mechanics and Engineering 368: 113157. doi:10.1016/j.cma.2020.113157.
- Ferro, C., R. Grassi, C. Seclì, and P. Maggiore. 2016. “Additive Manufacturing Offers New Opportunities in UAV Research.” Procedia CIRP 41: 1004–1010. doi:10.1016/j.procir.2015.12.104.
- Ferro, C. G., A. Mazza, D. Belmonte, C. Seclì, and P. Maggiore. 2017. “A Comparison Between 3D Printing and Milling Process for a Spar Cap Fitting (Wing-Fuselage) of UAV Aircraft.” Procedia CIRP 62: 487–493. doi:10.1016/j.procir.2016.06.028.
- Fetisov, K. V., and P. V. Maksimov. 2018. “Topology Optimization and Laser Additive Manufacturing in Design Process of Efficiency Lightweight Aerospace Parts.” Journal of Physics: Conference Series 1015: 52006. doi:10.1088/1742-6596/1015/5/052006.
- Flint, T. F., J. A. Francis, M. C. Smith, and A. N. Vasileiou. 2018. “Semi-Analytical Solutions for the Transient Temperature Fields Induced by a Moving Heat Source in an Orthogonal Domain.” International Journal of Thermal Sciences 123: 140–150. doi:10.1016/j.ijthermalsci.2017.09.012.
- Fraldi, M., L. Esposito, G. Perrella, A. Cutolo, and S. C. Cowin. 2010. “Topological Optimization in Hip Prosthesis Design.” Biomechanics and modeling in mechanobiology 9 (4): 389–402. doi:10.1007/s10237-009-0183-0.
- Francois, M. M., et al. 2017. “Modeling of Additive Manufacturing Processes for Metals: Challenges and Opportunities.” Current Opinion in Solid State & Materials Science 21 (4): 198–206. doi:10.1016/j.cossms.2016.12.001.
- Frazier, W. E. 2014. “Metal Additive Manufacturing: A Review.” Journal of Materials Engineering and Performance 23 (6): 1917–1928. doi:10.1007/s11665-014-0958-z.
- Galvao, J., P. Faria, A. Mateus, T. Pereira, and S. Fernandes. 2021. “Heatsinks to Cool Batteries for Unmanned Aerial Vehicles.” Renewable Energy and Power Quality Journal 19: 327–332. doi:10.24084/repqj19.287.
- Ganesh-Ram, A., Samarth Ramachandra, B. B. Ravichander, N. Swails, and A. Amerinatanzi. 2021. “Study on the Microstructural and Hardness Variations of Unsupported Overhangs Fabricated Using Selective Laser Melting.” Behavior and Mechanics of Multifunctional Materials XV. SPIE, doi:10.1117/12.2585605.
- Gao, W., et al. 2015. “The Status, Challenges, and Future of Additive Manufacturing in Engineering.” CAD Computer Aided Design 69: 65–89. doi:10.1016/j.cad.2015.04.001.
- Gao, T., W. H. Zhang, J. H. Zhu, Y. J. Xu, and D. H. Bassir. 2008. “Topology Optimization of Heat Conduction Problem Involving Design-Dependent Heat Load Effect.” Finite Elements in Analysis and Design 44 (14): 805–813. doi:10.1016/j.finel.2008.06.001.
- Garaigordobil, A., R. Ansola, J. Santamaría, and I. F. de Bustos. 2018. “A New Overhang Constraint for Topology Optimization of Self-Supporting Structures in Additive Manufacturing.” Structural and Multidisciplinary Optimization 58 (5): 2003–2017. doi:10.1007/s00158-018-2010-7.
- Garaigordobil, A., R. Ansola, E. Veguería, and I. Fernandez. 2019. “Overhang Constraint for Topology Optimization of Self-Supported Compliant Mechanisms Considering Additive Manufacturing.” Computer-Aided Design 109: 33–48. doi:10.1016/j.cad.2018.12.006.
- Gardan, N., and A. Schneider. 2015. “Topological Optimization of Internal Patterns and Support in Additive Manufacturing.” Journal of Manufacturing Systems 37: 417–425. doi:10.1016/j.jmsy.2014.07.003.
- Gatsos, T., K. A. Elsayed, Y. Zhai, and D. A. Lados. 2019. “Review on Computational Modeling of Process–Microstructure–Property Relationships in Metal Additive Manufacturing.” JOM Journal of the Minerals Metals and Materials Society 72 (1): 403–419. doi:10.1007/s11837-019-03913-x.
- Gaymann, A., F. Montomoli, and M. Pietropaoli. 2017. “Design for Additive Manufacturing: Valves Without Moving Parts.” Volume 2C: Turbomachinery. American Society of Mechanical Engineers, doi:10.1115/gt2017-64872.
- Gaynor, A. T., and J. K. Guest. 2014. “Topology Optimization for Additive Manufacturing: Considering Maximum Overhang Constraint.” AIAA AVIATION 2014 – 15th AIAA/ISSMO Multidisciplinary Analysis and Optimization Conference, AIAA 2014-2036. doi:10.2514/6.2014-2036.
- Gaynor, A. T., and J. K. Guest. 2016. “Topology Optimization Considering Overhang Constraints: Eliminating Sacrificial Support Material in Additive Manufacturing Through Design.” Structural and Multidisciplinary Optimization 54 (5): 1157–1172. doi:10.1007/s00158-016-1551-x.
- Gebisa, A. W., and H. G. Lemu. 2017a. “A Case Study on Topology Optimized Design for Additive Manufacturing.” IOP Conf Ser Mater Sci Eng 276: 12026. doi:10.1088/1757-899x/276/1/012026.
- Gebisa, A. W., and H. G. Lemu. 2017b. “Design for Manufacturing to Design for Additive Manufacturing: Analysis of Implications for Design Optimality and Product Sustainability.” Procedia Manuf 13: 724–731. doi:10.1016/j.promfg.2017.09.120.
- Geuzaine, C., and J.-F. Remacle. 2009. “Gmsh: A 3-D Finite Element Mesh Generator with Built- in Pre- and Post-Processing Facilities.” International Journal for Numerical Methods in Engineering 79 (11): 1309–1331. doi:10.1002/nme.2579.
- Gisario, A., M. Kazarian, F. Martina, and M. Mehrpouya. 2019. “Metal Additive Manufacturing in the Commercial Aviation Industry: A Review.” Journal of Manufacturing Systems 53: 124–149. doi:10.1016/j.jmsy.2019.08.005.
- Gleadall, A. 2021. “FullControl GCode Designer: Open-Source Software for Unconstrained Design in Additive Manufacturing.” Addit Manuf 46: 102109. doi:10.1016/j.addma.2021.102109.
- Goda, I., J. F. Ganghoffer, S. Czarnecki, R. Czubacki, and P. Wawruch. 2019. “Topology Optimization of Bone Using Cubic Material Design and Evolutionary Methods Based on Internal Remodeling.” Mechanics Research Communications 95: 52–60. doi:10.1016/j.mechrescom.2018.12.003.
- Gómez Pérez, C. A., H. I. Medellín-Castillo, and R. Espinosa-Castañeda. 2017. “Computer Assisted Design and Structural Topology Optimization of Customized Craniofacial Implants.” Volume 3: Biomedical and Biotechnology Engineering. American Society of Mechanical Engineers 3: 1–11. doi:10.1115/imece2017-72219.
- Gralow, M., F. Weigand, D. Herzog, T. Wischeropp, and C. Emmelmann. 2020. “Biomimetic Design and Laser Additive Manufacturing – a Perfect Symbiosis?” Journal of Laser Applications 32 (2): 21201. doi:10.2351/1.5131642.
- Gray, J. S., J. T. Hwang, J. R. R. A. Martins, K. T. Moore, and B. A. Naylor. 2019. “OpenMDAO: An Open-Source Framework for Multidisciplinary Design, Analysis, and Optimization.” Structural and Multidisciplinary Optimization 59 (4): 1075–1104. doi:10.1007/s00158-019-02211-z.
- Großmann, A., P. Weis, C. Clemen, and C. Mittelstedt. 2020. “Optimization and re-Design of a Metallic Riveting Tool for Additive Manufacturing – a Case Study.” Addit Manuf 31: 100892. doi:10.1016/j.addma.2019.100892.
- Gu, D. D., W. Meiners, K. Wissenbach, and R. Poprawe. 2012. “Laser Additive Manufacturing of Metallic Components: Materials, Processes and Mechanisms.” International Materials Reviews 57 (3): 133–164. doi:10.1179/1743280411y.0000000014.
- Guan, X., and Y. F. Zhao. 2020. “Modeling of the Laser Powder–Based Directed Energy Deposition Process for Additive Manufacturing: A Review.” The International Journal of Advanced Manufacturing Technology 107 (5–6): 1959–1982. doi:10.1007/s00170-020-05027-0.
- Guest, J. K. 2009a. “Topology Optimization with Multiple Phase Projection.” Computer Methods in Applied Mechanics and Engineering 199 (1): 123–135. doi:10.1016/j.cma.2009.09.023.
- Guest, J. K. 2009b. “Imposing Maximum Length Scale in Topology Optimization.” Structural and Multidisciplinary Optimization 37 (5): 463–473. doi:10.1007/s00158-008-0250-7.
- Guest, J. K., J. H. Prévost, and T. Belytschko. 2004. “Achieving Minimum Length Scale in Topology Optimization Using Nodal Design Variables and Projection Functions.” International Journal for Numerical Methods in Engineering 61 (2): 238–254. doi:10.1002/nme.1064.
- Guo, X. X., and Z. H. Chen. 2020. “Numerical Simulation of Laser Additive Manufacturing Process: A Review.” Acta Aeronautica et Astronautica Sinica 42 (10): 13. doi:10.7527/S1000-6893.2020.24227.
- Guo, X., Z. Du, C. Liu, and S. Tang. 2021. “A New Uncertainty Analysis-Based Framework for Data-Driven Computational Mechanics.” Journal of Applied Mechanics, Transactions ASME 88 (11): 1–6. doi:10.1115/1.4051594.
- Guo, L. X., and J. Y. Yin. 2019. “Finite Element Analysis and Design of an Interspinous Device Using Topology Optimization.” Medical and Biological Engineering and Computing 57 (1): 89–98. doi:10.1007/s11517-018-1838-8.
- Guo, X., J. Zhou, W. Zhang, Z. Du, C. Liu, and Y. Liu. 2017. “Self-Supporting Structure Design in Additive Manufacturing Through Explicit Topology Optimization.” Computer Methods in Applied Mechanics and Engineering 323: 27–63. doi:10.1016/j.cma.2017.05.003.
- Haase, K., and G. Rouhi. 2013. “Prediction of Stress Shielding Around an Orthopedic Screw: Using Stress and Strain Energy Density as Mechanical Stimuli.” Computers in Biology and Medicine 43 (11): 1748. doi:10.1016/j.compbiomed.2013.07.032.
- Hajializadeh, F., and A. Ince. 2019. “Short Review on Modeling Approaches for Metal Additive Manufacturing Process.” Material Design & Processing Communications 2 (2), doi:10.1002/mdp2.56.
- Han, Q., H. Gu, S. Soe, R. Setchi, F. Lacan, and J. Hill. 2018. “Manufacturability of AlSi10Mg Overhang Structures Fabricated by Laser Powder bed Fusion.” Materials and Design 160: 1080–1095. doi:10.1016/j.matdes.2018.10.043.
- Hashemi, S. M., et al. 2021. “Computational Modelling of Process–Structure–Property–Performance Relationships in Metal Additive Manufacturing: A Review.” International Materials Reviews, 1–46. doi:10.1080/09506608.2020.1868889.
- Hayes, A. C., and G. L. Whiting. 2021. “Reducing the Structural Mass of Large Direct Drive Wind Turbine Generators Through Triply Periodic Minimal Surfaces Enabled by Hybrid Additive Manufacturing.” Clean Technologies 3 (1): 227–242. doi:10.3390/cleantechnol3010013.
- He, Y., D. Burkhalter, D. Durocher, and J. M. Gilbert. 2018. “Solid-Lattice Hip Prosthesis Design: Applying Topology and Lattice Optimization to Reduce Stress Shielding from Hip Implants.” 2018 Design of Medical Devices Conference. American Society of Mechanical Engineers, doi:10.1115/dmd2018-6804.
- Hennes, C. 2022. “FreeCAD.” Version 0.20.2 [Software]. Accessed February 7, 2023. [Online]. https://www.freecad.org/.
- Herbin, P., D. Grzesiak, and M. A. Krolikowski. 2017. “Topology Optimisation Aimed at Additive – SLM Manufacturing of Metal Parts of ExoArm 7-DOF.” Lecture Notes in Mechanical Engineering. Springer International Publishing, 533–541. doi:10.1007/978-3-319-68619-6_51.
- Herzog, H., et al. 2015. “Optical Fabrication of Lightweighted 3D Printed Mirrors.” Optomechanical Engineering 2015. SPIE, doi:10.1117/12.2188197.
- Ho, J. Y., Y. S. See, K. C. Leong, and T. N. Wong. 2021. “An Experimental Investigation of a PCM-Based Heat Sink Enhanced with a Topology-Optimized Tree-Like Structure.” Energy Convers Manag 245: 114608. doi:10.1016/j.enconman.2021.114608.
- Høghøj, L. C., D. R. Nørhave, J. Alexandersen, O. Sigmund, and C. S. Andreasen. 2020. “Topology Optimization of Two Fluid Heat Exchangers.” International Journal of Heat and Mass Transfer 163), doi:10.1016/j.ijheatmasstransfer.2020.120543.
- Hu, R., et al. 2017. “Design Optimization Method for Additive Manufacturing of the Primary Mirror of a Large-Aperture Space Telescope.” Journal of Aerospace Engineering 30 (3): 4016093–4000000. doi:10.1061/(asce)as.1943-5525.0000690.
- Hu, K., S. Jin, and C. C. L. Wang. 2015. “Support Slimming for Single Material Based Additive Manufacturing.” Computer-Aided Design 65: 1–10. doi:10.1016/j.cad.2015.03.001.
- Hu, J., S. Wang, B. Li, F. Li, Z. Luo, and L. Liu. 2022. “Efficient Representation and Optimization for TPMS-Based Porous Structures.” IEEE Transactions on Visualization and Computer Graphics 28 (7): 2615–2627. doi:10.1109/TVCG.2020.3037697.
- Hu, J., J. H. Wang, R. Wang, X. B. Yu, Y. Liu, and D. A. Baur. 2019. “Analysis of Biomechanical Behavior of 3D Printed Mandibular Graft with Porous Scaffold Structure Designed by Topological Optimization.” 3D Print Med 5 (1): 5. doi:10.1186/s41205-019-0042-2.
- Huang, Y., et al. 2019b. “Rapid Prediction of Real-Time Thermal Characteristics, Solidification Parameters and Microstructure in Laser Directed Energy Deposition (Powder-Fed Additive Manufacturing).” Journal of Materials Processing Technology 274: 116286. doi:10.1016/j.jmatprotec.2019.116286.
- Huang, S., X. Deng, and L. K. Lam. 2021. “Integrated Design Framework of 3D Printed Planar Stainless Tubular Joint: Modelling, Optimization, Manufacturing, and Experiment.” Thin-Walled Structures 169: 108463. doi:10.1016/j.tws.2021.108463.
- Huang, Y., M. B. Khamesee, and E. Toyserkani. 2016. “A Comprehensive Analytical Model for Laser Powder-Fed Additive Manufacturing.” Addit Manuf 12: 90–99. doi:10.1016/j.addma.2016.07.001.
- Huang, Y., M. B. Khamesee, and E. Toyserkani. 2019a. “A New Physics-Based Model for Laser Directed Energy Deposition (Powder-fed Additive Manufacturing): From Single-Track to Multi-Track and Multi-Layer.” Optics & Laser Technology 109: 584–599. doi:10.1016/j.optlastec.2018.08.015.
- Hunar, M., L. Jancar, D. Krzikalla, D. Kaprinay, and D. Srnicek. 2020. “Comprehensive View on Racing Car Upright Design and Manufacturing.” Symmetry (Basel) 12 (6): 1020. doi:10.3390/sym12061020.
- Hussein, A., L. Hao, C. Yan, R. Everson, and P. Young. 2013. “Advanced Lattice Support Structures for Metal Additive Manufacturing.” Journal of Materials Processing Technology 213 (7): 1019–1026. doi:10.1016/j.jmatprotec.2013.01.020.
- Ibhadode, O., Z. Zhang, A. Bonakdar, and E. Toyserkani. 2021. “IbIPP for Topology Optimization – An Image-Based Initialization and Post-Processing Code Written in MATLAB.” SoftwareX 14: 100701. doi:10.1016/j.softx.2021.100701.
- Iqbal, T., et al. 2019. “A General Multi-Objective Topology Optimization Methodology Developed for Customized Design of Pelvic Prostheses.” Medical Engineering & Physics 69: 8–16. doi:10.1016/j.medengphy.2019.06.008.
- Ishii, K., and S. Aomura. 2004. “Topology Optimization for the Extruded Three Dimensional Structure with Constant Cross Section.” JSME International Journal, Series A: Solid Mechanics and Material Engineering 47 (2): 198–206. doi:10.1299/jsmea.47.198.
- Jankovics, D., H. Gohari, and A. Barari. 2018. “Constrained Topology Optimization for Additive Manufacturing of Structural Components in Ansys®”.
- Jiang, L., S. Chen, C. Sadasivan, and X. Jiao. 2017. “Structural Topology Optimization for Generative Design of Personalized Aneurysm Implants: Design, Additive Manufacturing, and Experimental Validation.” 2017 IEEE Healthcare Innovations and Point of Care Technologies (HI-POCT). IEEE, doi:10.1109/hic.2017.8227572.
- Jiang, J., X. Xu, and J. Stringer. 2018. “Support Structures for Additive Manufacturing: A Review.” Journal of Manufacturing and Materials Processing 2 (4): 64. doi:10.3390/jmmp2040064.
- Johnson, T. E., and A. T. Gaynor. 2018. “Three-dimensional Projection-Based Topology Optimization for Prescribed-Angle Self-Supporting Additively Manufactured Structures.” Addit Manuf 24: 667–686. doi:10.1016/j.addma.2018.06.011.
- Jung, M., M. Oh, and J. Yoo. 2021. “Reaction–Diffusion Equation-Based Topology Optimization Code for Electromagnetic Wave Problems Using FreeFEM++.” Structural and Multidisciplinary Optimization, doi:10.1007/s00158-021-03032-9.
- Junk, S., C. Fleig, and B. Fink. 2017. “Improvement of Sustainability Through the Application of Topology Optimization in the Additive Manufacturing of a Brake Mount.” Sustainable Design and Manufacturing 2017. Springer International Publishing, 151–161. doi:10.1007/978-3-319-57078-5_15.
- Kajima, Y., et al. 2018. “Effect of Adding Support Structures for Overhanging Part on Fatigue Strength in Selective Laser Melting.” Journal of the Mechanical Behavior of Biomedical Materials 78: 1–9. doi:10.1016/j.jmbbm.2017.11.009.
- Kambampati, S. et al., 2018. OpenLSTO: Open-Source Software for Level Set Topology Optimization. doi:10.2514/6.2018-3882.
- Kang, H., J. P. Long, G. D. Urbiel Goldner, S. A. Goldstein, and S. J. Hollister. 2012. “A Paradigm for the Development and Evaluation of Novel Implant Topologies for Bone Fixation: Implant Design and Fabrication.” Journal of Biomechanics 45 (13): 2241–2247. doi:10.1016/j.jbiomech.2012.06.011.
- Kanyilmaz, A., F. Berto, I. Paoletti, R. J. Caringal, and S. Mora. 2020. “Nature-Inspired Optimization of Tubular Joints for Metal 3D Printing.” Structural and Multidisciplinary Optimization 63 (2): 767–787. doi:10.1007/s00158-020-02729-7.
- Kazakov, M. 2022. “Open CASCADE.” Version 7.7.0 [Software]. Accessed February 7, 2023. [Online]. https://dev.opencascade.org/.
- Kazemi, H., A. Vaziri, and J. A. Norato. 2020. “Multi-Material Topology Optimization of Lattice Structures Using Geometry Projection.” Computer Methods in Applied Mechanics and Engineering 363: 112895. doi:10.1016/j.cma.2020.112895.
- Keller, N., and V. Ploshikhin. 2014. “New Method for Fast Predictions of Residual Stress and Distortion of AM Parts.” 25th Annual International Solid Freeform Fabrication Symposium — An Additive Manufacturing Conference, SFF 2014, 1229–1237. https://hdl.handle.net/2152/89269.
- Keshavarzkermani, A., et al. 2019. “Controlling Mechanical Properties of Additively Manufactured Hastelloy X by Altering Solidification Pattern During Laser Powder-bed Fusion.” Materials Science and Engineering: A 762: 138081. doi:10.1016/j.msea.2019.138081.
- Khanoki, S. A., and D. Pasini. 2012. “Multiscale Design and Multiobjective Optimization of Orthopedic Hip Implants with Functionally Graded Cellular Material.” Journal of Biomechanical Engineering 134 (3): 31004. doi:10.1115/1.4006115.
- Kim, C., M. Jung, T. Yamada, S. Nishiwaki, and J. Yoo. 2020. “FreeFEM++ Code for Reaction-Diffusion Equation–Based Topology Optimization: For High-Resolution Boundary Representation Using Adaptive Mesh Refinement.” Structural and Multidisciplinary Optimization 62 (1): 439–455. doi:10.1007/s00158-020-02498-3.
- King, W., A. T. Anderson, R. M. Ferencz, N. E. Hodge, C. Kamath, and S. A. Khairallah. 2014. “Overview of Modelling and Simulation of Metal Powder Bed Fusion Process at Lawrence Livermore National Laboratory.” Materials Science and Technology 31 (8): 957–968. doi:10.1179/1743284714y.0000000728.
- Kintel, M. 2022. “OpenSCAD.” Version 2021.01 [Software]. Accessed February 7, 2023. [Online]. https://openscad.org/.
- Kirk, B. S., J. W. Peterson, R. H. Stogner, and G. F. Carey. 2006. “libMesh: A C++ Library for Parallel Adaptive Mesh Refinement/Coarsening Simulations.” Engineering With Computers 22 (3): 237–254. doi:10.1007/s00366-006-0049-3.
- Kok, Y., et al. 2018. “Anisotropy and Heterogeneity of Microstructure and Mechanical Properties in Metal Additive Manufacturing: A Critical Review.” Materials and Design 139: 565–586. doi:10.1016/j.matdes.2017.11.021.
- Kouraytem, N., X. Li, W. Tan, B. Kappes, and A. D. Spear. 2021. “Modeling Process–Structure–Property Relationships in Metal Additive Manufacturing: A Review on Physics-Driven Versus Data-Driven Approaches.” Journal of Physics: Materials 4 (3): 32002. doi:10.1088/2515-7639/abca7b.
- Körner, C., M. Markl, and J. A. Koepf. 2020. “Modeling and Simulation of Microstructure Evolution for Additive Manufacturing of Metals: A Critical Review.” Metallurgical and Materials Transactions A 51 (10): 4970–4983. doi:10.1007/s11661-020-05946-3.
- Kuo, Y.-H., and C.-C. Cheng. 2019. “Self-supporting Structure Design for Additive Manufacturing by Using a Logistic Aggregate Function.” Structural and Multidisciplinary Optimization 60: 1–13. doi:10.1007/s00158-019-02261-3.
- Lang, J. J., et al. 2021. “Improving Mandibular Reconstruction by Using Topology Optimization, Patient Specific Design and Additive Manufacturing? – a Biomechanical Comparison Against Miniplates on Human Specimen.” PLoS One 16 (6): e0253002–e0253002. doi:10.1371/journal.pone.0253002.
- Langelaar, M. 2016a. “Topology Optimization of 3D Self-Supporting Structures for Additive Manufacturing.” Addit Manuf 12: 60–70. doi:10.1016/j.addma.2016.06.010.
- Langelaar, M. 2016b. “An Additive Manufacturing Filter for Topology Optimization of Print-Ready Designs.” Structural and Multidisciplinary Optimization 55 (3): 871–883. doi:10.1007/s00158-016-1522-2.
- Langelaar, M. 2018. “Combined Optimization of Part Topology, Support Structure Layout and Build Orientation for Additive Manufacturing.” Structural and Multidisciplinary Optimization 57 (5): 1985–2004. doi:10.1007/s00158-017-1877-z.
- Langelaar, M. 2019. “Integrated Component-Support Topology Optimization for Additive Manufacturing with Post-Machining.” Rapid Prototyping Journal 25 (2): 255–265. doi:10.1108/RPJ-12-2017-0246.
- Laurain, A. 2018. “A Level Set-Based Structural Optimization Code Using FEniCS.” Structural and Multidisciplinary Optimization 58 (3): 1311–1334. doi:10.1007/s00158-018-1950-2.
- Lazarov, B. S., O. Sigmund, K. E. Meyer, and J. Alexandersen. 2018. “Experimental Validation of Additively Manufactured Optimized Shapes for Passive Cooling.” Applied Energy 226: 330–339. doi:10.1016/j.apenergy.2018.05.106.
- Lazarov, B. S., and F. Wang. 2017. “Maximum Length Scale in Density Based Topology Optimization.” Computer Methods in Applied Mechanics and Engineering 318: 826–844. doi:10.1016/j.cma.2017.02.018.
- le Hyaric, A., P. Jolivet, and S. Garnotel. 2022. “FreeFEM.” Version 4.12 [Software]. Accessed February 7, 2023. [Online]. https://freefem.org/.
- Leary, M. 2018. “Design of Titanium Implants for Additive Manufacturing.” In Titanium in Medical and Dental Applications, edited by F. H. Froes and M. Qian. Elsevier Inc. doi:10.1016/B978-0-12-812456-7.00009-3.
- Leary, M., D. Downing, B. Lozanovski, and J. Harris. 2021. “Design Principles.” Fundamentals of Laser Powder Bed Fusion of Metals. Elsevier, 119–154. doi:10.1016/b978-0-12-824090-8.00013-5.
- Leary, M., T. Maconachie, A. Sarker, O. Faruque, and M. Brandt. 2019. “Mechanical and Thermal Characterisation of AlSi10Mg SLM Block Support Structures.” Materials and Design 183: 108138. doi:10.1016/j.matdes.2019.108138.
- Leary, M., L. Merli, F. Torti, M. Mazur, and M. Brandt. 2014. “Optimal Topology for Additive Manufacture: A Method for Enabling Additive Manufacture of Support-Free Optimal Structures.” Materials and Design 63: 678–690. doi:10.1016/j.matdes.2014.06.015.
- Lei, X., C. Liu, Z. Du, W. Zhang, and X. Guo. 2019. “Machine Learning-Driven Real-Time Topology Optimization Under Moving Morphable Component-Based Framework.” Journal of Applied Mechanics, Transactions ASME 86 (1): 1–9. doi:10.1115/1.4041319.
- Lewandowski, J. J., and M. Seifi. 2016. “Metal Additive Manufacturing: A Review of Mechanical Properties.” Annual Review of Materials Research 46 (1): 151–186. doi:10.1146/annurev-matsci-070115-032024.
- Li, H., et al. 2021. “Full-scale 3D Structural Topology Optimization Using Adaptive Mesh Refinement Based on the Level-Set Method.” Finite Elements in Analysis and Design 194: 103561. doi:10.1016/j.finel.2021.103561.
- Li, H., et al. 2022. “Three-Dimensional Topology Optimization of a Fluid–Structure System Using Body-Fitted Mesh Adaption Based on the Level-Set Method.” Applied Mathematical Modelling 101: 276–308. doi:10.1016/j.apm.2021.08.021.
- Li, C., and A. Chen. 2018. “Numerical Methods for Fractional Partial Differential Equations.” International Journal of Computer Mathematics 95 (6–7): 1048–1099. doi:10.1080/00207160.2017.1343941.
- Li, Q., W. Chen, S. Liu, and L. Tong. 2016a. “Structural Topology Optimization Considering Connectivity Constraint.” Structural and Multidisciplinary Optimization 54 (4): 971–984. doi:10.1007/s00158-016-1459-5.
- Li, J., C. Duan, M. Zhao, and X. Luo. 2019. “A Review of Metal Additive Manufacturing Application and Numerical Simulation.” IOP Conf Ser Earth Environ Sci 252: 22036. doi:10.1088/1755-1315/252/2/022036.
- Li, C., C. H. Fu, Y. B. Guo, and F. Z. Fang. 2016b. “A Multiscale Modeling Approach for Fast Prediction of Part Distortion in Selective Laser Melting.” Journal of Materials Processing Technology 229: 703–712. doi:10.1016/j.jmatprotec.2015.10.022.
- Li, C.-H., C.-H. Wu, and C.-L. Lin. 2020a. “Design of a Patient-Specific Mandible Reconstruction Implant with Dental Prosthesis for Metal 3D Printing Using Integrated Weighted Topology Optimization and Finite Element Analysis.” Journal of the Mechanical Behavior of Biomedical Materials 105: 103700. doi:10.1016/j.jmbbm.2020.103700.
- Li, Z., D. Z. Zhang, P. Dong, and I. Kucukkoc. 2016c. “A Lightweight and Support-Free Design Method for Selective Laser Melting.” The International Journal of Advanced Manufacturing Technology 90 (9–12): 2943–2953. doi:10.1007/s00170-016-9509-0.
- Li, J., X. Zhou, M. Brochu, N. Provatas, and Y. F. Zhao. 2020c. “Solidification Microstructure Simulation of Ti-6Al-4V in Metal Additive Manufacturing: A Review.” Addit Manuf 31: 100989. doi:10.1016/j.addma.2019.100989.
- Lin, C.-L., Y.-T. Wang, C.-M. Chang, C.-H. Wu, and W.-H. Tsai. 2021. “Design Criteria for Patient-Specific Mandibular Continuity Defect Reconstructed Implant with Lightweight Structure Using Weighted Topology Optimization and Validated with Biomechanical Fatigue Testing.” Int J Bioprint 8 (1): 437. doi:10.18063/ijb.v8i1.437.
- Lin, C.-Y., T. Wirtz, F. LaMarca, and S. J. Hollister. 2007. “Structural and Mechanical Evaluations of a Topology Optimized Titanium Interbody Fusion Cage Fabricated by Selective Laser Melting Process.” Journal of Biomedical Materials Research Part A 83A (2): 272–279. doi:10.1002/jbm.a.31231.
- Liu, J., et al. 2018a. “Current and Future Trends in Topology Optimization for Additive Manufacturing.” Structural and Multidisciplinary Optimization 57 (6): 2457–2483. doi:10.1007/s00158-018-1994-3.
- Liu, W., et al. 2021a. “Review on Scanning Pattern Evaluation in Laser-Based Additive Manufacturing.” Optical Engineering 60 (7): 1–18. doi:10.1117/1.OE.60.7.070901.
- Liu, R., Y. Chen, Y. Liu, Z. Yan, and Y.-X. Wang. 2021b. “Topological Design of a Trabecular Bone Structure With Morphology and Mechanics Control for Additive Manufacturing.” IEEE Access 9: 11123–11133. doi:10.1109/access.2021.3050745.
- Liu, W., L. Chen, G. Mai, and L. Song. 2020a. “Toolpath Planning for Additive Manufacturing Using Sliced Model Decomposition and Metaheuristic Algorithms.” Advances in Engineering Software 149: 102906. doi:10.1016/j.advengsoft.2020.102906.
- Liu, Y.-F., Y.-Y. Fan, X.-F. Jiang, and D. A. Baur. 2017. “A Customized Fixation Plate with Novel Structure Designed by Topological Optimization for Mandibular Angle Fracture Based on Finite Element Analysis.” Biomedical Engineering Online 16 (1): 131. doi:10.1186/s12938-017-0422-z.
- Liu, J., B. Jalalahmadi, Y. B. Guo, M. P. Sealy, and N. Bolander. 2018b. “A Review of Computational Modeling in Powder-Based Additive Manufacturing for Metallic Part Qualification.” Rapid Prototyping Journal 24 (8): 1245–1264. doi:10.1108/rpj-04-2017-0058.
- Liu, H. C., J. S. Jiang, and C. L. Lin. 2020b. “Biomechanical Investigation of a Novel Hybrid Dorsal Double Plating for Distal Radius Fractures by Integrating Topology Optimization and Finite Element Analysis.” Injury 51 (6): 1271–1280. doi:10.1016/j.injury.2020.03.011.
- Liu, S., Q. Li, W. Chen, L. Tong, and G. Cheng. 2015. “An Identification Method for Enclosed Voids Restriction in Manufacturability Design for Additive Manufacturing Structures.” Frontiers of Mechanical Engineering 10 (2): 126–137. doi:10.1007/s11465-015-0340-3.
- Liu, J., and A. C. To. 2017. “Deposition Path Planning-Integrated Structural Topology Optimization for 3D Additive Manufacturing Subject to Self-Support Constraint.” Computer-Aided Design 91: 27–45. doi:10.1016/j.cad.2017.05.003.
- Liu, J., and H. Yu. 2020. “Self-Support Topology Optimization with Horizontal Overhangs for Additive Manufacturing.” Journal of Manufacturing Science and Engineering 142 (September), doi:10.1115/1.4047352.
- Liu, J., Y. Zheng, R. Ahmad, J. Tang, and Y. Ma. 2019. “Minimum Length Scale Constraints in Multi-Scale Topology Optimisation for Additive Manufacturing.” Virtual and Physical Prototyping 14 (3): 229–241. doi:10.1080/17452759.2019.1584944.
- Lohan, D. J., E. M. Dede, and J. T. Allison. 2019. “A Study on Practical Objectives and Constraints for Heat Conduction Topology Optimization.” Structural and Multidisciplinary Optimization 61 (2): 475–489. doi:10.1007/s00158-019-02369-6.
- López-Castro, J. D., A. Marchal, L. González, and J. Botana. 2017. “Topological Optimization and Manufacturing by Direct Metal Laser Sintering of an Aeronautical Part in 15-5PH Stainless Steel.” Procedia Manuf 13: 818–824. doi:10.1016/j.promfg.2017.09.121.
- Luo, Y., O. Sigmund, Q. Li, and S. Liu. 2020. “Additive Manufacturing Oriented Topology Optimization of Structures with Self-Supported Enclosed Voids.” Computer Methods in Applied Mechanics and Engineering 372: 113385. doi:10.1016/j.cma.2020.113385.
- Luo, Z., and Y. Zhao. 2018. “A Survey of Finite Element Analysis of Temperature and Thermal Stress Fields in Powder bed Fusion Additive Manufacturing.” Addit Manuf 21: 318–332. doi:10.1016/j.addma.2018.03.022.
- Lynch, M. E., et al. 2013. “Design and Topology/Shape Structural Optimisation for Additively Manufactured Cold Sprayed Components.” Virtual and Physical Prototyping 8 (3): 213–231. doi:10.1080/17452759.2013.837629.
- Lynch, M. E., S. Sarkar, and K. Maute. 2019. “Machine Learning to Aid Tuning of Numerical Parameters in Topology Optimization.” Journal of Mechanical Design 141 (11), doi:10.1115/1.4044228.
- Magerramova, L., B. Vasilyev, and V. Kinzburskiy. 2016. “Novel Designs of Turbine Blades for Additive Manufacturing.” Volume 5C: Heat Transfer. American Society of Mechanical Engineers, doi:10.1115/gt2016-56084.
- Mahadevan, V., I. Grindeanu, R. Jain, P. Wilson, and P. Shriwise. 2022. “MeshKit.” Version MOAB 5.4.0 [Software]. Accessed February 7, 2023. [Online]. https://sigma.mcs.anl.gov/.
- Mantovani, S., G. A. Campo, and A. Ferrari. 2020. “Additive Manufacturing and Topology Optimization: A Design Strategy for a Steering Column Mounting Bracket Considering Overhang Constraints.” Proc Inst Mech Eng C J Mech Eng Sci 235 (10): 1703–1723. doi:10.1177/0954406220917717.
- Marchesi, T. R., et al. 2015. “Topologically Optimized Diesel Engine Support Manufactured with Additive Manufacturing.” IFAC-PapersOnLine 48 (3): 2333–2338. doi:10.1016/j.ifacol.2015.06.436.
- Markl, M., and C. Körner. 2016. “Multiscale Modeling of Powder Bed-Based Additive Manufacturing.” Annual Review of Materials Research 46: 93–123. doi:10.1146/annurev-matsci-070115-032158.
- Mass, Y., and O. Amir. 2017. “Topology Optimization for Additive Manufacturing: Accounting for Overhang Limitations Using a Virtual Skeleton.” Addit Manuf 18: 58–73. doi:10.1016/j.addma.2017.08.001.
- McEwen, I., D. Cooper, J. Warnett, N. Kourra, M. Williams, and G. Gibbons. 2018. “Design & Manufacture of a High-Performance Bicycle Crank by Additive Manufacturing.” Applied Sciences 8 (8): 1360. doi:10.3390/app8081360.
- McGregor, D. J., S. Tawfick, and W. P. King. 2019. “Automated Metrology and Geometric Analysis of Additively Manufactured Lattice Structures.” Addit Manuf 28 (May): 535–545. doi:10.1016/j.addma.2019.05.026.
- Megahed, M., et al. 2016. “Metal Additive-Manufacturing Process and Residual Stress Modeling.” Integr Mater Manuf Innov 5 (1): 61–93. doi:10.1186/s40192-016-0047-2.
- Meng, L., et al. 2019. “From Topology Optimization Design to Additive Manufacturing: Today’s Success and Tomorrow’s Roadmap.” Archives of Computational Methods in Engineering 27 (3): 805–830. doi:10.1007/s11831-019-09331-1.
- Meng, X., Z. Li, D. Zhang, and G. E. Karniadakis. 2020. “PPINN: Parareal Physics-Informed Neural Network for Time-Dependent PDEs.” Computer Methods in Applied Mechanics and Engineering 370: 113250. doi:10.1016/j.cma.2020.113250.
- Mercelis, P., and J.-P. J. P. Kruth. 2006. “Residual Stresses in Selective Laser Sintering and Selective Laser Melting.” Rapid Prototyping Journal 12 (5): 254–265. doi:10.1108/13552540610707013.
- Mesicek, J., et al. 2021. “Comprehensive View of Topological Optimization Scooter Frame Design and Manufacturing.” Symmetry (Basel) 13 (7): 1201. doi:10.3390/sym13071201.
- Mezzadri, F., V. Bouriakov, and X. Qian. 2018. “Topology Optimization of Self-Supporting Support Structures for Additive Manufacturing.” Addit Manuf 21: 666–682. doi:10.1016/j.addma.2018.04.016.
- Mezzadri, F., and X. Qian. 2020. “A Second-Order Measure of Boundary Oscillations for Overhang Control in Topology Optimization.” Journal of Computational Physics 410: 109365. doi:10.1016/j.jcp.2020.109365.
- Mhapsekar, K., M. McConaha, and S. Anand. 2018. “Additive Manufacturing Constraints in Topology Optimization for Improved Manufacturability.” Journal of Manufacturing Science and Engineering 140 (5): 51017. doi:10.1115/1.4039198.
- Michopoulos, J., et al. 2021. “Multiphysics Integrated Computational Materials Engineering Linking Additive Manufacturing Process Parameters with Part Performance.” Advances in Computers and Information in Engineering Research, Volume 2. ASME, 293–338. doi:10.1115/1.862025_ch10.
- Miki, T., and S. Nishiwaki. 2022. “Topology Optimization of the Support Structure for Heat Dissipation in Additive Manufacturing.” Finite Elements in Analysis and Design 203: 103708. doi:10.1016/j.finel.2021.103708.
- Miki, T., and T. Yamada. 2021. “Topology Optimization Considering the Distortion in Additive Manufacturing.” Finite Elements in Analysis and Design 193: 103558. doi:10.1016/j.finel.2021.103558.
- Min, Z., et al. 2017. “Research on 3D Modeling Technology of Craniofacial Implants Based on Topology Optimization Method.” 2017 International Conference on Virtual Reality and Visualization (ICVRV). IEEE, doi:10.1109/icvrv.2017.00036.
- Mirkoohi, E., J. R. Dobbs, and S. Y. Liang. 2020a. “Analytical Modeling of Residual Stress in Direct Metal Deposition Considering Scan Strategy.” The International Journal of Advanced Manufacturing Technology 106 (9–10): 4105–4121. doi:10.1007/s00170-019-04919-0.
- Mirkoohi, E., D. Li, H. Garmestani, and S. Y. Liang. 2021. “Residual Stress Modeling Considering Microstructure Evolution in Metal Additive Manufacturing.” Journal of Manufacturing Processes 68: 383–397. doi:10.1016/j.jmapro.2021.04.041.
- Mirkoohi, E., J. Ning, P. Bocchini, O. Fergani, K.-N. Chiang, and S. Liang. 2018. “Thermal Modeling of Temperature Distribution in Metal Additive Manufacturing Considering Effects of Build Layers, Latent Heat, and Temperature-Sensitivity of Material Properties.” Journal of Manufacturing and Materials Processing 2 (3): 63. doi:10.3390/jmmp2030063.
- Mirkoohi, E., D. E. Sievers, H. Garmestani, and S. Y. Liang. 2020b. “Thermo-mechanical Modeling of Thermal Stress in Metal Additive Manufacturing Considering Elastoplastic Hardening.” CIRP J Manuf Sci Technol 28: 52–67. doi:10.1016/j.cirpj.2020.01.002.
- Mirzendehdel, A. M., M. Behandish, and S. Nelaturi. 2022. “Topology Optimization for Manufacturing with Accessible Support Structures.” Computer-Aided Design 142: 103117. doi:10.1016/j.cad.2021.103117.
- Mirzendehdel, A. M., and K. Suresh. 2016. “Support Structure Constrained Topology Optimization for Additive Manufacturing.” Computer-Aided Design 81: 1–13. doi:10.1016/j.cad.2016.08.006.
- Misiun, G., et al. 2021. “Topology Optimization for Additive Manufacturing with Distortion Constraints.” Computer Methods in Applied Mechanics and Engineering 386: 114095. doi:10.1016/j.cma.2021.114095.
- Misiun, G. 2021. “Topology Optimization with Additive Manufacturing Constraints.” PhD Thesis, University of Twente, Enschede, The Netherlands, doi:10.3990/1.9789036551496.
- Moerman, K. M. 2018. “GIBBON: The Geometry and Image-Based Bioengineering Add-On.” J Open Source Softw 3 (22): 506. doi:10.21105/joss.00506.
- Montemurro, M., and K. Refai. 2021. “A Topology Optimization Method Based on Non-Uniform Rational Basis Spline Hyper-Surfaces for Heat Conduction Problems.” Symmetry (Basel) 13 (5): 888. doi:10.3390/sym13050888.
- Moran, T. P., D. H. Warner, and N. Phan. 2021. “Scan-by-Scan Part-Scale Thermal Modelling for Defect Prediction in Metal Additive Manufacturing.” Addit Manuf 37: 101667. doi:10.1016/j.addma.2020.101667.
- Morand, L. M. 2021. “Development of Guidelines for Support Structure Design and Placement in Metal Additive Manufacturing.” M.Sc Thesis, Clemson University.
- Morse, M. J., A. Rahimian, and D. Zorin. 2021. “A Robust Solver for Elliptic PDEs in 3D Complex Geometries.” Journal of Computational Physics 442: 110511. doi:10.1016/j.jcp.2021.110511.
- Moussa, A., S. Rahman, M. Xu, M. Tanzer, and D. Pasini. 2020. “Topology Optimization of 3D-Printed Structurally Porous Cage for Acetabular Reinforcement in Total hip Arthroplasty.” Journal of the Mechanical Behavior of Biomedical Materials 105: 103705. doi:10.1016/j.jmbbm.2020.103705.
- Muir, M. J., et al. 2013. “The Use of MDO and Advanced Manufacturing to Demonstrate Rapid, Agile Construction of a Mission Optimized UAV.” 54th AIAA/ASME/ASCE/AHS/ASC Structures, Structural Dynamics, and Materials Conference. American Institute of Aeronautics and Astronautics, doi:10.2514/6.2013-1675.
- Munk, D. J., D. J. Auld, G. P. Steven, and G. A. Vio. 2019. “On the Benefits of Applying Topology Optimization to Structural Design of Aircraft Components.” Structural and Multidisciplinary Optimization 60 (3): 1245–1266. doi:10.1007/s00158-019-02250-6.
- Munk, D. J., and J. D. Miller. 2022. “Topology Optimization of Aircraft Components for Increased Sustainability.” AIAA Journal 60 (1): 445–460. doi:10.2514/1.J060259.
- Naik, A., T. Sujan, S. Desai, and S. Shanmugam. 2019. “Light-Weighting of Additive Manufactured Automotive Fixtures Through Topology Optimization Techniques.” SAE Technical Paper Series. SAE International, doi:10.4271/2019-28-2544.
- Naresh, D. M. R., S. Iyer, Amir M Mirzendehdel, Sathyanarayanan Raghavan, Yang Jiao, Erva Ulu, Morad Behandish, and Saigopal Nelaturi. 2021. “PATO: Producibility-Aware Topology Optimization using Deep Learning for Metal Additive Manufacturing.” arXiv:2112.04552.
- Ngim, D. B., J.-S. Liu, and R. C. Soar. 2007. “Design Optimization for Manufacturability of Axisymmetric Continuum Structures Using Metamorphic Development.” International Journal of Solids and Structures 44 (2): 685–704. doi:10.1016/j.ijsolstr.2006.05.016.
- Ning, J., E. Mirkoohi, Y. Dong, D. E. Sievers, H. Garmestani, and S. Y. Liang. 2019. “Analytical Modeling of 3D Temperature Distribution in Selective Laser Melting of Ti-6Al-4V Considering Part Boundary Conditions.” Journal of Manufacturing Processes 44: 319–326. doi:10.1016/j.jmapro.2019.06.013.
- Ninpetch, P., P. Kowitwarangkul, S. Mahathanabodee, P. Chalermkarnnon, and P. Ratanadecho. 2020. “A Review of Computer Simulations of Metal 3D Printing.” The Second Materials Research Society of Thailand International Conference. AIP Publishing, doi:10.1063/5.0022974.
- Noronha, J., M. Leary, M. Qian, E. Kyriakou, and M. Brandt. 2022. “Geometrical Parameters and Mechanical Properties of Ti6Al4 V Hollow-Walled Lattices.” Materials Science and Engineering A 840 (October 2021): 142667. doi:10.1016/j.msea.2022.142667.
- Nourbakhsh, M., N. Morris, M. Bergin, F. Iorio, and D. Grandi. 2016. “Embedded Sensors and Feedback Loops for Iterative Improvement in Design Synthesis for Additive Manufacturing.” Volume 1A: 36th Computers and Information in Engineering Conference. American Society of Mechanical Engineers, doi:10.1115/detc2016-59627.
- Nsiempba, K. M., M. Wang, and M. Vlasea. 2021. “Geometrical Degrees of Freedom for Cellular Structures Generation: A New Classification Paradigm.” Applied Sciences 11 (9): 3845. doi:10.3390/app11093845.
- nTopology. 2023. “nTopology.” Version 3.41 [Software]. Accessed February 7, 2023. [Online]. https://ntopology.com/.
- OpenCFD and ESI Group. 2021. “OpenFOAM.” Version 10 [Software]. Accessed February 7, 2023. [Online]. https://www.openfoam.com/.
- Orme, M. E., M. Gschweitl, M. Ferrari, I. Madera, and F. Mouriaux. 2017. “Designing for Additive Manufacturing: Lightweighting Through Topology Optimization Enables Lunar Spacecraft.” Journal of Mechanical Design 139 (10), doi:10.1115/1.4037304.
- Osanov, M., and J. K. Guest. 2017. “Topology Optimization for Additive Manufacturing Considering Layer-Based Minimum Feature Sizes.” In ASME 2017 International Design Engineering Technical Conferences and Computers and Information in Engineering Conference, 1–8. doi:10.1115/DETC2017-68383.
- Pan, T., et al. 2020a. “Investigation of Significant Factors on Deformation with Powder Bed Fusion System.” Proc Inst Mech Eng B J Eng Manuf 235 (5): 902–911. doi:10.1177/0954405420970088.
- Pan, T., S. Karnati, and F. Liou. 2020b. “General Rules for Pre-Process Planning in Powder Bed Fusion System – A Review,” Solid Freeform Fabrication 2018: Proceedings of the 29th Annual International Solid Freeform Fabrication Symposium – an Additive Manufacturing Conference, SFF 2018, 1161–1173.
- Pandey, P. M., K. Thrimurthulu, and N. V. Reddy*. 2004. “Optimal Part Deposition Orientation in FDM by Using a Multicriteria Genetic Algorithm.” International Journal of Production Research 42 (19): 4069–4089. doi:10.1080/00207540410001708470.
- Park, J., D. Lee, and A. Sutradhar. 2019. “Topology Optimization of Fixed Complete Denture Framework.” International Journal for Numerical Methods in Biomedical Engineering 35 (6), doi:10.1002/cnm.3193.
- Park, J., A. Sutradhar, J. J. Shah, and G. H. Paulino. 2018. “Design of Complex Bone Internal Structure Using Topology Optimization with Perimeter Control.” Computers in Biology and Medicine 94 (January): 74–84. doi:10.1016/j.compbiomed.2018.01.001.
- Park, J., T. Zobaer, and A. Sutradhar. 2021. “A Two-Scale Multi-Resolution Topologically Optimized Multi-Material Design of 3D Printed Craniofacial Bone Implants.” Micromachines (Basel) 12 (2), doi:10.3390/mi12020101.
- Pellens, J., G. Lombaert, B. Lazarov, and M. Schevenels. 2018. “Combined Length Scale and Overhang Angle Control in Minimum Compliance Topology Optimization for Additive Manufacturing.” Structural and Multidisciplinary Optimization 59 (6): 2005–2022. doi:10.1007/s00158-018-2168-z.
- Pellens, J., G. Lombaert, M. Michiels, T. Craeghs, and M. Schevenels. 2020. “Topology Optimization of Support Structure Layout in Metal-Based Additive Manufacturing Accounting for Thermal Deformations.” Structural and Multidisciplinary Optimization 61 (6): 2291–2303. doi:10.1007/s00158-020-02512-8.
- Pilagatti, A. N., G. Piscopo, E. Atzeni, L. Iuliano, and A. Salmi. 2021. “Design of Additive Manufactured Passive Heat Sinks for Electronics.” Journal of Manufacturing Processes 64: 878–888. doi:10.1016/j.jmapro.2021.01.035.
- Plocher, J., and A. Panesar. 2019. “Review on Design and Structural Optimisation in Additive Manufacturing: Towards Next-Generation Lightweight Structures.” Materials and Design 183: 108164. doi:10.1016/j.matdes.2019.108164.
- Priarone, P. C., M. Robiglio, G. Ingarao, and L. Settineri. 2017. “Assessment of Cost and Energy Requirements of Electron Beam Melting (EBM) and Machining Processes.” Sustainable Design and Manufacturing 2017, 723–735. doi:10.1007/978-3-319-57078-5_68.
- Project, T. C. 2021. CGAL User and Reference Manual, 5.3. CGAL Editorial Board.
- Qian, X. 2017. “Undercut and Overhang Angle Control in Topology Optimization: A Density Gradient Based Integral Approach.” International Journal for Numerical Methods in Engineering 111 (3): 247–272. doi:10.1002/nme.5461.
- Rathore, J. S., C. Mang, C. Vienne, Y. Quinsat, and C. Tournier. 2021. “A Methodology for Computed Tomography-Based Nondestructive Geometrical Evaluations of Lattice Structures by Holistic Strut Measurement Approach.” Journal of Manufacturing Science and Engineering, Transactions of the ASME 143 (5): 1–12. doi:10.1115/1.4049492.
- Rawat, M. H., and S., Shen. 2018. “A Novel Topology Design Approach Using an Integrated Deep Learning Network Architecture.” arXiv preprint arXiv:1808.02334.
- Raz, K., Z. Chval, and M. Stepanek. 2022. “Topological Optimization of the Milling Head.” Lecture Notes in Mechanical Engineering. Springer Singapore, 171–177. doi:10.1007/978-981-16-9632-9_19.
- Reddy, S. N., K. I. Ferguson, M. Frecker, T. W. Simpson, and C. J. Dickman. 2016a. “Topology Optimization Software for Additive Manufacturing: A Review of Current Capabilities and a Real-World Example.” Volume 2A: 42nd Design Automation Conference. American Society of Mechanical Engineers, doi:10.1115/detc2016-59718.
- Reddy, S. N., K. V. Maranan, T. W. Simpson, T. Palmer, and C. J. Dickman. 2016b. “Application of Topology Optimization and Design for Additive Manufacturing Guidelines on an Automotive Component.” Volume 2A: 42nd Design Automation Conference. American Society of Mechanical Engineers, doi:10.1115/detc2016-59719.
- Reinhart, G., and S. Teufelhart. 2011. “Load-Adapted Design of Generative Manufactured Lattice Structures.” Physics Procedia 12 (PART 1): 385–392. doi:10.1016/j.phpro.2011.03.049.
- Reinhart, G., and S. Teufelhart. 2013. “Optimization of Mechanical Loaded Lattice Structures by Orientating Their Struts Along the Flux of Force.” Procedia CIRP 12: 175–180. doi:10.1016/j.procir.2013.09.031.
- Ren, F., et al. 2021. “Transition Boundaries and Stiffness Optimal Design for Multi-TPMS Lattices.” Materials and Design 210: 110062. doi:10.1016/j.matdes.2021.110062.
- Ribeiro, T. P., L. F. A. Bernardo, and J. M. A. Andrade. 2021. “Topology Optimisation in Structural Steel Design for Additive Manufacturing.” Applied Sciences 11 (5): 2112. doi:10.3390/app11052112.
- Rodgers, T. M., et al. 2021. “Simulation of Powder Bed Metal Additive Manufacturing Microstructures with Coupled Finite Difference-Monte Carlo Method.” Addit Manuf 41: 101953. doi:10.1016/j.addma.2021.101953.
- Rozvany, G. I. N. 2008. “A Critical Review of Established Methods of Structural Topology Optimization.” Structural and Multidisciplinary Optimization 37 (3): 217–237. doi:10.1007/s00158-007-0217-0.
- Sahoo, S., and K. Chou. 2014. “Review on Phase-Field Modeling of Microstructure Evolutions: Application to Electron Beam Additive Manufacturing.” Volume 2: Processing. American Society of Mechanical Engineers, doi:10.1115/msec2014-3901.
- Saudan, H., et al. 2018. “Compliant Mechanisms and Space Grade Product Redesign Based on Additive Manufacturing.” Advances in Optical and Mechanical Technologies for Telescopes and Instrumentation III. SPIE, doi:10.1117/12.2312087.
- Sá, L. F. N., C. M. Okubo, and E. C. N. Silva. 2021. “Topology Optimization of Subsonic Compressible Flows.” Structural and Multidisciplinary Optimization 64 (1): 1–22. doi:10.1007/s00158-021-02903-5.
- Schneck, M., M. Horn, M. Schmitt, C. Seidel, G. Schlick, and G. Reinhart. 2021. “Review on Additive Hybrid- and Multi-Material-Manufacturing of Metals by Powder bed Fusion: State of Technology and Development Potential.” Progress in Additive Manufacturing, doi:10.1007/s40964-021-00205-2.
- Schoinochoritis, B., D. Chantzis, and K. Salonitis. 2016. “Simulation of Metallic Powder Bed Additive Manufacturing Processes with the Finite Element Method: A Critical Review.” Proc Inst Mech Eng B J Eng Manuf 231 (1): 96–117. doi:10.1177/0954405414567522.
- Schuh, G., G. Bergweiler, K. Lichtenthäler, F. Fiedler, and S. de la Puente Rebollo. 2020. “Topology Optimisation and Metal Based Additive Manufacturing of Welding Jig Elements.” Procedia CIRP 93: 62–67. doi:10.1016/j.procir.2020.04.066.
- Schwerdtfeger, J., et al. 2011. “Design of Auxetic Structures via Mathematical Optimization.” Advanced Materials 23 (22–23): 2650–2654. doi:10.1002/adma.201004090.
- Seabra, M., et al. 2016. “Selective Laser Melting (SLM) and Topology Optimization for Lighter Aerospace Componentes.” Procedia Structural Integrity 1: 289–296. doi:10.1016/j.prostr.2016.02.039.
- See, Y. S., J. Y. Ho, K. C. Leong, and T. N. Wong. 2022. “Experimental Investigation of a Topology-Optimized Phase Change Heat Sink Optimized for Natural Convection.” Applied Energy 314: 118984. doi:10.1016/j.apenergy.2022.118984.
- Seebach, M., C. Fritz, J. Kerschreiter, and M. F. Zaeh. 2020. “Shape Accuracy and Surface Quality of Additively Manufactured, Optimized, Patient-Specific Bone Plates.” Journal of Medical Devices 15 (2), doi:10.1115/1.4049193.
- Seebach, M., F. Theurer, P. Foehr, C. von Deimling, R. Burgkart, and M. F. Zaeh. 2017. “Design of Bone Plates for Mandibular Reconstruction Using Topology and Shape Optimization.” Advances in Structural and Multidisciplinary Optimization. Springer International Publishing, 2086–2096. doi:10.1007/978-3-319-67988-4_154.
- Senck, S., et al. 2020. “Additive Manufacturing and Non-Destructive Testing of Topology-Optimised Aluminium Components.” Nondestructive Testing and Evaluation 35 (3): 315–327. doi:10.1080/10589759.2020.1774582.
- Sha, W., M. Xiao, L. Gao, and Y. Zhang. 2021. “A New Level Set Based Multi-Material Topology Optimization Method Using Alternating Active-Phase Algorithm.” Computer Methods in Applied Mechanics and Engineering 377: 113674. doi:10.1016/j.cma.2021.113674.
- Shidid, D., M. Leary, P. Choong, and M. Brandt. 2016. “Just-in-Time Design and Additive Manufacture of Patient-Specific Medical Implants.” Physics Procedia 83: 4–14. doi:10.1016/j.phpro.2016.08.002.
- Si, H. 2015. “TetGen, a Delaunay-Based Quality Tetrahedral Mesh Generator.” ACM Transactions on Mathematical Software 41 (2), doi:10.1145/2629697.
- Siewert, M., F. Neugebauer, J. Epp, and V. Ploshikhin. 2019. “Validation of Mechanical Layer Equivalent Method for Simulation of Residual Stresses in Additive Manufactured Components.” Computers & Mathematics with Applications 78 (7): 2407–2416. doi:10.1016/j.camwa.2018.08.016.
- Sigmund, O. 2001. “A 99 Line Topology Optimization Code Written in Matlab.” Structural and Multidisciplinary Optimization 21 (2): 120–127. doi:10.1007/s001580050176.
- Singamneni, S., Y. Lv, A. Hewitt, R. Chalk, W. Thomas, and D. Jordison. 2019. “Additive Manufacturing for the Aircraft Industry: A Review.” Journal of Aeronautics & Aerospace Engineering 8 (1): 13. doi:10.4172/2329-6542.1000214.
- Smith, C. J., M. Gilbert, I. Todd, and F. Derguti. 2016. “Application of Layout Optimization to the Design of Additively Manufactured Metallic Components.” Structural and Multidisciplinary Optimization 54 (5): 1297–1313. doi:10.1007/s00158-016-1426-1.
- Smith, H., and J. A. Norato. 2020. “A MATLAB Code for Topology Optimization Using the Geometry Projection Method.” Structural and Multidisciplinary Optimization 62 (3): 1579–1594. doi:10.1007/s00158-020-02552-0.
- Song, L., et al. 2021. “An All-Movable Rudder Designed by Thermo-Elastic Topology Optimization and Manufactured by Additive Manufacturing.” Computers & Structures 243: 106405. doi:10.1016/j.compstruc.2020.106405.
- Sosnovik, I., and I. Oseledets. 2019. “Neural Networks for Topology Optimization.” Russian Journal of Numerical Analysis and Mathematical Modelling 34 (4): 215–223. doi:10.1515/rnam-2019-0018.
- Srivastava, S., et al. 2020b. “Multi-Physics Continuum Modelling Approaches for Metal Powder Additive Manufacturing: A Review.” Rapid Prototyping Journal 26 (4): 737–764. doi:10.1108/rpj-07-2019-0189.
- Srivastava, S., R. K. Garg, V. S. Sharma, and A. Sachdeva. 2020a. “Measurement and Mitigation of Residual Stress in Wire-Arc Additive Manufacturing: A Review of Macro-Scale Continuum Modelling Approach.” Archives of Computational Methods in Engineering 28 (5): 3491–3515. doi:10.1007/s11831-020-09511-4.
- Stavropoulos, P., and P. Foteinopoulos. 2018. “Modelling of Additive Manufacturing Processes: A Review and Classification.” Manuf Rev (Les Ulis) 5: 2. doi:10.1051/mfreview/2017014.
- Steuben, J. C., A. J. Birnbaum, J. G. Michopoulos, and A. P. Iliopoulos. 2019. “Enriched Analytical Solutions for Additive Manufacturing Modeling and Simulation.” Addit Manuf 25: 437–447. doi:10.1016/j.addma.2018.10.017.
- Steuben, J. C., J. G. Michopoulos, A. P. Iliopoulos, and A. J. Birnbaum. 2017. “Functional Performance Tailoring of Additively Manufactured Components via Topology Optimization.” Volume 1: 37th Computers and Information in Engineering Conference. American Society of Mechanical Engineers, doi:10.1115/detc2017-67600.
- Strano, G., L. Hao, R. M. Everson, and K. E. Evans. 2012. “A New Approach to the Design and Optimisation of Support Structures in Additive Manufacturing.” The International Journal of Advanced Manufacturing Technology 66 (9–12): 1247–1254. doi:10.1007/s00170-012-4403-x.
- Strömberg, N. 2022. “A New Multi-Scale Topology Optimization Framework for Optimal Combinations of Macro-Layouts and Local Gradings of TPMS-Based Lattice Structures.” Mechanics Based Design of Structures and Machines, 1–18. doi:10.1080/15397734.2022.2107538.
- Suárez, A., F. Veiga, T. Bhujangrao, and E. Aldalur. 2022. “Study of the Mechanical Behavior of Topologically Optimized Arc Wire Direct Energy Deposition Aerospace Fixtures.” Journal of Materials Engineering and Performance, doi:10.1007/s11665-022-06702-x.
- Subedi, S. C., C. S. Verma, and K. Suresh. 2020. “A Review of Methods for the Geometric Post-Processing of Topology Optimized Models.” Journal of Computing and Information Science in Engineering 20 (6), doi:10.1115/1.4047429.
- Sun, S., P. Liebersbach, and X. Qian. 2020. “3D Topology Optimization of Heat Sinks for Liquid Cooling.” Applied Thermal Engineering 178 (C): 115540. doi:10.1016/j.applthermaleng.2020.115540.
- Sun, W., Y. E. Ma, W. Zhang, X. Qian, W. Huang, and Z. Wang. 2021. “Effects of the Build Direction on Mechanical Performance of Laser Powder Bed Fusion Additively Manufactured Ti6Al4 V Under Different Loadings.” Advanced Engineering Materials, 2100611. doi:10.1002/adem.202100611.
- Sutradhar, A., J. Park, D. Carrau, T. H. Nguyen, M. J. Miller, and G. H. Paulino. 2015. “Designing Patient-Specific 3D Printed Craniofacial Implants Using a Novel Topology Optimization Method.” Medical and Biological Engineering and Computing 54 (7): 1123–1135. doi:10.1007/s11517-015-1418-0.
- Sutradhar, A., G. H. Paulino, M. J. Miller, and T. H. Nguyen. 2010. “Topological Optimization for Designing Patient-Specific Large Craniofacial Segmental Bone Replacements.” Proceedings of the National Academy of Sciences 107 (30): 13222–13227. doi:10.1073/pnas.1001208107.
- Süß, M., C. Schöne, R. Stelzer, B. Klöden, A. Kirchner, and T. Weißgärber. 2016. “Aerospace Case Study on Topology Optimization for Additive Manufacturing.” DDMC 2016 Proceedings March 2016: 6.
- Takezawa, A., et al. 2020. “Sensitivity Analysis and Lattice Density Optimization for Sequential Inherent Strain Method Used in Additive Manufacturing Process.” Computer Methods in Applied Mechanics and Engineering 370: 113231. doi:10.1016/j.cma.2020.113231.
- Takezawa, A., Q. Chen, and A. C. To. 2021. “Optimally Variable Density Lattice to Reduce Warping Thermal Distortion of Laser Powder bed Fusion.” Addit Manuf 48: 102422. doi:10.1016/j.addma.2021.102422.
- Takezawa, A., H. Guo, R. Kobayashi, Q. Chen, and A. C. To. 2022. “Simultaneous Optimization of Hatching Orientations and Lattice Density Distribution for Residual Warpage Reduction in Laser Powder bed Fusion Considering Layerwise Residual Stress Stacking.” Addit Manuf 60: 103194. doi:10.1016/j.addma.2022.103194.
- Takezawa, A., Y. Koizumi, and M. Kobashi. 2017. “High-stiffness and Strength Porous Maraging Steel via Topology Optimization and Selective Laser Melting.” Addit Manuf 18: 194–202. doi:10.1016/j.addma.2017.10.004.
- Takezawa, A., X. Zhang, M. Kato, and M. Kitamura. 2019. “Method to Optimize an Additively-Manufactured Functionally-Graded Lattice Structure for Effective Liquid Cooling.” Addit Manuf 28: 285–298. doi:10.1016/j.addma.2019.04.004.
- Talischi, C., G. H. Paulino, A. Pereira, and I. F. M. Menezes. 2012. “PolyTop: A Matlab Implementation of a General Topology Optimization Framework Using Unstructured Polygonal Finite Element Meshes.” Structural and Multidisciplinary Optimization 45 (3): 329–357. doi:10.1007/s00158-011-0696-x.
- Tan, J. H. K., S. L. Sing, and W. Y. Yeong. 2019. “Microstructure Modelling for Metallic Additive Manufacturing: A Review.” Virtual and Physical Prototyping 15 (1): 87–105. doi:10.1080/17452759.2019.1677345.
- Tang, Y., A. Kurtz, and Y. F. Zhao. 2015. “Bidirectional Evolutionary Structural Optimization (BESO) Based Design Method for Lattice Structure to be Fabricated by Additive Manufacturing.” Computer-Aided Design 69: 91–101. doi:10.1016/j.cad.2015.06.001.
- Tang, Y., K. Mak, and Y. F. Zhao. 2016. “A Framework to Reduce Product Environmental Impact Through Design Optimization for Additive Manufacturing.” Journal of Cleaner Production 137: 1560–1572. doi:10.1016/j.jclepro.2016.06.037.
- Thomas, D. S., and S. W. Gilbert. 2014. Costs and Cost Effectiveness of Additive Manufacturing. Gaithersburg, MD: National Institute of Standards and Technology (NIST). doi:10.6028/NIST.SP.1176.
- Thore, C.-J., H. A. Grundström, B. Torstenfelt, and A. Klarbring. 2019. “Penalty Regulation of Overhang in Topology Optimization for Additive Manufacturing.” Structural and Multidisciplinary Optimization 60 (1): 59–67. doi:10.1007/s00158-019-02194-x.
- Torigaki, T., and K. Fujitani. 2000. “Power of a Voxel Approach to Structural Analysis and Topology-Shape Optimization in Automobile Industries.” Japan Journal Of industrial and Applied Mathematics 17 (1): 129–147. doi:10.1007/bf03167341.
- Townsend, A., N. Senin, L. Blunt, R. K. Leach, and J. S. Taylor. 2016. “Surface Texture Metrology for Metal Additive Manufacturing: A Review.” Precis Eng 46: 34–47. doi:10.1016/j.precisioneng.2016.06.001.
- Toyserkani, E., D. Sarker, O. O. Ibhadode, F. Liravi, P. Russo, and K. Taherkhani. 2021. Metal Additive Manufacturing. Hoboken, NJ: Wiley. [Online]. https://books.google.ca/books?id=_ScQswEACAAJ.
- Tyflopoulos, E., M. Lien, and M. Steinert. 2021. “Optimization of Brake Calipers Using Topology Optimization for Additive Manufacturing.” Applied Sciences 11 (4): 1437. doi:10.3390/app11041437.
- Ueda, Y., Y. C. Kim, and M. G. Yuan. 1988. “A Predicting Method of Welding Residual Stress Using Source of Residual Stress.” Quarterly Journal of the Japan Welding Society 6 (1): 59–64. doi:10.2207/qjjws.6.59.
- Ueno, A., H. Guo, A. Takezawa, R. Moritoyo, and M. Kitamura. 2021. “Temperature Distribution Design Based on Variable Lattice Density Optimization and Metal Additive Manufacturing.” Symmetry (Basel) 13 (7): 1194. doi:10.3390/sym13071194.
- van Belle, L., G. Vansteenkiste, and J. C. Boyer. 2013. “Investigation of Residual Stresses Induced During the Selective Laser Melting Process.” Key Engineering Materials 554–557: 1828–1834. doi:10.4028/www.scientific.net/kem.554-557.1828.
- van de Ven, E., R. Maas, C. Ayas, M. Langelaar, and F. van Keulen. 2018. “Continuous Front Propagation-Based Overhang Control for Topology Optimization with Additive Manufacturing.” Structural and Multidisciplinary Optimization 57 (5): 2075–2091. doi:10.1007/s00158-017-1880-4.
- van de Ven, E., R. Maas, C. Ayas, M. Langelaar, and F. van Keulen. 2020. “Overhang Control Based on Front Propagation in 3D Topology Optimization for Additive Manufacturing.” Computer Methods in Applied Mechanics and Engineering 369: 113169. doi:10.1016/j.cma.2020.113169.
- van Dijk, N. P., K. Maute, M. Langelaar, and F. Van Keulen. 2013. “Level-set Methods for Structural Topology Optimization: A Review.” Structural and Multidisciplinary Optimization 48 (3): 437–472. doi:10.1007/s00158-013-0912-y.
- Vatanabe, S. L., T. N. Lippi, C. R. de Lima, G. H. Paulino, and E. C. N. Silva. 2016. “Topology Optimization with Manufacturing Constraints: A Unified Projection-Based Approach.” Advances in Engineering Software 100: 97–112. doi:10.1016/j.advengsoft.2016.07.002.
- Vaverka, O., D. Koutny, and D. Palousek. 2019. “Topologically Optimized Axle Carrier for Formula Student Produced by Selective Laser Melting.” Rapid Prototyping Journal 25 (9): 1545–1551. doi:10.1108/rpj-07-2018-0171.
- Vogiatzis, P., S. Chen, and C. Zhou. 2017. “An Open Source Framework for Integrated Additive Manufacturing and Level-Set-Based Topology Optimization.” Journal of Computing and Information Science in Engineering 17 (4), doi:10.1115/1.4037738.
- Vouga, E., M. Höbinger, J. Wallner, and H. Pottmann. 2012. “Design of Self-Supporting Surfaces.” Acm Transactions. on Graphics 31 (4): 1–11. doi:10.1145/2185520.2185583.
- Vrancken, B., V. Cain, R. Knutsen, and J. Van Humbeeck. 2014. “Residual Stress via the Contour Method in Compact Tension Specimens Produced via Selective Laser Melting.” Scripta Materialia 87: 29–32. doi:10.1016/j.scriptamat.2014.05.016.
- Walton, D., and H. Moztarzadeh. 2017. “Design and Development of an Additive Manufactured Component by Topology Optimisation.” Procedia CIRP 60: 205–210. doi:10.1016/j.procir.2017.03.027.
- Wang, X., et al. 2016. “Topological Design and Additive Manufacturing of Porous Metals for Bone Scaffolds and Orthopaedic Implants: A Review.” Biomaterials 83: 127–141. doi:10.1016/j.biomaterials.2016.01.012.
- Wang, H., et al. 2020a. “Porous Fusion Cage Design via Integrated Global-Local Topology Optimization and Biomechanical Analysis of Performance.” Journal of the Mechanical Behavior of Biomedical Materials 112: 103982. doi:10.1016/j.jmbbm.2020.103982.
- Wang, C. 2021a. “Topology Optimization of Self-Supported Enclosed Voids for Additive Manufacturing.” Volume 2: 41st Computers and Information in Engineering Conference (CIE), doi:10.1115/DETC2021-68785.
- Wang, S., et al. 2022. “Efficient Representation and Optimization of TPMS-Based Porous Structures for 3D Heat Dissipation.” Computer-Aided Design 142: 103123. doi:10.1016/j.cad.2021.103123.
- Wang, Y., J. Gao, and Z. Kang. 2018a. “Level Set-Based Topology Optimization with Overhang Constraint: Towards Support-Free Additive Manufacturing.” Computer Methods in Applied Mechanics and Engineering 339: 591–614. doi:10.1016/j.cma.2018.04.040.
- Wang, W., D. Munro, C. C. L. Wang, F. van Keulen, and J. Wu. 2020b. “Space-Time Topology Optimization for Additive Manufacturing.” Structural and Multidisciplinary Optimization 61 (1): 1–18. doi:10.1007/s00158-019-02420-6.
- Wang, C., and X. Qian. 2020. “Optimizing Support for Heat Dissipation in Additive Manufacturing.” Volume 9: 40th Computers and Information in Engineering Conference (CIE). American Society of Mechanical Engineers, doi:10.1115/detc2020-22198.
- Wang, X., C. Zhang, and T. Liu. 2018b. “A Topology Optimization Algorithm Based on the Overhang Sensitivity Analysis for Additive Manufacturing.” IOP Conference Series: Materials Science and Engineering 382 (3): 32036. doi:10.1088/1757-899X/382/3/032036.
- Wang, C., W. Zhang, L. Zhou, T. Gao, and J. Zhu. 2021b. “Topology Optimization of Self-Supporting Structures for Additive Manufacturing with B-Spline Parameterization.” Computer Methods in Applied Mechanics and Engineering 374: 113599. doi:10.1016/j.cma.2020.113599.
- Wang, C., Z. Zhao, M. Zhou, O. Sigmund, and X. S. Zhang. 2021c. “A Comprehensive Review of Educational Articles on Structural and Multidisciplinary Optimization.” Structural and Multidisciplinary Optimization 64 (5): 2827–2880. doi:10.1007/s00158-021-03050-7.
- Wei, H. L., et al. 2021. “Mechanistic Models for Additive Manufacturing of Metallic Components.” Progress in Materials Science 116: 100703. doi:10.1016/j.pmatsci.2020.100703.
- Wei, C., Z. Sun, Q. Chen, Z. Liu, and L. Li. 2019. “Additive Manufacturing of Horizontal and 3D Functionally Graded 316L/Cu10Sn Components via Multiple Material Selective Laser Melting.” Journal of Manufacturing Science and Engineering 141 (8), doi:10.1115/1.4043983.
- Wein, F., P. D. Dunning, and J. A. Norato. 2020. “A Review on Feature-Mapping Methods for Structural Optimization.” Structural and Multidisciplinary Optimization 62 (4): 1597–1638. doi:10.1007/s00158-020-02649-6.
- Weinans, H., D. R. Sumner, R. Igloria, and R. N. Natarajan. 2000. “Sensitivity of Periprosthetic Stress-Shielding to Load and the Bone Density-Modulus Relationship in Subject-Specific Finite Element Models.” Journal of Biomechanics 33 (7): 809–817. doi:10.1016/s0021-9290(00)00036-1.
- Weiss, B. M., J. M. Hamel, M. A. Ganter, and D. W. Storti. 2021. “Data-Driven Additive Manufacturing Constraints for Topology Optimization.” Journal of Manufacturing Science and Engineering 143 (2): 1–10. doi:10.1115/1.4048264.
- White, D. A., Y. Choi, and J. Kudo. 2020. “A Dual Mesh Method with Adaptivity for Stress-Constrained Topology Optimization.” Structural and Multidisciplinary Optimization 61 (2): 749–762. doi:10.1007/s00158-019-02393-6.
- White, D. A., M. L. Stowell, and D. A. Tortorelli. 2018. “Toplogical Optimization of Structures Using Fourier Representations.” Structural and Multidisciplinary Optimization 58 (3): 1205–1220. doi:10.1007/s00158-018-1962-y.
- Wildman, R. A., and A. T. Gaynor. 2017. “Topology Optimization for Reducing Additive Manufacturing Processing Distortions.” Weapons and Materials Research Directorate, United States, 1–32. [Online]. https://apps.dtic.mil/docs/citations/AD1043622.
- Willner, R., et al. 2020. “Potential and Challenges of Additive Manufacturing for Topology Optimized Spacecraft Structures.” Journal of Laser Applications 32 (3): 32012. doi:10.2351/7.0000111.
- Woldseth, R. V., N. Aage, J. A. Bærentzen, and O. Sigmund. 2022. “On the use of Artificial Neural Networks in Topology Optimisation.” Structural and Multidisciplinary Optimization 65 (10): 294. doi:10.1007/s00158-022-03347-1.
- Wu, J., N. Aage, R. Westermann, and O. Sigmund. 2018. “Infill Optimization for Additive Manufacturing – Approaching Bone-Like Porous Structures.” IEEE Transactions on Visualization and Computer Graphics 24 (2): 1127–1140. doi:10.1109/TVCG.2017.2655523.
- Wu, T., S. A. Jahan, Y. Zhang, J. Zhang, H. Elmounayri, and A. Tovar. 2017. “Design Optimization of Plastic Injection Tooling for Additive Manufacturing.” Procedia Manuf 10: 923–934. doi:10.1016/j.promfg.2017.07.082.
- Wu, J., W. Wang, and X. Gao. 2019. “Design and Optimization of Conforming Lattice Structures.” arXiv preprint arXiv:1905.02902.
- Xia, L., Q. Xia, X. Huang, and Y. M. Xie. 2016. “Bi-Directional Evolutionary Structural Optimization on Advanced Structures and Materials: A Comprehensive Review.” Archives of Computational Methods in Engineering 25 (2): 437–478. doi:10.1007/s11831-016-9203-2.
- Xiao, D., Y. Yang, X. Su, D. Wang, and J. Sun. 2013. “An Integrated Approach of Topology Optimized Design and Selective Laser Melting Process for Titanium Implants Materials.” Bio-medical Materials and Engineering 23 (5): 433–445. doi:10.3233/BME-130765.
- Xiao, Z., Y. Yang, D. Wang, C. Song, and Y. Bai. 2018. “Structural Optimization Design for Antenna Bracket Manufactured by Selective Laser Melting.” Rapid Prototyping Journal 24 (3): 539–547. doi:10.1108/rpj-05-2017-0084.
- Xie, D., et al. 2018. “Assumption of Constraining Force to Explain Distortion in Laser Additive Manufacturing.” Materials (Basel) 11 (11): 2327. doi:10.3390/ma11112327.
- Xie, D., et al. 2021. “Towards a Comprehensive Understanding of Distortion in Additive Manufacturing Based on Assumption of Constraining Force.” Virtual and Physical Prototyping 16 (sup1): S85–S97. doi:10.1080/17452759.2021.1881873.
- Xillo. 2011. “The World’s First 3D Printed Total Jaw Reconstruction.” https://www.xilloc.com/patients/stories/total-mandibular-implant/.
- Xiong, Y., S. Yao, Z.-L. Zhao, and Y. M. Xie. 2020. “A new Approach to Eliminating Enclosed Voids in Topology Optimization for Additive Manufacturing.” Addit Manuf 32: 101006. doi:10.1016/j.addma.2019.101006.
- Xu, S., J. Liu, and Y. Ma. 2022. “Residual Stress Constrained Self-Support Topology Optimization for Metal Additive Manufacturing.” Computer Methods in Applied Mechanics and Engineering 389: 114380. doi:10.1016/j.cma.2021.114380.
- Xu, Y., D. Zhang, Y. Zhou, W. Wang, and X. Cao. 2017. “Study on Topology Optimization Design, Manufacturability, and Performance Evaluation of Ti-6Al-4V Porous Structures Fabricated by Selective Laser Melting (SLM).” Materials (Basel) 10 (9): 1048. doi:10.3390/ma10091048.
- Yaghi, A., S. Ayvar-Soberanis, S. Moturu, R. Bilkhu, and S. Afazov. 2018. “Design Against Distortion for Additive Manufacturing.” 1st International Conference on Additive Manufacturing Benchmarks 27 (March): 224–235. doi:10.1016/j.addma.2019.03.010.
- Yan, L., et al. 2022. “Assembly-Level Topology Optimization and Additive Manufacturing of Aluminum Alloy Primary Mirrors.” Optics Express 30 (4): 6258. doi:10.1364/oe.453585.
- Yang, Y., M. F. Knol, F. van Keulen, and C. Ayas. 2018. “A Semi-Analytical Thermal Modelling Approach for Selective Laser Melting.” Addit Manuf 21: 284–297. doi:10.1016/j.addma.2018.03.002.
- Yang, Y., F. van Keulen, and C. Ayas. 2020. “A Computationally Efficient Thermal Model for Selective Laser Melting.” Addit Manuf 31: 100955. doi:10.1016/j.addma.2019.100955.
- Yap, C. Y., et al. 2015. “Review of Selective Laser Melting: Materials and Applications.” Appl Phys Rev 2 (4): 41101. doi:10.1063/1.4935926.
- Yasin, S. B. M., N. F. Mohd, J. Mahmud, N. S. Whashilah, and Z. Razak. 2018. “A Reduction of Protector Cover Warpage via Topology Optimization.” The International Journal of Advanced Manufacturing Technology 98 (9–12): 2531–2537. doi:10.1007/s00170-018-2388-9.
- Ye, J., P. Kyvelou, F. Gilardi, H. Lu, M. Gilbert, and L. Gardner. 2021. “An End-to-End Framework for the Additive Manufacture of Optimized Tubular Structures.” IEEE Access, 1. doi:10.1109/access.2021.3132797.
- Yeranee, K., Y. Rao, L. Yang, and H. Li. 2022. “Improved Thermal Performance of a Serpentine Cooling Channel by Topology Optimization Infilled with Triply Periodic Minimal Surfaces.” Energies (Basel) 15 (23): 8924. doi:10.3390/en15238924.
- Yu, Y., T. Hur, J. Jung, and I. G. Jang. 2018. “Deep Learning for Determining a Near-Optimal Topological Design Without any Iteration.” Structural and Multidisciplinary Optimization 59 (3): 787–799. doi:10.1007/s00158-018-2101-5.
- Zegard, T., and G. H. Paulino. 2016. “Bridging Topology Optimization and Additive Manufacturing.” Structural and Multidisciplinary Optimization 53 (1): 175–192. doi:10.1007/s00158-015-1274-4.
- Zeng, K. 2015. “Optimization of Support Structures for Selective Laser Melting.” Ph.D. Thesis, University of Louisville, doi:10.18297/etd/2221.
- Zeng, K., D. Pal, and B. Stucker. 2012. “A Review of Thermal Analysis Methods in Laser Sintering and Selective Laser Melting.” 23rd Annual International Solid Freeform Fabrication Symposium – An Additive Manufacturing Conference, SFF 2012, 796–814. doi:10.26153/tsw/15390.
- Zeng, K., D. Pal, C. Teng, and B. E. Stucker. 2015. “Evaluations of Effective Thermal Conductivity of Support Structures in Selective Laser Melting.” Addit Manuf 6: 67–73. doi:10.1016/j.addma.2015.03.004.
- Zhai, Y., D. A. Lados, and J. L. LaGoy. 2014. “Additive Manufacturing: Making Imagination the Major Limitation.” JOM Journal of the Minerals Metals and Materials Society 66 (5): 808–816. doi:10.1007/s11837-014-0886-2.
- Zhang, P., et al. 2015c. “Efficient Design-Optimization of Variable-Density Hexagonal Cellular Structure by Additive Manufacturing: Theory and Validation.” Journal of Manufacturing Science and Engineering, Transactions of the ASME 137 (2): 41–45. doi:10.1115/1.4028724.
- Zhang, Z., et al. 2019a. “3-Dimensional Heat Transfer Modeling for Laser Powder-Bed Fusion Additive Manufacturing with Volumetric Heat Sources Based on Varied Thermal Conductivity and Absorptivity.” Optics & Laser Technology 109: 297–312. doi:10.1016/j.optlastec.2018.08.012.
- Zhang, Z.-D., et al. 2020a. “Topology Optimization Parallel-Computing Framework Based on the Inherent Strain Method for Support Structure Design in Laser Powder-bed Fusion Additive Manufacturing.” International Journal of Mechanics and Materials in Design 16 (4): 897–923. doi:10.1007/s10999-020-09494-x.
- Zhang, Y., A. Bernard, R. Harik, and K. P. Karunakaran. 2015b. “Build Orientation Optimization for Multi-Part Production in Additive Manufacturing.” Journal Of intelligent Manufacturing 28 (6): 1393–1407. doi:10.1007/s10845-015-1057-1.
- Zhang, K., and G. Cheng. 2020. “Three-dimensional High Resolution Topology Optimization Considering Additive Manufacturing Constraints.” Addit Manuf 35: 101224. doi:10.1016/j.addma.2020.101224.
- Zhang, K., G. Cheng, and L. Xu. 2019b. “Topology Optimization Considering Overhang Constraint in Additive Manufacturing.” Computers & Structures 212: 86–100. doi:10.1016/j.compstruc.2018.10.011.
- Zhang, S., D. Da, and Y. Wang. 2022. “TPMS-Infill MMC-Based Topology Optimization Considering Overlapped Component Property.” International Journal of Mechanical Sciences 235: 107713. doi:10.1016/j.ijmecsci.2022.107713.
- Zhang, Z.-D. D., O. Ibhadode, A. Bonakdar, and E. Toyserkani. 2021. “TopADD: A 2D/3D Integrated Topology Optimization Parallel-Computing Framework for Arbitrary Design Domains.” Structural and Multidisciplinary Optimization 64 (3): 1701. doi:10.1007/s00158-021-02917-z.
- Zhang, W., D. Li, J. Zhang, and X. Guo. 2016. “Minimum Length Scale Control in Structural Topology Optimization Based on the Moving Morphable Components (MMC) Approach.” Computer Methods in Applied Mechanics and Engineering 311: 327–355. doi:10.1016/j.cma.2016.08.022.
- Zhang, X., C. C. L. Wang, X. Le, A. Panotopoulou, E. Whiting, and C. C. L. Wang. 2015a. “Perceptual Models of Preference in 3D Printing Direction.” Acm Transactions. on Graphics 34 (6): 1–12. doi:10.1145/2816795.2818121.
- Zhang, Y., S. Yang, and Y. F. Zhao. 2020b. “Manufacturability Analysis of Metal Laser-Based Powder Bed Fusion Additive Manufacturing – a Survey.” The International Journal of Advanced Manufacturing Technology 110 (1–2): 57–78. doi:10.1007/s00170-020-05825-6.
- Zhang, W., J. Yuan, J. Zhang, and X. Guo. 2015d. “A New Topology Optimization Approach Based on Moving Morphable Components (MMC) and the Ersatz Material Model.” Structural and Multidisciplinary Optimization 53 (6): 1243–1260. doi:10.1007/s00158-015-1372-3.
- Zhang, W., L. Zhao, T. Gao, and S. Cai. 2017. “Topology Optimization with Closed B-Splines and Boolean Operations.” Computer Methods in Applied Mechanics and Engineering 315: 652–670. doi:10.1016/j.cma.2016.11.015.
- Zhang, W., W. Zhong, and X. Guo. 2014. “An Explicit Length Scale Control Approach in SIMP-Based Topology Optimization.” Computer Methods in Applied Mechanics and Engineering 282: 71–86. doi:10.1016/j.cma.2014.08.027.
- Zhang, W., and L. Zhou. 2018. “Topology Optimization of Self-Supporting Structures with Polygon Features for Additive Manufacturing.” Computer Methods in Applied Mechanics and Engineering 334: 56–78. doi:10.1016/j.cma.2018.01.037.
- Zhao, D., and W. Guo. 2020. “Shape and Performance Controlled Advanced Design for Additive Manufacturing: A Review of Slicing and Path Planning.” Journal of Manufacturing Science and Engineering 142 (1), doi:10.1115/1.4045055.
- Zhao, D., M. Li, and Y. Liu. 2020a. “A Novel Application Framework for Self-Supporting Topology Optimization.” The Visual Computer 37 (5): 1169–1184. doi:10.1007/s00371-020-01860-2.
- Zhao, G., J. Yang, W. Wang, Y. Zhang, X. Du, and G. Mayi. 2020b. “T-Splines Based Isogeometric Topology Optimization with Arbitrarily Shaped Design Domains.” Computer Modeling in Engineering & Sciences 123: 1033–1059. doi:10.32604/cmes.2020.09920.
- Zhao, Z., and X. S. Zhang. 2021a. “Design of Graded Porous Bone-Like Structures via a Multi-Material Topology Optimization Approach.” Structural and Multidisciplinary Optimization 64 (2): 677–698. doi:10.1007/s00158-021-02870-x.
- Zhao, Z., and X. S. Zhang. 2021b. “Additive Manufacturing of Topology-Optimized Graded Porous Structures: An Experimental Study.” JOM Journal of the Minerals Metals and Materials Society, doi:10.1007/s11837-021-04705-y.
- Zhao, J., M. Zhang, Y. Zhu, X. Li, and L. Wang. 2019. “A Novel Optimization Design Method of Additive Manufacturing Oriented Porous Structures.” ASME 2018 International Mechanical Engineering Congress and Exposition, 1–7. doi:10.1115/IMECE2018-86952.
- Zhou, M., R. Fleury, Y. K. Shyy, H. Thomas, and J. M. Brennan. 2002. “Progress in Topology Optimization with Manufacturing Constraints.” 9th AIAA/ISSMO Symposium on Multidisciplinary Analysis and Optimization September, doi:10.2514/6.2002-5614.
- Zhou, M., B. S. Lazarov, F. Wang, and O. Sigmund. 2015. “Minimum Length Scale in Topology Optimization by Geometric Constraints.” Computer Methods in Applied Mechanics and Engineering 293: 266–282. doi:10.1016/j.cma.2015.05.003.
- Zhou, M., Y. Liu, and Z. Lin. 2019a. “Topology Optimization of Thermal Conductive Support Structures for Laser Additive Manufacturing.” Computer Methods in Applied Mechanics and Engineering 353: 24–43. doi:10.1016/j.cma.2019.03.054.
- Zhou, Y., T. Nomura, and K. Saitou. 2019b. “Multicomponent Topology Optimization for Additive Manufacturing with Build Volume and Cavity Free Constraints.” Journal of Computing and Information Science in Engineering 19 (2): 21011. doi:10.1115/1.4042640.
- Zhou, L., O. Sigmund, and W. Zhang. 2021. “Self-Supporting Structure Design with Feature-Driven Optimization Approach for Additive Manufacturing.” Computer Methods in Applied Mechanics and Engineering 386: 114110. doi:10.1016/j.cma.2021.114110.
- Zhou, L., and W. Zhang. 2019. “Topology Optimization Method with Elimination of Enclosed Voids.” Structural and Multidisciplinary Optimization 60: 1–20. doi:10.1007/s00158-019-02204-y.
- Zhou, H., J. Zhang, Y. Zhou, and K. Saitou. 2019c. “Multi-Component Topology Optimization for Die Casting (MTO-D).” Structural and Multidisciplinary Optimization, 1–15. doi:10.1016/j.cma.2016.06.027.
- Zhou, Y., W. Zhang, J. Zhu, and Z. Xu. 2016. “Feature-Driven Topology Optimization Method with Signed Distance Function.” Computer Methods in Applied Mechanics and Engineering 310: 1–32. doi:10.1016/j.cma.2016.06.027.
- Zhu, B., et al. 2021a. “An 89-Line Code for Geometrically Nonlinear Topology Optimization Written in FreeFEM.” Structural and Multidisciplinary Optimization 63 (2): 1015–1027. doi:10.1007/s00158-020-02733-x.
- Zhu, J., H. Zhou, C. Wang, L. Zhou, S. Yuan, and W. Zhang. 2021b. “A Review of Topology Optimization for Additive Manufacturing: Status and Challenges.” Chinese Journal of Aeronautics 34 (1): 91–110. doi:10.1016/j.cja.2020.09.020.
- Živčák, J., R. Hudák, M. Schnitzer, and T. Kula. 2018. “Numerical Simulation and Experimental Testing of Topologically Optimized PLA Cervical Implants Made by Additive Manufacturing Methodics.” Acta Mechanica et Automatica 12 (2): 141–144. doi:10.2478/ama-2018-0022.