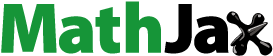
ABSTRACT
Efecto de las condiciones de atomización electrohidrodinámica sobre las características morfométricas y la resistencia mecánica de las partículas de mucílago de chía y alginato
Electrohydrodynamic atomization (EHDA) is a technique which produces monodispersed particles and can employ food grade biopolymers as wall materials, such as chia mucilage. The aim of this work was to study the changes on the morphometric characteristics (Feret, roundness) and mechanical resistance of chia mucilage-sodium alginate microparticles obtained at different process conditions (voltage: 11–14 kV; distance to collector 5.5–8.5 cm). The diameter of particles was ≤1 mm, being more deformed (roundness, RD < 0.61), with higher mechanical strength (MS: 7–7.5 N) and Weber numbers (9.9 x 10−5 – 3.7 × 10−4) than those processed without voltage. A descriptive model relating We and process parameters was developed, being corroborated by Pearson analysis, and observing correlations larger than 0.8 between We with Feret and MS (0.817, 0.807), and Feret with MS and voltage (0.837, 0.826). These results confirmed the feasibility of applying EHDA to produce chia mucilage-sodium alginate particles with different morphologies and mechanical characteristics depending on process conditions.
Resumen
La atomización electrohidrodinámica (EHDA) es una técnica que produce partículas monodispersas y puede emplear biopolímeros de grado alimenticio como materiales de pared, como el mucílago de chía. El objetivo de este trabajo fue estudiar los cambios en las características morfométricas (Feret, redondez) y la resistencia mecánica de las micropartículas de mucílago de chía y alginato de sodio obtenidas en diferentes condiciones de proceso (voltaje: 11-14 kV; distancia al colector 5.5 - 8.5 cm). El diámetro de las partículas fue ≤ 1 mm, estando más deformado (redondez, RD < 0.61), con mayor resistencia mecánica (MS: 7-7.5 N) y números de Weber (We) (9.9 x 10−5 - 3.7 × 10−4) que aquellos procesado sin tensión. Se desarrolló un modelo descriptivo que relaciona We y los parámetros del proceso, corroborados por análisis de Pearson y observando correlaciones mayores que 0.8 entre We con Feret y MS (0.817, 0.807) y Feret con MS y voltaje (0.837, 0.826). Estos resultados confirmaron la viabilidad de aplicar EHDA para producir partículas de alginato de sodio y mucílago de chía con diferentes características morfométricas y mecánicas dependientes de las condiciones de proceso.
1. Introduction
The ionic gelation and the spray drying techniques are the main methods of encapsulation in food-related areas (Ogrodowska et al., Citation2019). These methodologies have been applied to a wide variety of food ingredients such as proteins (Sari et al., Citation2016), enzymes (Amara et al. 2016), probiotics (Poletto et al., Citation2019), microorganisms (Zhao et al. 2016), antioxidants (Niu et al., Citation2020) and other materials to form a capsule. Recent advances in the field of encapsulation of active compounds have shown the need to apply techniques that do not use high temperatures and in this regard, the electrohydrodynamic atomization (EHDA) or electrospraying fulfill this requirement since materials can be handled at ambient-low temperatures with the extra advantage that micro and nanoparticles can be produced (Liu et al., Citation2018; Niu et al., Citation2020). One of the advantages of EHDA is to facilitate the manipulation of non-thermostable raw materials in the food applications and has widely been used as, for example, in the development of intelligent packaging with antibacterial/antioxidant and barrier properties that can resist the entry of a pathogen that causes food to rot (Tapia-Hernández et al., Citation2015) or when preparing encapsulates to control the release of rapidly oxidizing compounds or other food additives. Specifically, several studies have been reported on this technique regarding fiber formation (Hadad & Goli, Citation2019), single and multilayer films production (Cerqueira et al., Citation2016) and encapsulation of bioactive compounds such as folic acid (Pérez-Masiá et al., Citation2015), antioxidants (Niu et al., Citation2020) and enzymes (Alehosseini et al., Citation2019) amongst others. At the industrial level, R&D companies offer consulting services for the development of customized industrial electrospinning systems (RED SERVICES, Citation2020).
The principle of the EHDA is based on the theory of deformation of charged droplets of a liquid that moves rapidly through another fluid when leaving a nozzle or capillary, and is deformed as a result of the high velocities induced by the electrical forces, and which overcome surface tension as given by the Weber number (We), generating different atomization modes (dripping, spindle and cone jet) (Ardila et al., Citation2018; Boda et al., Citation2018). These forces are regulated by the physical properties of the feed, the type of nozzle, the applied voltage, the working distance, and the liquid feed rate, having influence in the size and shapes of the generated droplets (Li et al., Citation2018).
Different studies have been carried out relating the processing conditions, the morphometric characteristics of the capsule, the release of bioactive ingredients, and the stability of microorganisms (García-Salcedo et al., Citation2018; Zhao et al., Citation2017). Also, the use of coaxial EHDA for preparing multicomponent nanoparticles has been reported (Liu et al., Citation2018b). However, only just a few studies on the mechanical properties of capsules and particles have been carried out, differing in the type of method of preparation. Some of them include the use of the single capsule method in which both synthetic and biological polymers (Carin et al., Citation2003) have been tested, while others applied ensemble methods (Neubauer et al., Citation2014; Zhao et al., Citation2017). In all last cases, the capsules have been prepared by an emulsification/internal gelation technique (Cai et al., Citation2014; Zhao et al., Citation2017) or with a vibrating nozzle system (Schuldt et al., Citation2019) in which sodium alginate has been used as wall material.
In these studies, the mechanical properties of the final produced capsules have been determined by compression or centrifugation methods, using for the first case a rheometer (Cai et al., Citation2014) and for the second, a commercial multi-sample analytical centrifuge (Schuldt et al., Citation2019). Regarding the mechanical properties of particles obtained by EHDA and to the best of our knowledge only one study has been published (Young et al., Citation2012) but using synthetic polymers (PVA), and none by preparing the capsules with chia mucilage or other types of biopolymers.
The importance of determining the mechanical properties of the capsule is related to the capacity of its wall material to withstand the handling that could damage or burst it, affecting the release of active components (Carin et al., Citation2003), which is of importance in food enzyme additives technology, for example, in bread making.
Nowadays there are several sources of biopolymers in the market that can be used as wall materials for capsules and films, such as Lipids as waxes, paraffins, diglycerides, monoglycerides, oils, fats, stearic acid and tristearin (Del Río et al., Citation2013). Proteins as gelatin, caseinates, whey, zein, gluten, and albumin (Pedroza-Islas, Citation2002) and carbohydrates as starch, maltodextrins, chitosan dextrans, sucrose, pectin, mucilage, alginate (Nesterenko et al., Citation2013). The sodium salt of alginates is considered one of the best wall materials, due to its stabilizing, gelling, and film-forming properties in addition to its high biocompatibility with other biopolymers (Shao et al., Citation2018). Other biopolymers that have received special attention as wall materials are those extracted from mucilages (Eshun & He, Citation2004) due to their unique rheological properties, their ability to form gels upon hydration and the property of becoming hydrophobic after dehydration in addition to the improvement of flavor, texture, palatability, mouthfeel and the general appearance of the products to which are added (Ozilgen & Bucak, Citation2018).
Previous studies have shown that the mucilage coming from the seeds of the balangu (Sadeghi-Varkani et al., Citation2018) and chia (De Campo et al., Citation2017), as well as nopal (Aceituno-Medina et al., Citation2013), and quince (Jouki et al., Citation2014) have good emulsifying and stabilizing properties, besides a nutritional role, that in the case of chia mucilage has proven to modify the glycemic index of breadmaking products when added (Salgado-Cruz et al., Citation2017). This nutritional effect has been related to the mucilage structure and composition, which is formed by D xylose, α-D-glucose and 4-0-methyl-α-D- glucuronic acid, as their main simple components, forming a complex tetrasaccharide of β-D-xylopyranosyl units (main chain), branched with 4-O-methyl-α-D-glucuronopyranosyl residues (Lin et al., Citation1994; Velázquez-Gutiérrez et al., Citation2015). Also, chia mucilage is considered a good source of minerals as Mg, P and Ca and, in particular, the presence of Ca+2 ions plays a role in the gelling of the complex formed by mixing chia mucilage with sodium alginate, which supports its functional properties (García-Salcedo et al., Citation2018).
More recently, chia seed mucilage has been used for preparing biodegradable films (Capitani et al., Citation2016) and to encapsulate oil (De Campo et al., Citation2017; García-Salcedo et al., Citation2018) during the elaboration of gluten-free bread (Ziemichód et al., Citation2019) and in the encapsulation of microorganisms (Bustamante et al., Citation2017) by using ionic gelation with encapsulation efficiencies above 80%. Sodium alginate controls gel uniformity and strength (Lee & Mooney, Citation2012) and induces the formation of a more geometrically well-ordered structure of the gel particles (Nikoo et al., Citation2018). However, no reports have been published regarding their use in EHDA. Hence, considering the importance for different fields, including food science and technology, to generate more information about physical properties of particles prepared by EHDA using different biopolymeric materials, the objective of this work was to evaluate the feasibility of applying the electrospraying technique for obtaining chia mucilage-sodium alginate particles and to analyze the effect of different process conditions (voltage and the distance from the capillary to the collector) on the morphometric and mechanical characteristics of the capsules and their relation with the Weber number, information that may be useful in a number of food-related processing applications.
2. Materials and methods
2.1. Extraction of the mucilage from the chia seed
Chia mucilage (MC) was obtained according to Salgado-Cruz et al. (Citation2013). Briefly, 15 g of chia seed (La Palma, Nopala, Villagran, Hidalgo, Mex) were mixed with distilled water (1000 mL) at 6000 rpm during 60 min at 40°C (Thermo Scientific heating grill, CIMAREC, Mod; SP131325, China). The mucilage was then separated from the seed by rubbing the particles onto mesh screen and the product was sieved (40 mesh) (Monyl 132–10XX, Sefar Nytal PA, Switzerland). The resulting filtrate was placed in an ethanol-acetone solution (70:30) for separating the mucilage. The extracted residue was dried to 6.0% (d.b.) final moisture (40°C for 4 h, TERLAB MR, Mod: MAH25D, Mexico), ground (KRUPS milled, Mod: GX410011, Mexico) and kept into hermetically sealed plastic containers until further use.
2.2. Preparation of chia mucilage-sodium alginate solution (MC-AlgNa)
A 0.5% chia mucilage – 0.5% sodium alginate solution (MC-AlgNa; surface tension = 65.67 ± 1.53 dyne/cm; density = 0.99 ± 0.44 g/mL; conductivity 0.030 ± 0.0013 Sm) was prepared following the methodology proposed by Sadeghi-Varkani et al. (Citation2018). The 0.5% (w/v) sodium alginate solution was stirred at 6000 rpm (Thermo scientific, China) for 15 min at room temperature (25°C) until a homogeneous mixture was obtained (surface tension = 58.17 ± 0.28 dyne/cm; density = 0.95 ± 0.00 g/mL). The same process was followed to prepare the 0.5% (w/v) chia mucilage solution (surface tension = 83.22 ± 0.5 dyne/cm; density = 0.712 ± 0.005 g/mL). The 1:1 wall materials concentration was chosen based on Moran Aguilar (Citation2018) results, who reported that chia mucilage capsules containing rodamine and prepared by a dripping method, generated at this ratio the best encapsulation efficiency and the desired rodamine liberation rate.
2.3. Electrohydrodynamic atomization
The droplets were obtained by using the electrohydrodynamic atomization equipment (, CICATA-IPN Querétaro, Mexico), which consisted of 7 main elements: 1) Syringe pump with linear actuator; 2) Plastic syringe (10 mL, BD Plastipak); 3) Stainless steel capillary tube (ID = 0.6 mm, wall thickness 0.1 mm, gauge 21G1); 4) Power supply (0 a 30 kV DC, 30A24-P4. Ultravolt, Ronkonkoma, NY, USA); 5) Positive electrode; 6) Negative electrode; 7) Collector.
Figure 1. Electrohydrodynamic atomization equipment (CICATA-IPN Querétaro).
Figura 1. Equipo de atomización electrohidrodinámica (CICATA-IPN Querétaro).
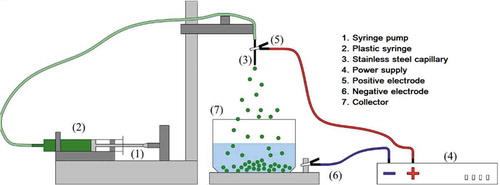
The 0.5% chia mucilage-alginate solution (w/v) (MC-AlgNa) was fed to the equipment through the syringe, which was connected to the positive electrode of the high voltage source (DC) while the collector was grounded (negative electrode). During electrospraying, the 2% CaCl2 solution (w/v) was placed into an aluminum collector (12 cm diameter). The distance between the tip of the capillary and the gelling solution (CaCl2 2% w/v) located in the collector was variable (5.5, 7 and 8 cm), as was the applied voltage (11, 14 and 17 kV), while the flow rate was kept constant at 2 mL/h.
2.4. Dripping mode
Tests were run by using the above described electrohydrodynamic atomization equipment, fixing the same distances to the collector (5.5, 7.0, 8.5 cm) and using the same flow rate (2 mL/h) than for EHDA, but without the application voltage.
2.5. Characterization of the particles
The morphology and structure of the particles were studied by using a light stereomicroscope (Nikon SMZ1500, Japan) fitted with a digital camera (NIKON Japan DS-2 Mv Digital Sight TV Lens 0.55xDS). Captured images were analyzed using the NIS-Elements F 2.30 and ImageJ (ImageJ 1.50i National Institute of Health, Bethesda, Maryland, USA) software. The evaluated parameters were Feret (Fe) (maximum distance between the farthest two points of the perimeter) and roundness (Rd) (EquationEquation (1))(1)
(1) .
Images of the drops formed as leaving the capillary were captured by using telescopic lenses (VZM ™ 1000i Zoom Imaging Lens, Edmund Optics, Barrington, New Jersey) attached to the DxK23U274 digital camera (1600 X 1200 resolution). Images were captured by means of the IC Capture 2.4 software.
2.6. Weber number
The final shape of electrosprayed particles is related to the atomization modes and specifically to the type of drop formed during its detachment from the nozzle as a result of the inertial and surface tension acting on the flowing liquid and measured by the Weber number which was calculated as reported by Xu et al. (Citation2018) by means of EquationEquation (2)(2)
(2) , and which describes the ratio between deforming inertial forces, related to velocity, density and distance, and the stabilizing cohesive forces associated with the surface tension.
Where:
We is the dimensionless Weber number; ρ is the MC-AlgNa density (Kg/m3); V is velocity of the MC-AlgNa atomized solution (m/s); D is the Feret of the droplet (m), and σ is the surface tension of the MC-AlgNa solution (dyne/cm).
The Feret (Fe) was evaluated for each processing condition, while the velocity was calculated as reported by Yazdekhasti et al. (Citation2019) by means of EquationEquation (3)(3)
(3) as shown below:
where Q is the operating flow rate (2.0 mL/h). In all cases, Fe of the final particle was considered to evaluate V.
2.7. Mechanical properties
The mechanical properties of the collected capsules were measured according to the method described by Zhao et al. (Citation2017) using a rheometer (Hybrid DH3 Discovery, TA Instruments, EE. UU) with a parallel-plate geometry (40 mm in diameter) at 25°C. The mechanical resistance was obtained in compression mode. The particle initial height was established based on the average diameter of the particles. Based on this height, the gap, the values of the loading gap and the minimum volume of the sample were fed to the equipment software. Subsequently, the initial value of the measurements was set at an axial force of 0.3 N and a sensitivity of 0.1 N. The axial force F (N) was registered during compression up to 40% of the initial height of the particles. Also, the compression time and the gap (μm) were considered for the test.
2.8. Experimental design and statistical analyses
The effect of voltage (0, 11, 14 and 17 kV) and working distance (5.5, 7.0, 8.5 cm) on the mechanical strength, particle size and roundness (Rd) of particles were studied using a central rotatable composite statistical design (Design Expert V 9.0, Stat-Ease In., MN, USA), centered on its faces with 5 central point repetitions and duplicates at the other points, for a total of 27 experimental conditions. The levels of each variable were selected according to preliminary tests (results not shown), looking for the smallest possible Fe of droplet, the largest mechanical resistance and preventing the formation of an electric arc.
The correlations between the roundness (Rd), the percentage of particles with diameter smaller than 1 mm, mechanical resistance, Weber number and the voltage were evaluated by using SigmaPlot V. 12.0 (Systat Software Inc., San Jose CA, USA.).
3. Results and discussion
3.1. Morphometric characteristics of the particles
The effect generated by the electric potential and the distance to the collector on the percentage of particles with Feret diameters smaller than 1 mm is presented in . Data were fitted to a quadratic model (p ≤ 0.0001) with a determination coefficient (R2) of 0.8424.
Figure 2. Changes in the percentage of particles with diameters smaller than 1 mm (2A) and in their size (2B) due to the processing method. (a) Electrohydrodynamic atomization (Quadratic model, R2 = 0.84), voltage (p ≤ 0.0001); working distance (p = 0.2383). (b) Dripping mode.
Figura 2. Cambios en el porcentaje de partículas con diámetros menores a 1 mm (2A) y en su tamaño (2B) debido al método de procesamiento. (A) Atomización electrohidrodinámica (modelo cuadrático, R2 = 0,84), voltaje (p ≤ 0,0001); distancia de trabajo (p = 0.2383). (B) Modo de goteo.
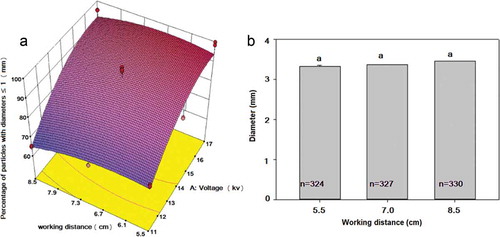
Regarding the size of particles, in ) it can be seen that as the voltage increased the percentage of particles with Fe lower than 1 mm also increased (p ≤ 0.05), without statistical effect of distance (p = 0.2383). In this regard, various authors have reported that large electric charges induced the rupture of drops thus generating more and smaller particles (Songsurang et al., Citation2011). Besides, Strand et al. (Citation2002) reported that the size and the shape of the particles are also influenced by the magnitude of the voltage applied and by the diameter of the atomizing needle (capillary), having more practical acceptability for bioactive delivery the smaller ones due to their faster release rates (Wang et al., Citation2019).
On the other hand, in ), the results of the morphometric parameters of the particles produced without the application of a voltage load (dripping mode) showed no statistical effect (p > 0.05) of the distance between the capillary and the collector, being the average Fe of these particles 3.2 times larger than those obtained by electrospraying ()). Similar results were obtained by Zhao et al. (2016) who mentioned that for Ganoderma lucidum spores-alginate micro beads, smaller diameters were obtained at high working voltages (10 kV) than when applying low voltages (5 kV).
The size distribution of particles, obtained by EHDA, as well as the corresponding micrographs for each process condition showing their shape, along with their dripping mode, are presented in . From these results, it is possible to observe that a larger proportion of particles had diameters between 0.9 and 1 mm, reaching the maximum percentage (97%) at high voltages (17 kV) and the smallest working distances (5.5 cm). These findings evidenced that under the experimental conditions used in this work, close to mono-disperse size distributions of the particles were obtained, probably due to the jet destabilization, which forms small highly charged droplets due to the direct relationship of the charge, the dielectric constant and the surface tension of the liquid (Bock et al., Citation2012). These drops prevent their agglomeration and coagulation (Jaworek and Sobczyk, Citation2008) by the repulsion forces between them, making monodisperse particles; similar results were reported by Boda et al. (Citation2018) who studied the encapsulation of hydrophilic and hydrophobic drugs within polymeric carriers, also by Nikoo et al. (Citation2018) who produced small particles (765.29 ± 14.53 μm) by EHDA at 8 kV and Soleimanifar et al. (Citation2019) for the encapsulation of olive leaf extract in serum protein concentrate by electrospraying at 0–30 kV.
Figure 3. Diameter frequency distributions of electrosprayed particles at different working distances (WD) and voltages. a: WD 5.5 cm, voltage 11Kv; b: WD 5.5 cm, 14Kv voltage; c: WD 5.5 cm, voltage 17Kv; d: WD 7 cm, voltage 11kv; e: WD 7 cm, 14kv voltage; f: WD 7 cm, voltage 17kv; g: WD 8.5 cm, voltage 11kv; h: WD 8.5 cm, 14kv voltage; i: WD 8.5 cm, voltage 11kv. In all cases, an image of the droplet upon being released is presented. Reference bars for droplets 0.5 mm; reference bars for particles 1.0 mm.
Figura 3. Distribuciones de frecuencia de diámetro de partículas electropulverizadas a diferentes distancias de trabajo (WD) y voltajes. a: WD 5.5 cm, voltaje 11Kv; b: WD 5.5 cm, voltaje de 14Kv; c: WD 5.5 cm, voltaje 17Kv; d: WD 7 cm, voltaje 11kv; e: WD 7 cm, voltaje de 14kv; f: WD 7 cm, voltaje 17kv; g: WD 8.5 cm, voltaje 11kv; h: WD 8.5 cm, voltaje de 14kv; i: WD 8.5 cm, voltaje 11kv. En todos los casos, se presenta una imagen de la gota al ser liberada. Barras de referencia para gotas de 0,5 mm; barras de referencia para partículas de 1.0 mm.
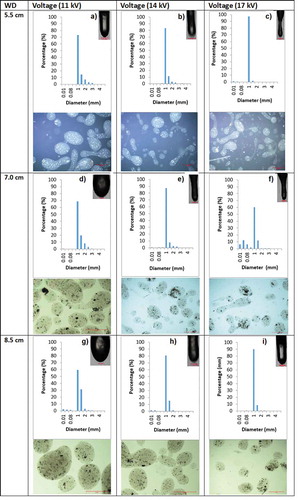
It can also be seen from , that particles presented, in most of the cases, four different types of shapes: tear, double tear, elongated, and spherical, which clearly changed depending on the processing conditions, the dripping mode and the distances used to obtain them. As mentioned above, the most deformed objects were produced by applying high voltages at short working distances, and in this regard, Bodnár et al. (Citation2018) explained that for many polymer/solvent combinations, the particles froze or vitrified following three different scenarios (atomization modes), based on the presence or not of Coulombic instabilities and generating different shapes (spindle, tear-shaped relics, spheric). They also cited that the transitions between these scenarios depend on the number of entanglements each polymer chain has and on the droplet formation history, which must be related to the process conditions (voltage, distance) and to the properties of the solution (electrical conductivity, viscosity, surface tension) by changing the electric field strength which generates the formation of the atomization modes, as well as to the molecular weight and concentration of polymer in the electrosprayed material. In this context, Ardila et al. (Citation2018) reported that the voltage applied during the EHDA affected the shape and size of particles, as a result of a change on the atomization modes (from dripping and spindle, to cone jet).
In , the roundness of obtained particles can be observed and as described earlier, it changed as a result of the process parameters, having significant effect both variables (voltage, p ≤ 0.0001; distance to the collector, p = 0.0022) and fitting the data to a quadratic model (p ≤ 0.0001, R2 = 0.8441). It can also be noticed that the most deformed materials (Rd < 0.6), with tear or double tear shapes, were obtained when applying 17 kV at 5.5 cm of capillary-collector distance, and became rounder, in most of the cases, when increasing the working distance and decreasing the voltage. In particular, the amount of deformed particles increased from 26.82 ± 2.46% to 48.31 ± 0.53% at the shortest working distance (5.5 cm) when voltage was increased from 11 to 17 kV. In this respect Boda et al. (Citation2018) cited that the third forming particles scenario is characterized by particles with not attached filaments, besides a mechanically strong skin or shell which stabilizes the droplet against deformation, that in our case correspond to larger diameter and more circular particles at the farthest distance (8.5 cm), that allows higher rates of solvent evaporation, causing a vitrification of the particle, instead of the generation of the varicose mode. Also, the concentration of the chia mucilage-alginate solution (1%) and its reported molecular weight (Camacho et al., Citation2019; Dick et al., Citation2015) are within the range cited to follow the mentioned scenarios. Boda et al. (Citation2018) cited that a strong electric field causes a decrease in particle size as well as an elongation of the particle, changing its morphology and Bodnár et al. (Citation2018) that the polymer molecular weight and concentration of the solution have an influence on the shape of the particle.
Figure 4. Changes of the roundness (Rd) due to the elaboration method. (a) Electrohydrodynamic atomization (Quadratic model, R2 = 0.8441), voltage (p ≤ 0.0001); working distance (p = 0.0022). (b) Dripping mode.
Figura 4. Cambios de la redondez (Rd) debido al método de elaboración. (a) Atomización electrohidrodinámica (modelo cuadrático, R2 = 0.8441), voltaje (p ≤ 0.0001); distancia de trabajo (p = 0.0022). (B) Modo de goteo.
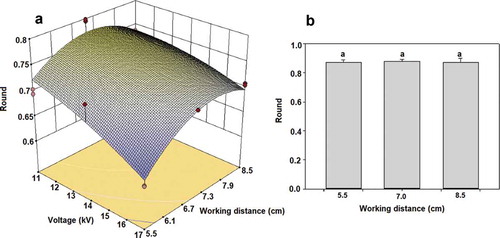
On the other hand, when no electric charge was applied ()), particles increased their size, and their shape was close to a sphere (Rd > 0.8), independently of the working distances (p > 0.05), which is a typical feature of this process as reported by Nikoo et al. (Citation2018) for electrospray encapsulated caffeine with alginate and chitosan, while Medina et al. (Citation2018) cited the development of mostly spherical particles of sodium caseinate-lactose- chia mucilage, of various sizes, with continuous walls and without apparent cracks or fissures.
4. Weber number (We)
We values ()) were fitted to a 2FI model (p ≤ 0.0001, R2 = 0.7362), having significant effects both, the voltage (p = 0.0027) and the capillary-collector distance (p = 0.0030), as well as their interaction, and observing that at the higher voltage, and the shortest distance to the collector, the less spherical, and deformed particle (), linked to the highest Weber values and being these results similar to those reported by Chang et al. (Citation2014), who cited that the shape of the obtained particles depends on the We number, stressing that beads were formed at We < 1.2, while nanofibers at We > 10. In other work, Ardila et al. (Citation2018) reported We numbers associated to the cone jet mode, and established the no-dependence of the concentration of the sprayed material (chitosan-Acetic acid) with high We numbers (> 0.96 × 10−6) and more recently, Yazdekhasti et al. (Citation2019) studied the effect of electrical conductivity of the feed solutions on the EHDA modes and maintained the We number almost invariable (9.85 x 10−3) and as a control process parameter.
Figure 5. Changes of the Weber number (We) due to the elaboration method. (a) Electrohydrodynamic atomization (Quadratic model, R2 = 0.7362) voltage (p ≤ 0.0027); working distance (p = 0.0030). (b) Dripping mode.
Figura 5. Cambios del número de Weber (We) debido al método de elaboración. (A) Atomización electrohidrodinámica (modelo cuadrático, R2 = 0.7362) (p ≤ 0.0027); distancia de trabajo (p = 0.0030). (B) Modo de goteo.
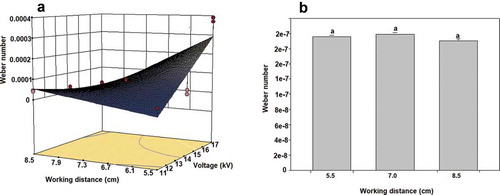
Concerning the production of particles by the dripping mode (no electric current applied, )), no significant effect of capillary-collector distance was noticed (p > 0.05) and the smallest We values were obtained in this operation, as expected from the lowest velocity as a result of the no voltage appliance. These results are in accordance with those observed in ).
4.1. Mechanical resistance
The effect of voltage and working distance on the mechanical resistance to compression is shown in ). Data were fitted to a quadratic model, where both variables and their interactions showed significant effect (p ≤ 0.05), promoting that the higher the voltage and the lower the working distance, the larger the mechanical resistance up to a maximum of 7.58 N obtained at 5.5 cm and 17 kV. This value of mechanical resistance is related to higher surface-volume ratios of particles and is associated with small and deformed objects as shown in (Shafiei Dastgerdi et al., Citation2019). Both variables, voltage (p = .0004) and working distance (p = .038) were significant and the response values obtained were within the range reported by Forster et al. (Citation2010) for calcium alginate particles. On the other hand, when no voltage was applied (dripping mode) the working distance ()) did not affect significantly (p > 0.05) the mechanical strength of the particles and an average value of 3.34 N was obtained, which could be related to the large sizes of the particles.
Figure 6. Effect of voltage and working distance on particle mechanical strength due to the elaboration method. (A) Electrohydrodynamic atomization (Quadratic model, R2 of 0.7916), voltage (p ≤ 0.0004); working distance (p = 0.0381). (B) Dripping mode.
Figura 6. Efecto del voltaje y la distancia de trabajo sobre la resistencia mecánica de las partículas debido al método de elaboración. (A) Atomización electrohidrodinámica (modelo cuadrático, R2 de 0.7916), voltaje (p ≤ 0.0004); distancia de trabajo (p = 0.0381). (B) Modo de goteo.
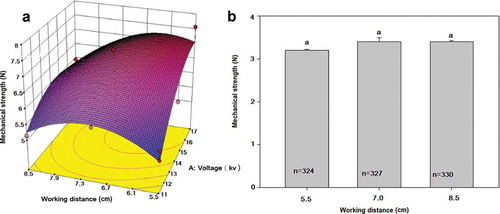
As mentioned, the observed differences in the mechanical resistance could be related to the size of the particle, but also to the type of biopolymer utilized. In this regard, Sun et al. (Citation2010) reported that the mechanical strength of copper nanowires encapsulated in helical carbon nanotubes was dependent on the diameter of the capsule and on the width of the wall coating material, while Zhao et al. (Citation2017) published that differences in mechanical strength were associated to the size of the capsule. In the same context, Bustamante et al. (Citation2017) and Cortés-Camargo et al., Citation2018) cited a reduction in the particle size and an improvement in the resistance of encapsulates, in the first case when combining mixtures of chia mucilage and flaxseed protein, while for the second when using chia seed mucilage and mesquite gum. In other work, Kostov et al. (Citation2010) mentioned that the flexibility of calcium alginate capsules changed with the material concentration.
Regarding the type of biopolymer, it has been reported that the size and the shape, and as consequence of these last two parameters, the resistance of capsules, are dependent on the functional groups that conforms the biopolymer (Dodero et al., Citation2019), as well as on their concentration and molecular weight (Bodnár et al., Citation2018). As example, the increase in resistance of our capsules could be ascribed to the interaction, of polymers with the Ca+2 ions, that changes the droplets into particles, by binding together the alginate carbohydrate chains (α-L- guluronic acid) and forming the typical egg-shell structure (Dodero et al., Citation2019) that gives mechanical resistance to the gelled particles. Parallel, it is expected that at higher voltages, more Ca+2 ions were brought into con tact with the acid residues of the carbohydrate chain, giving place to multiple egg-shell structures in comparison to low-voltage operations (Tekieh et al., Citation2016). In the same context, it also has been reported (Lee & Mooney, Citation2012) that the interaction between sodium alginate and calcium ions possibly causes that the (1 − 4) ß-D-manuronic acid, and the alpha-L-guluronic acid chains from alginate get closer to chia mucilage entanglements, helping by this way to form a more stable and firmer gel. In this regard, García-Salcedo et al. (Citation2018) demonstrated that chia seed has a high content of Ca and Mg, forming complexes of CaCO3; hence, it is probable that the calcium ion present in mucilage participate in the gelling process.
With respect to concentration and molecular weight, it has been established that these parameters are related to the shape of particles, generating elongated shapes at high molecular weights (tens to hundreds). Moreover, spherical particles are obtained when using process conditions that facilitate solvent evaporation (Bodnár et al., Citation2018).
4.2. Descriptive model and Pearson correlation
From the results presented it can be summarized that when increasing the percentage of particles with diameters ≤1 mm, the We and the mechanical resistance increased, while the shape of the particles showed a dependence of voltage and working distance, finding elongated particles, associated to the spindle atomization mode. At larger We, similar results to those reported by Rosell-Llompart et al. (Citation2018) were obtained from the Taylor cone formation to spray development. This information is presented in a descriptive form in .
Figure 7. Descriptive model showing the effect of EHDA variables on We, mechanical resistance, shape and percentage of particles with diameters less than ≤ 1 mm.
Figura 7. Modelo descriptivo que muestra el efecto de las variables EDHA en We, resistencia mecánica, forma y porcentaje de partículas con diámetros menores a ≤ 1 mm.
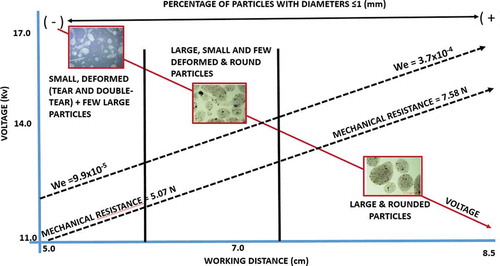
To corroborate the possible linear relations among the response variables (We, PD, Rd and MS) a Pearson analysis was carried out and the correlation coefficients (R) and their probability values (p) are shown (). It can be seen from this data, that more than one half of these parameters (8/14) presented a statistically significant correlation (p ≤ 0.05), but only four of them had an R value higher than 0.8, which means that even though most of these variables are related, they do not follow a lineal relationship.
Table 1. Pearson correlation analysis of EHDA variables and responses.
It can also be noticed from these results, that the Weber number is directly related to percentage of particles with diameter ≤1 mm (R = 0.817), and to the mechanical strength (R = 0.807), due to this dimensionless number represents the competence of the deforming and the stabilizing cohesive forces of a liquid moving through a fluid medium (EquationEquation (2)(2)
(2) ). Also, and as already commented, the percentage of particles smaller to 1 mm (PD) has a direct relation (R = 0.837) with their resistance to be deformed (MS), and as expected, with the voltage (R = 0.826). These results are in accordance with those presented by Gomez-Estaca et al. (Citation2012) and Partovinia and Vatankhah (Citation2019) who reported that voltage is one of the most important factors that influences the size of the particles (PD). In this respect, Schuldt et al. (Citation2019) found that alginate beads prepared by electrospraying showed shapes close to spherical and mono-dispersion and Zhao et al. (Citation2017) related the diameter of alginate microcapsules to their mechanical resistance in the encapsulation of lactobacillus. From these results, it can be said that the EHDA operating conditions used in this work could serve as the basis for developing a standardized methodology to produce calcium alginate particles having a wide range of characteristics and which can be used as wall materials in a number of food processing operations.
5. Conclusions
These results confirm the feasibility of applying the electrohydrodynamic atomization technique to produce chia mucilage-sodium alginate micro particles with different morphology and mechanic characteristics depending on process conditions, which could allow a better protective action on active compounds when added. In all operating conditions, particles prepared by electrospraying were smaller (≤1 mm), more deformed (roundness < 0.6), with more homogeneous sizes and with higher mechanical strength (7–7.5 N) than those produced without the application of voltage (dripping mode). It was also observed that different We numbers gave place to a wide range of sizes and shapes of particles (tear, double tear, elongated, and spherical) and it can be used to establishing adequate operating conditions for obtaining capsules with the desired morphometric and mechanical resistance. On the other hand, the complex mechanisms involved in EHDA constitute a challenge for the food processing industry, opening a window for the use of a different food grade polymeric materials for the preparation of enzymatic or nutraceutical additives, with possible application in bread making and other food industries.
Acknowledgments
Minerva Rentería Ortega wishes to express her gratitude to CONACYT-Mexico and BEIFI-IPN-Mexico for the study grants provided. This research was financed through the projects, 20160097, 20170467, 20181299, and 20195500 from the Instituto Politécnico Nacional (IPN-México) and the project 1668 from CONACYT.
Disclosure statement
No potential conflict of interest was reported by the authors.
Additional information
Funding
References
- Aceituno-Medina, M., Mendoza, S., Lagaron, J. M., & López-Rubio, A. (2013). Development and characterization of food-grade electrospun fibers from amaranth protein and pullulan blends. Food Research International, 54(1), 667–674. https://doi.org/10.1016/j.foodres.2013.07.055
- Alehosseini, A., Sarabi-Jamab, M., Ghorani, B., & Kadkhodaee, R. (2019). Electro-encapsulation of Lactobacillus casei in high-resistant capsules of whey protein containing transglutaminase enzyme. LWT - Food Science and Technology, 102, 150–158. https://doi.org/10.1016/j.lwt.2018.12.022
- Ardila, N., Ajji, Z., Heuzey, M.-C., & Ajji, A. (2018). Chitosan electrospraying: Mapping of process stability and micro and nanoparticle formation. Journal of Aerosol Science, 126, 85–98. https://doi.org/10.1016/j.jaerosci.2018.08.010.
- Ben, A. C., Eghbal, N., Degraeve, P., & Gharsallaoui, A. (2016). Using complex coacervation for lysozyme encapsulation by spray-drying. Journal of Food Engineering, 183, 50–57. https://doi.org/10.1016/J.JFOODENG.2016.03.016
- Bock, N., Dargaville, T. R., & Woodruff, M. A. (2012). Electrospraying of polymers with therapeutic molecules: State of the art. Progress in Polymer Science, 37(11), 1510–1551. https://doi.org/10.1016/j.progpolymsci.2012.03.002
- Boda, S. K., Li, X., & Xie, J. (2018). Electrospraying an enabling technology for pharmaceutical and biomedical applications: A review. Journal of Aerosol Science, 125, 164–181. https://doi.org/10.1016/j.jaerosci.2018.04.002
- Bodnár, E., Grifoll, J., & Rosell-Llompart, J. (2018). Polymer solution electrospraying: A tool for engineering particles and films with controlled morphology. Journal of Aerosol Science, 125, 93–118. https://doi.org/10.1016/j.jaerosci.2018.04.012
- Bustamante, M., Oomah, B. D., Rubilar, M., & Shene, C. (2017). Effective Lactobacillus plantarum and Bifidobacterium infantis encapsulation with chia seed (Salvia hispanica L.) and flaxseed (Linum usitatissimum L.) mucilage and soluble protein by spray drying. Food Chemistry, 216, 97–105. https://doi.org/10.1016/j.foodchem.2016.08.019
- Cai, S., Zhao, M., Fang, Y., Nishinari, K., Phillips, G. O., & Jiang, F. (2014). Microencapsulation of Lactobacillus acidophilus CGMCC1.2686 via emulsification/internal gelation of alginate using Ca-EDTA and CaCO3 as calcium sources. Food Hydrocolloids, 39, 295–300. https://doi.org/10.1016/j.foodhyd.2014.01.021.
- Camacho, D. H., Uy, S. J. Y., Cabrera, M. J. F., Lobregas, M. O. S., & Fajardo, T. J. M. C. (2019). Encapsulation of folic acid in copper-alginate hydrogels and it’s slow in vitro release in physiological pH condition. Food Research International, 119, 15–22. https://doi.org/10.1016/j.foodres.2019.01.053
- Capitani, M. I., Matus-Basto, A., Ruiz-Ruiz, J. C., Santiago-García, J. L., Betancur-Ancona, D. A., Nolasco, S. M., Tomás, M. C., & Segura-Campos, M. R. (2016). Characterization of biodegradable films based on Salvia hispanica L. Protein and Mucilage. Food and Bioprocess Technology, 9(8), 1276–1286. https://doi.org/10.1007/s11947-016-1717-y
- Carin, M., Barthès-Biesel, D., Edwards-Lévy, F., Postel, C., & Andrei, D. C. (2003). Compression of biocompatible liquid-filled HSA-alginate capsules: Determination of the membrane mechanical properties. Biotechnology and Bioengineering, 82(2), 207–212. https://doi.org/10.1002/bit.10559
- Cerqueira, M. A., Fabra, M. J., Castro-Mayorga, J. L., Bourbon, A. I., Pastrana, L. M., Vicente, A. A., & Lagaron, J. M. (2016). Use of electrospraying to develop antimicrobial biodegradable multilayer systems: Encapsulation of cinnamaldehyde and their physicochemical characterization. Food and Bioprocess Technology, 9(11), 1874. https://doi.org/doi.doi.doi.10.1007/s11947-016-1772-4
- Chang, W.-M., Wang, C.-C., & Chen, C.-Y. (2014). The combination of electrospinning and forcespinning: Effects on a viscoelastic jet and a single nanofiber. Chemical Engineering Journal, 244, 540–551. https://doi.org/10.1016/j.cej.2014.02.001
- Cortés-Camargo, S., Acuña-Avila, P. E., Rodríguez-Huezo, M. E., Varela-Guerrero, R.-G. A., & Pérez-Alonso, C. (2018). Effect of chia mucilage addition on oxidation and release kinetics of lemon essential oil microencapsulated using mesquite gum – Chia mucilage mixtures. Food Research, 116, 1010–1019. https://doi.org/10.1016/j.foodres.2018.09.040
- de Campo, C., Dos Santos, P. P., Costa, T. M. H., Paese, K., Guterres, S. S., Rios, A. D. O., & Flôres, S. H. (2017). Nanoencapsulation of chia seed oil with chia mucilage (Salvia hispanica L.) as wall material: Characterization and stability evaluation. Food Chemistry, 234, 1–9. https://doi.org/10.1016/j.foodchem.2017.04.153
- Del Río, J. C., Prinsen, P., & Gutiérrez, A. (2013). Chemical composition of lipids in brewer’s spent grain: A promising source of valuable phytochemicals. Journal of Cereal Science, 58(2), 248–254. https://doi.org/10.1016/j.jcs.2013.07.001
- Dick, M., Costa, T. M. H., Gomaa, A., Subirade, M., Rios, A. D. O., & Flôres, S. H. (2015). Edible film production from chia seed mucilage: Effect of glycerol concentration on its physicochemical and mechanical properties. Carbohydrate Polymers, 130, 198–205. https://doi.org/10.1016/j.carbpol.2015.05.040
- Dodero, A., Pianella, L., Vicini, S., Alloisio, M., Ottonelli, M., & Castellano, M. (2019). Alginate-based hydrogels prepared via ionic gelation: An experimental design approach to predict the crosslinking degree. European Polymer Journal, 118, 586–594. https://doi.org/10.1016/j.eurpolymj.2019.06.028
- Eshun, K., & He, Q. (2004). Aloe vera: a valuable ingredient for the food, pharmaceutical and cosmetic industries - a review. Critical Reviews in Food Science and Nutrition, 44(2), 91–96. https://doi.org/10.1080/10408690490424694
- Forster, R. E. J., Thürmer, F., Wallrapp, C., Lloyd, A. W., Macfarlane, W., Phillips, G. J., & Lewis, A. L. (2010). Characterisation of physico-mechanical properties and degradation potential of calcium alginate beads for use in embolisation. Journal of Materials Science. Materials in Medicine, 21(7), 2243–2251. https://doi.org/10.1007/s10856-010-4080y
- García-Salcedo, Á. J., Torres-Vargas, O. L., Del Real, A., Contreras-Jiménez, B., & Rodriguez-Garcia, M. E. (2018). Pasting, viscoelastic, and physicochemical properties of chia (Salvia hispanica L) flour and mucilage. Food Structure, 16, 59–66. https://doi.org/10.1016/j.foostr.2018.03.004
- Gomez-Estaca, J., Balaguer, M. P., Gavara, R., & Hernandez-Munoz, P. (2012). Formation of zein nanoparticles by electrohydrodynamic atomization: Effect of the main processing variables and suitability for encapsulating the food coloring and active ingredient curcumin. Food Hydrocolloids, 28(1), 82–91. https://doi.org/10.1016/j.foodhyd.2011.11.013
- Hadad, S., & Goli, S. A. H. (2019). Improving oxidative stability of flaxseed oil by encapsulation in electrospun flaxseed mucilage nanofiber. Food and Bioprocess Technology, 12(5), 829. https://doi.org/10.1007/s11947-019-02259-1
- Jaworek, A., & Sobczyk, A. T. (2008). Electrospraying route to nanotechnology: An overview. Journal of Electrostatics, 66(3–4), 197–219. https://doi.org/10.1016/j.elstat.2007.10.001
- Jouki, M., Mortazavi, S. A., Yazdi, F. T., & Koocheki, A. (2014). Optimization of extraction, antioxidant activity and functional properties of quince seed mucilage by RSM. International Journal of Biological Macromolecules, 66, 113–124. https://doi.org/10.1016/j.ijbiomac.2014.02.026
- Kostov, G., Profile, S., Angelov, M., Mihaylov, I., & Poncelet, D. (2010). Mechanical properties of Ca-alginate beads for ethanol fermentation with immobilized yeast. Revue de Génie Industriel Revue de Génie Industriel, 5, 25–35. https://www.researchgate.net/publication/258840267
- Lee, K. Y., & Mooney, D. J. (2012). Alginate: Properties and biomedical applications. Progress in Polymer Science (Oxford), 37(1), 106–126. https://doi.org/10.1016/j.progpolymsci.2011.06.003
- Li, J., Zhang, H., & Liu, Q. (2018). Dynamics of a successive train of monodispersed millimetric-sized droplets impact on solid surfaces at low Weber number. Experimental Thermal and Fluid Science, 102, 81–93. https://doi.org/10.1016/j.expthermflusci.2018.08.029
- Lin, K.-Y., Daniel, J. R., & Whistler, R. L. (1994). Structure of chia seed polysaccharide exudate. Carbohydrate Polymers, 23(1), 13–18. https://doi.org/10.1016/0144-8617(94)90085-x
- Liu, Z.-P., Zhang, -L.-L., Yang, -Y.-Y., Wu, D., Jiang, G., & Yu, D.-G. (2018). Preparing composite nanoparticles for immediate drug release by modifying electrohydrodynamic interfaces during electrospraying. Powder Technology, 327, 179–187. https://doi.org/10.1016/J.POWTEC.2017.12.066
- Medina, U., Julio, L. M., Segura-Campos, M. R., Ixtaina, V. Y., & Tomás, M. C. (2018). Development and characterization of spray-dried chia oil microcapsules using by-products from chia as wall material. Powder Technology, 50(2), 642–650. https://doi.org/10.1016/j.powtec.2018.04.060.
- Moran Aguilar, H. F. (2018). Optimización del proceso de extracción del mucilago de la semilla de chía (Salvia hispánica L) mediante diseño de experimentos y su aplicación como material de pared en encapsulación. Escuela Nacional de Ciencias Biológicas. Instituto Politécnico Nacional. Ciudad de México. México
- Nesterenko, A., Alric, I., Silvestre, F., & Durrieu, V. (2013). Vegetable proteins in microencapsulation: A review of recent interventions and their effectiveness. Industrial Crops and Products, 42(1), 469–479. https://doi.org/10.1016/j.indcrop.2012.06.035
- Neubauer, M. P., Poehlmann, M., & Fery, A. (2014). Microcapsule mechanics: From stability to function. Advances in Colloid and Interface Science, 207, 65–80. https://doi.org/10.1016/j.cis.2013.11.016
- Nikoo, A. M., Kadkhodaee, R., Ghorani, B., Razzaq, H., & Tucker, N. (2018). Electrospray-assisted encapsulation of caffeine in alginate microhydrogels. International Journal of Biological Macromolecules, 116, 208–216. https://doi.org/10.1016/j.ijbiomac.2018.04.167
- Niu, B., Shao, P., Luo, Y., & Sun, P. (2020). Recent advances of electrosprayed particles as encapsulation systems of bioactives for food application. Food Hydrocolloids, 99, 105376. https://doi.org/10.1016/j.foodhyd.2019.105376
- Ogrodowska, D., Tańska, M., Brandt, W., & Czaplicki, S. (2019). The influence of emulsion drying on the fatty acid composition, bioactive compounds content and oxidative stability of encapsulated bio-oils. CyTA - Journal of Food, 17(1), 949–959. https://doi.org/10.1080/19476337.2019.1676316
- Ozilgen, S., & Bucak, S. (2018). Functional Biopolymers in. In F. Manufacturing, A. M. Grumezescu, & A. M. Holban, (Eds..), Biopolymers for food design (pp. pp. 157–189). https://doi.org/10.1016/b978-0-12-811449-0.00006-2
- Partovinia, A., & Vatankhah, E. (2019). Experimental investigation into size and sphericity of alginate micro-beads produced by electrospraying technique: Operational condition optimization. Carbohydrate Polymers, 209, 389–399. https://doi.org/10.1016J.carpol.2019.01.019
- Pedroza-Islas, R. (2002). Alimentos Microencapsulados: Particularidades de los Procesos para la Microencapsulación de Alimentos para Larvas de Especies Acuícolas. Avances En Nutrición Acuicola VI. Memorias Del VI Simposium Internacional de Nutrición Acuicola, 438–447. https://doi.org/10.3305/nh.2014.29.6.7047
- Pérez-Masiá, R., López-Nicolás, R., Periago, M. J., Ros, G., Lagaron, J. M., & López-Rubio, A. (2015). Encapsulation of folic acid in food hydrocolloids through nanospray drying and electrospraying for nutraceutical applications. Food Chemistry, 168, 124–133. https://doi.org/10.1016/J.FOODCHEM.2014.07.051
- Poletto, G., Raddatz, G. C., Cichoski, A. J., Zepka, L. Q., Lopes, E. J., Barin, J. S., Wagner., R., & de Menezes, C. R. (2019). Study of viability and storage stability of Lactobacillus acidophillus when encapsulated with the prebiotics rice bran, inulin and Hi-maize. Food Hydrocolloids, 95, 238–244. https://doi.org/10.1016/j.foodhyd.2019.04.049
- RED SERVICES. (2020). Limitless consulting support from concept to market. Inovenso. Accessed 14 April 2020 https://www.inovenso.com/rd-service/
- Rosell-Llompart, J., Grifoll, J., & Loscertales, I. G. (2018). Electrosprays in the cone-jet mode: From Taylor cone formation to spray development. Journal of Aerosol Science, 125, 2–31. https://doi.org/10.1016/j.jaerosci.2018.04.008
- Sadeghi-Varkani, A., Emam-Djomeh, Z., & Askari, G. (2018). Physicochemical and microstructural properties of a novel edible film synthesized from Balangu seed mucilage. International Journal of Biological Macromolecules, 108, 1110–1119. https://doi.org/10.1016/j.ijbiomac.2017.11.029
- Salgado-Cruz, M. D. L. P., Calderón-Domínguez, G., Chanona-Pérez, J., Farrera-Rebollo, R. R., Méndez-Méndez, J. V., & Díaz-Ramírez, M. (2013). Chia (Salvia hispanica L.) seed mucilage release characterisation. A microstructural and image analysis study. Industrial Crops and Products, 51, 453–462. https://doi.org/10.1016/j.indcrop.2013.09.036
- Salgado-Cruz, M. D. L. P., Ramírez-Miranda, M., Díaz-Ramírez, M., Alamilla-Beltran, L., & Calderón-Domínguez, G. (2017). Microstructural characterisation and glycemic index evaluation of pita bread enriched with chia mucilage. Food Hydrocolloids, 69, 141–149. https://doi.org/10.1016/j.foodhyd.2017.01.027
- Sari, R. S., de Almeida, A. C., Cangussu, A. S. R., Jorge, E. V., Mozzer, O. D., Santos, H. O., Quintilio, W., Brandi, I. V., Andrade, V. A., Samir, A., & Sobrinho Santos, E. M. (2016). Anti-botulism single-shot vaccine using chitosan for protein encapsulation by simple coacervation. Anaerobe, 42, 182–187. https://doi.org/10.1016/J.ANAEROBE.2016.10.013
- Schuldt, U., Woehlecke, H., & Lerche, D. (2019). Characterization of mechanical parameters of microbeads by means of analytical centrifugation. Food Hydrocolloids, 86, 201–209. https://doi.org/10.1016/j.foodhyd.2018.07.005
- Shafiei Dastgerdi, A., Peterman, R. J., Riding, K., & Beck, B. T. (2019). Effect of concrete mixture components, proportioning, and compressive strength on fracture parameters. Construction and Building Materials, 206, 179–192. https://doi.org/10.1016/j.conbuildmat.2019.02.025
- Shao, Y., Wu, C., Wu, T., Yuan, C., Chen, S., Ding, T., Ye, X., & Hu, Y. (2018). Green synthesis of sodium alginate-silver nanoparticles and their antibacterial activity. International Journal of Biological Macromolecules, 111, 1281–1292. https://doi.org/10.1016/j.ijbiomac.2018.01.012
- Soleimanifar, M., Jafari, S. M., & Assadpour, E. (2019). Encapsulation of olive leaf phenolics within electrosprayed whey protein nanoparticles; production and characterization. Food Hydrocolloids, 101, 105572. https://doi.org/10.1016/j.foodhyd.2019.105572
- Songsurang, K., Praphairaksit, N., Siraleartmukul, K., & Muangsin, N. (2011). Electrospray fabrication of doxorubicin-chitosan-tripolyphosphate nanoparticles for delivery of doxorubicin. Archives of Pharmacal Research, 34(4), 583–592. https://doi.org/10.1007/s12272-011-0408-5
- Strand, B. L., Gåserød, O., Kulseng, B., Espevik, T., & Skjåk-Bræk, G. (2002). Alginate-polylysine-alginate microcapsules: Effect of size reduction on capsule properties. Journal of Microencapsulation, 19(5), 615–630. https://doi.org/10.1080/02652040210144243
- Sun, F. W., Li, H., & Liew, K. M. (2010). Compressive mechanical properties of carbon nanotubes encapsulating helical copper nanowires. Carbon, 48(5), 1586–1591. https://doi.org/10.1016/j.carbon.2009.12.056
- Tapia-Hernández, J. A., Torres-Chávez, P. I., Ramírez-Wong, B., Rascón-Chu, A., Plascencia-Jatomea, M., Barreras-Urbina, C. G., & Rodríguez-Félix, F. (2015). Micro- and nanoparticles by electrospray: advances and applications in foods. Journal of Agricultural and Food Chemistry, 63(19), 4699–4707. https://doi.org/10.1021/acs.jafc.5b01403
- Tekieh, T., Sasanpour, P., & Rafii-Tabar, H. (2016). Effects of electromagnetic field exposure on conduction and concentration of voltage gated calcium channels: A Brownian dynamics study. Brain Research, 1646, 560–569. https://doi.org/10.1016/j.brainres.2016.06.034
- Velázquez-Gutiérrez, S. K., Figueira, A. C., Rodríguez-Huezo, M. E., Román-Guerrero, A., Carrillo-Navas, H., & Pérez-Alonso, C. (2015). Sorption isotherms, thermodynamic properties and glass transition temperature of mucilage extracted from chia seeds (Salvia hispanica L). Carbohydrate Polymers, 121, 411–419. https://doi.org/10.1016/j.carbpol.2014.11.068
- Wang, J., Helder, L., Shao, J., Jansen, J. A., Yang, M., & Yang, F. (2019). Encapsulation and release of Doxycycline from electrospray-generated PLGA microspheres: Effect of polymer end groups. International Journal of Pharmaceutics, 564, 1–9. https://doi.org/10.1016/j.ijpharm.2019.04.023
- Xu, M., Zhang, J., Li, Q., & Lu, S. (2018). The influence of liquid pool temperature on the critical impact Weber number for surface bubble formation. International Journal of Heat and Mass Transfer, 127, 677–682. https://doi.org/10.1016/j.ijheatmasstransfer.2018.08.085
- Yazdekhasti, A., Pishevar, A., & Valipouri, A. (2019). Investigating the effect of electrical conductivity on electrospray modes. Experimental Thermal and Fluid Science, 100, 328–336. https://doi.org/10.1016/j.expthermflusci.2018.09.012
- Young, C. J., Poole-Warren, L. A., & Martens, P. J. (2012). Combining submerged electrospray and UV photopolymerization for production of synthetic hydrogel microspheres for cell encapsulation. Biotechnology and Bioengineering, 109(6), 1561–1570. https://doi.org/10.1002/bit.24430
- Zhao, M., Qu, F., Wu, Z., Nishinari, K., Phillips, G. O., & Fang, Y. (2017). Protection mechanism of alginate microcapsules with different mechanical strength for Lactobacillus plantarum ST-III. Food Hydrocolloids, 66, 396–402. https://doi.org/10.1016/j.foodhyd.2016.12.013
- Ziemichód, A., Wójcik, M., & Różyło, R. (2019). Ocimum tenuiflorum seeds and Salvia hispanica seeds: Mineral and amino acid composition, physical properties, and use in gluten-free bread. CyTA - Journal of Food, 17(1), 804–813. https://doi.org/10.1080/19476337.2019.1658645