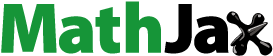
Abstract
We report two typical morphologies (elongated- and blocky-shaped) of the Laves phase in tempered martensite ferritic steels during creep process, originating from the two independent formation paths, i.e. along grain boundaries (GBs) and neighboring M23C6. This is attributed to the multi-element segregation (Cr, Mn, Si and W) at GBs and adjacent M23C6 that serves as suppliers of Laves phase formers. Furthermore, the subsequent different growth mechanisms play crucial roles in the two typical morphologies. Our findings improve the understanding of Laves phase heterogeneous precipitation and provide new insights for the innovation of novel heat-resistant steels with superior creep strength.
1. Introduction
Ultra-supercritical (USC) power plants with improved steam temperatures are urgently desirable for enhancing the thermal efficiencies and reducing CO2 emissions [Citation1–3]. Of particular interest, 9–12 wt.% Cr tempered martensite ferritic steels (TMFSs) are attractive for use in the crucial structural components due to their excellent creep strength and oxidation resistance [Citation4–9]. However, after long-term service at high temperatures, these steels are susceptible to form coarse intermetallic compound Laves phase such as Fe2Mo, Fe2W, and (Fe,Cr)2(Mo,W), resulting from the high concentrations of Mo and W [Citation10–12]. Normally, the Laves phase precipitation consumes a large amount of Mo and W in the ferrite matrix, which reduces the solid solution strengthening and deteriorates the creep strength [Citation13,Citation14]. It has been demonstrated that the hexagonal close-packed (HCP) Laves phase is structurally dissimilar to the ferrite matrix, leading to the inhomogeneous distribution at grain boundaries (GBs) due to a loss of coherency [Citation15, Citation16]. Meanwhile, the high migration rate of the incoherent interfaces also yields the rapid coarsening of the Laves phase, which makes these steels prone to the catastrophic failures upon load-bearing applications [Citation17–19]. Thereby, in the past few decades, numerous researchers have attempted to unveil the creep-induced precipitation mechanism of the Laves phase in TMFSs [Citation11, Citation20–23]. However, due to the absence of in-situ creep experiments and multiscale characterization techniques, the precipitation mechanism of Laves phase remains not clearly understood, thus seriously hindering their structural applications.
In this work, the precipitation behaviors of Laves phase in TMFSs are systematically investigated by using interrupted creep experiments in conjunction with advanced characterizations. More specifically, two typical morphologies (i.e. elongated- and blocky-like) resulting from two independent precipitation routes are captured for the Laves phases. Both GBs and M23C6 are considered to play an essential role in the nucleation and growth of Laves phase. The obtained results may provide a new avenue for the innovation of TMFSs with enhanced creep resistance.
2. Experimental procedure
Here we selected the 9Cr-3W-3Co steels as our experiment materials, whose chemical composition is 0.08, 8.8 Cr, 3.0 Co, 2.8 W, 1.0 Cu, 0.5 Mn, 0.3 Si, 0.2 V, 0.06 Nb, 0.008 N, 0.014 B and balanced by Fe (wt. %). The as-received steel was austenitized at 1373 K for 1 h followed by air cooling, and then tempered at 1033 K for 3 h. Subsequently, a series of interrupted creep tests with different durations (i.e. 100, 302, 1045 h, 2000h, 2945, and 4132 h) were performed at 923 K and 140 MPa using a creep machine (RDJ) with a lever arm ratio of 50:1 [Citation24]. The tested temperature along the gauge length was controlled to within ±2.0 °C. The creep-deformed microstructures were captured by using scanning electron microscopy (SEM, Gemini 450), transmission Kikuchi diffraction (TKD), and transmission electron microscopy (TEM, Tecnai G2 F30 and JEOL-2100F) equipped with an energy dispersive spectrometer (EDS). The TKD mapping was acquired employing a Gemini 450 SEM equipped with a Symmetry camera and Aztec (Oxford Instruments) software at a current of 15 nA and an accelerating voltage of 30 kV. As shown in Supplementary Figure S1, the 9Cr-3Co-3W steel demonstrates a typical tempered martensitic microstructure together with high-density dislocations and nanoscale precipitates like M23C6 and MX.
3. Results
To start with, we carefully characterized the microstructural evolution of the 9Cr-3Co-3W steel during creep process with different durations. We observed the Laves phase precipitation with two different morphologies, consistent with the reports of Cui et al. [Citation11] and Isik et al. [Citation23]. Our experimental observations present that such two different morphologies are primarily attributed to the two independent paths of Laves phase precipitation (Figure ). One is the elongated-shaped Laves phase formed by isolated nucleation and coalescence at the GBs (Figure (a–c)). A typical example is shown in Figure (a). The small elongated Laves phases are nucleated in the early creep and then grow along the GBs (Figure (b)) followed by a coalescence with the neighboring particles (Figure (c)). Another path is assisted by the pre-precipitated M23C6, as illustrated in Figure (d–f). Firstly, the small blocky-shaped Laves phases nucleate at the M23C6/ferrite interface (Figure (d)). Afterwards, they grow simultaneously with the neighboring M23C6 (Figure (e–f)), and eventually evolve into the blocky-like morphology. Particularly, we characterized the M23C6-assisted Laves phase precipitation utilizing the high-resolution TEM. The combined SAED and EDS analyses confirm that the Laves phase and M23C6 are coexistent in Supplementary Figure S2, where the particles A and B are identified as Laves phase while the particles C and D are deduced to be M23C6 due to compositional enrichment in Cr and C. The interfaces between these particles are indicated by the red dashed lines. Our high-resolution characterization again proves that the blocky-shaped Laves phase could nucleate and grow adjacent to the M23C6.
Figure 1. Two independent paths and associated morphologies of Laves phase during creep process. (a–c) Elongated-shaped Laves phase formed by the isolated nucleation and coalescence. (d–f) Blocky-shaped Laves phase formed adjacent to the M23C6.
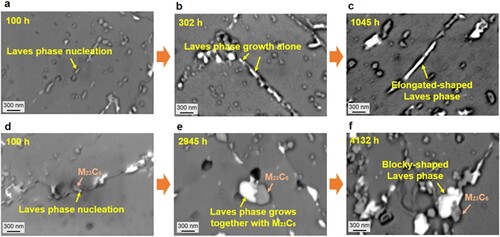
Identifying the crystallographic relationship between Laves phase and neighboring particles is key to understand the mechanism of Laves phase precipitation. Figure shows a TKD mapping of the Laves phase nucleated adjacent to M23C6 during creep for 1045 h, where the M23C6 and Laves phase are indicated by green and blue in Figure (a). The inverse pole figure (IPF) map of the Laves phase and M23C6 is shown in Figure (b), and the color key for orientation is revealed in Figure (c). The pole figures (PFs) of Laves phase, M23C6, and ferrite exhibit that the any two of them obey an orientation relationship (OR), i.e. ()M//()L and [
]M//[
]L, (110)M//(
)F and [
]M//[110]F, (110)F//(0001)L and [
]F//[
]L. The M, L, and F are separately denoted as M23C6, Laves, and ferrite. Furthermore, we also analyzed the crystallographic relationship of the elongated-like Laves phase and neighboring ferrite grains from the TKD data. As shown in Supplementary Figure S3, the enlarged IPF presents the elongated-like Laves phase along ferrite GBs, which exhibits an OR of (
)F//(
)L and [
]F//[
]L with one neighboring ferrite grain and an irrational OR with another one, consistent with the previous report [Citation25]. Moreover, another two new ORs of [
13]F//[1
10]L and (110)F//(10
3)L, [
13]F//[01
0]L and (110)F//(
110)L were determined from independent analysis on the isolated Laves phases, as seen in Supplementary Figures S4 and S5. It therefore suggests that there could be various ORs between the Laves phase and ferrite matrix, which agrees with the previous reports [Citation25–30]. The ORs that have been already reported and those determined from the current study are summarized in Table .
Figure 2. The crystallographic characteristics among Laves phase, M23C6 and ferrite. (a) Phase map showing the M23C6 and Laves phase indicated by green and blue, respectively. (b) IPF map along axis X, where the Laves phase adjacent to the M23C6 is highlighted by the red arrows. (c) Color legends of M23C6, ferrite, and Laves phase. (d) PFs for Laves phase, M23C6, and ferrite showing three types of ORs of ()M//(
)L and [
]M//[
]L, (
)M//(
)F and [
]M//[110]F, (
)F//(0001)L and [
]F//[11
]L.
![Figure 2. The crystallographic characteristics among Laves phase, M23C6 and ferrite. (a) Phase map showing the M23C6 and Laves phase indicated by green and blue, respectively. (b) IPF map along axis X, where the Laves phase adjacent to the M23C6 is highlighted by the red arrows. (c) Color legends of M23C6, ferrite, and Laves phase. (d) PFs for Laves phase, M23C6, and ferrite showing three types of ORs of (110)M//(101¯3)L and [11¯3]M//[21¯1¯1¯]L, (110)M//(11¯1)F and [11¯1]M//[110]F, (110)F//(0001)L and [11¯1]F//[112¯0]L.](/cms/asset/577ffc6d-466f-4385-a8a3-ebe49984e9c3/tmrl_a_2208613_f0002_oc.jpg)
Table 1. Summary of reported ORs between ferrite and Laves phase.
To probe the effect of GB character on Laves phase precipitation, the size evolutions of the Laves phase at different GBs are quantified. For each scenario, about 50 Laves phase particles were measured. The size distributions of the isolated Laves phase and those adjacent to M23C6 at different boundaries with increasing creep time are shown in Supplementary Figure S6. It reveals that the size distribution of the Laves phase is quite inhomogeneous even with a prolonged creep, and the average size of the Laves phase next to M23C6 is generally larger than that of the isolated for each creep condition, suggesting that the site for Laves phase precipitation plays a big role in its growth behavior. Furthermore, regardless of the formation site next to M23C6 and isolated, the fraction of the Laves phase particles located at the high-angle GBs (HAGBs) is higher than those at the low-angle GBs (LAGBs), which implies that HAGBs serve as a preferential nucleation site for Laves phase precipitation. The high-angle GBs (HAGBs) and low-angle GBs (LAGBs) are defined by the misorientation of θ ≥ 15° and 2° < θ < 15° [Citation31]. Generally, HAGBs provide a fast diffusion path for solute atoms, and accordingly accelerate the precipitation kinetics.
4. Discussion
4.1. Heterogeneous nucleation mechanism of Laves phase
The experimental observations (Figures and , Supplementary Figures S2–S5) have demonstrated that creep induces two preferential nucleation sites of Laves phase in TMFSs, i.e. (i) next to M23C6, and (ii) at the GBs. According to the heterogeneous nucleation theory [Citation32, Citation33], two important terms, namely chemical driving force and interfacial energy, are often considered to illustrate the precipitation behaviors of new phase. The chemical driving force is generally related to the chemistry of nucleation site. For the isolated Laves phase, the elemental concentration profiles across the GB before Laves phase nucleation are measured as shown in Figure (a and b). Clearly, various alloying elements like Cr, Mn, Si, and W segregate at the GB. Subsequently, the effects of these alloying elements on Laves phase nucleation are examined in terms of the phase stability by using ThermoCalc software. As shown in Figure (c–e), less W is required for the Laves phase formation when the bulk Si, Cr, and Mn concentrations increase. In other words, the chemical driving force for Laves phase nucleation raises with presence of more alloying elements (e.g. Cr, Mn, and Si) even the W content is maintained. Therefore, the multi-element segregation at the GBs may provide a chemical advantage for the nucleation of the isolated Laves phase.
Figure 3. Multi-element segregation and thermodynamic calculations of the creep-deformed samples. (a) Typical bright-field TEM graph, (b) corresponding elemental composition line scans of the 9Cr-3W-3Co steel at 923 K and 140 MPa for 1045 h, showing the multi-element segregation (i.e. Cr, Mn, Si, and W) takes place at GBs before Laves phase nucleation. The influence of alloying elements on the stability of Laves phase at 923 K: (c) Si, (d) Cr, and (e) Mn. Notably, a line from the upper left to the lower right of the figure separates two fields. The field on the left of the line represents a three-phase region, with ferrite, MX and M23C6, and on the right is a four-phase region, with ferrite, MX, M23C6 and Laves phase.
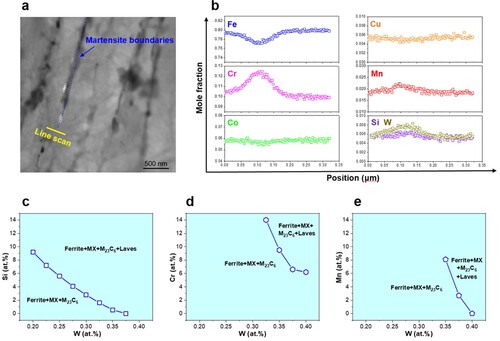
As for the Laves phase next to M23C6, Supplementary Figure S2 has shown that M23C6 are rich in Cr with a small amount of W. These elements act as composition suppliers during the formation of Laves phase and thereby promote the nucleation. Moreover, the M23C6 that are widely distributed along the GBs will accentuate the favorable condition for Laves phase formation, i.e. at these sites both multi-element segregation at the GBs and supplier of Laves phase formers are achieved, which could be responsible for the obtained larger numbers of the Laves phase next to M23C6 when compared with the isolated counterpart (Supplementary Figure S6).
Interfacial energy is another critical factor for the Laves phase nucleation. It should be noted that regardless of the morphologies, those particles are all preferential to precipitate at the GBs because of the reduced nucleation barrier by replacing the original GB area. Here we focus on the change of interfacial energy of Laves phase/M23C6 and ferrite/M23C6. According to the experimentally obtained ORs, the interplanar distances of (1)F, (
)L, and (
)M are determined to be d1-11 = ∼0.1651 nm, d10-13 = ∼0.2168 nm and d110 = ∼0.7524 nm, respectively. The lattice misfit for ferrite and M23C6 is 20.05%, while that for M23C6 and Laves phase is 21.05%. Obviously, the lattice misfit of M23C6 and Laves phase is slightly larger than that of ferrite and M23C6, which suggests that the Laves phase is not prone to nucleate nearby the M23C6. Therefore, crystallographic constrains might not be the main factor for the heterogeneous nucleation of Laves phase. As above discussed, the interface energy from lattice misfit is insufficient to explain the experimental results. Other factors such as chemical contribution to the interfacial energy arising from the composition difference of two phases could also be considered, which requires more theoretical studies such as by first-principles calculations.
Aside from the aforementioned heterogeneous precipitation, it has been reported that the Laves phase can also be formed in the vicinity of Cu-rich phase (CRP) [Citation9, Citation34], To further unravel the role of CRP in Laves phase precipitation for the 9Cr-3W-3Co steel, we analyzed the effect of Cu precipitation on the stability of Laves phase at 650 °C. Both phase map and formation energy result (Supplementary Figure S7) suggest that Cu is energetically unfavorable in the Laves phase. Furthermore, the evolution of Cu content in Laves phase with creep time is measured carefully as seen in Supplementary Figure S8. It reveals that Cu content decreases from 0.16 ± 0.02 at. % to 0.01 ± 0.02 at. % with increasing the creep time from 1045 h to 2945 h, which again proves that Cu destabilizes the Fe2W Laves phase, in consistent with our thermodynamic calculation. Accordingly, we suggest that the chemical driving force for Laves phase nucleation is not a key reason for the Laves phase formation neighboring the CRP. Instead, replacement of the CRP/Fe-matrix interface by the CRP/Laves phase interface with a lower interfacial energy might play a big role, which requires more theoretical basis in the near future.
4.2. Growth kinetics of Laves phase at two formation paths
The growth kinetics of Laves phase can be described by the following equation [Citation35, Citation36]:
(1)
(1) where
is the average volume-equivalent radius at the creep duration t,
is the average radius at the onset of growth, t is the creep duration, k is the constant of growth rate, and n is the temporal exponent. n = 4 and 2 represent that the growth kinetics is governed by the GB diffusion and by the trans-interface diffusion-controlled model (TIDC), respectively [Citation37, Citation38]. To determine the operative growth mechanism for the Laves phase with two morphologies, the linear fit to the data points of r4 vs. t and r2 vs. t during creep process is made, as shown in Figure . Here we only consider the Laves phase particles located at the HAGBs. It indicates that the square law shows a better linear fit (R2 = 0.975) for the Laves phase next to the M23C6, while both the fourth law (R2 = 0.969) and square law (R2 = 0.977) fit very well for the isolated Laves phase. Therefore, the growth of the Laves phase next to the M23C6 is supposed to be controlled by the TIDC mechanism. Though the growth mechanism of the isolated Laves phase remains unclear, it is probably controlled by the GB diffusion mechanism. Because the GB provides a fast diffusion channel of solutes compared with those in the bulk.
4.3. Heterogeneous precipitation-governed two morphologies of Laves phase
Based on our experiments and theoretical analysis, the possible mechanisms of the Laves phase with two morphologies are summarized in Figure . Two independent paths for the Laves phase precipitated adjacent to M23C6 and alone at the GBs are emphasized. At the nucleation stage, both types of Laves phase tend to precipitate at the GBs and intergranular M23C6 because of the chemical advantages (i.e. multi-element segregation and M23C6 serving as suppliers of W and Cr). After finish of nucleation, these precipitates start to grow along the GBs. For the isolated precipitates, the segregated W solutes will feed their growth via GB diffusion and eventually result in an elongated morphology. As for those adjacent to M23C6, the M23C6 could continuously provide W solute and assists the growth of Laves phase by the TIDC mechanism, thereby leading to a blocky shape. It has been recognized that the W atoms can significantly stabilize the M23C6 [Citation39]. Accordingly, the loss of W atoms will also promote the growth of M23C6 in turn.
Figure 5. Schematic of the heterogeneous precipitation mechanisms of Laves phase with two morphologies. Path 1: the isolated Laves phase; Path 2: Laves phase next to the M23C6.
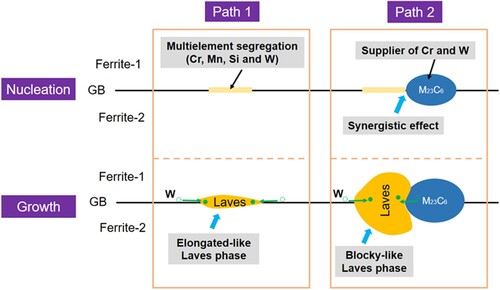
Generally, Laves phase with severe brittleness causes local stress concentration upon creep deformation and thus accelerates the creep failures. In the current study, both morphologies of Laves phase are expected to be detrimental to the creep strength of steels, particularly for those neighboring the M23C6 due to their rapid coarsening rate, leading to the premature occurrence of accelerated creep stage. Since GBs and M23C6 have proven to assist the Laves phase precipitation, a new metallurgy strategy that tailors the GB character (or reduces the fraction of HAGBs) and suppresses the intergranular precipitation of M23C6 is urgently required. Alternatively, the MX carbonitride does not help Laves phase precipitation and shows an excellent thermal stability, which could be a promising strengthening candidate for the improvement of long-term creep strength. To better understand the precipitation mechanism of Laves phase for further alloy design, more efforts on the theoretical calculations for the interfacial energies (particularly from the chemical contributions) and modelling for the Laves phase growth adjacent to M23C6 are needed.
5. Conclusions
Through the interrupted creep tests and multi-aspect characterization techniques, we report two typical morphologies (elongated- and blocky-shaped) of Laves phase in TMFSs, resulting from the two independent precipitation routes (at the GBs and neighboring the M23C6). The multi-element segregation (Cr, Mn, Si, and W) at the GBs and M23C6 as suppliers of Laves phase formers are the key factors for the heterogeneous precipitation of Laves phase. The subsequent growth mechanisms play a key role in the morphology of Laves phase. This work improves the understanding of creep-induced Laves phase precipitation and might provide an efficient design route of novel TMFSs with superior creep strength.
Statement of novelty
We have demonstrated the creep-induced heterogeneous precipitation mechanisms of Laves phase in tempered martensitic ferritic steels through a combination of high-resolution characterization techniques and interrupted creep tests.
Supplemental Material
Download MS Word (3.7 MB)Disclosure statement
No potential conflict of interest was reported by the author(s).
Additional information
Funding
References
- Basirat M, Shrestha T, Potirniche GP, et al. A study of the creep behavior of modified 9Cr-1Mo steel using continuum-damage modeling. Int. J. Plast. 2012;37:95–107.
- Mishnev R, Dudova N, Kaibyshev R. On the origin of the superior long-term creep resistance of a 10% Cr steel. Mater Sci Eng A. 2018;713:161–173.
- Xiao B, Luan JH, Zhao SJ, et al. Achieving thermally stable nanoparticles in chemically complex alloys via controllable sluggish lattice diffusion. Nat. Commun. 2022;13:4870.
- Aghajani A, Somsen C, Eggeler G. On the effect of long-term creep on the microstructure of a 12% chromium tempered martensite ferritic steel. Acta Mater. 2009;57:5093–5106.
- Chatterjee A, Ghosh A, Moitra A, et al. Role of hierarchical martensitic microstructure on localized deformation and fracture of 9Cr-1Mo steel under impact loading at different temperatures. Inter. J. Plast. 2018;104:104–133.
- Oruganti R, Karadge M, Swaminathan S. Damage mechanics-based creep model for 9-10%Cr ferritic steels. Acta Mater. 2011;59:2145–2155.
- Wu DL, Xuan FZ, Guo SJ, et al. Uniaxial mean stress relaxation of 9-12% Cr steel at high temperature: Experiments and viscoplastic constitutive modeling. Int. J. Plast. 2016;77:156–173.
- Zhao JF, Gong JD, Saboo A, et al. Dislocation-based modeling of long-term creep behaviors of Grade 91 steels. Acta Mater. 2018;149:19–28.
- Xiao B, Xu LY, Cayron C, et al. Solute-dislocation interactions and creep-enhanced Cu precipitation in a novel ferritic-martensitic steel. Acta Mater. 2020;195:199–208.
- Kipelova A, Kaibyshev R, Belyakov A, et al. Microstructure evolution in a 3%Co modified P911 heat resistant steel under tempering and creep conditions. Mater Sci Eng A. 2011;528:1280–1286.
- Cui HR, Sun F, Chen K, et al. Precipitation behavior of Laves phase in 10%Cr steel X12CrMoWVNbN10-1-1 during short-term creep exposure. Mater Sci Eng A. 2010;527:7505–7509.
- Zhu S, Yang M, Song XL, et al. Characterisation of Laves phase precipitation and its correlation to creep rupture strength of ferritic steels. Mater. Charact. 2014;98:60–65.
- Maddi L, Deshmukh GS, Ballal AR, et al. Effect of Laves phase on the creep rupture properties of P92 steel. Mater Sci Eng A. 2016;668:215–223.
- Saini N, Mulik RS, Mahapatra MM. Study on the effect of ageing on Laves phase evolution and their effect on mechanical properties of P92 steel. Mater Sci Eng A. 2018;716:179–188.
- Dimmler G, Weinert P, Kozeschnik E, et al. Quantification of the Laves phase in advanced 9-12% Cr steels using a standard SEM. Mater. Charact. 2003;51:341–352.
- Jang TJ, Choi WS, Kim DW, et al. Shear band-driven precipitate dispersion for ultrastrong ductile medium-entropy alloys. Nat. Commun. 2021;12:4703.
- Miyahara K, Hwang JH, Shimoide Y. Aging phenomena before the precipitation of the bulky Laves phase in Fe-10%Cr ferritic alloys. Scripta Mater. 1995;32:1917–1921.
- Prat O, Garcia J, Rojas D, et al. The role of Laves phase on microstructure evolution and creep strength of novel 9%Cr heat resistant steels. Intermetallics. 2013;32:362–372.
- Zhang XZ, Wu XJ, Liu R, et al. Influence of Laves phase on creep strength of modified 9Cr-1Mo steel. Mater Sci Eng A. 2017;706:279–286.
- Xu YT, Nie YH, Wang MJ, et al. The effect of microstructure evolution on the mechanical properties of martensite ferritic steel during long-term aging. Acta Mater. 2017;131:110–122.
- Tsuchida Y, Okamoto K, Tokunaga Y. Improvement of creep rupture strength of high Cr ferritic steel by addition of W. ISIJ Inter. 1995;35:317–323.
- Zhang KQ. Therodynamic and kinetic calculation and optimization of precipitates in martensitic heat-resistant stainless steel. Liao Ning: University of Science and Technology Liaoning. 2018.
- Isik MI, Kostka A, Eggeler G. On the nucleation of Laves phase particles during high-temperature exposure and creep of tempered martensite ferritic steels. Acta Mater. 2014;81:230–240.
- Xiao B, Xu LY, Tang ZX, et al. A physical-based yield strength model for the microstructural degradation of G115 steel during long-term creep. Mater Sci Eng A. 2019;747:161–176.
- Fedorova I, Belyakov A, Kozlov P, et al. Laves-phase precipitates in a low-carbon 9% Cr martensitic steel during aging and creep at 923 K. Mater Sci Eng A. 2014;615:153–163.
- Abe F, Araki H, Noda T. The effect of tungsten on dislocation recovery and precipitation behavior of low-activation martensitic 9Cr steels. Metall Trans A 1991;22:2225–2235.
- Chai YW, Kato K, Yabu C, et al. Disconnections and Laves (C14) precipitation in high-Cr ferritic stainless steels. Acta Mater. 2020;198:230–241.
- Li Q. Precipitation of Fe2W Laves phase and modeling of its direct influence on the strength of a 12Cr-2W steel. Metall Mater Trans A 2006;37:89–97.
- Sawatani T, Minamino S, Morikawa H. Effect of Laves phase on the properties of Ti and Nb stabilized low C, N-19%Cr-2%Mo stainless steel sheets. Trans. ISIJ. 1982;22:172–180.
- Yamamoto K, Kimura Y, Mishima Y. Effect of matrix substructures on precipitation of the Laves phase in Fe-Cr-Nb-Ni system. ISIJ Inter. 2003;43:1253–1259.
- Zhang JY, Xu LY, Han YD, et al. New perspectives on the grain boundary misorientation angle dependent intergranular corrosion of polycrystalline nickel-based 625 alloy. Corros. Sci. 2020;172:108718.
- Takahashi J, Kawakami K, Kawasaki K. Study on complex precipitation kinetics in Cr- and Cu-added nitriding steels by atom probe tomography. Acta Mater. 2019;169:88–98.
- Shen C, Simmons JP, Wang Y. Effect of elastic interaction on nucleation: I. Calculation of the strain energy of nucleus formation in an elastically anisotropic crystal of arbitrary microstructure. Acta Mater. 2006;54:5617–5630.
- Ku BS, Yu J. Effects of Cu addition on the creep rupture properties of a 12% Cr steel. Scr. Mater. 2001;45:205–211.
- Lifshitz IM, Slyozov VV. The kinetics of precipitation from supersaturated solid solutions. J Phys Chem Solids. 1961;19:35–50.
- Xu SS, Liu YW, Zhang Y, et al. Precipitation kinetics and mechanical properties of nanostructured steels with Mo additions. Mater. Res. Let. 2020;8:187–194.
- Ardell AJ. Trans-interface-diffusion-controlled coarsening in ternary alloys. Acta Mater. 2013;61:7749–7754.
- Zhao YL, Yang T, Han B, et al. Exceptional nanostructure stability and its origins in the CoCrNi-based precipitation-strengthened medium-entropy alloy. Mater. Res. Let. 2019;7:152–158.
- Maruyama K, Sawada K, Koike J. Advances in physical metallurgy and processing of steels. strengthening mechanisms of creep resistant tempered martensitic steel.. ISIJ Inter. 2001;41:641–653.