Figures & data
Figure 1. (a) is the prototype of the meal-assisting robot, (b) is the 3D CAD test bench model of the meal-assisting robot.
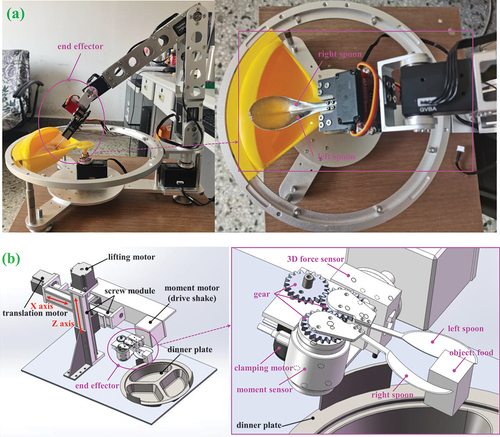
Figure 2. Finite element model of friction coefficient measurement by induced slippage method: (a1) clamp the cube-shaped food, (a2) the contact surface of the initial state of the cube, (a3) the contact surface of the end state of the cube, (b1) clamp the ellipsoid-shaped food, (b2) the contact surface of the initial state of the ellipsoid, (b3) the contact surface of the end state of the ellipsoid, (c1) clamp the sphere-shaped food, (c2) the contact surface of the initial state of the sphere, (c3) the contact surface of the end state of the sphere.
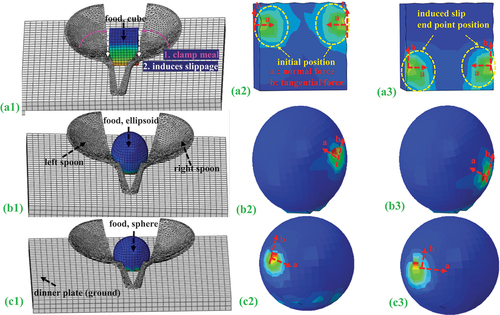
Table 1. Finite element analysis of structural dimensions and grid element attributes.
Figure 3. Food model and moment curve of food fetching process: (a) diagram of clamping process and food model, (b) moment curve during food fetching process.
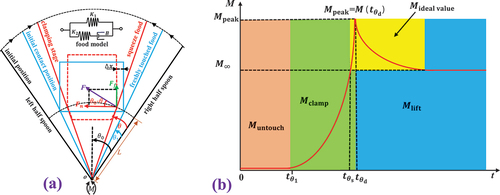
Figure 4. Results of relative friction coefficients between the FEM computational values and the true values obtained by the induced slippage method: (a) true value 0.1, (b) true value 0.2, (c) true value 0.3, (d) true value 0.5.
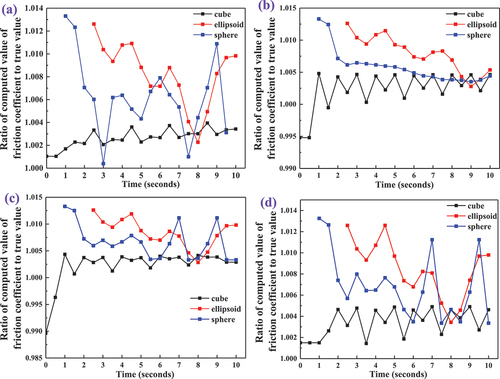
Figure 5. Fitting results using the macroscopic moment to characterize food viscoelasticity when fetching food at different velocities: (a) clamping angular velocity 0.01 rad/s, lifting velocity 4 mm/s; (b) clamping angular velocity 0.02 rad/s, lifting velocity 4 mm/s; (c) clamping angular velocity 0.03 rad/s, lifting velocity 4 mm/s; (d) clamping angular velocity 0.04 rad/s, lifting velocity 4 mm/s.
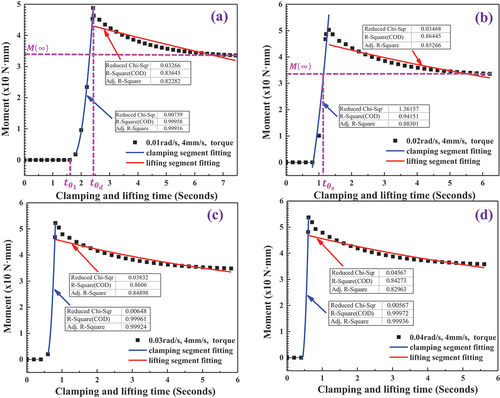
Figure 6. Results of viscoelastic parameters: (a) computational values of viscoelastic model parameters, (b) computational and true values of finite element viscoelastic parameters.
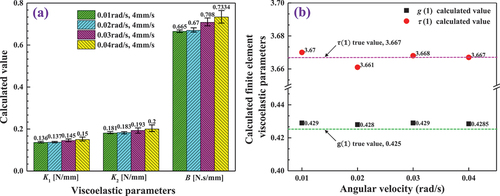
Figure 7. Results of fetching block foods: (a1) – (a4) the distribution of single-row block foods and the results of fetching, (b1) – (b4) the distribution of multi-row block foods and the results of fetching.
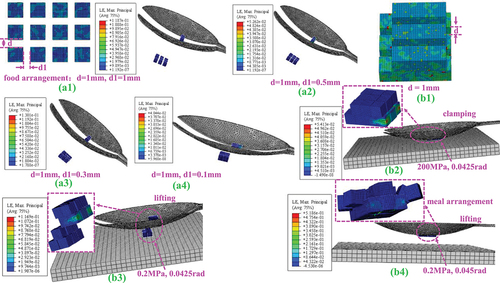
Figure 8. Results of fetching diced mixed foods: (a) the diced mixed foods close to the distribution, (b1) initial clamping state, (b2) initial lifting state, (c1) final clamping state, (c2) final lifting state, (d1) final clamping state, (d2) final lifting state, (e1) final clamping state, (e2) final lifting state.
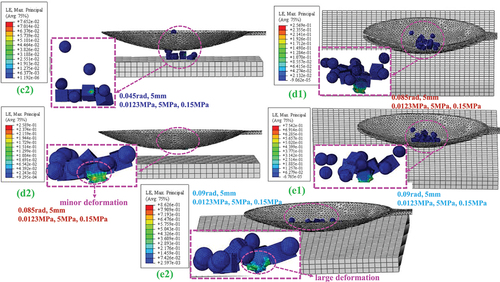
Figure 9. Results of the force and moment at different velocities: (a1) the force and moment of the left spoon when fetching block foods with a predetermined angular displacement of 0.045 rad, (a2) the force and moment of the right spoon when fetching block foods with a predetermined angular displacement of 0.045 rad, (b1) the force and moment of the left spoon when fetching diced mixed foods with a predetermined angular displacement of 0.085 rad, (b2) the force and moment of the right spoon when fetching diced mixed foods with a predetermined angular displacement of 0.085 rad.
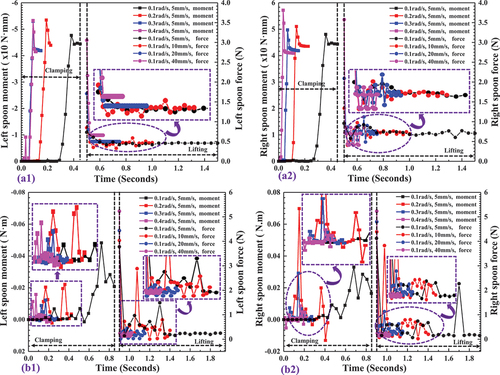
Data availability statement
The original contributions presented in the study are included in the article/supplementary material, further inquiries can be directed to the corresponding author.