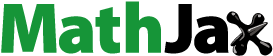
ABSTRACT
The operation object of the meal-assisting robot is a non-rigid food individual with complex and differentiated physical characteristics, and the contact force between the spoon and the food is very complicated, which brings difficulties to the fetching of the food and has a large impact on the fetching rate and force of the foods. In this paper, the finite element simulation of the display algorithm is used to reproduce the scenario of the meal-assisting robot fetching food and verify the measurement method of viscoelasticity and friction coefficient of solid foods. A standard linear solid model in Maxwell form is characterized using moment relaxation and the model parameters are estimated. The tangential and normal forces obtained by the induced slippage method are used to estimate the friction coefficient of the contact surface of the food and the spoon. Simulation results show that the viscoelastic properties of solid foods can be characterized by moment relaxation, the parameters of the model can be estimated, and the friction coefficient can be measured by the induced slippage method. Finally, the effects of food traits and predetermined angular displacement on food fetching rates were verified by fetching a mixture of block and diced foods, and comparing the effects of different velocities on the moments and forces of action.
Introuction
Food is fundamental to human survival and is an important member of providing the body with nutrition, energy, and resistance. However, in recent years, the number of patients with physical dysfunction caused by stroke and its sequelae, spinal cord injury, cerebral lesions, nerve injury, and muscular atrophy lesions has been increasing year by year. To free the physical strength and energy of health care workers and their families for patients with physical dysfunction, more and more countries have started to develop devices that can assist patients with physical dysfunction in eating and drinking, therefore the research of meal-assisting robots technology has been rapidly developed. Although most of these early meal-assisting robots have advanced to the market,[Citation1–5] their end-effectors are not very intelligent. With the development of electronics and computer vision, there are many end-effectors with intelligence, that have been developed one after another .[Citation6–9] However, the end-effectors of these robots only use a spoon or a pair of chopsticks to fetch foods, which leads to a great limitation in the types of foods that can be fetched, for example, it is difficult to fetch a large block of foods with a spoon end-effector or sticky foods with a pair of chopsticks end-effector. Therefore, to meet the need to fetch as many foods as possible, a combined spoon and chopstick meal-assisting robot needs to be developed.[Citation10–12]
Although the combined spoon and chopsticks type meal-assisting robot is capable of fetching a variety of foods, it is a challenging technical challenge to reasonably improve the fetching rate of the end-effector. During food fetching, the mechanical properties of the food need to be further considered to prevent large plastic deformation of the foods, or to prevent the food from being broken when fetching a larger volume of solid foods, to obtain a higher fetching rate. Hamazawa[Citation13] classified food properties into four categories: physical and physicochemical properties, kinetic properties, sensory properties, and health properties. Mechanical properties of food belong to the first category, and further mechanical properties can be divided into rheological properties, surface properties, morphological properties, mass-volume-area properties, and acoustic properties.
Foods viscoelasticity is an important member of food rheological properties and has a wide range of applications. Congcong et al.[Citation14] studied the effect of freezing temperature on the viscoelasticity of carrots. Singh et al.[Citation15] used broadband viscoelastic spectroscopy (BVS) to describe the linear viscoelasticity of mozzarella, fudge, and cooked ham. Sritham et al.[Citation16] used broadband viscoelastic spectroscopy to characterize the rheological behavior of solid foods. Boisly et al.[Citation17] used a finite element model to simulate the nonlinear viscoelasticity of cutting foods. Krokida et al.[Citation18] studied the linear viscoelasticity of dehydrated carrots and potatoes using compression experiments. Fakhreddin et al.[Citation19] used the Peleg-Normand model and the quaternary Maxwell model to study the stress relaxation behavior of the warm melon sponge cake. The difference between linear and nonlinear models is that the linear model applies to the small strain domain and the nonlinear model applies to the large strain domain.
On the other hand, frictional properties of solid food surfaces have been developed in recent years and have been intensively studied not only in the food field but in the engineering field. Fuhrmann et al.[Citation20] studied the friction between oral PDMS surfaces with gelatin and sausage using a Tribolab mechanical tester. Joyner et al.[Citation21] proposed a two-ball tribological system to evaluate the frictional behavior of acidic emulsion gels with and without added saliva. Prinz et al.[Citation22] studied the frictional conditions of two mucosal surfaces using a device consisting of a rotating axis and a crossbar of measuring elements. Wragge-Morley et al.[Citation23] used a novel pendulum decay test method to measure friction coefficients in a study of the transmission efficiency of pendulum rigs. Kokorian et al.[Citation24] used a microelectromechanical system tribometer to demonstrate a new method for analyzing and visualizing friction measurements in mesoscale viscous slip motion. However, most of these methods for measuring friction are with the help of specialized friction testing instruments, which may lead to some deviation from the friction coefficient in real engineering applications. This paper will introduce a method to measure the coefficient of friction on the food surface during the actual fetching of food, and will analyze the accuracy and deviation of the measurement method by finite elements.
With the development of automation and robotics, more and more researchers are studying strategies to deal with food properties. Pettersson et al.[Citation25] proposed a force gripper applied to vegetables and fruits, an apparatus that measures gripping and lifting forces. Xu and Chen[Citation26] used a fractional-order derivative model to study the creep behavior of cantaloupe linear creep behavior of viscoelasticity. Jinghu et al.[Citation27] studied the semi-solid viscoelasticity of agar gel under compressive mastication using the Ogden model. Mahiuddin et al.[Citation28] studied eight fruits and vegetables, and they used the Caputo fractional order model and the Maxwell model to perform compression experiments and stress relaxation experiments, respectively, to establish the relationship between viscoelastic properties and porosity. Gyeong-Won et al.[Citation29] performed finite element optimization studies of compression rupture and stress relaxation on agar gels using two parallel Maxwell models. Michal et al.[Citation30] used the Perzyna model and conducted a finite element simulation study of the nonlinear viscoelasticity of Jatropha curcas seeds under compressive loading. Hui et al.[Citation31] used finite element simulation to simulate a Maxwell composite model with five parameters as a constitutive model for characterizing small deformation nonlinear viscoelasticity of food materials. Sakamoto et al.[Citation32,Citation33] proposed an optimal design method to deal with Japanese food Norimaki, using the Maxwell model and Burgers model as a viscoelastic model for food materials. Zhongkui et al.[Citation34] studied the measurement of viscoelasticity of four tempura based on the Maxwell standard linear solid model containing three parameters from the perspective of macroscopic forces and linear displacements. They used a device with two mutually parallel fingers used to clamp food to obtain force relaxation data. These methods improve the optimal combination of manipulator stiffness and operating velocity and ensure minimal plastic deformation of the food material, which is essential to maintain the quality of the food product.
The purpose of this paper is to establish a method applicable to measuring the viscoelasticity and friction coefficient of food material from the perspective of a meal-assisting robot fetching solid foods. When fetching foods using an end-effector, it is desired to apply the smallest possible clamping moment to minimize damage to the food target or to prevent the food from being clamped off. On the other hand, maintain a suitable clamping moment during food lifting to prevent relative slippage between the food and the two half-spoon contact surfaces, or to prevent food from falling out. Based on the weight and lifting acceleration of the target food, the required clamping moment during the fetching process is planned. In this paper, we will verify the accuracy of using the moment relaxation method to characterize the food viscoelasticity model by simulating a practical scenario reflecting a combined spoon and chopstick type meal-assisting robots during the fetching of solid foods, and verify the accuracy of the estimation of model parameter method and the estimation of friction coefficient method. Finally, the effects of food traits and predetermined angular displacements on the fetching rate of foods will be investigated by simulating the fetching process of block foods and diced mixed foods. The variation of the force on multiple block foods and diced mixed foods with different velocities during the fetching process will be investigated. The proposed viscoelastic model and friction coefficient measurement method can be applied in Europe and the world in the field of automation for clamping and lifting food products in the food industry, such as fetching fruits, vegetables, and meat products with viscoelastic characteristics.[Citation35–37] In addition, path planning algorithms (such as ant colony algorithm, genetic algorithm, and neural network algorithm) can be combined to improve the food fetching rate as the starting point for a more novel path planning method for a four-degree-of-freedom or six-degree-of-freedom meal-assisting robot to fetch food reasonably.
Methods and modeling
Working principle of meal-assisting robots test bench
(a) is the meal-assisting robot prototype. To study the food properties and the estimation of food model parameters, a meal-assisting robot test bench was designed with the mechanical structure shown in ). The device is composed of X, Y, and Z three-dimensional servo modules and end-effectors. The end-effector is composed of a left spoon, a right spoon, a clamping motor, a 3D force sensor, a moment sensor, and a gear. The clamping motor drives the left spoon and the right spoon to realize the food clamping. The moment sensor is used to measure the moment of action of the food on the spoon, and the 3D force sensor is used to measure the force during the food fetching process.
Figure 1. (a) is the prototype of the meal-assisting robot, (b) is the 3D CAD test bench model of the meal-assisting robot.
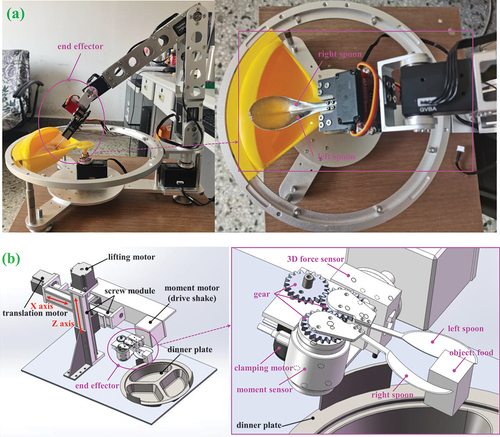
Figure 2. Finite element model of friction coefficient measurement by induced slippage method: (a1) clamp the cube-shaped food, (a2) the contact surface of the initial state of the cube, (a3) the contact surface of the end state of the cube, (b1) clamp the ellipsoid-shaped food, (b2) the contact surface of the initial state of the ellipsoid, (b3) the contact surface of the end state of the ellipsoid, (c1) clamp the sphere-shaped food, (c2) the contact surface of the initial state of the sphere, (c3) the contact surface of the end state of the sphere.
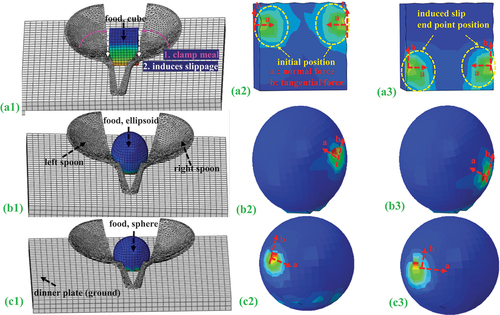
Coefficient of friction measurement methods and modeling
The induced slippage method to measure the friction coefficient follows the following four steps:
The left spoon and right spoon are moved according to a predetermined angular displacement to achieve mutual contact between the two half spoons and both sides of the food, as shown in (a1).
Moving in the direction close to the dinner plate with predetermined linear displacement, relative slippage occurs between the half spoon and the food due to the presence of the dinner plate.
The tangential and normal forces on the contact surface between the half spoon and the food caused by the relative slippage are measured, and the initial and termination positions of the induced slippage are shown in (a2-a3).
The ratio of the obtained tangential force to the normal force was used as the estimated friction coefficient of the contact surface between the half spoon and the food.
To verify the accuracy of using the induced slippage method to estimate the friction coefficient, a finite element model was constructed using ABAQUS 6.14 as shown in (a1-c1). A cube, ellipsoid, and sphere are used as the geometric models of the solid food, respectively, and the solid food is placed freely on the dinner plate, which is fixedly constrained to limit the degrees of freedom in three directions. The Young’s modulus of the left spoon, the right spoon, and the dinner plate is 19.402 GPa, and the two half spoons and the dinner plate are bound as rigid bodies, respectively. Since most of the foods are soft substances, their Young’s modulus was set to 0.2 MPa, because Young’s modulus of the food set in the finite element can be similar to many soft substance foods, such as gummy bears,[Citation38] cooked Japanese radish and carrot .[Citation39] The structural dimensions and grid element attributes of the geometric model for finite element analysis are set as shown in .
Table 1. Finite element analysis of structural dimensions and grid element attributes.
The contact between the half spoon and the food is modeled using the penalty method, and 0.1, 0.2, 0.3, and 0.5 are set as the true values of the friction coefficient between the half spoon and the food in the simulation. The simulations will be performed in three steps as follows:
The period of the first step is 1s, and the gravity and temperature of the food are added in the first analysis step to reproduce the actual scene.
The period of the second step is 10s, and the angular displacement boundary condition is added to make full contact between the two sides of the food and the two half spoons to realize the clamping action. Since it is difficult to realize the control of the moment in the finite element simulation, moment control is not used in this analysis step.
The period of the third step is 10s. A displacement of 5 mm along the direction close to the dinner plate is applied on both sides of the two half spoons to realize the downward sliding of the two half spoons on both surfaces of the food. To save the calculation time and computer memory, the tangential and normal forces of the contact surface of the half spoon and the food in the third analysis step are set in the history field. The positions of the contact surfaces between the cube, ellipsoidal and spherical shapes of the food and the half-spoon for the simulation process are shown in (a2-c3).
Moment relaxation characterizes the viscoelastic model method
The standard linear solids model in Maxwell’s form was used as the base model for viscoelasticity of solid foods, which was chosen because it has fewer parameters and allows for the calculation of model parameters by disposable food fetching. As shown in ), this model describes the viscoelasticity of the food through the Maxwell cell with a spring in parallel, and Zhongkui and Shinichi[Citation40] proposed the control equation for this model as follows:
Figure 3. Food model and moment curve of food fetching process: (a) diagram of clamping process and food model, (b) moment curve during food fetching process.
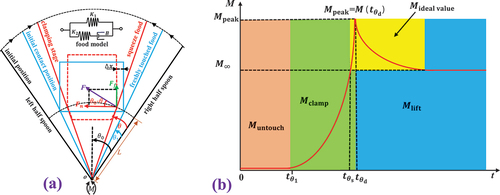
where and
represent displacement and force, respectively,
and
are the elasticity of the food, and
is the viscosity of the food target. The standard solid linear model in Maxwell form described by EquationEquation (1)
(1)
(1) is used to describe the stress relaxation behavior of viscoelastic food from the perspective of macroscopic force and linear displacement. However, in the practical application of meal-assisting robots fetching foods, fetching foods is not only used to fetch food in a parallel moving manner but in a rotational fetching manner. This restricts the way the meal-assisting robots adopt the latter.
In response to the above adoption of Maxwell standard linear solid model described in EquationEquation (1)(1)
(1) , the problem of characterizing food viscoelasticity by rotating fetching foods cannot be satisfied. In this paper, macroscopic moments and angular displacements are used to equivalently replace the macroscopic forces and linear displacements at each moment, and EquationEquation (2)
(2)
(2) and EquationEquation (3)
(3)
(3) represent the macroscopic forces and linear displacements after the equivalent replacement, and EquationEquation (4)
(4)
(4) represents the relationship between macroscopic moments and angular displacements.
where
is the force of equivalent substitution,
is the line displacement of equivalent substitution,
is the spacing between the equivalent cross-section and the rotary axis of the half spoon,
is the angle displacement when the half spoon is closed,
is the angular displacement,
is the derivative of
,
is the angular displacement of the half spoon when it first touches the sides of the food,
is the macroscopic moment, and
is the derivative of
.
) shows the relationship between the food model and the physical quantities in the clamping process, and ) shows the macroscopic moment and time relationship curves when the half spoon fetches the food. In clamping segment, the clamping moment () from the untouched food (the orange region in )) to the two half spoons touching both sides of the food (green region) at the same time, its value is approximately 0 (because the clamping moment in the orange region depends on the moment caused by the real friction between the food and the dinner plate, and the actual scenario friction is smaller, therefore a smaller friction coefficient is set in the simulation) to time
increases rapidly to
. When the clamping ends, the angular displacement of the two half spoons remains unchanged and the moment
(light blue area) during lifting starts to decrease and finally stabilizes at
, and this behavior of moment reduction reflects the stress relaxation of the viscoelastic object. The value of the moment in the yellow region of ) is higher than the stabilizing moment (
), at this point, the angular displacement is less than or equal to
. The clamping moment reaches
when the time of clamping reaches
, therefore the food lifting action can be performed at the moment
instead of waiting for
. This saves time for fetching foods, and for food assistance tasks, it is necessary to fetch and transport foods to the mouth position multiple times, so we do not want to spend more time on the process of fetching foods. To determine the yellow region in ), the viscoelasticity of the food target needs to be known. Assuming that in the time period of
, when clamping with a constant angular velocity
(
), EquationEq. (4)
(4)
(4) becomes:
where
is the predetermined angular displacement, and
is the time required to reach the predetermined angular displacement. At
=
, the initial condition
and solving for EquationEq. (8
(8)
(8) ), get:
where
Similarly, when ,
,
, and solve it in substitution EquationEq. (4
(4)
(4) ), get:
The initial condition, when ,
, solve it in substitution EquationEq. (15)
(15)
(15) and get:
Finally, the target moment can be calculated using EquationEq. (10)(10)
(10) and EquationEq. (16)
(16)
(16) by
,
, and
with known viscoelastic parameters.
Model parameters estimation methods
To estimate the viscoelastic model parameters ,
, and
, the solution is carried out according to the following three steps:
Calculation of parameter
. Assuming that the moment data in ) and the angular displacement
at the end of clamping are known, the equivalent deformation of
corresponds to
. As long as the angular velocity is kept constant during clamping, these viscoelastic parameter values can be easily obtained by the predetermined moment or deformation during the food fetching process. According to the standard solid linear model, since the spring element
and the damping element
are connected in series in the model, the deformation of
will be absorbed by
during the clamping process, therefore the deformation will also disappear after the clamping is completed, and the deformation of the final solid food is only related to the spring element
, which is calculated as:
(2) Calculate the specific value of
. Using
obtained in the first step and fitting the data of the moment relaxation part (yellow area in )) by Equation (16), the specific value of
can finally be determined, therefore that the specific parameter values of the viscoelastic model can be calculated as long as the value of
or
is known.
(3) Calculation of parameters
and
. By substituting
obtained in the first step,
obtained in the second step and the peak moment
into EquationEq. (10
(10)
(10) ),
can be calculated and thus the final determination of
. In this way, the parameters of the model can be determined by the action of disposable food fetching.
Viscoelastic and food fetching modeling
Viscoelasticity and model parameter modeling
To verify the accuracy of describing the solid food viscoelastic model using the moment relaxation method, the display algorithm finite element dynamics was used to simulate the viscoelastic behavior of the solid food in the end-effector simulation fetching the solid food to avoid the spoon from pinching off the food or making the food deformed to a large extent. In addition, Zhongkui and Shinichi[Citation41] suggested that it is difficult to capture both force and plastic deformation using a linear model, so the plastic deformation that eventually remains in the solid food is not considered in the simulation. The simulation will follow the following three steps: The first step adds the food gravity and temperature. The second step sets the predetermined angular displacement (0.0244 rad) in the boundary conditions and clamps the food at constant angular velocities 0.01 rad/s, 0.02 rad/s, 0.03 rad/s, and 0.04 rad/s, respectively, so that the predetermined time
to reach the predetermined angular displacement at each constant angular velocity can be calculated. The predetermined time for the third analysis step is 5s, and the lifting velocity is 4 mm/s.
The relationship between the standard linear solid model parameters ,
, and
in Maxwell form and the Prony series
and
in finite elements is calculated according to Che-Yu .[Citation42] In this paper,
=0.425,
=3.667 are set as the true values of the viscoelastic parameters, which are used to compare the deviations between the parameter values calculated by the viscoelastic model estimation method and the true values. This set of values was chosen as the true values because it can describe more types of solid food viscoelasticity, such as agar gel, and tempura.
Block foods fetching simulation process
To verify the effect of one-way spacing between food and food on the fetching rate, block foods will be divided into two groups for simulation. The first group is a single row of multiple cube foods with the same viscoelastic and same hardness material properties, whose material parameters are kept consistent with those of the viscoelastic simulation. The single row spacing is shown in (a1-a4), the spacing between the food and the food along the clamping direction is 1 mm, and the perpendicular to the clamping direction is set to 1 mm, 0.5 mm, 0.3 mm, and 0.1 mm respectively. The simulation will be performed in three steps, the first step is to add the gravity and temperature of the solid foods, the second step is to clamp the action, and the third step is to lift the action.
The second group was a simulation of multi-row block foods. To verify the effect of multi-row food traits and predetermined angular displacement on the fetching rate, the spacing between foods and foods along the clamp direction is 1 mm, and the spacing perpendicular to the clamp direction is 0.01 mm, as shown in (b1). Young’s modulus is set to 200MPa and 0.2MPa, respectively, because it can be used to characterize harder and softer foods. The finite element boundary condition is set to 0.0425 rad and 0.045 rad as the predetermined angular displacement, respectively.
Simulation process of fetching diced mixed foods
To verify the effects of food properties and predetermined angular displacement on the fetching rate of diced mixed foods, the boundary condition of 0.1 rad/s was set as the fetching velocity during the clamping process and the boundary condition of 5 mm/s was set as the velocity during the lifting process. The Young’s modulus of the food was set to 200 MPa, 40 MPa, 5 MPa, 0.15 MPa, and 0.0123 MPa as the material properties of the food, and the cube, ellipsoid, and sphere were used as the three different hardness of the food respectively, and their combinations are shown in (b1-e2). The clamped predetermined angular displacements were 0.045 rad, 0.085 rad, and 0.09 rad, respectively, with a lifting displacement of 5 mm.
Results and discussion
Friction coefficient
shows the relative friction coefficients between the computational and true values of the friction coefficients between the food and the half-spoon. The computational value is calculated by tangential and normal forces when the two half spoons and the food come into contact with each other and induced slippage. The true value is the coefficient of friction set in contact with each other of the finite elements, and the true value of the friction coefficient is 0.1, 0.2, 0.3, and 0.5, respectively. In , for the same shape of food, although the ratio between the calculated and true values remains close to the same, however, the deviation between the calculated and true values increases as the true value of the friction coefficient increases. When the true value of the friction coefficient increases from 0.1 to 0.5, the maximum deviations between the computational value and the true value are 0.00132, 0.00272, 0.00400, and 0.00665, respectively. However, the maximum rate of variation of the deviation of the finite element calculated values with respect to the true values during the measurements from 0.1, 0.2, 0.3 to 0.5 are 1.32%, 1.36%, 1.33% and 1.33%, respectively. It can be seen that the friction coefficient (computational values) obtained by the induced slippage method does not exceed 0.007 (1.40%) in the maximum deviation from the true value, and the true value at this time is 0.5, which verifies the use of the induced slippage method. The accuracy of estimating the coefficient of friction between the food and the two half spoons is satisfactory.
Figure 4. Results of relative friction coefficients between the FEM computational values and the true values obtained by the induced slippage method: (a) true value 0.1, (b) true value 0.2, (c) true value 0.3, (d) true value 0.5.
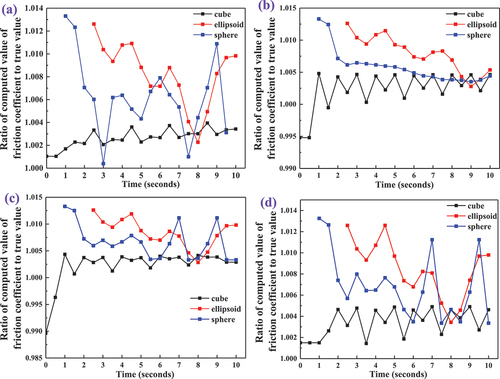
In , we can calculate that the deviation of the calculated value of the friction coefficient from the true value decreases gradually from ellipsoid, sphere to cube. This is because the end-effector uses a predetermined angular displacement to clamp the food when fetching the food under the condition that the food does not undergo large deformation, and the contact area between the two half spoons and different shapes of the food is different. According to Otsuki and Matsukawa and Katano et al.,[Citation43,Citation44] the magnitude of the friction coefficient decreases with the decrease of the contact area or the increase of the loading force. In contrast, the two half spoons can contact with a larger mutual contact area when clamping the ellipsoidal food at a predetermined angular displacement, and the mutual contact area with the two half spoons gradually decreases from ellipsoidal, spherical to cubic-shaped foods, therefore the computational value of the friction coefficient is greater for ellipsoidal shaped foods than for spherical ones, and for spherical ones than for cubic ones.
Viscoelasticity of solid foods
To verify the accuracy of the moment relaxation method adopted in Section 2.3 to characterize the viscoelasticity of the solid food. OriginPro2016 nonlinear custom fitting functions were used to fit the moment and time relationships for the clamping and lifting processes using EquationEquations (10(10)
(10) –Equation16
(16)
(16) ), respectively. Smaller clamping velocities were set in the boundary conditions of the simulation to describe the deviations between the moment data and the fitted curves as accurately as possible.
shows the results of the fitted moment relaxation for the viscoelastic model describing the food. The coefficient of determination of the fitted viscoelastic model () =0.94151) is lower for clamping the food at an angular velocity of 0.02 rad/s in the clamping section and higher for other angular velocities (
=0.99958–0.99972). By fitting the value of the coefficient of determination (
), it was verified that EquationEquation (10)
(10)
(10) can more accurately describe the standard linear solid model in Maxwell form using the moment and time relationship in a rotational clamping manner. In the lifting section, the predetermined angular displacement
of the half spoon is constant, at which time the food is in a tight grip and exhibits moment relaxation. As can be seen from , the viscoelastic model fitting results at angular velocities of 0.02 rad/s and 0.03 rad/s ()) are better (
=0.86445 and
=0.8606), and the fitting results at angular velocities 0.01 rad/s and 0.04 rad/s ()) are poorer relative to ) (
=0.83645 and
=0.84273), however, it is also possible to describe the moment relaxation exhibited by the food during the lifting process, which verifies that the viscoelastic model of the food can be described more accurately using EquationEquation (16)
(16)
(16) .
Figure 5. Fitting results using the macroscopic moment to characterize food viscoelasticity when fetching food at different velocities: (a) clamping angular velocity 0.01 rad/s, lifting velocity 4 mm/s; (b) clamping angular velocity 0.02 rad/s, lifting velocity 4 mm/s; (c) clamping angular velocity 0.03 rad/s, lifting velocity 4 mm/s; (d) clamping angular velocity 0.04 rad/s, lifting velocity 4 mm/s.
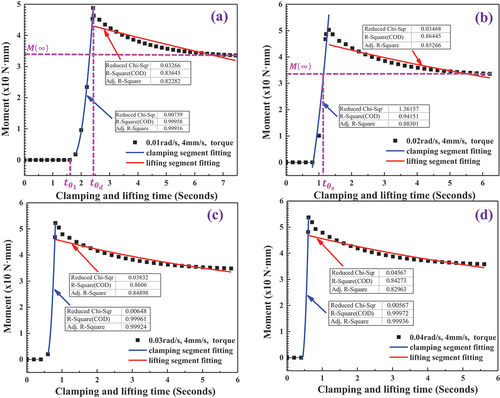
To verify the accuracy of the viscoelastic model parameters obtained by the three-step method in Section 2.4, the model parameters ,
, and
of the food were verified using different clamping velocities. From ), it can be seen that the standard solid linear viscoelastic model parameters
,
, and
all show a tendency to increase with increasing clamping velocity. The rate of variation of the increase of
was 0.735%, 6.618%, and 10.294%, respectively, when the clamping velocity increased from 0.01 rad/s to 0.02 rad/s, 0.03 rad/s, and 0.04 rad/s, respectively, and the
was 1.105%, 6.630%, and 10.497%, respectively, and the
was 0.752%, 6.466%, and 10.286%, respectively. Further, to verify the deviation between the values of viscoelastic parameters estimated using the three-step method and the true values, the values of
,
, and
obtained by the three-step method are converted to the finite element Prony series g(1) and
(1) values as computational value and then compared with the true values in the finite elements. ) shows the deviation of the true values of g(1) and
(1) from the computational value and the clamping velocity, and it can be seen that as the clamping velocity increases, the deviation of
(1) increases first and then decreases, the maximum deviation of
(1) is 0.006 (deviation change rate of 0.164%), and the maximum deviation of the computational value of g(1) from the true value is 0.004 (deviation change rate of 0.941%). The maximum deviation of
(1) and the maximum deviation of g (1) are within the allowable deviation range, which verifies that the viscoelastic model parameters estimated using the three-step method can approximate the true viscoelastic model parameters of the food.
Fetching rate and force
(a1–a4) shows the results of fetching a single row of multiple block foods using clamping. The single row of foods is affected by the spacing in both directions, and to verify the effect of the spacing perpendicular to the clamping direction on the fetching rate, the food spacing d = 1 mm in the clamping direction is kept constant, and it can be seen that the spacing is at a small value in both perpendiculars to the clamping direction, and the fetching rate reaches the maximum only when it is close to the tight ((a4)), and the plastic deformation LE variable does not reach a large value, and no large plastic deformation occurs in this process.
Figure 7. Results of fetching block foods: (a1) – (a4) the distribution of single-row block foods and the results of fetching, (b1) – (b4) the distribution of multi-row block foods and the results of fetching.
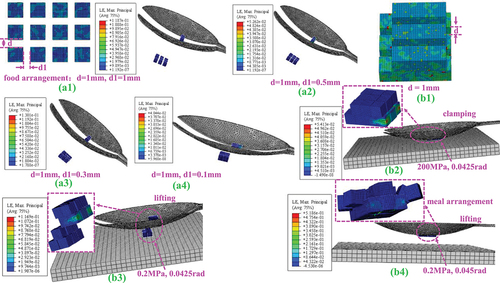
Further analyzing the fetching rate of two rows of multiple block foods at a smaller spacing perpendicular to the clamping direction ( (b1)), it can be seen from (b2,b3) that the same predetermined clamping angle displacement for relatively soft substance foods (0.2 MPa), the fetching rate is higher when fetching the foods using the clamping approach, while for relatively hard substance foods (200 MPa), the fetching rate is lower when the clamping method is used to fetch foods. As can be seen from (b3–b4), for fetching soft substance foods by the clamping method, the predetermined angular displacement has a greater effect on the fetching rate, and (b4) shows the maximum fetching rate when the food does not undergo large nonlinear deformation (LE<0.34). This indicates that the block food trait, perpendicular to the clamping direction spacing and predetermined clamping angular displacement has an effect on the fetching rate when multiple block foods are fetched by the clamping method.
shows the results of the fetching for clamping and lifting the diced mixed foods. ) shows the schematic diagram of the diced mixed foods close to the distribution, and the boundary conditions in the simulation are set at a clamping velocity of 0.1 rad/s and a lifting velocity of 5 mm/s. b1–b2) show the results of food fetching for clamping soft and hard foods, and it can be seen that in the clamping section (with a predetermined angular displacement of 0.045 rad), no major deformation of the food occurs at the beginning (LE<0.017), however, during the clamping process, some of the foods ran away, which led to a decrease in the fetching rate of the clamping process.
Figure 8. Results of fetching diced mixed foods: (a) the diced mixed foods close to the distribution, (b1) initial clamping state, (b2) initial lifting state, (c1) final clamping state, (c2) final lifting state, (d1) final clamping state, (d2) final lifting state, (e1) final clamping state, (e2) final lifting state.
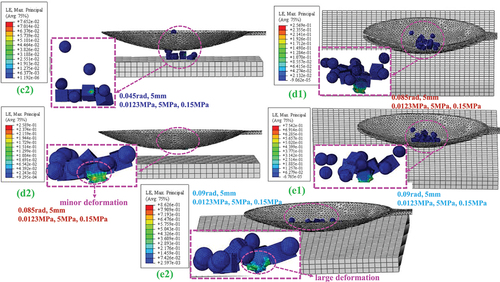
c1,e2) show the results of the foods fetching of the predetermined angular displacement for relatively soft foods. From c1), it can be seen that when the predetermined angular displacement is 0.045 rad, no major deformation occurs when clamping the diced mixed foods (LE< 0.1), however, the foods appear to fall off in the lifting section (c2)), which may be due to the small setting of the predetermined angular displacement. When the predetermined angular displacement was further increased to observe the fetching rate of soft foods, the food did not show large deformation in the clamping section (d1)) when the predetermined angular displacement was 0.085 rad, and the food was able to fetch all the foods in the lifting section (d2)), which had a high fetching rate. Further increasing the angular displacement to observe the deformation during food fetching, when the angular displacement was 0.09 rad, although the food was able to fetch all the foods in the lifting section (e2), LE>0.43), however, the food underwent large nonlinear deformation in the clamping section (e1), LE>0.38). Through the results of the diced mixed foods, it can be seen that the fetching rate of the diced mixed foods containing the harder diced foods is low in the clamping section, and the predetermined angular displacement in the clamping section affects the deformation of the foods, and the predetermined angular displacement also affects the fetching rate of the lifting process. This suggests that the traits of the food and the predetermined clamping angle displacement affect the fetching rate and food deformation of the diced mixed foods.
To minimize the nonlinear deformation of the food when fetching multiple block foods and to meet with a high fetching rate at the same time, the predetermined angular displacement of (a1,a2) was set to 0.045 rad according to the fetching rate and food deformation results of . From (a1,a2), it can be seen that the moment of action and force of the food on the left spoon and the right spoon are different when clamping and lifting multiple block foods, which may be due to the different viscoelastic properties and friction with time between the food and the food when fetching multiple block foods. In the clamping stage, when the clamping angular velocity increased from 0.1 rad/s to 0.4 rad/s, the peak moment of the food acting on the half spoon showed an increasing trend with the increase of the clamping angular velocity, which might be because when the angular velocity was larger, it affected the food deformation and viscoelasticity, and then made the clamping moment larger. Another reason may be that the food is affected by the friction between the food and the half spoon, and the friction between the food and the plate in the clamping process. During the clamping phase of fetching block foods, the moment of action of the food on the half spoon shows a moment of relaxation. Therefore, when fetching multiple block solid foods, we have to apply the maximum clamping moment received by the half spoon during the clamping process, which can improve the clamping rate of block foods. This may be due to the different frictional forces caused by the contact area between multiple pieces of food and the two half spoons when lifting multiple pieces of food, which in turn affects the force of the two half spoons. During the process of increasing the lifting velocity from 5 mm/s to 40 mm/s, the force of the two half spoons was rapidly reduced from a large value to a minimum and then reached a steady state. In the steady-state stage, it can be seen that the force of the food on the two half spoons increases with the increase of the lifting velocity, which may be because the different velocities affect the friction between the food and the two half spoons when multiple blocks of the food are taken, and the force between the food and the food generated by the viscoelasticity of the food above and the food below increases, thus showing that the force of the food on the two half spoons increases with the increase of the velocity.
Figure 9. Results of the force and moment at different velocities: (a1) the force and moment of the left spoon when fetching block foods with a predetermined angular displacement of 0.045 rad, (a2) the force and moment of the right spoon when fetching block foods with a predetermined angular displacement of 0.045 rad, (b1) the force and moment of the left spoon when fetching diced mixed foods with a predetermined angular displacement of 0.085 rad, (b2) the force and moment of the right spoon when fetching diced mixed foods with a predetermined angular displacement of 0.085 rad.
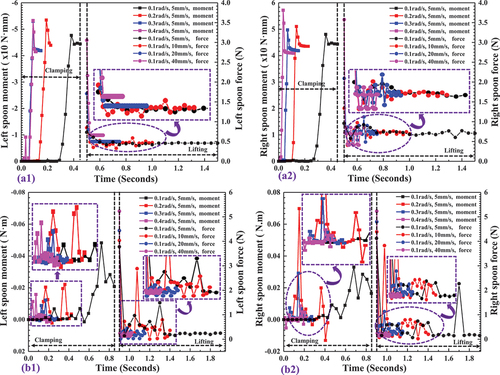
The predetermined angular displacement of (b1,b2) was set to 0.085 rad according to the results of the fetching rate and food deformation in . (b1,b2) show the results of the moments and forces of the food on the left and right spoons when fetching the diced mixed foods. It can be seen that at the same time, the moment and force of the diced mixed foods on the left spoon are different from those on the right spoon, however, the overall trend is similar. During the clamping phase, the diced mixed foods did not show moment relaxation to the two half spoons, and the clamping moment tended to decrease as the clamping angular velocity increased, a result that was different from that of a single food and multiple block foods, probably because multiple foods with different traits (such as softness and hardness and shape) produced different viscoelasticity from each other, which in turn caused different moments of action for fetching the diced mixed foods. In the lifting section, when the two half spoons lift the food to reach a stable velocity, the force of the two half spoons tends to decrease with the increase in lifting velocity, and this result shows a different trend from the force of the block foods.
Conclusion
Aiming at the problem of evaluating the viscoelastic and friction characteristics of meal-assisting robots in the process of food fetching, this paper proposes an experimental bench scheme and measurement method for measuring food fetching. The standard linear solid model in Maxwell form is characterized by the moment relaxation method, which can describe the microscopic stress relaxation behavior of solid foods from the macroscopic moment angle. In this paper, the accuracy of the method was verified by display algorithm finite element simulation. The viscoelasticity of solid food is described by a standard linear solid model with three unknown parameters (,
, and
), which can be easily obtained by the action of disposable food fetching. The ratio of the tangential and normal forces obtained by induced slippage was modeled to estimate the friction coefficient of the contact surface between the two half spoons and the food. The accuracy of using the induced slippage method to measure the coefficient of friction between the contact surface of solid food and the two half spoons was verified by finite element simulation. The process of food fetching was simulated by finite element simulation, and the fetching rate and force of mixed foods of different traits and shapes of block foods and diced mixed foods were investigated. The results showed that at the same predetermined angular displacement, the trait of the solid food had a greater effect on the food fetching rate, with a higher fetching rate for the relatively softer block foods and a lower fetching rate for the relatively harder block foods. The peak moment tends to increase with the increase of the clamping angular velocity, and the force increases with the increase of the lifting velocity. The above research work has laid the foundation for rational planning of food fetching parameters and improving the food fetching rate. In the future, we will conduct experimental verification of perfectly shaped (cubes, ellipsoids, and spheres used in this paper) and irregularly shaped solid food fetching and establish a database of viscoelastic parameters and friction coefficients for various shapes and properties of solid foods fetched by the combined spoon and chopstick meal-assisting robots, to understand the rheological and frictional properties of solid foods, and to lay the groundwork for the improvement of the foods fetching strategy of the new meal-assisting robot. In addition, the viscoelastic mechanics model and the friction coefficient measurement method adopted in this paper can also be applied to the automated robots in the food industry to reasonably adjust the required force control and position control strategies in the process of gripping and lifting food to reduce the large deformation to the viscoelastic food so as to ensure the food quality.
Declaration
The authors declared no potential conflicts of interest with respect to the research, authorship, and/or publication of this article.
Disclosure statement
No potential conflict of interest was reported by the author(s).
Data availability statement
The original contributions presented in the study are included in the article/supplementary material, further inquiries can be directed to the corresponding author.
Additional information
Funding
References
- Mokhtari, M.; Feki, M. A.; Abdulrazak, B.; Grandjean, B. 3 toward a Human-Friendly User Interface to Control an Assistive Robot in the Context of Smart Homes. Lect. Notes Control Inf. Sci. 2004, 306, 47–56.
- Topping, M. J.; Smith, J. K. The Development of Handy 1. A Robotic System to Assist the Severely Disabled. Technol. Disability. 1999, 10, 95–105.
- Topping, M. Flexibot–a Multi‐functional general-purpose Service Robot. Ind. Rob. 2001, 28(5), 395–401. DOI: 10.1108/01439910110401466.
- Ishii, S. Food-assistance Robot “My Spoon.” Int. J. Soc. Rob. 2003, 21(4), 378–381. DOI: 10.7210/jrsj.21.378.
- Zhang, X.; Wang, X.; Wang, B.; Sugi, T.; Nakamura, M. Automatic Adaptive Onset Detection Using an Electromyogram with Individual Difference for Control of a Food Assistance Robot. J. Med. Eng. Technol. 2009, 33(4), 322–327. DOI: 10.1080/03091900902744031.
- Daehyung, P.; Yuuna, H.; Charles, C. K. A Multimodal Anomaly Detector for Robot-Assisted Feeding Using an LSTM-Based Variational Autoencoder. IEEE Robot. Autom. Lett. 2018, 3(3), 1544–1551. DOI: 10.1109/LRA.2018.2801475.
- Jihyeon, H.; Sangin, P.; Chang-Hwan, I. Laehyun, K.A Hybrid Brain–Computer Interface for Real-Life Food-Assist Robot Control. Sensors. 2021 21 4578. doi:10.3390/s21134578
- Nabil, E.; Aman, B. A Learning from Demonstration Framework for Implementation of A Feeding Task. Ency. Semant. Comput. Robot. Intell. 2018, 2(1), 1850001. DOI: 10.1142/S2529737618500016.
- Tejas, K. S.; Maria, K. G.; Gräser, A. Application of Reinforcement Learning to a Robotic Drinking Assistant. Robotics. 2019, 9(1), 1–15. DOI: 10.3390/robotics9010001.
- Yantao, L.; Lixun, Z.; Lan, W. 1811-1815. Mechanism Design and Dynamics Study of Food-assistance Robot. Mechatron. Autom. 2009.
- Fei, L.; Hongliu, Y.; Wentao, W.; Changcheng, Q. I-feed: A Robotic Platform of an Assistive Feeding Robot for the Disabled Elderly Population. Technol. Health Care 2020, 2, 1–5.
- Fei, L.; Peng, X.; Hongliu, Y. Robot-assisted Feeding: A Technical Application that Combines Learning from Demonstration and Visual Interaction. Technol. Health Care 2020, 1, 1–6.
- Hamazawa, M. Robot Applications in the Japanese Food Industry. Ind. Rob. 1999, 26(4), 274–277. DOI: 10.1108/01439919910277530.
- Congcong, X.; Liping, W.; Liyu, S.; Chi, Y.; Huaning, Y.; Yunfei, L. Effect of freezing/thawing Temperature on the Viscoelastic and Nutritional Qualities of Carrots. Int. J. Food Prop. 2016, 19(6), 1413–1424. DOI: 10.1080/10942912.2015.1079788.
- Singh, P.; Lakes, R. S.; Gunasekaran, S. Viscoelastic Characterization of Selected Foods over an Extended Frequency Range. Rheol. Acta. 2006, 46(1), 131–142. DOI: 10.1007/s00397-006-0107-1.
- Sritham, E.; Sundaram, G.; Roderic, S. L. Broadband Viscoelastic Spectroscopy: A New Technique for Characterizing Rheological Behavior of Solid Foods. Int. J. Food Prop. 2009, 12(1), 102–113. DOI: 10.1080/10942910802223388.
- Boisly, M.; Schuldt, S.; Kastner, M.; Schneider, Y.; Rohm, H. Experimental Characterisation and Numerical Modelling of Cutting Processes in Viscoelastic Solids. J. Food Eng. 2016, 191, 1–9. DOI: 10.1016/j.jfoodeng.2016.06.019.
- Krokida, M. K.; Maroulis, Z. B.; Marinos-Kouris, D. Viscoelastic Behavior of Dehydrated Carrot and Potato. Drying Technol. 1998, 16(3–5), 687–703. DOI: 10.1080/07373939808917430.
- Fakhreddin, S.; Mahdi, K. Texture Profile Analysis and Stress Relaxation Characteristics of Quince Sponge Cake. J. Food Meas. Charact. 2018, 12(2), 1203–1210. DOI: 10.1007/s11694-018-9734-3.
- Fuhrmann, P. L.; Aguayo-Mendoza, M.; Jansen, B.; Stieger, M.; Scholten, E. Characterisation of Friction Behaviour of Intact Soft Solid Foods and Food Boli. Food Hydrocolloids. 2020, 100, 105441. DOI: 10.1016/j.foodhyd.2019.105441.
- Joyner, H. S.; Pernell, C. W.; Daubert, C. R. Impact of Formulation and Saliva on Acid Milk Gel Friction Behavior. J. Food Sci. 2014, 79(5), 867–880. DOI: 10.1111/1750-3841.12439.
- Prinz, J. F.; Wijk, R. A.; Huntjens, L. Load Dependency of the Coefficient of Friction of Oral Mucosa. Food Hydrocolloids. 2007, 21(3), 402–408. DOI: 10.1016/j.foodhyd.2006.05.005.
- Wragge-Morley, R.; Yon, J.; Lock, R.; Alexander, B.; Burgess, S. A Novel Pendulum Test for Measuring Roller Chain Efficiency. Meas. Sci. Technol. 2018, 29(7), 075008. DOI: 10.1088/1361-6501/aaa239.
- Kokorian, J.; Spengen, W. M. V. Improved Analysis and Visualization of Friction Loop Data: Unraveling the Energy Dissipation of meso-scale stick–slip Motion. Meas. Sci. Technol. 2017, 28(11), 115011. DOI: 10.1088/1361-6501/aa870a.
- Pettersson, T.; Ohlsson, S.; Davis, J. O.; Dodd, T. J.; Dodd, T. J. A Hygienically Designed Force Gripper for Flexible Handling of Variable and Easily Damaged Natural Food Products. Innovative Food Sci. Emerging Technol. 2011, 12(3), 344–351. DOI: 10.1016/j.ifset.2011.03.002.
- Xu, Z.; Chen, W. A fractional-order Model on New Experiments of Linear Viscoelastic Creep of Hami Melon. Comput. Math. with Appl. 2013, 66(5), 677–681. DOI: 10.1016/j.camwa.2013.01.033.
- Jinghu, Y.; Santos, P. H. S.; Campanlla, O. H. A Study to Characterize the Mechanical Behavior of Semisolid Viscoelastic Systems under Compression chewing-case Study of Agar Gel. J. Texture Stud. 2012, 43(6), 459–467. DOI: 10.1111/j.1745-4603.2012.00356.x.
- Mahiuddin, M.; Godhani, D.; Feng, L.; Liu, F.; Langrish, T.; Karim, M. A. Application of Caputo Fractional Rheological Model to Determine the Viscoelastic and Mechanical Properties of Fruit and Vegetables. Postharvest. Biol. Technol. 2020, 163, 111147. DOI: 10.1016/j.postharvbio.2020.111147.
- Gyeong-Won, K.; Gab-Soo, D.; Yeonghwan, B.; Yasuyuki, S. Determination of the Viscoelastic Properties of Agar/Agar-Gelatin Gels Based on Finite Element Method Optimization. Food Sci. Technol. Res. 2008, 14(6), 525–532. DOI: 10.3136/fstr.14.525.
- Michal, P.; Ondrej, N.; David, H.; Satya, S. Finite Element Method Model of the Mechanical Behaviour of Jatropha Curcas L. seed under compression loading. Bio. Eng. 2012, 111, 412–421.
- Hui, L.; Dejun, M.; Jiasen, W.; Jinghu, Y. Research on Mechanical Behavior of Viscoelastic Food Material in the Mode of Compressed Chewing. Math. Probl. Eng. 2015, 4, 1–6.
- Sakamoto, N.; Higashimori, M.; Tsuji, T.; Kaneko, M. An Optimum Design of Robotic Hand for Handling a visco-elastic Object Based on Maxwell Model. 2007 IEEE International Conference on Robotics and Automation. 10-14 April 2007 Roma, Italy. 2007, 1219–1225. doi:10.1109/ROBOT.2007.363151.
- Sakamoto, N.; Higashimori, M.; Tsuji, T.; Kaneko, M. An Optimum Design of Robotic Food Handling by Using Burger Model. Intell Service Robot. 2009, 2(1), 53–60. DOI: 10.1007/s11370-008-0032-5.
- Zhongkui, W.; Syogo, I.; Yasutaka, H.; Sadao, K. Measuring Viscoelasticity and Friction of Tempuras for Robotic Handling. J. Food Eng. 2021, 310, 110707. DOI: 10.1016/j.jfoodeng.2021.110707.
- Mahiuddin, M.; Khan, M. I. H.; Kumar, C.; Rahman, M. M.; Karim, M. A. Shrinkage of Food Materials during Drying: Current Status and Challenges. Compr. Rev. Food Sci. Food Saf. 2018, 17(5), 1113–1126. DOI: 10.1111/1541-4337.12375.
- Mahiuddin, M.; Khan, M. I. H.; Duc Pham, N.; Karim, M. A. Development of Fractional Viscoelastic Model for Characterizing Viscoelastic Properties of Food Material during Drying. Food Biosci. 2018, 23, 45–53. DOI: 10.1016/j.fbio.2018.03.002.
- Llave, Y.; Takemori, K.; Fukuoka, M.; Takemori, T.; Tomita, H.; Sakai, N. Mathematical Modeling of Shrinkage Deformation in Eggplant Undergoing Simultaneous Heat and Mass Transfer during convection-oven Roasting. J. Food Eng. 2016, 178, 124–136. DOI: 10.1016/j.jfoodeng.2016.01.013.
- Williams, S. H.; Wright, B. W.; Truong, V. D.; Daubert, C. R.; Vinyard, C. J. Mechanical Properties of Foods Used in Experimental Studies of Primate Masticatory Function. Am. J. Primatol. 2005, 67(3), 329–346. DOI: 10.1002/ajp.20189.
- Ogawa, Y.; Matsuura, M.; Yamamoto, N. Young’s Modulus and Poisson’s Ratio Changes in Japanese Radish and Carrot Root Tissues during Boiling. Int. J. Food Prop. 2015, 18(5), 1006–1013. DOI: 10.1080/10942912.2013.879388.
- Zhongkui, W.; Shinichi, H. Modeling and Parameter Estimation of Rheological Objects for Simultaneous Reproduction of Force and Deformation. ICABB. October 14-16, 2010 Venice, Italy. 2010, 14–16. https://www.researchgate.net/publication/228708234_Modeling_and_parameter_estimation_of_rheological_objects_for_simultaneous_reproduction_of_force_and_deformation
- Zhongkui, W.; Shinichi, H. Finite Element Modeling and Physical Property Estimation of Rheological Food Objects. J. Food Res. 2012, 1(1), 48–67. DOI: 10.5539/jfr.v1n1p48.
- Che-Yu, L. Alternative Form of Standard Linear Solid Model for Characterizing Stress Relaxation and Creep: Including a Novel Parameter for Quantifying the Ratio of Fluids to Solids of a Viscoelastic Solid. Front. Mater. 2020, 7, 1–11.
- Otsuki, M.; Matsukawa, H. Systematic Breakdown of Amontons’ Law of Friction for an Elastic Object Locally Obeying Amontons’ Law. Sci. Rep. 2013, 3(1), 1586–1592. DOI: 10.1038/srep01586.
- Katano, Y.; Nakano, K.; Otsuki, M.; Matsukawa, H. Novel Friction Law for the Static Friction Force Based on Local Precursor Slipping. Sci. Rep. 2014, 4(1), 3630–6324. DOI: 10.1038/srep06324.