Abstract
High pressure processing (HPP) is an emerging technology for food preservation, however its application in pretreatment of lignocellulosic biomass has not been studied; therefore, the objective of this work was to evaluate the effect of HPP in combination with sodium hydroxide on the enzymatic hydrolysis of sugarcane raw and prehydrolyzed bagasse. The results indicated that high pressure treatments alone or combined with sodium hydroxide had a little effect on the lignocellulosic fraction of sugarcane bagasse, however in prehydrolyzed bagasse, removal of the major hemicellulose was observed. Also, changes in the microstructure and crystallinity of sugarcane bagasse were observed at 450 MPa as the modification of the cellulose fiber improved the porosity, increasing the susceptibility of bagasse to cellulases, obtaining a glucose concentration of 25.91 g/L with NaOH (6% treatment). These results are important because the application of HPP on lignocellulosic materials could be used to get fermentable sugars for production of food additives.
El procesamiento de alta presión (APH) es una tecnología emergente para la conservación de alimentos, sin embargo su aplicación como pretratamiento de biomasa lignocelulósica no ha sido estudiada. El objetivo de este trabajo fue evaluar el efecto de la alta presión en combinación con el uso de soluciones de hidróxido de sodio sobre la hidrólisis enzimática del bagazo de caña normal y prehidrolizado. Los resultados indicaron que los tratamientos de alta presión solos o en combinación con el hidróxido de sodio tuvieron un ligero efecto sobre la fracción lignocelulósica del bagazo de caña de azúcar, sin embargo, en el bagazo prehidrolizado se observó la mayor reducción de hemicelulosa. También, cambios importantes en la microestructura y en la cristalinidad del bagazo de caña fueron observados a 450 MPa con una alteración de las fibras de celulosa que mejoraron la susceptibilidad del bagazo a las celulasas, obteniendo una concentración de glucosa de 25,91 g/L con el tratamiento con hidróxido de sodio al 6%. Estos resultados son importantes ya que muestran que la aplicación de APH sobre materiales lignocelulósicos podría ser utilizada para obtener azúcares fermentables para la producción de aditivos alimentarios.
Introduction
The interest in alternative sources to produce fuels has been increasing in last few years. In this regard, lignocellulosic materials (LCM) are preferred because of their ready availability, low cost, and because their use does not compete with human food supply like the use of cereals such as maize, sorghum, or sugarcane. Sugarcane bagasse (SCB) is the lignocellulosic byproduct obtained from sugarcane (Saccharum officinarum) during sugar production (Martín, Klinke, & Thomsen, Citation2007). It has been estimated that sugar mills generate 270 kg of bagasse per ton of harvested cane. SCB contains about 40–50% of cellulose, 25–35% of hemicelluloses, an amorphous polymer composed of xylose, glucose, galactose, arabinose, and mannose; the rest is lignin, trace amounts of minerals, wax, and other compounds (Sun, Sun, Zhao, & Sun, Citation2004). SCB can be used to produce value-added products like food additives, ethanol, and other chemical compounds that could offer economic, environmental, and strategic advantages for the sugar industry (Adsul et al., Citation2005; Baudel, Zaror, & Abreu, Citation2005; Pandey, Soccol, Nigam, & Soccol, Citation2000). The bioconversion of this lignocellulosic material requires suitable pretreatment, hydrolysis, and fermentation processes (Dermibas, Citation2005). When obtaining fermentable sugars from lignocellulosic biomass, the main challenge is pretreatment. Several pretreatment methods have been studied and many are still under development. Pretreatments can be classified into physical, chemical, biological, and combined methods (Agbor, Cicek, Saprling, Berlin, & Levin, Citation2011; Sun & Cheng, Citation2002; Yang & Wyman, Citation2008).
Physicochemical pretreatments are the most extensively studied and commonly used. The alkaline pretreatment with sodium hydroxide (NaOH) is effective for solubilization of lignin, exhibiting minor cellulose and hemicellulose solubilization than acid or hydrothermal processes. Sodium hydroxide causes swelling, increasing the internal contact surface of cellulose as the degree of polymerization and crystallinity decreases, promoting lignin structure disruption (Alvira, Tomás-Pejó, Ballesteros, & Negro, Citation2010; Taherzadeh & Karimi, Citation2008).
Alkaline treatment is considered to be one of the best chemical pretreatment methods for surface modification of lignocellulosic materials. Treating this material with sodium hydroxide solutions breaks down the covalent association between lignocellulose components, hydrolyzing hemicelluloses and de-polymerizing lignin (Vadiveloo, Nurfariza, & Fadel, Citation2009). This treatment has an important effect on morphological and molecular properties of cellulose, causing changes in crystallinity, pore structure, accessibility, stiffness, unit-cell structure, and orientation of cellulose fibers (Široký, Blackburn, Bechtold, Taylor, & White, Citation2011). Alkaline treatment improves mechanical and chemical properties of cellulose such as structural durability, reactivity, and natural ion-exchange capacity; this treatment also removes natural fats and waxes from the cellulose fiber surfaces revealing chemically reactive groups like –OH (Ndazi, Karlsson, Tesha, & Nyahumwa, Citation2007).
High pressure processing (HPP) is an emerging technology with a growing number of commercial processing applications that are reaching consumers over the world. An advantage of HPP technology, when compared to thermal treatments, is that the pressure is transmitted uniformly and almost instantaneously over the product regardless of the size and geometry or the dimensions of the processing equipment. Hydrostatic pressures used for commercial purposes range from 300 to 700 MPa with holding times from 3 to 5 minutes (Barba, Esteve, & Frigola, Citation2012; Bermúdez-Aguirre & Barbosa-Cánovas, Citation2011). HPP treatment is based on two fundamental concepts: (1) the Le Chatelier principle, which proposes that high pressure favors all reactions and structural changes involving a decrease in volume, and (2) the isostatic principle which proposes that the distribution of pressure is homogenous in all parts of a treated material (Hereman, Citation2002; Valdez-Fragoso, Mujica-Paz, Welti-Chanes, & Torres, Citation2011). HPP has been proposed to be used in different ways such as a quarantine alternative process against fruit flies for tropical fruits (Neven, Follet, & Raghubeer, Citation2007; Vargas-Ortiz et al., Citation2013) besides its traditional use in food preservation. The efficacy of HPP combined with alkaline treatment has not been tested as pretreatment in lignocellulosic materials. In the present study, the combined effect of high pressure processing with alkaline treatment was used in sugarcane bagasse to produce fermentable sugars and analyze its possible use in pretreatment of biomass.
Materials and methods
Materials
Sugarcane bagasse (SCB) was provided by a local sugar industry (Ingenio el Higo, Veracruz, Mexico) from the last milling resulting after juice extraction. The raw material was dried at 50°C for 24 h, milled using a knife mill (Dettingen-teck, Wets, Germany) at room temperature with a final particle size of 500 µm and stored in plastic bags at ambient room temperature until use. All chemical reagents used were of analytical grade.
High pressure processing equipment
Pressure treatments were carried out in a 2 L high hydrostatic pressure food processor (Model Welch, Avure Autoclave Systems, Columbus, OH) using a pressure chamber of 10 cm inner diameter and 25.4 cm length and an operating pressure capacity of 690 MPa. Distilled water was used as pressurizing fluid; pressure vessel and water inside were kept at 50°C during treatments by a constant flow of water through an external jacket. The time required to reach the processing pressure (come up time, CUT) was less than 40 s and the release time was always less than 10 s.
High pressure pretreatment
The pretreatment was carried out in vacuum-sealed polyethylene bags containing 25 g of sugarcane bagasse in a 6:1 (v/m) liquid:solid ratio (LSR). The liquid phase used in this study was sodium hydroxide at a concentration of 0%, 3%, 6%, or 9% (w/v). Three pressure levels were used: 350, 400, and 450 MPa, during 15 min at 50°C. These conditions were selected considering previous results using high pressure to treat sugar cane bagasse (Castañón-Rodríguez et al., Citation2013). Two bagasses were studied: raw bagasse as control and pressurized bagasse (previously hydrolyzed with 2% (v/v) sulfuric acid at 121°C for 40 min, LSR 6:1), the lignocellulosic fraction composition of the prehydrolyzed bagasse was: 38.87% cellulose, 14.02% hemicelluloses, and 13.66% lignin.
Enzymatic hydrolysis
Cellulase from Trichoderma reesei American Type Culture Collection 26,921 (0.5 mL) and cellobiase from Aspergillus niger (Novozyme® 188) (0.5 mL) were purchased from Sigma Chemical Co. (St. Louis, MO). Enzymatic hydrolysis was performed using solid residue samples (10 g) obtained after pretreatment and suspended in a solution of 50 mM acetate buffer (pH 4.8) in a volume of 90 mL (LSR 1:9). Hydrolysis was performed in a shaker at 50°C and 200 rpm for up to 72 h. Samples were placed in a boiled water bath for 5 min to inactivate enzymes and stored at 4°C until sugar analysis by HPLC.
Analytical methods
The lignocellulosic fraction was determined according to ANKOM Technology methods following the procedure reported by McIntosh and Vancov (Citation2011). The content of glucose, acetic acid, and furfural present in the liquid fraction after pressurization and during enzymatic hydrolysis was analyzed using a high performance liquid chromatography water 600 TSP (pressure transducer sensor) spectra system (Waters, Milford, MA, USA) using a Shodex SH1011 column (8 × 300 mm) to separate components. The column was maintained at 55°C, and the mobile phase was 0.05 N sulfuric acid, with a flow rate of 0.6 mL/min obtained using an index refraction detector (Waters 2414, TSP Refracto Monitor V Waters, Milford, MA, USA) at 50°C. Samples were pretreated with 0.3 N barium oxide and 5% zinc sulfate solutions at 4°C for 10 min, centrifuged at 10,000 rpm for 10 min and the supernatant was filtered (0.45 μm) before injection.
Samples of sugarcane bagasse before and after enzymatic hydrolysis and high pressure treatments were observed on a scanning electron microscope (SEM)(JEOL JSM-6060 LV, Tokyo, Japan).
To evaluate the effects on the crystallinity structure, X-ray diffraction (XRD) analysis of the dry, ground samples was carried out using a diffractometer Siemens (Model D5000; Madison, WI) with a radiation wavelength of (λ) 1.5406 Å, corresponding to copper radiation, operating at 35 kV and 15 mA from 10° to 45° on a 2θ scale with a step size of 0.05° at room temperature. The results are expressed as intensity (cps).
Statistical analysis
The effect of high pressure processing and alkaline treatments on lignocellulosic fraction sugarcane bagasse was evaluated using the regression function in Excel 2010 (Microsoft Inc. Redmond, WA). A second-order polynomial model (Equation 1) was applied as the first approach to fit the experimental data:
Results and discussion
Effects of treatments on the lignocellulosic fraction
The combined effect of HPP and alkaline treatment sodium hydroxide at different concentrations (0, 3, 6, and 9%) on cellulose, hemicellulose, and lignin of raw bagasse and prehydrolyzed bagasse is shown in . For both types of bagasse, the correlation value (R2) and the adjusted R2 were higher than 0.754 and 0.6856, respectively; also, the critical F values calculated were lower than 1.351 × 10−5 indicating that the equation calculated for each type of bagasse can be used to adequately describe the effect of sodium hydroxide concentration and the high pressure processing level on the concentration of cellulose, hemicellulose, or lignin (). Raw and prehydrolyzed bagasse showed a similar initial concentration of cellulose which was reduced in a similar way (near to 10%) when increasing the sodium hydroxide with almost no effect induced by the pressurization level ( and ). Similar results according to the reduction of hemicellulose and lignin with sodium hydroxide have been previously reported by Castañon-Rodríguez et al. (Citation2013); however, in that work the concentration of sodium hydroxide was kept constant at 2% (w/v) and the levels of pressure were lower, which indicates that both variables have a synergic effect. This reduction on cellulose levels has been associated with a loss of microcrystalline cellulose, which is more sensible to chemical hydrolysis (Chen, Tu, & Sheen, Citation2011).
Table 1. Adjusted parameters and model coefficients used in evaluation of high pressure processing and alkaline treatment effects on sugarcane bagasse lignocellulosic fraction.
Tabla 1. Parámetros ajustados y coeficientes del modelo utilizado en la evaluación de los efectos de los tratamientos de alta presión y alcalino sobre la fracción lignocelulósica del bagazo de caña de azúcar.
Figure 1. Effect of high pressure treatments in combination with alkaline treatment at 15 min on cellulose (a), hemicellulose (b), and lignin (c) of sugarcane raw bagasse and prehydrolyzed bagasse.
Figura 1. Efecto de los tratamientos de alta presión en combinación con tratamiento alcalino durante 15 min sobre celulosa (a), hemicelulosa (b) y lignina (c) de bagazo azúcar de caña normal y prehidrolizado.
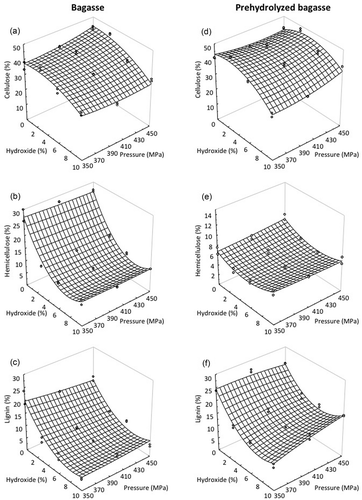
The reduction of hemicellulose in the raw bagasse was estimated to be 74.70% due mainly to the increase in the sodium hydroxide concentration (). On the other hand, the hemicellulose content of the prehydrolyzed bagasse was not affected for either the pressure level or sodium hydroxide or the combination of both factors ().
The lignin fraction of the raw bagasse was reduced considerably by increasing the sodium hydroxide level, decreasing from 19% to 5% with no effect of the pressurization level (). The concentration of lignin in the prehydrolyzed bagasse showed a less decrease associated with the increase in sodium hydroxide concentration and was not sensible to the pressurization level. In this material, the final lignin concentration was estimated to be 6% (), these results could be because this alkali has more affinity over lignin and this component is the most recalcitrant which cannot be removed or reduced by pressure.
Different alkaline and acid treatments are used to increase the hydrolysis of cellulose, causing the rupture of the lignocellulosic compounds, reducing the content of hemicellulose and lignin, and decreasing the crystallinity of the cellulose (Banerjee et al., Citation2010). Alkaline treatments are more effective than acid treatments for the lignin solubilization (Carvalheiro, Duarte, & Gírio, Citation2008), as it was observed in this study. The sodium hydroxide in the lignocellulosic material induces the swelling of the material, increasing the internal surface and reducing the polymerization degree and crystallinity, which results in the rupture of the lignin. The lignin concentration in wheat straw was reduced to 15% with 0.75% NaOH at 121°C for 30 min, and 42% with 2.0% NaOH for 90 min at the same temperature, indicating that the alkali concentration and exposure time are key factors for the removal of lignin (Arni, Zilli, & Converti, Citation2007); a similar behavior was observed in the present study.
The efficiency of the alkaline hydrolysis of lignocellulose materials has been improved when combined with other treatments. Velmurugan and Muthukumar (Citation2011) observed that SCB pretreated with 2% NaOH subjected to ultrasound for 20 min, achieved a lignin reduction of 75.44%. The application of the AFEX process (ammonia fiber explosion) induces a structural arrangement of the material, increasing the accessibility of water in the fiber structure. This treatment causes the break of the hydrogen bonds that hold together the lignocellulosic fraction, exposing polar groups that were not available (Pernalete, Piña, Suarez, Ferrer, & Aiello, Citation2008).
A similar effect than AFEX was expected by applying HPP treatments, because the high hydrostatic pressure has been reported to affect the weak intermolecular interactions, such as hydrogen bonds, hydrophobic and electrostatic interactions with no effect on covalent bonds (Yang, Jiang, Wang, Zhao, & Sun, Citation2009). In this study, the effect of HPP alone or combined with sodium hydroxide seemed to have little or no effect on the alkaline hydrolysis of the lignocellulosic fraction specifically on cellulose of the sugarcane bagasse, but lignin was found to be the most sensible component in the presence of high concentrations of sodium hydroxide which favored the susceptibility to enzymatic hydrolysis to get fermentable sugars.
Changes in the crystallinity of sugarcane bagasse
The X-ray diffraction patterns of the cellulose crystallographic planes from the raw and prehydrolyzed bagasses, observed at 2θ, are shown in . Raw bagasse showed two major peaks (), one in the region of 15º, which corresponds to the amorphous region and other at 23º, which corresponds to the crystalline region (Binod et al., Citation2012; Huang et al., Citation2009). The prehydrolyzed bagasse showed a slightly bigger area for the amorphous region (15º) as well as a reduced area for the crystalline region (23º), which showed a less pronounced peak (). Additionally, the peak observed at 27º was higher in the prehydrolyzed bagasse than in the raw bagasse; also, a new peak was observed at 29º in the prehydrolyzed bagasse. In this regard, cellulose I is the predominant crystal structure present in the lignocellulosic material (other cellulose forms that can be found are II, III, and IV). Cellulose I is partially crystalline and can be converted into other polymorphic forms through several treatments (Foston & Ragauskas, Citation2010; Sun, Xu, Sun, Sun, & Wu, Citation2004).
Figure 2. XRD patterns of raw bagasse (a) and prehydrolyzed bagasse (b) controls and prehydrolyzed bagasse pressurized at 450 MPa and 3% NaOH before (c) and after (d) enzymatic hydrolysis.
Figura 2. Patrones de difracción de rayos X sobre bagazo normal (a) y bagazo prehidrolizado (b) en muestras sin presurizar y muestras presurizadas a 450 MPa e NaOH 3% antes (c) y después (d) de la hidrólisis enzimática.
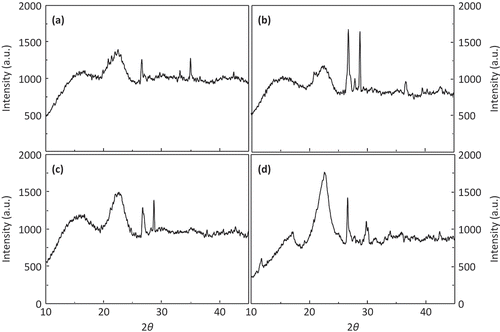
Raw bagasse treated at 450 MPa with 3% of sodium hydroxide showed a taller and wider peak for both the amorphous (15º) and the crystalline (23º) region, indicating that this treatment modified the microstructure of the cellulose (). Finally, shows the diffractogram of the sugarcane bagasse treated at 450 MPa with 3% of sodium hydroxide, after the enzymatic process to hydrolyze the residual cellulose. The peak for the amorphous region (15º) was the smallest of all the analyzed samples, while the peak for the crystalline region (23º) was the tallest and better defined, suggesting that cellulases used in this study were able to degrade the amorphous region although they had less effect on the crystalline region. These results suggest that treatment with 3% sodium hydroxide and 450 MPa caused the swelling of the cellulose fibers increasing the internal surface area. Swelling would have allowed cellulases to have major contact with the substrate inducing a greater level of hydrolysis in the amorphous region and subsequently increasing the proportion of crystalline cellulose.
Figure 3. Structural morphology of sugarcane bagasse subjected to high pressure processing at 350 (a), 400 (b), and 450 (c) MPa in combination with 3% NaOH. 1000× resolution.
Figura 3. Morfología estructural de bagazo de caña sujeto a procesamiento por alta presión a 350 (a), 400 (b) y 450 MPa (c) en combinación con NaOH 3%. Resolución 1,000X.
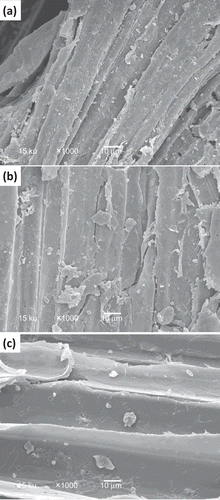
Changes in the microstructure of sugarcane bagasse
SCB showed changes in the surface caused by the treatments combining pressurization and sodium hydroxide (). SCB treated at 350 MPa and 3% NaOH showed a less compact structure as the structure showed the rupture of fibers and small particles on the surface () at difference of raw bagasse. This appearance changed by the effect of the pressurization level, getting a more smoothie structure when SCB was pressurized at 450 MPa with 3% of sodium hydroxide, showing a more uniform surface in presence of surface particles, fracture of fibers, and more exposition of the pores (). The higher pore sizes could be related to the increase in the amorphous region observed in the X-ray diffraction patterns () and could be associated with partial removal of the lignocellulose fractions. It has been observed that the removal of hemicelluloses during acid hydrolysis increased the pore size of the lignocellulosic fraction and therefore increases the accessibility and the probability that the fibers were more easily hydrolyzed (Alvira et al., Citation2010). Also, it has been observed that the pore size of the substrate in relation to the size of the enzymes is a limiting factor during enzymatic hydrolysis of lignocellulosic biomass, because cellulases might become trapped in the pores when the internal area is much larger than the external area, which is the case with many lignocellulosic biomass (Chandra et al., Citation2007). Thus, an increase in the porosity of sugarcane bagasse could improve the subsequent enzymatic hydrolysis, because cellulases might act on both external and internal surfaces (Hosseini & Shah, Citation2011).
Effect of treatments on the susceptibility to enzymatic hydrolysis
The pressurization level and the sodium hydroxide concentration affected the degree of conversion of cellulose to glucose monomers during enzymatic hydrolysis of raw bagasse and prehydrolyzed bagasse (). However, the effect of the pressurizing level was very small and only could be appreciated in the control samples treated without sodium hydroxide obtaining low glucose concentrations at difference of the prehydrolyzed bagasse, the removal of the hemicelluloses fraction with sulfuric acid promoted the susceptibility of enzymatic hydrolysis at both levels of sodium hydroxide 0 (control) and 3%. However, when 3% of sodium hydroxide was used, a lower level of glucose was obtained when increasing the pressure level at 450 MPa, therefore, HPP probably enhances the hydrolysis, but with a previous acid or alkaline pretreatment or increasing temperature could be another alternative to improve the hydrolysis. The level of glucose obtained from raw bagasse increased when 3% of sodium hydroxide was used compared with control treatment. However, the yield of glucose did not increase when changing the level of sodium hydroxide from 3% to 10% (). The concentration of glucose obtained from prehydrolyzed bagasse was higher than the concentration obtained from raw bagasse, indicating the importance of removing the hemicellulose fraction to improve the efficiency of cellulases. An increased yield of glucose was obtained by changing the concentration of sodium hydroxide from 0% to 6%, reaching the maximal concentration of glucose when 6% of sodium hydroxide was used (25.91 g/L of glucose). However, a significant decrease in the glucose concentration was obtained when 10% of sodium hydroxide was used. This behavior might be caused by the formation of phenolic compounds from the lignin degradation induced by the higher concentration of alkali. Phenolic compounds are particularly toxic to enzymes because they induce a cross linking reaction, inactivating them by a denaturation/aggregation phenomenon (Cantarrela, Cantarrela, Gallifuoco, Spera, & Alfani, Citation2004; Kim, Ximenes, Mosier, & Ladisch, Citation2011).
Table 2. Concentration of glucose (g/L) obtained in different sugarcane bagasse after high pressure at 350, 400, and 450 MPa with alkaline treatments (0% and 3% of sodium hydroxide).
Tabla 2. Concentración de glucosa (g/L) obtenidos en diferentes bagazos de caña después del tratamiento por alta presión a 350, 400 y 450 MPa alcalino (0 y 3% de hidróxido de sodio).
Table 3. Effect of different NaOH concentrations on production of glucose of sugarcane bagasse subjected to HPP at 450 MPa.
Tabla 3. Efecto de las diferentes concentraciones de NaOH sobre la producción de glucosa de bagazo de azúcar de caña a tratado por HPP a 450 MPa.
The enzymatic hydrolysis induced changes in the surface of the raw and prehydrolyzed bagasse (). The main microscopic alterations were the disintegration of the continuous structure of the fibers, showing the presence of disintegrated parts and an increase in the opacity of the surface. This behavior suggests that treatments used in this study increased the susceptibility of the sugarcane bagasse to cellulases.
Figure 4. Microstructure observed after hydrolysis enzymatic of raw bagasse (1) and prehydrolyzed bagasse (2) pressurized at 450 MPa with 3% NaOH. (a) 1000× resolution; (b) 5000× resolution.
Figura 4. Microestructura observada después de la hidrolisis enzimática de bagazo normal (1) y bagazo prehidrolizado (2) presurizados a 450 MPa con NaOH 3%. (a) 1,000X resolución; (b) 5,000X resolución.
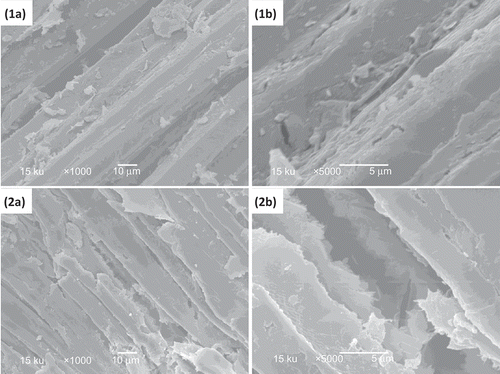
Conclusions
The results obtained indicated that high pressure treatments used in the present study had a slightly favorable effect on improving the susceptibility of the sugarcane bagasse to cellulases. These changes seemed to be associated with alteration of the cellulose fiber structure improving the porosity and allowing the cellulases to have easier access to the amorphous regions located in the inside and outside regions of the fibers. However, the effects of pressurization were minimized by the higher effect of sodium hydroxide, which induces the swelling of the cellulose and the dissolution of the lignin resulting in a higher efficiency of cellulases. High-pressure treatments in combination with sodium hydroxide at 3% induced microscopic and macroscopic changes in the lignocellulosic fraction of sugarcane bagasse, which enhance enzymatic digestibility of cellulose, demonstrating a synergistic effect between these two variables. However, it is necessary to do more experimentation in relation to assessing higher values of high pressure with and without sodium hydroxide, in order to elucidate the direct effect of high pressure on the structural modification of the lignocellulosic residue for higher glucose yields.
Disclosure statement
No potential conflict of interest was reported by the authors.
Additional information
Funding
References
- Adsul, M. G., Ghule, J. E., Shaikh, H., Singh, R., Bastawde, K. B., Gokhale, D. V., & Varma, A. J. (2005). Enzymatic hydrolysis of delignified bagasse polysaccharides. Carbohydrate Polymers, 62, 6–10. doi:10.1016/j.carbpol.2005.07.010
- Agbor, V. B., Cicek, N., Saprling, R., Berlin, A., & Levin, D. B. (2011). Biomass pretreatment: Fundamentals toward application. Biotechnology Advances, 30, 1–11.
- Alvira, P., Tomás-Pejó, E., Ballesteros, M., & Negro, M. J. (2010). Pretreatment technologies for an efficient bioethanol production process based on enzymatic hydrolysis: A review. Bioresource Technology, 101, 4851–4861. doi:10.1016/j.biortech.2009.11.093
- Arni, A. S., Zilli, M., & Converti, A. (2007). Solubilization of lignin components of food concern from sugarcane bagasse by alkaline hydrolysis. Ciencia Y Tecnologia Alimentaria, 5, 271–277. doi:10.1080/11358120709487701
- Banerjee, S., Mudliar, S., Sen, R., Giri, B., Satpute, D., Chakrabarti, T., & Pandey, R. A. (2010). Commercializing lignocellulosic bioethanol: Technology bottlenecks and possible remedies. Biofuels, Bioproducts and Biorefining, 4, 77–93. doi:10.1002/bbb.188
- Barba, F. J., Esteve, M. J., & Frígola, A. (2012). High pressure treatment effect on physicochemical and nutritional properties of fluid foods during storage: A review. Comprehensive Reviews in Food Science and Food Safety, 11, 307–322. doi:10.1111/j.1541-4337.2012.00185.x
- Baudel, H. M., Zaror, C., & Abreu, C. A. M. (2005). Improving the value of sugarcane bagasse wastes via integrated chemical production systems: An environmentally friendly approach. Industrial Crops and Products, 21, 309–315. doi:10.1016/j.indcrop.2004.04.013
- Bermúdez-Aguirre, D., & Barbosa-Cánovas, G. V. (2011). An update on high hydrostatic pressure, from the laboratory to industrial applications. Food Engineering Reviews, 3, 44–61. doi:10.1007/s12393-010-9030-4
- Binod, P., Satyanagalakshmi, K., Sindhu, R., Janu, K. U., Sukumaran, R. K., & Pandey, A. (2012). Short duration microwave assisted pretreatment enhances the enzymatic saccharification and fermentable sugar yield from sugarcane bagasse. Renewable Energy, 37, 109–116. doi:10.1016/j.renene.2011.06.007
- Cantarrela, M., Cantarrela, L., Gallifuoco, A., Spera, A., & Alfani, F. (2004). Effect of inhibitors released during steam-explosion treatment of poplar wood on subsequent enzymatic hydrolysis and SSF. Biotechnology Progress, 20, 200–206. doi:10.1021/bp0257978
- Carvalheiro, F., Duarte, L. C., & Gírio, F. M. (2008). Hemicellulose biorefineries: A review on biomass pretreatments. Journal of Scientific & Industrial Research, 67, 849–864.
- Castañón-Rodríguez, J. F., Torrestiana-Sánchez, B., Montero-Lagunes, M., Portilla-Arias, J., Ramírez De León, J. A., & Aguilar-Uscanga, M. G. (2013). Using high pressure processing (HPP) to pretreat sugarcane bagasse. Carbohydrate Polymers, 98, 1018–1024. doi:10.1016/j.carbpol.2013.06.068
- Chandra, C. R., Bura, R., Mabee, W. E., Berlin, A., Pan, X., & Saddler, J. N. (2007). Substrate pretreatment: The key to effective enzymatic hydrolysis of lignocellulosic. Advances Biochemical Engineering & Biotechnology, 108, 67–93.
- Chen, W.-H., Tu, Y.-J., & Sheen, H.-K. (2011). Disruption of sugarcane bagasse lignocellulosic structure by means of dilute sulfuric acid pretreatment with microwave-assisted heating. Applied Energy, 88, 2726–2734. doi:10.1016/j.apenergy.2011.02.027
- Dermibas, A. (2005). Bioethanol from cellulosic materials: A renewable motor fuel from biomass. Energy Sources, 21, 327–337.
- Foston, M., & Ragauskas, A. J. (2010). Changes in lignocellulosic supramolecular and ultrastructure during dilute acid pretreatment of Populus and switchgrass. Biomass and Bioenergy, 34, 1885–1895. doi:10.1016/j.biombioe.2010.07.023
- Hereman, K. (2002). High pressure bioscience and biotechnology: A century and a decade perspective. Trends in High Pressure Bioscience and Biotechnology, 19, 1–6.
- Hosseini, S. A., & Shah, N. (2011). Multi-scale process and supply chain modeling from lignocellulosic feedstock to process and products. Interface Focus, 1, 255–262.
- Huang, Z., Liang, X., Hu, H., Gao, L., Chen, Y., & Tong, Z. (2009). Influence of mechanical activation on the graft copolymerization of sugarcane bagasse and acrylic acid. Polymer Degradation and Stability, 94, 1737–1745. doi:10.1016/j.polymdegradstab.2009.06.023
- Kim, Y., Ximenes, E., Mosier, N. S., & Ladisch, M. R. (2011). Soluble inhibitors/deactivators of cellulase enzymes from lignocellulosic biomass. Enzyme and Microbial Technology, 48, 408–415. doi:10.1016/j.enzmictec.2011.01.007
- Martín, C., Klinke, H. B., & Thomsen, A. B. (2007). Wet oxidation as a pretreatment method for enhancing the enzymatic convertibility of sugarcane bagasse. Enzyme Microbial Technology, 40, 426–432. doi:10.1016/j.enzmictec.2006.07.015
- McIntosh, S., & Vancov, T. (2011). Optimisation of dilute alkaline pretreatment for enzymatic saccharification of wheat straw. Biomass and Bioenergy, 35, 3094–3103. doi:10.1016/j.biombioe.2011.04.018
- Ndazi, B. S., Karlsson, S., Tesha, J. V., & Nyahumwa, C. W. (2007). Chemical and physical modifications of rice husks for use as composite panels. Composites Part A: Applied Science and Manufacturing, 38, 925–935. doi:10.1016/j.compositesa.2006.07.004
- Neven, L., Follet, P. A., & Raghubeer, E. (2007). Potential for high hydrostatic pressure processing to control quarantine insects in fruit. Journal of Economic Entomology, 100, 1499–1503. doi:10.1093/jee/100.5.1499
- Pandey, A., Soccol, C. R., Nigam, P., & Soccol, V. T. (2000). Biotechnological potential of agro-industrial residues. I: Sugarcane bagasse. Bioresource Technology, 74, 69–80. doi:10.1016/S0960-8524(99)00142-X
- Pernalete, S., Piña, F., Suarez, M., Ferrer, A., & Aiello, C. (2008). Fraccionamiento del bagazo de cana de azúcar mediante tratamiento amoniacal: Efecto de la humedad del bagazo y la carga de amoniaco. Bioagro, 20, 3–10.
- Široký, J., Blackburn, R. S., Bechtold, T., Taylor, J., & White, P. (2011). Alkali treatment of cellulose II fibres and effect on dye sorption. Carbohydrate Polymers, 84, 299–307. doi:10.1016/j.carbpol.2010.11.037
- Sun, J. X., Sun, X. F., & Zhao, H. (2004). Isolation and characterization of cellulose from sugarcane bagasse. Polymer Degradation and Stability, 84, 331–339. doi:10.1016/j.polymdegradstab.2004.02.008
- Sun, J.-X., Xu, F., Sun, X.-F., Sun, R.-C., & Wu, S.-B. (2004). Comparative study of lignins from ultrasonic irradiated sugar-cane bagasse. Polymer International, 53, 1711–1721. doi:10.1002/pi.1539
- Sun, Y., & Cheng, J. (2002). Hydrolysis of lignocellulosic materials for ethanol production: A review. Bioresource Technology, 83, 1–11. doi:10.1016/S0960-8524(01)00212-7
- Taherzadeh, M. J., & Karimi, K. (2008). Enzyme-based hydrolysis processes for ethanol from lignocellulosic materials: A review. BioResources, 2, 707–738.
- Vadiveloo, J., Nurfariza, B., & Fadel, J. G. (2009). Nutritional improvement of rice husks. Animal Feed Science and Technology, 151, 299–305. doi:10.1016/j.anifeedsci.2009.03.002
- Valdez-Fragoso, A., Mújica-Paz, H., Welti-Chanes, J., & Torres, J. A. (2011). Reaction kinetics at high pressure and temperature: Effects on milk flavor volatiles and on chemical compounds with nutritional and safety importance in several foods. Food Bioprocess Technology, 4, 986–995. doi:10.1007/s11947-010-0489-z
- Vargas Ortiz, M. A., De-la-Cruz-Medina, J., Oliart-Ross, R. M., Rebolledo-Martínez, A., Ramírez, J. A., & García, H. S. (2013). Efecto de las altas presiones hidrostáticas sobre los cambios poscosecha de mango (Mangifera indica) `manila´ en madurez fisiológica. CienciaUAT, 26, 56–63.
- Velmurugan, R., & Muthukumar, K. (2011). Utilization of sugarcane bagasse for bioethanol production: Sono-assisted acid hydrolysis approach. Bioresource Technology, 102, 7119–7123. doi:10.1016/j.biortech.2011.04.045
- Yang, B., Jiang, Y., Wang, R., Zhao, M., & Sun, J. (2009). Ultra-high pressure treatment effects on polysaccharides and lignins of longan fruit pericarp. Food Chemistry, 112, 428–431. doi:10.1016/j.foodchem.2008.05.097
- Yang, B., & Wyman, C. E. (2008). Pretreatment: The key to unlocking low-cost cellulosic ethanol. Biofuels Bioproducts and Biorefining, 2, 26–40. doi:10.1002/bbb.49